Unlock Savings: The Complete Guide to Patch Panel Custom (2025)
Introduction: Navigating the Global Market for patch panel custom
In today’s interconnected world, sourcing patch panel custom solutions can be a daunting challenge for international B2B buyers, particularly those in Africa, South America, the Middle East, and Europe. With a myriad of options available, understanding the nuances of different types of patch panels and their applications is crucial for making informed purchasing decisions. This guide aims to demystify the complexities of the global market by providing comprehensive insights into various patch panel configurations, their specific use cases, and best practices for supplier vetting.
From exploring the benefits of modular versus fixed patch panels to understanding the implications of fiber versus copper connectivity, this resource serves as a roadmap for buyers seeking to optimize their network infrastructures. Additionally, we delve into cost considerations, offering strategies for balancing quality with budget constraints while ensuring compliance with local and international standards.
By equipping B2B buyers with actionable insights and practical advice, this guide empowers you to navigate the global market with confidence. Whether you are in Egypt looking for reliable suppliers or in Italy assessing the latest innovations, our comprehensive approach ensures that you will have the knowledge necessary to make strategic purchasing decisions that align with your business objectives.
Understanding patch panel custom Types and Variations
Type Name | Key Distinguishing Features | Primary B2B Applications | Brief Pros & Cons for Buyers |
---|---|---|---|
Standard Patch Panels | Fixed number of ports, typically 24 or 48 | Office networks, data centers | Pros: Cost-effective, easy installation. Cons: Limited scalability. |
Modular Patch Panels | Customizable port configurations, hot-swappable | Large enterprises, telecom sectors | Pros: Flexible, scalable. Cons: Higher initial cost. |
Fiber Optic Patch Panels | Designed for fiber optic connections, LC/SC ports | ISPs, data centers, enterprise networks | Pros: High-speed connectivity, space-efficient. Cons: More fragile than copper panels. |
Blank Patch Panels | Unpopulated panels for future expansion | Growing businesses, temporary setups | Pros: Cost-effective for future needs. Cons: Requires additional components later. |
Shielded Patch Panels | Enhanced shielding against electromagnetic interference | Industrial environments, data-sensitive operations | Pros: Improved signal quality, reduced interference. Cons: Higher cost, bulkier design. |
What Are the Key Characteristics of Standard Patch Panels?
Standard patch panels are the most common type used in B2B environments. They come with a fixed number of ports, usually 24 or 48, and are designed for straightforward installations in office networks and data centers. These panels are cost-effective and easy to set up, making them ideal for small to medium-sized businesses. However, their limited scalability can be a drawback as companies grow and require more connectivity options.
How Do Modular Patch Panels Offer Flexibility?
Modular patch panels allow for customizable port configurations, enabling businesses to adapt their setups based on current and future needs. These panels often include hot-swappable modules, which makes it easy to upgrade or replace components without significant downtime. They are particularly suited for large enterprises and telecom sectors that demand high flexibility and scalability. However, the initial investment is typically higher than that of standard panels, which may deter some budget-conscious buyers.
Why Choose Fiber Optic Patch Panels for High-Speed Connectivity?
Fiber optic patch panels are specifically designed for high-speed data transmission and feature connections like LC and SC ports. These panels are essential for ISPs, data centers, and enterprise networks that prioritize speed and bandwidth. They offer significant advantages in terms of space efficiency and signal quality, but their fragility compared to copper panels can pose challenges during installation and maintenance. Buyers should consider their operational environment when choosing this type.
What Benefits Do Blank Patch Panels Provide for Future Expansion?
Blank patch panels are unpopulated units that allow businesses to plan for future expansion without immediate investment in additional ports. They are particularly useful for growing businesses or temporary setups where flexibility is crucial. While they are cost-effective, buyers must remember that additional components will be needed later, which can complicate future installations and increase overall costs.
How Do Shielded Patch Panels Enhance Signal Quality?
Shielded patch panels are designed to minimize electromagnetic interference, making them ideal for industrial environments or data-sensitive operations. They provide improved signal quality and can be crucial for maintaining data integrity in challenging environments. However, these panels tend to be bulkier and more expensive than standard options, which may not fit every buyer’s budget or space constraints. Businesses should weigh the benefits of enhanced performance against the higher costs when considering this option.
Related Video: Terminating Patch Panel – How to do it fast and easy
Key Industrial Applications of patch panel custom
Industry/Sector | Specific Application of patch panel custom | Value/Benefit for the Business | Key Sourcing Considerations for this Application |
---|---|---|---|
Telecommunications | Custom patch panels for network management | Enhances network organization and reduces downtime | Compatibility with existing infrastructure and scalability |
Data Centers | High-density patch panels for server racks | Maximizes space utilization and improves airflow | Heat resistance and modular design to accommodate future needs |
Industrial Automation | Patch panels for machine-to-machine communication | Streamlines operations and enhances data transfer efficiency | Durability and resistance to environmental factors |
Smart Buildings | Integrated patch panels for IoT devices | Facilitates seamless connectivity and energy management | Compliance with local regulations and integration capabilities |
Healthcare Facilities | Custom patch panels for medical equipment networking | Improves patient care through reliable data connectivity | Compliance with health standards and ease of maintenance |
How are Patch Panels Custom Used in Telecommunications?
In the telecommunications sector, custom patch panels play a crucial role in managing complex network infrastructures. They help to organize numerous connections, which can reduce the risk of errors and downtime during maintenance. For international B2B buyers, especially in regions like Africa and the Middle East, sourcing high-quality patch panels that are compatible with existing systems is essential. Buyers should also consider scalability, as future growth might require more connections without significant infrastructure changes.
What Role do Custom Patch Panels Play in Data Centers?
