Cut Costs: The Ultimate Guide to Storage Box Manufacturer (2025)
Introduction: Navigating the Global Market for storage box manufacturer
Navigating the complexities of sourcing storage box manufacturers can be a daunting task for international B2B buyers, especially when considering factors such as quality, cost, and supplier reliability. As companies in Africa, South America, the Middle East, and Europe (including regions like Argentina and Spain) expand their operations, the need for efficient storage solutions becomes paramount. This guide aims to demystify the process of sourcing storage boxes by providing a comprehensive overview of the different types available, their applications across various industries, and key considerations for supplier vetting.
Understanding the nuances of the storage box market is crucial for making informed purchasing decisions. Buyers must evaluate not only the materials and designs that best fit their needs but also the reputability of manufacturers in an increasingly global marketplace. This guide will delve into essential topics such as pricing structures, shipping logistics, and quality assurance practices, equipping buyers with actionable insights to enhance their sourcing strategies.
By leveraging this resource, B2B buyers will be empowered to identify reliable storage box manufacturers, ensuring that their procurement processes are both efficient and effective. With the right knowledge, businesses can optimize their storage solutions, ultimately leading to improved operational efficiency and cost savings. Whether you are a seasoned procurement professional or new to the industry, this guide will serve as a valuable tool in navigating the global market for storage box manufacturers.
Understanding storage box manufacturer Types and Variations
Type Name | Key Distinguishing Features | Primary B2B Applications | Brief Pros & Cons for Buyers |
---|---|---|---|
Plastic Storage Boxes | Lightweight, durable, water-resistant options | Warehousing, retail storage, logistics | Pros: Cost-effective, versatile. Cons: Limited temperature resistance. |
Metal Storage Boxes | Heavy-duty, secure, often lockable | Industrial storage, archival solutions | Pros: High security, long-lasting. Cons: Heavier, can be more expensive. |
Cardboard Storage Boxes | Eco-friendly, lightweight, customizable sizes | E-commerce, shipping, temporary storage | Pros: Affordable, recyclable. Cons: Less durable, not suitable for long-term use. |
Stackable Storage Boxes | Designed for efficient stacking and maximizing space | Warehouses, retail, and home organization | Pros: Space-saving, easy to organize. Cons: May not be as sturdy as metal or plastic options. |
Specialty Storage Boxes | Tailored designs for specific products (e.g., electronics) | Pharmaceuticals, electronics, delicate items | Pros: Custom fit, enhanced protection. Cons: Higher cost, longer lead times. |
What Are the Characteristics of Plastic Storage Boxes?
Plastic storage boxes are characterized by their lightweight and durable nature, often made from high-density polyethylene (HDPE) or polypropylene. They are water-resistant and can be used in various environments, making them suitable for warehousing, retail storage, and logistics applications. When purchasing plastic storage boxes, consider the size, load capacity, and whether the boxes are stackable for optimal space efficiency.
How Do Metal Storage Boxes Differ from Other Types?
Metal storage boxes are heavy-duty and typically constructed from steel or aluminum, offering high security and durability. These boxes are ideal for industrial storage and archival solutions where protection against theft or damage is crucial. Buyers should assess the weight of the boxes, lock mechanisms, and whether they can withstand environmental factors, as these features significantly impact their suitability for specific applications.
Why Choose Cardboard Storage Boxes for B2B Needs?
Cardboard storage boxes are a popular choice for businesses due to their eco-friendly nature and cost-effectiveness. They are lightweight and customizable, making them ideal for e-commerce and shipping applications. However, buyers should be aware that while cardboard boxes are affordable and recyclable, they lack durability and may not be suitable for long-term storage solutions.
What Are the Benefits of Stackable Storage Boxes?
Stackable storage boxes are specifically designed to maximize vertical space in warehouses and retail settings. They come in various sizes and materials, allowing for easy organization and accessibility. When considering stackable options, buyers should evaluate the material strength and stacking capacity to ensure they meet their storage needs without compromising safety.
What Are Specialty Storage Boxes and When Should They Be Used?
Specialty storage boxes are custom-designed for specific products, such as electronics or pharmaceuticals, providing tailored protection. These boxes often include features like foam inserts or specific compartmentalization to prevent damage. While they may come at a higher cost and longer lead times, they are essential for businesses that require enhanced protection for delicate or valuable items. Buyers should assess their specific needs and the potential return on investment when considering these options.
Related Video: Equipment Review: The Best Plastic and The Best Glass Food Storage Containers & Our Testing Winners
Key Industrial Applications of storage box manufacturer
Industry/Sector | Specific Application of storage box manufacturer | Value/Benefit for the Business | Key Sourcing Considerations for this Application |
---|---|---|---|
Logistics and Supply Chain | Custom storage boxes for inventory management | Improved organization and efficiency in warehousing | Material durability, size specifications, and weight capacity |
Retail | Point-of-sale storage solutions for merchandise display | Enhanced customer experience and product visibility | Aesthetic design, branding options, and size adaptability |
Manufacturing | Storage for raw materials and components | Streamlined production processes and reduced waste | Compliance with industry standards and material quality |
Pharmaceuticals | Secure storage for sensitive medical supplies | Ensured safety and compliance with regulations | Temperature control features and security options |
E-commerce | Versatile packaging solutions for shipping | Cost-effective shipping and reduced damage rates | Customizability, eco-friendliness, and scalability |
How Are Storage Boxes Utilized in Logistics and Supply Chain Management?
