Optimize Costs with Custom Heat Exchangers: A Complete Guide (2025)
Introduction: Navigating the Global Market for heat exchangers custom
In the increasingly interconnected global marketplace, sourcing custom heat exchangers presents a unique set of challenges for international B2B buyers. Companies from diverse regions, including Africa, South America, the Middle East, and Europe, must navigate a complex landscape of suppliers, regulations, and technological advancements. This guide offers a comprehensive overview of the custom heat exchanger market, addressing crucial aspects such as types of heat exchangers, their applications across various industries, and strategic supplier vetting processes.
By delving into the intricacies of cost analysis, quality standards, and logistics, this guide empowers B2B buyers to make informed purchasing decisions. Whether you’re based in France or Brazil, understanding the specific requirements and operational nuances of your region is essential to ensure compliance and efficiency.
Furthermore, this resource emphasizes the importance of aligning your purchasing strategy with the latest industry trends and innovations in heat exchange technology. With actionable insights tailored to the unique needs of international buyers, you will be equipped to identify the right suppliers and negotiate favorable terms. As you navigate the global market for custom heat exchangers, this guide serves as your essential companion, helping you to not only overcome challenges but also seize opportunities for growth and competitive advantage.
Understanding heat exchangers custom Types and Variations
Type Name | Key Distinguishing Features | Primary B2B Applications | Brief Pros & Cons for Buyers |
---|---|---|---|
Shell and Tube | Composed of a series of tubes; high heat transfer efficiency | Oil & gas, chemical processing | Pros: Versatile, high capacity. Cons: Larger footprint, potential for leakage. |
Plate Heat Exchanger | Thin plates stacked together; compact design | HVAC, food processing | Pros: Space-efficient, easy maintenance. Cons: Limited pressure handling. |
Air-Cooled Heat Exchanger | Uses air to cool fluids; no water required | Power generation, refrigeration | Pros: Environmentally friendly, lower operational costs. Cons: Less effective in humid conditions. |
Double-Pipe Heat Exchanger | Simple design with two pipes; easy to construct | Water heating, small-scale applications | Pros: Cost-effective, straightforward design. Cons: Limited efficiency, not suitable for high flow rates. |
Fin Fan Heat Exchanger | Utilizes fans to enhance air flow over fins | Industrial cooling, petrochemical plants | Pros: High cooling efficiency, adaptable to various environments. Cons: Requires power for fans, noise considerations. |
What Are the Characteristics of Shell and Tube Heat Exchangers?
Shell and tube heat exchangers consist of a series of tubes, with one set carrying the hot fluid and the other the cold fluid. This design allows for a high level of heat transfer efficiency, making it ideal for applications in the oil and gas industry as well as chemical processing. When considering a purchase, B2B buyers should evaluate the size requirements, material compatibility, and maintenance needs, as these systems can be larger and may require more space than other types.
How Do Plate Heat Exchangers Stand Out?
Plate heat exchangers are characterized by their compact design, consisting of thin plates stacked together to maximize surface area for heat transfer. They are commonly used in HVAC and food processing applications due to their efficiency and ease of maintenance. Buyers should consider factors such as the specific heat transfer requirements, pressure handling capabilities, and the potential for fouling when selecting a plate heat exchanger.
What Are the Benefits of Air-Cooled Heat Exchangers?
Air-cooled heat exchangers utilize ambient air to cool fluids, eliminating the need for water, which can be a significant advantage in regions where water is scarce. They are widely used in power generation and refrigeration applications. When purchasing, B2B buyers should assess the local climate, as these systems may be less effective in humid conditions, and consider the operational cost savings associated with reduced water usage.
Why Choose Double-Pipe Heat Exchangers?
Double-pipe heat exchangers feature a straightforward design consisting of one pipe inside another, making them easy to construct and cost-effective. They are suitable for water heating and small-scale applications. However, buyers should be aware that their efficiency is limited compared to other types, and they are not ideal for high flow rates or complex processes.
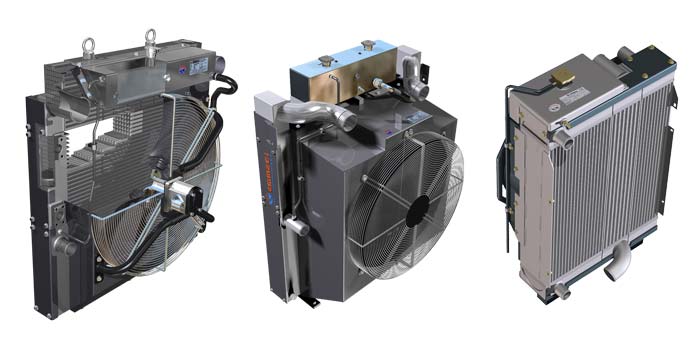
A stock image related to heat exchangers custom.
What Are the Applications of Fin Fan Heat Exchangers?
Fin fan heat exchangers enhance cooling efficiency by using fans to increase airflow over finned surfaces. They are commonly found in industrial cooling and petrochemical plants. Buyers should consider the power requirements for the fans, as well as potential noise issues, when evaluating these systems. Their adaptability to various environments makes them a versatile option for many industrial applications.
