Discover Top Dining Chair Suppliers to Cut Costs (2025)
Introduction: Navigating the Global Market for dining chair supplier
In the ever-evolving landscape of global trade, sourcing the right dining chair supplier can pose significant challenges for international B2B buyers. Whether you are in the bustling markets of South Africa, the vibrant cities of South America, or the culturally rich regions of the Middle East and Europe, finding suppliers that provide quality, comfort, and style is paramount. This guide delves into the intricacies of the dining chair market, addressing critical factors such as types of chairs, their applications in various settings, and the complexities of supplier vetting processes.
Understanding the nuances of cost structures and the implications of international shipping will also be explored, empowering buyers to make informed decisions that align with their business needs. By leveraging the insights and practical strategies outlined in this guide, B2B buyers can navigate the complexities of sourcing dining chairs effectively. We aim to equip you with the knowledge necessary to identify reliable suppliers, ensuring that your procurement process is efficient and cost-effective.
This comprehensive resource is designed specifically for international buyers, particularly those from Africa, South America, the Middle East, and Europe, including key markets like Egypt and South Africa. By addressing common challenges and offering actionable solutions, this guide serves as a valuable tool for enhancing your purchasing strategy in the global dining chair market.
Understanding dining chair supplier Types and Variations
Type Name | Key Distinguishing Features | Primary B2B Applications | Brief Pros & Cons for Buyers |
---|---|---|---|
Solid Wood Dining Chairs | Crafted from hardwoods like oak or maple; durable and timeless design | Restaurants, hotels, and upscale dining | Pros: Long-lasting, classic appeal. Cons: Heavier and may require more maintenance. |
Metal Frame Dining Chairs | Constructed with steel or aluminum frames; often paired with various seat materials | Cafés, outdoor dining, and event spaces | Pros: Lightweight, modern design. Cons: May lack warmth compared to wood. |
Upholstered Dining Chairs | Features fabric or leather upholstery; offers comfort and style options | Fine dining establishments, banquet halls | Pros: High comfort level, diverse aesthetics. Cons: Can be difficult to clean and maintain. |
Stackable Dining Chairs | Designed for easy storage; often made from plastic or lightweight metals | Events, conferences, and temporary setups | Pros: Space-saving, versatile. Cons: May sacrifice comfort for practicality. |
Vintage/Antique Dining Chairs | Unique, often one-of-a-kind pieces; can be restored or refurbished | Specialty restaurants, boutique hotels | Pros: Distinctive character, can be a conversation starter. Cons: Availability can be inconsistent; may require more investment. |
What Are the Characteristics of Solid Wood Dining Chairs for B2B Buyers?
Solid wood dining chairs are renowned for their durability and classic aesthetic. Typically made from hardwoods like oak, maple, or walnut, these chairs offer a timeless appeal that suits various dining environments. B2B buyers should consider the weight and maintenance requirements of solid wood, as they can be heavier and may need periodic refinishing. However, their longevity makes them a worthwhile investment for establishments like restaurants and hotels looking to create a warm, inviting atmosphere.
How Do Metal Frame Dining Chairs Benefit B2B Buyers?
Metal frame dining chairs are often constructed from lightweight materials such as steel or aluminum, providing a modern look and feel. These chairs are particularly suitable for outdoor dining settings or trendy cafés. For B2B buyers, the ease of movement and storage can be a significant advantage, especially in spaces that require frequent reconfiguration. However, while they are durable, they may not offer the same level of warmth and comfort as wooden options, which could impact customer experience in certain dining settings.
Why Choose Upholstered Dining Chairs for Comfort and Style?
Upholstered dining chairs are designed with fabric or leather coverings, providing a plush seating experience that enhances customer comfort. They are ideal for fine dining establishments and banquet halls where aesthetic appeal is crucial. B2B buyers should weigh the benefits of comfort and style against the potential challenges of cleaning and maintenance, as upholstery can attract stains and wear over time. Selecting durable, high-quality materials can mitigate these concerns, making them a valuable choice for upscale venues.
What Are the Advantages of Stackable Dining Chairs for Events?
Stackable dining chairs are designed with practicality in mind, allowing for easy storage and transport. Often made from plastic or lightweight metals, these chairs are ideal for events, conferences, and temporary setups. B2B buyers appreciate their versatility and space-saving features, which enable quick setup and breakdown. However, it’s essential to consider that stackable chairs may compromise comfort, making them less suitable for long dining experiences where guests will be seated for extended periods.
How Do Vintage/Antique Dining Chairs Offer Unique Value?
Vintage or antique dining chairs provide a unique aesthetic that can set a restaurant or hotel apart from competitors. These one-of-a-kind pieces often feature intricate designs and craftsmanship, appealing to buyers looking to create a distinctive atmosphere. However, sourcing vintage chairs can be inconsistent, and they may require restoration or refurbishment, which adds to the initial investment. For B2B buyers, the character and story behind each piece can enhance the dining experience, making it a worthwhile consideration for specialty venues.
Related Video: SQUARERULE FURNITURE – Making a Dining Chair
Key Industrial Applications of dining chair supplier
Industry/Sector | Specific Application of dining chair supplier | Value/Benefit for the Business | Key Sourcing Considerations for this Application |
---|---|---|---|
Hospitality | Restaurant and Café Seating | Enhances customer experience and comfort | Durability, design aesthetics, and compliance with health regulations |
Education | School and University Dining Facilities | Promotes a conducive learning environment | Ergonomic design, ease of cleaning, and bulk purchasing options |
Corporate Offices | Employee Cafeterias and Break Rooms | Improves employee satisfaction and productivity | Space efficiency, modern design, and material quality |
Event Management | Banquet and Conference Seating | Maximizes space utilization and flexibility | Portability, stackability, and rental options available |
Residential Projects | Home Dining Areas and Outdoor Spaces | Personalizes living spaces and enhances usability | Style compatibility, weather resistance for outdoor use, and customization options |
How Are Dining Chairs Used in the Hospitality Industry?
