Discover Cost-Effective Drawer Slides from China (2025)
Introduction: Navigating the Global Market for drawer slides china
In the rapidly evolving global market, sourcing high-quality drawer slides from China poses unique challenges for international B2B buyers, especially those from regions like Africa, South America, the Middle East, and Europe. The key concerns often revolve around understanding product specifications, ensuring compliance with international standards, and navigating supplier relationships. This guide offers a comprehensive roadmap to help you tackle these challenges effectively.
Within this resource, you will find detailed insights into various types of drawer slides, including ball-bearing, soft-close, and heavy-duty options, tailored to meet diverse application needs. We delve into the intricacies of supplier vetting processes, enabling you to identify reliable manufacturers that align with your quality expectations and budget constraints. Additionally, we explore cost considerations, import regulations, and logistics, providing you with actionable strategies to optimize your purchasing decisions.
By leveraging the information presented in this guide, B2B buyers can make informed choices that enhance their procurement processes, ensuring they secure the best products for their businesses. Whether you are a furniture manufacturer in Vietnam or a cabinetry supplier in Egypt, understanding the nuances of sourcing drawer slides from China can significantly impact your operational efficiency and product quality. Embrace the opportunity to navigate this global market with confidence and clarity.
Understanding drawer slides china Types and Variations
Type Name | Key Distinguishing Features | Primary B2B Applications | Brief Pros & Cons for Buyers |
---|---|---|---|
Ball Bearing Slides | Smooth operation, durable, high load capacity | Furniture manufacturing, cabinetry | Pros: Quiet, strong, easy to install. Cons: Higher cost compared to other types. |
Side Mount Slides | Mounting on the side of drawers, typically less visible | Retail fixtures, office furniture | Pros: Space-efficient, easy access. Cons: Limited weight capacity compared to ball bearing slides. |
Under Mount Slides | Hidden installation under the drawer, soft-close options available | Kitchen cabinets, high-end furniture | Pros: Aesthetic appeal, soft-close feature. Cons: More complex installation. |
Telescopic Slides | Extendable design for full drawer access | Industrial applications, tool storage | Pros: Full extension, heavy-duty options. Cons: Requires more space for installation. |
Roller Slides | Simple design, often made from plastic or steel | Budget furniture, temporary setups | Pros: Cost-effective, easy to replace. Cons: Less durable, limited weight capacity. |
What are the Characteristics of Ball Bearing Slides?
Ball bearing slides are renowned for their smooth operation and high load capacity, making them a preferred choice in various B2B applications, particularly in furniture manufacturing and cabinetry. These slides utilize ball bearings to reduce friction, allowing drawers to glide effortlessly. When considering ball bearing slides, buyers should evaluate the load requirements, installation ease, and overall durability, as these factors can significantly impact performance and longevity in commercial settings.
How Do Side Mount Slides Differ from Other Types?
Side mount slides are characterized by their installation on the sides of the drawers, which often makes them less visible. Commonly used in retail fixtures and office furniture, these slides offer easy access and space efficiency. However, B2B buyers should be aware of their limited weight capacity compared to ball bearing slides. When selecting side mount slides, consider the specific application needs, as well as the drawer’s intended weight load to ensure optimal performance.
Why Choose Under Mount Slides for High-End Furniture?
Under mount slides provide a sleek, hidden installation beneath the drawer, often featuring soft-close mechanisms that enhance the user experience. This makes them particularly suitable for kitchen cabinets and high-end furniture applications where aesthetics are paramount. For B2B buyers, the complexity of installation and potential additional costs should be weighed against the aesthetic benefits and functionality offered by under mount slides.
What are the Advantages of Telescopic Slides in Industrial Applications?
Telescopic slides are designed for full drawer extension, making them ideal for industrial applications and tool storage. Their extendable design allows for easy access to the entire drawer content, which is crucial in settings where efficiency is key. When purchasing telescopic slides, B2B buyers should consider the space available for installation and the weight of items stored, as these factors will influence the type of telescopic slide required for optimal performance.
How Do Roller Slides Compare for Budget-Conscious Buyers?
Roller slides feature a simple design, often made from plastic or steel, making them an economical choice for budget-conscious buyers. They are commonly used in budget furniture and temporary setups where durability is less of a concern. While roller slides are easy to replace, B2B buyers should recognize their limitations in terms of weight capacity and overall durability compared to other slide types. Understanding these trade-offs is essential for making informed purchasing decisions in cost-sensitive projects.
Related Video: How to Install 3 Types of Drawer Slides in Cabinets | WOOD magazine
Key Industrial Applications of drawer slides china
Industry/Sector | Specific Application of drawer slides china | Value/Benefit for the Business | Key Sourcing Considerations for this Application |
---|---|---|---|
Furniture Manufacturing | Kitchen cabinets and storage solutions | Enhances functionality and user experience | Material quality, weight capacity, and warranty terms |
Automotive Industry | Vehicle interior storage compartments | Improves organization and accessibility | Durability under extreme conditions, load ratings |
Healthcare Equipment | Medical carts and mobile storage units | Ensures easy access to medical supplies | Compliance with health standards, corrosion resistance |
Retail Display Solutions | Point-of-sale displays and shelving units | Increases product visibility and customer interaction | Customization options, aesthetic appeal, and lead times |
Industrial Storage Systems | Warehousing and logistics storage solutions | Optimizes space utilization and inventory management | Load capacity, installation requirements, and sourcing speed |
How are Drawer Slides Used in Furniture Manufacturing?
