Cut Costs with a Trusted Truck Spare Parts Supplier (2025)
Introduction: Navigating the Global Market for truck spare parts supplier
In today’s global economy, sourcing truck spare parts can pose significant challenges for international B2B buyers. Whether you are in Africa, South America, the Middle East, or Europe, navigating the complexities of the supply chain is crucial to maintaining your fleet’s efficiency and reliability. This guide delves into the intricacies of finding reputable truck spare parts suppliers, addressing key factors such as product types, applications, and supplier vetting processes.
By providing comprehensive insights into market trends, regulatory considerations, and cost management strategies, this guide empowers decision-makers to make informed purchases that align with their operational needs. Buyers will gain valuable knowledge on identifying high-quality components, understanding the implications of sourcing from different regions, and evaluating suppliers based on reliability and service.
Additionally, we will explore how regional differences affect the availability and pricing of truck spare parts, particularly for markets in Germany, Poland, and other European countries, as well as in emerging markets across Africa and South America. Ultimately, our aim is to equip you with the tools and information necessary to navigate the global market for truck spare parts effectively, ensuring your business can thrive in a competitive landscape.
Understanding truck spare parts supplier Types and Variations
Type Name | Key Distinguishing Features | Primary B2B Applications | Brief Pros & Cons for Buyers |
---|---|---|---|
OEM (Original Equipment Manufacturer) | Provides parts made to manufacturer specifications; often more expensive | Fleet maintenance, new vehicle assembly | Pros: High quality, perfect fit; Cons: Higher costs, limited flexibility. |
Aftermarket Suppliers | Offers a wide range of parts, often at lower prices; may vary in quality | Cost-effective repairs, customization | Pros: Competitive pricing, diverse options; Cons: Quality inconsistency, potential fit issues. |
Wholesale Distributors | Bulk purchasing options; often partners with various manufacturers | Large-scale operations, inventory stocking | Pros: Lower prices per unit, reliable supply; Cons: Larger minimum order quantities. |
Specialty Suppliers | Focuses on specific truck parts or brands; expert knowledge in niche areas | Specialized repairs, unique vehicle needs | Pros: Expertise, tailored solutions; Cons: Limited product range, potentially higher costs. |
Online Marketplaces | Wide selection of parts from various suppliers; convenient shopping experience | Small to medium repairs, urgent needs | Pros: Easy comparison, accessibility; Cons: Variable quality, longer shipping times. |
What Are the Characteristics of OEM Suppliers?
OEM suppliers are known for producing parts that meet the exact specifications set by vehicle manufacturers. This ensures a perfect fit and high-quality performance, making them ideal for fleet maintenance and new vehicle assembly. However, B2B buyers should be aware that OEM parts often come at a premium price. When considering OEM suppliers, it’s essential to evaluate the long-term value versus the upfront costs, especially for businesses operating on tight budgets.
How Do Aftermarket Suppliers Operate?
Aftermarket suppliers provide a diverse range of truck spare parts that may not be manufactured by the original vehicle makers. These suppliers often offer lower prices, making them an attractive option for cost-conscious businesses. However, the quality of aftermarket parts can vary significantly, which poses a risk for buyers. Companies should conduct thorough research and possibly seek recommendations to ensure they select reputable aftermarket suppliers that balance cost with quality.
What Advantages Do Wholesale Distributors Offer?
Wholesale distributors are a vital resource for businesses looking to purchase truck spare parts in bulk. They typically have partnerships with various manufacturers, allowing them to offer competitive pricing for large orders. This is particularly beneficial for large-scale operations or companies that need to maintain significant inventory levels. However, buyers should be prepared for larger minimum order quantities, which can impact cash flow and storage capabilities.
What Should You Know About Specialty Suppliers?
Specialty suppliers focus on specific types of truck parts or particular brands, providing an in-depth understanding of their niche. This expertise allows them to offer tailored solutions that can be invaluable for specialized repairs or unique vehicle needs. While specialty suppliers can deliver high-quality parts and excellent service, their limited product range and potentially higher prices may not suit every buyer’s needs. Businesses should assess their specific requirements and budget before engaging with these suppliers.
How Do Online Marketplaces Benefit B2B Buyers?
Online marketplaces have transformed the way B2B buyers source truck spare parts, offering a vast selection from various suppliers in one convenient location. This allows for easy comparison of prices and products, making it simpler to find the best deals. However, the quality of parts can vary widely, and shipping times may be longer than traditional suppliers. Buyers should carefully read reviews and check ratings to ensure they are purchasing from reputable vendors to mitigate risks associated with online purchases.
Related Video: Functions and Classification of Spare Parts Management
Key Industrial Applications of truck spare parts supplier
Industry/Sector | Specific Application of truck spare parts supplier | Value/Benefit for the Business | Key Sourcing Considerations for this Application |
---|---|---|---|
Logistics and Transportation | Replacement parts for fleet maintenance | Minimizes downtime and enhances operational efficiency | Quality assurance, compatibility with existing vehicles, and lead times. |
Construction | Heavy-duty truck parts for site operations | Increases productivity and ensures safety on-site | Durability, supplier reliability, and compliance with local regulations. |
Agriculture | Spare parts for agricultural transport vehicles | Ensures timely delivery of produce and reduces losses | Availability of parts specific to agricultural machinery and seasonal demands. |
Mining | Components for mining trucks | Improves performance and reduces maintenance costs | Specialized parts for harsh environments and supplier expertise in mining applications. |
Waste Management | Parts for refuse collection vehicles | Enhances service efficiency and reduces operational costs | Availability of eco-friendly parts and compliance with waste management regulations. |
How Are Truck Spare Parts Suppliers Used in Logistics and Transportation?
