Discover Top Wiring Harnes Manufacturers: A Complete Guide (2025)
Introduction: Navigating the Global Market for wiring harnes manufacturer
In an increasingly interconnected world, sourcing high-quality wiring harness manufacturers can present a formidable challenge for international B2B buyers. The complexity of this component—integral to various applications from automotive to aerospace—demands not only a robust understanding of technical specifications but also the ability to navigate diverse market landscapes. Buyers from regions such as Africa, South America, the Middle East, and Europe face unique hurdles, including fluctuating supply chains, varying regulatory environments, and the need for reliable quality assurance.
This comprehensive guide aims to demystify the global market for wiring harness manufacturers by providing actionable insights tailored to your specific needs. We will explore different types of wiring harnesses, their applications across various industries, and essential criteria for supplier vetting. Furthermore, we will discuss cost considerations and pricing strategies, equipping you with the knowledge necessary to make informed purchasing decisions.
By leveraging this guide, B2B buyers will gain clarity on how to identify and collaborate with reputable manufacturers, ensuring that they receive products that meet international standards. Whether you are sourcing from established markets or emerging ones, understanding the nuances of the wiring harness industry can lead to significant operational efficiencies and enhanced product performance. Prepare to navigate the global market with confidence and expertise.
Understanding wiring harnes manufacturer Types and Variations
Type Name | Key Distinguishing Features | Primary B2B Applications | Brief Pros & Cons for Buyers |
---|---|---|---|
Custom Wiring Harnesses | Tailored designs to specific client requirements | Automotive, Aerospace, Industrial | Pros: Perfect fit for unique applications. Cons: Higher costs and longer lead times. |
Standard Wiring Harnesses | Pre-manufactured designs with common specifications | Consumer Electronics, Home Appliances | Pros: Cost-effective and quicker delivery. Cons: Limited customization options. |
High-Temperature Wiring Harnesses | Specially designed for extreme heat environments | Aerospace, Military, Heavy Machinery | Pros: Enhanced durability and reliability. Cons: May require specific installation expertise. |
Multi-Purpose Wiring Harnesses | Versatile designs for various applications | Automotive, Telecommunications | Pros: Flexible use across different sectors. Cons: May not meet niche requirements. |
Eco-Friendly Wiring Harnesses | Made from sustainable materials with reduced environmental impact | Green Technologies, Electric Vehicles | Pros: Aligns with sustainability goals. Cons: Potentially higher costs and limited suppliers. |
What Are Custom Wiring Harnesses and When Should You Consider Them?
Custom wiring harnesses are specifically engineered to meet the unique requirements of a project, making them ideal for industries such as automotive and aerospace. Their tailored nature allows for precise integration with existing systems, enhancing performance and reliability. B2B buyers should consider these harnesses when standard solutions do not meet their specifications, but they should also be prepared for longer lead times and potentially higher costs.
How Do Standard Wiring Harnesses Benefit B2B Buyers?
Standard wiring harnesses are mass-produced and adhere to common specifications, making them a cost-effective solution for industries like consumer electronics and home appliances. They offer quick delivery times and generally lower prices, which can be advantageous for companies looking to scale production rapidly. However, businesses should be aware that these harnesses may lack the customization necessary for specialized applications.
What Makes High-Temperature Wiring Harnesses Unique?
High-temperature wiring harnesses are specifically designed to withstand extreme heat, making them suitable for demanding environments such as aerospace and military applications. These harnesses feature materials that offer enhanced durability and reliability under stress. B2B buyers should consider them when operating in high-temperature conditions, but they may require specialized installation knowledge to ensure performance.
Why Choose Multi-Purpose Wiring Harnesses for Your Business?
Multi-purpose wiring harnesses are designed to serve various applications, particularly in automotive and telecommunications. Their versatility allows businesses to use them across different projects, reducing the need for multiple inventory items. While they provide flexibility, buyers should consider whether these harnesses meet the specific requirements of niche applications, as they may not always offer tailored solutions.
What Are the Advantages of Eco-Friendly Wiring Harnesses?
Eco-friendly wiring harnesses are made from sustainable materials, aligning with the growing demand for environmentally responsible products, especially in sectors like green technology and electric vehicles. These harnesses can enhance a company’s sustainability profile and appeal to eco-conscious consumers. However, buyers should be aware that they might come at a premium price and may have fewer manufacturers available.
Related Video: Introduction to Wiring Harness (Part – 1) | Skill-Lync
Key Industrial Applications of wiring harnes manufacturer
Industry/Sector | Specific Application of Wiring Harness Manufacturer | Value/Benefit for the Business | Key Sourcing Considerations for this Application |
---|---|---|---|
Automotive | Electrical Systems Integration | Improved vehicle performance and reliability | Compliance with regional standards and certifications |
Aerospace | Avionics and Control Systems | Enhanced safety and operational efficiency | High-quality materials and rigorous testing protocols |
Industrial Machinery | Automation and Robotics Wiring | Increased productivity and reduced downtime | Customization capabilities and scalability |
Renewable Energy | Solar and Wind Energy Systems | Maximized energy efficiency and system longevity | Expertise in environmental conditions and regulations |
Consumer Electronics | Smart Devices and IoT Applications | Enhanced user experience and device functionality | Rapid prototyping and flexibility in design changes |
How is Wiring Harness Manufacturing Used in the Automotive Sector?
In the automotive industry, wiring harnesses are integral to the electrical systems that power everything from headlights to complex infotainment systems. A reliable wiring harness ensures seamless communication between components, improving vehicle performance and reliability. For international buyers, especially in regions like Africa and South America, sourcing manufacturers who comply with local automotive standards is crucial. Buyers should prioritize manufacturers with experience in producing harnesses that meet specific regional regulations and certifications.
What Role Do Wiring Harnesses Play in Aerospace Applications?
