Discover Cost-Saving Tips from Top Motor Accessories Suppliers (2025)
Introduction: Navigating the Global Market for motor accessories supplier
In today’s competitive landscape, sourcing high-quality motor accessories suppliers can be a daunting challenge for international B2B buyers. Companies across Africa, South America, the Middle East, and Europe face an array of obstacles, from understanding regional compliance standards to navigating cultural differences in business negotiations. This guide is designed to streamline the process, equipping buyers with the knowledge necessary to make informed decisions in selecting reliable suppliers for motor accessories.
Covering a comprehensive range of topics, this guide delves into the various types of motor accessories, their applications across different industries, and essential criteria for vetting potential suppliers. Buyers will gain insights into cost structures, logistics considerations, and best practices for establishing long-term partnerships. By addressing key concerns such as quality assurance, product compatibility, and supply chain resilience, this resource empowers businesses to mitigate risks while enhancing operational efficiency.
Whether you are a purchasing manager in France seeking innovative solutions or a procurement officer in Brazil navigating local markets, this guide offers actionable insights tailored to your specific needs. With a focus on fostering informed purchasing decisions, we aim to demystify the global market for motor accessories suppliers, enabling businesses to thrive in an increasingly interconnected world.
Understanding motor accessories supplier Types and Variations
Type Name | Key Distinguishing Features | Primary B2B Applications | Brief Pros & Cons for Buyers |
---|---|---|---|
OEM (Original Equipment Manufacturer) | Supplies parts made to original specifications; high quality assurance | Automotive manufacturing, vehicle repairs | Pros: Reliable quality, compatibility; Cons: Higher costs, limited flexibility in customization |
Aftermarket Suppliers | Provides a wide range of parts, often at lower prices; may vary in quality | Vehicle modifications, budget repairs | Pros: Cost-effective, diverse options; Cons: Quality inconsistency, potential compatibility issues |
Specialty Suppliers | Focuses on niche markets, offering unique or custom products | Custom builds, performance enhancements | Pros: Tailored solutions, expertise; Cons: Higher price points, longer lead times |
Wholesale Distributors | Sells large quantities of various motor accessories; often acts as a middleman | Retailers, workshops, fleet operators | Pros: Bulk pricing, broad selection; Cons: Less direct manufacturer support, potential stock issues |
E-commerce Platforms | Online marketplaces offering a range of motor accessories; easy access to global suppliers | Small businesses, individual buyers | Pros: Convenience, competitive pricing; Cons: Quality assurance challenges, shipping delays |
What Are the Characteristics of OEM Suppliers?
OEM suppliers are critical for businesses seeking high-quality motor accessories that meet specific manufacturing standards. These suppliers create components that are often used in the original assembly of vehicles, ensuring compatibility and reliability. B2B buyers, especially those involved in automotive manufacturing and vehicle repairs, benefit from the assurance of quality and adherence to industry standards. However, the trade-off includes higher costs and limited options for customization, which may not suit all budgets.
How Do Aftermarket Suppliers Differ from OEM Suppliers?
Aftermarket suppliers offer a broader range of motor accessories, often at lower prices than OEM alternatives. They cater to various applications, including vehicle modifications and budget repairs, making them popular among businesses looking to save costs. While they provide diverse options, B2B buyers must navigate potential quality inconsistencies and compatibility issues. It’s crucial to conduct thorough research and vet suppliers to ensure that the aftermarket products meet the necessary standards for performance and safety.
What Advantages Do Specialty Suppliers Provide?
Specialty suppliers focus on niche markets, offering unique or custom motor accessories that cater to specific needs. These suppliers are ideal for businesses looking to enhance vehicle performance or create custom builds. They bring expertise in their respective areas, allowing for tailored solutions that can significantly improve operational efficiency. However, buyers should be prepared for potentially higher price points and longer lead times, which may affect project timelines.
Why Should B2B Buyers Consider Wholesale Distributors?
Wholesale distributors play a vital role in the supply chain by providing large quantities of various motor accessories. They are particularly beneficial for retailers, workshops, and fleet operators seeking to purchase in bulk at competitive prices. While they offer a broad selection and cost savings, B2B buyers should be cautious of less direct manufacturer support and potential stock issues, which could disrupt their operations. Establishing strong relationships with reliable distributors can mitigate these risks.
How Do E-commerce Platforms Impact the Motor Accessories Market?
E-commerce platforms have revolutionized the way businesses procure motor accessories by providing easy access to a global marketplace. They are particularly advantageous for small businesses and individual buyers seeking convenience and competitive pricing. However, the challenges of quality assurance and potential shipping delays are significant considerations. B2B buyers should prioritize platforms with robust return policies and seller ratings to ensure they are making informed purchasing decisions.
Related Video: MOTORCYCLE ACCESSORIES BUSINESS: TIPS + LESSONS
Key Industrial Applications of motor accessories supplier
Industry/Sector | Specific Application of motor accessories supplier | Value/Benefit for the Business | Key Sourcing Considerations for this Application |
---|---|---|---|
Manufacturing | Motor control systems in assembly lines | Enhanced efficiency and reduced downtime | Compatibility with existing machinery and regulatory standards |
Agriculture | Motors for irrigation systems | Improved crop yield and water management | Durability in harsh conditions and energy efficiency |
Transportation | Electric motors for public transport vehicles | Lower operational costs and reduced carbon footprint | Compliance with safety regulations and maintenance support |
Mining and Minerals | Motors for conveyor belts and drilling equipment | Increased productivity and reduced operational costs | Reliability and performance under extreme conditions |
Renewable Energy | Motors in wind turbines and solar panel trackers | Sustainable energy generation and cost savings | Technical support and warranty terms for long-term reliability |
How are Motor Accessories Suppliers Applied in Manufacturing?
In the manufacturing sector, motor accessories suppliers play a crucial role in the development of motor control systems used in assembly lines. These systems are essential for automating processes, thereby enhancing efficiency and minimizing downtime. International B2B buyers should ensure that the motor accessories they source are compatible with their existing machinery and comply with local regulatory standards, particularly in regions like Europe where compliance is stringent.
What Role do Motor Accessories Suppliers Play in Agriculture?
