Discover Top Benefits from Automotive Accessorie Manufacturer (2025)
Introduction: Navigating the Global Market for automotive accessorie manufacturer
The global market for automotive accessory manufacturing presents a wealth of opportunities for international B2B buyers. However, sourcing the right automotive accessories can be a daunting challenge, especially for businesses in regions like Africa, South America, the Middle East, and Europe. Understanding the diverse landscape of suppliers, product types, and market dynamics is crucial for making informed purchasing decisions. This guide aims to equip buyers with essential insights into the automotive accessory manufacturing sector, covering various types of accessories, their applications, and effective supplier vetting strategies.
In the following sections, we will delve into the specific types of automotive accessories available, from performance-enhancing components to aesthetic enhancements. We will also explore the applications of these products across different vehicle categories and market segments. Additionally, the guide will provide practical advice on evaluating suppliers, including quality assurance practices, compliance with international standards, and cost considerations.
By navigating this comprehensive guide, B2B buyers can enhance their procurement strategies and ensure they select the most suitable automotive accessory manufacturers for their needs. This resource empowers businesses to forge strong partnerships and optimize their supply chains, ultimately leading to improved product offerings and customer satisfaction in competitive markets.
Understanding automotive accessorie manufacturer Types and Variations
Type Name | Key Distinguishing Features | Primary B2B Applications | Brief Pros & Cons for Buyers |
---|---|---|---|
OEM (Original Equipment Manufacturer) | Produces parts that meet vehicle manufacturers’ specifications | Vehicle assembly and replacement | Pros: High quality, compatibility; Cons: Higher cost, limited customization options |
Aftermarket Manufacturers | Provides parts and accessories not made by OEMs | Customization, performance upgrades | Pros: Variety, often lower cost; Cons: Quality can vary, compatibility issues |
Specialty Accessory Suppliers | Focus on niche markets, such as off-road or luxury accessories | Specific vehicle enhancements | Pros: Unique offerings, expertise; Cons: Limited availability, potential for higher prices |
Tiered Suppliers | Sells components at different levels of the supply chain | Bulk purchasing, component sourcing | Pros: Scalability, cost-effectiveness; Cons: Possible quality inconsistency, longer lead times |
E-commerce Platforms | Online marketplaces for automotive accessories | Wide range of products, convenience | Pros: Easy access, competitive pricing; Cons: Risk of counterfeit products, varying shipping times |
What Are OEM Manufacturers and Why Are They Important for B2B Buyers?
OEMs are crucial for ensuring that automotive parts fit seamlessly into the original vehicle designs. They adhere to strict quality and safety standards set by vehicle manufacturers. For B2B buyers, particularly those in industries like automotive repair or fleet management, purchasing from OEMs guarantees reliability and compatibility. However, buyers should be prepared for higher prices and limited options for customization. It’s essential to assess the specific needs of your business against the benefits of OEM parts.
How Do Aftermarket Manufacturers Offer Flexibility to B2B Buyers?
Aftermarket manufacturers produce a wide range of automotive accessories that cater to various customer preferences, often at a lower cost than OEMs. They enable businesses to offer customized solutions, such as performance upgrades or aesthetic enhancements. However, the quality of aftermarket parts can be inconsistent, so B2B buyers must conduct thorough research and vet potential suppliers to ensure product reliability. This sector is ideal for businesses looking to differentiate their offerings while managing costs.
What Are the Benefits of Specialty Accessory Suppliers for Niche Markets?
Specialty accessory suppliers focus on specific segments of the automotive market, such as off-road vehicles or luxury cars. They provide unique products that are not typically available from larger manufacturers. For B2B buyers, working with these suppliers can enhance their product offerings and cater to niche customer bases. However, the limited availability of these products can lead to higher prices and longer lead times, making it crucial to establish strong relationships with reliable suppliers.
How Can Tiered Suppliers Enhance Your B2B Supply Chain?
Tiered suppliers operate at different levels within the automotive supply chain, offering components for various applications. They can provide bulk purchasing options, which is advantageous for businesses looking to scale operations. While tiered suppliers can offer cost-effective solutions, buyers need to be aware of potential quality inconsistencies and longer lead times. Establishing clear communication and quality assurance protocols can mitigate these risks.
Why Should B2B Buyers Consider E-commerce Platforms for Automotive Accessories?
E-commerce platforms have revolutionized the way B2B buyers source automotive accessories, providing access to a vast range of products at competitive prices. These platforms allow for easy comparison of products and suppliers, enhancing purchasing decisions. However, buyers must be cautious of counterfeit products and varying shipping times. Building relationships with reputable sellers on these platforms can help ensure quality and reliability in the supply chain.
Key Industrial Applications of automotive accessorie manufacturer
Industry/Sector | Specific Application of Automotive Accessorie Manufacturer | Value/Benefit for the Business | Key Sourcing Considerations for this Application |
---|---|---|---|
Automotive Manufacturing | Production of custom-fit floor mats and seat covers | Enhances vehicle aesthetics and comfort, increasing customer satisfaction | Quality of materials, durability, compliance with safety standards |
Fleet Management | Installation of GPS tracking and telematics systems | Improved operational efficiency and vehicle management | Compatibility with existing systems, ease of installation, and support |
Aftermarket Retail | Supply of performance-enhancing parts (e.g., exhaust systems) | Attracts performance-oriented customers, boosts sales | Brand reputation, product certifications, and warranty terms |
Electric Vehicle (EV) Sector | Development of charging station accessories | Supports the growing EV market, meeting consumer demand for charging solutions | Compliance with electrical standards, availability of local support |
Logistics and Transportation | Provision of cargo management accessories (e.g., tie-downs) | Increases cargo security and reduces damage during transit | Load capacity ratings, material strength, and versatility in use |
How Do Automotive Accessorie Manufacturers Serve the Automotive Manufacturing Sector?