In the furniture manufacturing sector, drawer slides from China are integral to kitchen cabinets and storage solutions. They allow drawers to open and close smoothly, enhancing user experience and functionality. International buyers must focus on material quality and weight capacity, ensuring that the slides can withstand daily use. Furthermore, warranty terms should be considered to protect against defects and ensure long-term satisfaction.
What Role do Drawer Slides Play in the Automotive Industry?
In the automotive industry, drawer slides are used in vehicle interior storage compartments. These slides facilitate the organization and accessibility of tools and equipment within the vehicle, which is crucial for both manufacturers and end-users. Buyers from regions like Africa and South America should prioritize durability under extreme conditions, as well as load ratings to ensure that the slides can handle varying weights and stresses during operation.
Why are Drawer Slides Important for Healthcare Equipment?
Drawer slides are essential in healthcare equipment, particularly in medical carts and mobile storage units. They provide easy access to medical supplies, which is vital for efficient patient care. B2B buyers in the healthcare sector must ensure compliance with health standards and look for corrosion-resistant materials to maintain hygiene. This is particularly important in regions with varying climate conditions, such as the Middle East, where humidity can affect equipment performance.
How are Drawer Slides Used in Retail Display Solutions?
In retail, drawer slides are commonly applied in point-of-sale displays and shelving units. They enhance product visibility and allow for easy access, ultimately improving customer interaction. For international buyers, customization options are crucial, as they may require specific designs to fit their branding. Additionally, aesthetic appeal and lead times should be considered to align with retail launch schedules.
What is the Role of Drawer Slides in Industrial Storage Systems?
In industrial storage systems, drawer slides optimize space utilization and facilitate efficient inventory management. They are commonly used in warehousing and logistics setups, allowing for quick access to stored items. Buyers must evaluate load capacity and installation requirements to ensure that the slides fit their operational needs. Speed of sourcing is also critical, especially in fast-paced industrial environments, to minimize downtime.
Related Video: How To Install Drawer Slides The Easy Way
3 Common User Pain Points for ‘drawer slides china’ & Their Solutions
Scenario 1: Quality Assurance Challenges with Drawer Slides from China
The Problem: International buyers often face significant challenges regarding the quality of drawer slides sourced from China. This can include discrepancies in material strength, poor finish, or even mechanical failure after installation. For businesses in Africa and South America, where local standards may vary, importing subpar products can lead to costly recalls, project delays, and damage to reputation. The challenge is compounded by the language barrier and time zone differences, making it difficult to communicate quality expectations and specifications with suppliers.
The Solution: To mitigate quality assurance issues, B2B buyers should prioritize conducting thorough due diligence on potential suppliers. This includes requesting samples before placing bulk orders to evaluate material quality and durability firsthand. Establishing a clear and detailed specification document that outlines quality standards, testing procedures, and compliance with international norms can bridge the communication gap. Additionally, leveraging third-party inspection services can provide an unbiased assessment of product quality prior to shipment, ensuring that only compliant items reach your facility. Engaging with suppliers who are ISO certified or have other recognized quality certifications can also enhance reliability.
Scenario 2: Navigating Complex Supply Chain Logistics
The Problem: Importing drawer slides from China often involves navigating a complex supply chain that can lead to delays, increased costs, and unexpected complications. For B2B buyers in the Middle East and Europe, factors such as customs regulations, tariffs, and shipping logistics can introduce significant unpredictability. Delays in delivery can disrupt manufacturing schedules and result in financial penalties or lost business opportunities.
The Solution: To streamline supply chain logistics, buyers should invest time in understanding the logistics landscape of their target market. Partnering with experienced freight forwarders who are knowledgeable about customs regulations and tariffs can alleviate many logistical burdens. Building strong relationships with suppliers that offer reliable shipping options is also crucial. Buyers can implement a just-in-time inventory system to maintain flexibility and reduce excess stock costs. Furthermore, utilizing technology platforms that provide real-time tracking of shipments can help in anticipating delays and adjusting project timelines accordingly.
Scenario 3: Customization and Compatibility Issues
The Problem: Many B2B buyers encounter compatibility challenges when integrating drawer slides into existing furniture or cabinetry designs. This is particularly true for businesses in Europe, where design standards may differ significantly from those commonly produced in China. The risk of ordering non-compatible products can lead to increased costs and project delays, as modifications may be necessary to accommodate mismatched hardware.
The Solution: To address customization and compatibility issues, buyers should take a proactive approach by investing in design consultations before sourcing drawer slides. Collaborating with a design engineer who understands both the local requirements and the capabilities of Chinese manufacturers can result in tailored solutions. Additionally, providing manufacturers with detailed CAD drawings and specifications can ensure that the drawer slides meet the exact design requirements. Exploring suppliers that offer modular solutions or customization options can also enhance compatibility with existing products, thus reducing the likelihood of costly modifications post-delivery. Engaging in open dialogue with suppliers about design expectations and limitations from the outset can foster a collaborative approach, ultimately leading to better results.
