Discover Top Gas Compressor Suppliers: Your 2025 Guide
Introduction: Navigating the Global Market for gas compressor supplier
In the intricate landscape of global commerce, sourcing a reliable gas compressor supplier can pose significant challenges for international B2B buyers. The demand for high-performance gas compressors is surging, driven by industries such as oil and gas, manufacturing, and energy production. Buyers must navigate a plethora of options while ensuring they select suppliers who not only meet their technical specifications but also align with their operational needs and budget constraints. This guide serves as a comprehensive resource, demystifying the complexities of the gas compressor market.
Throughout this guide, you will explore various types of gas compressors, their applications across diverse sectors, and the critical factors to consider when vetting suppliers. We delve into the nuances of cost structures and provide insights on how to negotiate favorable terms. By equipping B2B buyers from regions such as Africa, South America, the Middle East, and Europe with actionable insights, this guide empowers you to make informed purchasing decisions. Whether you are a buyer in Indonesia seeking to enhance operational efficiency or a procurement manager in Argentina looking for cost-effective solutions, the information presented here will enable you to navigate the global market with confidence and clarity.
Understanding gas compressor supplier Types and Variations
Type Name | Key Distinguishing Features | Primary B2B Applications | Brief Pros & Cons for Buyers |
---|---|---|---|
Positive Displacement Compressors | Consistently delivers a fixed volume of gas per cycle | Oil & gas, chemical processing | Pros: High efficiency; Cons: Limited flow rates. |
Dynamic Compressors | Uses kinetic energy to compress gas | HVAC systems, refrigeration | Pros: High flow rates; Cons: Less efficient at low flow. |
Reciprocating Compressors | Uses pistons driven by a crankshaft | Natural gas extraction, industrial uses | Pros: Versatile; Cons: Higher maintenance needs. |
Rotary Screw Compressors | Continuous operation with twin rotating screws | Manufacturing, pneumatic tools | Pros: Low maintenance; Cons: Higher initial cost. |
Centrifugal Compressors | Employs a rotating disk to increase gas velocity | Power generation, large-scale applications | Pros: High efficiency for large volumes; Cons: Expensive installation. |
What are Positive Displacement Compressors and When Should B2B Buyers Consider Them?
Positive displacement compressors are characterized by their ability to deliver a fixed volume of gas per cycle, making them ideal for applications requiring consistent pressure. They are commonly used in oil and gas, as well as chemical processing industries. When considering a positive displacement compressor, buyers should evaluate the specific flow rate requirements and the importance of energy efficiency, as these compressors excel in low-flow applications but can be less efficient at higher rates.
How Do Dynamic Compressors Function and What Are Their Advantages for B2B Buyers?
Dynamic compressors operate by imparting kinetic energy to the gas, allowing for high flow rates, which makes them suitable for HVAC systems and refrigeration applications. Their ability to maintain performance across varying flow conditions can be a significant advantage for B2B buyers looking for flexibility. However, it’s essential to consider that while they offer high efficiency at peak performance, they may not be as efficient at lower flow rates, which could affect operational costs.
What Are the Key Features of Reciprocating Compressors for Industrial Use?
Reciprocating compressors utilize pistons driven by a crankshaft to compress gas, making them highly versatile for various industrial applications, including natural gas extraction. They are well-suited for B2B buyers needing reliable performance in fluctuating demand scenarios. However, potential buyers should be aware of the higher maintenance requirements and possible wear and tear, which can impact long-term operational costs.
Why Choose Rotary Screw Compressors for Manufacturing Applications?
Rotary screw compressors are designed for continuous operation, featuring twin rotating screws that compress gas efficiently. They are particularly popular in manufacturing and pneumatic tool applications due to their low maintenance needs and reliability. B2B buyers should consider the initial investment cost, as rotary screw compressors typically require a higher upfront expenditure but can result in lower operational costs over time.
What Benefits Do Centrifugal Compressors Offer for Large-Scale Applications?
Centrifugal compressors use a rotating disk to increase the velocity of gas, making them suitable for large-scale applications, such as power generation. Their high efficiency in handling large volumes is a significant benefit for B2B buyers engaged in expansive operations. However, the installation costs can be substantial, so it’s crucial for buyers to assess their long-term needs and budget constraints before making a decision.
Related Video: Natural Gas Compressor Station Intro and Overview [Oil & Gas Training Basics]
Key Industrial Applications of gas compressor supplier
Industry/Sector | Specific Application of Gas Compressor Supplier | Value/Benefit for the Business | Key Sourcing Considerations for this Application |
---|---|---|---|
Oil and Gas | Natural Gas Processing | Enhances gas extraction efficiency and reduces losses | Look for suppliers with expertise in high-pressure systems and certifications for safety standards. |
Manufacturing | Pneumatic Equipment Operation | Increases production efficiency and operational reliability | Ensure compatibility with existing systems and assess energy consumption rates. |
Food and Beverage | Refrigeration and Cooling Systems | Preserves product quality and extends shelf life | Consider suppliers who offer energy-efficient models that comply with food safety regulations. |
Chemical Processing | Gas Transportation and Compression | Facilitates safe and efficient transport of gases | Evaluate suppliers based on their ability to provide customized solutions and technical support. |
Mining and Minerals | Ventilation Systems | Ensures worker safety and compliance with environmental regulations | Source from suppliers with proven track records in harsh environments and robust service agreements. |
How are Gas Compressors Used in the Oil and Gas Industry?
In the oil and gas sector, gas compressors are crucial for natural gas processing. They enhance the extraction efficiency by compressing natural gas for transportation through pipelines. This application solves problems related to gas losses and ensures the safe transfer of hydrocarbons. International buyers, particularly from Africa and the Middle East, should prioritize suppliers with expertise in high-pressure systems and safety certifications, as these are essential for compliance with local regulations and operational safety.
