The Ultimate Guide to Kitchen Scale Manufacturer (2025)
Introduction: Navigating the Global Market for kitchen scale manufacturer
In today’s competitive landscape, sourcing reliable kitchen scales that meet both quality and functionality standards poses a significant challenge for international B2B buyers. With a growing demand across various sectors—ranging from culinary arts to food production—understanding the global market for kitchen scale manufacturers is crucial. This guide delves into the complexities of selecting the right kitchen scales by examining different types, their applications, and the critical factors to consider when evaluating suppliers.
International buyers, particularly from regions such as Africa, South America, the Middle East, and Europe, will find actionable insights tailored to their unique market dynamics. We will explore essential criteria for vetting suppliers, including quality assurance, production capabilities, and compliance with international standards. Additionally, we will address cost considerations, helping you to navigate pricing structures and negotiate favorable terms without compromising on quality.
By the end of this guide, you will be equipped with the knowledge needed to make informed purchasing decisions. Whether you are a retailer looking to expand your product line or a manufacturer seeking reliable components, understanding the nuances of the kitchen scale market will empower you to source effectively and enhance your business operations. Prepare to streamline your procurement process and forge lasting partnerships with reputable kitchen scale manufacturers globally.
Understanding kitchen scale manufacturer Types and Variations
Type Name | Key Distinguishing Features | Primary B2B Applications | Brief Pros & Cons for Buyers |
---|---|---|---|
Mechanical Kitchen Scales | Analog display, no batteries required | Restaurants, bakeries, and small cafes | Pros: Durable, low maintenance. Cons: Less precise than digital scales. |
Digital Kitchen Scales | Electronic display, often with tare and unit conversion | Food processing, catering, and retail | Pros: High precision, easy to read. Cons: Requires batteries, may be less durable. |
Portion Control Scales | Designed for portioning food, often with preset weights | Meal prep services, nutrition-focused businesses | Pros: Streamlines portioning, improves consistency. Cons: Limited weight capacity. |
Smart Kitchen Scales | Connects to apps for tracking and analytics | Health-focused businesses, meal delivery | Pros: Offers data insights, user-friendly. Cons: Higher cost, requires connectivity. |
Industrial Kitchen Scales | Heavy-duty scales for large quantities and bulk items | Food manufacturing, logistics, and export | Pros: Robust, designed for high capacity. Cons: Bulky, can be expensive. |
What Are the Key Characteristics of Mechanical Kitchen Scales?
Mechanical kitchen scales are traditional, analog devices that do not rely on batteries or electricity. They typically feature a spring mechanism that measures weight based on the compression of the spring. These scales are particularly suited for environments like restaurants and bakeries where durability and low maintenance are crucial. When considering a mechanical scale, B2B buyers should assess the scale’s capacity and build quality, as these factors can significantly impact longevity and reliability in high-usage settings.
How Do Digital Kitchen Scales Enhance Precision?
Digital kitchen scales utilize electronic sensors to provide precise weight measurements, often displaying results on an LCD screen. They usually come with features such as tare functionality and unit conversion, making them ideal for food processing, catering, and retail environments. B2B buyers should focus on the scale’s accuracy, ease of use, and battery life when making a purchasing decision. While digital scales offer high precision, it is essential to consider the potential for higher replacement costs due to battery dependency.
Why Choose Portion Control Scales for Food Services?
Portion control scales are specifically designed for businesses that require consistent food portioning, such as meal prep services or nutrition-focused establishments. These scales often come with preset weights, enabling users to measure ingredients quickly and accurately. Buyers should evaluate the scale’s weight capacity and ease of use, as these factors can influence operational efficiency. While these scales enhance portion consistency, they may have limitations in terms of maximum weight capacity, making them less versatile for larger items.
What Advantages Do Smart Kitchen Scales Offer?
Smart kitchen scales connect to mobile applications, allowing users to track nutritional data and analyze consumption trends. This feature is particularly beneficial for health-focused businesses and meal delivery services that prioritize customer engagement and data-driven insights. When considering a smart kitchen scale, B2B buyers should evaluate the connectivity options, app functionality, and overall cost. While these scales offer advanced features, the investment can be higher compared to traditional models, and they require a stable internet connection for optimal use.
When Should Businesses Invest in Industrial Kitchen Scales?
Industrial kitchen scales are designed to handle large quantities and bulk items, making them suitable for food manufacturing, logistics, and export operations. These scales are built for robustness and can often accommodate heavier loads than standard kitchen scales. B2B buyers should consider the scale’s weight capacity, accuracy, and durability when making their selection. Although these scales are essential for high-volume environments, they tend to be bulkier and may come at a higher price point, which should be factored into the overall budget.
Related Video: Variations In Construction Projects Explained
Key Industrial Applications of kitchen scale manufacturer
Industry/Sector | Specific Application of Kitchen Scale Manufacturer | Value/Benefit for the Business | Key Sourcing Considerations for this Application |
---|---|---|---|
Food Processing | Ingredient Measurement in Production | Ensures accurate formulation, reducing waste and costs | Durability, precision, and compliance with food safety standards |
Retail | Portion Control in Food Service | Enhances customer satisfaction through consistent serving sizes | Portability, ease of use, and battery life |
Pharmaceutical | Compounding and Formulation | Guarantees accurate dosages, improving product quality | Calibration capabilities, load capacity, and regulatory compliance |
Agriculture | Feed Measurement for Livestock | Optimizes feed costs and livestock health | Weather resistance, ease of cleaning, and capacity for bulk measurement |
Hospitality | Recipe Standardization in Catering Services | Streamlines operations and ensures menu consistency | User-friendly interface, multi-unit conversions, and maintenance support |
How is Kitchen Scale Manufacturer Used in Food Processing?
