Cut Costs & Boost Efficiency with Metal Cutting Machine China (2025)
Introduction: Navigating the Global Market for metal cutting machine china
Navigating the global market for metal cutting machines from China presents a unique set of challenges for international B2B buyers. Whether you’re sourcing precision equipment for manufacturing in Argentina or heavy-duty machines for construction in Saudi Arabia, understanding the intricacies of this market is crucial. This comprehensive guide will explore various types of metal cutting machines, their applications across different industries, and essential considerations for supplier vetting. Additionally, we will analyze cost factors and provide insights on negotiating favorable terms with manufacturers.
By delving into the specifics of sourcing metal cutting machines from China, this guide empowers B2B buyers to make informed purchasing decisions tailored to their unique regional needs. From Africa to Europe, buyers will gain valuable knowledge about the latest technological advancements, compliance requirements, and best practices for evaluating suppliers. Understanding these elements not only helps mitigate risks but also enhances operational efficiency and competitiveness in local markets.
As we navigate through this guide, you will find actionable insights that address common pain points such as quality assurance, logistical challenges, and after-sales support. Ultimately, the goal is to equip you with the tools and knowledge necessary to confidently engage with Chinese suppliers, ensuring that your investment in metal cutting machines yields substantial returns.
Understanding metal cutting machine china Types and Variations
Type Name | Key Distinguishing Features | Primary B2B Applications | Brief Pros & Cons for Buyers |
---|---|---|---|
CNC Milling Machines | Computer-controlled for precision cutting; versatile tooling. | Aerospace, automotive, and manufacturing. | Pros: High accuracy, repeatability. Cons: Higher initial investment. |
Laser Cutting Machines | Uses high-powered laser beams for cutting; minimal thermal distortion. | Electronics, metal fabrication, and signage. | Pros: Clean cuts, intricate designs. Cons: Limited material thickness. |
Plasma Cutting Machines | Employs plasma to cut through conductive materials; fast operation. | Shipbuilding, automotive, and construction. | Pros: Speedy cutting, effective for thick metals. Cons: Rougher edges compared to laser. |
Waterjet Cutting Machines | Utilizes high-pressure water streams; suitable for various materials. | Aerospace, food processing, and art. | Pros: No heat-affected zone, versatile. Cons: Slower than laser and plasma cutting. |
Band Saw Machines | Uses a continuous band of metal teeth; ideal for large materials. | Lumber, metal fabrication, and recycling. | Pros: Cost-effective for bulk cutting. Cons: Limited to straight cuts. |
What are the Characteristics of CNC Milling Machines?
CNC (Computer Numerical Control) milling machines are known for their precision and versatility in metal cutting. These machines are programmable, allowing for complex designs and repeatable cuts. They are particularly suitable for industries requiring high accuracy, such as aerospace and automotive manufacturing. Buyers should consider factors such as the machine’s spindle speed, tooling options, and the software compatibility with their existing systems. While the initial investment can be significant, the long-term savings from reduced labor costs and increased productivity often justify the expense.
How Do Laser Cutting Machines Stand Out?
Laser cutting machines utilize focused laser beams to cut through materials with high precision and minimal thermal distortion. They are ideal for applications in electronics and metal fabrication, where intricate designs and clean edges are paramount. When purchasing, B2B buyers should assess the wattage of the laser, the thickness of materials it can handle, and the types of materials suitable for cutting. Although laser cutting provides superior quality, it may not be the best choice for thicker materials, where plasma cutting may offer better results.
What are the Advantages of Plasma Cutting Machines?
Plasma cutting machines are known for their speed and efficiency in cutting through conductive materials like steel and aluminum. They are particularly advantageous in industries such as shipbuilding and construction, where fast processing times are essential. Buyers should evaluate the machine’s cutting thickness capabilities, consumable costs, and the quality of the cut edges. While plasma cutting is faster than other methods, it may produce rougher edges, requiring additional finishing processes.
Why Choose Waterjet Cutting Machines?
Waterjet cutting machines utilize high-pressure water streams to cut through a variety of materials without generating heat, making them ideal for applications in aerospace and food processing. This technology allows for intricate designs and eliminates the risk of thermal distortion. B2B buyers should consider the waterjet’s cutting speed, the types of materials it can process, and the maintenance costs involved. While they offer versatility and precision, waterjet machines may operate slower than laser and plasma options, which could impact production timelines.
What Makes Band Saw Machines a Cost-Effective Option?
Band saw machines use a continuous band of metal teeth to cut through large materials efficiently. They are commonly used in lumber and metal fabrication industries. When considering a band saw for purchase, buyers should focus on the blade width, cutting capacity, and the type of materials they intend to cut. Although band saws are cost-effective for bulk cutting, they are limited to straight cuts, which may not suit all manufacturing needs.
Related Video: Metal laser cutting machine LS7 | BLM GROUP
Key Industrial Applications of metal cutting machine china
Industry/Sector | Specific Application of Metal Cutting Machine China | Value/Benefit for the Business | Key Sourcing Considerations for this Application |
---|---|---|---|
Automotive Manufacturing | Precision cutting of components like gears and shafts | Enhanced product quality and reduced material waste | Machine accuracy, tooling options, and after-sales support |
Aerospace Engineering | Cutting of lightweight alloys for aircraft parts | Improved efficiency and safety in flight operations | Compliance with international standards and certifications |
Construction and Fabrication | Custom metal fabrication for structural components | Faster project completion and reduced labor costs | Durability, versatility, and ease of maintenance |
Electronics and Electrical | Cutting and shaping of circuit boards and casings | Increased production speed and reduced assembly errors | Precision, compatibility with existing systems, and cost-effectiveness |
Shipbuilding | Fabrication of hulls and large metal structures | Enhanced structural integrity and longevity of vessels | Resistance to corrosion, cutting speed, and machine size |
How is Metal Cutting Machine China Used in Automotive Manufacturing?
In the automotive sector, metal cutting machines from China are primarily employed for precision cutting of components such as gears, shafts, and brackets. These machines enhance product quality by ensuring exact dimensions, thus minimizing material waste and production errors. For international B2B buyers, especially in regions like South America and Africa, sourcing machines that offer advanced features like CNC capabilities and automation can significantly improve production efficiency and reduce operational costs.
What Are the Applications in Aerospace Engineering?