What Role Do Gas Compressors Play in Manufacturing?
Gas compressors are widely used in manufacturing for operating pneumatic equipment. By providing the necessary pressure for tools and machinery, they significantly increase production efficiency and reliability. This application is particularly vital for manufacturers in South America and Europe, where energy costs can impact overall profitability. Buyers should ensure that the compressors are compatible with their existing systems and evaluate energy consumption rates to optimize operational costs.
How Do Gas Compressors Benefit the Food and Beverage Industry?
In the food and beverage sector, gas compressors support refrigeration and cooling systems, which are essential for preserving product quality and extending shelf life. This application is critical in regions like Europe and Africa, where maintaining food safety standards is paramount. Buyers should consider suppliers that offer energy-efficient models compliant with food safety regulations to reduce operational costs while ensuring product integrity.
What Are the Applications of Gas Compressors in Chemical Processing?
In chemical processing, gas compressors facilitate the transportation and compression of gases, ensuring safe and efficient operations. This is particularly important for industries in South America and the Middle East, where the safe handling of chemicals is crucial. Buyers should evaluate suppliers based on their ability to provide customized solutions and technical support, as well as their experience in dealing with various gas types and pressures.
How Are Gas Compressors Used in Mining and Minerals?
In the mining and minerals industry, gas compressors are integral to ventilation systems, ensuring adequate airflow in underground operations. This application is vital for worker safety and compliance with environmental regulations, especially in regions like Africa and South America. Buyers should source from suppliers with a proven track record in harsh environments and robust service agreements to ensure reliability and support in critical operations.
Related Video: How a Centrifugal Gas Compressor Works
3 Common User Pain Points for ‘gas compressor supplier’ & Their Solutions
Scenario 1: Struggling with Equipment Reliability and Downtime
The Problem: B2B buyers often face significant challenges with the reliability of gas compressors. Frequent breakdowns can lead to extended downtime, disrupting operations and causing financial losses. For example, a manufacturing plant in South America relying on gas compressors for their production process may experience delays in output, loss of revenue, and increased operational costs due to the need for emergency repairs and replacements. This scenario is particularly concerning for industries where continuous operation is critical, such as oil and gas or chemical processing.
The Solution: To mitigate the risk of equipment failure, buyers should prioritize sourcing compressors from reputable suppliers with a proven track record of reliability. Conduct thorough due diligence by requesting references and performance data from current users. When selecting a gas compressor, ensure that it meets the specific operational demands of your application, including pressure requirements and duty cycle. Additionally, consider investing in predictive maintenance tools that utilize IoT technology to monitor compressor performance in real-time. This proactive approach can help identify potential issues before they escalate, allowing for scheduled maintenance rather than reactive repairs.
Scenario 2: Navigating Complex Regulatory Compliance
The Problem: International buyers often encounter challenges with regulatory compliance related to gas compressor installations, particularly when operating in multiple regions with varying standards. For example, a gas compression project in the Middle East may need to adhere to strict environmental regulations, safety standards, and local certifications that differ significantly from those in Europe. Failure to comply can lead to hefty fines, project delays, and reputational damage.
The Solution: To effectively navigate these complexities, buyers should partner with a gas compressor supplier that has extensive knowledge of local regulations and compliance requirements. Engage with suppliers who can provide guidance on necessary certifications and documentation for your specific region. Additionally, consider working with local consultants who specialize in regulatory compliance to ensure that all aspects of the installation meet legal standards. Establishing a strong relationship with your supplier can also facilitate a smoother approval process by ensuring that all equipment meets the required specifications before it arrives on-site.
Scenario 3: Difficulty in Sizing and Selecting the Right Compressor
The Problem: Selecting the appropriate gas compressor can be a daunting task, particularly for buyers unfamiliar with the technical specifications required for their operations. A common pain point arises when companies either overestimate their needs and invest in oversized compressors, leading to unnecessary costs, or underestimate their requirements, resulting in inefficiencies and inadequate performance. For instance, a business in Africa may choose a smaller compressor to save costs, only to find that it cannot handle peak production demands.
The Solution: To avoid the pitfalls of improper sizing, B2B buyers should engage in a comprehensive needs assessment before making a purchase. This includes evaluating the specific application requirements, understanding the gas composition, and analyzing expected flow rates and pressure needs. Collaborate closely with your supplier to leverage their expertise in selecting the right compressor based on your unique operational parameters. Request detailed performance curves and operational data to better understand how different models will perform under various conditions. Additionally, consider future scalability in your decision-making to ensure that the compressor can accommodate potential growth without requiring immediate replacement.
Strategic Material Selection Guide for gas compressor supplier
When selecting materials for gas compressors, international B2B buyers must consider various factors that influence performance, durability, and cost. Here, we analyze four common materials used in gas compressor construction: carbon steel, stainless steel, aluminum, and composite materials. Each material has unique properties and implications for specific applications, particularly in diverse markets such as Africa, South America, the Middle East, and Europe.