In the food processing industry, kitchen scales are crucial for ingredient measurement during production. Manufacturers require precise weights to ensure the correct formulation of products, which helps in minimizing waste and controlling costs. International B2B buyers should consider scales that meet food safety standards and offer durability for continuous use in high-volume environments. Additionally, features like easy calibration and high load capacity can significantly enhance operational efficiency.
What Role Do Kitchen Scales Play in Retail?
In the retail sector, particularly within food service environments, kitchen scales are employed for portion control. This application not only ensures that customers receive consistent serving sizes but also aids in managing inventory effectively. For buyers in regions like Africa and South America, sourcing scales that are portable, easy to operate, and have a long battery life is essential to accommodate varying operational conditions and enhance customer satisfaction.
How Are Kitchen Scales Used in Pharmaceuticals?
The pharmaceutical industry relies on kitchen scales for accurate compounding and formulation of medications. Accurate dosing is critical to product quality and patient safety, making high-precision scales a necessity. When sourcing kitchen scales for this application, international buyers should prioritize calibration capabilities, load capacity, and compliance with regulatory standards to ensure that their operations meet industry requirements and maintain high-quality outputs.
What is the Importance of Kitchen Scales in Agriculture?
In agriculture, kitchen scales are used to measure feed for livestock, helping optimize feed costs and ensuring animal health. Accurate measurement is vital for balancing nutritional needs and preventing overfeeding. Buyers should look for scales that can withstand outdoor conditions, are easy to clean, and have the capacity to handle bulk measurements. These features are especially important for agricultural operations in regions with diverse climates.
How Do Kitchen Scales Benefit the Hospitality Industry?
In the hospitality sector, kitchen scales facilitate recipe standardization, crucial for catering services. By ensuring that ingredients are measured accurately, businesses can streamline their operations and maintain consistency across menus. B2B buyers in Europe and the Middle East should seek user-friendly scales that offer multi-unit conversions and robust maintenance support to cater to various culinary needs and enhance operational efficiency.
Related Video: Uses and Gratifications Theory – UGT
3 Common User Pain Points for ‘kitchen scale manufacturer’ & Their Solutions
Scenario 1: Inaccurate Weighing and Measurement Challenges
The Problem: In the fast-paced environments of restaurants and food processing plants, B2B buyers often encounter the issue of inaccurate weighing. This can lead to significant discrepancies in recipe formulations, resulting in inconsistent product quality. For example, a bakery that uses a kitchen scale to measure ingredients may find that their cakes differ in texture and flavor if the scale provides inconsistent readings. Such variations can not only affect customer satisfaction but also lead to wastage of ingredients and increased operational costs.
The Solution: To address this challenge, buyers should prioritize sourcing kitchen scales with high precision and stability. Look for models that offer features such as tare functions, calibration options, and a clear digital display. When specifying a kitchen scale, ensure it is suited for the specific range of weights you will be using, with a minimum readability of 0.1 grams for fine measurements. Additionally, implementing a regular calibration schedule—perhaps weekly or bi-weekly depending on usage—can maintain accuracy. Partnering with reputable manufacturers who provide clear guidelines on maintenance and calibration will also enhance the reliability of the scales over time.
Scenario 2: Lack of Durability in Commercial Kitchen Settings
The Problem: In commercial kitchens, equipment must endure constant use and the occasional mishap. Many B2B buyers have experienced the frustration of kitchen scales that break or malfunction due to the rigors of the environment, leading to downtime and costly replacements. For instance, a catering service that relies on portable scales for various events may find themselves without functional equipment during critical times, impacting service delivery and customer satisfaction.
The Solution: Buyers should focus on sourcing kitchen scales that are specifically designed for commercial use, featuring durable materials such as stainless steel or high-grade plastic that can withstand frequent handling and exposure to moisture. It is advisable to inquire about the scale’s IP rating, which indicates its resistance to dust and water. Furthermore, consider investing in warranty programs that cover repairs or replacements, ensuring that you’re protected against unexpected breakdowns. Engaging with manufacturers who have a track record of producing robust, long-lasting kitchen scales will help mitigate this pain point significantly.
Scenario 3: Difficulty in Integration with Inventory Management Systems
The Problem: Many businesses struggle with integrating their kitchen scales into existing inventory management systems, which can lead to inefficient operations and inaccurate stock levels. For example, a food distributor might find that manually inputting measurements from kitchen scales into inventory software creates delays and increases the risk of human error, ultimately affecting order fulfillment and inventory tracking.
The Solution: To overcome integration issues, buyers should look for kitchen scales that offer connectivity options such as Bluetooth or USB interfaces. Scales with built-in software or compatibility with popular inventory management systems can streamline data transfer, allowing for real-time updates and reducing manual entry errors. When selecting a kitchen scale, ask manufacturers about their data integration capabilities and ensure that they provide adequate technical support for installation and troubleshooting. Additionally, training staff on how to use these integrated systems effectively will maximize the benefits of the new equipment. By prioritizing technology-friendly kitchen scales, businesses can enhance their operational efficiency and maintain accurate inventory records.
Strategic Material Selection Guide for kitchen scale manufacturer
When selecting materials for kitchen scales, manufacturers must consider several factors that directly influence product performance, durability, and market acceptance. Below, we analyze four common materials used in kitchen scale manufacturing, highlighting their properties, advantages, disadvantages, and specific considerations for international B2B buyers.
What are the Key Properties of Stainless Steel in Kitchen Scales?
Stainless steel is a popular choice for kitchen scales due to its excellent corrosion resistance and durability. It can withstand high temperatures and is relatively easy to clean, making it suitable for kitchen environments. The material typically has a temperature rating of up to 800°F (427°C) and is resistant to rust and staining.
Pros & Cons:
The primary advantage of stainless steel is its longevity and resistance to wear and tear. However, it can be more expensive than other materials and may require specialized manufacturing processes, which can increase production costs.
