Cut Costs with a Top Container House Manufacturer Guide (2025)
Introduction: Navigating the Global Market for container house manufacturer
Navigating the global market for container house manufacturing can be a daunting task for international B2B buyers, especially when sourcing sustainable and cost-effective solutions tailored to diverse regional needs. As the demand for container houses grows, businesses in Africa, South America, the Middle East, and Europe are increasingly seeking reliable manufacturers that can provide innovative designs and robust construction techniques. This comprehensive guide aims to simplify the sourcing process by exploring various types of container houses, their applications, and key factors to consider when selecting a manufacturer.
From residential units to commercial spaces, the versatility of container houses opens up numerous opportunities for businesses looking to invest in sustainable architecture. Throughout this guide, we will delve into critical aspects such as supplier vetting processes, cost considerations, and the latest trends in container construction. By equipping buyers with actionable insights and practical strategies, this guide empowers decision-makers to make informed purchasing choices that align with their specific project requirements and budget constraints.
For B2B buyers in regions like Italy and Egypt, understanding the nuances of the container house market is vital for leveraging local opportunities and mitigating potential risks. With a focus on transparency and quality, this guide serves as a valuable resource for navigating the complexities of the global container house manufacturing landscape, ensuring that your investment leads to successful outcomes.
Understanding container house manufacturer Types and Variations
Type Name | Key Distinguishing Features | Primary B2B Applications | Brief Pros & Cons for Buyers |
---|---|---|---|
Modular Container Homes | Pre-fabricated sections, customizable layouts | Residential, temporary housing | Pros: Quick assembly, flexible design. Cons: Limited structural integrity in extreme conditions. |
Shipping Container Conversions | Use of standard shipping containers, often retrofitted | Retail spaces, offices | Pros: Cost-effective, sustainable. Cons: May require significant modifications for comfort. |
Eco-Friendly Container Homes | Incorporation of sustainable materials and energy-efficient designs | Eco-tourism, green buildings | Pros: Lower environmental impact, energy savings. Cons: Higher initial investment. |
Luxury Container Homes | High-end finishes, advanced technology features | High-end residential, hospitality | Pros: Aesthetic appeal, modern amenities. Cons: Premium pricing, longer lead times. |
Container Office Solutions | Designed specifically for office use, often modular | Remote work sites, temporary offices | Pros: Quick deployment, functional design. Cons: May lack permanence and traditional office feel. |
What Are the Characteristics of Modular Container Homes?
Modular container homes consist of pre-fabricated sections that can be easily transported and assembled on-site. These structures are highly customizable, allowing buyers to modify layouts according to specific needs. They are particularly suitable for residential projects and temporary housing solutions. When purchasing, consider the modular design’s flexibility versus the potential need for additional permits or site preparation.
How Do Shipping Container Conversions Serve B2B Needs?
Shipping container conversions utilize standard shipping containers, which are often retrofitted for various commercial uses. These conversions are popular for retail spaces and offices due to their cost-effectiveness and sustainability. B2B buyers should evaluate the extent of modifications required for comfort and usability, as these can significantly affect overall project timelines and budgets.
What Makes Eco-Friendly Container Homes Attractive?
Eco-friendly container homes focus on sustainable materials and energy-efficient designs, appealing to environmentally conscious businesses. They are well-suited for eco-tourism projects and green building initiatives. However, while they offer long-term energy savings, the initial investment can be higher compared to traditional options. Buyers should assess their budget against the potential for future savings and environmental impact.
Why Choose Luxury Container Homes?
Luxury container homes are designed with high-end finishes and advanced technology features, targeting high-end residential and hospitality markets. These homes provide aesthetic appeal and modern amenities, catering to discerning buyers. However, they come at a premium price and may have longer lead times due to customizations. Businesses should weigh the benefits of luxury against the investment required.
What Are the Benefits of Container Office Solutions?
Container office solutions are specifically designed for office use, often in modular formats that facilitate quick deployment. Ideal for remote work sites or temporary offices, these solutions offer functional designs that meet immediate business needs. However, they may lack the permanence and traditional feel of conventional office spaces. B2B buyers should consider the trade-off between flexibility and long-term operational requirements when evaluating these options.
Related Video: How to Build Prefabricated Detachable Container House / Porta Cabin? (2021)
Key Industrial Applications of container house manufacturer
Industry/Sector | Specific Application of Container House Manufacturer | Value/Benefit for the Business | Key Sourcing Considerations for this Application |
---|---|---|---|
Construction | Modular housing units for quick deployment | Reduced construction time and costs | Local regulations, transportation logistics, customization options |
Education | Mobile classrooms for remote learning | Flexibility in location, cost-effective solutions | Durability, insulation standards, design adaptability |
Healthcare | Temporary medical facilities and clinics | Rapid response to healthcare needs | Compliance with health regulations, accessibility features, utility connections |
Hospitality and Tourism | Eco-friendly lodging options | Attracts eco-conscious travelers, unique experiences | Aesthetic design, sustainability certifications, local amenities |
Oil and Gas | Workforce accommodations on-site | Enhanced worker productivity and morale | Safety standards, modularity for harsh environments, supply chain reliability |
How Are Container Houses Used in the Construction Sector?