In the hospitality sector, dining chair suppliers play a crucial role in providing seating solutions for restaurants and cafés. These chairs not only need to be aesthetically pleasing but also comfortable, as they directly influence the dining experience. Suppliers must consider the durability of materials used, as high foot traffic can lead to wear and tear. Additionally, compliance with health regulations regarding materials and finishes is essential, particularly in regions like Europe and the Middle East, where standards can be stringent.
What Are the Applications of Dining Chairs in Education?
In educational institutions, dining chair suppliers cater to school and university dining facilities, where the focus is on creating a conducive environment for students. Ergonomic design is paramount to support prolonged seating during meals, while ease of cleaning is critical for maintaining hygiene standards. International buyers from Africa and South America should prioritize suppliers that offer bulk purchasing options to accommodate large student bodies, ensuring cost-effectiveness without compromising quality.
How Do Dining Chairs Improve Corporate Office Environments?
Dining chair suppliers also serve corporate offices by furnishing employee cafeterias and break rooms. Comfortable seating can significantly enhance employee satisfaction and productivity during breaks. Buyers in the Middle East and Europe should consider sourcing chairs that are space-efficient and modern in design, aligning with the overall office aesthetic. Material quality is another important factor, as it affects longevity and maintenance costs, directly impacting the office’s bottom line.
What Role Do Dining Chairs Play in Event Management?
In the event management industry, dining chair suppliers provide essential seating for banquets and conferences. The ability to maximize space utilization and offer flexible seating arrangements is vital for event planners. Buyers should look for chairs that are portable and stackable, allowing for easy setup and breakdown. Rental options are also worth considering, especially for events that require a temporary setup, providing an economical solution without long-term commitment.
How Are Dining Chairs Customized for Residential Projects?
In residential projects, dining chair suppliers offer solutions for home dining areas and outdoor spaces. Personalization is key, as homeowners often seek styles that reflect their taste and complement their interior design. For outdoor use, weather resistance becomes a critical factor. Buyers should consider suppliers that provide customization options to ensure the chairs fit their specific needs, enhancing usability and aesthetic appeal in their living spaces.
3 Common User Pain Points for ‘dining chair supplier’ & Their Solutions
Scenario 1: Sourcing Quality Dining Chairs from International Suppliers
The Problem: B2B buyers often struggle to find dining chair suppliers that meet their quality standards while also offering competitive pricing. This is particularly challenging for buyers in regions like Africa and South America, where local suppliers may lack the necessary manufacturing capabilities. As a result, buyers face the risk of receiving subpar products that can damage their reputation and lead to costly returns or replacements.
The Solution: To effectively source high-quality dining chairs, buyers should conduct thorough research on potential suppliers. Start by verifying their certifications, such as ISO standards, which indicate compliance with international quality benchmarks. Utilize platforms like Alibaba or Global Sources to compare suppliers and read reviews from other businesses. Additionally, consider requesting samples before placing large orders to assess the quality firsthand. Establishing direct communication with suppliers can also help clarify specifications and expectations, ensuring that the products meet your quality needs.
Scenario 2: Navigating Shipping and Logistics Challenges
The Problem: For B2B buyers importing dining chairs from overseas, logistics can be a significant pain point. Issues such as long shipping times, unexpected tariffs, and customs clearance delays can disrupt business operations. Buyers from the Middle East and Europe may find themselves facing additional hurdles due to varying regulations and shipping practices, which can complicate the procurement process.
The Solution: To mitigate shipping and logistics challenges, it is crucial to partner with suppliers who have experience in international shipping. Inquire about their logistics capabilities and whether they can provide door-to-door shipping services. Additionally, working with a freight forwarder who specializes in furniture can streamline the customs process and provide insights into the best shipping routes and options. Buyers should also familiarize themselves with the import regulations in their country to avoid unexpected tariffs and delays. Maintaining a buffer in inventory can help manage the risk of shipping delays.
Scenario 3: Customization and Design Flexibility
The Problem: B2B buyers often require dining chairs that align with their specific branding or design preferences. However, many suppliers offer limited customization options, which can be frustrating for businesses looking to create a unique dining experience. This is particularly true for hospitality businesses, such as hotels and restaurants, where ambiance plays a crucial role in attracting customers.
The Solution: To overcome the customization challenge, buyers should seek out dining chair suppliers that specialize in bespoke solutions. When engaging with potential suppliers, clearly communicate your design needs, including materials, colors, and styles. Many manufacturers are willing to collaborate on custom projects if they understand the buyer’s vision and requirements. Consider leveraging design software or mood boards to illustrate your concepts effectively. Additionally, negotiate terms that allow for smaller initial orders of customized chairs to test market response before committing to larger quantities. This approach not only ensures that the final products meet your expectations but also reduces the risk of overstocking unwanted inventory.
Strategic Material Selection Guide for dining chair supplier
When considering materials for dining chairs, international B2B buyers must evaluate various factors that influence performance, cost, and suitability for specific markets. Below, we analyze four common materials used in dining chair manufacturing, focusing on their properties, advantages, limitations, and implications for buyers from diverse regions such as Africa, South America, the Middle East, and Europe.
What Are the Key Properties of Wood in Dining Chair Manufacturing?
Wood is a classic choice for dining chairs, known for its aesthetic appeal and structural integrity. Key properties include its natural strength and ability to withstand moderate pressure, making it suitable for everyday use. However, wood can be sensitive to temperature and humidity changes, which may lead to warping or cracking over time.
Pros:
– Aesthetically pleasing and customizable with finishes.
– Generally durable and can last for years with proper care.
– Renewable resource, aligning with sustainability trends.
Cons:
– Higher maintenance requirements compared to synthetic materials.
