Find Cost-Effective Copper Foil Suppliers: The Ultimate Guide (2025)
Introduction: Navigating the Global Market for copper foil supplier
In the fast-evolving landscape of electronics and renewable energy, sourcing the right copper foil supplier can pose significant challenges for international B2B buyers. Whether you are in Africa, South America, the Middle East, or Europe, understanding the nuances of copper foil procurement is essential to ensure quality and cost-effectiveness. This comprehensive guide aims to demystify the global market for copper foil suppliers, offering insights into various types of copper foils, their applications across industries, and best practices for supplier vetting.
Throughout this guide, we will explore critical considerations such as the different grades of copper foil available, the specific needs of your application—be it for printed circuit boards (PCBs), batteries, or other electrical components—and the factors influencing pricing and availability. Additionally, we will provide actionable tips on evaluating suppliers, from assessing their production capabilities and certifications to understanding their supply chain reliability.
By leveraging this guide, B2B buyers can make informed purchasing decisions that not only meet their technical requirements but also align with their budgetary constraints. This resource empowers you to navigate the complexities of international sourcing, ensuring that you partner with suppliers who can support your business goals and deliver quality products consistently.
Understanding copper foil supplier Types and Variations
Type Name | Key Distinguishing Features | Primary B2B Applications | Brief Pros & Cons for Buyers |
---|---|---|---|
Electrolytic Copper Foil | Produced through an electrochemical process; high purity and uniform thickness | Electronics, circuit boards, flexible circuits | Pros: High conductivity, excellent surface finish; Cons: Higher cost compared to other types. |
Rolled Copper Foil | Manufactured by rolling copper sheets into foil; thicker than electrolytic foil | Automotive, battery production, and heat sinks | Pros: Cost-effective for bulk applications; Cons: Lower conductivity and flexibility than electrolytic. |
Copper Clad Laminate | Composite material with a layer of copper foil bonded to an insulating substrate | PCB manufacturing, telecommunications | Pros: Versatile and customizable; Cons: Limited thermal conductivity compared to pure copper foil. |
High-Temperature Copper Foil | Designed to withstand extreme temperatures; often coated or treated | Aerospace, high-performance electronics | Pros: Excellent thermal and chemical resistance; Cons: Typically more expensive due to specialized production. |
Thin Copper Foil | Very thin sheets (often < 0.1 mm); lightweight and flexible | RF applications, medical devices, and sensors | Pros: Ideal for compact designs; Cons: Can be more fragile and less durable in harsh environments. |
What are the Characteristics of Electrolytic Copper Foil and Its Suitability for B2B Buyers?
Electrolytic copper foil is produced through an electrochemical process that yields high purity and uniform thickness, making it ideal for applications requiring excellent conductivity and surface finish. This type is particularly suited for electronics, including circuit boards and flexible circuits, where precision is essential. B2B buyers should consider the higher cost associated with electrolytic copper foil but can justify the investment through its superior performance in critical applications.
How Does Rolled Copper Foil Differ from Other Types and What Are Its Key Considerations?
Rolled copper foil is created by mechanically rolling copper sheets into thinner forms. It is generally thicker than electrolytic foil, making it suitable for applications in automotive manufacturing, battery production, and heat sinks. Buyers may find rolled copper foil to be more cost-effective for bulk applications, but they should be aware of its lower conductivity and flexibility compared to electrolytic options, which could impact performance in sensitive electronic applications.
What Is Copper Clad Laminate and How Can It Be Used in B2B Applications?
Copper clad laminate (CCL) is a composite material that consists of a layer of copper foil bonded to an insulating substrate. This type is commonly used in PCB manufacturing and telecommunications due to its versatility and customization options. When considering CCL, B2B buyers should evaluate its trade-offs, such as limited thermal conductivity compared to pure copper foil, which may affect performance in high-frequency applications.
Why Should B2B Buyers Consider High-Temperature Copper Foil for Specialized Applications?
High-temperature copper foil is engineered to withstand extreme heat and is often treated or coated for enhanced performance. It finds applications in aerospace and high-performance electronics, where durability under harsh conditions is critical. While this type offers excellent thermal and chemical resistance, B2B buyers must consider the higher costs associated with specialized production, ensuring that the investment aligns with their operational needs.
What Are the Advantages and Disadvantages of Thin Copper Foil for B2B Buyers?
Thin copper foil, typically less than 0.1 mm in thickness, is lightweight and flexible, making it suitable for applications in RF devices, medical technology, and sensors. Its compact design allows for innovative product development, but buyers should be cautious of its fragility and potential durability issues in demanding environments. Assessing the specific requirements of the application will help buyers determine if thin copper foil is the right choice for their projects.
Related Video: ProPress 450 Pneumatic Hot Foil Stamping Press
Key Industrial Applications of copper foil supplier
Industry/Sector | Specific Application of copper foil supplier | Value/Benefit for the Business | Key Sourcing Considerations for this Application |
---|---|---|---|
Electronics | Printed Circuit Boards (PCBs) | Enhanced conductivity and reliability in devices | Quality certifications, thickness, and purity levels |
Automotive | Battery and Charging Systems | Increased efficiency and safety in electric vehicles | Compliance with automotive standards and testing |
Renewable Energy | Solar Panel Manufacturing | Improved energy conversion and durability | Sourcing from certified suppliers and material traceability |
Telecommunications | Antenna and Signal Transmission | Higher signal strength and reduced interference | Custom sizes and specifications, delivery timelines |
Medical Devices | Diagnostic Equipment and Imaging Systems | Precision and reliability in critical applications | Regulatory compliance and biocompatibility standards |
How is Copper Foil Used in Electronics for PCBs?