Metal cutting machines are crucial in aerospace engineering for processing lightweight alloys used in aircraft parts. The machines enable the precise cutting required for components that must meet stringent safety standards while maintaining performance efficiency. Buyers from Europe and the Middle East should focus on sourcing machines that comply with international aerospace standards, ensuring reliability and safety in their applications.
How Do These Machines Benefit Construction and Fabrication?
In construction and fabrication, metal cutting machines are utilized for custom metal work, such as creating structural components for buildings and bridges. The ability to produce complex shapes quickly leads to faster project completion and lower labor costs. International buyers should consider the durability and versatility of the machines, as well as their ability to adapt to various materials and designs.
What Role Do They Play in Electronics and Electrical Applications?
Metal cutting machines are essential in the electronics sector for cutting and shaping materials used in circuit boards and casings. The speed and precision of these machines contribute to increased production rates and reduced assembly errors, enhancing overall product quality. Buyers in regions like Africa and South America should prioritize machines that offer high precision and compatibility with existing production lines to ensure seamless integration.
Why Are Metal Cutting Machines Important in Shipbuilding?
In the shipbuilding industry, metal cutting machines facilitate the fabrication of hulls and other large metal structures. These machines contribute to enhanced structural integrity and longevity of vessels, crucial for safety and performance at sea. When sourcing machines, international buyers must consider factors such as resistance to corrosion, cutting speed, and the ability to handle large materials, ensuring they meet the specific demands of the maritime industry.
Related Video: CNC Working High Speed Milling – iMachining Cutting Metal – CNC Machine Process
3 Common User Pain Points for ‘metal cutting machine china’ & Their Solutions
Scenario 1: Navigating Quality Assurance Challenges in Metal Cutting Machines from China
The Problem:
International B2B buyers often face significant challenges when sourcing metal cutting machines from China, particularly concerning quality assurance. Many buyers have reported receiving machines that do not meet the promised specifications, leading to production delays and financial losses. The lack of stringent quality control can result in defects, inconsistent performance, and a higher rate of machine failures. This is especially concerning for buyers from regions like Africa and South America, where accessing replacement parts or skilled maintenance technicians can be difficult.
The Solution:
To mitigate these quality assurance challenges, B2B buyers should implement a thorough vetting process for potential suppliers. Start by requesting certifications such as ISO 9001, which indicates adherence to quality management standards. Additionally, buyers should conduct on-site inspections or hire third-party inspection services to evaluate the machines before shipment. Establishing a clear communication channel with the manufacturer is essential—request detailed specifications, performance metrics, and test results. Also, consider negotiating a warranty that includes service agreements for maintenance and parts replacement, ensuring that you have support post-purchase.
Scenario 2: Understanding Technical Support and Training Needs for Metal Cutting Machines
The Problem:
Another common pain point for B2B buyers is the lack of technical support and training associated with metal cutting machines sourced from China. Many buyers find that the machines come with limited user manuals and insufficient training resources, which can lead to operational inefficiencies and safety risks. This issue is particularly critical for companies in the Middle East and Europe, where regulatory standards for machine operation and safety are stringent.
The Solution:
To address the training and support gap, buyers should prioritize suppliers that offer comprehensive training programs as part of the purchase agreement. Ensure that the supplier provides on-site training for operators, covering machine setup, operation, maintenance, and troubleshooting. Additionally, inquire about the availability of online resources, such as video tutorials and webinars, which can serve as ongoing references. Establish a contact point within the supplier’s organization for ongoing technical support, ensuring you can resolve issues quickly and efficiently. Buyers should also consider enrolling key staff in external courses or certifications related to metal cutting technologies to enhance their expertise.
Scenario 3: Managing Logistics and Delivery Timelines for Imported Metal Cutting Machines
The Problem:
Logistics and delivery timelines can pose significant challenges when importing metal cutting machines from China. Many international buyers experience delays due to customs clearance, shipping issues, or miscommunication with freight forwarders. These delays can disrupt production schedules and lead to increased costs, particularly for businesses in industries that rely on just-in-time manufacturing.
The Solution:
To streamline logistics and improve delivery timelines, buyers should work closely with experienced freight forwarders who specialize in machinery imports. Ensure that the freight forwarder has a proven track record of handling customs documentation effectively and can provide real-time tracking updates. Establish a clear timeline with the supplier, including production schedules, shipping dates, and expected delivery timelines. Additionally, consider exploring air freight options for urgent deliveries, despite the higher cost, to mitigate the impact of delays. Finally, maintain open lines of communication with all parties involved—suppliers, logistics providers, and customs agents—to quickly address any issues that may arise during transportation.
Strategic Material Selection Guide for metal cutting machine china
What Are the Key Materials for Metal Cutting Machines in China?
When selecting materials for metal cutting machines manufactured in China, international B2B buyers must consider several factors, including performance characteristics, cost, and compliance with regional standards. Below, we analyze four common materials used in the construction of these machines, highlighting their properties, advantages, and specific considerations for buyers from Africa, South America, the Middle East, and Europe.
Which Steel Types Are Commonly Used in Metal Cutting Machines?
Carbon Steel
Key Properties: Carbon steel is known for its excellent strength and hardness, making it suitable for high-stress applications. It typically has a temperature rating up to 400°C and exhibits good wear resistance.
Pros & Cons: The primary advantage of carbon steel is its durability and strength, which translates into longer service life for cutting tools. However, it can be prone to corrosion if not properly treated, which may require additional coatings or maintenance.
Impact on Application: Carbon steel is compatible with various cutting media, including metals and plastics, making it versatile for different manufacturing processes.
Considerations for International Buyers: Buyers should ensure compliance with ASTM standards for carbon steel grades. The cost-effectiveness of carbon steel makes it a popular choice in regions like Africa and South America, where budget constraints are often a concern.
How Does Stainless Steel Compare in Metal Cutting Applications?
Stainless Steel
Key Properties: Stainless steel is characterized by its corrosion resistance and ability to withstand high temperatures (up to 800°C). Its composition often includes chromium, which enhances its durability.
Pros & Cons: The key advantage of stainless steel is its resistance to oxidation and corrosion, making it ideal for environments with moisture or chemicals. However, it is generally more expensive than carbon steel and can be more challenging to machine due to its toughness.
