Improve Quality & Cut Costs: Steel Cable Manufacturer Guide (2025)
Introduction: Navigating the Global Market for steel cable manufacturer
In today’s rapidly evolving industrial landscape, sourcing steel cables that meet specific project requirements can be a daunting challenge for international B2B buyers. With diverse applications ranging from construction to telecommunications, the demand for high-quality steel cable manufacturers has surged globally. This comprehensive guide delves into the critical aspects of navigating the global market for steel cable manufacturing, equipping buyers from Africa, South America, the Middle East, and Europe with the insights needed to make informed purchasing decisions.
Within these pages, we will explore various types of steel cables, their applications across different industries, and essential criteria for supplier vetting. Understanding the nuances of cost structures, quality standards, and compliance regulations will also be a focal point, allowing you to compare and evaluate potential suppliers effectively. By addressing these key elements, this guide empowers you to mitigate risks, optimize procurement strategies, and foster long-term partnerships with reliable manufacturers.
Whether you are based in Argentina, Vietnam, or any other region, navigating the complexities of the steel cable market requires a strategic approach. Armed with the knowledge contained herein, you will be better positioned to identify the right suppliers, negotiate favorable terms, and ultimately enhance the efficiency of your operations. Dive in to discover how to streamline your sourcing processes and ensure your projects have the robust steel cable solutions they need.
Understanding steel cable manufacturer Types and Variations
Type Name | Key Distinguishing Features | Primary B2B Applications | Brief Pros & Cons for Buyers |
---|---|---|---|
General Purpose Steel Cable | Versatile, multi-stranded construction | Construction, manufacturing, shipping | Pros: Cost-effective, widely available. Cons: Limited specialty applications. |
High-Strength Steel Cable | Enhanced tensile strength, often with alloying | Heavy lifting, mining, and offshore work | Pros: Superior durability, reduced weight. Cons: Higher cost, may require specialized suppliers. |
Stainless Steel Cable | Corrosion-resistant, aesthetic finish | Marine, architectural, and food industry | Pros: Long lifespan, low maintenance. Cons: Higher initial investment. |
Plastic Coated Steel Cable | Additional plastic layer for protection and grip | Safety applications, playgrounds, fencing | Pros: Increased safety, colorful options. Cons: Limited temperature tolerance. |
Wire Rope | Comprised of multiple wires, often larger diameter | Cranes, elevators, and heavy machinery | Pros: High load capacity, flexible. Cons: Requires maintenance to avoid wear. |
What are the Characteristics of General Purpose Steel Cable?
General Purpose Steel Cables are designed for versatility, making them suitable for a wide range of applications across various industries. They are typically constructed with multiple strands, which provide flexibility and strength. When considering a supplier, buyers should evaluate the cable’s diameter, breaking strength, and compliance with industry standards. This type is ideal for buyers looking for cost-effective solutions in construction, manufacturing, and shipping, though they may find limitations in specialized applications.
How Does High-Strength Steel Cable Stand Out?
High-Strength Steel Cables are engineered for demanding applications where tensile strength is critical. Often made with alloyed materials, these cables excel in heavy lifting scenarios, such as mining and offshore operations. Buyers should consider factors like the cable’s weight-to-strength ratio and specific certification for heavy-duty use. While they provide superior durability and can reduce overall weight, the higher cost and potential need for specialized suppliers may be drawbacks.
What Makes Stainless Steel Cable a Preferred Choice?
Stainless Steel Cables offer excellent corrosion resistance, making them ideal for marine and food industry applications. Their aesthetic finish also appeals to architectural projects. Buyers should assess the grade of stainless steel used, as this impacts both durability and cost. Although these cables have a longer lifespan and require less maintenance, the initial investment is higher, which may deter budget-conscious buyers.
Why Consider Plastic Coated Steel Cable?
Plastic Coated Steel Cables feature an additional layer of plastic, enhancing safety and grip, making them suitable for applications such as playgrounds and safety barriers. When purchasing, buyers should consider the type of plastic used and its temperature tolerance. While these cables provide increased safety and a variety of colors for aesthetic appeal, they may be less durable under extreme conditions, which can limit their use in harsh environments.
What are the Key Features of Wire Rope?
Wire Rope is characterized by its construction from multiple wires twisted together, providing flexibility and a high load capacity. This type is commonly used in cranes, elevators, and other heavy machinery. Buyers should evaluate the rope’s diameter, construction method, and breaking strength. While wire ropes offer significant load-bearing capabilities, they require regular maintenance to prevent wear, which is an essential consideration for long-term use.
Related Video: Stainless steel wire manufacturing
Key Industrial Applications of steel cable manufacturer
Industry/Sector | Specific Application of Steel Cable Manufacturer | Value/Benefit for the Business | Key Sourcing Considerations for this Application |
---|---|---|---|
Construction | Structural Support and Lifting Systems | Enhanced safety and reliability in lifting heavy materials | Compliance with local regulations, load capacity requirements |
Mining | Hoisting and Transporting Materials | Increased efficiency and reduced downtime in material handling | Durability in harsh environments, resistance to wear and tear |
Marine and Offshore | Mooring and Towing Solutions | Improved operational safety and reduced risk of accidents | Corrosion resistance, suitable certifications for marine use |
Telecommunications | Cable Management for Data Transmission | Reliable connectivity and reduced signal loss | Compatibility with existing infrastructure, tensile strength |
Energy | Wind and Solar Energy Installation Support | Enhanced structural integrity and reliability of installations | Compliance with energy sector standards, environmental impact assessments |
How is Steel Cable Used in Construction Projects?