Data centers require high-density patch panels to optimize server rack space. These custom solutions allow for organized cabling, which not only maximizes physical space but also improves airflow, essential for cooling systems. For buyers in Europe and South America, it’s vital to source panels that meet heat resistance standards and offer modular designs for potential future expansions. This ensures that the data center can adapt to increasing demands without incurring significant additional costs.
How Can Custom Patch Panels Enhance Industrial Automation?
In the realm of industrial automation, custom patch panels facilitate machine-to-machine communication, which is essential for streamlined operations. They enable quick and efficient data transfer between machines, reducing delays and improving productivity. Buyers from Africa and South America should prioritize durability and resistance to environmental factors, as industrial settings often expose equipment to harsh conditions. Ensuring that the chosen patch panels can withstand these challenges is crucial for long-term operational efficiency.
Why are Integrated Patch Panels Important for Smart Buildings?
Smart buildings rely on integrated patch panels to manage connections for various IoT devices, enhancing connectivity and energy management. These custom solutions allow for seamless communication between devices, which is vital for optimizing building operations. For buyers in Europe and the Middle East, compliance with local regulations regarding energy efficiency and connectivity standards is a key consideration when sourcing these panels. Integration capabilities with existing systems can also significantly impact the effectiveness of smart technologies implemented in the building.
How Do Custom Patch Panels Support Healthcare Facilities?
In healthcare facilities, custom patch panels are essential for networking medical equipment, which directly impacts patient care. Reliable data connectivity ensures that critical information can be accessed quickly and accurately. International buyers, particularly from regions like Egypt, should consider compliance with health standards when sourcing these panels. Additionally, ease of maintenance is crucial, as healthcare environments require minimal downtime to maintain operational efficiency and patient safety.
Related Video: How to Punch Down a Network Ethernet Patch Panel
3 Common User Pain Points for ‘patch panel custom’ & Their Solutions
Scenario 1: Difficulty in Customization for Diverse Network Needs
The Problem:
International B2B buyers often face challenges when trying to source patch panels that fit specific network configurations. For instance, a telecommunications company in Egypt may require a patch panel that accommodates both fiber optic and copper connections to support various client needs. However, many suppliers offer generic solutions that do not meet these diverse requirements, leading to inefficiencies and potential downtimes in their operations.
The Solution:
To address this issue, buyers should prioritize suppliers who offer flexible customization options. When evaluating vendors, inquire about their ability to tailor patch panels to your specifications, including port types, sizes, and labeling preferences. Additionally, consider collaborating with a manufacturer who provides design consultations to help you identify the best configurations. Utilizing advanced CAD software can also facilitate the visualization of your custom patch panel before production, ensuring that it meets all technical requirements.
Scenario 2: Managing Inventory and Supply Chain Challenges
The Problem:
Another common pain point for B2B buyers is managing inventory and the complexities of the supply chain, particularly when dealing with custom orders. A South American IT firm might find itself with a backlog of orders due to delays in receiving custom patch panels, which can affect their project timelines and client satisfaction. This issue is often exacerbated by the lack of real-time tracking and updates from suppliers.
The Solution:
To mitigate these supply chain challenges, businesses should establish strong communication channels with their suppliers. Opt for vendors that offer comprehensive project management tools that provide real-time updates on order status. Implementing a just-in-time inventory system can also help manage stock levels effectively, reducing the risk of overstocking or stockouts. Furthermore, consider suppliers that have local distribution centers in your region, which can enhance delivery speed and reliability.
Scenario 3: Ensuring Compatibility with Existing Infrastructure
The Problem:
Ensuring that custom patch panels are compatible with existing network infrastructure is crucial for seamless integration. For instance, a European enterprise may invest in a new custom patch panel, only to discover that it does not align with their current cabling and network equipment, resulting in costly modifications and downtime.
The Solution:
To avoid compatibility issues, conduct a thorough assessment of your existing network infrastructure before placing an order for custom patch panels. Create a detailed inventory of your current equipment, including specifications for cabling types, connectors, and any relevant standards. Engage with your supplier early in the design process, sharing this information to ensure that the custom patch panels are designed with compatibility in mind. Additionally, consider conducting pilot tests with a small batch of patch panels to confirm their performance within your existing setup before committing to a larger order.
Strategic Material Selection Guide for patch panel custom
When selecting materials for custom patch panels, international B2B buyers must consider various factors that influence performance, cost, and suitability for specific applications. Below, we analyze four common materials used in the manufacturing of patch panels, highlighting their properties, advantages, disadvantages, and specific considerations for buyers from regions such as Africa, South America, the Middle East, and Europe.
What Are the Key Properties of Steel for Custom Patch Panels?
Steel, particularly stainless steel, is a popular choice for custom patch panels due to its strength and durability. It typically offers high corrosion resistance, making it suitable for environments with moisture or chemicals. Steel patch panels can withstand significant temperature fluctuations and mechanical stress, ensuring longevity in demanding conditions.
Pros & Cons: The main advantage of steel is its robustness, providing excellent protection for internal components. However, it can be heavier than other materials, which may complicate installation and transportation. Additionally, while steel is generally cost-effective, the price can vary based on the grade and finish required.
Impact on Application: Steel is compatible with various media, including electrical and optical signals, making it versatile for telecommunications and data centers. Buyers should consider local regulations regarding the use of metals in electronic applications, especially in regions with stringent environmental standards.
How Does Aluminum Compare for Custom Patch Panels?
Aluminum is another prevalent material for patch panels, known for its lightweight and corrosion-resistant properties. It is often used in environments where weight is a critical factor, such as in mobile or temporary installations.
Pros & Cons: The primary advantage of aluminum is its lightweight nature, which simplifies installation and reduces shipping costs. However, it may not offer the same level of mechanical strength as steel, making it less suitable for high-stress applications. Additionally, aluminum can be more expensive than steel, depending on the alloy used.
