Customize Your Oil Cooler: The Ultimate Sourcing Guide (2025)
Introduction: Navigating the Global Market for oil cooler custom
Navigating the complexities of sourcing custom oil coolers can be a daunting challenge for international B2B buyers. The demand for tailored solutions that effectively manage heat in various industrial applications is increasing, yet finding the right supplier can be overwhelming. This guide aims to demystify the global market for custom oil coolers by providing a comprehensive overview of essential factors, including types, applications, supplier vetting processes, and cost considerations.
As a buyer from regions such as Africa, South America, the Middle East, or Europe (including emerging markets like Vietnam and Turkey), understanding the nuances of the oil cooler market is crucial for making informed purchasing decisions. Custom oil coolers are not just components; they play a vital role in enhancing the efficiency and longevity of machinery across industries. Therefore, this guide equips you with actionable insights that will help you identify reputable suppliers, negotiate effectively, and select solutions tailored to your specific operational needs.
By the end of this guide, you will be empowered to navigate the intricate landscape of custom oil cooler sourcing with confidence. Whether you’re looking to enhance your manufacturing processes or improve the performance of your equipment, our expert analysis will ensure that you are well-prepared to make strategic decisions that align with your business goals.
Understanding oil cooler custom Types and Variations
Type Name | Key Distinguishing Features | Primary B2B Applications | Brief Pros & Cons for Buyers |
---|---|---|---|
Air-Cooled Oil Coolers | Uses air to dissipate heat; often compact and lightweight. | Automotive, industrial machinery | Pros: Lower cost, easy installation. Cons: Less efficient in high-temperature environments. |
Liquid-Cooled Oil Coolers | Utilizes liquid (often water) for heat exchange; more efficient. | Marine engines, heavy equipment | Pros: Higher cooling efficiency, better for high-load applications. Cons: More complex installation and maintenance. |
Plate Oil Coolers | Composed of multiple plates for enhanced surface area. | Refrigeration, HVAC systems | Pros: Compact size, high thermal efficiency. Cons: Potential for clogging, requires regular cleaning. |
Shell and Tube Oil Coolers | Features a series of tubes; versatile and robust. | Oil and gas, chemical processing | Pros: Durable, suitable for high-pressure applications. Cons: Larger footprint, higher initial cost. |
Custom Fabricated Oil Coolers | Tailored designs to meet specific operational needs. | Specialized industrial applications | Pros: Optimized performance for unique requirements. Cons: Longer lead times, potentially higher costs. |
What Are the Characteristics of Air-Cooled Oil Coolers?
Air-cooled oil coolers are designed to utilize ambient air for heat dissipation, making them a popular choice in industries such as automotive and industrial machinery. Their compact and lightweight design enables easy installation in various environments, particularly where space is limited. However, buyers should consider their efficiency, as they may not perform optimally in extremely high-temperature settings. For B2B buyers, the lower cost and straightforward installation process can be significant advantages.
How Do Liquid-Cooled Oil Coolers Function?
Liquid-cooled oil coolers operate by circulating a liquid medium, often water, to absorb and transfer heat away from the oil. This type is favored in demanding applications, including marine engines and heavy equipment, where high efficiency is critical. The primary purchasing considerations include the complexity of installation and potential maintenance requirements, which may be higher than air-cooled options. Buyers should weigh the benefits of superior cooling performance against these factors.
What Are the Advantages of Plate Oil Coolers?
Plate oil coolers consist of multiple thin plates that create a large surface area for heat exchange, resulting in high thermal efficiency. They are commonly used in refrigeration and HVAC systems due to their compact size and effectiveness. However, B2B buyers should be aware of the potential for clogging, necessitating regular maintenance. The high efficiency and space-saving design make them an attractive option for companies looking to optimize performance without sacrificing space.
Why Choose Shell and Tube Oil Coolers?
Shell and tube oil coolers feature a robust design with a series of tubes encased in a shell, making them suitable for high-pressure applications found in the oil and gas or chemical processing industries. Their durability and versatility are significant selling points, although they require a larger footprint and come with a higher initial cost. B2B buyers must consider the long-term benefits of reliability and performance against the upfront investment.
When Are Custom Fabricated Oil Coolers Necessary?
Custom fabricated oil coolers are tailored to meet specific operational requirements, making them ideal for specialized industrial applications. These coolers are designed to optimize performance for unique challenges, but they often come with longer lead times and potentially higher costs. B2B buyers should evaluate their specific needs and the potential for increased efficiency against the investment and waiting period for custom solutions.
Related Video: How to Install an OIL COOLER
Key Industrial Applications of oil cooler custom
Industry/Sector | Specific Application of oil cooler custom | Value/Benefit for the Business | Key Sourcing Considerations for this Application |
---|---|---|---|
Automotive Manufacturing | Engine cooling in production vehicles | Enhanced engine performance and longevity | Material compatibility, heat exchange efficiency |
Heavy Machinery | Hydraulic systems in construction equipment | Improved operational efficiency and reduced downtime | Custom sizing, environmental durability, maintenance needs |
Oil & Gas | Cooling systems for drilling equipment | Increased reliability and safety in extreme conditions | Resistance to corrosive environments, certification standards |
Marine Industry | Cooling for propulsion and auxiliary engines | Optimal performance and fuel efficiency | Space constraints, vibration resistance, regulatory compliance |
Renewable Energy | Thermal management in wind turbines | Maximized energy output and equipment lifespan | Lightweight materials, thermal conductivity, scalability |
How is ‘oil cooler custom’ utilized in the automotive manufacturing industry?
