Custom Garden Bench Solutions: Your Ultimate Buying Guide (2025)
Introduction: Navigating the Global Market for garden bench custom
In the ever-evolving global market, sourcing custom garden benches presents unique challenges for international B2B buyers. Whether you are looking to furnish an outdoor space in Africa, South America, the Middle East, or Europe, understanding the nuances of this niche can be daunting. Buyers often grapple with ensuring quality, durability, and aesthetic appeal while navigating diverse supplier landscapes and fluctuating costs. This guide is designed to empower B2B buyers by providing comprehensive insights into the types of custom garden benches available, their various applications, and effective supplier vetting processes.
What Are the Different Types of Custom Garden Benches?
Understanding the range of options available is crucial. From modern designs to traditional styles, this guide explores the myriad choices that can cater to different market preferences.
How to Evaluate Suppliers for Custom Garden Benches?
Selecting the right supplier can significantly impact your purchasing decision. We will delve into key criteria for vetting suppliers, including quality assurance practices and responsiveness to international shipping requirements.
What Are the Cost Considerations for Custom Garden Benches?
Pricing can vary widely based on materials, design complexity, and order volume. This guide will outline how to effectively budget for your purchases and negotiate favorable terms.
By the end of this guide, international B2B buyers will be equipped with actionable insights and strategies to make informed purchasing decisions, ensuring that your investment in custom garden benches meets both aesthetic desires and functional needs.
Understanding garden bench custom Types and Variations
Type Name | Key Distinguishing Features | Primary B2B Applications | Brief Pros & Cons for Buyers |
---|---|---|---|
Classic Wooden Benches | Traditional design, often made from hardwoods like teak or oak | Landscaping, parks, and gardens | Pros: Timeless appeal, durable; Cons: Requires maintenance, may be costly. |
Metal Garden Benches | Made from materials like aluminum or wrought iron, often with intricate designs | Urban parks, commercial spaces | Pros: Low maintenance, modern aesthetic; Cons: Can be heavy, may rust without treatment. |
Eco-Friendly Benches | Constructed from recycled materials or sustainably sourced wood | Eco-parks, green building projects | Pros: Environmentally friendly, unique designs; Cons: May have limited availability, potentially higher costs. |
Modular Benches | Flexible designs that can be rearranged or expanded | Public spaces, event venues | Pros: Versatile, customizable; Cons: May require more space, can be expensive. |
Storage Benches | Benches with integrated storage compartments | Gardens, patios, and outdoor events | Pros: Functional, space-saving; Cons: Limited seating capacity, can be bulky. |
What Are the Characteristics of Classic Wooden Benches?
Classic wooden benches are characterized by their traditional craftsmanship and use of high-quality hardwoods such as teak or oak. These benches are often designed with simple lines and elegant finishes, making them suitable for a variety of outdoor settings, including gardens, parks, and private landscaping projects. B2B buyers should consider the durability and aesthetic appeal of these benches, as they can enhance the overall look of outdoor spaces. However, maintenance is required to preserve the wood, which can be a drawback for some buyers.
How Do Metal Garden Benches Differ from Other Types?
Metal garden benches are typically made from materials like aluminum or wrought iron, featuring both functional and decorative designs. They are ideal for urban parks and commercial spaces due to their ability to withstand harsh weather conditions and require minimal maintenance. For B2B buyers, the long-term cost-effectiveness of metal benches is appealing, although their weight and potential for rusting if not treated can be concerns. The modern aesthetic they offer is also a significant selling point.
What Are the Benefits of Eco-Friendly Benches?
Eco-friendly benches are crafted from recycled materials or sustainably sourced wood, making them an excellent choice for environmentally conscious projects. These benches often feature unique designs that stand out in parks and green building initiatives. B2B buyers interested in promoting sustainability will find these benches appealing, although they may face challenges related to availability and potentially higher costs compared to conventional options. The positive brand image associated with eco-friendly products can also enhance a company’s reputation.
Why Choose Modular Benches for Public Spaces?
Modular benches provide flexibility in design, allowing for easy rearrangement and expansion based on the needs of public spaces or event venues. Their customizable nature makes them suitable for various applications, from urban parks to outdoor festivals. B2B buyers should weigh the benefits of versatility against potential space requirements and higher costs. Modular benches can significantly enhance the functionality and appeal of communal areas, making them a worthwhile investment.
What Are the Key Features of Storage Benches?
Storage benches combine seating with practical storage solutions, making them ideal for gardens, patios, and outdoor events. Their design typically includes compartments for stowing away cushions, gardening tools, or outdoor accessories, offering a space-saving solution. For B2B buyers, the dual functionality of these benches is a strong advantage, although they may have limited seating capacity and can be bulkier than other types. Understanding the specific needs of the intended environment can help buyers choose the right storage bench.
Related Video: Project – How to build a quick and easy garden bench out of redwood 2×6’s and 2×4’s
Key Industrial Applications of garden bench custom
Industry/Sector | Specific Application of garden bench custom | Value/Benefit for the Business | Key Sourcing Considerations for this Application |
---|---|---|---|
Hospitality & Tourism | Custom benches in outdoor dining areas | Enhances guest experience and extends seating capacity | Durability against weather, design alignment with brand aesthetics |
Urban Development & Parks | Benches in public parks and urban spaces | Promotes community engagement and beautifies public areas | Compliance with local regulations, material sustainability |
Retail & Shopping Centers | Decorative benches in shopping malls and plazas | Increases foot traffic and provides resting spots for shoppers | Customization options, integration with overall mall design |
Educational Institutions | Benches in campus gardens and recreational areas | Provides students with relaxation spaces, fostering social interaction | Safety standards, weather resistance, and aesthetic appeal |
Real Estate & Property Management | Outdoor benches in residential complexes and developments | Adds value to properties and enhances outdoor living spaces | Quality of materials, maintenance requirements, and cost-effectiveness |
How is ‘garden bench custom’ utilized in the hospitality and tourism sector?