In the logistics and supply chain sector, storage box manufacturers provide custom solutions for inventory management. These boxes are designed to optimize space utilization in warehouses, allowing businesses to categorize and store products efficiently. By implementing these storage solutions, companies can reduce retrieval times and improve overall operational efficiency. International buyers should consider factors such as material durability and size specifications to ensure the boxes meet their specific logistical needs.
What Role Do Storage Boxes Play in Retail Environments?
In retail, storage boxes are essential for point-of-sale displays, enhancing customer experience by improving product visibility. These boxes can be customized to match the store’s branding and aesthetic, making them an integral part of visual merchandising strategies. For B2B buyers, it is crucial to assess design options, branding capabilities, and adaptability to different product sizes to maximize their retail impact.
How Do Storage Solutions Benefit Manufacturing Operations?
Manufacturers utilize storage boxes to organize raw materials and components, which streamlines production processes. By keeping materials readily accessible and properly categorized, businesses can minimize downtime and reduce waste. Buyers in this sector should prioritize compliance with industry standards and the quality of materials to ensure the longevity and safety of their storage solutions.
Why Are Secure Storage Solutions Important in Pharmaceuticals?
In the pharmaceutical industry, secure storage boxes are vital for safeguarding sensitive medical supplies. These boxes often feature temperature control and security mechanisms to comply with strict regulatory requirements. International buyers must focus on these features to ensure that they are investing in storage solutions that not only protect their products but also adhere to industry regulations.
How Can E-commerce Businesses Benefit from Versatile Storage Solutions?
E-commerce companies require versatile packaging solutions for shipping products to customers. Storage boxes that can be customized for various products help reduce shipping costs and minimize damage during transit. When sourcing these solutions, B2B buyers should consider customizability, eco-friendliness, and scalability to ensure they can adapt to fluctuating market demands and customer preferences.
Related Video: Industrial Control Panel Basics
3 Common User Pain Points for ‘storage box manufacturer’ & Their Solutions
Scenario 1: Limited Space for Inventory Management
The Problem: Many B2B buyers, particularly in sectors like retail and logistics, face the challenge of limited storage space. This issue becomes critical during peak seasons when inventory levels fluctuate significantly. Buyers often struggle to find storage solutions that maximize vertical space while being easily accessible. This lack of efficient storage can lead to operational inefficiencies, increased labor costs, and ultimately affect customer satisfaction due to delays in order fulfillment.
The Solution: To address this issue, buyers should consider collaborating with storage box manufacturers that offer customizable solutions tailored to specific storage needs. By utilizing modular storage boxes that can stack efficiently, businesses can optimize vertical space while ensuring easy access to products. Moreover, integrating an inventory management system with these storage solutions can help track stock levels in real-time, allowing for better organization and faster retrieval processes. When sourcing storage boxes, inquire about options that provide flexibility in size and configuration, enabling the system to adapt as your inventory needs change.
Scenario 2: Durability Concerns in Harsh Environments
The Problem: Buyers in industries such as construction, agriculture, or food service often deal with harsh environments where standard storage solutions may not hold up. The risk of damage from moisture, extreme temperatures, or physical impacts can compromise the integrity of stored items, leading to losses and increased replacement costs. Many manufacturers do not adequately address these conditions, leaving buyers with unreliable options.
The Solution: To mitigate this challenge, buyers should seek storage box manufacturers that specialize in producing heavy-duty, weather-resistant storage solutions. Look for boxes made from high-quality materials such as polyethylene or reinforced steel that are designed to withstand extreme conditions. Additionally, ensure that the manufacturer provides testing data or certifications that demonstrate the durability of their products. When negotiating with suppliers, discuss your specific environmental challenges and ask for recommendations on the best materials and designs that will meet those needs. Investing in robust storage solutions will not only protect your items but also enhance long-term cost efficiency.
Scenario 3: Compliance with Safety and Regulatory Standards
The Problem: In sectors such as healthcare, pharmaceuticals, and food service, compliance with safety and regulatory standards is paramount. Buyers often struggle to find storage solutions that not only meet their operational needs but also adhere to strict regulations regarding materials, hygiene, and safety. Non-compliance can lead to hefty fines and damage to reputation, creating significant stress for procurement teams.
The Solution: Buyers should prioritize partnering with storage box manufacturers that have a strong understanding of industry regulations and can provide compliant products. When sourcing, ask for documentation that verifies compliance with relevant standards, such as FDA, ISO, or local health regulations. Additionally, consider manufacturers that offer specialized storage solutions, like antimicrobial storage boxes for healthcare or food-safe containers for the food industry. Engaging in early discussions with potential suppliers about compliance requirements can facilitate the customization of storage solutions that align with your business’s operational and regulatory needs, ensuring peace of mind and operational continuity.
Strategic Material Selection Guide for storage box manufacturer
When selecting materials for storage box manufacturing, international B2B buyers must consider various factors that impact product performance, cost, and compliance with regional standards. Here, we analyze four common materials used in the production of storage boxes: plastic, metal, wood, and cardboard. Each material has unique properties, advantages, and limitations that can influence the final product’s suitability for specific applications.
What are the Key Properties of Plastic for Storage Boxes?
Plastic is a versatile material widely used in storage box manufacturing due to its lightweight nature and resistance to moisture. Common types of plastic, such as polypropylene and polyethylene, offer good temperature resistance and can withstand a range of pressures. They are also resistant to corrosion, making them ideal for various environments.
Pros & Cons: The primary advantage of plastic storage boxes is their durability and low weight, which makes them easy to handle and transport. However, they can be less environmentally friendly than other materials and may not be suitable for high-temperature applications, as they can deform under extreme heat.