In automotive manufacturing, oil cooler custom systems are crucial for maintaining optimal engine temperatures during production processes. These coolers help manage the heat generated by engines, ensuring they operate efficiently and prolonging their lifespan. For international buyers, particularly in regions like Africa and South America where climatic conditions can be extreme, sourcing oil coolers that can withstand high temperatures while providing effective cooling is essential. Buyers should consider factors such as material compatibility and heat exchange efficiency to ensure they meet specific vehicle requirements.
What role does ‘oil cooler custom’ play in heavy machinery applications?
In the heavy machinery sector, oil cooler custom systems are vital for hydraulic systems used in construction equipment. These coolers enhance operational efficiency by dissipating heat generated during intensive machinery use, thereby reducing the risk of component failure and downtime. For B2B buyers in the Middle East and Europe, it is important to focus on custom sizing to fit specific machinery designs and to ensure environmental durability, as these machines often operate in harsh conditions. Maintenance needs should also be evaluated to minimize operational interruptions.
How does ‘oil cooler custom’ contribute to safety in the oil and gas industry?
In the oil and gas industry, custom oil coolers are employed in drilling equipment to maintain safe operational temperatures. This is particularly important in extreme conditions where overheating can lead to equipment failures and safety hazards. International buyers, especially from Africa and South America, must consider the resistance of these coolers to corrosive environments common in oil extraction. Ensuring that these systems meet certification standards is also critical for compliance and operational safety.
Why is ‘oil cooler custom’ essential for the marine industry?
In the marine industry, custom oil coolers are used for both propulsion and auxiliary engines, playing a key role in maintaining optimal engine performance. By ensuring effective heat dissipation, these coolers contribute to improved fuel efficiency and lower emissions, which are increasingly important in regulatory environments across Europe and the Middle East. Buyers should pay attention to space constraints and vibration resistance when sourcing these systems, as marine applications often face unique challenges.
How does ‘oil cooler custom’ enhance performance in renewable energy systems?
In renewable energy, particularly within wind turbine applications, oil cooler custom systems manage thermal loads to maximize energy output and extend equipment lifespan. These coolers are designed to handle varying temperatures and maintain efficiency under different operational conditions. For buyers in regions like Africa and South America, lightweight materials and high thermal conductivity are critical factors to consider, as they can significantly impact the overall performance and scalability of renewable energy projects.
Related Video: Double Pipe Heat Exchanger Basics Explained – industrial engineering
3 Common User Pain Points for ‘oil cooler custom’ & Their Solutions
Scenario 1: Navigating Compatibility Issues with Custom Oil Coolers
The Problem: One of the significant challenges faced by B2B buyers in sectors like automotive manufacturing or heavy machinery is ensuring that a custom oil cooler is compatible with their existing systems. Buyers often find that the specifications of their current setups vary widely, making it difficult to choose a cooler that will function effectively without causing overheating or operational inefficiencies. This misalignment can lead to costly downtime and extensive modifications to existing machinery.
The Solution: To tackle compatibility issues, it’s crucial to engage with suppliers early in the design process. Buyers should provide detailed schematics of their existing systems, including dimensions, mounting points, and flow rates. This information allows manufacturers to create tailored solutions that seamlessly integrate with current equipment. Additionally, consider requesting prototypes or pilot runs to test compatibility before full-scale production. Engaging in open communication with suppliers about specific operational conditions—such as ambient temperature and fluid types—can also help ensure the custom oil cooler meets all necessary requirements.
Scenario 2: Managing High Costs of Custom Oil Coolers
The Problem: B2B buyers, particularly in regions with fluctuating currency values such as South America and the Middle East, often face budget constraints when sourcing custom oil coolers. The high costs associated with bespoke designs can strain financial resources, making it challenging to justify the investment when cheaper, off-the-shelf alternatives are available.
The Solution: To manage costs effectively, buyers should explore a few strategic approaches. First, conducting a comprehensive market analysis to compare prices from various suppliers can yield competitive quotes. Additionally, opting for a modular design can allow for future upgrades without the need for complete replacements, spreading costs over time. Collaborating with manufacturers that offer flexible payment terms or bulk purchase discounts can also alleviate financial pressure. Finally, consider assessing the total cost of ownership, including maintenance and efficiency gains, to make a more informed decision regarding the investment in a custom solution.
Scenario 3: Ensuring Timely Delivery of Custom Oil Coolers
The Problem: Delays in delivery can severely impact production schedules, particularly for B2B buyers in fast-paced industries. When sourcing custom oil coolers, buyers often find themselves at the mercy of suppliers’ timelines, which can lead to unexpected project delays and financial losses. This is especially critical in regions like Africa, where logistical challenges can exacerbate the situation.
The Solution: To mitigate delivery risks, it’s essential to establish clear timelines and expectations with suppliers at the outset of the project. Buyers should create a detailed project timeline that includes milestones for design, production, and delivery. Regular check-ins and progress updates can help identify potential delays early on. Additionally, consider working with local suppliers who can provide shorter lead times and lower shipping costs. Implementing a just-in-time inventory strategy can also help manage stock levels more efficiently, ensuring that production is not halted while waiting for essential components. Finally, building strong relationships with multiple suppliers can provide backup options in case of unforeseen delays.
Strategic Material Selection Guide for oil cooler custom
When selecting materials for custom oil coolers, understanding the properties, advantages, and limitations of each material is crucial for ensuring optimal performance and compliance with international standards. Here, we analyze four common materials used in the manufacturing of oil coolers: aluminum, stainless steel, copper, and carbon steel. Each material has unique characteristics that can significantly impact the performance and longevity of the oil cooler in various applications.
