The Ultimate Guide to Current Transformer Manufacturer (2025)
Introduction: Navigating the Global Market for current transformer manufacturer
In today’s interconnected world, sourcing the right current transformer manufacturer is pivotal for businesses aiming to enhance their electrical systems’ efficiency and reliability. However, with a plethora of options available globally, international B2B buyers, particularly those from Africa, South America, the Middle East, and Europe, face the daunting challenge of selecting a supplier that meets both technical specifications and budget constraints. This guide aims to simplify that process by offering a thorough exploration of the current transformer market, including various types, applications, and critical factors to consider when evaluating suppliers.
Throughout this guide, we will delve into essential topics such as the different types of current transformers, their specific applications across industries, and expert strategies for vetting suppliers to ensure quality and compliance with international standards. Additionally, we will provide insights into pricing structures, helping you to navigate the complexities of cost-effectiveness in your sourcing decisions.
By equipping you with actionable insights and expert knowledge, this comprehensive resource empowers international B2B buyers to make informed decisions that align with their operational goals. Whether you’re based in Nigeria, Thailand, or anywhere in between, understanding the nuances of the current transformer market will enable you to forge partnerships that drive innovation and efficiency in your electrical infrastructure.
Understanding current transformer manufacturer Types and Variations
Type Name | Key Distinguishing Features | Primary B2B Applications | Brief Pros & Cons for Buyers |
---|---|---|---|
Wound Current Transformers | Directly connected to the primary circuit, offering high accuracy. | Power generation, industrial applications. | Pros: High accuracy, robust design. Cons: Higher initial cost. |
Toroidal Current Transformers | Ring-shaped design, compact and lightweight. | Renewable energy systems, compact machinery. | Pros: Space-saving, lower weight. Cons: Limited current range. |
Split-Core Current Transformers | Easy installation without disconnecting the circuit. | Retrofit applications, maintenance sectors. | Pros: Quick installation, flexible use. Cons: Potential accuracy loss. |
Instrument Current Transformers | Designed for measuring and metering applications. | Energy monitoring, substations. | Pros: High precision, reliable data. Cons: May require calibration. |
Rogowski Coil Current Transformers | Flexible coil design, suitable for large currents. | Industrial automation, transient measurement. | Pros: Wide current range, non-intrusive. Cons: Requires signal conditioning. |
What Are Wound Current Transformers and When Should B2B Buyers Consider Them?
Wound current transformers (WCTs) are characterized by their direct connection to the primary circuit, which enhances their accuracy and reliability. These transformers are ideal for high-voltage applications in power generation and industrial settings. For B2B buyers, the primary consideration should be the initial investment, as WCTs often have a higher upfront cost. However, their durability and precision make them a worthwhile investment for businesses prioritizing long-term operational efficiency.
How Do Toroidal Current Transformers Benefit B2B Buyers?
Toroidal current transformers feature a ring-shaped design that makes them compact and lightweight, allowing for easy installation in space-constrained environments. They are particularly suited for renewable energy applications and compact machinery. B2B buyers looking for efficient solutions in limited spaces will find toroidal transformers appealing. However, it’s essential to note that they may have a limited current range, which could affect their applicability in larger installations.
Why Are Split-Core Current Transformers Ideal for Retrofit Applications?
Split-core current transformers offer unique advantages for retrofit applications due to their ability to be installed without disconnecting the primary circuit. This feature is particularly beneficial in maintenance sectors where downtime needs to be minimized. B2B buyers should weigh the ease of installation against the potential for slight accuracy loss, especially in critical measurement scenarios. These transformers provide flexibility, making them a smart choice for businesses looking to upgrade existing systems.
What Should B2B Buyers Know About Instrument Current Transformers?
Instrument current transformers are specifically designed for metering and measurement applications, providing high precision in energy monitoring and substations. For B2B buyers, the reliability of data is paramount, making these transformers an essential component in energy management systems. However, they may require periodic calibration to maintain accuracy, which should be factored into the overall cost of ownership.
How Do Rogowski Coil Current Transformers Enhance Measurement Capabilities?
Rogowski coil current transformers are known for their flexible design, allowing them to handle large currents effectively. This makes them suitable for industrial automation and transient measurement applications. B2B buyers will appreciate the non-intrusive nature of these transformers, which simplifies installation. However, it’s crucial to consider that they require additional signal conditioning for accurate measurements, which could add complexity to the installation process.
Related Video: What is Instrument Transformer | Current Transformer and Voltage Transformer
Key Industrial Applications of current transformer manufacturer
Industry/Sector | Specific Application of Current Transformer Manufacturer | Value/Benefit for the Business | Key Sourcing Considerations for this Application |
---|---|---|---|
Energy and Utilities | Power Generation and Distribution Monitoring | Enhanced grid reliability and efficiency | Compliance with local regulations and standards; supplier certifications |
Manufacturing | Motor Protection and Control Systems | Improved operational safety and reduced downtime | Compatibility with existing systems; availability of technical support |
Renewable Energy | Wind and Solar Energy Integration | Maximized energy output and optimized grid connection | Adaptability to diverse environmental conditions; efficiency ratings |
Transportation and Logistics | Electric Vehicle Charging Infrastructure | Support for sustainable transportation solutions | Scalability of solutions; integration with smart grid technologies |
Mining and Metals | Load Monitoring in Heavy Machinery | Increased productivity and reduced operational costs | Robustness in harsh environments; availability of spare parts |
How is Current Transformer Used in Power Generation and Distribution Monitoring?
