Cut Costs with a Reliable Card Holder Manufacturer (2025)
Introduction: Navigating the Global Market for card holder manufacturer
In today’s competitive landscape, sourcing high-quality card holders can be a significant challenge for international B2B buyers. With a multitude of manufacturers globally, identifying reliable suppliers that meet your specific requirements in design, functionality, and pricing is crucial. This comprehensive guide will delve into the diverse types of card holders available, their various applications across industries, and essential strategies for vetting suppliers effectively.
International buyers from Africa, South America, the Middle East, and Europe, including key markets like Brazil and Kenya, will find actionable insights tailored to their unique needs. By understanding the nuances of the card holder manufacturing sector, you can make informed purchasing decisions that enhance your business operations.
Whether you’re looking to bulk order eco-friendly card holders or premium leather options, this guide covers essential factors such as cost considerations, material quality, and manufacturing standards. Additionally, we will provide practical tips on negotiating terms and establishing long-term partnerships with suppliers. Empower yourself with the knowledge to navigate the global market confidently and secure the best products for your business needs.
Understanding card holder manufacturer Types and Variations
Type Name | Key Distinguishing Features | Primary B2B Applications | Brief Pros & Cons for Buyers |
---|---|---|---|
Plastic Card Holders | Lightweight, customizable, and water-resistant. | Retail, events, and loyalty programs. | Pros: Cost-effective, versatile. Cons: Less durable than other materials. |
Metal Card Holders | Premium finish, durable, and often RFID-blocking. | Corporate gifts, high-end retail. | Pros: Stylish, long-lasting. Cons: Higher cost, heavier. |
Eco-Friendly Card Holders | Made from recycled materials or biodegradable options. | Sustainability-focused businesses. | Pros: Environmentally friendly, unique appeal. Cons: Limited design options. |
Leather Card Holders | Luxurious texture, durable, and professional appearance. | Financial services, corporate branding. | Pros: Elegant, durable. Cons: More expensive, requires care. |
Custom Printed Card Holders | Personalized designs, logos, and branding options. | Marketing, trade shows, and promotions. | Pros: Brand visibility, unique. Cons: Higher minimum order quantities. |
What Are Plastic Card Holders and Their B2B Relevance?
Plastic card holders are lightweight and highly customizable, making them ideal for various applications such as retail, events, and loyalty programs. They can be designed to hold multiple cards and are often water-resistant, which adds to their practicality. When purchasing, B2B buyers should consider the cost-effectiveness and versatility of plastic holders, as they can be produced in bulk at a lower price point. However, their durability may not match that of other materials, which could be a consideration for long-term use.
How Do Metal Card Holders Stand Out for Corporate Use?
Metal card holders offer a premium finish that appeals to businesses aiming to project a sophisticated image. Their durability and often RFID-blocking capabilities make them suitable for corporate gifts or high-end retail environments. B2B buyers should weigh the stylish appearance and longevity against the higher cost and increased weight. These holders are particularly effective for businesses looking to enhance their branding and customer experience through quality presentation.
Why Choose Eco-Friendly Card Holders for Your Business?
Eco-friendly card holders are made from recycled or biodegradable materials, appealing to businesses focused on sustainability. They are suitable for companies wanting to showcase their commitment to environmental responsibility. When considering these holders, buyers should evaluate the unique appeal and marketing advantages they offer. However, the limited design options may require compromises in branding or aesthetics.
What Are the Benefits of Leather Card Holders in Professional Settings?
Leather card holders are known for their luxurious texture and professional appearance, making them ideal for financial services and corporate branding. Their durability ensures they can withstand regular use, providing excellent value over time. B2B buyers should consider the elegance and longevity of leather options, although the higher price point and maintenance requirements may deter some businesses seeking more economical solutions.
How Do Custom Printed Card Holders Enhance Brand Visibility?
Custom printed card holders allow businesses to personalize designs, logos, and branding elements, making them highly effective for marketing, trade shows, and promotional events. They offer excellent brand visibility and can help businesses stand out in competitive markets. However, buyers should be aware of the higher minimum order quantities often required for custom designs, which could impact initial investment decisions.
Related Video: LUXURY MENS WALLET REVIEW | Card Holder, Wallets, Pocket Organiser + Long Wallets
Key Industrial Applications of card holder manufacturer
Industry/Sector | Specific Application of card holder manufacturer | Value/Benefit for the Business | Key Sourcing Considerations for this Application |
---|---|---|---|
Financial Services | Credit card and ID card holders | Enhances customer experience and brand visibility | Material quality, security features, and customization options |
Retail and E-commerce | Loyalty and membership card holders | Increases customer retention and promotes brand loyalty | Design flexibility, durability, and compatibility with existing systems |
Hospitality and Tourism | Room key card holders | Improves guest convenience and enhances branding | Weather resistance, aesthetics, and secure locking mechanisms |
Corporate and Business Services | Employee ID card holders | Facilitates access control and improves security | Customization options for branding, material durability, and bulk purchasing discounts |
Events and Conferences | Event badge holders | Streamlines attendee management and enhances branding | Lightweight materials, customization for different events, and quick turnaround time |
How Are Card Holders Used in Financial Services?
In the financial services sector, card holder manufacturers provide specialized holders for credit and debit cards, as well as identification cards. These holders not only protect cards from wear and tear but also enhance the customer experience by offering a polished presentation. International buyers, particularly from regions like Africa and South America, should prioritize sourcing holders made from durable materials that comply with local regulations regarding security and data protection. Customization options, such as branding and color schemes, can further enhance customer loyalty and brand visibility.