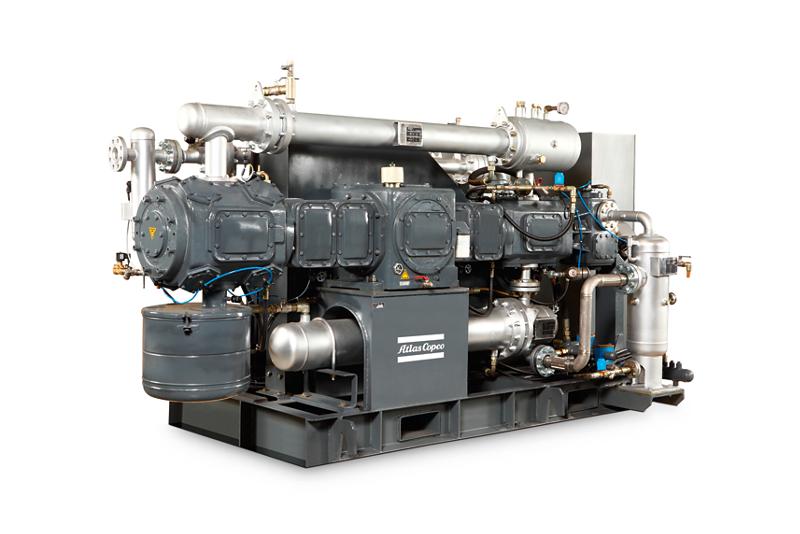
A stock image related to gas compressor supplier.
What Are the Key Properties of Carbon Steel in Gas Compressors?
Carbon steel is a widely used material in gas compressor manufacturing due to its excellent mechanical properties and cost-effectiveness. It typically offers good strength and durability, making it suitable for high-pressure applications. Carbon steel can withstand temperatures up to 400°F (204°C) and has a moderate level of corrosion resistance, which can be enhanced with protective coatings.
Pros & Cons: While carbon steel is relatively inexpensive and easy to machine, it is susceptible to corrosion, especially in humid or corrosive environments. This limitation may require additional maintenance or protective measures, which could increase overall operational costs.
Impact on Application: Carbon steel is compatible with various gases, but its corrosion vulnerability makes it less suitable for applications involving aggressive media, such as sour gas or corrosive chemicals.
Considerations for International Buyers: Buyers from regions like Africa and South America should ensure compliance with local standards such as ASTM A106 or ASTM A53 for carbon steel pipes. Understanding local climatic conditions can also inform the need for additional protective measures.
How Does Stainless Steel Enhance Performance in Gas Compressors?
Stainless steel is known for its superior corrosion resistance and strength, making it an ideal choice for gas compressors operating in harsh environments. It can handle temperatures exceeding 1000°F (538°C) and maintains structural integrity under high pressure. Its resistance to oxidation and scaling is particularly beneficial in applications involving wet or corrosive gases.
Pros & Cons: The primary advantage of stainless steel is its longevity and reduced maintenance needs. However, it is more expensive than carbon steel and can be more challenging to machine, which may increase manufacturing complexity.
Impact on Application: Stainless steel is highly compatible with a wide range of gases, including those that are corrosive or reactive, making it suitable for diverse applications, from oil and gas to chemical processing.
Considerations for International Buyers: Buyers should be aware of standards such as ASTM A312 for stainless steel pipes. In regions with stringent environmental regulations, such as Europe, stainless steel may be preferred for its sustainability and lower lifecycle costs.
What Are the Benefits of Using Aluminum in Gas Compressors?
Aluminum is increasingly being utilized in gas compressor applications due to its lightweight nature and good corrosion resistance. It can operate effectively at temperatures up to 300°F (149°C) and is often used in applications where weight reduction is a priority, such as mobile or portable compressors.
Pros & Cons: The lightweight characteristic of aluminum allows for easier installation and reduced energy consumption during operation. However, its lower strength compared to steel means it may not be suitable for high-pressure applications, limiting its use in specific sectors.
Impact on Application: Aluminum is compatible with a variety of gases but may not perform well in high-pressure environments. It is often used in applications where portability and ease of handling are essential.
Considerations for International Buyers: Buyers should consider compliance with standards such as ASTM B221 for aluminum extrusions. In regions like the Middle East, where temperatures can be extreme, understanding the thermal properties of aluminum is crucial.
How Do Composite Materials Offer Versatility in Gas Compressors?
Composite materials, often made from a combination of resins and fibers, are gaining traction in gas compressor design due to their lightweight and high-strength properties. They can operate effectively at moderate temperatures and pressures, making them suitable for specific applications.
Pros & Cons: The main advantage of composites is their resistance to corrosion and chemical attack, which extends the lifespan of the equipment. However, they can be more expensive and complex to manufacture, which may deter some buyers.
Impact on Application: Composites are particularly advantageous in applications involving corrosive gases, where traditional materials may fail. Their lightweight nature also makes them ideal for portable compressor designs.
Considerations for International Buyers: Buyers should investigate local regulations regarding composite materials and ensure compliance with relevant standards. In Europe, for instance, adherence to EN standards may be necessary.
Summary Table of Material Selection for Gas Compressors
Material | Typical Use Case for gas compressor supplier | Key Advantage | Key Disadvantage/Limitation | Relative Cost (Low/Med/High) |
---|---|---|---|---|
Carbon Steel | Standard industrial applications | Cost-effective and durable | Susceptible to corrosion | Low |
Stainless Steel | Corrosive and high-temperature environments | Superior corrosion resistance | Higher cost and machining complexity | High |
Aluminum | Portable and lightweight applications | Lightweight and easy to handle | Lower strength limits applications | Medium |
Composite | Corrosive gas applications | Excellent corrosion resistance | Higher manufacturing complexity | High |
This strategic material selection guide provides international B2B buyers with actionable insights to make informed decisions when sourcing gas compressors. Understanding the properties, advantages, and limitations of each material is essential for optimizing performance and ensuring compliance with regional standards.
In-depth Look: Manufacturing Processes and Quality Assurance for gas compressor supplier
What Are the Key Stages in the Manufacturing Process of Gas Compressors?