– Vulnerable to pests and moisture damage.
– Cost can vary significantly based on species and sourcing.
Impact on Application:
Wood chairs are compatible with a variety of dining settings, from rustic to modern. However, buyers must consider local climate conditions that may affect wood longevity.
Considerations for International Buyers:
Compliance with standards such as ASTM for structural integrity is essential. Buyers in regions like South Africa may prefer locally sourced woods to reduce costs and support local economies.
How Does Metal Compare as a Material for Dining Chairs?
Metal, particularly steel and aluminum, is increasingly popular in dining chair designs. Its key properties include high strength-to-weight ratio and excellent corrosion resistance, making it ideal for both indoor and outdoor settings.
Pros:
– Extremely durable and resistant to wear and tear.
– Low maintenance; easy to clean and maintain.
– Can be designed in various styles, including modern and industrial.
Cons:
– Can be cold and uncomfortable without proper cushioning.
– Risk of rusting if not treated or coated properly.
– Generally heavier than other materials, which may affect mobility.
Impact on Application:
Metal chairs are suitable for high-traffic areas and outdoor dining spaces. They can withstand various environmental conditions, making them a versatile choice.
Considerations for International Buyers:
Buyers should ensure compliance with safety standards like DIN in Europe or JIS in Japan. In regions like the Middle East, where outdoor dining is popular, corrosion-resistant coatings are crucial.
What Are the Benefits and Limitations of Plastic in Dining Chair Design?
Plastic is a versatile and cost-effective material for dining chairs. Key properties include lightweight design and resistance to moisture, making it ideal for diverse environments.
Pros:
– Highly affordable and available in numerous colors and designs.
– Resistant to moisture and easy to clean.
– Lightweight, facilitating easy movement and stacking.
Cons:
– Less durable than wood or metal; may crack or fade over time.
– Can feel less premium compared to natural materials.
– Environmental concerns regarding plastic waste.
Impact on Application:
Plastic chairs are perfect for casual dining settings and outdoor use, especially in regions with high humidity or rain.
Considerations for International Buyers:
Ensure compliance with environmental regulations regarding plastic use. Buyers in Europe may favor recycled plastics, while those in Africa may prioritize cost-effectiveness.
Why is Upholstered Fabric a Popular Choice for Dining Chairs?
Upholstered fabric chairs offer comfort and style, making them a popular choice for dining settings. Key properties include softness and a wide range of design options, but they require careful maintenance.
Pros:
– Comfortable and inviting, enhancing the dining experience.
– Available in various fabrics and colors, allowing for customization.
– Can be designed to match specific decor styles.
Cons:
– Requires regular cleaning and maintenance to prevent stains.
– May not be as durable as wood or metal, especially in high-use environments.
– Can be more expensive due to the cost of fabric and labor.
Impact on Application:
Upholstered chairs are ideal for upscale dining environments but may not be suitable for high-traffic commercial spaces without proper care.
Considerations for International Buyers:
Buyers should assess fabric durability and cleaning requirements, especially in regions with high humidity. Compliance with fire safety standards is also critical, particularly in commercial settings.
Summary Table of Material Selection for Dining Chair Suppliers
Material | Typical Use Case for dining chair supplier | Key Advantage | Key Disadvantage/Limitation | Relative Cost (Low/Med/High) |
---|---|---|---|---|
Wood | Traditional dining settings | Aesthetic appeal and durability | Vulnerable to moisture and pests | Medium |
Metal | Outdoor and high-traffic areas | High durability and low maintenance | Risk of rust without treatment | Medium |
Plastic | Casual and outdoor dining | Lightweight and affordable | Less durable and environmental concerns | Low |
Upholstered Fabric | Upscale dining environments | Comfort and customization | Requires maintenance and can be costly | Medium to High |
This strategic material selection guide provides valuable insights for international B2B buyers, helping them make informed decisions based on performance, cost, and regional considerations.
In-depth Look: Manufacturing Processes and Quality Assurance for dining chair supplier
What Are the Key Manufacturing Processes for Dining Chair Suppliers?
When sourcing dining chairs from international suppliers, understanding their manufacturing processes is crucial. The production of dining chairs typically involves several stages: material preparation, forming, assembly, and finishing. Each stage plays a vital role in ensuring that the final product meets quality and durability standards.
Material Preparation: What Materials Are Used in Dining Chair Manufacturing?
The first step in the manufacturing process involves selecting and preparing materials. Common materials used in dining chair production include:
- Wood: Solid wood, plywood, and engineered wood are frequently used due to their strength and aesthetic appeal.
- Metal: Steel and aluminum frames are often employed for modern designs, offering durability and a sleek look.
- Upholstery: Fabrics or leather are selected based on design requirements and comfort considerations.
Buyers should inquire about the source of these materials to ensure sustainability and compliance with local regulations. This is particularly important for buyers from regions like Africa and South America, where eco-friendly sourcing is increasingly prioritized.
How Are Dining Chairs Formed During Manufacturing?
The forming stage involves shaping the materials into the desired chair components. Various techniques are employed:
- Cutting: Precision cutting tools are used to create chair parts from sheets of wood or metal.
- Molding: For plastic chairs, molds are created to shape the material into the final product.
- Joinery Techniques: Methods like dovetailing, mortise and tenon, and dowel joints are crucial for wooden chairs, enhancing strength and durability.
Buyers should assess whether suppliers use advanced technology, such as CNC machines, for precision cutting and shaping, as this can significantly impact the quality of the finished product.
What Does the Assembly Process Entail for Dining Chairs?
During assembly, the pre-formed components are put together. This process can vary significantly based on the design complexity:
- Mechanical Fastening: Screws, bolts, and brackets are commonly used for assembling metal and wooden frames.
- Adhesives: High-strength adhesives may be employed in conjunction with mechanical fasteners to enhance stability.
