Enhance Quality: The Ultimate Cables Custom Guide (2025)
Introduction: Navigating the Global Market for cables custom
In today’s interconnected world, sourcing custom cables can present a myriad of challenges for international B2B buyers, particularly those operating in emerging markets like Africa, South America, the Middle East, and Europe. The complexity of navigating diverse supplier landscapes and ensuring quality and compliance can often feel overwhelming. This guide aims to demystify the global market for custom cables, offering valuable insights into various types, applications, and critical factors influencing purchasing decisions.
As you explore this comprehensive resource, you will gain a deeper understanding of the different categories of custom cables available, ranging from industrial to telecommunications applications. Additionally, we will delve into essential supplier vetting processes to help you identify reliable partners who can meet your specific needs. Cost considerations, including pricing trends and budget management strategies, will also be addressed, equipping you with the knowledge to negotiate effectively.
By leveraging the information provided in this guide, B2B buyers from regions such as Brazil and Mexico will be empowered to make informed purchasing decisions that align with their operational goals. Whether you are seeking to enhance your supply chain or improve product performance, this resource will serve as a vital tool in your journey towards successful sourcing of custom cables, ensuring you stay competitive in the global market.
Understanding cables custom Types and Variations
Type Name | Key Distinguishing Features | Primary B2B Applications | Brief Pros & Cons for Buyers |
---|---|---|---|
Custom Power Cables | High voltage, tailored lengths, specialized connectors | Manufacturing, energy distribution | Pros: Enhanced safety, tailored for specific needs. Cons: Higher initial costs, longer lead times. |
Custom Data Cables | Shielding options, varied gauge sizes, specific connectors | Telecommunications, data centers | Pros: Improved signal integrity, reduced interference. Cons: Complexity in specifications, potential over-engineering. |
Custom Control Cables | Multi-conductor designs, flexible materials, temperature resistance | Automation, robotics | Pros: Versatile applications, excellent durability. Cons: May require extensive testing for new applications. |
Custom Coaxial Cables | Impedance matching, specific shielding, length variations | Broadcasting, satellite communications | Pros: Reliable signal transmission, tailored for specific frequencies. Cons: Limited flexibility in design changes. |
Custom Fiber Optic Cables | Single/multi-mode options, various jacket materials, connector types | High-speed data transfer, medical devices | Pros: High bandwidth, immune to electromagnetic interference. Cons: Higher installation costs, fragility in handling. |
What Are Custom Power Cables and Their B2B Applications?
Custom power cables are designed to meet specific electrical requirements, often used in manufacturing and energy distribution sectors. Their key features include high voltage capacity, tailored lengths, and specialized connectors that ensure safety and efficiency. B2B buyers should consider the initial costs versus the long-term benefits of enhanced safety and reliability. Additionally, understanding the specific voltage and current ratings required for the application is crucial.
How Do Custom Data Cables Enhance Business Operations?
Custom data cables are essential for telecommunications and data centers, offering shielding options and varied gauge sizes to enhance signal integrity. These cables are tailored to reduce interference, which is critical in environments with high data traffic. Buyers need to carefully assess the specifications to avoid over-engineering, which can lead to unnecessary costs. Understanding the specific data transfer rates required for their operations will guide B2B buyers in making informed choices.
What Makes Custom Control Cables Ideal for Automation?
Custom control cables feature multi-conductor designs and flexible materials that withstand various environmental conditions, making them ideal for automation and robotics applications. Their versatility allows for use in diverse industries, but buyers must consider the durability and temperature resistance required for their specific applications. Extensive testing may be necessary to ensure performance in new environments, adding to the purchasing complexity.
Why Are Custom Coaxial Cables Important for Broadcasting?
Custom coaxial cables are vital in broadcasting and satellite communications, designed for impedance matching and specific shielding to optimize signal transmission. Their reliability in carrying signals over long distances makes them a preferred choice. However, buyers should be aware of the limitations in flexibility regarding design changes once the specifications are set. Understanding the frequency requirements of their applications will help in choosing the right coaxial cable.
How Do Custom Fiber Optic Cables Support High-Speed Data Transfer?
Custom fiber optic cables are engineered for high-speed data transfer, featuring single or multi-mode options and various jacket materials. They are immune to electromagnetic interference, making them ideal for sensitive applications such as medical devices. While they offer significant advantages in bandwidth, buyers must factor in higher installation costs and the fragility of the materials during handling. A thorough understanding of the installation environment and data requirements will assist B2B buyers in selecting the right fiber optic solutions.
Related Video: Custom Cables & Guide to Crimping Dupont PCB Interconnect Cables
Key Industrial Applications of cables custom
Industry/Sector | Specific Application of cables custom | Value/Benefit for the Business | Key Sourcing Considerations for this Application |
---|---|---|---|
Renewable Energy | Custom cables for solar power installations | Enhanced efficiency and reliability in energy systems | Compliance with local regulations and certifications |
Telecommunications | Tailored cables for high-speed networks | Improved data transmission and reduced latency | Compatibility with existing infrastructure and scalability |
Manufacturing | Specialized cables for machinery and robotics | Increased operational efficiency and safety | Durability and resistance to environmental factors |
Transportation and Logistics | Custom cables for electric vehicles (EVs) | Supporting the transition to sustainable transport | Weight, flexibility, and heat resistance requirements |
Construction | Customized wiring solutions for smart buildings | Enhanced automation and energy management | Adherence to safety standards and building codes |
How Are Custom Cables Used in Renewable Energy Applications?
In the renewable energy sector, custom cables play a crucial role in solar power installations. These cables are designed to withstand harsh environmental conditions while ensuring optimal energy transfer from solar panels to inverters and storage systems. By using cables that meet specific voltage and temperature ratings, businesses can enhance the efficiency and reliability of their energy systems. International buyers must consider local regulatory compliance and necessary certifications to ensure their installations are safe and effective.