In the construction industry, steel cables are integral for structural support and lifting systems. They are utilized in cranes and other lifting equipment to safely elevate heavy materials, ensuring that projects adhere to strict safety standards. For international buyers, particularly from regions like Africa and South America, sourcing steel cables that meet local regulatory requirements is crucial. Additionally, understanding load capacity and environmental factors can help mitigate risks associated with construction delays.
What Role Does Steel Cable Play in the Mining Sector?
Steel cables are essential in the mining sector for hoisting and transporting materials from deep underground. They facilitate the efficient movement of ore and waste, significantly reducing operational downtime. Buyers from the Middle East and Europe should prioritize cables that offer exceptional durability and resistance to abrasion, given the harsh conditions of mining environments. Evaluating the specifications related to tensile strength and flexibility can help ensure that the selected cables can withstand demanding operational conditions.
How Do Steel Cables Enhance Marine and Offshore Operations?
In marine and offshore industries, steel cables are vital for mooring and towing applications. They provide the necessary strength to secure vessels and facilitate safe towing operations, thus minimizing the risk of accidents at sea. For international B2B buyers, especially in regions like Africa, it is important to source cables that are resistant to corrosion and comply with industry certifications for marine use. This ensures the longevity and reliability of the cables under challenging environmental conditions.
How is Steel Cable Essential for Telecommunications Infrastructure?
In the telecommunications sector, steel cables play a crucial role in cable management systems that support data transmission. They help maintain the integrity and reliability of connections, reducing the risk of signal loss. Buyers in Europe and South America should focus on sourcing cables that are compatible with existing infrastructure and meet specific tensile strength requirements. Additionally, understanding the installation environment and potential stress factors can help in selecting the right cable solutions.
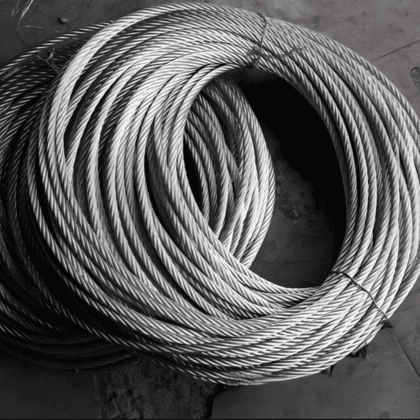
A stock image related to steel cable manufacturer.
Why are Steel Cables Important for Energy Sector Installations?
Steel cables are used extensively in the energy sector, particularly in wind and solar energy installations, for structural support. They enhance the integrity and reliability of these installations, ensuring they can withstand environmental challenges. For international buyers, especially from emerging markets, it is vital to consider compliance with energy sector standards and conduct environmental impact assessments. This proactive approach can lead to more sustainable and efficient energy solutions.
Related Video: SWA Cable – Steel Wire Armoured
3 Common User Pain Points for ‘steel cable manufacturer’ & Their Solutions
Scenario 1: Quality Assurance Challenges in Steel Cable Procurement
The Problem:
International buyers often face significant challenges when it comes to ensuring the quality and reliability of steel cables from manufacturers. This is particularly critical for industries like construction and mining, where cable failure can lead to catastrophic safety issues and substantial financial losses. Many buyers report receiving cables that do not meet the promised specifications, leading to project delays and increased costs. The challenge is further compounded by the lack of standardized quality certifications across different regions, especially for buyers in Africa and South America, where local manufacturers may not adhere to international standards.
The Solution:
To mitigate quality assurance issues, buyers should establish a clear set of quality standards based on international benchmarks, such as ISO 9001. Before placing orders, conduct thorough due diligence on potential suppliers, including checking for ISO certifications and reviewing their production processes. Additionally, consider engaging third-party inspection services to perform quality checks at various stages of the manufacturing process. This proactive approach not only helps ensure that the steel cables meet the required specifications but also builds a long-term relationship with manufacturers who prioritize quality. Utilizing technology, such as blockchain for supply chain transparency, can further enhance trust in the quality of products being delivered.
Scenario 2: Navigating Complex Import Regulations for Steel Cables
The Problem:
B2B buyers often encounter hurdles related to complex import regulations and tariffs when sourcing steel cables from international manufacturers. This is particularly true for companies in the Middle East and Europe, where varying regulations can lead to unexpected costs and delays at customs. Buyers may find themselves unprepared for stringent documentation requirements or specific product certifications needed to comply with local laws, resulting in shipment holds and potential penalties.
The Solution:
To navigate these complexities, buyers should invest time in understanding the import regulations specific to their country and industry. This includes familiarizing themselves with tariff codes, necessary documentation, and compliance requirements for steel cables. Engaging with a customs broker or a logistics provider that specializes in international trade can provide valuable insights and assistance in managing these processes. Additionally, building strong relationships with suppliers who are experienced in exporting to the buyer’s region can facilitate smoother transactions. They can offer guidance on the paperwork and certifications required, helping to streamline the import process and avoid costly delays.