In the logistics and transportation sector, truck spare parts suppliers play a crucial role in maintaining fleet vehicles. By providing high-quality replacement parts, these suppliers help businesses minimize vehicle downtime, which is essential for meeting delivery schedules. International B2B buyers must prioritize sourcing suppliers that ensure compatibility with their fleet models and offer reliable quality assurance. Timely delivery of parts is also vital to avoid disruptions in operations.
What Is the Importance of Truck Spare Parts in Construction?
In construction, heavy-duty trucks are essential for transporting materials and equipment to job sites. Truck spare parts suppliers provide robust components that enhance vehicle performance and safety. This is particularly important in regions where construction projects are time-sensitive. Buyers should consider the durability of parts, as well as the supplier’s reliability and ability to meet local regulatory requirements to ensure compliance and safety on-site.
How Do Truck Spare Parts Impact Agricultural Efficiency?
Agricultural transport vehicles require specialized spare parts to operate efficiently. Suppliers of truck parts play a significant role in ensuring that agricultural goods are delivered promptly, reducing potential losses due to delays. For international buyers, it’s crucial to source parts that are specifically designed for agricultural machinery and can withstand varying seasonal demands. Availability and timely delivery are key factors in maintaining productivity during peak seasons.
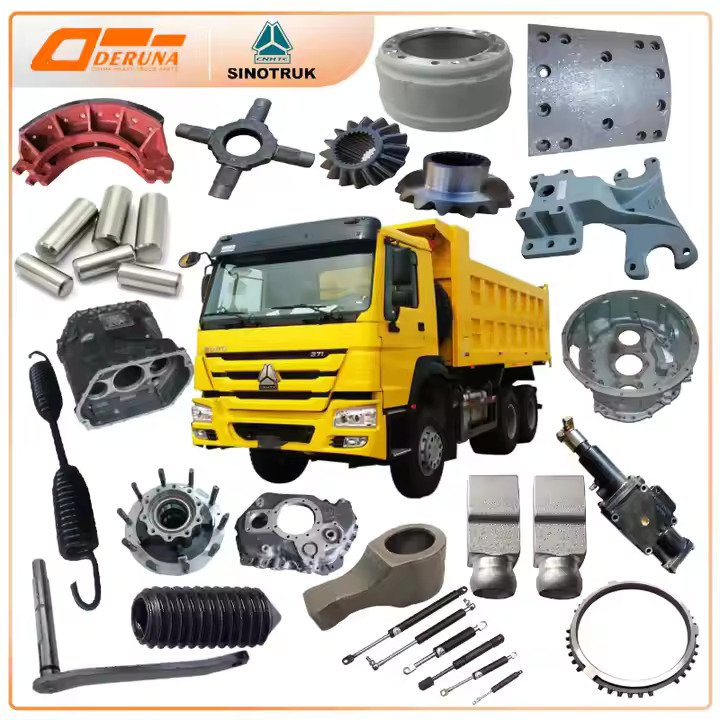
A stock image related to truck spare parts supplier.
Why Are Quality Spare Parts Essential in Mining Operations?
In the mining industry, the performance of mining trucks is critical to operational success. Truck spare parts suppliers provide components that are specifically engineered for the harsh conditions of mining environments. This specialization helps improve vehicle performance and reduces maintenance costs. Buyers should look for suppliers with expertise in mining applications and a strong reputation for providing durable parts that can withstand extreme conditions.
How Do Spare Parts Suppliers Enhance Waste Management Operations?
Waste management companies rely on refuse collection vehicles that require regular maintenance and timely replacement of parts. Truck spare parts suppliers contribute to enhancing service efficiency and reducing operational costs by providing high-quality components. For B2B buyers in this sector, it is essential to consider suppliers who offer eco-friendly parts and comply with local waste management regulations, ensuring that operations are both effective and sustainable.
Related Video: Diesel Generator Parts and its Functions | Major Parts of DG Set
3 Common User Pain Points for ‘truck spare parts supplier’ & Their Solutions
Scenario 1: Navigating Complex Supply Chains for Spare Parts
The Problem:
International B2B buyers often encounter challenges when navigating complex supply chains for truck spare parts. In regions like Africa and South America, where logistical issues can be compounded by political instability or infrastructural deficits, sourcing parts can become a daunting task. Buyers may face delays in shipments, leading to prolonged vehicle downtime and increased operational costs. Additionally, the lack of reliable local suppliers can make it difficult to find quality parts that meet specific regulatory standards, resulting in compromised vehicle performance and safety.
The Solution:
To overcome these challenges, B2B buyers should establish a robust vendor management system that includes multiple suppliers from different geographical locations. By diversifying their supplier base, companies can mitigate risks associated with supply chain disruptions. It is also essential to conduct thorough due diligence on potential suppliers, including checking their certifications, customer reviews, and delivery capabilities. Implementing a just-in-time inventory system can help maintain optimal stock levels while minimizing excess inventory costs. Lastly, leveraging technology such as supply chain management software can provide real-time tracking of shipments, helping buyers stay informed and responsive to potential delays.
Scenario 2: Ensuring Quality and Compatibility of Spare Parts
The Problem:
A common pain point for B2B buyers is ensuring the quality and compatibility of spare parts purchased from suppliers. In regions like the Middle East and Europe, where various truck models may require specific parts, buyers often struggle with discrepancies in part specifications. This can lead to costly returns, wasted resources, and significant delays in repairs, ultimately impacting business operations.
The Solution:
To ensure quality and compatibility, buyers should invest time in detailed communication with suppliers regarding their specific needs. This includes providing comprehensive specifications and, when possible, requesting samples before committing to large orders. Establishing relationships with suppliers who have a reputation for quality assurance can also be beneficial. Implementing a standardized evaluation process for incoming parts can help identify and resolve compatibility issues early in the procurement process. Additionally, utilizing platforms that offer user reviews and ratings on spare parts can provide valuable insights into the performance and reliability of specific components.