Impact on Application: Aluminum patch panels are particularly effective in applications where weight savings are essential, such as in aerospace or mobile telecommunications. Buyers should verify compliance with international standards, such as ASTM and DIN, to ensure suitability for their specific applications.
What Are the Benefits of Using Plastic for Custom Patch Panels?
Plastic, particularly high-density polyethylene (HDPE) or polycarbonate, is increasingly used in custom patch panels due to its lightweight and insulating properties. These materials are resistant to moisture and chemicals, making them suitable for various indoor and outdoor applications.
Pros & Cons: The key advantage of plastic patch panels is their lightweight design, which facilitates easy handling and installation. They are also generally less expensive than metal options. However, plastic may have lower mechanical strength and can be susceptible to UV degradation unless treated.
Impact on Application: Plastic patch panels are ideal for environments where electrical insulation is crucial, such as residential or commercial buildings. International buyers should consider the specific environmental conditions and compliance with local standards when selecting plastic materials.
What Role Does Composite Material Play in Custom Patch Panels?
Composite materials, which combine multiple substances to enhance performance, are gaining traction in the patch panel market. These materials can offer a balance of strength, weight, and thermal stability, making them suitable for various applications.
Pros & Cons: The main advantage of composite materials is their ability to be tailored for specific applications, providing unique properties such as enhanced durability and resistance to environmental factors. However, they can be more complex and costly to manufacture, which may impact overall pricing.
Impact on Application: Composites are particularly beneficial in high-performance environments, such as data centers or industrial applications. Buyers should ensure that the composite materials meet relevant international standards to guarantee reliability and safety.
Summary Table of Material Selection for Custom Patch Panels
Material | Typical Use Case for patch panel custom | Key Advantage | Key Disadvantage/Limitation | Relative Cost (Low/Med/High) |
---|---|---|---|---|
Steel | Telecommunications, data centers | High strength and durability | Heavier, potential corrosion | Medium |
Aluminum | Mobile installations, aerospace | Lightweight and corrosion-resistant | Lower strength than steel | Medium to High |
Plastic | Residential, commercial buildings | Lightweight and cost-effective | Lower mechanical strength | Low |
Composite | High-performance industrial applications | Tailored properties | Higher manufacturing complexity | High |
This strategic material selection guide provides B2B buyers with essential insights into the various materials available for custom patch panels, helping them make informed decisions that align with their specific operational needs and regional standards.
In-depth Look: Manufacturing Processes and Quality Assurance for patch panel custom
What Are the Key Manufacturing Processes for Custom Patch Panels?
The manufacturing of custom patch panels involves several critical stages that ensure both functionality and reliability. Understanding these processes can help B2B buyers from Africa, South America, the Middle East, and Europe make informed decisions when selecting suppliers.
1. Material Preparation: What Materials Are Commonly Used?
The first step in the manufacturing process is material preparation. Custom patch panels are typically made from high-quality materials such as:
- Metal Enclosures: Usually made from aluminum or steel for durability.
- Plastic Components: Often used for housing and insulation to prevent electrical interference.
- Copper or Fiber Optic Cables: Essential for data transmission, with copper being common for traditional networks and fiber optics for high-speed connections.
B2B buyers should ensure that suppliers source materials from reputable manufacturers, as the quality of materials directly impacts the performance and longevity of the patch panels.
2. Forming: How Are Patch Panels Shaped?
The forming stage involves shaping the materials into the desired configuration. This can include:
- Laser Cutting: A precise method for cutting metal or plastic to required dimensions.
- Bending: This is often done using CNC machines to create the necessary angles and shapes for the patch panels.
- Molding: For plastic components, injection molding is commonly used to produce complex shapes.
Buyers should inquire about the technologies and equipment used in this stage, as advanced techniques can enhance precision and reduce waste.
3. Assembly: What Techniques Are Used for Assembly?
Once the components are prepared, the assembly process begins. This stage typically involves:
- Soldering and Welding: Critical for ensuring strong connections between electrical components.
- Mechanical Fastening: Using screws, nuts, and bolts to secure parts together.
- Quality Checks During Assembly: Incorporating in-process checks to catch defects early can significantly improve overall quality.
B2B buyers should look for suppliers that implement rigorous assembly protocols to minimize defects and ensure product integrity.
4. Finishing: What Are the Final Touches?
The finishing stage involves final treatments and inspections that enhance the product’s durability and appearance. This can include:
- Coating: Applying protective coatings to prevent corrosion and wear.
- Labeling: Clear labeling for ports and connections enhances usability.
- Final Inspection: A thorough check to ensure all specifications are met.
Buyers should ask suppliers about the finishing processes to ensure that the patch panels will withstand the intended environmental conditions.
How Is Quality Assurance Implemented in Custom Patch Panel Manufacturing?
Quality assurance (QA) is crucial in the manufacturing process to ensure that products meet international standards and customer specifications.
What International Standards Should B2B Buyers Consider?
International standards such as ISO 9001 are essential for ensuring quality management systems are in place. This standard focuses on:
- Customer Satisfaction: Ensuring that products meet customer needs.
- Process Improvement: Continuous evaluation and improvement of manufacturing processes.
Additionally, industry-specific certifications like CE (Conformité Européenne) for European markets and API (American Petroleum Institute) for oil and gas sectors may be relevant depending on the application of the patch panels.
What Are the Key QC Checkpoints in Manufacturing?
Quality control (QC) checkpoints are critical for maintaining high standards throughout the manufacturing process. Key checkpoints include:
- Incoming Quality Control (IQC): Inspecting raw materials upon receipt to ensure they meet specified criteria.
- In-Process Quality Control (IPQC): Monitoring processes during production to catch defects early.
- Final Quality Control (FQC): A comprehensive inspection of the finished product before shipping.