What Role Do Card Holders Play in Retail and E-commerce?
In retail and e-commerce, card holders are often used for loyalty and membership cards. These holders serve as a tangible representation of a customer’s loyalty to a brand, promoting repeat business. Buyers in Europe and the Middle East should consider the design flexibility and durability of the card holders, ensuring they align with the brand’s aesthetic. Additionally, compatibility with existing loyalty programs is crucial for seamless integration and customer satisfaction.
How Do Hospitality Card Holders Enhance Guest Experience?
For the hospitality and tourism industry, room key card holders are essential. They not only protect the key cards but also serve as a branding tool that enhances the guest experience. International buyers from regions like Africa and the Middle East should focus on sourcing holders that are weather-resistant and aesthetically pleasing, as these factors significantly influence guest perception. Security features, such as tamper-proof designs, are also vital to ensure guest safety.
What Benefits Do Corporate Card Holders Offer?
In corporate environments, employee ID card holders play a critical role in access control and security management. These holders help identify employees while safeguarding sensitive information. B2B buyers from South America and Europe should emphasize customization options that reflect the company’s branding. Furthermore, sourcing durable materials that can withstand daily use is essential, as well as negotiating bulk purchasing discounts to reduce costs.
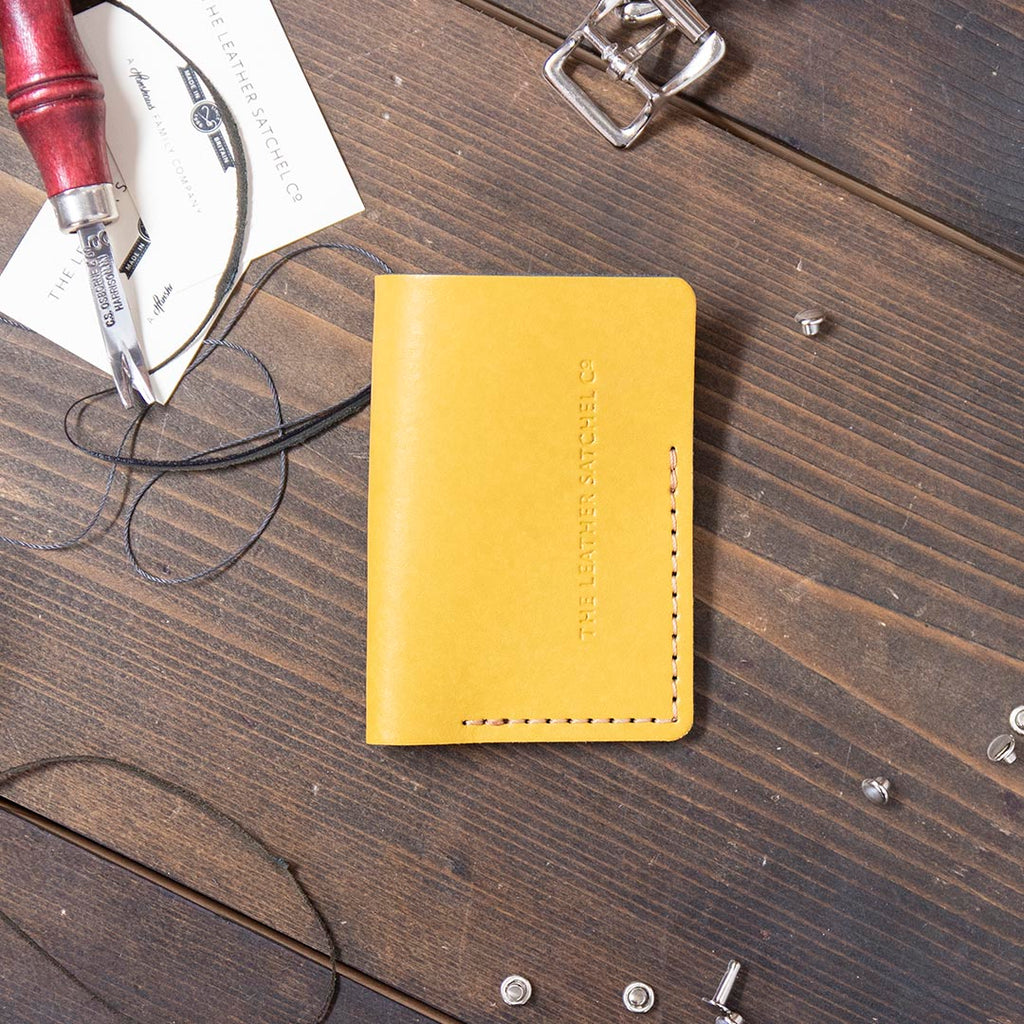
A stock image related to card holder manufacturer.
How Do Event Badge Holders Improve Event Management?
Event badge holders are crucial for managing attendees at conferences and events. They streamline the check-in process and enhance branding visibility for sponsors. Buyers from Africa and the Middle East should prioritize lightweight materials that are easy to distribute and customize for different events. Quick turnaround times are also a key consideration, as event timelines can be tight. Ensuring that the holders can accommodate various badge sizes and designs is essential for effective management.
