The Ultimate Guide to Shrink Wrapping Machine Manufacturer (2025)
Introduction: Navigating the Global Market for shrink wrapping machine manufacturer
In the fast-evolving landscape of international trade, sourcing the right shrink wrapping machine manufacturers poses a significant challenge for B2B buyers, especially those operating in Africa, South America, the Middle East, and Europe. As businesses strive to enhance product protection, streamline packaging processes, and improve supply chain efficiency, the demand for reliable shrink wrapping solutions has surged. However, navigating the myriad of options available globally can be daunting, making informed purchasing decisions critical.
This comprehensive guide aims to demystify the global market for shrink wrapping machines by exploring various types and their applications across different industries. From semi-automatic to fully automatic systems, each machine offers unique advantages tailored to specific operational needs. Additionally, we will delve into the essential factors for vetting suppliers, ensuring that you partner with reputable manufacturers that meet your quality and service expectations.
Furthermore, we’ll provide insights into cost considerations, helping you to budget effectively and evaluate the total cost of ownership. By addressing these key elements, this guide empowers international B2B buyers to make strategic decisions that align with their operational goals. Whether you are based in Spain, Brazil, or any other region, understanding these dynamics will enable you to optimize your packaging processes and enhance your competitive edge in the marketplace.
Understanding shrink wrapping machine manufacturer Types and Variations
Type Name | Key Distinguishing Features | Primary B2B Applications | Brief Pros & Cons for Buyers |
---|---|---|---|
Automatic Shrink Wrappers | Fully automated processes, high-speed operation, integrated systems | High-volume production in food, beverages, and consumer goods | Pros: Efficiency, reduced labor costs. Cons: Higher initial investment. |
Semi-Automatic Shrink Wrappers | Manual loading with automated sealing and shrinking, flexibility in operation | Medium-sized businesses, varied product sizes | Pros: Cost-effective, adaptable to different products. Cons: Slower than fully automatic options. |
L-Bar Sealers | Compact design, suitable for smaller packages, combines sealing and shrinking | E-commerce, small batch production | Pros: Space-saving, easy to use. Cons: Limited speed, best for low-volume applications. |
Shrink Bundlers | Bundling multiple products together, often with a tray or film | Multi-packaging in retail and distribution | Pros: Cost-efficient for bundling, enhances shelf appeal. Cons: May require additional equipment for sealing. |
Chamber Shrink Wrappers | Enclosed chamber for shrinking, ideal for various product shapes | Food packaging, electronics, and pharmaceuticals | Pros: Uniform shrinkage, excellent for irregular shapes. Cons: Slower cycle time, limited to chamber size. |
What Are the Characteristics of Automatic Shrink Wrappers?
Automatic shrink wrappers are designed for high-volume production lines, offering fully automated processes that significantly enhance efficiency. They are typically integrated with other packaging machinery, allowing for seamless operation. B2B buyers should consider the initial investment costs, as these machines can be more expensive than manual options. However, the long-term savings in labor and increased throughput make them a compelling choice for large-scale manufacturers, particularly in industries like food and beverage.
How Do Semi-Automatic Shrink Wrappers Suit Various Business Needs?
Semi-automatic shrink wrappers strike a balance between automation and manual operation, making them suitable for medium-sized businesses that handle a range of product sizes. These machines require manual loading but automate the sealing and shrinking processes. B2B buyers should evaluate their production volume and flexibility needs, as semi-automatic machines offer adaptability without the high costs associated with full automation. They are ideal for businesses that may not require continuous operation but still seek efficiency.
Why Choose L-Bar Sealers for Smaller Operations?
L-Bar sealers are compact machines that are particularly effective for smaller packaging operations. They combine the sealing and shrinking processes into one, making them user-friendly and efficient for low-volume applications. B2B buyers, especially in e-commerce or small batch production, will find L-Bar sealers beneficial due to their space-saving design and ease of use. However, they may not be suitable for high-speed production environments, so understanding your volume needs is crucial.
What Are the Advantages of Using Shrink Bundlers?
Shrink bundlers are specialized machines that bundle multiple products together, often enhancing product presentation and shelf appeal. They are especially useful in retail and distribution sectors where products are sold in multi-pack configurations. While they provide cost savings and improve visual merchandising, B2B buyers must consider that bundlers might require additional sealing equipment, depending on the packaging strategy. It’s essential to assess how bundling fits into your overall packaging process.
How Do Chamber Shrink Wrappers Cater to Diverse Product Shapes?
Chamber shrink wrappers utilize an enclosed chamber to create a controlled environment for shrinking, making them ideal for products of various shapes and sizes. They provide uniform shrinkage and are particularly effective for packaging food items, electronics, and pharmaceuticals. Buyers should be aware that while chamber wrappers deliver consistent results, they may have slower cycle times and are limited by the size of the chamber. Evaluating the specific products to be packaged will guide the decision-making process for B2B buyers in these industries.
Related Video: SWM 100 – Automatic Continuous Motion Shrink Wrapping Machine
Key Industrial Applications of shrink wrapping machine manufacturer
Industry/Sector | Specific Application of shrink wrapping machine manufacturer | Value/Benefit for the Business | Key Sourcing Considerations for this Application |
---|---|---|---|
Food and Beverage | Packaging of bottled beverages | Enhances shelf life and protects products from contamination | Compliance with food safety regulations, machine hygiene standards |
Pharmaceuticals | Securing blister packs and vials | Ensures product integrity and prevents tampering | Need for precision, compliance with pharmaceutical standards |
Consumer Electronics | Bundling and protecting electronic devices | Minimizes damage during transport and improves presentation | Customization options, compatibility with various product shapes |
Building Materials | Wrapping construction materials like tiles and lumber | Reduces moisture exposure and simplifies handling | Durability of materials used, ability to handle heavy loads |
Cosmetics and Personal Care | Packaging beauty products and toiletries | Enhances visual appeal and provides tamper evidence | Variety of film options, aesthetic considerations |
How are Shrink Wrapping Machines Used in the Food and Beverage Industry?