Scenario 3: Sourcing Custom Steel Cable Solutions for Specific Applications
The Problem:
Many industries require customized steel cable solutions tailored to specific applications, such as marine engineering or heavy lifting. However, buyers frequently struggle to find manufacturers who can provide bespoke products that meet their unique specifications. This challenge is exacerbated by the lack of communication between buyers and manufacturers, leading to misinterpretations of requirements and resulting in unsuitable products that do not perform as needed.
The Solution:
To effectively source custom steel cable solutions, buyers should start by clearly defining their requirements, including load capacity, length, diameter, and environmental conditions the cables will face. Detailed specifications should be shared with potential manufacturers from the outset. Engaging in direct communication through video conferencing or site visits can help ensure that both parties have a clear understanding of the project requirements. Additionally, consider conducting a pilot test with a small batch of cables before committing to larger orders. This allows for adjustments based on performance feedback, ensuring that the final product meets the specific needs of the application. Collaborating with manufacturers known for their R&D capabilities can also result in innovative solutions tailored to unique challenges.
Strategic Material Selection Guide for steel cable manufacturer
When selecting materials for steel cable manufacturing, understanding the properties, advantages, and limitations of each option is crucial for international B2B buyers. This guide explores four common materials used in steel cable production, focusing on their performance characteristics, application impacts, and specific considerations for buyers from diverse regions, including Africa, South America, the Middle East, and Europe.
What Are the Key Properties of Carbon Steel in Steel Cable Manufacturing?
Carbon steel is one of the most widely used materials in steel cable manufacturing due to its excellent tensile strength and ductility. It typically has a temperature rating that can withstand moderate to high temperatures, making it suitable for various applications. The corrosion resistance of carbon steel can be enhanced through galvanization or coatings, which is vital for applications exposed to harsh environments.
Pros: Carbon steel cables are durable and cost-effective, making them a popular choice for construction and industrial applications. Their high strength-to-weight ratio allows for efficient load-bearing capabilities.
Cons: However, carbon steel is susceptible to corrosion if not properly treated, which can lead to reduced lifespan in corrosive environments. Additionally, the manufacturing complexity can increase with the need for protective coatings.
Impact on Application: Carbon steel cables are commonly used in construction, mining, and transportation sectors, where high strength and reliability are essential.
How Does Stainless Steel Compare in Terms of Performance and Durability?
Stainless steel is another prevalent material in steel cable manufacturing, known for its exceptional corrosion resistance and aesthetic appeal. It can handle a wide range of temperatures and pressures, making it suitable for diverse applications, including marine and chemical industries.
Pros: The primary advantage of stainless steel cables is their longevity and resistance to rust and corrosion, which significantly reduces maintenance costs over time. They are also highly durable, making them suitable for high-stress applications.
Cons: The main drawback is the higher cost compared to carbon steel, which can impact budget-sensitive projects. Additionally, stainless steel cables may be more challenging to work with during manufacturing due to their toughness.
Impact on Application: Stainless steel cables are ideal for applications in corrosive environments, such as offshore oil rigs and chemical plants, where durability and resistance to environmental factors are critical.
What Are the Benefits of Using Galvanized Steel for Steel Cables?
Galvanized steel, which involves coating carbon steel with a layer of zinc, offers a balance between cost and performance. This coating provides significant corrosion resistance, extending the life of the cable in outdoor or humid conditions.
Pros: The key advantage of galvanized steel cables is their affordability combined with enhanced corrosion resistance. They are widely used in construction and outdoor applications where exposure to moisture is a concern.
Cons: However, the galvanization process can add to manufacturing complexity and may not provide the same level of durability as stainless steel in extreme conditions. Over time, the zinc coating can wear off, exposing the underlying steel to corrosion.
Impact on Application: Galvanized steel cables are commonly used in agricultural settings, construction, and general outdoor applications, where cost-effectiveness and moderate durability are required.
Why Consider Alloy Steel for High-Performance Applications?
Alloy steel, which combines carbon steel with other elements like chromium, nickel, or molybdenum, is designed for high-performance applications. This material offers superior strength and toughness, making it suitable for heavy-duty applications.
Pros: The primary advantage of alloy steel cables is their high strength and resistance to wear and fatigue, making them ideal for extreme conditions. They can also be tailored for specific applications through the selection of alloying elements.
Cons: The main disadvantage is the higher cost and complexity of manufacturing. Alloy steels may also require specialized knowledge for proper handling and processing.
Impact on Application: Alloy steel cables are often used in heavy machinery, aerospace, and automotive applications, where performance and safety are paramount.
Summary Table of Material Selection for Steel Cable Manufacturing
Material | Typical Use Case for steel cable manufacturer | Key Advantage | Key Disadvantage/Limitation | Relative Cost (Low/Med/High) |
---|---|---|---|---|
Carbon Steel | Construction, mining, transportation | High strength-to-weight ratio | Susceptible to corrosion | Medium |
Stainless Steel | Marine, chemical industries | Exceptional corrosion resistance | Higher cost | High |
Galvanized Steel | Outdoor construction, agriculture | Affordable with moderate corrosion resistance | Coating can wear off | Low |
Alloy Steel | Heavy machinery, aerospace | Superior strength and toughness | Higher cost and manufacturing complexity | High |
This strategic material selection guide provides international B2B buyers with essential insights into the properties and applications of various materials used in steel cable manufacturing, allowing for informed decision-making tailored to specific project requirements and regional considerations.