In aerospace, wiring harnesses are essential for avionics and control systems, where they facilitate the transmission of electrical signals between critical components. These harnesses must adhere to stringent safety standards due to the high-stakes nature of air travel. International B2B buyers in the Middle East and Europe should seek manufacturers that provide high-quality materials and rigorous testing protocols. This ensures that the wiring harnesses can withstand extreme conditions and maintain operational efficiency throughout their lifecycle.
How Are Wiring Harnesses Used in Industrial Machinery?
Wiring harnesses in industrial machinery are vital for automation and robotics, connecting various sensors and actuators that drive efficiency. They help streamline operations, reduce downtime, and enhance productivity. For buyers in South America and Africa, sourcing manufacturers that offer customization capabilities and scalability is essential. This allows businesses to adapt their wiring solutions as machinery evolves or scales, ensuring continued operational efficiency.
What is the Importance of Wiring Harnesses in Renewable Energy Systems?
In renewable energy sectors, such as solar and wind, wiring harnesses are crucial for connecting various components of energy systems. They help maximize energy efficiency and ensure the longevity of the systems. International buyers should consider manufacturers with expertise in environmental conditions and regulations specific to their region. This knowledge is vital for ensuring that the harnesses can withstand local climate challenges while maintaining optimal performance.
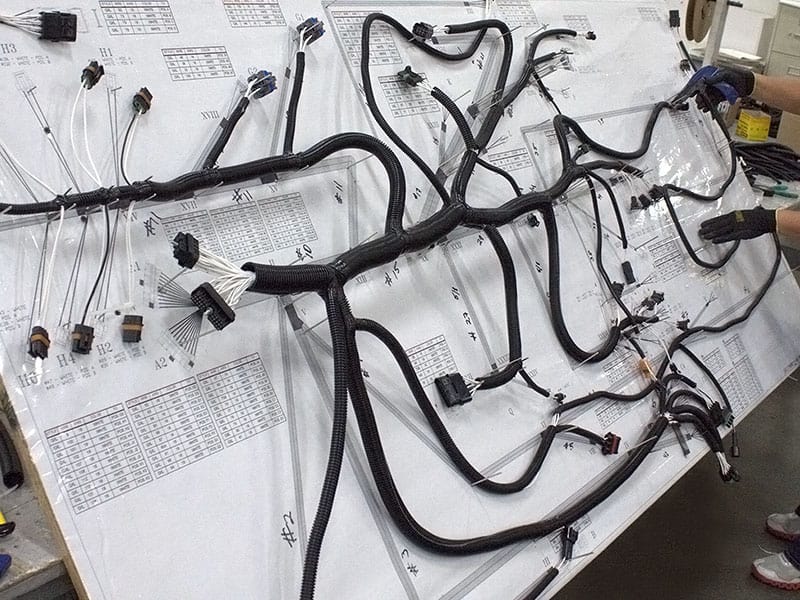
A stock image related to wiring harnes manufacturer.
How Do Wiring Harnesses Enhance Consumer Electronics?
Wiring harnesses play a significant role in consumer electronics, particularly in smart devices and IoT applications. They enable the complex interconnectivity required for enhanced user experiences and device functionality. For B2B buyers in Europe and Africa, rapid prototyping and flexibility in design changes are key considerations when sourcing wiring harness manufacturers. This adaptability allows businesses to innovate quickly and respond to market demands efficiently.
Related Video: How an Automotive Wiring Harness is Taped.
3 Common User Pain Points for ‘wiring harnes manufacturer’ & Their Solutions
Scenario 1: Inconsistent Quality Across Suppliers
The Problem: B2B buyers often encounter variability in the quality of wiring harnesses sourced from different manufacturers. This inconsistency can lead to a range of issues, including increased production downtime, additional costs for reworks, and even reputational damage if the end product fails. Buyers in regions like Africa and South America may struggle with limited options, making it challenging to find reliable manufacturers who can meet their quality expectations.
The Solution: To mitigate quality inconsistencies, buyers should prioritize establishing clear specifications and standards for wiring harnesses before initiating the sourcing process. This includes defining the required materials, tolerances, and testing procedures. Additionally, conducting thorough supplier audits and quality checks before placing bulk orders can significantly reduce risks. Collaborating with manufacturers who are ISO-certified or who have established quality management systems can provide an added layer of assurance. Building strong, communicative relationships with suppliers can also help in aligning expectations and maintaining quality throughout the production process.
Scenario 2: Complicated Customization Processes
The Problem: Many B2B buyers require customized wiring harnesses to fit specific applications, yet the customization process can often be convoluted and time-consuming. Buyers may find themselves frustrated by manufacturers who lack the flexibility to adapt to unique specifications or who have cumbersome communication channels that lead to misunderstandings. This is particularly problematic for buyers in the Middle East and Europe, where technological advancements necessitate tailored solutions.
The Solution: To streamline the customization process, buyers should engage manufacturers who utilize advanced design software and prototyping technologies. This allows for rapid iterations and adjustments based on feedback. It is advisable for buyers to provide comprehensive design documents, including CAD files, to facilitate clearer communication. Setting up regular checkpoints during the development phase can help ensure the project stays aligned with the buyer’s expectations. Lastly, consider manufacturers that offer a collaborative design approach, where both parties can contribute to the product’s development, thus fostering innovation and efficiency.
Scenario 3: Delayed Delivery Timelines
The Problem: Timely delivery is crucial for B2B operations, yet many buyers experience delays when sourcing wiring harnesses. These delays can stem from various factors, including supply chain disruptions, inadequate inventory management, or unforeseen manufacturing issues. For buyers in regions like South America and Africa, where logistics can be more complex, these delays can severely impact production schedules and project timelines.