Related Video: Heat Exchangers Types | How Many Types of Heat Exchanger |
Key Industrial Applications of heat exchangers custom
Industry/Sector | Specific Application of heat exchangers custom | Value/Benefit for the Business | Key Sourcing Considerations for this Application |
---|---|---|---|
Oil and Gas | Heat recovery in refining processes | Increases energy efficiency, reduces operational costs | Material compatibility, high-pressure ratings |
Food and Beverage | Pasteurization and cooling in dairy production | Ensures product safety, improves shelf life | Hygiene standards, corrosion resistance |
Chemical Manufacturing | Temperature control in chemical reactions | Enhances reaction efficiency, minimizes waste | Custom design for specific chemicals, thermal efficiency |
HVAC Systems | Heat exchange in district heating systems | Reduces energy consumption, improves system performance | Size and capacity requirements, environmental regulations |
Power Generation | Cooling in turbine systems | Increases operational reliability, enhances energy output | High thermal conductivity materials, maintenance access |
How are Custom Heat Exchangers Used in the Oil and Gas Sector?
In the oil and gas industry, custom heat exchangers play a crucial role in heat recovery during refining processes. By efficiently transferring heat between fluids, these exchangers enhance energy efficiency, leading to significant reductions in operational costs. International buyers in regions like the Middle East, where oil production is paramount, must consider material compatibility and high-pressure ratings to withstand extreme conditions and ensure longevity.
What Role Do Custom Heat Exchangers Play in the Food and Beverage Industry?
In the food and beverage sector, particularly in dairy production, custom heat exchangers are essential for pasteurization and cooling processes. They help maintain product safety and extend shelf life by ensuring that harmful bacteria are eliminated during processing. B2B buyers, especially from Europe and South America, should focus on hygiene standards and corrosion resistance when sourcing these systems to comply with health regulations and ensure product integrity.
Why Are Custom Heat Exchangers Important in Chemical Manufacturing?
Chemical manufacturing relies heavily on custom heat exchangers for effective temperature control during various chemical reactions. These systems enhance reaction efficiency and minimize waste, contributing to overall production quality. International buyers should prioritize custom designs tailored for specific chemicals, ensuring optimal thermal efficiency while addressing any unique operational challenges faced in their regions, such as fluctuating temperatures.
How Do Custom Heat Exchangers Improve HVAC Systems?
In HVAC systems, custom heat exchangers are vital for district heating applications. They facilitate heat transfer between different sources, significantly reducing energy consumption and improving overall system performance. Buyers from Africa and Europe should consider size and capacity requirements along with compliance with local environmental regulations to ensure that the systems not only meet operational needs but also align with sustainability goals.
What Benefits Do Custom Heat Exchangers Offer in Power Generation?
In power generation, custom heat exchangers are used for cooling turbine systems, which is critical for maintaining operational reliability and enhancing energy output. These systems help manage the high temperatures generated during energy production. B2B buyers should focus on sourcing materials with high thermal conductivity and ensuring easy maintenance access to optimize performance and reduce downtime in their operations.
Related Video: Heat Exchangers Explained: Types, Working & Industrial Applications❄️🔥
3 Common User Pain Points for ‘heat exchangers custom’ & Their Solutions
Scenario 1: Inadequate Thermal Performance in Custom Heat Exchangers
The Problem:
International B2B buyers often face significant challenges when their custom heat exchangers do not meet the expected thermal performance requirements. This situation can arise due to various factors, including incorrect specifications, subpar materials, or inadequate design for specific applications. For example, a manufacturing plant in Brazil might purchase a heat exchanger that fails to transfer heat efficiently under local operating conditions, leading to increased energy costs and reduced operational efficiency.
The Solution:
To overcome this issue, buyers must engage in a comprehensive needs assessment before purchasing. This includes collaborating closely with manufacturers to clearly define thermal performance expectations based on specific application parameters. Buyers should request detailed thermal calculations and simulations to validate performance claims. Additionally, specifying high-quality materials that are compatible with the process fluids can enhance thermal efficiency. Lastly, consider leveraging the expertise of thermal engineers during the design phase to optimize the configuration of the heat exchanger for maximum performance.
Scenario 2: Long Lead Times for Custom Heat Exchanger Production
The Problem:
A frequent pain point for B2B buyers is the long lead times associated with the production of custom heat exchangers. Companies in regions such as the Middle East may require urgent replacements or modifications to their systems but find themselves facing delays due to manufacturing bottlenecks or a lack of available resources. This delay can lead to operational downtime and significant financial losses, especially in industries where temperature regulation is critical.
The Solution:
To mitigate this risk, buyers should proactively establish relationships with multiple suppliers to ensure flexibility in sourcing. When seeking custom heat exchangers, it is advisable to inquire about the manufacturer’s production capabilities, including their capacity to handle urgent orders. Implementing a just-in-time inventory system can also help manage lead times effectively. Buyers might consider investing in stockpiling standard components that can be quickly assembled into custom solutions when needed. Additionally, leveraging local suppliers may significantly reduce transportation times and costs.
Scenario 3: Compliance with Industry Standards and Regulations
The Problem:
B2B buyers often struggle with ensuring that their custom heat exchangers comply with local and international industry standards and regulations. For instance, a company in Europe may need to adhere to stringent environmental regulations, while a buyer in Africa might face challenges related to local safety standards. Failure to comply can result in costly fines, project delays, and even operational shutdowns.
The Solution:
To address compliance issues, buyers should conduct thorough research on the relevant regulations governing their industry and region. Engaging with legal or compliance experts early in the procurement process can provide valuable insights into the necessary standards. When sourcing custom heat exchangers, buyers must insist on certifications and documentation that prove compliance with relevant standards, such as ASME, PED, or ISO. It is also beneficial to work with manufacturers who are experienced in navigating regulatory landscapes. Buyers should also consider conducting regular audits of their suppliers to ensure ongoing compliance and mitigate any potential risks associated with non-compliance.