In the energy and utilities sector, current transformers (CTs) are essential for monitoring power generation and distribution systems. They provide accurate measurement of current flowing through electrical lines, enabling utilities to manage load and detect faults quickly. This application is vital for enhancing grid reliability and efficiency, especially in regions with fluctuating energy demands. International buyers should ensure that the manufacturers comply with local regulations and possess necessary certifications, as this impacts the reliability of the CTs in their specific markets, such as in Nigeria or Brazil.
What Role Do Current Transformers Play in Motor Protection and Control Systems?
In manufacturing, current transformers are crucial for motor protection and control systems. They help monitor the operational state of electric motors, allowing for early detection of overloads or faults that could lead to equipment failure. This application not only improves operational safety but also reduces downtime, which can significantly impact productivity. Buyers should consider compatibility with existing systems and the availability of technical support when sourcing CTs to ensure seamless integration into their operations.
How Do Current Transformers Enhance Renewable Energy Integration?
Current transformers are increasingly used in renewable energy applications, particularly in wind and solar energy integration. They are instrumental in measuring the output current and ensuring efficient connection to the grid. This maximizes energy output and stabilizes the grid, which is particularly important in regions like South America and the Middle East where renewable energy initiatives are growing. Buyers should seek CTs that are adaptable to diverse environmental conditions and have high efficiency ratings to ensure optimal performance.
What Benefits Do Current Transformers Provide in Electric Vehicle Charging Infrastructure?
In the transportation and logistics sector, current transformers facilitate the development of electric vehicle (EV) charging infrastructure. They are used to monitor current flow in charging stations, ensuring safe and efficient energy distribution. This application supports the transition to sustainable transportation solutions, which is a growing priority in Europe and Africa. Buyers should focus on the scalability of solutions and their integration with smart grid technologies to accommodate future expansions in EV infrastructure.
How Are Current Transformers Utilized for Load Monitoring in Mining and Metals?
In the mining and metals industry, current transformers are employed for load monitoring in heavy machinery. They help track the operational load of equipment, providing data that can lead to increased productivity and reduced operational costs. Given the harsh environments typical of mining operations, buyers must prioritize the robustness of the CTs and the availability of spare parts to minimize downtime and maintain operational efficiency.
3 Common User Pain Points for ‘current transformer manufacturer’ & Their Solutions
Scenario 1: Inconsistent Quality of Current Transformers
The Problem: Many B2B buyers encounter significant frustration when sourcing current transformers due to inconsistent product quality. This issue is particularly acute in regions like Africa and South America, where local suppliers may not adhere to international standards. Such variability can lead to operational inefficiencies, increased maintenance costs, and even project delays. In some cases, buyers may find themselves stuck with faulty units that compromise the performance of their electrical systems, resulting in costly downtime and reputational damage.
The Solution: To mitigate quality inconsistencies, international buyers should prioritize sourcing from manufacturers that have established quality assurance processes and certifications, such as ISO 9001. Conducting thorough due diligence is essential; this includes reviewing the manufacturer’s history, customer testimonials, and case studies that demonstrate their track record in quality management. Additionally, consider requesting samples or trial orders before committing to larger purchases. Engaging in direct communication with the manufacturer about their production methods and quality control measures will also provide insight into their reliability. Establishing long-term partnerships with reputable manufacturers who are committed to quality can lead to more consistent supply and better overall performance.
Scenario 2: Difficulty in Understanding Technical Specifications
The Problem: B2B buyers often face challenges when trying to interpret the technical specifications of current transformers, which can vary significantly between manufacturers. This lack of clarity can lead to poor purchasing decisions, resulting in equipment that does not meet the specific needs of their operations. For instance, mismatches in voltage ratings, frequency specifications, or insulation types can cause integration issues and safety hazards in electrical systems, particularly in regions with varying infrastructure standards.
The Solution: To overcome the challenges of understanding technical specifications, buyers should invest time in educating themselves about the essential parameters of current transformers. Engaging with technical experts or consultants who specialize in electrical engineering can provide invaluable insights into the selection process. Buyers should also request detailed product datasheets from manufacturers, which should clearly outline all relevant specifications and applications. Additionally, participating in webinars or industry trade shows can enhance understanding and provide opportunities to ask manufacturers direct questions about their products. Building a relationship with the manufacturer’s technical support team can also facilitate easier communication regarding complex specifications and ensure that buyers make informed decisions.
Scenario 3: Lack of After-Sales Support and Service
The Problem: Another common pain point for B2B buyers is the inadequate after-sales support provided by current transformer manufacturers. Once a purchase is made, many buyers find themselves without sufficient guidance on installation, maintenance, or troubleshooting, which can lead to operational challenges. In emerging markets, this lack of support can be even more pronounced, leaving companies vulnerable to equipment failures without immediate recourse.
The Solution: To address this issue, buyers should prioritize manufacturers that offer comprehensive after-sales support, including installation services, maintenance training, and access to technical assistance. Before finalizing a purchase, inquire about the manufacturer’s support policies and the availability of local representatives who can provide on-site assistance when needed. Establishing a service agreement that outlines the scope of support can also be beneficial. Additionally, buyers should leverage online resources such as instructional videos, manuals, and FAQs provided by manufacturers to enhance their understanding of product usage and maintenance. Building a partnership with a manufacturer that values customer support can significantly reduce downtime and enhance the longevity of current transformers in their operations.
Strategic Material Selection Guide for current transformer manufacturer
When selecting materials for current transformers, manufacturers must consider various factors that impact performance, durability, and compliance with international standards. Below, we analyze four common materials used in the production of current transformers, focusing on their properties, advantages, disadvantages, and implications for international buyers, particularly from Africa, South America, the Middle East, and Europe.
What Are the Key Properties of Silicon Steel in Current Transformers?
Silicon steel is a prevalent material in current transformer manufacturing due to its excellent magnetic properties. It typically exhibits high permeability, which enhances the efficiency of the transformer. Additionally, silicon steel can withstand temperature ratings up to 150°C and offers decent corrosion resistance, making it suitable for various environments.