In the electronics industry, copper foil is essential for the manufacturing of printed circuit boards (PCBs). It provides a conductive pathway for electrical signals, ensuring efficient operation of devices such as smartphones, computers, and other electronic gadgets. For international B2B buyers, particularly from regions like Africa and Europe, sourcing high-quality copper foil with precise thickness and purity is crucial. This ensures optimal performance and reliability in their products, addressing issues like signal loss and component failure.
What Role Does Copper Foil Play in Automotive Applications?
Copper foil is increasingly utilized in battery and charging systems for electric vehicles. Its excellent conductivity helps improve energy transfer efficiency, which is vital for the performance and safety of these systems. B2B buyers in the automotive sector, especially in South America and the Middle East, should consider suppliers who meet stringent automotive standards and can provide detailed testing results. This ensures that the copper foil will withstand the demanding conditions of automotive applications.
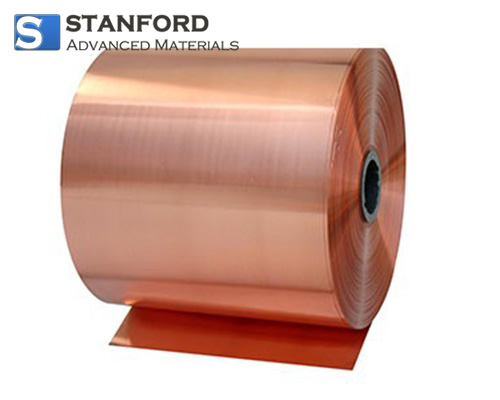
A stock image related to copper foil supplier.
How is Copper Foil Beneficial in Renewable Energy?
In renewable energy, particularly in solar panel manufacturing, copper foil is used to create efficient conductive layers that enhance energy conversion rates. This application is critical for businesses aiming to produce high-performance solar panels. Buyers from Europe and Africa must prioritize sourcing from suppliers that offer traceable and certified materials, as these factors significantly impact the longevity and effectiveness of solar products.
Why is Copper Foil Important in Telecommunications?
Copper foil is a key component in the production of antennas and signal transmission equipment in the telecommunications sector. It provides higher signal strength and reduces interference, which are essential for maintaining communication quality. B2B buyers in this field should focus on sourcing custom-sized copper foils that meet specific design requirements, along with reliable delivery timelines to ensure timely production and deployment.
What are the Applications of Copper Foil in Medical Devices?
In the medical sector, copper foil is used in diagnostic equipment and imaging systems, where precision and reliability are paramount. It enables accurate signal transmission and is crucial for the functionality of devices like MRI machines and ultrasound equipment. Buyers in this industry, particularly in Europe and the Middle East, must ensure that their suppliers adhere to strict regulatory compliance and biocompatibility standards, which are vital for patient safety and device efficacy.
Related Video: Uses Of Metals – Gold, Copper, Aluminium, Steel | Properties of Matter | Chemistry | FuseSchool
3 Common User Pain Points for ‘copper foil supplier’ & Their Solutions
Scenario 1: Delays in Delivery Times Affecting Production Schedules
The Problem:
Many B2B buyers, especially in industries like electronics or automotive manufacturing, face significant challenges when their copper foil supplier experiences delays in delivery. These delays can disrupt production schedules, leading to missed deadlines and potentially damaging client relationships. Buyers often find themselves in a position where they have to scramble for alternative sources at the last minute, which can incur additional costs and further delays.
The Solution:
To mitigate this issue, it’s crucial for buyers to establish clear communication channels with their copper foil suppliers. Before finalizing contracts, inquire about the supplier’s logistics capabilities and delivery timelines. Implementing regular check-ins throughout the order process can also help identify any potential delays early on. Additionally, consider diversifying your supplier base to include multiple sources of copper foil. This not only helps in maintaining a steady supply chain but also provides leverage in negotiations, ensuring that you are not solely dependent on one supplier. Lastly, utilizing just-in-time inventory management techniques can help reduce the impact of delivery delays by aligning inventory levels with production schedules.
Scenario 2: Inconsistent Quality Standards Leading to Product Failures
The Problem:
Inconsistent quality of copper foil can lead to product failures, particularly in applications where precision is critical, such as in circuit boards or battery manufacturing. Buyers often encounter variations in thickness, conductivity, and surface finish, which can result in defective products and increased waste. This not only affects production efficiency but also raises costs and damages reputations in the market.
The Solution:
To ensure consistent quality, buyers should conduct thorough due diligence before selecting a copper foil supplier. This includes reviewing the supplier’s quality control processes, certifications, and any third-party testing they may employ. Establishing a clear set of specifications for the copper foil required, along with performance metrics, can help align expectations. Implementing a robust incoming inspection process can further catch any quality discrepancies before the materials are used in production. Additionally, consider establishing long-term partnerships with suppliers who demonstrate a commitment to continuous improvement and quality assurance, as this can lead to more reliable product consistency over time.
Scenario 3: Lack of Technical Support and Expertise
The Problem:
Many international B2B buyers encounter difficulties when their copper foil supplier lacks the necessary technical support and expertise to address specific application needs. This can be particularly frustrating for companies in emerging markets, where access to technical resources may be limited. Buyers may find themselves struggling to optimize the use of copper foil in their products, leading to suboptimal performance and increased costs.
