Cut Costs with Container House China: The Complete Guide (2025)
Introduction: Navigating the Global Market for container house china
The global market for container houses from China presents both opportunities and challenges for international B2B buyers. As businesses and organizations seek innovative and cost-effective solutions for housing and workspace, navigating the complexities of sourcing high-quality container houses becomes paramount. This guide delves into the various types of container houses available, their diverse applications across industries, and essential considerations for supplier vetting. By addressing the key challenge of ensuring quality and compliance, we empower buyers from regions such as Africa, South America, the Middle East, and Europe—including countries like Mexico and Nigeria—to make informed purchasing decisions.
Understanding the intricacies of container house sourcing is crucial for businesses aiming to optimize their investments. This comprehensive guide will provide insights into pricing structures, material quality, design options, and logistical considerations. Additionally, we will outline best practices for assessing suppliers, ensuring that buyers can identify reliable partners who align with their specific needs.
Whether you’re looking for sustainable housing solutions, portable office spaces, or customized designs, this guide equips you with the knowledge to navigate the global market effectively. With actionable insights and a focus on strategic sourcing, international B2B buyers can confidently engage with the container house market in China, paving the way for successful projects and partnerships.
Understanding container house china Types and Variations
Type Name | Key Distinguishing Features | Primary B2B Applications | Brief Pros & Cons for Buyers |
---|---|---|---|
Standard Container House | Typically made from 20ft or 40ft containers; modular design; customizable interiors | Housing, offices, pop-up shops | Pros: Cost-effective, quick assembly; Cons: Limited space unless combined. |
Luxury Container House | High-end finishes, larger layouts, often multi-story; includes amenities like plumbing and electrical | High-end residential, boutique hotels | Pros: Attractive, premium quality; Cons: Higher initial investment. |
Eco-Friendly Container House | Built using sustainable materials, energy-efficient designs; often includes green roofs | Eco-lodges, sustainable housing projects | Pros: Reduced environmental impact; Cons: Potentially higher costs for materials. |
Mobile Container House | Designed for mobility; lightweight, often on trailers; easily transportable | Temporary housing, disaster relief, events | Pros: Flexibility in location; Cons: May lack durability in extreme weather. |
Office Container House | Designed specifically for office use; includes workspaces, meeting rooms, and utilities | Construction sites, remote offices | Pros: Quick setup, functional design; Cons: May require additional permits. |
What Are the Characteristics of Standard Container Houses?
Standard container houses are primarily constructed from 20ft or 40ft shipping containers. Their modular design allows for easy customization, making them suitable for various applications such as housing and temporary offices. B2B buyers should consider the ease of assembly and cost-effectiveness, as these structures can be delivered and set up quickly. However, space limitations may necessitate combining multiple units for larger projects.
Why Choose Luxury Container Houses?
Luxury container houses offer a high-end alternative with superior finishes and larger layouts, often designed to accommodate multiple stories. These structures typically come equipped with modern amenities, including plumbing and electrical systems, making them ideal for high-end residential projects or boutique hotels. B2B buyers should weigh the attractive aesthetics and quality against the higher initial investment required.
How Do Eco-Friendly Container Houses Stand Out?
Eco-friendly container houses are designed with sustainability in mind, utilizing green materials and energy-efficient features. These houses often incorporate elements like green roofs and solar panels, making them perfect for eco-lodges and sustainable housing initiatives. Buyers focused on reducing their environmental footprint will find these options appealing, although they may face higher costs for eco-friendly materials.
What Are the Benefits of Mobile Container Houses?
Mobile container houses are crafted for flexibility, often built on trailers for easy transport. These units are ideal for temporary housing solutions, disaster relief, or events where mobility is crucial. While they offer significant advantages in location flexibility, buyers must consider the potential downsides, such as durability issues in extreme weather conditions.
Why Are Office Container Houses a Practical Choice?
Office container houses are specifically designed for workspace functionality, featuring dedicated workspaces, meeting rooms, and necessary utilities. They are particularly useful for construction sites or remote locations needing quick office setups. B2B buyers should note the rapid deployment and utility of these structures, but also be aware of possible regulatory requirements for permits and zoning.
Related Video: China Expandable container house —10 minutes one house!
Key Industrial Applications of container house china
Industry/Sector | Specific Application of container house china | Value/Benefit for the Business | Key Sourcing Considerations for this Application |
---|---|---|---|
Construction & Housing | Temporary or permanent housing for workers | Reduces construction time and costs, enhances mobility | Quality of materials, customization options, and delivery times |
Education & Training | Mobile classrooms and training facilities | Flexible learning environments, quick setup and relocation | Compliance with local regulations, space requirements, and durability |
Disaster Relief & Humanitarian Aid | Emergency shelters and medical facilities | Rapid deployment in crisis situations, cost-effective solutions | Logistics for transport, adaptability to harsh conditions, and safety standards |
Hospitality & Tourism | Unique accommodation solutions (hotels, lodges) | Differentiates offerings, attracts eco-conscious travelers | Design aesthetics, sustainability certifications, and local market trends |
Retail & Commercial Spaces | Pop-up shops and kiosks | Low overhead costs, quick market entry, and brand visibility | Location suitability, modularity, and branding opportunities |
How Are Container Houses Used in Construction & Housing?