In the food and beverage sector, shrink wrapping machines are vital for packaging bottled beverages. They provide an airtight seal that enhances shelf life and protects products from contamination during storage and transport. For international buyers, especially those from Africa and South America, compliance with local food safety regulations is crucial. Buyers must ensure that the machines can accommodate various bottle shapes and sizes, as well as meet hygiene standards to prevent product spoilage.
What Role do Shrink Wrapping Machines Play in Pharmaceuticals?
Shrink wrapping machines are essential in the pharmaceutical industry for securing blister packs and vials. They ensure product integrity and prevent tampering, which is critical for maintaining trust in pharmaceutical products. Buyers in the Middle East and Europe should prioritize machines that offer precision and comply with stringent pharmaceutical standards. The ability to handle small, delicate packages without damage is also a key requirement in this sector.
Why are Shrink Wrapping Machines Important for Consumer Electronics?
In the consumer electronics sector, shrink wrapping machines are used to bundle and protect devices such as smartphones and tablets. This application minimizes damage during transport and enhances product presentation on retail shelves. B2B buyers from Europe and South America should consider customization options that allow for different shapes and sizes of products. Additionally, the machines must be capable of high-speed operations to meet the demands of fast-paced production lines.
How Do Shrink Wrapping Machines Benefit the Building Materials Industry?
In the building materials industry, shrink wrapping machines are employed to wrap construction materials like tiles and lumber. This application reduces moisture exposure, which can lead to product degradation, and simplifies handling during transportation. Buyers from Africa and the Middle East need to focus on the durability of materials used in the wrapping process, ensuring that the machines can handle heavy loads without compromising on performance.
What Advantages Do Shrink Wrapping Machines Offer to Cosmetics and Personal Care Products?
Shrink wrapping machines play a significant role in the packaging of cosmetics and personal care products. They enhance visual appeal and provide tamper evidence, which is increasingly important to consumers. B2B buyers, particularly from Europe, should look for machines that offer a variety of film options to meet aesthetic considerations while ensuring the integrity of the products. Compatibility with diverse product shapes and sizes is also a critical factor in the sourcing process.
Related Video: SWM 50 – Automatic Shrink Wrapping Machine
3 Common User Pain Points for ‘shrink wrapping machine manufacturer’ & Their Solutions
Scenario 1: Inefficient Production Processes and Downtime
The Problem: One of the most significant challenges B2B buyers face when sourcing shrink wrapping machines is the inefficiency that can lead to excessive downtime. In sectors such as food and beverage, pharmaceuticals, and consumer goods, any halt in production can result in considerable losses. Buyers often discover that machines are not compatible with their existing production lines, leading to integration issues that can disrupt workflow. Furthermore, if the machinery is prone to frequent breakdowns, the reliability of the entire packaging operation comes into question, affecting delivery schedules and customer satisfaction.
The Solution: To mitigate these issues, it is crucial for buyers to conduct thorough research before making a purchase. Start by assessing the compatibility of the shrink wrapping machine with your current production setup. Engage with manufacturers that offer customized solutions tailored to your specific operational needs. Inquire about the machine’s uptime statistics and maintenance requirements. A proactive approach would be to establish a robust preventive maintenance schedule post-purchase, ensuring regular checks and servicing to keep the machine in optimal condition. Opt for manufacturers that provide comprehensive training for your staff to minimize operational errors and enhance efficiency.
Scenario 2: High Operational Costs and Energy Consumption
The Problem: Another common pain point for international B2B buyers is the high operational costs associated with shrink wrapping machines. Buyers often underestimate the energy consumption and maintenance costs involved in running these machines. In regions like Africa and South America, where energy prices can be volatile, these costs can erode profit margins. Additionally, machines that require frequent replacements of parts or consumables can significantly increase the total cost of ownership over time.
The Solution: When sourcing shrink wrapping machines, prioritize energy-efficient models that are designed to minimize electricity usage without compromising performance. Look for equipment that features advanced technology, such as servo motors or variable speed drives, which can adapt to production needs while conserving energy. Request detailed operational cost analyses from manufacturers, including estimates of energy consumption and maintenance costs over the machine’s lifecycle. Consider investing in machines that utilize sustainable materials or processes, as they may provide long-term savings and enhance your company’s green credentials, appealing to environmentally conscious customers.
Scenario 3: Difficulty in Sourcing Spare Parts and Technical Support
The Problem: Buyers frequently encounter difficulties in sourcing spare parts and receiving timely technical support from shrink wrapping machine manufacturers. This issue can be especially pronounced in regions like the Middle East and parts of Europe, where local suppliers may not stock essential components. A lack of readily available spare parts can lead to prolonged downtime, hindering production and impacting overall profitability. Furthermore, inadequate technical support can leave buyers struggling to resolve issues quickly, affecting their operational efficiency.
The Solution: To alleviate these concerns, buyers should prioritize manufacturers with a strong global presence and robust supply chain management. Before finalizing a purchase, inquire about the availability of spare parts and the manufacturer’s commitment to providing ongoing support. Establish a relationship with manufacturers who offer comprehensive service agreements that include rapid response times for technical assistance and parts delivery. Additionally, consider investing in machines that are designed for easy maintenance and have a modular design, allowing for quick repairs and replacements. Building a network of local service providers can also be beneficial, ensuring you have support when needed without excessive delays.
Strategic Material Selection Guide for shrink wrapping machine manufacturer
What Are the Key Materials Used in Shrink Wrapping Machines?
When selecting materials for shrink wrapping machines, it is crucial to consider their properties, advantages, and limitations. The right material can significantly impact the performance, durability, and cost-effectiveness of the machinery. Below, we analyze four common materials used in shrink wrapping machines, providing insights tailored for international B2B buyers, particularly those from Africa, South America, the Middle East, and Europe.
How Does Polyethylene Influence Shrink Wrapping Machine Performance?
Polyethylene (PE) is one of the most widely used materials in shrink wrapping applications. It is known for its excellent clarity and flexibility, making it suitable for a variety of products.