The manufacturing process of gas compressors involves several critical stages, each designed to ensure high performance and reliability. Understanding these stages can help B2B buyers identify the capabilities of potential suppliers.
-
Material Preparation
The first step involves sourcing high-quality materials such as stainless steel, aluminum, or specialized alloys. The choice of material directly impacts the compressor’s durability and efficiency. Suppliers should conduct rigorous material inspections to verify compliance with international standards. Buyers should request documentation proving the material specifications and certifications. -
Forming Techniques
This stage encompasses various techniques such as machining, welding, and casting. Advanced CNC (Computer Numerical Control) machining is often employed to achieve precise dimensions and tolerances. Other forming methods may include die casting for complex shapes. Buyers should inquire about the technologies used and the skills of the workforce to ensure high-quality outcomes. -
Assembly Process
The assembly of gas compressors is critical, as it combines all components into a functional unit. Skilled technicians usually perform this step, following detailed assembly instructions. Automated assembly lines may be utilized for efficiency, but manual assembly is often preferred for complex or high-value components. Buyers should assess whether the assembly process includes thorough checks for alignment and fit. -
Finishing Techniques
After assembly, compressors undergo finishing processes such as surface treatment, painting, and coating. These processes not only enhance the aesthetic appeal but also protect against corrosion and wear. Buyers should ensure that finishing methods are appropriate for the operational environment of the compressor, especially in harsh conditions typical in regions like Africa and the Middle East.
How Is Quality Assurance Implemented in Gas Compressor Manufacturing?
Quality assurance (QA) is vital for ensuring that gas compressors meet performance standards and regulatory requirements. B2B buyers should familiarize themselves with the key QA processes used by suppliers.
-
International Standards for Quality Control
Many gas compressor suppliers adhere to international standards such as ISO 9001, which focuses on quality management systems. Compliance with these standards indicates a commitment to quality and continuous improvement. Other relevant certifications include CE marking for compliance with European safety standards and API (American Petroleum Institute) certifications for oil and gas applications. -
Quality Control Checkpoints
Quality control is typically integrated into various stages of the manufacturing process, involving several checkpoints:
– Incoming Quality Control (IQC): This involves inspecting raw materials upon arrival to ensure they meet specified standards.
– In-Process Quality Control (IPQC): Continuous monitoring during the manufacturing process helps identify any deviations from quality standards.
– Final Quality Control (FQC): A comprehensive assessment of the finished product, including performance testing and compliance verification. -
Common Testing Methods for Gas Compressors
Various testing methods are employed to ensure functionality and safety. These may include:
– Pressure Testing: To verify the integrity of the compressor under operational conditions.
– Vibration Analysis: To detect any irregularities that could indicate potential failures.
– Performance Testing: To ensure the compressor meets specified output and efficiency metrics.
How Can B2B Buyers Verify Supplier Quality Control?
For international buyers, verifying the quality control processes of potential suppliers is crucial for mitigating risks. Here are actionable steps to ensure comprehensive evaluation:
-
Conduct Supplier Audits
Regular audits of suppliers can provide insights into their quality management systems and manufacturing processes. Buyers should request access to audit reports and findings to assess compliance with international standards. -
Request Quality Assurance Documentation
Suppliers should provide documentation regarding their quality control processes, including inspection reports, test results, and certifications. This information can help buyers evaluate the reliability of the supplier. -
Engage Third-Party Inspectors
Independent third-party inspections can provide an unbiased assessment of the supplier’s quality practices. This can be especially beneficial for buyers from regions like Africa and South America, where local regulations may differ significantly from international standards.
What Are the Quality Control Nuances for International B2B Buyers?
International buyers need to navigate various nuances related to quality control when sourcing gas compressors:
-
Understanding Regional Standards
Different regions may have unique compliance requirements. For instance, while CE marking is essential for European markets, other regions may prioritize ISO certifications. Buyers should be aware of these variations and ensure that suppliers comply with relevant local regulations. -
Cultural and Communication Considerations
Cultural differences may influence how quality control is perceived and implemented. Buyers should foster open communication with suppliers to clarify expectations regarding quality standards and compliance. This can help bridge any gaps that may arise from differing practices. -
Supply Chain Transparency
A transparent supply chain is crucial for ensuring quality at every stage. Buyers should seek suppliers who are willing to share information about their sourcing practices, sub-suppliers, and the overall manufacturing process. This transparency can enhance trust and accountability.
By understanding the intricacies of the manufacturing processes and quality assurance practices, B2B buyers from Africa, South America, the Middle East, and Europe can make informed decisions when selecting gas compressor suppliers. This knowledge not only aids in risk management but also fosters long-term partnerships built on quality and reliability.
Practical Sourcing Guide: A Step-by-Step Checklist for ‘gas compressor supplier’
Introduction
Sourcing a reliable gas compressor supplier is critical for businesses aiming to enhance operational efficiency and reduce costs. This guide offers a step-by-step checklist to help international B2B buyers, particularly from Africa, South America, the Middle East, and Europe, navigate the procurement process effectively. By following these steps, buyers can ensure they select a supplier that meets their technical, financial, and logistical requirements.
Step 1: Define Your Technical Specifications
Before engaging suppliers, clearly outline your technical requirements. This includes the type of gas compressor needed, capacity, pressure ratings, and any specific features or certifications.
– What to consider: Ensure your specifications align with your operational needs and regulatory standards in your region.
Step 2: Research and Identify Potential Suppliers
Conduct thorough research to compile a list of potential gas compressor suppliers. Utilize online platforms, industry trade shows, and referrals from trusted industry contacts.
– Where to look: Websites like Alibaba, ThomasNet, or industry-specific directories can provide a wealth of options.