In the construction and housing sector, container houses from China serve as both temporary and permanent housing solutions for workers in remote locations, such as mining sites or large construction projects. They significantly reduce construction time and costs while providing a mobile and adaptable living space. Buyers should consider the quality of materials used, customization options for layout and amenities, and delivery times to ensure that the housing meets the project’s specific requirements.
What Role Do Container Houses Play in Education & Training?
Container houses are increasingly used as mobile classrooms and training facilities, particularly in regions where traditional infrastructure is lacking. These structures provide flexible learning environments that can be quickly set up and relocated as needed. For international buyers, key considerations include compliance with local educational regulations, specific space requirements for various educational activities, and the durability of the containers to withstand local weather conditions.
How Are Container Houses Beneficial for Disaster Relief & Humanitarian Aid?
In the context of disaster relief and humanitarian aid, container houses can be rapidly deployed as emergency shelters or medical facilities in crisis situations. Their cost-effectiveness and ease of transport make them ideal for NGOs and governments responding to natural disasters or humanitarian crises. When sourcing these solutions, buyers should focus on logistics for transport, the adaptability of the containers to various environments, and adherence to safety standards to ensure the well-being of occupants.
Why Are Container Houses Popular in Hospitality & Tourism?
The hospitality and tourism industry is leveraging container houses to create unique accommodation solutions, such as boutique hotels and eco-lodges. These innovative structures not only differentiate offerings but also attract eco-conscious travelers looking for sustainable lodging options. Buyers should pay attention to design aesthetics, sustainability certifications, and local market trends to ensure that their investment aligns with consumer preferences and regulations.
How Can Container Houses Be Used in Retail & Commercial Spaces?
Container houses are also being utilized as pop-up shops and kiosks, providing businesses with low overhead costs and quick market entry. This flexibility allows brands to test new markets or locations without significant financial commitment. Key sourcing considerations for international buyers include the suitability of the location for their target audience, the modularity of the design for easy relocation, and opportunities for branding to enhance visibility and customer engagement.
Related Video: From Waste to Wonder: The Surprising Uses of Carbon Dioxide
3 Common User Pain Points for ‘container house china’ & Their Solutions
Scenario 1: Navigating Quality Assurance Challenges in Container Housing
The Problem:
B2B buyers in regions like Africa and South America often face significant challenges regarding the quality and durability of container houses sourced from China. Many buyers report inconsistencies in materials and construction standards. This can lead to costly repairs, safety hazards, and dissatisfaction among end-users, especially in areas with extreme weather conditions. The lack of clear quality assurance processes can leave buyers feeling uncertain about the longevity and safety of their investments.
The Solution:
To mitigate these quality assurance challenges, buyers should prioritize establishing robust relationships with reputable manufacturers. Conducting thorough due diligence is essential; this includes checking for certifications, such as ISO standards, and visiting production facilities if possible. It’s also beneficial to request samples of materials and detailed specifications before placing large orders. Collaborating with third-party inspection services can further ensure that quality standards are met throughout the production process. Establishing clear communication regarding quality expectations and penalties for non-compliance in contracts can also safeguard against potential issues.
Scenario 2: Overcoming Delivery Delays and Logistics Issues
The Problem:
International buyers often encounter logistical challenges when importing container houses from China, including unexpected delays in shipping and customs clearance. These delays can disrupt project timelines, especially in construction and housing initiatives that are time-sensitive. Buyers in the Middle East and Europe have particularly noted issues related to the coordination of shipping schedules and the complexities of navigating customs regulations.
The Solution:
To address logistics challenges, it is crucial for buyers to engage with experienced logistics partners who specialize in international shipping of construction materials. Buyers should inquire about the shipping process, including estimated delivery times, and develop a comprehensive timeline that includes buffer periods for potential delays. Additionally, understanding the customs regulations of the destination country is vital; working with customs brokers can streamline this process. Implementing a tracking system for shipments can also enhance visibility and allow buyers to proactively manage any potential delays, thus keeping projects on track.
Scenario 3: Managing Compliance with Local Building Regulations
The Problem:
Container houses must comply with local building codes and regulations, which can vary significantly across regions. Buyers in Europe and Africa may find themselves struggling to navigate these legal requirements, leading to potential fines, project stoppages, or even legal actions. The challenge is compounded when sourcing from a foreign manufacturer that may not be familiar with local standards.
The Solution:
To effectively manage compliance with local building regulations, buyers should conduct thorough research into the specific codes applicable in their regions before finalizing any purchases. Consulting with local architects or construction professionals can provide invaluable insights into the regulatory landscape. It is also advisable to engage with manufacturers who have experience exporting to the buyer’s country and are knowledgeable about local compliance requirements. Buyers should insist on receiving all necessary documentation related to building codes, such as structural integrity reports and fire safety certifications, to ensure that their container houses meet the required standards upon arrival. This proactive approach can save time and resources while ensuring a smooth integration into the local market.
Strategic Material Selection Guide for container house china
When selecting materials for container houses in China, international B2B buyers must consider various factors that influence performance, durability, and compliance with regional standards. Here, we analyze four common materials used in container house construction: steel, aluminum, wood, and composite materials. Each material has unique properties, advantages, and disadvantages that can impact the overall success of a project.
