Customize Your Safety: The Ultimate Caution Tape Custom Guide (2025)
Introduction: Navigating the Global Market for caution tape custom
In an increasingly interconnected world, sourcing caution tape custom solutions can pose significant challenges for international B2B buyers. Whether you’re operating in the bustling markets of Africa, the dynamic economies of South America, the rapidly developing sectors in the Middle East, or the established industries of Europe, understanding the nuances of this specialized product is crucial. This comprehensive guide serves as your roadmap, covering various types of caution tape, their diverse applications across industries, and essential criteria for supplier vetting.
Our focus extends beyond mere product specifications; we delve into cost considerations, quality assurance, and the regulatory standards that vary by region. With the right insights, B2B buyers can navigate the complexities of global sourcing, ensuring that their procurement processes are efficient and aligned with their operational needs.
This guide is designed to empower international B2B buyers, including those from regions like Indonesia and Turkey, to make informed purchasing decisions. By equipping you with actionable insights and strategic approaches, we aim to enhance your understanding of the caution tape market, enabling you to select the best products that meet your safety and compliance requirements. As you explore the following sections, you will find valuable information that will streamline your sourcing process and ultimately contribute to your business’s success in a competitive global landscape.
Understanding caution tape custom Types and Variations
Type Name | Key Distinguishing Features | Primary B2B Applications | Brief Pros & Cons for Buyers |
---|---|---|---|
Standard Caution Tape | Bright yellow with black lettering; non-adhesive | Construction sites, event management | Pros: Highly visible; Cons: Limited durability in harsh conditions. |
Adhesive Caution Tape | Sticky backing; available in various colors | Hazard marking, safety signage | Pros: Strong adherence; Cons: Can leave residue; may damage surfaces upon removal. |
Reflective Caution Tape | Contains reflective materials; enhances visibility | Nighttime construction, emergency services | Pros: Increases visibility in low light; Cons: Higher cost than standard types. |
Custom Printed Caution Tape | Tailored designs and messages; various colors | Branding, marketing events | Pros: Promotes brand visibility; Cons: Higher minimum order quantities. |
Biodegradable Caution Tape | Eco-friendly materials; decomposes over time | Environmentally conscious projects | Pros: Sustainable choice; Cons: May not be as durable as traditional options. |
What Are the Characteristics of Standard Caution Tape?
Standard caution tape is typically bright yellow with bold black lettering that clearly states “Caution” or similar warnings. This type is widely used in construction sites and event management to alert individuals to potential hazards. Its non-adhesive nature makes it easy to deploy and remove without damaging surfaces. However, buyers should consider its limited durability in harsh weather conditions, which may necessitate more frequent replacements.
How Does Adhesive Caution Tape Differ from Other Types?
Adhesive caution tape features a sticky backing that allows it to adhere firmly to various surfaces. It is available in multiple colors, making it suitable for different applications, including hazard marking and safety signage. The strong adherence ensures that the tape stays in place, but buyers should be aware that it can leave residue and potentially damage surfaces when removed. This trade-off between performance and surface integrity is crucial for B2B buyers in sectors where aesthetics matter.
When Should You Use Reflective Caution Tape?
Reflective caution tape is designed to enhance visibility, especially in low-light conditions. It incorporates reflective materials that catch light, making it ideal for nighttime construction sites and emergency services. While it offers superior visibility, this type of tape comes at a higher cost than standard options. B2B buyers must weigh the benefits of increased safety against budget constraints when considering this product.
What Are the Benefits of Custom Printed Caution Tape?
Custom printed caution tape allows businesses to tailor designs and messages to their specific needs. This type of tape is particularly useful for branding and marketing events, as it can feature logos and custom warnings. While this customization promotes brand visibility, it often requires higher minimum order quantities, which can be a barrier for smaller businesses. Buyers should assess their needs for branding versus the investment required.
Why Choose Biodegradable Caution Tape?
Biodegradable caution tape is made from eco-friendly materials that decompose over time, making it an excellent choice for environmentally conscious projects. This type aligns with sustainability goals and can enhance a company’s reputation. However, buyers should note that biodegradable options may not be as durable as traditional tapes, particularly in extreme conditions. Evaluating the environmental impact versus performance is essential for B2B buyers committed to sustainability.
Related Video: Plastic Barrier Caution Tape Custom Printed For Safety Warning
Key Industrial Applications of caution tape custom
Industry/Sector | Specific Application of Caution Tape Custom | Value/Benefit for the Business | Key Sourcing Considerations for this Application |
---|---|---|---|
Construction | Safety Marking for Hazardous Areas | Reduces accidents and enhances worker safety | Compliance with local safety regulations |
Event Management | Crowd Control and Area Restriction | Improves event organization and safety | Weather resistance and visibility requirements |
Manufacturing | Equipment Maintenance and Warning Signals | Minimizes downtime and enhances operational efficiency | Durability and adhesive strength |
Utilities and Infrastructure | Temporary Barricades for Repair Zones | Protects workers and the public, ensuring safe operations | Customization for visibility and weather conditions |
Transportation and Logistics | Loading Dock Safety and Delineation | Prevents accidents and streamlines operations | Compliance with international shipping regulations |
How is Caution Tape Custom Used in Construction?
In the construction industry, caution tape custom is essential for marking hazardous areas, such as open pits or construction sites. It serves to alert workers and passersby of potential dangers, thereby reducing the likelihood of accidents. Buyers in this sector should ensure that the tape complies with local safety regulations and is made from durable materials that withstand outdoor conditions. Custom prints can also include specific warnings or branding, enhancing safety awareness while promoting the company’s identity.
What Role Does Caution Tape Custom Play in Event Management?