Step 3: Evaluate Supplier Credentials and Experience
Before committing, it’s crucial to vet suppliers thoroughly. Review their company profiles, years in business, and case studies relevant to your industry.
– Key aspects: Look for suppliers with a proven track record in your specific application and region. Request references from similar businesses to gauge their reliability.
Step 4: Verify Supplier Certifications
Ensure that potential suppliers hold the necessary certifications, such as ISO standards or local compliance certifications. This step is vital for ensuring product quality and safety.
– Why it matters: Valid certifications indicate adherence to industry standards and can prevent costly compliance issues down the line.
Step 5: Assess Pricing and Payment Terms
Analyze the pricing structure of each supplier, including upfront costs, maintenance fees, and potential hidden charges.
– Important considerations: Negotiate payment terms that align with your cash flow needs, such as installment plans or early payment discounts.
Step 6: Request Samples or Demonstrations
Whenever possible, request samples or demonstrations of the gas compressors. This allows you to assess the quality and performance firsthand before making a larger commitment.
– What to observe: Pay attention to the compressor’s efficiency, noise levels, and ease of use during the demonstration.
Step 7: Review Logistics and Support Services
Finally, evaluate the supplier’s logistics capabilities and after-sales support. Consider their delivery timelines, installation assistance, and availability of spare parts.
– Why this is crucial: Reliable logistics and robust support services can significantly minimize downtime and ensure smooth operations post-purchase.
By following this checklist, B2B buyers can make informed decisions when sourcing gas compressor suppliers, fostering successful partnerships that enhance operational performance.
Comprehensive Cost and Pricing Analysis for gas compressor supplier Sourcing
Understanding the cost structure and pricing dynamics of gas compressor suppliers is crucial for international B2B buyers, particularly those operating in diverse regions such as Africa, South America, the Middle East, and Europe. This analysis breaks down the key components of costs and factors influencing pricing, along with actionable tips for effective procurement.
What Are the Key Cost Components for Gas Compressors?
-
Materials: The primary cost driver in gas compressor manufacturing is the raw materials, including metals like steel and aluminum, as well as specialized components such as seals and gaskets. Fluctuations in the prices of these materials can significantly impact the overall cost.
-
Labor: Labor costs vary by region and can include both skilled and unskilled workers involved in assembly, testing, and quality control. Countries with higher wage standards will typically see increased labor costs, affecting the final price of the compressors.
-
Manufacturing Overhead: This includes costs related to factory maintenance, utilities, and administrative expenses. Efficient production processes can help mitigate overhead costs, leading to competitive pricing.
-
Tooling: Tooling refers to the investment in equipment and molds required for manufacturing specific components of gas compressors. These costs are typically amortized over production volumes, meaning higher initial tooling costs can be offset by larger order quantities.
-
Quality Control (QC): Ensuring the reliability and performance of gas compressors necessitates rigorous quality control processes. These processes add to the overall cost but are essential for maintaining high standards and securing necessary certifications.
-
Logistics: The costs associated with transporting compressors from the manufacturing facility to the buyer’s location can vary significantly. Factors such as distance, shipping method, and local tariffs play a critical role in determining logistics costs.
-
Margin: Suppliers typically add a profit margin to cover their expenses and provide a return on investment. Understanding the standard margins within the industry can help buyers assess the fairness of a supplier’s pricing.
What Influences the Pricing of Gas Compressors?
-
Volume and Minimum Order Quantity (MOQ): Larger orders often lead to better pricing per unit due to economies of scale. Buyers should consider negotiating MOQs to optimize costs.
-
Specifications and Customization: Custom-built compressors may incur additional costs due to specialized design and engineering efforts. Clear communication of requirements can help manage expectations and costs.
-
Material Quality and Certifications: Higher-quality materials and necessary certifications (e.g., ISO, API) can increase costs but may also enhance reliability and performance. Buyers should evaluate the trade-off between initial costs and long-term performance.
-
Supplier Factors: The reputation and reliability of a supplier can influence pricing. Established suppliers may command higher prices due to their proven track record, while new entrants might offer lower prices to attract buyers.
-
Incoterms: The choice of Incoterms (International Commercial Terms) affects the distribution of costs and responsibilities between buyers and sellers. Understanding these terms can help buyers avoid unexpected expenses.
What Are the Best Practices for Negotiating Prices?
-
Leverage Total Cost of Ownership (TCO): When evaluating suppliers, consider the TCO rather than just the upfront price. This includes maintenance, operational costs, and potential downtime.
-
Research Market Trends: Stay informed about market conditions, including material prices and supply chain dynamics, to negotiate effectively.
-
Build Long-term Relationships: Establishing a strong relationship with suppliers can lead to better pricing and terms over time. Loyalty often results in discounts and prioritized service.
-
Be Prepared to Walk Away: If negotiations are not yielding favorable results, be willing to explore other suppliers. This not only gives you leverage but also encourages suppliers to be more competitive.
-
Understand Regional Nuances: Buyers from Africa, South America, the Middle East, and Europe should be aware of regional factors that may influence pricing, such as local economic conditions, import duties, and logistical challenges.
Disclaimer on Indicative Prices
Prices for gas compressors can vary widely based on specifications, supplier, and market conditions. It is advisable for buyers to obtain multiple quotes and conduct thorough due diligence to ensure the best value for their specific needs.
Alternatives Analysis: Comparing gas compressor supplier With Other Solutions
Understanding the Importance of Alternative Solutions
When considering gas compressors for industrial applications, it’s essential for B2B buyers to explore various alternatives. Different technologies can achieve similar goals, often with unique advantages that may align better with specific operational needs or budgets. This analysis will compare traditional gas compressor suppliers with two viable alternatives: Scroll Compressors and Centrifugal Compressors.