Key Properties: PE has a temperature rating of up to 80°C and is resistant to moisture, which helps protect products during storage and transport.
Pros & Cons: The primary advantage of polyethylene is its cost-effectiveness and ease of manufacturing. However, it may not offer the same level of durability as other materials, particularly in high-stress environments.
Impact on Application: PE is compatible with a wide range of products, including food items, electronics, and consumer goods. However, its lower resistance to punctures can be a limitation for more fragile items.
Considerations for International Buyers: Buyers should be aware of compliance with local standards, such as ASTM and DIN, especially concerning food safety regulations. In regions like Europe, adherence to EU regulations on food packaging is crucial.
What Role Does Polypropylene Play in Shrink Wrapping?
Polypropylene (PP) is another popular material for shrink wrapping, known for its strength and clarity.
Key Properties: PP can withstand temperatures up to 120°C and offers good chemical resistance, making it suitable for various applications.
Pros & Cons: The strength of polypropylene makes it ideal for heavy-duty applications. However, it is generally more expensive than polyethylene, which could affect budget considerations.
Impact on Application: Polypropylene is particularly effective for packaging items that require a higher level of protection, such as pharmaceuticals and industrial components.
Considerations for International Buyers: Buyers from regions like South America and the Middle East should ensure that their suppliers meet local compliance standards, as well as international certifications like ISO.
How Does PVC Compare in Shrink Wrapping Applications?
Polyvinyl Chloride (PVC) is a versatile material that is often used in shrink wrapping due to its excellent shrinkage properties.
Key Properties: PVC can handle temperatures of up to 90°C and offers good resistance to chemicals and UV light.
Pros & Cons: The main advantage of PVC is its ability to conform tightly around products, providing a secure seal. However, it can be less environmentally friendly and may face regulatory scrutiny in certain regions.
Impact on Application: PVC is suitable for a variety of products, including toys and consumer goods, but its use may be restricted in food packaging in some jurisdictions.
Considerations for International Buyers: Buyers should be cautious about PVC regulations, especially in Europe, where there are stringent rules regarding its use in food packaging.
What Are the Advantages of Using PET in Shrink Wrapping?
Polyethylene Terephthalate (PET) is gaining popularity in shrink wrapping due to its superior strength and clarity.
Key Properties: PET can withstand temperatures up to 120°C and has excellent barrier properties against moisture and gases.
Pros & Cons: The primary advantage of PET is its recyclability, making it an environmentally friendly option. However, it is typically more expensive than other materials, which may impact overall costs.
Impact on Application: PET is ideal for high-end products, including beverages and cosmetics, where presentation and protection are paramount.
Considerations for International Buyers: Buyers should consider the recycling capabilities in their region, as well as compliance with local and international packaging standards.
Summary Table of Material Selection for Shrink Wrapping Machines
Material | Typical Use Case for shrink wrapping machine manufacturer | Key Advantage | Key Disadvantage/Limitation | Relative Cost (Low/Med/High) |
---|---|---|---|---|
Polyethylene | Food packaging, consumer goods | Cost-effective and flexible | Lower puncture resistance | Low |
Polypropylene | Pharmaceuticals, industrial components | High strength and durability | Higher cost compared to PE | Med |
PVC | Toys, consumer goods | Excellent shrinkage properties | Environmental concerns | Med |
PET | Beverages, cosmetics | Recyclable and strong | Higher cost | High |
This guide provides actionable insights into material selection for shrink wrapping machines, helping international B2B buyers make informed decisions tailored to their specific regional needs and compliance requirements.
In-depth Look: Manufacturing Processes and Quality Assurance for shrink wrapping machine manufacturer
What Are the Key Stages in the Manufacturing Process of Shrink Wrapping Machines?
The manufacturing process for shrink wrapping machines involves several critical stages that ensure the final product meets high standards of functionality and durability. Understanding these stages can empower B2B buyers to make informed decisions when selecting suppliers.
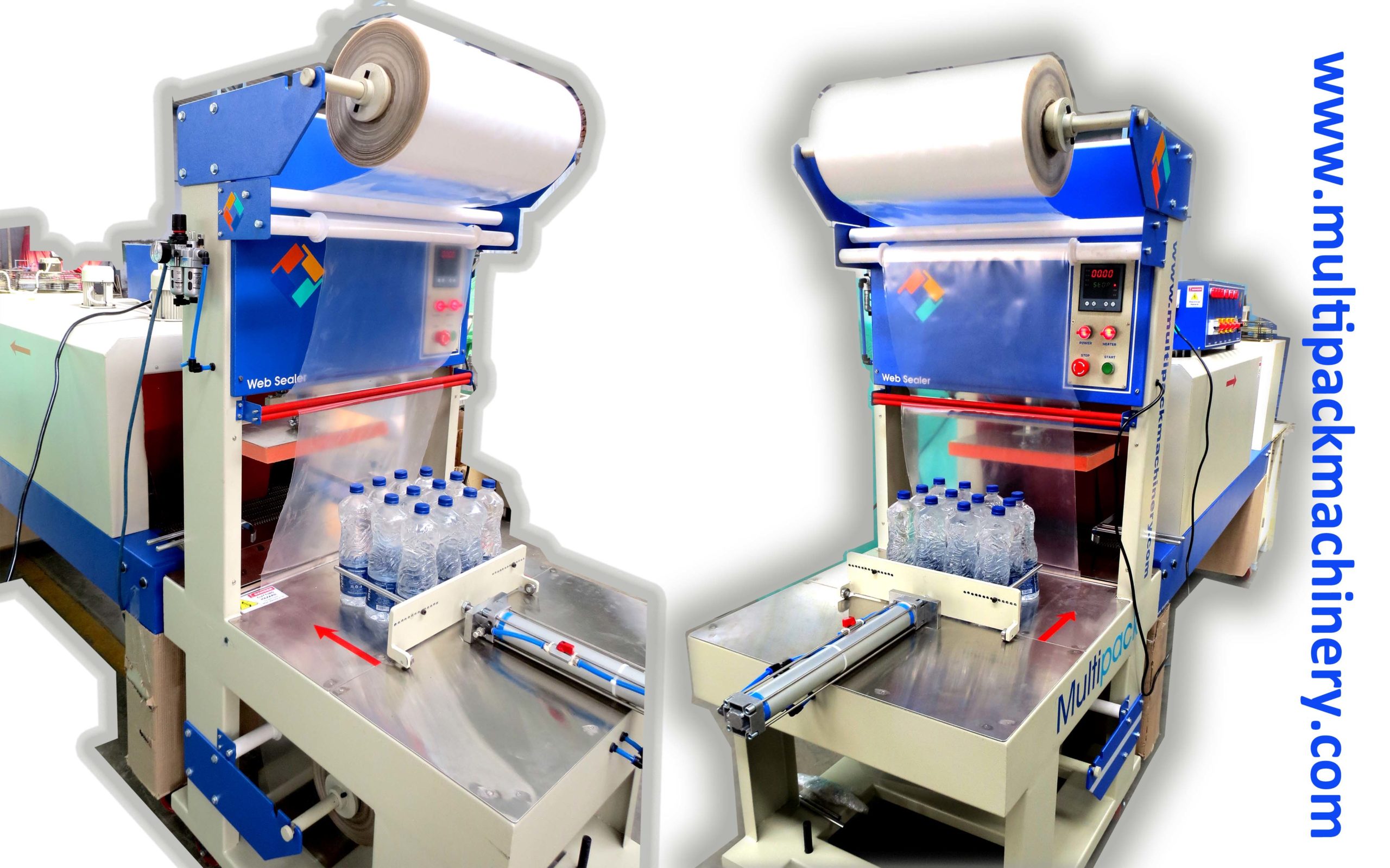
A stock image related to shrink wrapping machine manufacturer.
