Cut Costs on Building Materials: The Ultimate China Guide (2025)
Introduction: Navigating the Global Market for building materials china
In today’s competitive landscape, sourcing building materials from China presents a unique set of challenges and opportunities for international B2B buyers. The growing demand for high-quality construction products, coupled with the complexities of global supply chains, necessitates a strategic approach to procurement. This guide on building materials from China is designed to help you navigate these complexities, ensuring that you make informed decisions that align with your business objectives.
Throughout this comprehensive guide, you will discover an array of essential information, including the various types of building materials available, their diverse applications, and effective strategies for supplier vetting. We will also delve into cost considerations and logistics, providing you with the tools needed to negotiate favorable terms and conditions. By understanding the nuances of the Chinese market, particularly for buyers in Africa, South America, the Middle East, and Europe—including key markets like Egypt and South Africa—you can effectively mitigate risks and enhance your procurement strategies.
Empowered with actionable insights and expert recommendations, this guide aims to transform the way you source building materials from China, ultimately enabling you to capitalize on the advantages of this vast market. Whether you’re looking to establish long-term supplier relationships or seeking innovative materials that meet your project requirements, this resource will serve as your roadmap to success in the global building materials arena.
Understanding building materials china Types and Variations
Type Name | Key Distinguishing Features | Primary B2B Applications | Brief Pros & Cons for Buyers |
---|---|---|---|
Ceramic Tiles | Durable, water-resistant, available in various designs | Flooring, wall coverings, commercial spaces | Pros: Aesthetic appeal, easy maintenance. Cons: Can be brittle, requires skilled installation. |
Steel Reinforcement | High tensile strength, corrosion-resistant options | Construction of buildings, bridges, infrastructure | Pros: Essential for structural integrity. Cons: Price fluctuations, requires careful sourcing. |
Concrete Blocks | Versatile, strong, and energy-efficient | Walls, foundations, landscaping | Pros: Cost-effective, good insulation. Cons: Heavy, requires proper handling and transportation. |
PVC Panels | Lightweight, moisture-resistant, easy to install | Interior walls, ceilings, and cladding | Pros: Quick installation, low maintenance. Cons: Less durable than traditional materials, limited aesthetic options. |
Glass Facades | Modern aesthetic, energy-efficient with insulation options | High-rise buildings, commercial properties | Pros: Enhances natural light, aesthetic appeal. Cons: Higher initial costs, requires specialized installation. |
What Are the Characteristics and Suitability of Ceramic Tiles for B2B Buyers?
Ceramic tiles are a popular choice in the building materials market due to their durability and water resistance. They come in a wide variety of designs, making them suitable for both aesthetic and functional applications. B2B buyers should consider the tile’s slip resistance and maintenance requirements, especially for commercial spaces. While ceramic tiles offer an appealing finish, they can be brittle, necessitating skilled installation to avoid damage during handling and fitting.
Why Is Steel Reinforcement Essential for Construction Projects?
Steel reinforcement is crucial for ensuring the structural integrity of buildings and infrastructure projects. Its high tensile strength makes it suitable for various applications, from residential buildings to large-scale bridges. B2B purchasers should pay attention to the quality and corrosion resistance of the steel, as these factors significantly influence longevity and performance. Although the cost can fluctuate based on market conditions, sourcing high-quality steel reinforcement is vital for any serious construction endeavor.

A stock image related to building materials china.
How Do Concrete Blocks Benefit Construction Projects?
Concrete blocks are a versatile building material known for their strength and energy efficiency. They are commonly used in walls, foundations, and landscaping projects. For B2B buyers, the cost-effectiveness of concrete blocks is a significant advantage, along with their good thermal insulation properties. However, their heavy weight requires careful handling and transportation, which can add to logistics costs. Buyers should assess the local availability and delivery options to optimize their procurement strategy.
What Advantages Do PVC Panels Offer for Interior Applications?
PVC panels are lightweight, moisture-resistant, and easy to install, making them an attractive option for interior walls and ceilings. They allow for quick installation, which can significantly reduce labor costs on projects. However, buyers should note that while PVC panels require low maintenance, they may not be as durable as traditional materials. This trade-off between ease of use and durability is crucial for B2B buyers planning long-term investments in building materials.
Why Are Glass Facades Becoming Popular in Modern Architecture?
Glass facades are increasingly favored for their modern aesthetic and energy-efficient properties. They allow for abundant natural light, enhancing the ambiance of commercial properties and high-rise buildings. For B2B buyers, investing in glass facades can elevate the overall design of a project, although they come with higher initial costs and require specialized installation. Ensuring proper sourcing and installation practices is essential to maximize the benefits of this sophisticated building material.
Related Video: Introduction to Building Materials
Key Industrial Applications of building materials china
Industry/Sector | Specific Application of Building Materials China | Value/Benefit for the Business | Key Sourcing Considerations for this Application |
---|---|---|---|
Construction and Infrastructure | Prefabricated Concrete Elements | Reduced construction time and labor costs | Quality certifications, transportation logistics, and local regulations |
Real Estate Development | Sustainable Building Materials | Enhanced property value and marketability | Compliance with international environmental standards, sourcing transparency |
Industrial Manufacturing | Steel and Metal Components | Increased durability and strength in structures | Material specifications, supplier reliability, and delivery timelines |
Energy Sector | Composite Materials for Renewable Energy | Improved efficiency and reduced operational costs | Technical support, compatibility with existing systems, and warranty terms |
Hospitality and Tourism | Decorative Finishes and Interior Materials | Enhanced aesthetic appeal leading to higher guest satisfaction | Customization options, availability of design samples, and lead times |
How Are Building Materials from China Used in the Construction and Infrastructure Sector?