Impact on Application: Stainless steel is particularly suitable for cutting applications involving corrosive materials, such as in food processing or chemical manufacturing.
Considerations for International Buyers: Buyers should verify compliance with DIN and JIS standards, especially in European and Middle Eastern markets. The higher initial cost may be justified by the longer lifespan and reduced maintenance needs.
What Role Does Tool Steel Play in Metal Cutting Machines?
Tool Steel
Key Properties: Tool steel is designed for high wear resistance and toughness, often rated for temperatures up to 600°C. It is engineered to maintain its hardness even under extreme conditions.
Pros & Cons: The primary advantage of tool steel is its ability to retain sharp cutting edges, which enhances machining efficiency. However, it can be costly and may require specialized machining processes.
Impact on Application: Tool steel is ideal for precision cutting applications, particularly in high-volume manufacturing environments.
Considerations for International Buyers: Buyers should be aware of specific tool steel grades and their corresponding standards (ASTM A681). The investment in tool steel is often justified in high-demand sectors, including automotive and aerospace.
Why Is Aluminum a Popular Choice for Metal Cutting Machines?
Aluminum
Key Properties: Aluminum is lightweight, with excellent corrosion resistance and thermal conductivity. It typically operates effectively at temperatures up to 200°C.
Pros & Cons: The main advantage of aluminum is its lightweight nature, which can reduce the overall weight of the machine, leading to easier handling and lower shipping costs. However, it is less durable than steel and may not withstand high-stress applications as effectively.
Impact on Application: Aluminum is suitable for applications requiring lightweight components, such as in the aerospace and automotive industries.
Considerations for International Buyers: Compliance with international standards like ASTM B221 is crucial. The lower cost and ease of machining make aluminum an attractive option for manufacturers in emerging markets.
Summary Table of Material Selection for Metal Cutting Machines
Material | Typical Use Case for metal cutting machine china | Key Advantage | Key Disadvantage/Limitation | Relative Cost (Low/Med/High) |
---|---|---|---|---|
Carbon Steel | General cutting applications | High strength and durability | Prone to corrosion without treatment | Low |
Stainless Steel | Corrosive environments | Excellent corrosion resistance | Higher cost and machining difficulty | High |
Tool Steel | Precision cutting in high-demand sectors | Retains sharp edges for efficient machining | Expensive and requires specialized processes | High |
Aluminum | Lightweight components in aerospace/automotive | Lightweight and cost-effective | Less durable under high stress | Med |
This strategic material selection guide provides B2B buyers with essential insights into the properties and implications of various materials used in metal cutting machines from China, enabling informed purchasing decisions tailored to their specific regional and industrial requirements.
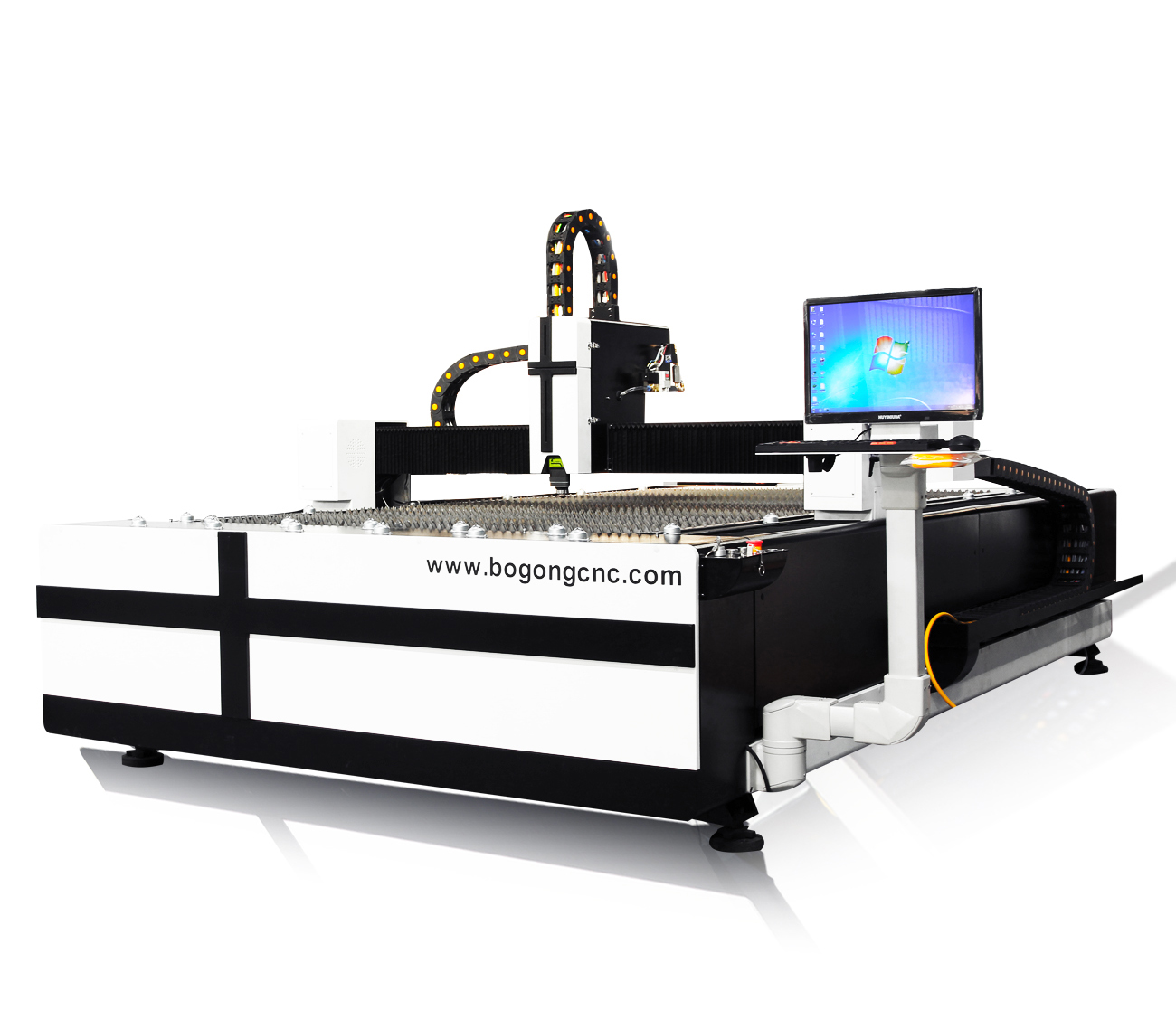
A stock image related to metal cutting machine china.