Comparison Table of Gas Compressor Solutions
Comparison Aspect | Gas Compressor Supplier | Scroll Compressors | Centrifugal Compressors |
---|---|---|---|
Performance | High efficiency; good for varied pressures | Moderate efficiency; best for low to medium flow rates | High efficiency; excellent for high flow rates |
Cost | Medium to high initial investment | Lower initial cost; generally more affordable | High initial investment; operational costs can vary |
Ease of Implementation | Requires skilled installation | Easier to install; compact design | Complex installation; requires significant space |
Maintenance | Regular maintenance needed; skilled personnel required | Low maintenance; fewer moving parts | Moderate maintenance; skilled personnel may be needed |
Best Use Case | Industrial applications with varying demands | Applications with consistent low to medium pressure needs | Large-scale operations needing high volume and continuous operation |
What Are the Advantages and Disadvantages of Scroll Compressors?
Scroll Compressors are an excellent alternative for industries with consistent, low to medium pressure requirements. They are quieter, have fewer moving parts, and are less prone to wear, which leads to lower maintenance costs. Their compact design allows for easier installation in limited spaces. However, they may not perform well in applications requiring high-pressure variations or extreme flow rates, limiting their versatility compared to traditional gas compressors.
How Do Centrifugal Compressors Compare?
Centrifugal Compressors excel in applications requiring high flow rates and consistent pressure. They are particularly beneficial for large-scale operations in sectors such as oil and gas or chemical processing. Their efficiency at high volumes can lead to lower operational costs over time. However, the initial investment is substantial, and their installation can be complex, requiring ample space and skilled labor. Additionally, maintenance can be moderate to high depending on the operational environment, necessitating a trained workforce.
How Can B2B Buyers Choose the Right Solution?
Selecting the appropriate solution depends on several factors, including the specific application, budget constraints, and operational requirements. B2B buyers should assess their pressure and flow rate needs, evaluate the total cost of ownership—including installation and maintenance—and consider the availability of skilled personnel for ongoing support. For those prioritizing efficiency and long-term savings, a detailed analysis of each alternative’s performance metrics and cost implications will be critical. Ultimately, aligning the chosen technology with business objectives and operational realities will facilitate a more informed decision-making process.
Essential Technical Properties and Trade Terminology for gas compressor supplier
What Are the Essential Technical Properties of Gas Compressors?
Understanding the key technical properties of gas compressors is crucial for B2B buyers, particularly when evaluating suppliers from diverse regions such as Africa, South America, the Middle East, and Europe. Here are the critical specifications that buyers should consider:
1. Material Grade
The material grade of a gas compressor significantly influences its durability and performance. Common materials include carbon steel, stainless steel, and aluminum alloys. The choice of material affects not only the compressor’s lifespan but also its resistance to corrosion, pressure, and temperature fluctuations. Buyers should prioritize suppliers who provide detailed material specifications to ensure compliance with industry standards and operational requirements.
2. Tolerance Levels
Tolerance refers to the permissible limit of variation in a physical dimension of the compressor components. This is crucial for ensuring the proper fit and function of the compressor within a given system. Tight tolerances can lead to better efficiency and performance, while loose tolerances may result in increased wear and tear. Understanding tolerance levels helps buyers assess the quality and reliability of the compressor, ultimately influencing maintenance costs.
3. Compression Ratio
The compression ratio is the ratio of the volume of gas before compression to the volume after compression. A higher compression ratio typically indicates a more efficient compressor, capable of delivering greater pressure. Buyers should evaluate the required compression ratio based on their application needs, as it directly affects energy consumption and operational costs.
4. Power Requirements
Power requirements denote the amount of energy needed to operate the gas compressor effectively. This specification is vital for ensuring compatibility with existing power infrastructure. Buyers should consider the energy efficiency of the compressor, as it impacts long-term operational costs. Understanding the power requirements also aids in selecting the appropriate motor and drive system.
5. Noise Levels
Noise levels produced by gas compressors can be a significant concern, particularly in urban settings or enclosed environments. Buyers should seek compressors that comply with relevant noise regulations and consider options with sound-dampening features. Evaluating noise levels can help mitigate potential complaints from stakeholders and ensure smoother operations.
What Are Common Trade Terminology and Jargon Used by Gas Compressor Suppliers?
Familiarity with industry terminology can enhance communication and negotiation with suppliers. Here are some essential terms that B2B buyers should know:
1. OEM (Original Equipment Manufacturer)
An OEM refers to a company that produces parts or equipment that may be marketed by another manufacturer. Understanding the role of OEMs can help buyers identify reputable suppliers who offer high-quality, reliable compressors. It also aids in recognizing potential warranty and support options.
2. MOQ (Minimum Order Quantity)
MOQ is the smallest quantity of a product that a supplier is willing to sell. Buyers should be aware of MOQ requirements, as they can impact purchasing decisions and inventory management. Negotiating MOQs can lead to cost savings and better alignment with business needs.
3. RFQ (Request for Quotation)
An RFQ is a document used to solicit price quotes from suppliers for specific products or services. Buyers should prepare detailed RFQs that include technical specifications, delivery timelines, and payment terms. This process helps ensure accurate quotes and fosters competitive pricing.
4. Incoterms (International Commercial Terms)
Incoterms are standardized international shipping terms that define the responsibilities of buyers and sellers in the transportation of goods. Understanding these terms is crucial for international transactions, as they clarify who is responsible for shipping costs, insurance, and risk during transit. This knowledge can help avoid misunderstandings and disputes.