- Upholstery Application: The final stage of assembly involves attaching the upholstery, which can be done by hand or with automated machines.
For B2B buyers, understanding the assembly techniques used by suppliers can provide insights into the durability and longevity of the chairs.
What Quality Assurance Measures Should Dining Chair Suppliers Implement?
Quality assurance is a critical aspect of the manufacturing process, ensuring that dining chairs meet international standards and buyer expectations. International buyers should look for suppliers who adhere to recognized quality standards.
Which International Standards Should Dining Chair Suppliers Comply With?
Suppliers should ideally comply with several international quality standards, including:
- ISO 9001: This standard focuses on quality management systems and is essential for ensuring consistent quality in manufacturing processes.
- CE Marking: Required for products sold in the European Economic Area, it indicates that the product meets safety and environmental protection standards.
- API Standards: For suppliers using metal components, adhering to API standards can be crucial for quality assurance.
These certifications not only enhance product reliability but also serve as assurance for buyers regarding the supplier’s commitment to quality.
What Are the Critical Quality Control Checkpoints in Dining Chair Manufacturing?
Quality control (QC) involves several checkpoints throughout the manufacturing process:
- Incoming Quality Control (IQC): This initial checkpoint ensures that raw materials meet specified standards before production begins.
- In-Process Quality Control (IPQC): Continuous monitoring during the manufacturing process helps detect any deviations from quality standards early.
- Final Quality Control (FQC): The final inspection ensures that the assembled chairs meet all specifications and quality requirements before shipping.
By understanding these checkpoints, buyers can better evaluate suppliers’ commitment to quality.
How Can B2B Buyers Verify Supplier Quality Assurance Practices?
To ensure that a supplier adheres to stringent quality control measures, B2B buyers should consider the following verification methods:
- Audits: Conducting regular audits of supplier facilities can provide insights into their manufacturing processes and quality assurance practices.
- Quality Reports: Requesting detailed quality reports can help buyers understand the QC measures implemented by the supplier.
- Third-Party Inspections: Engaging independent inspection services can provide an unbiased assessment of the supplier’s quality assurance practices.
This proactive approach can mitigate risks associated with sourcing dining chairs, especially for buyers from regions with diverse manufacturing standards.
What Testing Methods Are Commonly Used in Dining Chair Manufacturing?
Quality assurance also involves rigorous testing methods to ensure that dining chairs can withstand daily use. Common testing methods include:
- Load Testing: This involves applying weight to the chair to assess its strength and stability.
- Durability Testing: Chairs are subjected to repeated use scenarios to evaluate wear and tear.
- Safety Testing: Ensuring that there are no sharp edges or hazardous materials is crucial for compliance with safety standards.
Understanding these testing methods enables buyers to make informed decisions when selecting suppliers.
What Nuances Should International B2B Buyers Consider Regarding QC and Certification?
When sourcing dining chairs from suppliers across different regions, it’s important to consider the nuances of quality certification and standards:
- Regional Compliance: Different regions may have specific compliance requirements. For example, suppliers in Europe must adhere to CE marking, while suppliers in Africa may have different local standards.
- Cultural Practices: Understanding cultural practices related to manufacturing can help buyers gauge the reliability of suppliers.
- Certification Validity: Buyers should verify the validity of certifications by checking with the issuing organizations to avoid potential issues.
By being aware of these nuances, international B2B buyers can navigate the complexities of sourcing dining chairs more effectively, ensuring that they partner with reliable suppliers committed to quality assurance.
Practical Sourcing Guide: A Step-by-Step Checklist for ‘dining chair supplier’
This guide serves as a practical checklist for international B2B buyers seeking reliable dining chair suppliers. Whether you’re in Africa, South America, the Middle East, or Europe, following these steps will help streamline your sourcing process and ensure you partner with a supplier that meets your business needs.
Step 1: Define Your Technical Specifications
Before initiating your search, it’s crucial to outline the specific requirements for the dining chairs you need. Consider materials, design, dimensions, and functionality to align with your market’s preferences. A well-defined specification helps you filter suppliers and ensures that the products meet your standards.
Step 2: Conduct Market Research for Suppliers
Identify potential suppliers through online directories, trade shows, and industry networks. Look for suppliers with a proven track record in the dining chair sector. Research their reputation, customer reviews, and market presence to gauge their reliability and performance.
Step 3: Evaluate Potential Suppliers
Before committing, vet suppliers thoroughly. Request company profiles, case studies, and references from buyers in a similar industry or region. Don’t just rely on their website; instead, assess their capacity to meet your volume needs and delivery timelines.
- Check for certifications: Ensure suppliers hold relevant certifications for quality and safety standards, particularly if you are importing to regions with stringent regulations.
Step 4: Request Samples for Quality Assessment
It’s vital to request product samples before finalizing any deals. This allows you to assess the craftsmanship, materials, and overall quality of the dining chairs. Pay attention to details such as finishes, sturdiness, and comfort, as these factors will influence customer satisfaction and retention.
Step 5: Negotiate Pricing and Terms
Once you’ve shortlisted potential suppliers, initiate discussions on pricing and payment terms. Consider factors such as bulk discounts, shipping costs, and payment options. Be transparent about your budget constraints while also ensuring the quality of the chairs is not compromised.
Step 6: Understand the Supply Chain Logistics
Evaluate the logistics of working with your chosen supplier. Consider factors like lead times, shipping methods, and customs regulations specific to your country. Understanding these elements will help you anticipate delivery schedules and manage inventory levels effectively.
Step 7: Establish a Clear Communication Plan
Effective communication is key to a successful supplier relationship. Set up regular check-ins to discuss order status, address concerns, and provide feedback. This proactive approach helps to build trust and ensures both parties are aligned throughout the sourcing process.
By following this practical sourcing checklist, you can navigate the complexities of finding a reliable dining chair supplier and make informed decisions that align with your business goals.
