The Ultimate Guide to Sandwich Panel Manufacturer (2025)
Introduction: Navigating the Global Market for sandwich panel manufacturer
Navigating the complexities of sourcing from a diverse array of sandwich panel manufacturers can be a daunting task for international B2B buyers, especially those based in Africa, South America, the Middle East, and Europe. With the increasing demand for sustainable and efficient building materials, understanding how to effectively evaluate suppliers and their offerings is crucial. This guide aims to simplify the procurement process by providing detailed insights into various types of sandwich panels, their applications across different industries, and the critical factors to consider when selecting a reliable manufacturer.
Throughout this comprehensive resource, we will delve into essential topics such as the different materials used in sandwich panel production, the advantages and disadvantages of each type, and how they can be tailored to meet specific project requirements. Additionally, we will cover key aspects of supplier vetting, including certifications, production capacity, and customer service quality. Understanding the cost structures associated with sandwich panels, as well as potential hidden costs in international shipping and tariffs, will also be a focal point of this guide.
By equipping B2B buyers with actionable insights and a structured approach to sourcing sandwich panels, this guide will empower you to make informed purchasing decisions that align with your business goals. Whether you’re looking to enhance your construction projects in Egypt, Indonesia, or elsewhere, the information presented here will help you navigate the global market effectively, ensuring that you select the best sandwich panel manufacturer for your needs.
Understanding sandwich panel manufacturer Types and Variations
Type Name | Key Distinguishing Features | Primary B2B Applications | Brief Pros & Cons for Buyers |
---|---|---|---|
EPS (Expanded Polystyrene) | Lightweight, cost-effective, good thermal insulation | Cold storage, roofing, wall cladding | Pros: Affordable, versatile; Cons: Lower fire resistance than others. |
PIR (Polyisocyanurate) | Higher thermal resistance, fire-resistant, rigid core | Industrial buildings, refrigerated units | Pros: Excellent insulation, fire safety; Cons: Higher cost than EPS. |
PUR (Polyurethane) | Superior thermal performance, flexible design options | Commercial buildings, clean rooms | Pros: Very high insulation value; Cons: More expensive, limited recyclability. |
Mineral Wool | Non-combustible, soundproofing capabilities, eco-friendly | Industrial and commercial applications | Pros: Fire-resistant, sustainable; Cons: Heavier, potential for moisture absorption. |
Aluminum Composite Panels | Durable, aesthetic appeal, weather-resistant | Facades, signage, interior applications | Pros: Lightweight, high visual appeal; Cons: Higher initial investment. |
What Are the Key Characteristics of EPS Sandwich Panels?
EPS (Expanded Polystyrene) sandwich panels are recognized for their lightweight nature and cost-effectiveness, making them a popular choice for various applications, especially in cold storage and roofing. They provide good thermal insulation, which can be crucial in regions with extreme temperatures. When considering EPS panels, buyers should assess their fire resistance, as they may not perform as well under fire conditions compared to other materials. They are suitable for projects with budget constraints but may require additional fireproofing measures.
How Do PIR Sandwich Panels Compare in Terms of Thermal Resistance?
PIR (Polyisocyanurate) sandwich panels are known for their high thermal resistance and fire-resistant properties. This makes them ideal for industrial buildings and refrigerated units where maintaining a stable temperature is crucial. Their rigid core contributes to overall structural integrity. Buyers should evaluate the initial investment against long-term energy savings, as the superior insulation can lead to reduced heating and cooling costs. However, the higher price point may be a consideration for budget-conscious projects.
Why Choose PUR Sandwich Panels for Commercial Applications?
PUR (Polyurethane) sandwich panels offer superior thermal performance and flexible design options, making them suitable for commercial buildings and clean rooms where hygiene and temperature control are paramount. They provide a very high insulation value, which can significantly reduce energy costs over time. However, potential buyers should be aware of the higher costs associated with PUR panels and consider their recyclability, as this can impact sustainability goals.
What Are the Benefits of Using Mineral Wool Sandwich Panels?
Mineral wool sandwich panels are distinguished by their non-combustible nature and excellent soundproofing capabilities, making them an eco-friendly choice for industrial and commercial applications. Their sustainability and fire resistance make them suitable for projects with strict safety regulations. Buyers should consider the weight of mineral wool panels and potential moisture absorption, which could necessitate additional protective measures. These panels are ideal for projects prioritizing safety and environmental responsibility.
When Should You Consider Aluminum Composite Panels?
Aluminum composite panels are known for their durability and aesthetic appeal, making them popular for facades, signage, and interior applications. They are weather-resistant and lightweight, offering a modern look to various structures. However, the initial investment can be higher than other sandwich panel types. Buyers should weigh the long-term benefits of aesthetic and functional durability against the upfront costs, especially for projects where visual impact is a priority.
Related Video: KINDUS – Continuous PUR/PIR Sandwich Panel Production Line
Key Industrial Applications of sandwich panel manufacturer
Industry/Sector | Specific Application of Sandwich Panel Manufacturer | Value/Benefit for the Business | Key Sourcing Considerations for this Application |
---|---|---|---|
Construction | Prefabricated Buildings | Reduced construction time and labor costs | Local regulations, thermal insulation standards |
Cold Storage Facilities | Insulated Cold Rooms | Enhanced energy efficiency and temperature control | Compliance with food safety standards, durability |
Industrial Warehousing | Warehouse Partitioning | Space optimization and operational efficiency | Load-bearing capacity, fire rating certifications |
Clean Rooms | Controlled Environment Facilities | Maintained cleanliness and air quality | Material specifications, ease of installation |
Transportation and Logistics | Mobile Offices and Containers | Portability and rapid setup | Weight limitations, weather resistance |
How Are Sandwich Panels Used in Construction Projects?