The Solution:
To overcome this challenge, buyers should prioritize selecting suppliers who offer comprehensive technical support as part of their service package. During the supplier evaluation phase, inquire about the availability of technical experts and the types of support services they provide, such as application engineering or troubleshooting assistance. Additionally, fostering open lines of communication with the supplier’s technical team can facilitate a collaborative approach to solving challenges. If a supplier lacks this capability, consider working with external consultants or industry experts who can provide additional insights and support tailored to your specific needs. Regular training sessions and workshops can also be beneficial in keeping your team informed about best practices in using copper foil, which can ultimately enhance product quality and performance.
Strategic Material Selection Guide for copper foil supplier
When selecting materials for copper foil applications, international B2B buyers must consider various factors that influence product performance, cost, and compliance with regional standards. Below is an analysis of four common materials used in copper foil manufacturing, focusing on their properties, advantages, disadvantages, and specific considerations for buyers from Africa, South America, the Middle East, and Europe.
What Are the Key Properties of Electrolytic Copper Foil?
Electrolytic copper foil is widely used in electronics due to its excellent conductivity and uniform thickness. This material is produced through an electrochemical process, resulting in a foil that can handle high temperatures and pressures. Its corrosion resistance is moderate, making it suitable for applications involving exposure to moisture or chemicals.
Pros & Cons: The primary advantage of electrolytic copper foil is its high electrical conductivity, which is crucial for applications like printed circuit boards (PCBs). However, the manufacturing process can be complex and costly, leading to a higher price point compared to other materials. Additionally, while it is durable, it may not perform well in highly corrosive environments.
Impact on Application: Electrolytic copper foil is particularly compatible with electronic media, making it ideal for the telecommunications and consumer electronics sectors.
Considerations for International Buyers: Buyers should ensure compliance with international standards such as ASTM B370 and JIS H 3100, particularly in regions like Europe and the Middle East, where strict regulations govern electronic components.
How Does Polyimide Copper Foil Compare?
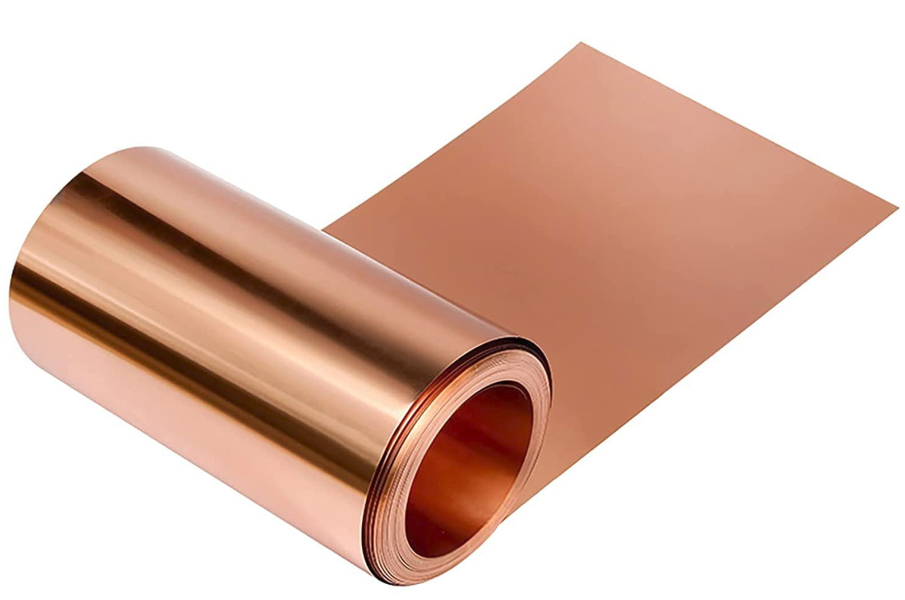
A stock image related to copper foil supplier.
Polyimide copper foil combines copper with a polyimide film, offering enhanced thermal stability and flexibility. This material can withstand extreme temperatures, making it ideal for applications in aerospace and automotive industries.
Pros & Cons: The key advantage of polyimide copper foil is its excellent thermal and chemical resistance, which extends its lifespan in harsh environments. However, the cost is significantly higher due to the complex manufacturing process, making it less accessible for budget-sensitive projects.
Impact on Application: This material is particularly suitable for flexible printed circuits (FPCs) and high-frequency applications, where performance under heat and stress is critical.
Considerations for International Buyers: Buyers from regions like Africa and South America should be aware of the limited availability of polyimide copper foil and the need for specialized suppliers who comply with ASTM and DIN standards.
What Are the Benefits of Copper Clad Laminate (CCL)?
Copper clad laminate (CCL) consists of a layer of copper foil bonded to a substrate material, typically resin. This composite material is commonly used in PCB manufacturing due to its balance of electrical performance and mechanical strength.
Pros & Cons: The main advantage of CCL is its versatility, allowing for various applications from consumer electronics to industrial machinery. However, the bonding process can introduce weaknesses in the laminate, making it less durable under mechanical stress.
Impact on Application: CCL is compatible with a wide range of media, including moisture and chemicals, making it suitable for diverse applications.
Considerations for International Buyers: Buyers must ensure that their CCL suppliers meet relevant standards, such as IPC-4101, particularly in markets like Europe, where compliance is crucial for product certification.
Why Choose High-Purity Copper Foil?
High-purity copper foil is characterized by its low impurity content, enhancing conductivity and overall performance. This material is essential for high-end applications, including aerospace, military, and medical devices.
Pros & Cons: The key advantage of high-purity copper foil is its superior electrical performance, which is critical for advanced technology applications. However, the production process is more expensive and time-consuming, leading to higher costs.