In-depth Look: Manufacturing Processes and Quality Assurance for steel cable manufacturer
What Are the Key Stages in the Manufacturing Process of Steel Cables?
The manufacturing of steel cables involves several critical stages that ensure the final product meets industry demands for strength, durability, and safety. Understanding these processes can help B2B buyers make informed decisions when selecting suppliers.
Material Preparation
The first stage involves the selection and preparation of raw materials, typically high-carbon steel wire. The steel undergoes processes such as drawing, where it is pulled through a series of dies to achieve the desired diameter and tensile strength. Buyers should inquire about the source of the steel and its composition, as these factors significantly influence the quality of the final cable.
Forming Techniques
Once the material is prepared, it is subjected to various forming techniques. The most common methods include:
-
Stranding: In this process, individual wires are twisted together to form strands. This enhances flexibility and strength. B2B buyers should look for manufacturers that use advanced stranding techniques to ensure uniformity and minimize defects.
-
Laying Up: Strands are then laid together in a specific configuration, often in a helical manner, to form the cable. The choice of lay and the number of strands can affect the cable’s performance in different applications.
Assembly and Finishing
The assembly phase involves the application of additional components, such as coatings or sheathing, to enhance corrosion resistance and durability. Common finishing processes include:
-
Galvanization: This involves coating the steel with zinc to prevent rust. Buyers should ask about the galvanization process to ensure it meets their specific environmental and operational needs.
-
Heat Treatment: This process can improve the mechanical properties of the cable, increasing its strength and fatigue resistance. Manufacturers should provide documentation on any heat treatment methods used.
How Is Quality Assurance Integrated Throughout the Manufacturing Process?
Quality assurance is integral to the manufacturing of steel cables and involves multiple checkpoints and standards that ensure product reliability and compliance.
What International Standards Should B2B Buyers Be Aware Of?
International standards, such as ISO 9001, provide a framework for quality management systems. These standards help manufacturers ensure consistent quality and customer satisfaction. Additionally, industry-specific certifications like CE for European markets and API for oil and gas applications are crucial for B2B buyers to verify.
What Are the Key QC Checkpoints in Steel Cable Manufacturing?
Quality control (QC) is typically divided into several critical checkpoints:
-
Incoming Quality Control (IQC): This involves inspecting raw materials upon arrival. B2B buyers should request documentation of IQC practices to ensure that only high-quality materials are used.
-
In-Process Quality Control (IPQC): During the manufacturing process, various parameters such as diameter, tensile strength, and surface quality are monitored. Buyers should inquire about the frequency and methods of these inspections.
-
Final Quality Control (FQC): At this stage, the finished products are subjected to rigorous testing. Common tests include tensile tests, fatigue tests, and corrosion resistance assessments. B2B buyers should ask for detailed reports of FQC to ensure that the products meet their specifications.
What Testing Methods Are Commonly Used in Steel Cable Quality Assurance?
Various testing methods are employed to validate the quality of steel cables:
-
Tensile Testing: This measures the maximum load a cable can bear before breaking. It’s essential for determining the cable’s strength and suitability for specific applications.
-
Fatigue Testing: This simulates the conditions the cable will face over time, assessing how it withstands repeated loading cycles.
-
Corrosion Testing: This evaluates the cable’s resistance to environmental factors. Buyers should ensure that manufacturers perform such tests, especially for cables intended for harsh environments.
How Can B2B Buyers Verify a Supplier’s Quality Control Processes?
To establish confidence in a supplier’s QC processes, B2B buyers can take several actionable steps:
-
Request Documentation: Buyers should ask for quality management system documentation, including ISO certifications and QC reports. This provides insight into the manufacturer’s commitment to quality.
-
Conduct Audits: On-site audits allow buyers to assess the manufacturing environment, equipment, and QC practices firsthand. This is particularly important when dealing with suppliers in regions like Africa or South America, where standards may vary.
-
Engage Third-Party Inspectors: Utilizing independent inspection services can provide an unbiased assessment of the manufacturer’s capabilities and compliance with international standards.
What Are the Quality Control Nuances for International B2B Buyers?
B2B buyers from different regions may face unique challenges in ensuring quality. For instance:
-
Cultural and Regulatory Differences: Understanding local regulations and standards in regions like the Middle East or Europe can help buyers navigate compliance issues. It’s advisable to work with suppliers familiar with these regulations.
-
Supply Chain Considerations: Shipping and logistics can introduce risks to product quality. Buyers should discuss packaging and handling procedures with suppliers to mitigate these risks.
-
After-Sales Support: Quality assurance doesn’t end at delivery. Buyers should evaluate the manufacturer’s commitment to after-sales support, including warranties and service agreements, to ensure ongoing product reliability.
Conclusion
Understanding the manufacturing processes and quality assurance protocols of steel cable manufacturers is essential for international B2B buyers. By focusing on the key stages of production, relevant international standards, and effective verification methods, buyers can make informed decisions that align with their operational needs and regulatory requirements. Engaging with suppliers who prioritize quality assurance will ultimately lead to stronger business partnerships and successful project outcomes.
Practical Sourcing Guide: A Step-by-Step Checklist for ‘steel cable manufacturer’
In the complex landscape of international procurement, sourcing a reliable steel cable manufacturer is critical for businesses across various sectors. This guide provides a structured checklist to help B2B buyers navigate the sourcing process effectively, ensuring they select a manufacturer that meets their technical, logistical, and financial needs.