What Are the Key Properties of Steel for Container Houses?
Steel is the most widely used material for container houses due to its strength and durability. It has a high temperature and pressure rating, making it suitable for various climates. Steel is also resistant to pests and rot, which is crucial in regions with high humidity or insect activity. However, it is susceptible to corrosion if not properly treated, particularly in coastal areas.
Pros and Cons of Steel:
– Pros: High strength-to-weight ratio, excellent durability, and fire resistance.
– Cons: Higher initial cost and weight compared to other materials; requires protective coatings to prevent rust.
Impact on Application:
Steel’s high tensile strength allows it to withstand harsh weather conditions, making it ideal for regions prone to storms or heavy winds. However, buyers must ensure that the steel used complies with international standards like ASTM or DIN to guarantee quality.
How Does Aluminum Compare for Container House Construction?
Aluminum is another popular choice for container houses due to its lightweight nature and resistance to corrosion. It is particularly advantageous in regions with high moisture levels, as it does not rust. Aluminum is also recyclable, making it an environmentally friendly option.
Pros and Cons of Aluminum:
– Pros: Lightweight, corrosion-resistant, and easy to work with.
– Cons: Lower strength compared to steel and can be more expensive.
Impact on Application:
Aluminum’s lightweight properties make it suitable for modular designs and easy transportation. However, B2B buyers should be aware of the structural limitations and ensure that the design accounts for aluminum’s lower load-bearing capacity.
What Are the Advantages of Using Wood in Container Houses?
Wood offers a natural aesthetic and excellent insulation properties, making it a popular choice for interior finishes in container houses. It is readily available and can be sourced sustainably, appealing to environmentally conscious buyers.
Pros and Cons of Wood:
– Pros: Good thermal insulation, aesthetic appeal, and renewable resource.
– Cons: Susceptible to rot, pests, and fire; requires regular maintenance.
Impact on Application:
Wood is particularly suitable for interior applications and can enhance the comfort of living spaces. However, international buyers must ensure that the wood complies with local building codes and standards to prevent issues related to moisture and pests.
Why Consider Composite Materials for Container Houses?
Composite materials, such as fiberglass or reinforced plastics, are gaining popularity in container house construction due to their versatility and strength. These materials can be engineered to provide specific properties, such as enhanced insulation or fire resistance.
Pros and Cons of Composite Materials:
– Pros: Lightweight, customizable properties, and resistant to corrosion and decay.
– Cons: Higher manufacturing complexity and cost; may not be as widely available.
Impact on Application:
Composites can be tailored for specific environmental conditions, making them suitable for diverse applications. Buyers should consider the availability and compliance with international standards when selecting composite materials.
Summary Table of Material Selection for Container Houses
Material | Typical Use Case for container house china | Key Advantage | Key Disadvantage/Limitation | Relative Cost (Low/Med/High) |
---|---|---|---|---|
Steel | Structural framework and exterior panels | High strength and durability | Susceptible to corrosion | High |
Aluminum | Lightweight structures and facades | Corrosion-resistant | Lower strength compared to steel | Medium |
Wood | Interior finishes and insulation | Aesthetic appeal and insulation | Susceptible to rot and pests | Low |
Composite | Custom applications and insulation | Versatile and customizable | Higher cost and complexity | High |
By understanding the properties, advantages, and limitations of these materials, international B2B buyers can make informed decisions that align with their project requirements and regional standards.
In-depth Look: Manufacturing Processes and Quality Assurance for container house china
What Are the Main Stages of Manufacturing Container Houses in China?
The manufacturing process for container houses in China typically follows a series of well-defined stages: material preparation, forming, assembly, and finishing. Each stage is crucial to ensure the structural integrity and quality of the final product.
Material Preparation
The first stage involves sourcing high-quality shipping containers, which are the primary building blocks for container houses. Manufacturers usually select containers that meet specific criteria, such as structural soundness and resistance to corrosion. In addition to containers, other materials like insulation, windows, and roofing components are procured, often from local suppliers to reduce costs and lead times.
Forming
During the forming stage, containers undergo modifications to meet the design specifications. This may include cutting openings for doors and windows, reinforcing structural elements, and applying insulation materials. Advanced techniques such as CNC cutting and welding are commonly used to ensure precision and efficiency. Manufacturers may also employ robotic automation for repetitive tasks, which enhances productivity and minimizes human error.
Assembly
Once the modifications are complete, the assembly phase begins. This involves joining multiple containers together or integrating them with additional structural components. Quality assurance during this stage is vital, as improper assembly can lead to structural weaknesses. Manufacturers often utilize advanced joining techniques, including welding and bolting, to ensure stability.
Finishing
The finishing stage focuses on aesthetic and functional enhancements. This includes painting, installing fixtures, and ensuring that all systems (like plumbing and electrical) are properly integrated. Manufacturers often adhere to local and international design standards to meet buyer expectations and regulatory requirements.
How Is Quality Assurance Implemented in Container House Manufacturing?
Quality assurance (QA) is an integral part of the manufacturing process, especially for international B2B buyers who require high standards. In China, the QA process typically aligns with international standards such as ISO 9001, as well as industry-specific certifications like CE for the European market.
What International Standards Should B2B Buyers Be Aware Of?