In the construction industry, sandwich panels are often employed for prefabricated buildings, offering significant advantages such as reduced construction time and lower labor costs. These panels consist of two outer layers and an insulating core, providing superior thermal insulation that meets various energy efficiency standards. For international buyers, particularly from regions like Africa and South America, it is crucial to consider local building regulations and thermal insulation requirements to ensure compliance and sustainability in construction projects.
What Role Do Sandwich Panels Play in Cold Storage Facilities?
Sandwich panels are essential in the construction of insulated cold rooms, which are vital for preserving perishable goods. Their insulating properties help maintain consistent low temperatures, enhancing energy efficiency and reducing operational costs. B2B buyers in the Middle East and Europe must prioritize compliance with food safety standards and durability when sourcing these panels, as they directly impact the quality of stored products and the facility’s overall performance.
How Can Sandwich Panels Optimize Industrial Warehousing?
In industrial warehousing, sandwich panels are utilized for partitioning spaces, allowing for optimized layouts and improved operational efficiency. These panels can create separate zones for different storage needs without compromising structural integrity. Buyers from Europe and Africa should focus on the panels’ load-bearing capacity and fire rating certifications, as these factors are critical for ensuring workplace safety and adhering to local regulations.
Why Are Sandwich Panels Important for Clean Rooms?
Sandwich panels are ideal for clean rooms, where maintaining a controlled environment is paramount. Their smooth surfaces and insulation properties help prevent contamination, ensuring high air quality and cleanliness. For international buyers, particularly in the Middle East, it is essential to consider material specifications and ease of installation to align with stringent industry standards in pharmaceuticals and electronics manufacturing.
How Are Sandwich Panels Used in Transportation and Logistics?
In the transportation and logistics sector, sandwich panels are commonly used in mobile offices and containers, providing a portable solution that can be rapidly deployed in various locations. These panels offer durability and weather resistance, making them suitable for diverse climates. Buyers from South America and Africa should assess weight limitations and environmental resilience to ensure that the panels can withstand the rigors of transportation and outdoor use.
3 Common User Pain Points for ‘sandwich panel manufacturer’ & Their Solutions
Scenario 1: Navigating Quality Assurance Challenges in Sandwich Panels
The Problem: One of the primary concerns for international B2B buyers, especially in regions like Africa and South America, is ensuring the quality and durability of sandwich panels. Many manufacturers may provide low-cost options, but these often come at the expense of structural integrity and insulation performance. Buyers face the risk of receiving subpar materials that could lead to costly repairs or replacements, jeopardizing project timelines and budgets. This scenario is particularly critical in construction projects, where compliance with local regulations and standards is non-negotiable.
The Solution: To mitigate quality assurance issues, buyers should establish a robust vetting process for potential manufacturers. Start by requesting detailed product specifications and certifications that demonstrate compliance with international standards, such as ISO or ASTM. Additionally, consider conducting factory audits or site visits to assess production capabilities firsthand. Engaging third-party inspection services can provide unbiased evaluations of product quality before shipment. Furthermore, fostering a long-term relationship with a reputable manufacturer can facilitate better quality control and responsiveness to any issues that arise post-purchase.
Scenario 2: Understanding Customization Needs for Diverse Applications
The Problem: B2B buyers often struggle with finding sandwich panels that meet specific project requirements, particularly when dealing with unique architectural designs or insulation needs. For instance, buyers in the Middle East may require panels that withstand extreme temperatures, while those in Europe might prioritize eco-friendly materials. The lack of clear communication regarding customization options can lead to frustration and delays in project execution.
The Solution: Buyers should prioritize manufacturers that offer tailored solutions and have a flexible production process. Start by preparing a comprehensive list of project requirements, including thermal performance, aesthetic preferences, and compliance with local building codes. Engage in open discussions with manufacturers about their customization capabilities and request samples of different materials and finishes. Utilizing 3D modeling and design software can help visualize how specific sandwich panels will fit into your project, ensuring that both parties are aligned before finalizing orders. Building a collaborative relationship with your manufacturer will enable more efficient design iterations and faster turnaround times.
Scenario 3: Managing Supply Chain Disruptions Effectively
The Problem: Supply chain disruptions can pose significant challenges for B2B buyers, particularly in regions with less stable logistics infrastructure. Delays in shipping, customs clearance issues, or unforeseen material shortages can halt construction projects, leading to financial losses and strained relationships with clients. This is a critical concern for buyers in emerging markets like Egypt or Brazil, where logistics can be unpredictable.
The Solution: To effectively manage supply chain risks, buyers should diversify their sourcing strategies. Instead of relying on a single manufacturer, consider building a network of multiple suppliers across different regions. This approach allows for greater flexibility and ensures that you have alternative options in case of disruptions. Additionally, negotiating favorable lead times and maintaining clear communication with suppliers can help set realistic expectations for delivery schedules. Implementing a just-in-time inventory system can further enhance your ability to respond quickly to changes in demand. Regularly reviewing and adjusting your supply chain strategy will help you remain resilient in the face of challenges, ensuring that your projects stay on track.
Strategic Material Selection Guide for sandwich panel manufacturer
What Are the Key Materials Used in Sandwich Panels?
When selecting materials for sandwich panels, it is crucial to understand the properties and suitability of each option. The most common materials include Polyurethane (PUR), Polystyrene (EPS), Mineral Wool, and Aluminum. Each material has unique characteristics that can significantly impact performance, cost, and application.
How Does Polyurethane (PUR) Perform in Sandwich Panels?
Polyurethane is renowned for its excellent thermal insulation properties, making it a popular choice for sandwich panels. It typically boasts a temperature rating of up to 120°C and offers significant resistance to moisture and chemicals, which is vital for applications in humid or corrosive environments.
Pros & Cons: The primary advantage of PUR is its high insulation value, leading to energy efficiency in buildings. However, its manufacturing complexity can increase production costs. Additionally, PUR can be sensitive to UV exposure, which may limit its application in outdoor settings without proper coatings.