In the hospitality and tourism industry, custom garden benches are strategically placed in outdoor dining areas and relaxation zones. These benches not only enhance the aesthetic appeal of the venue but also improve guest comfort by providing additional seating options. Buyers in this sector should focus on sourcing benches that are durable and weather-resistant, as they need to withstand various environmental conditions while aligning with the brand’s design and ambiance.
What role do custom benches play in urban development and public parks?
In urban development, custom garden benches are essential for enhancing public parks and outdoor spaces. They serve as a focal point for community engagement, encouraging residents to gather and interact. For international buyers, particularly in Africa and the Middle East, it is crucial to consider local regulations and sustainability practices when sourcing these benches. The materials used should be eco-friendly and capable of enduring the local climate.
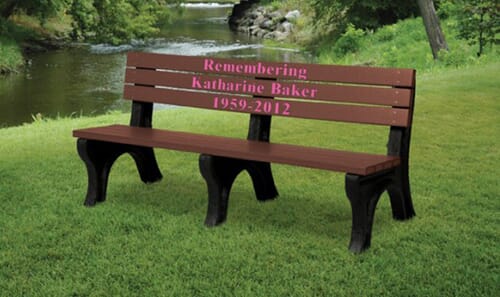
A stock image related to garden bench custom.
How can retail and shopping centers benefit from custom garden benches?
Shopping malls and plazas utilize decorative custom benches to create inviting spaces for shoppers. These benches not only provide a place for customers to rest but also contribute to the overall shopping experience, potentially increasing foot traffic. When sourcing benches, retailers should prioritize customization options that align with their branding and ensure that the benches are durable enough to handle high usage.
Why are custom benches important for educational institutions?
Educational institutions often incorporate custom benches into campus gardens and recreational areas to provide students with comfortable spaces for relaxation and socialization. These benches foster a sense of community and enhance the overall campus experience. Buyers should ensure that the benches meet safety standards and are constructed from weather-resistant materials to withstand outdoor conditions while maintaining an appealing design.
How do garden benches add value in real estate and property management?
In the real estate sector, custom garden benches are a valuable addition to residential complexes and developments. They enhance outdoor living spaces, making properties more attractive to potential buyers or renters. Property managers should consider the quality of materials used in the benches, as well as their maintenance requirements, to ensure long-term value and satisfaction for residents.
Related Video: The PERFECT Woodworking Workbench // How To Build The Ultimate Hybrid Workholding Bench
3 Common User Pain Points for ‘garden bench custom’ & Their Solutions
Scenario 1: Understanding Material Quality and Durability Concerns
The Problem: When sourcing custom garden benches, many B2B buyers face uncertainty regarding the quality and durability of materials. Buyers from regions like Africa and the Middle East often deal with harsh weather conditions that can significantly affect outdoor furniture. Without a clear understanding of which materials withstand these challenges, buyers risk investing in products that may deteriorate quickly, leading to increased costs and customer dissatisfaction.
The Solution: To ensure the longevity of custom garden benches, buyers should prioritize sourcing from reputable manufacturers who provide detailed specifications about materials used. For example, hardwoods like teak or mahogany are known for their resilience against weather elements. Additionally, consider benches made with high-quality metal frames, coated with rust-resistant finishes. Request samples or conduct tests to verify durability claims before placing large orders. Collaborating with suppliers who offer warranties can also safeguard against premature wear and tear, ensuring your investment remains sound over time.
Scenario 2: Navigating Customization Options and Design Limitations
The Problem: B2B buyers often encounter challenges when trying to customize garden benches to fit specific aesthetic or functional requirements. Buyers from South America, for instance, might want benches that align with local cultural themes or color schemes. However, many suppliers provide limited customization options, leading to frustration and a mismatch with buyers’ expectations.
The Solution: To effectively navigate customization challenges, buyers should engage in thorough discussions with manufacturers about design capabilities. Before finalizing a supplier, request a portfolio of past custom projects to assess their flexibility and creativity. Consider using design software or collaborating with local designers who can provide tailored suggestions aligned with regional tastes. Establish clear communication about your specifications, including dimensions, materials, and style, to ensure the end product meets your vision. A well-defined design brief can help manufacturers deliver a product that resonates with your market.
Scenario 3: Overcoming Shipping and Logistical Issues
The Problem: International buyers, particularly in Europe and the Middle East, often face logistical hurdles when importing custom garden benches. Shipping delays, customs regulations, and high freight costs can complicate the procurement process, leading to project timelines being pushed back and unexpected expenses arising.
The Solution: To mitigate shipping and logistical challenges, buyers should consider working with suppliers who have established logistics networks and experience in international shipping. Ask potential suppliers about their shipping options and timelines before placing orders. It is beneficial to select suppliers who offer comprehensive shipping solutions, including door-to-door delivery. Additionally, familiarize yourself with local customs regulations to avoid unexpected fees and delays. Planning ahead by ordering well in advance of peak seasons can also help ensure that products arrive on time, maintaining project schedules and customer satisfaction.
Strategic Material Selection Guide for garden bench custom
What Are the Key Properties of Common Materials for Custom Garden Benches?
When selecting materials for custom garden benches, it is essential to consider their properties, durability, cost, and suitability for specific applications. Here, we analyze four common materials used in the manufacturing of garden benches: wood, metal, plastic, and composite materials.