-
Material Preparation: This initial stage involves sourcing high-quality raw materials such as stainless steel, plastic, and electronic components. Suppliers typically conduct rigorous assessments of these materials to ensure they meet industry standards. B2B buyers should inquire about the types of materials used and their sourcing practices to ensure longevity and performance.
-
Forming: In this stage, the prepared materials are shaped into various components of the shrink wrapping machine. Techniques such as CNC machining and laser cutting are commonly employed to achieve precise dimensions. Buyers should consider suppliers that utilize advanced technology in this phase to enhance accuracy and reduce waste.
-
Assembly: Once the components are formed, they are assembled into a complete machine. This process often involves both manual labor and automated systems to ensure efficiency. Quality control measures should be integrated throughout assembly, such as continuous monitoring and adjustments to align with specifications.
-
Finishing: The final stage includes surface treatment, painting, and applying protective coatings. This not only enhances the aesthetic appeal but also improves corrosion resistance and durability. B2B buyers should request information about the finishing techniques employed and the specific coatings used, as these can significantly impact the machine’s lifespan.
How Is Quality Assurance Implemented in Shrink Wrapping Machine Manufacturing?
Quality assurance (QA) is integral to manufacturing shrink wrapping machines, helping to ensure that products meet both international standards and customer expectations. Here are the key aspects of QA that B2B buyers should consider.
What International Standards Should B2B Buyers Be Aware Of?
-
ISO 9001 Certification: This globally recognized standard focuses on quality management systems. Manufacturers that hold ISO 9001 certification demonstrate their commitment to quality and continuous improvement, which can be a deciding factor for buyers.
-
CE Marking: In Europe, CE marking signifies that a product meets EU safety, health, and environmental protection standards. For buyers in Europe, verifying this certification is crucial as it affects market access.
-
API Standards: For those in industries that require adherence to American Petroleum Institute standards, understanding these certifications is essential for ensuring the machine’s compatibility with specific operational needs.
What Quality Control Checkpoints Are Essential in the Manufacturing Process?
Quality control (QC) checkpoints are critical in ensuring that each stage of the manufacturing process adheres to established standards. Here are the main QC checkpoints to consider:
-
Incoming Quality Control (IQC): This initial checkpoint involves inspecting raw materials upon arrival. Manufacturers should have protocols for verifying material specifications and conducting tests to ensure quality before production begins.
-
In-Process Quality Control (IPQC): During the manufacturing process, continuous monitoring is essential. This includes checking dimensions, tolerances, and other specifications at various stages of production. B2B buyers should inquire about the frequency and methods of these checks.
-
Final Quality Control (FQC): Before shipment, a thorough inspection of the finished product is conducted to ensure compliance with quality standards. This may include functional testing, performance verification, and visual inspections.
What Common Testing Methods Are Used to Ensure Quality?
Several testing methods are employed to validate the functionality and safety of shrink wrapping machines:
- Functional Testing: Ensures that the machine operates as intended under various conditions.
- Durability Testing: Assesses the machine’s performance over extended periods, simulating real-world usage.
- Safety Testing: Verifies compliance with safety regulations and standards, ensuring that the machine poses no risk to operators.
How Can B2B Buyers Verify Supplier Quality Control Practices?
For international B2B buyers, particularly those from Africa, South America, the Middle East, and Europe, it is crucial to verify the quality control practices of potential suppliers. Here are actionable steps:
-
Supplier Audits: Conducting on-site audits allows buyers to observe the manufacturing process and QA measures firsthand. This can reveal a lot about the supplier’s operational integrity.
-
Requesting Quality Reports: Suppliers should provide documentation detailing their QC processes, including results from IQC, IPQC, and FQC. These reports can offer insights into their commitment to quality.
-
Third-Party Inspections: Engaging third-party inspection agencies can provide an unbiased assessment of the supplier’s compliance with quality standards. This is especially beneficial for buyers unfamiliar with local manufacturing practices.
What Nuances Should International Buyers Consider Regarding Quality Control?
International buyers must navigate various nuances when assessing quality control in shrink wrapping machine manufacturing:
-
Regulatory Differences: Understanding local regulations is essential, as these can differ significantly between regions. Buyers from Europe, for instance, should prioritize CE marking, while those in the Middle East may focus on specific local certifications.