Impact on Application: High-purity copper foil is particularly effective in applications requiring high reliability and performance, such as RF and microwave devices.
Considerations for International Buyers: Buyers should be aware of the stringent quality control measures in place for high-purity copper foil and ensure suppliers adhere to ISO 9001 standards, especially in regions like Europe and the Middle East.
Summary Table of Material Selection for Copper Foil Suppliers
Material | Typical Use Case for copper foil supplier | Key Advantage | Key Disadvantage/Limitation | Relative Cost (Low/Med/High) |
---|---|---|---|---|
Electrolytic Copper Foil | Printed circuit boards (PCBs) | High electrical conductivity | Complex manufacturing process | High |
Polyimide Copper Foil | Flexible printed circuits (FPCs) | Excellent thermal and chemical resistance | High cost due to manufacturing complexity | High |
Copper Clad Laminate (CCL) | General PCB manufacturing | Versatile for various applications | Potential bonding weaknesses | Medium |
High-Purity Copper Foil | Aerospace and medical devices | Superior electrical performance | Higher production costs | High |
This guide provides a comprehensive overview of the materials available for copper foil applications, enabling international B2B buyers to make informed decisions based on their specific needs and regional compliance requirements.
In-depth Look: Manufacturing Processes and Quality Assurance for copper foil supplier
What Are the Main Stages in the Manufacturing Process of Copper Foil?
The manufacturing of copper foil is a multi-stage process that requires precision and attention to detail. The primary stages include material preparation, forming, assembly, and finishing.
-
Material Preparation: This initial stage involves sourcing high-purity copper cathodes, which are essential for producing quality foil. The copper is subjected to processes like annealing and cleaning to remove impurities. Buyers should ensure that suppliers use only high-grade materials, as this directly affects the conductivity and mechanical properties of the final product.
-
Forming: During this stage, the prepared copper is rolled into thin sheets. This is typically done using a combination of cold rolling and hot rolling techniques. Cold rolling is critical for achieving the desired thickness and surface finish. Buyers should inquire about the rolling techniques employed by suppliers, as they can influence the foil’s performance in specific applications.
-
Assembly: In some cases, copper foil is laminated with other materials to enhance its properties, such as insulation or adhesion. This step may involve adhesive application and pressing techniques. Understanding the assembly processes can help buyers determine if the foil will meet their specific application requirements.
-
Finishing: The final stage includes surface treatments such as coating or etching to improve the foil’s functionality. This may involve applying a protective layer or modifying the surface for better adhesion in electronic applications. Buyers should seek detailed information about the finishing processes to ensure compatibility with their intended use.
How Do Quality Control Practices Impact Copper Foil Production?
Quality control (QC) is crucial in the copper foil manufacturing process to ensure consistency and reliability. Various international standards and industry-specific certifications guide these practices.
-
International Standards: Suppliers should adhere to ISO 9001 standards, which focus on quality management systems. This certification demonstrates that the supplier has established a framework for continuous improvement and customer satisfaction. Buyers from Africa, South America, the Middle East, and Europe should prioritize suppliers with this certification.
-
Industry-Specific Certifications: Depending on the application, additional certifications like CE (for European markets) or API (for oil and gas industries) may be relevant. Buyers should confirm that suppliers have the necessary certifications applicable to their sector.
-
QC Checkpoints: Quality checks are typically performed at three critical checkpoints:
– Incoming Quality Control (IQC): This involves inspecting raw materials upon receipt to ensure they meet specified standards.
– In-Process Quality Control (IPQC): Continuous monitoring during the manufacturing process helps catch defects early.
– Final Quality Control (FQC): This final inspection ensures that the finished product meets all quality standards before shipment.
What Testing Methods Are Commonly Used in Copper Foil Quality Control?
Various testing methods are employed to assess the quality of copper foil. These methods help verify attributes such as thickness, tensile strength, and electrical conductivity.
-
Thickness Measurement: Precision instruments like micrometers or laser measurement systems are used to ensure the foil’s thickness meets specifications. For international buyers, especially from regions with strict regulations, it is vital to ensure these measurements adhere to local standards.
-
Tensile Strength Testing: This test evaluates the foil’s ability to withstand forces without breaking. Using standardized methods such as ASTM E8 can provide insights into the mechanical properties of the foil.
-
Electrical Conductivity Tests: Ensuring that the copper foil maintains high conductivity is essential for electronic applications. Techniques such as eddy current testing can be employed to verify this attribute.
How Can B2B Buyers Verify Supplier Quality Control Practices?
Verifying a supplier’s quality control practices is essential for B2B buyers to ensure they receive products that meet their specifications. Here are some actionable steps:
-
Supplier Audits: Conducting audits of potential suppliers can provide insight into their QC processes and adherence to international standards. Buyers should establish a checklist based on ISO 9001 and relevant industry standards.
-
Reviewing Quality Reports: Suppliers should provide detailed quality reports that outline their testing methods and results. Buyers should request samples of these reports to evaluate the supplier’s commitment to quality.
-
Third-Party Inspections: Engaging third-party inspection services can add an extra layer of assurance. These independent entities can assess the supplier’s processes and products, providing unbiased evaluations.
What Nuances in Quality Control Should International B2B Buyers Consider?
When sourcing copper foil internationally, buyers must be aware of specific nuances in quality control:
-
Cultural Differences: Different regions may have varying approaches to quality management. For example, European suppliers might emphasize stringent documentation, while suppliers in other regions might focus more on production speed.