Related Video: LABORATORY APPARATUS AND THEIR USES
3 Common User Pain Points for ‘card holder manufacturer’ & Their Solutions
Scenario 1: Sourcing Quality Materials for Durable Card Holders
The Problem: International B2B buyers often struggle to find a card holder manufacturer that uses high-quality, durable materials. This is particularly important for businesses in regions like Africa and South America, where environmental factors can degrade products quickly. Buyers may face challenges in verifying the material quality and sustainability of the card holders, leading to potential dissatisfaction and increased return rates.
The Solution: To address this issue, buyers should conduct thorough research on potential manufacturers. Start by requesting material samples and certifications that indicate the quality and sustainability of the materials used. Look for manufacturers who provide detailed specifications on their materials and production processes. Additionally, consider visiting manufacturing facilities, if feasible, or utilizing third-party audits to assess quality control measures. Establishing clear communication regarding your material requirements upfront will ensure the manufacturer understands your needs, ultimately leading to higher-quality products that meet your expectations.
Scenario 2: Navigating Language Barriers and Cultural Differences
The Problem: When dealing with card holder manufacturers in different regions, language barriers and cultural differences can pose significant challenges for international buyers. This can lead to miscommunication regarding order specifications, timelines, and payment terms, ultimately affecting the overall purchasing experience.
The Solution: To mitigate these risks, buyers should prioritize manufacturers that have experience working with international clients and demonstrate cultural competency. Engage in discussions with potential suppliers to assess their English proficiency and willingness to accommodate language preferences. Utilizing translation services or hiring a local intermediary can also facilitate smoother communication. Moreover, setting up regular check-ins and using visual aids or prototypes can help clarify expectations and reduce misunderstandings. Building a strong rapport with the manufacturer will foster better collaboration and enhance the overall experience.
Scenario 3: Ensuring Timely Delivery Amid Supply Chain Disruptions
The Problem: B2B buyers often face the challenge of supply chain disruptions, which can lead to delays in the delivery of card holders. This is especially critical for businesses that rely on timely inventory replenishment, such as retail stores in Europe or promotional companies in the Middle East. Delayed shipments can result in lost sales opportunities and strained customer relationships.
The Solution: To combat potential supply chain issues, buyers should develop a proactive approach to managing their orders. Start by establishing clear timelines with manufacturers, including production lead times and shipping schedules. Request regular updates throughout the production process to monitor progress and anticipate any potential delays. Additionally, consider diversifying your supplier base to reduce reliance on a single manufacturer, which can help mitigate risks associated with regional disruptions. Implementing inventory management software can also help track stock levels and forecast demand more accurately, ensuring that you have the right amount of product on hand when needed. By proactively managing your supply chain, you can maintain a steady flow of card holders and meet your business needs effectively.
Strategic Material Selection Guide for card holder manufacturer
When selecting materials for card holders, manufacturers must consider various factors that affect performance, durability, and cost. Below is an analysis of four common materials used in card holder manufacturing, focusing on their properties, advantages, disadvantages, and specific considerations for international B2B buyers.
What Are the Key Properties of Polypropylene (PP) for Card Holders?
Polypropylene (PP) is a thermoplastic polymer known for its versatility and durability. It boasts a temperature resistance of up to 100°C (212°F) and excellent chemical resistance, making it suitable for various environments. Its lightweight nature contributes to reduced shipping costs and ease of handling.
Pros & Cons:
The primary advantage of polypropylene is its cost-effectiveness and resistance to impact and fatigue. However, it can be less durable than other materials in extreme conditions and may not provide the same aesthetic appeal, limiting its use in high-end markets.
Impact on Application:
Polypropylene is compatible with various printing techniques, allowing for branding and customization. However, it may not be suitable for applications requiring high-temperature resistance, such as in automotive or industrial settings.
Considerations for International Buyers:
B2B buyers from regions like Africa and South America should ensure compliance with local regulations regarding plastic use. Standards such as ASTM D638 for tensile properties may be relevant.
How Does PVC Compare as a Material for Card Holders?
Polyvinyl Chloride (PVC) is another popular choice for card holders due to its durability and flexibility. It can withstand temperatures from -15°C to 60°C (5°F to 140°F) and offers good resistance to moisture and chemicals.
Pros & Cons:
PVC is highly durable and can be manufactured in various colors and finishes, making it visually appealing. However, it can be more expensive than polypropylene and may pose environmental concerns due to its production process and disposal challenges.
Impact on Application:
PVC is ideal for applications requiring waterproofing and resistance to wear and tear, such as in travel-related products. Its compatibility with various printing methods also enhances branding opportunities.
Considerations for International Buyers:
Buyers in Europe and the Middle East should consider compliance with REACH regulations regarding chemical safety in materials. Standards such as DIN EN 71 for toy safety may also apply if the card holder is marketed to children.
What Are the Advantages of Using Leather in Card Holder Manufacturing?
Leather is a traditional material known for its premium look and feel. It offers excellent durability, withstanding wear and tear over time, and can be treated for additional water resistance.
Pros & Cons:
The main advantage of leather is its aesthetic appeal and perceived value, making it suitable for luxury card holders. However, it is significantly more expensive than synthetic materials and requires more complex manufacturing processes.
Impact on Application:
Leather is ideal for high-end markets and products that emphasize craftsmanship and quality. However, it may not be suitable for environments where moisture or extreme temperatures are prevalent.
Considerations for International Buyers:
B2B buyers should be aware of sourcing regulations regarding animal products, especially in Europe, where animal welfare standards are stringent. Certifications like the Leather Working Group (LWG) can enhance credibility.
Why Choose Metal for Card Holders?