In-depth Look: Manufacturing Processes and Quality Assurance for metal cutting machine china
What Are the Main Stages in the Manufacturing Process of Metal Cutting Machines from China?
The manufacturing process of metal cutting machines involves several critical stages that ensure the final product meets industry standards and buyer specifications. Understanding these stages can help B2B buyers make informed purchasing decisions.
Material Preparation: How Is Raw Material Sourced and Processed?
The first step in manufacturing metal cutting machines is the procurement of raw materials, typically high-quality steel or aluminum alloys. Suppliers often source materials from trusted manufacturers who comply with international quality standards. Once the materials are received, they undergo rigorous inspection to ensure they meet the required specifications.
Material preparation also includes cutting, shearing, and sometimes surface treatment to enhance properties such as corrosion resistance. Buyers should inquire about the suppliers’ sourcing methods and the certifications of the raw materials to ensure they are of high quality.
Forming: What Techniques Are Used in the Production Process?
Forming is a crucial stage where the prepared materials are shaped into the components of the metal cutting machine. Common techniques include:
- CNC Machining: This computer-controlled process offers precision in shaping metal parts, ensuring that dimensions are exact.
- Laser Cutting: Utilized for its accuracy, laser cutting allows for complex shapes to be formed with minimal waste.
- Press Forming: This method uses mechanical or hydraulic presses to form metal sheets into specific shapes.
B2B buyers should assess the technologies used by suppliers, as advanced machinery often results in better quality and efficiency.
Assembly: How Are Components Brought Together?
The assembly stage involves integrating various components, such as the cutting head, frame, and control systems. This process is typically carried out in a clean, organized environment to prevent contamination and ensure precision.
Quality control checkpoints during assembly include:
- In-Process Quality Control (IPQC): Regular inspections are conducted to ensure components meet specifications as they are assembled.
- Final Assembly Checks: Once the machine is fully assembled, a thorough inspection is performed to verify that all parts function correctly.
B2B buyers should inquire about the assembly process and the qualifications of the personnel involved to ensure expertise in handling complex machinery.
Finishing: What Steps Are Taken to Enhance Durability?
The finishing stage is essential for enhancing the durability and aesthetic appeal of the metal cutting machine. This may involve:
- Surface Treatment: Techniques like anodizing, powder coating, or galvanizing are used to protect against corrosion and wear.
- Painting: A final coat of paint not only improves appearance but also adds a layer of protection.
Buyers should request details on the finishing processes used and the types of coatings applied, as these can significantly impact the longevity and performance of the machinery.
What International Quality Standards Are Relevant for Metal Cutting Machines?
Quality assurance is paramount in the manufacturing of metal cutting machines, and several international standards guide this process.
ISO 9001: What Does This Standard Entail?
ISO 9001 is a widely recognized quality management standard that outlines the requirements for a quality management system (QMS). Manufacturers certified under ISO 9001 demonstrate their ability to consistently provide products that meet customer and regulatory requirements. B2B buyers should seek suppliers with ISO 9001 certification to ensure they adhere to high-quality standards.
What Are Industry-Specific Certifications Like CE and API?
In addition to ISO 9001, certain industry-specific certifications may apply:
- CE Marking: This indicates compliance with European health, safety, and environmental protection standards, which is crucial for buyers in Europe.
- API Spec Q1: Relevant for manufacturers in the oil and gas sector, this certification ensures that products meet the stringent requirements of the American Petroleum Institute.
Understanding these certifications can help buyers gauge the reliability and safety of the machines they intend to purchase.
What Are the Key Quality Control Checkpoints in the Manufacturing Process?
Effective quality control (QC) is vital in ensuring that metal cutting machines function correctly and safely. Several QC checkpoints are typically established throughout the manufacturing process:
Incoming Quality Control (IQC): How Are Raw Materials Inspected?
IQC involves the inspection of raw materials upon arrival at the manufacturing facility. This step ensures that materials meet the required specifications before they are processed further. Buyers should ask suppliers about their IQC procedures and documentation practices.
In-Process Quality Control (IPQC): How Is Quality Monitored During Production?
IPQC involves regular monitoring of processes and products during manufacturing. This can include dimensional checks, functional tests, and adherence to specifications. Buyers can request reports on IPQC activities to gain insights into the manufacturing quality.
Final Quality Control (FQC): What Tests Are Conducted Before Shipment?
FQC is conducted after the assembly of the machine and includes comprehensive testing to ensure the equipment operates correctly. Common testing methods include:
- Functional Testing: Verifying that all machine functions work as intended.
- Performance Testing: Assessing the machine’s cutting capabilities under various conditions.
B2B buyers should insist on receiving FQC reports to confirm that the machine meets all operational standards before shipment.
How Can B2B Buyers Verify Supplier Quality Control?
Verifying a supplier’s quality control practices is crucial for B2B buyers, especially when sourcing from international markets. Here are some strategies to ensure quality:
Conducting Audits: What Should Buyers Look for?
Performing on-site audits can provide buyers with firsthand knowledge of a supplier’s manufacturing processes and quality control systems. During audits, buyers should assess:
- Compliance with international quality standards.
- The qualifications of QC personnel.
- The effectiveness of the QC checkpoints in place.
Requesting Quality Reports: What Documentation Is Important?
Buyers should request detailed quality reports, including IQC, IPQC, and FQC documentation. These reports should outline the testing methods used, results obtained, and any corrective actions taken.
Utilizing Third-Party Inspection Services: How Can Buyers Ensure Objectivity?
Engaging third-party inspection services can provide an unbiased evaluation of the manufacturing process and the quality of the final product. These services can conduct audits, perform testing, and offer certifications, giving buyers additional confidence in their purchasing decisions.
What Are the Nuances of Quality Control for International B2B Buyers?
International B2B buyers, particularly from regions like Africa, South America, the Middle East, and Europe, should be aware of several nuances in quality control:
- Cultural Differences: Understanding local manufacturing practices and standards can aid in effective communication with suppliers.
- Regulatory Compliance: Different regions may have specific regulations that affect product compliance, so buyers should be familiar with these requirements.