The Solution: To address delivery concerns, buyers should conduct a thorough assessment of potential manufacturers’ supply chain capabilities before engaging in contracts. This involves understanding their lead times, production capacity, and logistics strategies. Establishing a clear timeline and milestones can help both parties stay accountable. Additionally, working with manufacturers who have robust contingency plans and diversified supply chains can mitigate the risks of delays. Buyers should also consider building relationships with multiple suppliers to ensure they have alternatives if one source encounters challenges. Finally, utilizing real-time tracking tools can provide transparency throughout the delivery process, allowing buyers to anticipate and react to potential delays effectively.
Strategic Material Selection Guide for wiring harnes manufacturer
When selecting materials for wiring harness manufacturing, it is essential to consider various factors that influence performance, cost, and compliance with regional standards. Below, we analyze four common materials used in wiring harnesses, focusing on their properties, advantages, disadvantages, and specific considerations for international B2B buyers.
What are the Key Properties of PVC in Wiring Harnesses?
Polyvinyl Chloride (PVC) is one of the most widely used materials in wiring harnesses due to its excellent electrical insulation properties and cost-effectiveness. PVC can withstand temperatures ranging from -10°C to 70°C, making it suitable for a variety of applications. Additionally, it offers good resistance to moisture and chemicals, which is crucial in environments where exposure to liquids is possible.
Pros: PVC is durable and relatively inexpensive, making it a popular choice for mass production. Its flexibility allows for easy handling and installation in complex configurations.
Cons: However, PVC has limitations regarding high-temperature applications, as prolonged exposure can lead to degradation. It is also less environmentally friendly compared to other materials, which may be a consideration for companies looking to improve sustainability.
Impact on Application: PVC is compatible with various media, including water and oils, but may not perform well in high-temperature or aggressive chemical environments.
Considerations for International Buyers: Buyers from regions like Africa and South America should ensure that PVC materials comply with local regulations, such as RoHS and REACH, which govern the use of hazardous substances.
How Does Polypropylene Compare for Wiring Harness Applications?
Polypropylene (PP) is another commonly used material, particularly valued for its high chemical resistance and lightweight properties. It can handle temperatures up to 100°C, making it suitable for applications that experience moderate heat.
Pros: The lightweight nature of PP reduces overall harness weight, which is beneficial in automotive and aerospace applications. It also offers good impact resistance.
Cons: The main drawback is its lower flexibility compared to PVC, which can complicate installation in tight spaces. Additionally, PP can be more expensive than PVC, impacting overall production costs.
Impact on Application: PP is particularly effective in environments with exposure to solvents and chemicals, making it ideal for automotive and industrial applications.
Considerations for International Buyers: Compliance with ASTM and ISO standards is crucial, especially for buyers in Europe and the Middle East, where stringent quality controls are enforced.
What are the Advantages of Using Teflon in Wiring Harness Manufacturing?
Teflon (PTFE) is renowned for its exceptional thermal stability and chemical resistance, withstanding temperatures up to 260°C. This material is particularly useful in high-performance applications where extreme conditions are present.
Pros: Teflon’s outstanding dielectric properties make it an excellent choice for high-frequency applications. Its resistance to a wide range of chemicals ensures longevity in harsh environments.
Cons: The primary disadvantage of Teflon is its high cost, which can significantly increase the manufacturing expense. Additionally, its rigidity can make it challenging to work with in certain configurations.
Impact on Application: Teflon is ideal for applications requiring high thermal and chemical resistance, such as aerospace and military sectors.
Considerations for International Buyers: Buyers should ensure that Teflon products meet specific military and aerospace standards, particularly in Europe and the Middle East, where compliance with MIL-SPEC standards is often required.
How Does Silicone Enhance Wiring Harness Performance?
Silicone is increasingly being used in wiring harnesses due to its flexibility and ability to withstand extreme temperatures, ranging from -60°C to 200°C. This makes it suitable for various applications, including automotive and industrial sectors.
Pros: Silicone’s flexibility allows for easy installation and routing, while its resistance to UV rays and ozone makes it suitable for outdoor applications.
Cons: The main limitation of silicone is its higher cost compared to PVC and PP, which may deter budget-conscious buyers. Additionally, it may not provide the same level of chemical resistance as Teflon.
Impact on Application: Silicone is particularly effective in environments with temperature fluctuations, making it ideal for automotive wiring harnesses.
Considerations for International Buyers: Buyers should verify compliance with local automotive standards and certifications, particularly in Europe, where regulations can be stringent.
Summary Table of Material Selection for Wiring Harnesses
Material | Typical Use Case for wiring harness manufacturer | Key Advantage | Key Disadvantage/Limitation | Relative Cost (Low/Med/High) |
---|---|---|---|---|
PVC | General-purpose wiring harnesses in automotive | Cost-effective and durable | Limited high-temperature performance | Low |
Polypropylene | Automotive and industrial applications | Lightweight and chemically resistant | Less flexible, higher cost than PVC | Medium |
Teflon | High-performance applications (aerospace/military) | Excellent thermal and chemical resistance | High cost and rigidity | High |
Silicone | Automotive and outdoor applications | Flexibility and UV resistance | Higher cost, less chemical resistance | Medium |
This guide provides a comprehensive overview of material options for wiring harness manufacturers, enabling international B2B buyers to make informed decisions based on performance, cost, and compliance considerations.
In-depth Look: Manufacturing Processes and Quality Assurance for wiring harnes manufacturer
What Are the Key Stages in the Manufacturing Process of Wiring Harnesses?
The manufacturing process of wiring harnesses involves several critical stages that ensure the final product meets quality and performance standards. Understanding these stages is essential for international B2B buyers looking for reliable suppliers.
1. Material Preparation
The first stage in the manufacturing process is material preparation, which involves selecting and cutting raw materials, such as wires, connectors, and insulation. The quality of these materials directly impacts the durability and functionality of the wiring harness. B2B buyers should inquire about the suppliers’ sourcing practices and the certifications of the materials used. This can include asking for compliance with international standards like RoHS (Restriction of Hazardous Substances) to ensure environmentally safe practices.