How Does Wood Perform as a Material for Garden Benches?
Wood is a traditional choice for garden benches, offering aesthetic appeal and natural warmth. Key properties include its natural insulation, which makes it comfortable in varying temperatures, and its ability to withstand moderate pressure. However, wood is susceptible to rot, pests, and weathering, which can significantly affect its longevity.
Pros:
– Aesthetically pleasing and customizable.
– Good insulation properties.
– Generally lower initial cost.
Cons:
– Requires regular maintenance (e.g., sealing, staining).
– Vulnerable to environmental damage (e.g., UV rays, moisture).
– Limited lifespan compared to metals.
For international buyers, wood must comply with local regulations regarding sustainability and sourcing. In regions like Europe and parts of Africa, certified wood (e.g., FSC-certified) is preferred to ensure environmental responsibility.
What Are the Advantages of Metal for Custom Garden Benches?
Metal, particularly aluminum and stainless steel, is increasingly popular for garden benches due to its strength and durability. Key properties include high corrosion resistance, especially in stainless steel, and the ability to withstand extreme temperatures and pressures without deforming.
Pros:
– Extremely durable and low maintenance.
– Resistant to pests and rot.
– Can be recycled, aligning with sustainability goals.
Cons:
– Higher initial cost compared to wood.
– Can become hot in direct sunlight, impacting comfort.
– May require special coatings for corrosion resistance in humid environments.
International buyers should consider the specific metal grades that comply with local standards, such as ASTM for the U.S. or EN standards in Europe. In the Middle East, where humidity is high, selecting corrosion-resistant metals is crucial.
How Do Plastic Materials Compare for Garden Bench Applications?
Plastic materials, particularly high-density polyethylene (HDPE), offer a lightweight and weather-resistant option for garden benches. Key properties include excellent resistance to moisture, UV rays, and a wide range of temperatures, making them ideal for outdoor use.
Pros:
– Very low maintenance and easy to clean.
– Resistant to fading and cracking.
– Generally lower cost and lightweight.
Cons:
– Less aesthetic appeal compared to wood or metal.
– Can be less sturdy and may not support heavier weights.
– Environmental concerns regarding plastic waste.
For international buyers, ensuring compliance with recycling standards and certifications (such as ISO 14001) is vital, especially in regions with stringent environmental regulations, like Europe.
What Are the Benefits of Composite Materials for Custom Garden Benches?
Composite materials, which combine wood fibers with plastic, provide a blend of the best properties of both materials. Key properties include resistance to moisture and pests, along with a more natural appearance compared to pure plastic.
Pros:
– Durable and resistant to weathering.
– Requires minimal maintenance.
– Offers a natural look without the drawbacks of wood.
Cons:
– Higher cost compared to traditional wood.
– Limited color options compared to pure plastic.
– May not be as strong as solid wood or metal.
International buyers should ensure that composite materials meet local building codes and standards, particularly in regions like South America and Africa, where environmental conditions can vary widely.
Summary Table of Material Selection for Custom Garden Benches
Material | Typical Use Case for garden bench custom | Key Advantage | Key Disadvantage/Limitation | Relative Cost (Low/Med/High) |
---|---|---|---|---|
Wood | Residential gardens, parks | Aesthetic appeal and natural warmth | Requires maintenance and is weather-sensitive | Low |
Metal | Commercial spaces, public parks | High durability and low maintenance | Can get hot and may require coatings | High |
Plastic | Playgrounds, casual outdoor settings | Low maintenance and lightweight | Less aesthetic and potential environmental concerns | Low |
Composite | High-end residential and commercial areas | Durable and natural appearance | Higher cost and limited color options | Medium |
This guide provides actionable insights for international B2B buyers, helping them make informed decisions when selecting materials for custom garden benches.
In-depth Look: Manufacturing Processes and Quality Assurance for garden bench custom
What Are the Main Stages of Manufacturing Custom Garden Benches?
The manufacturing process for custom garden benches typically involves several key stages that ensure high-quality and durable products. Understanding these stages is essential for B2B buyers to ensure they partner with suppliers who adhere to best practices.
Material Preparation: What Materials Are Commonly Used?
The first step in the manufacturing process is material preparation, which involves selecting the right type of wood, metal, or composite materials. Common choices for garden benches include:
- Wood: Teak, cedar, and eucalyptus are popular for their natural resistance to weather and decay.
- Metal: Aluminum and steel are favored for their strength and durability.
- Composites: Recycled materials and plastics are increasingly used for their sustainability and low maintenance.
Once the materials are selected, they undergo treatments such as drying or chemical preservation to enhance longevity and resistance to environmental factors.
How Is the Forming Process Conducted?
Following material preparation, the forming process shapes the materials into the desired bench components. This stage may involve various techniques:
- Cutting: Precision cutting tools are used to achieve accurate dimensions.
- Shaping: Techniques such as bending for metal or routing for wood allow for intricate designs.
- Joining: Components are joined using methods like doweling, mortise-and-tenon, or welding for metal parts.
Advanced technology, such as CNC (Computer Numerical Control) machines, can enhance accuracy and efficiency during this stage.
What Does the Assembly Process Involve?
The assembly stage is where all components come together to form the final product. This process generally includes:
- Dry Assembly: A preliminary assembly is conducted to check fit and alignment before final attachment.
- Final Assembly: Components are securely fastened, often using adhesives, screws, or bolts.
- Quality Checks: Initial quality checks are performed to ensure structural integrity and design fidelity.
Proper assembly techniques not only enhance the aesthetics of the benches but also ensure their functionality and durability.
How Is the Finishing Process Executed?