International standards play a significant role in ensuring product quality. ISO 9001 outlines the requirements for a quality management system, emphasizing continuous improvement and customer satisfaction. For buyers from Europe, CE certification indicates that the product complies with EU safety and environmental requirements.
Additionally, other standards may apply depending on the intended use of the container house. For instance, if the structure will be used in the oil and gas sector, API (American Petroleum Institute) standards may be relevant.
What Are the Key Quality Control Checkpoints in Container House Production?
Quality control (QC) checkpoints are critical for maintaining high-quality standards throughout the manufacturing process. Common QC checkpoints include:
-
Incoming Quality Control (IQC): This involves inspecting raw materials and components upon arrival. Ensuring that materials meet specified standards is crucial for preventing defects later in the process.
-
In-Process Quality Control (IPQC): During the various manufacturing stages, ongoing inspections and tests are performed to ensure adherence to quality standards. This includes checking welds, structural integrity, and assembly accuracy.
-
Final Quality Control (FQC): Before the product is shipped, a final inspection is conducted to verify that the container house meets all specifications and standards. This may involve functional tests, such as checking plumbing and electrical systems.
What Common Testing Methods Are Used to Ensure Quality in Container Houses?
Manufacturers utilize several testing methods to ensure the quality and safety of container houses:
-
Visual Inspection: This basic yet effective method checks for visible defects in materials and assembly.
-
Non-Destructive Testing (NDT): Techniques like ultrasonic testing and magnetic particle testing assess the integrity of welds and materials without causing damage.
-
Load Testing: This involves applying weight to the structure to ensure it can withstand expected loads without failure.
-
Environmental Testing: Containers may be subjected to various environmental conditions to verify their durability and resistance to elements like moisture and temperature fluctuations.
How Can International B2B Buyers Verify Supplier Quality Control?
To ensure that suppliers adhere to quality standards, international B2B buyers can implement several verification strategies:
-
Supplier Audits: Conducting on-site audits allows buyers to assess the manufacturing process, quality control measures, and compliance with international standards firsthand.
-
Requesting Quality Reports: Suppliers should provide detailed quality reports that outline testing methods, results, and any corrective actions taken for defects.
-
Third-Party Inspections: Engaging third-party inspection services can provide an unbiased assessment of the supplier’s quality control practices and product quality.
-
Certification Verification: Buyers should verify that suppliers hold relevant certifications (like ISO 9001 and CE) and ensure that they are up to date.
What Are the QC and Certification Nuances for Buyers from Africa, South America, the Middle East, and Europe?
B2B buyers from diverse regions must be aware of specific nuances related to QC and certification. For instance:
-
Africa: Buyers may face challenges related to local regulatory compliance. It’s crucial to understand the specific building codes and regulations applicable in their country.
-
South America: Import tariffs and regulations may affect the cost and feasibility of sourcing container houses. Buyers should factor in these elements when negotiating terms.
-
Middle East: The demand for sustainable and energy-efficient designs is increasing. Buyers should ensure that their suppliers can meet these requirements.
-
Europe: Compliance with strict EU regulations is essential. Buyers should ensure that their suppliers can provide the necessary certifications and documentation to facilitate smooth import processes.
By understanding the manufacturing processes and quality assurance measures involved in container house production in China, B2B buyers can make informed decisions, ensuring they receive high-quality products that meet their specific needs and regulatory requirements.
Practical Sourcing Guide: A Step-by-Step Checklist for ‘container house china’
In the rapidly growing market for container houses, particularly from China, international B2B buyers face a unique set of challenges and opportunities. This practical sourcing guide provides a step-by-step checklist designed to streamline the procurement process, ensuring that buyers from Africa, South America, the Middle East, and Europe can make informed decisions.
Step 1: Define Your Project Requirements
Before initiating contact with suppliers, clearly outline your project requirements. This includes the intended use of the container house, size specifications, and any customization needed, such as insulation or energy efficiency features. A well-defined project scope helps in filtering suppliers who can meet your specific needs.
Step 2: Research Potential Suppliers
Conduct thorough research to identify reputable suppliers in China. Look for companies with a strong track record in manufacturing container houses, focusing on their experience, client testimonials, and industry certifications. Utilize platforms like Alibaba or Global Sources, and pay attention to suppliers’ ratings and feedback from other B2B buyers.
Step 3: Verify Supplier Certifications
Before proceeding, ensure that your potential suppliers hold the necessary certifications. Key certifications to look for include ISO 9001 for quality management systems and any local building codes relevant to container houses. These certifications not only demonstrate compliance with industry standards but also enhance trust in the supplier’s capabilities.
Step 4: Request Samples and Prototypes
To assess the quality of the container houses, request samples or prototypes. This step is crucial as it allows you to inspect the materials used, craftsmanship, and overall design. Evaluate how well the sample meets your specifications, and consider conducting a site visit if feasible, to get a firsthand look at the manufacturing process.
Step 5: Understand the Logistics and Shipping Process
Familiarize yourself with the logistics involved in importing container houses from China. This includes understanding shipping methods, costs, and delivery timelines. Additionally, inquire about the supplier’s experience with international shipping and their ability to handle customs clearance, which can significantly affect your project’s timeline.