What Are the Key Properties of Aluminum for Oil Cooler Customization?
Aluminum is a lightweight and highly conductive material, making it a popular choice for oil coolers. It typically exhibits excellent thermal conductivity, allowing for efficient heat transfer, which is essential for maintaining optimal operating temperatures. Aluminum can withstand moderate pressure and has good corrosion resistance, particularly when anodized.
Pros & Cons: The primary advantage of aluminum is its lightweight nature, which reduces the overall weight of the oil cooler, making it easier to install and transport. However, aluminum can be more expensive than other materials and may require specialized manufacturing processes, such as welding or extrusion, which can increase production complexity.
Impact on Application: Aluminum is compatible with various oils and fluids, making it suitable for a wide range of applications. However, it may not be the best choice for environments with high chloride exposure, as it can corrode under such conditions.
Considerations for International Buyers: Buyers from regions like Africa and the Middle East should ensure compliance with local standards, such as ASTM or DIN, particularly regarding corrosion resistance. The availability of aluminum in local markets can also affect sourcing strategies.
How Does Stainless Steel Compare for Custom Oil Coolers?
Stainless steel is renowned for its strength and corrosion resistance, making it an excellent choice for oil coolers that operate in harsh environments. It can handle high temperatures and pressures, which is vital for heavy-duty applications.
Pros & Cons: The durability of stainless steel is a significant advantage, providing longevity and reliability. However, it is heavier and more expensive than aluminum, which could be a drawback for applications where weight is a concern. The manufacturing process can also be more complex, requiring specialized equipment for welding and forming.
Impact on Application: Stainless steel is compatible with a wide range of fluids, including aggressive oils and chemicals, making it suitable for diverse applications. Its resistance to corrosion makes it ideal for marine or coastal environments.
Considerations for International Buyers: Buyers in Europe and South America should be aware of the specific grades of stainless steel required for their applications, as compliance with standards like ASTM A240 or JIS G4304 may be necessary.
What Are the Advantages of Copper in Oil Cooler Applications?
Copper is another material commonly used in oil coolers due to its excellent thermal conductivity and resistance to corrosion. It is often used in applications where heat dissipation is critical.
Pros & Cons: The primary advantage of copper is its superior heat transfer capabilities, which can enhance the efficiency of the oil cooler. However, copper is generally more expensive than both aluminum and carbon steel, and it can be prone to corrosion if not properly coated or treated.
Impact on Application: Copper is highly compatible with various oils and fluids, although it may not be suitable for all chemical environments. Its high thermal conductivity makes it ideal for applications requiring rapid heat dissipation.
Considerations for International Buyers: Buyers should consider the availability of copper in their region, as well as compliance with international standards. In regions like Turkey, where copper is abundant, sourcing may be easier.
Why Choose Carbon Steel for Custom Oil Coolers?
Carbon steel is a cost-effective option for oil coolers, offering good strength and durability. It is often used in applications where budget constraints are a primary concern.
Pros & Cons: The main advantage of carbon steel is its lower cost compared to other materials. However, it is less resistant to corrosion and may require protective coatings to enhance its longevity. Additionally, it is heavier, which can impact installation and transport.
Impact on Application: Carbon steel is suitable for many oil types but may not be ideal for corrosive environments without proper treatment. It is often used in industrial applications where cost is a significant factor.
Considerations for International Buyers: Buyers should be aware of the need for protective coatings to prevent rust and corrosion, especially in humid climates found in parts of Africa and South America. Compliance with standards such as ASTM A36 is also essential.
Summary Table of Material Selection for Oil Cooler Customization
Material | Typical Use Case for oil cooler custom | Key Advantage | Key Disadvantage/Limitation | Relative Cost (Low/Med/High) |
---|---|---|---|---|
Aluminum | Lightweight applications | Excellent thermal conductivity | Higher cost, complex manufacturing | Medium |
Stainless Steel | Heavy-duty, corrosive environments | High strength and corrosion resistance | Heavier, more expensive | High |
Copper | High-performance cooling systems | Superior heat transfer | Prone to corrosion, higher cost | High |
Carbon Steel | Budget-sensitive industrial applications | Cost-effective | Less corrosion resistance | Low |
This detailed analysis provides international B2B buyers with critical insights into material selection for custom oil coolers, ensuring they make informed decisions that align with their operational needs and compliance requirements.
In-depth Look: Manufacturing Processes and Quality Assurance for oil cooler custom
What Are the Main Stages in the Manufacturing Process for Custom Oil Coolers?
The manufacturing process of custom oil coolers involves several critical stages that ensure the final product meets both performance and quality standards. Understanding these stages can empower B2B buyers to make informed decisions when selecting suppliers.
Material Preparation
The first stage in manufacturing custom oil coolers is material preparation. This often involves selecting high-grade materials such as aluminum or copper, which are known for their excellent thermal conductivity and corrosion resistance. Suppliers should provide material certifications to verify the quality and origin of the materials used. Buyers should request these certifications to ensure compliance with international standards.
Forming Techniques
Once the materials are prepared, the forming process begins. Techniques like extrusion, stamping, and CNC machining are commonly employed. Extrusion is particularly effective for creating complex profiles, while CNC machining offers precision and flexibility for custom designs. Buyers should inquire about the specific forming techniques used by potential suppliers, as these can significantly affect the performance and durability of the oil cooler.
Assembly Processes
After forming, the next step is assembly. This involves joining various components, such as the core, tanks, and end caps, typically using methods like brazing or welding. Proper assembly is crucial to prevent leaks and ensure optimal heat transfer. B2B buyers should assess the supplier’s assembly techniques and ask for examples of previous projects to gauge their experience and expertise.