Comprehensive Cost and Pricing Analysis for dining chair supplier Sourcing
What Are the Key Cost Components in Dining Chair Supplier Sourcing?
When sourcing dining chairs, understanding the cost structure is essential for international B2B buyers. The main cost components include:
-
Materials: The choice of materials significantly impacts the overall price. Common materials for dining chairs include wood, metal, plastic, and upholstery fabrics. Each material has its own cost implications, with wood typically being more expensive than plastic.
-
Labor: Labor costs vary widely depending on the supplier’s location. In regions with lower wage standards, like some parts of Africa and South America, labor costs may be significantly lower than in Europe or the Middle East. However, the skill level of workers can also affect the quality of craftsmanship.
-
Manufacturing Overhead: This includes indirect costs associated with the production process, such as utilities, rent, and administrative expenses. Suppliers with efficient operations may offer better pricing.
-
Tooling: Initial setup costs for molds and machinery can be substantial, especially for custom-designed chairs. This cost is typically amortized over larger production runs, so minimum order quantities (MOQs) can significantly influence pricing.
-
Quality Control (QC): Ensuring that the chairs meet international quality standards can add to costs. Suppliers who invest in rigorous QC processes might charge higher prices, but this can lead to better long-term value through reduced returns and increased customer satisfaction.
-
Logistics: Shipping costs, including freight, insurance, and customs duties, can vary dramatically based on the supplier’s location and the buyer’s destination. International buyers should consider these costs when evaluating supplier pricing.
-
Margin: Suppliers typically include a profit margin in their pricing, which can vary based on market conditions and competition. Understanding the typical margin for dining chair suppliers in different regions can help buyers negotiate better deals.
How Do Price Influencers Affect Dining Chair Sourcing?
Several factors can influence the price of dining chairs beyond the basic cost structure:
-
Volume/MOQ: Larger orders usually lead to lower per-unit costs. Suppliers may offer discounts for bulk orders, making it essential for buyers to assess their needs accurately.
-
Specifications and Customization: Custom designs and specific requirements can lead to higher costs. Buyers should weigh the benefits of customization against the potential price increase.
-
Materials and Quality Certifications: Higher quality materials and certifications (like ISO or environmental certifications) can increase costs. Buyers must balance quality with budget constraints.
-
Supplier Factors: The reputation, reliability, and location of the supplier can also influence pricing. Established suppliers with a track record of quality may charge more.
-
Incoterms: Understanding the chosen Incoterms (International Commercial Terms) is vital. Terms like FOB (Free on Board) or CIF (Cost, Insurance, and Freight) can affect total costs and responsibilities in shipping.
What Are the Best Negotiation Tips for International B2B Buyers?
To optimize sourcing costs, international buyers should consider the following strategies:
-
Conduct Comprehensive Market Research: Before negotiating, gather data on industry pricing standards and competitor offers. This knowledge can empower buyers during discussions.
-
Leverage Total Cost of Ownership (TCO): When evaluating suppliers, consider not just the initial price but the total cost over the product’s lifecycle, including maintenance and potential replacement costs.
-
Build Strong Relationships: Developing a rapport with suppliers can lead to better pricing and terms. Long-term partnerships often yield benefits like priority service and reduced prices.
-
Be Transparent About Your Needs: Clearly communicating your requirements and budget can help suppliers tailor their offerings more effectively.
-
Negotiate Payment Terms: Flexible payment terms can ease cash flow and improve overall cost efficiency. Explore options like extended payment periods or discounts for early payments.
Conclusion
Understanding the comprehensive cost structure and pricing influences in dining chair supplier sourcing is crucial for international B2B buyers. By focusing on the various cost components, price influencers, and strategic negotiation tips, buyers can make informed decisions that align with their budget and quality expectations. Always remember to obtain indicative prices and conduct thorough due diligence to ensure the best possible outcomes in your sourcing endeavors.
Alternatives Analysis: Comparing dining chair supplier With Other Solutions
When considering a dining chair supplier, B2B buyers must evaluate various alternatives that may suit their needs. These alternatives can range from different types of suppliers to innovative technologies that fulfill similar roles. Understanding the strengths and weaknesses of each option helps in making an informed decision that aligns with business objectives.
Comparison Aspect | Dining Chair Supplier | Alternative 1: Custom Furniture Manufacturer | Alternative 2: Rental Furniture Services |
---|---|---|---|
Performance | High-quality, durable chairs tailored for specific needs | Tailored designs that meet specific aesthetics and functionality | Flexible options with quick availability, but quality may vary |
Cost | Moderate to high initial investment depending on materials | Generally higher due to customization | Lower upfront costs but recurring rental fees can add up |
Ease of Implementation | Straightforward ordering process with established suppliers | Longer lead times for design and production | Quick setup, but terms and conditions can complicate usage |
Maintenance | Low maintenance; durable materials | Varies; bespoke items may require special care | Minimal maintenance; furniture is typically well-maintained by the service |
Best Use Case | Ideal for businesses seeking a permanent solution | Best for unique spaces or specific brand alignment | Suitable for short-term needs or events with changing requirements |
What Are the Advantages and Disadvantages of Custom Furniture Manufacturers?
Custom furniture manufacturers offer tailored solutions that allow businesses to specify every detail, from the materials used to the design aesthetics. The primary advantage of this option is the ability to create unique pieces that align with a brand’s identity. However, the downside is that this can come with a significant cost and longer lead times for delivery. Businesses with a clear vision and a larger budget may find this a worthwhile investment.
How Do Rental Furniture Services Compare in Terms of Flexibility?
Rental furniture services present an appealing alternative for companies that require flexibility. These services allow businesses to rent furniture for short-term needs, such as events or temporary offices. The main advantage is lower upfront costs and the ability to change styles quickly. However, the quality of rental furniture can vary significantly between providers, and ongoing rental fees can accumulate, potentially making it more expensive over time.