In the construction and infrastructure sector, building materials from China, particularly prefabricated concrete elements, are increasingly favored for their efficiency. These elements streamline the construction process by allowing for quicker assembly on-site, which significantly reduces labor costs and project timelines. For international buyers, especially in Africa and South America, it is crucial to ensure that these materials meet local building codes and quality standards to avoid delays and compliance issues.
What Are the Benefits of Using Sustainable Building Materials in Real Estate Development?
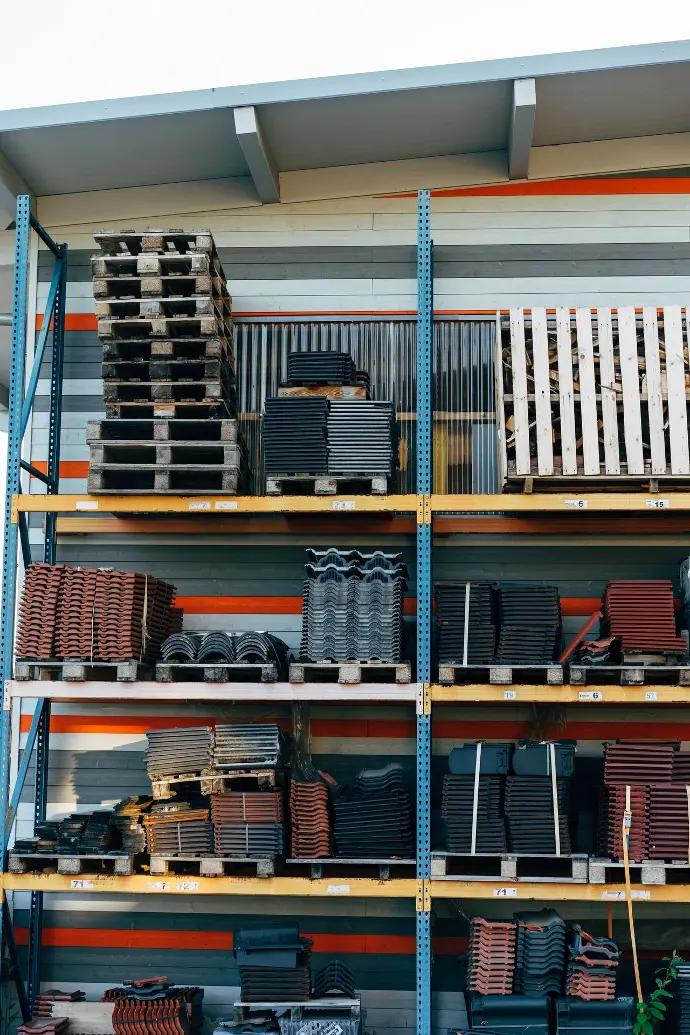
A stock image related to building materials china.
Sustainable building materials sourced from China offer significant advantages in real estate development, particularly in enhancing property value and marketability. These materials often comply with green building certifications, appealing to environmentally conscious buyers and investors. For buyers in Europe and the Middle East, understanding the environmental regulations in their markets is essential for sourcing materials that not only meet aesthetic requirements but also contribute to sustainability goals.
How Do Steel and Metal Components Benefit Industrial Manufacturing?
In industrial manufacturing, the use of steel and metal components from China is vital for constructing robust structures that require durability and strength. These materials are integral in various applications, including machinery and factory buildings. Buyers should prioritize suppliers who offer reliable material specifications and can guarantee timely deliveries, especially in regions like South Africa where manufacturing timelines are critical for project success.
Why Are Composite Materials Important in the Energy Sector?
The energy sector benefits from the use of composite materials sourced from China, particularly for renewable energy applications such as wind turbines and solar panels. These materials improve efficiency and reduce operational costs, making them an attractive option for energy companies. For international buyers, especially in the Middle East, it is essential to evaluate the technical support offered by suppliers and ensure compatibility with existing energy systems to maximize investment returns.
How Do Decorative Finishes Enhance Hospitality and Tourism?
In the hospitality and tourism sector, decorative finishes and interior materials from China significantly enhance the aesthetic appeal of hotels and resorts. This, in turn, leads to higher guest satisfaction and repeat business. Buyers should consider customization options and request design samples to ensure that the materials align with their brand identity and customer expectations. Lead times are also a critical factor to ensure timely project completion, particularly in competitive markets like Europe.
Related Video: Uses of materials
3 Common User Pain Points for ‘building materials china’ & Their Solutions
Scenario 1: Navigating Quality Assurance Challenges in Chinese Building Materials
The Problem: One of the most pressing challenges faced by B2B buyers sourcing building materials from China is the inconsistency in quality. Products can vary significantly from one supplier to another, leading to a situation where the materials do not meet local building codes or project specifications. This inconsistency can result in costly delays, project overruns, and potential safety hazards. Buyers often find themselves stuck with materials that are subpar, which can compromise the integrity of their projects.
The Solution: To mitigate quality assurance issues, buyers should implement a robust supplier evaluation process. This includes conducting thorough background checks on potential suppliers, examining their production facilities, and reviewing their quality control processes. Requesting samples before placing bulk orders is crucial. Additionally, consider partnering with third-party inspection services in China that can conduct pre-shipment inspections to ensure that the materials meet specified standards. Establishing clear quality criteria and maintaining open lines of communication with suppliers will also help in aligning expectations and ensuring that the final products meet the necessary specifications.