Pros and Cons of Silicon Steel:
The primary advantage of silicon steel is its cost-effectiveness and high performance in magnetic applications. However, it can be susceptible to mechanical stress and may require careful handling during manufacturing. This sensitivity can complicate the manufacturing process, especially in regions with less advanced production technologies.
Impact on Application:
Silicon steel is particularly compatible with electrical media, making it ideal for indoor installations. However, its limitations in harsh environments may necessitate additional protective measures.
Considerations for International Buyers:
Buyers from regions like Africa and South America should ensure that suppliers comply with ASTM standards for silicon steel. Additionally, understanding local manufacturing capabilities can help mitigate risks associated with handling and processing.
How Does Copper Perform as a Material for Current Transformers?
Copper is another common choice for current transformers, known for its excellent electrical conductivity and thermal properties. It can handle high currents and has a temperature rating of up to 200°C, making it suitable for demanding applications.
Pros and Cons of Copper:
The primary advantage of copper is its superior conductivity, which leads to lower energy losses. However, copper is more expensive than other materials and can be prone to corrosion if not adequately protected. This corrosion risk can be a significant concern in humid or saline environments, particularly in coastal regions.
Impact on Application:
Copper is highly compatible with various electrical media and is preferred in high-performance applications. Its durability makes it suitable for both indoor and outdoor installations.
Considerations for International Buyers:
Buyers should look for compliance with JIS standards, especially in regions like Japan and parts of Europe. Additionally, understanding the local market for copper can help in negotiating better prices and ensuring quality.
What Are the Benefits of Using Resin for Insulation in Current Transformers?
Resin, often used as an insulating material, offers excellent dielectric properties and can withstand high temperatures. It is typically rated for use up to 180°C and provides good resistance to moisture and chemicals, making it suitable for various environments.
Pros and Cons of Resin:
The main advantage of resin is its excellent insulation properties, which enhance the safety and efficiency of current transformers. However, the manufacturing process can be complex, requiring specialized equipment and expertise, which may not be readily available in all regions.
Impact on Application:
Resin is compatible with a wide range of media and is particularly effective in environments with high humidity or chemical exposure.
Considerations for International Buyers:
Buyers should ensure that resin materials comply with international standards such as IEC and ASTM. Understanding the local availability of resin materials can help streamline the procurement process.
Why Is Aluminum Considered for Current Transformer Manufacturing?
Aluminum is increasingly being used in current transformer manufacturing due to its lightweight nature and reasonable conductivity. It typically has a temperature rating of up to 150°C and offers good resistance to corrosion.
Pros and Cons of Aluminum:
The key advantage of aluminum is its lower weight, which can reduce shipping costs and ease installation. However, its conductivity is lower than that of copper, which may lead to higher energy losses in some applications. Additionally, aluminum can be more prone to mechanical deformation.
Impact on Application:
Aluminum is suitable for various electrical media but is particularly advantageous in applications where weight is a critical factor, such as in portable or mobile transformers.
Considerations for International Buyers:
Buyers should be aware of compliance with local and international standards, such as DIN and ASTM, when sourcing aluminum components. Understanding the local market dynamics can also aid in cost-effective sourcing.
Summary Table of Material Selection for Current Transformers
Material | Typical Use Case for current transformer manufacturer | Key Advantage | Key Disadvantage/Limitation | Relative Cost (Low/Med/High) |
---|---|---|---|---|
Silicon Steel | Indoor electrical applications | Cost-effective with high magnetic efficiency | Susceptible to mechanical stress | Low |
Copper | High-performance electrical applications | Superior conductivity, low energy losses | Higher cost, prone to corrosion | High |
Resin | Insulation in various environments | Excellent dielectric properties | Complex manufacturing process | Medium |
Aluminum | Portable or mobile transformers | Lightweight, reduces shipping costs | Lower conductivity, prone to deformation | Medium |
This material selection guide provides international B2B buyers with critical insights into the properties, advantages, and limitations of various materials used in current transformer manufacturing. Understanding these factors can help ensure successful procurement and application in diverse environments.
In-depth Look: Manufacturing Processes and Quality Assurance for current transformer manufacturer
What Are the Main Stages of Manufacturing Current Transformers?
The manufacturing process of current transformers (CTs) involves several critical stages, each designed to ensure the final product meets the required performance and safety standards. The primary stages include material preparation, forming, assembly, and finishing.
Material Preparation: How Are Raw Materials Selected and Processed?
The first step in manufacturing current transformers is the selection and preparation of raw materials. High-quality electrical steel is often used for the core, while copper or aluminum serves as the conductor. Suppliers typically assess the material properties, such as conductivity and magnetic permeability, to ensure they meet industry standards. For international B2B buyers, verifying the source and quality of these materials is crucial, as subpar materials can affect performance and reliability.
Forming: What Techniques Are Used to Shape Components?
Once the materials are prepared, they undergo forming processes. Techniques such as stamping, winding, and molding are employed to create the core and winding assemblies. Precision in these processes is vital; any defects can lead to inefficiencies in the transformer’s operation. Buyers should inquire about the machinery used and the technical expertise of the workforce, as these factors directly influence the quality of the formed components.
Assembly: How Are Components Integrated into a Final Product?
After forming, the components are assembled. This stage involves integrating the core with the windings and encapsulating them in a protective housing. The assembly process may utilize automated machinery or manual techniques, depending on the manufacturer’s capabilities. B2B buyers should evaluate whether the manufacturer employs skilled labor for assembly, as this can impact the consistency and reliability of the final product.
