Discover Top Benefits of Auto Accessorie Manufacturer (2025)
Introduction: Navigating the Global Market for auto accessorie manufacturer
In today’s dynamic landscape of the auto accessories market, international B2B buyers face a significant challenge: sourcing high-quality auto accessory manufacturers that align with their specific needs and standards. As the demand for innovative and reliable automotive products continues to grow, understanding the intricacies of this global market becomes essential for businesses seeking to enhance their offerings. This guide delves deep into the diverse world of auto accessory manufacturers, covering everything from product types and applications to effective supplier vetting and cost considerations.
Navigating this complex marketplace requires a strategic approach, especially for buyers in regions like Africa, South America, the Middle East, and Europe, including key markets such as the UAE and Turkey. Our comprehensive resource empowers you with the knowledge necessary to make informed purchasing decisions, helping you to identify reputable manufacturers, negotiate favorable terms, and ultimately secure products that enhance your competitive edge.
Whether you are looking for suppliers of high-performance car mats, cutting-edge infotainment systems, or eco-friendly automotive accessories, this guide will equip you with actionable insights and best practices. By leveraging the information provided, you can streamline your sourcing process, minimize risks, and maximize your investment in quality automotive products. Let’s embark on this journey to unlock the potential of the global auto accessories market together.
Understanding auto accessorie manufacturer Types and Variations
Type Name | Key Distinguishing Features | Primary B2B Applications | Brief Pros & Cons for Buyers |
---|---|---|---|
OEM (Original Equipment Manufacturer) | Produces parts that meet original specifications for vehicle manufacturers. | Supply chains for automotive production. | Pros: High quality, reliability. Cons: Often higher costs and longer lead times. |
Aftermarket Manufacturers | Specializes in producing parts that improve or replace OEM components. | Retail and wholesale distribution. | Pros: Competitive pricing, variety. Cons: Quality can vary significantly. |
Custom Accessory Manufacturers | Designs and fabricates unique accessories tailored to specific customer needs. | Niche markets and specialized applications. | Pros: Personalized solutions, unique offerings. Cons: Potentially higher costs and longer production times. |
Tier 1 Suppliers | Provide complete assemblies or systems directly to OEMs. | Large-scale manufacturing and assembly. | Pros: Integrated solutions, strong partnerships. Cons: Limited to large volume orders. |
Tier 2 and Tier 3 Suppliers | Supply individual components or raw materials to Tier 1 suppliers. | Support for larger manufacturers. | Pros: Lower cost options, flexibility. Cons: Quality assurance can be challenging. |
What are OEM Manufacturers and Their Role in the B2B Market?
OEM manufacturers produce components that adhere to the original specifications set by vehicle manufacturers. These parts are crucial for maintaining vehicle integrity and performance. B2B buyers focused on quality and reliability should prioritize OEM suppliers, as they guarantee compatibility and durability. However, buyers must be prepared for potentially higher costs and longer lead times, especially when sourcing for mass production.
How Do Aftermarket Manufacturers Differ from OEMs?
Aftermarket manufacturers create parts that can replace or enhance OEM components. They are a popular choice for businesses looking to provide customers with cost-effective alternatives without sacrificing performance. B2B buyers in regions like Africa and South America may find aftermarket parts particularly appealing due to their competitive pricing. However, the quality can vary widely, making it essential for buyers to conduct thorough due diligence.
Why Consider Custom Accessory Manufacturers for Unique Needs?
Custom accessory manufacturers offer tailored solutions designed to meet specific customer requirements. This type of manufacturing is ideal for businesses targeting niche markets or looking to differentiate their product offerings. Buyers should evaluate the customization capabilities and previous work of these manufacturers. While the personalized nature of these products can lead to higher costs and longer production times, the unique features can significantly enhance brand value.
What are the Advantages of Partnering with Tier 1 Suppliers?
Tier 1 suppliers provide complete assemblies or systems directly to OEMs, offering integrated solutions that streamline the manufacturing process. For B2B buyers involved in large-scale automotive production, partnering with Tier 1 suppliers can enhance efficiency and reduce logistical complexities. However, these suppliers typically cater to high-volume orders, which may not suit all businesses, particularly smaller operations or startups.
How Do Tier 2 and Tier 3 Suppliers Fit into the Supply Chain?
Tier 2 and Tier 3 suppliers focus on providing individual components or raw materials to Tier 1 suppliers. They can offer lower-cost options and greater flexibility, making them suitable for businesses looking to optimize their supply chains. However, buyers must be vigilant regarding quality assurance, as sourcing from multiple lower-tier suppliers can complicate quality control processes. Understanding the supply chain dynamics is crucial for B2B buyers aiming to maintain high standards in their offerings.
Key Industrial Applications of auto accessorie manufacturer
Industry/Sector | Specific Application of auto accessorie manufacturer | Value/Benefit for the Business | Key Sourcing Considerations for this Application |
---|---|---|---|
Automotive Aftermarket | Custom floor mats and seat covers | Enhances vehicle aesthetics and resale value | Quality materials, customization options, and durability |
Fleet Management | GPS tracking devices and telematics solutions | Improves operational efficiency and vehicle monitoring | Compatibility with existing systems and scalability |
E-commerce and Retail | Online sales of car accessories | Expands market reach and customer engagement | Reliable shipping, product variety, and competitive pricing |
Car Rental Services | Vehicle protection accessories | Reduces maintenance costs and enhances customer experience | Bulk purchasing options and warranty support |
Automotive Repair and Maintenance | Replacement parts and tools | Ensures reliability and safety for vehicles | Certification standards and supplier reliability |
How is Auto Accessory Manufacturing Applied in the Automotive Aftermarket?