In agriculture, motor accessories are vital for powering irrigation systems. By integrating efficient motors, farmers can significantly improve crop yield while managing water resources more effectively. For buyers in Africa and South America, sourcing durable motors that can withstand harsh environmental conditions is critical. Additionally, energy efficiency is a key consideration, as it directly impacts operational costs and sustainability goals.
How are Motor Accessories Suppliers Transforming Transportation?
Motor accessories suppliers are increasingly essential in the transportation sector, particularly for electric motors used in public transport vehicles. These motors contribute to lower operational costs and help reduce the carbon footprint of urban transportation systems. Buyers from the Middle East and Europe should focus on suppliers that ensure compliance with stringent safety regulations and offer maintenance support to ensure long-term performance.
Why are Motor Accessories Suppliers Important in Mining and Minerals?
In the mining and minerals sector, motor accessories are used in applications such as conveyor belts and drilling equipment. The reliability and performance of these motors are crucial for increasing productivity and reducing operational costs. Buyers from regions with challenging mining conditions should prioritize suppliers that provide robust motors designed for extreme environments, ensuring consistent operation and minimal downtime.
How do Motor Accessories Suppliers Contribute to Renewable Energy?
Motor accessories suppliers are pivotal in the renewable energy sector, particularly in wind turbines and solar panel trackers. The use of advanced motors in these applications supports sustainable energy generation and offers significant cost savings. International buyers should consider suppliers that provide comprehensive technical support and favorable warranty terms, ensuring the long-term reliability of these critical components in renewable energy installations.
Related Video: What is Industrial Automation?
3 Common User Pain Points for ‘motor accessories supplier’ & Their Solutions
Scenario 1: Inconsistent Quality of Motor Accessories
The Problem: B2B buyers often encounter the issue of inconsistent quality when sourcing motor accessories. This can lead to significant operational setbacks, including increased maintenance costs and customer dissatisfaction. For example, a supplier may offer a wide range of products, but the quality of these items can vary greatly. This inconsistency may stem from inadequate quality control processes, differing manufacturing standards, or reliance on subpar materials. Buyers, especially those in Africa and South America, may find it challenging to maintain their reputation when the products they receive do not meet expected standards.
The Solution: To mitigate quality issues, B2B buyers should prioritize due diligence when selecting a motor accessories supplier. This involves thoroughly researching potential suppliers, including checking for industry certifications and reviewing past customer feedback. Establishing a clear set of quality benchmarks and communicating these to the supplier can set a foundation for better consistency. Additionally, buyers can request samples before committing to larger orders, allowing them to assess the quality firsthand. Regular quality audits and establishing a feedback loop with suppliers can also ensure ongoing adherence to quality standards.
Scenario 2: High Shipping Costs and Delays in Motor Accessories Delivery
The Problem: International B2B buyers often face the challenge of high shipping costs and unexpected delays when ordering motor accessories. This is particularly pronounced for businesses in Europe and the Middle East, where logistics can become complex due to varying regulations and customs requirements. These delays can disrupt supply chains, hinder production schedules, and ultimately affect customer satisfaction.
The Solution: To navigate shipping challenges, buyers should consider local suppliers or those with established distribution networks within their region. Building relationships with logistics providers who specialize in international shipping can also help in negotiating better rates and understanding the nuances of customs processes. It’s advisable to leverage technology, such as supply chain management software, to track shipments in real-time, providing visibility that allows businesses to plan accordingly. Lastly, discussing shipping terms upfront, including Incoterms, can help clarify responsibilities and costs, reducing the risk of unexpected charges.
Scenario 3: Limited Product Variety and Customization Options
The Problem: B2B buyers often struggle to find a motor accessories supplier that offers a wide variety of products tailored to their specific needs. This limitation can be particularly frustrating for businesses in diverse markets like Africa and South America, where local preferences and vehicle models may differ significantly from those in other regions. The inability to customize orders can lead to a mismatch between the products available and the actual market demand, resulting in lost sales opportunities.
The Solution: Buyers should seek suppliers who offer flexible customization options and a broad product range. Engaging in direct discussions with potential suppliers can help identify those willing to adapt their offerings to meet unique market demands. Buyers can also explore partnerships with manufacturers who specialize in bespoke solutions, enabling them to tailor products according to local needs. Furthermore, utilizing platforms that connect buyers with multiple suppliers can enhance the search for variety, ensuring access to a more extensive selection of motor accessories that can cater to specific requirements. By being proactive in negotiations and expressing clear needs, buyers can significantly improve their chances of securing a diverse and customizable product line.
Strategic Material Selection Guide for motor accessories supplier
When selecting materials for motor accessories, international B2B buyers must consider various factors that impact performance, cost, and compliance with regional standards. Here, we analyze four common materials used in motor accessories, focusing on their properties, advantages, disadvantages, and specific considerations for buyers from Africa, South America, the Middle East, and Europe.
What Are the Key Properties of Aluminum in Motor Accessories?
Aluminum is a lightweight metal known for its excellent corrosion resistance and good thermal conductivity. It typically has a temperature rating of up to 150°C and can withstand moderate pressure levels. These properties make aluminum suitable for various motor accessories, including housings and brackets.
Pros & Cons:
The primary advantage of aluminum is its low weight, which can enhance fuel efficiency in automotive applications. However, it may not be as durable as steel under high-stress conditions, making it less suitable for heavy-duty applications. Additionally, while aluminum is relatively affordable, the manufacturing process can be more complex due to its malleability.
Impact on Application:
Aluminum is compatible with various media, including oils and fuels, but may not perform well in environments with high salt content, which can lead to pitting corrosion.
Considerations for International Buyers:
Buyers should ensure compliance with standards such as ASTM B221 for aluminum extrusions. In Europe, EN 573-3 is relevant, while in South America, local standards may vary. Understanding these regulations is crucial for ensuring product quality and safety.
How Does Steel Compare in Terms of Performance for Motor Accessories?
Steel is a robust material with high tensile strength, making it ideal for heavy-duty applications. It can withstand high temperatures (up to 300°C) and pressures, making it suitable for components like gears and structural supports.
Pros & Cons:
The key advantage of steel is its durability and strength, which can lead to longer service life in demanding applications. However, it is heavier than aluminum, which may negatively impact fuel efficiency. Additionally, steel is prone to corrosion unless treated, which can increase maintenance costs.
