Cut Costs with Foam Cutter China: The Complete Buying Guide (2025)
Introduction: Navigating the Global Market for foam cutter china
When it comes to sourcing reliable foam cutters from China, international B2B buyers face the challenge of navigating a complex market filled with numerous suppliers and varying product quality. Understanding the nuances of foam cutter technologies—such as the differences between manual and automatic models, and the specific applications they serve—can significantly impact procurement decisions. This guide aims to demystify the landscape of foam cutters, providing insights into the types available, their applications across industries, and key considerations for supplier vetting.
By exploring critical factors such as cost, material compatibility, and manufacturer reliability, this comprehensive resource equips buyers from Africa, South America, the Middle East, and Europe—including regions like Thailand and Egypt—with the knowledge needed to make informed purchasing decisions. Whether you are looking to optimize production processes or enhance product offerings, this guide serves as a roadmap to effectively source foam cutters that meet your business needs. Get ready to streamline your procurement strategy and partner with the right suppliers to elevate your operations in the competitive foam industry.
Understanding foam cutter china Types and Variations
Type Name | Key Distinguishing Features | Primary B2B Applications | Brief Pros & Cons for Buyers |
---|---|---|---|
Hot Wire Foam Cutter | Utilizes heated wire to cut through foam; precise cuts | Packaging, prototyping, arts and crafts | Pros: High precision; Cons: Limited to softer foams. |
CNC Foam Cutter | Computer-controlled for intricate designs | Aerospace, automotive, and architectural models | Pros: Automation and consistency; Cons: Higher initial investment. |
Handheld Foam Cutter | Portable, manual operation; versatile | Small-scale projects, DIY, and crafting | Pros: Cost-effective; Cons: Labor-intensive, less precision. |
Vertical Foam Cutter | Vertical cutting mechanism; efficient for large sheets | Furniture manufacturing, insulation panels | Pros: Space-saving; Cons: Limited mobility. |
Laser Foam Cutter | Uses laser technology for high-speed cutting | Electronics, medical packaging, and custom designs | Pros: Clean cuts and minimal waste; Cons: Expensive maintenance. |
What are the Key Features of Hot Wire Foam Cutters?
Hot wire foam cutters are designed to slice through softer foam materials using a heated wire. This type of cutter is particularly useful in industries such as packaging and prototyping, where precision is crucial. When considering a hot wire cutter, buyers should evaluate the wire gauge and temperature control settings, as these factors directly affect cutting speed and foam compatibility. While these cutters offer high precision, they are limited to softer foams, which may restrict their applicability in certain projects.
How Do CNC Foam Cutters Enhance Production Efficiency?
CNC foam cutters leverage computer numerical control technology to automate the cutting process, allowing for intricate designs and patterns. This type of foam cutter is widely used in sectors like aerospace and automotive, where accuracy and repeatability are essential. B2B buyers should consider the software compatibility and the machine’s cutting speed when investing in CNC foam cutters. While the initial investment may be higher, the efficiency and consistency gained can lead to significant long-term cost savings.
Why Choose Handheld Foam Cutters for Small Projects?
Handheld foam cutters are portable and versatile, making them ideal for small-scale projects, DIY tasks, and crafting. These tools are typically more affordable and accessible for businesses that may not require high-volume production. However, buyers should be aware that while they are cost-effective, handheld cutters can be labor-intensive and may not deliver the same level of precision as other types. This trade-off is essential for businesses focused on smaller, less complex foam cutting tasks.
What Advantages Do Vertical Foam Cutters Offer?
Vertical foam cutters are designed with a vertical cutting mechanism that allows for efficient processing of large foam sheets. This design is particularly advantageous in furniture manufacturing and insulation panel production, where space-saving and efficiency are paramount. When purchasing a vertical foam cutter, businesses should evaluate the cutter’s capacity and the ease of changing cutting blades. Although these machines save space, their stationary nature may limit mobility and flexibility in the workspace.
How Do Laser Foam Cutters Stand Out in Precision Cutting?
Laser foam cutters utilize advanced laser technology to provide high-speed and precise cutting capabilities. This method is particularly beneficial in industries such as electronics and medical packaging, where clean cuts and minimal waste are critical. Buyers should assess the cutter’s wattage and the types of foam it can handle, as this affects operational costs and cutting quality. Despite their advantages, laser foam cutters come with higher maintenance costs, which should be factored into the overall budget.
Related Video: DIY Hot Wire Foam Cutter, What It Does, and How To Cut an Airfoil
Key Industrial Applications of foam cutter china
Industry/Sector | Specific Application of foam cutter china | Value/Benefit for the Business | Key Sourcing Considerations for this Application |
---|---|---|---|
Furniture Manufacturing | Precision cutting of PU foam for cushions and upholstery | Enhances product quality and comfort, reduces waste material | Machine specifications, cutting precision, and material compatibility |
Automotive Industry | Foam cutting for sound insulation panels | Improves vehicle acoustics, enhances passenger comfort | Compliance with automotive standards, durability, and weight considerations |
Packaging Solutions | Custom foam inserts for protective packaging | Ensures product safety during transport, reduces damage | Material type (EVA, PE), customization options, and cost-effectiveness |
Construction Industry | Cutting foam for insulation materials in buildings | Increases energy efficiency, reduces heating/cooling costs | Thermal properties, fire resistance standards, and sourcing from reliable suppliers |
Medical Sector | Foam cutting for ergonomic support in medical devices | Improves patient comfort and support, enhances product usability | Biocompatibility, compliance with health regulations, and customization needs |
How is Foam Cutter China Used in Furniture Manufacturing?