Scenario 2: Overcoming Language and Cultural Barriers in Procurement
The Problem: Language and cultural differences can pose significant challenges for international buyers when sourcing building materials from China. Miscommunication can lead to misunderstandings about product specifications, pricing, and delivery timelines. For instance, a buyer may think they have agreed on a specific type of material, only to find that the supplier has interpreted the order differently. Such situations can result in wasted resources and strained business relationships.
The Solution: To navigate these barriers effectively, buyers should consider hiring a local sourcing agent or a consultant who understands both the market and the language. This intermediary can facilitate communication, help clarify product specifications, and ensure that both parties are on the same page regarding expectations. Additionally, investing in translation tools or services can also be beneficial for direct communication. When drafting contracts or agreements, using clear, straightforward language and including visual aids or diagrams can further minimize the risk of misunderstandings.
Scenario 3: Managing Logistics and Delivery Timelines from China
The Problem: Logistics is another critical pain point for B2B buyers dealing with building materials from China. Delays in shipping, customs clearance, and unexpected costs can significantly affect project timelines. For instance, a buyer may plan a project around a specific delivery date, only to face unforeseen shipping delays that push back the entire schedule, leading to increased costs and potential penalties.
The Solution: To improve logistics management, buyers should engage with reputable freight forwarders who specialize in international shipping of building materials. These professionals can provide insights into the best shipping routes, help with customs paperwork, and offer solutions for potential delays. Additionally, incorporating buffer time into project schedules can help accommodate possible shipping disruptions. Establishing strong relationships with suppliers to receive real-time updates on order statuses and delivery timelines can also provide greater transparency and allow for proactive planning. Implementing a robust tracking system for shipments will enable buyers to monitor their orders closely and address any issues as they arise.
By addressing these common pain points with actionable strategies, B2B buyers can improve their procurement processes and ensure a smoother experience when sourcing building materials from China.
Strategic Material Selection Guide for building materials china
When selecting building materials from China, international B2B buyers must consider various factors that affect performance, cost, and compliance with local standards. Here, we analyze four common materials used in the construction industry, highlighting their properties, advantages, disadvantages, and specific considerations for buyers from Africa, South America, the Middle East, and Europe.
What Are the Key Properties of Steel in Building Materials?
Steel is a widely used construction material known for its high strength-to-weight ratio and versatility. Key properties include:
- Temperature/Pressure Rating: Steel can withstand high temperatures and pressures, making it suitable for structural applications.
- Corrosion Resistance: While standard steel is prone to rust, galvanized or stainless steel variants offer enhanced corrosion resistance.
Pros: Steel is durable, provides excellent load-bearing capabilities, and can be prefabricated for faster assembly.
Cons: The cost can be high, especially for corrosion-resistant grades, and manufacturing complexity may increase due to the need for specialized techniques.
Impact on Application: Steel is compatible with various media, including water and chemicals, making it suitable for diverse environments.
Considerations for Buyers: Buyers should ensure compliance with international standards such as ASTM and DIN. Understanding local regulations regarding fire resistance and structural integrity is crucial, particularly in regions prone to seismic activity.
How Does Concrete Compare as a Building Material?
Concrete is another fundamental building material known for its compressive strength and durability.
- Temperature/Pressure Rating: Concrete can withstand significant pressure, though its performance can vary with temperature changes.
- Corrosion Resistance: While inherently resistant to corrosion, concrete can degrade if exposed to aggressive chemicals or moisture without proper treatment.
Pros: Concrete is cost-effective, widely available, and offers excellent fire resistance.
Cons: It can be heavy and requires reinforcement (often with steel), which adds to overall costs and complexity.
Impact on Application: Concrete is ideal for load-bearing structures and foundations but may not be suitable for environments with extreme temperature fluctuations unless properly formulated.
Considerations for Buyers: International standards like ASTM C150 for cement and ASTM C33 for aggregates should be adhered to. Buyers should also consider local preferences for concrete mixes, particularly in regions with unique environmental challenges.
What Are the Advantages of Using Wood in Construction?
Wood is a traditional building material that offers aesthetic appeal and sustainability.
- Temperature/Pressure Rating: Wood performs well under normal temperature conditions but can be affected by moisture and temperature variations.
- Corrosion Resistance: While not inherently resistant to pests and decay, treated wood can withstand various environmental conditions.
Pros: Wood is lightweight, easy to work with, and offers excellent insulation properties.
Cons: It is less durable than steel and concrete, particularly in humid or pest-prone environments, and can be subject to warping.
Impact on Application: Wood is suitable for residential buildings and decorative elements but may not be ideal for high-load applications without proper treatment.
Considerations for Buyers: Compliance with local building codes and standards (like EN 1995 for Europe) is essential. Buyers should also assess the sustainability of wood sources, especially in regions focused on environmental conservation.
How Does Brick Stand Up as a Building Material?
Brick is a classic building material known for its durability and thermal mass properties.
- Temperature/Pressure Rating: Bricks can withstand significant pressure and are generally stable under temperature changes.
- Corrosion Resistance: Brick is resistant to many environmental factors, though it can be affected by freeze-thaw cycles.
Pros: Bricks are fire-resistant, provide excellent insulation, and have a long lifespan.
Cons: They can be labor-intensive to install and may require additional structural support.
Impact on Application: Bricks are often used in walls and facades, providing aesthetic value and energy efficiency.
Considerations for Buyers: Compliance with standards such as ASTM C62 for brick should be prioritized. Buyers should also consider the local availability of bricks and the associated transportation costs.