Strategic Material Selection Guide for drawer slides china
When selecting materials for drawer slides sourced from China, international B2B buyers must consider various factors that impact performance, durability, and compliance with regional standards. Here, we analyze four common materials used in the manufacturing of drawer slides, focusing on their properties, advantages, disadvantages, and implications for buyers from Africa, South America, the Middle East, and Europe.
What are the Key Properties of Steel Drawer Slides?
Steel is one of the most prevalent materials for drawer slides due to its strength and durability. Steel drawer slides typically have a high-temperature rating and excellent corrosion resistance when treated with coatings like zinc or powder. This makes them suitable for a variety of applications, from residential to heavy-duty industrial use.
Pros & Cons: The primary advantage of steel is its robustness, which allows it to handle heavy loads and withstand wear over time. However, steel can be heavier than other materials, which may complicate installation and increase shipping costs. Additionally, untreated steel is prone to rust, necessitating protective coatings that can raise manufacturing complexity and costs.
Impact on Application: Steel drawer slides are compatible with a wide range of media, including heavy tools and equipment in industrial settings. Buyers should ensure that the selected slides meet relevant standards such as ASTM A653 for galvanized steel.
How Does Aluminum Compare as a Material for Drawer Slides?
Aluminum is another popular choice for drawer slides, particularly in applications where weight reduction is critical. Aluminum slides typically have good corrosion resistance and can be anodized for enhanced durability.
Pros & Cons: The lightweight nature of aluminum makes it easier to handle and install, reducing labor costs. However, aluminum is generally less robust than steel, which may limit its use in heavy-duty applications. The cost of aluminum can also be higher than that of steel, impacting overall project budgets.
Impact on Application: Aluminum drawer slides are suitable for lighter applications, such as in kitchen cabinets or office furniture. Buyers should verify compliance with standards like DIN EN 573 for aluminum alloys to ensure quality.
What are the Benefits of Plastic Drawer Slides?
Plastic drawer slides, often made from high-density polyethylene (HDPE) or polyamide, offer unique advantages in specific applications. These materials are lightweight, resistant to moisture, and can withstand a wide range of temperatures.
Pros & Cons: The main advantage of plastic is its resistance to corrosion and moisture, making it ideal for environments like kitchens and bathrooms. However, plastic slides may not support heavy loads as effectively as metal alternatives, limiting their application scope. The manufacturing process can also be less complex, potentially lowering costs.
Impact on Application: Plastic drawer slides are particularly suited for residential furniture and lightweight commercial applications. Buyers should consider compliance with standards like ASTM D638 for tensile properties of plastics.
Why Choose Stainless Steel for Drawer Slides?
Stainless steel is a premium material choice for drawer slides, known for its exceptional resistance to corrosion and high aesthetic appeal. It is often used in environments where hygiene is paramount, such as in hospitals and food service.
Pros & Cons: The primary advantage of stainless steel is its durability and resistance to rust, making it suitable for both indoor and outdoor applications. However, it is typically more expensive than other materials, which could impact budget-sensitive projects.
Impact on Application: Stainless steel drawer slides are ideal for heavy-duty applications and environments with high moisture levels. Buyers should ensure that the products meet standards like ASTM A240 for stainless steel to guarantee quality and performance.
Summary Table of Material Selection for Drawer Slides
Material | Typical Use Case for drawer slides china | Key Advantage | Key Disadvantage/Limitation | Relative Cost (Low/Med/High) |
---|---|---|---|---|
Steel | Industrial and heavy-duty applications | High strength and durability | Heavier, prone to rust without treatment | Medium |
Aluminum | Kitchen cabinets and office furniture | Lightweight and easy to install | Less robust for heavy loads | High |
Plastic | Residential furniture and lightweight commercial | Corrosion-resistant and moisture-proof | Limited load capacity | Low |
Stainless Steel | Hospitals and food service environments | Excellent corrosion resistance | Higher cost | High |
In conclusion, the selection of materials for drawer slides is crucial for ensuring product performance and compliance with regional standards. By understanding the properties, advantages, and limitations of each material, international B2B buyers can make informed decisions that align with their specific application needs and budget constraints.
In-depth Look: Manufacturing Processes and Quality Assurance for drawer slides china
What Are the Main Manufacturing Processes for Drawer Slides in China?
The manufacturing of drawer slides in China involves several critical stages that ensure both functionality and durability. Understanding these processes can help B2B buyers make informed decisions when sourcing these products.
Material Preparation: What Materials Are Used for Drawer Slides?
The first step in the manufacturing process is material preparation. Typically, drawer slides are made from high-quality steel, aluminum, or plastic, depending on the intended application. Steel slides often undergo galvanization or powder coating to enhance corrosion resistance, while aluminum offers a lightweight alternative with good strength-to-weight ratios. Plastic slides, often used in lighter applications, are typically made from high-density polyethylene (HDPE) or polyvinyl chloride (PVC).
Forming: How Are Drawer Slides Shaped?
Once the materials are selected, the next stage is forming. This process involves cutting, bending, and shaping the raw materials into the components of the drawer slides. Techniques such as stamping and extrusion are commonly employed. Stamping involves using a die to cut and shape the metal sheets, while extrusion is mainly used for aluminum to create continuous profiles. Advanced machinery ensures precision and consistency, crucial for ensuring the slides fit correctly and operate smoothly.
Assembly: What Are the Key Steps in Assembling Drawer Slides?