-
Cultural Factors: Approaches to quality assurance can vary based on cultural attitudes toward manufacturing and quality. Building strong relationships with suppliers can help bridge these gaps and foster better communication regarding quality expectations.
-
Language Barriers: Effective communication is key in any B2B relationship. Buyers should ensure that they can clearly communicate their quality expectations and understand the supplier’s responses, potentially considering translation services if necessary.
By comprehensively understanding the manufacturing processes and quality assurance protocols involved in shrink wrapping machine production, B2B buyers can make informed decisions that align with their operational needs and standards.
Practical Sourcing Guide: A Step-by-Step Checklist for ‘shrink wrapping machine manufacturer’
Introduction
When sourcing a shrink wrapping machine manufacturer, it’s crucial to approach the process methodically to ensure you choose a supplier that meets your operational needs and quality standards. This guide provides a structured checklist to help international B2B buyers, particularly those from Africa, South America, the Middle East, and Europe, navigate the complexities of procurement effectively.
Step 1: Define Your Technical Specifications
Establishing clear technical specifications is fundamental to the procurement process. Consider factors such as the type of products you need to wrap, the required speed of the machine, and the materials compatible with the shrink wrapping process.
– Key Points to Include:
– Product dimensions and weight
– Desired output rate (units per hour)
– Types of shrink films to be used
Step 2: Research Potential Manufacturers
Conduct thorough research to identify potential manufacturers who specialize in shrink wrapping machines. Utilize industry directories, trade shows, and online platforms to create a shortlist of suppliers.
– Look for:
– Industry reputation and reviews
– Experience with your specific type of packaging
– Compliance with international standards
Step 3: Evaluate Supplier Capabilities
Before committing to a supplier, it’s essential to evaluate their production capabilities. Assess their technology, machinery, and production processes to ensure they can meet your volume and quality requirements.
– Consider:
– Facility certifications (ISO, CE)
– Availability of custom solutions
– Lead times and production flexibility
Step 4: Request Samples and Demonstrations
Ask potential suppliers for samples of their shrink wrapping machines in action. A demonstration can provide insights into the machine’s performance and ease of operation.
– What to Observe:
– Quality of the shrink wrap
– Machine speed and efficiency
– User interface and ease of operation
Step 5: Verify Supplier Certifications
Ensure that the manufacturers you are considering hold relevant certifications. Certifications not only guarantee quality but also compliance with safety and environmental regulations.
– Important Certifications to Check:
– ISO 9001 for quality management
– CE marking for compliance with European standards
– Any local certifications relevant to your region
Step 6: Assess After-Sales Support and Warranty Options
After-sales support is critical for maintaining productivity and ensuring machine longevity. Inquire about warranty terms, availability of spare parts, and technical support.
– Key Aspects to Evaluate:
– Duration and coverage of warranties
– Access to training and technical assistance
– Availability of spare parts and service centers
Step 7: Negotiate Terms and Finalize the Contract
Once you have selected a supplier, carefully negotiate the terms of purchase. Focus on pricing, payment terms, delivery schedules, and penalties for non-compliance.
– Key Considerations:
– Include clauses for service and maintenance
– Establish clear timelines for delivery
– Outline procedures for dispute resolution
By following this step-by-step checklist, B2B buyers can streamline their sourcing process and make informed decisions when procuring shrink wrapping machines.
Comprehensive Cost and Pricing Analysis for shrink wrapping machine manufacturer Sourcing
What Are the Key Cost Components for Sourcing Shrink Wrapping Machines?
When evaluating the total cost of sourcing shrink wrapping machines, several critical components come into play:
-
Materials: The primary materials used in the manufacturing of shrink wrapping machines include stainless steel, plastics, and electronic components. The quality and availability of these materials can significantly influence pricing. For instance, sourcing high-grade stainless steel may increase costs but provide durability.
-
Labor: Labor costs vary widely by region and can affect the overall pricing structure. In countries with higher labor costs, such as those in Europe, manufacturers might charge more. Conversely, sourcing from regions with lower labor costs, such as parts of South America or Africa, could yield savings.
-
Manufacturing Overhead: This includes costs related to utilities, facilities, and administrative expenses. Manufacturers in regions with high operational costs will typically reflect these in their pricing. It’s essential to assess whether the manufacturer’s location affects their overhead significantly.
-
Tooling: Specialized tools and machinery required for production can add to costs. If a manufacturer needs to invest in custom tooling for specific machine specifications, this will be reflected in the final price.
-
Quality Control (QC): Rigorous QC processes ensure the machines meet industry standards. While this might increase upfront costs, it often leads to reduced long-term expenses due to lower failure rates and warranty claims.
-
Logistics: Transportation costs are a crucial factor, especially for international buyers. Freight charges, import duties, and tariffs can add substantial costs to the final price. Understanding the shipping methods and associated costs is vital for accurate budgeting.
-
Margin: Manufacturers typically apply a profit margin based on their costs and market positioning. This margin can vary significantly depending on the manufacturer’s reputation and the perceived value of their machines.
How Do Price Influencers Affect Sourcing Decisions for Shrink Wrapping Machines?
Several factors can influence the pricing of shrink wrapping machines:
-
Volume/MOQ (Minimum Order Quantity): Larger orders often come with discounts. Understanding the MOQ can help buyers negotiate better pricing.
-
Specifications and Customization: Custom features or specifications can increase costs. Buyers should evaluate whether these modifications are essential for their operations.
-
Materials and Quality Certifications: Machines that meet certain industry certifications may cost more but can provide peace of mind regarding performance and compliance.
-
Supplier Factors: The reputation and reliability of the supplier can impact pricing. Established suppliers may charge more due to their proven track record.
-
Incoterms: The chosen Incoterms affect the responsibility of shipping costs and risks. Familiarizing oneself with terms like FOB (Free on Board) or CIF (Cost, Insurance, and Freight) can help in negotiating better shipping arrangements.
What Buyer Tips Can Enhance Cost Efficiency in Shrink Wrapping Machine Procurement?