In the construction industry, container houses serve as modular housing units that can be quickly deployed at job sites. This approach significantly reduces construction time and costs, allowing for immediate housing solutions for workers. For international buyers, particularly in regions like Africa and South America, understanding local regulations and transportation logistics is crucial. Customization options to meet specific project requirements are also key considerations when sourcing container houses for construction purposes.
What Role Do Container Houses Play in Education?
Container houses are increasingly utilized as mobile classrooms, particularly in remote or underserved areas. They provide a flexible and cost-effective solution for educational institutions looking to expand their facilities without the need for permanent structures. For buyers in the Middle East and Europe, considerations such as durability and insulation standards are essential to ensure that the classrooms are conducive to learning in various climates. Design adaptability can also enhance the appeal and functionality of these educational spaces.
How Are Container Houses Beneficial in Healthcare?
In the healthcare sector, container houses can be transformed into temporary medical facilities or clinics, especially in response to emergencies or natural disasters. This rapid deployment capability is vital for addressing urgent healthcare needs. International buyers must focus on compliance with health regulations and accessibility features when sourcing these units. Additionally, ensuring proper utility connections is critical for the effective operation of medical services within these container facilities.
How Can Container Houses Enhance Hospitality and Tourism?
The hospitality industry is leveraging container houses to create eco-friendly lodging options that attract environmentally conscious travelers. These unique accommodations offer a sustainable alternative to traditional hotels, often featuring innovative designs and amenities. For buyers in Europe and Africa, sourcing considerations include aesthetic design and sustainability certifications, which can enhance the marketability of these properties. Local amenities and services can further elevate the guest experience.
What Are the Applications of Container Houses in Oil and Gas?
In the oil and gas sector, container houses are used for workforce accommodations on-site, providing essential living quarters for employees in remote locations. This solution enhances worker productivity and morale by offering comfortable and secure housing. Buyers in this industry should prioritize safety standards and modularity, particularly for operations in harsh environments. Additionally, ensuring a reliable supply chain for these container units is critical to maintain operational efficiency.
Related Video: 40ft foldable expandable container home with two bedrooms
3 Common User Pain Points for ‘container house manufacturer’ & Their Solutions
Scenario 1: Navigating Regulatory Compliance in Container Construction
The Problem:
International B2B buyers, particularly from regions like Africa and the Middle East, often encounter significant hurdles when it comes to regulatory compliance for container houses. Each country has its own building codes, zoning laws, and safety regulations that must be adhered to, which can vary drastically even within a single region. Failing to meet these standards can lead to project delays, increased costs, and potential legal repercussions, making it crucial for buyers to understand the local regulations in the markets they wish to operate.
The Solution:
To effectively navigate these regulatory challenges, buyers should engage with local experts, such as architects or legal consultants, who are familiar with the specific requirements in their target markets. It is advisable to conduct thorough research into local building codes and zoning laws before finalizing any contracts with container house manufacturers. Additionally, collaborating with manufacturers who have experience in the target region can be invaluable. These manufacturers often have established relationships with local authorities and can provide insights into the approval process, reducing the risk of non-compliance.
Scenario 2: Sourcing Quality Materials for Container Houses
The Problem:
Another common pain point for B2B buyers is sourcing high-quality materials that are suitable for container house construction. Buyers may find that not all manufacturers use materials that meet their quality or sustainability standards, leading to concerns about the durability and environmental impact of their structures. This is particularly significant for buyers in Europe, where there is a strong emphasis on sustainability and eco-friendly building practices.
The Solution:
To ensure the quality of materials, buyers should prioritize manufacturers who provide transparent information about their sourcing and production processes. Requesting samples and detailed specifications can help assess material quality before making large orders. Furthermore, buyers should inquire about certifications for sustainability, such as LEED or ISO standards, which can indicate a manufacturer’s commitment to eco-friendly practices. Establishing a solid line of communication with manufacturers about material expectations and sustainability goals will foster a stronger partnership and lead to better project outcomes.
Scenario 3: Managing Logistics and Delivery Challenges
The Problem:
Logistics and delivery issues pose significant challenges for B2B buyers in the container house sector. Buyers may face delays in the shipping of container houses due to unforeseen circumstances, such as port congestion or customs delays, which can lead to project timelines being disrupted. These delays can be particularly frustrating for buyers who are operating on tight schedules and budgets, especially in emerging markets in South America and Africa where logistics infrastructure may be less developed.
The Solution:
To mitigate logistics challenges, buyers should work closely with manufacturers who have a proven track record in handling international shipping and delivery. Establishing a clear timeline and communication plan from the outset is crucial. Buyers should also consider working with logistics partners who specialize in international transport and customs clearance to streamline the process. Additionally, having contingency plans in place, such as alternative shipping routes or additional suppliers, can help manage unexpected delays. Regular updates and proactive communication with both the manufacturer and logistics partners will ensure that buyers remain informed and can adjust their plans accordingly.
Strategic Material Selection Guide for container house manufacturer
What Are the Key Properties of Steel for Container Houses?
Steel is the most common material used in container house manufacturing due to its strength and versatility. Key properties include high tensile strength, which allows it to withstand significant loads and extreme weather conditions. Steel also has excellent corrosion resistance when treated with proper coatings, making it suitable for various climates, especially in humid regions such as parts of Africa and South America.
Pros & Cons:
The primary advantages of steel are its durability and structural integrity, which contribute to the longevity of container houses. However, the manufacturing complexity can be high, particularly when fabricating custom designs. Additionally, steel can be relatively expensive compared to other materials, impacting overall project budgets.