In the furniture manufacturing sector, foam cutters from China are utilized for precision cutting of polyurethane (PU) foam, essential for creating cushions and upholstery. This application not only enhances the quality and comfort of the final products but also minimizes waste material through accurate cuts. International buyers, particularly from regions like Africa and Europe, should prioritize sourcing machines that offer high cutting precision and are compatible with various foam types to ensure optimal production efficiency.
What Role Does Foam Cutting Play in the Automotive Industry?
In the automotive industry, foam cutters are employed to produce sound insulation panels that significantly improve vehicle acoustics. By integrating these panels, manufacturers can enhance passenger comfort, which is increasingly demanded by consumers. Buyers from South America and the Middle East should consider the compliance of foam cutting machines with automotive standards, focusing on durability and weight specifications to meet industry requirements.
How is Foam Cutting Essential for Packaging Solutions?
Foam cutting technology is vital in the packaging sector for creating custom foam inserts that protect products during transport. These inserts ensure that items are secured and cushioned, reducing the risk of damage. For B2B buyers, especially in Europe and Africa, it is crucial to evaluate the type of foam used (such as EVA or PE), the customization options available, and the overall cost-effectiveness of the foam cutting solutions to enhance their packaging strategies.
Why is Foam Cutting Important in the Construction Industry?
In construction, foam cutters are used to create insulation materials that improve energy efficiency in buildings. By using cutting-edge foam technology, companies can significantly reduce heating and cooling costs, making their projects more sustainable. International buyers should pay attention to the thermal properties and fire resistance standards of the foam materials, ensuring they partner with reliable suppliers to meet stringent regulations.
How Does Foam Cutting Benefit the Medical Sector?
The medical sector utilizes foam cutting for producing ergonomic supports in medical devices, enhancing patient comfort and usability. This application is critical as it directly impacts patient care and recovery. Buyers from diverse regions must ensure that the foam materials are biocompatible and comply with health regulations, while also considering customization needs to cater to specific medical applications.
3 Common User Pain Points for ‘foam cutter china’ & Their Solutions
Scenario 1: Difficulty in Sourcing Quality Foam Cutters from China
The Problem: B2B buyers often face significant challenges when sourcing foam cutters from China due to the overwhelming number of suppliers and varying product quality. Buyers might struggle to differentiate between reputable manufacturers and those that do not meet international standards. This can lead to purchasing equipment that is subpar, resulting in poor cutting performance, increased maintenance costs, and ultimately, financial losses. Additionally, language barriers and lack of local support can complicate communication and after-sales service.
The Solution: To effectively source quality foam cutters from China, buyers should begin by conducting thorough research on potential suppliers. Utilize platforms like Alibaba, Made-in-China, or Global Sources to identify manufacturers with good reviews and established reputations. Look for suppliers that have international certifications (e.g., ISO 9001) and significant export experience. Engage in direct communication through video calls to discuss technical specifications and inquire about warranty and support services. Request samples before making bulk purchases, and consider using third-party inspection services to ensure the product meets your specifications and quality standards.
Scenario 2: Understanding Technical Specifications and Features
The Problem: Many international buyers struggle to understand the technical specifications and features of foam cutters, which can vary significantly between manufacturers. For instance, terms like “cutting speed,” “power consumption,” and “cutting thickness” can be confusing, leading to mismatches between the equipment’s capabilities and the buyer’s actual needs. This misunderstanding can result in purchasing a foam cutter that does not meet operational requirements, leading to inefficiencies in production.
The Solution: To overcome this knowledge gap, buyers should invest time in understanding the essential specifications that impact their operations. Create a checklist of required features based on your specific foam cutting needs, such as material type (PU, EVA, etc.), desired cutting precision, and production volume. Engage with suppliers to clarify any ambiguities and ask for detailed product manuals or specification sheets. Participating in online forums or industry groups can also provide valuable insights into best practices and common pitfalls. Additionally, consider consulting with industry experts or hiring a local consultant who understands the market and can provide tailored advice.
Scenario 3: Navigating Import Regulations and Logistics
The Problem: Importing foam cutters from China can be daunting due to complex regulations, tariffs, and logistical challenges. Buyers from regions such as Africa and South America may face additional hurdles, including customs delays and unexpected fees, which can severely disrupt production schedules and increase operational costs. The lack of knowledge about local import laws can lead to compliance issues and additional penalties.
The Solution: To navigate these challenges effectively, buyers should conduct comprehensive research on their country’s import regulations regarding machinery and equipment. Collaborating with a local customs broker or logistics expert can provide clarity on tariffs, necessary documentation, and compliance requirements. Buyers should also consider engaging with suppliers who have experience in exporting to their region, as they can often assist with logistics and documentation. Establishing a robust logistics plan that includes estimated delivery times, shipping options, and contingency plans for delays can help mitigate risks associated with importing equipment. Finally, maintaining open communication with the supplier throughout the shipping process can help ensure that any issues are addressed promptly.