Step 6: Negotiate Terms and Conditions
Once you have shortlisted suppliers, initiate negotiations on pricing, payment terms, and delivery schedules. Be clear about your expectations regarding warranties and after-sales support. Establishing favorable terms upfront can help mitigate risks and ensure a smoother transaction.
Step 7: Finalize the Contract
Before committing to any supplier, ensure that all agreements are documented in a formal contract. This should include detailed specifications, payment terms, delivery schedules, and penalties for non-compliance. Having a well-structured contract protects both parties and serves as a reference point throughout the project.
By following this step-by-step checklist, international B2B buyers can navigate the complexities of sourcing container houses from China effectively, ensuring a successful procurement process tailored to their unique needs.
Comprehensive Cost and Pricing Analysis for container house china Sourcing
What Are the Key Cost Components for Sourcing Container Houses from China?
When evaluating the cost structure for sourcing container houses from China, it is essential to consider several key components. These include materials, labor, manufacturing overhead, tooling, quality control (QC), logistics, and profit margins.
-
Materials: The choice of materials significantly impacts the overall cost. High-quality steel, insulation, and finishes will increase the initial expense but may provide long-term savings through durability and energy efficiency.
-
Labor: Labor costs can vary widely based on the region within China and the complexity of the construction process. Skilled labor may command higher wages, but it often results in better craftsmanship.
-
Manufacturing Overhead: This includes expenses related to factory operations such as utilities, rent, and equipment maintenance. Understanding the overhead can help buyers gauge the supplier’s pricing strategy.
-
Tooling: If customization is required, tooling costs can be a significant factor. This is particularly relevant for bespoke designs that may necessitate specialized molds or machinery.
-
Quality Control: Investing in robust QC processes ensures that the final product meets international standards. While this may add to the upfront costs, it can reduce risks associated with defects and non-compliance.
-
Logistics: Shipping costs from China to the buyer’s location can be substantial, especially for large items like container houses. Factors like distance, shipping method, and current freight rates should be carefully assessed.
-
Margin: Suppliers typically include a profit margin in their pricing, which can range from 10% to 30% depending on the complexity of the project and market competition.
How Do Price Influencers Affect Container House Sourcing?
Several factors can influence pricing when sourcing container houses from China. Understanding these can help buyers make informed decisions.
-
Volume/MOQ: Minimum order quantities (MOQs) can significantly affect unit prices. Larger orders often receive discounts, making it crucial for buyers to evaluate their needs carefully.
-
Specifications and Customization: Custom designs or specifications usually lead to higher costs due to additional materials and labor requirements. Buyers should weigh the benefits of customization against the added expenses.
-
Materials Quality and Certifications: The quality of materials and relevant certifications (like ISO or CE) can impact pricing. While premium materials may cost more upfront, they can yield better long-term performance and lower maintenance costs.
-
Supplier Factors: The supplier’s reputation, location, and production capacity can all influence pricing. Established suppliers with good track records might charge more, but the reliability can justify the expense.
-
Incoterms: Understanding the chosen Incoterms (e.g., FOB, CIF) is critical, as they dictate who is responsible for shipping and insurance costs. Buyers should clarify these terms to avoid unexpected expenses.
What Are the Best Negotiation Strategies for International B2B Buyers?
Negotiating effectively can yield significant savings for international buyers. Here are some strategies tailored for businesses in Africa, South America, the Middle East, and Europe:
-
Research and Benchmarking: Conduct thorough market research to understand typical pricing structures and cost components. This knowledge empowers buyers during negotiations.
-
Establish Clear Requirements: Clearly outline specifications, including quality standards and delivery timelines. This clarity helps suppliers provide accurate quotes and reduces misunderstandings.
-
Leverage Volume Discounts: If possible, consolidate purchases to meet MOQs or negotiate larger orders to benefit from lower per-unit costs.
-
Evaluate Total Cost of Ownership: Consider not just the purchase price but also maintenance, operation, and potential resale value when evaluating offers. A higher upfront cost may be justified by lower long-term expenses.
-
Build Relationships: Cultivating a strong relationship with suppliers can lead to better terms and more favorable pricing in the long run.
What Should Buyers Consider Regarding Pricing Nuances in Different Regions?
International B2B buyers must be aware of regional pricing nuances when sourcing container houses from China. Factors such as currency fluctuations, import tariffs, and local economic conditions can all impact final costs. For instance, buyers from Nigeria may face different tariffs compared to those in Mexico, affecting their overall budget.
Additionally, understanding local regulations and compliance requirements can prevent costly delays and fines. It is advisable to consult with local experts or legal advisors to navigate these complexities effectively.
Disclaimer on Pricing Estimates
It is crucial to note that the prices mentioned in this analysis are indicative and can vary based on numerous factors, including market conditions and specific supplier negotiations. Buyers should conduct their own due diligence and obtain detailed quotes before proceeding with purchases.
Alternatives Analysis: Comparing container house china With Other Solutions
When considering the acquisition of modular housing solutions, international B2B buyers have various options to explore. One prevalent choice is the “Container House China,” which offers unique benefits but may not always be the best fit for every project. Understanding alternative solutions can help buyers make informed decisions based on their specific needs, geographical location, and budget constraints.