Impact on Application:
Steel’s compatibility with various media, such as water and electricity, makes it ideal for container houses that require plumbing and electrical systems.
Considerations for International Buyers:
When sourcing steel, B2B buyers must consider compliance with local standards such as ASTM in the USA, EN in Europe, and JIS in Japan. It’s essential to verify that suppliers can meet these standards to ensure product safety and performance.
How Does Wood Compare as a Material for Container Houses?
Wood is another viable option for container house construction, particularly for interior finishes and insulation. Its key properties include natural insulation capabilities and aesthetic appeal, making it a popular choice for residential applications.
Pros & Cons:
Wood is generally more cost-effective than steel and offers a warm, inviting atmosphere. However, it is less durable and more susceptible to pests and moisture, which can lead to long-term maintenance issues. The manufacturing complexity is lower, but care must be taken to ensure that the wood is treated to prevent rot and insect damage.
Impact on Application:
Wood is compatible with various finishes and can be easily modified, making it suitable for custom designs. However, its susceptibility to fire and water damage can limit its use in certain climates.
Considerations for International Buyers:
Buyers should ensure that the wood used complies with local regulations regarding sustainability and sourcing, especially in regions like Europe where eco-friendly materials are preferred.
What Are the Benefits of Using Insulated Panels in Container Houses?
Insulated panels, typically made from materials like polyurethane or polystyrene, are increasingly popular in container house construction due to their thermal efficiency. Key properties include high insulation values and lightweight construction, which can enhance energy efficiency.
Pros & Cons:
The primary advantage of insulated panels is their ability to maintain temperature, reducing heating and cooling costs. However, they can be more expensive than traditional materials and may require specialized installation techniques, increasing manufacturing complexity.
Impact on Application:
Insulated panels are particularly effective in climates with extreme temperatures, making them suitable for regions in the Middle East and parts of Europe.
Considerations for International Buyers:
Buyers should look for panels that meet local building codes and energy efficiency standards. Compliance with standards such as ISO or local equivalents is crucial for ensuring product quality and performance.
How Does Concrete Play a Role in Container House Construction?
Concrete is often used in combination with steel or as a standalone material for container houses, particularly for foundations and structural elements. Its key properties include high compressive strength and excellent fire resistance, making it a robust choice for various applications.
Pros & Cons:
Concrete is highly durable and requires minimal maintenance over time. However, it is heavier than other materials, which can complicate transportation and installation. Additionally, the initial cost can be high, impacting budget considerations.
Impact on Application:
Concrete is ideal for load-bearing structures and can withstand harsh environmental conditions, making it suitable for diverse applications across Africa and South America.
Considerations for International Buyers:
Buyers must ensure that the concrete used meets local standards for strength and durability, such as EN in Europe or ACI in the USA. Understanding local regulations is essential for ensuring compliance and project success.
Summary Table of Material Selection for Container House Manufacturing
Material | Typical Use Case for container house manufacturer | Key Advantage | Key Disadvantage/Limitation | Relative Cost (Low/Med/High) |
---|---|---|---|---|
Steel | Structural framework and exterior cladding | High strength and durability | High cost and manufacturing complexity | High |
Wood | Interior finishes and insulation | Cost-effective and aesthetic appeal | Susceptible to pests and moisture | Medium |
Insulated Panels | Walls and roofs for energy efficiency | Excellent thermal insulation | Higher cost and installation complexity | High |
Concrete | Foundations and structural elements | High durability and fire resistance | Heavy and costly | Medium to High |
This strategic material selection guide provides international B2B buyers with actionable insights into the various materials used in container house manufacturing, allowing for informed decision-making tailored to specific regional needs and standards.
In-depth Look: Manufacturing Processes and Quality Assurance for container house manufacturer
What Are the Key Stages of the Manufacturing Process for Container Houses?
The manufacturing of container houses involves several critical stages, each essential for ensuring structural integrity and quality. Understanding these stages can help international B2B buyers assess the capabilities of potential suppliers.
1. Material Preparation: What Materials Are Used in Container House Manufacturing?
The initial stage focuses on sourcing and preparing high-quality materials. Container houses primarily utilize steel shipping containers, which are often modified to meet specific design requirements. Buyers should ensure that the containers used are made from high-grade corten steel, known for its durability and resistance to corrosion.
In addition to steel, insulation materials, windows, doors, and other architectural elements are sourced. Buyers should inquire about the suppliers’ sourcing practices to ensure compliance with international standards and environmental regulations.
2. Forming: How Are Containers Modified and Reinforced?
Once the materials are prepared, the forming stage begins. This involves cutting, welding, and reinforcing the container structure. Key techniques in this phase include:
- Cutting: Utilizing precision cutting tools to create openings for windows, doors, and ventilation.
- Welding: Employing various welding techniques, such as MIG or TIG welding, to ensure the joints are strong and durable.
- Reinforcement: Adding structural elements, such as steel frames, to enhance stability, especially in regions prone to extreme weather conditions.
Buyers should ask suppliers about the technologies used in this phase, as advanced machinery can lead to more precise modifications and improved structural integrity.
3. Assembly: How Are Container Houses Constructed?
The assembly stage involves integrating various components into a cohesive structure. This includes installing insulation, plumbing, electrical systems, and interior finishes. Key techniques include:
- Modular Assembly: Many manufacturers employ modular design principles, allowing for quicker assembly and customization based on client specifications.