Scenario 3: Managing Cost Efficiency in Spare Parts Procurement
The Problem:
Cost management is a critical concern for B2B buyers, especially in competitive markets across Africa and South America. Fluctuating prices for truck spare parts can strain budgets, and buyers may find themselves paying inflated prices due to a lack of negotiation leverage or market knowledge. This financial pressure can lead to reduced profitability and hinder the ability to invest in other areas of the business.
The Solution:
B2B buyers can enhance cost efficiency by implementing strategic sourcing practices. This involves conducting market research to understand price trends and establishing long-term contracts with suppliers for better pricing stability. Building strong relationships with suppliers can also empower buyers to negotiate discounts, especially for bulk purchases. Additionally, buyers should consider participating in industry trade shows or networking events to connect with multiple suppliers and gain insights into competitive pricing. Utilizing procurement software can streamline the purchasing process, allowing for better tracking of spending and identifying opportunities for cost savings.
Strategic Material Selection Guide for truck spare parts supplier
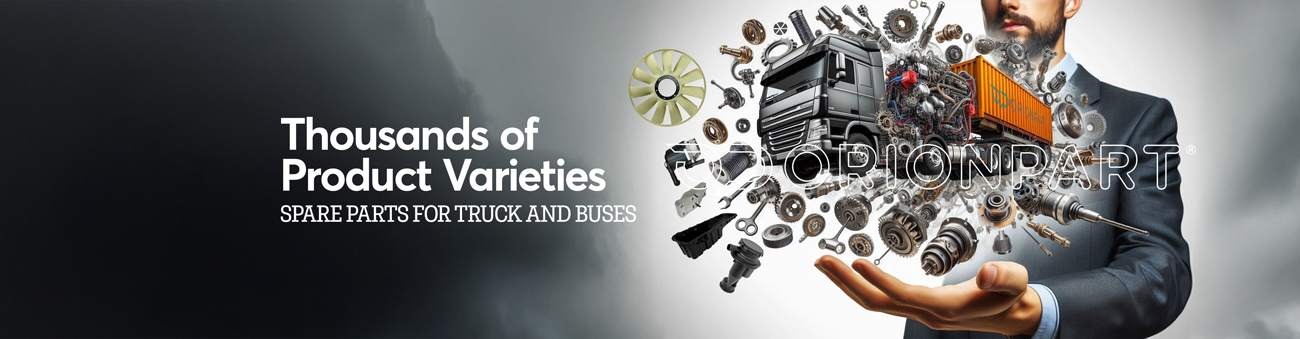
A stock image related to truck spare parts supplier.
When selecting materials for truck spare parts, international B2B buyers must consider various factors that influence performance, durability, and compliance with regional standards. Below is an analysis of four common materials used in truck spare parts, detailing their properties, advantages, disadvantages, and specific considerations for buyers from Africa, South America, the Middle East, and Europe.
What Are the Key Properties of Steel for Truck Spare Parts?
Steel is one of the most widely used materials in the manufacturing of truck spare parts due to its excellent mechanical properties. It offers high tensile strength, making it suitable for components that experience significant stress, such as axles and frames. Steel also has good temperature resistance, capable of withstanding high temperatures without losing structural integrity. However, it is susceptible to corrosion, particularly in humid or saline environments.
Pros & Cons: The durability of steel makes it a preferred choice for heavy-duty applications. However, the need for protective coatings or treatments to prevent rust can increase manufacturing complexity and costs.
Impact on Application: Steel is compatible with a variety of media, including hydraulic fluids and fuels, but its corrosion susceptibility can limit its use in certain environments unless adequately treated.
Considerations for International Buyers: Buyers in regions like Europe may need to adhere to specific standards such as DIN or EN for steel quality. In contrast, buyers in Africa and South America should consider local availability and the cost implications of importing high-grade steel.
How Does Aluminum Compare as a Material for Truck Spare Parts?
Aluminum is increasingly used in truck spare parts due to its lightweight nature and resistance to corrosion. It is particularly advantageous for components where weight reduction is critical, such as engine parts and wheels. Aluminum can withstand moderate temperatures and pressures, making it suitable for various applications.
Pros & Cons: The primary advantage of aluminum is its lightweight property, which can enhance fuel efficiency. However, it has lower tensile strength compared to steel, which may limit its use in high-stress applications.
Impact on Application: Aluminum’s corrosion resistance makes it suitable for environments with high humidity or exposure to saltwater. However, its compatibility with certain chemicals should be assessed to avoid degradation.
Considerations for International Buyers: Buyers in the Middle East and Europe may find that aluminum components comply with various industry standards, such as ASTM or JIS. Understanding local recycling regulations can also be beneficial, as aluminum is highly recyclable.
What Are the Advantages of Using Composite Materials in Truck Spare Parts?
Composite materials, such as fiberglass and carbon fiber, are gaining traction in the truck spare parts market due to their unique properties. These materials offer excellent strength-to-weight ratios and are highly resistant to corrosion and fatigue. Composites can be tailored to meet specific performance requirements, making them suitable for a range of applications.
Pros & Cons: The primary advantage of composites is their lightweight nature combined with high strength, which can significantly improve vehicle performance. However, they can be more expensive and complex to manufacture, which may deter some buyers.
Impact on Application: Composites are often used in high-performance applications where weight savings are critical, such as in racing trucks or specialized vehicles. Their chemical resistance makes them suitable for various media, but compatibility must be verified for specific applications.