B2B buyers should inquire about these checkpoints and the methodologies employed to ensure consistent quality.
What Common Testing Methods Are Used?
Testing methods play a vital role in quality assurance. Common tests include:
- Electrical Testing: Ensuring that connections work correctly and meet voltage and current specifications.
- Mechanical Testing: Assessing the strength and durability of the patch panels under various conditions.
- Environmental Testing: Evaluating performance in different temperature and humidity levels.
Understanding the testing methods used can give buyers confidence in the reliability of the products.
How Can B2B Buyers Verify Supplier Quality Control?
Verifying a supplier’s quality control processes is essential for ensuring that the products meet the required standards. Here are some strategies B2B buyers can use:
What Should Buyers Look for in Supplier Audits?
Conducting or requesting audits of potential suppliers can provide insights into their quality management systems. Buyers should focus on:
- Certification Compliance: Verify that suppliers hold relevant certifications.
- Process Documentation: Review records of manufacturing processes and QC checks.
- Employee Training Programs: Assess whether staff are trained in quality control practices.
How Can Buyers Use Reports and Third-Party Inspections?
Suppliers should provide regular QC reports detailing inspection results, testing outcomes, and any corrective actions taken. Buyers may also consider hiring third-party inspection services to conduct independent assessments of suppliers. This adds an extra layer of assurance regarding product quality.
What Are the Quality Control Nuances for International B2B Buyers?
For international buyers, particularly those from Africa, South America, the Middle East, and Europe, there are additional nuances to consider:
- Regional Regulations: Buyers must understand local regulations that may affect product specifications and certifications.
- Cultural Differences: Variations in business practices and communication styles may influence supplier relationships and negotiations.
- Logistics and Supply Chain Considerations: Ensure that suppliers have robust logistics plans to manage international shipping, including customs clearance and delivery timelines.
By being aware of these factors, B2B buyers can make more informed decisions and foster successful partnerships with manufacturers of custom patch panels.
Practical Sourcing Guide: A Step-by-Step Checklist for ‘patch panel custom’
In the competitive landscape of international B2B procurement, sourcing custom patch panels requires a strategic approach to ensure that the products meet both technical specifications and business needs. This guide provides a step-by-step checklist that will assist buyers from Africa, South America, the Middle East, and Europe in making informed purchasing decisions.
Step 1: Define Your Technical Specifications
Before initiating the sourcing process, it’s essential to have a clear understanding of your technical requirements. Consider factors such as size, port density, connectivity options (e.g., fiber vs. copper), and environmental conditions (e.g., temperature or humidity). A well-defined specification helps to communicate your needs effectively to potential suppliers.
- Identify Industry Standards: Ensure compliance with relevant industry standards, such as ISO or IEC, to avoid compatibility issues.
Step 2: Research Potential Suppliers
Conduct thorough research to identify potential suppliers that specialize in custom patch panels. Utilize online directories, industry trade shows, and recommendations from industry peers to compile a list of candidates.
- Check Supplier Reputation: Look for reviews, ratings, and testimonials to gauge the reliability and credibility of each supplier.
Step 3: Evaluate Supplier Certifications
Verify that potential suppliers hold the necessary certifications that demonstrate their commitment to quality and safety. Certifications such as ISO 9001 for quality management systems or UL certification for safety can provide assurance of the supplier’s capabilities.
- Request Documentation: Ask suppliers for copies of their certifications and quality control processes to ensure compliance with your expectations.
Step 4: Request Samples and Prototypes
Once you have shortlisted suppliers, request samples or prototypes of their custom patch panels. This allows you to evaluate the quality, functionality, and design before making a large-scale commitment.
- Perform Functional Testing: Ensure that the samples meet your technical specifications through rigorous testing, including stress tests and compatibility checks with existing systems.
Step 5: Assess Pricing and Payment Terms
After evaluating the quality of the products, it’s time to discuss pricing and payment terms. Compare quotes from different suppliers while considering the total cost of ownership, which includes shipping, duties, and potential tariffs.
- Negotiate Terms: Don’t hesitate to negotiate better pricing or flexible payment terms, especially for bulk orders or long-term partnerships.
Step 6: Verify Delivery Times and Logistics
Understanding the logistics involved in the delivery of your custom patch panels is critical. Confirm lead times and shipping methods to ensure timely delivery that aligns with your project timelines.
- Consider Local Regulations: Be aware of import regulations in your country to avoid unexpected delays or complications during customs clearance.
Step 7: Establish a Communication Plan
Effective communication is key to a successful procurement process. Establish a clear plan for ongoing communication with your chosen supplier regarding updates, potential issues, and order status.
- Set Up Regular Check-Ins: Schedule periodic meetings or updates to discuss progress and address any concerns that may arise during production and delivery.
By following this step-by-step checklist, B2B buyers can navigate the complexities of sourcing custom patch panels, ensuring that their procurement process is efficient and aligned with their business objectives.
Comprehensive Cost and Pricing Analysis for patch panel custom Sourcing
What Are the Key Cost Components for Custom Patch Panels?
When analyzing the cost structure for custom patch panels, several key components must be considered:
-
Materials: The choice of materials significantly influences the overall cost. Common materials include high-quality metals, plastics, and specialized coatings that enhance durability and conductivity. Opting for premium materials may increase upfront costs but can lead to better long-term performance.
-
Labor: Labor costs vary based on the complexity of the design and the location of the manufacturing facility. Skilled labor is essential for precision in customization, which can elevate costs. Buyers should consider regions with a balance of skilled labor availability and competitive wages.
-
Manufacturing Overhead: This includes costs associated with utilities, maintenance, and equipment depreciation. Facilities with advanced manufacturing technologies may have higher overheads, but this can be offset by increased efficiency and output quality.