Impact on Application:
Steel is compatible with a wide range of media, including water and various oils, but it requires protective coatings in corrosive environments.
Considerations for International Buyers:
Compliance with standards such as ASTM A36 for carbon steel is essential. Buyers in the Middle East should consider the impact of high temperatures and humidity on steel performance, while European buyers may look for compliance with EN 10025.
What Are the Benefits of Using Composite Materials for Motor Accessories?
Composite materials, often made from a combination of fibers and resins, offer a unique blend of lightweight properties and high strength. They can typically withstand temperatures up to 200°C and provide excellent resistance to corrosion and fatigue.
Pros & Cons:
The primary advantage of composites is their ability to reduce weight without sacrificing strength, making them ideal for performance-oriented applications. However, they can be more expensive than metals and may require specialized manufacturing processes, which can complicate supply chains.
Impact on Application:
Composites are highly resistant to chemicals, making them suitable for applications involving aggressive media. However, they may not be suitable for high-temperature applications beyond their rated limits.
Considerations for International Buyers:
Buyers should be aware of the lack of standardized testing for composites in some regions. Compliance with specific industry standards, such as ASTM D3039 for tensile properties, is crucial for ensuring product reliability.
How Do Plastics Fit into the Material Selection for Motor Accessories?
Plastics, particularly engineering-grade varieties like nylon and polycarbonate, are increasingly used in motor accessories due to their lightweight and corrosion-resistant properties. They can typically withstand temperatures up to 120°C.
Pros & Cons:
Plastics are cost-effective and can be molded into complex shapes, allowing for versatile designs. However, they may not be as strong as metals and can degrade under UV exposure or extreme temperatures.
Impact on Application:
Plastics are compatible with various media, including water and oils, but may not perform well in high-stress applications or environments with extreme temperatures.
Considerations for International Buyers:
Compliance with standards such as ASTM D638 for tensile properties is essential. Buyers in Europe should also consider REACH regulations regarding chemical safety.
Summary Table of Material Selection for Motor Accessories
Material | Typical Use Case for motor accessories supplier | Key Advantage | Key Disadvantage/Limitation | Relative Cost (Low/Med/High) |
---|---|---|---|---|
Aluminum | Housings, brackets | Lightweight and corrosion-resistant | Less durable under high stress | Medium |
Steel | Gears, structural supports | High strength and durability | Heavier and prone to corrosion | Low |
Composite | Performance components | Lightweight and strong | Higher cost and complex manufacturing | High |
Plastics | Covers, non-load bearing parts | Cost-effective and versatile | Limited strength and UV degradation | Low |
By understanding these materials’ properties and implications, international B2B buyers can make informed decisions that align with their operational needs and compliance requirements.
In-depth Look: Manufacturing Processes and Quality Assurance for motor accessories supplier
What Are the Main Stages of Manufacturing Motor Accessories?
The manufacturing of motor accessories involves several critical stages, each designed to ensure the final product meets the necessary specifications for quality and performance. The primary stages include material preparation, forming, assembly, and finishing.
-
Material Preparation: This initial stage involves sourcing high-quality raw materials, which could include metals, plastics, and rubber. Suppliers often prioritize materials that meet international standards for durability and performance. An effective materials procurement strategy can help buyers from Africa, South America, the Middle East, and Europe ensure they receive consistent quality.
-
Forming: This phase includes techniques such as casting, forging, and machining. Each method is chosen based on the specific requirements of the motor accessory being produced. For instance, die casting may be used for complex shapes, while machining is ideal for precision parts. Understanding these techniques can help buyers evaluate the capabilities of potential suppliers.
-
Assembly: In this stage, individual components are brought together to create the final product. This process may involve manual labor or automated systems, depending on the complexity of the accessory. B2B buyers should inquire about the assembly processes used by suppliers to ensure efficiency and quality control.
-
Finishing: The final stage often includes processes such as painting, plating, or surface treatment to enhance the aesthetic appeal and corrosion resistance of the accessory. Buyers should consider how finishing processes impact both the appearance and longevity of the product, ensuring they meet their specific needs.
Which Key Techniques Are Used in Manufacturing Motor Accessories?
Several techniques are integral to the manufacturing of motor accessories, each with its advantages:
-
Injection Molding: Commonly used for plastic components, this technique allows for high-volume production with consistent quality. Buyers should look for suppliers that utilize advanced molding technologies to ensure precision.
-
CNC Machining: This method is crucial for producing parts that require high accuracy. CNC machines can create complex geometries and are essential for maintaining tight tolerances, which is vital for performance in automotive applications.
-
Welding and Joining: For metal components, welding techniques such as TIG and MIG are commonly used. Buyers should assess the supplier’s capabilities in joining techniques to ensure the integrity and durability of the finished products.
-
Surface Treatment: Techniques like anodizing or galvanizing improve the resistance of components to wear and corrosion. This is especially important for accessories exposed to harsh environments.
How Is Quality Assurance Implemented in Motor Accessories Manufacturing?
Quality assurance (QA) is a critical aspect of manufacturing motor accessories, ensuring that products meet both international standards and specific industry requirements. Various checkpoints and methods are employed throughout the manufacturing process.
-
International Standards: Suppliers should adhere to standards such as ISO 9001, which focuses on quality management systems. This certification is recognized globally and indicates a commitment to continuous improvement and customer satisfaction. Buyers should prioritize suppliers with these certifications to mitigate risks.
-
Industry-Specific Certifications: Depending on the type of motor accessory, additional certifications may be relevant. For example, accessories used in the European market may require CE marking, while those intended for oil and gas applications might need API certification. Understanding these nuances is essential for international buyers.
-
Quality Control Checkpoints:
– Incoming Quality Control (IQC): This initial checkpoint verifies the quality of raw materials before production begins. Effective IQC processes help prevent defects early in the manufacturing process.
– In-Process Quality Control (IPQC): Conducted during production, IPQC ensures that operations are performed correctly and that any issues are addressed immediately. This can involve regular inspections and testing.
– Final Quality Control (FQC): This final checkpoint assesses the completed product before it is shipped. It may include functional testing and visual inspections to ensure compliance with specifications.