Event management professionals utilize caution tape custom for crowd control and area restriction during festivals, concerts, and public gatherings. By clearly delineating safe zones and restricted areas, it helps maintain order and enhances the safety of attendees. For international buyers, sourcing tape that is weather-resistant and highly visible is crucial, as events can occur in varying environmental conditions. Custom designs can also reflect the event’s branding, adding a professional touch to safety measures.
How Does Caution Tape Custom Benefit Manufacturing Operations?
In manufacturing, caution tape custom is used to signal maintenance areas and warn employees of potential hazards around machinery. This application is vital for minimizing downtime due to accidents and ensuring a safe working environment. Buyers should prioritize tapes that offer high adhesive strength and durability to withstand industrial conditions. Customization can include color coding for different hazards, which aids in quick identification and compliance with safety standards.
Why is Caution Tape Custom Important for Utilities and Infrastructure?
Utilities and infrastructure sectors frequently use caution tape custom to create temporary barricades around repair zones. This application is critical for protecting workers and the public while maintenance activities are underway. B2B buyers in this field should consider sourcing tapes that are highly visible and can withstand various weather conditions to ensure effectiveness. Custom messaging can also be included to inform the public about the nature of the work being done, enhancing transparency and safety.
How Does Caution Tape Custom Enhance Safety in Transportation and Logistics?
In the transportation and logistics sector, caution tape custom is utilized for marking loading docks and delineating safe pathways for personnel and equipment. This application is crucial for preventing accidents and ensuring smooth operations in busy environments. Buyers should ensure the tape meets international shipping regulations and is designed for high visibility. Custom options can include specific instructions or branding, which can improve operational efficiency and safety compliance across different regions.
Related Video: tesa® 4600 Self Fusing Silicone Tape for Heavy Duty Applications
3 Common User Pain Points for ‘caution tape custom’ & Their Solutions
Scenario 1: Difficulty in Sourcing High-Quality Caution Tape
The Problem:
Many B2B buyers, particularly those in construction or event management sectors across Africa, South America, the Middle East, and Europe, face challenges in sourcing high-quality custom caution tape. These buyers often encounter unreliable suppliers who deliver products that do not meet their specifications. Issues such as poor adhesive quality, fading colors, or inadequate durability can lead to safety hazards and increased costs due to frequent replacements.
The Solution:
To address these sourcing challenges, B2B buyers should conduct thorough supplier evaluations. Start by requesting samples from multiple manufacturers to assess the quality of the tape, paying close attention to the adhesive strength and material durability. Utilize platforms like Alibaba or local industry trade shows to connect with reputable suppliers who have positive customer reviews. Additionally, establish clear specifications, including material type, thickness, and intended use, in your request for quotes (RFQ). This clarity will help ensure that suppliers understand your needs and provide suitable options.
Scenario 2: Inconsistent Branding on Custom Caution Tape
The Problem:
Another common issue faced by international B2B buyers is the inconsistency in branding when ordering custom caution tape. Companies often struggle to maintain a unified brand image across their safety materials, leading to confusion in messaging and a lack of professionalism. This is particularly crucial for businesses in sectors like construction and logistics, where clear communication of safety measures is essential.
The Solution:
To overcome branding inconsistencies, B2B buyers should invest time in developing a comprehensive branding guide that includes logo placement, color codes, and font styles. When placing orders for custom caution tape, share this guide with suppliers to ensure they adhere to your branding standards. Additionally, work with suppliers who offer proofing services, allowing you to review designs before production. This step can prevent miscommunications and ensure that the final product aligns with your brand identity. Regularly review supplier performance and consider building long-term relationships with those who consistently deliver quality results.
Scenario 3: Navigating Regulatory Compliance for Caution Tape
The Problem:
B2B buyers in various regions, especially those involved in construction and public safety, often face challenges with regulatory compliance regarding the use of caution tape. Different countries have varying regulations about colors, labeling, and materials, which can create confusion and potential legal issues for companies operating internationally.
The Solution:
To navigate the complex landscape of regulatory compliance, B2B buyers should stay informed about local safety standards and regulations relevant to caution tape. This can be achieved by consulting with local safety authorities or industry associations. Create a checklist of compliance requirements for each target market and share it with potential suppliers during the sourcing process. Prioritize suppliers who have experience with international regulations and can provide documentation confirming compliance. This proactive approach not only mitigates the risk of penalties but also enhances the credibility of your brand in the eyes of clients and stakeholders. Regular training sessions for your procurement team on compliance updates can further streamline the purchasing process.
Strategic Material Selection Guide for caution tape custom
When selecting materials for custom caution tape, international B2B buyers must consider various factors that affect performance, compliance, and application suitability. Below is an analysis of four common materials used in the production of caution tape, focusing on their properties, advantages, disadvantages, and specific considerations for buyers in Africa, South America, the Middle East, and Europe.
What Are the Key Properties of Polyethylene in Caution Tape?
Polyethylene (PE) is a widely used material for caution tape due to its excellent balance of durability and flexibility. It offers good resistance to moisture and chemicals, making it suitable for various environments. PE can withstand temperatures ranging from -40°C to 80°C, ensuring performance in diverse climates.
Pros & Cons:
Polyethylene is lightweight and cost-effective, making it an attractive option for large-scale applications. However, its lower resistance to UV radiation can lead to fading over time, which may reduce visibility. Additionally, while it is durable, it may not perform well in extreme temperatures or under heavy mechanical stress.
Impact on Application:
PE is compatible with most media, including water and non-corrosive chemicals. However, it is not recommended for applications involving strong solvents or oils, which can degrade the material.
Considerations for International Buyers:
Buyers should ensure compliance with local safety standards, such as ASTM D4956 in the U.S. or EN 13422 in Europe. Awareness of regional preferences for tape thickness and color can also influence purchasing decisions.
How Does PVC Compare as a Material for Caution Tape?