In the automotive aftermarket, auto accessory manufacturers provide custom floor mats and seat covers tailored to specific vehicle models. These accessories not only enhance the aesthetic appeal of vehicles but also contribute to their resale value. For international buyers, particularly from regions like Africa and South America, sourcing high-quality materials that withstand local climate conditions is essential. Buyers should prioritize customization options that align with market trends and consumer preferences in their regions.
What Role Do Auto Accessories Play in Fleet Management?
For fleet management, auto accessory manufacturers supply GPS tracking devices and telematics solutions. These products enable businesses to monitor vehicle locations, optimize routes, and improve operational efficiency. International buyers, especially from the Middle East and Europe, should consider compatibility with existing fleet management systems and the scalability of solutions as they expand their operations. Additionally, understanding local regulatory requirements regarding vehicle tracking is crucial for compliance.
How Do Auto Accessories Benefit E-commerce and Retail?
In the e-commerce and retail sector, auto accessory manufacturers facilitate online sales of a wide range of car accessories. This channel allows businesses to expand their market reach and engage customers more effectively. For international B2B buyers, reliable shipping options, diverse product offerings, and competitive pricing are key considerations. Understanding regional preferences and trends can also help tailor marketing strategies to boost sales in specific markets.
How Can Car Rental Services Utilize Auto Accessories?
Car rental services benefit from vehicle protection accessories, such as seat covers and floor mats, which help reduce maintenance costs and enhance customer experience. These accessories protect the vehicle’s interior from wear and tear, making them more appealing to renters. For buyers in regions like Turkey and the UAE, bulk purchasing options and warranty support are significant factors to consider, ensuring that they can maintain a fleet of vehicles that meet customer expectations.
Why Are Replacement Parts Critical for Automotive Repair and Maintenance?
Auto accessory manufacturers play a vital role in the automotive repair and maintenance industry by providing high-quality replacement parts and tools. These components are essential for ensuring vehicle reliability and safety. International buyers must prioritize suppliers that meet certification standards and demonstrate reliability in product delivery. This focus on quality not only enhances the service provided to end customers but also builds trust in the repair business.
Related Video: FANUC Industrial Robots | AUDI Case Study
3 Common User Pain Points for ‘auto accessorie manufacturer’ & Their Solutions
Scenario 1: Navigating Quality Assurance Challenges with Auto Accessories
The Problem: B2B buyers often face significant challenges related to quality assurance when sourcing auto accessories from manufacturers. In regions like Africa and South America, where the market is burgeoning, buyers may encounter products that do not meet international standards. This can lead to customer dissatisfaction, increased returns, and damage to the buyer’s reputation. For instance, a buyer in the UAE may import a batch of seat covers that are not durable, leading to complaints from automotive retailers who expected high-quality products.
The Solution: To mitigate quality assurance issues, B2B buyers should implement a robust vendor evaluation process. This includes requesting product samples before placing bulk orders and conducting factory audits, either in-person or through third-party services. Additionally, establishing clear quality benchmarks and specifications in the contract can help ensure that the manufacturer understands the expectations. Buyers should also consider leveraging platforms that facilitate transparency and feedback, allowing them to connect with other businesses that have previously sourced from the same manufacturer. Regular communication and quality checks throughout the production process can further enhance the chances of receiving high-quality products.
Scenario 2: Overcoming Supply Chain Disruptions in Auto Accessories Procurement
The Problem: Supply chain disruptions pose a significant threat to B2B buyers in the auto accessories market, particularly those operating in diverse regions such as the Middle East and Europe. Factors such as political instability, natural disasters, or logistical delays can severely impact delivery timelines. For example, a buyer in Turkey may find that a shipment of tire accessories is delayed due to port congestion, resulting in missed sales opportunities and dissatisfied customers.
The Solution: To effectively manage supply chain disruptions, buyers should diversify their supplier base by not relying solely on one manufacturer or geographical location. This strategy allows for flexibility and backup options in case of delays. Additionally, buyers can utilize predictive analytics to better forecast demand and adjust orders proactively. Engaging in proactive communication with manufacturers to understand their production capabilities and potential risks can also help buyers plan accordingly. Establishing a buffer inventory of critical items can mitigate the impact of unexpected delays, ensuring that operations continue smoothly.
Scenario 3: Addressing Customization Needs for Diverse Markets
The Problem: B2B buyers often struggle to find manufacturers that can accommodate specific customization needs for auto accessories, which can vary greatly between markets in Africa, South America, the Middle East, and Europe. For instance, a buyer may require a unique design or features for car mats tailored to local climate conditions, but many manufacturers offer limited options. This lack of flexibility can lead to missed market opportunities and subpar product offerings.
The Solution: To address customization challenges, buyers should actively seek out manufacturers known for their flexibility and capability in product development. Engaging in early discussions about customization possibilities can reveal the manufacturer’s willingness to adapt their products. Buyers should prepare detailed specifications, including materials, designs, and functionality, to help manufacturers understand their unique needs. Collaborating with manufacturers during the design phase can also facilitate innovation and ensure that the final product meets market demands. Establishing long-term partnerships with manufacturers that prioritize customization can lead to better responsiveness and tailored solutions in the future, ultimately enhancing the buyer’s competitive edge in their respective markets.
Strategic Material Selection Guide for auto accessorie manufacturer
When selecting materials for auto accessories, manufacturers must consider various factors that can significantly impact product performance, durability, and compliance with international standards. Below is an analysis of four common materials used in the auto accessories industry, focusing on their properties, advantages, disadvantages, and implications for international buyers, particularly from Africa, South America, the Middle East, and Europe.