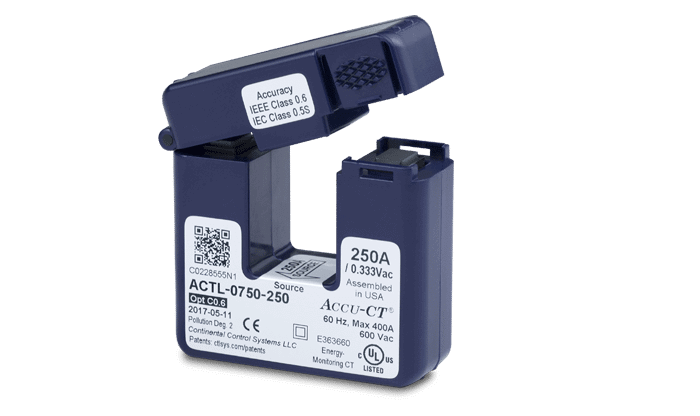
A stock image related to current transformer manufacturer.
Finishing: What Processes Ensure Quality and Aesthetics?
The final stage involves finishing processes such as insulation, painting, and quality checks. Insulation is crucial for safety and performance, often requiring specific materials that comply with international standards. Aesthetic considerations, such as the appearance of the housing, are also addressed during this stage. International buyers should ensure that finishing processes align with their branding and quality expectations.
How Is Quality Assurance Implemented in Current Transformer Manufacturing?
Quality assurance (QA) is paramount in the manufacturing of current transformers, ensuring that each unit meets stringent performance and safety standards.
What International Standards Should B2B Buyers Be Aware Of?
Manufacturers of current transformers often adhere to international standards such as ISO 9001 for quality management systems. Additionally, industry-specific certifications like CE (Conformité Européenne) and API (American Petroleum Institute) are critical for ensuring compliance with safety and performance benchmarks. Buyers from Africa, South America, the Middle East, and Europe should prioritize suppliers who hold these certifications, as they indicate a commitment to quality and compliance.
What Are the Key Quality Control Checkpoints in Manufacturing?
Quality control (QC) involves several checkpoints throughout the manufacturing process, including Incoming Quality Control (IQC), In-Process Quality Control (IPQC), and Final Quality Control (FQC).
-
IQC: This checkpoint assesses the quality of raw materials before production begins. Suppliers should have documented procedures for evaluating incoming materials.
-
IPQC: Conducted during the manufacturing process, IPQC ensures that components meet specifications at various stages. Regular inspections and tests should be performed to catch any defects early.
-
FQC: The final inspection occurs after assembly and finishing. This involves rigorous testing of the current transformers to confirm they meet performance standards before they are shipped to customers.
What Common Testing Methods Are Used to Ensure Quality?
Testing methods employed in the quality assurance of current transformers include:
-
Electrical Testing: This involves measuring the transformer’s performance characteristics, such as turns ratio, insulation resistance, and burden testing.
-
Mechanical Testing: These tests evaluate the physical integrity of the transformer, ensuring it can withstand environmental stresses.
-
Thermal Testing: Conducted to assess the transformer’s ability to operate under high temperatures, which is crucial for long-term reliability.
B2B buyers should request detailed reports of these tests from potential suppliers to verify compliance with relevant standards.
How Can B2B Buyers Verify Supplier Quality Control Practices?
For international B2B buyers, particularly those from regions with varying manufacturing standards, verifying a supplier’s quality control practices is essential.
What Role Do Audits and Reports Play?
Regular audits of manufacturing facilities can provide insight into a supplier’s adherence to quality standards. Buyers should consider conducting on-site audits or requesting third-party audit reports to ensure compliance with industry practices. Additionally, reviewing quality control reports can provide transparency regarding the manufacturer’s QC processes.
Why Should Buyers Consider Third-Party Inspections?
Engaging third-party inspection services can further assure buyers of product quality. These independent organizations evaluate the manufacturing process and testing methods, providing an unbiased assessment of the supplier’s capabilities. This is particularly important for buyers in Africa and South America, where local manufacturing standards may differ significantly from international norms.
What Nuances Should International Buyers Consider Regarding Quality Certifications?
Quality certifications can vary significantly across regions. Buyers from Europe may prioritize CE certifications, while those in the Middle East might look for compliance with local standards. It is vital for B2B buyers to understand these nuances and ensure that the certifications held by suppliers are recognized in their respective markets.
Furthermore, some manufacturers may hold certifications that are not widely recognized outside their region, which can complicate international transactions. Buyers should ask potential suppliers about their certifications and whether they have plans to obtain additional international certifications to meet buyer expectations.
Conclusion: Ensuring Quality in Your Supply Chain
For international B2B buyers, understanding the manufacturing processes and quality assurance measures in current transformer production is crucial. By focusing on material quality, rigorous manufacturing techniques, and comprehensive quality control measures, buyers can make informed decisions that enhance their supply chain reliability. Engaging in thorough due diligence, including audits and inspections, will further ensure that the transformers you procure meet your operational needs and safety standards.
Practical Sourcing Guide: A Step-by-Step Checklist for ‘current transformer manufacturer’
Introduction
In the competitive landscape of B2B procurement, sourcing the right current transformer manufacturer is crucial for ensuring quality, reliability, and cost-effectiveness. This practical sourcing guide provides a step-by-step checklist to help international buyers, particularly from Africa, South America, the Middle East, and Europe, navigate the complexities of this process. By following these actionable steps, you can enhance your sourcing strategy and make informed decisions.
Step 1: Define Your Technical Specifications
Before engaging with potential suppliers, it’s essential to clearly outline your technical requirements for the current transformers. This includes specifications such as voltage ratings, frequency, insulation type, and physical dimensions. Having a detailed specification document will not only facilitate clearer communication with manufacturers but also ensure that you receive products that meet your operational needs.