The finishing stage enhances the visual appeal and protects the bench from environmental damage. Common finishing processes include:
- Sanding: Smooths surfaces to prepare for finishing.
- Staining or Painting: Adds color and protects the surface; UV-resistant finishes are preferred for outdoor use.
- Sealing: A final sealant is applied to protect against moisture and pests.
This stage is critical for ensuring that the benches maintain their appearance and functionality over time.
What International Standards Guide Quality Assurance for Garden Benches?
Quality assurance in the manufacturing of custom garden benches is crucial for ensuring that products meet safety and performance standards. B2B buyers should be familiar with relevant international standards and quality control checkpoints.
Which International Standards Are Relevant?
International standards such as ISO 9001 are widely recognized in manufacturing. This standard focuses on maintaining consistent quality through effective quality management systems. Additionally, specific industry standards may apply:
- CE Marking: Required for products sold in the European Economic Area, indicating compliance with health, safety, and environmental protection standards.
- API Standards: Relevant for metal products, ensuring they meet specific safety and performance criteria.
Understanding these standards helps buyers ensure that their suppliers adhere to recognized quality benchmarks.
What Are the Key Quality Control Checkpoints?
Quality control (QC) is integral to the manufacturing process, involving several checkpoints to ensure product quality at various stages:
- Incoming Quality Control (IQC): This initial checkpoint assesses raw materials for compliance with specifications.
- In-Process Quality Control (IPQC): Conducted during manufacturing to monitor processes and identify defects early.
- Final Quality Control (FQC): The final inspection of completed products to ensure they meet design specifications and quality standards.
Each checkpoint serves to catch potential issues before they escalate, ensuring that only high-quality products reach the buyer.
How Can B2B Buyers Verify Supplier Quality Control?
For international B2B buyers, verifying a supplier’s quality control processes is essential for mitigating risks associated with product quality. Here are effective strategies:
What Audits and Reports Should Buyers Request?
- Quality Audits: Buyers should request periodic audits of the supplier’s manufacturing processes. These audits can be conducted by third-party organizations to ensure objectivity.
- Quality Reports: Suppliers should provide comprehensive reports detailing their quality control processes, including any certifications obtained.
What Role Do Third-Party Inspections Play?
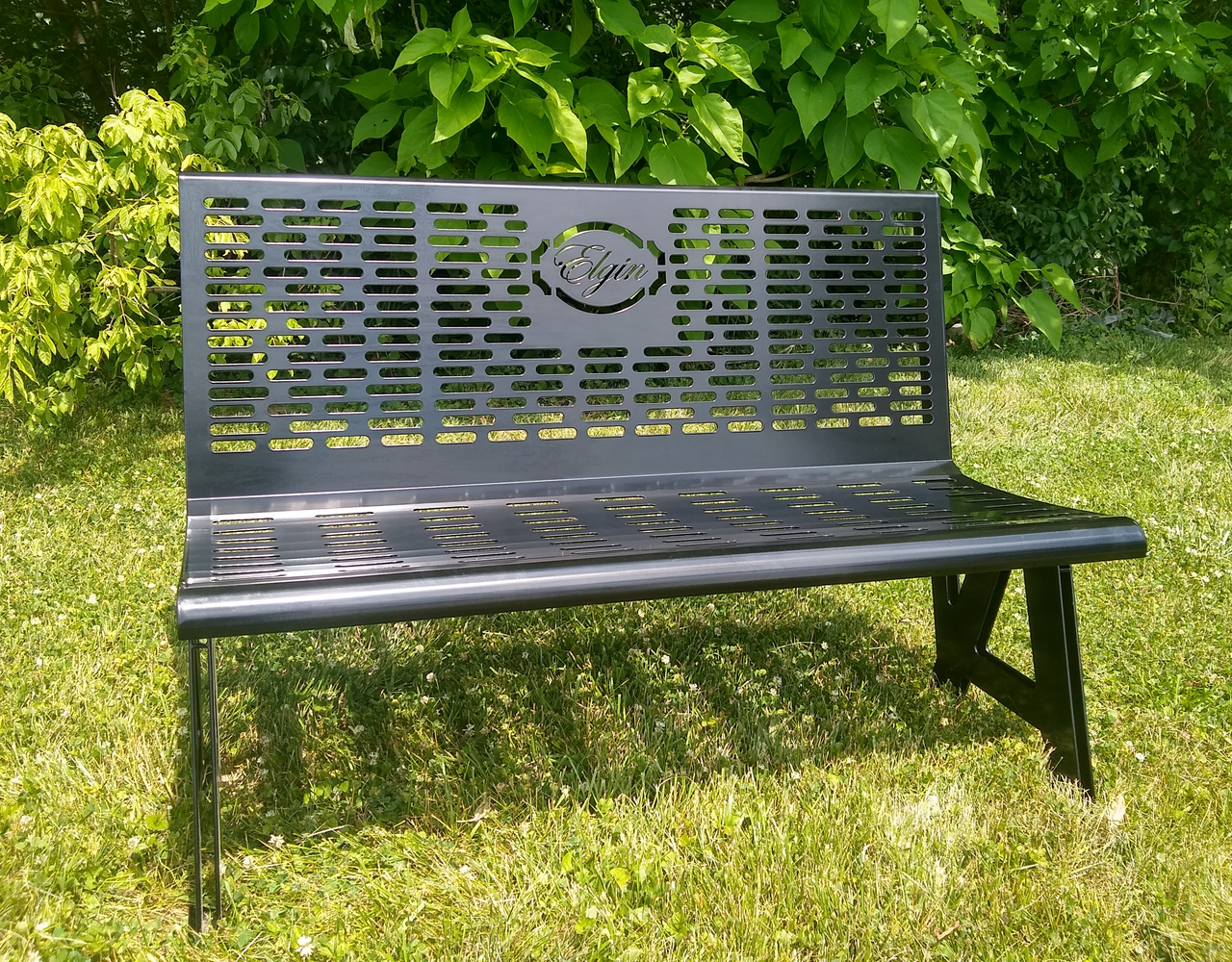
A stock image related to garden bench custom.