Impact on Application: PUR is particularly suited for cold storage facilities and refrigerated transport due to its superior insulation properties. International buyers should consider compliance with standards such as ASTM C518 for thermal resistance.
What Are the Benefits of Polystyrene (EPS) in Sandwich Panels?
Expanded Polystyrene (EPS) is another widely used material in sandwich panel manufacturing. It has a lower density compared to other materials, providing a lightweight option that is easy to handle and install. EPS panels can typically withstand temperatures up to 75°C, making them suitable for various applications.
Pros & Cons: The cost-effectiveness of EPS is one of its biggest advantages, as it is generally less expensive than PUR or mineral wool. However, EPS has lower fire resistance and can be more susceptible to damage from moisture, which may limit its use in certain environments.
Impact on Application: EPS is commonly used in residential and commercial buildings for insulation. Buyers from regions like Africa and South America should be aware of local fire safety regulations, as compliance with standards such as DIN 4102 may be necessary.
Why Choose Mineral Wool for Sandwich Panels?
Mineral wool, made from natural or synthetic fibers, is highly regarded for its fire resistance and sound insulation properties. It can withstand temperatures up to 1,000°C, making it ideal for applications requiring high fire safety standards.
Pros & Cons: The key advantage of mineral wool is its excellent fire resistance, which is critical for industrial applications. However, it is heavier than other materials, which can complicate transportation and installation. Additionally, mineral wool is generally more expensive than EPS and PUR.
Impact on Application: Mineral wool is particularly suitable for buildings requiring high fire safety standards, such as industrial warehouses and commercial kitchens. International buyers should ensure compliance with local fire safety codes and standards like EN 13501.
How Does Aluminum Enhance Sandwich Panel Performance?
Aluminum is often used as a facing material in sandwich panels due to its strength, lightweight nature, and corrosion resistance. It can withstand a wide range of temperatures and is often used in applications exposed to harsh environmental conditions.
Pros & Cons: The primary advantage of aluminum is its durability and resistance to corrosion, making it suitable for outdoor applications. However, aluminum can be more expensive than other materials, and its thermal conductivity is higher, which may require additional insulation layers.
Impact on Application: Aluminum-faced panels are commonly used in commercial buildings and industrial applications. Buyers should consider the local availability of aluminum and its cost implications, especially in regions like the Middle East where raw materials may be sourced locally.
Summary Table of Material Properties for Sandwich Panels
Material | Typical Use Case for sandwich panel manufacturer | Key Advantage | Key Disadvantage/Limitation | Relative Cost (Low/Med/High) |
---|---|---|---|---|
Polyurethane (PUR) | Cold storage facilities, refrigerated transport | High thermal insulation | Sensitive to UV exposure | Medium |
Polystyrene (EPS) | Residential and commercial buildings | Cost-effective | Lower fire resistance | Low |
Mineral Wool | Industrial warehouses, commercial kitchens | Excellent fire resistance | Heavier and more expensive | High |
Aluminum | Commercial buildings, industrial applications | Durable and corrosion-resistant | Higher cost and thermal conductivity | High |
This strategic material selection guide serves as a comprehensive resource for international B2B buyers, enabling them to make informed decisions based on specific project requirements and regional compliance standards.
In-depth Look: Manufacturing Processes and Quality Assurance for sandwich panel manufacturer
What Are the Main Stages of the Manufacturing Process for Sandwich Panels?
The manufacturing process for sandwich panels involves several critical stages that ensure the final product meets industry standards and customer expectations. Understanding these stages is essential for B2B buyers looking to source high-quality sandwich panels.
1. Material Preparation
The first step involves sourcing and preparing the core and face materials. Common core materials include polystyrene, polyurethane, and mineral wool, while face materials can consist of steel, aluminum, or fiberglass. B2B buyers should inquire about the sourcing practices of manufacturers to ensure they use high-quality raw materials.
Additionally, the preparation phase includes cutting these materials to the required dimensions and ensuring they are free from defects. A thorough inspection at this stage can prevent costly errors later in the manufacturing process.
2. Forming
During the forming stage, the core material is sandwiched between the face materials using various techniques such as hot pressing or cold bonding. The choice of method can significantly affect the thermal insulation properties and structural integrity of the panels. Buyers should ask manufacturers about the techniques they employ and their impact on panel performance.
The forming process must be precisely controlled, as variations in temperature and pressure can lead to inconsistencies. This is where automation plays a crucial role, enhancing repeatability and reducing human error.
3. Assembly
Once the materials are formed, the panels are assembled. This may involve cutting, trimming, and edge finishing. Manufacturers often utilize automated cutting machines to ensure precision and efficiency. B2B buyers should consider the level of automation in a manufacturer’s assembly line, as it can indicate the efficiency and scalability of production.
Quality checks during assembly are vital. Manufacturers should implement in-process quality control (IPQC) to monitor the assembly stage, ensuring that any defects are caught early.
4. Finishing
The final stage is finishing, which includes surface treatment, painting, or coating to enhance durability and aesthetic appeal. This stage can also improve weather resistance, an essential factor for panels used in various climates. Buyers should inquire about the types of finishes available and their respective performance characteristics.
How Do Manufacturers Ensure Quality Control in Sandwich Panel Production?
Quality control (QC) is a critical component of the sandwich panel manufacturing process. For B2B buyers, understanding the QC measures in place can significantly influence purchasing decisions.
Relevant International Standards for Quality Assurance
Manufacturers should adhere to international quality standards such as ISO 9001, which focuses on effective quality management systems. Additionally, industry-specific certifications like CE marking in Europe and API standards in the oil and gas sector can provide assurance of product quality and safety.
B2B buyers should verify that their suppliers are certified and regularly audited against these standards. This not only confirms compliance but also reflects a commitment to continuous improvement.