Step 1: Define Your Technical Specifications
Before reaching out to potential suppliers, clearly outline your requirements. Consider factors such as cable type, diameter, tensile strength, and any specific industry standards that must be met. This clarity will aid in communicating your needs and evaluating suppliers’ capabilities.
Step 2: Conduct Market Research
Understanding the market landscape is essential. Research potential manufacturers in regions of interest, such as Africa, South America, the Middle East, and Europe. Use online directories, industry associations, and trade shows to identify key players and gather insights on pricing, production capabilities, and market trends.
Step 3: Evaluate Potential Suppliers
Before committing, vet suppliers thoroughly. Request company profiles, case studies, and references from buyers in a similar industry or region. Look for:
– Reputation: Check reviews and testimonials to gauge reliability.
– Experience: Ensure they have a proven track record in manufacturing steel cables for your specific application.
Step 4: Verify Supplier Certifications
Ensure that the manufacturers you are considering hold relevant certifications. Compliance with international standards such as ISO 9001 for quality management and ISO 14001 for environmental management can indicate a commitment to quality and sustainability. Ask for documentation and verify their legitimacy.
Step 5: Assess Production Capabilities
Evaluate the manufacturer’s production capabilities to ensure they can meet your demand. Inquire about:
– Production capacity: Can they handle your order volume?
– Technology and equipment: Are they using modern manufacturing techniques that ensure quality and efficiency?
Step 6: Request Samples and Conduct Testing
Before finalizing any contracts, request samples of the steel cables. Testing these samples against your technical specifications will confirm their suitability for your intended application. Look for:
– Durability: Ensure the cables can withstand the required stress and environmental conditions.
– Compliance: Verify that the samples meet the necessary industry standards.
Step 7: Discuss Payment Terms and Logistics
Lastly, negotiate payment terms and logistics with your chosen supplier. Understand the total cost of procurement, including shipping, duties, and any potential tariffs. Discuss timelines for production and delivery, ensuring that they align with your project schedules.
By following this checklist, B2B buyers can make informed decisions when sourcing steel cable manufacturers, ultimately leading to successful partnerships that enhance their operational capabilities.
Comprehensive Cost and Pricing Analysis for steel cable manufacturer Sourcing
What Are the Key Cost Components in Steel Cable Manufacturing?
When sourcing steel cables, understanding the cost structure is critical for international buyers. The primary components influencing the total cost include:
-
Materials: The type and quality of steel used significantly impact costs. High-grade steel with certifications such as ISO or ASTM will cost more but will offer better durability and performance. Raw material prices can fluctuate based on global market trends, so keeping an eye on these changes is crucial for budgeting.
-
Labor: Labor costs vary significantly by region. In countries with lower wage standards, labor can represent a smaller portion of the overall cost. However, skilled labor for specialized manufacturing processes may require a premium.
-
Manufacturing Overhead: This includes costs related to factory maintenance, utilities, and equipment depreciation. Efficient manufacturing processes can help reduce these overheads, making it essential to choose suppliers with advanced technology and streamlined operations.
-
Tooling: The initial setup for manufacturing steel cables requires substantial investment in tooling. Custom tooling for specific cable designs can add to this cost, but it may be necessary for unique applications.
-
Quality Control (QC): Rigorous quality control processes ensure that the cables meet industry standards. While these processes add to the overall cost, they are essential for minimizing defects and ensuring customer satisfaction.
-
Logistics: Transportation and shipping costs can vary widely based on distance, mode of transport, and the chosen Incoterms. Buyers should consider these logistics costs as part of their total cost of ownership (TCO).
-
Margin: Finally, the manufacturer’s profit margin will influence the final price. Understanding the typical margins in the region can help buyers gauge whether a quoted price is reasonable.
What Factors Influence Pricing for Steel Cable Manufacturing?
Several price influencers come into play when negotiating with steel cable manufacturers:
-
Volume and Minimum Order Quantity (MOQ): Bulk orders typically attract discounts. Understanding the MOQ can help buyers negotiate better pricing, especially if they can commit to larger volumes.
-
Specifications and Customization: Custom cables designed for specific applications may incur additional costs. Buyers should clarify their requirements upfront to get accurate pricing.
-
Material Quality and Certifications: Higher quality materials and recognized certifications can increase prices but also ensure better performance and longevity. Buyers should weigh these factors against their budget constraints.
-
Supplier Factors: The supplier’s location, reputation, and production capacity can all influence pricing. Established suppliers with a track record of reliability may charge more but offer peace of mind.
-
Incoterms: The chosen Incoterms can affect shipping costs and responsibilities. Understanding terms like FOB (Free on Board) or CIF (Cost, Insurance, and Freight) can lead to better negotiation outcomes.
How Can International Buyers Optimize Their Sourcing Strategy for Steel Cables?
For international B2B buyers, particularly in regions such as Africa, South America, the Middle East, and Europe, here are actionable tips for optimizing sourcing:
-
Negotiate Wisely: Always enter negotiations with a clear understanding of your budget and the pricing structure. Leverage your purchasing volume to negotiate better terms.
-
Focus on Cost-Efficiency: Assess the total cost of ownership rather than just the initial purchase price. Consider factors like durability, maintenance, and potential downtime when evaluating options.