Polyvinyl Chloride (PVC) is another popular choice for caution tape, known for its high durability and resistance to abrasion and chemicals. PVC can handle temperatures from -10°C to 60°C, making it suitable for moderate climates.
Pros & Cons:
The key advantage of PVC is its superior resistance to UV light and weathering, ensuring longevity even in outdoor conditions. However, it tends to be more expensive than polyethylene and can be less flexible, which may limit its application in certain scenarios.
Impact on Application:
PVC caution tape is ideal for environments that require high visibility and resistance to harsh conditions. It is compatible with various media, including oils and solvents, making it versatile for industrial applications.
Considerations for International Buyers:
When sourcing PVC caution tape, buyers should check for compliance with regulations such as REACH in Europe, which governs chemical safety. Additionally, understanding local market preferences for color coding and tape width can enhance product selection.
What Are the Benefits of Using BOPP for Caution Tape?
Biaxially Oriented Polypropylene (BOPP) is a synthetic polymer known for its excellent tensile strength and clarity. This material offers a temperature range of -20°C to 80°C, making it suitable for many environments.
Pros & Cons:
BOPP is lightweight and offers high resistance to tearing, making it ideal for high-traffic areas. However, it may not be as chemically resistant as PVC or PE, limiting its use in certain industrial applications.
Impact on Application:
BOPP caution tape is often used in construction and event management where visibility and strength are paramount. It is compatible with a range of media, although caution should be exercised in environments with strong solvents.
Considerations for International Buyers:
Buyers should ensure that BOPP tape meets local standards for visibility and safety. Additionally, understanding the preferences for tape width and print quality can help in selecting the right product.
Why Choose Cloth for Custom Caution Tape?
Cloth caution tape, often made from a blend of cotton and synthetic fibers, offers unique properties such as high durability and flexibility. It can withstand temperatures from -30°C to 70°C, making it suitable for various applications.
Pros & Cons:
The primary advantage of cloth tape is its ability to conform to uneven surfaces, enhancing adherence and visibility. However, it is generally more expensive than plastic-based tapes and may not be suitable for wet environments.
Impact on Application:
Cloth caution tape is ideal for indoor applications, especially in construction and maintenance settings. It is compatible with many media but should be kept dry to maintain its integrity.
Considerations for International Buyers:
Buyers should look for compliance with local safety standards and consider the environmental impact of cloth materials. Understanding local preferences for tape design can also influence purchasing decisions.
Summary Table of Material Selection for Caution Tape Custom
Material | Typical Use Case for caution tape custom | Key Advantage | Key Disadvantage/Limitation | Relative Cost (Low/Med/High) |
---|---|---|---|---|
Polyethylene | General-purpose warning and marking | Lightweight and cost-effective | Poor UV resistance | Low |
PVC | Outdoor safety and construction marking | High UV and weather resistance | Higher cost and less flexibility | Medium |
BOPP | Event management and construction | High tensile strength and visibility | Limited chemical resistance | Medium |
Cloth | Indoor construction and maintenance | Excellent adherence to surfaces | Higher cost and moisture sensitivity | High |
This strategic material selection guide provides actionable insights for B2B buyers seeking to make informed decisions on custom caution tape, ensuring compliance and suitability for their specific needs.
In-depth Look: Manufacturing Processes and Quality Assurance for caution tape custom
What Are the Key Stages in the Manufacturing Process of Custom Caution Tape?
The manufacturing process for custom caution tape involves several critical stages that ensure the final product meets the required specifications and quality standards. Understanding these stages can help B2B buyers make informed decisions when selecting suppliers.
Material Preparation: What Materials Are Used?
The first step in manufacturing custom caution tape is material preparation. The most common materials used include polyethylene and vinyl, chosen for their durability, flexibility, and resistance to weather elements. These materials are sourced from reputable suppliers who adhere to international quality standards. Buyers should inquire about the origin of these raw materials and their compliance with environmental regulations, especially when sourcing from regions like Africa and South America, where regulations may differ.
Forming: How Is Caution Tape Produced?
Once the materials are prepared, they undergo a forming process. This typically involves extrusion, where the raw plastic is melted and formed into thin sheets. The thickness and width of the tape can be customized based on buyer specifications. Advanced machinery, such as multi-layer extrusion systems, can produce tapes with enhanced properties, including increased tensile strength and better visibility. Buyers should ensure that the manufacturing facility has the necessary technology and expertise to deliver high-quality products.