After forming, the components move to the assembly stage. Here, various parts such as rails, brackets, and ball bearings are combined. Automated assembly lines are often used to increase efficiency and reduce labor costs. The use of robotics in this phase can enhance precision, ensuring that all components fit together seamlessly. Quality control measures are implemented during assembly to catch any defects early in the process.
Finishing: What Finishing Techniques Are Used?
The finishing stage is essential for enhancing both the aesthetics and performance of drawer slides. Common finishing techniques include powder coating, anodizing, and plating. Powder coating provides a durable and visually appealing surface, while anodizing is primarily used for aluminum to increase corrosion resistance. Proper finishing not only improves the product’s lifespan but also its marketability, especially for international buyers looking for high-quality finishes.
How Is Quality Assurance Implemented in Drawer Slide Manufacturing?
Quality assurance (QA) is a critical aspect of the drawer slide manufacturing process. Buyers must understand how manufacturers implement QA to ensure that the products meet international standards.
What International Standards Are Relevant for Drawer Slide Quality?
Many manufacturers in China adhere to international quality standards, such as ISO 9001, which outlines requirements for a quality management system. Compliance with this standard indicates that a manufacturer has established processes to ensure consistent product quality. Additionally, certifications like CE (Conformité Européenne) for European markets and API (American Petroleum Institute) for specific industrial applications may also be relevant, depending on the intended use of the drawer slides.
What Are the Key Quality Control Checkpoints?
Quality control is typically integrated at various stages of the manufacturing process. The key checkpoints include:
- Incoming Quality Control (IQC): Inspecting raw materials upon arrival to ensure they meet specified standards.
- In-Process Quality Control (IPQC): Monitoring production processes to catch defects during manufacturing.
- Final Quality Control (FQC): Conducting comprehensive inspections of finished products to ensure they meet all specifications before shipment.
These checkpoints help mitigate the risk of defects and ensure that the products are reliable and durable.
What Testing Methods Are Commonly Used for Drawer Slides?
To ensure that drawer slides meet quality standards, various testing methods are employed. Common tests include:
- Load Testing: This evaluates how much weight the slides can handle without failure.
- Cycle Testing: Assessing the durability of the slides by simulating repeated opening and closing actions.
- Corrosion Resistance Testing: This determines how well the slides withstand environmental factors, particularly for those intended for outdoor or humid environments.
These tests are crucial for validating the performance characteristics of the drawer slides and ensuring they meet the expectations of international buyers.
How Can B2B Buyers Verify Supplier Quality Control?
B2B buyers must take proactive steps to verify the quality control measures of their suppliers in China. Here are some actionable strategies:
Conducting Supplier Audits: What Should Buyers Look For?
Auditing potential suppliers can provide invaluable insights into their manufacturing processes and quality assurance practices. Buyers should look for:
- Documentation of quality management systems.
- Evidence of compliance with international standards.
- Details about their quality control checkpoints and testing methods.
Regular audits can help build trust and ensure that suppliers maintain high standards.
Requesting Quality Reports: What Information Should Be Included?
Buyers should ask suppliers for detailed quality reports that outline the results of their quality control processes. These reports should include:
- Results from IQC, IPQC, and FQC checkpoints.
- Documentation of testing methods and outcomes.
- Certifications obtained from relevant authorities.
These documents serve as proof of the supplier’s commitment to quality and can help buyers make informed purchasing decisions.
Utilizing Third-Party Inspection Services: How Can They Help?
Engaging third-party inspection services can provide an additional layer of assurance. These independent entities can conduct on-site inspections and testing to validate the supplier’s claims. This is especially important for international buyers who may not have the capacity to conduct inspections themselves.
What Are the Quality Control and Certification Nuances for International Buyers?
International buyers, especially from Africa, South America, the Middle East, and Europe, should be aware of specific nuances in quality control and certification:
- Cultural Differences: Understanding the local business culture in China can facilitate better communication regarding quality expectations.
- Regulatory Compliance: Different regions may have unique compliance requirements. Buyers should familiarize themselves with these regulations to ensure that the products meet local standards.
- Language Barriers: Clear communication is crucial. Engaging translators or local representatives can help bridge any gaps in understanding technical specifications and quality requirements.
By taking these factors into account, international B2B buyers can navigate the complexities of sourcing drawer slides from China more effectively, ensuring they receive high-quality products that meet their needs.
Practical Sourcing Guide: A Step-by-Step Checklist for ‘drawer slides china’
The following practical sourcing guide is designed to assist international B2B buyers in the procurement of drawer slides from China. This checklist aims to streamline the sourcing process, ensuring that buyers make informed decisions that align with their operational needs and quality standards.
Step 1: Define Your Technical Specifications
Before initiating the sourcing process, clearly outline your technical requirements for the drawer slides. This includes dimensions, weight capacity, material specifications, and any industry compliance standards relevant to your region. Having a detailed specification will not only help you communicate effectively with potential suppliers but also ensure that you receive products that meet your exact needs.
Step 2: Conduct Market Research for Suppliers
Understanding the market landscape is crucial when sourcing drawer slides from China. Utilize platforms such as Alibaba, Global Sources, and Made-in-China to identify potential suppliers. Pay attention to their product offerings, client reviews, and market reputation to narrow down your choices. This research will provide a solid foundation for further evaluation.