Summary Table of Building Materials
Material | Typical Use Case for building materials china | Key Advantage | Key Disadvantage/Limitation | Relative Cost (Low/Med/High) |
---|---|---|---|---|
Steel | Structural frameworks, beams, and reinforcements | High strength-to-weight ratio | Can be expensive, especially for corrosion-resistant types | High |
Concrete | Foundations, load-bearing walls, and pavements | Cost-effective and durable | Heavy and requires reinforcement | Medium |
Wood | Residential structures, decorative elements | Lightweight and easy to work with | Less durable in humid environments | Medium |
Brick | Walls, facades, and energy-efficient structures | Fire-resistant and long-lasting | Labor-intensive installation | Medium |
By understanding the properties, advantages, and limitations of these materials, international B2B buyers can make informed decisions that align with their specific project requirements and local standards.
In-depth Look: Manufacturing Processes and Quality Assurance for building materials china
What Are the Key Manufacturing Processes for Building Materials in China?
The manufacturing of building materials in China involves several critical stages that ensure the production of high-quality products. Understanding these stages is essential for international B2B buyers looking to source building materials effectively.
What Are the Main Stages of Manufacturing Building Materials?
-
Material Preparation:
The first stage involves sourcing and preparing raw materials. This includes selecting high-quality aggregates, cement, metals, and other components. Suppliers often conduct rigorous tests on raw materials to ensure they meet the required specifications and standards. -
Forming:
In this stage, the raw materials undergo various forming processes, which may include casting, molding, or extrusion. For instance, concrete blocks are often produced by mixing cement with aggregates, then pouring the mixture into molds. Advanced machinery and technology, such as automated mixing and forming equipment, are frequently employed to enhance precision and efficiency. -
Assembly:
For building materials that consist of multiple components, assembly is a crucial phase. This could involve the joining of prefabricated elements or the integration of various materials into a final product. Effective assembly techniques are vital for ensuring structural integrity and performance. -
Finishing:
The final stage of the manufacturing process includes surface treatment, coating, and packaging. Finishing processes not only enhance the aesthetic appeal of the materials but also improve durability and resistance to environmental factors. Quality checks are often performed at this stage to confirm that the finished products meet market requirements.
How Is Quality Assurance Implemented in Building Materials Manufacturing?
Quality assurance (QA) is a fundamental component of the manufacturing process in China, especially given the increasing global demand for reliable building materials. Buyers should familiarize themselves with international standards and industry-specific certifications that ensure product quality.
What International Standards Are Relevant for Building Materials?
-
ISO 9001: This standard outlines the criteria for a quality management system and is essential for manufacturers aiming to demonstrate their ability to consistently provide products that meet customer and regulatory requirements.
-
CE Marking: Particularly relevant for the European market, CE marking indicates that products conform to health, safety, and environmental protection standards. It is vital for buyers in Europe to ensure that their suppliers comply with this certification.
-
API Standards: For building materials related to oil and gas industries, the American Petroleum Institute (API) standards are crucial. These standards ensure that materials can withstand the rigorous demands of these sectors.
What Are the Key Quality Control Checkpoints?
Quality control (QC) is vital throughout the manufacturing process. Buyers should be aware of the common QC checkpoints that ensure product integrity.
-
Incoming Quality Control (IQC):
This involves inspecting raw materials upon arrival to verify their quality against specifications. Effective IQC helps prevent defects in the final product. -
In-Process Quality Control (IPQC):
During the manufacturing process, IPQC checks are conducted at various stages. This includes monitoring the forming and assembly processes to identify and address issues in real-time. -
Final Quality Control (FQC):
Once the products are finished, FQC involves comprehensive testing and inspection. This ensures that the final output meets all quality standards and specifications before shipping.
What Common Testing Methods Are Used for Building Materials?
Manufacturers in China employ various testing methods to ensure compliance with quality standards. Some common methods include:
-
Compressive Strength Testing: Essential for concrete and masonry materials, this test evaluates the material’s load-bearing capacity.
-
Durability Testing: This involves exposing materials to environmental conditions to assess their long-term performance.
-
Dimensional Inspection: Ensuring that products meet specified dimensions and tolerances is crucial for compatibility in construction applications.
How Can B2B Buyers Verify Supplier Quality Control Practices?
For international B2B buyers, verifying a supplier’s quality control practices is essential to mitigate risks and ensure product reliability. Here are actionable steps:
-
Conduct Supplier Audits:
Regular audits of potential suppliers can provide insights into their manufacturing processes and quality control systems. This includes reviewing their certifications, quality management systems, and production capabilities. -
Request Quality Control Reports:
Suppliers should provide documentation of their quality control processes, including results from IQC, IPQC, and FQC. These reports can help buyers assess compliance with international standards. -
Engage Third-Party Inspection Services:
Utilizing independent inspection services can add an extra layer of assurance. Third-party inspectors can evaluate the manufacturing facility, processes, and final products to confirm they meet required standards.
What Are the Quality Control Nuances for International B2B Buyers?
International buyers, particularly from regions such as Africa, South America, the Middle East, and Europe, should be aware of specific nuances in quality control:
-
Cultural Differences: Understanding cultural expectations regarding quality can impact negotiations and agreements with suppliers. Buyers should communicate their quality expectations clearly.
-
Regulatory Compliance: Different markets have varying regulations. For example, products exported to the EU must comply with CE marking requirements, while those going to Africa may need to meet different local standards.
-
Logistics and Shipping Considerations: Quality can be affected during transportation. Buyers should work with suppliers who have robust packaging and shipping practices to minimize damage during transit.