Impact on Application: Plastic boxes are often used for storing food items, tools, and sensitive electronic equipment due to their moisture resistance. Buyers should consider local regulations regarding food safety and material recycling.
How Does Metal Compare as a Material for Storage Boxes?
Metal, particularly steel and aluminum, is known for its strength and durability. These materials can withstand significant pressure and offer excellent corrosion resistance, especially when treated with protective coatings.
Pros & Cons: The key advantage of metal storage boxes is their robustness, making them suitable for heavy-duty applications, such as industrial storage. However, they are generally heavier and more expensive than plastic options, which can increase shipping costs. Additionally, metal boxes may require more complex manufacturing processes.
Impact on Application: Metal boxes are ideal for storing tools, machinery parts, and hazardous materials. International buyers should ensure compliance with safety standards, such as those set by ASTM or DIN, particularly in industries like construction and manufacturing.
What are the Benefits of Using Wood for Storage Boxes?
Wood is a traditional material that offers aesthetic appeal and good structural integrity. It is particularly suitable for applications requiring a natural look, such as in retail or home storage.
Pros & Cons: The main advantage of wood is its strength and insulation properties, which can protect contents from temperature fluctuations. However, wood can be susceptible to moisture damage and pests, requiring treatment to enhance durability. Additionally, it is often more expensive than plastic and cardboard.
Impact on Application: Wooden storage boxes are commonly used for decorative purposes or in environments where aesthetics matter. Buyers should consider local sourcing and sustainability certifications, as well as compliance with regulations regarding wood treatment.
Why is Cardboard a Viable Option for Storage Boxes?
Cardboard is a lightweight and cost-effective material, making it a popular choice for temporary storage solutions. It is easily recyclable and can be produced in various strengths.
Pros & Cons: The primary advantage of cardboard is its affordability and ease of customization. However, it is less durable than other materials and may not withstand moisture or heavy loads, limiting its use to lighter items.
Impact on Application: Cardboard boxes are often used for shipping and storing non-perishable goods. Buyers should be aware of the potential need for additional protective packaging in humid environments, particularly in regions like Africa and South America.
Summary Table of Material Selection for Storage Box Manufacturing
Material | Typical Use Case for storage box manufacturer | Key Advantage | Key Disadvantage/Limitation | Relative Cost (Low/Med/High) |
---|---|---|---|---|
Plastic | Food storage, tools, electronics | Lightweight and moisture-resistant | Less environmentally friendly | Low |
Metal | Industrial storage, hazardous materials | Extremely durable and corrosion-resistant | Heavy and more expensive | High |
Wood | Decorative storage, retail displays | Aesthetic appeal and good insulation | Susceptible to moisture and pests | Medium |
Cardboard | Shipping, temporary storage | Affordable and easily customizable | Limited durability and moisture sensitivity | Low |
This analysis provides a comprehensive overview of the materials available for storage box manufacturing, highlighting essential properties and considerations for international B2B buyers. By understanding the pros and cons of each material, buyers can make informed decisions that align with their specific needs and compliance requirements.
In-depth Look: Manufacturing Processes and Quality Assurance for storage box manufacturer
What Are the Main Stages of Manufacturing for Storage Box Production?
The manufacturing process for storage boxes involves several key stages, each crucial for ensuring the final product meets the desired quality and specifications. Understanding these stages can help international B2B buyers make informed decisions when selecting suppliers.
1. Material Preparation
The first step in the manufacturing process is material preparation, which includes sourcing and preparing the raw materials. Storage boxes can be made from various materials, including plastic, wood, and metal. The choice of material significantly affects durability, cost, and suitability for specific applications.
- Material Selection: Buyers should inquire about the sourcing of materials, ensuring they meet industry standards and environmental regulations.
- Pre-processing: This may involve cutting, shaping, or treating materials to enhance their properties, such as adding moisture resistance to wood or UV protection to plastics.
2. Forming Techniques
Once the materials are ready, the next stage is forming, where the raw materials are shaped into the desired forms.
- Injection Molding: Commonly used for plastic storage boxes, this method involves injecting molten plastic into molds, allowing for high precision and repeatability.
- Die-Casting: For metal boxes, die-casting can be employed to create complex shapes with a high degree of accuracy.
- Woodworking Techniques: For wooden storage boxes, techniques such as cutting, routing, and sanding are used to create aesthetically pleasing and functional products.
Each technique has its advantages and specific applications, which buyers should consider based on their needs.
3. Assembly Process
After forming, the next step is assembly, where various components are put together to create the final product.
- Joining Methods: Depending on the material, methods such as welding, adhesive bonding, or mechanical fastening may be used.
- Automation vs. Manual Assembly: Some manufacturers may employ automated assembly lines for efficiency, while others may rely on skilled labor for intricate designs. Buyers should assess the balance between cost and quality in the assembly process.
4. Finishing Touches
The final stage involves finishing, which enhances the aesthetic and functional properties of the storage boxes.
- Surface Treatment: Techniques such as painting, varnishing, or applying protective coatings can improve durability and appearance.
- Quality Checks: This is also the stage where initial quality checks take place to ensure that the product meets the required specifications before packaging.
How Is Quality Assurance Implemented in Storage Box Manufacturing?
Quality assurance (QA) is a critical aspect of manufacturing that ensures products meet specific standards and customer expectations. Understanding QA practices can help international buyers ensure they are sourcing high-quality products.
Relevant International Standards for Storage Box Quality
International standards play a vital role in maintaining product quality. For storage box manufacturers, the following standards are particularly relevant:
- ISO 9001: This standard outlines requirements for a quality management system (QMS). Compliance indicates that a manufacturer has consistent processes in place to ensure quality.