-
Tooling: Custom patch panels often require specialized tooling. This one-time cost can be significant but is essential for achieving precise specifications. Buyers should inquire about tooling costs and whether they are included in the pricing.
-
Quality Control (QC): Investing in rigorous QC processes ensures that the final product meets the required standards. While this adds to the cost, it mitigates the risk of defects, which can lead to higher expenses in the long run.
-
Logistics: Shipping costs can vary greatly depending on distance, weight, and the chosen shipping method. International buyers should consider local tariffs and shipping fees when evaluating total costs.
-
Margin: Suppliers typically incorporate a margin that reflects their business model and market conditions. Understanding the margin expectations can aid in negotiations.
How Do Price Influencers Impact Custom Patch Panel Costs?
Several factors can influence the pricing of custom patch panels:
-
Volume/MOQ: Minimum Order Quantities (MOQs) can significantly affect pricing. Larger orders often benefit from bulk discounts, while smaller orders may incur higher per-unit costs. Buyers should evaluate their needs and negotiate MOQs accordingly.
-
Specifications and Customization: The level of customization required will directly impact the cost. More complex designs with unique features or specifications will generally lead to higher prices.
-
Materials and Quality Certifications: The choice of materials and any required quality certifications (like ISO or RoHS compliance) can affect costs. Buyers should weigh the importance of certifications against potential price increases.
-
Supplier Factors: The reputation and reliability of the supplier can also influence pricing. Established suppliers with a track record of quality may charge more, but they often provide better guarantees and support.
-
Incoterms: Understanding the Incoterms applied to the transaction is crucial. They define responsibilities for shipping, insurance, and tariffs, which can impact the total cost and liability during transport.
What Buyer Tips Can Help Achieve Cost-Efficiency in Custom Patch Panel Sourcing?
-
Effective Negotiation: Establishing a good relationship with suppliers can lead to better negotiation outcomes. Transparency about your requirements and budget can help suppliers provide more tailored pricing options.
-
Total Cost of Ownership (TCO): When evaluating costs, consider the Total Cost of Ownership, which includes not just the purchase price but also shipping, installation, maintenance, and potential downtime. A lower upfront cost may not always equate to better value.
-
Pricing Nuances for International Buyers: For buyers from regions like Africa, South America, the Middle East, and Europe, understanding local market dynamics is essential. Currency fluctuations, import duties, and regional demand can affect pricing strategies.
-
Request for Quotes (RFQ): Utilize RFQs to gather competitive pricing from multiple suppliers. This not only helps in comparing costs but also encourages suppliers to offer their best prices.
-
Consider Long-Term Partnerships: Building long-term relationships with suppliers can yield advantages such as price stability, priority production, and access to new products or technologies.
Disclaimer on Indicative Prices
Prices for custom patch panels can vary widely based on the aforementioned factors. Buyers are encouraged to conduct thorough market research and obtain multiple quotes to ensure competitive pricing tailored to their specific needs.
Alternatives Analysis: Comparing patch panel custom With Other Solutions
In the realm of network infrastructure, selecting the right solution for organizing and managing cabling is crucial for operational efficiency. While custom patch panels are a popular choice for many businesses, there are several alternative solutions that can also meet the needs of international B2B buyers. This section explores these alternatives, comparing their performance, cost, ease of implementation, maintenance, and best use cases.
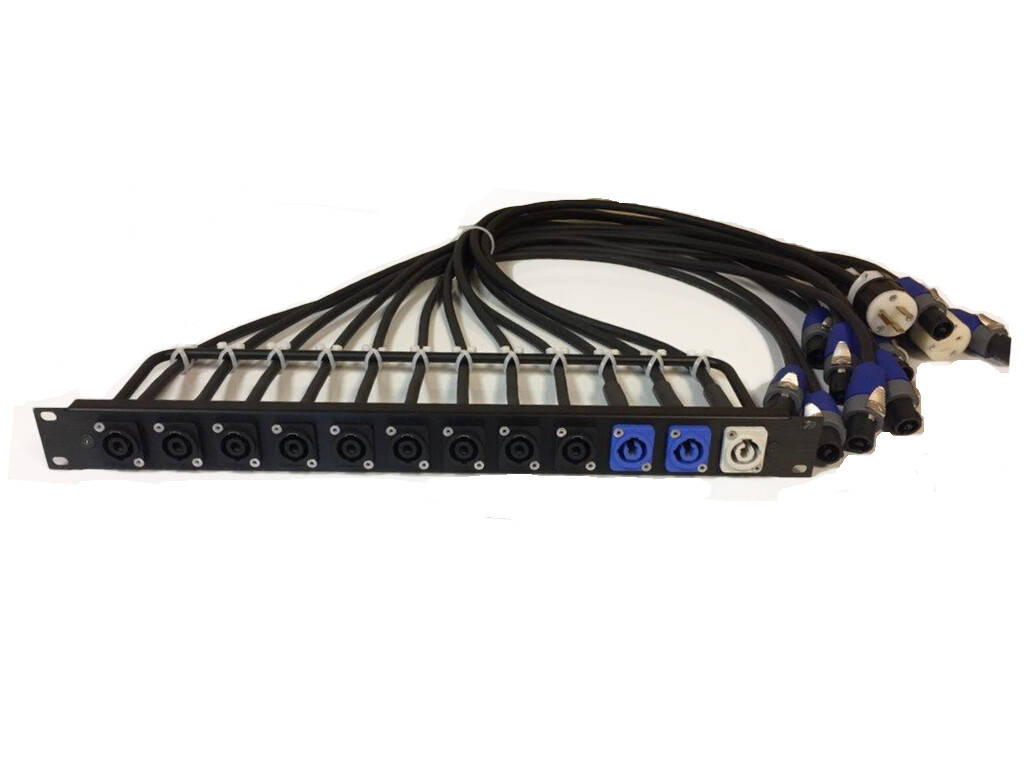
A stock image related to patch panel custom.