Metal, particularly aluminum or stainless steel, is increasingly popular for card holders due to its durability and modern aesthetic. Metals can withstand extreme temperatures and are resistant to corrosion.
Pros & Cons:
The key advantage of metal is its strength and longevity, making it ideal for high-use applications. However, it can be more expensive and heavier than other materials, potentially increasing shipping costs.
Impact on Application:
Metal card holders are suitable for premium markets and tech-savvy consumers. They also offer unique customization options through engraving or anodizing.
Considerations for International Buyers:
Buyers should consider international shipping regulations for metal products, especially in regions with strict import laws. Compliance with standards like ASTM B117 for corrosion resistance may also be necessary.
Summary Table of Material Selection
Material | Typical Use Case for Card Holder Manufacturer | Key Advantage | Key Disadvantage/Limitation | Relative Cost (Low/Med/High) |
---|---|---|---|---|
Polypropylene | General-purpose card holders | Cost-effective and lightweight | Less durable under extreme conditions | Low |
PVC | Waterproof card holders | Highly durable and flexible | Environmental concerns | Medium |
Leather | Luxury card holders | Premium aesthetic and durability | High cost and complex manufacturing | High |
Metal | Premium and tech-savvy card holders | Strength and longevity | Higher cost and weight | High |
This analysis provides international B2B buyers with actionable insights into material selection for card holders, helping them make informed decisions based on performance, cost, and compliance considerations.
In-depth Look: Manufacturing Processes and Quality Assurance for card holder manufacturer
What Are the Main Manufacturing Processes for Card Holders?
The manufacturing of card holders typically involves several key stages: material preparation, forming, assembly, and finishing. Each stage is crucial for ensuring that the final product meets both aesthetic and functional standards.
How Is Material Prepared for Card Holders?
The process begins with the selection of materials, which can vary from leather and synthetic fabrics to metals and plastics. High-quality materials are essential for durability and appearance. Material preparation involves cutting, treating, and sometimes dyeing the materials to achieve the desired color and texture. For instance, leather might undergo tanning, while synthetic materials may be coated for water resistance.
What Forming Techniques Are Used in Card Holder Production?
Once the materials are prepared, they move to the forming stage. Techniques vary based on the design and material used. Common methods include:
- Die Cutting: This technique allows for precise shapes and sizes, ensuring uniformity across batches.
- Stitching and Bonding: For leather card holders, stitching is often employed, whereas synthetic materials may use adhesives or heat sealing.
- Molding: In cases where plastic is used, injection molding can create intricate designs and textures.
How Is Assembly Conducted in Card Holder Manufacturing?
The assembly stage involves bringing together the formed components. This may include adding pockets, fasteners, and branding elements. Assembly can be manual or automated, depending on the scale of production and complexity of the design. Quality control during assembly is vital to ensure that all components fit together seamlessly and function as intended.
What Finishing Processes Are Important for Card Holders?
Finishing touches are what set a high-quality card holder apart. This stage might include polishing, applying protective coatings, or adding embellishments such as embossing or screen printing. Proper finishing enhances the durability and aesthetic appeal of the product, making it more attractive to potential buyers.
What Quality Assurance Standards Are Relevant for Card Holder Manufacturers?
Quality assurance (QA) is paramount in the manufacturing process, especially for B2B buyers who seek reliable suppliers. Various international and industry-specific standards guide QA efforts.
How Do International Standards Like ISO 9001 Impact Quality Assurance?
ISO 9001 is a widely recognized standard that focuses on quality management systems (QMS). Manufacturers aiming for ISO certification must demonstrate their ability to consistently provide products that meet customer and regulatory requirements. This certification is crucial for international B2B transactions, as it assures buyers of the manufacturer‘s commitment to quality.
What Are Industry-Specific Certifications to Look For?
In addition to ISO 9001, other certifications may be relevant depending on the target market. For instance:
- CE Marking: Essential for products sold within the European Economic Area, indicating compliance with health, safety, and environmental protection standards.
- API Standards: Relevant for card holders that might be used in specialized applications, ensuring they meet specific performance criteria.
What Are the Key Quality Control Checkpoints in Card Holder Manufacturing?
Quality control in card holder manufacturing typically includes several checkpoints throughout the production process:
- Incoming Quality Control (IQC): This initial checkpoint verifies the quality of raw materials before they enter the production line. It ensures that only high-grade materials are used, reducing defects later on.
- In-Process Quality Control (IPQC): During manufacturing, continuous monitoring is essential to catch any deviations from quality standards. This might involve visual inspections, dimensional checks, and adherence to specified processes.
- Final Quality Control (FQC): Before products are packaged and shipped, a thorough inspection is conducted. This includes checking the functionality, aesthetics, and overall quality of the finished card holders.
What Common Testing Methods Are Employed to Ensure Quality?
Testing methods vary but commonly include:
- Durability Testing: Ensures the card holder can withstand regular use, including stress tests and abrasion resistance.
- Colorfastness Testing: Important for dyed materials, ensuring colors do not fade with exposure to light or moisture.
- Functional Testing: Verifying that all pockets and closures operate as intended.
How Can B2B Buyers Verify Supplier Quality Control Practices?
B2B buyers must take proactive steps to ensure their suppliers maintain high-quality standards. Here are some strategies:
What Are the Benefits of Conducting Supplier Audits?
Conducting on-site audits allows buyers to assess the manufacturing processes and quality control measures firsthand. This can help identify potential issues and ensure that the supplier adheres to international standards.