Considerations for International Buyers: Buyers in Europe may find that composite materials must meet stringent safety and environmental regulations. Understanding the manufacturing process and sourcing from reputable suppliers is crucial for quality assurance.
What Role Does Rubber Play in Truck Spare Parts Manufacturing?
Rubber is essential in truck spare parts, particularly for components requiring flexibility and shock absorption, such as bushings, seals, and gaskets. Its inherent elasticity allows it to withstand a range of temperatures and pressures, making it suitable for various applications.
Pros & Cons: The flexibility and durability of rubber make it ideal for vibration dampening and sealing applications. However, its susceptibility to degradation from environmental factors such as UV light and ozone can limit its lifespan.
Impact on Application: Rubber is compatible with many fluids, including oils and coolants, but care must be taken to choose the right type of rubber for specific applications to avoid chemical breakdown.
Considerations for International Buyers: Buyers in Africa and South America should consider local sourcing of rubber products to reduce costs and ensure compliance with local standards. Additionally, understanding the specific rubber grades and their properties is vital for ensuring compatibility with various media.
Summary Table of Material Selection for Truck Spare Parts
Material | Typical Use Case for truck spare parts supplier | Key Advantage | Key Disadvantage/Limitation | Relative Cost (Low/Med/High) |
---|---|---|---|---|
Steel | Axles, frames, and structural components | High tensile strength | Susceptible to corrosion | Medium |
Aluminum | Engine parts, wheels, and lightweight components | Lightweight and corrosion-resistant | Lower tensile strength than steel | Medium to High |
Composite | High-performance parts, specialized vehicles | Excellent strength-to-weight ratio | High manufacturing complexity | High |
Rubber | Bushings, seals, and gaskets | Flexibility and shock absorption | Degradation from environmental factors | Low to Medium |
This guide provides a strategic overview of material selection for truck spare parts, enabling international B2B buyers to make informed decisions based on performance, cost, and compliance with regional standards.
In-depth Look: Manufacturing Processes and Quality Assurance for truck spare parts supplier
What Are the Key Stages in the Manufacturing Process of Truck Spare Parts?
The manufacturing of truck spare parts is a complex process that involves several critical stages, each essential for producing high-quality components. Here’s a breakdown of the main stages:
-
Material Preparation
The first step in the manufacturing process involves selecting and preparing raw materials. Common materials for truck spare parts include steel, aluminum, and various polymers. Suppliers should ensure that the materials meet specific industry standards and are sourced from reliable suppliers. For instance, using high-grade steel can significantly enhance the durability of parts like brake pads and gears. -
Forming
This stage involves shaping the raw materials into the desired form. Techniques such as casting, forging, and machining are commonly used. For example, forging is particularly beneficial for parts that require high strength, such as crankshafts. Buyers should inquire about the forming techniques employed by suppliers, as they can impact the final product’s quality and performance. -
Assembly
Once the individual components are formed, they are assembled into complete parts. This stage may involve welding, fastening, or using adhesives, depending on the design and material of the spare part. Precision in assembly is crucial, as misalignment can lead to premature wear or failure in the field. B2B buyers should look for suppliers who use automated assembly processes, as these often yield higher accuracy and consistency. -
Finishing
The finishing stage enhances the appearance and functionality of the spare parts. Techniques such as surface treatment, painting, or coating are used to protect against corrosion and wear. Additionally, finishing can improve aesthetics, which may be important for certain customers. Buyers should ask about the finishing processes to ensure that the parts will withstand environmental conditions specific to their region.
How Is Quality Assurance Implemented in Truck Spare Parts Manufacturing?
Quality assurance (QA) is a fundamental aspect of manufacturing truck spare parts, ensuring that the products meet specified standards and customer expectations. Here’s how QA is typically structured:
-
International Standards for Quality Assurance
Many suppliers adhere to international standards such as ISO 9001, which outlines the requirements for a quality management system. Compliance with ISO 9001 ensures that suppliers have consistent processes that lead to continual improvement and customer satisfaction. Additionally, industry-specific certifications like CE (Conformité Européenne) for European markets and API (American Petroleum Institute) for certain components can provide further assurance of quality. -
Quality Control Checkpoints
– Incoming Quality Control (IQC): This initial checkpoint evaluates the quality of raw materials before they enter the production line. Suppliers conduct inspections to verify material specifications and compliance with standards.
– In-Process Quality Control (IPQC): Throughout the manufacturing process, IPQC monitors production to catch defects early. Regular inspections and testing at this stage help maintain quality and reduce waste.
– Final Quality Control (FQC): This stage involves a comprehensive inspection of finished products before shipment. FQC checks for dimensional accuracy, functionality, and overall quality. -
Common Testing Methods Used in Quality Assurance
Various testing methods ensure the integrity and performance of spare parts. These may include:
– Mechanical Testing: Evaluates properties such as tensile strength, hardness, and fatigue resistance.
– Non-Destructive Testing (NDT): Techniques like ultrasonic and radiographic testing help identify internal defects without damaging the parts.
– Functional Testing: Ensures that parts perform as intended under simulated operational conditions.
How Can B2B Buyers Verify the Quality Control Processes of Suppliers?
For international B2B buyers, especially those from regions like Africa, South America, the Middle East, and Europe, verifying a supplier’s quality control (QC) practices is crucial. Here are actionable steps to ensure that suppliers meet quality standards:
-
Conduct Supplier Audits
Regular audits help assess a supplier’s adherence to quality standards and identify potential areas for improvement. Buyers should consider scheduling both announced and unannounced audits to get a realistic view of the supplier’s operations. -
Request Quality Assurance Documentation
Suppliers should provide documentation that details their QA processes, including inspection reports, certification copies, and compliance records. This documentation can offer insights into the supplier’s commitment to quality. -
Engage Third-Party Inspection Services
Utilizing third-party inspection agencies can provide an unbiased assessment of the supplier’s quality control measures. These agencies can conduct inspections at various stages of production and provide detailed reports to buyers. -
Understand Regional Certification Nuances
Different regions may have specific certification requirements that can impact the acceptance of spare parts. For example, European buyers may require CE certification, while Middle Eastern buyers might look for compliance with GSO standards. Understanding these nuances will help buyers make informed decisions and ensure compliance with local regulations.