Strategic Material Selection Guide for heat exchangers custom
When selecting materials for custom heat exchangers, it is essential to consider the specific requirements of the application, including temperature and pressure ratings, corrosion resistance, and compatibility with the media being processed. Below, we analyze four common materials used in heat exchanger manufacturing, highlighting their properties, advantages, disadvantages, and considerations for international B2B buyers.
What are the Key Properties of Stainless Steel in Heat Exchangers?
Stainless steel is one of the most widely used materials for heat exchangers due to its excellent corrosion resistance and high-temperature performance. It typically has a temperature rating of up to 800°F (427°C) and can handle high pressures, making it suitable for various applications, including chemical processing and food production.
Pros & Cons: The primary advantages of stainless steel include its durability, resistance to rust, and ease of cleaning. However, it is relatively expensive compared to other materials and may require more complex manufacturing processes, which can increase lead times.
Impact on Application: Stainless steel is compatible with a wide range of media, including water, oils, and various chemicals, making it a versatile choice for many industries.
Considerations for International Buyers: Buyers from regions such as Europe and the Middle East should ensure compliance with standards like ASTM A240 or EN 10088. In Africa and South America, local sourcing of stainless steel may also be a factor to consider, as it can affect delivery times and costs.
How Does Copper Perform as a Material for Heat Exchangers?
Copper is another popular choice for heat exchangers, particularly in applications requiring excellent thermal conductivity. With a thermal conductivity rating significantly higher than stainless steel, copper can efficiently transfer heat, making it ideal for HVAC systems and refrigeration.
Pros & Cons: The key advantage of copper is its superior heat transfer capabilities, which can lead to smaller and more efficient designs. However, copper is prone to corrosion in certain environments, particularly when exposed to acidic or alkaline media, which can limit its application.
Impact on Application: Copper is particularly well-suited for applications involving water and refrigerants but may not be ideal for corrosive chemicals.
Considerations for International Buyers: Buyers should be aware of the varying standards and regulations regarding copper usage in different regions. In Europe, for instance, compliance with EN 1057 is essential, while in Brazil, local regulations may dictate specific copper grades.
What are the Benefits and Limitations of Aluminum in Heat Exchanger Design?
Aluminum is increasingly used in heat exchanger applications due to its lightweight nature and good thermal conductivity. It typically operates effectively at temperatures up to 400°F (204°C) and is resistant to corrosion, especially when anodized.
Pros & Cons: The main benefits of aluminum include its low weight, which can reduce shipping costs, and its relatively low price compared to stainless steel. However, its lower temperature and pressure ratings can limit its use in high-demand applications.
Impact on Application: Aluminum is suitable for applications involving air and water but may not be ideal for high-pressure steam systems.
Considerations for International Buyers: Buyers from Africa and South America should consider local availability and manufacturing capabilities, as aluminum may require specialized welding techniques. Compliance with standards such as ASTM B221 is crucial for ensuring quality.
Why is Carbon Steel a Viable Option for Heat Exchangers?
Carbon steel is often chosen for heat exchangers in applications where cost is a significant factor. It has a good strength-to-weight ratio and can handle high pressures and temperatures, typically up to 600°F (316°C).
Pros & Cons: Carbon steel is generally more affordable than stainless steel and offers good mechanical properties. However, it is susceptible to corrosion, which can lead to shorter service life and increased maintenance costs.
Impact on Application: Carbon steel is suitable for applications involving non-corrosive fluids, such as water and steam, but should be avoided in highly corrosive environments.
Considerations for International Buyers: Buyers should ensure compliance with relevant standards like ASTM A106 or EN 10216. In regions like the Middle East, where high temperatures and humidity can accelerate corrosion, protective coatings may be necessary.
Summary Table of Material Selection for Custom Heat Exchangers
Material | Typical Use Case for heat exchangers custom | Key Advantage | Key Disadvantage/Limitation | Relative Cost (Low/Med/High) |
---|---|---|---|---|
Stainless Steel | Chemical processing, food production | Excellent corrosion resistance | Higher cost and manufacturing complexity | High |
Copper | HVAC systems, refrigeration | Superior thermal conductivity | Prone to corrosion in certain media | Medium |
Aluminum | Air conditioning, water cooling | Lightweight and cost-effective | Limited high-temperature performance | Low |
Carbon Steel | Steam systems, water heating | Cost-effective and strong | Susceptible to corrosion | Low |
This strategic material selection guide provides essential insights for international B2B buyers, enabling them to make informed decisions based on their specific application needs and regional considerations.
In-depth Look: Manufacturing Processes and Quality Assurance for heat exchangers custom
What Are the Key Stages in the Manufacturing Process of Custom Heat Exchangers?
Manufacturing custom heat exchangers involves several critical stages, each designed to ensure the end product meets the specific requirements of the application. The main stages include material preparation, forming, assembly, and finishing.
-
Material Preparation: The process begins with selecting the right materials, typically stainless steel, copper, or aluminum, based on thermal conductivity, corrosion resistance, and mechanical properties. Suppliers must ensure that raw materials conform to international standards such as ASTM or ASME. Conducting thorough material inspections before fabrication is essential to avoid complications later in the production process.