What Are the Key Properties of Plastic in Auto Accessories?
Plastic, particularly high-density polyethylene (HDPE) and polypropylene, is widely used in auto accessories due to its lightweight nature and versatility. Key properties include excellent corrosion resistance, low moisture absorption, and a temperature rating that typically ranges from -40°C to 80°C. These characteristics make plastics suitable for various applications, including interior components and exterior trims.
Pros & Cons:
The advantages of plastic include its low cost and ease of manufacturing, which allows for complex shapes and designs. However, its durability can be a concern, especially under extreme temperature fluctuations or exposure to UV light, which can lead to degradation over time.
Impact on Application:
Plastic is compatible with a wide range of automotive fluids, making it suitable for applications like fluid reservoirs and interior fittings. However, buyers must consider the specific type of plastic to ensure it meets the required performance standards.
Considerations for International Buyers:
Buyers from regions like the UAE and Turkey should ensure compliance with local regulations regarding plastic materials, such as those set by ASTM or DIN. Additionally, preferences for recyclable materials are growing, which may influence sourcing decisions.
How Do Metals Like Aluminum Benefit Auto Accessory Manufacturing?
Aluminum is another popular material in the auto accessories sector, known for its strength-to-weight ratio and corrosion resistance. It typically performs well in temperature ranges from -50°C to 150°C, making it suitable for various automotive applications.
Pros & Cons:
The primary advantage of aluminum is its durability and lightweight nature, which can enhance fuel efficiency in vehicles. However, the cost can be higher than that of plastic, and manufacturing processes such as welding can be more complex.
Impact on Application:
Aluminum is ideal for components that require strength and lightweight properties, such as brackets and structural parts. Its compatibility with various coatings and finishes allows for aesthetic versatility.
Considerations for International Buyers:
International buyers should be aware of the different grades of aluminum and their respective standards, such as JIS for Japan or EN for Europe. Compliance with these standards is crucial for ensuring product quality and market acceptance.
What Advantages Does Rubber Offer for Auto Accessories?
Rubber is commonly used in auto accessories for its flexibility and excellent vibration dampening properties. It can withstand a temperature range from -40°C to 120°C, making it suitable for seals, gaskets, and suspension components.
Pros & Cons:
The flexibility of rubber provides significant advantages in applications requiring tight seals or shock absorption. However, rubber can degrade when exposed to ozone or UV light, necessitating careful selection of rubber compounds.
Impact on Application:
Rubber is particularly effective in applications where fluid resistance is essential, such as in gaskets for oil pans or fuel systems.
Considerations for International Buyers:
Buyers must consider the specific rubber grades that comply with automotive standards, such as ASTM D2000. Additionally, local sourcing of rubber may be influenced by environmental regulations in regions like South America.
How Does Composite Material Impact Auto Accessory Manufacturing?
Composite materials, which combine two or more constituent materials, are increasingly being used in the auto accessories sector due to their high strength-to-weight ratio and design flexibility. Composites can perform well in temperature ranges from -40°C to 120°C.
Pros & Cons:
The key advantage of composites is their ability to be tailored for specific applications, providing excellent durability and aesthetic options. However, they can be more expensive to manufacture and require specialized processing techniques.
Impact on Application:
Composites are particularly useful in high-performance applications, such as body panels and interior components where weight savings are critical.
Considerations for International Buyers:
Buyers should ensure that composite materials meet international standards and regulations, particularly in terms of fire safety and environmental impact. Awareness of local manufacturing capabilities for composites is also essential.
Summary Table of Material Selection for Auto Accessories
Material | Typical Use Case for auto accessorie manufacturer | Key Advantage | Key Disadvantage/Limitation | Relative Cost (Low/Med/High) |
---|---|---|---|---|
Plastic | Interior components, exterior trims | Lightweight and cost-effective | Less durable under extreme conditions | Low |
Aluminum | Brackets, structural parts | High strength-to-weight ratio | Higher cost and complex manufacturing | Medium |
Rubber | Seals, gaskets, suspension components | Excellent flexibility and dampening | Degrades with ozone/UV exposure | Medium |
Composite | Body panels, high-performance interiors | Tailored properties and aesthetics | Higher manufacturing costs | High |
This strategic material selection guide provides a comprehensive overview for international B2B buyers in the auto accessories market, ensuring informed decisions that align with regional standards and performance requirements.
In-depth Look: Manufacturing Processes and Quality Assurance for auto accessorie manufacturer
What Are the Key Stages in the Manufacturing Process of Auto Accessories?
The manufacturing process for auto accessories involves several critical stages designed to ensure quality and efficiency. Understanding these stages can help international B2B buyers make informed decisions when selecting suppliers.
1. Material Preparation
The first stage involves sourcing and preparing raw materials, which may include metals, plastics, rubber, and textiles. Quality control starts here, as the choice of materials significantly affects the final product’s durability and safety. B2B buyers should inquire about the supplier’s sourcing practices and certifications for materials, ensuring they meet international standards.
2. Forming Techniques
Once materials are prepared, they undergo various forming techniques, such as injection molding, stamping, or extrusion. Each technique has its advantages based on the type of accessory being produced. For example, injection molding is ideal for producing complex shapes with high precision. Buyers should assess the supplier’s capabilities in these techniques and any associated technology to ensure they can meet specific design requirements.