Step 3: Evaluate Potential Suppliers
Before committing to any supplier, conduct a thorough vetting process. Request company profiles, including their manufacturing capabilities and experience in the drawer slide industry. Additionally, ask for case studies or references from buyers in similar markets, which can help you gauge the supplier’s reliability and quality assurance processes.
Step 4: Verify Supplier Certifications
Ensure that the suppliers you are considering have the necessary certifications for quality management systems, such as ISO 9001 or industry-specific certifications relevant to drawer slides. This step is vital as it demonstrates the supplier’s commitment to quality and compliance with international standards. Check if they also have product certifications that are recognized in your target market.
Step 5: Request Samples for Quality Assessment
Before placing a bulk order, always request samples of the drawer slides. This allows you to assess the quality, functionality, and finish of the product firsthand. Evaluate the samples based on your defined specifications and consider testing them under actual usage conditions to ensure they meet your expectations.
Step 6: Negotiate Terms and Conditions
Once you have identified a suitable supplier and assessed the product quality, it’s time to negotiate terms and conditions. Discuss pricing, payment terms, lead times, and shipping arrangements to ensure they align with your budget and operational timeline. Clear communication during this phase can help prevent misunderstandings later on.
Step 7: Establish a Quality Control Process
Finally, set up a quality control process for your orders. This could involve pre-shipment inspections or quality audits to ensure that the drawer slides meet your specifications before they leave the factory. Implementing quality control measures will help mitigate risks associated with product defects and ensure consistent supply chain performance.
By following this structured checklist, B2B buyers can navigate the complexities of sourcing drawer slides from China effectively, ensuring they secure high-quality products that meet their specific requirements.
Comprehensive Cost and Pricing Analysis for drawer slides china Sourcing
What Are the Key Cost Components for Sourcing Drawer Slides from China?
When sourcing drawer slides from China, it is essential to understand the various cost components involved. The primary elements include:
-
Materials: The type of materials used significantly affects the overall cost. Common materials for drawer slides include steel, aluminum, and plastic. Higher quality materials may incur additional costs but can lead to enhanced durability and performance.
-
Labor: Labor costs in China can vary by region and the complexity of the manufacturing process. While labor is generally cheaper in China compared to many Western countries, fluctuating wage rates and labor standards can impact pricing.
-
Manufacturing Overhead: This includes costs associated with factory operations, such as utilities, maintenance, and indirect labor. Efficient manufacturing processes can reduce overhead costs, ultimately benefiting buyers.
-
Tooling: The initial investment in tooling can be substantial, especially for custom designs. Tooling costs should be amortized over the production volume to understand the impact on unit pricing.
-
Quality Control (QC): Quality assurance processes are crucial to ensure product reliability. Investing in robust QC can prevent costly defects and returns, but it adds to the overall cost structure.
-
Logistics: Shipping costs, including freight, customs duties, and insurance, can vary widely based on the shipping method and destination. Understanding Incoterms can help clarify responsibilities and costs.
-
Margin: Suppliers will add a profit margin to their costs. This margin can vary based on the supplier’s pricing strategy and market competition.
How Do Price Influencers Affect Drawer Slide Costs?
Several factors influence the pricing of drawer slides, which are essential for international buyers to consider:
-
Volume/MOQ: Minimum Order Quantities (MOQ) can significantly affect pricing. Larger orders often result in lower per-unit costs due to economies of scale. Buyers should evaluate their needs and negotiate favorable terms.
-
Specifications and Customization: Custom designs or specific specifications can increase costs. Buyers should balance their requirements with their budget, as high customization might not always yield proportional benefits.
-
Materials and Quality Certifications: The choice of materials and the presence of quality certifications (e.g., ISO, CE) can affect pricing. Certified products may command higher prices but offer greater reliability and market acceptance.
-
Supplier Factors: Supplier reputation, experience, and location can influence pricing. Established suppliers may charge a premium, but their reliability can lead to long-term savings.
-
Incoterms: Understanding the implications of different Incoterms (e.g., FOB, CIF) is crucial for cost management. These terms dictate who bears the cost and risk at various stages of transport.
What Are the Best Negotiation Tips for International Buyers?
Negotiating effectively can lead to significant savings when sourcing drawer slides from China:
-
Research and Benchmarking: Conduct thorough market research to understand typical pricing and terms. Use this data to negotiate from a position of knowledge.
-
Build Relationships: Establishing a good rapport with suppliers can lead to better pricing and more favorable terms. Long-term partnerships often yield benefits beyond initial pricing.
-
Focus on Total Cost of Ownership (TCO): Instead of just looking at the purchase price, consider the TCO, which includes maintenance, shipping, and potential replacement costs. This perspective can justify higher upfront costs for better quality products.
-
Explore Payment Terms: Flexible payment terms can improve cash flow. Consider negotiating for extended payment terms or discounts for early payments.
-
Be Prepared to Walk Away: Having alternative suppliers can strengthen your negotiating position. If a supplier is unwilling to meet your needs, being prepared to explore other options can lead to better outcomes.
What Are the Pricing Nuances for B2B Buyers from Different Regions?
International buyers, particularly from Africa, South America, the Middle East, and Europe, should be aware of regional pricing nuances:
-
Currency Fluctuations: Exchange rates can impact pricing significantly. Buyers should consider hedging strategies or negotiating prices in a stable currency.