What Common Testing Methods Are Used in Quality Assurance?
To ensure the quality of motor accessories, various testing methods are employed, including:
-
Dimensional Inspection: This involves measuring the physical dimensions of the product to ensure they meet design specifications. Tools such as calipers and coordinate measuring machines (CMM) are commonly used.
-
Material Testing: Techniques such as tensile testing and hardness testing assess the material properties to ensure they can withstand operational stresses.
-
Functional Testing: For motor accessories, functional tests simulate real-world conditions to verify performance under expected load and stress. This is crucial for components that directly affect vehicle safety and performance.
How Can B2B Buyers Verify Supplier Quality Control?
B2B buyers can take several steps to verify the quality control processes of potential suppliers:
-
Supplier Audits: Conducting on-site audits can provide insights into a supplier’s quality management practices. Buyers should evaluate the supplier’s facilities, equipment, and processes to ensure they align with industry standards.
-
Quality Control Reports: Requesting detailed quality control reports can help buyers assess a supplier’s historical performance. These reports should include information on defect rates, corrective actions taken, and compliance with international standards.
-
Third-Party Inspections: Engaging third-party inspection services can offer an unbiased assessment of the supplier’s quality control processes. This step can be particularly beneficial for buyers who lack the resources to perform their own inspections.
What Are the QC and Certification Nuances for International B2B Buyers?
For international B2B buyers, understanding the nuances of quality control and certification is crucial. Different regions may have varying standards and regulations that affect product compliance.
-
Regional Standards: Buyers should familiarize themselves with the specific quality standards applicable in their target markets. For instance, the European Union has strict regulations concerning product safety and environmental impact, which may not be the case in other regions.
-
Documentation and Traceability: It’s essential for buyers to ensure that suppliers maintain accurate documentation of quality control measures. This includes tracking production batches and maintaining records of inspections and tests performed.
-
Cultural Considerations: In regions such as Africa and South America, local practices may influence quality control processes. Buyers should consider these cultural factors when evaluating suppliers to ensure compatibility and effective communication.
By understanding the manufacturing processes and quality assurance practices of motor accessory suppliers, international B2B buyers can make informed decisions that align with their operational needs and market expectations. This knowledge not only facilitates better supplier relationships but also enhances the overall quality and reliability of the products purchased.
Practical Sourcing Guide: A Step-by-Step Checklist for ‘motor accessories supplier’
Introduction
Sourcing motor accessories requires a strategic approach, particularly for international B2B buyers. This step-by-step checklist is designed to help you navigate the complexities of procurement, ensuring you find reliable suppliers that meet your technical and logistical needs. By following these actionable steps, you can streamline the sourcing process and make informed purchasing decisions.
Step 1: Define Your Technical Specifications
Before you start your search for motor accessories suppliers, it’s essential to have a clear understanding of your technical specifications. Define the types of accessories you need, such as batteries, tires, or electronic components, along with their quality standards and compliance requirements.
- Consider factors like material durability, compatibility with existing products, and safety certifications.
- Having precise specifications will help you communicate effectively with potential suppliers and filter out those who do not meet your requirements.
Step 2: Research Potential Suppliers
Conduct thorough research to identify potential suppliers that specialize in motor accessories. Utilize online directories, trade platforms, and industry-specific forums to compile a list of candidates.
- Focus on suppliers with a strong presence in your target regions (Africa, South America, the Middle East, and Europe).
- Check reviews and ratings from previous clients to gauge their reliability and customer service.
Step 3: Evaluate Supplier Certifications and Compliance
Verify that the suppliers you are considering possess the necessary certifications and comply with international standards. This step is critical to ensure the quality and safety of the products you intend to purchase.
- Look for certifications such as ISO, CE, or local regulatory compliance specific to your region.
- Confirm that the supplier adheres to ethical sourcing practices, as this can impact your brand reputation.
Step 4: Request Samples for Quality Assessment
Before making a bulk purchase, request samples from shortlisted suppliers. Assessing the quality of samples will provide insights into the product’s durability, performance, and overall suitability for your needs.
- Use the samples to test against your defined specifications and quality benchmarks.
- This step can also help establish a relationship with the supplier and gauge their responsiveness.
Step 5: Negotiate Pricing and Terms
Once you have evaluated the suppliers and their products, it’s time to negotiate pricing and terms. Effective negotiation can lead to better pricing, payment terms, and delivery schedules.
- Be transparent about your budget and expectations while remaining open to the supplier’s offers.
- Consider discussing bulk purchase discounts, shipping costs, and after-sales support to maximize your investment.
Step 6: Conduct Due Diligence on Supplier Reputation
Before finalizing your choice, conduct due diligence to ensure the supplier has a good reputation in the industry. This includes checking their financial stability, years in business, and any legal issues.
- Look for testimonials or case studies that highlight their experience with other B2B clients.
- Engage with industry contacts or associations to gather additional insights into the supplier’s reliability.
Step 7: Establish a Communication Plan
Effective communication is key to a successful supplier relationship. Establish a communication plan to ensure ongoing dialogue throughout the sourcing process and beyond.
- Set expectations for response times, updates on order status, and channels of communication.
- Regular check-ins can help address any issues promptly and build a strong partnership.
By following this practical sourcing guide, you can enhance your procurement process for motor accessories, ensuring you select suppliers that align with your business goals and operational needs.
Comprehensive Cost and Pricing Analysis for motor accessories supplier Sourcing
What Are the Key Cost Components for Motor Accessories Suppliers?
When sourcing motor accessories, understanding the cost structure is essential for effective budgeting and negotiation. The primary cost components include:
-
Materials: The choice of materials significantly impacts the overall cost. For example, high-quality or specialized materials may increase the base price but can enhance durability and performance, ultimately providing better value.
-
Labor: Labor costs vary based on geographic location and skill levels. Regions with higher labor costs might result in higher prices, but they may also offer superior craftsmanship.
-
Manufacturing Overhead: This includes indirect costs such as utilities, rent, and administrative expenses. Understanding these costs can help buyers gauge supplier pricing strategies.