Impact on Application:
Stainless steel scales are compatible with a wide range of media, including liquids and solids, making them versatile for various kitchen applications.
Considerations for International Buyers:
Buyers from regions like Europe and the Middle East should ensure compliance with food safety standards, such as those set by the European Food Safety Authority (EFSA) and the U.S. Food and Drug Administration (FDA). Additionally, ASTM standards related to stainless steel grades should be considered to ensure quality.
How Does Plastic Compare as a Material for Kitchen Scales?
Plastic is another commonly used material in kitchen scale manufacturing, particularly for the outer casing and components. It is lightweight, cost-effective, and can be molded into various shapes.
Pros & Cons:
While plastic is less durable than stainless steel, it offers a lower manufacturing complexity and cost, making it attractive for budget-conscious buyers. However, plastics may not withstand high temperatures and can degrade over time, especially if exposed to certain chemicals.
Impact on Application:
Plastic scales are often used for lighter applications, such as measuring dry ingredients. However, they may not be suitable for heavy-duty use or for measuring liquids that could react with the plastic.
Considerations for International Buyers:
B2B buyers in Africa and South America should be aware of local regulations regarding plastic materials, especially concerning food safety and environmental impact. Compliance with standards like ISO 9001 can also be beneficial.
What are the Advantages of Glass in Kitchen Scale Manufacturing?
Glass is often used for the weighing surface in kitchen scales due to its aesthetic appeal and ease of cleaning. It offers a smooth surface that is less likely to harbor bacteria.
Pros & Cons:
The key advantage of glass is its non-reactive nature, which makes it safe for measuring various food items. However, glass is fragile and can break easily, posing a risk in busy kitchen environments. It is also heavier than plastic, which may affect portability.
Impact on Application:
Glass scales are ideal for measuring dry and liquid ingredients, particularly in settings where aesthetics matter, such as in high-end kitchens or restaurants.
Considerations for International Buyers:
Buyers in Europe and the Middle East should ensure that the glass used meets safety standards to prevent breakage and injury. Compliance with regulations such as EN 1186 is crucial for food contact materials.
How Does Aluminum Fit into the Kitchen Scale Material Selection?
Aluminum is gaining traction in kitchen scale manufacturing due to its lightweight nature and good strength-to-weight ratio. It is often used for structural components or as an alloy in combination with other materials.
Pros & Cons:
Aluminum scales are lightweight and resistant to corrosion, making them suitable for various kitchen environments. However, they may not be as durable as stainless steel and can be prone to scratching.
Impact on Application:
Aluminum is suitable for both solid and liquid measurements, but care must be taken to avoid using it with highly acidic substances, which can cause corrosion.
Considerations for International Buyers:
B2B buyers from regions like Africa and South America should consider local sourcing options for aluminum to reduce costs. Compliance with standards such as ASTM B221 for aluminum alloy specifications is also important.
Summary Table of Material Selection for Kitchen Scales
Material | Typical Use Case for kitchen scale manufacturer | Key Advantage | Key Disadvantage/Limitation | Relative Cost (Low/Med/High) |
---|---|---|---|---|
Stainless Steel | Heavy-duty kitchen scales | Excellent durability and corrosion resistance | Higher cost and manufacturing complexity | High |
Plastic | Budget-friendly kitchen scales | Lightweight and cost-effective | Less durable and temperature sensitive | Low |
Glass | Aesthetic and hygienic kitchen scales | Non-reactive and easy to clean | Fragile and heavy | Medium |
Aluminum | Lightweight and portable kitchen scales | Good strength-to-weight ratio | Prone to scratching and corrosion with acids | Medium |
This strategic material selection guide provides B2B buyers with critical insights into the materials used in kitchen scale manufacturing, enabling informed purchasing decisions that align with their operational needs and compliance requirements.
In-depth Look: Manufacturing Processes and Quality Assurance for kitchen scale manufacturer
What Are the Main Stages of the Kitchen Scale Manufacturing Process?
The manufacturing process for kitchen scales typically involves several key stages, each crucial for ensuring the quality and functionality of the final product. The main stages include material preparation, forming, assembly, and finishing.
Material Preparation: What Materials Are Used?
Material preparation is the first step in the manufacturing process. Common materials used in kitchen scales include:
- Plastic: Lightweight and cost-effective, often used for the body.
- Stainless Steel: Provides durability and a sleek appearance, frequently used for the weighing platform.
- Electronic Components: Such as sensors and display screens, vital for accurate weight measurement.
Buyers should ensure that suppliers source high-quality materials that comply with relevant safety and environmental standards.
How Is Forming Done in Kitchen Scale Manufacturing?
Once materials are prepared, the next stage is forming. This involves shaping the components through various techniques:
- Injection Molding: Commonly used for plastic parts, allowing for complex designs and high-volume production.
- Metal Stamping: Utilized for stainless steel components, ensuring precision in shape and size.
- Circuit Board Assembly: Involves soldering electronic components onto printed circuit boards (PCBs) for electronic scales.
Understanding these techniques can help buyers assess the capabilities and technology used by potential suppliers.
What Does the Assembly Process Entail?
The assembly stage is where all the individual components come together to create the final product. This includes:
- Integrating Electronic Components: Connecting the PCB to the display and weighing sensors.
- Final Assembly: Combining the plastic and metal parts, ensuring everything fits correctly and operates smoothly.
Effective assembly processes often involve automated systems, which can enhance efficiency and reduce labor costs. Buyers should inquire about the level of automation and workforce skills to gauge production capabilities.
How Is Finishing Achieved for Kitchen Scales?
The finishing stage involves adding the final touches to the kitchen scales. This can include:
- Surface Treatment: Applying coatings to enhance aesthetics and durability.
- Calibration: Ensuring that each scale provides accurate measurements before packaging.