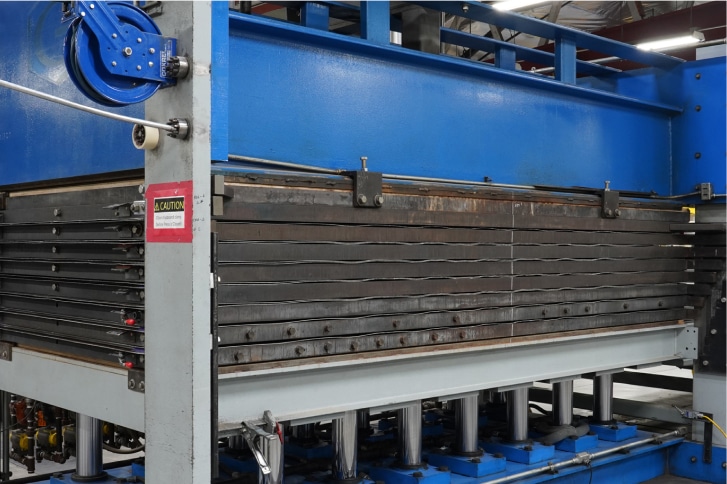
A stock image related to sandwich panel manufacturer.
What Are the Key QC Checkpoints in Sandwich Panel Manufacturing?
Quality control in sandwich panel production typically involves several checkpoints:
-
Incoming Quality Control (IQC): This is the first line of defense, where raw materials are inspected upon arrival. Buyers should ensure that suppliers have robust IQC processes to prevent defective materials from entering production.
-
In-Process Quality Control (IPQC): During manufacturing, continuous monitoring is essential. This involves checking parameters such as adhesive application and curing times to ensure consistency and quality.
-
Final Quality Control (FQC): After production, panels undergo comprehensive testing to verify they meet specifications. This may include dimensional checks, thermal resistance testing, and structural integrity assessments.
What Common Testing Methods Are Used to Ensure Quality?
Various testing methods are employed to ensure the quality of sandwich panels. Some common methods include:
- Thermal Conductivity Testing: Measures how well the panel insulates against heat.
- Compressive Strength Testing: Assesses the ability of the panel to withstand loads without deformation.
- Water Absorption Testing: Evaluates the panel’s resistance to moisture, crucial for longevity in humid environments.
B2B buyers should ask manufacturers for detailed reports on testing methodologies and results to understand the performance capabilities of the panels.
How Can B2B Buyers Verify Supplier Quality Control Practices?
To ensure that suppliers maintain high-quality standards, B2B buyers can take several proactive steps:
-
Conduct Supplier Audits: Regular audits can help assess the manufacturing processes and QC practices. This includes reviewing documentation, visiting production facilities, and observing QC measures in action.
-
Request Quality Reports: Buyers should ask for detailed QC reports, including IQC, IPQC, and FQC findings. This transparency can provide insight into the supplier’s commitment to quality.
-
Utilize Third-Party Inspection Services: Engaging third-party inspectors can provide an unbiased assessment of the supplier’s quality practices. This is particularly beneficial for international buyers who may not be able to visit facilities personally.
What Are the QC and Certification Nuances for International B2B Buyers?
International B2B buyers need to be aware of specific nuances in QC and certification that can vary by region. For example, in Europe, compliance with CE marking is mandatory, while in some Middle Eastern countries, local standards may apply.
Buyers should be proactive in understanding the regulatory landscape in their regions and ensure that their suppliers are compliant with local and international standards. This may include verifying that products meet specific fire safety regulations, especially for panels used in construction.
In summary, understanding the manufacturing processes and quality assurance measures for sandwich panels is crucial for B2B buyers. By focusing on material preparation, forming, assembly, and finishing, along with robust QC practices, buyers can make informed decisions and ensure they source high-quality products that meet their needs.
Practical Sourcing Guide: A Step-by-Step Checklist for ‘sandwich panel manufacturer’
This step-by-step guide aims to assist international B2B buyers in effectively sourcing sandwich panel manufacturers. By following these actionable insights, you can streamline your procurement process, ensuring that you choose a reliable supplier that meets your specific needs.
Step 1: Define Your Technical Specifications
Before initiating the sourcing process, clearly outline your technical requirements. This includes dimensions, insulation properties, fire resistance ratings, and aesthetic considerations. A well-defined specification helps narrow down potential suppliers who can meet your standards and reduces the risk of costly mistakes later in production.
Step 2: Research Market Trends and Standards
Understanding the latest trends in sandwich panel technology and regional building codes is crucial. Research the materials commonly used in your target regions, such as Africa or Europe, and identify standards that manufacturers must comply with. This knowledge allows you to ask informed questions and ensures that the products you consider are compliant with local regulations.
Step 3: Identify Potential Suppliers
Begin by compiling a list of potential sandwich panel manufacturers. Use industry directories, trade shows, and online marketplaces to find suppliers. Pay attention to their experience in serving clients from your region, as local knowledge can significantly impact service quality and product adaptability.
Step 4: ✅ Verify Supplier Certifications
Ensure that your shortlisted suppliers possess relevant certifications, such as ISO 9001 for quality management and fire safety certifications. These certifications demonstrate a commitment to quality and compliance with international standards. Request copies of these documents and check their validity to avoid future compliance issues.
Step 5: Evaluate Supplier Capabilities and Capacity
Assess the manufacturing capabilities of your potential suppliers. This includes evaluating their production capacity, technology used, and their ability to scale production based on your needs. Additionally, inquire about their supply chain logistics and lead times to ensure they can meet your project deadlines.
Step 6: Request Samples and Conduct Quality Checks
Once you have shortlisted potential suppliers, request samples of their sandwich panels. Examine the samples for quality, durability, and adherence to your technical specifications. Conduct thorough quality checks to ensure that the product aligns with your expectations before placing a larger order.
Step 7: Negotiate Terms and Establish Communication Protocols
Before finalizing your supplier, negotiate the terms of your contract, including pricing, payment terms, delivery schedules, and warranty provisions. Establish clear communication protocols to ensure that both parties are aligned throughout the procurement process. Effective communication can prevent misunderstandings and foster a stronger supplier relationship.