In the automotive manufacturing sector, accessory manufacturers produce custom-fit floor mats and seat covers that enhance vehicle aesthetics and comfort. By investing in high-quality materials and designs, manufacturers can significantly increase customer satisfaction. For international buyers, especially from regions like Africa and South America, it is crucial to consider durability and compliance with local safety standards to ensure that products meet consumer expectations and regulatory requirements.
What Role Do Automotive Accessories Play in Fleet Management?
In fleet management, the installation of GPS tracking and telematics systems is critical for improving operational efficiency. These accessories allow businesses to monitor vehicle performance and optimize routes, ultimately reducing costs. For B2B buyers in the Middle East and Europe, sourcing these systems requires careful consideration of compatibility with existing fleet management software, ease of installation, and the availability of ongoing technical support.
How Do Aftermarket Retailers Benefit from Performance-Enhancing Accessories?
Aftermarket retailers can significantly boost sales by offering performance-enhancing parts, such as exhaust systems and air filters. These accessories attract performance-oriented customers looking to upgrade their vehicles. Buyers from regions like Colombia and Indonesia should prioritize sourcing from reputable brands with established product certifications and favorable warranty terms to ensure quality and customer satisfaction.
Why Are Charging Station Accessories Important for the Electric Vehicle Sector?
As the electric vehicle (EV) market continues to expand, the development of charging station accessories becomes increasingly important. These accessories support the infrastructure needed for EV adoption, meeting consumer demand for accessible charging solutions. International B2B buyers must ensure that these products comply with electrical standards and consider the availability of local support to facilitate installation and maintenance.
How Do Cargo Management Accessories Enhance Logistics and Transportation?
In logistics and transportation, cargo management accessories, such as tie-downs and cargo nets, play a vital role in securing loads and preventing damage during transit. This is particularly important for businesses operating in regions with varied road conditions, where load security can impact delivery efficiency. Buyers should evaluate the load capacity ratings and material strength of these accessories to ensure they meet the specific needs of their operations.
Related Video: Top 10 New Technologies in Cars | The Future of Automotive Innovation
3 Common User Pain Points for ‘automotive accessorie manufacturer’ & Their Solutions
Scenario 1: Challenges with Quality Control in Sourcing Automotive Accessories
The Problem:
B2B buyers often face significant hurdles when sourcing automotive accessories due to quality control issues. This is particularly prevalent in regions like Africa and South America, where manufacturers may not adhere to international standards. Buyers may receive products that do not meet specifications, leading to customer dissatisfaction and potential financial losses. The inconsistency in quality can create a ripple effect, damaging brand reputation and complicating inventory management.
The Solution:
To mitigate these quality control challenges, B2B buyers should prioritize manufacturers with a proven track record of quality assurance. Conducting thorough due diligence is essential; this includes requesting certifications and quality assurance processes from potential suppliers. Buyers should also consider on-site inspections or third-party audits to verify manufacturing practices. Additionally, establishing clear communication channels with manufacturers and setting specific quality benchmarks can help ensure that the products meet the required standards. Leveraging technology, such as digital quality control platforms, can also enhance monitoring and reporting, thereby reducing the risk of receiving subpar products.
Scenario 2: Navigating the Complexities of International Shipping and Logistics
The Problem:
For international buyers, particularly in the Middle East and Europe, the logistics of shipping automotive accessories can be daunting. Issues such as customs delays, unexpected tariffs, and fluctuating shipping costs can disrupt supply chains and lead to increased overhead. Moreover, the lack of transparency in tracking shipments can create anxiety regarding delivery timelines, affecting inventory levels and customer satisfaction.
The Solution:
B2B buyers can streamline their logistics by partnering with manufacturers that have established relationships with reliable shipping and logistics companies. It’s crucial to discuss shipping terms upfront, including Incoterms, to avoid confusion later. Buyers should also utilize freight forwarders who specialize in automotive accessories, as they can offer tailored solutions and keep buyers informed about shipping statuses. Implementing robust inventory management software can provide real-time updates on stock levels and shipments, allowing businesses to plan more effectively. Additionally, considering local manufacturers or regional suppliers can reduce shipping complexities and costs.
Scenario 3: Difficulty in Customization and Meeting Market Demands
The Problem:
As consumer preferences evolve, B2B buyers in regions like South America and Africa often struggle to find automotive accessories that cater to specific market demands. Many manufacturers provide limited customization options, which can hinder a buyer’s ability to differentiate their offerings in a competitive market. This limitation not only affects sales but also the buyer’s ability to build strong customer relationships.
The Solution:
To address the challenge of customization, buyers should seek out automotive accessory manufacturers that offer flexible design capabilities and are open to collaboration. Engaging in discussions about specific market needs and providing feedback on product features can lead to tailored solutions that resonate with local consumers. Additionally, buyers can explore partnerships with manufacturers that specialize in bespoke products, as this can lead to unique offerings that set them apart from competitors. Leveraging tools such as 3D modeling software during the design phase can facilitate the customization process, enabling buyers to visualize and refine products before production. Regular market research to keep abreast of consumer trends will also help buyers communicate their needs effectively to manufacturers.
Strategic Material Selection Guide for automotive accessorie manufacturer
What Are the Key Properties of Common Materials Used in Automotive Accessories?