- Supply Chain Considerations: Buyers should consider the entire supply chain, from raw material sourcing to final product delivery, to ensure consistent quality.
By being informed about these aspects, international B2B buyers can navigate the complexities of sourcing metal cutting machines from China more effectively.
Practical Sourcing Guide: A Step-by-Step Checklist for ‘metal cutting machine china’
To successfully procure a metal cutting machine from China, international B2B buyers must navigate a series of critical steps to ensure they select the right equipment and supplier. This practical sourcing guide provides a comprehensive checklist that will help streamline your procurement process while minimizing risks.
Step 1: Define Your Technical Specifications
Before initiating the sourcing process, clearly outline the technical specifications required for your metal cutting machine. Consider factors such as the types of metals you will be cutting, thickness, and desired precision. This clarity will enable you to filter suppliers effectively and ensure the machine meets your operational needs.
- Key considerations:
- Material types (e.g., steel, aluminum).
- Cutting speed and accuracy requirements.
Step 2: Conduct Market Research on Suppliers
Take the time to research potential suppliers in China specializing in metal cutting machines. Utilize online platforms, industry trade shows, and local business directories to create a list of candidates. This step is essential to identify suppliers with a proven track record and relevant experience in your industry.
- Research tips:
- Look for reviews and ratings on platforms like Alibaba or Made-in-China.
- Check for participation in international trade shows or exhibitions.
Step 3: Evaluate Potential Suppliers
Before committing, it’s crucial to vet suppliers thoroughly. Request company profiles, case studies, and references from buyers in a similar industry or region. This will help you gauge their reliability and the quality of their machines.
- What to ask for:
- Certifications such as ISO 9001 or CE for quality assurance.
- Customer testimonials or case studies demonstrating their capabilities.
Step 4: Request Quotes and Compare Pricing
Once you have shortlisted potential suppliers, request detailed quotes that include pricing, shipping costs, and payment terms. This is a vital step for understanding the financial implications of your purchase and ensuring you stay within budget.
- Comparison criteria:
- Total cost of ownership including installation and maintenance.
- Payment terms and conditions, ensuring they are favorable for your cash flow.
Step 5: Verify Supplier Certifications
Ensure that your chosen supplier complies with international standards and regulations relevant to metal cutting machines. Certification verification is crucial for ensuring product quality and safety.
- Key certifications to check:
- ISO certifications for quality management.
- Compliance with local regulations in your country.
Step 6: Negotiate Terms and Conditions
Engage in negotiations to finalize the terms of your purchase. This includes discussing warranty, after-sales support, and delivery schedules. Clear agreements on these points can prevent misunderstandings and potential disputes later on.
- Negotiation tips:
- Be clear about your expectations regarding after-sales service.
- Ensure delivery timelines are documented and agreed upon.
Step 7: Arrange for Quality Inspection Before Shipment
Before finalizing the transaction, arrange for a quality inspection of the metal cutting machine at the supplier’s facility. This step is crucial to ensure that the machine meets your specifications and quality standards before it is shipped.
- Inspection aspects:
- Confirm operational functionality.
- Ensure compliance with agreed-upon specifications.
By following this step-by-step checklist, B2B buyers can confidently navigate the complexities of sourcing a metal cutting machine from China, ensuring they make informed decisions that align with their business needs.
Comprehensive Cost and Pricing Analysis for metal cutting machine china Sourcing
What Are the Key Cost Components for Sourcing Metal Cutting Machines from China?
When sourcing metal cutting machines from China, understanding the cost structure is vital for international B2B buyers. The primary cost components include:
-
Materials: The quality and type of materials used directly influence the machine’s durability and performance. Steel and aluminum are common materials, but variations in alloys can affect prices significantly.
-
Labor: Labor costs in China are generally lower than in Europe or North America. However, skilled labor for assembly and quality control can command higher wages, impacting the overall cost.
-
Manufacturing Overhead: This includes utility costs, factory maintenance, and administrative expenses. Suppliers with efficient manufacturing processes may offer lower overhead costs, which can be a negotiation point.
-
Tooling: The initial setup for production, including dies and molds, is essential. Custom tooling for specific machine designs may lead to higher initial costs but can save money in mass production.
-
Quality Control (QC): Rigorous QC processes ensure that machines meet international standards. Investing in quality checks can increase upfront costs but often leads to long-term savings by reducing defects and returns.
-
Logistics: Shipping costs, including freight, insurance, and customs duties, can significantly impact the total cost. Incoterms (International Commercial Terms) will dictate who is responsible for these expenses.
-
Margin: Suppliers will typically add a profit margin to cover their expenses and risks, which can vary based on competition and demand.
How Do Price Influencers Affect the Cost of Metal Cutting Machines?
Several factors influence the pricing of metal cutting machines, particularly for international buyers:
-
Volume and Minimum Order Quantity (MOQ): Larger orders usually qualify for bulk pricing, reducing per-unit costs. Understanding the supplier’s MOQ policy is crucial for cost management.
-
Specifications and Customization: Customized machines tailored to specific needs will be more expensive than standard models. Buyers should clearly define their requirements to avoid unnecessary costs.
-
Materials Used: Higher-grade materials lead to higher costs but may offer better performance and longevity. Buyers must weigh the initial investment against potential savings from reduced maintenance and downtime.
-
Quality Certifications: Machines that meet international quality standards (e.g., ISO, CE) may command higher prices. Such certifications can enhance resale value and ensure compliance in various markets.
-
Supplier Factors: Established suppliers with a strong reputation might charge more due to perceived reliability. Newer suppliers may offer lower prices to build their client base, but this could come with risks regarding quality and support.
-
Incoterms: The choice of Incoterms affects who bears the costs and risks associated with shipping. Understanding these terms can help buyers negotiate better deals and manage costs effectively.
What Are Effective Buyer Tips for Negotiating Costs?
To maximize value when sourcing metal cutting machines from China, consider the following strategies:
-
Negotiate with Multiple Suppliers: Request quotes from several suppliers to gauge the market rate. This competitive approach can lead to better pricing and terms.
-
Focus on Total Cost of Ownership (TCO): Rather than just the purchase price, consider the TCO, which includes operational costs, maintenance, and potential downtime. This holistic view can guide purchasing decisions.