- Quality Control Checkpoints: Throughout the assembly process, manufacturers should implement regular quality control checkpoints to ensure that each component meets the required standards.
International buyers should verify if suppliers offer customization options, as this can significantly affect the usability and aesthetic appeal of the final product.
4. Finishing: What Are the Final Touches in Container House Manufacturing?
The finishing stage involves applying exterior and interior finishes, including paint, cladding, and flooring. This stage enhances both the aesthetic appeal and the durability of the container house. Key considerations include:
- Weatherproofing: Applying sealants and coatings that protect against moisture and UV damage.
- Sustainability: Many buyers prioritize eco-friendly finishes; inquire about the availability of sustainable materials and finishes.
Buyers should assess suppliers’ portfolios to understand the range of finishes offered and how they align with their project requirements.
What Quality Assurance Processes Should Buyers Expect?
Quality assurance is critical in ensuring that container houses meet international standards and client expectations. Understanding the key quality control checkpoints and certifications can help buyers make informed decisions.
1. What Are the Relevant International Standards for Container House Manufacturing?
Manufacturers should comply with various international quality standards to ensure product reliability. Key certifications include:
- ISO 9001: This standard focuses on quality management systems and is essential for any manufacturer aiming to ensure consistent quality in their products.
- CE Marking: Particularly important for the European market, CE marking indicates that the product meets EU safety, health, and environmental protection standards.
- API Standards: For specialized container applications, adherence to API standards ensures that containers meet specific industry requirements.
Buyers should verify that suppliers possess these certifications as a baseline for quality assurance.
2. What Are the Quality Control Checkpoints in the Manufacturing Process?
Quality control checkpoints, often abbreviated as IQC (Incoming Quality Control), IPQC (In-Process Quality Control), and FQC (Final Quality Control), play a vital role in the manufacturing process:
- IQC: This checkpoint involves inspecting raw materials and components before production begins, ensuring that only high-quality inputs are used.
- IPQC: During the assembly process, manufacturers should conduct periodic inspections to identify and rectify defects early.
- FQC: At the completion of the manufacturing process, a thorough inspection is conducted to ensure that the final product meets all specifications and quality standards.
Buyers should inquire about the frequency and methods of these inspections to gauge the supplier’s commitment to quality.
3. What Common Testing Methods Are Used in Quality Assurance?
Manufacturers should employ various testing methods to validate the quality of container houses. Common methods include:
- Structural Integrity Testing: Assessing the strength and durability of the container structure under various load conditions.
- Thermal Insulation Testing: Evaluating the effectiveness of insulation materials in regulating temperature.
- Water Tightness Testing: Ensuring that the container is sealed and can withstand moisture exposure.
Buyers can request testing reports from suppliers to verify the results of these assessments.
How Can B2B Buyers Verify Supplier Quality Control?
To ensure that suppliers adhere to high-quality standards, B2B buyers should implement several verification methods:
1. What Role Do Audits Play in Verifying Supplier Quality?
Conducting audits is a critical step in assessing a supplier’s quality control processes. Buyers can perform:
- On-Site Audits: Visiting the manufacturing facility to evaluate processes, equipment, and quality control measures firsthand.
- Document Reviews: Analyzing quality control documentation, including inspection reports and certification records, to ensure compliance with standards.
2. How Can Buyers Use Third-Party Inspections?
Engaging third-party inspection services can provide an unbiased assessment of a supplier’s quality control measures. Buyers should consider:
- Pre-Shipment Inspections: Verifying that the products meet specified standards before they leave the manufacturing facility.
- Random Sampling: Conducting random inspections of finished products to ensure consistency in quality.
By utilizing these methods, buyers from Africa, South America, the Middle East, and Europe can significantly mitigate risks associated with purchasing container houses and ensure they receive high-quality products that meet their requirements.
Practical Sourcing Guide: A Step-by-Step Checklist for ‘container house manufacturer’
The following practical sourcing guide is designed for international B2B buyers interested in procuring container houses. This checklist provides actionable steps to ensure a successful procurement process.
Step 1: Define Your Project Requirements
Before initiating the sourcing process, clearly outline your project specifications, including size, design, and intended use of the container houses. This step is crucial as it sets the foundation for your entire procurement strategy. Consider factors such as:
- Local regulations: Investigate any building codes or restrictions in your target market (e.g., Italy, Egypt).
- Customization needs: Determine if you require unique features like insulation, plumbing, or electrical systems.
Step 2: Research Potential Suppliers
Conduct thorough research to identify reputable container house manufacturers. Use online directories, trade shows, and industry forums to compile a list of potential suppliers. This step is vital to ensure you are considering only trustworthy manufacturers. Look for:
- Customer reviews: Check testimonials and ratings from previous buyers.
- Industry experience: Favor suppliers with a proven track record in your target region.
Step 3: Evaluate Supplier Certifications and Compliance
Verify that your shortlisted suppliers have the necessary certifications and comply with international standards. This is important to guarantee product quality and safety. Key certifications to look for include:
- ISO Certification: Indicates adherence to quality management systems.
- Local compliance: Ensure the manufacturer meets the regulatory requirements of your specific country.