Comparison Aspect | Container House China | Prefabricated Modular Homes | Traditional Brick-and-Mortar Construction |
---|---|---|---|
Performance | High durability, weather-resistant | Good insulation, customizable | Strong structural integrity, long-lasting |
Cost | Lower initial investment | Moderate cost, varies with customization | Higher upfront costs due to labor and materials |
Ease of Implementation | Quick setup, minimal site work | Moderate setup time, requires foundation | Lengthy construction time, extensive site work |
Maintenance | Low maintenance, durable materials | Moderate maintenance depending on materials | High maintenance, potential for structural repairs |
Best Use Case | Temporary housing, disaster relief | Residential, commercial, and industrial applications | Permanent housing, large-scale projects |
What Are the Advantages of Prefabricated Modular Homes?
Prefabricated modular homes are constructed in sections in a factory setting and then transported to the site for assembly. They offer a good balance of cost and performance, with customization options that can cater to specific buyer needs. However, they require a foundational setup and may take longer to install than container houses. Buyers may find this option appealing for residential or commercial projects where aesthetics and design are a priority.
How Does Traditional Brick-and-Mortar Construction Compare?
Traditional brick-and-mortar construction is well-known for its durability and long-term viability. It provides a sense of permanence and can accommodate larger projects. However, the costs are significantly higher due to labor and raw materials, and the construction timeline can extend several months. This method is best suited for buyers looking to invest in permanent structures or large-scale developments.
Conclusion: How Can B2B Buyers Choose the Right Solution?
When selecting the most appropriate housing solution, B2B buyers should evaluate their specific project requirements, budget constraints, and intended use. Container House China offers a cost-effective, quick-to-implement option, particularly suitable for temporary housing and urgent needs. In contrast, prefabricated modular homes and traditional brick-and-mortar construction provide alternative benefits in terms of aesthetics and permanence. Each option comes with its own set of pros and cons, and understanding these will empower buyers to make the best choice for their unique circumstances.
Essential Technical Properties and Trade Terminology for container house china
What Are the Key Technical Properties of Container Houses from China?
When considering container houses from China, understanding the technical specifications is crucial for international B2B buyers. These properties not only influence the quality and durability of the structure but also affect the overall cost-effectiveness and compliance with local regulations. Here are some essential properties to consider:
1. Material Grade: What Should You Look For?
Container houses are primarily constructed from corten steel, which is known for its weather resistance and strength. The grade of steel used can significantly impact the longevity and structural integrity of the container. For B2B buyers, selecting a high-grade material (such as S355 or S420) ensures that the container can withstand harsh weather conditions, particularly in regions like Africa and South America where environmental factors can be extreme.
2. Tolerance Levels: Why Are They Important?
Tolerance levels refer to the permissible limits of variation in the dimensions of the container. A typical tolerance for container houses is ±5mm. Maintaining tight tolerances is vital for ensuring that the containers fit together seamlessly during assembly. For B2B buyers, this translates to reduced labor costs and quicker installation times, making it essential to verify these specifications with suppliers.
3. Insulation Properties: How Do They Affect Energy Efficiency?
The insulation properties of a container house are critical for energy efficiency, particularly in extreme climates. Look for containers that use high-quality insulation materials, such as polyurethane or polystyrene, with R-values that indicate thermal resistance. For buyers, this is not only about comfort but also about reducing long-term energy costs, making it a key consideration in your purchasing decision.
4. Load-Bearing Capacity: What Are the Standards?
Understanding the load-bearing capacity of a container house is essential for its intended use. Typically, a standard 20-foot container can support a maximum payload of 28,000 lbs (12,700 kg). For B2B buyers, ensuring that the container meets local building codes and standards is crucial for safety and compliance, especially in commercial or industrial applications.
5. Corrosion Resistance: Why Is It Essential?
Corrosion resistance is a vital property for container houses, particularly in coastal or humid environments. Containers should ideally have a protective coating or be made from weather-resistant materials to prevent rust and degradation. For international buyers, investing in containers with high corrosion resistance can minimize maintenance costs and prolong the lifespan of the structure.
What Are Common Trade Terms Used in Container House Transactions?
Understanding trade terminology is essential for smooth negotiations and transactions. Here are some commonly used terms in the container house industry:
1. OEM (Original Equipment Manufacturer): What Does It Mean?
OEM refers to companies that produce parts or equipment that may be marketed by another manufacturer. In the context of container houses, it indicates that the manufacturer can customize the design or features according to the buyer’s specifications. This term is critical for B2B buyers looking for tailored solutions.
2. MOQ (Minimum Order Quantity): How Does It Impact Your Purchase?
MOQ is the smallest quantity of a product that a supplier is willing to sell. For container houses, this can vary significantly between manufacturers. Understanding the MOQ is essential for buyers to ensure that they can meet their project needs without overcommitting financially.
3. RFQ (Request for Quotation): Why Is It Important?
An RFQ is a document issued by a buyer to solicit price quotes from suppliers. It typically includes detailed specifications and quantities needed. For international buyers, issuing an RFQ can help streamline the procurement process, ensuring that all potential suppliers provide comparable pricing and terms.
4. Incoterms: What Are They and Why Do They Matter?
Incoterms are international commercial terms that define the responsibilities of buyers and sellers in international transactions. They clarify aspects like shipping costs, insurance, and customs clearance. For B2B buyers, understanding Incoterms is crucial for avoiding unexpected costs and ensuring smooth logistics.