By following this structured checklist, you can enhance your sourcing strategy for sandwich panel manufacturers, leading to successful procurement that meets your project requirements.
Comprehensive Cost and Pricing Analysis for sandwich panel manufacturer Sourcing
Understanding the cost structure and pricing nuances of sandwich panel manufacturing is crucial for international B2B buyers, especially those from Africa, South America, the Middle East, and Europe. This section breaks down the key components that influence costs and provides actionable insights for making informed sourcing decisions.
What Are the Key Cost Components in Sandwich Panel Manufacturing?
1. Materials
The primary cost driver in sandwich panel manufacturing is the raw materials used, which typically include insulation cores (like polyurethane or polystyrene), metal skins (steel or aluminum), and adhesives. The choice of materials not only affects the price but also the thermal efficiency, fire resistance, and overall durability of the panels. Buyers should evaluate material specifications based on their project requirements to avoid overspending on unnecessary features.
2. Labor
Labor costs can vary significantly based on the region and the skill level of the workforce. Manufacturers in regions with lower labor costs may offer competitive pricing, but this could also impact quality and production timelines. It’s essential to consider the balance between cost and quality when selecting suppliers.
3. Manufacturing Overhead
This includes indirect costs associated with production, such as utilities, facility maintenance, and administrative expenses. Overhead costs can be a hidden factor in pricing, so understanding a supplier’s operational efficiency is vital for assessing their pricing structure.
4. Tooling
Tooling refers to the equipment and molds required for production. High initial tooling costs can lead to higher prices for low-volume orders. Buyers should inquire about the tooling setup and whether it can be amortized over larger orders to reduce per-unit costs.
5. Quality Control (QC)
Investments in quality control processes can significantly affect manufacturing costs. Suppliers that prioritize QC may have higher prices, but they also reduce the risk of defects and associated costs down the line. Buyers should assess the QC certifications and practices of potential suppliers to ensure they meet industry standards.
6. Logistics
Logistics costs encompass transportation, warehousing, and handling fees. These can vary widely depending on the supplier’s location and the delivery terms. Understanding the logistics landscape can help buyers negotiate better terms and avoid unexpected expenses.
7. Margin
Finally, the manufacturer’s profit margin is a key factor in pricing. While it’s essential for suppliers to maintain profitability, buyers should seek transparency regarding margins to ensure they are not overpaying.
How Do Price Influencers Affect Sandwich Panel Costs?
1. Volume and Minimum Order Quantity (MOQ)
Larger orders typically reduce the per-unit cost due to economies of scale. Buyers should negotiate MOQs that align with their project needs to optimize pricing.
2. Specifications and Customization
Custom specifications can increase costs. Buyers should clearly define their requirements to avoid unnecessary customizations that may inflate prices.
3. Quality and Certifications
Panels that meet higher quality standards or certifications often come at a premium. Buyers should assess whether the additional cost is justified based on the intended use and local regulations.
4. Supplier Factors
The supplier’s reputation, production capacity, and financial stability can influence pricing. Conducting thorough due diligence on potential suppliers can uncover hidden costs or risks.
5. Incoterms
Understanding Incoterms is essential for managing shipping costs and responsibilities. Different terms can significantly affect the total landed cost of the panels.
What Tips Can Help Buyers Optimize Costs?
1. Negotiation Strategies
Engaging in open negotiations about pricing, payment terms, and delivery schedules can lead to significant savings. Buyers should be prepared to discuss their needs and explore flexible options.
2. Focus on Total Cost of Ownership (TCO)
Instead of just considering the initial purchase price, evaluate the total cost of ownership, including installation, maintenance, and energy efficiency. This broader perspective can lead to better long-term decisions.
3. Pricing Nuances for International Buyers
Buyers from Africa, South America, the Middle East, and Europe should be aware of regional pricing variations due to exchange rates, tariffs, and local economic conditions. It’s advisable to conduct market research specific to their region to understand typical pricing benchmarks.
Disclaimer on Indicative Prices
Prices for sandwich panels can fluctuate based on market conditions, material availability, and geopolitical factors. It is essential for buyers to obtain updated quotes directly from manufacturers to ensure accuracy in budgeting and planning.
By understanding these cost components and price influencers, B2B buyers can make more informed decisions when sourcing sandwich panels, ultimately leading to better project outcomes and cost savings.
Alternatives Analysis: Comparing sandwich panel manufacturer With Other Solutions
Exploring Alternatives to Sandwich Panel Manufacturers in Construction
In the construction and manufacturing sectors, sandwich panels have gained popularity due to their superior thermal insulation and lightweight properties. However, international B2B buyers should consider various alternatives that may also meet their structural and insulation needs. Here, we compare sandwich panels with two viable alternatives: Structural Insulated Panels (SIPs) and traditional brick-and-mortar construction.
Comparison Table of Sandwich Panel Manufacturer vs. Alternatives
Comparison Aspect | Sandwich Panel Manufacturer | Structural Insulated Panels (SIPs) | Traditional Brick-and-Mortar Construction |
---|---|---|---|
Performance | High thermal efficiency; lightweight | Excellent insulation; good structural integrity | Strong durability; lower insulation efficiency |
Cost | Moderate initial investment; lower long-term costs | Higher initial costs; savings on energy bills | High initial costs; variable long-term costs |
Ease of Implementation | Quick assembly; minimal labor | Requires skilled labor; prefabrication needed | Labor-intensive; longer construction time |
Maintenance | Low maintenance; resistant to pests and moisture | Low maintenance; requires periodic checks | High maintenance; susceptible to weather damage |
Best Use Case | Industrial buildings, cold storage | Residential homes, commercial buildings | Traditional residential and commercial buildings |
What are the Advantages and Disadvantages of Structural Insulated Panels (SIPs)?