2. Forming
Once materials are prepared, the next step is forming, where wires are shaped and configured according to specific design requirements. This may involve techniques like crimping, which attaches connectors to wires securely. Advanced machinery, such as automatic crimping machines, enhances precision and efficiency. Buyers should consider suppliers that utilize state-of-the-art technology in forming processes, as this can significantly affect the reliability of the final product.
3. Assembly
The assembly stage is where the formed components are integrated into complete wiring harnesses. This process often requires skilled labor for tasks like soldering and bundling wires. Suppliers may employ both manual and automated assembly techniques, depending on the complexity of the harness. Buyers should look for manufacturers that have a balanced approach, utilizing automation for efficiency while ensuring skilled technicians handle intricate tasks.
4. Finishing
The final stage of manufacturing is finishing, which includes processes like insulation, marking, and packaging. Proper insulation is crucial for preventing short circuits and ensuring safety. Additionally, clear marking facilitates easy installation and maintenance. Buyers should confirm that suppliers follow best practices in finishing, as this stage can significantly impact the performance and longevity of the wiring harness.
What Quality Assurance Measures Should B2B Buyers Look For?
Quality assurance (QA) is a vital aspect of the manufacturing process, ensuring that wiring harnesses meet industry standards and customer expectations. International B2B buyers should familiarize themselves with the various quality assurance practices employed by suppliers.
What International Standards Are Relevant for Wiring Harness Manufacturers?
Adherence to international standards is critical in the wiring harness industry. ISO 9001 is one of the most recognized quality management standards, demonstrating a commitment to continuous improvement and customer satisfaction. Additionally, industry-specific certifications such as CE (Conformité Européenne) for products sold in Europe and API (American Petroleum Institute) for oil and gas applications are important indicators of quality and compliance. Buyers should request copies of these certifications to assess supplier credibility.
What Are the Key QC Checkpoints in Wiring Harness Manufacturing?
Quality control (QC) involves several checkpoints throughout the manufacturing process:
-
Incoming Quality Control (IQC): This stage inspects raw materials upon arrival to ensure they meet specified standards.
-
In-Process Quality Control (IPQC): Continuous monitoring during manufacturing helps identify defects early, reducing waste and rework.
-
Final Quality Control (FQC): The final inspection ensures that the finished product adheres to all quality specifications before shipment.
Buyers should ask suppliers about their QC protocols and how they handle deviations from quality standards.
What Common Testing Methods Are Used in Wiring Harness Manufacturing?
Testing is a crucial part of the quality assurance process. Common testing methods include:
-
Electrical Testing: Ensures the harness functions correctly under expected electrical loads. This may include continuity tests and insulation resistance tests.
-
Mechanical Testing: Assesses the physical properties of the harness, such as tensile strength and flexibility.
-
Environmental Testing: Evaluates the harness’s performance under various environmental conditions, such as temperature extremes and humidity.
B2B buyers should inquire about the specific testing methods employed by suppliers and request test reports to verify compliance with standards.
How Can B2B Buyers Verify Supplier Quality Control?
For international B2B buyers, verifying a supplier’s quality control processes is essential to mitigate risks. Here are several strategies to ensure supplier credibility:
1. Conduct Supplier Audits
Regular audits can provide an in-depth understanding of a supplier’s manufacturing processes and quality control measures. Buyers should establish a schedule for audits and consider using third-party auditing services for an impartial assessment.
2. Request Quality Assurance Reports
Suppliers should be willing to share quality assurance reports, including results from IQC, IPQC, and FQC stages. Reviewing these documents helps buyers gauge the effectiveness of a supplier’s quality management system.
3. Engage Third-Party Inspection Services
Utilizing third-party inspection services adds an extra layer of verification. These services can conduct inspections at various stages of the manufacturing process, ensuring compliance with quality standards.
What Are the Nuances of Quality Control for International Buyers?
B2B buyers from Africa, South America, the Middle East, and Europe should be aware of regional nuances in quality control. Different markets may have varying expectations and regulatory requirements, which can impact the selection of suppliers.
-
Cultural Considerations: Understanding cultural differences in business practices can help in negotiations and establishing trust with suppliers.
-
Regulatory Compliance: Buyers must ensure that suppliers comply with local regulations and international standards relevant to their specific market.
-
Logistical Challenges: Supply chain dynamics can affect the consistency of quality control. Buyers should consider suppliers’ logistical capabilities to ensure timely delivery of quality products.
By addressing these aspects, international B2B buyers can make informed decisions when selecting wiring harness manufacturers, ensuring they partner with suppliers committed to quality and excellence.
Practical Sourcing Guide: A Step-by-Step Checklist for ‘wiring harnes manufacturer’
Introduction
Sourcing a reliable wiring harness manufacturer is a critical step for international B2B buyers aiming to ensure the quality and efficiency of their products. This guide provides a practical, step-by-step checklist designed to help you navigate the complexities of supplier selection and procurement. By following these steps, you can make informed decisions and establish fruitful partnerships in the wiring harness industry.
Step 1: Define Your Technical Specifications
Establishing clear technical specifications is vital to ensure that the wiring harness meets your product requirements. Define the dimensions, materials, performance standards, and compliance with industry regulations. This clarity will not only streamline your procurement process but also help potential suppliers understand your needs accurately.
- Considerations: Voltage ratings, temperature resistance, and environmental conditions are crucial factors to include in your specifications.
Step 2: Conduct Market Research for Potential Suppliers
Before reaching out to manufacturers, conduct thorough market research to identify potential suppliers. Utilize industry-specific directories, trade shows, and online platforms like Alibaba and ThomasNet. This step will help you compile a list of manufacturers that specialize in wiring harness production.