Engaging third-party inspection services can provide an additional layer of assurance. These services can conduct inspections at various stages of production, providing unbiased evaluations of product quality and compliance with specifications.
What Nuances Should International Buyers Consider?
When sourcing custom garden benches, international buyers, particularly from Africa, South America, the Middle East, and Europe, should be aware of certain nuances:
- Cultural Preferences: Different regions may have specific design preferences or material availability that influence sourcing decisions.
- Regulatory Compliance: Each region may have unique regulations regarding product safety and environmental impact that suppliers must comply with.
- Logistics and Supply Chain: Consideration of shipping times, costs, and customs regulations is crucial for timely delivery and cost management.
By understanding these factors, B2B buyers can make informed decisions that align with their business needs and market demands.
Conclusion
In summary, a thorough understanding of the manufacturing processes and quality assurance measures for custom garden benches is essential for international B2B buyers. By focusing on material preparation, forming, assembly, and finishing stages, as well as adhering to international standards and implementing rigorous quality control measures, buyers can ensure that they procure high-quality products that meet their specifications and expectations.
Practical Sourcing Guide: A Step-by-Step Checklist for ‘garden bench custom’
Introduction
Sourcing a custom garden bench involves careful consideration of various factors to ensure you get the best product for your needs. This guide provides a step-by-step checklist tailored for B2B buyers, particularly those in Africa, South America, the Middle East, and Europe. By following these steps, you can streamline your procurement process and make informed decisions.
1. Define Your Design Requirements
Clearly outline the design specifications for your custom garden bench. Consider factors such as dimensions, material preferences (e.g., wood, metal, or composite), and style (modern, rustic, etc.). This step is crucial because it helps you communicate your vision to potential suppliers and ensures that the final product meets your expectations.
2. Research Potential Suppliers
Conduct thorough research to identify potential suppliers who specialize in custom garden benches. Utilize online platforms, trade shows, and industry directories to compile a list. Focus on suppliers who have experience in your specific market region, as they will better understand local preferences and regulations.
3. ✅ Verify Supplier Certifications
Before engaging with suppliers, verify their certifications and compliance with industry standards. Check for ISO certifications, environmental compliance, and quality assurance practices. This verification is vital to ensure that the supplier adheres to high manufacturing standards, which directly impacts the quality of the benches you will receive.
4. Request Samples and Prototypes
Ask potential suppliers for samples or prototypes of their previous work. This step allows you to assess the quality of their craftsmanship and materials firsthand. Pay attention to details such as finish quality, durability, and comfort, as these factors will affect customer satisfaction and the longevity of the benches.
5. Evaluate Pricing and Payment Terms
Gather quotes from multiple suppliers and compare their pricing structures. Be sure to consider not only the base price but also additional costs such as shipping, taxes, and potential import duties. Understanding payment terms is equally important; look for flexible payment options that align with your cash flow needs.
6. Check Customer Reviews and References
Investigate customer reviews and request references from previous clients. This feedback can provide insights into the supplier’s reliability, customer service, and post-sale support. Positive testimonials from businesses similar to yours can give you confidence in your supplier choice.
7. Establish Clear Communication Channels
Once you’ve selected a supplier, establish clear communication channels for ongoing dialogue. Discuss timelines, updates, and any potential changes during the production process. Effective communication is key to resolving issues promptly and ensuring that the project stays on track.
By following this checklist, international B2B buyers can navigate the complexities of sourcing custom garden benches more effectively, ensuring a successful procurement process that meets their business needs.
Comprehensive Cost and Pricing Analysis for garden bench custom Sourcing
What Are the Key Cost Components in Custom Garden Bench Sourcing?
Understanding the cost structure is crucial for international B2B buyers when sourcing custom garden benches. The primary cost components include:
-
Materials: The choice of materials—such as hardwood, metal, or recycled plastic—significantly impacts the cost. High-quality materials not only enhance durability but also increase the price. Buyers should consider sourcing locally available materials to reduce costs.
-
Labor: Labor costs vary by region and can be influenced by local wage standards. In areas with a high cost of living, labor will be more expensive. Understanding the labor market in the supplier’s country can help buyers gauge potential costs.
-
Manufacturing Overhead: This includes costs associated with factory operations, utilities, and administrative expenses. Suppliers may have different overhead structures based on their operational efficiency and scale.
-
Tooling: Custom designs may require specialized tooling, which adds to the initial setup costs. Buyers should ask suppliers about any tooling fees and whether these can be amortized over larger orders to reduce per-unit costs.
-
Quality Control (QC): Ensuring product quality often incurs additional costs. Implementing strict QC measures can help prevent defects but may increase the overall price. Buyers should clarify the QC processes with suppliers to align on expectations.
-
Logistics: Shipping and handling costs can significantly affect pricing, especially for international orders. Factors such as distance, shipping method, and packaging all play a role. Buyers must consider these logistics costs when calculating total expenses.
-
Margin: Suppliers typically include a profit margin in their pricing. Understanding how much margin is standard in the industry can help buyers negotiate more effectively.
How Do Price Influencers Affect Custom Garden Bench Pricing?