For international B2B buyers, particularly in Africa, South America, the Middle East, and Europe, consider these actionable tips:
-
Negotiate Effectively: Don’t hesitate to negotiate terms, especially on volume discounts or payment terms. Establishing a good relationship with the supplier can lead to better pricing over time.
-
Evaluate Total Cost of Ownership (TCO): Beyond the initial purchase price, consider operational costs, maintenance, and potential downtime. A cheaper machine may lead to higher TCO if it requires frequent repairs or replacement.
-
Understand Pricing Nuances: Different regions have distinct pricing structures due to local economic conditions. For example, while a machine may be cheaper in Brazil, logistics costs might offset these savings for buyers in Europe.
-
Consider Local Regulations: Ensure that the machines comply with local regulations in your market, as non-compliance can lead to additional costs down the line.
Disclaimer for Indicative Prices
While this analysis provides a comprehensive overview of the cost and pricing structure for shrink wrapping machines, it is essential to note that prices can vary widely based on specific requirements, market conditions, and supplier negotiations. Always request detailed quotes and perform due diligence before finalizing any procurement decisions.
Alternatives Analysis: Comparing shrink wrapping machine manufacturer With Other Solutions
When considering packaging solutions, it’s crucial for international B2B buyers to evaluate various methods that can effectively meet their operational needs. Shrink wrapping machines are a popular choice for packaging products, but several alternatives exist that may provide better alignment with specific business requirements. This section will compare shrink wrapping machines with two viable alternatives: stretch wrapping and vacuum sealing.
Comparison Table: Shrink Wrapping vs. Alternatives
Comparison Aspect | Shrink Wrapping Machine Manufacturer | Stretch Wrapping | Vacuum Sealing |
---|---|---|---|
Performance | High-speed, effective for various products | Good for palletizing, less effective for single items | Excellent for preserving freshness, ideal for food products |
Cost | Moderate to high initial investment | Generally lower cost for equipment | Moderate cost, especially for high-quality machines |
Ease of Implementation | Requires setup and training | Easier to operate, quick setup | Requires training for optimal use |
Maintenance | Regular maintenance needed | Low maintenance requirements | Regular maintenance required, especially for seals |
Best Use Case | Ideal for large volume production | Best for shipping and storing bulk items | Best for food packaging and preserving perishables |
What Are the Advantages and Disadvantages of Stretch Wrapping?
Stretch wrapping is a method that involves wrapping a stretchable plastic film around products, typically on pallets.
Pros:
– Cost-Effective: The machinery and materials are generally less expensive than shrink wrapping.
– Quick Application: Stretch wrapping can be set up quickly and is easy to operate, making it ideal for businesses with fast-paced shipping needs.
– Versatile: Suitable for various products, especially bulk items.
Cons:
– Limited Protection: While it secures items, it does not provide the same level of protection from external elements as shrink wrapping.
– Less Aesthetic Appeal: The appearance may not be as polished as shrink-wrapped products, which can affect branding.
How Does Vacuum Sealing Compare for Product Packaging?
Vacuum sealing removes air from packaging, creating a tight seal around products, particularly food items.
Pros:
– Extended Shelf Life: Vacuum sealing is exceptional for prolonging the freshness of food products, making it ideal for food exporters.
– Space Efficient: Reduces storage space by compressing products, which is advantageous for logistics.
Cons:
– Higher Operational Costs: Depending on the quality of the machine, vacuum sealing can become costly, especially for larger operations.
– Training Required: Staff may require training to operate vacuum sealers effectively, especially for high-volume production.
How Can B2B Buyers Choose the Right Packaging Solution?
When selecting the right packaging solution, B2B buyers must assess their specific needs, including the type of products they are handling, production volume, and budget constraints. Shrink wrapping machines are excellent for high-volume production with a focus on presentation, while stretch wrapping may be more appropriate for bulk shipping. Conversely, vacuum sealing is the best option for food products requiring preservation. By carefully evaluating the performance, cost, ease of implementation, and maintenance needs of each solution, buyers can make informed decisions that align with their operational goals and market demands.
Essential Technical Properties and Trade Terminology for shrink wrapping machine manufacturer
What Are the Key Technical Properties of Shrink Wrapping Machines?
When selecting a shrink wrapping machine, understanding the essential technical specifications is crucial for making informed purchasing decisions. Here are some critical specs that every international B2B buyer should consider:
1. Material Grade
The material grade of the shrink film used in the machine significantly influences the durability and performance of the packaging. Common materials include polyethylene (PE), polyvinyl chloride (PVC), and polyolefin. Each type has unique properties, such as heat resistance and clarity, which can affect product presentation and shelf life. Selecting the right material grade ensures that your products are well-protected during shipping and storage, a vital consideration for B2B operations.
2. Tolerance
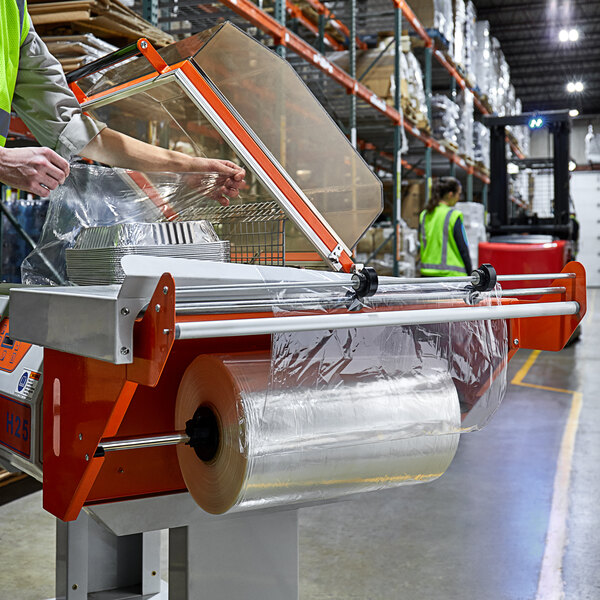
A stock image related to shrink wrapping machine manufacturer.