- Tip: Focus on suppliers with a strong presence in your target region, as they may better understand local regulations and market demands.
Step 3: Evaluate Supplier Capabilities and Experience
Assessing the capabilities of potential suppliers is essential to ensure they can meet your production needs. Look for manufacturers with relevant experience in producing wiring harnesses for your specific industry. Request case studies and examples of previous projects to gauge their expertise.
- Key Indicators: Certifications such as ISO 9001 or IATF 16949 can also serve as proof of quality management systems in place.
Step 4: Verify Supplier Certifications and Compliance
Ensure that the manufacturers you are considering hold necessary certifications and comply with international standards. This verification process is crucial for guaranteeing product quality and safety. Request copies of certifications and check for compliance with standards relevant to your industry, such as RoHS or UL.
- Why It Matters: Non-compliance can lead to costly recalls and damage to your brand reputation.
Step 5: Request Quotes and Compare Pricing Structures
Once you have shortlisted potential suppliers, request detailed quotes that outline pricing, lead times, and payment terms. Comparing these quotes will help you understand the market rates and identify suppliers that offer the best value without compromising on quality.
- Considerations: Pay attention to hidden costs, such as shipping fees and duties, which can significantly affect your overall budget.
Step 6: Conduct Site Visits or Virtual Audits
If feasible, conduct site visits or virtual audits to evaluate the manufacturing processes and working conditions of the suppliers. This firsthand observation will provide insights into their operational capabilities and quality control measures.
- Benefits: Building a personal relationship with the supplier can also foster trust and improve communication.
Step 7: Establish Clear Communication Channels
Effective communication is key to a successful supplier relationship. Establish clear channels for ongoing dialogue regarding production schedules, quality issues, and other concerns. Regular updates and feedback loops can prevent misunderstandings and ensure alignment throughout the manufacturing process.
- Best Practices: Utilize project management tools and platforms for real-time communication and tracking project progress.
By following this checklist, international B2B buyers can make more informed decisions when sourcing wiring harness manufacturers, ultimately leading to improved product quality and successful partnerships.
Comprehensive Cost and Pricing Analysis for wiring harnes manufacturer Sourcing
What Are the Key Cost Components in Wiring Harness Manufacturing?
Understanding the cost structure of wiring harness manufacturing is crucial for international B2B buyers. The primary components influencing the overall cost include:
-
Materials: The type of materials used, such as copper, plastic, and insulation, significantly impacts the cost. High-quality materials may offer better durability and performance but can increase initial expenses.
-
Labor: Labor costs vary by region and can significantly affect the total price. Skilled labor is often more expensive, especially in countries with higher wage standards. It’s important to consider the labor market dynamics of the supplier’s location.
-
Manufacturing Overhead: This encompasses indirect costs such as utilities, rent, and administrative expenses. Efficient manufacturing processes can lower overhead costs, which can be passed on to buyers.
-
Tooling: The cost of molds, dies, and other tooling necessary for production can be substantial. Custom tooling for unique designs will increase upfront costs but may reduce per-unit costs in high-volume orders.
-
Quality Control (QC): Implementing rigorous QC processes ensures product reliability and compliance with industry standards. While this can add to the cost, it mitigates the risk of defects that could lead to costly recalls or failures.
-
Logistics: Shipping and handling costs are critical, especially for international transactions. Factors such as distance, mode of transport, and customs duties can significantly affect the final price.
-
Margin: Finally, the manufacturer’s profit margin will influence pricing. This can vary widely based on the supplier’s business model and market competition.
How Do Price Influencers Affect Wiring Harness Sourcing?
Several factors can influence the pricing of wiring harnesses, making it essential for buyers to understand these elements:
-
Volume/MOQ: Minimum Order Quantities (MOQ) often dictate pricing. Larger orders typically reduce the per-unit cost, so negotiating volume discounts is advantageous for buyers.
-
Specifications and Customization: Custom designs or specific technical specifications can elevate costs. Buyers should weigh the necessity of customization against potential price increases.
-
Materials and Quality Certifications: The choice of materials and the presence of quality certifications (like ISO or RoHS compliance) can influence pricing. Premium materials and certifications often justify higher costs through enhanced performance and reliability.
-
Supplier Factors: Supplier reputation, experience, and capacity can affect pricing. Established suppliers may charge more due to their proven track record, while newer entrants may offer competitive rates to gain market share.
-
Incoterms: Understanding Incoterms is crucial for international buyers. They define the responsibilities of buyers and sellers in shipping arrangements, impacting total costs and risk management.
What Buyer Tips Can Enhance Cost-Efficiency in Wiring Harness Sourcing?
International B2B buyers can adopt several strategies to optimize their sourcing costs effectively:
-
Negotiation Tactics: Engage in strategic negotiations with suppliers. Be clear about your budget and requirements, and don’t hesitate to request better terms, especially for larger orders.
-
Total Cost of Ownership (TCO): Look beyond the initial purchase price. Consider the TCO, which includes maintenance, durability, and potential failure costs. A slightly higher upfront cost may lead to savings in the long run.
-
Market Research: Conduct thorough market research to understand the pricing landscape across different regions. This insight can provide leverage during negotiations and help identify competitive suppliers.
-
Consider Regional Factors: When sourcing from Africa, South America, the Middle East, or Europe, be aware of local economic conditions, currency fluctuations, and trade agreements. These factors can impact pricing and logistics.
-
Build Long-term Relationships: Establishing long-term relationships with suppliers can lead to better pricing and terms over time. Loyalty often results in preferential treatment regarding pricing and service.
Conclusion and Disclaimer
This analysis provides an overview of the cost structure and pricing influences related to wiring harness manufacturing. Prices can vary widely based on numerous factors, and the insights provided are indicative rather than definitive. Buyers should conduct their own due diligence and seek multiple quotes to ensure they are making informed purchasing decisions.