Finishing Touches
The final stage is finishing, which may include processes like surface treatment, painting, or coating. These finishes not only enhance the aesthetic appeal of the oil coolers but also improve resistance to environmental factors. Buyers should understand the finishing options available and how they can impact the product’s longevity and performance in different climates.
How Is Quality Assurance Implemented in the Custom Oil Cooler Manufacturing Process?
Quality assurance (QA) is integral to the manufacturing of custom oil coolers. A robust QA system ensures that the products meet both customer specifications and international standards.
What International Standards Should Buyers Be Aware Of?
International standards like ISO 9001 are essential for ensuring consistent quality across manufacturing processes. ISO 9001 outlines requirements for a quality management system (QMS), focusing on customer satisfaction and continuous improvement. Additionally, industry-specific standards such as CE marking for European markets and API standards for oil and gas applications are crucial for compliance. Buyers should prioritize suppliers who are certified under these standards, as this is a strong indicator of reliability and quality.
What Are the Key Quality Control Checkpoints?
Quality control (QC) checkpoints are critical in ensuring that every stage of the manufacturing process meets the required standards. Common QC checkpoints include:
-
Incoming Quality Control (IQC): This involves inspecting raw materials and components upon arrival to ensure they meet specifications.
-
In-Process Quality Control (IPQC): During manufacturing, ongoing inspections are conducted to monitor the process and identify any issues early on.
-
Final Quality Control (FQC): After assembly, the final product undergoes comprehensive testing to verify its performance and compliance with specifications.
Buyers should request information about the specific QC processes employed by suppliers to understand how they maintain quality throughout production.
What Common Testing Methods Are Used for Quality Assurance?
To ensure that custom oil coolers function effectively, several testing methods are commonly employed:
-
Pressure Testing: This test assesses the ability of the cooler to withstand operational pressures, crucial for preventing leaks.
-
Thermal Performance Testing: This evaluates the heat exchange efficiency of the oil cooler, ensuring it meets the necessary thermal performance specifications.
-
Visual Inspection: A thorough visual examination checks for any surface defects, weld integrity, and overall craftsmanship.
Buyers should ask suppliers about their testing methodologies and request test reports to verify the performance of the products.
How Can B2B Buyers Verify Supplier Quality Control?
B2B buyers can take several steps to verify a supplier’s quality control processes:
-
Supplier Audits: Conducting on-site audits allows buyers to assess the manufacturing environment, processes, and adherence to quality standards firsthand.
-
Requesting Quality Reports: Suppliers should be able to provide detailed quality reports, including inspection results and compliance with international standards.
-
Third-Party Inspections: Engaging independent third-party inspection services can provide an unbiased assessment of the supplier’s quality control practices.
These steps can help mitigate risks and ensure that the buyer receives a product that meets their expectations.
What Are the QC Nuances for International B2B Buyers?
International B2B buyers, particularly from regions like Africa, South America, the Middle East, and Europe, should be aware of specific nuances in quality control:
-
Regulatory Compliance: Different regions have varying regulations regarding manufacturing and product safety. Buyers should familiarize themselves with local standards and ensure that suppliers comply with both international and regional requirements.
-
Cultural Differences: Understanding cultural nuances can facilitate better communication with suppliers. For instance, in some cultures, direct feedback may be less common, so buyers should approach discussions with sensitivity.
-
Logistical Considerations: Shipping and logistics can affect product quality. Buyers should discuss packaging and transport methods with suppliers to minimize potential damage during transit.
By considering these factors, international B2B buyers can make more informed decisions and foster successful partnerships with suppliers in the custom oil cooler industry.
Practical Sourcing Guide: A Step-by-Step Checklist for ‘oil cooler custom’
Introduction
Navigating the procurement of custom oil coolers can be a complex process, especially for international B2B buyers in regions like Africa, South America, the Middle East, and Europe. This step-by-step checklist is designed to streamline your sourcing process, ensuring you make informed decisions that meet your specific needs while mitigating risks associated with cross-border transactions.
Step 1: Define Your Technical Specifications
Clearly articulating your technical requirements is the foundation of sourcing a custom oil cooler. This includes understanding the cooling capacity, size, and materials needed to meet your operational demands. Be specific about the conditions in which the cooler will operate, including temperature ranges and fluid types, to ensure suppliers can provide suitable solutions.
- Cooling Capacity: Determine the heat load that needs to be dissipated.
- Material Requirements: Specify if you need corrosion-resistant materials, especially if the cooler will be used in harsh environments.
Step 2: Conduct Market Research on Suppliers
Before reaching out to potential suppliers, conduct thorough market research to identify reputable manufacturers. Look for companies with a proven track record in producing custom oil coolers and those that specialize in your industry sector. This can save time and help avoid low-quality suppliers.
- Industry Specialization: Focus on suppliers that have experience in your specific application.
- Geographical Considerations: Consider suppliers in regions with strong manufacturing capabilities, such as Turkey or Vietnam.
Step 3: Evaluate Potential Suppliers
Before committing, it’s crucial to vet suppliers thoroughly. Request company profiles, case studies, and references from buyers in a similar industry or region. Don’t just rely on their website; ask for details about their manufacturing processes and quality control measures.
- Quality Certifications: Check for ISO certifications or other industry-specific standards.
- Customer Feedback: Seek testimonials or reviews from previous clients to gauge reliability.
Step 4: Request Detailed Quotes
Once you have shortlisted suppliers, request detailed quotations that outline pricing, lead times, and payment terms. Ensure that these quotes include all relevant costs, including shipping and customs duties, to avoid unexpected expenses down the line.