Several factors influence the pricing of custom garden benches:
-
Volume/MOQ: Minimum order quantities (MOQ) can affect pricing. Larger orders often lead to lower per-unit costs due to economies of scale. Buyers should negotiate MOQs that align with their purchasing needs to optimize costs.
-
Specifications/Customization: Custom features, such as unique designs or additional functionalities, can raise costs. Buyers should prioritize essential specifications to manage their budget effectively.
-
Materials and Quality Certifications: The selection of materials and any required quality certifications (e.g., FSC certification for sustainable wood) can impact pricing. Buyers should assess the importance of these factors in relation to their market demands.
-
Supplier Factors: The reliability and reputation of the supplier can affect pricing. Established suppliers may charge more but offer better quality assurance and service. Conducting thorough supplier assessments is crucial.
-
Incoterms: Understanding Incoterms (International Commercial Terms) is vital for determining liability and cost responsibilities in shipping. Clear agreements on Incoterms can prevent unexpected expenses.
What Tips Can Help Buyers Negotiate Better Prices?
To achieve cost efficiency and better pricing in custom garden bench sourcing, consider the following tips:
-
Negotiate Firmly: Effective negotiation can lead to significant savings. Discussing bulk orders, payment terms, and delivery schedules can create leverage in pricing discussions.
-
Total Cost of Ownership (TCO): Assessing the total cost of ownership, including purchase price, maintenance, and logistics, can help buyers make informed decisions. A lower initial price may not always translate to lower overall costs.
-
Understand Pricing Nuances for International Buyers: Different regions may have varying pricing standards and expectations. Buyers from Africa, South America, the Middle East, and Europe should familiarize themselves with local market conditions to negotiate effectively.
-
Seek Multiple Quotes: Obtaining quotes from several suppliers can help buyers understand the market range and negotiate better prices.
-
Be Aware of Indicative Prices: Pricing can fluctuate based on market conditions, currency exchange rates, and material availability. Buyers should be cautious of relying solely on indicative prices and ensure they receive detailed quotes.
By understanding these cost components, price influencers, and negotiation strategies, international B2B buyers can effectively manage their sourcing of custom garden benches, ensuring they receive value while meeting their specific needs.
Alternatives Analysis: Comparing garden bench custom With Other Solutions
When considering the acquisition of garden benches, international B2B buyers should explore various solutions that meet their specific needs. Custom garden benches offer unique advantages, but it is essential to compare them against alternative solutions to ensure the best investment. This section analyzes ‘garden bench custom’ against two viable alternatives: pre-manufactured garden benches and modular seating systems.
Comparison Aspect | Garden Bench Custom | Pre-Manufactured Garden Benches | Modular Seating Systems |
---|---|---|---|
Performance | Tailored to specific requirements; high durability | Good quality, but limited customization options | Flexible configurations; can adapt to various spaces |
Cost | Higher initial cost due to customization | Lower upfront cost; fixed pricing | Moderate cost; varies with complexity |
Ease of Implementation | May require longer lead times due to production | Immediate availability; ready to install | Easy to assemble; requires some planning |
Maintenance | Custom materials may require specific care | Generally low maintenance | Varies by material; some require more upkeep |
Best Use Case | Unique designs for specific projects | Quick solutions for standard needs | Versatile solutions for dynamic environments |
What Are the Pros and Cons of Pre-Manufactured Garden Benches?
Pre-manufactured garden benches provide a cost-effective solution for businesses looking to furnish outdoor spaces without significant investment. They are readily available, allowing for immediate installation, which is ideal for projects with tight deadlines. However, the main drawback is the lack of customization. Buyers may find it challenging to match their brand aesthetics or accommodate specific spatial needs, which can limit their suitability for unique environments.
How Do Modular Seating Systems Compare?
Modular seating systems are an innovative alternative that offers flexibility and adaptability. These systems can be rearranged to suit different occasions or layouts, making them perfect for spaces that require versatility, such as parks, cafes, or event venues. The assembly is generally straightforward, which enhances their appeal for rapid deployment. However, the complexity of the design may necessitate more maintenance, particularly if the materials used are not durable. Additionally, while they provide a modern aesthetic, they may not suit all traditional landscaping designs.
Conclusion: How Can B2B Buyers Choose the Right Solution?
Selecting the appropriate garden bench solution hinges on understanding the specific requirements of your project. For businesses that prioritize uniqueness and brand identity, custom garden benches may justify the higher investment due to their tailored nature. Conversely, if immediate availability and budget constraints are primary considerations, pre-manufactured benches could be the most practical choice. Modular seating systems serve as an excellent compromise for those seeking flexibility and modern design. By carefully assessing these alternatives, B2B buyers can make informed decisions that align with their operational goals and aesthetic preferences.
Essential Technical Properties and Trade Terminology for garden bench custom
What Are the Key Technical Properties for Custom Garden Benches?
When sourcing custom garden benches, understanding the essential technical properties is crucial for ensuring product quality and durability. Here are some critical specifications that buyers should consider:
1. Material Grade
The grade of material used in manufacturing garden benches significantly affects their longevity and performance. Common materials include hardwoods (like teak and mahogany), metal (such as aluminum and steel), and synthetic materials (like recycled plastic). Each material offers unique advantages; for instance, teak is known for its weather resistance, while aluminum is lightweight and rust-resistant. Buyers must assess the material grade to ensure it meets the environmental conditions of their target market.
2. Load Capacity
This specification refers to the maximum weight a garden bench can safely support. It is vital for ensuring safety and functionality, especially in commercial settings like parks or public gardens. A typical garden bench should have a load capacity of at least 300 lbs (136 kg) to accommodate multiple users. Understanding load capacity helps buyers select benches that are suitable for their intended use.