Comparison Aspect | Patch Panel Custom | Fiber Optic Distribution Frame | Network Switch |
---|---|---|---|
Performance | High flexibility and scalability | Excellent for high-speed data transfer | Varies by model, generally good for multiple devices |
Cost | Higher initial investment | Moderate to high depending on fiber type | Generally lower, especially for unmanaged switches |
Ease of Implementation | Moderate; requires some technical skill | Moderate; installation of fiber can be complex | High; plug-and-play options available |
Maintenance | Low to moderate; requires periodic checks | Moderate; fiber maintenance can be specialized | Low; minimal upkeep required |
Best Use Case | Custom configurations for specific needs | High-speed networks requiring fiber optics | Standard networking for small to medium businesses |
What Are the Benefits and Drawbacks of Using a Fiber Optic Distribution Frame?
Fiber optic distribution frames (ODFs) are a robust alternative to custom patch panels, particularly in environments demanding high-speed data transfer. One of the primary benefits of fiber optic solutions is their ability to support significantly higher bandwidths, making them ideal for data centers and telecom applications. However, the installation and maintenance of fiber optic systems can be more complex, requiring specialized knowledge and tools. For companies in regions like Europe and the Middle East where high-speed data is critical, ODFs can be an excellent investment despite the initial learning curve.
How Do Network Switches Compare to Patch Panels in Terms of Flexibility?
Network switches provide a straightforward alternative to patch panels, particularly for smaller networks. Their ease of use is a significant advantage; many models are designed to be plug-and-play, making them accessible even for teams with limited technical expertise. However, switches typically do not offer the same level of customization as patch panels. They can also become costly when scaling up, especially if managed switches are required for more control over network traffic. For businesses in Africa and South America looking for quick deployment, switches may be the most practical choice, but they may lack the tailored performance of custom patch panels.
How to Choose the Right Solution for Your Business Needs?
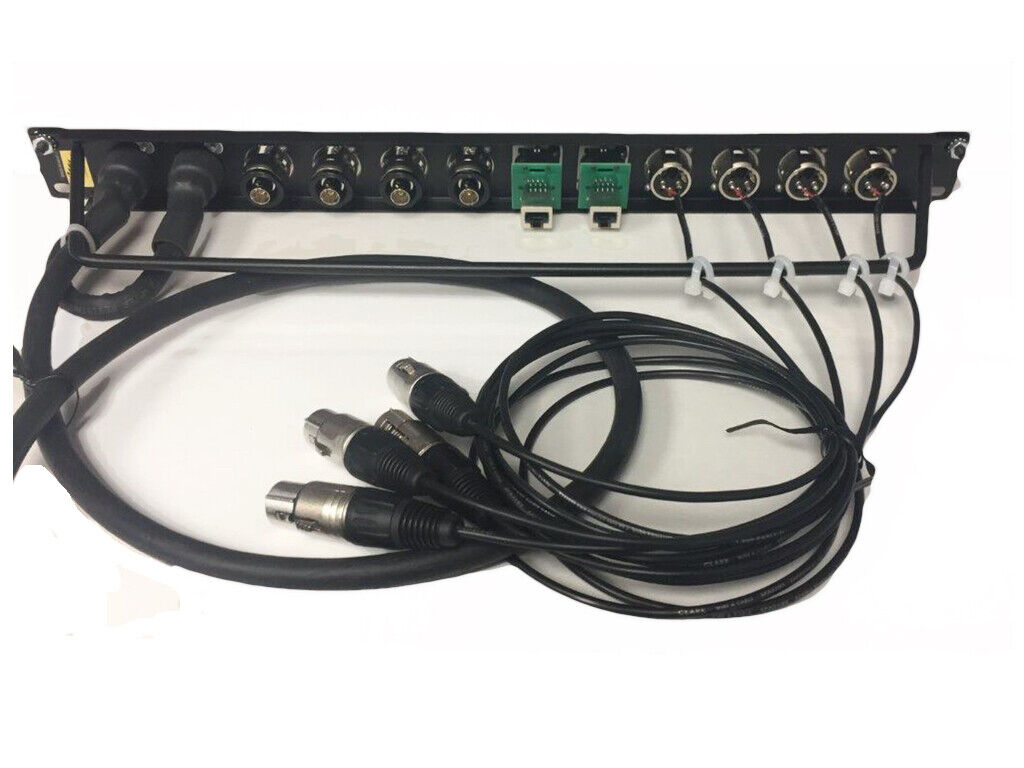
A stock image related to patch panel custom.
When selecting a network solution, B2B buyers should evaluate their specific operational requirements, budget constraints, and future growth projections. Custom patch panels are ideal for businesses needing tailored configurations and scalability, especially in complex environments. In contrast, fiber optic distribution frames are suited for high-performance requirements, while network switches offer simplicity and lower upfront costs. Ultimately, the choice will depend on balancing performance needs with cost-effectiveness and ease of use, ensuring the selected solution aligns with both current and future business objectives.
Essential Technical Properties and Trade Terminology for patch panel custom
Understanding the technical specifications and industry terminology related to custom patch panels is crucial for international B2B buyers. This knowledge aids in making informed purchasing decisions and helps in streamlining communication with manufacturers and suppliers.
What Are the Key Technical Properties of Custom Patch Panels?
1. Material Grade: Why Does It Matter?
The material grade of a patch panel, typically aluminum or steel, influences its durability and performance. For instance, aluminum is lightweight and corrosion-resistant, ideal for environments with high humidity, while steel offers better strength and is suitable for heavy-duty applications. Choosing the right material ensures longevity and reliability, which is essential for maintaining network integrity.