- CE Marking: For products sold in the European market, CE marking indicates conformity with health, safety, and environmental protection standards.
- API Standards: For storage solutions in industrial applications, compliance with American Petroleum Institute (API) standards may be necessary.
Buyers should request documentation of compliance with these standards to verify a supplier’s commitment to quality.
What Are the Key Quality Control Checkpoints?
Quality control (QC) checkpoints are essential in ensuring products meet quality standards at various stages of the manufacturing process. Key checkpoints include:
- Incoming Quality Control (IQC): This involves inspecting raw materials upon arrival to ensure they meet specified standards before production begins.
- In-Process Quality Control (IPQC): Conducted during the manufacturing process, this checkpoint involves regular inspections to catch defects early and minimize waste.
- Final Quality Control (FQC): Before products are packaged and shipped, a final inspection ensures that the finished goods meet all quality requirements.
What Common Testing Methods Are Used in Storage Box Manufacturing?
Testing methods vary depending on the material and intended use of the storage boxes. Common testing methods include:
- Physical Testing: This includes strength tests, load tests, and drop tests to assess the durability and functionality of the boxes.
- Chemical Testing: For plastic storage boxes, chemical resistance testing may be necessary to ensure they do not degrade when exposed to various substances.
- Environmental Testing: This involves testing boxes under various environmental conditions (e.g., humidity, temperature) to ensure they perform as expected in real-world scenarios.
How Can International B2B Buyers Verify Supplier Quality Control?
For buyers from Africa, South America, the Middle East, and Europe, verifying a supplier’s quality control processes is crucial to ensure product reliability. Here are actionable strategies:
- Conduct Supplier Audits: Regular audits can provide insight into a supplier’s manufacturing processes and quality assurance measures.
- Request Quality Reports: Suppliers should provide documentation of their quality control processes, including test results and compliance certifications.
- Engage Third-Party Inspectors: Hiring third-party inspection services can provide an unbiased assessment of the manufacturing processes and product quality.
What Nuances Should B2B Buyers Consider Regarding QC and Certification?
When dealing with international suppliers, B2B buyers should be aware of specific nuances related to quality control and certification:
- Cultural Differences: Understanding cultural attitudes toward quality and compliance can aid in navigating supplier relationships.
- Regional Regulations: Different regions may have unique regulatory requirements; for instance, CE marking is essential for products sold in Europe, while other regions may have different standards.
- Communication: Clear communication about quality expectations and standards from the outset can prevent misunderstandings and ensure alignment with supplier capabilities.
By comprehensively understanding manufacturing processes and quality assurance practices, international B2B buyers can make informed decisions and establish fruitful partnerships with storage box manufacturers.
Practical Sourcing Guide: A Step-by-Step Checklist for ‘storage box manufacturer’
In the competitive landscape of sourcing storage boxes, international B2B buyers must navigate a myriad of options to ensure they select the right manufacturer. This practical checklist provides a step-by-step approach to streamline the sourcing process, helping you identify quality suppliers that align with your business needs.
Step 1: Define Your Technical Specifications
Before reaching out to manufacturers, it’s essential to clearly outline your technical requirements. This includes the dimensions, materials, and any specific features your storage boxes need to have.
- Why it matters: Clear specifications help avoid miscommunication and ensure that suppliers understand your needs.
- What to look for: Ensure your specifications are realistic and consider industry standards to facilitate better supplier responses.
Step 2: Conduct Market Research
Explore potential manufacturers by researching the market landscape. Utilize online platforms, trade shows, and industry publications to identify key players.
- Why it matters: Understanding the market gives you insights into pricing, capabilities, and trends that can influence your purchasing decisions.
- What to look for: Seek manufacturers with a strong reputation and positive reviews, especially from businesses in your region.
Step 3: Evaluate Potential Suppliers
Before committing, it’s crucial to vet suppliers thoroughly. Request company profiles, case studies, and references from buyers in a similar industry or region.
- Why it matters: A supplier’s track record can indicate reliability and quality of service.
- What to look for: Look for consistency in product quality, timely delivery, and responsiveness to inquiries.
Step 4: Request Samples
Once you have shortlisted potential suppliers, request samples of their storage boxes. This step is vital to assess the quality and suitability of the products.
- Why it matters: Seeing and handling the product firsthand helps you make an informed decision.
- What to look for: Evaluate the materials, craftsmanship, and overall design of the samples.
Step 5: Verify Supplier Certifications
Ensure that the manufacturers you are considering hold the necessary certifications relevant to your market, such as ISO standards or environmental compliance.
- Why it matters: Certifications demonstrate a commitment to quality and regulatory adherence, which can be crucial for international trade.
- What to look for: Confirm that certifications are current and relevant to the storage box industry.
Step 6: Discuss Pricing and Terms
Engage in discussions regarding pricing structures, minimum order quantities, and payment terms.
- Why it matters: Understanding the financial aspects upfront can prevent misunderstandings later in the process.
- What to look for: Look for transparency in pricing, including any hidden costs, and ensure terms are favorable for your business.
Step 7: Establish Communication Protocols
Effective communication is key to successful supplier relationships. Establish clear communication channels and protocols for ongoing interaction.
- Why it matters: Strong communication reduces the likelihood of errors and misunderstandings.
- What to look for: Ensure that the supplier is responsive and open to regular updates and feedback.
By following this checklist, you can enhance your sourcing process for storage box manufacturers and ensure that you partner with suppliers who meet your business needs effectively.
Comprehensive Cost and Pricing Analysis for storage box manufacturer Sourcing
What Are the Key Cost Components in Storage Box Manufacturing?