What Are the Challenges and Solutions in Quality Assurance for International B2B Buyers?
B2B buyers from diverse regions face unique challenges in ensuring quality assurance when sourcing truck spare parts. Here are common challenges and their potential solutions:
-
Language Barriers: Communication difficulties can lead to misunderstandings about quality expectations. Solution: Engage translators or local representatives who can facilitate clear communication.
-
Cultural Differences: Varying business practices may affect how quality assurance is perceived. Solution: Conduct training sessions for both buyers and suppliers to align on quality expectations and practices.
-
Logistical Issues: Shipping delays can complicate the timely delivery of quality-assured parts. Solution: Establish clear timelines and contingency plans with suppliers to manage potential delays effectively.
By understanding the intricacies of manufacturing processes and quality assurance, B2B buyers can make informed decisions when sourcing truck spare parts, ensuring they receive high-quality products that meet their operational needs.
Practical Sourcing Guide: A Step-by-Step Checklist for ‘truck spare parts supplier’
The purpose of this sourcing guide is to provide international B2B buyers with a practical checklist to streamline the procurement process for truck spare parts suppliers. Whether you are sourcing from Africa, South America, the Middle East, or Europe, following these steps will help ensure that you select a reliable supplier who can meet your specific needs.
Step 1: Define Your Technical Specifications
Before reaching out to suppliers, clearly outline the technical specifications of the truck spare parts you need. This includes dimensions, material types, compatibility with different truck models, and any certifications required for safety or quality standards. A well-defined specification helps in minimizing misunderstandings and ensures that you receive the correct parts.
Step 2: Research Potential Suppliers
Conduct thorough research to identify potential suppliers who specialize in truck spare parts. Use online directories, trade shows, and industry forums to gather information. Pay attention to suppliers with a strong presence in your target regions, such as Africa or Europe, as they may offer better shipping options and understand local regulations.
Step 3: ✅ Verify Supplier Certifications
It is crucial to verify that your selected suppliers have the necessary certifications to guarantee quality and compliance with industry standards. Look for ISO certifications, compliance with local regulations, and any specific certifications relevant to the truck parts you are sourcing. This step is vital for ensuring product reliability and safety.
Step 4: Evaluate Supplier Experience and Reputation
Assess the experience and reputation of potential suppliers in the truck spare parts industry. Check for reviews, testimonials, and case studies to gauge their track record. A supplier with extensive experience is likely to understand the nuances of the market and can provide valuable insights into product choices and sourcing strategies.
Step 5: Request Samples and Product Specifications
Before making a bulk order, request samples of the truck spare parts to evaluate their quality. This allows you to physically inspect the parts for compliance with your specifications and standards. Additionally, ask for detailed product specifications and data sheets to ensure that the parts meet your requirements.
Step 6: Negotiate Terms and Conditions
Once you have shortlisted potential suppliers, engage in negotiations regarding pricing, payment terms, delivery schedules, and warranty conditions. Clear agreements on these aspects can prevent misunderstandings later on and help build a strong supplier relationship. Be sure to discuss any penalties for late deliveries or defective parts.
Step 7: Establish a Communication Plan
Develop a communication plan that outlines how you and your supplier will interact throughout the procurement process. Regular updates on order status, shipping information, and any potential issues are essential for maintaining transparency. Effective communication can significantly enhance the supplier relationship and ensure smooth operations.
By following this step-by-step checklist, international B2B buyers can effectively navigate the complexities of sourcing truck spare parts, ensuring they select the right supplier to meet their needs.
Comprehensive Cost and Pricing Analysis for truck spare parts supplier Sourcing
What are the Key Cost Components in Sourcing Truck Spare Parts?
When sourcing truck spare parts, understanding the cost structure is crucial for B2B buyers. The primary cost components include:
-
Materials: The type of materials used significantly affects the overall cost. Premium materials like high-strength steel or specialized alloys can increase prices, but they often result in better durability and performance.
-
Labor: Labor costs vary depending on the region where the parts are manufactured. Countries with lower labor costs can offer competitive pricing, but it’s essential to consider the skill level and expertise of the workforce.
-
Manufacturing Overhead: This includes indirect costs such as utilities, rent, and administrative expenses. These costs can vary widely based on the supplier’s location and operational efficiency.
-
Tooling: Initial tooling costs can be significant, especially for custom parts. It’s advisable to inquire about these costs upfront, particularly if you have specific design requirements.
-
Quality Control (QC): Effective QC processes ensure that parts meet necessary specifications and standards. Suppliers with stringent QC measures may charge more but often provide better reliability.
-
Logistics: Transportation costs can vary based on distance, mode of transport, and customs fees. Understanding the logistics involved will help in calculating the total cost accurately.
-
Margin: Suppliers will add a profit margin to cover their operational costs and risks. This margin can fluctuate based on market conditions and the supplier’s pricing strategy.
How Do Price Influencers Affect Truck Spare Parts Costs?
Several factors can influence the pricing of truck spare parts:
-
Volume and Minimum Order Quantity (MOQ): Higher order volumes often lead to lower per-unit prices. Negotiating favorable MOQs can significantly enhance cost-efficiency.
-
Specifications and Customization: Custom parts usually come at a premium. Clearly defining your specifications can help in obtaining accurate quotes and avoiding unexpected costs.