5. Lead Time: How Does It Affect Your Project Timeline?
Lead time refers to the amount of time from placing an order until it is delivered. In the container house industry, this can vary based on production capacity and shipping logistics. For international buyers, knowing the lead time helps in project planning and managing client expectations effectively.
By familiarizing yourself with these technical properties and trade terms, you can make informed purchasing decisions and ensure successful transactions in the container house market from China.
Navigating Market Dynamics and Sourcing Trends in the container house china Sector
What Are the Current Market Dynamics and Key Trends in the Container House Sector in China?
The container house sector in China is witnessing a significant transformation driven by various global trends. The increasing demand for affordable housing solutions, particularly in rapidly urbanizing regions of Africa, South America, the Middle East, and Europe, is a primary driver. With the rise in urban migration and the need for sustainable living spaces, container houses are emerging as an attractive option. Additionally, technological advancements in construction methods and materials are making container houses more versatile and appealing to B2B buyers.
Emerging technologies such as modular construction and digital design tools are reshaping sourcing strategies. Buyers can leverage Building Information Modeling (BIM) to visualize projects before execution, allowing for better planning and resource allocation. Moreover, the integration of smart technologies in container homes is gaining traction, catering to the growing demand for energy-efficient and technologically equipped living spaces. This trend is particularly relevant for buyers in Europe and the Middle East, where energy efficiency standards are stringent.
International B2B buyers must also stay informed about the evolving regulatory landscape. Countries are increasingly adopting building codes that emphasize sustainability and resilience, which can affect procurement strategies. Understanding these dynamics is crucial for buyers looking to source container houses that meet both local regulations and international standards.
How Can Sustainability and Ethical Sourcing Impact Your Container House Procurement Strategy?
Sustainability is no longer just a buzzword; it is a critical factor influencing procurement decisions in the container house sector. The environmental impact of construction materials and practices is under scrutiny, prompting buyers to prioritize sustainable options. Container houses, often constructed from repurposed materials, inherently offer a lower carbon footprint compared to traditional building methods.
Ethical sourcing is equally important, as buyers are increasingly aware of the social implications of their procurement choices. Ensuring that suppliers adhere to fair labor practices and environmental regulations can enhance a company’s reputation and align with corporate social responsibility goals. Buyers should seek out manufacturers in China that provide transparency about their supply chains and can demonstrate compliance with international labor standards.
Additionally, certifications such as ISO 14001 (Environmental Management) and LEED (Leadership in Energy and Environmental Design) can serve as indicators of a supplier’s commitment to sustainability. By prioritizing partnerships with certified manufacturers, B2B buyers can ensure that their sourcing strategies align with global sustainability goals.
What Is the Brief Evolution of the Container House Sector in China?
The container house sector in China has evolved dramatically over the past two decades. Initially, container homes were seen as temporary solutions for housing shortages during construction booms and natural disasters. However, as the benefits of modular construction became apparent, the perception shifted towards viewing container houses as viable long-term housing solutions.
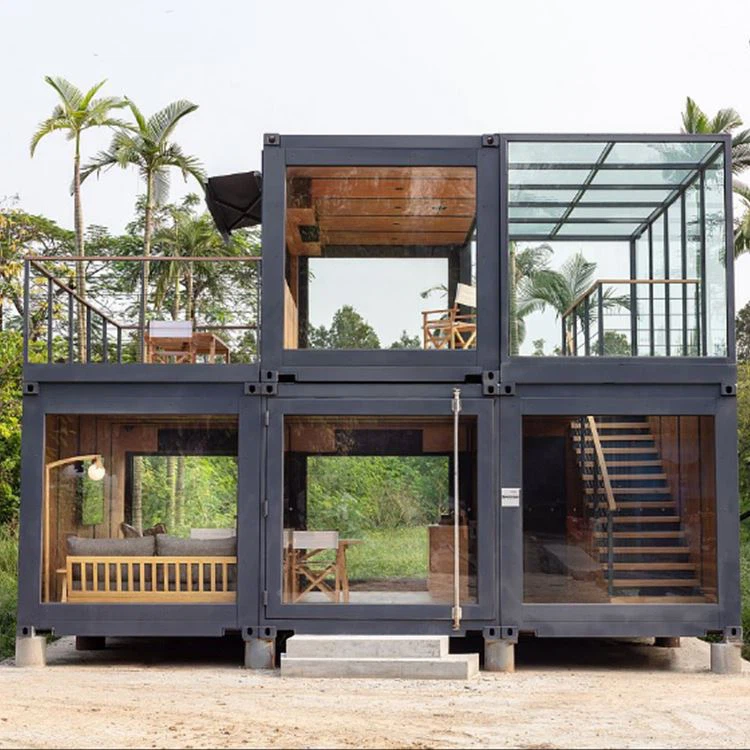
A stock image related to container house china.
The introduction of innovative design practices and sustainable materials has further propelled the sector’s growth. Today, container houses are recognized not only for their affordability but also for their flexibility in design and functionality. This evolution has opened up new markets for international B2B buyers, particularly in developing regions where cost-effective housing solutions are urgently needed. As the sector continues to mature, it offers promising opportunities for buyers looking to invest in modern, sustainable living spaces.