What Are the Benefits of Custom Cables in Telecommunications?
Telecommunications relies heavily on tailored cables for high-speed network setups. Custom cables are engineered to support specific data transmission needs, enabling faster internet speeds and reduced latency. This is particularly important for businesses in regions with growing digital demands, such as Africa and South America. Buyers should prioritize compatibility with existing infrastructure and the scalability of solutions to accommodate future growth.
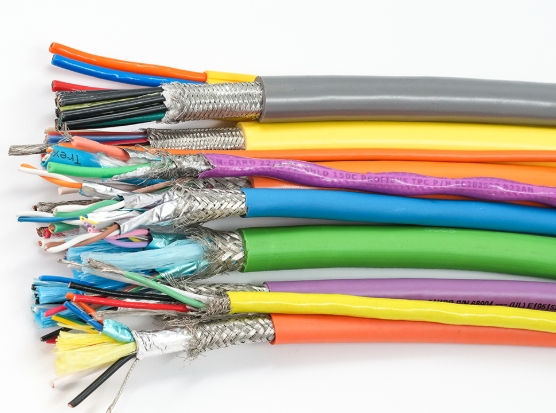
A stock image related to cables custom.
How Do Custom Cables Enhance Manufacturing Operations?
In manufacturing, specialized cables are essential for the operation of machinery and robotics. These cables are designed to provide robust performance under heavy-duty conditions, thereby increasing operational efficiency and safety. They can also be customized to meet unique requirements such as flexibility and resistance to chemicals. For international buyers, sourcing durable cables that can withstand environmental factors is critical to ensuring long-term productivity.
Why Are Custom Cables Important for Electric Vehicles?
The transportation sector, particularly electric vehicles (EVs), increasingly relies on custom cables for efficient power management. These cables must be lightweight, flexible, and capable of handling high temperatures to support the growing demand for EVs. By investing in specialized cables, businesses can contribute to the transition toward sustainable transport solutions. Buyers should focus on weight, flexibility, and heat resistance when selecting cables for this application.
How Do Custom Cables Contribute to Smart Building Construction?
In the construction industry, customized wiring solutions are vital for developing smart buildings that integrate automation and energy management systems. Custom cables facilitate seamless communication between devices, enhancing operational efficiency and reducing energy consumption. International buyers must ensure that their solutions adhere to local safety standards and building codes to avoid compliance issues and ensure the longevity of their installations.
Related Video: Uses and Gratifications Theory – UGT
3 Common User Pain Points for ‘cables custom’ & Their Solutions
Scenario 1: Inconsistent Quality Across Suppliers
The Problem:
Many B2B buyers, especially those in emerging markets like Africa and South America, face the challenge of inconsistent product quality when sourcing custom cables. This inconsistency can stem from varying manufacturing standards and practices among suppliers. For instance, a buyer in Brazil may find that cables sourced from one supplier have a high failure rate, while those from another supplier are more reliable but come at a premium. This unpredictability can lead to project delays, increased costs, and damage to the buyer’s reputation.
The Solution:
To mitigate quality issues, B2B buyers should conduct thorough due diligence on potential suppliers. This involves requesting samples and performing rigorous testing before placing bulk orders. Establishing a quality assurance protocol that includes inspection and testing criteria can help ensure that only cables meeting specific standards are accepted. Additionally, leveraging third-party inspection services can provide an unbiased assessment of product quality. Buyers should also consider forming long-term relationships with suppliers known for their reliability, as consistent partnerships often lead to improved quality and better pricing over time.
Scenario 2: Complex Customization Requirements
The Problem:
B2B buyers frequently encounter challenges when their projects require highly specific customization of cables, such as unique lengths, specialized coatings, or particular electrical properties. For example, a telecommunications company in the Middle East may need cables that can withstand extreme temperatures and harsh environmental conditions. However, not all suppliers have the capability or expertise to accommodate such specialized requests, which can lead to project delays and increased costs.
The Solution:
To effectively address customization challenges, buyers should begin by clearly defining their specifications and requirements. This includes detailed documentation that outlines the intended application, environmental conditions, and any regulatory standards the cables must meet. Once these specifications are established, engaging with suppliers who specialize in custom cable solutions is crucial. Buyers should also inquire about the supplier’s previous experience with similar projects and request case studies or references. Utilizing technology, such as CAD software, can help visualize the required specifications, making it easier to communicate with suppliers and ensure that the final product aligns with project needs.
Scenario 3: Navigating Regulatory Compliance
The Problem:
International B2B buyers often grapple with the complexities of regulatory compliance when sourcing custom cables, particularly when operating across multiple regions. For instance, a manufacturer in Europe may face stringent safety and environmental regulations that differ significantly from those in South America or Africa. Failure to comply can result in costly fines, legal challenges, and disruptions in supply chains.
The Solution:
To navigate these regulatory landscapes effectively, buyers should invest in understanding the compliance requirements for each region they operate in. This may involve consulting with legal experts or compliance specialists familiar with both local and international standards. Buyers should also seek suppliers that are not only compliant with their own region’s regulations but also have certifications that validate their adherence to international standards, such as ISO or RoHS. Additionally, maintaining open lines of communication with suppliers regarding their compliance processes can foster transparency and ensure that all parties are aligned on regulatory expectations. Establishing a compliance checklist can also help streamline the procurement process and mitigate risks associated with non-compliance.
Strategic Material Selection Guide for cables custom
When selecting materials for custom cables, international B2B buyers must consider various factors that impact performance, cost, and application suitability. Below, we analyze four common materials used in custom cables, focusing on their properties, advantages, disadvantages, and specific considerations for international markets, particularly in Africa, South America, the Middle East, and Europe.