Conclusion: How Can B2B Buyers Choose the Right Solution for Their Needs?
When selecting between a dining chair supplier and its alternatives, B2B buyers should consider their specific requirements, including budget constraints, the intended duration of use, and the importance of brand alignment. A permanent solution like a dining chair supplier may be ideal for long-term investments, while custom manufacturers can offer unique designs for specific needs. Conversely, rental services can provide flexibility for businesses with dynamic requirements. By carefully evaluating these options against their operational goals, international buyers can make a decision that best suits their needs.
Essential Technical Properties and Trade Terminology for dining chair supplier
What Are the Key Technical Properties of Dining Chairs?
When sourcing dining chairs, understanding the technical properties is crucial for ensuring quality and durability. Here are some of the most important specifications to consider:
1. Material Grade: Why Does It Matter?
The material grade refers to the quality of the raw materials used in the construction of dining chairs. Common materials include solid wood, plywood, metal, and upholstered fabrics. A higher material grade typically implies better durability, aesthetics, and resistance to wear and tear. For international buyers, selecting the right material is essential as it affects not only the chair’s lifespan but also its suitability for various climates and usage scenarios.
2. Weight Capacity: How Much Can It Hold?
Weight capacity indicates the maximum load a dining chair can safely support. This specification is particularly important for buyers targeting markets with diverse body types and usage conditions. Chairs designed for heavier weight limits are essential in ensuring customer satisfaction and minimizing returns. Always verify the weight capacity to align with your target demographic’s needs.
3. Dimensions and Tolerance: What Are the Standard Sizes?
Dimensions encompass the height, width, depth, and seat height of the dining chair. Tolerance refers to the allowable variation in these dimensions during manufacturing. Accurate dimensions ensure that the chairs fit well in various dining environments, while proper tolerance levels guarantee that even slight deviations do not compromise functionality. For B2B buyers, understanding these specifications is crucial for space planning and compliance with local regulations.
4. Finish Type: How Does It Affect Maintenance?
The finish type describes the protective coating applied to the chair surface, such as lacquer, varnish, or oil. This specification impacts both the aesthetics and maintenance requirements of the chair. For instance, certain finishes may be easier to clean but could require more frequent touch-ups. Buyers should consider the end-use environment—whether indoor or outdoor—and select finishes that are suitable for their specific applications.
What Are Common Trade Terms Used in the Dining Chair Supply Industry?
Navigating the world of B2B dining chair procurement requires familiarity with industry jargon. Here are some essential terms:
1. OEM (Original Equipment Manufacturer): What Does It Entail?
OEM refers to a company that manufactures products for another brand, which then sells them under its own name. Understanding OEM relationships is vital for B2B buyers who want to source unique designs without incurring high development costs. This term is especially relevant for buyers looking to customize dining chairs to fit specific branding requirements.
2. MOQ (Minimum Order Quantity): Why Is It Significant?
MOQ is the smallest quantity of a product that a supplier is willing to sell. This term is crucial for international buyers as it directly affects inventory management and cash flow. Knowing the MOQ can help you assess whether a supplier aligns with your business scale and purchasing strategy.
3. RFQ (Request for Quotation): How to Use It Effectively?
An RFQ is a document used by buyers to solicit price quotes from suppliers. It typically includes specifications for the desired products, quantities, and delivery timelines. For B2B buyers, crafting a clear and detailed RFQ is essential to receiving accurate quotes and ensuring that suppliers understand your requirements.
4. Incoterms (International Commercial Terms): What Should You Know?
Incoterms are international rules that define the responsibilities of buyers and sellers regarding shipping and delivery. Understanding these terms is critical for international buyers to clarify who bears the risk and costs during transportation. Familiarity with Incoterms can help avoid disputes and ensure smoother transactions.
5. Lead Time: How Long Will It Take?
Lead time refers to the time taken from placing an order to receiving the product. It is crucial for planning inventory and meeting customer demands. Buyers should communicate their lead time expectations to suppliers to ensure timely delivery and maintain competitive advantage in their markets.
By grasping these essential technical properties and trade terminologies, international B2B buyers can make informed decisions when sourcing dining chairs, ultimately leading to successful partnerships and customer satisfaction.
Navigating Market Dynamics and Sourcing Trends in the dining chair supplier Sector
What Are the Current Market Dynamics Affecting Dining Chair Suppliers?
The dining chair supplier market is experiencing a dynamic shift, largely driven by evolving consumer preferences, technological advancements, and changing economic landscapes. Global demand for dining chairs is projected to grow as urbanization and disposable incomes rise, particularly in regions like Africa and South America, where a burgeoning middle class seeks stylish yet functional furniture. In Europe and the Middle East, there is an increasing inclination toward luxury and bespoke designs, influenced by trends in interior design and hospitality.
Emerging B2B technologies are revolutionizing the sourcing process. For instance, digital platforms facilitate direct communication between buyers and manufacturers, enhancing transparency and efficiency. Virtual reality (VR) and augmented reality (AR) tools are becoming popular in showcasing product designs, allowing buyers to visualize furniture in their spaces before making decisions. Additionally, the rise of e-commerce and online marketplaces is enabling international buyers to access a wider range of suppliers, streamlining the procurement process.
International buyers should also be aware of fluctuating material costs, particularly for wood and upholstery, which can impact pricing and availability. Trade policies and tariffs between countries can further complicate sourcing strategies, making it essential for buyers to stay informed about geopolitical developments that may affect their supply chains.
How Is Sustainability Shaping the Dining Chair Supplier Sector?
Sustainability has become a cornerstone in the dining chair supplier sector, with buyers increasingly prioritizing environmentally responsible products. The environmental impact of furniture production is significant, prompting a shift towards sustainable materials and manufacturing processes. Suppliers are now seeking certifications such as Forest Stewardship Council (FSC) and Global Organic Textile Standard (GOTS) to demonstrate their commitment to ethical sourcing.