3. Assembly Process
The assembly stage involves combining different components to create the final product. This can be done manually or through automated processes, depending on the scale of production. Automated assembly lines can enhance efficiency and reduce labor costs, but they may require a higher initial investment. Buyers should evaluate the supplier’s assembly processes to ensure they align with their volume and customization needs.
4. Finishing Techniques
Finishing processes, such as painting, coating, or polishing, enhance the product’s aesthetic appeal and protect it from environmental factors. Suppliers may use various finishing techniques, which can affect lead times and costs. B2B buyers should discuss finishing options with suppliers to understand the implications for both product quality and delivery schedules.
How Is Quality Assurance Implemented in Auto Accessory Manufacturing?
Quality assurance (QA) is a crucial component in the manufacturing process of auto accessories, ensuring that products meet established standards and specifications.
What Are the Relevant International Quality Standards?
Many auto accessory manufacturers adhere to international quality standards such as ISO 9001, which focuses on quality management systems. Additionally, industry-specific standards like CE marking in Europe or API certification for automotive parts may also apply. B2B buyers should confirm that suppliers are compliant with these standards, which can assure the reliability and safety of the products.
What Are the Key Quality Control Checkpoints?
Quality control checkpoints are integral to maintaining product integrity throughout the manufacturing process. These checkpoints typically include:
- Incoming Quality Control (IQC): This involves inspecting raw materials before they enter the production process to ensure they meet specified criteria.
- In-Process Quality Control (IPQC): This stage monitors the production process to catch defects early, minimizing waste and rework.
- Final Quality Control (FQC): After assembly, products undergo a final inspection to ensure they meet the required standards before shipment.
B2B buyers should ask suppliers about their specific QC procedures and the frequency of inspections at each checkpoint.
What Common Testing Methods Are Used?
Manufacturers employ various testing methods to verify product performance and safety, including:
- Mechanical Testing: This includes tensile tests, impact tests, and fatigue tests to assess the material’s strength and durability.
- Environmental Testing: Products may undergo tests to evaluate their performance under different environmental conditions, such as temperature and humidity.
- Electrical Testing: For accessories with electronic components, testing for electrical safety and functionality is essential.
Buyers should request documentation of these tests and understand the methodologies used to ensure compliance with industry standards.
How Can B2B Buyers Verify Supplier Quality Control Processes?
Verifying a supplier’s quality control processes is essential for B2B buyers to mitigate risks associated with product quality.
What Should Buyers Look for in Supplier Audits?
Conducting audits is one of the most effective ways to verify a supplier’s quality control processes. Buyers can perform:
- On-Site Audits: Visiting the manufacturing facility allows buyers to assess the operational environment, machinery, and quality control protocols firsthand.
- Third-Party Audits: Engaging an independent third-party organization to conduct audits can provide an objective assessment of the supplier’s compliance with quality standards.
Buyers should also request the supplier’s audit reports, certifications, and any corrective action plans that have been implemented to address previous quality issues.
How Can Buyers Utilize Quality Reports?
Suppliers should provide regular quality reports detailing performance metrics, defect rates, and corrective actions taken. These reports can offer insights into the supplier’s commitment to quality and areas for improvement. B2B buyers should establish a routine for reviewing these reports to maintain oversight of product quality.
What Nuances Should International B2B Buyers Consider?
When sourcing auto accessories from manufacturers in different regions, international B2B buyers must consider various nuances that can impact quality assurance.
How Do Regional Standards Affect Quality Assurance?
Different regions may have varying quality standards and regulatory requirements. For example, products sold in Europe must comply with CE marking regulations, while those in the Middle East may adhere to different standards. Buyers should familiarize themselves with the specific regulations applicable to their target market and ensure that their suppliers comply accordingly.
What Are the Cultural Considerations in Quality Control?
Cultural differences can influence communication and expectations around quality control. In some regions, there may be a strong emphasis on relationship-building, while others may prioritize strict adherence to processes. B2B buyers should be aware of these cultural nuances and adapt their communication and negotiation strategies accordingly to foster effective partnerships with suppliers.
In conclusion, understanding the manufacturing processes and quality assurance practices of auto accessory manufacturers is vital for international B2B buyers. By focusing on material preparation, forming techniques, assembly, finishing, and robust quality control measures, buyers can ensure they partner with reliable suppliers who meet their specific needs and standards.
Practical Sourcing Guide: A Step-by-Step Checklist for ‘auto accessorie manufacturer’
In the competitive landscape of the auto accessories industry, sourcing from reliable manufacturers is crucial for B2B buyers. This step-by-step checklist aims to guide international buyers from Africa, South America, the Middle East, and Europe through the critical steps of sourcing auto accessory manufacturers. By following these actionable insights, you can ensure a smoother procurement process and establish fruitful partnerships.
Step 1: Define Your Technical Specifications
Establishing clear technical specifications is the foundation of successful sourcing. This includes understanding the materials, dimensions, and performance standards required for the auto accessories you wish to procure. By defining these parameters, you can effectively communicate your needs to potential suppliers, ensuring they can meet your expectations.
- Identify key features: Consider aspects such as durability, compatibility with existing products, and any certifications that may be required in your market.
- Benchmark against competitors: Research similar products to understand industry standards and customer preferences.
Step 2: Research and Shortlist Potential Manufacturers
Conduct thorough research to identify a list of potential manufacturers that specialize in auto accessories. Utilize online directories, trade shows, and industry publications to gather information about manufacturers’ capabilities and reputation.
- Look for industry experience: Prioritize manufacturers with a proven track record in your specific accessory category.
- Consider geographical advantages: Evaluate suppliers based on their location to minimize shipping costs and lead times.