Alternatives Analysis: Comparing wiring harnes manufacturer With Other Solutions
Understanding the Importance of Alternative Solutions in Wiring Harness Manufacturing
When considering wiring harness manufacturers, it’s crucial for B2B buyers to explore alternative solutions that may offer different advantages depending on their specific needs and circumstances. The landscape of manufacturing and design is continually evolving, prompting buyers to evaluate the most efficient and cost-effective options available. This section will compare traditional wiring harness manufacturing with two viable alternatives: 3D Printed Wiring Harnesses and Modular Wiring Systems.
Comparison Table of Wiring Harness Solutions
Comparison Aspect | Wiring Harness Manufacturer | 3D Printed Wiring Harnesses | Modular Wiring Systems |
---|---|---|---|
Performance | High reliability and durability | Variable; depends on materials used | High adaptability and scalability |
Cost | Higher upfront costs due to tooling | Lower initial costs; variable material costs | Moderate; upfront costs can be offset by reduced labor |
Ease of Implementation | Requires skilled labor and time | Relatively quick; can be done in-house | Easy to assemble; less technical skill required |
Maintenance | Standard maintenance practices | Minimal; replacements can be printed on-demand | Simplified; components can be replaced easily |
Best Use Case | High-volume production with stringent quality | Prototyping and low-volume production | Projects requiring flexibility and quick changes |
What Are the Advantages and Disadvantages of 3D Printed Wiring Harnesses?
3D printed wiring harnesses represent a modern approach that leverages additive manufacturing. The primary advantage of this method is the reduction in initial costs, as it eliminates the need for expensive molds and tooling. This makes it particularly suitable for prototyping or low-volume runs where traditional manufacturing would be cost-prohibitive. However, the performance can be variable, heavily reliant on the materials used, which may not always match the durability and reliability of traditionally manufactured harnesses. Additionally, while implementation is relatively quick, the technology may require skilled personnel familiar with 3D printing processes.
How Do Modular Wiring Systems Compare?
Modular wiring systems offer an adaptable solution that stands out for its ease of use and flexibility. These systems enable quick assembly and modification, making them ideal for projects where specifications may change frequently. The moderate costs associated with modular systems can be offset by reduced labor time, as they are designed to be user-friendly. However, while the adaptability is a significant advantage, the overall performance may not match that of a custom-made wiring harness, especially in high-demand environments where robustness is essential.
How Can B2B Buyers Choose the Right Wiring Solution?
Selecting the appropriate wiring solution ultimately depends on the specific requirements of your project. For B2B buyers, key considerations include the volume of production, budget constraints, and the need for flexibility. If your project demands high reliability and you are dealing with large-scale production, a traditional wiring harness manufacturer may be the best choice. Conversely, for prototypes or projects with fluctuating needs, exploring 3D printing or modular systems could lead to significant cost savings and enhanced agility. It’s essential to align your choice with both your immediate needs and long-term goals to ensure a successful procurement strategy.
Essential Technical Properties and Trade Terminology for wiring harnes manufacturer
What Are the Key Technical Properties of Wiring Harnesses?
When sourcing wiring harnesses, understanding their technical properties is essential for making informed purchasing decisions. Here are some critical specifications that should be considered:
-
Material Grade
– Definition: The grade of materials used in wiring harnesses, such as copper for conductors and various plastics for insulation.
– B2B Importance: Higher-grade materials ensure better conductivity and durability, which translates to lower failure rates and longer service life. Buyers should evaluate the material grades to ensure they meet industry standards and specific application requirements. -
Temperature Rating
– Definition: The maximum and minimum temperatures at which a wiring harness can operate effectively.
– B2B Importance: Different applications, particularly in automotive and industrial environments, have varying temperature extremes. Selecting wiring harnesses with appropriate temperature ratings minimizes the risk of insulation breakdown and electrical failure. -
Tolerance Levels
– Definition: The allowable deviation from specified dimensions in the manufacturing process.
– B2B Importance: Tighter tolerances often indicate higher precision in manufacturing, which is crucial for applications requiring strict performance standards. Buyers should specify tolerance levels to ensure compatibility with existing systems and components. -
Voltage Rating
– Definition: The maximum voltage that a wiring harness can safely carry.
– B2B Importance: Choosing a wiring harness with an appropriate voltage rating is critical for preventing insulation breakdown and ensuring safety. Buyers should assess voltage requirements based on the specific applications to avoid potential hazards. -
Shielding Type
– Definition: The method used to protect wires from electromagnetic interference (EMI), such as foil or braided shielding.
– B2B Importance: Effective shielding is vital in environments with high EMI, as it ensures signal integrity and reduces noise. Buyers should inquire about shielding types to match their specific operational environments.
What Are Common Trade Terms in the Wiring Harness Industry?
Understanding industry jargon is essential for effective communication and negotiation in the B2B wiring harness market. Here are some commonly used terms:
-
OEM (Original Equipment Manufacturer)
– Definition: A company that produces parts or equipment that may be marketed by another manufacturer.
– B2B Importance: Knowing whether a manufacturer is an OEM can help buyers understand the quality and reliability of the wiring harnesses, as OEM products typically adhere to strict quality standards. -
MOQ (Minimum Order Quantity)
– Definition: The smallest quantity of an item that a supplier is willing to sell.
– B2B Importance: Understanding the MOQ is critical for budget-conscious buyers, especially for small businesses or startups. It can also impact inventory management and cash flow. -
RFQ (Request for Quotation)
– Definition: A document sent to suppliers requesting pricing and terms for specific products.
– B2B Importance: An RFQ is a fundamental tool for buyers to gather information from multiple suppliers, allowing for comparative analysis and informed decision-making. -
Incoterms (International Commercial Terms)
– Definition: A set of predefined international trade terms that delineate responsibilities of buyers and sellers.