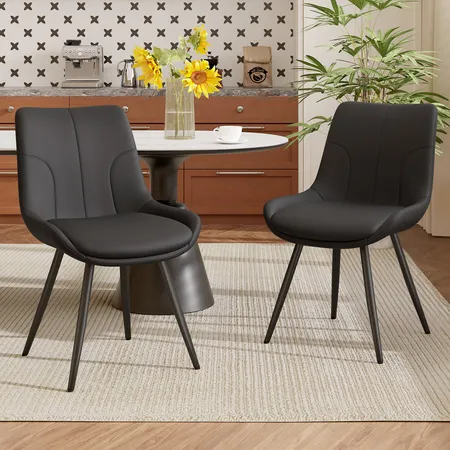
A stock image related to dining chair supplier.
Ethical supply chains are crucial for B2B buyers who wish to align their purchasing decisions with corporate social responsibility (CSR) goals. Sustainable practices not only minimize environmental footprints but also resonate with consumers who are more inclined to support brands that prioritize eco-friendliness. Additionally, suppliers that utilize recycled materials or adopt energy-efficient production methods are gaining a competitive edge in the market.
For buyers in regions like Africa and South America, where local sourcing can reduce transportation emissions and support local economies, embracing sustainability can also translate into cost savings. International buyers should actively seek partnerships with suppliers that prioritize sustainability, ensuring that their procurement practices reflect both ethical values and market demands.
What Is the Historical Context of Dining Chair Supply?
The evolution of the dining chair supply sector can be traced back to the industrial revolution, which marked a significant shift from handcrafted to mass-produced furniture. In the early 20th century, dining chairs became more accessible to the average consumer, thanks to advancements in manufacturing techniques and materials. Post-World War II, the demand surged as economies recovered, and homeownership rates increased, particularly in Europe and North America.
In recent decades, the sector has seen a diversification of styles and materials, influenced by cultural trends and global design movements. The rise of globalization has enabled suppliers to source materials from various parts of the world, enhancing the variety of dining chairs available in the market. Today, the focus is not only on aesthetics and functionality but also on sustainability and ethical sourcing, reflecting the changing priorities of both consumers and B2B buyers.
Understanding this historical context is essential for international buyers as they navigate the current landscape, allowing them to make informed sourcing decisions that align with both market trends and consumer expectations.
Frequently Asked Questions (FAQs) for B2B Buyers of dining chair supplier
-
How do I ensure the quality of dining chairs from international suppliers?
To ensure quality when sourcing dining chairs from international suppliers, conduct thorough research and vetting. Request samples to assess materials and craftsmanship firsthand. Check for certifications that meet international standards, such as ISO or ANSI. Additionally, establish clear quality assurance processes in your purchase agreements, specifying your expectations for quality and durability. Consider working with third-party inspection services to verify product quality before shipment. -
What is the best way to assess dining chair suppliers for reliability?
Assessing dining chair suppliers for reliability involves a multi-faceted approach. Start by examining their business history and customer reviews, focusing on their experience in the industry. Look for suppliers with a proven track record of on-time delivery and responsiveness to inquiries. Utilize platforms like Alibaba or Global Sources for verified supplier ratings. Additionally, consider visiting their manufacturing facilities if possible, or request references from other businesses that have worked with them. -
What are the typical minimum order quantities (MOQs) for dining chairs?
Minimum order quantities (MOQs) for dining chairs can vary significantly based on the supplier and the type of chairs being ordered. Generally, MOQs may range from 50 to 500 units, depending on customization options and material specifications. It’s advisable to discuss MOQs upfront and negotiate terms that fit your business needs, especially if you’re a smaller retailer or startup. Some suppliers may offer flexible MOQs for first-time orders or bulk purchases. -
How can I customize dining chairs for my brand?
Customizing dining chairs to align with your brand can be achieved by working closely with suppliers who offer bespoke services. Discuss your specific requirements, such as materials, colors, and design features. Many suppliers have in-house design teams that can assist in creating prototypes. Be prepared to provide detailed specifications and possibly higher MOQs for custom designs. Make sure to request samples to ensure the final product meets your expectations before full-scale production. -
What payment terms should I expect when sourcing dining chairs internationally?
Payment terms can vary widely among suppliers, but common practices include a deposit (usually 30-50%) upfront and the balance upon shipment. Some suppliers may offer net terms (e.g., net 30 or net 60), especially for established buyers. Ensure you discuss and agree on payment methods, such as wire transfers, letters of credit, or PayPal, which may offer varying levels of buyer protection. Always clarify any additional costs that may arise, such as taxes and shipping fees. -
What logistics considerations should I keep in mind when importing dining chairs?
When importing dining chairs, logistics considerations are crucial for timely delivery. Evaluate shipping options, including air freight for speed versus sea freight for cost-effectiveness. Understand the customs regulations and import duties applicable in your country to avoid unexpected delays or costs. Collaborate with a reliable freight forwarder who can assist with documentation and ensure compliance with international shipping laws. Additionally, consider warehousing solutions if you anticipate high demand. -
How can I effectively communicate my requirements to a dining chair supplier?
Effective communication with a dining chair supplier involves being clear and specific about your needs. Provide detailed specifications, including dimensions, materials, design preferences, and expected delivery timelines. Use visual aids, such as sketches or mood boards, to convey your ideas more effectively. Establish regular check-ins throughout the production process to ensure alignment and address any concerns promptly. Building a good rapport with your supplier can facilitate smoother transactions. -
What should I do if I receive defective dining chairs?
If you receive defective dining chairs, act swiftly to address the issue. Document the defects with clear photographs and detailed descriptions, and communicate your concerns to the supplier immediately. Refer to your purchase agreement for warranty or return policies. Most reputable suppliers will have processes in place for handling defects, which may include replacements, refunds, or repairs. Maintain a professional tone in your communication to foster a cooperative resolution.