-
Understand Pricing Nuances: International buyers should be aware of currency fluctuations, tariffs, and trade agreements that may influence final costs. Being informed allows for better budget management.
-
Build Long-Term Relationships: Establishing a good rapport with suppliers can lead to better terms, discounts on future purchases, and priority support.
-
Request Detailed Quotations: Ensure that suppliers provide comprehensive quotes that break down costs. This transparency allows for easier comparison and negotiation.
Disclaimer on Indicative Prices
Prices for metal cutting machines can vary significantly based on the aforementioned factors. It’s advisable for buyers to conduct thorough market research and consult with suppliers directly to obtain accurate pricing tailored to their specific requirements.
Alternatives Analysis: Comparing metal cutting machine china With Other Solutions
When considering metal cutting solutions, it is essential for international B2B buyers to evaluate not only the offerings from China but also viable alternatives that may better suit their specific operational needs. This analysis aims to provide a comparative overview of ‘Metal Cutting Machine China’ against other cutting technologies to inform purchasing decisions.
Comparison Aspect | Metal Cutting Machine China | CNC Laser Cutting Machine | Plasma Cutting Machine |
---|---|---|---|
Performance | High precision and speed | Extremely precise with fine cuts | Good for thick materials but less precise |
Cost | Competitive pricing | Higher initial investment but lower operating costs | Lower initial cost but higher consumable costs |
Ease of Implementation | Requires skilled labor for setup and operation | Moderate; requires programming knowledge | Generally easier to set up and operate |
Maintenance | Regular maintenance needed; parts readily available | Low maintenance due to fewer moving parts | High maintenance due to wear on consumables |
Best Use Case | Ideal for intricate designs and high-volume production | Best for thin materials and complex shapes | Suitable for thick metals and quick cuts |
What Are the Advantages of CNC Laser Cutting Machines?
CNC laser cutting machines offer high precision and versatility, making them ideal for applications requiring intricate designs. They use a focused laser beam to cut through various materials, providing a clean and accurate finish. While the initial investment may be higher than that of a metal cutting machine from China, the long-term operational costs can be lower due to reduced material waste and energy efficiency. However, CNC laser cutting requires skilled operators who can manage the programming and operation, which may pose a challenge for some businesses.
What Benefits Do Plasma Cutting Machines Provide?
Plasma cutting machines are known for their speed and efficiency when cutting through thick metals, making them a popular choice in industries such as automotive and construction. They have a lower initial purchase price compared to laser cutting machines, which can be appealing for smaller companies or startups. However, plasma cutting is less precise than laser or traditional metal cutting methods, making it less suitable for applications that require tight tolerances. Additionally, the consumables used in plasma cutting can incur higher ongoing costs, affecting long-term profitability.
Conclusion: How to Choose the Right Metal Cutting Solution?
When selecting the right metal cutting solution, international B2B buyers must consider multiple factors, including performance requirements, budget constraints, ease of implementation, and maintenance needs. A metal cutting machine from China might be ideal for high-volume production with intricate designs, while CNC laser cutting machines may serve better in precision applications. Plasma cutting machines can be a cost-effective solution for thicker materials but may lack the precision required for more detailed work. By aligning the specific needs of their operations with the strengths of each technology, buyers can make informed decisions that enhance productivity and profitability in their manufacturing processes.
Essential Technical Properties and Trade Terminology for metal cutting machine china
What Are the Essential Technical Properties of Metal Cutting Machines?
When considering metal cutting machines from China, it’s crucial to understand specific technical properties that affect performance and suitability for various applications. Here are several key specifications that B2B buyers should prioritize:
-
Material Grade
– The material used in the construction of the machine significantly impacts its durability and performance. Common materials include high-carbon steel, alloy steel, and cast iron. For example, machines made from high-carbon steel are typically more robust and suitable for heavy-duty applications, while alloy steel offers enhanced wear resistance. Understanding material grades helps buyers select machines that meet their operational demands. -
Cutting Tolerance
– Cutting tolerance refers to the permissible limit of variation in a machined part. In metal cutting, tighter tolerances ensure higher precision, which is critical in industries such as aerospace and automotive. Machines with a tolerance of ±0.01 mm are considered high-precision, making them ideal for applications requiring exact specifications. This property is vital for buyers to ensure product quality and reduce waste. -
Power Rating
– The power rating of a metal cutting machine is measured in horsepower (HP) or kilowatts (kW). A higher power rating allows the machine to cut through tougher materials more efficiently. For instance, a machine rated at 10 HP can handle heavier workloads than one rated at 5 HP. Buyers must assess their production needs to select a machine that can deliver the necessary power without overloading. -
Spindle Speed
– Spindle speed, measured in revolutions per minute (RPM), indicates how fast the cutting tool rotates. Higher spindle speeds can improve cutting efficiency and surface finish. However, the optimal speed varies depending on the material being cut. Understanding spindle speed is crucial for buyers to ensure that the machine can perform effectively across different materials and thicknesses. -
Feed Rate
– The feed rate is the speed at which the workpiece is fed into the cutting tool. It is typically measured in inches per minute (IPM) or millimeters per minute (MPM). A balanced feed rate is essential for achieving the desired cutting efficiency and surface finish. Buyers should consider their production volume and the specific materials to determine the appropriate feed rate for their operations.
What Are Common Trade Terms Related to Metal Cutting Machines?
Familiarity with industry terminology is essential for navigating the procurement process effectively. Here are some common terms that B2B buyers should know:
-
OEM (Original Equipment Manufacturer)
– An OEM is a company that produces parts or equipment that may be marketed by another manufacturer. When sourcing metal cutting machines, buyers often prefer OEMs for their reliability and quality assurance. Understanding the role of OEMs can help buyers identify trustworthy suppliers. -
MOQ (Minimum Order Quantity)
– MOQ refers to the smallest quantity of a product that a supplier is willing to sell. For metal cutting machines, MOQs can vary significantly based on the supplier and the machine model. Knowing the MOQ helps buyers plan their budgets and inventory more effectively. -
RFQ (Request for Quotation)
– An RFQ is a document that buyers send to suppliers to request price quotes for specific products. It usually includes detailed specifications of the desired machines. Submitting an RFQ allows buyers to compare prices and negotiate terms with multiple suppliers. -
Incoterms (International Commercial Terms)
– Incoterms are a set of internationally recognized rules that define the responsibilities of buyers and sellers in international trade. They cover aspects such as shipping, insurance, and risk transfer. Familiarity with Incoterms helps buyers clarify shipping terms and avoid misunderstandings in cross-border transactions. -
Lead Time
– Lead time is the amount of time it takes from placing an order until the product is delivered. For metal cutting machines, lead times can vary based on the complexity of the machine and the supplier’s production capacity. Understanding lead times is crucial for buyers to effectively plan their production schedules.