How Can Buyers Request Quality Reports?
Buyers should request detailed quality reports that outline the manufacturing process, quality control measures, and testing results. This documentation provides transparency and reassurance regarding the supplier’s capabilities.
Why Should B2B Buyers Consider Third-Party Inspections?
Engaging third-party inspection services can add an extra layer of assurance. These independent inspections verify that the products meet the specified quality standards before shipment, helping to mitigate risks associated with international procurement.
What Quality Control Nuances Should International B2B Buyers Be Aware Of?
For buyers from Africa, South America, the Middle East, and Europe, understanding the nuances of quality control is critical. Factors such as local regulations, cultural expectations regarding quality, and logistical considerations can all impact the procurement process.
How Do Regional Standards Influence Quality Assurance?
Different regions may have varying standards and expectations for product quality. For instance, European buyers might prioritize CE marking, while African buyers may focus more on durability and functionality in local conditions. Understanding these regional nuances can help buyers make informed decisions.
Conclusion
In summary, a thorough understanding of the manufacturing processes and quality assurance practices is essential for international B2B buyers looking to source card holders. By focusing on material preparation, forming, assembly, finishing, and adhering to relevant quality standards, buyers can ensure they partner with reliable manufacturers that meet their expectations. Engaging in audits, requesting reports, and considering third-party inspections are all effective strategies to verify supplier quality and ensure a successful procurement process.
Practical Sourcing Guide: A Step-by-Step Checklist for ‘card holder manufacturer’
In today’s global marketplace, procuring card holders from manufacturers requires a strategic approach. This guide outlines a step-by-step checklist designed specifically for B2B buyers from regions such as Africa, South America, the Middle East, and Europe. By following these actionable insights, you can ensure a successful sourcing experience.
Step 1: Define Your Technical Specifications
Before initiating your search, clearly outline your technical requirements for card holders. This includes materials, dimensions, color options, and any special features like RFID blocking. Having precise specifications helps suppliers understand your needs, reducing miscommunication and ensuring product compatibility with your market.
Step 2: Conduct Market Research on Suppliers
Research potential suppliers to identify those who specialize in card holder manufacturing. Use industry directories, trade shows, and online platforms like Alibaba or ThomasNet. Pay close attention to suppliers with a strong presence in your target regions, as they are more likely to understand local demands and compliance requirements.
Step 3: Evaluate Supplier Credentials and Certifications
When considering suppliers, verify their credentials and certifications. Look for ISO certifications, quality management systems, and compliance with international standards. These certifications not only demonstrate a commitment to quality but also ensure that the supplier adheres to ethical manufacturing practices, which is particularly important in regions with strict regulations.
Step 4: Request Samples for Quality Assessment
Before placing a bulk order, always request product samples. This step allows you to evaluate the quality, craftsmanship, and materials used in the card holders. When assessing samples, consider the durability and aesthetic appeal, as these factors will impact your brand’s reputation and customer satisfaction.
Step 5: Analyze Pricing and Payment Terms
Obtain detailed pricing information from multiple suppliers, including shipping costs and potential discounts for bulk orders. Compare these costs while considering the total cost of ownership, which includes shipping, duties, and handling fees. Additionally, clarify payment terms to avoid any misunderstandings later in the procurement process.
Step 6: Assess Production and Delivery Capabilities
Inquire about the supplier’s production capacity and lead times. Understanding their ability to meet your order quantities and timelines is critical, especially if you are operating within tight deadlines. Check if they have contingency plans for delays, which can help mitigate risks associated with international shipping.
Step 7: Establish Clear Communication Channels
Effective communication is essential throughout the sourcing process. Ensure you have a dedicated contact person at the supplier’s company who can provide updates and address concerns. Utilize project management tools or communication platforms to maintain transparency and keep all stakeholders informed.
By following this practical checklist, international B2B buyers can streamline the sourcing process for card holders, ensuring they partner with the right manufacturers who meet their specific needs and standards.
Comprehensive Cost and Pricing Analysis for card holder manufacturer Sourcing
What Are the Key Cost Components in Card Holder Manufacturing?
When sourcing card holders, understanding the cost structure is vital for international buyers. The primary components that contribute to the overall cost include:
-
Materials: The choice of materials significantly impacts pricing. High-quality leather, durable plastics, or eco-friendly materials will vary in cost. Buyers should evaluate the sustainability of materials, especially if targeting markets in Europe or the Middle East, where eco-conscious sourcing is increasingly valued.
-
Labor: Labor costs can fluctuate based on geographic location. For instance, manufacturers in regions with lower labor costs, such as parts of South America or Africa, may offer competitive pricing. However, consider the skill level and craftsmanship required for high-quality production, which can influence labor expenses.
-
Manufacturing Overhead: This includes costs associated with facilities, utilities, and equipment maintenance. Understanding a manufacturer’s overhead can provide insights into their pricing strategy and overall efficiency.
-
Tooling: Initial tooling costs for creating molds or custom designs can be significant, especially for unique specifications. Buyers should inquire about these costs upfront, particularly if they require bespoke designs or features.
-
Quality Control (QC): Implementing stringent QC processes ensures that the products meet specified standards. While this may increase costs, it can prevent larger expenses related to returns or defects.
-
Logistics: Shipping costs can vary dramatically based on distance, shipping method, and volume. International buyers should consider Incoterms to clarify responsibilities regarding freight, insurance, and customs clearance.