-
Understand Pricing Nuances: Familiarize yourself with local market conditions and currency fluctuations that may affect pricing. This knowledge can provide leverage during negotiations.
-
Build Relationships with Suppliers: Establishing long-term relationships with manufacturers can lead to better pricing and terms over time. Regular communication helps in understanding their capabilities and constraints.
-
Research Local Regulations: Different regions may have specific regulations regarding steel cables. Ensuring compliance can prevent costly delays and penalties.
In conclusion, a comprehensive understanding of the cost structure and pricing dynamics in steel cable manufacturing is essential for international buyers. By leveraging these insights, B2B buyers can make informed decisions that align with their operational needs and budgetary constraints.
Alternatives Analysis: Comparing steel cable manufacturer With Other Solutions
Understanding the Importance of Alternatives in Steel Cable Manufacturing
In the competitive landscape of industrial solutions, B2B buyers must evaluate various options to ensure they select the most suitable materials and technologies for their projects. While steel cables are a common choice due to their strength and durability, it is essential to consider alternative solutions that may offer specific benefits depending on the application. This analysis will compare steel cable manufacturing against two viable alternatives: synthetic ropes and fiber cables.
Comparison Table of Steel Cable Manufacturer and Alternatives
Comparison Aspect | Steel Cable Manufacturer | Synthetic Ropes | Fiber Cables |
---|---|---|---|
Performance | High tensile strength; suitable for heavy loads | Good for moderate loads; lightweight | Excellent for data transmission; lower load capacity |
Cost | Generally higher initial investment | Lower initial cost; long-term durability varies | Moderate cost; potentially high installation cost |
Ease of Implementation | Requires specialized equipment for installation | Easy to handle; minimal tools needed | Can require specialized training for installation |
Maintenance | Regular inspections needed; susceptible to corrosion | Low maintenance; resistant to environmental factors | Minimal maintenance; check for wear on connections |
Best Use Case | Heavy-duty applications like construction and mining | Marine applications, outdoor sports, and rescue operations | Telecommunications and data networks |
What Are the Pros and Cons of Synthetic Ropes?
Synthetic Ropes are an increasingly popular alternative to steel cables. They are lighter and easier to handle, which can reduce labor costs during installation. Additionally, synthetic ropes are resistant to moisture, UV radiation, and abrasion, making them ideal for outdoor and marine applications. However, they typically cannot handle the same weight loads as steel cables, which limits their use in heavy-duty scenarios. For B2B buyers in sectors such as shipping or outdoor equipment, synthetic ropes may provide a cost-effective solution that meets specific operational needs.
How Do Fiber Cables Compare to Steel Cable Manufacturing?
Fiber Cables serve a different purpose compared to steel cables, primarily focusing on data transmission rather than load-bearing capabilities. Their lightweight nature and superior flexibility make them ideal for telecommunications and networking applications. The installation process can be more complex and may require specialized skills, potentially increasing upfront costs. However, fiber cables offer minimal maintenance and are less prone to wear and tear over time. For businesses in sectors like telecommunications or IT, fiber cables can be an excellent choice, particularly where speed and data integrity are paramount.
Conclusion: How to Choose the Right Solution for Your Needs
Selecting the right solution between steel cables, synthetic ropes, and fiber cables depends on several factors, including the specific application, budget constraints, and long-term operational goals. B2B buyers should carefully assess the performance requirements, cost implications, and maintenance needs associated with each option. By aligning the chosen solution with their operational demands, buyers can enhance efficiency and ensure the longevity of their investments. Ultimately, understanding the unique advantages and limitations of each alternative will empower businesses to make informed decisions that drive success in their respective industries.
Essential Technical Properties and Trade Terminology for steel cable manufacturer
What Are the Essential Technical Properties of Steel Cables?
When selecting steel cables for industrial applications, understanding their technical properties is crucial for ensuring performance, safety, and compliance with industry standards. Here are several key specifications that B2B buyers should consider:
1. Material Grade: Why Is It Important?
Steel cables are often classified by their material grade, which indicates the quality and strength of the steel used. Common grades include AISI 304 and AISI 316 for stainless steel cables, which offer different levels of corrosion resistance and tensile strength. For buyers in industries like construction or marine applications, choosing the correct material grade is essential for durability and safety.
2. Diameter: How Does It Affect Performance?
The diameter of steel cables directly influences their load-bearing capacity and flexibility. Thicker cables can carry heavier loads but may be less flexible, while thinner cables are easier to handle but may have lower strength. Buyers should assess the specific requirements of their application to determine the optimal diameter, balancing load capacity with handling ease.
3. Tolerance: Why Should Buyers Pay Attention?
Tolerance refers to the permissible limits of variation in the dimensions of the cable. High tolerance levels ensure that cables fit precisely within their intended applications, reducing the risk of failure. For international buyers, understanding tolerance specifications is crucial for compliance with local regulations and industry standards.
4. Breaking Strength: What Does It Indicate?
Breaking strength is the maximum load a cable can withstand before failing. This property is critical for safety and performance assessments. Buyers should always verify the breaking strength against the anticipated loads in their applications to ensure that the selected cable will perform reliably.
5. Lay Length and Direction: What Do They Mean?
Lay length refers to the distance over which the strands of the cable are twisted together, while lay direction indicates whether the strands are twisted to the left or right. These factors affect the cable’s flexibility and overall performance. Buyers should consider lay length and direction based on application requirements, particularly in environments where bending or twisting is common.