What Are the Key Properties of Copper in Custom Cables?
Copper is one of the most widely used materials in cable manufacturing due to its excellent electrical conductivity and thermal properties. It typically has a temperature rating of up to 200°C and can withstand moderate pressure levels. Its corrosion resistance is decent, particularly when coated or alloyed.
Pros and Cons of Copper Cables
Copper cables offer high durability and reliable performance, making them suitable for various applications, including power transmission and telecommunications. However, the high cost of copper can be a significant drawback, especially for large-scale projects. Additionally, the manufacturing complexity can increase costs further due to the need for specialized processes.
Impact on Application
Copper is compatible with a wide range of media, including water and oil, making it versatile. However, its susceptibility to corrosion in harsh environments necessitates additional protective measures.
Considerations for International Buyers
Buyers from regions such as Africa and South America should be aware of local regulations regarding copper use and recycling, as well as compliance with standards like ASTM and IEC. In Europe, buyers must also consider RoHS compliance to avoid hazardous substances.
How Does Aluminum Compare as a Material for Custom Cables?
Aluminum is another popular choice for cable manufacturing, especially in applications requiring lightweight materials. It has a temperature rating similar to copper but is less effective in high-pressure environments. Its corrosion resistance is better than that of copper, particularly when anodized.
Pros and Cons of Aluminum Cables
The primary advantage of aluminum is its lower cost and lightweight nature, making it easier to handle and install. However, aluminum cables have lower conductivity than copper, which may necessitate larger diameters to achieve the same performance, potentially offsetting cost savings.
Impact on Application
Aluminum is suitable for overhead power lines and applications where weight is a critical factor. However, its compatibility with certain media, like aggressive chemicals, may be limited.
Considerations for International Buyers
In regions like the Middle East, where environmental conditions can be harsh, buyers should ensure that aluminum cables meet local standards for corrosion resistance. Compliance with international standards such as DIN and JIS is also crucial.
What Are the Benefits of Using Polyvinyl Chloride (PVC) in Custom Cables?
PVC is a widely used insulating material in custom cables due to its excellent electrical insulation properties and flexibility. It can withstand temperatures up to 70°C and offers good resistance to moisture and chemicals.
Pros and Cons of PVC Cables
PVC cables are cost-effective and easy to manufacture, making them a popular choice for various applications, including residential and commercial wiring. However, PVC can become brittle over time, particularly when exposed to UV light, which may limit its lifespan.
Impact on Application
PVC is compatible with a range of media, including water and oils, making it suitable for indoor and outdoor applications. However, it may not be ideal for high-temperature environments.
Considerations for International Buyers
Buyers in Europe must ensure that PVC cables comply with REACH regulations concerning chemical safety. In South America, local standards may vary, so understanding regional compliance is essential.
How Does Cross-Linked Polyethylene (XLPE) Enhance Cable Performance?
XLPE is known for its superior thermal stability and electrical insulation properties. It can operate at temperatures up to 90°C and is highly resistant to moisture and chemicals, making it suitable for demanding environments.
Pros and Cons of XLPE Cables
XLPE cables offer excellent durability and performance, making them ideal for high-voltage applications. However, they are generally more expensive than PVC and require more complex manufacturing processes.
Impact on Application
XLPE is particularly effective in underground installations and environments where high temperatures and moisture are prevalent. It is compatible with various media, including oils and chemicals.
Considerations for International Buyers
International buyers should be aware of the specific standards governing XLPE use in their regions. Compliance with ASTM and IEC standards is critical, especially in Europe, where regulations are stringent.
Summary Table of Material Selection for Custom Cables
Material | Typical Use Case for cables custom | Key Advantage | Key Disadvantage/Limitation | Relative Cost (Low/Med/High) |
---|---|---|---|---|
Copper | Power transmission, telecommunications | High conductivity and durability | High cost and manufacturing complexity | High |
Aluminum | Overhead power lines | Lightweight and cost-effective | Lower conductivity than copper | Medium |
PVC | Residential and commercial wiring | Cost-effective and flexible | Can become brittle over time | Low |
XLPE | High-voltage and underground cables | Superior thermal stability and insulation | Higher cost and complex manufacturing | High |
This strategic guide aims to equip international B2B buyers with the knowledge needed to make informed material selections for custom cables, considering both performance and compliance with regional standards.
In-depth Look: Manufacturing Processes and Quality Assurance for cables custom
What Are the Key Stages in the Manufacturing Process for Custom Cables?
The manufacturing process for custom cables is a complex and multifaceted operation that involves several critical stages. Understanding these stages can help B2B buyers make informed decisions when selecting suppliers.
1. Material Preparation
The first step in the custom cable manufacturing process is material preparation. This involves sourcing high-quality raw materials, such as copper or aluminum for conductors, and various insulating materials like PVC, polyethylene, or rubber. Buyers should inquire about the supplier’s material sourcing practices, as the quality of raw materials directly impacts the performance and longevity of the cables.
Additionally, proper storage conditions must be maintained to prevent material degradation. Buyers should ensure that suppliers adhere to international standards regarding the quality of materials, as this will significantly influence the final product’s reliability.
2. Forming the Cable Structure
Once materials are prepared, the next stage involves forming the cable structure. This includes processes like wire drawing, which reduces the diameter of the metal wires, and stranding, where multiple wires are twisted together to form a conductor. Techniques such as extrusion are also employed to apply insulation around the conductors.
At this stage, buyers should look for suppliers that utilize advanced technologies like computer-controlled machinery to ensure precision and consistency. A reliable supplier will also have capabilities for producing cables in various configurations, such as multi-core cables or cables with additional shielding.
3. Assembly of Components
After the cable structure is formed, the assembly process begins. This step may involve adding additional elements such as shields, jackets, and connectors. The assembly must be conducted in controlled environments to minimize contamination and defects.