Step 3: Evaluate Potential Suppliers
Before making any commitments, it’s essential to assess the shortlisted suppliers rigorously. This involves requesting detailed company profiles, case studies, and references from previous clients.
- Check for industry certifications: Ensure that the manufacturers comply with relevant standards, such as ISO certifications or specific automotive industry regulations.
- Request samples: If possible, obtain product samples to evaluate quality and craftsmanship firsthand.
Step 4: Verify Financial Stability
Assessing the financial health of a potential supplier is crucial to ensure they can fulfill your orders consistently. Request financial statements or credit reports to gauge their stability.
- Look for growth indicators: A supplier with a stable or growing revenue stream is more likely to invest in quality improvements and innovation.
- Assess creditworthiness: This can help mitigate risks associated with order fulfillment and delivery.
Step 5: Negotiate Terms and Conditions
Once you’ve identified a suitable manufacturer, begin negotiations on pricing, payment terms, and delivery schedules. This step is vital to ensuring that both parties have a clear understanding of expectations.
- Be transparent about your needs: Clearly communicate your budget constraints and desired timelines.
- Discuss warranties and returns: Establish terms for product warranties and return policies to protect your investment.
Step 6: Conduct a Factory Audit
If feasible, perform a factory audit to observe manufacturing processes and quality control measures in place. This is particularly important for large orders where quality consistency is critical.
- Evaluate production capacity: Confirm that the manufacturer can meet your order volumes within your required timelines.
- Inspect quality control processes: Understanding their quality assurance protocols can help you gauge the reliability of the manufacturer.
Step 7: Establish a Clear Communication Plan
Effective communication is key to a successful partnership. Set up a structured communication plan that includes regular updates and feedback loops.
- Define points of contact: Ensure that both parties have designated representatives for streamlined communication.
- Utilize project management tools: Consider using tools that facilitate tracking orders, changes, and timelines to enhance collaboration.
By following this checklist, B2B buyers can navigate the complexities of sourcing auto accessories, ensuring they partner with manufacturers that align with their operational goals and quality standards.
Comprehensive Cost and Pricing Analysis for auto accessorie manufacturer Sourcing
When sourcing auto accessories, understanding the comprehensive cost structure and pricing dynamics is crucial for international B2B buyers. This analysis will delve into the essential cost components, price influencers, and actionable buyer tips tailored for businesses in Africa, South America, the Middle East, and Europe.
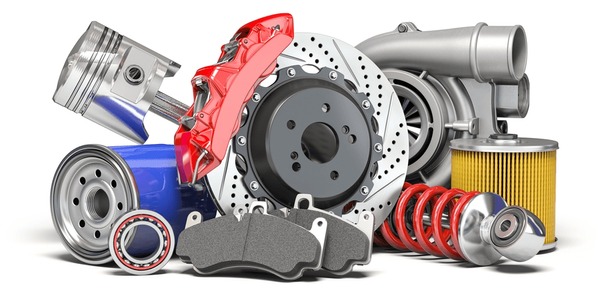
A stock image related to auto accessorie manufacturer.
What Are the Key Cost Components in Auto Accessories Manufacturing?
The cost structure of auto accessory manufacturing can be broken down into several key components:
-
Materials: Raw materials are often the most significant expense. Costs can vary dramatically based on the type of materials used (e.g., plastics, metals, textiles) and market fluctuations. Buyers should consider the quality and sustainability of materials, as this can impact both pricing and brand reputation.
-
Labor: Labor costs depend on the manufacturing location and local wage standards. Countries in Africa and South America may offer lower labor costs, while Europe and the Middle East might have higher wages but potentially offer more skilled labor.
-
Manufacturing Overhead: This includes utilities, rent, equipment depreciation, and administrative expenses. Overhead can vary based on the efficiency of the manufacturing process and the scale of production.
-
Tooling: Initial tooling costs for molds and specialized equipment can be substantial but are typically amortized over larger production runs. Custom tooling for unique designs can significantly increase costs, so it’s vital to assess the necessity of such investments.
-
Quality Control (QC): Implementing robust QC measures is essential to maintain product standards. While this may add to the overall cost, it can prevent costly recalls and damage to brand reputation.
-
Logistics: Shipping and handling costs can vary based on distance, transportation mode, and destination regulations. Understanding the logistics landscape is crucial for estimating total costs.
-
Margin: Manufacturers typically apply a margin to cover their costs and profit. This can vary widely based on market competition and brand positioning.
How Do Price Influencers Impact Auto Accessories Costs?
Several factors can influence the pricing of auto accessories:
-
Volume and Minimum Order Quantity (MOQ): Larger orders often lead to lower per-unit costs due to economies of scale. Buyers should assess their demand patterns to negotiate favorable MOQs.
-
Specifications and Customization: Custom designs or specifications can increase costs. Buyers need to balance the desire for customization with budget constraints.
-
Material Quality and Certifications: Higher quality materials or compliance with international certifications (e.g., ISO, CE) can increase costs but also enhance product appeal and marketability.
-
Supplier Factors: The reliability, reputation, and negotiation power of the supplier can influence pricing. A well-established supplier may offer better terms due to their experience and efficiency.
-
Incoterms: Understanding Incoterms is essential for determining who bears responsibility for shipping costs, insurance, and customs clearance. This can significantly impact the total landed cost.
What Are the Best Practices for Negotiating and Achieving Cost Efficiency?
For international B2B buyers, particularly from regions like Africa, South America, the Middle East, and Europe, the following tips can help ensure cost efficiency:
-
Negotiation: Leverage your purchasing power by negotiating terms, especially if placing large orders. Building a good relationship with suppliers can also yield better pricing and terms.