-
Margin: Manufacturers typically include a profit margin in their pricing. Understanding market benchmarks for margins can help buyers negotiate better deals.
How Do Price Influencers Affect Card Holder Sourcing?
Several factors influence the pricing of card holders, including:
-
Volume and Minimum Order Quantity (MOQ): Higher order volumes often lead to discounts, which can significantly reduce the per-unit price. Buyers should assess their purchasing capacity and negotiate MOQs that align with their needs.
-
Specifications and Customization: Custom designs or specific features can increase production costs. Clear communication about requirements can help manufacturers provide accurate quotes.
-
Material Quality and Certifications: Premium materials and certifications (e.g., ISO, eco-labels) can elevate costs but may also enhance product value. Buyers should weigh the benefits of these certifications against their budget constraints.
-
Supplier Factors: The reputation and reliability of the supplier can impact pricing. Established manufacturers may charge more but offer better quality and service.
-
Incoterms: Understanding the terms of shipping (like FOB or CIF) is essential. It determines who bears the cost and risk during transit, which can affect the overall pricing.
What Are Some Buyer Tips for Cost Efficiency in Card Holder Sourcing?
To maximize value and minimize costs, international buyers should consider the following strategies:
-
Negotiate Wisely: Engage in open discussions about pricing and be prepared to walk away if terms are not favorable. Use competitive quotes from other manufacturers as leverage.
-
Evaluate Total Cost of Ownership (TCO): TCO encompasses all costs associated with acquiring and using the product, including logistics, maintenance, and potential wastage. Buyers should assess this to make informed decisions.
-
Understand Pricing Nuances: Pricing can vary based on regional market trends. For example, buyers in Africa and South America may find different pricing structures compared to those in Europe due to currency fluctuations and local demand.
-
Stay Informed About Market Trends: Keeping abreast of changes in material costs, labor rates, and global supply chain dynamics can help buyers anticipate pricing shifts.
Disclaimer on Indicative Prices
Prices for card holders can fluctuate based on market conditions, material availability, and supplier negotiations. Buyers are encouraged to conduct thorough research and obtain multiple quotes to ensure competitive pricing.
Alternatives Analysis: Comparing card holder manufacturer With Other Solutions
When considering solutions for cardholder needs in the B2B space, it is essential to evaluate various alternatives that can fulfill similar objectives. While traditional card holder manufacturers offer specific benefits, alternative solutions may provide unique advantages based on your business requirements. This analysis will compare card holder manufacturers with two notable alternatives: digital wallet solutions and RFID-enabled card holders.
Comparison Table
Comparison Aspect | Card Holder Manufacturer | Digital Wallet Solutions | RFID-Enabled Card Holders |
---|---|---|---|
Performance | High durability and design | Instant access to cards, but dependent on device | Secure and easy scanning |
Cost | Varies by materials and design | Usually low or no cost (app-based) | Higher initial investment |
Ease of Implementation | Simple ordering process | Requires smartphone and app installation | May need additional training |
Maintenance | Minimal, long-lasting | Regular updates needed for app functionality | Low, but requires device compatibility |
Best Use Case | Physical cards for events or corporate branding | Contactless payments and loyalty programs | Secure access and payment systems |
What Are the Benefits and Drawbacks of Digital Wallet Solutions?
Digital wallet solutions have gained immense popularity due to their convenience and efficiency. These applications allow users to store multiple payment methods and loyalty cards on their smartphones, facilitating quick access and contactless payments. The primary advantage of digital wallets is their low cost, as many apps are free to download and use. However, reliance on technology can be a drawback, as users must have a compatible device and may face issues with app updates or software glitches. Furthermore, security concerns regarding data breaches can deter some users from fully adopting this solution.
How Do RFID-Enabled Card Holders Enhance Security and Usability?
RFID-enabled card holders provide a modern twist on traditional card storage by incorporating radio-frequency identification technology. This allows for easy scanning and secure access, ideal for environments like corporate offices or events where quick identification is necessary. The main advantage of RFID card holders is their ability to enhance security through encrypted communication, reducing the risk of unauthorized access. However, they typically require a higher upfront investment compared to standard card holders, and businesses may need to invest time in training staff on how to use the technology effectively.
Conclusion: How Can B2B Buyers Choose the Right Solution for Their Needs?
Selecting the right solution for cardholder needs involves evaluating your business objectives, budget constraints, and the technological proficiency of your team. If your organization values physical branding and durability, partnering with a card holder manufacturer might be the best route. However, if your focus is on enhancing customer experience through convenience and speed, digital wallet solutions could be a compelling alternative. For businesses prioritizing security and streamlined access, RFID-enabled card holders offer a robust solution. Ultimately, the choice depends on the specific requirements of your operations and the user experience you wish to provide.
Essential Technical Properties and Trade Terminology for card holder manufacturer
What Are the Essential Technical Properties for Card Holder Manufacturing?