Strategic Material Selection Guide for foam cutter china
What Are the Key Materials Used in Foam Cutters from China?
When selecting a foam cutter from China, understanding the materials used in its construction is crucial for ensuring optimal performance and longevity. Here, we analyze four common materials—Polyurethane (PU), Ethylene Vinyl Acetate (EVA), Neoprene, and Polyethylene (PE)—that are prevalent in foam cutter applications.
How Does Polyurethane (PU) Perform in Foam Cutters?
Polyurethane (PU) is a versatile material known for its excellent flexibility and durability. It can withstand a wide range of temperatures, typically from -30°C to 80°C, making it suitable for various applications. PU foam is also resistant to wear and tear, which enhances the lifespan of foam cutters.
Pros: PU offers high resilience and cushioning properties, making it ideal for applications requiring shock absorption. It is lightweight and can be manufactured in various densities, allowing customization for specific needs.
Cons: The primary drawback of PU is its sensitivity to UV light and moisture, which can lead to degradation over time. Additionally, while PU is generally cost-effective, high-performance grades can be more expensive.
Impact on Application: PU foam is compatible with a range of media, including adhesives and coatings, but care must be taken to avoid exposure to harsh chemicals.
Considerations for International Buyers: Buyers from regions such as Africa and the Middle East should ensure compliance with local regulations regarding chemical safety and environmental impact, as PU may require specific handling and disposal measures.
What Advantages Does Ethylene Vinyl Acetate (EVA) Offer?
EVA is a popular choice due to its excellent cushioning properties and resistance to stress cracking. It typically operates effectively within a temperature range of -40°C to 70°C.
Pros: EVA is lightweight, flexible, and provides good thermal insulation. Its non-toxic nature makes it suitable for applications in sensitive environments, such as packaging and children’s products.
Cons: While EVA is durable, it can be less resistant to certain chemicals compared to PU. Its cost can also be higher than traditional polyethylene options.
Impact on Application: EVA is ideal for applications requiring cushioning, such as packaging foam or protective gear, but may not be suitable for high-temperature applications.
Considerations for International Buyers: Buyers should verify compliance with international standards like ASTM D3574 for foam quality, especially in regions like Europe, where regulations may be stricter.
Why Choose Neoprene for Foam Cutters?
Neoprene is a synthetic rubber known for its excellent chemical resistance and durability. It can handle temperatures ranging from -40°C to 120°C, making it suitable for various industrial applications.
Pros: Neoprene is highly resistant to oil, ozone, and weathering, which enhances its longevity. Its flexibility and cushioning properties are also notable, making it suitable for applications requiring impact absorption.
Cons: The main limitation of neoprene is its higher cost compared to EVA and PE. Additionally, it can be heavier, which may affect the overall weight of the foam cutter.
Impact on Application: Neoprene is particularly effective in applications involving exposure to oils and chemicals, making it a preferred choice in automotive and industrial settings.
Considerations for International Buyers: Buyers should consider the specific chemical compatibility of neoprene with the intended application and ensure compliance with local material safety standards.
What Role Does Polyethylene (PE) Play in Foam Cutters?
Polyethylene (PE) is a widely used thermoplastic known for its excellent chemical resistance and lightweight properties. It typically operates effectively between -50°C and 80°C.
Pros: PE is cost-effective and offers good impact resistance, making it suitable for a variety of applications. Its moisture resistance also makes it ideal for outdoor use.
Cons: While PE is durable, it is less flexible than PU and EVA, which may limit its application in certain scenarios. Additionally, it can be less effective in high-temperature environments.
Impact on Application: PE is often used in packaging and insulation applications but may not provide the cushioning needed for sensitive items.
Considerations for International Buyers: Buyers should ensure that the PE used complies with relevant standards such as ISO 9001 for quality management systems, especially when sourcing from regions with stringent regulatory frameworks.
Summary Table of Material Properties
Material | Typical Use Case for foam cutter china | Key Advantage | Key Disadvantage/Limitation | Relative Cost (Low/Med/High) |
---|---|---|---|---|
Polyurethane (PU) | Shock absorption in protective gear | High resilience and flexibility | Sensitive to UV and moisture | Medium |
Ethylene Vinyl Acetate (EVA) | Packaging and cushioning foam | Lightweight and non-toxic | Less chemical resistance | Medium |
Neoprene | Automotive and industrial applications | Excellent chemical resistance | Higher cost and weight | High |
Polyethylene (PE) | Insulation and packaging | Cost-effective and moisture resistant | Less flexibility | Low |
This comprehensive analysis of foam cutter materials provides international B2B buyers with the insights needed to make informed purchasing decisions, ensuring compliance with regional standards and suitability for their specific applications.
In-depth Look: Manufacturing Processes and Quality Assurance for foam cutter china
What Are the Key Manufacturing Processes for Foam Cutters in China?
Manufacturing foam cutters involves several critical stages, each designed to ensure efficiency, precision, and quality. The primary stages include material preparation, forming, assembly, and finishing.
How Is Material Prepared for Foam Cutter Manufacturing?
The first step in the manufacturing process involves selecting and preparing the appropriate materials. Typically, foam cutters are made from high-quality stainless steel or carbon steel, which provides durability and resistance to corrosion. Suppliers often use specialized coatings to enhance the performance and longevity of the tools.