When selecting materials for automotive accessories, manufacturers must consider various properties that affect product performance. Common materials include plastics, metals, composites, and rubber. Each material has unique characteristics that influence durability, manufacturing complexity, and suitability for specific applications.
How Do Plastics Perform in Automotive Accessories Manufacturing?
Plastics, particularly engineering plastics like polycarbonate and nylon, are widely used in automotive accessories due to their lightweight nature and versatility. They exhibit excellent temperature resistance and can withstand pressures typical in automotive environments. However, their susceptibility to UV degradation and chemical exposure can limit their longevity.
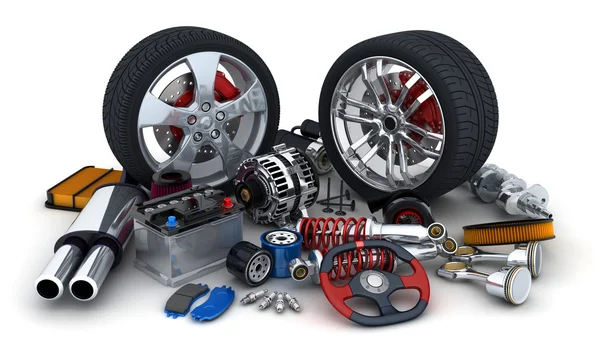
A stock image related to automotive accessorie manufacturer.
Pros: Plastics are generally cost-effective and easy to mold, allowing for complex shapes and designs. They also offer good corrosion resistance, making them suitable for various automotive applications.
Cons: While they are durable, plastics may not perform well under extreme conditions, such as high temperatures or exposure to certain chemicals. This can lead to premature failure in critical components.
Impact on Application: Plastics are often used in interior components like dashboards and trim, where aesthetics and weight savings are critical. However, their compatibility with specific automotive fluids should be evaluated to prevent degradation.
Considerations for International Buyers: Buyers from regions like Africa and South America should ensure compliance with local regulations regarding plastic use, including recycling standards. Familiarity with ASTM and ISO standards can aid in selecting the right type of plastic for specific applications.
What Advantages Do Metals Offer for Automotive Accessories?
Metals, such as aluminum and stainless steel, are favored for their strength and durability. They have high-temperature ratings and excellent corrosion resistance, making them ideal for components exposed to harsh environments.
Pros: Metals provide superior structural integrity and can withstand significant mechanical stress. They are also recyclable, which aligns with sustainability goals.
Cons: The manufacturing complexity of metal components can lead to higher costs and longer lead times. Additionally, metals are heavier than plastics, which can negatively impact fuel efficiency in automotive applications.
Impact on Application: Metals are commonly used in structural components, brackets, and fasteners where strength is paramount. Their compatibility with various media, including oils and fuels, is generally high.
Considerations for International Buyers: Buyers in the Middle East and Europe should be aware of specific standards like DIN and JIS for metal components. Understanding the local market’s preferences for material sourcing can also influence procurement strategies.
How Do Composites Enhance Performance in Automotive Accessories?
Composites, such as carbon fiber and fiberglass, combine the best properties of plastics and metals. They offer high strength-to-weight ratios and excellent resistance to environmental factors.
Pros: Composites are lightweight and can be tailored for specific applications, improving fuel efficiency and performance. They also resist corrosion and fatigue, enhancing product longevity.
Cons: The cost of composites can be significantly higher than traditional materials, and their manufacturing processes can be complex, requiring specialized techniques.
Impact on Application: Composites are ideal for high-performance automotive accessories, such as body panels and structural components, where weight savings are crucial.
Considerations for International Buyers: Buyers from Europe may find a growing market for composites due to environmental regulations pushing for lighter vehicles. Understanding compliance with EU standards for composite materials is essential for successful procurement.
How Does Rubber Contribute to Automotive Accessories?
Rubber is primarily used in seals, gaskets, and vibration dampening components. It has excellent flexibility and can withstand a range of temperatures and pressures.
Pros: Rubber provides effective sealing properties and noise reduction, enhancing the overall performance of automotive accessories. Its ability to absorb shocks makes it invaluable in various applications.
Cons: Rubber can degrade over time due to exposure to heat, ozone, and certain chemicals, which may limit its lifespan in some applications.
Impact on Application: Rubber is crucial in applications requiring flexibility and sealing, such as weather stripping and engine mounts.
Considerations for International Buyers: Buyers in regions like South America should ensure that rubber materials meet local quality standards and regulations, as improper materials can lead to failures in critical components.
Summary Table of Material Selection for Automotive Accessories
Material | Typical Use Case for automotive accessorie manufacturer | Key Advantage | Key Disadvantage/Limitation | Relative Cost (Low/Med/High) |
---|---|---|---|---|
Plastics | Interior components (dashboards, trim) | Lightweight and cost-effective | Susceptible to UV and chemical degradation | Medium |
Metals | Structural components (brackets, fasteners) | High strength and durability | Higher manufacturing costs | High |
Composites | Body panels, high-performance parts | Superior strength-to-weight ratio | High cost and complex manufacturing | High |
Rubber | Seals, gaskets, vibration dampeners | Excellent flexibility and sealing | Degradation over time | Medium |
In-depth Look: Manufacturing Processes and Quality Assurance for automotive accessorie manufacturer
What Are the Main Stages of the Manufacturing Process for Automotive Accessories?