In conclusion, understanding the manufacturing processes and quality assurance protocols for building materials in China is crucial for international B2B buyers. By familiarizing themselves with the stages of production, relevant standards, QC checkpoints, and verification methods, buyers can make informed sourcing decisions that align with their quality expectations and market requirements.
Practical Sourcing Guide: A Step-by-Step Checklist for ‘building materials china’
Introduction
Sourcing building materials from China can be a lucrative opportunity for international B2B buyers, particularly in regions like Africa, South America, the Middle East, and Europe. However, navigating the complexities of international procurement requires a strategic approach. This checklist serves as a practical guide to streamline your sourcing process, ensuring you make informed decisions that align with your project requirements and business goals.
Step 1: Define Your Technical Specifications
Before initiating the sourcing process, it’s crucial to clearly define your technical specifications for the building materials you need. This includes understanding the dimensions, material quality, and compliance with local regulations.
- Why It Matters: Accurate specifications help avoid misunderstandings with suppliers and ensure that the products meet your project needs.
- What to Look For: Detailed documentation of required materials, including any certifications or standards they must meet.
Step 2: Conduct Market Research on Suppliers
Engage in thorough market research to identify potential suppliers in China. Utilize online platforms, industry trade shows, and local business directories to create a shortlist of manufacturers and distributors.
- Why It Matters: Understanding the market landscape allows you to identify reputable suppliers and avoid subpar options.
- What to Look For: Supplier ratings, customer reviews, and their experience in the specific building materials sector.
Step 3: Evaluate Potential Suppliers
Before committing, it’s essential to vet suppliers thoroughly. Request company profiles, case studies, and references from buyers in a similar industry or region.
- Why It Matters: A well-evaluated supplier can significantly impact the quality and timely delivery of your materials.
- What to Look For: Evidence of past projects, testimonials, and any industry awards or certifications they may have received.
Step 4: Request Samples and Conduct Quality Checks
Always request samples of the building materials before placing a bulk order. This step allows you to assess the quality and suitability of the products.
- Why It Matters: Samples provide a tangible way to evaluate material performance and compatibility with your requirements.
- What to Look For: Consistency in quality, adherence to specifications, and any visible defects.
Step 5: Negotiate Payment Terms and Conditions
Establish clear payment terms with your chosen supplier, including pricing, payment methods, and delivery schedules.
- Why It Matters: Clear financial agreements can prevent disputes and ensure a smooth transaction process.
- What to Look For: Flexible payment options, potential discounts for bulk orders, and clarity on payment timelines.
Step 6: Verify Supplier Certifications
Ensure that your selected suppliers have the necessary certifications and compliance with international standards relevant to building materials.
- Why It Matters: Certifications often indicate a supplier’s commitment to quality and safety, which is critical for building materials.
- What to Look For: ISO certifications, CE marking for European compliance, and any local certifications that apply to your region.
Step 7: Establish a Communication Plan
Effective communication is key to a successful sourcing experience. Develop a communication plan that outlines how you will interact with the supplier throughout the procurement process.
- Why It Matters: A clear communication strategy helps manage expectations and addresses any issues proactively.
- What to Look For: Regular updates on production status, shipping timelines, and a designated point of contact at the supplier’s end.
By following this step-by-step checklist, B2B buyers can navigate the sourcing process for building materials in China with greater confidence and efficiency, ultimately leading to successful procurement outcomes.
Comprehensive Cost and Pricing Analysis for building materials china Sourcing
Understanding the cost structure and pricing of building materials sourced from China is crucial for international B2B buyers, especially those operating in Africa, South America, the Middle East, and Europe. This analysis will delve into the various components that influence pricing, as well as provide actionable insights to optimize procurement strategies.
What Are the Key Cost Components in Building Materials Sourcing?
-
Materials: The raw materials used in manufacturing building products significantly impact overall costs. Prices can fluctuate based on market demand, availability, and quality. Buyers should prioritize sourcing from suppliers who offer sustainable and high-quality materials, as these often lead to better long-term value.
-
Labor: Labor costs in China can vary widely based on the region and skill level required for production. Urban areas typically have higher labor costs, while rural zones may offer lower rates. Understanding these dynamics can help buyers choose the right supplier location to optimize costs.
-
Manufacturing Overhead: This includes costs associated with factory operations such as utilities, maintenance, and administrative expenses. Buyers should inquire about a supplier’s efficiency and production capacity, as well-managed operations can lead to lower overhead costs.
-
Tooling: The initial investment in tooling can be significant, especially for customized products. Buyers should consider the tooling costs when negotiating prices, particularly for high-volume orders where tooling can be amortized over larger production runs.
-
Quality Control (QC): Implementing stringent QC processes can add to costs but is essential for ensuring product reliability and compliance with international standards. Buyers should factor in the costs of QC when assessing supplier proposals.
-
Logistics: Shipping costs from China can vary depending on the mode of transport (air vs. sea), distance, and current fuel prices. Additionally, customs duties and tariffs should be considered, as they can significantly affect the final price.
-
Margin: Suppliers typically include a margin to cover their risks and ensure profitability. Understanding the market dynamics can help buyers negotiate more effectively and secure better pricing.
How Do Price Influencers Affect Building Materials Procurement?
-
Volume and Minimum Order Quantity (MOQ): Larger orders often yield better pricing due to economies of scale. Buyers should negotiate MOQs that align with their purchasing power while ensuring they do not overstock.
-
Specifications and Customization: Custom products may incur additional costs. Clear specifications can prevent misunderstandings and ensure that the product meets the buyer’s needs without incurring unnecessary expenses.