When engaging with card holder manufacturers, understanding the technical properties of the products is crucial. This knowledge not only aids in making informed purchasing decisions but also ensures that the products meet the required standards for functionality and durability. Here are some key technical specifications:
-
Material Grade
The material used in card holders can significantly affect their durability and aesthetic appeal. Common materials include leather, plastic, and metal, each offering distinct advantages. For instance, leather provides a premium feel and longevity, while plastic is lightweight and cost-effective. B2B buyers should evaluate material grades to ensure they align with their brand image and customer expectations. -
Tolerance
Tolerance refers to the allowable deviation in dimensions during manufacturing. For card holders, maintaining precise tolerances is vital to ensure that cards fit snugly without being difficult to insert or remove. A tight tolerance can enhance the perceived quality of the product, making it essential for manufacturers to adhere to specified standards. -
Finish and Texture
The finish of a card holder, whether matte, glossy, or textured, influences not only its appearance but also its grip and user experience. Textured surfaces may prevent slipping, while glossy finishes can enhance visual appeal. Buyers should consider the finish based on the target market’s preferences and functional requirements. -
Capacity
The capacity of a card holder refers to how many cards it can accommodate without compromising usability. It’s important for B2B buyers to specify their needs—whether they require a slim design for minimalism or a bulkier option for practicality—to ensure customer satisfaction. -
Weight
The weight of a card holder impacts its portability and user experience. Lighter materials may appeal to consumers who prioritize convenience, while heavier materials might be preferred for their robust feel. Buyers should analyze the weight in conjunction with the intended use of the card holder.
What Are the Common Trade Terms in Card Holder Manufacturing?
Understanding trade terminology is essential for navigating negotiations and contracts within the card holder manufacturing industry. Here are several key terms:
-
OEM (Original Equipment Manufacturer)
This term refers to companies that produce components or products that are then sold under another company’s brand. B2B buyers often work with OEMs to create custom card holders that align with their branding and design requirements. -
MOQ (Minimum Order Quantity)
MOQ indicates the smallest number of units a supplier is willing to sell. Knowing the MOQ is essential for buyers to determine if a supplier can meet their needs without incurring excess costs. It also helps in planning inventory and managing cash flow effectively. -
RFQ (Request for Quotation)
An RFQ is a formal document sent by buyers to suppliers requesting pricing and other details for specific products. In the context of card holders, issuing an RFQ helps buyers gather competitive quotes and evaluate potential suppliers based on price and service offerings. -
Incoterms (International Commercial Terms)
These are standardized terms that define the responsibilities of buyers and sellers regarding shipping, risk, and costs. Familiarity with Incoterms is critical for international B2B buyers to avoid misunderstandings related to delivery and payment terms. -
Lead Time
Lead time refers to the duration from placing an order to receiving the finished product. Understanding lead times helps buyers manage their supply chain efficiently and ensures they can meet market demand without delays. -
Customization
Customization involves tailoring products to meet specific buyer requirements, such as size, color, or branding. Offering customization options can be a significant selling point, allowing businesses to differentiate themselves in competitive markets.
By grasping these technical properties and trade terms, international B2B buyers can enhance their purchasing strategies and establish strong partnerships with card holder manufacturers.
Navigating Market Dynamics and Sourcing Trends in the card holder manufacturer Sector
What Are the Current Market Dynamics and Key Trends in the Card Holder Manufacturing Sector?
The card holder manufacturing sector is witnessing a transformative phase driven by several global factors. Increasing consumer demand for personalized and innovative designs is reshaping product offerings, while the rise of e-commerce platforms is facilitating easier access for international B2B buyers. Notably, the integration of advanced technologies such as 3D printing and artificial intelligence is streamlining production processes, enhancing customization options, and reducing lead times. These technological advancements are particularly relevant for buyers in regions like Africa and South America, where rapid urbanization is driving a surge in retail and e-commerce activities.
Emerging sourcing trends are heavily influenced by the need for greater supply chain resilience. B2B buyers are increasingly looking for manufacturers that can offer flexible sourcing options and diversified supply channels, especially in light of recent disruptions. Additionally, the focus on quality assurance and compliance with international standards is paramount. Buyers from Europe and the Middle East, for example, are particularly discerning about product certifications and quality guarantees when selecting card holder manufacturers.
Moreover, sustainability is becoming a crucial consideration in the decision-making process. Buyers are not only interested in the aesthetic and functional aspects of card holders but are also prioritizing eco-friendly materials and ethical manufacturing practices. This shift is prompting manufacturers to adopt greener processes and materials, making the sector more responsive to changing consumer preferences.
How Is Sustainability and Ethical Sourcing Impacting the Card Holder Manufacturing Sector?
Sustainability and ethical sourcing are no longer optional in the card holder manufacturing sector; they are essential components that influence purchasing decisions. The environmental impact of manufacturing practices is under scrutiny, prompting B2B buyers to seek suppliers committed to reducing their carbon footprint. This includes the use of sustainable materials such as recycled plastics, organic cotton, and biodegradable alternatives, which resonate well with environmentally conscious consumers.
Additionally, the importance of ethical supply chains is gaining traction. Buyers are increasingly demanding transparency in sourcing practices, ensuring that labor standards are met and that workers are treated fairly throughout the production process. Certifications such as Fair Trade, GOTS (Global Organic Textile Standard), and FSC (Forest Stewardship Council) are becoming significant indicators of a manufacturer’s commitment to ethical practices.
For international buyers, particularly those in Africa and South America, aligning with manufacturers that prioritize sustainability can enhance brand reputation and customer loyalty. By investing in partnerships with ethically responsible suppliers, businesses can differentiate themselves in a competitive marketplace while contributing positively to the environment and society.
How Has the Card Holder Manufacturing Sector Evolved Over Time?
The evolution of the card holder manufacturing sector reflects broader trends in consumer behavior and technology. Initially, card holders were utilitarian products made from basic materials, often lacking in style and functionality. Over the years, as consumer preferences shifted towards personalization and aesthetics, manufacturers began to innovate with various materials and designs, including leather, fabric, and synthetic options.