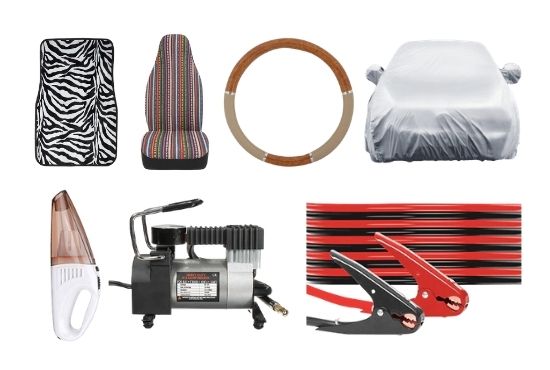
A stock image related to automotive accessorie manufacturer.
The manufacturing process for automotive accessories typically consists of four main stages: material preparation, forming, assembly, and finishing. Each stage is crucial for ensuring that the final product meets both quality standards and customer specifications.
1. Material Preparation
Material preparation involves selecting the appropriate raw materials, which can include plastics, metals, and composites. For B2B buyers, understanding the source and quality of materials is vital. Suppliers often utilize advanced material testing techniques to ensure consistency and compliance with international standards. It’s advisable for buyers to inquire about the origin of materials and any certifications that support their quality.
2. Forming Techniques
Forming is the process where raw materials are shaped into specific designs. Common techniques include injection molding for plastics, stamping for metals, and extrusion for creating profiles. Each technique has its advantages; for instance, injection molding allows for complex shapes and is highly efficient for mass production. Buyers should assess whether the manufacturer has the capability to utilize advanced forming techniques that can enhance product functionality and reduce waste.
3. Assembly Processes
The assembly stage brings together various components to create the final product. This can involve manual assembly, automated processes, or a combination of both. Automation can significantly increase efficiency and consistency, which is crucial for large-scale orders. B2B buyers should evaluate a manufacturer’s assembly capabilities, including the level of automation and the expertise of the workforce involved in the assembly process.
4. Finishing Techniques
Finishing is the final stage where products are treated to enhance their appearance and durability. Techniques such as painting, coating, and polishing are common in the automotive accessories sector. The finishing process not only improves aesthetics but also provides protection against environmental factors. Buyers should look for manufacturers that adhere to best practices in finishing to ensure longevity and performance of the accessories.
How Do Quality Assurance Processes Ensure Product Reliability?
Quality assurance (QA) is integral to the manufacturing of automotive accessories, ensuring that products meet both regulatory standards and customer expectations. For international B2B buyers, understanding these QA processes can help in selecting reliable suppliers.
International Quality Standards: Why Are They Important?
Adhering to international quality standards such as ISO 9001 is essential for manufacturers. ISO 9001 outlines criteria for a quality management system, focusing on customer satisfaction and continuous improvement. B2B buyers should request evidence of certification, as it demonstrates a supplier’s commitment to maintaining quality throughout the manufacturing process.
What Are the Industry-Specific Standards for Automotive Accessories?
In addition to ISO standards, there are industry-specific certifications that may be relevant, such as CE marking in Europe and API standards for oil-related products. These certifications ensure that products are safe, reliable, and compliant with regional regulations. Buyers should verify that their suppliers hold the necessary certifications for the markets they intend to serve.
What Are the Key Quality Control Checkpoints in Manufacturing?
Quality control (QC) checkpoints are critical in the manufacturing process, helping to identify defects and ensure product consistency. Key checkpoints include:
-
Incoming Quality Control (IQC): This step involves inspecting raw materials upon arrival to ensure they meet specified standards. Buyers should confirm that their suppliers have robust IQC procedures in place.
-
In-Process Quality Control (IPQC): During the manufacturing process, IPQC measures and inspects products at various stages. This helps catch defects early on and reduces waste. Manufacturers should provide documentation of their IPQC processes for buyer assurance.
-
Final Quality Control (FQC): This final inspection occurs before products are shipped. FQC checks for overall product functionality, aesthetics, and compliance with specifications. Buyers should request reports from FQC to ensure products meet their expectations.
What Common Testing Methods Are Used in Quality Assurance?
Testing methods play a vital role in ensuring the quality and reliability of automotive accessories. Common methods include:
-
Mechanical Testing: Evaluating the strength, durability, and elasticity of materials through tensile, compression, and impact tests.
-
Environmental Testing: Assessing how products withstand various environmental conditions, such as temperature fluctuations and humidity.
-
Functional Testing: Ensuring that the accessory performs its intended function under normal use conditions.
B2B buyers should inquire about the specific testing methods employed by manufacturers to ensure comprehensive quality assurance.
How Can B2B Buyers Verify Supplier Quality Control?
Verifying a supplier’s quality control processes is essential for B2B buyers to mitigate risks associated with product defects. Here are several strategies:
-
Conduct Audits: Regularly auditing suppliers can help buyers assess their manufacturing processes and quality assurance measures. This includes reviewing documentation, visiting facilities, and observing practices in action.
-
Request Quality Reports: Buyers should ask for detailed quality reports, including data on inspections, test results, and any corrective actions taken. This transparency can build trust and ensure accountability.
-
Engage Third-Party Inspectors: Utilizing third-party inspection services can provide an unbiased evaluation of a supplier’s quality control practices. This is especially useful for buyers in regions where travel may be difficult or costly.
What Are the Quality Control Nuances for International B2B Buyers?
International B2B buyers must navigate various quality control nuances when sourcing automotive accessories. Understanding regional regulations, cultural expectations, and logistical challenges is crucial. For example, buyers from Africa may face different regulatory landscapes compared to those in Europe or South America.