-
Materials and Quality Certifications: Higher-quality materials and certifications (like ISO or CE) can raise costs but may be necessary for compliance and durability. Buyers should weigh the long-term benefits against upfront costs.
-
Supplier Factors: The supplier’s reputation, reliability, and financial stability can affect pricing. Established suppliers may offer better quality and service, justifying a higher price point.
-
Incoterms: Understanding Incoterms (International Commercial Terms) is essential for clarifying who is responsible for shipping, insurance, and tariffs. This knowledge helps buyers calculate the total cost more accurately.
What Are the Best Negotiation Tips for International B2B Buyers?
-
Focus on Total Cost of Ownership (TCO): Instead of just negotiating the unit price, consider the TCO, which includes all related expenses. This approach can lead to better long-term savings.
-
Leverage Competitive Quotes: Obtain multiple quotes from different suppliers to gauge the market rate. Presenting competitive offers can strengthen your negotiating position.
-
Build Relationships: Establishing a strong relationship with suppliers can lead to better pricing and favorable terms over time. Trust can often result in more flexibility during negotiations.
-
Be Clear on Payment Terms: Clear payment terms can affect pricing. Consider negotiating for terms that improve cash flow, such as extended payment periods or discounts for upfront payments.
-
Stay Informed on Market Trends: Keeping up with market trends in both China and your local region can provide leverage in negotiations. Understanding when to buy and the factors affecting prices can lead to strategic purchasing decisions.
Final Thoughts
Navigating the complexities of building materials sourcing from China requires a keen understanding of cost structures and price influencers. By applying these insights, international B2B buyers from Africa, South America, the Middle East, and Europe can optimize their procurement strategies, negotiate effectively, and enhance their supply chain efficiencies. Always remember that prices can fluctuate, and it’s advisable to seek multiple quotes and stay informed about market conditions to make the best purchasing decisions.
Alternatives Analysis: Comparing building materials china With Other Solutions
Understanding the Importance of Alternatives in Building Materials
In the competitive landscape of international construction, B2B buyers must carefully evaluate the materials they choose for their projects. While ‘building materials from China’ offer numerous advantages, it is essential to explore alternative solutions to ensure that the best choice is made based on specific project needs and regional considerations. This analysis will compare building materials from China with two viable alternatives: locally sourced materials and innovative sustainable options, providing actionable insights for buyers from Africa, South America, the Middle East, and Europe.
Comparison Table of Building Materials
Comparison Aspect | Building Materials China | Locally Sourced Materials | Innovative Sustainable Options |
---|---|---|---|
Performance | High durability; varied options available | Performance varies; dependent on local suppliers | Generally high; designed for efficiency and sustainability |
Cost | Competitive pricing; often lower due to mass production | Variable; can be higher due to logistics and limited supply | Potentially higher initial investment but savings in long-term costs |
Ease of Implementation | Established supply chains; logistical support available | May face challenges in availability and consistency | Requires training and adaptation; may need local expertise |
Maintenance | Low maintenance; long-lasting | Maintenance depends on material type; can vary significantly | Low maintenance; often more durable against environmental factors |
Best Use Case | Large-scale projects, commercial buildings | Small to medium projects, culturally relevant designs | Eco-friendly projects, modern constructions aiming for LEED certification |
Pros and Cons of Locally Sourced Materials
Locally sourced materials offer the advantage of supporting regional economies and reducing transportation costs. They can be ideal for projects that require cultural relevance and aesthetic alignment with local architecture. However, the performance of locally sourced materials can be inconsistent, as it heavily relies on the availability and quality provided by local suppliers. Additionally, the cost can be higher due to limited supply and potential logistical challenges, particularly in remote areas.
Exploring Innovative Sustainable Options
Innovative sustainable building materials, such as bamboo, recycled steel, or hempcrete, are gaining traction due to their eco-friendly attributes. These materials often have a lower carbon footprint and can lead to significant savings in energy costs over time. However, the initial investment may be higher compared to traditional building materials, and they require specialized knowledge for implementation. Furthermore, the adoption of these materials can be limited by the availability of local suppliers and expertise, which may pose challenges in certain regions.
Making the Right Choice for Your Building Project
When selecting the best building material for your project, consider the specific needs of your construction, including budget constraints, project scale, and sustainability goals. Building materials from China can provide excellent performance and cost-effectiveness, making them suitable for large-scale projects. However, if cultural alignment and local economic support are priorities, locally sourced materials may be preferable. For projects with a strong emphasis on sustainability, innovative options should be considered despite their higher initial costs. Ultimately, a thorough assessment of all alternatives will empower B2B buyers to make informed decisions that align with their project objectives and values.
Essential Technical Properties and Trade Terminology for building materials china
What Are the Key Technical Properties of Building Materials from China?
Understanding the essential technical properties of building materials is crucial for international buyers, especially in diverse markets like Africa, South America, the Middle East, and Europe. Here are some critical specifications to consider:
Material Grade: What Does It Indicate?
Material grade refers to the quality and performance standards of building materials. In China, various grading systems are used, depending on the type of material—be it steel, concrete, or wood. Higher grades typically signify superior durability, strength, and resistance to environmental factors. For B2B buyers, selecting materials with the appropriate grade ensures compliance with local building codes and enhances the longevity of the structure, reducing long-term costs.
Tolerance: Why Is It Important in Construction?
Tolerance defines the acceptable variation in dimensions for materials. In construction, precision is paramount; even minor deviations can lead to significant structural issues. For instance, steel beams must adhere to specific tolerances to ensure proper load distribution. Understanding tolerance specifications allows buyers to ensure compatibility with other components and maintain quality standards, ultimately avoiding costly rework or structural failures.