-
Material Selection: B2B buyers should ensure that the materials used meet their specific needs. Look for suppliers that provide detailed specifications about the materials, including tensile strength, hardness, and corrosion resistance.
-
Cutting and Shaping: The selected metal is then cut into the required shapes using advanced laser cutting or CNC machining technologies. This stage requires precision to ensure that the components fit together seamlessly.
What Techniques Are Used in Forming Foam Cutters?
After material preparation, the next stage is forming. This includes various processes that shape the materials into the final product.
-
Forging: Some manufacturers may use forging processes to shape the metal while it is heated, enhancing its strength and durability. This technique is particularly effective for high-stress applications.
-
Welding: For components that require assembly, welding techniques are employed. TIG (Tungsten Inert Gas) welding is commonly used for its precision and ability to produce strong joints.
-
Heat Treatment: To achieve the desired hardness and flexibility, heat treatment processes such as quenching and tempering are applied. This ensures that the foam cutter can withstand rigorous use.
What Happens During the Assembly Stage of Foam Cutter Manufacturing?
Once the individual components are formed, they move to the assembly stage.
-
Component Assembly: Skilled technicians assemble the parts, ensuring that each piece fits perfectly. This stage often includes the installation of electrical components for powered foam cutters.
-
Final Adjustments: After assembly, adjustments are made to ensure that all moving parts operate smoothly. This is crucial for powered foam cutters, where precision affects performance.
How Is Finishing Performed on Foam Cutters?
The final stage in the manufacturing process is finishing, which enhances the appearance and functionality of the foam cutters.
-
Surface Treatment: Various surface treatments, such as polishing or coating, are applied to improve resistance to wear and corrosion. This is particularly important in humid or corrosive environments.
-
Quality Control Check: Before leaving the factory, each foam cutter undergoes a quality control check to ensure it meets specified standards.
What Quality Assurance Standards Should B2B Buyers Look For?
Quality assurance is critical in the manufacturing of foam cutters, particularly for international buyers who must ensure compliance with various standards.
Which International Standards Are Relevant for Foam Cutter Manufacturers?
-
ISO 9001: This standard outlines the requirements for a quality management system. Manufacturers adhering to ISO 9001 demonstrate a commitment to quality and continuous improvement.
-
CE Marking: For buyers in Europe, CE marking is essential as it indicates that the product complies with EU safety, health, and environmental protection standards.
-
API Standards: If foam cutters are used in specific industries such as oil and gas, compliance with American Petroleum Institute (API) standards may be necessary.
What Are the Key Quality Control Checkpoints in Foam Cutter Production?
Quality control (QC) is integrated throughout the manufacturing process. Key checkpoints include:
-
Incoming Quality Control (IQC): Raw materials are inspected upon arrival to ensure they meet specifications.
-
In-Process Quality Control (IPQC): During the manufacturing stages, regular inspections are conducted to catch any defects early.
-
Final Quality Control (FQC): After assembly and finishing, the final product undergoes thorough testing, including performance and safety checks.
How Can B2B Buyers Verify Supplier Quality Control?
To ensure that suppliers adhere to high-quality standards, B2B buyers should consider the following actions:
-
Conduct Audits: Regular audits of the manufacturing facility can provide insights into the supplier’s processes and adherence to quality standards.
-
Request Quality Reports: Suppliers should provide detailed quality reports, including testing results and certifications. This transparency helps build trust.
-
Third-Party Inspections: Engaging third-party inspection agencies can offer an unbiased assessment of the product quality before shipment.
What Are the Nuances of Quality Control for International Buyers?
International B2B buyers, particularly from Africa, South America, the Middle East, and Europe, must navigate various quality control nuances:
-
Cultural Differences: Understanding the manufacturing culture and practices in China can aid in effective communication and expectation management.
-
Regulatory Compliance: Different regions have specific regulatory requirements that must be met. Buyers should ensure that their suppliers are familiar with these regulations.
-
Language Barriers: Clear communication is vital. Buyers should consider engaging translators or using standardized documentation to minimize misunderstandings.
Conclusion
The manufacturing processes and quality assurance measures for foam cutters in China are designed to meet international standards and customer expectations. By understanding these processes, B2B buyers can make informed decisions, ensuring they select high-quality products that align with their operational needs. Engaging with suppliers who prioritize quality control and transparency will help mitigate risks and enhance the buyer-supplier relationship.
Practical Sourcing Guide: A Step-by-Step Checklist for ‘foam cutter china’
To assist international B2B buyers looking to procure foam cutters from China, this practical sourcing guide outlines essential steps to ensure a successful procurement process. By following this checklist, buyers can minimize risks and make informed decisions when selecting suppliers.
Step 1: Define Your Technical Specifications
Establishing clear technical specifications is crucial for sourcing the right foam cutter. Consider factors such as cutting thickness, speed, and material compatibility. Specify whether you need features like automatic feed or programmable settings, as this will help suppliers provide accurate solutions tailored to your needs.
Step 2: Conduct Market Research on Suppliers
Researching potential suppliers is essential to identify reputable manufacturers. Look for companies that specialize in foam cutting technology and have a proven track record. Utilize platforms like Alibaba or Global Sources to compare suppliers, read reviews, and assess their production capabilities.