5. Lead Time
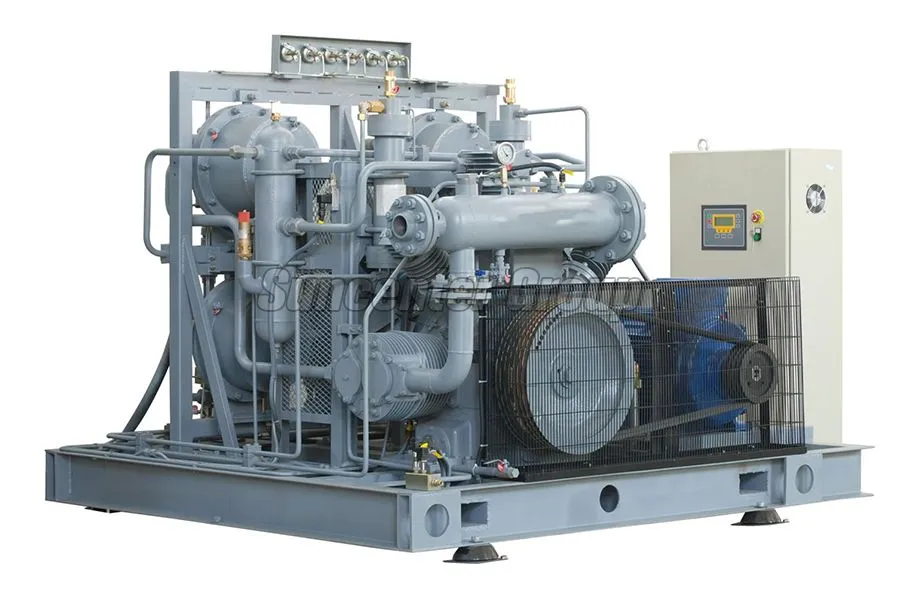
A stock image related to gas compressor supplier.
Lead time refers to the amount of time it takes from placing an order to the delivery of the product. Understanding lead times is essential for planning and scheduling operations. Buyers should inquire about lead times to ensure they align with project timelines and operational needs.
By grasping these technical properties and trade terminologies, international B2B buyers can make informed decisions when sourcing gas compressors, ultimately leading to improved operational efficiency and cost-effectiveness.
Navigating Market Dynamics and Sourcing Trends in the gas compressor supplier Sector
What Are the Current Market Dynamics and Key Trends in the Gas Compressor Supplier Sector?
The global gas compressor supplier market is experiencing transformative growth, driven by several key factors. Increased demand for natural gas, coupled with the transition towards cleaner energy sources, is propelling investment in gas infrastructure. In regions like Africa and South America, where energy access remains a challenge, gas compressors are pivotal in boosting energy availability and reliability. Emerging technologies, such as IoT and AI, are being integrated into compressor systems to enhance efficiency and predictive maintenance, allowing international B2B buyers to reduce operational costs.
Moreover, as industries seek to optimize production processes, there is a noticeable trend towards modular and scalable compressor solutions. Buyers from Europe and the Middle East are increasingly prioritizing suppliers who offer customizable products that can be tailored to specific operational needs. This flexibility is crucial for businesses aiming to adapt to fluctuating market conditions and regulatory requirements.
The ongoing geopolitical tensions and fluctuating oil prices also impact sourcing decisions. Buyers are advised to stay informed about supplier stability and regional market conditions, as these factors can influence pricing and availability. Establishing strong relationships with reliable suppliers can mitigate risks associated with market volatility.
How Can Sustainability and Ethical Sourcing Impact Your B2B Strategy in the Gas Compressor Sector?
Sustainability has become a cornerstone of strategic sourcing in the gas compressor supplier sector. International buyers are increasingly aware of the environmental impact of their supply chains. Gas compressors can contribute to greenhouse gas emissions if not sourced and operated responsibly. Thus, selecting suppliers who prioritize sustainable practices is essential.
Ethical sourcing not only aligns with corporate social responsibility goals but also appeals to a growing base of environmentally-conscious consumers. Buyers should seek suppliers who provide transparency in their operations, focusing on those who utilize ‘green’ certifications and materials. For instance, suppliers adopting eco-friendly manufacturing processes or using recycled materials in their compressors can help companies reduce their carbon footprint.
Additionally, regulatory frameworks in regions like Europe are becoming stricter regarding emissions and sustainability practices. International buyers must ensure compliance with these regulations, making it vital to partner with suppliers that meet or exceed these standards. This proactive approach not only mitigates risks but also enhances brand reputation and customer trust.
What Is the Brief Evolution of the Gas Compressor Supplier Market?
The gas compressor market has evolved significantly over the last few decades, transitioning from basic mechanical devices to sophisticated systems integrated with advanced technologies. Initially, gas compressors were primarily utilized in the oil and gas industry for transportation and storage. However, with the rise of natural gas as a cleaner energy source, their application has expanded to various sectors, including manufacturing, power generation, and even renewable energy.
Technological advancements, particularly in automation and digitalization, have further propelled this evolution. The introduction of smart compressors, equipped with sensors and IoT capabilities, has revolutionized performance monitoring and maintenance strategies. This shift towards intelligent systems not only improves efficiency but also extends the lifespan of equipment, offering significant cost savings for international B2B buyers.
In conclusion, understanding the market dynamics and sourcing trends within the gas compressor supplier sector is crucial for international buyers, especially those from Africa, South America, the Middle East, and Europe. By prioritizing sustainability and ethical sourcing, companies can enhance their operational efficiency while contributing positively to the environment.
Frequently Asked Questions (FAQs) for B2B Buyers of gas compressor supplier
-
How do I choose the right gas compressor supplier for my business needs?