Tolerance refers to the allowable variation in the dimensions of the machine’s components and the shrink film. A tighter tolerance often indicates higher precision in packaging, which is essential for products that require specific dimensions for optimal protection and presentation. For international buyers, especially those in industries like pharmaceuticals or electronics, understanding tolerance levels can help mitigate risks associated with product damage.
3. Speed and Throughput
The speed at which a shrink wrapping machine operates is a critical factor for production efficiency. Measured in packages per minute, understanding the throughput capacity allows businesses to align their production schedules with demand. Buyers from regions like South America and Africa, where production scales may vary, should assess their operational needs to select a machine that balances speed and quality.
4. Heating Method
Shrink wrapping machines utilize various heating methods, including electric, gas, or infrared. The choice of heating method impacts energy consumption, operational costs, and the quality of the shrink wrap. Buyers should consider the availability of energy sources in their region and the long-term cost implications when evaluating machines with different heating technologies.
5. Control Systems
Advanced control systems enhance the functionality of shrink wrapping machines by enabling precise adjustments to speed, temperature, and film tension. Machines equipped with programmable logic controllers (PLCs) offer greater flexibility and efficiency. For B2B buyers, particularly in competitive markets like Europe, investing in machines with sophisticated control systems can lead to significant operational advantages.
What Are Common Trade Terms in the Shrink Wrapping Industry?
Familiarity with industry-specific terminology is essential for effective communication and negotiation in the B2B sector. Here are some common terms relevant to shrink wrapping machinery:
1. OEM (Original Equipment Manufacturer)
An OEM refers to a company that produces parts and equipment that may be marketed by another manufacturer. In the context of shrink wrapping machines, understanding whether a supplier is an OEM can affect pricing, warranty, and support services. Buyers should ensure they are sourcing from reputable OEMs to ensure quality and reliability.
2. MOQ (Minimum Order Quantity)
MOQ is the smallest quantity of a product that a supplier is willing to sell. For B2B buyers, especially those in regions with diverse market needs, understanding MOQ is vital for inventory management and cost-effectiveness. Negotiating MOQs can help businesses optimize their purchasing strategy while minimizing excess inventory.
3. RFQ (Request for Quotation)
An RFQ is a standard business process where buyers request quotes from suppliers for specific products or services. For international buyers, submitting a well-structured RFQ can facilitate clear communication regarding specifications and pricing, ultimately leading to better purchasing decisions.
4. Incoterms (International Commercial Terms)
Incoterms are a set of international rules that define the responsibilities of buyers and sellers in international transactions. Understanding these terms is essential for B2B buyers to clarify shipping responsibilities, costs, and risks. Familiarity with Incoterms can help buyers avoid misunderstandings and ensure smoother transactions.
5. Lead Time
Lead time refers to the period from placing an order to receiving the goods. In the context of shrink wrapping machines, shorter lead times can enhance operational efficiency. International buyers should inquire about lead times when negotiating contracts, as this will impact their production schedules and inventory management.
By grasping these essential technical properties and trade terminologies, international B2B buyers can navigate the complexities of acquiring shrink wrapping machines more effectively, ensuring they select the right equipment for their operational needs.
Navigating Market Dynamics and Sourcing Trends in the shrink wrapping machine manufacturer Sector
What Are the Key Market Dynamics Affecting Shrink Wrapping Machine Manufacturers?
The global shrink wrapping machine market is influenced by several key drivers that shape sourcing strategies for international B2B buyers. The rise of e-commerce and the growing demand for packaged goods across various sectors, including food and beverage, pharmaceuticals, and consumer products, are significant contributors to market growth. Notably, emerging economies in Africa and South America are witnessing increased investments in manufacturing capabilities, leading to higher demand for efficient packaging solutions.
Technological advancements also play a crucial role in this sector. Innovations in automation, such as the integration of artificial intelligence and Internet of Things (IoT) technologies, are improving operational efficiency and reducing waste. For instance, manufacturers are increasingly adopting smart shrink wrapping machines that can be monitored and controlled remotely, providing real-time data on production processes. This trend not only enhances productivity but also enables manufacturers to respond swiftly to market changes.
Furthermore, international buyers should be aware of regional market dynamics. In Europe, stringent regulations regarding packaging waste and sustainability are driving manufacturers to invest in eco-friendly solutions. Conversely, in the Middle East, rapid urbanization and industrialization are propelling demand for advanced packaging technologies. Understanding these regional trends is essential for B2B buyers looking to source shrink wrapping machines that align with their operational needs and market demands.
How Does Sustainability Influence Sourcing Decisions for Shrink Wrapping Machines?
Sustainability has become a pivotal consideration for B2B buyers in the shrink wrapping machine sector. The environmental impact of packaging materials is under scrutiny, prompting manufacturers to adopt more sustainable practices. Buyers are increasingly prioritizing suppliers that demonstrate a commitment to ethical sourcing and environmentally friendly materials.
For instance, materials such as biodegradable films and recyclable plastics are gaining traction in the shrink wrapping industry. By choosing suppliers who offer these ‘green’ alternatives, buyers can significantly reduce their carbon footprint and contribute to a circular economy. Additionally, certifications like ISO 14001 for environmental management and Forest Stewardship Council (FSC) for sustainable materials are indicators of a supplier’s commitment to sustainability.
Moreover, ethical supply chains are critical for maintaining brand reputation and customer loyalty. B2B buyers should seek manufacturers who transparently disclose their sourcing practices and adhere to ethical labor standards. This not only ensures compliance with international regulations but also fosters trust among stakeholders and consumers alike.
What Is the Historical Context of Shrink Wrapping Machine Manufacturing?
The shrink wrapping machine industry has evolved significantly over the past few decades. Initially, shrink wrapping technology was primarily used for basic packaging needs. However, advancements in machine design and materials have transformed the sector, allowing for greater versatility and efficiency.
In the 1980s, the introduction of heat-shrinkable films revolutionized the packaging process, enabling manufacturers to wrap products tightly and securely. As globalization increased, so did the demand for efficient packaging solutions that could accommodate diverse products and markets. Today, the industry is characterized by a focus on automation and sustainability, reflecting broader trends in manufacturing and consumer preferences.