Step 3: Evaluate Supplier Certifications and Compliance
Verify that suppliers hold relevant certifications, such as ISO 9001 for quality management and CE marking for compliance with European standards. These certifications indicate a commitment to quality and safety, which is particularly important in the manufacturing of machinery. Request documentation to ensure compliance with industry standards.
Step 4: Request Samples Before Committing
Before finalizing your order, request samples of the foam cutters to evaluate their performance. Testing the equipment helps ascertain whether it meets your specifications and quality expectations. Pay attention to aspects such as cutting precision, ease of operation, and durability during your assessment.
Step 5: Understand Payment Terms and Conditions
Clarify payment terms with your chosen supplier to avoid misunderstandings. Common payment methods include letters of credit, bank transfers, or payment through escrow services. Ensure that you are comfortable with the terms and that they align with your financial capabilities and risk management strategies.
Step 6: Establish Clear Communication Channels
Effective communication is vital for a successful procurement process. Ensure that you have direct contact with your supplier’s sales representative and technical support. Establish preferred communication methods and response time expectations to facilitate smooth interactions throughout the procurement process.
Step 7: Plan for Logistics and Shipping
Consider logistics and shipping arrangements early in the process to avoid delays. Discuss shipping options with your supplier and assess costs associated with different methods. Factor in customs clearance and potential tariffs, especially when importing foam cutters into your region.
By following this checklist, B2B buyers can streamline their sourcing process for foam cutters from China, ensuring they select a reliable supplier and obtain machinery that meets their operational needs.
Comprehensive Cost and Pricing Analysis for foam cutter china Sourcing
What Are the Key Cost Components for Sourcing Foam Cutters from China?
When sourcing foam cutters from China, understanding the cost structure is crucial for effective budgeting and negotiation. The primary cost components include:
-
Materials: The quality and type of materials used in foam cutters significantly impact costs. Common materials include high-density polyurethane (PU) foam and various metals for the cutting mechanism. Sourcing higher quality materials can enhance product durability but may also increase the unit price.
-
Labor: Labor costs in China can vary based on the region and the skill level required for manufacturing foam cutters. Generally, urban areas may have higher labor costs compared to rural regions. However, skilled labor may be necessary for complex machinery, influencing the overall cost.
-
Manufacturing Overhead: This encompasses costs associated with factory operations such as utilities, maintenance, and administrative expenses. Overhead costs can vary widely depending on the efficiency and scale of the manufacturing operation.
-
Tooling: Initial tooling costs for foam cutter production can be significant, especially for custom designs. These costs are often amortized over the production run, affecting the per-unit cost.
-
Quality Control (QC): Implementing rigorous QC processes ensures that foam cutters meet international standards. This can add to the cost but is essential for maintaining quality and reducing returns.
-
Logistics: Shipping costs from China to the destination country can vary greatly depending on the mode of transport (air vs. sea), freight rates, and distance. Customs duties and taxes should also be factored in.
-
Margin: Suppliers typically add a profit margin to cover their costs and risks. Understanding the market rate can help buyers assess whether a supplier’s pricing is competitive.
How Do Price Influencers Affect Foam Cutter Costs?
Several factors influence the pricing of foam cutters, which international B2B buyers should consider:
-
Volume/MOQ: Minimum Order Quantities (MOQs) often affect pricing. Ordering in bulk can lead to significant discounts, while smaller orders may incur higher per-unit costs.
-
Specifications and Customization: Custom-designed foam cutters or those with specific features (e.g., enhanced cutting precision) typically cost more. Buyers should weigh the necessity of these specifications against their budget.
-
Materials and Quality Certifications: Higher quality materials and certifications (e.g., ISO standards) can increase costs but may be essential for certain applications. Buyers should evaluate the importance of these factors based on their end-use requirements.
-
Supplier Factors: The reputation, reliability, and experience of the supplier can also affect pricing. Established suppliers may charge more due to their track record of quality and service.
-
Incoterms: Understanding the International Commercial Terms (Incoterms) used in the contract is essential, as they dictate who bears the shipping costs, insurance, and risks during transit.
What Buyer Tips Can Enhance Cost-Efficiency When Sourcing Foam Cutters?
To maximize cost-efficiency when sourcing foam cutters from China, consider the following strategies:
-
Negotiate Wisely: Engage in thorough negotiations with suppliers. Building a good relationship can lead to better pricing and terms, especially for repeat orders.
-
Evaluate Total Cost of Ownership (TCO): Beyond initial purchase price, consider the TCO which includes maintenance, operational costs, and the potential for product longevity. A cheaper foam cutter may incur higher long-term costs.
-
Stay Informed on Pricing Nuances: Prices can fluctuate based on market conditions, currency exchange rates, and changes in material costs. Regularly reviewing these factors can help buyers make informed purchasing decisions.
-
Consider Payment Terms: Flexible payment terms can ease cash flow issues. Discussing options like partial payments or extended payment periods may benefit both parties.
-
Conduct Market Research: Understanding the competitive landscape and pricing benchmarks in the industry can empower buyers during negotiations and help them identify the best deals.
Disclaimer on Indicative Prices
Prices for foam cutters can vary based on the factors mentioned above, and it is advisable for buyers to obtain multiple quotations to ensure competitive pricing. Always verify current market conditions and supplier capabilities before finalizing purchases.