- Why it matters: Accurate specifications help prevent misunderstandings and ensure compliance with industry standards.
- What to include: Consider application details, environmental conditions, and regulatory compliance requirements.
Step 2: Conduct Market Research on Manufacturers
Engage in thorough market research to identify reputable current transformer manufacturers. Utilize industry reports, trade publications, and online platforms to gather information about potential suppliers. Pay attention to their experience, market presence, and product range.
- Why it matters: Understanding the market landscape helps you identify manufacturers that align with your needs and standards.
- What to look for: Focus on manufacturers with a proven track record in your industry and positive customer feedback.
Step 3: Evaluate Potential Suppliers
Before committing to a supplier, it’s crucial to vet them thoroughly. Request detailed company profiles, case studies, and references from other buyers in similar industries or regions. This step can help you gauge their reliability and service quality.
- Why it matters: A comprehensive evaluation minimizes risks associated with poor-quality products and unreliable suppliers.
- What to check: Assess their production capabilities, quality assurance processes, and customer service responsiveness.
Step 4: Verify Supplier Certifications and Standards
Ensure that the manufacturers you are considering possess relevant certifications and adhere to international quality standards, such as ISO 9001. Certifications indicate that the supplier meets specific quality benchmarks and regulatory requirements.
- Why it matters: Verified certifications enhance your confidence in the supplier’s ability to deliver high-quality products.
- What to ask for: Request copies of certifications and inquire about their quality control processes.
Step 5: Request Samples for Testing
Once you have shortlisted potential suppliers, request product samples to evaluate their quality firsthand. Testing samples under your operational conditions can help you assess performance and reliability.
- Why it matters: Direct evaluation of samples allows you to identify any potential issues before placing larger orders.
- What to focus on: Analyze the transformers for durability, accuracy, and overall performance in real-world scenarios.
Step 6: Negotiate Terms and Pricing
After selecting a preferred supplier, initiate negotiations on pricing, delivery timelines, and payment terms. Be transparent about your budget constraints while ensuring that you do not compromise on quality.
- Why it matters: Effective negotiation can lead to cost savings and better contractual terms, benefiting your overall procurement strategy.
- What to consider: Look for flexibility in payment options and delivery schedules that accommodate your operational requirements.
Step 7: Establish a Clear Communication Plan
Finally, set up a robust communication plan with your chosen supplier. Establish regular check-ins and updates to monitor the progress of your orders and address any issues promptly.
- Why it matters: Clear communication helps build a strong partnership and ensures that both parties are aligned throughout the procurement process.
- What to include: Outline communication channels, frequency of updates, and key contact personnel on both sides.
By following this checklist, international B2B buyers can streamline their sourcing process for current transformers, ensuring that they partner with reliable manufacturers that meet their specific needs.
Comprehensive Cost and Pricing Analysis for current transformer manufacturer Sourcing
What are the Key Cost Components in Sourcing Current Transformers?
Understanding the cost structure of current transformers is essential for B2B buyers seeking to optimize their sourcing strategies. The primary cost components include:
-
Materials: The choice of materials significantly impacts the overall cost. High-quality copper, silicon steel for cores, and insulation materials are crucial for performance and reliability. Prices fluctuate based on global demand and supply chain dynamics.
-
Labor: Labor costs can vary widely by region. Manufacturers in countries with lower labor costs may offer competitive pricing, but this can affect the quality and reliability of the product. It’s vital to evaluate the skill level of the workforce and the potential implications for product quality.
-
Manufacturing Overhead: This includes expenses related to facility maintenance, equipment depreciation, and utilities. A manufacturer with efficient operations may have lower overhead costs, allowing for more competitive pricing.
-
Tooling: The cost of specialized tools and machinery used in the manufacturing process can be significant. Custom designs or modifications may increase tooling costs, which should be factored into the overall pricing.
-
Quality Control (QC): Investing in robust QC processes ensures that products meet international standards and certifications. While this adds to the cost, it can prevent issues down the line, making it a worthwhile investment.
-
Logistics: Shipping, handling, and customs duties can dramatically affect total costs, especially for international buyers. Understanding the logistics involved in transporting current transformers can help buyers anticipate and manage these expenses.
-
Margin: Manufacturers typically apply a markup to cover their expenses and profit margins. This varies by supplier and can be influenced by their market positioning and the perceived value of their products.
How Do Price Influencers Impact Current Transformer Costs?
Several factors can influence the final price of current transformers, which international B2B buyers should consider:
-
Volume and Minimum Order Quantity (MOQ): Larger orders often qualify for bulk pricing discounts. Buyers should negotiate MOQs to achieve better pricing, especially if they can commit to larger volumes.
-
Specifications and Customization: Custom specifications can lead to increased costs due to additional engineering and production requirements. Buyers should balance their need for customization with budget constraints.
-
Material Quality and Certifications: Premium materials and compliance with international standards can increase costs. However, these factors enhance reliability and performance, making them worthwhile investments for critical applications.
-
Supplier Factors: The reputation, experience, and location of the supplier can influence pricing. Established suppliers may charge more due to their track record, but they often provide better support and reliability.
-
Incoterms: The chosen Incoterms (International Commercial Terms) can impact logistics costs and responsibilities. Understanding these terms helps buyers manage risks and costs effectively.
What Buyer Tips Can Help in Negotiating Current Transformer Prices?
International B2B buyers can adopt several strategies to enhance their sourcing efficiency:
-
Negotiate Wisely: Engaging in open dialogue about pricing can lead to favorable terms. Buyers should be prepared to discuss their needs and demonstrate their potential as long-term partners to secure better deals.
-
Focus on Cost Efficiency: Evaluate the Total Cost of Ownership (TCO) rather than just the initial purchase price. This includes installation, maintenance, and operational costs over the product’s lifecycle.