B2B buyers should verify if suppliers have established assembly protocols that follow international best practices. Inquiring about the specific equipment used and the qualifications of personnel involved in the assembly can provide insights into the potential quality of the final product.
4. Finishing Touches
The final stage in the manufacturing process involves finishing touches, including testing, marking, and packaging the cables. This stage is crucial as it ensures that the product meets all specified requirements before delivery.
Buyers should pay attention to the packaging methods used by suppliers, as this affects the cables’ integrity during transit. Proper labeling is also essential for traceability and compliance with international regulations.
How Is Quality Assurance Implemented in Custom Cable Manufacturing?
Quality assurance (QA) is an integral part of the manufacturing process for custom cables, ensuring that products meet both client specifications and industry standards.
Relevant International Standards for Custom Cables
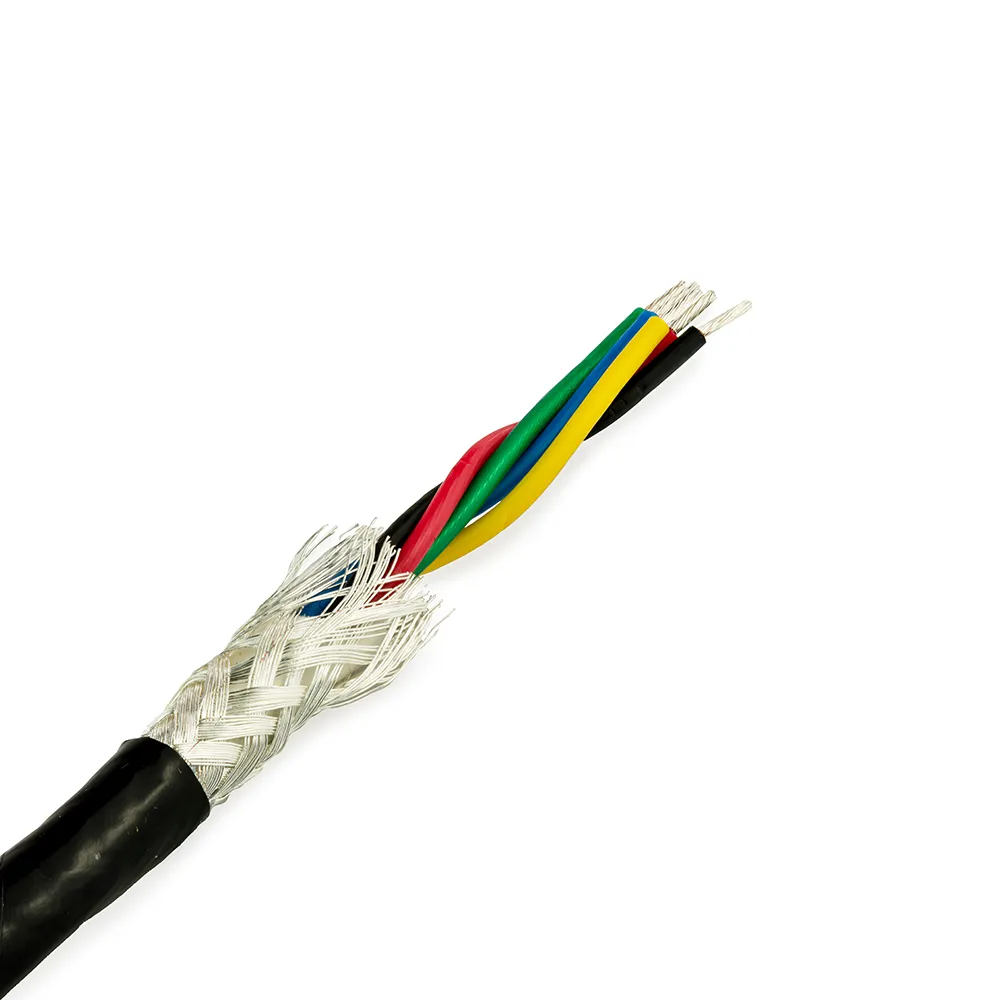
A stock image related to cables custom.
B2B buyers should be aware of the international standards that govern cable manufacturing. ISO 9001 is a widely recognized standard that focuses on quality management systems, and compliance with this standard indicates that a supplier has implemented processes for continuous improvement and customer satisfaction.
In addition to ISO certifications, industry-specific standards such as CE marking for European markets and API standards for oil and gas applications should also be considered. Buyers should ensure that suppliers have the necessary certifications to comply with the regulations in their respective regions.
What Are the Key Quality Control Checkpoints?
Quality control (QC) is performed at various checkpoints throughout the manufacturing process. Key QC checkpoints include:
-
Incoming Quality Control (IQC): This involves inspecting raw materials upon arrival to ensure they meet specified quality standards.
-
In-Process Quality Control (IPQC): Conducted during the manufacturing stages, IPQC checks for defects and ensures that processes are in control.
-
Final Quality Control (FQC): This step verifies that the finished product meets all specifications before shipping.
Buyers should ask suppliers for detailed QC procedures and documentation, as this reflects the rigor of their quality assurance processes.
Common Testing Methods for Custom Cables
Testing is a critical component of quality assurance. Common testing methods include:
-
Electrical Testing: Measures parameters such as resistance, capacitance, and insulation resistance to ensure proper functionality.
-
Mechanical Testing: Assesses the physical characteristics of the cables, including tensile strength and flexibility.
-
Environmental Testing: Evaluates the cables’ performance under various environmental conditions, such as temperature extremes and humidity.
B2B buyers should request test reports and certifications from suppliers to verify that the cables have passed necessary tests.
How Can B2B Buyers Verify Supplier Quality Control?