Alternatives Analysis: Comparing foam cutter china With Other Solutions
When evaluating the best options for foam cutting, international B2B buyers should consider various alternatives to ‘foam cutter China’. Each alternative comes with unique benefits and drawbacks, making it essential to understand their comparative advantages in terms of performance, cost, ease of implementation, maintenance, and best use cases.
Comparison Aspect | Foam Cutter China | CNC Foam Cutter | Hot Wire Foam Cutter |
---|---|---|---|
Performance | High precision | Very high precision | Moderate precision |
Cost | Competitive pricing | Higher upfront cost | Lower upfront cost |
Ease of Implementation | Easy setup | Requires training | Simple operation |
Maintenance | Low maintenance | Moderate maintenance | Low maintenance |
Best Use Case | General foam cutting | Complex shapes & designs | Straight cuts & basic shapes |
What Are the Advantages of Using a CNC Foam Cutter?
CNC foam cutters offer very high precision and are ideal for creating complex shapes and intricate designs. They are particularly useful in industries where precision is critical, such as aerospace or automotive. However, they come with a higher upfront cost and may require specialized training for operators. Maintenance is moderate, as these machines can have more parts that may require servicing. Overall, CNC foam cutters are best suited for businesses that prioritize accuracy over cost.
How Does a Hot Wire Foam Cutter Compare?
Hot wire foam cutters are another viable alternative that is often more affordable than CNC machines. They are easy to operate and maintain, making them suitable for smaller businesses or startups. However, the precision offered by hot wire cutters is moderate, and they are best for straight cuts or basic shapes rather than intricate designs. This option is ideal for businesses focused on cost-effectiveness and simplicity but may not meet the needs of those requiring high precision.
Conclusion: How to Choose the Right Foam Cutting Solution?
Choosing the right foam cutting solution depends on several factors, including the specific needs of your business, the complexity of the projects, and budget considerations. For high-precision needs, a CNC foam cutter may be the best choice, albeit at a higher cost. If your focus is on simplicity and lower initial investment, a hot wire foam cutter could suffice. Ultimately, assessing your operational requirements and long-term goals will help in selecting the most appropriate solution for your foam cutting needs.
Essential Technical Properties and Trade Terminology for foam cutter china
What Are the Key Technical Properties of Foam Cutters from China?
When considering the procurement of foam cutters from China, understanding their technical properties is crucial for making informed purchasing decisions. Here are some essential specifications:
-
Material Grade
Foam cutters are typically made from high-quality steel or aluminum. The material grade influences durability and performance. For example, cutters made from carbon steel may offer a balance between cost and performance, while stainless steel options provide resistance to corrosion, which is particularly important in humid environments. -
Cutting Tolerance
This specification indicates the precision with which a foam cutter can operate. A tighter tolerance (e.g., ±0.5 mm) is essential for applications that require high accuracy, such as in the automotive or aerospace industries. Understanding cutting tolerance helps buyers ensure that the foam cutter meets the specific requirements of their production processes. -
Power Rating
The power rating of a foam cutter, usually measured in watts, determines its efficiency and capability to cut through various foam densities. Higher wattage often equates to faster cutting speeds and the ability to handle tougher materials. Buyers should assess their production needs to select a cutter with the appropriate power rating. -
Cutting Speed
This property refers to the speed at which the cutter can operate, typically measured in meters per minute (m/min). A higher cutting speed can significantly enhance productivity, making it a key consideration for manufacturers with high-volume requirements. -
Weight and Portability
The weight of the foam cutter can affect its portability and ease of use. Lighter models may be more suitable for smaller operations or mobile applications, while heavier models may offer stability but could be cumbersome to transport. This consideration is vital for businesses that may need to relocate their equipment frequently.
What Are Common Trade Terms Used in the Foam Cutting Industry?
Familiarity with industry jargon can facilitate smoother negotiations and transactions. Here are some common terms that B2B buyers should know:
-
OEM (Original Equipment Manufacturer)
This term refers to companies that manufacture products that are sold under another company’s brand name. Understanding OEM relationships is essential for buyers looking to source foam cutters that meet specific branding or quality standards. -
MOQ (Minimum Order Quantity)
MOQ is the smallest quantity of a product that a supplier is willing to sell. This term is crucial for buyers as it impacts inventory management and cash flow. Negotiating MOQs can lead to better pricing but may require larger upfront investments. -
RFQ (Request for Quotation)
An RFQ is a document sent to suppliers to request pricing and other details for a specific quantity of goods. This process is vital for buyers to compare offers and ensure they are getting competitive pricing and terms. -
Incoterms (International Commercial Terms)
These are a series of pre-defined commercial terms published by the International Chamber of Commerce (ICC) that clarify the responsibilities of buyers and sellers in international trade. Familiarity with terms like FOB (Free on Board) and CIF (Cost, Insurance, and Freight) can help buyers understand shipping costs and liability. -
Lead Time
This term refers to the time it takes from placing an order to receiving the goods. Understanding lead times is essential for supply chain management, as it affects production schedules and inventory levels.
By grasping these technical properties and trade terms, international B2B buyers from regions such as Africa, South America, the Middle East, and Europe can navigate the foam cutter market in China more effectively, ensuring they make informed purchasing decisions that align with their operational needs.