-
Materials and Quality Certifications: Parts made from superior materials or those that come with quality certifications (like ISO or CE) may have higher upfront costs but can lead to lower Total Cost of Ownership (TCO) due to enhanced durability.
-
Supplier Factors: Supplier reputation, reliability, and past performance can influence pricing. Established suppliers may charge more due to their track record, but the investment can pay off in terms of reliability.
-
Incoterms: Understanding the terms of trade (such as FOB, CIF, or DDP) is critical. These terms dictate who is responsible for shipping costs, insurance, and risk during transit, which can have a significant impact on the final price.
What Negotiation Tips Can Help B2B Buyers Optimize Costs?
For international B2B buyers, particularly from Africa, South America, the Middle East, and Europe, effective negotiation can lead to significant cost savings:
-
Research and Benchmarking: Gather data on market prices and competitor offerings to establish a baseline for negotiation. This knowledge empowers you to negotiate from a position of strength.
-
Build Relationships: Establishing a good rapport with suppliers can lead to better pricing and terms. Suppliers are often more willing to negotiate with buyers they trust.
-
Consider Total Cost of Ownership (TCO): When evaluating quotes, consider not just the purchase price but also the long-term costs associated with the parts, including maintenance and potential downtime.
-
Flexibility in Specifications: If possible, be flexible with your specifications. This can open up options for lower-cost alternatives without compromising quality.
-
Leverage Local Suppliers: Whenever feasible, consider sourcing from local suppliers. This can reduce logistics costs and lead to faster delivery times.
What Should Buyers Be Aware of Regarding Indicative Prices?
It’s essential to recognize that prices for truck spare parts can fluctuate based on various factors, including market demand, raw material costs, and geopolitical issues. Always request detailed quotes that break down costs and clarify any potential additional fees. This transparency will help you make informed decisions and avoid unexpected expenses.
Alternatives Analysis: Comparing truck spare parts supplier With Other Solutions
Understanding Alternative Solutions to Truck Spare Parts Suppliers
In the dynamic landscape of the truck spare parts industry, international B2B buyers often seek alternative solutions to traditional suppliers. These alternatives may provide cost savings, improved performance, or enhanced flexibility in procurement. Below, we compare truck spare parts suppliers against two viable alternatives: aftermarket parts and direct manufacturer sourcing.
Comparison Aspect | Truck Spare Parts Supplier | Aftermarket Parts | Direct Manufacturer Sourcing |
---|---|---|---|
Performance | High quality, OEM parts available | Varies; can be high quality but often lower than OEM | Typically high, with potential for customization |
Cost | Moderate to high, depending on brand | Generally lower than OEM, but quality varies | Often higher due to direct sourcing costs |
Ease of Implementation | Straightforward, established processes | May require more research to find reliable suppliers | Complex logistics and longer lead times |
Maintenance | Regular support and warranty options | Limited support; warranties may not apply | High maintenance due to direct relationships |
Best Use Case | Consistent quality for fleet maintenance | Budget-conscious fleets or older vehicles | Custom needs or large volume purchases |
How Do Aftermarket Parts Compare to Traditional Suppliers?
Aftermarket parts are an appealing alternative for many B2B buyers, especially those managing older truck models or operating on tighter budgets. These parts are typically less expensive than OEM (Original Equipment Manufacturer) parts, which can significantly reduce overall maintenance costs. However, the performance of aftermarket parts can be inconsistent, leading to potential quality issues. Buyers must carefully vet suppliers to ensure they provide reliable and durable components.
What Are the Benefits of Direct Manufacturer Sourcing?
Direct manufacturer sourcing allows businesses to procure spare parts straight from the factory, often resulting in better prices for bulk orders and the possibility of customization. This method is particularly advantageous for companies with specific requirements or those looking to establish long-term partnerships with manufacturers. However, the complexity of logistics and longer lead times can pose challenges, especially for businesses needing immediate replacements. Moreover, this option may not be feasible for smaller operations due to higher minimum order quantities.
Conclusion: How Can B2B Buyers Choose the Right Solution for Their Needs?
When evaluating options for truck spare parts, B2B buyers must consider various factors, including budget constraints, the urgency of parts needed, and the specific requirements of their fleet. While truck spare parts suppliers provide reliable, high-quality options, alternatives like aftermarket parts and direct manufacturer sourcing can offer significant benefits under the right circumstances. By thoroughly analyzing these alternatives, businesses can make informed decisions that align with their operational goals and financial realities, ensuring they maintain efficient and cost-effective fleet operations.
Essential Technical Properties and Trade Terminology for truck spare parts supplier
When sourcing truck spare parts, understanding essential technical properties and trade terminology is vital for making informed purchasing decisions. Below are critical specifications and commonly used industry terms that every B2B buyer should be familiar with.
What Are the Key Technical Properties of Truck Spare Parts?
1. Material Grade
Material grade refers to the specific classification of materials based on their properties and performance characteristics. Common grades for truck spare parts include steel, aluminum, and composite materials. Understanding the material grade is crucial as it directly impacts the durability, weight, and overall performance of the parts. For instance, high-grade steel components are often preferred for their strength and resistance to wear, which can lead to lower maintenance costs over time.
2. Tolerance
Tolerance defines the permissible limits of variation in a physical dimension of a part. In the context of truck spare parts, tighter tolerances are often necessary for components that require precise fit and function, such as engine parts or brake systems. Knowing the tolerance specifications helps ensure that parts will fit correctly and function as intended, which is essential for safety and reliability in operations.
3. Finish
The finish of a spare part refers to the surface quality and treatment applied to it, such as painting, galvanizing, or anodizing. A proper finish not only enhances aesthetic appeal but also protects against corrosion and wear. For international buyers, understanding the finish specifications is essential, especially in regions with extreme weather conditions, as it can significantly impact the longevity of the parts.