Step 4: Request Detailed Quotes
Once you have narrowed down your options, request detailed quotes from multiple suppliers. A comprehensive quote should include pricing, lead times, payment terms, and shipping costs. This will facilitate a better comparison of offers. Pay attention to:
- Hidden costs: Inquire about additional fees such as customs duties or handling charges.
- Volume discounts: Check if the supplier offers reduced rates for larger orders.
Step 5: Assess Quality Control Measures
Inquire about the quality control processes that each manufacturer employs. Understanding their quality assurance protocols is crucial to ensure that the container houses meet your specifications. Look for:
- Inspection protocols: Ask if they conduct inspections during and after production.
- Return policies: Clarify the terms for returns or replacements in case of defects.
Step 6: Review Shipping and Logistics Options
Discuss the logistics of shipping your container houses to your location. Efficient logistics are essential to minimize delays and additional costs. Consider:
- Shipping partners: Ask about their experience with international shipping and any partnerships with logistics companies.
- Delivery timelines: Confirm estimated shipping times to avoid potential project delays.
Step 7: Finalize Terms and Contract
After selecting a supplier, finalize the terms of the agreement. Draft a contract that outlines all aspects of the transaction, including payment schedules, delivery dates, and warranty information. This step is critical to protect your investment and ensure accountability. Ensure to include:
- Dispute resolution: Specify how any disagreements will be managed.
- Payment security: Consider using escrow services to safeguard your payment until delivery confirmation.
By following this checklist, international B2B buyers can confidently navigate the procurement process for container houses, ensuring that they choose the right manufacturer to meet their needs.
Comprehensive Cost and Pricing Analysis for container house manufacturer Sourcing
What are the Key Cost Components in Container House Manufacturing?
Understanding the cost structure of container house manufacturing is essential for international B2B buyers. The primary cost components include:
-
Materials: The foundation of any container house, materials such as steel, insulation, and finishing products significantly impact overall costs. Prices for these materials can fluctuate based on global market conditions, so it’s crucial to establish reliable suppliers who can provide quality materials at competitive rates.
-
Labor: Labor costs vary widely depending on the region and the skill level required for manufacturing. In regions like Africa or South America, labor may be more affordable, but it’s important to assess the skill level and productivity of the workforce. In contrast, European countries may have higher labor costs but also higher quality standards.
-
Manufacturing Overhead: This includes expenses related to facilities, utilities, and equipment maintenance. Understanding the overhead costs is vital as they can significantly affect the price per unit of the container houses.
-
Tooling: Depending on the level of customization, tooling costs can vary. Custom molds or specialized equipment may require significant investment, which is often passed on to the buyer.
-
Quality Control (QC): Implementing a rigorous QC process ensures that the final product meets industry standards. However, this can also increase costs. Buyers should ensure that the manufacturers they engage with have robust QC measures in place to avoid future issues.
-
Logistics: Transportation costs, including shipping and handling, can add significant expenses, especially for international buyers. Understanding the logistics involved in getting the product from the manufacturer to the buyer’s location is crucial for accurate budgeting.
-
Margin: Manufacturers typically build a profit margin into their pricing. This margin can vary significantly based on the manufacturer’s market positioning and brand reputation.
How Do Price Influencers Affect Container House Sourcing?
Several factors influence the pricing of container houses:
-
Volume and Minimum Order Quantity (MOQ): Larger orders often lead to discounts. Understanding a manufacturer’s MOQ can help buyers negotiate better pricing.
-
Specifications and Customization: Custom designs or specific requirements can drive up costs. Buyers should weigh the benefits of customization against budget constraints.
-
Material Quality and Certifications: Higher-quality materials and certifications (like ISO) can lead to increased costs but may also enhance the durability and resale value of the container houses.
-
Supplier Factors: The reputation and experience of the supplier can influence pricing. Established suppliers may charge more due to their proven track record.
-
Incoterms: Understanding Incoterms is essential for international buyers. These terms define responsibilities for shipping, insurance, and tariffs, which can significantly impact total costs.
What Are the Best Negotiation Tips for International B2B Buyers?
When sourcing container houses, effective negotiation can lead to significant cost savings:
-
Research and Benchmarking: Conduct thorough research on industry pricing and competitor offerings to strengthen your negotiating position.
-
Highlight Long-term Relationships: Emphasizing the potential for ongoing business can incentivize suppliers to offer better pricing.
-
Focus on Total Cost of Ownership (TCO): Rather than just the upfront costs, consider the long-term value and operational costs associated with the container houses. This approach can help justify higher initial investments for better quality.
-
Leverage Regional Advantages: Buyers from Africa, South America, the Middle East, and Europe should consider local manufacturing options to reduce logistics costs and take advantage of regional pricing.
What Should International Buyers Keep in Mind Regarding Pricing Nuances?
Pricing nuances vary across regions, impacting the overall sourcing strategy:
-
Currency Fluctuations: International buyers should be aware of currency exchange rates and potential impacts on pricing. Locking in prices through contracts can mitigate this risk.
-
Cultural Differences in Negotiation: Understanding regional negotiation styles can enhance communication and lead to better deals.
-
Regulatory Compliance: Ensure that the container houses meet local regulations, as non-compliance can incur additional costs and delays.
Disclaimer on Indicative Prices
It is important to note that prices for container houses can vary widely based on the factors outlined above. Buyers should seek multiple quotes and conduct due diligence to ensure they are making informed purchasing decisions.