-
Regulatory Compliance: Buyers from Africa, South America, and the Middle East should be aware of local regulations that may affect product specifications. It’s essential to confirm that the supplier understands and complies with these requirements.
-
Communication Barriers: Language and time zone differences can complicate the verification of quality control practices. Establishing clear communication channels and regular updates can help mitigate these issues.
By understanding the manufacturing processes and quality assurance practices of copper foil suppliers, international B2B buyers can make informed decisions that align with their needs and standards. This proactive approach not only enhances product quality but also fosters long-term supplier relationships.
Practical Sourcing Guide: A Step-by-Step Checklist for ‘copper foil supplier’
In the competitive landscape of B2B procurement, sourcing copper foil requires a strategic approach to ensure quality, reliability, and cost-effectiveness. This guide provides a practical checklist for international buyers, particularly those in Africa, South America, the Middle East, and Europe, looking to identify and engage with the right copper foil suppliers.
Step 1: Define Your Technical Specifications
Before initiating contact with suppliers, it’s essential to clarify your requirements. Determine the thickness, purity, and dimensions of the copper foil you need, as well as any specific industry standards you must meet. This clarity will help you communicate effectively with potential suppliers and ensure they can meet your expectations.
Step 2: Conduct Market Research
Understanding the market landscape is vital. Research various suppliers operating in your target regions and their offerings. Look for industry reports, customer reviews, and competitive pricing structures. This knowledge will empower you to make informed decisions and negotiate better terms.
Step 3: Evaluate Potential Suppliers
Before committing, it’s crucial to vet suppliers thoroughly. Request company profiles, case studies, and references from buyers in similar industries or regions. Assess their production capabilities, lead times, and logistical arrangements to ensure they align with your operational needs.
- Supplier Certifications: Confirm that the suppliers hold relevant certifications such as ISO or RoHS compliance, which guarantee quality and environmental standards.
Step 4: Request Samples
Never underestimate the importance of product samples. Request samples of the copper foil to evaluate the quality firsthand. Check for consistency in thickness, surface finish, and any other specific characteristics that are critical for your application. This step can significantly reduce the risk of quality issues later on.
Step 5: Negotiate Terms and Pricing
Once you identify a shortlist of potential suppliers, engage in negotiations. Discuss pricing, payment terms, and delivery schedules openly. Consider the total cost of ownership, including shipping and customs duties, as these can impact your overall budget significantly.
- Long-Term Partnerships: Explore options for long-term contracts or bulk purchasing agreements, which can lead to better pricing and supply stability.
Step 6: Verify Logistics and Delivery Capabilities
Assess the supplier’s logistics capabilities to ensure timely delivery. Investigate their shipping methods, timelines, and how they handle customs clearance, especially if sourcing from international suppliers. Efficient logistics are essential to maintaining your production schedules.
Step 7: Establish Quality Control Processes
Once you finalize a supplier, implement a robust quality control process. Define inspection criteria and how you will monitor the quality of the copper foil upon delivery. Regular audits and feedback loops can help maintain the standards you expect and foster a strong supplier relationship.
By following this checklist, B2B buyers can navigate the complexities of sourcing copper foil with confidence, ensuring they make informed choices that align with their business objectives.
Comprehensive Cost and Pricing Analysis for copper foil supplier Sourcing
Understanding the cost structure and pricing dynamics of copper foil suppliers is essential for international B2B buyers looking to make informed procurement decisions. This analysis delves into the various cost components, price influencers, and strategic buyer tips tailored for markets in Africa, South America, the Middle East, and Europe, including countries like France and Colombia.
What Are the Key Cost Components in Copper Foil Production?
The cost structure of copper foil production consists of several critical components:
-
Materials: The primary raw material is copper, which is subject to price fluctuations based on global demand and mining conditions. Buyers should monitor copper prices on commodities exchanges to anticipate changes in costs.
-
Labor: Labor costs vary significantly by region. Suppliers in countries with higher wage standards may charge more, impacting the overall price. Understanding the local labor market can provide insights into potential cost variations.
-
Manufacturing Overhead: This includes utilities, rent, and equipment depreciation. Efficient production processes can reduce overhead costs, which may be passed on to buyers.
-
Tooling: The costs associated with molds and machinery setup for producing specific foil specifications can be significant. Custom tooling for specialized products increases upfront costs but may lead to long-term savings through efficiency.
-
Quality Control (QC): Rigorous QC processes ensure product reliability and compliance with industry standards. While this adds to production costs, it is crucial for maintaining quality, especially for sectors like electronics where performance is critical.
-
Logistics: Shipping costs can vary based on distance, mode of transport, and Incoterms used. Understanding logistics can help buyers negotiate better terms and reduce transportation expenses.
-
Margin: Suppliers typically add a profit margin to cover risks and business sustainability. Knowing the average margins in the industry can help in assessing fair pricing.
How Do Price Influencers Affect Copper Foil Procurement?
Several factors influence the pricing of copper foil, including:
-
Volume/MOQ (Minimum Order Quantity): Higher order volumes often lead to discounts. Establishing long-term relationships with suppliers can facilitate better pricing structures.
-
Specifications and Customization: Customized products generally cost more due to the complexity of production. Buyers should assess if standard products can meet their needs to optimize costs.
-
Material Quality and Certifications: Higher quality materials and certifications (e.g., ISO) may command higher prices. However, investing in certified materials can reduce long-term risks associated with product failures.
-
Supplier Factors: The reputation and reliability of a supplier can significantly impact pricing. Established suppliers with a track record of quality may charge more but offer better service and reliability.