Structural Insulated Panels (SIPs) are a modern building material made from a layer of insulating foam sandwiched between two structural facings, often oriented strand board (OSB).
Pros:
– Energy Efficiency: SIPs provide excellent thermal insulation, which can lead to substantial energy savings over time.
– Strength and Durability: They offer a high strength-to-weight ratio, making them suitable for various structures.
Cons:
– Cost: The initial investment can be higher than sandwich panels, which may deter budget-sensitive projects.
– Installation: SIPs require skilled labor for assembly, which could lead to increased labor costs and project timelines.
How Does Traditional Brick-and-Mortar Construction Compare?
Traditional brick-and-mortar construction involves building walls using bricks or blocks, which are then plastered and finished.
Pros:
– Durability: Brick structures are well-known for their longevity and resistance to various environmental conditions.
– Aesthetic Versatility: Offers a classic look and can be adapted to different architectural styles.
Cons:
– Energy Inefficiency: Compared to sandwich panels and SIPs, traditional methods often have lower insulation values, leading to higher energy costs.
– Construction Time: Building with bricks is labor-intensive and time-consuming, which may delay project completion.
How Should B2B Buyers Choose the Right Solution?
When selecting the appropriate building solution, international B2B buyers should assess their specific project requirements, including budget constraints, energy efficiency goals, and timelines. Sandwich panels might be optimal for projects that require quick assembly and good insulation, while SIPs could be preferable for energy-conscious constructions despite the higher initial costs. Traditional brick-and-mortar may suit projects where durability and aesthetics take precedence, but buyers should be prepared for longer construction times and maintenance needs.
In conclusion, understanding the strengths and weaknesses of these alternatives allows B2B buyers to make informed decisions that align with their strategic objectives and operational needs.
Essential Technical Properties and Trade Terminology for sandwich panel manufacturer
What Are the Key Technical Properties of Sandwich Panels?
When sourcing sandwich panels for construction or industrial applications, international B2B buyers must understand essential technical properties that influence product performance, durability, and suitability for various environments. Here are some critical specifications to consider:
1. Material Grade
Material grade refers to the classification of the core and facing materials used in sandwich panels. Common materials include polyurethane, polystyrene, and mineral wool for the core, while steel or aluminum are often used for the facings. The grade determines the panel’s thermal insulation, fire resistance, and structural integrity. Buyers should select the material grade based on the environmental conditions and regulatory standards of their specific market.
2. Thickness and Tolerance
The thickness of sandwich panels typically ranges from 40mm to 200mm, affecting both insulation properties and load-bearing capabilities. Tolerance refers to the allowable deviation from specified dimensions, which is crucial for ensuring a proper fit during installation. Understanding these specifications helps buyers ensure that the panels meet their project requirements and comply with local building codes.
3. Thermal Conductivity
Thermal conductivity measures how well a material conducts heat, expressed in watts per meter-kelvin (W/m·K). Lower values indicate better insulating properties. For buyers in regions with extreme temperatures, such as the Middle East or South America, selecting panels with appropriate thermal conductivity can significantly impact energy efficiency and comfort in buildings.
4. Fire Resistance Rating
Fire resistance ratings indicate how well sandwich panels can withstand fire exposure. Ratings are often classified as Class A, B, or C, with Class A providing the highest level of fire resistance. This property is particularly important for buyers in industrial sectors and regions with strict safety regulations. Ensuring compliance with local fire safety standards can mitigate risks and enhance the safety of structures.
What Are Common Trade Terms Used in the Sandwich Panel Industry?
Understanding industry jargon is essential for effective communication and negotiation in the sandwich panel market. Here are several common terms that B2B buyers should be familiar with:
1. OEM (Original Equipment Manufacturer)
OEM refers to a company that produces parts or equipment that may be marketed by another manufacturer. In the context of sandwich panels, buyers may work directly with OEMs for customized solutions or specific designs tailored to their projects. Understanding OEM relationships can help buyers secure quality products that meet their precise needs.
2. MOQ (Minimum Order Quantity)
MOQ signifies the smallest quantity of a product that a supplier is willing to sell. For international buyers, knowing the MOQ is vital for budgeting and inventory management. Suppliers in Africa or South America may have different MOQs based on local market conditions, so it’s essential to clarify these details early in negotiations to avoid unexpected costs.
3. RFQ (Request for Quotation)
An RFQ is a document that buyers send to suppliers to request pricing and terms for specific products. This is a critical step in the procurement process, allowing buyers to compare options from different manufacturers. Crafting a comprehensive RFQ can lead to better pricing and service terms, especially when dealing with multiple suppliers across Europe and the Middle East.
4. Incoterms (International Commercial Terms)
Incoterms are a set of predefined international rules that clarify the responsibilities of buyers and sellers in global trade. These terms define who is responsible for shipping, insurance, and tariffs. Familiarity with Incoterms is crucial for B2B buyers to understand their liabilities and ensure smooth transactions across borders, particularly in complex trade environments.
By grasping these technical properties and trade terms, international B2B buyers can make informed decisions when sourcing sandwich panels, ensuring they meet both performance standards and market requirements.
Navigating Market Dynamics and Sourcing Trends in the sandwich panel manufacturer Sector
What Are the Key Market Dynamics and Trends Affecting Sandwich Panel Manufacturers?
The sandwich panel manufacturing sector is experiencing significant transformations driven by globalization, technological advancements, and shifting consumer preferences. For international B2B buyers, particularly those in Africa, South America, the Middle East, and Europe, understanding these dynamics is crucial for informed sourcing decisions.
One of the primary drivers of market growth is the escalating demand for lightweight, energy-efficient building materials. This trend aligns with the global push for sustainable construction practices. Additionally, technological innovations such as automated production lines and advanced insulation materials are enhancing the quality and performance of sandwich panels, making them more appealing to buyers across diverse markets.