2. Tolerance: How Does It Impact Performance?
Tolerance refers to the acceptable deviation in dimensions during manufacturing. High tolerance levels in patch panels ensure that connectors fit securely, reducing the risk of signal loss or degradation. For B2B buyers, specifying tight tolerances can enhance system performance, especially in high-frequency applications.
3. Port Density: What Should You Consider?
Port density indicates how many connections a patch panel can accommodate within a given space. High port density is crucial for maximizing network performance in limited physical space. Buyers should evaluate their current and future network needs to select a patch panel that supports scalability without compromising performance.
4. Mounting Style: Which One Suits Your Needs?
Patch panels can be designed for wall-mounting or rack-mounting. The choice between these styles depends on the available space and installation preferences. Understanding the mounting requirements helps in ensuring that the patch panel integrates seamlessly into existing infrastructure.
5. Shielding: Why Is It Important for Signal Integrity?
Shielding refers to the protective layer that prevents electromagnetic interference (EMI) from affecting the signals transmitted through the patch panel. Effective shielding is essential for maintaining high data integrity, particularly in environments with significant electronic noise. B2B buyers should prioritize shielded options for critical applications.
What Are the Common Trade Terms in the Patch Panel Industry?
1. OEM: What Does It Mean for Custom Solutions?
OEM stands for Original Equipment Manufacturer. In the context of custom patch panels, an OEM produces products that are rebranded by other companies. Understanding OEM relationships can help buyers leverage quality manufacturing while ensuring that the product meets their specific requirements.
2. MOQ: Why Is It Significant in Bulk Purchasing?
MOQ stands for Minimum Order Quantity. This term indicates the smallest amount of product a supplier is willing to sell. For international buyers, understanding MOQ is crucial for budgeting and inventory management, especially when negotiating terms with manufacturers.
3. RFQ: How Does It Facilitate Procurement?
RFQ, or Request for Quotation, is a standard process used by buyers to solicit price quotes from suppliers. Crafting a detailed RFQ that specifies technical requirements and quantities can lead to better pricing and more tailored offerings, making it a vital tool for B2B procurement.
4. Incoterms: What Are They and Why Are They Important?
Incoterms are international commercial terms that define the responsibilities of buyers and sellers in shipping and logistics. Familiarity with these terms helps buyers understand shipping costs, risks, and delivery responsibilities, ensuring smoother transactions across borders.
5. Lead Time: How Does It Affect Project Planning?
Lead time refers to the time taken from placing an order to receiving the product. For B2B buyers, understanding lead times is essential for project scheduling and ensuring that the required patch panels are available when needed. Clear communication with suppliers about lead times can prevent delays in deployment.
Incorporating these technical properties and trade terminologies into your procurement strategy will empower you to make informed decisions, optimize your supply chain, and enhance overall operational efficiency.
Navigating Market Dynamics and Sourcing Trends in the patch panel custom Sector
What Are the Current Market Dynamics and Key Trends in the Patch Panel Custom Sector?
The patch panel custom sector is witnessing transformative market dynamics driven by technological advancements, increasing network demands, and the globalization of supply chains. International B2B buyers, particularly from Africa, South America, the Middle East, and Europe, are now navigating a landscape characterized by rapid digitalization and the growing necessity for customized networking solutions. This shift is propelled by the rise of smart cities, IoT devices, and enhanced data center requirements, demanding more versatile and reliable patch panel solutions.
Emerging trends in sourcing indicate a strong inclination towards modular and flexible designs, allowing for easier scalability and adaptability to changing network needs. Buyers are increasingly prioritizing suppliers that offer not just products, but comprehensive solutions that include installation, support, and future upgrades. Moreover, the proliferation of e-commerce platforms has made it easier for international buyers to access suppliers worldwide, leading to increased competition and better pricing options.
Regional considerations are also vital; for example, in Europe, stringent regulations on data privacy and sustainability are influencing purchasing decisions. In contrast, African markets are experiencing a surge in mobile connectivity, driving demand for cost-effective yet high-quality networking solutions. Understanding these regional dynamics will enable B2B buyers to make more informed decisions when sourcing patch panels.
How Can Sustainability and Ethical Sourcing Impact Your Supply Chain in the Patch Panel Custom Sector?
Sustainability and ethical sourcing are becoming pivotal in the decision-making processes of international B2B buyers. The environmental impact of manufacturing processes in the patch panel custom sector is under scrutiny, with a growing emphasis on minimizing carbon footprints and reducing waste. Buyers are increasingly seeking suppliers that prioritize eco-friendly materials and practices, such as using recycled metals and sustainable plastics in their products.
Furthermore, ethical supply chains are essential for building brand reputation and customer loyalty. International buyers are encouraged to partner with manufacturers who have transparent sourcing practices and adhere to fair labor standards. Certifications such as ISO 14001 for environmental management and the Global Recycle Standard (GRS) can serve as indicators of a supplier’s commitment to sustainability.
By prioritizing suppliers that align with these values, B2B buyers not only contribute to a more sustainable future but also position themselves favorably in a market that increasingly values corporate responsibility. This alignment can lead to long-term benefits, including reduced regulatory risks, improved operational efficiencies, and enhanced brand image.
What Is the Evolution of the Patch Panel Custom Sector and Its Relevance to B2B Buyers?
The patch panel custom sector has evolved significantly over the past few decades, transitioning from basic connectivity solutions to highly specialized, customizable products designed to meet specific networking needs. Initially, patch panels were primarily used for telephone networks; however, the advent of data networking technologies has transformed their role into critical components of modern IT infrastructure.
With the rise of high-speed internet and the increasing complexity of networking environments, manufacturers began to offer custom solutions that allow for greater flexibility and scalability. This evolution has led to the development of features such as color-coded ports for easier management and the integration of advanced technologies like fiber optics.