What Are Common Trade Terminology Terms in the Steel Cable Industry?
Understanding trade terminology is essential for effective communication and negotiation in the B2B steel cable market. Here are some common terms that buyers should familiarize themselves with:
1. OEM (Original Equipment Manufacturer): What Role Does It Play?
OEM refers to companies that manufacture products that are marketed by another company. In the steel cable industry, an OEM may produce cables that are sold under a different brand name. For buyers, working with OEMs can often lead to cost savings and better customization options.
2. MOQ (Minimum Order Quantity): Why Is It Relevant?
MOQ is the minimum quantity of units that a supplier is willing to sell. Understanding MOQ is vital for international buyers, as it can impact inventory management and cash flow. Buyers should negotiate MOQs to align with their project needs without overcommitting resources.
3. RFQ (Request for Quotation): How Does It Facilitate Procurement?
An RFQ is a document sent to suppliers requesting pricing and other details for specific products. For B2B buyers, issuing an RFQ is a crucial step in the procurement process, enabling them to compare offers and ensure they are getting the best value for their investment.
4. Incoterms: What Are They and Why Do They Matter?
Incoterms are international commercial terms that define the responsibilities of buyers and sellers regarding shipping, insurance, and tariffs. Familiarity with Incoterms is essential for international transactions, as they clarify costs and risks associated with transporting steel cables across borders.
5. Lead Time: What Should Buyers Expect?
Lead time refers to the amount of time from when an order is placed until it is delivered. Understanding lead time is important for buyers to manage project timelines effectively. Buyers should inquire about lead times during negotiations to ensure their supply chain remains uninterrupted.
By grasping these essential technical properties and trade terms, international B2B buyers can make informed decisions when sourcing steel cables, ultimately enhancing their operational efficiency and reducing risks.
Navigating Market Dynamics and Sourcing Trends in the steel cable manufacturer Sector
What Are the Key Market Dynamics Driving the Steel Cable Manufacturing Sector?
The global steel cable manufacturing market is influenced by a variety of factors that international B2B buyers must navigate. One of the primary drivers is the rising demand from construction and infrastructure projects, particularly in developing regions such as Africa and South America. These areas are experiencing rapid urbanization and economic growth, necessitating the use of high-quality steel cables for construction, telecommunications, and energy sectors.
Emerging technologies also play a significant role in shaping the market. Innovations such as automation and advanced manufacturing techniques are reducing production costs and enhancing product quality. Additionally, the integration of Industry 4.0 technologies—such as IoT and AI—enables manufacturers to streamline operations and improve supply chain visibility. For B2B buyers, understanding these technological advancements can lead to better sourcing decisions and partnerships.
Another important trend is the increasing focus on regional sourcing. With geopolitical uncertainties and supply chain disruptions becoming more prevalent, buyers are looking to local manufacturers or regional suppliers to mitigate risks. This trend is particularly evident in Europe, where companies seek to balance cost-effectiveness with reliability. For buyers in Africa and South America, leveraging local suppliers can also foster economic development within their regions.
How Can Sustainability and Ethical Sourcing Impact Your Steel Cable Supply Chain?
Sustainability is no longer a peripheral concern; it is central to the operations of steel cable manufacturers. The environmental impact of steel production, particularly carbon emissions, has led many companies to adopt greener practices. B2B buyers should prioritize suppliers that utilize recycled materials or renewable energy sources in their manufacturing processes.
The importance of ethical supply chains cannot be overstated. Buyers should seek manufacturers that adhere to international labor standards and maintain transparency in their sourcing practices. Certifications such as ISO 14001 (Environmental Management) and ISO 45001 (Occupational Health and Safety) indicate a commitment to sustainable and ethical practices. By partnering with responsible manufacturers, buyers not only enhance their brand reputation but also contribute to a more sustainable industry.
The trend toward ‘green’ materials is also gaining traction. Buyers are encouraged to inquire about the availability of eco-friendly steel cables, which are produced with lower environmental impact. This shift not only meets consumer demand for sustainability but can also lead to cost savings through energy-efficient practices.
What Is the Brief Evolution of the Steel Cable Manufacturing Industry?
The steel cable manufacturing industry has evolved significantly over the past century, transitioning from manual processes to highly automated and technologically advanced production lines. Initially, steel cables were primarily used in construction and shipping. However, with advancements in metallurgy and engineering, the applications have expanded to include telecommunications, energy transmission, and even aerospace.
In recent decades, globalization has further transformed the industry, allowing manufacturers to access a broader market while also facing increased competition. The rise of digital technologies has also reshaped operational efficiencies and customer engagement. As the industry continues to adapt to changing consumer needs and environmental regulations, it remains crucial for international B2B buyers to stay informed about these trends to make strategic sourcing decisions.
Frequently Asked Questions (FAQs) for B2B Buyers of steel cable manufacturer
-
How do I ensure quality when sourcing steel cables from manufacturers?
To ensure quality, start by verifying the manufacturer’s certifications, such as ISO 9001 or industry-specific standards. Request samples to assess the material’s strength and durability. It’s also crucial to review customer testimonials and case studies. Engage in quality assurance measures by establishing clear specifications and conducting regular audits or inspections during the production process. For international buyers, consider third-party inspection services to provide an unbiased evaluation before shipment. -
What are the common customization options available for steel cables?