Alternatives Analysis: Comparing container house manufacturer With Other Solutions
When evaluating the best housing solutions, international B2B buyers must consider various alternatives to container houses. Each option presents unique advantages and challenges that can impact the decision-making process. This analysis focuses on comparing container house manufacturers with two viable alternatives: traditional modular buildings and prefabricated wooden structures.
Comparison Table of Housing Solutions
Comparison Aspect | Container House Manufacturer | Traditional Modular Buildings | Prefabricated Wooden Structures |
---|---|---|---|
Performance | High durability, weather-resistant | Good insulation and energy efficiency | Aesthetic appeal, natural materials |
Cost | Moderate initial investment, lower long-term costs | Higher upfront costs, but energy-efficient | Variable costs based on material quality |
Ease of Implementation | Quick assembly, requires minimal site preparation | Moderate complexity, requires skilled labor | Simple assembly, but may need on-site adjustments |
Maintenance | Low maintenance due to durable materials | Moderate, depending on material used | Higher maintenance due to natural wear and tear |
Best Use Case | Temporary housing, emergency shelters, industrial applications | Permanent structures, residential, and commercial | Eco-friendly homes, vacation cabins, and rural housing |
What are the Advantages and Disadvantages of Traditional Modular Buildings?
Traditional modular buildings offer a robust alternative to container houses. They are typically designed with high insulation values, making them energy-efficient and suitable for a range of climates. The initial investment may be higher than container houses, but their long-term efficiency can offset costs. However, their construction often requires skilled labor, which can complicate the implementation process, especially in regions with a shortage of qualified workers.
How do Prefabricated Wooden Structures Compare?
Prefabricated wooden structures stand out for their aesthetic appeal and the use of sustainable materials. They are an excellent choice for eco-conscious buyers looking for natural building solutions. While these structures are relatively easy to assemble, they may require more maintenance over time due to the susceptibility of wood to elements such as moisture and pests. The costs can vary significantly based on the quality of materials used, making it essential for buyers to budget accordingly.
How Can B2B Buyers Choose the Right Solution for Their Needs?
Selecting the right housing solution depends on the specific requirements of the project. B2B buyers should consider factors such as the intended use, budget constraints, and the local availability of skilled labor. For example, container houses may be preferable for temporary installations or rapid deployment in remote areas. In contrast, traditional modular buildings might be better suited for long-term residential or commercial projects. Lastly, prefabricated wooden structures can cater to buyers focused on sustainability and aesthetics. By carefully evaluating these options, buyers can make informed decisions that align with their operational and financial goals.
Essential Technical Properties and Trade Terminology for container house manufacturer
What Are the Essential Technical Properties for Container House Manufacturing?
When selecting a container house manufacturer, understanding the technical properties of the materials and construction methods is crucial. Here are some critical specifications to consider:
1. Material Grade: What is the Best Steel for Container Construction?
Container houses are primarily constructed from steel, and the grade of steel significantly affects durability and resistance to environmental factors. Common grades include Corten steel, known for its weathering properties, and mild steel, which is cost-effective yet less durable. High-grade materials ensure longevity and reduce maintenance costs, making it vital for B2B buyers to assess the material grade used in construction.
2. Tolerance Levels: How Do Tolerances Impact Container House Quality?
Tolerance levels refer to the allowable deviations in dimensions during manufacturing. For container houses, maintaining tight tolerances is essential for ensuring structural integrity and proper fitting of components. Poor tolerances can lead to issues such as water leakage or structural instability. Buyers should inquire about the manufacturer’s tolerance standards to ensure quality and safety in their projects.
3. Insulation Properties: What Should You Know About Thermal Efficiency?
Insulation is a crucial factor in container houses, affecting energy efficiency and comfort. The R-value, which measures insulation effectiveness, should be considered. Higher R-values indicate better insulation, reducing heating and cooling costs. Buyers from regions with extreme weather conditions, such as the Middle East or Europe, should prioritize manufacturers that offer high-performance insulation solutions.
4. Load-Bearing Capacity: How Much Weight Can Your Container House Support?
The load-bearing capacity of a container house determines how much weight it can support without compromising structural integrity. This is especially important for multi-story designs or when accommodating heavy equipment. Buyers should request load capacity specifications to ensure that the container house meets their intended use, whether for residential, commercial, or industrial applications.
5. Corrosion Resistance: How Important is Weather Resistance in Container Design?
Given the exposure to various weather conditions, corrosion resistance is a vital property. Manufacturers often apply protective coatings or utilize weather-resistant materials to prolong the lifespan of container houses. In regions like Africa or South America, where humidity and salt exposure may be prevalent, understanding the corrosion resistance measures taken by the manufacturer can prevent costly repairs in the future.
What Key Trade Terminology Should B2B Buyers Understand?
Familiarity with industry jargon can streamline communication and negotiations between buyers and manufacturers. Here are some essential terms to know:
1. OEM (Original Equipment Manufacturer): What Role Does OEM Play in Container Production?
OEM refers to a company that produces parts or equipment that may be marketed by another manufacturer. In the context of container houses, an OEM might provide specialized components like windows or insulation systems. Understanding OEM relationships can help buyers gauge the quality and origin of different components used in the construction process.
2. MOQ (Minimum Order Quantity): Why Is MOQ Important for Bulk Purchases?
MOQ is the minimum quantity of units a supplier is willing to sell. For B2B buyers, understanding MOQ is essential for budgeting and inventory management. Lower MOQs can allow smaller companies to enter the market, while larger projects may benefit from negotiating lower prices on bulk orders.