-
Total Cost of Ownership (TCO): Evaluate the TCO instead of just the initial purchase price. Consider factors like durability, maintenance, and logistics to make informed decisions.
-
Pricing Nuances: Be aware of regional pricing differences and market trends. For instance, prices in the UAE may vary due to import duties and local demand, while suppliers in Turkey might offer competitive pricing for European buyers.
-
Research and Compare: Conduct thorough market research and obtain quotes from multiple suppliers to ensure competitive pricing. Utilize online platforms and trade shows to connect with potential suppliers.
Disclaimer on Pricing
It is important to note that prices can fluctuate based on market conditions, currency exchange rates, and geopolitical factors. Therefore, the figures discussed should be considered indicative rather than definitive. Always seek tailored quotes based on specific requirements and conditions.
By understanding these cost structures and price influencers, international B2B buyers can navigate the complexities of sourcing auto accessories more effectively and make informed purchasing decisions.
Alternatives Analysis: Comparing auto accessorie manufacturer With Other Solutions
When considering the procurement of auto accessories, international B2B buyers must evaluate not only the manufacturers themselves but also viable alternatives that may better suit their specific needs. This analysis will compare an auto accessory manufacturer against two alternative solutions: aftermarket accessories and 3D printing technology. Each of these options presents unique advantages and challenges, which are crucial for buyers to understand.
Comparison Aspect | Auto Accessorie Manufacturer | Aftermarket Accessories | 3D Printing Technology |
---|---|---|---|
Performance | High quality, tailored products | Variable quality, dependent on brand | High precision, customizable |
Cost | Moderate to high, depending on customization | Generally lower, but variable | Initial investment high, but cost-effective for small batches |
Ease of Implementation | Streamlined for bulk orders | Easy access through retailers | Requires design expertise and setup |
Maintenance | Manufacturer support available | Limited support, variable | Minimal for printed items, but requires design updates |
Best Use Case | Large-scale orders, specific branding | General use, quick replacements | Custom, low-volume needs, rapid prototyping |
What Are the Advantages and Disadvantages of Aftermarket Accessories?
Aftermarket accessories offer a flexible option for businesses seeking cost-effective solutions. They often come at a lower price point compared to directly sourcing from manufacturers. However, the quality can be inconsistent, as it heavily depends on the brand. This can lead to potential issues with durability or compatibility, affecting customer satisfaction in the long run. Aftermarket solutions are best suited for businesses that need quick replacements without a significant investment or for those operating in markets where price sensitivity is high.
How Does 3D Printing Technology Compare in the Auto Accessories Market?
3D printing technology is revolutionizing the way auto accessories are manufactured, allowing for high precision and customization. This method is particularly advantageous for creating unique parts or limited runs, making it ideal for niche markets or specialized needs. However, the initial setup costs can be high, and companies must have design expertise to create the models. For businesses that require custom solutions and can manage the upfront investment, 3D printing can provide a highly efficient and innovative way to meet their needs.
Conclusion: How Should B2B Buyers Choose Between These Options?
Choosing the right solution for auto accessories requires a careful evaluation of your business’s specific needs, budget, and operational capabilities. If your focus is on bulk orders and brand consistency, partnering with an auto accessory manufacturer may be the most effective route. Conversely, if you are looking for cost-effective, readily available alternatives, aftermarket options might suffice. For businesses needing unique, tailored solutions and willing to invest in technology, 3D printing can offer unparalleled customization. Ultimately, understanding the trade-offs between performance, cost, and implementation will enable B2B buyers to make informed decisions that align with their strategic goals.
Essential Technical Properties and Trade Terminology for auto accessorie manufacturer
What Are the Key Technical Properties for Auto Accessory Manufacturing?
Understanding the essential technical properties of auto accessories is crucial for international B2B buyers looking to make informed decisions. Below are several critical specifications that manufacturers should consider when sourcing auto accessories.
1. Material Grade: Why Is It Important?
Material grade refers to the quality and composition of the materials used in manufacturing auto accessories. Common materials include plastic, rubber, metal, and composite materials. The grade affects durability, performance, and safety. For instance, high-grade plastics can withstand extreme temperatures and impact, making them suitable for external components. Buyers should ensure that the materials meet relevant industry standards for quality and safety to avoid costly replacements and liabilities.
2. Tolerance: How Does It Affect Fit and Function?
Tolerance is the allowable variation in dimensions during manufacturing. It is crucial for ensuring that components fit together seamlessly and function as intended. In auto accessory manufacturing, tight tolerances can significantly impact the performance of parts, such as those involved in engine systems or braking mechanisms. Buyers should specify the required tolerances clearly in their orders to avoid compatibility issues that could lead to safety hazards.
3. Surface Finish: What Role Does It Play?
Surface finish refers to the texture and appearance of the finished product. Different finishes can affect the aesthetic appeal, corrosion resistance, and ease of cleaning. A smooth finish may be essential for parts exposed to harsh environments, while a textured surface can enhance grip and usability. Buyers should consider the intended use of the accessory when discussing surface finish requirements with manufacturers.
4. Weight and Dimensions: Why Are They Critical?
Weight and dimensions are fundamental specifications that impact shipping costs, installation, and performance. For instance, lighter components can improve fuel efficiency, while precise dimensions ensure compatibility with vehicles. Buyers need to communicate their specific requirements regarding size and weight to avoid issues during installation and functionality.