Additionally, language barriers and differing quality standards can complicate communication. Buyers should prioritize suppliers with experience in international trade and those who can demonstrate a commitment to quality across different markets.
By understanding the manufacturing processes and quality assurance measures, international B2B buyers can make informed decisions that lead to successful partnerships in the automotive accessories sector.
Practical Sourcing Guide: A Step-by-Step Checklist for ‘automotive accessorie manufacturer’
This guide provides a structured approach for international B2B buyers looking to procure automotive accessories from manufacturers. Sourcing the right supplier is critical to ensuring quality, reliability, and value in your procurement process. Follow these steps to streamline your sourcing journey.
Step 1: Define Your Technical Specifications
Begin by clearly outlining the technical specifications of the automotive accessories you need. This includes materials, dimensions, performance standards, and any regulatory compliance relevant to your market. A well-defined specification helps in communicating your needs to potential suppliers and ensures you receive accurate quotes and samples.
- Material Requirements: Specify the type of materials you prefer (e.g., plastic, metal, eco-friendly options).
- Compliance Standards: Identify any local or international standards that must be met (e.g., ISO, ASTM).
Step 2: Conduct Market Research on Suppliers
Research potential suppliers to understand their market position and capabilities. Look for manufacturers that specialize in automotive accessories and have a proven track record in your target regions such as Africa, South America, the Middle East, and Europe.
- Online Directories: Utilize platforms like Alibaba, ThomasNet, or industry-specific directories.
- Trade Shows: Attend relevant trade shows and exhibitions to meet suppliers face-to-face.
Step 3: Evaluate Potential Suppliers
Before making any commitments, it’s essential to thoroughly vet potential suppliers. This evaluation process should include assessing their experience, production capacity, and customer feedback.
- Request Documentation: Ask for company profiles, case studies, and references from existing clients.
- Site Visits: If feasible, conduct site visits to assess manufacturing capabilities and quality control processes.
Step 4: Verify Supplier Certifications
Ensure that your selected suppliers hold the necessary certifications that demonstrate their commitment to quality and safety. Certifications like ISO 9001 or specific automotive quality standards (IATF 16949) are indicators of a reliable manufacturer.
- Certification Verification: Check the validity of the certifications by contacting the issuing bodies.
- Quality Assurance: Look into their quality management systems to understand their processes.
Step 5: Request Samples and Conduct Quality Testing
Always request samples of the automotive accessories before finalizing any orders. This step is crucial for assessing the product quality and suitability for your market.
- Testing Procedures: Implement your own testing protocols to evaluate durability, functionality, and compliance with specifications.
- Feedback Loop: Involve your team in the evaluation process to gather diverse insights on the samples.
Step 6: Negotiate Terms and Conditions
Once you are satisfied with a supplier’s capabilities and product quality, move on to negotiate terms and conditions. This includes pricing, payment terms, lead times, and delivery schedules.
- Long-term Agreements: Consider discussing long-term contracts for better pricing and reliability.
- Flexibility in Orders: Negotiate terms that allow for flexibility in order quantities based on demand fluctuations.
Step 7: Establish a Communication Plan
Effective communication is vital for a successful partnership. Establish clear channels and protocols for ongoing communication with your supplier.
- Regular Updates: Schedule regular check-ins to discuss production progress, quality issues, and future orders.
- Crisis Management: Develop a plan for addressing any potential issues that may arise during the procurement process.
By following this comprehensive checklist, international B2B buyers can enhance their sourcing strategy for automotive accessories, ensuring they partner with manufacturers who meet their specific needs and standards.
Comprehensive Cost and Pricing Analysis for automotive accessorie manufacturer Sourcing
What Are the Key Cost Components in Automotive Accessory Manufacturing?
Understanding the cost structure of automotive accessory manufacturing is crucial for B2B buyers, particularly those operating in diverse markets such as Africa, South America, the Middle East, and Europe. The main cost components include:
-
Materials: This is often the largest portion of the overall cost. The choice of materials affects not only the price but also the product’s durability and functionality. Buyers should consider sourcing materials locally to reduce import costs or explore alternatives that meet quality standards at a lower price.
-
Labor: Labor costs vary significantly by region. In developing markets, labor can be more affordable, but this often comes with trade-offs in skill and productivity. Buyers should evaluate the labor force’s expertise in manufacturing specific accessories to ensure product quality.
-
Manufacturing Overhead: This includes utilities, rent, and administrative costs associated with production facilities. Buyers should inquire about these costs when negotiating prices, as they can significantly impact the final quote.
-
Tooling: The initial setup costs for molds and machinery can be substantial, especially for custom products. Buyers should assess the tooling costs and consider whether they can share these costs with the supplier through larger orders.
-
Quality Control (QC): Investing in rigorous quality control processes is essential to ensure product reliability. Buyers should inquire about the QC measures implemented by manufacturers and how these affect pricing.
-
Logistics: Shipping costs, including freight, insurance, and handling, can vary widely based on the destination and Incoterms. Understanding these costs upfront can help buyers budget effectively.
-
Margin: Manufacturers will include their profit margin in the final price. Buyers should be aware of standard margins in the industry to gauge whether a price is fair.
How Do Price Influencers Affect Sourcing Decisions?
Several factors influence pricing in the automotive accessory manufacturing sector:
-
Volume/MOQ (Minimum Order Quantity): Larger orders typically lead to lower per-unit prices due to economies of scale. Buyers should analyze their demand to negotiate favorable terms.
-
Specifications and Customization: Customized products often incur higher costs due to unique tooling and design requirements. Clearly defining specifications can help avoid unexpected charges.