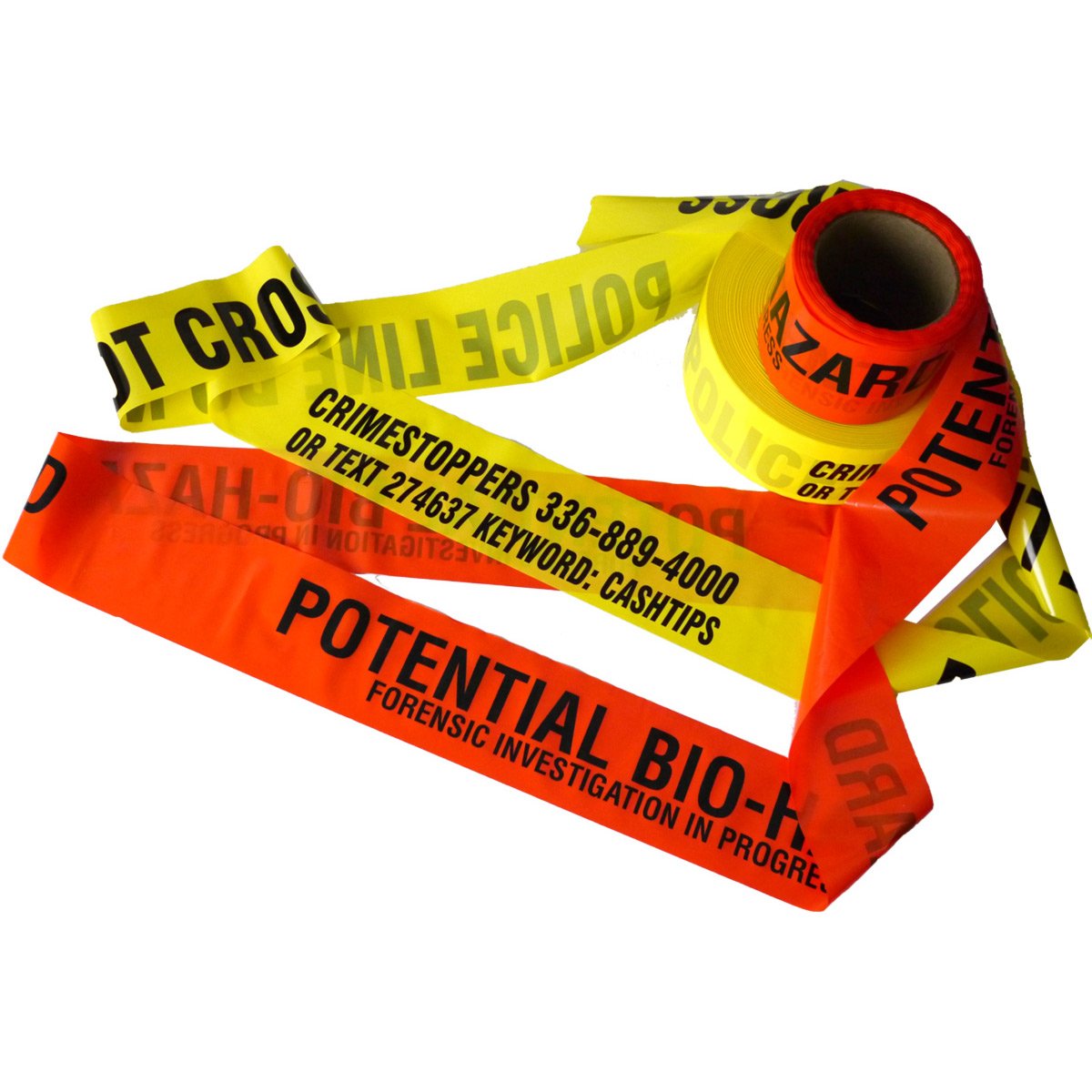
A stock image related to caution tape custom.
Assembly: What Techniques Are Used?
Following the forming stage, the assembly process includes printing and cutting the caution tape to the desired length. High-quality printing techniques, such as flexographic printing, are employed to ensure that the text and graphics are clear and durable. It’s essential for buyers to understand the printing methods used, as they directly impact the tape’s visibility and longevity. Customization options, such as adding reflective materials or specific branding elements, should also be discussed during this stage.
Finishing: How Is Quality Ensured?
The final stage is finishing, which involves quality checks and packaging. This includes winding the tape onto rolls and preparing it for shipment. A well-structured finishing process ensures that the tape is free from defects and meets the specifications outlined by the buyer. It is advisable for B2B buyers to request samples before placing large orders to assess the quality firsthand.
What Quality Assurance Measures Are in Place for Custom Caution Tape?
Quality assurance (QA) is a critical aspect of the manufacturing process for custom caution tape. Implementing robust QA measures helps maintain product consistency and reliability, which are essential for international buyers.
Which International Standards Should Buyers Be Aware Of?
For international B2B transactions, adherence to recognized quality standards is vital. One of the most relevant standards is ISO 9001, which outlines a framework for effective quality management systems. Additionally, industry-specific certifications such as CE marking for products sold in Europe and API certifications for certain applications can indicate compliance with safety and performance requirements. Buyers from Africa, South America, the Middle East, and Europe should verify that suppliers possess these certifications to ensure product reliability.
What Are the Key Quality Control Checkpoints?
Quality control (QC) checkpoints are integral to the manufacturing process and typically include:
- Incoming Quality Control (IQC): This phase involves inspecting raw materials upon arrival to ensure they meet predefined quality standards.
- In-Process Quality Control (IPQC): During production, continuous monitoring is conducted to identify and address any deviations from quality standards in real time.
- Final Quality Control (FQC): After production, a comprehensive inspection is performed on finished products to verify compliance with specifications.
B2B buyers should ask suppliers for detailed QC reports to understand how these checkpoints are managed.
What Common Testing Methods Are Used for Caution Tape?
Testing methods play a crucial role in ensuring the quality and safety of custom caution tape. Common testing methods include:
- Adhesion Testing: This assesses the tape’s ability to stick to various surfaces, which is crucial for its effectiveness in warning applications.
- Tensile Strength Testing: This evaluates how much force the tape can withstand before breaking, ensuring it can endure environmental stresses.
- UV Resistance Testing: Given the outdoor applications of caution tape, testing for UV resistance ensures that the tape does not degrade under sunlight exposure.
Buyers should request information on the testing protocols followed by suppliers to confirm product durability and safety.
How Can B2B Buyers Verify Supplier Quality Control?
For international buyers, verifying a supplier’s quality control processes is essential to mitigate risks associated with product quality. Here are some actionable steps:
Audits and Inspections: What Should Buyers Conduct?
Conducting audits of potential suppliers can provide insights into their manufacturing processes and quality control measures. Buyers should consider scheduling on-site visits or hiring third-party inspection agencies to assess the manufacturing facilities and their adherence to quality standards.
Reviewing Quality Reports: What Information Is Essential?
Requesting detailed quality control reports is another way to verify a supplier’s capabilities. These reports should include information on the QC checkpoints, testing results, and any corrective actions taken in response to quality issues. This transparency is crucial for establishing trust and ensuring product quality.