5. Compliance Standards: What Should Buyers Know?
Compliance with international and local standards is vital in the auto accessories sector. Regulations may pertain to safety, emissions, and environmental impact. For example, the ISO (International Organization for Standardization) and TS (Technical Specification) certifications are critical indicators of quality. Buyers should verify that the manufacturers adhere to these standards to ensure product reliability and market acceptance.
What Are Common Trade Terms in Auto Accessory Manufacturing?
Familiarity with industry jargon can enhance communication and negotiation processes. Here are some essential trade terms that every international B2B buyer should know.
1. OEM (Original Equipment Manufacturer): What Does It Mean?
An OEM refers to a company that produces parts and equipment that may be marketed by another manufacturer. Understanding OEM relationships is crucial for buyers, as it often indicates the quality and reliability of the products being sourced. Many auto accessories are supplied by OEMs, ensuring that they meet the original design specifications.
2. MOQ (Minimum Order Quantity): How Does It Impact Your Orders?
MOQ is the minimum quantity of units that a supplier is willing to sell. It is essential for buyers to be aware of MOQs, as they can affect inventory management and cash flow. Negotiating favorable MOQs can lead to better pricing and reduced costs, making it a critical factor in the purchasing process.
3. RFQ (Request for Quotation): Why Is It Necessary?
An RFQ is a document that buyers send to suppliers to request pricing and terms for specific products. It is an essential tool in the procurement process, allowing buyers to compare offers and ensure they are getting the best deal. Including detailed specifications in an RFQ can lead to more accurate and competitive quotes.
4. Incoterms: What Do They Cover?
Incoterms (International Commercial Terms) are a set of predefined international trade terms that clarify the responsibilities of buyers and sellers in shipping goods. Understanding these terms is vital for managing logistics, costs, and risks. Common Incoterms include FOB (Free On Board) and CIF (Cost, Insurance, and Freight), which determine who is responsible for shipping costs and insurance during transit.
By familiarizing themselves with these technical properties and trade terms, international B2B buyers can navigate the auto accessory manufacturing landscape more effectively, ensuring successful partnerships and high-quality products.
Navigating Market Dynamics and Sourcing Trends in the auto accessorie manufacturer Sector
What Are the Key Market Dynamics and Trends in the Auto Accessories Manufacturing Sector?
The global auto accessories market is currently undergoing significant transformation, driven by various factors that international B2B buyers should be aware of. The increasing demand for vehicle personalization and enhancement is a primary driver, particularly in regions like Africa, South America, the Middle East, and Europe. As urbanization rises and disposable incomes increase, consumers are more inclined to invest in auto accessories that improve functionality and aesthetics.
Additionally, the adoption of advanced technologies, such as IoT and smart accessories, is reshaping the landscape. Manufacturers are leveraging data analytics to understand consumer preferences better and to optimize production processes. For B2B buyers, this means sourcing products that not only meet current market demands but also align with technological advancements.
Sourcing trends are also leaning towards local suppliers, driven by the need for quicker delivery times and reduced transportation costs. This is particularly relevant for buyers in the Middle East and Africa, where regional manufacturing capabilities are expanding. Furthermore, strategic partnerships and collaborations are becoming essential for securing competitive pricing and ensuring product quality.
How Does Sustainability Impact Sourcing in the Auto Accessories Sector?
Sustainability and ethical sourcing have become paramount in the auto accessories manufacturing sector. The environmental impact of production processes is under increasing scrutiny, prompting manufacturers to adopt greener practices. This includes using sustainable materials and implementing energy-efficient manufacturing techniques.
For B2B buyers, the importance of ethical supply chains cannot be overstated. Buyers are increasingly prioritizing suppliers that demonstrate a commitment to sustainability, as this not only enhances brand reputation but also meets the growing consumer demand for environmentally friendly products. Certifications such as ISO 14001 for environmental management and the use of recycled materials are becoming critical indicators of a supplier’s commitment to sustainability.
Buyers in regions such as Europe and South America are particularly influenced by stringent regulations regarding environmental impact, making it essential to partner with manufacturers that prioritize compliance. By sourcing from companies that adopt sustainable practices, buyers can mitigate risks associated with supply chain disruptions and enhance their overall market competitiveness.
What Is the Historical Context of the Auto Accessories Manufacturing Sector?
The auto accessories manufacturing sector has evolved significantly over the decades. Initially focused on functional upgrades, the industry has shifted towards customization and personalization, driven by consumer preferences. The introduction of advanced materials and technologies has further transformed product offerings, allowing for innovations such as smart accessories and enhanced safety features.
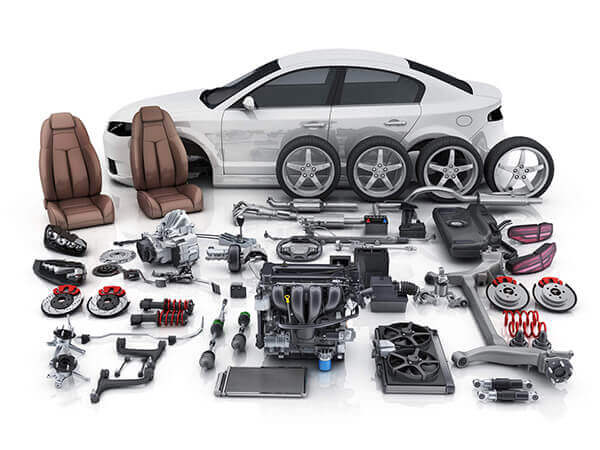
A stock image related to auto accessorie manufacturer.