-
Understand Pricing Nuances: Be aware that pricing can vary significantly based on regional market conditions. For buyers in Africa, South America, the Middle East, and Europe, understanding local economic factors and currency fluctuations can help in making informed decisions.
-
Stay Informed about Market Trends: Keeping abreast of industry trends, material costs, and geopolitical factors can provide leverage during negotiations.
Disclaimer on Indicative Prices
It is crucial to note that prices for current transformers can vary widely based on the aforementioned factors. Buyers should seek quotes from multiple suppliers and conduct thorough market research to obtain accurate and current pricing information.
Alternatives Analysis: Comparing current transformer manufacturer With Other Solutions
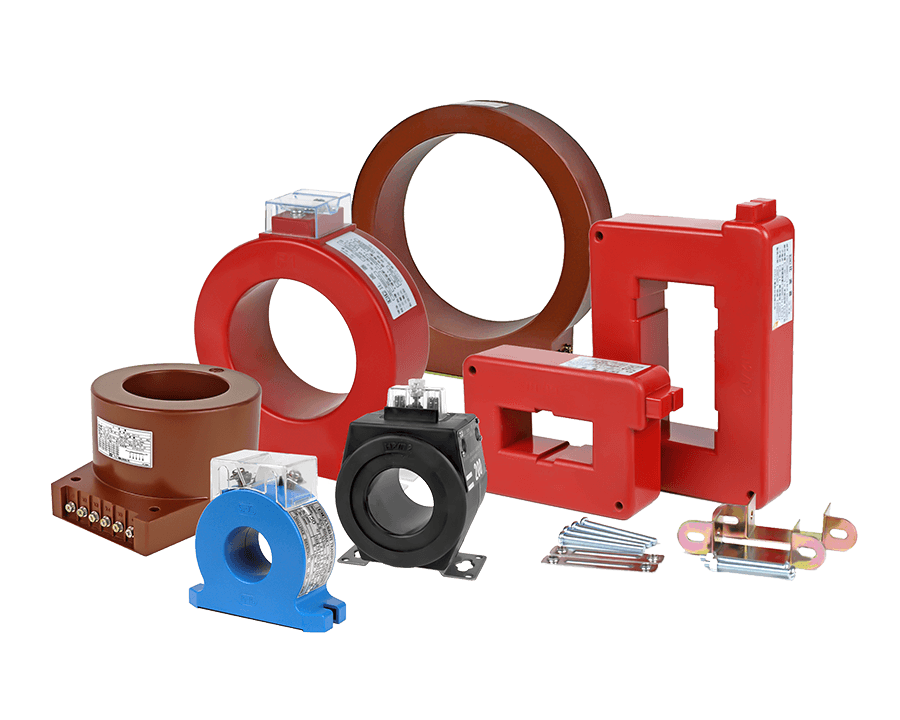
A stock image related to current transformer manufacturer.
In today’s competitive market, international B2B buyers must explore various solutions to meet their operational needs effectively. When considering current transformers, it is essential to evaluate alternatives that may offer different advantages depending on the specific requirements of your business. This analysis will compare current transformer manufacturers with two viable alternatives: Rogowski coils and Hall effect sensors.
Comparison Table of Current Transformer Manufacturer and Alternatives
Comparison Aspect | Current Transformer Manufacturer | Rogowski Coil | Hall Effect Sensor |
---|---|---|---|
Performance | High accuracy for AC measurements | Flexible and lightweight, good for high-frequency applications | Accurate for DC and AC, but less effective at high frequencies |
Cost | Moderate to high | Generally lower cost | Cost-effective for basic applications |
Ease of Implementation | Requires installation and calibration | Easy to install, minimal setup needed | Simple integration into existing systems |
Maintenance | Regular calibration needed | Low maintenance, no calibration required | Minimal maintenance required |
Best Use Case | Heavy industrial applications requiring precision | Temporary or portable measurements in various settings | Low-power applications, electric vehicles, and renewable energy systems |
What Are the Advantages and Disadvantages of Rogowski Coils?
Rogowski coils are an excellent alternative to traditional current transformers, particularly for applications requiring high-frequency measurements. Their flexible design allows for easy installation around conductors without the need for disconnection. However, they may not provide the same level of accuracy as traditional current transformers in specific high-load scenarios. They are also less suitable for applications that require continuous monitoring over extended periods due to potential drift in calibration.
How Do Hall Effect Sensors Compare to Current Transformers?
Hall effect sensors offer a cost-effective solution for measuring current, especially in low-power applications. They can accurately measure both AC and DC currents, making them versatile for various industries, including automotive and renewable energy. However, they may not perform as well as current transformers in high-frequency scenarios, and their accuracy can diminish under certain conditions. Thus, while they present a budget-friendly option, buyers should consider the specific application to ensure they meet performance needs.
How Can B2B Buyers Choose the Right Solution for Their Needs?
When selecting the most suitable current measurement solution, B2B buyers should carefully assess their specific operational requirements, including the type of current (AC or DC), the frequency of the signals involved, and the operational environment. Additionally, budget considerations, ease of installation, and maintenance capabilities should play a significant role in the decision-making process. By weighing these factors against the performance and cost characteristics of each option, buyers can make informed choices that align with their business objectives and operational demands.
Essential Technical Properties and Trade Terminology for current transformer manufacturer
What Are the Essential Technical Properties of Current Transformers?
When sourcing current transformers, understanding their technical specifications is crucial for ensuring compatibility, reliability, and performance in your electrical systems. Here are some key properties to consider:
1. Material Grade: Why Does It Matter?
The material grade of a current transformer affects its durability and performance. Common materials include silicon steel for the core and copper or aluminum for the winding. Higher-grade materials can enhance efficiency and reduce energy losses, which is particularly important for businesses looking to minimize operational costs. When assessing suppliers, ask about the specific material grades used to ensure they meet your operational requirements.