The introduction of digital technologies has further revolutionized the sector. The ability to create custom designs using computer-aided design (CAD) software and produce them efficiently with laser cutting and 3D printing has opened new avenues for product development. This evolution has not only allowed manufacturers to cater to diverse market needs but has also enabled them to respond rapidly to changing trends and consumer demands.
As the sector continues to grow, B2B buyers can expect further advancements in both product offerings and manufacturing processes. Embracing these changes will be crucial for businesses looking to stay competitive and meet the evolving needs of their customers.
Frequently Asked Questions (FAQs) for B2B Buyers of card holder manufacturer
-
How do I select the right card holder manufacturer for my business needs?
When selecting a card holder manufacturer, consider their experience in the industry, production capacity, and specialization in materials. Review their portfolio to assess the quality of their products. It’s also important to check customer testimonials and case studies to gauge reliability. Establish direct communication to discuss your specific requirements, including design and volume, to ensure they can meet your expectations. -
What are the key factors to evaluate when vetting a card holder supplier?
Key factors include the manufacturer’s compliance with international quality standards, their track record in timely delivery, and their ability to handle customs and logistics efficiently. Request samples to assess product quality and inquire about their production processes to understand their capacity for customization. Additionally, verify their certifications and industry affiliations to ensure credibility. -
What customization options are available when sourcing card holders?
Many manufacturers offer a range of customization options, including materials, colors, sizes, and branding elements such as logo printing or embossing. Discuss your specific needs with potential suppliers to explore the extent of their customization capabilities. Some manufacturers may also provide design services to help you create unique card holder solutions tailored to your brand identity. -
What is the minimum order quantity (MOQ) for card holders from manufacturers?
Minimum order quantities can vary widely among manufacturers, often ranging from 100 to several thousand units. Smaller manufacturers may offer lower MOQs, while larger ones typically require higher volumes to justify production costs. It’s advisable to negotiate the MOQ based on your business needs and discuss potential options for sample orders before committing to larger quantities. -
What payment terms should I expect when working with international card holder manufacturers?
Payment terms can differ significantly based on the manufacturer and the region. Common arrangements include a deposit upfront (usually 30-50%) with the balance due upon delivery or before shipment. Some suppliers may offer payment through letters of credit for added security. Always clarify payment methods, currencies, and terms in your agreement to avoid misunderstandings. -
How can I ensure quality assurance when sourcing card holders internationally?
To ensure quality assurance, establish clear specifications and standards before production begins. Request pre-production samples and conduct inspections at various stages of manufacturing. Consider hiring third-party quality control services for thorough inspections before shipment. Building a strong relationship with your supplier and maintaining open communication can also help address any quality concerns promptly. -
What logistics considerations should I keep in mind when importing card holders?
When importing card holders, consider shipping methods, costs, and delivery timelines. Assess whether you need air or sea freight based on your urgency and budget. Familiarize yourself with customs regulations in your country to avoid delays and additional charges. Collaborating with a freight forwarder can streamline the logistics process and ensure compliance with international shipping requirements. -
How do I handle potential disputes with my card holder supplier?
Handling disputes effectively begins with clear communication and documented agreements. In case of issues, address them directly with the supplier to seek a resolution. If necessary, refer to your contract for terms regarding disputes and mediation. Having an established dispute resolution process, such as arbitration, can also provide a framework for resolving conflicts amicably and efficiently.
Important Disclaimer & Terms of Use
⚠️ Important Disclaimer
The information provided in this guide, including content regarding manufacturers, technical specifications, and market analysis, is for informational and educational purposes only. It does not constitute professional procurement advice, financial advice, or legal advice.
While we have made every effort to ensure the accuracy and timeliness of the information, we are not responsible for any errors, omissions, or outdated information. Market conditions, company details, and technical standards are subject to change.
B2B buyers must conduct their own independent and thorough due diligence before making any purchasing decisions. This includes contacting suppliers directly, verifying certifications, requesting samples, and seeking professional consultation. The risk of relying on any information in this guide is borne solely by the reader.
Strategic Sourcing Conclusion and Outlook for card holder manufacturer
Why Is Strategic Sourcing Crucial for International B2B Buyers?
In the competitive landscape of card holder manufacturing, strategic sourcing emerges as a pivotal factor for success. By leveraging global supply chains, B2B buyers can access diverse materials, innovative designs, and competitive pricing. This not only enhances product quality but also fosters sustainability through responsible sourcing practices. For buyers from regions like Africa, South America, the Middle East, and Europe, understanding local market dynamics while tapping into international suppliers can yield significant advantages.
What Should B2B Buyers Focus on Moving Forward?
As we look ahead, international B2B buyers must prioritize building strong relationships with manufacturers that align with their values and operational goals. Investing time in supplier evaluations, quality assurance, and compliance with international standards will be essential in mitigating risks and enhancing supply chain resilience. Additionally, staying informed about market trends and technological advancements will empower buyers to make data-driven decisions that enhance their competitive edge.
How Can B2B Buyers Prepare for Future Opportunities?
To capitalize on emerging opportunities, B2B buyers should consider participating in industry trade shows and networking events. Engaging with manufacturers directly can lead to fruitful partnerships and innovative collaborations. By adopting a proactive approach to strategic sourcing, buyers can not only ensure a steady supply of high-quality card holders but also position themselves for long-term growth in an evolving marketplace.