3. RFQ (Request for Quotation): How to Effectively Use RFQs in Sourcing Container Houses?
An RFQ is a document sent to suppliers to invite them to bid on providing goods or services. For container house buyers, an RFQ helps clarify project specifications and obtain competitive pricing. Including detailed project requirements in the RFQ can yield more accurate quotes and facilitate better decision-making.
4. Incoterms: What Are Incoterms and How Do They Affect International Shipping?
Incoterms are international commercial terms that define the responsibilities of buyers and sellers in shipping and delivery. Understanding these terms is critical for B2B transactions, especially when sourcing from different countries. They clarify who is responsible for shipping costs, insurance, and risk, which can significantly impact overall project costs.
By grasping these technical properties and trade terminologies, international B2B buyers can make informed decisions when selecting a container house manufacturer, ensuring their projects meet quality, budget, and timeline expectations.
Navigating Market Dynamics and Sourcing Trends in the container house manufacturer Sector
What are the Key Market Dynamics in the Container House Manufacturing Sector?
The container house manufacturing sector is experiencing robust growth, driven by a confluence of global factors including urbanization, housing shortages, and the need for sustainable construction solutions. International B2B buyers from Africa, South America, the Middle East, and Europe (notably Italy and Egypt) are increasingly turning to container homes as a viable solution to meet housing demands efficiently and affordably. The rising trend of remote work and the desire for flexible living spaces further enhance the appeal of container houses, making them a preferred choice for both residential and commercial applications.
Emerging B2B technologies are reshaping sourcing trends in this sector. Digital platforms for sourcing materials and services are becoming prevalent, enabling buyers to connect with manufacturers globally. Technologies such as Building Information Modeling (BIM) and modular construction techniques streamline the design and building process, thus reducing costs and lead times. Additionally, the integration of IoT (Internet of Things) in container homes offers real-time monitoring and management solutions, adding value for buyers looking for modern, tech-savvy housing options.
How Does Sustainability Influence Sourcing Trends in Container House Manufacturing?
Sustainability is at the forefront of the container house manufacturing sector, influencing sourcing decisions significantly. The environmental impact of construction materials and methods is under scrutiny, leading buyers to prioritize eco-friendly options. For instance, using recycled steel and sustainable insulation materials not only minimizes the carbon footprint but also aligns with global sustainability goals.
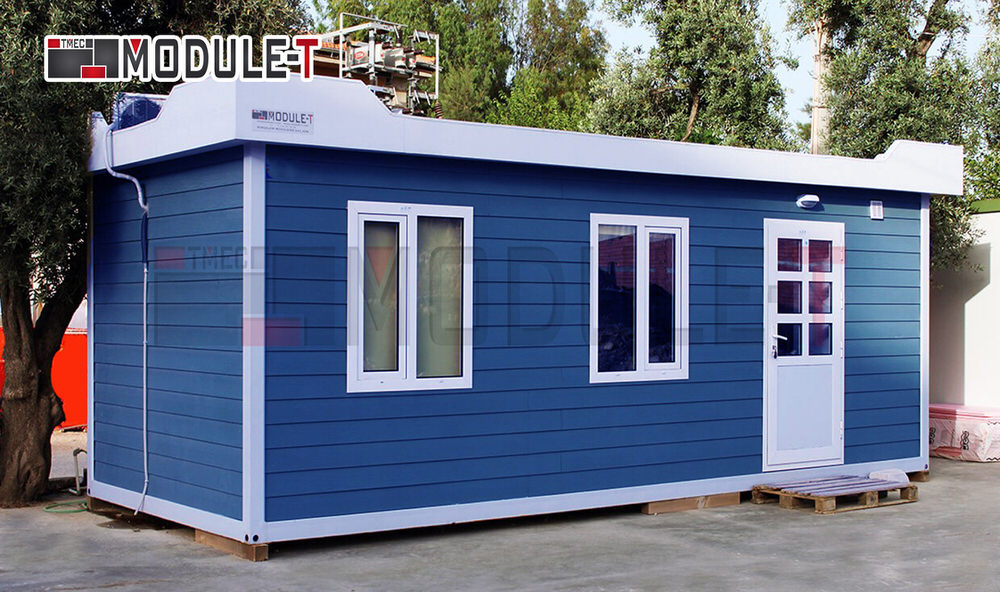
A stock image related to container house manufacturer.
Ethical sourcing is increasingly important for B2B buyers. Companies are now expected to provide transparency regarding their supply chains, ensuring materials are sourced responsibly without compromising environmental integrity or social equity. Certifications like LEED (Leadership in Energy and Environmental Design) and ISO 14001 (Environmental Management) are becoming essential for manufacturers to demonstrate their commitment to sustainable practices. Buyers should actively seek partnerships with manufacturers who prioritize these certifications, as they reflect a dedication to reducing environmental impact and fostering ethical labor practices.
What is the Historical Context of Container House Manufacturing?
The container house manufacturing sector has evolved significantly since its inception in the early 2000s. Initially seen as a temporary housing solution, container homes have transitioned into a mainstream option for both residential and commercial use. The versatility of shipping containers, combined with innovative architectural designs, has led to their acceptance in various markets, including Africa and South America, where housing shortages are acute.