Engaging Third-Party Inspection Services: How Can They Help?
Utilizing third-party inspection services can provide an unbiased evaluation of the supplier’s quality assurance processes. These services can conduct random inspections and testing of products before shipment, giving buyers additional confidence in the quality of their orders.
What Are the Quality Control Nuances for International Buyers?
Navigating quality control nuances can be particularly challenging for international buyers from diverse regions. Here are a few considerations:
- Regulatory Differences: Buyers should be aware of the varying regulations and standards across regions. For instance, European markets may have stricter compliance requirements than those in Africa or South America.
- Cultural and Communication Barriers: Effective communication is vital in ensuring that quality expectations are clearly understood. Buyers should establish a strong line of communication with suppliers to address any concerns promptly.
- Shipping and Logistics: Quality can be compromised during shipping. Buyers should discuss packaging standards and shipping methods to minimize potential damage during transit.
By understanding these manufacturing processes and quality assurance measures, B2B buyers can make informed decisions when sourcing custom caution tape, ensuring they partner with reliable suppliers who meet international standards.
Practical Sourcing Guide: A Step-by-Step Checklist for ‘caution tape custom’
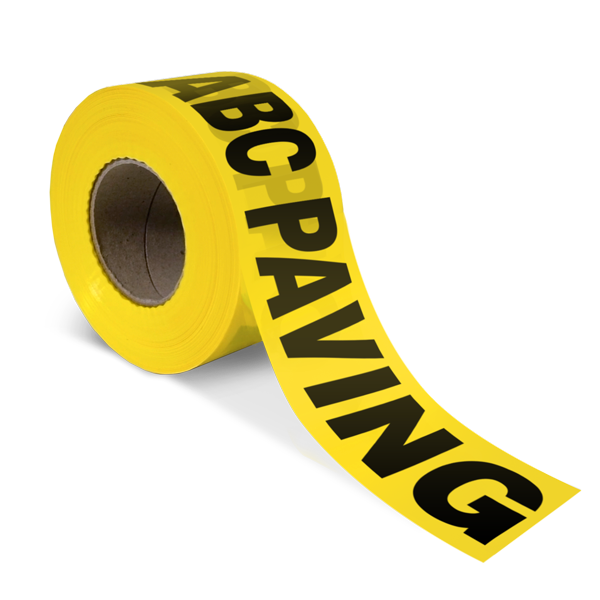
A stock image related to caution tape custom.
In the competitive landscape of B2B procurement, sourcing custom caution tape requires a systematic approach to ensure quality, compliance, and cost-effectiveness. This guide provides a step-by-step checklist to help international buyers, particularly from Africa, South America, the Middle East, and Europe, navigate the complexities of sourcing custom caution tape.
Step 1: Define Your Technical Specifications
Before engaging suppliers, clearly outline the technical specifications of the custom caution tape you require. This includes dimensions, material type (e.g., polyethylene, vinyl), adhesive strength, and printing requirements. Understanding these specifications will help you communicate effectively with potential suppliers and ensure that the product meets your specific needs.
Step 2: Research Potential Suppliers
Begin by identifying a pool of suppliers who specialize in custom caution tape. Utilize online B2B marketplaces, industry directories, and trade shows to gather a list of candidates. Focus on suppliers with experience in your target regions, as they may better understand local regulations and market demands.
Step 3: Evaluate Supplier Capabilities
Assess the capabilities of each supplier by reviewing their production processes, equipment, and technology. A supplier with advanced technology can offer higher quality and more customization options. Request detailed information about their production capacity and lead times to ensure they can meet your demands.
Step 4: Verify Supplier Certifications
It is essential to verify that potential suppliers hold relevant certifications, such as ISO 9001 for quality management and compliance with safety standards. These certifications indicate a commitment to maintaining high quality and safety in their products. Additionally, check for any region-specific certifications that may apply in your area.
Step 5: Request Samples and Test Quality
Before making a bulk order, request samples of the custom caution tape to evaluate the quality firsthand. Check for durability, print clarity, and adhesive performance. Testing samples will help you determine whether the product meets your specifications and expectations, preventing costly mistakes in your procurement process.
Step 6: Negotiate Pricing and Terms
Once you have identified a suitable supplier, engage in negotiations regarding pricing, payment terms, and delivery schedules. Be clear about your budget and expectations to foster a transparent relationship. Understanding the total cost of ownership, including shipping and potential tariffs, will help you make an informed decision.
Step 7: Establish Communication Channels
After selecting a supplier, establish clear communication channels for ongoing updates and issue resolution. Regular check-ins can help address any concerns early on and maintain a strong working relationship. Ensure that both parties are aligned on timelines and expectations to facilitate smooth transactions.
By following these steps, international B2B buyers can effectively source custom caution tape that meets their operational needs and compliance standards, leading to successful procurement outcomes.
Comprehensive Cost and Pricing Analysis for caution tape custom Sourcing
What Are the Key Cost Components in Custom Caution Tape Sourcing?
When sourcing custom caution tape, understanding the cost structure is essential for making informed purchasing decisions. The primary cost components include materials, labor, manufacturing overhead, tooling, quality control (QC), logistics, and supplier margins.
-
Materials: The type of plastic (such as polyethylene or PVC) and the thickness of the tape directly impact material costs. Custom printing and color specifications can also increase these costs.
-
Labor: Labor costs vary by region and can be influenced by local wage standards. Skilled labor is necessary for custom designs and high-quality production.
-
Manufacturing Overhead: This includes utilities, equipment maintenance, and facility costs. Regions with lower operational costs may offer more competitive pricing.
-
Tooling: Custom molds and dies are often required for unique designs, which can be a significant upfront investment.
-
Quality Control (QC): Ensuring the tape meets safety standards and specifications can add to costs but is crucial for compliance and reliability.