As markets have globalized, international trade dynamics have also played a crucial role in shaping sourcing strategies. With the rise of digital platforms, B2B buyers now have access to a broader range of suppliers, making it easier to compare prices and quality across different regions. This evolution highlights the importance of staying informed about market trends and supplier capabilities to make strategic sourcing decisions that align with business goals.
In conclusion, navigating the complexities of the auto accessories manufacturing sector requires a keen understanding of market dynamics, a commitment to sustainability, and awareness of historical trends that influence current practices. By leveraging these insights, B2B buyers can make informed decisions that enhance their competitive edge in the global marketplace.
Frequently Asked Questions (FAQs) for B2B Buyers of auto accessorie manufacturer
-
How do I ensure quality when sourcing from auto accessory manufacturers?
To guarantee quality, it’s essential to conduct thorough due diligence on potential manufacturers. Request samples to evaluate the product quality firsthand. Utilize third-party inspection services for pre-shipment checks, especially when dealing with suppliers from regions like Africa or the Middle East. Additionally, reviewing customer testimonials and certifications can provide insights into the manufacturer’s reliability and adherence to international quality standards. -
What is the best way to vet auto accessory manufacturers for international trade?
Start by researching manufacturers through industry directories and trade shows. Check for their business licenses, certifications, and compliance with international trade regulations. Engage in direct communication to assess their responsiveness and willingness to provide detailed information. Utilize platforms like Alibaba or Global Sources, which often have user reviews and ratings, to gauge the credibility of suppliers, particularly those from South America and Europe. -
What are the common payment terms offered by auto accessory manufacturers?
Payment terms can vary significantly between manufacturers. Common options include upfront deposits (usually 30-50%) with the balance due upon shipment. Some manufacturers may offer net payment terms (like 30, 60, or 90 days) for established relationships. It’s advisable to negotiate terms that align with your cash flow needs and to consider using escrow services to mitigate risk, especially in international transactions. -
What is the minimum order quantity (MOQ) for auto accessories, and how can I negotiate it?
MOQs can differ based on the manufacturer and the type of product. Typical MOQs range from 100 to 1000 units. To negotiate lower MOQs, present your business plan and potential for future orders. Building a relationship with the manufacturer can also lead to more favorable terms. Consider consolidating orders with other businesses to meet the MOQ without overextending your inventory. -
How can I customize auto accessories to fit my market’s needs?
Customization options often depend on the manufacturer’s capabilities. Discuss your specific requirements, such as design, color, and branding, during initial communications. Many manufacturers are open to custom orders, especially if they see a potential market in your region, such as the Middle East or Africa. Ensure you have clear specifications and consider a prototype to assess the final product before full-scale production. -
What logistics considerations should I be aware of when importing auto accessories?
Logistics can be complex, especially for international shipments. Understand the shipping options available, including air freight and sea freight, and their respective costs and delivery times. Work with a reputable freight forwarder to navigate customs regulations and ensure compliance with import/export laws specific to your region. Additionally, factor in duties and taxes that may apply upon arrival in your country. -
How do I manage quality assurance when sourcing auto accessories internationally?
Implement a robust quality assurance (QA) process that includes setting clear quality standards and expectations with your manufacturer. Regular communication throughout the production process is vital. Utilize third-party QA services to conduct inspections at various stages—pre-production, during production, and post-production. This proactive approach can help identify issues early and ensure that the final products meet your specifications. -
What are the best practices for maintaining a long-term relationship with auto accessory manufacturers?
Building a strong, long-term relationship with manufacturers requires consistent communication and mutual trust. Regularly provide feedback on product quality and performance, and be responsive to their inquiries. Consider visiting their facilities to strengthen the partnership and gain insight into their operations. Also, honor your payment terms and commitments, as reliability fosters loyalty and can lead to better deals in the future.
Important Disclaimer & Terms of Use
⚠️ Important Disclaimer
The information provided in this guide, including content regarding manufacturers, technical specifications, and market analysis, is for informational and educational purposes only. It does not constitute professional procurement advice, financial advice, or legal advice.
While we have made every effort to ensure the accuracy and timeliness of the information, we are not responsible for any errors, omissions, or outdated information. Market conditions, company details, and technical standards are subject to change.
B2B buyers must conduct their own independent and thorough due diligence before making any purchasing decisions. This includes contacting suppliers directly, verifying certifications, requesting samples, and seeking professional consultation. The risk of relying on any information in this guide is borne solely by the reader.
Strategic Sourcing Conclusion and Outlook for auto accessorie manufacturer
What Are the Key Takeaways for B2B Buyers in the Auto Accessories Market?
In summary, strategic sourcing remains a pivotal component for international B2B buyers in the auto accessories market. By adopting a comprehensive approach that considers supplier capabilities, market dynamics, and regional trends, businesses can unlock significant cost efficiencies and quality improvements. For buyers from Africa, South America, the Middle East, and Europe, understanding local regulations and cultural nuances is essential to foster strong supplier relationships.
How Can Strategic Sourcing Enhance Competitive Advantage?
Investing in strategic sourcing not only mitigates risks associated with supply chain disruptions but also enhances innovation through collaborative partnerships. By leveraging technology and data analytics, businesses can better forecast demand and optimize inventory management, ensuring they stay ahead of market trends.
What Is the Future Outlook for Auto Accessories Sourcing?
Looking ahead, the landscape for auto accessories will continue to evolve with advancements in technology and shifting consumer preferences. International buyers are encouraged to remain agile and proactive, exploring sustainable sourcing practices that align with global standards. Embrace this opportunity to enhance your sourcing strategies and position your company for long-term success in a competitive market.
Engage with your suppliers today to capitalize on these insights and drive your business forward.