As market dynamics shift towards sustainability and efficiency, the sector has embraced new technologies and materials that enhance the durability and aesthetic appeal of container homes. This evolution reflects a broader trend in construction, where traditional methods are being redefined to meet the needs of modern consumers and environmental standards. For international B2B buyers, understanding this historical context is crucial for making informed sourcing decisions that align with current market trends.
Frequently Asked Questions (FAQs) for B2B Buyers of container house manufacturer
-
How do I evaluate the credibility of a container house manufacturer?
When sourcing a container house manufacturer, it’s crucial to assess their credibility through various means. Start by reviewing their business certifications, industry experience, and customer testimonials. Request references from previous clients, especially those in your region (Africa, South America, the Middle East, or Europe), to gain insight into their reliability. Additionally, consider visiting their production facility if feasible, and ensure they comply with international quality standards such as ISO certification. -
What are the key factors to consider when customizing a container house?
Customization options for container houses are vast and can include layout, insulation, windows, and finishes. When considering customization, evaluate your specific needs such as climate, intended use, and local building regulations. Engage directly with manufacturers to discuss your requirements and ask for 3D models or prototypes. Understanding their design capabilities and previous projects can also help ensure they can deliver your vision effectively. -
What is the minimum order quantity (MOQ) for container houses from manufacturers?
The minimum order quantity (MOQ) can vary significantly between manufacturers. Some may require a single unit for custom designs, while others might set higher MOQs for bulk orders to ensure cost-effectiveness. It’s essential to clarify these terms upfront and explore potential discounts for larger orders. Additionally, consider the implications of MOQ on your project timeline and budget. -
What payment terms should I expect when purchasing from a container house manufacturer?
Payment terms can vary widely depending on the manufacturer and the scale of your order. Common terms may include a deposit (usually 30% to 50%) upfront, with the balance due upon completion or prior to shipping. Some manufacturers may also offer financing options or payment plans. Always ensure that payment terms are clearly outlined in the contract to avoid misunderstandings. -
How do I ensure quality assurance when sourcing container houses internationally?
To ensure quality assurance, request detailed specifications and samples before finalizing your order. Many manufacturers provide quality control documentation, including inspection reports and certifications. Consider hiring third-party inspection services to evaluate the production process and final product quality. Establishing clear communication regarding quality expectations and standards is also crucial for successful outcomes. -
What are the logistics considerations when importing container houses?
Logistics plays a vital role in the successful importation of container houses. Factors to consider include shipping methods (e.g., sea freight), customs clearance processes, and delivery timelines. Understand the import regulations in your country, including taxes and duties, to avoid unexpected costs. Collaborate with logistics providers experienced in handling oversized or heavy cargo to ensure smooth transport. -
How can I find reputable container house manufacturers in Europe, Africa, and South America?
To find reputable container house manufacturers, start by attending industry trade shows and exhibitions, which provide networking opportunities. Online platforms like Alibaba, ThomasNet, or local business directories can also help identify potential suppliers. Join industry associations or forums that focus on construction and modular housing to gain recommendations. Always conduct thorough research and vet potential manufacturers through reviews and case studies. -
What are the advantages of using container houses for businesses in emerging markets?
Container houses offer numerous advantages, particularly in emerging markets. They are cost-effective and can be rapidly deployed, making them ideal for temporary or permanent structures. Their modular design allows for flexibility and scalability, catering to diverse business needs. Additionally, container houses are often more environmentally friendly, utilizing recycled materials and providing energy-efficient options, which can align with sustainability goals in regions like Africa and South America.
Important Disclaimer & Terms of Use
⚠️ Important Disclaimer
The information provided in this guide, including content regarding manufacturers, technical specifications, and market analysis, is for informational and educational purposes only. It does not constitute professional procurement advice, financial advice, or legal advice.
While we have made every effort to ensure the accuracy and timeliness of the information, we are not responsible for any errors, omissions, or outdated information. Market conditions, company details, and technical standards are subject to change.
B2B buyers must conduct their own independent and thorough due diligence before making any purchasing decisions. This includes contacting suppliers directly, verifying certifications, requesting samples, and seeking professional consultation. The risk of relying on any information in this guide is borne solely by the reader.
Strategic Sourcing Conclusion and Outlook for container house manufacturer
In the evolving landscape of container house manufacturing, strategic sourcing emerges as a pivotal factor for international B2B buyers. Engaging with reliable suppliers ensures not only the acquisition of quality products but also fosters long-term partnerships that can adapt to changing market dynamics. Key takeaways include the importance of assessing supplier capabilities, understanding local market conditions, and leveraging technology for efficient procurement processes.
How can strategic sourcing enhance your procurement strategy? By focusing on transparency and communication, buyers can mitigate risks associated with supply chain disruptions, particularly in regions like Africa and the Middle East where logistical challenges may arise. Additionally, aligning with manufacturers who prioritize sustainability can offer competitive advantages in regions such as Europe, where eco-consciousness is increasingly influencing purchasing decisions.
Looking forward, the demand for container houses is set to grow as more businesses recognize their versatility and cost-effectiveness. We encourage B2B buyers from South America and Europe to proactively explore partnerships with innovative container house manufacturers. By doing so, you position your business to harness the benefits of this burgeoning market while contributing to sustainable construction practices. Take the next step in your strategic sourcing journey—invest in partnerships that drive growth and resilience in your supply chain.