-
Logistics: Shipping costs can vary widely based on distance, mode of transport, and volume. International buyers should consider additional fees such as customs duties and tariffs.
-
Margin: Suppliers typically add a margin to cover their costs and ensure profitability. This can vary based on the supplier’s market position and the level of service provided.
How Do Price Influencers Affect Custom Caution Tape Costs?
Several factors can influence the pricing of custom caution tape, and understanding these can help buyers negotiate better deals.
-
Volume/MOQ: Purchasing in larger quantities can significantly reduce the per-unit cost due to economies of scale. Minimum order quantities (MOQ) set by suppliers can also affect pricing structures.
-
Specifications/Customization: More complex designs or specific requirements (such as UV resistance or specific color combinations) can lead to higher costs. Buyers should clearly define their needs upfront to avoid unexpected expenses.
-
Materials: The choice of materials not only impacts the cost but also the durability and effectiveness of the caution tape. Higher-quality materials may come at a premium but could offer better value in the long run.
-
Quality/Certifications: Tapes that meet international safety standards or have specific certifications can be more expensive. However, they may also offer better compliance and assurance of quality.
-
Supplier Factors: The reputation, reliability, and production capabilities of the supplier can influence pricing. Established suppliers might charge more due to their proven track record.
-
Incoterms: Understanding shipping terms and responsibilities can greatly affect total costs. Different Incoterms (like FOB or CIF) dictate who bears shipping costs, customs duties, and insurance.
What Are the Best Buyer Tips for Cost-Efficiency in Custom Caution Tape Sourcing?
For international B2B buyers, particularly from Africa, South America, the Middle East, and Europe, several strategies can enhance cost-efficiency when sourcing custom caution tape.
-
Negotiate: Don’t hesitate to negotiate pricing and terms. Establishing a good relationship with suppliers can lead to better deals and potential long-term partnerships.
-
Consider Total Cost of Ownership (TCO): Look beyond the purchase price. Evaluate logistics, maintenance, and disposal costs to understand the full financial impact of your purchase.
-
Research Market Trends: Stay informed about fluctuations in raw material prices and shipping costs. This knowledge can provide leverage in negotiations.
-
Leverage Local Suppliers: Whenever possible, consider sourcing from local suppliers to reduce logistics costs and lead times, which can also minimize potential delays.
-
Request Samples: Before committing to large orders, request samples to assess quality and ensure it meets your specifications. This can prevent costly mistakes.
-
Understand Pricing Nuances: Be aware of regional pricing strategies and practices. Different markets may have unique factors that influence pricing, such as import tariffs or local competition.
Disclaimer on Indicative Prices
It is important to note that pricing for custom caution tape can vary significantly based on the factors discussed above. The information provided here is indicative and may not reflect current market conditions or specific supplier quotes. Always conduct thorough market research and consult directly with suppliers for the most accurate pricing.
Alternatives Analysis: Comparing caution tape custom With Other Solutions
When evaluating safety measures for construction sites, events, or hazardous areas, B2B buyers often consider various solutions to meet their specific needs. Caution tape custom is a popular option, but it’s essential to compare it with alternative solutions to determine the most effective choice for your business operations. This section explores viable alternatives to caution tape custom, highlighting their advantages and disadvantages to assist international buyers in making informed decisions.
Comparison Table: Caution Tape Custom vs. Alternative Solutions
Comparison Aspect | Caution Tape Custom | Barrier Fencing | Safety Cones |
---|---|---|---|
Performance | High visibility; customizable for various messages | Provides physical barriers; durable against weather | Portable; clear demarcation of areas |
Cost | Moderate; varies by customization options | Higher initial investment; long-term durability | Low-cost; generally less durable |
Ease of Implementation | Quick to deploy; requires minimal setup | Requires assembly; may need more manpower | Very easy to set up; lightweight |
Maintenance | Minimal; replace as needed | Low; high durability reduces frequent replacement | Moderate; can be damaged or misplaced |
Best Use Case | Temporary warnings; event management | Long-term site protection; outdoor events | Traffic control; short-term hazard marking |
What Are the Advantages and Disadvantages of Barrier Fencing?
Barrier fencing serves as a robust alternative to caution tape custom. Its primary advantage lies in its ability to create a physical barrier that prevents access to hazardous areas, making it suitable for long-term projects. Barrier fencing is also highly durable and can withstand various weather conditions, ensuring consistent safety over time. However, the higher initial investment and the need for assembly can be significant drawbacks, especially for smaller operations or those needing a quick setup.
How Do Safety Cones Compare to Caution Tape Custom?
Safety cones are another popular alternative, particularly for short-term applications such as traffic control or temporary hazard marking. Their lightweight design allows for easy deployment and repositioning, making them ideal for events that require frequent changes. While they are low-cost and effective for immediate visual cues, safety cones may lack the visibility and custom messaging capabilities of caution tape custom. Additionally, they are more prone to damage and may require regular replacement.
Conclusion: How Can B2B Buyers Choose the Right Solution?
In summary, when selecting between caution tape custom and its alternatives, B2B buyers should consider their specific operational needs, budget constraints, and the duration of use. Caution tape custom offers high visibility and customization, making it ideal for temporary hazards, while barrier fencing provides robust protection for long-term projects. Safety cones are excellent for quick deployments but may not be suitable for all scenarios. By carefully evaluating these aspects, international buyers can make informed choices that enhance safety and efficiency in their operations.
Essential Technical Properties and Trade Terminology for caution tape custom
What Are the Key Technical Properties of Custom Caution Tape?
When sourcing custom caution tape, understanding its technical properties is essential for ensuring product performance and compliance with safety regulations. Here are critical specifications to consider:
1. Material Grade
The material grade of caution tape typically ranges from polyethylene to vinyl. Polyethylene is lightweight and cost-effective, suitable for temporary uses, while vinyl offers higher durability and resistance to weather conditions. Selecting the right material is crucial for the intended application, as it affects visibility, flexibility, and lifespan.