- Quality Checks: Conducting inspections to identify any defects or inconsistencies.
Buyers should request information on finishing processes to ensure that the products meet their desired quality standards.
What Are the International Standards for Quality Assurance in Kitchen Scale Manufacturing?
Quality assurance (QA) is critical in the manufacturing process, particularly for kitchen scales, where accuracy and reliability are paramount. International standards such as ISO 9001 provide frameworks for establishing effective quality management systems.
How Do International Standards Impact Kitchen Scale Quality?
ISO 9001 focuses on consistent quality in products and services. Compliance with this standard indicates that a manufacturer has implemented processes to enhance customer satisfaction and continually improve their operations.
In addition to ISO 9001, kitchen scales may also need to adhere to specific industry standards such as:
- CE Marking: Required for products sold in the European Economic Area, indicating conformity with health, safety, and environmental protection standards.
- API Certification: Important for electronic components, ensuring they meet rigorous safety and performance criteria.
B2B buyers should verify that their suppliers comply with these standards to mitigate risks associated with product quality and safety.
What Are the Key Quality Control Checkpoints in Kitchen Scale Manufacturing?
Quality control (QC) is an integral part of the kitchen scale manufacturing process, typically conducted at various checkpoints:
- Incoming Quality Control (IQC): This involves inspecting raw materials upon arrival to ensure they meet specified standards.
- In-Process Quality Control (IPQC): Continuous checks during the manufacturing process to identify defects early.
- Final Quality Control (FQC): A thorough inspection of the finished product before packaging and shipping.
These checkpoints help ensure that any defects are caught and addressed before the product reaches the market.
What Common Testing Methods Are Used to Ensure Kitchen Scale Accuracy and Reliability?
To ensure kitchen scales meet quality standards, manufacturers employ various testing methods, including:
- Load Testing: Verifying the scale’s accuracy under different weight loads.
- Durability Testing: Assessing how well the scale withstands everyday use and environmental conditions.
- Electronic Testing: Ensuring that all electronic components function correctly and meet performance specifications.
Buyers should inquire about the specific testing methods used by potential suppliers to ensure the reliability of their products.
How Can B2B Buyers Verify Supplier Quality Control Processes?
Verifying a supplier’s quality control processes is essential for B2B buyers, especially in international markets. Here are some actionable steps:
- Request Documentation: Ask suppliers for their quality management certifications, testing reports, and process descriptions.
- Conduct Audits: Performing on-site audits can provide insights into the manufacturing and quality assurance processes.
- Utilize Third-Party Inspections: Engaging third-party inspection services can offer an unbiased assessment of the supplier’s quality control measures.
What Are the QC and Certification Nuances for International Buyers?
International buyers, particularly from regions like Africa, South America, the Middle East, and Europe, must be aware of specific nuances in quality control and certification:
- Regional Compliance: Ensure that products meet local regulatory requirements, which may differ from international standards.
- Supply Chain Transparency: Understand the entire supply chain, including sourcing and manufacturing processes, to assess overall quality.
- Cultural Considerations: Be mindful of cultural differences that may affect communication and expectations regarding quality assurance.
By focusing on these aspects, B2B buyers can make informed decisions when selecting kitchen scale manufacturers, ensuring they receive high-quality products that meet their market needs.
Practical Sourcing Guide: A Step-by-Step Checklist for ‘kitchen scale manufacturer’
To assist international B2B buyers in sourcing kitchen scale manufacturers, this guide outlines a comprehensive checklist that emphasizes critical steps in the procurement process. Each step ensures that buyers can make informed decisions, ultimately leading to successful partnerships and high-quality products.
Step 1: Define Your Technical Specifications
Understanding your technical requirements is the foundation of successful sourcing. Clearly define the features you need, such as weight capacity, precision level, and any additional functionalities (e.g., digital displays, tare functions). This clarity will streamline your search and help you communicate effectively with potential suppliers.
- Consider the market needs: Research the specific demands of your target market in regions like Africa, South America, or the Middle East to ensure your specifications align with local preferences.
Step 2: Conduct Market Research
Thorough market research is essential to identify potential manufacturers. Use online directories, trade shows, and industry reports to gather a list of kitchen scale manufacturers. Pay attention to their market reputation and customer reviews.
- Leverage local networks: Engage with local trade associations or chambers of commerce that can provide insights into reputable suppliers within specific regions.
Step 3: Evaluate Potential Suppliers
Before making any commitments, it’s crucial to vet suppliers thoroughly. Request detailed company profiles, product catalogs, and references from buyers in your industry. This step helps assess the supplier’s credibility and production capabilities.
- Assess their experience: Look for manufacturers with a proven track record in producing kitchen scales that meet international quality standards.
Step 4: Verify Supplier Certifications
Ensure that your potential suppliers possess relevant certifications such as ISO, CE, or other industry-specific standards. Certification verification is vital to guarantee that the products meet safety, quality, and regulatory requirements.
- Request documentation: Don’t hesitate to ask suppliers for copies of their certifications, which should be current and verifiable.
Step 5: Request Samples
Before finalizing any agreements, request samples of the kitchen scales to evaluate quality firsthand. This step allows you to test the product’s functionality, durability, and accuracy.
- Conduct thorough testing: Use the samples in real-world scenarios similar to your target market to assess performance and usability.
Step 6: Discuss Pricing and Payment Terms
Engage in transparent discussions regarding pricing structures and payment terms. Understanding the total cost of ownership, including shipping and customs duties, is critical for budget planning.
- Negotiate terms: Don’t shy away from negotiating better terms, especially if you plan to place large orders or establish a long-term partnership.
Step 7: Establish Communication Channels
Finally, ensure that there are clear communication channels between you and the supplier. Open lines of communication are crucial for addressing any concerns during the manufacturing process and after sales.
- Set expectations: Clearly outline how often you expect updates on production status and any other relevant communications to avoid misunderstandings.