For B2B buyers, understanding this evolution is crucial, as it informs purchasing decisions and supplier evaluations. Buyers should look for manufacturers who not only provide the latest innovations but also have a track record of adapting to the rapidly changing technology landscape. By choosing suppliers that are ahead of the curve, international buyers can ensure they are equipped with the most effective and future-proof networking solutions.
Frequently Asked Questions (FAQs) for B2B Buyers of patch panel custom
-
How do I solve compatibility issues with patch panels when sourcing custom solutions?
To address compatibility issues when sourcing custom patch panels, start by conducting a thorough assessment of your existing network infrastructure. Identify the specifications of your current cables and connectors, such as category ratings (e.g., Cat5e, Cat6) and connector types (e.g., RJ45, LC). Collaborate closely with your supplier to ensure they understand your requirements and can offer solutions tailored to your specific needs. Additionally, request samples or prototypes to test compatibility before committing to a larger order. -
What is the best way to evaluate suppliers for custom patch panels?
When evaluating suppliers for custom patch panels, focus on their industry experience, certifications, and customer reviews. Look for suppliers who specialize in B2B solutions and have a proven track record of delivering quality products. Request references from previous clients, and consider conducting site visits or virtual meetings to gauge their production capabilities. Additionally, inquire about their compliance with international standards and regulations to ensure reliability and quality assurance. -
What are the common minimum order quantities (MOQ) for custom patch panels?
Minimum order quantities for custom patch panels can vary significantly based on the supplier and the level of customization required. Typically, MOQs may range from 50 to 500 units. However, many suppliers are willing to negotiate MOQs, especially for long-term partnerships or larger contracts. It’s advisable to discuss your specific needs with potential suppliers to understand their flexibility and any associated cost implications. -
What payment terms should I expect when sourcing custom patch panels internationally?
Payment terms for international sourcing of custom patch panels usually involve a combination of upfront deposits and balance payments upon delivery. Common practices include a 30% deposit upon order confirmation and the remaining 70% before shipment. Some suppliers may offer letters of credit or other financing options, particularly for larger orders. Ensure to clarify payment terms upfront to avoid misunderstandings and consider using secure payment methods to protect your transaction. -
How can I ensure quality assurance for custom patch panels?
To ensure quality assurance for custom patch panels, request detailed product specifications and quality control processes from your supplier. Implement a quality assurance plan that includes pre-production samples, in-process inspections, and final product testing. Consider third-party inspections or audits to verify compliance with international standards. Establish a clear communication channel with your supplier to address any quality concerns promptly and ensure that all products meet your expectations. -
What logistics considerations should I keep in mind when importing custom patch panels?
When importing custom patch panels, logistics considerations include shipping methods, lead times, and customs clearance processes. Evaluate whether air freight or sea freight is more suitable based on your urgency and budget. Understand the tariffs and import duties applicable to your country and factor these into your cost calculations. Work closely with your supplier to ensure proper documentation is provided to facilitate smooth customs clearance. -
How can I customize patch panels to suit my specific network requirements?
Customizing patch panels to meet specific network requirements involves determining the number of ports, types of connectors, and additional features such as labeling and color coding. Engage with your supplier early in the design process to discuss your needs and explore available options. Provide them with detailed specifications, including dimensions and material preferences, to ensure the final product aligns with your operational goals. -
What are the benefits of sourcing custom patch panels from manufacturers in Africa, South America, the Middle East, and Europe?
Sourcing custom patch panels from manufacturers in Africa, South America, the Middle East, and Europe offers several advantages, including access to local expertise, potentially lower shipping costs, and reduced lead times. Additionally, many manufacturers in these regions are increasingly adopting international quality standards, making them competitive in the global market. Partnering with local suppliers can also facilitate easier communication and foster long-term relationships, which are vital for successful B2B transactions.
Important Disclaimer & Terms of Use
⚠️ Important Disclaimer
The information provided in this guide, including content regarding manufacturers, technical specifications, and market analysis, is for informational and educational purposes only. It does not constitute professional procurement advice, financial advice, or legal advice.
While we have made every effort to ensure the accuracy and timeliness of the information, we are not responsible for any errors, omissions, or outdated information. Market conditions, company details, and technical standards are subject to change.
B2B buyers must conduct their own independent and thorough due diligence before making any purchasing decisions. This includes contacting suppliers directly, verifying certifications, requesting samples, and seeking professional consultation. The risk of relying on any information in this guide is borne solely by the reader.
Strategic Sourcing Conclusion and Outlook for patch panel custom
What Are the Key Takeaways for B2B Buyers in Custom Patch Panels?
In conclusion, strategic sourcing for custom patch panels is not merely a procurement process; it is a vital component of enhancing operational efficiency and ensuring quality in network infrastructure. International B2B buyers from regions such as Africa, South America, the Middle East, and Europe must prioritize suppliers that offer tailored solutions, robust customer support, and scalability to meet their unique needs. Leveraging local market insights and global best practices can significantly impact supply chain resilience and cost-effectiveness.
How Can Strategic Sourcing Enhance Your Business Operations?
By engaging in strategic sourcing, businesses can foster long-term relationships with manufacturers who understand the nuances of local markets while adhering to international standards. This approach not only mitigates risks associated with supply chain disruptions but also allows for innovation in product offerings, which is crucial in today’s fast-paced tech environment.
What’s Next for International B2B Buyers?
As the demand for custom patch panels continues to rise, staying ahead of market trends and technological advancements will be essential. Buyers should actively seek partnerships with forward-thinking suppliers and invest in research to anticipate future needs. Embrace this opportunity to optimize your sourcing strategy, ensuring your organization remains competitive and agile in an ever-evolving landscape. Your proactive engagement today will shape the success of your network solutions tomorrow.