2. Thickness and Tolerance
Thickness is measured in mils (thousandths of an inch) and influences the tape’s strength and durability. A thicker tape (e.g., 3-5 mils) provides greater resistance to tearing and environmental factors. Tolerance indicates the acceptable variation in thickness, which is vital for quality control. Understanding these parameters helps ensure that the tape meets specific safety and operational requirements.
3. Adhesive Properties
The adhesive quality of caution tape determines how well it adheres to various surfaces. A strong, pressure-sensitive adhesive is preferred for outdoor applications to prevent peeling and ensure longevity. It is essential to evaluate the adhesive’s performance in different temperatures and conditions, especially for international buyers who may face diverse climates.
4. Visibility and Color Standards
Caution tape is often color-coded for specific warnings (e.g., yellow for caution, red for danger). Compliance with international visibility standards (such as those set by OSHA or ANSI) ensures that the tape is easily recognizable and effective in conveying warnings. This is particularly important for B2B buyers in safety-critical industries.
5. UV Resistance
For outdoor applications, UV resistance is a vital property. Caution tape exposed to sunlight can fade and lose its effectiveness over time. Selecting UV-resistant tape is essential for ensuring that warnings remain visible and effective throughout the tape’s intended lifespan.
6. Environmental Compliance
Understanding the environmental compliance of the materials used in caution tape production is increasingly important. Buyers should look for tapes that meet local and international regulations regarding hazardous materials and recyclability, which can influence purchasing decisions and brand reputation.
What Are Common Trade Terms Used in the Caution Tape Industry?
Navigating the terminology associated with custom caution tape can enhance communication and streamline the procurement process. Here are essential trade terms to know:
1. OEM (Original Equipment Manufacturer)
OEM refers to a company that produces products that can be rebranded and sold by another company. In the context of caution tape, sourcing from an OEM can provide flexibility in design and branding while ensuring high-quality production standards.
2. MOQ (Minimum Order Quantity)
MOQ is the minimum number of units a supplier is willing to sell. Understanding MOQ is crucial for budgeting and inventory management. It can vary significantly among manufacturers, so negotiating favorable terms can help optimize procurement costs.
3. RFQ (Request for Quotation)
An RFQ is a formal document sent to suppliers to request pricing and terms for specific products. For B2B buyers, issuing an RFQ for custom caution tape helps compare offers, negotiate better terms, and ensure transparency in the procurement process.
4. Incoterms (International Commercial Terms)
Incoterms are a set of predefined commercial terms published by the International Chamber of Commerce (ICC) that define the responsibilities of buyers and sellers in international transactions. Familiarity with these terms (such as FOB, CIF, or DDP) is essential for understanding shipping costs and risk management.
5. Lead Time
Lead time refers to the duration from placing an order to receiving the product. Understanding lead times is critical for project planning and ensuring that safety measures are in place when needed. It can vary based on the complexity of customization and supplier capabilities.
6. Customization Capabilities
This term refers to a manufacturer’s ability to tailor products to specific requirements, such as size, color, and printing options. Knowing the customization capabilities of potential suppliers allows buyers to align products with their unique branding and safety needs.
By understanding these technical properties and trade terms, international B2B buyers can make informed decisions when sourcing custom caution tape, ensuring compliance and effectiveness in their safety measures.
Navigating Market Dynamics and Sourcing Trends in the caution tape custom Sector
What Are the Key Market Drivers and Trends in the Caution Tape Custom Sector?
The global market for custom caution tape is experiencing significant growth, driven by rising safety regulations across various industries, including construction, manufacturing, and event management. This trend is particularly pronounced in regions such as Africa, South America, the Middle East, and Europe, where infrastructure development and urbanization are accelerating. For international B2B buyers, this means an expanding array of sourcing options, with manufacturers increasingly leveraging advanced technologies such as automation and digital printing to enhance product customization and reduce lead times.
Emerging technologies are reshaping sourcing strategies. For instance, online platforms that facilitate direct communication between manufacturers and buyers are becoming more prevalent. These platforms allow buyers to compare products, request quotes, and place orders with ease. Additionally, the integration of artificial intelligence in supply chain management is optimizing inventory levels and predicting market demand, which is crucial for maintaining competitive pricing in the custom caution tape market.
Market dynamics are also influenced by regional trade agreements and tariffs. Buyers from Africa and South America should stay informed about trade policies that could affect sourcing costs. Furthermore, the emphasis on local sourcing in various regions is pushing international suppliers to establish partnerships with local distributors, ensuring timely deliveries and compliance with regional regulations.
How Is Sustainability and Ethical Sourcing Impacting the Caution Tape Custom Sector?
Sustainability has become a cornerstone of purchasing decisions in the B2B sector, including for custom caution tape. The environmental impact of manufacturing processes, especially those involving plastic materials, is under scrutiny. As a result, many buyers are shifting towards suppliers that prioritize eco-friendly materials and production methods. This includes the use of biodegradable or recyclable materials in caution tape production, which not only meets regulatory standards but also appeals to environmentally conscious consumers.
Ethical sourcing is equally important. B2B buyers should consider the supply chain transparency of their suppliers, ensuring that labor practices meet international standards. Certifications such as ISO 14001 for environmental management and Fair Trade can serve as indicators of a supplier’s commitment to sustainability and ethical practices. By choosing suppliers with these certifications, buyers can enhance their brand reputation and meet the growing consumer demand for responsible sourcing.
Moreover, adopting sustainable practices can lead to cost savings in the long run. For instance, reducing waste through efficient manufacturing processes not only lowers material costs but can also enhance profitability. By aligning sourcing strategies with sustainability goals, international buyers can contribute to a greener economy while maintaining competitive advantage.