3. Dimensions and Tolerance
Accurate dimensions are essential for ensuring that the benches fit the intended space. Tolerance refers to the acceptable range of variation in dimensions, which is critical for maintaining consistency in production. Standard bench dimensions typically include seat height, width, and depth, but custom sizes may be requested. Buyers should specify tolerance levels to avoid discrepancies that could affect assembly and usability.
4. Surface Finish
The surface finish of a garden bench impacts not only its aesthetic appeal but also its resistance to environmental factors. Finishes can range from varnishes and paints to oils and stains, each providing different levels of protection against moisture, UV rays, and wear. Buyers should inquire about the type of finish used and its maintenance requirements to ensure longevity.
5. Assembly Requirements
Understanding whether a garden bench comes pre-assembled or requires assembly is vital for logistical planning. Some manufacturers offer flat-pack options for easier shipping, while others may provide fully assembled products. Buyers should consider the assembly requirements in their purchasing decision to streamline installation and reduce labor costs.
What Are Common Trade Terms in the Custom Garden Bench Industry?
Navigating the terminology used in the custom garden bench market can be challenging for B2B buyers. Here are some essential terms to understand:
1. OEM (Original Equipment Manufacturer)
OEM refers to companies that produce parts or products that are then marketed under another company’s brand. In the context of garden benches, buyers may work with OEMs to create customized designs that align with their branding. Understanding OEM relationships can help buyers leverage quality manufacturing without the need for extensive in-house production capabilities.
2. MOQ (Minimum Order Quantity)
MOQ is the minimum number of units that a supplier requires a buyer to purchase in a single order. This term is crucial for budgeting and inventory management. Buyers from regions like Africa or South America should negotiate MOQs to ensure they align with their market demand and financial capabilities.
3. RFQ (Request for Quotation)
An RFQ is a formal process where buyers request price quotes from suppliers for specific products or services. For custom garden benches, an RFQ should detail specifications, materials, and quantities. This process helps buyers compare prices and terms from multiple suppliers, ensuring they make informed purchasing decisions.
4. Incoterms (International Commercial Terms)
Incoterms are standardized trade terms that define the responsibilities of buyers and sellers in international transactions. Understanding Incoterms such as FOB (Free on Board) or CIF (Cost, Insurance, and Freight) is crucial for managing shipping costs and responsibilities. For B2B buyers, clear communication regarding Incoterms can prevent misunderstandings and unexpected expenses during shipping.
5. Lead Time
Lead time refers to the time required from placing an order to delivery. This term is critical for planning inventory and ensuring timely availability of products. Buyers should always inquire about lead times, especially when sourcing custom garden benches, to align with project timelines and customer expectations.
By understanding these technical properties and trade terms, B2B buyers can make informed decisions, ensuring they procure high-quality garden benches that meet their business needs.
Navigating Market Dynamics and Sourcing Trends in the garden bench custom Sector
What are the Current Trends in the Global Garden Bench Custom Market?
The garden bench custom sector is witnessing significant evolution, driven by several global trends that international B2B buyers should be aware of. Increasing urbanization, particularly in Africa and South America, has led to a surge in demand for outdoor furniture that complements limited space while providing comfort. Additionally, the rise of online marketplaces facilitates easier sourcing for buyers in regions like the Middle East and Europe, enabling them to connect with manufacturers globally.
Emerging technologies such as 3D printing and computer-aided design (CAD) are revolutionizing the customization process, allowing for unique designs tailored to specific customer needs. As buyers seek personalized solutions, manufacturers are increasingly adopting these technologies to enhance their offerings. Furthermore, the integration of smart technologies into outdoor furniture, such as solar-powered charging stations or built-in speakers, is becoming a popular trend, appealing particularly to younger consumers.
Another notable dynamic is the influence of social media on consumer preferences. Platforms like Instagram and Pinterest are shaping design trends, encouraging B2B buyers to consider aesthetics that resonate with contemporary outdoor living spaces. This shift underscores the importance of staying updated on design trends and consumer preferences, particularly for buyers in Europe and affluent regions of the Middle East.
How Important is Sustainability and Ethical Sourcing in the Garden Bench Custom Sector?
Sustainability and ethical sourcing are paramount in the garden bench custom sector, reflecting a growing global consciousness regarding environmental impacts. The production of outdoor furniture often involves materials that have significant ecological footprints, such as certain woods and plastics. As a result, buyers are increasingly prioritizing suppliers who demonstrate a commitment to sustainable practices.
Using sustainably sourced materials, such as reclaimed wood or recycled plastics, not only helps reduce environmental impact but also appeals to eco-conscious consumers. Certifications such as FSC (Forest Stewardship Council) for wood products or other green certifications can enhance a supplier’s credibility and attract B2B buyers who value sustainability.
Moreover, ethical supply chains are becoming a focal point for businesses aiming to build trust with their customers. Transparency in sourcing, fair labor practices, and community engagement are critical factors that buyers from Africa, South America, the Middle East, and Europe are considering when selecting suppliers. By ensuring that their sourcing practices align with these values, B2B buyers can foster strong partnerships that contribute to long-term success and positive brand reputation.
What is the Historical Evolution of the Garden Bench Custom Sector?
The garden bench custom sector has evolved significantly over the past few decades. Initially dominated by traditional designs made from wood or metal, the market has transitioned towards more innovative and diverse offerings. The introduction of synthetic materials in the late 20th century provided durability and low maintenance, appealing to a broader consumer base.