-
Tooling: The initial investment in tooling and machinery can be substantial, particularly for customized parts. Buyers should consider how tooling costs will affect overall pricing, especially for unique specifications.
-
Quality Control (QC): Implementing stringent QC processes ensures product reliability but can add to costs. Buyers should assess the value of these measures against their own quality requirements.
-
Logistics: Shipping and handling costs can fluctuate based on distance, shipping methods, and tariffs. A thorough understanding of logistics is vital for calculating the total cost of procurement.
-
Margin: Suppliers will typically add a profit margin to their costs. Understanding standard margins in the industry can help buyers negotiate better terms.
What Factors Influence Pricing for Motor Accessories?
Several factors can influence the pricing of motor accessories, making it crucial for buyers to consider them when sourcing:
-
Volume/MOQ (Minimum Order Quantity): Purchasing in larger quantities often results in lower per-unit prices. Buyers should analyze their needs to optimize order sizes.
-
Specifications and Customization: Custom orders generally incur additional costs. Buyers should evaluate whether the benefits of customization justify the extra expense.
-
Materials and Quality Certifications: Higher-grade materials and certifications can elevate costs but may be necessary for specific applications or compliance with industry standards.
-
Supplier Factors: The reputation, reliability, and production capabilities of suppliers can significantly affect pricing. Conducting thorough due diligence on potential suppliers is essential.
-
Incoterms: The agreed-upon terms of delivery can influence overall costs. Buyers should be clear on responsibilities regarding shipping, insurance, and tariffs.
How Can Buyers Optimize Costs When Sourcing Motor Accessories?
To maximize cost efficiency, international B2B buyers should consider the following strategies:
-
Effective Negotiation: Engaging suppliers in dialogue about pricing can lead to favorable terms. Be prepared with market data to support your position and demonstrate your seriousness as a buyer.
-
Total Cost of Ownership (TCO): Look beyond initial purchase prices. Consider maintenance, operational costs, and potential downtime associated with lower-quality products. This holistic view can lead to better long-term decisions.
-
Understanding Pricing Nuances: Different regions may have unique pricing dynamics based on local market conditions, tariffs, and demand. Buyers from Africa, South America, the Middle East, and Europe should familiarize themselves with these nuances to make informed decisions.
-
Leverage Technology: Utilize digital platforms and sourcing tools that provide market insights and price comparisons. This can enhance transparency and help identify the best suppliers.
Disclaimer on Indicative Prices
Pricing for motor accessories can vary widely based on numerous factors, including market conditions and supplier capabilities. As such, it is essential for buyers to conduct their own market research and engage in thorough discussions with suppliers to arrive at accurate pricing tailored to their specific needs.
Alternatives Analysis: Comparing motor accessories supplier With Other Solutions
Understanding the Importance of Evaluating Alternatives
When it comes to sourcing motor accessories, B2B buyers have a plethora of options available. While a traditional motor accessories supplier can provide a range of products and services, it’s crucial to explore alternative solutions that may offer enhanced efficiency, cost savings, or innovative technologies. This analysis will compare the traditional motor accessories supplier with two viable alternatives: 3D Printing Services and Online Marketplaces for Motor Parts.
Comparison Table of Motor Accessories Supplier and Alternatives
Comparison Aspect | Motor Accessories Supplier | 3D Printing Services | Online Marketplaces for Motor Parts |
---|---|---|---|
Performance | High-quality, reliable products | Customization and rapid prototyping | Varies widely by seller |
Cost | Moderate to high | Variable, often lower for low volumes | Competitive pricing, often lower |
Ease of Implementation | Established processes, but can be slow | Requires design expertise and setup | User-friendly platforms, quick access |
Maintenance | Dependable support and maintenance services | Limited ongoing maintenance, depends on design | Seller-dependent, may lack support |
Best Use Case | Bulk purchases and standard needs | Custom parts and prototyping | Price-sensitive, diverse inventory |
What Are the Pros and Cons of 3D Printing Services?
3D printing services have revolutionized the manufacturing landscape by allowing companies to create customized parts on-demand. One of the major advantages of this method is its ability to produce intricate designs that would be difficult or impossible to achieve with traditional manufacturing techniques. Additionally, 3D printing often leads to lower costs for small production runs, as there are no tooling costs involved. However, the downside includes the need for specialized knowledge in design and printing processes, which may require investment in training or hiring experts. Furthermore, the material options can be limited compared to traditional suppliers, which may affect durability or performance.
How Do Online Marketplaces for Motor Parts Compare?
Online marketplaces provide a platform for multiple sellers to offer motor accessories at competitive prices, making it easier for B2B buyers to find good deals. The convenience of browsing a vast array of products and comparing prices in real-time is a significant advantage. These platforms often have user-friendly interfaces and customer reviews that help buyers make informed decisions. However, the quality can be inconsistent, as it largely depends on the seller’s reputation. Additionally, after-sales support may be lacking, which can lead to challenges in maintenance or warranty claims.
Conclusion: How to Choose the Right Solution for Your Needs
Selecting the right solution for motor accessories procurement depends on various factors, including your specific business needs, budget, and the importance of customization versus reliability. If your focus is on bulk purchasing and reliability, sticking with a traditional motor accessories supplier may be the best choice. Conversely, if your operations require rapid prototyping and customization, exploring 3D printing services could provide significant advantages. For those seeking cost-effective options and a broad selection, online marketplaces can be a valuable resource. Conducting thorough research and assessing your unique requirements will guide you in making an informed decision that aligns with your operational goals.
Essential Technical Properties and Trade Terminology for motor accessories supplier
What Are the Essential Technical Properties for Motor Accessories?
Understanding the technical specifications of motor accessories is crucial for international B2B buyers. Here are some key properties that should be considered:
1. Material Grade: Why Is It Important?
Material grade refers to the classification of the materials used in manufacturing motor accessories, which directly impacts durability and performance. Common materials include steel, aluminum, and high-grade plastics. Buyers should prioritize materials that meet specific industry standards to ensure longevity and reliability, especially in harsh environments typical in regions like Africa and the Middle East.
2. Tolerance: How Does It Affect Performance?
Tolerance is the permissible limit of variation in a physical dimension of a part. For motor accessories, maintaining tight tolerances is essential for compatibility and function. Poor tolerance can lead to increased wear and tear, affecting the overall efficiency of the vehicle. B2B buyers should inquire about the tolerance levels during procurement to avoid costly replacements or repairs.