Furthermore, the rise of digital platforms for sourcing and procurement is reshaping how businesses connect with manufacturers. Buyers can now leverage online marketplaces and supplier databases to compare products, prices, and specifications with ease. This increased transparency is beneficial for international buyers looking to optimize their supply chain and ensure competitive pricing.
Another emerging trend is the customization of sandwich panels to meet specific regional requirements, such as climatic conditions and local building codes. Manufacturers are increasingly offering tailored solutions, which is vital for buyers in varied geographical locations, including Egypt and Indonesia.
How Does Sustainability Influence the Sourcing of Sandwich Panels?
Sustainability is becoming a non-negotiable factor for B2B buyers in the sandwich panel sector. The environmental impact of construction materials is under scrutiny, and buyers are seeking suppliers that prioritize eco-friendly practices. This includes the use of recyclable materials and energy-efficient production processes.
Incorporating sustainability into sourcing strategies not only aligns with global environmental goals but also enhances brand reputation. Buyers should look for manufacturers that possess certifications like ISO 14001 for environmental management and LEED (Leadership in Energy and Environmental Design) ratings, which signify a commitment to sustainable practices.
Moreover, the demand for ‘green’ materials is on the rise. This includes the use of polyurethane or polystyrene insulation, which offers superior thermal performance while minimizing environmental impact. By prioritizing suppliers who utilize sustainable materials and processes, B2B buyers can contribute to a more responsible supply chain, ultimately leading to long-term cost savings and compliance with increasingly stringent regulations.
How Has the Sandwich Panel Manufacturing Sector Evolved Over Time?
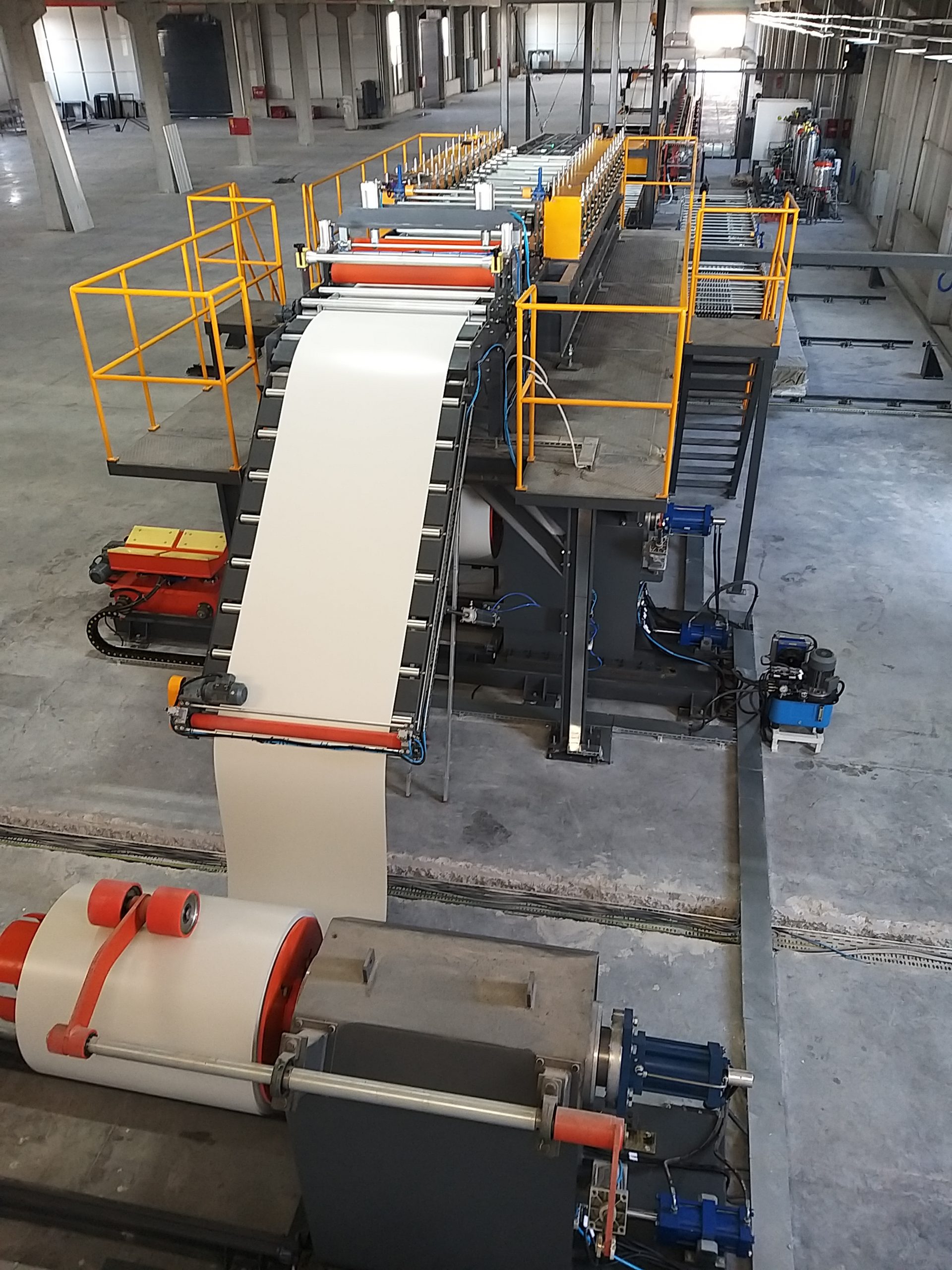
A stock image related to sandwich panel manufacturer.
The sandwich panel manufacturing sector has evolved significantly since its inception in the mid-20th century. Initially developed for cold storage applications, the use of sandwich panels has expanded dramatically across various industries, including construction, transportation, and refrigeration.
In the early days, the focus was primarily on functionality and cost-effectiveness. However, as environmental concerns gained prominence, manufacturers began to innovate, integrating advanced materials and technologies that improve insulation and structural integrity. Today, the sector is characterized by a blend of performance, sustainability, and customization, catering to a diverse range of applications and regulatory standards across different regions.