What Is the Historical Context of the Caution Tape Custom Sector?
The caution tape sector has evolved significantly over the past few decades. Initially, caution tape was predominantly used in construction and hazardous material management, primarily in a limited range of colors and designs. However, with the increasing focus on safety and compliance across various industries, the demand for customized solutions has surged.
In the early 2000s, advancements in printing technology allowed for more vibrant colors and intricate designs, paving the way for customized caution tape that meets specific branding and safety needs. This evolution was driven by the need for businesses to not only comply with safety regulations but also to enhance visibility and communicate messages effectively in diverse environments.
Today, the custom caution tape market is characterized by a wide variety of options, catering to diverse industries and applications. This growth trajectory presents international B2B buyers with numerous opportunities to source innovative and tailored solutions that align with their specific operational requirements.
Frequently Asked Questions (FAQs) for B2B Buyers of caution tape custom
-
How do I ensure the quality of custom caution tape from international suppliers?
To ensure quality, conduct thorough supplier vetting by checking certifications such as ISO and industry standards relevant to your region. Request samples before placing a bulk order to evaluate material durability and print quality. Additionally, establish clear specifications regarding materials, colors, and patterns in your purchase agreement. Regular communication during production can also help address any concerns early on. -
What customization options are available for caution tape?
Customization options for caution tape typically include size, color, printed messages, and logos. You can choose from various widths and lengths based on your specific needs. Many suppliers also offer different materials, such as polyethylene or PVC, which can affect durability and visibility. Discuss your requirements with potential suppliers to find the best match for your application. -
What is the minimum order quantity (MOQ) for custom caution tape?
Minimum order quantities for custom caution tape can vary widely based on the supplier and the complexity of your order. Generally, MOQs can range from a few hundred to several thousand units. Suppliers may offer lower MOQs for standard designs but require higher quantities for fully customized options. Always clarify MOQ requirements upfront to avoid misunderstandings. -
What payment terms should I expect when ordering custom caution tape?
Payment terms can vary depending on the supplier’s policies and your negotiation. Common terms include a deposit (typically 30-50%) upfront, with the balance due upon delivery or before shipping. Some suppliers may offer credit terms, especially for repeat customers. Ensure you understand the terms clearly and have them documented in your contract to avoid payment disputes. -
How can I assess the reliability of a caution tape supplier?
To assess supplier reliability, look for reviews and testimonials from other B2B buyers. Request references and reach out to past clients to gauge their experiences. Additionally, consider the supplier’s years in business, compliance with international trade regulations, and their ability to meet deadlines. A reliable supplier should also have a transparent production process and responsive customer service. -
What logistics considerations should I keep in mind when sourcing caution tape internationally?
When sourcing caution tape internationally, consider shipping methods, lead times, and customs clearance processes. Air freight may be faster but more expensive than sea freight. Factor in potential delays at customs and ensure all necessary documentation is prepared. Also, inquire about the supplier’s ability to manage logistics and whether they offer assistance with shipping arrangements. -
How do I handle disputes with international suppliers for custom caution tape?
In case of disputes, start by addressing the issue directly with the supplier through clear communication. Document all correspondence and agreements. If necessary, refer to the terms outlined in your contract, which should include a dispute resolution process. Consider mediation or arbitration if direct negotiation fails. Maintaining a professional relationship can also facilitate smoother resolutions. -
What are the environmental considerations when purchasing custom caution tape?
When purchasing custom caution tape, consider suppliers that offer eco-friendly materials and sustainable manufacturing practices. Inquire about the disposal and recyclability of the tape, as well as compliance with environmental regulations in your region. By prioritizing environmentally friendly options, you can enhance your corporate social responsibility profile and appeal to environmentally conscious clients.
Important Disclaimer & Terms of Use
⚠️ Important Disclaimer
The information provided in this guide, including content regarding manufacturers, technical specifications, and market analysis, is for informational and educational purposes only. It does not constitute professional procurement advice, financial advice, or legal advice.
While we have made every effort to ensure the accuracy and timeliness of the information, we are not responsible for any errors, omissions, or outdated information. Market conditions, company details, and technical standards are subject to change.
B2B buyers must conduct their own independent and thorough due diligence before making any purchasing decisions. This includes contacting suppliers directly, verifying certifications, requesting samples, and seeking professional consultation. The risk of relying on any information in this guide is borne solely by the reader.
Strategic Sourcing Conclusion and Outlook for caution tape custom
As international B2B buyers navigate the complexities of sourcing custom caution tape, understanding the strategic implications is paramount. The key takeaways emphasize the importance of aligning supplier capabilities with specific project needs, ensuring compliance with regional safety standards, and fostering long-term relationships with manufacturers. By leveraging global sourcing opportunities, buyers can secure competitive pricing while enhancing product quality and customization options.
How Can Strategic Sourcing Enhance Your Caution Tape Procurement?
Strategic sourcing not only optimizes procurement processes but also mitigates risks associated with supply chain disruptions. Buyers from Africa, South America, the Middle East, and Europe should prioritize suppliers who demonstrate reliability and innovation in production. This approach will not only result in cost savings but also ensure that your operational needs are met without compromising on quality.
What’s Next for International B2B Buyers in Custom Caution Tape?
Looking ahead, the demand for custom caution tape is expected to grow as industries increasingly prioritize safety and compliance. International buyers are encouraged to stay informed about emerging trends and technologies in the manufacturing sector. Engaging with suppliers who are committed to sustainable practices can also enhance your brand reputation and appeal to eco-conscious consumers.
Embrace the opportunity to redefine your sourcing strategies today. By doing so, you will not only enhance your operational efficiency but also position your business for success in a competitive global marketplace.