Understanding this evolution is crucial for B2B buyers, as it highlights the importance of selecting suppliers that are not only technologically advanced but also aligned with contemporary sustainability practices. This historical context can aid buyers in making informed sourcing decisions that are both strategic and responsible.
Frequently Asked Questions (FAQs) for B2B Buyers of shrink wrapping machine manufacturer
-
How do I choose the right shrink wrapping machine for my business needs?
Choosing the right shrink wrapping machine involves assessing your production requirements, including product size, volume, and type of packaging material. Start by determining the throughput you need—machines vary significantly in speed and capacity. Additionally, consider the machine’s adaptability for different product shapes and sizes, as well as compatibility with your current production line. Request samples from manufacturers to evaluate machine performance and ensure it meets your specifications before making a decision. -
What are the common features of shrink wrapping machines that I should look for?
When evaluating shrink wrapping machines, look for features such as adjustable temperature controls, efficient sealing mechanisms, and user-friendly interfaces. Consider machines with energy-saving options and quick changeover capabilities for different products. Additionally, assess the durability and build quality, as well as the availability of support and maintenance services from the manufacturer. These features will enhance operational efficiency and reduce downtime in your production line. -
What is the minimum order quantity (MOQ) for shrink wrapping machines from manufacturers?
Minimum order quantities for shrink wrapping machines can vary widely based on the manufacturer and the complexity of the machine. Typically, MOQs can range from one unit for standard machines to several units for custom or specialized models. It’s crucial to discuss your needs with potential suppliers to understand their MOQ policies. Negotiating terms based on your specific requirements can sometimes yield flexibility, especially if you establish a long-term partnership. -
What payment terms should I expect when purchasing shrink wrapping machines internationally?
Payment terms for international purchases of shrink wrapping machines can vary significantly. Common practices include upfront deposits (often 30-50% of the total cost) with the balance due before shipment or upon delivery. Some suppliers may offer credit terms or financing options, especially for bulk orders. Always clarify payment methods accepted (e.g., bank transfer, letter of credit) and ensure to factor in additional costs like tariffs and shipping fees when budgeting for your purchase. -
How can I ensure the quality of shrink wrapping machines from manufacturers?
To ensure the quality of shrink wrapping machines, request certifications such as ISO or CE marking, which indicate compliance with international standards. Additionally, ask for references or case studies from other clients to gauge the manufacturer’s reliability. Conducting a factory visit or auditing the manufacturer can provide deeper insights into their production processes. Implementing a trial period or warranty can also safeguard your investment and ensure the machine meets your operational requirements. -
What are the logistics considerations when importing shrink wrapping machines?
When importing shrink wrapping machines, consider shipping methods, customs clearance, and delivery timelines. Choose a reliable freight forwarder who understands the complexities of international shipping and can navigate customs regulations in your country. Factor in additional costs such as import duties, taxes, and insurance. Ensure that the supplier provides all necessary documentation, including bills of lading and certificates of origin, to facilitate smooth customs clearance. -
Can shrink wrapping machines be customized to fit specific product dimensions?
Yes, many manufacturers offer customization options for shrink wrapping machines to accommodate specific product dimensions and packaging needs. Customization can include adjustments to the machine’s size, sealing mechanisms, and even the type of film used. When discussing customization, provide detailed specifications and any product samples to the manufacturer. This collaboration can result in a tailored solution that optimizes your packaging process. -
What after-sales support should I expect from shrink wrapping machine manufacturers?
After-sales support is crucial for maintaining the efficiency of your shrink wrapping machines. Reputable manufacturers typically offer comprehensive support, including installation, operator training, and troubleshooting assistance. Inquire about the availability of spare parts and the warranty period for the machine. Additionally, check if the manufacturer provides ongoing maintenance services or technical support via phone or email to address any issues that may arise post-purchase.
Important Disclaimer & Terms of Use
⚠️ Important Disclaimer
The information provided in this guide, including content regarding manufacturers, technical specifications, and market analysis, is for informational and educational purposes only. It does not constitute professional procurement advice, financial advice, or legal advice.
While we have made every effort to ensure the accuracy and timeliness of the information, we are not responsible for any errors, omissions, or outdated information. Market conditions, company details, and technical standards are subject to change.
B2B buyers must conduct their own independent and thorough due diligence before making any purchasing decisions. This includes contacting suppliers directly, verifying certifications, requesting samples, and seeking professional consultation. The risk of relying on any information in this guide is borne solely by the reader.
Strategic Sourcing Conclusion and Outlook for shrink wrapping machine manufacturer
How Can Strategic Sourcing Enhance Your Procurement Process?
In the competitive landscape of shrink wrapping machinery, strategic sourcing emerges as a critical element for international B2B buyers. By leveraging a well-defined sourcing strategy, companies can significantly reduce costs while enhancing product quality and supplier relationships. Engaging with manufacturers that offer innovative technologies not only ensures better efficiency but also aligns with sustainability goals, which are increasingly important in markets across Africa, South America, the Middle East, and Europe.
What Are the Key Takeaways for B2B Buyers in Different Regions?
Buyers should prioritize evaluating suppliers based on their technological capabilities, production capacity, and after-sales support. Establishing long-term partnerships with reliable manufacturers can lead to better pricing structures and improved supply chain resilience. Additionally, understanding regional market trends and regulatory frameworks can empower buyers to make informed decisions that align with local needs.
What Does the Future Hold for Shrink Wrapping Machine Procurement?
Looking ahead, the demand for high-efficiency shrink wrapping machines is set to rise, driven by the growth of e-commerce and the need for robust packaging solutions. International B2B buyers are encouraged to stay proactive in their sourcing strategies, considering factors such as automation, customization, and environmental impact. By embracing these elements, businesses can not only enhance their operational efficiency but also position themselves favorably in a rapidly evolving market. Engaging with the right manufacturers today will set the foundation for success in the years to come.