-
Import Regulations: Customs duties and import regulations vary by country and can add to the total cost. Understanding local regulations can help avoid unexpected expenses.
-
Cultural Differences in Negotiation: Different regions may have varying negotiation styles. Being aware of these differences can aid in effective communication and deal-making.
Disclaimer on Indicative Prices
While this analysis provides insights into the cost structure and pricing dynamics of drawer slides from China, actual prices can vary based on market conditions, supplier relationships, and specific buyer requirements. It is advisable for buyers to obtain detailed quotes and conduct due diligence before finalizing any agreements.
Alternatives Analysis: Comparing drawer slides china With Other Solutions
Understanding the Importance of Alternative Solutions for Drawer Slides
In the competitive landscape of B2B manufacturing and sourcing, it is crucial for buyers to evaluate multiple options when considering drawer slides. While ‘drawer slides China’ has gained popularity for its affordability and variety, there are several alternatives that may better suit specific business needs. This analysis will compare drawer slides from China with two viable alternatives: European drawer slide systems and ball-bearing drawer slides.
Comparison Table
Comparison Aspect | Drawer Slides China | European Drawer Slide Systems | Ball-Bearing Drawer Slides |
---|---|---|---|
Performance | Good load capacity, decent durability | High precision, long lifespan | Smooth operation, low friction |
Cost | Generally low-cost | Higher initial investment | Moderate pricing, value for quality |
Ease of Implementation | Simple installation, requires basic tools | Requires skilled labor for installation | User-friendly, can be DIY installed |
Maintenance | Low maintenance, but quality varies | Low maintenance, premium materials | Regular maintenance recommended for longevity |
Best Use Case | General applications, budget-sensitive projects | High-end furniture, precision-required environments | Commercial and residential use, where smooth operation is critical |
What Are the Pros and Cons of European Drawer Slide Systems?
European drawer slide systems are known for their exceptional quality and precision. They typically feature advanced engineering, making them suitable for high-end furniture and applications where aesthetics and functionality are paramount. However, the main drawback is the higher cost, which might not align with budget-sensitive projects. Additionally, installation can require skilled labor, adding to overall expenses.
How Do Ball-Bearing Drawer Slides Compare in Performance?
Ball-bearing drawer slides offer a smooth and quiet operation, making them ideal for environments where noise reduction is essential, such as in residential settings. They are moderately priced, providing a good balance between quality and affordability. However, they may require more frequent maintenance than other options, as the ball bearings can accumulate dust and debris over time, potentially affecting performance. Their installation process is generally straightforward, appealing to DIY enthusiasts.
Conclusion: How to Choose the Right Drawer Slide Solution for Your Needs
When selecting the right drawer slide solution, international B2B buyers should carefully consider their specific requirements, including budget constraints, installation capabilities, and performance expectations. While drawer slides from China offer an attractive price point, alternatives like European systems and ball-bearing slides may provide enhanced durability and functionality. Evaluating these factors will ensure that you choose a solution that aligns with your operational needs and market demands, ultimately leading to improved product satisfaction and customer loyalty.
Essential Technical Properties and Trade Terminology for drawer slides china
What Are the Key Technical Properties of Drawer Slides from China?
When sourcing drawer slides from China, understanding their technical specifications is crucial for making informed purchasing decisions. Here are some essential properties to consider:
1. Material Grade
The material grade of drawer slides significantly affects their durability and load-bearing capacity. Common materials include steel, aluminum, and plastic. Steel slides typically offer the best strength and longevity, while aluminum provides a lighter alternative with corrosion resistance. For B2B buyers, selecting the right material is essential to ensure product longevity and reliability in various applications.
2. Load Capacity
Load capacity refers to the maximum weight a drawer slide can support safely. This specification is critical for applications ranging from residential furniture to industrial storage solutions. B2B buyers should carefully evaluate the load requirements of their end products to choose drawer slides that meet or exceed these needs, preventing potential failures and ensuring customer satisfaction.
3. Tolerance
Tolerance indicates the acceptable limits of variation in the dimensions of the drawer slides. High tolerance levels ensure that slides fit perfectly within the intended space, reducing installation issues. For international buyers, understanding tolerance is vital for maintaining quality control and ensuring compatibility with existing furniture or cabinetry designs.
4. Slide Mechanism Type
Different slide mechanisms include ball-bearing, roller, and soft-close systems. Ball-bearing slides offer smooth operation and durability, while soft-close mechanisms provide a gentle closure, enhancing user experience. B2B buyers should consider the operational needs of their products when selecting slide mechanisms, as this can significantly impact functionality and customer satisfaction.
5. Finish and Coating
The finish and coating of drawer slides influence their resistance to wear, corrosion, and aesthetics. Common finishes include zinc plating, powder coating, and chrome plating. A proper finish not only extends the life of the slides but also enhances their visual appeal, which is important for furniture manufacturers looking to attract customers with stylish designs.
What Are Common Trade Terms Associated with Drawer Slides?
Understanding industry jargon is critical for effective communication and negotiation in B2B transactions. Here are some common trade terms related to drawer slides:
1. OEM (Original Equipment Manufacturer)
OEM refers to companies that produce parts or equipment that may be marketed by another manufacturer. For B2B buyers, partnering with OEMs can provide access to high-quality products tailored to specific needs, often at competitive prices.