To ensure quality assurance in custom cable manufacturing, B2B buyers can take several proactive steps:
Conducting Supplier Audits
One effective way to verify a supplier’s quality control measures is through on-site audits. Buyers should assess the supplier’s facilities, machinery, and processes to understand their quality management practices. This can also include evaluating the qualifications of the workforce and the maintenance of equipment.
Requesting Quality Control Reports
Buyers should request access to quality control reports that outline the results of various tests and inspections performed on the cables. These reports should detail compliance with international standards and any corrective actions taken in case of non-conformance.
Engaging Third-Party Inspection Services
Utilizing third-party inspection services can provide an unbiased evaluation of the supplier’s quality control processes. These independent organizations can conduct comprehensive inspections and testing to ensure that the cables meet all required specifications.
What Are the Quality Control Nuances for International B2B Buyers?
International B2B buyers, particularly from Africa, South America, the Middle East, and Europe, should be aware of specific nuances in quality control when sourcing custom cables:
-
Regulatory Compliance: Different regions have varying regulations regarding electrical and safety standards. Buyers must ensure that suppliers are compliant with the regulations applicable to their target markets.
-
Cultural Considerations: Understanding cultural differences in business practices can aid in establishing better communication and expectations regarding quality assurance.
-
Logistical Challenges: International shipping can introduce risks such as damage or delays. Buyers should discuss quality assurance measures for packaging and handling to mitigate these risks.
By following these guidelines and insights, international B2B buyers can make informed decisions when sourcing custom cables, ensuring that they receive high-quality products that meet their specific needs.
Practical Sourcing Guide: A Step-by-Step Checklist for ‘cables custom’
Introduction
Sourcing custom cables for your business needs can be a complex process, especially when navigating international markets. This guide provides a practical checklist to help B2B buyers streamline their procurement process, ensuring that you select the right supplier and product that meets your specific requirements. Whether you are in Africa, South America, the Middle East, or Europe, following these steps will enhance your sourcing efficiency and effectiveness.
Step 1: Define Your Technical Specifications
Before engaging with suppliers, it’s vital to have a clear understanding of your technical requirements. This includes specifications such as cable type, gauge, insulation material, length, and any industry standards that must be met.
- Consider application needs: Understand the environment where the cables will be used (e.g., temperature, exposure to chemicals) to ensure compatibility.
- Identify regulatory standards: Research any local or international compliance requirements that may apply to your cables.
Step 2: Research Potential Suppliers
Start your search by identifying suppliers that specialize in custom cables. Utilize online directories, trade shows, and industry recommendations to compile a list of potential partners.
- Evaluate geographical proximity: Consider suppliers that are either local or have a strong logistical network in your region to minimize shipping times and costs.
- Check industry reputation: Look for reviews and testimonials from other businesses in your sector to gauge reliability and service quality.
Step 3: Evaluate Supplier Certifications
It’s crucial to verify that your potential suppliers hold the necessary certifications. This not only ensures product quality but also compliance with international standards.
- Request documentation: Ask for certificates such as ISO 9001 for quality management or UL certification for safety standards.
- Understand the implications: Suppliers without proper certifications may lead to compliance issues or product failures, impacting your operations.
Step 4: Request Samples and Prototypes
Before making a bulk purchase, request samples or prototypes of the custom cables. This step is essential to assess the quality and suitability of the product for your specific application.
- Conduct thorough testing: Evaluate the samples under real-world conditions to ensure they meet your expectations.
- Solicit feedback from team members: Involve your technical team in the evaluation process to gather insights on performance and usability.
Step 5: Negotiate Terms and Pricing
Once you have shortlisted suppliers, it’s time to negotiate pricing and terms. This includes payment terms, delivery schedules, and warranty conditions.
- Be clear about your budget: Share your budget constraints upfront to encourage suppliers to provide competitive offers.
- Explore bulk discounts: Discuss potential discounts for larger orders or long-term contracts to maximize your cost savings.
Step 6: Establish Communication Channels
Effective communication is key to a successful sourcing relationship. Establish clear communication channels with your chosen supplier to facilitate updates and address concerns promptly.
- Set expectations for responsiveness: Agree on timelines for responses to inquiries or issues that may arise.
- Utilize technology: Consider using project management tools or platforms to keep track of communications and milestones.
Step 7: Monitor and Evaluate Supplier Performance
After placing your order, continuously monitor the supplier’s performance to ensure they meet your expectations and contractual obligations.
- Gather feedback from your team: Regularly solicit input from users of the cables to identify any issues early on.
- Review performance metrics: Establish KPIs (Key Performance Indicators) to assess delivery times, product quality, and customer service.
By following these steps, international B2B buyers can effectively navigate the sourcing of custom cables, ensuring they find reliable suppliers that meet their specific needs.
Comprehensive Cost and Pricing Analysis for cables custom Sourcing
What Are the Key Cost Components in Custom Cable Sourcing?
Understanding the cost structure of custom cables is essential for international B2B buyers. The primary cost components include:
-
Materials: The type of materials used significantly affects the overall cost. High-quality copper, aluminum, or specialized insulation materials will drive up the price. Buyers should assess the specific requirements of their projects to determine the most cost-effective materials without compromising quality.
-
Labor: Labor costs vary widely by region and depend on the complexity of the manufacturing process. In countries with lower labor costs, such as some regions in Africa or South America, buyers may find more competitive pricing. However, it’s crucial to balance labor cost savings with the skill level and expertise required for high-quality production.
-
Manufacturing Overhead: This includes costs related to factory maintenance, utilities, and administrative expenses. Buyers should inquire about the overhead rates of potential suppliers, as these can vary significantly based on the supplier’s location and operational efficiency.
-
Tooling: Custom cable manufacturing often requires specialized tooling, which can be a substantial upfront cost. Buyers should discuss tooling costs upfront, especially if they plan to place large orders or frequent reorders.