When sourcing storage boxes, understanding the cost structure is essential for international B2B buyers. The main cost components include:
-
Materials: The choice of materials significantly impacts pricing. Common materials like plastic, cardboard, and metal have different cost implications. Buyers should assess the durability and cost-effectiveness of materials suitable for their specific needs.
-
Labor: Labor costs vary by region, affecting the overall pricing of storage boxes. Countries with lower labor costs may offer more competitive pricing, but this can sometimes come with trade-offs in quality.
-
Manufacturing Overhead: This includes indirect costs such as utilities, rent, and administrative expenses. Understanding the overhead structure of potential suppliers can provide insight into their pricing strategies.
-
Tooling: If custom designs are required, tooling costs can be significant. This upfront investment is essential for bespoke products but can lead to higher prices if minimum order quantities (MOQs) are not met.
-
Quality Control (QC): Investing in rigorous QC processes ensures that products meet quality standards. While this adds to the cost, it can prevent losses from defective products in the long run.
-
Logistics: Shipping and handling costs vary widely based on the destination and Incoterms agreed upon. Buyers should factor in these costs when evaluating supplier quotes.
-
Margin: The supplier’s profit margin will also be a determining factor in the final price. Understanding the market dynamics can help buyers negotiate better terms.
How Do Price Influencers Affect Storage Box Sourcing?
Several factors can influence the price of storage boxes, and savvy buyers should consider these when negotiating:
-
Volume/MOQ: Suppliers often provide better pricing for larger orders. Understanding the minimum order quantities can help buyers plan their purchases more effectively.
-
Specifications and Customization: Custom designs or specific features will typically increase costs. Buyers should evaluate whether the additional expense aligns with their business needs.
-
Materials and Quality Certifications: Higher-quality materials and certifications (like ISO or environmental standards) can increase costs. Buyers must weigh the benefits against the investment.
-
Supplier Factors: Relationships with suppliers, their market position, and financial health can influence pricing. Establishing a rapport can sometimes lead to better pricing and terms.
-
Incoterms: The chosen Incoterms (like FOB, CIF) will affect logistics costs and risks. Buyers should ensure they understand the implications of these terms on their total expenditure.
What Are Some Effective Buyer Tips for Cost-Efficiency?
For international B2B buyers, particularly in regions like Africa, South America, the Middle East, and Europe, here are some actionable tips:
-
Negotiate Terms: Engage suppliers in discussions about pricing, MOQs, and payment terms. Building a relationship can lead to favorable adjustments.
-
Focus on Total Cost of Ownership (TCO): Rather than just looking at the initial purchase price, consider the long-term costs associated with logistics, storage, and potential quality issues. This approach often reveals more cost-efficient options.
-
Understand Pricing Nuances: Be aware that pricing can vary significantly across regions due to factors like currency fluctuations, local economic conditions, and tariffs. Conducting thorough market research can help buyers navigate these complexities.
-
Request Samples: Before committing to larger orders, request samples to assess quality. This can prevent costly mistakes and ensure the product meets expectations.
Conclusion
While sourcing storage boxes, understanding the comprehensive cost and pricing structure is crucial for making informed decisions. By considering the key cost components and price influencers, and implementing strategic negotiation tactics, international B2B buyers can achieve better pricing and value in their purchases. Always remember to account for the Total Cost of Ownership, ensuring that the selected options align with long-term business goals.
Alternatives Analysis: Comparing storage box manufacturer With Other Solutions
Understanding the Importance of Alternative Solutions for Storage Needs
In the rapidly evolving landscape of logistics and supply chain management, B2B buyers must consider various storage solutions to meet their unique requirements. While storage box manufacturers offer specialized products, exploring alternative methods can uncover options that may provide better performance, cost savings, or ease of implementation. This analysis compares storage box manufacturers with two viable alternatives: pallet racking systems and portable storage containers.
Comparison of Storage Solutions
Comparison Aspect | Storage Box Manufacturer | Pallet Racking System | Portable Storage Containers |
---|---|---|---|
Performance | High durability and customization options | Excellent for maximizing vertical space | Flexible storage with easy access |
Cost | Moderate to high initial investment | High upfront costs but lower long-term expenses | Variable costs based on rental or purchase |
Ease of Implementation | Quick setup with minimal tools required | Requires professional installation | Simple to deploy and relocate |
Maintenance | Low maintenance if properly managed | Moderate; requires periodic inspections | Low; easy to clean and maintain |
Best Use Case | Ideal for retail and inventory management | Best for warehouses and distribution centers | Suitable for temporary or on-site storage |
What Are the Benefits and Drawbacks of Pallet Racking Systems?
Pallet racking systems are an efficient alternative for businesses that require extensive storage space. These systems allow for the vertical stacking of goods, which maximizes warehouse space. The primary advantage is their ability to accommodate large quantities of products while maintaining accessibility. However, the initial setup cost can be significant, and the need for professional installation may complicate the process for some businesses. Additionally, businesses must ensure compliance with safety standards, which can add to ongoing maintenance costs.
How Do Portable Storage Containers Compare?
Portable storage containers offer a flexible and convenient alternative to traditional storage solutions. They can be used for temporary storage on job sites or for long-term storage needs. The major benefit is their mobility; businesses can easily relocate them as needed without the need for heavy machinery. However, the cost can vary widely based on whether they are rented or purchased. While they require minimal maintenance, the lack of climate control in some models may not be suitable for sensitive goods.