Durability: How Does It Affect Your Investment?
Durability measures a material’s ability to withstand wear, pressure, or damage over time. Building materials sourced from China often come with durability ratings that indicate their expected lifespan under various environmental conditions. For B2B buyers, investing in durable materials can significantly reduce maintenance costs and extend the life of a building, which is especially important in regions prone to harsh weather.
Fire Resistance: What Should You Look For?
Fire resistance is a critical property for ensuring safety in construction. Many building materials are rated for their ability to withstand flames and heat. Understanding fire ratings helps buyers select materials that comply with local safety regulations and protect occupants. This is particularly relevant in regions with strict fire safety standards, such as parts of Europe and the Middle East.
Which Trade Terms Are Essential for Buying Building Materials from China?
Familiarity with trade terminology is equally important for navigating the complexities of international procurement. Here are some common terms you should know:
What Is OEM (Original Equipment Manufacturer)?
OEM refers to a company that produces parts or equipment that may be marketed by another manufacturer. In the context of building materials, an OEM might provide customized products tailored to a buyer’s specifications. Understanding OEM relationships can help buyers ensure they receive quality products that meet their specific needs.
What Does MOQ (Minimum Order Quantity) Mean?
MOQ indicates the minimum number of units a supplier is willing to sell. In the building materials industry, MOQs can vary significantly between manufacturers. For B2B buyers, knowing the MOQ is crucial for budgeting and inventory management, particularly for smaller businesses or projects with limited scope.
How Is RFQ (Request for Quotation) Used?
An RFQ is a formal document requesting price quotes from suppliers for specific products. This tool is vital for B2B buyers to gauge market pricing and make informed purchasing decisions. Crafting a clear RFQ can streamline the procurement process, ensuring all necessary specifications are communicated to potential suppliers.
Why Are Incoterms Important for International Shipping?
Incoterms (International Commercial Terms) define the responsibilities of buyers and sellers in international transactions, including shipping, insurance, and tariffs. Understanding these terms helps B2B buyers clarify their obligations and avoid misunderstandings that could lead to additional costs or delays in delivery.
By familiarizing yourself with these technical properties and trade terms, you can navigate the complexities of sourcing building materials from China more effectively, ensuring that your projects are both cost-efficient and compliant with international standards.
Navigating Market Dynamics and Sourcing Trends in the building materials china Sector
What Are the Current Market Dynamics and Key Trends in the China Building Materials Sector?
The building materials sector in China is shaped by a confluence of global economic trends and technological advancements that international B2B buyers must navigate. Recent years have seen a robust recovery in construction activities post-pandemic, driving demand for various building materials. Key trends influencing this market include the increasing adoption of digital technologies, such as Building Information Modeling (BIM) and artificial intelligence, which streamline sourcing and procurement processes. These technologies enable buyers to make data-driven decisions, improving efficiency and reducing costs.
Moreover, the shift towards modular construction is gaining traction, driven by the need for faster project completion and reduced labor costs. This trend is particularly relevant for international buyers from regions like Africa and South America, where rapid urbanization necessitates quick and cost-effective building solutions. Additionally, the focus on sustainable construction is reshaping sourcing strategies, with an increasing demand for eco-friendly materials that comply with international standards.
International buyers must also be aware of geopolitical factors affecting trade dynamics, such as tariffs and trade agreements, particularly between China and European countries or the Middle East. Understanding these dynamics can provide critical insights for making informed purchasing decisions, ensuring that supply chains remain resilient in the face of external pressures.
How Important Is Sustainability and Ethical Sourcing in the Building Materials Sector?
Sustainability and ethical sourcing are no longer optional considerations for international B2B buyers; they are essential components of a responsible business strategy. The environmental impact of building materials—ranging from carbon emissions during production to waste generated during construction—has prompted increased scrutiny from stakeholders. Buyers from regions like Africa and Europe are particularly attuned to these issues, as they align with both regulatory requirements and consumer preferences for green practices.
Ethical supply chains are increasingly prioritized, with buyers seeking suppliers who can demonstrate transparency and responsibility in their operations. This includes adherence to international labor standards and environmental regulations. Certifications such as LEED (Leadership in Energy and Environmental Design) and ISO 14001 for environmental management are becoming crucial criteria for evaluating potential suppliers in China. By sourcing materials that carry these certifications, international buyers can not only enhance their brand reputation but also contribute to broader sustainability goals.
Investing in green materials not only meets regulatory demands but can also lead to cost savings in the long run. For instance, energy-efficient materials can reduce operational costs over time, making them a financially sound choice. Therefore, prioritizing sustainability in sourcing decisions is not just a trend; it’s a strategic imperative for B2B buyers looking to thrive in a competitive market.
What Is the Historical Context of the Building Materials Sector in China?
The evolution of the building materials sector in China can be traced back to the country’s rapid industrialization in the late 20th century. Initially characterized by a focus on quantity over quality, the sector has undergone significant transformations over the past few decades. The introduction of advanced manufacturing techniques and stringent quality controls has propelled China to become one of the largest producers of building materials globally.
In the 2000s, a shift towards modernization and urban development led to the emergence of innovative building materials, aligning with international standards. This evolution has positioned China as a key player in the global building materials market, making it a vital sourcing destination for international buyers. Understanding this historical context enables B2B buyers to appreciate the advancements in quality and sustainability that define the current landscape, equipping them to make informed sourcing decisions.
Frequently Asked Questions (FAQs) for B2B Buyers of building materials china
-
How do I find reliable suppliers of building materials in China?