3. Load Capacity: What Should Buyers Consider?
Load capacity indicates the maximum weight that a component can support safely. This specification is particularly important for accessories like suspension parts and towing equipment. Buyers should assess the load requirements based on the intended application to prevent failure and ensure safety.
4. Corrosion Resistance: Why Is It Critical?
Corrosion resistance is a measure of a material’s ability to withstand degradation from environmental factors. For buyers in humid climates or regions with high salt content in the air, selecting accessories with high corrosion resistance can extend the lifespan of the products and reduce maintenance costs.
5. Temperature Range: How Does It Impact Functionality?
The temperature range defines the operational limits of motor accessories under varying thermal conditions. Accessories must perform optimally within these ranges to avoid malfunctions. Buyers should ensure that the products can withstand extreme conditions prevalent in their operational environments, such as high temperatures in South America or cold climates in parts of Europe.
What Are Common Trade Terms for Motor Accessories Suppliers?
Familiarity with trade terminology is essential for effective communication and negotiation. Here are some common terms that B2B buyers should understand:
1. OEM (Original Equipment Manufacturer): What Does It Mean?
OEM refers to companies that produce parts or equipment that may be marketed by another manufacturer. Understanding whether a supplier is an OEM can help buyers gauge the quality and authenticity of the products. OEM parts often come with warranties and are designed to meet specific vehicle standards, making them a safer choice.
2. MOQ (Minimum Order Quantity): How Does It Impact Procurement?
MOQ is the minimum number of units a supplier requires to process an order. This term is critical for budgeting and inventory management, as it can affect cash flow. B2B buyers should clarify MOQ with suppliers to ensure they can meet their needs without overcommitting resources.
3. RFQ (Request for Quotation): Why Is It Useful?
An RFQ is a document sent to suppliers requesting pricing and availability for specific products. It is a crucial tool for B2B buyers as it helps compare costs, terms, and supplier capabilities. Crafting a detailed RFQ can lead to better pricing and ensure that all essential specifications are met.
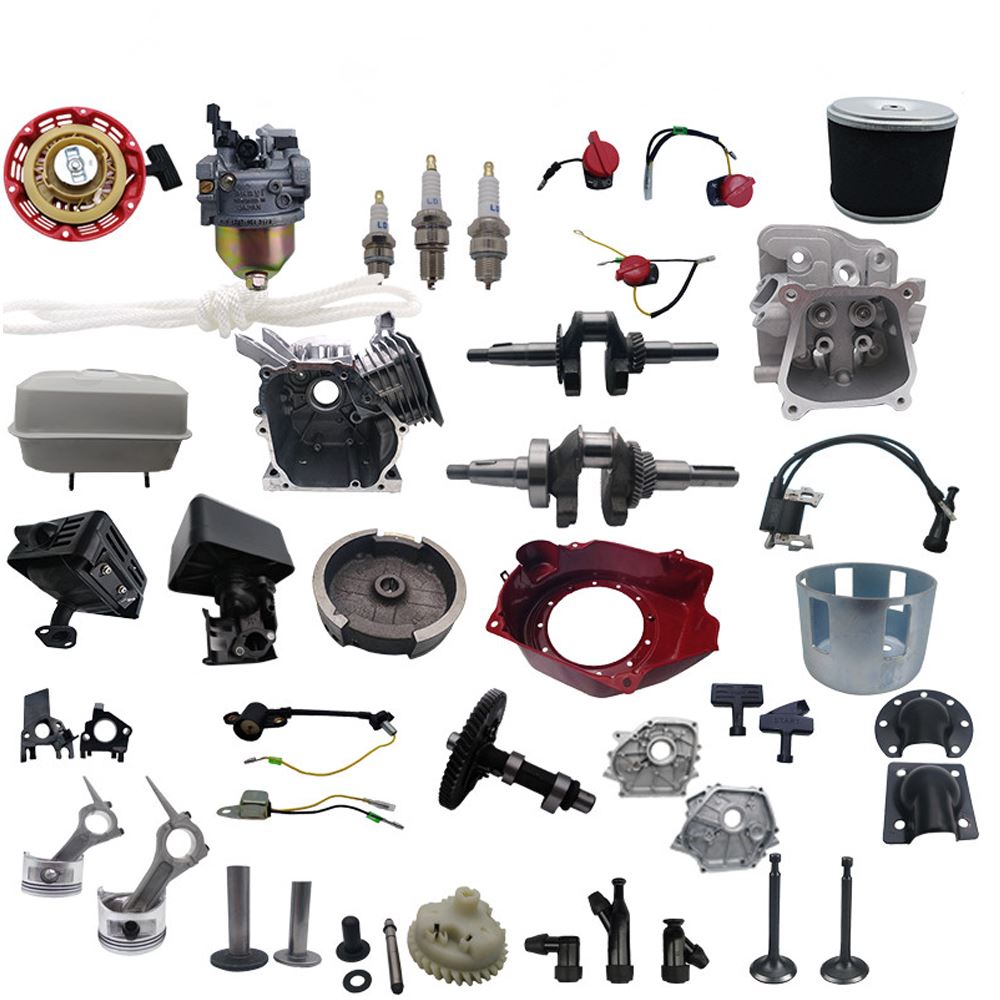
A stock image related to motor accessories supplier.
4. Incoterms: What Are They and Why Are They Important?
Incoterms are a set of international trade terms that define the responsibilities of buyers and sellers in shipping goods. Familiarity with Incoterms such as FOB (Free on Board) and CIF (Cost, Insurance, and Freight) helps buyers understand their liabilities and the total costs involved in international transactions, which is particularly important for buyers from diverse regions.
5. Lead Time: What Should Buyers Know?
Lead time is the period from placing an order to receiving the goods. Understanding lead times is vital for planning and inventory management. Buyers should discuss lead times with suppliers to ensure that they align with operational schedules, especially in industries with tight deadlines.
By familiarizing themselves with these essential technical properties and trade terms, B2B buyers can make informed decisions, ensuring that they procure high-quality motor accessories that meet their operational needs.