4. Compatibility
Compatibility indicates whether a spare part can function correctly with existing systems or other components. This is particularly important when sourcing parts for specific truck models or brands. B2B buyers should verify compatibility with manufacturers’ specifications to avoid costly mismatches that could lead to operational downtime.
5. Load Capacity
Load capacity is a critical specification that indicates the maximum weight a part can safely support or carry. This is especially relevant for components like axles, suspensions, and brakes. Understanding load capacity helps buyers select the right parts that meet the demands of their operational requirements, thereby ensuring safety and efficiency in their fleet operations.
What Are Common Trade Terms Used in the Truck Spare Parts Industry?
1. OEM (Original Equipment Manufacturer)
OEM refers to manufacturers who produce parts that are used in the original assembly of vehicles. When sourcing truck spare parts, understanding whether a part is OEM or aftermarket can influence quality and compatibility. OEM parts are typically more reliable and come with warranties, making them a preferred choice for many buyers.
2. MOQ (Minimum Order Quantity)
MOQ is the smallest number of units a supplier is willing to sell at one time. This term is crucial for B2B buyers as it affects inventory management and cash flow. Buyers should negotiate MOQs that align with their purchasing capacity and storage capabilities, especially when dealing with international suppliers.
3. RFQ (Request for Quotation)
An RFQ is a formal process where buyers request price quotes from suppliers for specific products or services. This term is essential for establishing clear communication and ensuring that buyers receive competitive pricing. B2B buyers should provide detailed specifications in their RFQs to receive accurate quotes.
4. Incoterms (International Commercial Terms)
Incoterms are standardized trade terms that define the responsibilities of buyers and sellers in international transactions. Familiarity with Incoterms, such as FOB (Free on Board) or CIF (Cost, Insurance, and Freight), is critical for understanding shipping costs, risk, and logistics responsibilities. Proper knowledge of Incoterms can help buyers negotiate better terms and manage international logistics more effectively.
5. Lead Time
Lead time refers to the time it takes from placing an order until the delivery of the goods. Understanding lead times is crucial for inventory planning and operational efficiency. B2B buyers should factor in lead times when scheduling maintenance or repairs to minimize downtime.
By familiarizing themselves with these technical properties and trade terms, international B2B buyers can make more informed decisions when sourcing truck spare parts, ultimately enhancing their operational efficiency and reducing costs.
Navigating Market Dynamics and Sourcing Trends in the truck spare parts supplier Sector
What Are the Current Market Dynamics and Key Trends in the Truck Spare Parts Supplier Sector?
The truck spare parts supplier sector is experiencing significant transformation driven by globalization, technological advancements, and evolving buyer preferences. One of the primary global drivers is the increasing demand for efficient logistics and transportation, particularly in emerging markets across Africa and South America. This demand is spurred by urbanization and industrial growth, leading to a surge in the number of commercial vehicles on the road. Consequently, international B2B buyers are actively seeking reliable suppliers who can provide high-quality parts at competitive prices.
Technological advancements are reshaping the sourcing landscape, with e-commerce platforms and digital marketplaces emerging as vital tools for procurement. These platforms facilitate easier comparisons of products, enabling buyers from Europe and the Middle East to source parts from diverse suppliers worldwide. Additionally, the rise of data analytics and IoT (Internet of Things) is enabling suppliers to offer predictive maintenance solutions, which can reduce downtime and improve operational efficiency for truck operators.
Moreover, sustainability and cost-efficiency are becoming increasingly important. Buyers are now prioritizing suppliers that demonstrate innovative practices in inventory management, reducing lead times and holding costs. Understanding these trends is crucial for B2B buyers looking to navigate the complexities of the truck spare parts market effectively.
How Is Sustainability and Ethical Sourcing Shaping the Truck Spare Parts Industry?
Sustainability has become a central theme in the truck spare parts supplier sector, driven by increasing environmental awareness and regulatory pressures. The environmental impact of manufacturing and sourcing practices is under scrutiny, compelling suppliers to adopt greener alternatives. International B2B buyers are increasingly favoring suppliers who can demonstrate a commitment to sustainability through responsible sourcing and production methods.
Ethical supply chains are also gaining traction. Buyers are seeking suppliers who adhere to fair labor practices and transparency in their operations. Certifications such as ISO 14001 (Environmental Management) and ISO 45001 (Occupational Health and Safety) are becoming prerequisites for doing business in many regions. Suppliers that utilize recycled materials or eco-friendly components can enhance their appeal to conscientious buyers, particularly in Europe, where regulations around sustainability are stringent.
For B2B buyers in Africa, South America, and the Middle East, establishing partnerships with suppliers committed to sustainability can not only mitigate risks associated with supply chain disruptions but also enhance brand reputation. As consumers increasingly demand eco-friendly products, aligning with sustainable suppliers can provide a competitive edge.
What Is the Evolution of the Truck Spare Parts Supplier Sector?
The truck spare parts supplier sector has evolved significantly over the past few decades, transitioning from traditional supply chains to more integrated and technologically advanced systems. Initially characterized by fragmented local suppliers, the industry has seen a consolidation trend, with larger companies acquiring smaller players to enhance their market presence and operational efficiency.
The introduction of e-commerce has further revolutionized sourcing processes, enabling buyers to access a global marketplace. This shift has been especially pronounced in regions like Europe and the Middle East, where digital procurement is becoming the norm. As the industry continues to adapt, the emphasis on sustainability and ethical sourcing will likely shape its future trajectory, ensuring that buyers are not only obtaining quality products but also contributing to a more sustainable global economy.