The rise of the DIY movement in the early 2000s further transformed the market, as consumers sought customizable options that allowed them to reflect their personal style. This shift led to the emergence of numerous small-scale manufacturers and artisans who specialize in bespoke designs.
In recent years, the focus has shifted towards sustainability and technological integration, with modern buyers demanding not only aesthetic appeal but also environmentally responsible products. As the market continues to adapt to changing consumer preferences and technological advancements, B2B buyers must stay informed to make strategic sourcing decisions that align with current trends and values.
Frequently Asked Questions (FAQs) for B2B Buyers of garden bench custom
-
How do I ensure the quality of custom garden benches from international suppliers?
To ensure quality, it’s essential to conduct thorough supplier vetting. Start by requesting samples of the benches to assess their craftsmanship and materials. Additionally, check for certifications that comply with international quality standards, such as ISO or CE. Establish clear quality assurance protocols, including inspection at different stages of production and before shipping. Consider using third-party inspection services for unbiased evaluations, especially if you’re sourcing from regions like Africa or South America. -
What are the common materials used in custom garden benches, and which is the best for durability?
Common materials for custom garden benches include hardwoods (like teak and mahogany), softwoods (like pine), metal (aluminum and wrought iron), and composite materials. For durability, hardwoods are often the best choice due to their natural resistance to weather and decay. Metal benches, particularly those treated for rust resistance, can also offer long-lasting performance. When selecting materials, consider the climate of your target market in regions such as the Middle East or Europe, as this will influence the longevity of the product. -
What is the minimum order quantity (MOQ) for custom garden benches?
The MOQ can vary significantly among suppliers, typically ranging from 50 to 500 units. Factors influencing MOQ include the complexity of the design, materials used, and production capabilities of the manufacturer. It’s advisable to communicate your needs clearly during negotiations and explore options for smaller initial orders, especially if you’re testing the market in regions like South America or Africa. Building a strong relationship with suppliers can also lead to more flexible terms over time. -
How can I customize my garden benches to meet specific market needs?
Customization can include adjustments in size, design, color, and materials used. Engage with your target audience through surveys or focus groups to understand their preferences. Collaborating with a designer can help create unique features that appeal to local tastes, such as incorporating regional motifs or using locally sourced materials. Ensure that your suppliers are equipped for customization and can efficiently handle the specific requirements you set. -
What payment terms should I negotiate with international suppliers for custom garden benches?
Payment terms can greatly impact your cash flow and should be negotiated carefully. Common terms include a 30% deposit upfront with the balance due upon delivery, or a letter of credit for larger orders. Always assess the financial stability of the supplier and consider using escrow services to protect your investment. Be mindful of currency fluctuations, particularly when dealing with suppliers in Africa or South America, and consider including price adjustments in your agreement to mitigate risks. -
What logistics considerations should I keep in mind when importing custom garden benches?
Logistics involves several factors, including shipping methods, customs clearance, and delivery timelines. Choose a reliable freight forwarder with experience in your target regions to streamline the process. Understand the import regulations of your country, including tariffs and taxes applicable to garden furniture. Plan for potential delays and ensure that your suppliers can accommodate your delivery schedules, particularly during peak seasons in Europe or the Middle East. -
How do I handle disputes with suppliers in international trade?
Dispute resolution should be addressed in your contract. Consider including a mediation clause to resolve conflicts amicably before escalating to legal action. Maintain open communication throughout the process to address issues promptly. If a dispute arises, document all correspondence and agreements to support your case. Familiarize yourself with international trade laws relevant to your agreements, especially when dealing with suppliers from different cultural and legal backgrounds. -
What are the best practices for maintaining a long-term relationship with suppliers of custom garden benches?
To foster long-term relationships, prioritize clear and consistent communication with your suppliers. Regularly provide feedback on product quality and delivery performance, and be open to discussions about improvements. Consider establishing a partnership approach rather than a transactional one by engaging suppliers in your business goals and challenges. Additionally, timely payments and adherence to agreed terms will build trust and encourage suppliers to prioritize your orders.
Important Disclaimer & Terms of Use
⚠️ Important Disclaimer
The information provided in this guide, including content regarding manufacturers, technical specifications, and market analysis, is for informational and educational purposes only. It does not constitute professional procurement advice, financial advice, or legal advice.
While we have made every effort to ensure the accuracy and timeliness of the information, we are not responsible for any errors, omissions, or outdated information. Market conditions, company details, and technical standards are subject to change.
B2B buyers must conduct their own independent and thorough due diligence before making any purchasing decisions. This includes contacting suppliers directly, verifying certifications, requesting samples, and seeking professional consultation. The risk of relying on any information in this guide is borne solely by the reader.
Strategic Sourcing Conclusion and Outlook for garden bench custom
In the evolving landscape of custom garden benches, strategic sourcing stands out as a critical component for international B2B buyers. By focusing on quality, supplier reliability, and sustainable materials, businesses can enhance their competitive edge in diverse markets across Africa, South America, the Middle East, and Europe. Key takeaways include the importance of establishing strong relationships with manufacturers, leveraging technology for efficient procurement, and being mindful of regional preferences that influence design and functionality.
As buyers navigate these complexities, it is vital to conduct thorough market research to identify suppliers who align with their strategic objectives. Engaging in collaborations with local artisans can also yield unique products that resonate with customers, thereby driving brand loyalty and increasing sales.
Looking ahead, the demand for custom garden benches is likely to grow as outdoor living spaces continue to gain popularity. Therefore, now is the time for businesses to invest in strategic sourcing initiatives that will not only meet current consumer needs but also anticipate future trends. Embrace the opportunity to innovate and differentiate your offerings in this vibrant market, ensuring your place as a leader in the custom garden bench sector.