- Breakdown of Costs: Ask for a detailed breakdown of material, labor, and shipping costs.
- Lead Times: Confirm production and delivery timelines to align with your project schedule.
Step 5: Assess After-Sales Support and Warranty Terms
Understanding the after-sales support and warranty terms offered by the supplier is essential. A strong warranty and responsive support can provide peace of mind and assistance in case of any issues post-purchase.
- Warranty Coverage: Clarify what the warranty includes and the duration.
- Technical Support: Inquire about the availability of technical support during installation and operation.
Step 6: Negotiate Terms and Conditions
Once you have selected a supplier, enter negotiations to finalize the terms and conditions. This includes payment terms, delivery schedules, and penalties for late delivery. Effective negotiation can lead to better pricing and terms that benefit both parties.
- Payment Flexibility: Discuss options for payment plans or discounts for early payment.
- Delivery Commitments: Ensure that delivery schedules are realistic and agreed upon in writing.
Step 7: Finalize the Purchase Agreement
After negotiations, draft a comprehensive purchase agreement that encapsulates all terms discussed. This legal document should outline all details regarding pricing, specifications, delivery, and penalties for non-compliance.
- Legal Review: Consider having a legal expert review the contract to ensure all aspects are covered.
- Sign-off Procedures: Establish a clear process for both parties to sign off on the agreement.
By following this checklist, international B2B buyers can streamline the procurement process for custom oil coolers, ensuring they find reliable suppliers that meet their technical and operational requirements.
Comprehensive Cost and Pricing Analysis for oil cooler custom Sourcing
What Are the Key Cost Components in Custom Oil Cooler Sourcing?
When sourcing custom oil coolers, understanding the cost structure is essential for international B2B buyers. The primary cost components include:
-
Materials: The choice of materials significantly impacts the overall cost. High-grade aluminum or copper alloys may increase the price but offer better thermal conductivity and durability. It’s crucial to balance cost with performance specifications.
-
Labor: Labor costs can vary significantly depending on the manufacturing location. Regions with lower labor costs, such as parts of Africa and South America, may offer competitive pricing, but this can sometimes compromise quality.
-
Manufacturing Overhead: This encompasses indirect costs associated with production, such as utilities, equipment depreciation, and facility costs. Efficient manufacturing processes can reduce these overheads, allowing suppliers to offer more competitive pricing.
-
Tooling: Custom oil coolers often require specialized tooling, which can be a significant upfront investment. Buyers should inquire about the tooling costs and whether these can be amortized over large orders.
-
Quality Control (QC): Implementing robust QC processes ensures product reliability but adds to the overall cost. Buyers should assess the QC certifications that suppliers possess, as they can impact both cost and quality.
-
Logistics: Shipping and handling costs should not be overlooked. These costs can vary based on distance, shipping method, and whether the supplier handles customs clearance.
-
Margin: Supplier margins can fluctuate based on market conditions and competitive pressures. Understanding the supplier’s pricing strategy can aid in negotiation efforts.
How Do Price Influencers Affect Custom Oil Cooler Sourcing?
Several factors influence the pricing of custom oil coolers, and being aware of these can help buyers make informed decisions:
-
Volume/MOQ (Minimum Order Quantity): Higher order volumes typically lead to lower per-unit costs. Buyers should consider negotiating for better pricing based on anticipated future demand.
-
Specifications and Customization: Custom specifications often lead to increased costs. Buyers should clearly define their requirements to avoid unnecessary expenses and ensure that the supplier can meet those specifications.
-
Material Quality and Certifications: The quality of materials used can affect pricing. Buyers should inquire about the certifications that guarantee material quality, as higher standards may result in higher costs but can lead to better long-term performance.
-
Supplier Factors: The supplier’s reputation, production capacity, and reliability can all influence pricing. Engaging with well-established suppliers may yield higher prices but often provides greater assurance of quality and service.
-
Incoterms: Understanding Incoterms (International Commercial Terms) is vital for determining who bears the shipping costs and risks. This knowledge can help buyers avoid unexpected expenses and negotiate better terms.
What Are the Best Buyer Tips for Cost-Efficiency in Custom Oil Cooler Sourcing?
To enhance cost-efficiency in sourcing custom oil coolers, buyers should consider the following strategies:
-
Effective Negotiation: Establishing strong relationships with suppliers can lead to better pricing and terms. Be prepared to negotiate on volume discounts, payment terms, and delivery schedules.
-
Total Cost of Ownership (TCO): Evaluate the TCO rather than just the initial purchase price. Consider factors such as maintenance, durability, and energy efficiency to ensure long-term value.
-
Research Local Markets: Understanding regional market dynamics in Africa, South America, the Middle East, and Europe can provide insights into pricing trends and potential cost-saving opportunities.
-
Leverage Technology: Utilize digital tools for supplier comparison and contract management. This can streamline sourcing processes and help identify the best deals.
-
Stay Informed on Global Trends: Monitor global supply chain disruptions, material costs, and trade policies that may affect pricing. Being proactive can allow buyers to make timely decisions that maximize cost savings.
Disclaimer on Indicative Prices
It is important to note that the prices discussed here are indicative and can vary based on a multitude of factors including market conditions, supplier negotiations, and specific buyer requirements. Always conduct thorough due diligence and obtain multiple quotes before finalizing any procurement decisions.
Alternatives Analysis: Comparing oil cooler custom With Other Solutions
Understanding Alternatives to Oil Cooler Custom Solutions
When considering oil cooler custom solutions, it’s essential to evaluate alternatives that may meet the same objectives. B2B buyers from regions such as Africa, South America, the Middle East, and Europe can benefit from understanding these options. This analysis focuses on two viable alternatives: Air-Cooled Oil Coolers and Heat Exchangers. Each alternative presents unique advantages and disadvantages, making it crucial to assess them based on specific operational needs.