– B2B Importance: Familiarity with Incoterms is crucial for international transactions, as they clarify shipping responsibilities, risk transfer, and cost allocation. Proper understanding can prevent disputes and ensure smoother logistics. -
Lead Time
– Definition: The time taken from placing an order to the delivery of goods.
– B2B Importance: Knowing lead times helps buyers plan their projects and manage supply chain expectations. It is essential for maintaining production schedules and avoiding delays.
By understanding these technical properties and trade terms, international B2B buyers can enhance their procurement strategies and make more informed decisions when sourcing wiring harnesses.
Navigating Market Dynamics and Sourcing Trends in the wiring harnes manufacturer Sector
What Are the Key Market Dynamics Influencing Wiring Harness Manufacturing?
The global wiring harness manufacturing sector is currently witnessing a transformation driven by several key trends. Rapid technological advancements, such as automation and IoT integration, are reshaping how manufacturers operate. For B2B buyers from regions like Africa, South America, the Middle East, and Europe, understanding these dynamics is crucial. The demand for electric vehicles (EVs) is surging, particularly in Europe, pushing manufacturers to adapt their offerings to accommodate higher volumes and more complex designs. This shift emphasizes the importance of flexibility in sourcing strategies.
Moreover, the rise of Industry 4.0 technologies is enabling manufacturers to optimize their supply chains. Real-time data analytics and predictive maintenance are becoming essential tools for ensuring efficiency and reducing downtime. Buyers should consider partnering with manufacturers who are early adopters of these technologies, as they are likely to offer better lead times and quality assurance.
Another noteworthy trend is the increasing focus on customization. With the growing demand for tailored wiring solutions across various industries, including automotive, aerospace, and telecommunications, B2B buyers need to seek out manufacturers capable of providing bespoke solutions. This customization is often supported by advancements in materials science, leading to the development of lighter and more durable wiring harnesses.
How Is Sustainability Shaping Sourcing Decisions in the Wiring Harness Sector?
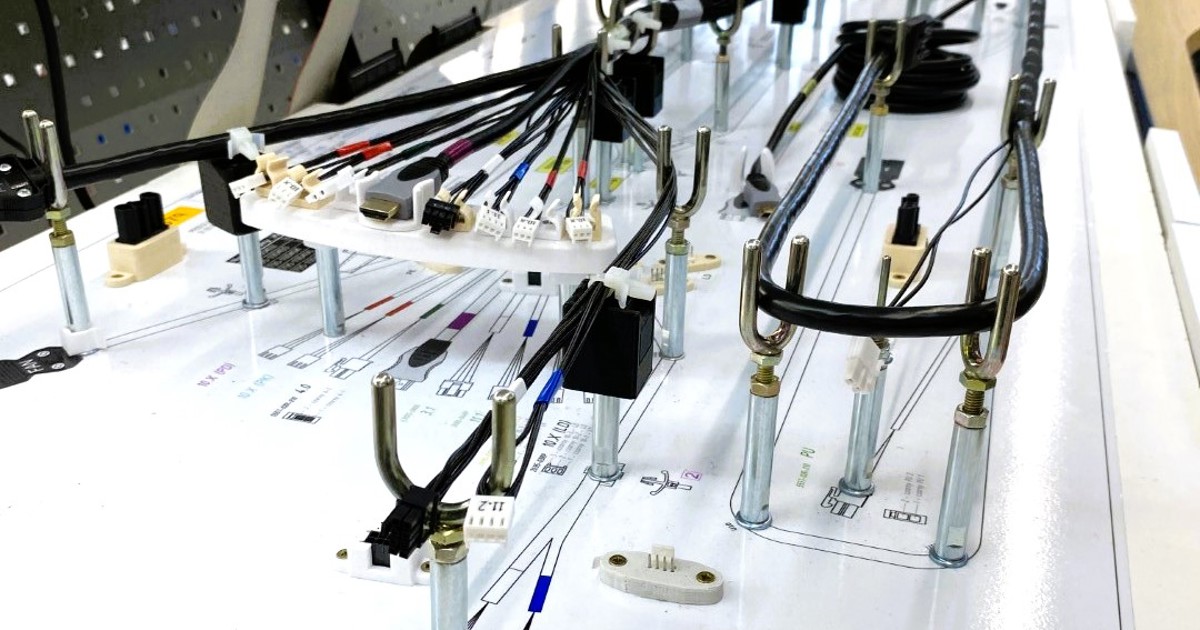
A stock image related to wiring harnes manufacturer.
Sustainability and ethical sourcing are becoming non-negotiable aspects of the wiring harness manufacturing sector. B2B buyers are increasingly prioritizing suppliers who demonstrate environmental responsibility and adhere to sustainable practices. The production of wiring harnesses can have significant environmental impacts, from raw material extraction to manufacturing processes. As a result, buyers should look for manufacturers that are committed to reducing their carbon footprint and have clear sustainability policies in place.
One effective way to assess a manufacturer’s commitment to sustainability is to inquire about their certifications and the materials they use. For instance, many manufacturers are now utilizing recycled or eco-friendly materials in their wiring harnesses, which not only reduces environmental impact but also appeals to environmentally conscious clients. Certifications such as ISO 14001 for environmental management systems can serve as indicators of a manufacturer’s dedication to sustainability.
Additionally, establishing ethical supply chains is crucial. B2B buyers should ensure that their suppliers adhere to fair labor practices and ethical sourcing of materials. This not only enhances the brand image but also mitigates risks associated with supply chain disruptions that may arise from unethical practices.
What Is the Evolution of the Wiring Harness Manufacturing Sector?
The wiring harness manufacturing sector has evolved significantly over the past few decades, transitioning from traditional manufacturing methods to more advanced and automated processes. Initially, wiring harnesses were predominantly handcrafted, leading to longer production times and variability in quality. With the advent of computer-aided design (CAD) and automated production lines, manufacturers have been able to enhance precision and scalability.