Important Disclaimer & Terms of Use
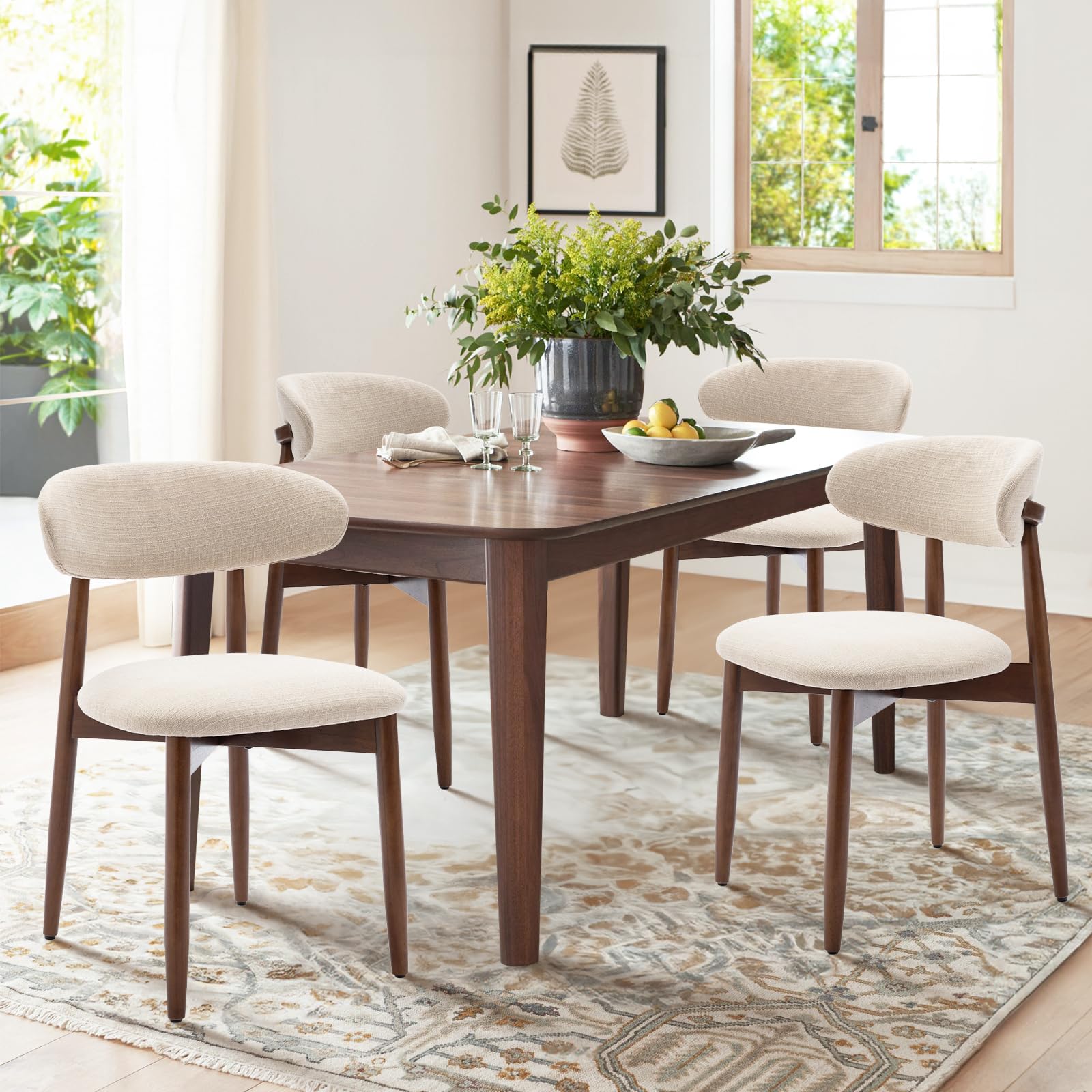
A stock image related to dining chair supplier.
⚠️ Important Disclaimer
The information provided in this guide, including content regarding manufacturers, technical specifications, and market analysis, is for informational and educational purposes only. It does not constitute professional procurement advice, financial advice, or legal advice.
While we have made every effort to ensure the accuracy and timeliness of the information, we are not responsible for any errors, omissions, or outdated information. Market conditions, company details, and technical standards are subject to change.
B2B buyers must conduct their own independent and thorough due diligence before making any purchasing decisions. This includes contacting suppliers directly, verifying certifications, requesting samples, and seeking professional consultation. The risk of relying on any information in this guide is borne solely by the reader.
Strategic Sourcing Conclusion and Outlook for dining chair supplier
In navigating the complexities of sourcing dining chairs, international B2B buyers must prioritize strategic sourcing as a pivotal aspect of their procurement process. By understanding market dynamics and leveraging supplier relationships, businesses can ensure not only cost-effectiveness but also quality and timely delivery. Key takeaways include the importance of conducting thorough supplier evaluations, emphasizing sustainability, and maintaining flexibility to adapt to market changes.
How can international buyers enhance their sourcing strategies for dining chairs? By focusing on building long-term partnerships with suppliers, buyers can gain access to innovative designs and custom solutions that meet specific market demands. Additionally, engaging with suppliers from diverse regions such as Africa, South America, the Middle East, and Europe can create unique competitive advantages, tapping into local craftsmanship and materials.
Looking forward, the landscape of dining chair sourcing is poised for transformation. As consumer preferences evolve and sustainability becomes a driving force, buyers must stay ahead of trends and invest in suppliers who prioritize eco-friendly practices. Now is the time to reassess your sourcing strategies and align with suppliers who can provide not only quality products but also insights into future market trends. Embrace the opportunities ahead and secure your position in the global market.