-
Incoterms: The choice of Incoterms affects logistics costs and risk distribution. Buyers should carefully consider which terms best suit their operational model to avoid unexpected expenses.
What Are the Best Strategies for Negotiating Copper Foil Prices?
-
Do Your Homework: Research current market prices and trends. Knowledge of raw material costs can empower buyers during negotiations.
-
Focus on Total Cost of Ownership (TCO): Evaluate not just the purchase price but also the long-term costs associated with quality, performance, and maintenance. A lower upfront cost may lead to higher TCO if quality is compromised.
-
Leverage Competitive Quotes: Obtain multiple quotes from different suppliers to create a competitive bidding environment. This can often lead to better pricing or value-added services.
-
Establish Long-term Relationships: Building a rapport with suppliers can yield better terms and pricing over time. Loyal customers often receive preferential treatment.
-
Be Aware of Pricing Nuances: Understand how local market conditions in Africa, South America, the Middle East, and Europe influence pricing. Economic stability, currency fluctuations, and political factors can all play a role.
Conclusion
Navigating the complexities of copper foil sourcing requires a comprehensive understanding of cost structures, pricing dynamics, and strategic negotiation techniques. By leveraging these insights, international B2B buyers can enhance their procurement strategies, ensuring they secure the best value while maintaining quality and compliance.
Disclaimer: Prices and costs mentioned in this analysis are indicative and may vary based on market conditions and specific supplier agreements.
Alternatives Analysis: Comparing copper foil supplier With Other Solutions
When evaluating copper foil suppliers, it is essential to consider alternative solutions that may meet similar requirements in the manufacturing and electronics sectors. These alternatives can vary significantly in performance, cost, and implementation challenges, making it crucial for international B2B buyers to analyze their options thoroughly. Below, we present a comparison of copper foil suppliers against two viable alternatives: aluminum foil and printed circuit board (PCB) technology.
Comparison Aspect | Copper Foil Supplier | Aluminum Foil | Printed Circuit Board (PCB) Technology |
---|---|---|---|
Performance | High conductivity and flexibility, ideal for intricate designs | Moderate conductivity, less flexible | High precision, customizable for complex circuits |
Cost | Generally higher due to raw material prices | Lower initial cost, but may incur higher operational costs | Variable costs based on complexity and design |
Ease of Implementation | Requires specialized handling and storage | Easier to handle, less stringent storage needs | Complex manufacturing process requiring specialized equipment |
Maintenance | Minimal maintenance if properly stored | Low maintenance required | Regular inspection and testing needed |
Best Use Case | High-performance applications in electronics | Lightweight applications where cost is critical | Complex electronic devices requiring customized solutions |
What Are the Advantages and Disadvantages of Aluminum Foil as an Alternative?
Aluminum foil serves as a cost-effective alternative to copper foil. It is particularly suitable for applications where lightweight and flexible materials are required, such as in packaging and insulation. The lower initial costs make aluminum appealing for budget-conscious projects. However, its moderate conductivity limits its effectiveness in high-performance electronic applications, and it may require a thicker layer to achieve desired performance levels. Additionally, while aluminum foil is easier to handle, it does not offer the same level of flexibility in intricate designs that copper foil provides.
How Does Printed Circuit Board (PCB) Technology Compare to Copper Foil Suppliers?
Printed circuit boards (PCBs) represent another alternative, especially for complex electronic devices. PCBs can be designed to accommodate intricate layouts and provide high precision in electrical connections. The main advantage of PCBs is their ability to integrate various electronic components in a compact form. However, the manufacturing process is significantly more complex and can lead to higher costs depending on the design requirements. Moreover, PCBs require regular maintenance and inspection to ensure functionality, which may be a drawback for some manufacturers.
How Can B2B Buyers Choose the Right Solution for Their Needs?
When selecting between a copper foil supplier and alternative solutions, B2B buyers should consider their specific application requirements, budget constraints, and the level of complexity involved in their projects. For high-performance applications, copper foil remains the superior choice despite its higher cost. In contrast, aluminum foil may be more suitable for projects where cost efficiency is paramount, and performance requirements are moderate. For intricate electronic designs, PCBs provide a robust solution but come with a need for careful planning and investment in specialized manufacturing processes. Ultimately, aligning the choice with the intended application and long-term goals will lead to the most effective procurement decision.
Essential Technical Properties and Trade Terminology for copper foil supplier
What Are the Key Technical Properties of Copper Foil That B2B Buyers Should Know?
Understanding the essential technical properties of copper foil is crucial for international B2B buyers, particularly in industries such as electronics, automotive, and renewable energy. Here are some of the most significant specifications to consider:
-
Material Grade
Copper foil is available in various grades, which indicate the purity and quality of the copper. Common grades include C11000 (99.9% pure copper) and C10200 (99.95% pure copper). The higher the grade, the better the electrical and thermal conductivity, making it vital for applications where performance is critical. Buyers should verify the grade to ensure it meets their specific performance requirements. -
Thickness
The thickness of copper foil can significantly influence its suitability for various applications. Common thicknesses range from 1 mil (0.001 inch) to over 10 mils. Thicker foils provide better durability and are often used in demanding environments, whereas thinner foils are preferred for high-density applications like flexible printed circuit boards (PCBs). Understanding the required thickness helps buyers avoid over-specifying, which can lead to unnecessary costs. -
Tolerance
Tolerance refers to the allowable variation in thickness and width of the copper foil. Tighter tolerances (e.g., ±10%) are essential for applications requiring precise measurements, such as in high-frequency circuits. Buyers should discuss tolerance requirements with suppliers to ensure that the product can be manufactured to their specifications, as this directly affects the performance and reliability of the end product. -
Surface Finish
The surface finish of copper foil can vary and may include options such as electroplated, rolled, or oxidized surfaces. Different finishes can impact solderability, adhesion, and overall performance in electronic applications. Buyers must communicate their specific surface finish needs to ensure compatibility with manufacturing processes. -
Electrical Conductivity
Electrical conductivity is a critical property that determines how well the copper foil can conduct electricity. It is typically measured in percentage IACS (International Annealed Copper Standard). High conductivity is essential in applications such as battery connections and circuit boards. Buyers should prioritize suppliers who can provide copper foil with high conductivity ratings to ensure optimal performance.