The introduction of advanced materials and innovative manufacturing techniques has also played a pivotal role. Today’s wiring harnesses are designed to meet the stringent requirements of modern industries, including increased durability and resistance to heat and chemicals. This evolution not only improves product performance but also aligns with the growing demand for environmentally friendly solutions, marking a significant shift in the sector towards sustainability and efficiency.
For international B2B buyers, understanding this historical context is essential for making informed sourcing decisions, as it highlights the importance of innovation and adaptability in selecting a manufacturing partner.
Frequently Asked Questions (FAQs) for B2B Buyers of wiring harnes manufacturer
-
How do I evaluate the quality of a wiring harness manufacturer?
To assess the quality of a wiring harness manufacturer, consider their certifications, such as ISO 9001 or TS 16949, which indicate adherence to international quality standards. Request samples to evaluate the materials and craftsmanship firsthand. Additionally, investigate their track record with other clients and look for reviews or testimonials. Establish communication with their quality assurance team to understand their testing processes and defect rates, which can provide deeper insights into their operational effectiveness. -
What are the key factors to consider when sourcing a wiring harness manufacturer internationally?
When sourcing a wiring harness manufacturer, evaluate their production capabilities, lead times, and shipping logistics. Consider the manufacturer’s experience in your specific industry, as expertise can significantly affect product quality. Additionally, assess their ability to provide customization options to meet your specific requirements. Lastly, analyze the political and economic stability of the manufacturer’s country, as this can impact supply chain reliability. -
What customization options should I expect from a wiring harness manufacturer?
Most reputable wiring harness manufacturers offer a range of customization options, including wire gauge, insulation materials, connector types, and length specifications. Discuss your project requirements in detail to ensure they can accommodate your needs. Some manufacturers may also provide design support or engineering consultations to optimize your harness for performance. Always request a prototype before finalizing the order to confirm that the customizations meet your expectations. -
What is the minimum order quantity (MOQ) when sourcing wiring harnesses?
Minimum order quantities (MOQs) can vary significantly among manufacturers, often ranging from 100 to several thousand units, depending on the complexity of the harness and the manufacturer’s production capabilities. For smaller businesses or startups, it’s advisable to discuss your needs with potential suppliers. Some manufacturers may offer flexible MOQs, especially for new clients, or provide a tiered pricing structure based on order volume. -
What payment terms should I negotiate with a wiring harness manufacturer?
Negotiating favorable payment terms is crucial when sourcing from international manufacturers. Common terms include a deposit (typically 30-50%) before production and the balance upon completion or delivery. Consider requesting payment via secure methods, such as letters of credit or escrow services, to mitigate risks. Additionally, explore options for bulk discounts or extended payment terms based on your order size and relationship with the supplier. -
How can I ensure reliable logistics and delivery from a wiring harness manufacturer?
To ensure reliable logistics, discuss shipping options with your manufacturer upfront. Inquire about their experience with international shipping and customs clearance, especially if you are sourcing from a different continent. Consider using freight forwarders to streamline the shipping process and mitigate risks. Establish clear timelines for production and delivery, and request regular updates to stay informed about your order status throughout the process. -
What quality assurance practices should a wiring harness manufacturer have in place?
A reputable wiring harness manufacturer should implement rigorous quality assurance practices, including in-process inspections and final product testing. Look for manufacturers that utilize automated testing equipment to ensure consistency and accuracy. They should also have established protocols for defect identification and resolution. Request documentation of their quality control processes and any relevant certifications to ensure they meet your quality standards. -
How do I handle communication and cultural differences when working with a wiring harness manufacturer?
Effective communication is key to successful international partnerships. Familiarize yourself with the cultural norms of your manufacturer’s country to avoid misunderstandings. Utilize clear and concise language in all communications, and consider using visual aids, such as diagrams or charts, to convey complex information. Establish regular check-ins via video calls or emails to maintain open lines of communication, and be patient and adaptable to different time zones and work styles.
Important Disclaimer & Terms of Use
⚠️ Important Disclaimer
The information provided in this guide, including content regarding manufacturers, technical specifications, and market analysis, is for informational and educational purposes only. It does not constitute professional procurement advice, financial advice, or legal advice.
While we have made every effort to ensure the accuracy and timeliness of the information, we are not responsible for any errors, omissions, or outdated information. Market conditions, company details, and technical standards are subject to change.
B2B buyers must conduct their own independent and thorough due diligence before making any purchasing decisions. This includes contacting suppliers directly, verifying certifications, requesting samples, and seeking professional consultation. The risk of relying on any information in this guide is borne solely by the reader.
Strategic Sourcing Conclusion and Outlook for wiring harnes manufacturer
In the evolving landscape of wiring harness manufacturing, strategic sourcing stands out as a pivotal approach for international B2B buyers. By carefully selecting suppliers based on quality, reliability, and cost-effectiveness, businesses can secure a competitive edge in their respective markets. Key takeaways for buyers in Africa, South America, the Middle East, and Europe include the importance of leveraging local insights to navigate supply chain complexities and fostering strong relationships with manufacturers who prioritize innovation and sustainability.
How can buyers enhance their strategic sourcing efforts? By investing in robust supplier assessments and utilizing technology to streamline procurement processes, companies can mitigate risks associated with supply chain disruptions. Additionally, focusing on collaboration with manufacturers can lead to tailored solutions that meet specific business needs, ultimately driving efficiency and profitability.
Looking ahead, the demand for high-quality wiring harnesses will continue to grow, particularly in sectors such as automotive and renewable energy. International B2B buyers are encouraged to remain proactive, explore new partnerships, and adapt to emerging trends in manufacturing. By prioritizing strategic sourcing now, businesses can position themselves for sustained success in an increasingly competitive global market.