2. MOQ (Minimum Order Quantity)
MOQ is the smallest quantity of a product that a supplier is willing to sell. Knowing the MOQ is essential for buyers to manage inventory costs and ensure they are purchasing enough to meet demand without overcommitting resources.
3. RFQ (Request for Quotation)
An RFQ is a document issued by buyers to solicit price quotes from suppliers. This process helps buyers compare costs and terms from multiple vendors, ensuring they make informed decisions based on budget and quality requirements.
4. Incoterms (International Commercial Terms)
Incoterms are standardized trade terms that define the responsibilities of buyers and sellers in international transactions. Understanding these terms is crucial for buyers to clarify shipping responsibilities, insurance, and risks involved in the delivery process.
5. Lead Time
Lead time is the period between placing an order and receiving the goods. For international B2B buyers, being aware of lead times helps in planning inventory and managing customer expectations, especially in industries with tight deadlines.
By familiarizing yourself with these essential technical properties and trade terminology, you can navigate the complexities of sourcing drawer slides from China more effectively, ensuring that you make informed, strategic purchasing decisions.
Navigating Market Dynamics and Sourcing Trends in the drawer slides china Sector
What Are the Current Market Dynamics and Key Trends in the Drawer Slides Sector?
The drawer slides market, particularly in China, is experiencing significant growth driven by several global factors. An increasing demand for furniture and cabinetry, coupled with rapid urbanization in emerging markets, has led to a surge in the production of drawer slides. B2B buyers from Africa, South America, the Middle East, and Europe should be aware of the rising trend of customization in product offerings. Manufacturers are increasingly focusing on tailored solutions that meet specific customer requirements, enhancing their competitive edge.
Technological advancements also play a crucial role in shaping sourcing trends. The integration of smart technologies into furniture design is becoming more prevalent. For instance, drawer slides equipped with soft-close mechanisms and motion sensors are gaining popularity, appealing to a tech-savvy consumer base. International buyers should explore partnerships with manufacturers who are investing in R&D to innovate their product lines, ensuring they stay ahead of market demands.
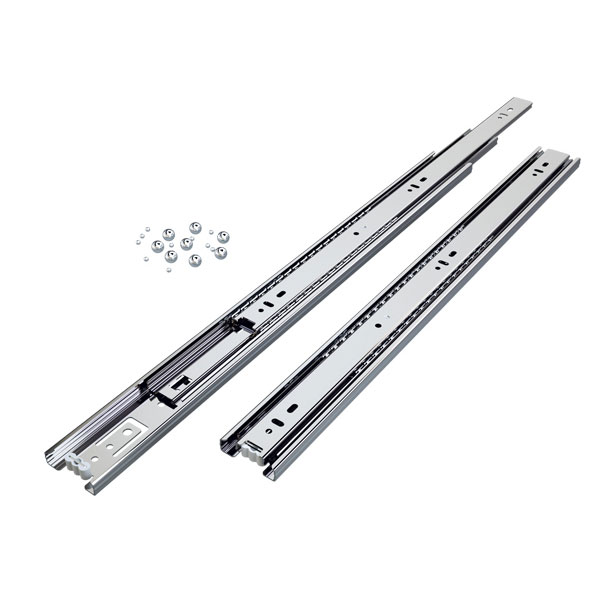
A stock image related to drawer slides china.
Furthermore, the impact of digital platforms in streamlining the sourcing process cannot be overlooked. B2B marketplaces are facilitating direct connections between suppliers and buyers, enabling easier access to a wider range of drawer slide options. This trend is particularly beneficial for buyers in regions like Africa and South America, where traditional sourcing methods may be less efficient.
How Important Is Sustainability and Ethical Sourcing in the Drawer Slides Sector?
Sustainability has become a pivotal concern for B2B buyers in the drawer slides market. The environmental impact of production processes, particularly in terms of resource consumption and waste generation, is under scrutiny. Buyers should prioritize suppliers who adopt sustainable manufacturing practices. This includes using eco-friendly materials, reducing emissions, and implementing waste management systems.
Ethical sourcing is equally significant, as businesses are increasingly held accountable for their supply chain practices. Buyers should seek manufacturers that can provide transparency regarding their sourcing of raw materials and labor practices. Certifications such as ISO 14001 (Environmental Management) and FSC (Forest Stewardship Council) can serve as indicators of a supplier’s commitment to sustainability and ethical practices.
In addition, the use of ‘green’ materials in the production of drawer slides, such as recycled metals and sustainable wood, is on the rise. By choosing suppliers who prioritize these materials, buyers not only enhance their brand reputation but also contribute positively to environmental conservation.
How Has the Drawer Slides Market Evolved Over Time?
The evolution of the drawer slides market can be traced back to the industrial revolution, which marked the beginning of mass production techniques. Initially, drawer slides were simple mechanisms made from basic materials. However, over the decades, advancements in manufacturing processes and materials have transformed the sector.
The introduction of ball-bearing slides in the mid-20th century revolutionized the functionality and ease of use of drawer slides. This innovation allowed for smoother operation and increased weight capacity, making them a staple in modern furniture design. Today, the market is characterized by continuous innovation, with manufacturers exploring new technologies and materials to meet evolving consumer demands.