By grasping these essential technical properties and trade terms, international B2B buyers can make informed decisions when sourcing metal cutting machines from China, ultimately enhancing their operational efficiency and product quality.
Navigating Market Dynamics and Sourcing Trends in the metal cutting machine china Sector
What Are the Current Market Dynamics and Key Trends in the Metal Cutting Machine Sector from China?
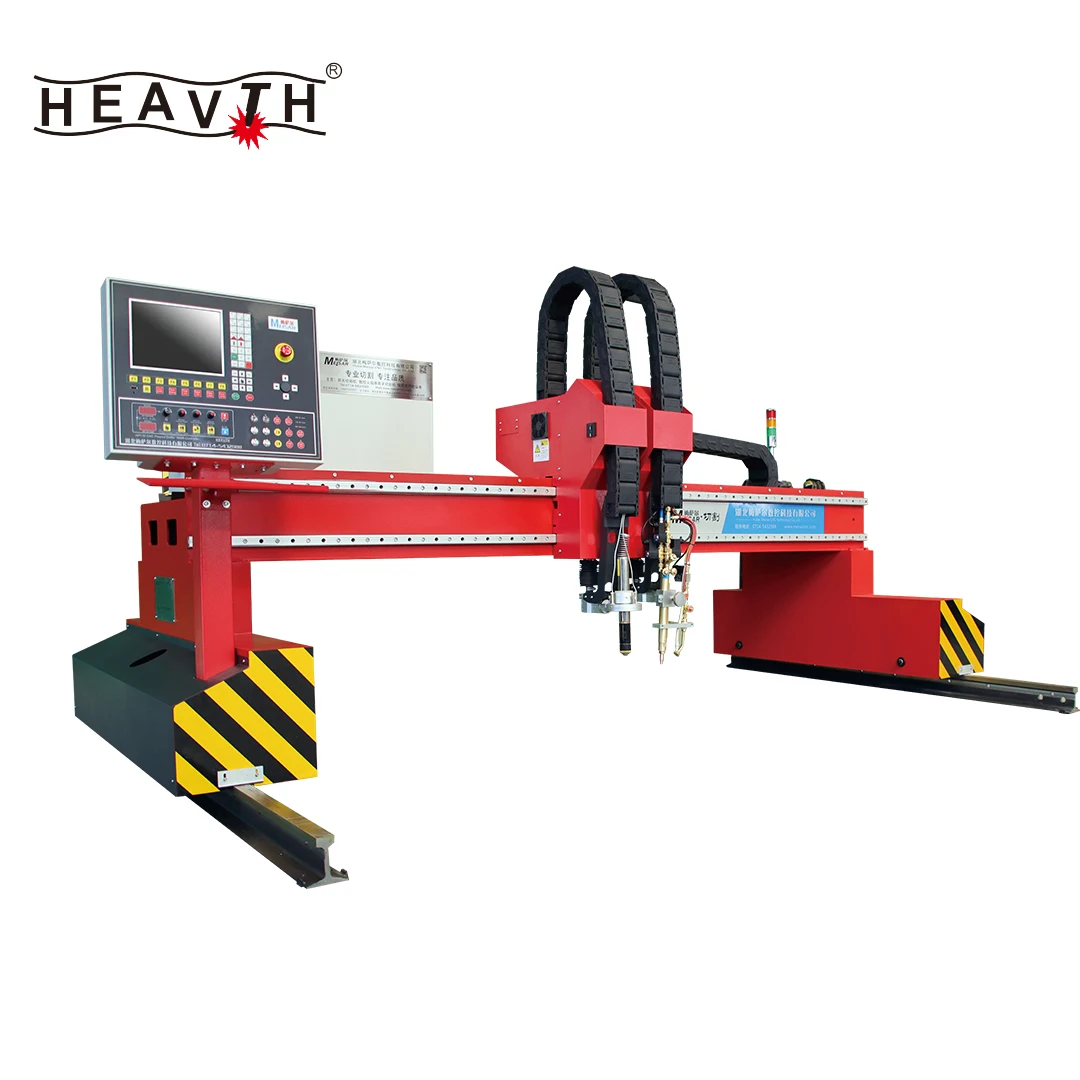
A stock image related to metal cutting machine china.
The global market for metal cutting machines is experiencing significant growth, driven by increasing industrial automation and technological advancements. In particular, the demand for precision engineering and customized solutions is on the rise, particularly among international B2B buyers in regions like Africa, South America, the Middle East, and Europe. These markets are increasingly adopting advanced manufacturing techniques, which include CNC (Computer Numerical Control) machines that enhance productivity and reduce waste.
Emerging trends include the integration of Industry 4.0 technologies, such as IoT (Internet of Things) and AI (Artificial Intelligence), which enable real-time monitoring and predictive maintenance. This trend allows manufacturers to optimize machine performance, leading to reduced downtime and increased efficiency. Furthermore, there is a growing demand for machines that can handle diverse materials, including composites and exotic alloys, which are becoming common in sectors like aerospace and automotive.
B2B buyers should also pay attention to the evolving landscape of supplier relationships. With the rise of digital platforms, sourcing processes have become more transparent, allowing buyers to access a broader range of suppliers and compare offerings more effectively. This shift not only enhances competitive pricing but also provides opportunities for establishing long-term partnerships with reliable manufacturers in China.
How Does Sustainability and Ethical Sourcing Impact the Metal Cutting Machine Sector?
Sustainability has become a pivotal concern in the metal cutting machine sector, particularly in the context of global supply chains. The environmental impact of manufacturing processes, such as energy consumption and waste generation, has prompted buyers to seek machines that comply with green standards. For instance, the adoption of energy-efficient technologies and the use of recyclable materials in machine components are increasingly prioritized.