Navigating Market Dynamics and Sourcing Trends in the motor accessories supplier Sector
What Are the Current Market Dynamics and Key Trends in the Motor Accessories Supplier Sector?
The motor accessories supplier sector is witnessing significant transformations driven by various global factors. Key market drivers include the increasing demand for vehicle personalization, the growth of e-commerce, and advancements in automotive technology. International B2B buyers, particularly those from Africa, South America, the Middle East, and Europe, are increasingly focusing on sourcing high-quality accessories that enhance vehicle performance and aesthetics.
Emerging B2B technology trends such as digital procurement platforms and data analytics are reshaping how suppliers and buyers interact. These technologies facilitate real-time inventory management, streamline order processes, and enhance supply chain transparency. Additionally, the rise of AI and machine learning is enabling suppliers to forecast demand more accurately, allowing buyers to make informed purchasing decisions.
Regional dynamics also play a crucial role. For example, in Europe, stringent regulations regarding automotive emissions are pushing suppliers to develop eco-friendly accessories. In contrast, markets in Africa and South America are experiencing rapid growth due to rising disposable incomes and increased vehicle ownership. Understanding these regional dynamics will empower international buyers to identify opportunities and mitigate risks when sourcing motor accessories.
How Does Sustainability and Ethical Sourcing Impact the Motor Accessories Supplier Sector?
Sustainability and ethical sourcing are increasingly becoming critical factors for B2B buyers in the motor accessories sector. The environmental impact of production processes, particularly in terms of carbon emissions and waste generation, is under scrutiny. Buyers are now prioritizing suppliers who demonstrate a commitment to sustainable practices, such as using recycled materials and reducing their carbon footprint.
The importance of ethical supply chains cannot be overstated. Buyers are increasingly concerned about the labor practices involved in the production of motor accessories. Ensuring that suppliers adhere to ethical labor practices not only fosters goodwill but also protects brands from potential reputational damage. Certifications such as ISO 14001 (Environmental Management) and Fair Trade are becoming essential in verifying the sustainability claims of suppliers.
Moreover, the trend towards green materials—such as biodegradable plastics and sustainably sourced metals—offers buyers an avenue to enhance their product offerings while appealing to environmentally conscious consumers. By aligning sourcing strategies with sustainability goals, B2B buyers can differentiate themselves in a competitive market.
What Is the Historical Context of the Motor Accessories Supplier Sector?
The motor accessories supplier sector has evolved significantly over the past few decades. Initially dominated by local artisans and small-scale manufacturers, the industry has transitioned into a more globalized market characterized by large suppliers and extensive distribution networks.
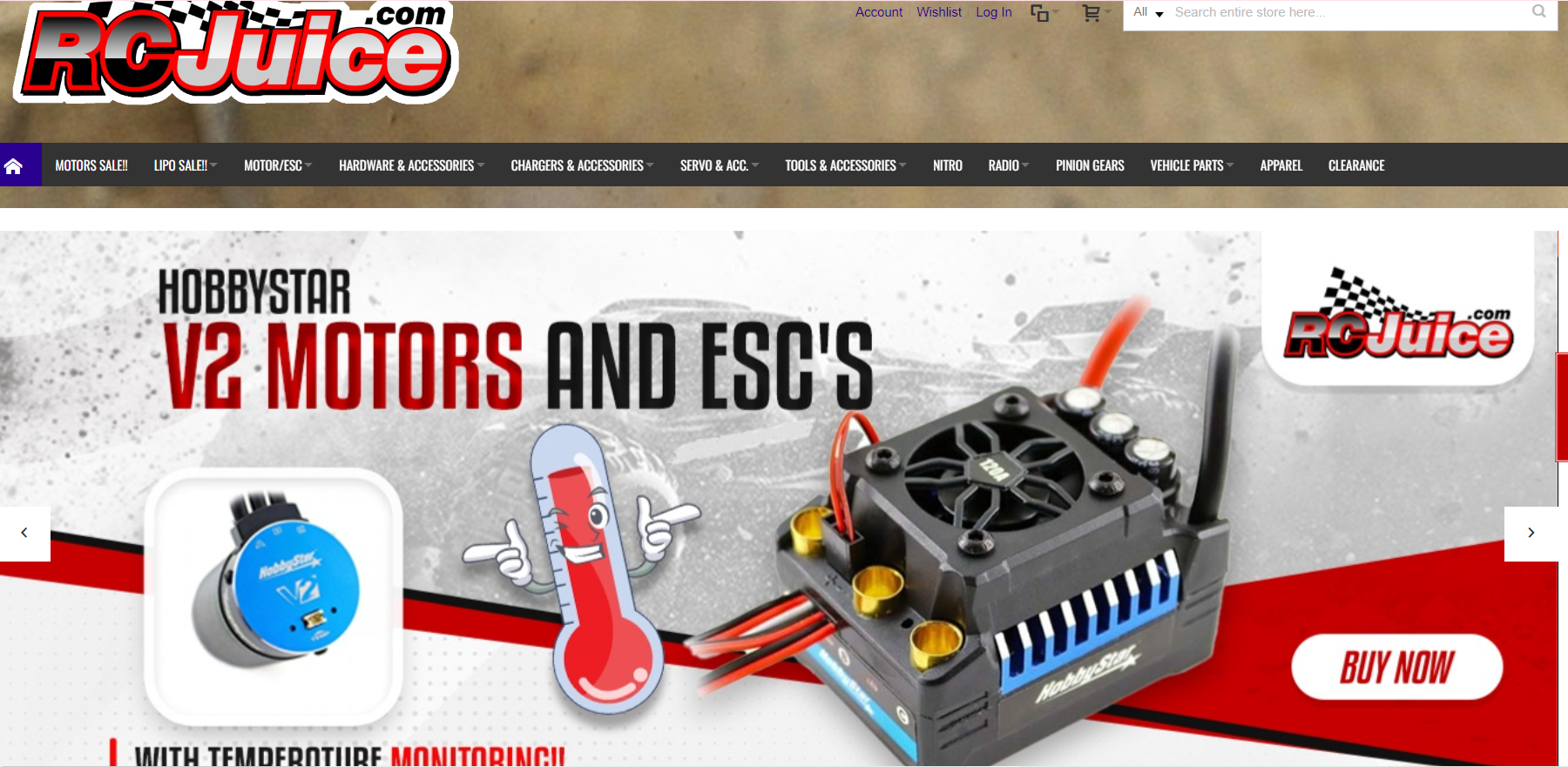
A stock image related to motor accessories supplier.