Which Trade Terms Should B2B Buyers Understand When Sourcing Copper Foil?
Navigating the trade terminology associated with copper foil can simplify the procurement process and improve communication with suppliers. Here are several key terms that international buyers should familiarize themselves with:
-
OEM (Original Equipment Manufacturer)
An OEM is a company that produces parts or equipment that may be marketed by another manufacturer. Understanding OEM relationships is vital for buyers looking for custom solutions, as it can affect lead times and pricing. -
MOQ (Minimum Order Quantity)
MOQ refers to the smallest quantity of a product that a supplier is willing to sell. This term is crucial for B2B buyers, as it can impact inventory levels and cash flow. Knowing the MOQ helps buyers plan their purchasing strategy and avoid excess stock. -
RFQ (Request for Quotation)
An RFQ is a document sent to suppliers requesting a quote for specific quantities and specifications of copper foil. This process allows buyers to compare prices and terms effectively. Crafting a detailed RFQ can lead to better pricing and terms, making it a valuable tool for procurement. -
Incoterms (International Commercial Terms)
Incoterms are internationally recognized rules that define the responsibilities of buyers and sellers in international transactions. Familiarity with terms like FOB (Free On Board) and CIF (Cost Insurance and Freight) helps buyers understand shipping costs, risks, and delivery responsibilities, which is essential for effective supply chain management. -
Lead Time
Lead time is the amount of time it takes from placing an order to receiving the goods. Understanding lead times is critical for B2B buyers to manage production schedules and inventory effectively. Discussing lead times upfront can help avoid delays and ensure timely project execution.
By grasping these technical properties and trade terminologies, international B2B buyers can make informed decisions when sourcing copper foil, ultimately leading to more successful partnerships and better product outcomes.
Navigating Market Dynamics and Sourcing Trends in the copper foil supplier Sector
What Are the Current Market Dynamics and Key Trends in the Copper Foil Supplier Sector?
The copper foil supplier sector is experiencing notable shifts driven by technological advancements, global supply chain reconfigurations, and evolving market demands. International B2B buyers, particularly from regions like Africa, South America, the Middle East, and Europe, must understand these dynamics to make informed sourcing decisions. One significant driver is the increasing demand for copper foil in electric vehicle (EV) batteries and renewable energy applications, which has surged as governments push for sustainable energy solutions.
Emerging technologies, such as advanced manufacturing processes and automation, are optimizing production efficiencies and reducing costs. Additionally, the rise of Industry 4.0 has led to greater connectivity and data analytics in supply chains, allowing suppliers to respond swiftly to market fluctuations. For buyers, leveraging these technologies can enhance negotiation power and streamline procurement processes.
Moreover, geopolitical factors, including trade tariffs and regulations, are influencing sourcing strategies. For instance, suppliers in Europe may face different compliance requirements compared to those in Africa or South America, necessitating a thorough understanding of regional trade agreements. By staying updated on these trends, B2B buyers can navigate the complexities of the copper foil market and secure reliable partnerships.
How Is Sustainability Influencing Sourcing Decisions in the Copper Foil Sector?
Sustainability and ethical sourcing have become paramount in the copper foil supplier industry, reflecting a global shift towards responsible business practices. The environmental impact of copper mining and processing is significant, prompting buyers to prioritize suppliers that adhere to sustainable practices. This includes reducing carbon footprints, managing waste responsibly, and ensuring that operations do not harm local ecosystems.
Ethical supply chains are increasingly important for B2B buyers who want to align with corporate social responsibility (CSR) goals. Suppliers with certifications such as ISO 14001 (Environmental Management) and the Responsible Minerals Initiative (RMI) are often preferred, as these certifications demonstrate a commitment to environmental stewardship and ethical sourcing practices.
For international buyers, particularly those in Europe, where regulatory frameworks are stringent, sourcing copper foil from suppliers who prioritize sustainability can enhance brand reputation and mitigate risks associated with non-compliance. Furthermore, integrating green materials and processes can lead to cost savings over time, making sustainability not just an ethical choice but also a financially sound strategy.
How Has the Copper Foil Supplier Sector Evolved Over Time?
The evolution of the copper foil supplier sector is marked by significant technological advancements and changing market demands. Initially, copper foil was primarily used in traditional electronics; however, the rapid growth of the electronics industry, particularly in the 20th century, catalyzed the development of high-performance copper foils. This evolution continued with the advent of flexible printed circuits and the increasing use of copper foil in battery technologies, especially with the rise of electric vehicles and renewable energy storage.
As the market has expanded, so too have the complexities of sourcing. The global supply chain has had to adapt to fluctuating demand, geopolitical tensions, and sustainability pressures. Today’s international B2B buyers must navigate a landscape where technological innovation and ethical considerations are intertwined, ensuring that their sourcing strategies are both efficient and responsible. Understanding this evolution is crucial for making strategic decisions that align with current and future market trends.