-
Forming: This stage involves shaping the materials into the desired form. Techniques such as welding, bending, and stamping are commonly used. Advanced technologies, like CNC machining, provide precision in manufacturing complex designs. For international buyers, understanding the forming techniques used by suppliers can help assess the capability and reliability of the manufacturing process.
-
Assembly: The assembly of heat exchangers is where all components come together. This can include assembling tubes, plates, and fins, depending on the design. Employing automated assembly lines can enhance consistency and reduce human error. Buyers should inquire about the assembly methods used, as this can significantly impact the heat exchanger’s performance and durability.
-
Finishing: The final stage includes surface treatments, such as passivation or coating, to enhance corrosion resistance and overall longevity. This step is vital, especially for heat exchangers used in harsh environments. Ensuring that the finishing processes align with international standards will help buyers maintain the quality of their products.
How Is Quality Assurance Integrated into the Manufacturing of Custom Heat Exchangers?
Quality assurance (QA) is paramount in the manufacturing of custom heat exchangers, ensuring that the final product meets both customer specifications and international standards. The QA process typically involves several checkpoints and testing methods.
-
Relevant International Standards: Compliance with standards such as ISO 9001 ensures a systematic approach to quality management. Specific industry standards may also apply, such as the CE mark for European markets and API standards for oil and gas applications. Buyers should verify that their suppliers have the necessary certifications and adhere to these standards.
-
Quality Control Checkpoints: Effective quality control is crucial at various stages of production:
– Incoming Quality Control (IQC): This initial stage involves inspecting raw materials to confirm they meet specified requirements.
– In-Process Quality Control (IPQC): During manufacturing, continuous monitoring and testing are conducted to ensure adherence to quality standards.
– Final Quality Control (FQC): Before shipment, the finished product undergoes comprehensive testing to validate its performance and compliance with specifications. -
Common Testing Methods: Various testing methods are employed to ensure quality, including:
– Hydrostatic Testing: This checks for leaks and assesses the structural integrity of the heat exchanger.
– Pressure Testing: Used to evaluate the performance under operational pressures.
– Non-Destructive Testing (NDT): Techniques such as ultrasonic testing or dye penetrant testing help detect flaws without damaging the product.
How Can B2B Buyers Verify Supplier Quality Control Processes?
For international B2B buyers, particularly in regions like Africa, South America, the Middle East, and Europe, verifying a supplier’s quality control processes is essential to ensure product reliability.
-
Supplier Audits: Conducting audits of potential suppliers can provide insights into their manufacturing capabilities and quality management systems. Buyers should look for suppliers that encourage transparency and are willing to undergo third-party audits.
-
Quality Reports: Requesting detailed quality reports can help assess the supplier’s performance history. These reports should include data on defect rates, compliance with testing protocols, and corrective actions taken on previous issues.
-
Third-Party Inspections: Engaging third-party inspection services can provide an unbiased evaluation of the manufacturing process and quality assurance measures. This is particularly valuable for buyers unfamiliar with the local manufacturing landscape.
What Are the Quality Control and Certification Nuances for International B2B Buyers?
Understanding the nuances of quality control and certification is crucial for B2B buyers operating in diverse international markets.
-
Regional Standards Variability: Different regions may have distinct standards and regulations governing the manufacture of heat exchangers. For instance, European buyers must ensure compliance with CE marking, while those in the Middle East may focus on local standards. Familiarizing oneself with these regional requirements can prevent costly compliance issues.
-
Documentation and Certification: Buyers should request comprehensive documentation from suppliers, including certificates of compliance, test reports, and quality management system certifications. This documentation acts as proof of adherence to quality standards and can be crucial for regulatory compliance in the buyer’s home country.
-
Cultural Considerations in Quality Assurance: Different cultures may approach quality assurance differently, influencing how suppliers operate. Buyers should consider these cultural factors when engaging with suppliers, particularly in negotiation and communication styles. Building strong relationships with suppliers can lead to better quality outcomes and more reliable service.
In summary, understanding the manufacturing processes and quality assurance protocols for custom heat exchangers is vital for international B2B buyers. By focusing on the key stages of manufacturing, ensuring compliance with relevant standards, and verifying supplier quality control measures, buyers can make informed decisions that enhance their operational efficiency and product reliability.
Practical Sourcing Guide: A Step-by-Step Checklist for ‘heat exchangers custom’
Introduction
In today’s global marketplace, sourcing custom heat exchangers requires a strategic approach to ensure optimal performance, cost-efficiency, and compliance with local regulations. This checklist serves as a practical guide for international B2B buyers, particularly those from Africa, South America, the Middle East, and Europe, to navigate the complexities of procuring these essential components effectively.
Step 1: Define Your Technical Specifications
Before engaging with suppliers, it’s essential to clearly outline your technical requirements. This includes factors such as the type of heat exchanger (e.g., shell and tube, plate), materials, operating temperatures, and pressure ratings. Providing detailed specifications helps suppliers understand your needs and prevents costly misunderstandings later in the process.
- Consider your industry standards: Different sectors, like oil and gas or food processing, have specific requirements that must be met.
- Document your performance expectations: Be clear about efficiency ratings and maintenance needs.
Step 2: Conduct Market Research for Suppliers
Identifying potential suppliers is crucial to finding the right partner for your heat exchanger needs. Research companies that specialize in custom manufacturing and have a proven track record in your target regions.