Finding reliable suppliers involves conducting thorough research and utilizing multiple platforms. Start by exploring B2B marketplaces like Alibaba and Global Sources, where you can filter suppliers based on ratings and reviews. It’s crucial to request samples and conduct video calls to assess their operations. Additionally, consider joining trade shows in China, such as the Canton Fair, to meet suppliers face-to-face. Establishing a relationship with local sourcing agents can also provide valuable insights and help navigate language barriers. -
What are the typical minimum order quantities (MOQ) for building materials from China?
Minimum order quantities (MOQ) vary significantly based on the type of building material and the supplier’s policies. Generally, MOQs can range from 100 to 1,000 units for standard items. For customized products, MOQs may increase to 2,000 or more. It’s essential to discuss MOQs upfront to understand the supplier’s capabilities and negotiate terms that suit your purchasing needs. In some cases, suppliers may be flexible with MOQs for repeat customers or larger contracts. -
What payment terms should I expect when sourcing building materials from China?
Payment terms in international B2B transactions often include options like T/T (telegraphic transfer), L/C (letter of credit), or PayPal. A common practice is to pay a 30% deposit upfront and the remaining 70% before shipment. Some suppliers may offer more favorable terms for long-term relationships or larger orders. Always ensure that you confirm payment methods and terms in writing to avoid misunderstandings, and consider using escrow services to secure transactions. -
How can I ensure quality assurance when sourcing building materials from China?
To ensure quality assurance, implement a strict vetting process for suppliers. Request product samples for evaluation before placing large orders. Consider hiring third-party inspection services to conduct quality checks during production and before shipment. It’s also beneficial to review the supplier’s certifications, such as ISO standards, to verify their commitment to quality. Establishing clear quality specifications in your contracts will help align expectations and reduce the risk of receiving substandard products. -
What logistics considerations should I keep in mind when importing building materials from China?
When importing building materials, logistics play a crucial role. Consider factors such as shipping methods (air vs. sea), freight forwarder selection, and customs clearance processes. It’s important to calculate total landed costs, including shipping fees, tariffs, and insurance. Make sure to comply with local regulations in your country regarding imports, which can vary widely. Working with experienced logistics partners can streamline the shipping process and mitigate potential delays. -
How can I customize building materials to meet specific project requirements?
Customization is often possible with Chinese manufacturers, but it requires clear communication. Start by providing detailed specifications, including dimensions, materials, and finishes. Discuss your customization needs early in the negotiation process to ensure the supplier can meet your requirements. Some suppliers may have design capabilities, while others may require you to provide your own designs. Be prepared for potential MOQ increases for customized products and ensure you receive prototypes for approval before mass production.
-
What are the common challenges faced by B2B buyers when sourcing building materials from China?
Common challenges include language barriers, cultural differences, and varying standards of quality. Buyers may also face difficulties in verifying supplier legitimacy and navigating customs regulations. To mitigate these challenges, invest time in building relationships with suppliers and consider hiring local agents who understand the market. Establishing clear communication and documentation processes can also help reduce misunderstandings and ensure a smoother transaction experience. -
How do trade regulations affect the sourcing of building materials from China?
Trade regulations can significantly impact the sourcing process. Tariffs, import duties, and compliance with local building codes are essential factors to consider. Regulations can vary by country, so it’s crucial to stay informed about current trade agreements and restrictions affecting your specific materials. Collaborating with a customs broker can provide insights into regulatory requirements and help you navigate the complexities of international trade, ensuring compliance and minimizing delays.
Important Disclaimer & Terms of Use
⚠️ Important Disclaimer
The information provided in this guide, including content regarding manufacturers, technical specifications, and market analysis, is for informational and educational purposes only. It does not constitute professional procurement advice, financial advice, or legal advice.
While we have made every effort to ensure the accuracy and timeliness of the information, we are not responsible for any errors, omissions, or outdated information. Market conditions, company details, and technical standards are subject to change.
B2B buyers must conduct their own independent and thorough due diligence before making any purchasing decisions. This includes contacting suppliers directly, verifying certifications, requesting samples, and seeking professional consultation. The risk of relying on any information in this guide is borne solely by the reader.
Strategic Sourcing Conclusion and Outlook for building materials china
What Are the Key Takeaways for Strategic Sourcing in Building Materials from China?
In summary, strategic sourcing for building materials from China offers significant advantages for international B2B buyers, especially in regions like Africa, South America, the Middle East, and Europe. By leveraging China’s extensive manufacturing capabilities, buyers can access a diverse range of high-quality materials at competitive prices. It’s crucial to conduct thorough supplier evaluations, emphasizing quality assurance, reliability, and compliance with international standards.
How Can International Buyers Enhance Their Sourcing Strategies?
International buyers should adopt a proactive approach to building relationships with Chinese suppliers. This includes regular communication, understanding cultural nuances, and utilizing local trade shows to foster connections. Additionally, implementing technology solutions for supply chain management can enhance transparency and efficiency, ensuring timely delivery and reducing risks associated with sourcing.
What Does the Future Hold for Sourcing Building Materials from China?
Looking ahead, the demand for sustainable and innovative building materials is expected to grow. Buyers should stay informed about emerging trends and technologies in the Chinese market, as these can provide opportunities for competitive advantage. By embracing strategic sourcing as a core component of their procurement strategy, international buyers can not only optimize their supply chains but also contribute to sustainable development in their respective regions.
As you move forward, consider engaging with trusted suppliers in China, exploring new partnerships, and continuously adapting your sourcing strategies to align with global market trends. The future of building materials sourcing is bright, and the opportunities are ripe for those ready to take action.