-
Quality Control (QC): Ensuring that cables meet industry standards involves rigorous quality control processes, which add to the overall cost. Buyers should look for suppliers with robust QC measures to ensure product reliability.
-
Logistics: Shipping and handling costs can be a significant part of the total price, especially for international shipments. Factors such as distance, shipping method, and local tariffs can influence these costs.
-
Margin: Suppliers will typically include a profit margin that reflects their operational costs and market position. Understanding the average margins in the industry can help buyers negotiate better deals.
How Do Price Influencers Impact Custom Cable Costs?
Several factors influence the pricing of custom cables, which can vary based on the buyer’s needs:
-
Volume/MOQ: Minimum order quantities (MOQs) can impact pricing significantly. Higher volumes often lead to lower per-unit costs due to economies of scale. Buyers should evaluate their needs against the supplier’s MOQs to find the best pricing strategy.
-
Specifications and Customization: The complexity of the required specifications can drive prices up. Custom designs or specific certifications (e.g., UL, CE) may incur additional costs. Buyers should clearly define their specifications to avoid unexpected charges.
-
Materials: The choice of materials not only affects the base cost but also influences long-term performance. Opting for premium materials may result in higher initial costs but can lead to savings through improved durability and reduced maintenance.
-
Quality and Certifications: Suppliers that provide certifications often charge a premium for their products. Buyers should weigh the benefits of such certifications against their project requirements and budget.
-
Supplier Factors: The supplier’s reputation, reliability, and production capabilities can significantly influence pricing. Established suppliers may offer better quality but at higher prices. It’s essential to assess suppliers not just on cost but also on their ability to meet delivery timelines and quality standards.
-
Incoterms: The agreed terms of shipping and delivery (Incoterms) can have a substantial impact on the final cost. Understanding terms like FOB (Free on Board) or CIF (Cost, Insurance, and Freight) is crucial for budgeting and cost management.
What Buyer Tips Can Enhance Cost-Efficiency in Custom Cable Sourcing?
To optimize costs in custom cable sourcing, international B2B buyers can implement several strategies:
-
Negotiation: Engage in open discussions with suppliers about pricing. Understanding their cost structure can provide leverage during negotiations.
-
Focus on Total Cost of Ownership (TCO): Rather than just considering the initial purchase price, evaluate the TCO, which includes maintenance, durability, and performance over time. This approach ensures long-term savings.
-
Leverage Technology: Utilize digital platforms and tools for sourcing, which can provide access to a wider range of suppliers and competitive pricing.
-
Build Relationships: Developing long-term relationships with suppliers can lead to better pricing, priority service, and more favorable terms.
-
Stay Informed on Market Trends: Keeping abreast of fluctuations in material costs and global supply chain issues can help buyers make informed decisions and anticipate price changes.
Disclaimer on Indicative Prices
Prices for custom cables can vary significantly based on the aforementioned factors. Buyers are advised to obtain detailed quotes from multiple suppliers to ensure competitive pricing and to verify all cost components before finalizing any agreements.
Alternatives Analysis: Comparing cables custom With Other Solutions
When considering the implementation of cables custom for specific applications, it is essential to evaluate alternative solutions that may meet similar objectives. Understanding the strengths and weaknesses of various options can help B2B buyers make informed decisions tailored to their unique requirements.
Comparison Table of Cables Custom and Alternatives
Comparison Aspect | Cables Custom | Pre-assembled Cable Assemblies | Fiber Optic Cables |
---|---|---|---|
Performance | High performance tailored to needs | Moderate performance | Very high data transmission rates |
Cost | Higher initial investment | Lower cost due to standardization | Variable costs depending on distance and type |
Ease of Implementation | Requires specialized knowledge | Simple installation | Requires skilled installation |
Maintenance | Moderate; customized for longevity | Low; standardized components | Moderate; sensitive to environmental factors |
Best Use Case | Specialized industrial applications | General purpose applications | High-speed data transmission |
What Are the Advantages and Disadvantages of Pre-assembled Cable Assemblies?
Pre-assembled cable assemblies are a popular alternative due to their cost-effectiveness and ease of use. They are manufactured with standardized components, making them less expensive than custom cables. The installation process is straightforward, allowing for quick deployment in general-purpose applications. However, their performance may not match the tailored solutions provided by cables custom, especially in specialized industrial contexts where specific parameters are critical.
How Do Fiber Optic Cables Compare to Cables Custom?
Fiber optic cables excel in high-speed data transmission and are ideal for telecommunications and data centers. They offer superior performance in bandwidth and distance compared to traditional copper cables. However, the cost can vary significantly based on the specific type of fiber optic cable and the distance required. Installation often necessitates skilled technicians, making it less accessible for all buyers. Additionally, fiber optic cables can be sensitive to environmental factors, requiring careful maintenance to ensure long-term reliability.
Conclusion: How to Choose the Right Solution for Your Business Needs
Choosing the right solution between cables custom, pre-assembled cable assemblies, and fiber optic cables hinges on specific business requirements. B2B buyers should assess their unique performance needs, budget constraints, and installation capabilities. For specialized industrial applications, cables custom may be the best fit despite a higher initial investment. Conversely, if cost and ease of implementation are priorities, pre-assembled assemblies may provide an adequate solution. For those focused on high-speed data transmission, fiber optic cables are an excellent choice, provided that the necessary expertise is available for installation and maintenance. Careful consideration of these factors will ensure that businesses select the most appropriate cable solution to support their operational goals.
Essential Technical Properties and Trade Terminology for cables custom
What Are the Key Technical Properties of Custom Cables?