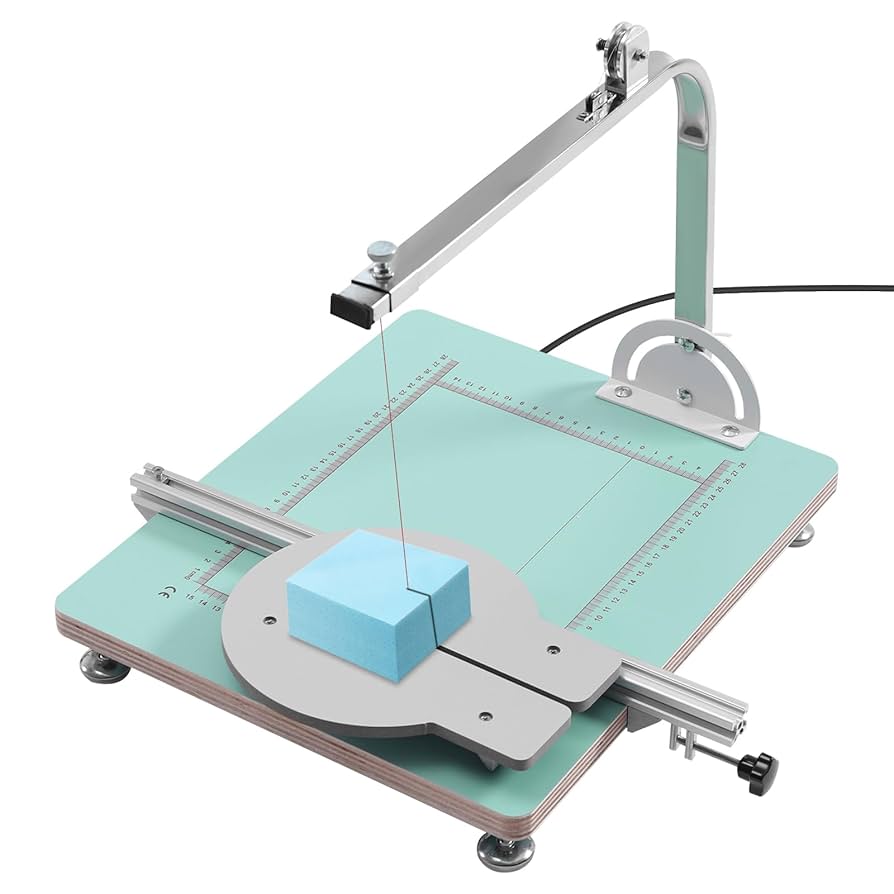
A stock image related to foam cutter china.
Navigating Market Dynamics and Sourcing Trends in the foam cutter china Sector
What Are the Current Market Dynamics and Key Trends in the Foam Cutter China Sector?
The foam cutter sector in China is experiencing significant growth, driven by global demand for advanced manufacturing solutions and innovative material handling technologies. B2B buyers from regions like Africa, South America, the Middle East, and Europe are particularly interested in sourcing foam cutters due to the increasing applications of foam materials across various industries, including packaging, construction, and automotive. The integration of automation and smart technologies in foam cutting processes is a key trend, as manufacturers seek to enhance efficiency and reduce labor costs. Additionally, the rise of e-commerce has accelerated the need for customized packaging solutions, further boosting the demand for foam cutting equipment.
Emerging technologies such as CNC foam cutting machines and laser cutters are reshaping the landscape of foam processing. These advancements not only improve precision but also expand the capabilities of foam cutters, allowing for intricate designs and faster production rates. International buyers should also be aware of the growing trend towards modular and scalable solutions, which enable companies to adapt their production lines according to changing market demands.
How Important Is Sustainability and Ethical Sourcing in the Foam Cutter China Sector?
Sustainability is becoming a critical consideration for B2B buyers in the foam cutter market. With increasing awareness of environmental issues, the demand for sustainable materials and ethical sourcing practices is on the rise. Buyers are encouraged to seek suppliers who utilize eco-friendly materials in their foam production processes, such as water-based adhesives and recyclable packaging options.
The environmental impact of foam production and cutting cannot be overlooked. Manufacturers are now focusing on reducing waste and emissions by implementing more efficient cutting technologies and processes. Certifications like ISO 14001 for environmental management systems can serve as indicators of a supplier’s commitment to sustainability. Additionally, buyers should consider suppliers that offer products made from recycled or biodegradable foam materials, which align with global sustainability goals.
What Is the Brief Evolution and History of Foam Cutting Technologies?
The evolution of foam cutting technologies dates back to the mid-20th century when basic manual cutting tools were primarily used. As the demand for foam products grew, particularly in packaging and insulation, manufacturers began to innovate. The introduction of electric and automated foam cutting machines in the 1980s marked a significant advancement, allowing for greater efficiency and precision.
In the late 1990s and early 2000s, CNC technology revolutionized foam cutting, enabling intricate designs and reducing waste. Today, laser cutting and water jet technologies are at the forefront of the industry, providing high levels of accuracy and flexibility. This evolution not only reflects technological advancements but also highlights the increasing importance of customization in manufacturing, catering to the diverse needs of B2B buyers across various sectors.