Making the Right Choice for Your Storage Needs
When selecting the appropriate storage solution, B2B buyers should evaluate their specific operational needs, budget constraints, and the physical space available. Understanding the performance, cost implications, and maintenance requirements of each option can significantly influence the decision-making process. For businesses focused on maximizing warehouse efficiency, pallet racking may be the best fit, while those needing flexibility might find portable containers more advantageous. Ultimately, aligning the chosen solution with the company’s long-term goals and operational demands will yield the best results.
Essential Technical Properties and Trade Terminology for storage box manufacturer
What Are the Essential Technical Properties for a Storage Box Manufacturer?
When sourcing storage boxes, understanding the technical specifications is vital for B2B buyers. Here are some critical properties to consider:
1. Material Grade
The material grade defines the quality and durability of the storage boxes. Common materials include high-density polyethylene (HDPE), polypropylene (PP), and metal. Each material offers different advantages, such as resistance to chemicals, UV stability, or structural integrity. For instance, HDPE is favored for its lightweight yet strong nature, making it ideal for various applications. Buyers should assess their specific needs, such as environmental factors and intended use, to choose the appropriate material.
2. Load Capacity
Load capacity indicates the maximum weight a storage box can safely hold. This property is crucial for buyers in industries like logistics and manufacturing, where boxes may be stacked or subjected to heavy loads. Understanding load capacity ensures that the boxes can handle the intended contents without risk of damage or failure, which can lead to costly disruptions in operations.
3. Tolerance Levels
Tolerance levels refer to the permissible variation in dimensions and specifications of the storage boxes. Accurate tolerances are essential for ensuring that boxes fit correctly within designated spaces and can be efficiently stacked or transported. For example, a tolerance of +/- 1mm may be acceptable in certain applications, while others may require tighter tolerances. Buyers must specify their tolerance requirements to avoid compatibility issues.
4. Temperature Resistance
Temperature resistance indicates how well storage boxes can withstand extreme temperatures. This property is particularly relevant for companies in sectors such as food and pharmaceuticals, where products need to be stored under specific conditions. Buyers should confirm that the boxes can endure the environmental conditions they will face, ensuring the integrity of the stored items.
5. Chemical Resistance
Chemical resistance is critical for storage boxes used in industries like pharmaceuticals, agriculture, or chemical manufacturing. Certain materials are designed to withstand exposure to various chemicals without degrading or compromising safety. Buyers must understand the types of chemicals their storage boxes will encounter to select the right material, minimizing risks and ensuring compliance with safety regulations.
What Are Common Trade Terms Used in the Storage Box Manufacturing Industry?
Familiarity with industry terminology is crucial for effective communication and negotiation. Here are several key terms relevant to B2B transactions in the storage box sector:
1. OEM (Original Equipment Manufacturer)
OEM refers to companies that produce parts or equipment that may be marketed by another manufacturer. For storage box buyers, partnering with an OEM can ensure that they receive high-quality products tailored to their specifications. Understanding OEM relationships can help buyers identify reliable suppliers and ensure they are sourcing genuine products.
2. MOQ (Minimum Order Quantity)
MOQ is the smallest quantity of a product that a supplier is willing to sell. This term is significant for B2B buyers, as it affects purchasing decisions and inventory management. Understanding the MOQ allows buyers to plan their orders strategically, ensuring they meet their operational needs without overcommitting resources.
3. RFQ (Request for Quotation)
An RFQ is a document sent to suppliers asking for price quotes on specific products. For buyers in the storage box industry, issuing an RFQ helps compare pricing and terms from multiple suppliers, facilitating informed decision-making. Clearly defining specifications in an RFQ can lead to more accurate and competitive quotes.
4. Incoterms (International Commercial Terms)
Incoterms are a set of predefined international trade terms that delineate the responsibilities of buyers and sellers in shipping and delivery. Understanding these terms is essential for buyers, as they clarify who bears the risk and costs at various stages of transportation. Familiarity with Incoterms can help avoid misunderstandings and ensure smooth logistics.
5. Lead Time
Lead time refers to the amount of time it takes from placing an order to receiving the product. In the storage box industry, understanding lead times is vital for inventory planning and meeting customer demand. Buyers should communicate their timelines clearly to suppliers to ensure timely delivery and avoid disruptions in their operations.
By grasping these essential technical properties and trade terms, international B2B buyers can make informed decisions when sourcing storage boxes, ultimately enhancing their operational efficiency and product management strategies.
Navigating Market Dynamics and Sourcing Trends in the storage box manufacturer Sector
What Are the Key Market Dynamics and Trends in the Storage Box Manufacturer Sector?
The storage box manufacturing sector is experiencing significant transformations driven by global market demands and technological advancements. For international B2B buyers, particularly from regions like Africa, South America, the Middle East, and Europe, understanding these dynamics is crucial for effective sourcing strategies. One of the primary drivers is the rapid growth in e-commerce, which has heightened the need for efficient storage solutions. Businesses are increasingly seeking customized storage boxes that cater to specific logistical and operational needs.
Emerging technologies such as automation and AI are reshaping manufacturing processes, allowing for more efficient production and reduced lead times. This shift not only enhances quality but also drives down costs, making sourcing from manufacturers in different regions more competitive. For buyers, leveraging these technologies can result in more informed decision-making, ensuring they obtain the best possible products at optimal prices.