By following this step-by-step checklist, B2B buyers can navigate the complexities of sourcing kitchen scale manufacturers effectively, ensuring they partner with reliable suppliers that meet their specific needs.
Comprehensive Cost and Pricing Analysis for kitchen scale manufacturer Sourcing
What Are the Key Cost Components in Kitchen Scale Manufacturing?
Understanding the cost structure of kitchen scale manufacturing is essential for international B2B buyers looking to make informed purchasing decisions. The main cost components typically include:
-
Materials: The choice of materials significantly impacts the overall cost. Common materials used in kitchen scales include plastic, stainless steel, and glass. Each material has its own price range, and opting for higher-quality materials can enhance durability but also increase costs.
-
Labor: Labor costs can vary widely based on geographic location and the complexity of manufacturing processes. Regions with lower labor costs, such as parts of Africa and South America, may offer more competitive pricing, but buyers should also consider the skill level and expertise of the workforce.
-
Manufacturing Overhead: This includes indirect costs such as utilities, rent, and administrative expenses. Overhead can fluctuate based on the manufacturer’s location and operational efficiency.
-
Tooling: Initial tooling costs for molds and production setups can be significant, especially for custom designs. Buyers should inquire about tooling fees when discussing custom kitchen scales.
-
Quality Control (QC): Implementing robust QC measures ensures product reliability and compliance with international standards. However, it adds to the cost. Buyers should look for manufacturers who prioritize quality without excessively inflating prices.
-
Logistics: Shipping and handling costs can vary based on the shipping method and distance. Incoterms can also affect logistics costs, and it’s essential to clarify these terms with suppliers.
-
Margin: Manufacturers typically apply a markup on their costs to achieve profit. Understanding the margin expectations of potential suppliers can help buyers negotiate better pricing.
How Do Price Influencers Impact Kitchen Scale Sourcing?
Several factors influence pricing in the kitchen scale market:
-
Volume/MOQ (Minimum Order Quantity): Larger orders often lead to discounts. Buyers should consider their volume needs and negotiate pricing based on expected order sizes.
-
Specifications and Customization: Custom features or specifications can increase costs. Buyers should weigh the benefits of customization against budget constraints.
-
Materials and Quality Certifications: Scales with specific certifications (e.g., ISO, CE) or premium materials typically command higher prices. Understanding the required certifications for your market can help in making cost-effective decisions.
-
Supplier Factors: The reputation and reliability of suppliers can influence pricing. Established manufacturers may charge more due to their brand value and proven quality.
-
Incoterms: The terms of shipping (e.g., FOB, CIF) can significantly affect the final cost. Buyers should clarify these terms to avoid unexpected expenses.
What Are the Best Practices for Negotiating Prices in Kitchen Scale Sourcing?
For international B2B buyers, particularly those from Africa, South America, the Middle East, and Europe, negotiating effectively can lead to significant savings. Here are some tips:
-
Understand Total Cost of Ownership (TCO): TCO includes purchase price, shipping, duties, and maintenance costs. Evaluating TCO rather than just upfront costs can reveal better long-term value.
-
Research Market Prices: Familiarize yourself with market rates and competitors’ pricing. This knowledge equips you to negotiate more effectively.
-
Leverage Relationships: Building strong relationships with suppliers can lead to better terms and pricing. Consider long-term partnerships rather than one-off transactions.
-
Consider Payment Terms: Flexible payment options can also influence pricing. Proposing favorable terms can lead to discounts.
-
Be Prepared to Walk Away: If negotiations don’t meet your budget requirements, be ready to explore other suppliers. This can often encourage better offers.
Are There Pricing Nuances for International Buyers of Kitchen Scales?
Yes, international buyers must navigate various pricing nuances when sourcing kitchen scales. Currency fluctuations can affect pricing, so locking in rates early can mitigate risks. Additionally, understanding local tariffs and import duties is crucial, as these can significantly impact the final cost. It’s advisable to work with local import/export experts to navigate these complexities effectively.
Disclaimer Regarding Indicative Prices
Prices for kitchen scales can vary widely based on the factors outlined above. Buyers should always seek detailed quotes from multiple suppliers and conduct thorough due diligence to ensure they are making the most cost-effective decisions for their business needs.
Alternatives Analysis: Comparing kitchen scale manufacturer With Other Solutions
When evaluating solutions for weight measurement in commercial kitchens, it’s crucial to consider alternatives to traditional kitchen scale manufacturers. Understanding these alternatives can help B2B buyers make informed decisions that align with their operational needs and budget constraints.
Comparison of Kitchen Scale Manufacturer with Alternative Solutions
Comparison Aspect | Kitchen Scale Manufacturer | Smart Weighing Solutions | Manual Weighing Techniques |
---|---|---|---|
Performance | High accuracy and precision for various weights | Advanced sensors with real-time data | Generally accurate but can vary by user |
Cost | Moderate initial investment with long-term savings | Higher upfront costs but potential for automation savings | Low cost, minimal investment required |
Ease of Implementation | Quick setup with user-friendly interfaces | Requires training for optimal use | Simple to implement but labor-intensive |
Maintenance | Regular calibration needed | Regular software updates and sensor maintenance | Minimal, but scales may need replacement |
Best Use Case | Ideal for high-volume kitchens requiring consistent measurements | Best for businesses looking to integrate technology and data analytics | Suitable for small-scale operations or low-budget scenarios |
What Are Smart Weighing Solutions and Their Benefits?
Smart weighing solutions leverage advanced technology, such as IoT sensors and cloud connectivity, to provide real-time data and analytics. These systems can offer significant advantages in performance and efficiency. However, the initial investment is typically higher than traditional kitchen scales, and staff may require training to fully utilize the technology. Businesses that prioritize data-driven decision-making and integration with inventory management systems will find smart weighing solutions particularly advantageous. Nevertheless, they may not be suitable for all operations, especially those with limited budgets.