Frequently Asked Questions (FAQs) for B2B Buyers of container house china
-
How do I ensure the quality of container houses sourced from China?
To guarantee quality when sourcing container houses from China, conduct thorough due diligence on potential suppliers. Request samples or visit factories if feasible. Verify certifications, such as ISO or CE, which indicate compliance with international standards. Additionally, consider hiring a third-party inspection service to assess the quality of materials and construction before shipment. Establish clear quality assurance (QA) protocols in your purchase agreement to mitigate risks. -
What customization options are available for container houses from China?
Most Chinese manufacturers offer a range of customization options for container houses, including size, layout, and interior finishes. You can also request specific features such as insulation, plumbing, and electrical installations tailored to your regional climate and needs. When discussing customization, provide detailed specifications to ensure the manufacturer understands your requirements. It’s beneficial to have a clear timeline and budget in mind to facilitate the design process. -
What are the typical minimum order quantities (MOQ) for container houses from Chinese suppliers?
Minimum order quantities (MOQ) for container houses can vary widely depending on the supplier and the complexity of the design. Generally, MOQs can range from one unit for standard models to several units for custom designs. It’s advisable to discuss your needs directly with suppliers, as many are willing to negotiate MOQs based on your purchasing power and long-term partnership potential. -
What payment terms should I expect when sourcing container houses from China?
Payment terms for container houses typically involve an upfront deposit, usually around 30%, with the balance due upon completion or before shipping. Some suppliers may offer flexible payment options, including letters of credit or escrow services for added security. It’s essential to negotiate these terms upfront and ensure that they are clearly documented in your purchase agreement to protect your interests. -
How do I vet suppliers for container houses in China?
Vetting suppliers involves researching their business credentials, customer reviews, and production capabilities. Utilize platforms like Alibaba, Global Sources, or trade shows to find reputable manufacturers. Request references from previous clients and check their response times and communication skills. Additionally, consider visiting their production facilities or hiring a local agent to conduct on-site evaluations, ensuring that they meet your standards for reliability and quality. -
What logistics considerations should I keep in mind when importing container houses from China?
When importing container houses, consider logistics factors such as shipping methods, lead times, and customs clearance. Choose between sea freight for cost-effectiveness or air freight for speed, depending on your urgency. Ensure that you have all necessary documentation, including bills of lading and import permits, to facilitate smooth customs clearance in your country. Working with a freight forwarder can simplify the logistics process and help avoid common pitfalls. -
What are the common challenges faced when sourcing container houses from China?
Challenges may include language barriers, time zone differences, and varying quality standards. Miscommunication can lead to errors in specifications, while longer lead times can impact project schedules. To overcome these challenges, establish clear communication channels and use translation services if necessary. Building strong relationships with suppliers through regular updates and feedback can also help mitigate issues and foster better collaboration. -
How can I ensure compliance with local building regulations when importing container houses?
To ensure compliance with local building regulations, research the specific requirements in your country or region. This may involve obtaining permits, adhering to safety standards, and ensuring that the container houses meet zoning laws. Collaborate with local architects or engineers who understand these regulations and can assist in adapting the designs to meet compliance. Engaging with local authorities early in the process can also provide clarity on necessary inspections and approvals.
Important Disclaimer & Terms of Use
⚠️ Important Disclaimer
The information provided in this guide, including content regarding manufacturers, technical specifications, and market analysis, is for informational and educational purposes only. It does not constitute professional procurement advice, financial advice, or legal advice.
While we have made every effort to ensure the accuracy and timeliness of the information, we are not responsible for any errors, omissions, or outdated information. Market conditions, company details, and technical standards are subject to change.
B2B buyers must conduct their own independent and thorough due diligence before making any purchasing decisions. This includes contacting suppliers directly, verifying certifications, requesting samples, and seeking professional consultation. The risk of relying on any information in this guide is borne solely by the reader.
Strategic Sourcing Conclusion and Outlook for container house china
In the evolving landscape of container housing, strategic sourcing stands out as a crucial element for international B2B buyers. By leveraging China’s manufacturing capabilities, buyers from regions such as Africa, South America, the Middle East, and Europe can access innovative, cost-effective solutions tailored to their unique needs. The versatility and sustainability of container houses offer not just immediate shelter solutions but also long-term investment potential in rapidly urbanizing areas.
What Are the Key Takeaways for B2B Buyers in Container Housing?
Understanding the importance of supplier reliability, product quality, and compliance with local regulations is essential for successful sourcing. Buyers must prioritize establishing strong partnerships with reputable manufacturers to ensure transparency and efficiency throughout the procurement process. Additionally, considering environmental impact and sustainability practices will not only enhance brand reputation but also align with global trends towards eco-friendly construction.
How Can International Buyers Prepare for Future Opportunities?
As the demand for container houses continues to grow, particularly in developing markets, now is the time for B2B buyers to act. Engaging in proactive sourcing strategies and exploring diverse suppliers will position businesses to capitalize on emerging trends. By investing in container housing solutions today, buyers can secure a competitive edge and contribute to sustainable development in their regions. Embrace the opportunity to innovate and lead in the container housing market, setting the stage for a resilient future.