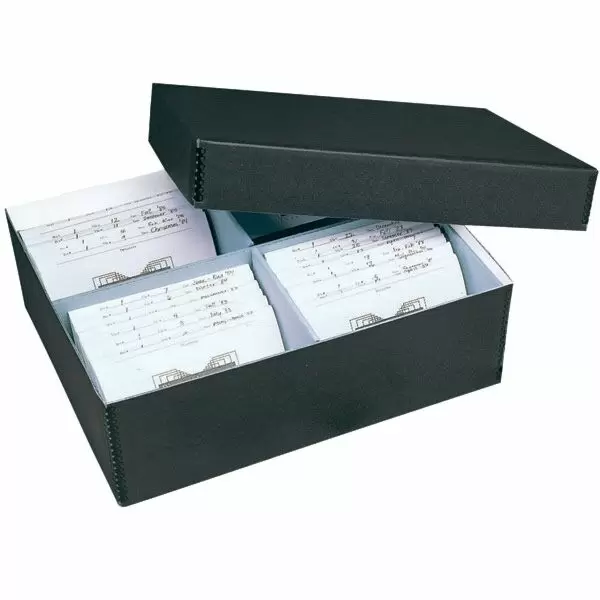
A stock image related to storage box manufacturer.
Additionally, the trend towards localization is notable. Many companies are opting to source storage boxes closer to their operational bases to reduce shipping costs and lead times. For buyers in Africa and South America, this presents an opportunity to engage with local manufacturers, fostering regional partnerships that can lead to better terms and tailored solutions.
How Does Sustainability Impact Sourcing in the Storage Box Manufacturing Sector?
Sustainability is no longer just a buzzword; it has become a core value for many businesses in the storage box manufacturing sector. B2B buyers are increasingly prioritizing environmentally responsible practices in their sourcing decisions. This includes selecting manufacturers who utilize sustainable materials, such as recycled plastics or biodegradable options, which not only minimize environmental impact but also resonate with eco-conscious consumers.
The importance of ethical supply chains cannot be overstated. Buyers must ensure that their suppliers adhere to fair labor practices and transparent sourcing methods. Certifications such as ISO 14001 (Environmental Management) and FSC (Forest Stewardship Council) are critical indicators of a manufacturer’s commitment to sustainability. These credentials signal to buyers that the products they are sourcing meet stringent environmental and ethical standards.
Incorporating sustainability into sourcing strategies can enhance brand reputation and customer loyalty, particularly in regions where consumers are increasingly demanding corporate responsibility. Buyers should actively seek partnerships with manufacturers who demonstrate a commitment to sustainable practices, as this can lead to long-term business relationships and mutual growth.
What Is the Historical Context of the Storage Box Manufacturing Sector?
The storage box manufacturing sector has evolved significantly over the past few decades. Initially dominated by traditional materials such as wood and metal, the industry has seen a substantial shift towards innovative materials like plastic and composites. This evolution was largely driven by advancements in technology and changing consumer preferences, which favored lightweight, durable, and cost-effective solutions.
As globalization expanded, manufacturers began to explore international markets, leading to increased competition and innovation. The rise of e-commerce in the late 1990s and early 2000s further accelerated the demand for versatile storage solutions, prompting manufacturers to diversify their offerings. Today, the sector is characterized by a blend of traditional craftsmanship and modern manufacturing techniques, catering to the diverse needs of B2B buyers across various industries.
Understanding this historical context is vital for buyers looking to navigate the complexities of sourcing in the storage box manufacturing sector. It provides insight into the industry’s current trends and future directions, enabling more strategic sourcing decisions.
Frequently Asked Questions (FAQs) for B2B Buyers of storage box manufacturer
-
How do I choose the right storage box manufacturer for my business needs?
Selecting the right storage box manufacturer involves assessing several factors. Start by identifying your specific requirements, such as the type of materials needed (plastic, metal, etc.), dimensions, and purpose (e.g., industrial storage, retail display). Research potential manufacturers’ reputations by reviewing customer testimonials and industry certifications. Additionally, request samples to evaluate product quality. Finally, consider their ability to meet lead times, production capacities, and after-sales support to ensure they align with your operational needs. -
What are the common payment terms offered by storage box manufacturers?
Payment terms can vary widely among storage box manufacturers. Typically, you may encounter terms like 30% upfront payment and 70% upon delivery, or full payment in advance. Some manufacturers might offer flexible financing options for larger orders. When negotiating, consider your cash flow and the manufacturer’s reliability; ensuring they have a solid reputation can mitigate risks associated with upfront payments. Always ensure that payment terms are documented clearly in the contract to avoid misunderstandings. -
What is the minimum order quantity (MOQ) for storage boxes?
Minimum order quantities (MOQs) for storage boxes vary by manufacturer and product type. While some manufacturers may have MOQs as low as 50 units, others might require orders of 500 or more, particularly for customized products. It is essential to communicate your needs clearly with potential suppliers and inquire about their MOQs. If you’re a small business, look for manufacturers who are willing to accommodate smaller orders or consider joining forces with other businesses to meet the MOQ requirements. -
How can I ensure the quality of storage boxes from a manufacturer?
To ensure product quality, start by verifying the manufacturer’s quality certifications, such as ISO 9001. Request samples of their products to evaluate materials, craftsmanship, and durability. Establish quality assurance (QA) protocols, including inspections during production and before shipment. Additionally, consider visiting the manufacturing facility if possible, or employing third-party inspection services. Engaging in transparent communication about your quality expectations will also help maintain standards throughout the production process. -
What customization options are typically available for storage boxes?
Many storage box manufacturers offer a range of customization options to meet specific business needs. These can include size, color, material, branding (such as logos), and additional features like locking mechanisms or stackability. When discussing customization, provide detailed specifications to the manufacturer and inquire about design capabilities. It’s advisable to request a prototype or mock-up before finalizing orders to ensure the product meets your expectations. -
What logistics considerations should I keep in mind when sourcing storage boxes internationally?