This evolution highlights the importance of staying informed about market trends and technological advancements, enabling international B2B buyers to make strategic sourcing decisions that align with their operational goals.
Frequently Asked Questions (FAQs) for B2B Buyers of sandwich panel manufacturer
-
How do I solve quality issues when sourcing sandwich panels?
To address quality concerns when sourcing sandwich panels, start by conducting thorough due diligence on potential manufacturers. Request samples and certifications that demonstrate compliance with international standards, such as ISO and ASTM. It’s also beneficial to visit the factory if possible or use third-party inspection services to ensure the manufacturing process meets your quality expectations. Establishing a clear quality assurance agreement and ongoing communication with the manufacturer can further mitigate risks. -
What is the best material for sandwich panels in different climates?
The best material for sandwich panels depends on the climate of your project location. For tropical climates, consider panels with moisture-resistant cores, such as polystyrene or polyurethane, to prevent mold and degradation. In colder regions, materials with excellent thermal insulation properties are crucial. Additionally, for areas prone to fire, look for panels with fire-rated cores. Consulting with local experts can help identify the most suitable materials for your specific environmental conditions. -
How can I verify the credibility of a sandwich panel manufacturer?
Verifying a manufacturer’s credibility involves several steps. Start by checking their business registration and industry certifications. Look for customer reviews and case studies to assess their reputation. Engage in direct communication to gauge responsiveness and expertise. Attending industry trade shows or exhibitions can also provide insights into their operations and allow for face-to-face discussions. Lastly, consider requesting references from other international buyers to gain further confidence in their reliability. -
What are the typical minimum order quantities (MOQs) for sandwich panels?
Minimum order quantities for sandwich panels can vary widely depending on the manufacturer and the complexity of the project. Generally, MOQs can range from a few hundred to several thousand square meters. It’s advisable to discuss your specific needs with potential suppliers to negotiate terms that work for both parties. Additionally, some manufacturers may offer flexibility on MOQs for first-time buyers or larger, long-term contracts. -
What payment terms should I expect when dealing with sandwich panel manufacturers?
Payment terms can vary based on the manufacturer and your negotiation. Common arrangements include a deposit upfront (usually 30% to 50%) with the balance due upon delivery or before shipping. Some manufacturers may offer letters of credit or milestone payments tied to production stages. Ensure you clarify terms in the contract to avoid misunderstandings. It is also wise to consider using secure payment methods to protect your investment. -
How do logistics and shipping work for sandwich panels internationally?
Logistics for international shipping of sandwich panels involve several steps, including packaging, transportation, and customs clearance. Collaborate with your manufacturer to understand their shipping capabilities and preferred carriers. It’s crucial to discuss delivery timelines, costs, and responsibilities for customs duties. Engaging a logistics partner with experience in handling construction materials can streamline the process and mitigate potential delays or issues at customs. -
Can sandwich panels be customized for specific projects?
Yes, many manufacturers offer customization options for sandwich panels to meet specific project requirements. Customizations can include variations in thickness, core materials, surface finishes, and dimensions. Discuss your project needs with manufacturers early in the sourcing process to ensure they can accommodate your specifications. Providing detailed drawings or project descriptions can facilitate better understanding and accuracy in the customization process. -
What are the common applications for sandwich panels in construction?
Sandwich panels are widely used in various construction applications due to their versatility and insulation properties. Common uses include wall cladding for commercial buildings, roofing systems for industrial facilities, and cold storage solutions. They are also popular for modular buildings and temporary structures. Understanding the specific requirements of your project will help you select the right type of sandwich panel for optimal performance and compliance with local building codes.
Important Disclaimer & Terms of Use
⚠️ Important Disclaimer
The information provided in this guide, including content regarding manufacturers, technical specifications, and market analysis, is for informational and educational purposes only. It does not constitute professional procurement advice, financial advice, or legal advice.
While we have made every effort to ensure the accuracy and timeliness of the information, we are not responsible for any errors, omissions, or outdated information. Market conditions, company details, and technical standards are subject to change.
B2B buyers must conduct their own independent and thorough due diligence before making any purchasing decisions. This includes contacting suppliers directly, verifying certifications, requesting samples, and seeking professional consultation. The risk of relying on any information in this guide is borne solely by the reader.
Strategic Sourcing Conclusion and Outlook for sandwich panel manufacturer
Why is Strategic Sourcing Essential for Sandwich Panel Manufacturers?
As we conclude our exploration of strategic sourcing within the sandwich panel manufacturing industry, it’s vital to recognize the pivotal role it plays in enhancing supply chain efficiency and reducing costs. International B2B buyers, particularly from regions like Africa, South America, the Middle East, and Europe, should prioritize sourcing strategies that leverage local suppliers and optimize logistics. This approach not only mitigates risks associated with global supply chains but also fosters strong partnerships with manufacturers who understand the regional market dynamics.
What Key Takeaways Should International Buyers Remember?
- Supplier Diversity: Engaging a diverse range of suppliers can lead to innovative solutions and improved responsiveness to market changes.
- Cost Management: Strategic sourcing enables better negotiation leverage, ultimately leading to more favorable pricing and terms.
- Sustainability Considerations: Buyers should prioritize suppliers who adhere to sustainable practices, aligning with global trends towards eco-friendly construction materials.
How Can International Buyers Prepare for Future Trends?
Looking ahead, the demand for high-quality, energy-efficient sandwich panels is expected to rise, driven by increasing construction activities across emerging markets. B2B buyers are encouraged to stay informed about technological advancements and evolving industry standards. By adopting a proactive approach to sourcing, buyers can position themselves advantageously within the competitive landscape.
In conclusion, as you navigate the complexities of sourcing sandwich panels, remember that strategic sourcing is not just a procurement function; it is a crucial element that can drive your business forward. Embrace these insights to foster meaningful partnerships and capitalize on the growth opportunities in your region.