How Do Manual Weighing Techniques Compare?
Manual weighing techniques, which often utilize simple balance scales or handheld measuring tools, present a cost-effective alternative. They require minimal investment and are easy to implement in any kitchen setting. However, the accuracy can depend heavily on the operator’s skill, and the process can be time-consuming, especially in high-volume environments. For small-scale operations or startups with budget constraints, manual weighing may be the most practical solution, but it lacks the precision and efficiency of more advanced systems.
Conclusion: How Can B2B Buyers Choose the Right Solution for Their Needs?
Selecting the right weighing solution depends on various factors, including budget, operational scale, and the importance of accuracy in your kitchen operations. For businesses in Africa, South America, the Middle East, and Europe, understanding the trade-offs between kitchen scale manufacturers, smart weighing solutions, and manual techniques is vital. Buyers should assess their specific needs—such as the volume of goods processed, the level of technological integration desired, and the skill level of their staff—to determine which solution aligns best with their operational goals. By carefully evaluating these alternatives, B2B buyers can enhance efficiency, maintain product quality, and ultimately drive profitability in their culinary endeavors.
Essential Technical Properties and Trade Terminology for kitchen scale manufacturer
What Are the Key Technical Properties of Kitchen Scales?
When selecting kitchen scales for commercial use, understanding the technical specifications is crucial for ensuring product quality and reliability. Here are several essential properties that B2B buyers should consider:
1. Material Grade: What Materials Are Used in Kitchen Scales?
The material grade of kitchen scales impacts durability, accuracy, and weight capacity. Common materials include stainless steel, plastic, and glass. Stainless steel is preferred for its strength, resistance to corrosion, and ease of cleaning, making it ideal for food-related applications. Buyers should verify material specifications to ensure compliance with food safety standards.
2. Maximum Capacity: How Much Weight Can the Scale Handle?
Maximum capacity refers to the upper limit of weight that a kitchen scale can measure accurately. This specification is vital for businesses that require precise measurements for bulk ingredients. Scales typically range from 1 kg to over 10 kg in capacity. Understanding your operational needs will help in selecting a scale that meets your requirements without sacrificing accuracy.
3. Tolerance: What Is the Margin of Error?
Tolerance indicates the scale’s precision and refers to the allowable deviation from the true weight. A lower tolerance means higher accuracy, which is essential in culinary environments where precision is paramount. Common tolerances range from ±0.1 g to ±1 g. B2B buyers should ensure that the scales they procure have tolerances suitable for their specific applications.
4. Calibration: How Important Is Scale Calibration?
Calibration is the process of adjusting the scale to ensure accurate readings. Kitchen scales should be easily calibratable to maintain their precision over time. Regular calibration is vital for businesses that rely on consistent measurements, such as restaurants and food manufacturers. Buyers should inquire about the calibration process and whether the manufacturer provides support or guidelines.
5. Power Source: What Are the Options for Kitchen Scales?
Kitchen scales may operate on batteries, rechargeable batteries, or direct AC power. The choice of power source can influence portability and convenience. Battery-operated scales are typically more portable, while AC-powered scales may offer more consistent performance in stationary setups. Buyers should consider their operational environment when selecting the appropriate power source.
What Are Common Trade Terms Used in the Kitchen Scale Industry?
Familiarity with industry jargon can enhance communication and negotiations between buyers and manufacturers. Here are some essential trade terms:
1. OEM (Original Equipment Manufacturer): What Does OEM Mean in Kitchen Scales?
OEM refers to companies that manufacture products based on specifications provided by another company. In the kitchen scale industry, buyers often work with OEMs to create branded scales. Understanding OEM relationships can help buyers navigate customization options and quality assurance processes.
2. MOQ (Minimum Order Quantity): Why Is MOQ Important?
MOQ represents the minimum number of units a manufacturer is willing to produce. This term is crucial for B2B buyers as it impacts pricing and inventory management. Manufacturers may set MOQs to ensure production efficiency, so understanding these requirements can help in planning purchases and managing budgets effectively.
3. RFQ (Request for Quotation): How to Use RFQ Effectively?
An RFQ is a document sent to suppliers requesting pricing and terms for specific products. For kitchen scale buyers, issuing an RFQ can facilitate competitive bidding and ensure that all potential suppliers are evaluated based on price, quality, and delivery terms. It’s a strategic tool for making informed procurement decisions.
4. Incoterms: What Are Incoterms and How Do They Affect Shipping?
Incoterms are standardized trade terms that define the responsibilities of buyers and sellers regarding shipping, insurance, and tariffs. Understanding Incoterms is essential for international transactions, as they clarify who bears the risk and cost at various stages of transport. Familiarity with these terms can help B2B buyers negotiate better shipping arrangements and avoid unexpected costs.
5. Lead Time: What Is Lead Time and Why Is It Critical?
Lead time refers to the period from placing an order to receiving the goods. It is a crucial factor for planning inventory and production schedules. Buyers should inquire about lead times when negotiating contracts to ensure timely delivery and maintain efficient operations.
By understanding these technical properties and trade terms, B2B buyers can make informed decisions when sourcing kitchen scales, ensuring they meet their operational needs while optimizing costs and quality.
Navigating Market Dynamics and Sourcing Trends in the kitchen scale manufacturer Sector
What Are the Current Market Dynamics and Key Trends in the Kitchen Scale Manufacturer Sector?
The kitchen scale manufacturer sector is experiencing significant growth, driven by increasing consumer awareness regarding health and nutrition. Global health trends have prompted both consumers and businesses to prioritize precise food measurements, enhancing the demand for high-quality kitchen scales. For international B2B buyers, especially from Africa, South America, the Middle East, and Europe, understanding these dynamics is crucial for strategic sourcing.