The 1980s and 1990s saw the introduction of advanced manufacturing technologies, allowing for mass production of motor accessories. This shift not only reduced costs but also increased the variety of products available to consumers. The advent of the internet in the late 1990s further transformed the sector, enabling suppliers to reach a global audience and facilitating the rise of e-commerce platforms.
Today, the market is shaped by a combination of technological advancements, consumer preferences for customization, and a growing emphasis on sustainability. Understanding this historical evolution provides B2B buyers with context for current trends and challenges within the sector, helping them make more informed sourcing decisions.
Frequently Asked Questions (FAQs) for B2B Buyers of motor accessories supplier
-
How do I solve the challenge of finding reliable motor accessories suppliers?
Finding a reliable motor accessories supplier requires thorough research and vetting. Start by identifying suppliers with a strong online presence and positive reviews. Utilize platforms like Alibaba or industry-specific directories to find verified suppliers. Request references and conduct background checks to assess their reputation. Additionally, consider attending trade shows or industry events to network and meet suppliers face-to-face. This proactive approach will help you establish trustworthy relationships that are essential for long-term success. -
What is the best way to evaluate motor accessories suppliers for quality?
To evaluate suppliers for quality, start by requesting product samples and conducting thorough quality assessments. Look for suppliers who adhere to international quality standards such as ISO certification. Review their production processes and quality control measures, including the use of advanced technology and materials. Additionally, consider obtaining third-party inspections or certifications to validate their quality claims. Engaging in open communication about quality expectations can also ensure alignment and foster a collaborative relationship. -
What are the common minimum order quantities (MOQs) for motor accessories?
Minimum order quantities (MOQs) can vary significantly among motor accessories suppliers, often ranging from 100 to 1,000 units or more, depending on the product type and supplier capabilities. It’s essential to discuss MOQs upfront to determine if they align with your purchasing needs. Some suppliers may be flexible with MOQs for new clients or bulk orders, while others may have strict policies. Always negotiate terms to ensure that the MOQ fits your inventory strategy and budget. -
What payment terms should I expect when dealing with international suppliers?
Payment terms with international suppliers can vary widely, but common options include advance payment, letters of credit, and payment upon delivery. Many suppliers require a deposit (often 30-50%) upfront to initiate production, with the balance due before shipment. It’s crucial to discuss payment terms early in negotiations and ensure they are documented in a contract. Be mindful of currency exchange rates and transaction fees, as these can impact the overall cost of your order. -
How can I ensure timely logistics and shipping for my motor accessories orders?
To ensure timely logistics and shipping, establish clear communication with your supplier regarding production timelines and shipping methods. Choose a reliable freight forwarder with experience in handling motor accessories and understand the customs regulations in your destination country. Consider using incoterms (like FOB or CIF) to clarify responsibilities for shipping costs and risks. Additionally, maintain a buffer in your ordering schedule to account for potential delays, especially during peak seasons. -
What are the key factors to consider in customizing motor accessories?
When considering customization of motor accessories, focus on factors such as design specifications, material selection, and compliance with local regulations. Engage in detailed discussions with your supplier about your specific needs and ensure they have the capability to fulfill them. Understand the implications of customizations on lead times and costs, as these can vary. Additionally, request prototypes to evaluate the quality and functionality of the customized products before committing to larger orders. -
How do I handle quality assurance and inspection of motor accessories?
To manage quality assurance, establish a robust inspection process that includes both pre-production and post-production checks. Work with your supplier to outline quality standards and inspection criteria in advance. Consider hiring third-party inspection services to perform checks at various stages of production, ensuring that products meet your specifications. Document all findings and address any quality issues immediately to prevent them from affecting your supply chain. -
What should I know about the legal requirements for importing motor accessories?
When importing motor accessories, familiarize yourself with the legal requirements of your destination country, including customs duties, import taxes, and product compliance regulations. Research any specific certifications or standards that your products must meet to enter the market. Ensure that your supplier provides all necessary documentation, such as certificates of origin and safety compliance. Working with a customs broker can simplify the process and help avoid delays or penalties associated with non-compliance.
Important Disclaimer & Terms of Use
⚠️ Important Disclaimer
The information provided in this guide, including content regarding manufacturers, technical specifications, and market analysis, is for informational and educational purposes only. It does not constitute professional procurement advice, financial advice, or legal advice.
While we have made every effort to ensure the accuracy and timeliness of the information, we are not responsible for any errors, omissions, or outdated information. Market conditions, company details, and technical standards are subject to change.
B2B buyers must conduct their own independent and thorough due diligence before making any purchasing decisions. This includes contacting suppliers directly, verifying certifications, requesting samples, and seeking professional consultation. The risk of relying on any information in this guide is borne solely by the reader.
Strategic Sourcing Conclusion and Outlook for motor accessories supplier
In the ever-evolving landscape of the motor accessories market, strategic sourcing emerges as a critical driver of competitive advantage for international B2B buyers. By leveraging global supplier networks, businesses can tap into diverse product offerings that meet specific regional demands, whether in Africa, South America, the Middle East, or Europe. Buyers should prioritize partnerships with suppliers who demonstrate adaptability, innovation, and a commitment to quality, ensuring that they can respond swiftly to market changes and consumer preferences.
Moreover, understanding local regulations and cultural nuances is essential for seamless transactions and effective supply chain management. Establishing robust communication channels and fostering long-term relationships with suppliers can significantly mitigate risks associated with sourcing and logistics.
As we look to the future, international B2B buyers are encouraged to embrace technology and data analytics in their sourcing strategies. These tools can provide valuable insights into market trends, supplier performance, and cost efficiencies. By adopting a proactive approach to strategic sourcing, businesses can enhance their operational resilience and drive sustainable growth.
Now is the time to assess your sourcing strategies and engage with innovative motor accessories suppliers who can support your business objectives in a dynamic global marketplace.