- Utilize industry directories: Resources like ThomasNet or industry-specific trade shows can provide valuable contacts.
- Network within local business communities: Leveraging local chambers of commerce can lead to recommendations for reputable suppliers.
Step 3: Evaluate Potential Suppliers
Before committing, it’s crucial to vet suppliers thoroughly. Request company profiles, case studies, and references from buyers in a similar industry or region. This step ensures that you are working with a reputable manufacturer who can meet your needs.
- Check for relevant certifications: Look for ISO certifications or other industry-specific qualifications that demonstrate quality control.
- Assess their manufacturing capabilities: Ensure they have the technology and capacity to produce your custom designs.
Step 4: Request and Compare Quotes
Once you have shortlisted potential suppliers, request detailed quotes that include pricing, lead times, and payment terms. Comparing multiple offers allows you to identify the best value for your investment.
- Look for transparency in pricing: Ensure that all costs, including shipping and installation, are clearly outlined.
- Consider long-term costs: Evaluate not just the initial price but also the potential for maintenance and energy efficiency over time.
Step 5: Verify Supplier Certifications
Confirm that your chosen suppliers hold necessary certifications that comply with international and local standards. This verification is essential to ensure quality and reliability in your final product.
- Request documentation: Ask for copies of certifications and any relevant compliance documents.
- Understand the implications of non-compliance: Non-certified products can lead to operational failures and regulatory fines.
Step 6: Establish Clear Communication Channels
Effective communication is key to successful procurement. Establish a point of contact for each supplier and set clear expectations regarding timelines, updates, and feedback mechanisms.
- Use project management tools: Platforms like Trello or Asana can help keep everyone aligned on project milestones.
- Schedule regular check-ins: Frequent updates will help address any potential issues proactively.
Step 7: Finalize Contracts and Terms of Service
Once you have chosen a supplier, finalize the contract details, ensuring that all terms of service, warranties, and delivery schedules are explicitly stated. This step is critical to protect your investment and establish a clear understanding between both parties.
- Include clauses for dispute resolution: This can help mitigate risks related to delays or quality issues.
- Review terms with legal counsel: Having a legal expert review the contract can prevent future complications.
By following this comprehensive sourcing checklist, B2B buyers can navigate the complexities of procuring custom heat exchangers with confidence, ensuring they select the right supplier to meet their specific needs.
Comprehensive Cost and Pricing Analysis for heat exchangers custom Sourcing
What Are the Key Cost Components for Custom Heat Exchangers?
When sourcing custom heat exchangers, understanding the cost structure is essential for making informed purchasing decisions. The primary cost components include:
-
Materials: The choice of materials significantly impacts the overall cost. Common materials such as stainless steel, copper, or aluminum vary in price due to market fluctuations and availability. Specialty alloys may be required for specific applications, which can drive costs even higher.
-
Labor: Skilled labor is necessary for the manufacturing of custom heat exchangers. Labor costs can vary by region; for example, manufacturing in Europe may incur higher labor costs compared to regions in Africa or South America, where labor is often less expensive.
-
Manufacturing Overhead: This includes indirect costs such as utilities, rent, and equipment depreciation. Efficient manufacturing processes can help reduce overhead, which is crucial for competitive pricing.
-
Tooling: Custom tooling may be required for unique designs, which can add to the initial investment. It’s essential to consider the amortization of these costs over the expected production volume.
-
Quality Control (QC): Implementing stringent QC measures ensures that the final product meets industry standards. While this adds to the cost, it also reduces the risk of costly failures or recalls.
-
Logistics: Transportation costs can vary greatly depending on the origin of the materials and the destination. Understanding these costs is vital, particularly for international buyers who may face additional tariffs or customs fees.
-
Margin: Suppliers will typically add a profit margin to the total costs, which can vary based on the supplier’s market positioning and the complexity of the custom order.
How Do Price Influencers Affect Custom Heat Exchanger Sourcing?
Several factors influence the pricing of custom heat exchangers, including:
-
Volume and Minimum Order Quantity (MOQ): Larger orders often lead to price breaks due to economies of scale. Understanding the MOQ can help buyers negotiate better pricing.
-
Specifications and Customization: The level of customization required can significantly affect pricing. More complex designs or specialized features increase production time and costs.
-
Material Quality and Certifications: Higher-quality materials and necessary certifications (e.g., ISO, ASME) may come at a premium. Ensure that your supplier can provide the required certifications to avoid future compliance issues.
-
Supplier Factors: The supplier’s reputation, location, and production capabilities can influence pricing. Established suppliers may charge higher prices for their reliability and quality assurance.
-
Incoterms: The chosen Incoterms can significantly impact the final cost. Understanding the responsibilities of both the buyer and supplier can help in budgeting for additional costs associated with shipping and handling.
What Are Effective Buyer Tips for Negotiating Custom Heat Exchanger Prices?
For international B2B buyers, particularly from Africa, South America, the Middle East, and Europe, employing effective negotiation strategies can lead to significant cost savings:
-
Negotiate with Multiple Suppliers: Request quotes from several suppliers to create competition. This can help in negotiating better prices or terms.
-
Focus on Total Cost of Ownership (TCO): Consider not only the purchase price but also the long-term costs associated with maintenance, energy efficiency, and potential downtime. This holistic view can justify a higher initial investment for better quality.
-
Understand Pricing Nuances: Be aware of regional pricing variations and the impact of local economic conditions. For example, sourcing from a supplier in a country with lower production costs can yield better pricing options.