-
Materials and Quality Certifications: The choice of materials directly impacts pricing. Additionally, products that meet certain quality certifications may command higher prices, reflecting their compliance with industry standards.
-
Supplier Factors: Relationships and reputation play a significant role. Established suppliers may charge more due to their reliability and brand strength. Buyers should assess the supplier’s track record in delivering quality products on time.
-
Incoterms: The choice of Incoterms affects who bears the cost of shipping and insurance. Buyers should understand these terms to negotiate better pricing and manage risk.
What Are the Best Negotiation Strategies for International B2B Buyers?
International buyers should approach negotiations with a comprehensive understanding of the total cost of ownership (TCO). Here are actionable tips:
-
Do Your Research: Analyze market prices and competitor offerings to establish a baseline for negotiations. Having data can empower buyers during discussions.
-
Focus on Total Cost of Ownership: Consider not just the purchase price but also potential costs associated with logistics, maintenance, and disposal. This broader view can justify a higher initial investment if it leads to lower long-term costs.
-
Be Clear About Specifications: Clearly communicating product specifications can minimize misunderstandings and unexpected costs later in the process.
-
Leverage Relationships: Building strong relationships with suppliers can lead to better pricing, improved service, and flexibility in negotiations.
-
Explore Payment Terms: Negotiating favorable payment terms can enhance cash flow management. Consider options such as installment payments or discounts for early payment.
Disclaimer on Indicative Prices
Prices in the automotive accessory manufacturing sector can fluctuate based on market conditions, material availability, and geopolitical factors. It is crucial for international B2B buyers to conduct thorough due diligence and obtain multiple quotes to ensure they are making well-informed purchasing decisions.
Alternatives Analysis: Comparing automotive accessorie manufacturer With Other Solutions
When considering the procurement of automotive accessories, B2B buyers must evaluate various solutions available in the market. Understanding the alternatives to traditional automotive accessory manufacturers allows international buyers—especially those from Africa, South America, the Middle East, and Europe—to make informed decisions that align with their business objectives. Below, we present a comparison of automotive accessory manufacturers against two viable alternatives: aftermarket parts suppliers and 3D printing technology.
Comparison Aspect | Automotive Accessorie Manufacturer | Aftermarket Parts Supplier | 3D Printing Technology |
---|---|---|---|
Performance | High-quality, standardized products | Variable quality, often lower than OEM | Customization potential, may vary in quality |
Cost | Typically higher due to brand value | Generally lower, competitive pricing | Initial setup cost high, but low per-unit cost |
Ease of Implementation | Straightforward with established supply chains | May require research to find reliable suppliers | Complex setup, requires technical expertise |
Maintenance | Regular updates and support available | Limited support; warranty varies | Minimal maintenance; dependent on software updates |
Best Use Case | Large-scale operations needing reliability | Cost-sensitive projects, repairs | Custom, low-volume needs or prototyping |
What Are the Pros and Cons of Aftermarket Parts Suppliers?
Aftermarket parts suppliers can provide a cost-effective solution for businesses looking to save on expenses. These suppliers often offer a wide range of products at competitive prices, making them an attractive option for budget-conscious buyers. However, the quality of aftermarket parts can be inconsistent, with some products falling short of OEM standards. This variability can lead to increased maintenance issues and potential damage to vehicles, which may negate initial savings. Buyers must conduct thorough research and vet suppliers to ensure they meet quality standards.
How Does 3D Printing Technology Compare to Traditional Manufacturing?
3D printing technology offers remarkable customization possibilities, allowing businesses to produce unique parts tailored to specific vehicle models or individual customer needs. This technology is particularly beneficial for low-volume production runs or prototyping, where traditional manufacturing processes may be cost-prohibitive. However, the initial investment in 3D printing technology can be significant, and the complexity of the setup may require specialized knowledge. Additionally, while the per-unit cost can be low for larger runs, the overall investment may not be justified for businesses with predictable, high-volume needs.
Conclusion: How Can B2B Buyers Choose the Right Automotive Accessory Solution?
Selecting the right automotive accessory solution requires a careful assessment of your specific business needs and operational context. Buyers should consider the scale of their operations, budget constraints, and the importance of quality versus cost. While automotive accessory manufacturers provide reliability and support, aftermarket parts suppliers and 3D printing technologies offer alternative benefits that may better suit certain projects. Ultimately, a comprehensive analysis of these factors will guide B2B buyers in making a choice that aligns with their strategic goals and enhances their competitive edge in the market.
Essential Technical Properties and Trade Terminology for automotive accessorie manufacturer
What Are the Essential Technical Properties of Automotive Accessories?
When sourcing automotive accessories, understanding the technical specifications is crucial. Here are several key properties that significantly impact product quality and performance:
1. Material Grade: Why Is It Important?
Material grade refers to the classification of the materials used in manufacturing automotive accessories. Common materials include plastics, metals, and composites, each graded based on their mechanical properties, durability, and suitability for specific applications. For B2B buyers, selecting the right material grade ensures that the products meet safety standards and performance expectations, reducing the risk of product failure and enhancing customer satisfaction.
2. Tolerance: How Does It Affect Product Quality?
Tolerance defines the permissible limits of variation in a physical dimension of a part. It is crucial in automotive accessories where precision is paramount. For instance, components that fit together must have tight tolerances to ensure proper functionality and safety. Buyers should be aware that tighter tolerances often lead to higher manufacturing costs but are essential for critical applications where performance cannot be compromised.