Furthermore, ethical sourcing practices are gaining traction among international B2B buyers. Ensuring that suppliers adhere to fair labor practices and environmentally friendly operations is essential for maintaining corporate social responsibility. Certifications such as ISO 14001 (Environmental Management) and ISO 45001 (Occupational Health and Safety) are becoming important benchmarks for evaluating suppliers.
Buyers should actively seek out manufacturers who have demonstrated commitment to sustainability through the use of ‘green’ materials and eco-friendly production techniques. This not only aligns with global sustainability goals but also enhances brand reputation and customer loyalty.
What Is the Brief Evolution of the Metal Cutting Machine Industry in China?
The metal cutting machine industry in China has evolved significantly over the past few decades. Initially focused on basic machinery production, the sector has transformed into a hub for advanced manufacturing technologies. The introduction of CNC technology in the 1990s marked a turning point, as it enabled precision machining and automated production processes.
In recent years, Chinese manufacturers have increasingly invested in R&D to develop innovative solutions that meet global standards. This commitment to technological advancement has positioned China as a leading exporter of metal cutting machines, catering to diverse international markets. Today, the sector is characterized by a blend of traditional craftsmanship and cutting-edge technology, making it a key player in the global manufacturing landscape.
Overall, international B2B buyers looking to source metal cutting machines from China should focus on understanding these dynamics, prioritizing sustainability, and leveraging the technological advancements that define the current market landscape.
Frequently Asked Questions (FAQs) for B2B Buyers of metal cutting machine china
-
How do I choose the right metal cutting machine for my business needs?
Choosing the right metal cutting machine involves assessing your specific requirements, such as material types, thickness, and production volume. Consider the machine’s capabilities, including cutting precision, speed, and versatility. Evaluate the available technologies, such as laser, plasma, or waterjet cutting, and determine which best suits your production goals. Additionally, consult with suppliers to understand customization options that align with your operations. -
What are the key features to look for in a metal cutting machine from China?
When sourcing a metal cutting machine from China, prioritize features like cutting speed, precision, and ease of operation. Look for machines with advanced technology, such as CNC capabilities for enhanced automation and control. Assess the machine’s build quality, as robust construction can lead to better durability. Additionally, inquire about after-sales support, warranty, and availability of spare parts to ensure long-term reliability. -
What should I consider when vetting suppliers of metal cutting machines in China?
Vetting suppliers involves researching their reputation, experience, and customer feedback. Check for certifications like ISO or CE, which indicate adherence to international quality standards. Request references from previous clients to gauge their satisfaction levels. It’s also beneficial to perform a factory visit or request a video inspection to assess manufacturing processes and working conditions, ensuring transparency and reliability. -
What are the typical minimum order quantities (MOQs) for metal cutting machines in China?
Minimum order quantities (MOQs) can vary significantly based on the supplier and the type of machine. Generally, MOQs for standard models range from one to five units, while customized machines may require higher quantities. Discuss your specific needs with suppliers to negotiate MOQs that align with your budget and inventory strategy. Be aware that lower MOQs can lead to higher per-unit costs, so balance your requirements with financial considerations. -
What payment terms should I negotiate when purchasing a metal cutting machine from China?
When negotiating payment terms, aim for options that minimize risk. Common terms include a 30% deposit upon order confirmation and the remaining 70% before shipment. Consider using secure payment methods like letters of credit or escrow services for added protection. It’s crucial to clarify payment schedules and conditions upfront to avoid misunderstandings and ensure a smooth transaction process. -
How can I ensure quality assurance when sourcing metal cutting machines from China?
Implementing a quality assurance strategy starts with selecting reputable suppliers with established quality control processes. Request detailed product specifications and certifications before purchase. Conduct pre-shipment inspections through third-party services to verify compliance with your standards. Establish clear communication with the supplier regarding quality expectations and consider including penalties for non-compliance in your contract. -
What logistics considerations should I keep in mind when importing metal cutting machines from China?
When importing machines, consider shipping methods, transit times, and customs clearance processes. Evaluate the total landed cost, which includes shipping, duties, and insurance. Collaborate with a reliable freight forwarder who understands the complexities of international shipping and can navigate potential challenges. Ensure that all shipping documentation is accurate to prevent delays at customs and facilitate a smooth delivery. -
Are there customization options available for metal cutting machines sourced from China?
Yes, many Chinese manufacturers offer customization options to meet specific operational needs. Customizations can include size adjustments, additional features, or tailored software solutions. When discussing your requirements, provide detailed specifications to ensure the machine aligns with your production processes. Confirm the lead time for custom orders and any additional costs involved to make informed budgeting decisions.
Important Disclaimer & Terms of Use
⚠️ Important Disclaimer
The information provided in this guide, including content regarding manufacturers, technical specifications, and market analysis, is for informational and educational purposes only. It does not constitute professional procurement advice, financial advice, or legal advice.
While we have made every effort to ensure the accuracy and timeliness of the information, we are not responsible for any errors, omissions, or outdated information. Market conditions, company details, and technical standards are subject to change.
B2B buyers must conduct their own independent and thorough due diligence before making any purchasing decisions. This includes contacting suppliers directly, verifying certifications, requesting samples, and seeking professional consultation. The risk of relying on any information in this guide is borne solely by the reader.
Strategic Sourcing Conclusion and Outlook for metal cutting machine china
In the evolving landscape of global manufacturing, strategic sourcing of metal cutting machines from China presents significant opportunities for international B2B buyers. By leveraging China’s advanced technology and competitive pricing, businesses in Africa, South America, the Middle East, and Europe can enhance their operational efficiency and product quality. It is essential to consider factors such as supplier reliability, technological advancements, and after-sales support when selecting a partner.
Why is Strategic Sourcing Essential for Metal Cutting Machines?
Strategic sourcing not only reduces costs but also fosters innovation through access to the latest machine technologies. Establishing strong relationships with Chinese manufacturers can lead to tailored solutions that meet specific industry needs, ensuring that buyers remain competitive in their respective markets.
What Should Buyers Do Next?
As you navigate the procurement process, prioritize suppliers who demonstrate a commitment to quality and sustainability. Engage in thorough due diligence and consider attending industry trade shows in China to foster direct connections with potential partners.
Looking ahead, the demand for high-performance metal cutting machines will continue to rise. By making informed sourcing decisions today, international buyers can position themselves for success in the dynamic global market. Embrace the opportunity to collaborate with Chinese manufacturers and drive your business forward.