In conclusion, understanding these market dynamics and sourcing trends is essential for international B2B buyers in the truck spare parts supplier sector. By leveraging technology, prioritizing sustainability, and adapting to evolving market conditions, buyers can make informed purchasing decisions that align with their operational goals.
Frequently Asked Questions (FAQs) for B2B Buyers of truck spare parts supplier
-
How do I ensure the quality of truck spare parts from international suppliers?
To ensure quality, start by conducting thorough due diligence on potential suppliers. Request samples to assess the quality of the parts and verify certifications, such as ISO or other relevant standards. It’s also advisable to read reviews and testimonials from other clients, particularly those in similar markets. Establishing a clear quality assurance (QA) process, including inspections and testing before shipment, can further mitigate risks associated with subpar products. -
What are the best practices for vetting truck spare parts suppliers?
Vetting suppliers involves checking their reputation, experience, and reliability. Request references from past clients and verify their business credentials. Conduct site visits if possible, or utilize third-party inspection services. Evaluate their production capabilities and lead times to ensure they can meet your demands. Additionally, consider their compliance with international trade regulations and their ability to provide after-sales support. -
How can I negotiate favorable payment terms with a truck spare parts supplier?
Negotiating payment terms starts with understanding the supplier’s policies and the risks they face. Propose terms that are mutually beneficial, such as partial upfront payments and the remainder upon delivery. Consider using letters of credit or escrow services to protect both parties. Building a strong relationship with the supplier can also facilitate better terms, as trust and reliability can lead to more favorable negotiations. -
What is the minimum order quantity (MOQ) when sourcing truck spare parts?
The MOQ can vary significantly between suppliers and depends on the type of parts being ordered. It’s essential to discuss your specific needs with potential suppliers upfront. Some may offer flexibility on MOQs for first-time buyers or bulk orders. If the MOQ is higher than your current needs, consider discussing a phased approach or grouping orders with other buyers to meet the supplier’s requirements. -
How do I handle logistics when importing truck spare parts internationally?
Effective logistics management involves selecting the right shipping methods, understanding import regulations, and working with reliable freight forwarders. Create a detailed shipping plan that includes timelines, costs, and customs documentation. Familiarize yourself with the import duties and taxes applicable in your country to avoid unexpected expenses. Lastly, maintain open communication with your supplier throughout the shipping process to ensure timely deliveries. -
What factors should I consider when customizing truck spare parts?
When looking to customize truck spare parts, consider the specific requirements of your fleet and the compatibility with existing vehicles. Discuss customization options with your supplier, including material choices, dimensions, and design specifications. Be aware of the lead times for custom parts and ensure that the supplier has the necessary capabilities and experience. Additionally, factor in the potential costs associated with customization. -
How can I assess the reliability of a supplier in the truck spare parts industry?
Assessing supplier reliability involves reviewing their track record, including delivery timelines and quality consistency. Look for suppliers with a long-standing presence in the industry and positive feedback from other international buyers. Utilize platforms that provide supplier ratings and audits. Additionally, engage in direct communication to gauge their responsiveness and willingness to address your concerns, which can be indicative of their overall reliability. -
What are the common pitfalls to avoid when sourcing truck spare parts?
Common pitfalls include failing to verify the supplier’s credentials, not conducting sufficient market research, and overlooking the importance of contracts. Avoid making decisions based solely on price, as this can lead to quality issues. Ensure that all agreements are documented to protect your interests. Additionally, be cautious of suppliers who are unwilling to provide references or transparent information about their operations, as this may indicate potential risks.
Important Disclaimer & Terms of Use
⚠️ Important Disclaimer
The information provided in this guide, including content regarding manufacturers, technical specifications, and market analysis, is for informational and educational purposes only. It does not constitute professional procurement advice, financial advice, or legal advice.
While we have made every effort to ensure the accuracy and timeliness of the information, we are not responsible for any errors, omissions, or outdated information. Market conditions, company details, and technical standards are subject to change.
B2B buyers must conduct their own independent and thorough due diligence before making any purchasing decisions. This includes contacting suppliers directly, verifying certifications, requesting samples, and seeking professional consultation. The risk of relying on any information in this guide is borne solely by the reader.
Strategic Sourcing Conclusion and Outlook for truck spare parts supplier
What Are the Key Takeaways for B2B Buyers in the Truck Spare Parts Market?
In the competitive landscape of truck spare parts sourcing, international buyers must prioritize strategic sourcing to ensure cost efficiency, quality assurance, and timely delivery. Understanding local regulations, market trends, and supplier capabilities in regions such as Africa, South America, the Middle East, and Europe is crucial. Engaging in long-term partnerships with reliable suppliers can significantly enhance operational resilience and reduce lead times, thereby optimizing your supply chain.
How Can Strategic Sourcing Enhance Your Procurement Process?
Strategic sourcing not only streamlines procurement but also fosters innovation through collaboration with suppliers. By leveraging data analytics and market intelligence, businesses can make informed decisions that align with their operational goals. It is essential for buyers to continuously assess their supplier networks, adapting to changes in demand and exploring new technologies that can improve efficiency.
What Should International Buyers Focus on for Future Success?
As the truck spare parts market evolves, buyers should focus on sustainability and digital transformation in their sourcing strategies. Embracing eco-friendly practices and investing in digital tools will not only enhance brand reputation but also meet the increasing consumer demand for responsible business practices.
In conclusion, the future of truck spare parts sourcing is promising for international buyers willing to embrace strategic sourcing. By staying informed, adapting to market changes, and fostering strong supplier relationships, businesses can navigate the complexities of the global supply chain successfully. Now is the time to take action—evaluate your current sourcing strategies and align them with the insights provided to drive sustainable growth and competitive advantage in your markets.