Emerging technologies such as smart kitchen scales, which connect to mobile applications, are revolutionizing the market. These scales offer features like nutritional tracking and recipe integration, appealing to tech-savvy consumers and businesses. B2B buyers should consider suppliers that incorporate innovative technology to stay ahead of the competition. Additionally, the rise of e-commerce platforms has made it easier for manufacturers to reach global markets, allowing buyers to explore a wider range of products and suppliers.
Another significant trend is the shift towards personalized and customizable kitchen scales. As consumers seek products that fit their unique lifestyles, manufacturers are adapting their offerings. International buyers can leverage this trend by sourcing from suppliers that provide customization options, catering to specific market needs.
How Is Sustainability and Ethical Sourcing Affecting the Kitchen Scale Manufacturing Sector?
Sustainability has become a cornerstone of the kitchen scale manufacturer sector, with increasing pressure on businesses to adopt environmentally friendly practices. The environmental impact of production processes, including waste generation and resource consumption, is under scrutiny. International B2B buyers must prioritize suppliers committed to sustainable manufacturing practices, as this not only aligns with global trends but also enhances brand reputation.
Ethical sourcing is equally important, as buyers increasingly demand transparency in supply chains. Manufacturers that prioritize fair labor practices and ethical sourcing of materials are more likely to attract conscious consumers. Certifications such as ISO 14001 for environmental management and Fair Trade certification can serve as indicators of a supplier’s commitment to sustainability and ethical practices.
Using eco-friendly materials in the production of kitchen scales, such as recycled plastics or sustainably sourced metals, can also appeal to environmentally conscious buyers. By choosing suppliers that align with these values, B2B buyers can foster long-term partnerships that contribute positively to their corporate social responsibility goals.
What Is the Brief Evolution of the Kitchen Scale Manufacturer Sector?
The kitchen scale manufacturer sector has evolved significantly over the past few decades, transitioning from mechanical scales to advanced digital models. Initially, kitchen scales were simple mechanical devices that required manual calibration. The introduction of digital scales in the late 20th century revolutionized the market, providing greater accuracy and ease of use.
In recent years, the integration of technology has further transformed the sector. Smart kitchen scales now feature connectivity options, allowing users to track nutritional data and manage cooking processes via mobile applications. This evolution reflects broader trends in consumer behavior, where convenience and technology play crucial roles in purchasing decisions. For international B2B buyers, recognizing this evolution is essential in identifying suppliers that are not only keeping pace with technological advancements but also innovating to meet future demands.
Frequently Asked Questions (FAQs) for B2B Buyers of kitchen scale manufacturer
-
How do I evaluate the quality of kitchen scales from manufacturers?
To assess the quality of kitchen scales, request samples before placing bulk orders. Look for certifications such as ISO or CE, which indicate adherence to international quality standards. Additionally, review product specifications, including weight capacity, accuracy, and material durability. Customer reviews and case studies can also provide insights into the manufacturer’s reliability and product performance. Establishing direct communication with the supplier can clarify any doubts regarding quality assurance processes. -
What is the best kitchen scale for small businesses in Africa?
For small businesses in Africa, digital kitchen scales with a capacity of 5-10 kg and accuracy to the gram are ideal. Look for models with tare functions for precise measurements, as well as user-friendly interfaces. Additionally, consider scales with rechargeable batteries or solar power options to accommodate areas with limited electricity. Choosing a manufacturer that offers customization options can also ensure the scale meets specific local needs. -
What customization options should I consider when sourcing kitchen scales?
Customization options can include branding, color, size, and specific features such as waterproofing or Bluetooth connectivity. Discuss your requirements with manufacturers to understand their capabilities. Some manufacturers may offer the ability to design unique packaging or integrate specific technologies that cater to your target market. This differentiation can enhance brand visibility and customer satisfaction. -
What are the minimum order quantities (MOQs) for kitchen scales?
MOQs can vary significantly between manufacturers. Typically, they range from 100 to 1,000 units, depending on the scale type and customization requested. It is essential to negotiate MOQs, especially for new partnerships, as some manufacturers may be flexible to accommodate first-time buyers. Always clarify any implications on pricing and lead times associated with lower MOQs. -
What payment terms should I expect when sourcing kitchen scales internationally?
Payment terms can differ based on the manufacturer and your negotiation power. Common terms include a 30% deposit upfront, with the balance payable upon shipment or delivery. Some manufacturers may offer credit terms for established clients, while others may require full payment before production begins. Always ensure that the terms are clearly documented in the purchase agreement to avoid misunderstandings. -
How can I ensure reliable logistics for kitchen scale shipments?
To ensure reliable logistics, partner with reputable freight forwarders experienced in international shipping. Discuss shipping options, including air freight for faster delivery or sea freight for cost-effectiveness. Verify the manufacturer’s ability to handle customs documentation and compliance for your region. Additionally, consider insurance for your shipment to mitigate risks associated with loss or damage during transit. -
What quality assurance processes should manufacturers have in place for kitchen scales?
Manufacturers should implement rigorous quality assurance (QA) processes, including regular inspections during production and final testing of each unit. Look for suppliers that utilize third-party QA services to validate their claims. Request documentation of their QA protocols and any relevant certifications, ensuring they comply with international standards. This will help guarantee the reliability and accuracy of the kitchen scales you source. -
How do I vet potential kitchen scale suppliers?
Begin by researching potential suppliers through online directories and trade shows. Evaluate their reputation by checking customer reviews and requesting references. Conduct a factory visit, if possible, to inspect production capabilities and working conditions. Additionally, assess their communication responsiveness and willingness to accommodate your needs. Utilizing platforms that offer supplier verification can also provide an added layer of security in your decision-making process.