Choosing the right gas compressor supplier involves several key factors. First, evaluate the supplier’s industry experience and expertise in your specific sector. Consider their product range, including the types of compressors they offer and their suitability for your applications. Check for certifications and compliance with international standards, as this indicates reliability and quality. Additionally, seek reviews and testimonials from previous clients, particularly those in your region, to gauge their reputation. Lastly, establish whether they offer after-sales support and maintenance services, as this can significantly impact your operational efficiency. -
What are the common types of gas compressors available for international buyers?
International buyers can choose from various types of gas compressors, including reciprocating, rotary screw, and centrifugal compressors. Reciprocating compressors are ideal for high-pressure applications and are commonly used in the oil and gas industry. Rotary screw compressors offer continuous airflow and are suitable for moderate pressure applications, often found in manufacturing. Centrifugal compressors, on the other hand, are best for large volume requirements and are typically used in large industrial operations. Understanding the specific application and operational requirements will help you select the most suitable type for your needs. -
What should I consider regarding customization options for gas compressors?
When sourcing gas compressors, inquire about customization options that align with your operational requirements. Many suppliers offer tailored solutions, including modifications in size, power, and efficiency to meet specific industry demands. Additionally, consider the compatibility of the compressor with your existing systems and any environmental factors such as temperature and humidity that may affect performance. It’s also essential to discuss potential upgrades or features that enhance energy efficiency and reduce operational costs. Ensure that the supplier can provide technical documentation and support for any customized solutions. -
What is the minimum order quantity (MOQ) for gas compressors from suppliers?
Minimum order quantities (MOQs) can vary significantly among gas compressor suppliers and depend on several factors, including the type of compressor and the supplier’s manufacturing capabilities. Some suppliers may have an MOQ of one unit for standard models, while others might require bulk orders to optimize production costs. Always clarify the MOQ before proceeding with negotiations to avoid unexpected expenses. If you’re a smaller buyer, look for suppliers that offer flexibility or sample units, which can be beneficial for testing before making larger commitments. -
What payment terms should I expect when sourcing gas compressors internationally?
Payment terms for international purchases of gas compressors typically include options such as advance payment, letters of credit, or payment upon delivery. It’s crucial to negotiate terms that protect your interests while ensuring the supplier’s confidence in the transaction. Look for suppliers who offer secure payment methods and consider escrow services for larger transactions. Additionally, be aware of any currency exchange rates and international banking fees that may apply. Clear communication regarding payment terms can help avoid disputes and ensure a smooth purchasing process. -
How can I ensure quality assurance when sourcing gas compressors?
To ensure quality assurance when sourcing gas compressors, first verify that the supplier adheres to international quality standards, such as ISO 9001. Request detailed product specifications and certifications to confirm compliance. Additionally, consider conducting a factory visit or requesting third-party inspections to assess manufacturing processes. Establish a clear quality control agreement that outlines acceptable quality levels and testing protocols. Engaging in regular communication with the supplier during production can also help address any concerns promptly and maintain product integrity. -
What logistics considerations should I take into account when importing gas compressors?
Logistics play a crucial role in the successful importation of gas compressors. Consider the shipping methods available, such as sea or air freight, and how they align with your timeline and budget. Evaluate the supplier’s experience with international shipping and their ability to handle customs documentation and tariffs. It’s also wise to plan for potential delays by factoring in lead times for production and shipping. Additionally, ensure that you have a reliable logistics partner who can manage the import process efficiently and mitigate risks associated with transportation. -
How do I handle after-sales support and maintenance for gas compressors?
After-sales support and maintenance are critical for the longevity and performance of gas compressors. When selecting a supplier, inquire about their warranty policies and the extent of technical support provided post-purchase. Check if they offer training for your staff on compressor operation and maintenance. Establish a maintenance schedule and discuss the availability of spare parts, as timely access can minimize downtime. Building a long-term relationship with your supplier can also facilitate better support and responsiveness to your maintenance needs.
Important Disclaimer & Terms of Use
⚠️ Important Disclaimer
The information provided in this guide, including content regarding manufacturers, technical specifications, and market analysis, is for informational and educational purposes only. It does not constitute professional procurement advice, financial advice, or legal advice.
While we have made every effort to ensure the accuracy and timeliness of the information, we are not responsible for any errors, omissions, or outdated information. Market conditions, company details, and technical standards are subject to change.
B2B buyers must conduct their own independent and thorough due diligence before making any purchasing decisions. This includes contacting suppliers directly, verifying certifications, requesting samples, and seeking professional consultation. The risk of relying on any information in this guide is borne solely by the reader.
Strategic Sourcing Conclusion and Outlook for gas compressor supplier
In navigating the complex landscape of gas compressor suppliers, strategic sourcing emerges as a vital approach for international B2B buyers. By carefully assessing supplier capabilities and understanding regional market dynamics, businesses can secure high-quality equipment that meets their operational needs while optimizing costs. Engaging with suppliers from diverse regions such as Africa, South America, the Middle East, and Europe allows for a broader selection of technology and innovation, crucial for enhancing operational efficiency.
How can international buyers maximize value through strategic sourcing? The key lies in fostering strong partnerships with suppliers who not only provide competitive pricing but also demonstrate reliability and a commitment to sustainability. This is particularly important in a global environment increasingly focused on reducing carbon footprints and adhering to environmental regulations.
Looking ahead, the demand for advanced gas compression solutions will only grow. International B2B buyers should remain proactive, leveraging strategic sourcing to stay ahead of market trends and technological advancements. By prioritizing collaboration and innovation in supplier relationships, businesses can ensure they are well-equipped to meet future challenges and capitalize on emerging opportunities. Engage with your suppliers today to build a resilient supply chain that drives success in your operations.