By understanding these market dynamics, sustainability considerations, and the historical context of foam cutting technologies, international B2B buyers can make informed sourcing decisions that align with their operational goals and environmental responsibilities.
Frequently Asked Questions (FAQs) for B2B Buyers of foam cutter china
-
How do I choose the right foam cutter from suppliers in China?
Selecting the right foam cutter involves assessing your specific needs, such as the type of foam you’ll be cutting (e.g., PU foam, EVA foam) and the desired precision. Research potential suppliers by reviewing their product specifications, customer reviews, and case studies. Ensure they offer a variety of models that fit your production scale. Request samples to evaluate the cutter’s performance and durability, and consider suppliers that provide comprehensive after-sales support. -
What is the best foam cutter for industrial applications?
For industrial applications, CNC foam cutters are often the best choice due to their precision and automation capabilities. These machines can handle a variety of foam materials and deliver consistent cuts at high volumes. Look for features such as adjustable cutting speeds, programmable controls, and compatibility with CAD software. It’s also essential to check if the supplier offers customization options to tailor the machine to your specific production requirements. -
What are the minimum order quantities (MOQs) for foam cutters from Chinese manufacturers?
MOQs for foam cutters can vary significantly between manufacturers, typically ranging from 1 to 10 units for standard models. However, customized machines may require higher MOQs due to the additional costs associated with design and production. When negotiating with suppliers, clarify their MOQ policies and explore the possibility of lower MOQs for first-time orders or trial runs to assess product quality without committing to large quantities. -
How can I ensure quality when sourcing foam cutters from China?
To ensure quality, conduct thorough due diligence on potential suppliers. Verify their certifications, such as ISO 9001, and request quality assurance documentation for their products. Consider visiting the factory or using third-party inspection services to evaluate manufacturing processes. Additionally, establish clear quality expectations in your purchase agreements, including testing protocols and warranty terms to protect your investment. -
What payment terms should I negotiate with Chinese foam cutter suppliers?
Common payment terms include a 30% deposit upon order confirmation, with the remaining 70% due before shipment. However, you can negotiate terms based on your relationship with the supplier and order size. Consider using secure payment methods such as letters of credit or escrow services for larger orders to mitigate risks. Always clarify the terms in writing to avoid misunderstandings. -
How do logistics and shipping work when importing foam cutters from China?
Logistics involve coordinating with freight forwarders to handle the transportation of your foam cutters from the supplier to your destination. Discuss shipping options, including air freight for faster delivery or sea freight for cost savings. Ensure that the supplier provides proper packaging to avoid damage during transit. Additionally, familiarize yourself with customs regulations and duties in your country to streamline the import process. -
What are the common challenges when sourcing foam cutters from China?
Challenges include language barriers, cultural differences, and varying standards of quality. To overcome these, engage with suppliers who have experience working with international clients and who can provide English-speaking representatives. Establish clear communication channels and use detailed specifications in your orders. Being proactive in addressing these challenges can lead to a smoother sourcing experience. -
How can I customize foam cutters to meet my specific production needs?
Customization options typically include adjustments to cutting dimensions, control systems, and additional features like conveyor belts or integrated dust collection systems. When discussing customization with suppliers, provide detailed specifications and requirements. It’s advisable to ask for prototypes or detailed CAD drawings to ensure the design meets your expectations before final production. Collaborating closely with the supplier during the design phase can lead to more effective solutions tailored to your needs.
Important Disclaimer & Terms of Use
⚠️ Important Disclaimer
The information provided in this guide, including content regarding manufacturers, technical specifications, and market analysis, is for informational and educational purposes only. It does not constitute professional procurement advice, financial advice, or legal advice.
While we have made every effort to ensure the accuracy and timeliness of the information, we are not responsible for any errors, omissions, or outdated information. Market conditions, company details, and technical standards are subject to change.
B2B buyers must conduct their own independent and thorough due diligence before making any purchasing decisions. This includes contacting suppliers directly, verifying certifications, requesting samples, and seeking professional consultation. The risk of relying on any information in this guide is borne solely by the reader.
Strategic Sourcing Conclusion and Outlook for foam cutter china
In the dynamic landscape of foam cutting technology, strategic sourcing emerges as a pivotal element for international B2B buyers. By understanding the intricacies of foam materials, such as PU foam and its various classifications, businesses can make informed decisions that enhance operational efficiency and product quality. The ability to evaluate suppliers based on their expertise, certifications, and product offerings ensures that buyers from Africa, South America, the Middle East, and Europe can secure reliable partnerships that align with their specific needs.
How Can Strategic Sourcing Benefit International Buyers?
Strategic sourcing not only facilitates cost reduction but also empowers buyers to leverage the latest innovations in foam cutting technology. By establishing strong relationships with suppliers in China, businesses can tap into advanced manufacturing processes and high-quality materials that meet global standards. This proactive approach enables companies to stay competitive and responsive to market demands.
What Should Buyers Consider Moving Forward?
As you navigate the foam cutter market, prioritize suppliers who demonstrate a commitment to sustainability and product excellence. By integrating these values into your sourcing strategy, you can position your business for long-term success. Embrace the opportunities that strategic sourcing presents and take the next step towards enhancing your operations by connecting with trusted foam cutter manufacturers in China. Your journey towards optimized sourcing begins today.