Understanding the essential technical properties of custom cables is crucial for international B2B buyers. These properties not only affect the performance and longevity of the cables but also ensure compliance with industry standards. Here are some of the most critical specifications to consider:
-
Material Grade
– The choice of materials, such as copper, aluminum, or specialized alloys, significantly influences the electrical conductivity and flexibility of the cable. For instance, copper is preferred for its superior conductivity, while aluminum is lighter and often more cost-effective. Selecting the right material grade is essential for optimizing performance and cost-effectiveness. -
Voltage Rating
– This specification defines the maximum voltage the cable can safely handle. It is crucial for ensuring that the cable can operate within the required parameters without risk of failure or hazards. Understanding voltage ratings helps buyers select cables suitable for specific applications, particularly in high-voltage environments. -
Temperature Rating
– Cables are designed to operate within specific temperature ranges. Knowing the temperature rating is vital for applications in extreme environments, ensuring that the cable maintains performance without degrading over time. Buyers should consider both ambient and operational temperatures to avoid premature failure. -
Insulation Type
– The insulation material affects both the safety and performance of the cable. Common insulation types include PVC, XLPE, and rubber, each offering different levels of resistance to heat, moisture, and chemicals. Choosing the right insulation type is critical for applications exposed to harsh conditions, ensuring longevity and reliability. -
Tolerance and Dimensional Specifications
– Tolerance refers to the allowable variation in dimensions of the cable. Precise tolerances are important for compatibility with connectors and other components. Buyers should seek manufacturers who can provide cables that meet specific tolerances, ensuring seamless integration into existing systems.
What Are Common Trade Terms in the Custom Cable Industry?
Familiarity with industry-specific terminology can facilitate smoother transactions and clearer communication. Here are some common trade terms that international B2B buyers should know:
-
OEM (Original Equipment Manufacturer)
– This term refers to a company that produces parts or equipment that may be marketed by another manufacturer. In the custom cable industry, OEM partnerships can allow buyers to obtain tailored products that meet specific requirements, enhancing their product offerings. -
MOQ (Minimum Order Quantity)
– MOQ indicates the smallest quantity of a product that a supplier is willing to sell. Understanding MOQs is essential for budgeting and inventory management, particularly for smaller businesses or those entering new markets. -
RFQ (Request for Quotation)
– An RFQ is a document sent by a buyer to suppliers to request price quotes for specific products or services. Crafting a detailed RFQ can help buyers receive accurate quotations and streamline the procurement process, ensuring they get the best value. -
Incoterms (International Commercial Terms)
– These terms define the responsibilities of buyers and sellers in international transactions, including shipping, insurance, and tariffs. Familiarity with Incoterms helps buyers understand their obligations and risks, facilitating smoother international trade. -
Lead Time
– Lead time refers to the amount of time it takes from placing an order to receiving the goods. Understanding lead times is crucial for supply chain management, allowing buyers to plan their operations and inventory levels accordingly. -
Certification Standards
– Many cables must meet specific industry standards and certifications, such as UL, CE, or ISO. Knowledge of these standards is vital for ensuring product quality and compliance, particularly for buyers in regulated markets.
By grasping these technical properties and trade terms, B2B buyers can make informed decisions, enhancing their procurement strategies and fostering successful partnerships in the custom cable industry.
Navigating Market Dynamics and Sourcing Trends in the cables custom Sector
What Are the Key Trends Shaping the Custom Cables Market?
The global custom cables market is experiencing dynamic shifts driven by technological advancements, evolving consumer demands, and geopolitical factors. One of the primary drivers is the increasing demand for high-speed data transmission, particularly in industries such as telecommunications and renewable energy. As businesses globally embrace digital transformation, the need for customized cable solutions that can handle greater bandwidth and specific applications is surging.
Emerging B2B technology trends include the integration of IoT (Internet of Things) capabilities into cable manufacturing processes, allowing for real-time monitoring and predictive maintenance. International buyers from regions like Africa and South America are particularly interested in solutions that enhance operational efficiency and reduce downtime. Moreover, advancements in manufacturing processes, such as additive manufacturing (3D printing), are enabling companies to create bespoke cable designs that meet specific client requirements without the traditional constraints of mass production.
Market dynamics are also influenced by fluctuating raw material prices and supply chain disruptions, particularly in the wake of global events such as the pandemic. For B2B buyers, understanding these fluctuations is crucial for effective budgeting and procurement strategies. In regions like the Middle East and Europe, where infrastructure projects are booming, sourcing custom cables that comply with local standards and regulations is essential for project success.
How Does Sustainability Impact the Sourcing of Custom Cables?
Sustainability has become a pivotal concern in the custom cables sector, influencing not only product design but also sourcing strategies. Environmental impacts associated with cable production, such as energy consumption and waste generation, are under scrutiny. International buyers are increasingly prioritizing suppliers who demonstrate a commitment to sustainable practices, including the use of recyclable materials and energy-efficient manufacturing processes.
The importance of ethical supply chains cannot be overstated. Buyers from Africa and South America, in particular, are seeking suppliers who ensure fair labor practices and transparency throughout their supply chains. Certifications such as ISO 14001 for environmental management and certifications for sustainable materials provide assurance to buyers regarding the ethical sourcing of custom cables.
Moreover, the market is witnessing a rise in demand for “green” cables, which utilize eco-friendly materials and are designed to minimize environmental impact. By prioritizing suppliers with such certifications and practices, B2B buyers can not only contribute to global sustainability efforts but also enhance their brand reputation in an increasingly eco-conscious marketplace.
How Has the Custom Cables Market Evolved Over Time?
The custom cables market has evolved significantly over the last few decades, transitioning from standard offerings to highly specialized solutions tailored to specific industry needs. Initially dominated by a few large manufacturers, the sector has diversified with the entry of numerous small to medium enterprises that focus on niche markets.