3. Finish Quality: What Does It Entail?
Finish quality encompasses the surface treatment of a product, affecting its aesthetics, corrosion resistance, and functionality. Common finishes include anodizing, painting, and polishing. For B2B buyers, understanding finish quality is essential for branding and durability. High-quality finishes can enhance the product’s lifespan and appeal, which is particularly important in competitive markets.
4. Load Capacity: Why Is It Critical?
Load capacity indicates the maximum weight or stress that an accessory can withstand without failure. This property is particularly relevant for components such as roof racks or towing accessories. Buyers must ensure that the load capacity aligns with the intended use to avoid potential liability issues and ensure customer safety.
5. Compliance Standards: What Should Buyers Know?
Compliance standards refer to the regulations and certifications that automotive accessories must meet, such as ISO, SAE, or specific regional certifications. Understanding these standards is vital for B2B buyers, as non-compliance can lead to legal issues, product recalls, and damage to brand reputation. It’s advisable for buyers to request documentation proving compliance before finalizing purchases.
Which Trade Terminology Should International Buyers Understand?
Navigating the automotive accessories market requires familiarity with specific trade terms. Here are some commonly used terms that every buyer should know:
1. OEM (Original Equipment Manufacturer): What Does It Mean?
OEM refers to companies that produce parts or equipment that may be marketed by another manufacturer. In the automotive industry, OEM parts are made to the exact specifications of the original vehicle manufacturer. Understanding OEM is crucial for buyers seeking quality and compatibility, ensuring that the accessories will function seamlessly with existing systems.
2. MOQ (Minimum Order Quantity): How Does It Impact Purchasing?
MOQ is the smallest quantity of a product that a supplier is willing to sell. For international B2B buyers, understanding MOQ is essential for budgeting and inventory management. Suppliers often set MOQs to cover production costs, so negotiating favorable terms can lead to better pricing and lower risk.
3. RFQ (Request for Quotation): What Is Its Purpose?
An RFQ is a formal process where buyers request pricing and terms from suppliers for specific products. Utilizing RFQs allows buyers to compare different suppliers and negotiate better deals. This is particularly important in international trade, where price variations can be significant.
4. Incoterms: Why Are They Important for Shipping?
Incoterms are international commercial terms that define the responsibilities of buyers and sellers in the shipping process. They clarify who pays for shipping, insurance, and duties, reducing the risk of misunderstandings. Familiarity with Incoterms helps buyers make informed decisions about shipping costs and logistics.
5. Lead Time: What Should Buyers Expect?
Lead time is the period between placing an order and receiving the product. Understanding lead times is essential for effective supply chain management. Buyers should factor in lead times when planning inventory and fulfilling customer orders to avoid disruptions in their operations.
By grasping these essential technical properties and trade terms, international B2B buyers from regions like Africa, South America, the Middle East, and Europe can make informed decisions, ensuring quality and compliance in their automotive accessory purchases.
Navigating Market Dynamics and Sourcing Trends in the automotive accessorie manufacturer Sector
What Are the Key Market Dynamics and Trends Impacting Automotive Accessory Manufacturing?
The automotive accessory manufacturing sector is experiencing significant transformation driven by various global factors. One of the key trends is the increasing demand for personalized and technologically advanced accessories, which is reshaping consumer expectations. B2B buyers, particularly in emerging markets like Africa and South America, are leaning towards suppliers who can offer innovative solutions tailored to local preferences. Additionally, the rise of e-commerce platforms is enabling manufacturers to reach broader international markets, facilitating easier sourcing and distribution.
Another critical aspect is the integration of advanced technologies such as Artificial Intelligence (AI) and the Internet of Things (IoT) in manufacturing processes. These technologies not only improve production efficiency but also enhance product quality and customization capabilities. For B2B buyers, this means they can expect shorter lead times and more reliable supply chains. Furthermore, sustainability is becoming a non-negotiable aspect of sourcing decisions. Manufacturers are increasingly adopting eco-friendly practices, making it essential for buyers to prioritize suppliers who align with these values.
How Is Sustainability Shaping the Automotive Accessory Supply Chain?
The environmental impact of automotive accessories is a growing concern among consumers and regulatory bodies alike. B2B buyers are now faced with the challenge of ensuring that their sourcing decisions contribute positively to the environment. Ethical sourcing is gaining traction, with businesses being held accountable for their supply chain practices. This shift is prompting manufacturers to adopt sustainable materials and processes, such as biodegradable plastics and energy-efficient production techniques.
Buyers should look for suppliers that hold certifications like ISO 14001 for environmental management or use materials that are certified as sustainable. These certifications not only reflect a commitment to environmental stewardship but also enhance brand reputation among increasingly eco-conscious consumers. Additionally, transparency in the supply chain is becoming paramount, as buyers seek assurance that their suppliers adhere to ethical labor practices. Engaging with manufacturers who prioritize sustainability can lead to long-term partnerships that are beneficial for both parties.
What Is the Historical Context of Automotive Accessory Manufacturing?
The automotive accessory manufacturing industry has evolved significantly over the decades. Initially focused on basic functional components, the sector has transformed into a dynamic landscape driven by technological advancements and changing consumer preferences. The 1980s and 1990s marked the onset of customization, where consumers began seeking unique accessories to personalize their vehicles. This trend has only intensified with the advent of digital technologies, enabling consumers to access a wider range of products online.
In the 21st century, the industry has increasingly focused on innovation and sustainability, reflecting broader societal shifts towards environmental responsibility. As international B2B buyers navigate this evolving landscape, understanding the historical context can provide valuable insights into current trends and future directions in automotive accessory manufacturing.