-
Leverage Incoterms for Cost Efficiency: Choose Incoterms that minimize your risk and costs. For example, opting for DDP (Delivered Duty Paid) can simplify logistics and ensure that all costs are accounted for upfront.
-
Build Long-term Relationships: Establishing a long-term partnership with suppliers can lead to preferential pricing and improved service over time.
Conclusion and Disclaimer
When sourcing custom heat exchangers, a thorough understanding of the cost structure and pricing influencers is crucial for effective negotiation and budgeting. Prices can vary widely based on materials, specifications, and supplier factors, so it is essential to conduct comprehensive market research. Always remember that the prices indicated in negotiations are subject to change due to market conditions and should be confirmed with the supplier for accuracy.
Alternatives Analysis: Comparing heat exchangers custom With Other Solutions
Introduction: What Are the Alternatives to Custom Heat Exchangers?
When considering the procurement of heat exchangers, international B2B buyers often evaluate custom solutions against a variety of alternatives. Custom heat exchangers are designed to meet specific process requirements, but other technologies can also provide effective thermal transfer solutions. Understanding these alternatives can help organizations make informed decisions that optimize performance and cost-effectiveness in their operations.
Comparison Table of Heat Exchangers Custom and Alternatives
Comparison Aspect | Heat Exchangers Custom | Plate Heat Exchangers | Air-Cooled Heat Exchangers |
---|---|---|---|
Performance | High efficiency, tailored to specific processes | Excellent thermal performance, compact design | Good for large-scale applications, less maintenance |
Cost | Higher initial investment due to customization | Moderate cost, economical for certain applications | Generally lower upfront cost, but may incur higher energy costs |
Ease of Implementation | Requires detailed specifications and longer lead times | Faster to install and integrate | Simple installation, but may need additional space |
Maintenance | Potentially complex due to custom designs | Easier maintenance, accessible parts | Low maintenance requirements, but less efficient in extreme conditions |
Best Use Case | Specific industrial applications needing unique configurations | Food processing, HVAC, and chemical industries | Power plants and large industrial systems |
Detailed Breakdown of Alternative Solutions
What Are the Advantages and Disadvantages of Plate Heat Exchangers?
Plate heat exchangers are known for their high thermal efficiency and compact size, making them suitable for industries such as food processing and HVAC systems. Their modular design allows for easy expansion or modification, which can be a significant advantage for growing businesses. However, they may not handle high-pressure applications as effectively as custom solutions. Additionally, while they offer moderate costs, the need for regular maintenance and potential for fouling can lead to increased operational expenses over time.
How Do Air-Cooled Heat Exchangers Compare?
Air-cooled heat exchangers are a cost-effective solution for large-scale applications, particularly in environments where water is scarce. They eliminate the need for cooling water and are relatively straightforward to install. While their upfront costs are lower compared to custom heat exchangers, they can incur higher energy costs due to reliance on fans and ambient air. Their maintenance is generally minimal, making them an attractive option for industries such as power generation. However, their performance may suffer in extreme heat or humidity, which can limit their effectiveness in certain regions.
Conclusion: How to Choose the Right Heat Exchanger Solution?
When selecting the appropriate heat exchanger solution, B2B buyers should consider their specific operational needs, budget constraints, and environmental factors. Custom heat exchangers offer tailored performance but come with higher costs and longer lead times. In contrast, plate heat exchangers provide a good balance of efficiency and cost, while air-cooled heat exchangers are ideal for large applications with limited water access. By evaluating these aspects, international buyers from regions such as Africa, South America, the Middle East, and Europe can make informed decisions that align with their operational goals and financial resources.
Essential Technical Properties and Trade Terminology for heat exchangers custom
What Are the Key Technical Properties of Custom Heat Exchangers?
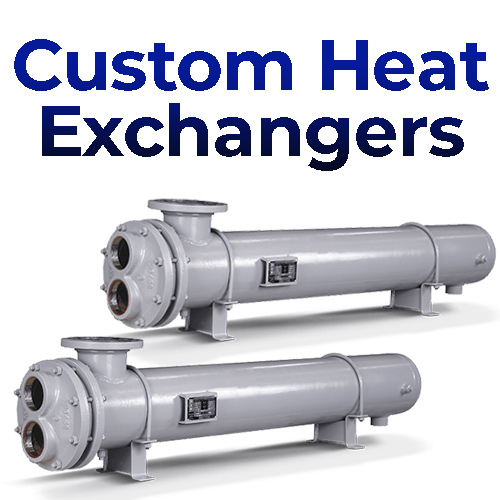
A stock image related to heat exchangers custom.
When sourcing custom heat exchangers, understanding the essential technical properties is crucial for making informed purchasing decisions. Here are several critical specifications that B2B buyers should consider:
1. Material Grade
The material used in heat exchangers significantly affects their performance, durability, and suitability for specific applications. Common materials include stainless steel, copper, and titanium. Each material has unique properties regarding corrosion resistance, thermal conductivity, and pressure ratings. For instance, stainless steel is often chosen for its strength and resistance to oxidation, making it ideal for chemical processing industries. Selecting the appropriate material grade can optimize efficiency and longevity, ultimately affecting total cost of ownership.
2. Tolerance
Tolerance refers to the allowable variation in dimensions and physical properties during the manufacturing process. Tight tolerances are crucial in applications requiring high efficiency and minimal leakage, such as in the oil and gas sector. Understanding the required tolerances can help buyers ensure that the heat exchanger will fit seamlessly into existing systems, reducing downtime and additional costs associated with modifications.