Comparison Table of Oil Cooler Custom and Alternatives
Comparison Aspect | Oil Cooler Custom | Air-Cooled Oil Coolers | Heat Exchangers |
---|---|---|---|
Performance | High efficiency, tailored to specific applications | Moderate efficiency, dependent on ambient conditions | High efficiency, suitable for various fluids |
Cost | Higher initial investment, but potential long-term savings | Lower initial cost, but may have higher operational costs | Moderate cost, varies by design and materials |
Ease of Implementation | Requires specialized installation and expertise | Simple installation, minimal technical knowledge required | Can be complex, depending on the system design |
Maintenance | Requires regular checks and potential part replacements | Low maintenance, but cleaning is necessary | Moderate maintenance, depends on the application |
Best Use Case | Industrial applications needing specific cooling requirements | Mobile and stationary equipment in varying climates | Applications needing heat transfer between fluids |
What Are the Advantages and Disadvantages of Air-Cooled Oil Coolers?
Air-cooled oil coolers are a popular alternative for those seeking a more straightforward solution. Their primary advantage is lower initial costs and ease of installation, making them ideal for smaller operations or projects with limited budgets. However, their performance can be significantly influenced by ambient temperature and airflow, leading to inefficiencies in hot climates. Additionally, while maintenance is generally low, regular cleaning is essential to maintain optimal performance.
How Do Heat Exchangers Compare in Functionality?
Heat exchangers represent another viable option, particularly for industries where heat transfer efficiency is paramount. They excel in applications that require the exchange of heat between two or more fluids, offering high efficiency and flexibility in design. However, the initial cost can be moderate, and installation may require specialized knowledge, leading to potential project delays. Maintenance can also be a concern, as it varies based on the specific application and materials used. Despite these drawbacks, heat exchangers are highly effective in various industrial processes, making them a strong contender in many scenarios.
Conclusion: How to Choose the Right Oil Cooling Solution for Your Needs
Choosing the right oil cooling solution involves a careful analysis of your specific operational requirements, budget constraints, and environmental conditions. Oil cooler customs offer tailored performance but come with higher initial costs and complex installation. On the other hand, air-cooled oil coolers provide an affordable and easy-to-implement option, albeit with potential performance limitations in extreme temperatures. Heat exchangers, while versatile and efficient, may require a more considerable investment and expertise for installation. By weighing these factors, international B2B buyers can make informed decisions that align with their strategic objectives and operational efficiency.
Essential Technical Properties and Trade Terminology for oil cooler custom
What Are the Key Technical Properties of Custom Oil Coolers?
When sourcing custom oil coolers, understanding the essential technical properties is vital for ensuring optimal performance and compliance with industry standards. Here are some critical specifications to consider:
1. Material Grade
The material used in manufacturing oil coolers significantly affects their durability and thermal efficiency. Common materials include aluminum and stainless steel, each offering different benefits. Aluminum is lightweight and offers excellent heat transfer, making it suitable for applications where weight is a concern. Stainless steel, on the other hand, provides superior corrosion resistance, ideal for harsh environments. Buyers should assess their specific needs based on the operating environment and thermal requirements.
2. Tolerance
Tolerance refers to the allowable deviation from specified dimensions in the manufacturing process. In custom oil coolers, tight tolerances are crucial to ensure proper fit and function within the system. Inaccurate tolerances can lead to leaks, reduced efficiency, and premature failure. Buyers should specify tolerance levels in their RFQ (Request for Quotation) to avoid issues down the line.
3. Heat Transfer Capacity
This property defines the oil cooler’s ability to dissipate heat effectively. It is often expressed in BTU/hr or watts. The heat transfer capacity must match the requirements of the engine or hydraulic system it serves. Buyers need to calculate the required capacity based on the system’s operating conditions and oil flow rates to select an appropriately sized cooler.
4. Pressure Rating
The pressure rating indicates the maximum pressure the oil cooler can withstand during operation. It is essential for ensuring safety and reliability, especially in high-pressure applications. Buyers should verify that the pressure rating aligns with the specifications of the equipment it will be integrated with, as exceeding this limit can lead to catastrophic failures.
5. Surface Finish
The surface finish of an oil cooler affects both its performance and longevity. A smoother finish can enhance heat transfer efficiency, while a rougher finish may increase fouling. Buyers should consider the application environment—coolers exposed to aggressive fluids or contaminants may benefit from a more durable, textured finish to minimize wear.
Which Trade Terminology Should Buyers Understand When Sourcing Oil Coolers?
Familiarizing oneself with industry terminology can streamline the purchasing process and improve communication with suppliers. Here are some essential terms to know:
1. OEM (Original Equipment Manufacturer)
OEM refers to a company that produces components that are used in another company’s end product. In the context of oil coolers, sourcing from an OEM ensures that the product meets the exact specifications and quality standards required for integration into the final assembly. This is crucial for buyers seeking reliability and performance.
2. MOQ (Minimum Order Quantity)
MOQ is the smallest quantity of a product that a supplier is willing to sell. Understanding the MOQ is essential for buyers, as it impacts inventory levels and cash flow. For international buyers, negotiating the MOQ can lead to cost savings, but it’s important to balance this with demand forecasts to avoid excess inventory.
3. RFQ (Request for Quotation)
An RFQ is a document sent to suppliers requesting pricing and availability for a specific product. It should include detailed specifications, quantities, and desired delivery timelines. A well-prepared RFQ can facilitate better pricing and service, making it a critical tool for B2B buyers.