2. Tolerance Levels: How Do They Impact Performance?
Tolerance levels define the acceptable range of deviation from specified measurements. In current transformers, tight tolerances are essential for accurate current measurement and protection systems. Poor tolerance can lead to measurement errors, affecting the reliability of your electrical installations. Ensure that your supplier provides clear tolerance specifications and confirm that they adhere to industry standards.
3. Rated Current: What Should You Look For?
The rated current indicates the maximum continuous current the transformer can measure without distortion. It’s vital to select a current transformer with a rated current that matches or exceeds the operational requirements of your system. This is especially important for industries with fluctuating loads, as under-rated transformers can lead to failures and operational disruptions.
4. Burden: Why Is It Important for Your Application?
Burden refers to the load connected to the secondary winding of the current transformer, typically expressed in VA (volt-amperes). A properly matched burden ensures the current transformer operates efficiently. If the burden is too high, it can lead to inaccurate readings and potential overheating. Always discuss your application needs with manufacturers to find the appropriate burden rating.
5. Accuracy Class: How Does It Affect Measurement Precision?
The accuracy class of a current transformer determines its measurement precision. Defined by international standards, it’s crucial for applications requiring high measurement fidelity, such as energy metering and protection relays. When comparing suppliers, consider those who offer current transformers with the required accuracy class for your specific application.
What Are Common Trade Terms Used in Current Transformer Manufacturing?
Understanding industry jargon can facilitate smoother negotiations and clearer communications with suppliers. Here are some essential terms:
1. OEM (Original Equipment Manufacturer): What Does It Mean for You?
OEM refers to a company that produces parts or equipment that may be marketed by another manufacturer. When sourcing current transformers, knowing whether a supplier is an OEM can be vital, as it often implies a higher level of quality control and reliability. Ensure that your suppliers are reputable OEMs to guarantee product integrity.
2. MOQ (Minimum Order Quantity): How Does It Affect Your Purchase?
MOQ is the smallest quantity of a product that a supplier is willing to sell. For B2B buyers, understanding the MOQ is crucial for budgeting and inventory management. If your needs are small, look for suppliers with lower MOQs, but be mindful that higher MOQs may lead to better pricing per unit.
3. RFQ (Request for Quotation): Why Is It Important?
An RFQ is a document sent to suppliers to solicit price proposals for specific products or services. Using RFQs can help you compare pricing and terms across multiple suppliers effectively. Make sure to include all necessary specifications in your RFQ to receive accurate quotes.
4. Incoterms: How Do They Affect Shipping and Costs?
Incoterms are international commercial terms that define the responsibilities of buyers and sellers in the shipping process. Understanding these terms can help you anticipate shipping costs and responsibilities, ensuring that your current transformers arrive on time and within budget. Familiarize yourself with common Incoterms like FOB (Free on Board) and CIF (Cost, Insurance, and Freight) to make informed decisions.
By grasping these essential properties and trade terminologies, B2B buyers can make more informed decisions when sourcing current transformers, ultimately leading to enhanced operational efficiency and better supplier relationships.
Navigating Market Dynamics and Sourcing Trends in the current transformer manufacturer Sector
What Are the Current Market Dynamics and Key Trends in the Current Transformer Manufacturing Sector?
The global current transformer market is experiencing a significant evolution driven by technological advancements and increasing demand for efficient energy management systems. Key trends include the rise of smart grid technologies and the integration of IoT (Internet of Things) solutions, which are reshaping how current transformers are utilized in monitoring and controlling electrical networks. For international B2B buyers, especially those from Africa, South America, the Middle East, and Europe, understanding these dynamics is crucial for making informed procurement decisions.
Another prominent trend is the shift towards digitalization and automation in manufacturing processes. This transformation not only enhances operational efficiency but also allows manufacturers to offer customized solutions tailored to specific market needs. Buyers should look for suppliers that leverage advanced manufacturing technologies, such as 3D printing and AI-driven analytics, to ensure they are sourcing innovative products that align with future market demands.
Additionally, the increasing emphasis on renewable energy sources is driving demand for current transformers that can effectively measure and manage the flow of electricity from alternative energy systems. This shift presents an opportunity for B2B buyers to explore partnerships with manufacturers who specialize in transformers designed for solar, wind, and other renewable applications. By aligning sourcing strategies with these trends, international buyers can enhance their supply chain resilience and capitalize on emerging market opportunities.
How Does Sustainability Influence Sourcing Decisions in the Current Transformer Sector?
Sustainability is becoming a pivotal factor in the sourcing decisions of international B2B buyers, particularly as global awareness of environmental issues grows. The manufacturing of current transformers involves various materials and processes that can have significant environmental impacts. Therefore, buyers are increasingly prioritizing suppliers who demonstrate a commitment to sustainability through responsible sourcing practices.
Ethical supply chains are essential for minimizing the ecological footprint of manufacturing operations. This includes selecting suppliers that use recyclable materials, energy-efficient production methods, and sustainable packaging solutions. B2B buyers should seek manufacturers that possess ‘green’ certifications, such as ISO 14001, which indicates adherence to environmental management standards.
Moreover, the demand for “green” current transformers is on the rise, as organizations aim to reduce their energy consumption and carbon emissions. Buyers should inquire about the materials used in the manufacturing process, such as eco-friendly insulation or low-impact metals, to ensure they are sourcing products that align with their sustainability goals. By prioritizing ethical sourcing, B2B buyers not only fulfill corporate social responsibility objectives but also enhance their brand reputation in increasingly eco-conscious markets.