3. Heat Transfer Efficiency
Heat transfer efficiency is a measure of how effectively a heat exchanger can transfer heat between two fluids. This is often quantified by the overall heat transfer coefficient (U-value). Higher efficiency translates to better energy savings and improved operational performance. Buyers should inquire about the U-value to ensure that the selected heat exchanger meets the specific thermal performance requirements of their application.
4. Pressure Drop
Pressure drop is the reduction in pressure that occurs as fluid flows through the heat exchanger. It is a critical parameter that affects the energy consumption of pumps and overall system efficiency. Understanding the acceptable pressure drop for a particular application can guide buyers in selecting a heat exchanger that optimizes flow rates without excessive energy costs.
5. Design Specifications
Custom heat exchangers can be tailored to meet specific design requirements, including size, shape, and configuration. Buyers should clearly communicate their application needs to manufacturers, as design specifications can significantly influence heat exchanger performance and integration into existing systems.
What Are Common Trade Terms Related to Custom Heat Exchangers?
Familiarity with industry jargon can facilitate smoother communication and negotiations. Here are some key terms that B2B buyers should know:
1. OEM (Original Equipment Manufacturer)
An OEM refers to a company that produces parts and equipment that may be marketed by another manufacturer. In the context of heat exchangers, working with an OEM can ensure that the product meets specific standards and integrates well with existing equipment. Buyers should consider OEM partnerships for custom solutions that align with their operational needs.
2. MOQ (Minimum Order Quantity)
MOQ is the smallest quantity of a product that a supplier is willing to sell. Understanding MOQ is essential for buyers, especially for custom heat exchangers, as it can impact inventory management and cash flow. Buyers should negotiate MOQs that align with their project timelines and budget constraints.
3. RFQ (Request for Quotation)
An RFQ is a formal process where buyers request pricing and terms from suppliers. It typically includes detailed specifications for the heat exchanger needed. Submitting a comprehensive RFQ can help buyers receive accurate quotes, ensuring better comparison and decision-making.
4. Incoterms (International Commercial Terms)
Incoterms are standardized trade terms that define the responsibilities of buyers and sellers regarding shipping, insurance, and tariffs. Familiarity with Incoterms can help buyers understand the logistics involved in importing custom heat exchangers, particularly in international transactions. Proper understanding can prevent misunderstandings and additional costs.
5. Lead Time
Lead time refers to the time required to manufacture and deliver a product after an order is placed. For custom heat exchangers, lead times can vary significantly based on design complexity and material availability. Buyers should account for lead times in their project planning to avoid delays in their operations.
By understanding these essential technical properties and trade terms, international B2B buyers can navigate the complexities of sourcing custom heat exchangers more effectively, ensuring that they make informed decisions that align with their operational requirements.
Navigating Market Dynamics and Sourcing Trends in the heat exchangers custom Sector
What Are the Current Market Dynamics and Key Trends in the Custom Heat Exchanger Sector?
The global custom heat exchanger market is driven by an increasing demand for efficient thermal management solutions across various industries, including oil and gas, pharmaceuticals, and food processing. Key trends shaping this sector include the integration of Industry 4.0 technologies, which enable real-time monitoring and predictive maintenance, enhancing operational efficiency. Additionally, the shift towards more compact and lightweight designs is gaining traction, driven by the need for space-saving solutions in urban and industrial settings.
International B2B buyers, particularly from Africa, South America, the Middle East, and Europe, should be aware of the regional variations in sourcing trends. For instance, while European buyers may prioritize advanced technology and energy efficiency, those in Africa might focus on cost-effective solutions that can withstand harsh environmental conditions. The increased emphasis on customization is also notable, as companies seek tailored solutions that meet specific operational needs. Furthermore, emerging markets are witnessing a rise in local manufacturing capabilities, reducing lead times and transportation costs, thereby influencing sourcing strategies.
How Can Sustainability and Ethical Sourcing Impact B2B Buying Decisions?
Sustainability has become a critical consideration for B2B buyers in the custom heat exchanger sector. The environmental impact of manufacturing processes and the materials used in heat exchangers are under scrutiny as companies strive to meet corporate social responsibility goals. Ethical sourcing practices are essential, as they ensure that materials are obtained from suppliers who adhere to sustainable practices, reducing the overall carbon footprint.
Buyers should look for suppliers that offer ‘green’ certifications, such as ISO 14001 for environmental management or LEED certification for energy-efficient products. Additionally, the use of recyclable and biodegradable materials in the production of heat exchangers can significantly enhance a company’s sustainability profile. By prioritizing suppliers that demonstrate a commitment to sustainability, B2B buyers can not only improve their own environmental impact but also align with the growing consumer preference for eco-friendly products.
What Is the Brief Evolution of the Custom Heat Exchanger Market?
The custom heat exchanger market has evolved significantly over the past few decades. Initially, heat exchangers were primarily standardized units, with limited customization options. However, as industries grew more specialized, the demand for tailored solutions increased, prompting manufacturers to innovate. The advent of advanced materials and computer-aided design (CAD) technology has enabled the production of highly specialized heat exchangers that cater to diverse applications.
Today, the market is characterized by a blend of traditional craftsmanship and modern engineering, resulting in products that not only meet stringent performance standards but also accommodate the unique requirements of different industries. This evolution reflects a broader trend in manufacturing towards customization and flexibility, making it essential for international B2B buyers to stay informed about technological advancements and sourcing capabilities in the sector.