4. Incoterms (International Commercial Terms)
Incoterms define the responsibilities of buyers and sellers in international transactions. They clarify who is responsible for shipping, insurance, and tariffs, which can significantly affect total landed costs. Understanding Incoterms is vital for buyers to avoid unexpected costs and ensure smooth logistics.
5. Lead Time
Lead time refers to the period between placing an order and receiving the product. It is critical for planning and inventory management. Buyers should discuss lead times with suppliers to align production schedules and avoid disruptions in their operations.
By familiarizing themselves with these technical properties and trade terms, international B2B buyers can make informed decisions when sourcing custom oil coolers, ultimately leading to better performance and cost efficiency in their operations.
Navigating Market Dynamics and Sourcing Trends in the oil cooler custom Sector
What Are the Current Market Dynamics and Key Trends in the Oil Cooler Custom Sector?
The oil cooler custom market is experiencing notable growth driven by several global factors, including increasing industrialization, the rise of electric vehicles (EVs), and heightened demand for energy efficiency across various sectors. In Africa and South America, burgeoning manufacturing industries are fuelling the need for custom oil coolers to optimize equipment performance. Meanwhile, in the Middle East and Europe, stringent regulations regarding emissions and energy consumption are compelling companies to invest in advanced cooling technologies.
Emerging B2B technologies, such as IoT-enabled monitoring systems and advanced materials like composites and aluminum, are transforming the landscape. These innovations enhance the efficiency of oil coolers, allowing for real-time performance tracking and maintenance scheduling, which is particularly beneficial for international buyers seeking to optimize their supply chain operations. Additionally, the trend towards customization is growing; clients are increasingly looking for tailored solutions that meet specific operational requirements, which opens up opportunities for suppliers who can deliver bespoke products.
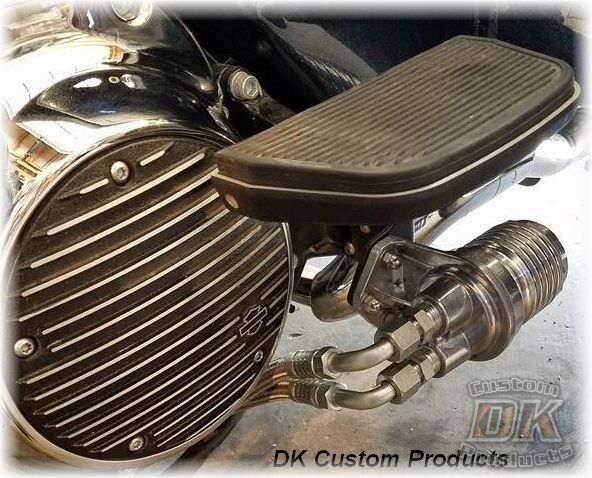
A stock image related to oil cooler custom.
International B2B buyers should also pay attention to the regional variations in demand. For instance, the Middle East’s oil and gas sector has a high demand for robust cooling solutions, while Europe is leaning towards sustainable and energy-efficient designs. Understanding these dynamics can help buyers make informed sourcing decisions, aligning their procurement strategies with market demands.
How Does Sustainability and Ethical Sourcing Impact the Oil Cooler Custom Sector?
Sustainability has become a crucial consideration in the oil cooler custom sector, with an increasing emphasis on reducing environmental impact. As industries across Africa, South America, the Middle East, and Europe strive to meet sustainability goals, the demand for eco-friendly cooling solutions is on the rise. This includes the use of recyclable materials, energy-efficient designs, and manufacturing processes that minimize waste.
Ethical sourcing is also gaining traction among international B2B buyers. Companies are now more vigilant about their supply chains, ensuring that materials are sourced responsibly and that suppliers adhere to ethical labor practices. This trend is particularly pertinent in regions with varying regulatory standards, such as Africa and South America, where buyers must navigate complex supply chains.
To align with these sustainability goals, buyers should prioritize suppliers that offer ‘green’ certifications, such as ISO 14001 for environmental management or certifications for sustainable materials. Engaging with suppliers who invest in sustainable technology not only enhances the corporate image but also can lead to cost savings through improved efficiency and reduced waste over time.
What Is the Brief Evolution of the Oil Cooler Custom Sector?
The oil cooler custom sector has evolved significantly over the past few decades. Initially, oil coolers were standard components primarily focused on functionality. However, as industries advanced and the demand for efficiency increased, the market shifted towards customization.
In the early 2000s, technological advancements began to play a pivotal role, with the introduction of more sophisticated materials and designs. The rise of digital technologies, such as CAD (Computer-Aided Design) systems, allowed for precise customization, enabling manufacturers to create oil coolers that met specific performance requirements.
Today, the sector is characterized by a blend of innovation and sustainability, where suppliers are not only focused on performance but also on environmental impact. This evolution reflects the growing need for businesses to adapt to changing market demands and regulatory landscapes, particularly for international buyers looking to enhance their operational efficiency while adhering to global sustainability standards.
Frequently Asked Questions (FAQs) for B2B Buyers of oil cooler custom
-
How do I solve issues related to oil cooler customization?
To address customization issues, begin by clearly defining your specifications and requirements. Engage with potential suppliers to discuss your needs, including dimensions, materials, and performance criteria. Request samples or prototypes to evaluate quality and fit before committing to larger orders. Establish a collaborative approach with your supplier, ensuring they understand your unique needs and can offer tailored solutions. Regular communication throughout the design process can also help mitigate misunderstandings. -
What is the best material for custom oil coolers in different climates?