Frequently Asked Questions (FAQs) for B2B Buyers of automotive accessorie manufacturer
-
How do I identify a reliable automotive accessories manufacturer for my business?
To identify a reliable automotive accessories manufacturer, start by conducting thorough research online, focusing on industry directories and platforms like Alibaba or Global Sources. Look for manufacturers with verified credentials, positive reviews, and a solid history of international trade. Request samples to evaluate product quality and assess their responsiveness to inquiries. Additionally, consider visiting their facility if possible or seeking third-party inspection services to ensure they meet your standards. -
What are the key factors to consider when choosing an automotive accessories supplier?
When selecting a supplier for automotive accessories, consider several key factors: product quality, pricing, minimum order quantities (MOQs), lead times, and payment terms. It’s essential to assess their ability to customize products according to your specifications. Also, evaluate their shipping capabilities, after-sales support, and warranty policies. Engaging in direct communication will also help gauge their reliability and willingness to partner long-term. -
What is the typical minimum order quantity (MOQ) for automotive accessories?
The MOQ for automotive accessories can vary widely depending on the manufacturer and the type of product. Generally, it ranges from 100 to 1,000 units. Some manufacturers may offer lower MOQs for specific items or sample orders. Always clarify MOQs upfront to avoid misunderstandings and ensure that your purchasing needs align with the supplier’s capabilities. -
How can I ensure quality assurance (QA) when sourcing automotive accessories?
To ensure quality assurance, implement a multi-step approach: first, request detailed product specifications and certifications from the manufacturer. Conduct factory audits and inspections, preferably through third-party services, to verify production processes. Establish a clear agreement on quality standards in your contract and consider including penalties for non-compliance. Regular communication during production will also help you address any issues proactively. -
What payment terms are common when dealing with automotive accessories manufacturers?
Common payment terms in the automotive accessories sector include options like 30% upfront and 70% upon delivery, or full payment in advance for smaller orders. Some manufacturers may offer credit terms after establishing a relationship. Always negotiate payment terms that suit your cash flow needs while ensuring the manufacturer feels secure in their transaction. Using secure payment methods like letters of credit can further protect both parties. -
What logistics considerations should I keep in mind when importing automotive accessories?
When importing automotive accessories, logistics considerations include shipping methods, customs regulations, and delivery times. Choose between air freight for speed or sea freight for cost-effectiveness based on your needs. Familiarize yourself with the customs processes in your country to avoid delays, and ensure all documentation is accurate. Partnering with a reliable freight forwarder can streamline the process and help navigate complex logistics. -
How can I customize automotive accessories to meet my market’s needs?
Customizing automotive accessories involves discussing your specific requirements with the manufacturer early in the sourcing process. Provide detailed specifications, including materials, dimensions, and design elements. Many manufacturers have design teams that can assist you in developing prototypes. Be prepared for possible additional costs and longer lead times for custom products, but ensure that the final design aligns with your target market’s preferences. -
What are the best practices for maintaining a long-term relationship with my automotive accessories supplier?
To maintain a long-term relationship with your automotive accessories supplier, prioritize open and honest communication. Regularly share feedback on product quality and delivery performance. Consider placing consistent orders to build trust and reliability. Additionally, engage in collaborative efforts, such as co-developing new products or exploring joint marketing initiatives. A mutually beneficial partnership will foster loyalty and improve overall business outcomes.
Important Disclaimer & Terms of Use
⚠️ Important Disclaimer
The information provided in this guide, including content regarding manufacturers, technical specifications, and market analysis, is for informational and educational purposes only. It does not constitute professional procurement advice, financial advice, or legal advice.
While we have made every effort to ensure the accuracy and timeliness of the information, we are not responsible for any errors, omissions, or outdated information. Market conditions, company details, and technical standards are subject to change.
B2B buyers must conduct their own independent and thorough due diligence before making any purchasing decisions. This includes contacting suppliers directly, verifying certifications, requesting samples, and seeking professional consultation. The risk of relying on any information in this guide is borne solely by the reader.
Strategic Sourcing Conclusion and Outlook for automotive accessorie manufacturer
In the rapidly evolving landscape of automotive accessories manufacturing, strategic sourcing emerges as a crucial component for B2B buyers aiming to enhance their competitive edge. By prioritizing supplier relationships and leveraging global supply chains, businesses can access innovative products while ensuring cost-efficiency. Particularly for buyers in Africa, South America, the Middle East, and Europe, understanding local market dynamics and regulatory requirements can significantly influence sourcing decisions.
How Can Strategic Sourcing Enhance Your Supply Chain?
Investing in strategic sourcing not only minimizes risks associated with supply disruptions but also fosters sustainability through responsible sourcing practices. As international markets become increasingly interconnected, tapping into diverse supplier networks can unlock opportunities for collaboration and innovation. Buyers should be proactive in conducting thorough market research, evaluating potential suppliers, and establishing clear communication channels to facilitate seamless transactions.
What Does the Future Hold for B2B Automotive Accessory Buyers?
Looking ahead, the focus on digital transformation and sustainability will shape the future of automotive accessories. B2B buyers are encouraged to embrace technology to streamline sourcing processes and enhance transparency. By prioritizing strategic partnerships and staying abreast of emerging trends, businesses can position themselves for long-term success in this dynamic sector.
In conclusion, as the automotive accessories market continues to evolve, strategic sourcing will be key to unlocking new opportunities. Buyers are urged to engage with suppliers who share their vision for innovation and sustainability, paving the way for a prosperous future in the automotive industry.