Frequently Asked Questions (FAQs) for B2B Buyers of heat exchangers custom
-
How do I select the right custom heat exchanger for my industrial application?
Choosing the right custom heat exchanger involves assessing your specific needs, including the type of fluid, temperature ranges, and pressure conditions. Start by evaluating your operational requirements and consider factors such as space constraints and installation conditions. Collaborate closely with suppliers to discuss your application, which can help them recommend the most suitable design—be it shell-and-tube, plate, or air-cooled heat exchangers. Also, consider future scalability and maintenance needs to ensure long-term efficiency. -
What are the key factors to consider when sourcing custom heat exchangers internationally?
When sourcing custom heat exchangers, key factors include supplier reliability, quality standards, and compliance with local regulations. Verify the supplier’s certifications (ISO, ASME) and their experience in your industry. Additionally, assess their ability to provide after-sales support and spare parts. Understanding the logistics involved, such as shipping costs and lead times, is also crucial. Engaging with suppliers who have a strong presence in your region can facilitate smoother transactions and reduce risks associated with international trade. -
What is the typical minimum order quantity (MOQ) for custom heat exchangers?
The minimum order quantity for custom heat exchangers varies by supplier and design complexity. Generally, manufacturers may have an MOQ ranging from one unit for specialized designs to several units for standard models. It’s essential to communicate your needs with potential suppliers to negotiate terms that align with your budget and project scale. Consider the implications of MOQ on your inventory management and future projects, especially if you’re a smaller company or a startup. -
What payment terms should I expect when purchasing custom heat exchangers?
Payment terms for custom heat exchangers can vary significantly between suppliers. Common practices include a deposit upfront (usually 30-50%) with the balance due upon delivery or after installation. Some suppliers may offer financing options or extended payment plans, especially for larger orders. Always clarify payment methods accepted (e.g., bank transfers, letters of credit) and ensure that terms are documented in the contract to prevent misunderstandings. -
How can I ensure the quality of custom heat exchangers?
To ensure the quality of custom heat exchangers, request detailed specifications and certifications from your supplier, such as material certifications and performance testing reports. Implement a quality assurance process that includes inspections during manufacturing and upon delivery. Consider third-party inspection services if necessary. Engaging in regular communication with the supplier throughout the manufacturing process can help address any quality concerns before they escalate. -
What logistics considerations should I keep in mind when importing custom heat exchangers?
Logistics considerations for importing custom heat exchangers include shipping methods, customs clearance, and delivery timelines. Choose a reliable freight forwarder familiar with your destination’s regulations. Understand the import duties and taxes applicable in your country, as these can significantly impact overall costs. Additionally, ensure that the supplier can accommodate packaging requirements to prevent damage during transit. -
How do I vet potential suppliers for custom heat exchangers?
Vetting potential suppliers involves researching their industry reputation, customer reviews, and case studies. Request references from previous clients and inquire about their experience with the supplier. Evaluate their manufacturing capabilities, quality control processes, and certifications. Additionally, visit their facility if possible, or conduct virtual audits to assess their operations. Trust and transparency are key, so ensure that the supplier communicates openly about their processes and timelines. -
What customization options are available for heat exchangers?
Customization options for heat exchangers can include size, material selection, and design modifications tailored to specific applications. Common materials include stainless steel, carbon steel, and titanium, depending on the fluids and temperatures involved. You may also request modifications to enhance efficiency, such as optimized flow paths or enhanced surface areas. Discussing your requirements in detail with the supplier allows them to propose the best solutions that meet your operational needs and compliance standards.
Important Disclaimer & Terms of Use
⚠️ Important Disclaimer
The information provided in this guide, including content regarding manufacturers, technical specifications, and market analysis, is for informational and educational purposes only. It does not constitute professional procurement advice, financial advice, or legal advice.
While we have made every effort to ensure the accuracy and timeliness of the information, we are not responsible for any errors, omissions, or outdated information. Market conditions, company details, and technical standards are subject to change.
B2B buyers must conduct their own independent and thorough due diligence before making any purchasing decisions. This includes contacting suppliers directly, verifying certifications, requesting samples, and seeking professional consultation. The risk of relying on any information in this guide is borne solely by the reader.
Strategic Sourcing Conclusion and Outlook for heat exchangers custom
In today’s competitive landscape, effective strategic sourcing is essential for international B2B buyers seeking custom heat exchangers. By prioritizing supplier relationships and leveraging regional advantages, businesses in Africa, South America, the Middle East, and Europe can optimize their procurement processes. It’s crucial to assess suppliers based on their technological capabilities, compliance with international standards, and ability to provide tailored solutions that meet specific operational needs.
Buyers should focus on developing a robust sourcing strategy that emphasizes transparency, sustainability, and risk management. Engaging with suppliers who demonstrate innovation and a commitment to quality can significantly enhance product performance and durability, ultimately leading to cost savings and increased operational efficiency.
Looking ahead, the demand for custom heat exchangers is expected to rise, driven by advancements in technology and a greater emphasis on energy efficiency. International B2B buyers are encouraged to remain proactive in exploring new partnerships and staying informed about market trends. By aligning their sourcing strategies with future industry shifts, companies can position themselves for sustained growth and success. Now is the time to take decisive action and invest in strategic sourcing initiatives that will yield long-term benefits.