Frequently Asked Questions (FAQs) for B2B Buyers of copper foil supplier
-
How can I ensure the quality of copper foil from suppliers?
To ensure the quality of copper foil, it is crucial to request certification documents, such as ISO 9001 or other relevant quality management certifications. Conducting factory audits or inspections can also help verify manufacturing practices. Establishing a clear set of quality specifications in your purchase agreement will enable suppliers to meet your expectations. Additionally, consider requesting samples before placing a bulk order, allowing you to assess the material’s properties and performance firsthand. -
What are the typical minimum order quantities (MOQs) for copper foil?
Minimum order quantities for copper foil can vary significantly depending on the supplier and the specific product specifications. Generally, MOQs can range from 100 kg to several tons. When negotiating with suppliers, it’s important to communicate your needs clearly and explore options for smaller orders, especially if you are a new buyer or testing a new product line. Some suppliers may offer flexibility on MOQs for long-term contracts or high-value orders. -
What payment terms should I expect from copper foil suppliers?
Payment terms can vary widely among suppliers, but common practices include a deposit upon order confirmation (often 30% to 50%) and the balance before shipping. Some suppliers may offer open account terms for established relationships. It’s advisable to negotiate payment terms that align with your cash flow needs while ensuring the supplier feels secure in the transaction. Using letters of credit can provide additional security for both parties in international transactions. -
How do I evaluate a copper foil supplier’s reliability?
Evaluating a supplier’s reliability involves checking their business credentials, such as years in operation and customer references. Online reviews and ratings can provide insights into their reputation. It’s also beneficial to inquire about their production capabilities, lead times, and past performance metrics. Engaging in a trial order can help assess their service quality and responsiveness before committing to larger contracts. -
What customization options are available for copper foil products?
Many copper foil suppliers offer customization options, including variations in thickness, width, and surface treatment. Some suppliers may also provide specialized grades of copper foil tailored for specific applications, such as electronics or automotive industries. When discussing your needs, provide detailed specifications to ensure that the supplier can meet your requirements. Collaborating closely during the design phase can lead to better product outcomes. -
What are the logistics considerations when sourcing copper foil internationally?
Logistics play a crucial role in sourcing copper foil internationally. Factors to consider include shipping methods, lead times, customs clearance, and potential tariffs. Establishing a clear logistics plan that outlines responsibilities for shipping, insurance, and delivery can prevent misunderstandings. Partnering with a freight forwarder experienced in handling copper products can streamline the process and mitigate risks associated with international shipping. -
How can I protect my business when sourcing from international suppliers?
To protect your business when sourcing from international suppliers, conduct thorough due diligence, including verifying their business licenses and checking for any legal disputes. Draft a comprehensive contract that includes terms on quality, delivery schedules, and remedies for non-compliance. Consider using a third-party escrow service for payment protection. Additionally, purchasing trade insurance can help mitigate risks associated with international transactions. -
What regulations should I be aware of when importing copper foil?
When importing copper foil, you must comply with both local and international regulations. This includes understanding import tariffs, duties, and any specific health and safety standards applicable to copper products in your country. Familiarize yourself with regulations from organizations such as the International Electrotechnical Commission (IEC) and any local governmental bodies. Consulting with a customs broker can help navigate these regulations and ensure compliance, reducing the risk of delays or penalties.
Important Disclaimer & Terms of Use
⚠️ Important Disclaimer
The information provided in this guide, including content regarding manufacturers, technical specifications, and market analysis, is for informational and educational purposes only. It does not constitute professional procurement advice, financial advice, or legal advice.
While we have made every effort to ensure the accuracy and timeliness of the information, we are not responsible for any errors, omissions, or outdated information. Market conditions, company details, and technical standards are subject to change.
B2B buyers must conduct their own independent and thorough due diligence before making any purchasing decisions. This includes contacting suppliers directly, verifying certifications, requesting samples, and seeking professional consultation. The risk of relying on any information in this guide is borne solely by the reader.
Strategic Sourcing Conclusion and Outlook for copper foil supplier
What Are the Key Takeaways for Strategic Sourcing of Copper Foil?
In navigating the competitive landscape of copper foil procurement, international B2B buyers must prioritize strategic sourcing to ensure supply chain resilience and cost efficiency. Key takeaways include understanding regional market dynamics, establishing strong relationships with suppliers, and leveraging technological advancements to enhance product quality and reduce lead times. Buyers should also stay informed about geopolitical factors that may impact supply chains, especially in regions like Africa and South America, where resource availability can fluctuate.
How Can Buyers Enhance Their Sourcing Strategies?
Investing time in supplier audits and performance evaluations can significantly mitigate risks associated with quality and reliability. Additionally, diversifying the supplier base across regions—such as the Middle East and Europe—can provide a buffer against market volatility. By utilizing data-driven insights, buyers can make informed decisions that align with their long-term objectives.
What Does the Future Hold for Copper Foil Sourcing?
As the demand for electronic components continues to grow, the outlook for copper foil suppliers remains positive. International B2B buyers are encouraged to explore innovative sourcing strategies that capitalize on emerging technologies and sustainable practices. By proactively adapting to market trends and fostering collaborative partnerships, businesses can position themselves for success in an evolving landscape.
In conclusion, effective strategic sourcing not only enhances operational efficiency but also contributes to long-term profitability. Now is the time for buyers in Africa, South America, the Middle East, and Europe to take decisive action in refining their sourcing strategies and securing a competitive edge in the copper foil market.