Important Disclaimer & Terms of Use
⚠️ Important Disclaimer
The information provided in this guide, including content regarding manufacturers, technical specifications, and market analysis, is for informational and educational purposes only. It does not constitute professional procurement advice, financial advice, or legal advice.
While we have made every effort to ensure the accuracy and timeliness of the information, we are not responsible for any errors, omissions, or outdated information. Market conditions, company details, and technical standards are subject to change.
B2B buyers must conduct their own independent and thorough due diligence before making any purchasing decisions. This includes contacting suppliers directly, verifying certifications, requesting samples, and seeking professional consultation. The risk of relying on any information in this guide is borne solely by the reader.
Strategic Sourcing Conclusion and Outlook for kitchen scale manufacturer
As the global market for kitchen scales continues to evolve, international B2B buyers must prioritize strategic sourcing to enhance their competitive edge. By leveraging data-driven insights, understanding market trends, and establishing robust supplier relationships, companies can optimize their procurement processes. Key takeaways include the importance of evaluating suppliers based on quality, reliability, and compliance with local regulations—particularly in diverse regions like Africa, South America, the Middle East, and Europe.
How can buyers ensure long-term success in sourcing kitchen scales? Embracing technology and innovative supply chain solutions will be crucial. This not only facilitates better tracking and management of inventory but also enhances communication with suppliers, ensuring timely delivery and reduced costs.
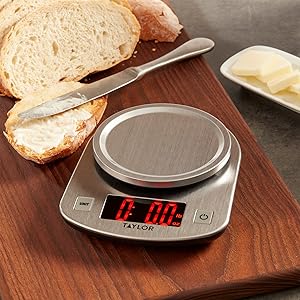
A stock image related to kitchen scale manufacturer.
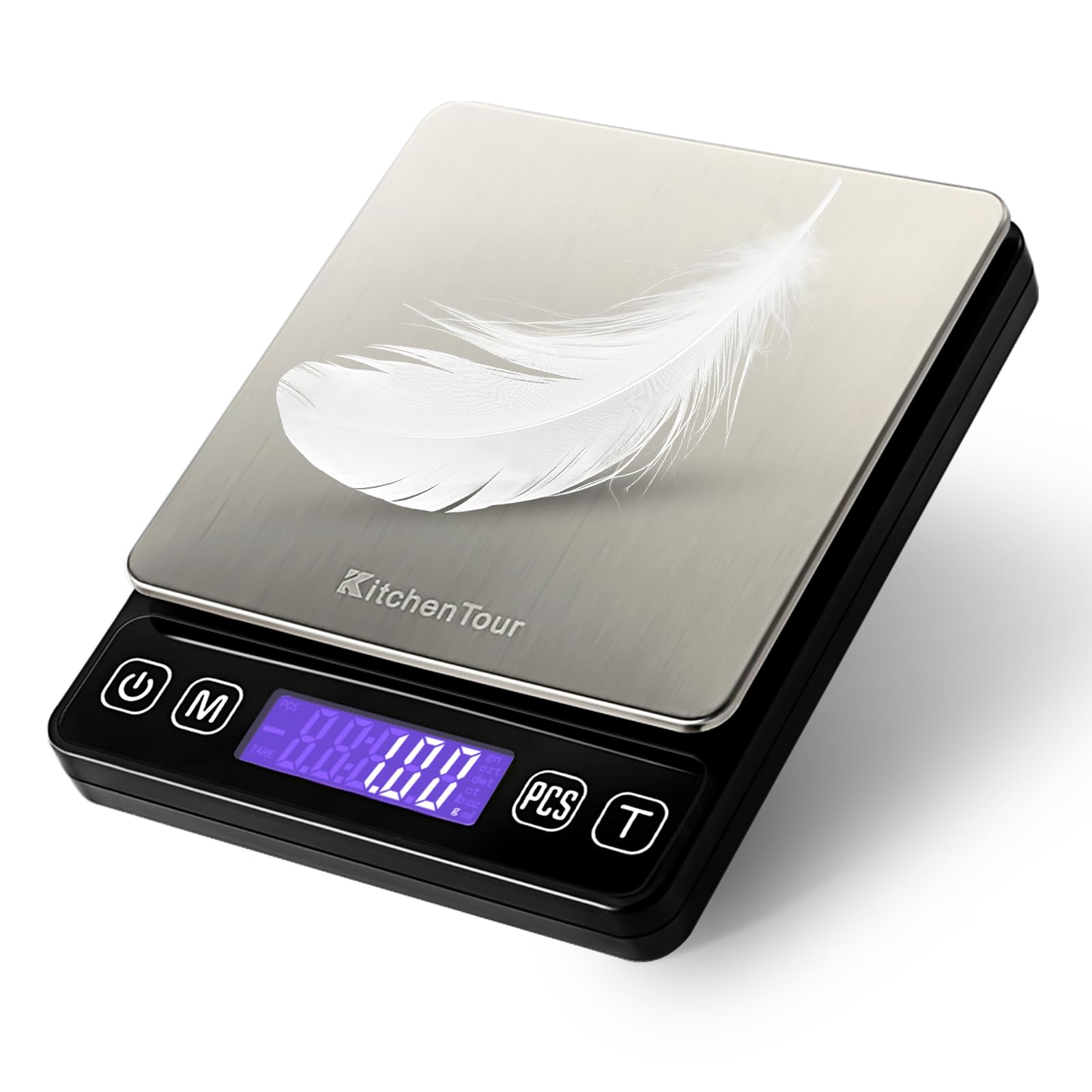
A stock image related to kitchen scale manufacturer.
Looking ahead, the kitchen scale manufacturing sector will increasingly align with sustainability goals and consumer preferences for smart technology. International B2B buyers are encouraged to stay informed about emerging trends and actively engage with manufacturers who share their commitment to quality and innovation. By doing so, they can secure a strategic advantage in a rapidly changing marketplace.