The optimal material for custom oil coolers often depends on the operating environment. For hot and humid climates, such as those in Africa and South America, aluminum is preferred for its lightweight properties and resistance to corrosion. In colder regions like parts of Europe, copper-nickel alloys may be beneficial due to their durability and thermal conductivity. Always consider local environmental factors and consult with suppliers who can recommend materials that meet both performance and durability needs. -
What are the minimum order quantities (MOQ) for custom oil coolers?
Minimum order quantities can vary significantly by supplier and the complexity of the design. Generally, MOQs for custom oil coolers range from 50 to 100 units, but some manufacturers may accommodate smaller runs for prototyping or pilot projects. It’s advisable to negotiate terms with suppliers, especially if you are testing a new design or entering a new market. Understanding the supplier’s production capacity can also inform your order strategy. -
How can I ensure quality assurance (QA) for custom oil coolers?
To guarantee quality assurance, establish clear standards and specifications upfront. Request documentation of the manufacturing process, including quality control measures. Consider conducting third-party inspections or audits during production, especially for larger orders. It’s also beneficial to build a relationship with your supplier, allowing for open communication about any concerns that may arise during the manufacturing process. -
What payment terms should I negotiate with suppliers for oil coolers?
When negotiating payment terms, aim for conditions that align with your cash flow and risk tolerance. Common options include a 30% deposit upfront with the balance due upon delivery or a letter of credit that provides security for both parties. Be cautious of suppliers asking for full payment upfront, especially if you’re unfamiliar with their reputation. Always ensure that payment terms are documented in your contract to avoid disputes later.
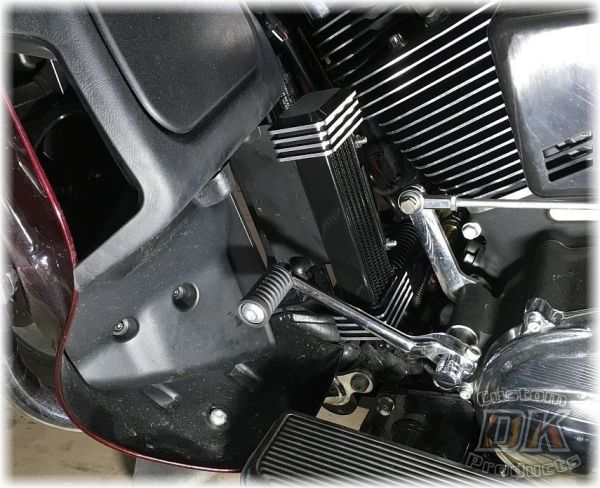
A stock image related to oil cooler custom.
-
How do I vet suppliers for custom oil coolers effectively?
Effective supplier vetting involves several steps: research their industry reputation through reviews and testimonials, verify their certifications and compliance with international standards, and assess their manufacturing capabilities. Request references from previous clients, particularly those in your industry or region. Additionally, consider visiting the facility if feasible, or utilizing virtual tours, to gain insights into their operations and quality control processes. -
What logistics considerations should I keep in mind when sourcing oil coolers internationally?
Logistics play a crucial role in international sourcing. Consider shipping methods that balance cost and delivery time, such as sea freight for bulk orders versus air freight for urgent needs. Be aware of customs regulations in your country and the supplier’s country, including tariffs and duties that may apply. Partnering with a reliable freight forwarder can help navigate these complexities, ensuring that your shipments arrive on time and in good condition. -
What are the common challenges in international trade for custom oil coolers, and how can I overcome them?
Common challenges in international trade include language barriers, cultural differences, and regulatory compliance. To overcome these issues, engage with suppliers who have experience in your target markets and can communicate effectively in your preferred language. Familiarize yourself with local regulations and standards that may affect your product. Building a strong relationship with your supplier can also facilitate smoother negotiations and foster trust, ultimately leading to better cooperation and fewer misunderstandings.
Important Disclaimer & Terms of Use
⚠️ Important Disclaimer
The information provided in this guide, including content regarding manufacturers, technical specifications, and market analysis, is for informational and educational purposes only. It does not constitute professional procurement advice, financial advice, or legal advice.
While we have made every effort to ensure the accuracy and timeliness of the information, we are not responsible for any errors, omissions, or outdated information. Market conditions, company details, and technical standards are subject to change.
B2B buyers must conduct their own independent and thorough due diligence before making any purchasing decisions. This includes contacting suppliers directly, verifying certifications, requesting samples, and seeking professional consultation. The risk of relying on any information in this guide is borne solely by the reader.
Strategic Sourcing Conclusion and Outlook for oil cooler custom
In today’s competitive landscape, strategic sourcing of custom oil coolers is essential for international B2B buyers seeking to optimize performance and reduce costs. By prioritizing partnerships with reliable manufacturers, especially in regions like Africa, South America, the Middle East, and Europe, companies can ensure high-quality products that meet specific operational needs. Key takeaways include the importance of thorough supplier evaluations, understanding local regulations, and leveraging technological advancements in production.
How can international buyers leverage strategic sourcing for better outcomes? By adopting a proactive approach to sourcing, buyers can negotiate better terms, gain access to innovative designs, and ensure timely delivery. Moreover, engaging with local suppliers can enhance supply chain resilience and foster sustainable practices.
As we look to the future, the demand for customized oil coolers will continue to grow, driven by advancements in industrial applications and environmental considerations. Now is the time for B2B buyers to take action—evaluate your sourcing strategies, establish meaningful partnerships, and stay ahead of market trends. Embrace this opportunity to enhance your operational efficiency and drive long-term success in your industry.