Most steel cable manufacturers offer customization in terms of diameter, length, construction type (e.g., wire rope, strand), and coating (e.g., galvanized, PVC). Some manufacturers may also provide bespoke solutions tailored to specific applications, such as marine, construction, or industrial uses. When discussing customization, be clear about your requirements and ensure the manufacturer can meet your specifications. Request detailed documentation to confirm the capabilities of the manufacturer. -
What is the minimum order quantity (MOQ) for steel cables?
The MOQ can vary significantly among manufacturers, often depending on the type and specifications of the steel cables. Generally, MOQs can range from 100 meters to several tons. It’s important to discuss your needs with potential suppliers early in the negotiation process. If your order falls below the MOQ, inquire about potential options for smaller orders or consider consolidating orders with other buyers to meet the manufacturer’s requirements. -
What payment terms should I expect when sourcing steel cables internationally?
Payment terms typically include options such as advance payments, letters of credit, or payment upon delivery. Many manufacturers may request a deposit (usually 30-50%) before production begins, with the balance due upon shipment. It’s advisable to clarify payment terms upfront and ensure they align with your financial capabilities. Additionally, consider using secure payment methods to protect against fraud, especially in international transactions. -
How can I vet potential steel cable suppliers effectively?
To vet suppliers, start by researching their reputation through online reviews, industry forums, and referrals from other businesses. Assess their production capabilities, lead times, and experience in exporting to your region. Request references and case studies to evaluate their track record with similar clients. Additionally, visiting the manufacturing facility, if possible, can provide valuable insights into their operational standards and quality control processes. -
What are the key logistics considerations when importing steel cables?
Logistics considerations include shipping methods (sea, air, or land), customs clearance, and delivery timelines. Choose a shipping method based on your budget and urgency. Understand the import regulations in your country, including tariffs and taxes, to avoid unexpected costs. Collaborate with a reliable freight forwarder who is experienced in handling steel products to streamline the shipping process and ensure compliance with all regulations. -
What should I know about warranties and after-sales support for steel cables?
Warranties for steel cables can vary widely, typically covering defects in material and workmanship for a specified period. Always request warranty information before finalizing your purchase. Additionally, inquire about after-sales support, including installation guidance and technical assistance. A reputable manufacturer should provide comprehensive support to address any issues that may arise post-purchase, ensuring you have the resources needed for optimal product performance. -
How do I manage risks associated with international sourcing of steel cables?
Managing risks involves conducting thorough due diligence on suppliers, including financial stability and production practices. Establish clear contracts that outline terms, delivery schedules, and quality expectations to mitigate misunderstandings. Consider purchasing insurance to cover potential losses during transit. Additionally, maintain open communication with your suppliers to quickly address any emerging issues, and be prepared with contingency plans to handle delays or product discrepancies.
Important Disclaimer & Terms of Use
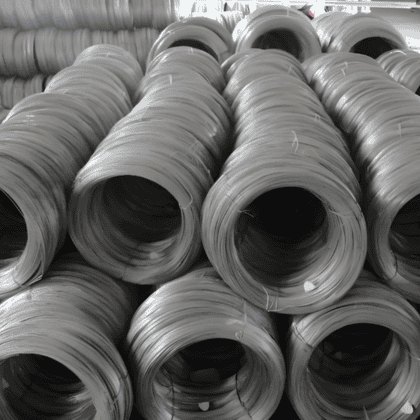
A stock image related to steel cable manufacturer.
⚠️ Important Disclaimer
The information provided in this guide, including content regarding manufacturers, technical specifications, and market analysis, is for informational and educational purposes only. It does not constitute professional procurement advice, financial advice, or legal advice.
While we have made every effort to ensure the accuracy and timeliness of the information, we are not responsible for any errors, omissions, or outdated information. Market conditions, company details, and technical standards are subject to change.
B2B buyers must conduct their own independent and thorough due diligence before making any purchasing decisions. This includes contacting suppliers directly, verifying certifications, requesting samples, and seeking professional consultation. The risk of relying on any information in this guide is borne solely by the reader.
Strategic Sourcing Conclusion and Outlook for steel cable manufacturer
In the competitive landscape of steel cable manufacturing, the importance of strategic sourcing cannot be overstated. By leveraging a well-defined sourcing strategy, international B2B buyers can optimize supply chain efficiency, reduce costs, and enhance product quality. Key takeaways emphasize the necessity of evaluating suppliers not just on price but also on factors like reliability, production capacity, and compliance with international standards. Buyers are encouraged to consider suppliers who demonstrate sustainability practices, as this not only aligns with global trends but also appeals to eco-conscious consumers.
How can international buyers navigate the complexities of sourcing steel cables effectively? Establishing strong relationships with manufacturers across Africa, South America, the Middle East, and Europe can lead to mutually beneficial partnerships. Engaging in regular communication and conducting thorough due diligence will ensure that you select the right partners for your business needs.
Looking ahead, the steel cable industry is poised for growth, driven by innovations and increasing demand across various sectors. As you explore sourcing options, remain agile and open to new opportunities that align with your strategic objectives. Embrace the future of steel cable manufacturing by making informed, data-driven decisions that propel your business forward in a global marketplace.