When sourcing storage boxes from international manufacturers, consider logistics factors like shipping costs, delivery timelines, and customs regulations. Evaluate the shipping methods available, such as air or sea freight, to balance cost and speed. Ensure that the manufacturer has experience with international shipping and can handle documentation for customs clearance. Additionally, factor in potential delays that may arise from customs processes, especially in regions with stricter regulations.
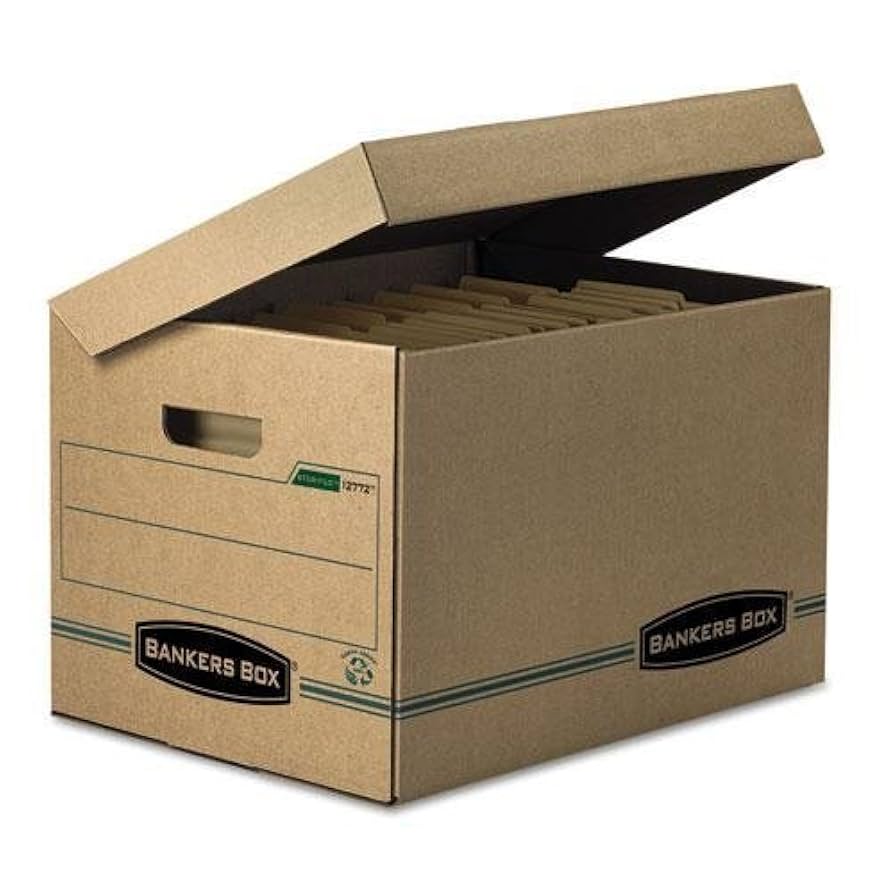
A stock image related to storage box manufacturer.
-
How do I vet potential storage box suppliers effectively?
Vetting suppliers involves a comprehensive approach. Start by researching their business history and reputation in the industry. Review customer feedback and case studies to gauge reliability and product quality. Engage in direct communication to assess their responsiveness and willingness to collaborate. Request references from other businesses, especially those in your industry, and consider visiting their facilities if feasible. Utilizing third-party services for supplier verification can also add an extra layer of assurance. -
What are the best practices for managing relationships with storage box manufacturers?
Building and maintaining strong relationships with storage box manufacturers is crucial for long-term success. Communicate openly and regularly about your needs and expectations. Establish clear contracts that outline terms, responsibilities, and quality standards. Provide constructive feedback on products and services to foster improvements. Consider scheduling regular check-ins or visits to their facilities to strengthen the partnership. Recognizing their efforts and collaborating on solutions will also help in building trust and loyalty over time.
Important Disclaimer & Terms of Use
⚠️ Important Disclaimer
The information provided in this guide, including content regarding manufacturers, technical specifications, and market analysis, is for informational and educational purposes only. It does not constitute professional procurement advice, financial advice, or legal advice.
While we have made every effort to ensure the accuracy and timeliness of the information, we are not responsible for any errors, omissions, or outdated information. Market conditions, company details, and technical standards are subject to change.
B2B buyers must conduct their own independent and thorough due diligence before making any purchasing decisions. This includes contacting suppliers directly, verifying certifications, requesting samples, and seeking professional consultation. The risk of relying on any information in this guide is borne solely by the reader.
Strategic Sourcing Conclusion and Outlook for storage box manufacturer
As international B2B buyers navigate the competitive landscape of storage solutions, the importance of strategic sourcing cannot be overstated. By prioritizing relationships with reliable manufacturers, businesses can secure high-quality storage boxes tailored to their specific needs, ultimately enhancing operational efficiency and reducing costs. Key takeaways include the necessity of understanding market trends, evaluating supplier capabilities, and leveraging technological advancements in logistics and production.
What should buyers consider for future procurement strategies? Looking ahead, the focus on sustainability and innovation will shape the storage box manufacturing industry. Buyers from Africa, South America, the Middle East, and Europe, including regions like Argentina and Spain, should seek manufacturers who not only meet current demand but also align with eco-friendly practices and smart manufacturing processes.
In conclusion, embracing a strategic sourcing approach will empower businesses to thrive in an ever-evolving market. Engage with potential partners today, assess their offerings, and pave the way for a successful procurement journey that meets your organization’s unique storage needs while fostering long-term growth.