Understanding this historical context can provide B2B buyers with insights into the ongoing innovations and trends that shape the drawer slides industry, guiding their sourcing strategies for future needs.
Frequently Asked Questions (FAQs) for B2B Buyers of drawer slides china
-
How do I choose the right drawer slides for my products?
Selecting the appropriate drawer slides involves understanding the weight capacity, length, and material needed for your specific application. Consider the type of drawer you are designing—whether it’s for kitchen cabinets, office furniture, or industrial use. Additionally, evaluate the slide mechanism, such as ball-bearing or roller slides, based on durability and smooth operation. Consult with suppliers in China who can provide samples and specifications to ensure compatibility with your design requirements. -
What are the key factors when sourcing drawer slides from China?
When sourcing drawer slides from China, consider the manufacturer’s reputation, quality certifications (like ISO 9001), and production capabilities. Verify their compliance with international standards, especially if you are importing into regions with strict regulations. Additionally, assess their ability to handle customization requests and their experience in exporting to your specific market, whether in Africa, South America, the Middle East, or Europe. -
What customization options are available for drawer slides from Chinese suppliers?
Many Chinese manufacturers offer customization options such as length, finish, color, and load capacity. Some suppliers may also provide branding services, allowing you to add your logo or unique packaging. Discuss your specific needs with potential suppliers and request prototypes to evaluate the quality and fit for your products. Ensure to confirm the minimum order quantities (MOQs) for customized items, as these can vary significantly among suppliers. -
What is the typical minimum order quantity (MOQ) for drawer slides from China?
The MOQ for drawer slides can vary widely based on the manufacturer and the specific product. Generally, it ranges from 500 to 1,000 pieces, but some suppliers may offer lower MOQs for standard products. Discuss your requirements upfront to find suppliers willing to accommodate your order size, particularly if you’re a smaller business or just starting. Be prepared to negotiate terms that align with your inventory management strategies. -
What payment terms should I expect when ordering from Chinese suppliers?
Payment terms can vary but typically include options like a 30% deposit upon order confirmation and the remaining 70% before shipment. Some suppliers may offer letters of credit or PayPal for smaller orders. It’s crucial to establish clear payment terms in your contract to protect your interests. Consider using escrow services for high-value transactions to ensure that funds are only released when you receive your goods as agreed. -
How can I ensure quality assurance when purchasing drawer slides from China?
To ensure quality assurance, request samples from potential suppliers before placing a large order. Implement a thorough quality control process, including inspections during production and pre-shipment checks. Consider hiring third-party inspection services to verify product quality and compliance with your specifications. Establish clear quality standards in your contract, and communicate these expectations with your supplier to minimize risks. -
What logistics considerations should I keep in mind when importing drawer slides from China?
Logistics is crucial when importing drawer slides. Consider shipping methods (air freight vs. sea freight) based on your budget and urgency. Factor in customs duties, taxes, and any additional fees that may arise during shipping. Collaborate with a reliable freight forwarder experienced in handling imports from China to ensure smooth delivery. Additionally, maintain clear communication with your supplier regarding shipping schedules and tracking information. -
What are common challenges faced by B2B buyers when sourcing drawer slides from China?
Common challenges include language barriers, cultural differences, and varying quality standards. Buyers may also encounter issues with supplier reliability and communication delays. To mitigate these risks, conduct thorough research on potential suppliers, utilize platforms that facilitate trade, and consider hiring local agents who understand the market dynamics. Building strong relationships with your suppliers can also help address challenges more effectively and foster long-term partnerships.
Important Disclaimer & Terms of Use
⚠️ Important Disclaimer
The information provided in this guide, including content regarding manufacturers, technical specifications, and market analysis, is for informational and educational purposes only. It does not constitute professional procurement advice, financial advice, or legal advice.
While we have made every effort to ensure the accuracy and timeliness of the information, we are not responsible for any errors, omissions, or outdated information. Market conditions, company details, and technical standards are subject to change.
B2B buyers must conduct their own independent and thorough due diligence before making any purchasing decisions. This includes contacting suppliers directly, verifying certifications, requesting samples, and seeking professional consultation. The risk of relying on any information in this guide is borne solely by the reader.
Strategic Sourcing Conclusion and Outlook for drawer slides china
In the rapidly evolving landscape of global manufacturing, strategic sourcing of drawer slides from China presents a wealth of opportunities for international B2B buyers. Key takeaways highlight the importance of understanding market dynamics, quality assurance, and establishing strong supplier relationships. By leveraging China’s extensive manufacturing capabilities and competitive pricing, buyers can significantly enhance their product offerings while maintaining cost efficiency.
What are the benefits of forging partnerships with Chinese suppliers? Establishing direct connections can lead to better communication, customization options, and reduced lead times. Moreover, as global trade policies continue to shift, maintaining flexibility in sourcing strategies will be crucial for navigating potential disruptions.
Looking ahead, the demand for innovative and sustainable drawer slide solutions is poised to grow, particularly in emerging markets across Africa, South America, the Middle East, and Europe. International buyers should actively engage with suppliers to explore new technologies and sustainable practices that align with their business goals.
Now is the time to initiate conversations with Chinese manufacturers and capitalize on the advantages they offer. Embrace the potential of strategic sourcing to drive your business forward in a competitive marketplace.