Technological advancements have played a crucial role in this evolution, enabling manufacturers to produce cables that are not only more efficient but also capable of withstanding harsher environments. As industries like telecommunications and renewable energy have expanded, the demand for customized solutions has skyrocketed.
In summary, understanding the historical context of the custom cables market provides valuable insights into current trends and future opportunities, especially for B2B buyers looking to make informed sourcing decisions. By staying attuned to these dynamics, international buyers can better navigate the complexities of the marketplace and secure the best solutions for their needs.
Frequently Asked Questions (FAQs) for B2B Buyers of cables custom
-
How do I solve the challenge of sourcing high-quality custom cables?
To ensure you source high-quality custom cables, start by conducting thorough research on potential suppliers. Look for manufacturers with a solid reputation and positive reviews from previous clients. Request samples to evaluate the quality and durability of their products. Additionally, consider suppliers who offer certifications that align with international standards, as this often indicates a commitment to quality. Engaging in direct communication with suppliers can also help clarify your specific needs and ensure they can meet your requirements. -
What is the best way to determine the right custom cable specifications for my project?
Determining the right specifications for your custom cables involves understanding your project’s specific requirements. Begin by analyzing the electrical and mechanical needs, such as voltage, current capacity, and environmental conditions. Collaborate with your engineering team to outline these specifications clearly. It is also beneficial to consult with cable manufacturers, as they can provide insights into materials and designs that optimize performance while adhering to industry standards. -
What should I consider when negotiating minimum order quantities (MOQs) for custom cables?
When negotiating MOQs, consider your budget, storage capacity, and projected demand. Suppliers often have MOQs to ensure cost-effectiveness, but you can negotiate these terms based on your unique situation. If your needs are lower than the MOQ, inquire about the possibility of combining orders with other buyers or adjusting your design to meet the MOQ. Additionally, understand that higher MOQs might lead to lower per-unit costs, which could be advantageous for future projects. -
How can I effectively vet suppliers for custom cable manufacturing?
Vetting suppliers requires a multi-faceted approach. Start by checking their credentials, including certifications and industry experience. Request references from previous clients, particularly those in your industry. Evaluate their production capabilities and quality assurance processes by visiting their facilities if possible. Additionally, assess their responsiveness and customer service, as strong communication is crucial for successful collaboration. Utilize platforms that provide supplier ratings to gain further insights into their reliability. -
What payment terms should I negotiate with custom cable suppliers?
Negotiating payment terms is crucial to maintaining cash flow while securing your orders. Standard terms may include a deposit upfront and the balance upon delivery, but you can negotiate based on your relationship with the supplier and the order size. Consider options like letters of credit for larger transactions to mitigate risk. Always ensure that payment terms align with your budget and project timelines, and document all agreements to avoid misunderstandings. -
How do I ensure quality assurance for custom cables during production?
Quality assurance (QA) is vital to ensure the reliability of custom cables. Establish clear specifications and performance criteria with your supplier before production begins. Implement regular inspections during the manufacturing process, including testing samples for electrical performance and durability. Consider hiring third-party QA inspectors to validate compliance with international standards. Additionally, request documentation of test results and certifications to ensure that the final products meet your requirements. -
What logistics considerations are important when importing custom cables?
Logistics play a critical role in the successful importation of custom cables. Assess the shipping methods available and select one that balances cost and delivery time, considering the urgency of your project. Familiarize yourself with customs regulations in your country to ensure compliance and avoid delays. Collaborate with logistics providers who specialize in international trade to manage documentation and shipping processes effectively. Plan for potential tariffs and duties that may impact your overall budget. -
How can I manage risks associated with international sourcing of custom cables?
Managing risks in international sourcing involves several strategies. Start by diversifying your supplier base to mitigate the impact of potential disruptions from any single source. Stay informed about geopolitical factors and economic conditions in the supplier’s country that could affect production and shipping. Establish clear contracts that outline terms, responsibilities, and dispute resolution processes. Regular communication with suppliers and monitoring of production timelines can also help identify issues early, allowing for timely interventions.
Important Disclaimer & Terms of Use
⚠️ Important Disclaimer
The information provided in this guide, including content regarding manufacturers, technical specifications, and market analysis, is for informational and educational purposes only. It does not constitute professional procurement advice, financial advice, or legal advice.
While we have made every effort to ensure the accuracy and timeliness of the information, we are not responsible for any errors, omissions, or outdated information. Market conditions, company details, and technical standards are subject to change.
B2B buyers must conduct their own independent and thorough due diligence before making any purchasing decisions. This includes contacting suppliers directly, verifying certifications, requesting samples, and seeking professional consultation. The risk of relying on any information in this guide is borne solely by the reader.
Strategic Sourcing Conclusion and Outlook for cables custom
In the dynamic landscape of custom cables, strategic sourcing emerges as a crucial component for international B2B buyers. By prioritizing the selection of reliable suppliers, businesses can ensure not only quality but also cost-effectiveness, ultimately enhancing their competitive edge. Buyers from regions such as Africa, South America, the Middle East, and Europe should focus on establishing long-term relationships with manufacturers who understand their specific needs and compliance requirements.
What are the key benefits of strategic sourcing for custom cables? Engaging in comprehensive market research, leveraging technology for supply chain transparency, and implementing stringent quality control measures can significantly reduce risks associated with sourcing. Additionally, understanding regional market trends and regulatory landscapes will help buyers make informed decisions, aligning their sourcing strategies with local demands and standards.
Looking ahead, the demand for custom cables is expected to rise, driven by advancements in technology and increasing connectivity needs. International B2B buyers are encouraged to remain proactive, exploring innovative sourcing strategies and embracing collaboration with suppliers. This forward-thinking approach will not only enhance operational efficiency but also position businesses for sustainable growth in an increasingly interconnected world.