How Has the Current Transformer Manufacturing Sector Evolved Over Time?
The evolution of the current transformer manufacturing sector has been marked by significant technological advancements and changing market demands. Initially, current transformers were primarily mechanical devices used for basic electrical measurement. However, as the global energy landscape transformed, so did the technology behind these devices.
The introduction of digital technology has revolutionized current transformers, allowing for enhanced accuracy, reliability, and functionality. This evolution has been driven by the need for better performance in increasingly complex electrical systems, particularly with the rise of renewable energy sources and smart grid initiatives. As a result, modern current transformers are now equipped with smart capabilities that enable real-time data monitoring and remote management.
For international B2B buyers, recognizing this historical context is vital. It underscores the importance of partnering with manufacturers who not only understand the current landscape but are also innovating to meet future energy challenges. By leveraging these advancements, buyers can ensure they are equipped with the most effective and efficient solutions available in the market.
Frequently Asked Questions (FAQs) for B2B Buyers of current transformer manufacturer
-
How do I choose the right current transformer manufacturer for my business needs?
Selecting the right current transformer manufacturer involves evaluating several key factors. Start by assessing the manufacturer’s industry reputation, certifications, and experience with similar projects. Look for suppliers that offer customization options to meet your specific technical requirements. Additionally, consider their production capacity and lead times to ensure they can meet your demand. Engaging in direct communication can also provide insights into their customer service and support capabilities. -
What are the common specifications I should consider when sourcing current transformers?
When sourcing current transformers, focus on specifications such as the transformer’s accuracy class, rated primary and secondary currents, and frequency ratings. It’s essential to consider the insulation class and the environment where the transformer will be used, as this affects durability and performance. Additionally, inquire about the physical dimensions and weight, as these factors can impact installation and logistics. -
What are the advantages of customizing current transformers for my specific application?
Customizing current transformers can provide numerous advantages, such as improved performance tailored to your application, enhanced accuracy, and integration with existing systems. Custom designs can also help accommodate space constraints and specific environmental conditions, ensuring reliability and longevity. Moreover, a tailored solution can lead to greater efficiency and reduced operational costs in the long run. -
What is the typical minimum order quantity (MOQ) for current transformers from manufacturers?
Minimum order quantities (MOQs) for current transformers vary significantly among manufacturers and can depend on factors like production capabilities and design complexity. Generally, MOQs can range from a few units to several hundred. It’s advisable to discuss your specific needs with potential suppliers to negotiate MOQs that align with your project requirements without incurring excessive costs. -
What payment terms should I expect when working with international current transformer manufacturers?
Payment terms can vary widely based on the manufacturer and your negotiation power. Common practices include a deposit upon order confirmation (typically 30-50%) with the balance due before shipment. For larger orders, some manufacturers may offer flexible terms, such as installment payments or letters of credit. Always ensure that payment terms are clearly outlined in your contract to avoid disputes later. -
How can I ensure the quality of current transformers from international manufacturers?
To ensure quality, start by requesting certifications, such as ISO 9001, which indicate compliance with international quality standards. Ask about the manufacturer’s quality assurance processes, including testing methods and quality control measures. It’s also beneficial to request samples for testing before committing to larger orders. Building a relationship with the supplier can enhance transparency regarding their production practices. -
What logistics considerations should I keep in mind when importing current transformers?
Logistics is critical when importing current transformers. Consider factors like shipping methods, transit times, and customs regulations in your country. Ensure that your supplier provides clear information on packaging to prevent damage during transit. It’s also wise to work with a reliable freight forwarder who can help navigate the complexities of international shipping and ensure timely delivery. -
How can I effectively communicate with current transformer manufacturers across different time zones and languages?
Effective communication across different time zones and languages can be achieved by setting clear expectations and using collaborative tools. Establish a primary point of contact within the manufacturer’s team and use email for detailed inquiries. Scheduling regular video calls can help clarify complex issues. If language barriers exist, consider using translation services or bilingual staff to facilitate smoother conversations.
Important Disclaimer & Terms of Use
⚠️ Important Disclaimer
The information provided in this guide, including content regarding manufacturers, technical specifications, and market analysis, is for informational and educational purposes only. It does not constitute professional procurement advice, financial advice, or legal advice.
While we have made every effort to ensure the accuracy and timeliness of the information, we are not responsible for any errors, omissions, or outdated information. Market conditions, company details, and technical standards are subject to change.
B2B buyers must conduct their own independent and thorough due diligence before making any purchasing decisions. This includes contacting suppliers directly, verifying certifications, requesting samples, and seeking professional consultation. The risk of relying on any information in this guide is borne solely by the reader.
Strategic Sourcing Conclusion and Outlook for current transformer manufacturer
In conclusion, strategic sourcing for current transformers is not merely a procurement function but a vital component of operational success in the energy sector. By prioritizing quality, reliability, and supplier relationships, international B2B buyers can significantly enhance their supply chain resilience and mitigate risks associated with fluctuating market conditions. Engaging with manufacturers that offer robust support and innovation can yield long-term benefits, including improved efficiency and cost savings.
Why is strategic sourcing essential for current transformers in diverse markets? As regions like Africa, South America, the Middle East, and Europe evolve, the demand for reliable energy solutions grows. Buyers must leverage local and global suppliers who understand regional regulatory requirements and technological advancements. This approach not only ensures compliance but also fosters sustainable partnerships that can adapt to future challenges.
Looking ahead, international buyers should actively seek out manufacturers committed to transparency, sustainability, and technological innovation. By doing so, they position themselves to capitalize on emerging opportunities in the energy sector. Take the next step in your sourcing strategy by exploring partnerships that align with your business objectives and support your growth in a rapidly changing landscape.