Cut Costs with Packaging Machinery China: The Ultimate Guide (2025)
Introduction: Navigating the Global Market for packaging machinery china
In today’s competitive landscape, sourcing reliable packaging machinery from China poses a significant challenge for international B2B buyers, particularly those operating in Africa, South America, the Middle East, and Europe. With an array of options available, understanding the nuances of the market is crucial for making informed purchasing decisions. This comprehensive guide on packaging machinery from China will illuminate the various types of machinery available, their applications across different industries, and the essential steps for supplier vetting.
Navigating the complexities of costs and logistics is also a key focus, ensuring that buyers are equipped with the insights necessary to negotiate favorable terms and avoid common pitfalls. By delving into supplier backgrounds, certifications, and customer reviews, this guide empowers businesses to build lasting partnerships with trustworthy manufacturers.
Furthermore, we will explore the latest trends in packaging technology, enabling buyers to stay ahead of the curve and adapt to evolving market demands. Whether you’re in Egypt seeking efficient bottling solutions or in Mexico looking for sustainable packaging options, this guide serves as your roadmap to successfully sourcing packaging machinery from China. With actionable insights and expert recommendations, you will be better positioned to enhance your operational efficiency and achieve your business objectives.
Understanding packaging machinery china Types and Variations
Type Name | Key Distinguishing Features | Primary B2B Applications | Brief Pros & Cons for Buyers |
---|---|---|---|
Automatic Filling Machines | High-speed operation, customizable filling volumes, precision | Food and beverage, pharmaceuticals, cosmetics | Pros: Increased efficiency, reduced labor costs. Cons: Higher initial investment. |
Labeling Machines | Versatile labeling options, high-speed application, integration with production lines | Food packaging, consumer goods, electronics | Pros: Enhanced branding, accuracy in labeling. Cons: Maintenance can be complex. |
Shrink Wrapping Machines | Use of heat to shrink film around products, adjustable speed | E-commerce, food packaging, industrial goods | Pros: Effective protection, cost-efficient. Cons: Limited to specific product shapes. |
Cartoning Machines | Automatic loading, sealing, and forming of cartons | Pharmaceuticals, food, personal care products | Pros: Streamlined packaging process, reduces manual labor. Cons: Space-intensive. |
Vacuum Packaging Machines | Removal of air from packaging to extend shelf life | Meat processing, dairy, electronics | Pros: Prolongs product freshness, reduces spoilage. Cons: Higher operational costs. |
What Are the Key Characteristics of Automatic Filling Machines?
Automatic filling machines are designed for high-speed operations, making them suitable for industries like food and beverage, pharmaceuticals, and cosmetics. They can be customized to fill varying volumes, ensuring precise measurements and reducing waste. When considering such machinery, buyers should evaluate their production capacity needs and the types of products being packaged, as well as the machine’s compatibility with existing production lines.
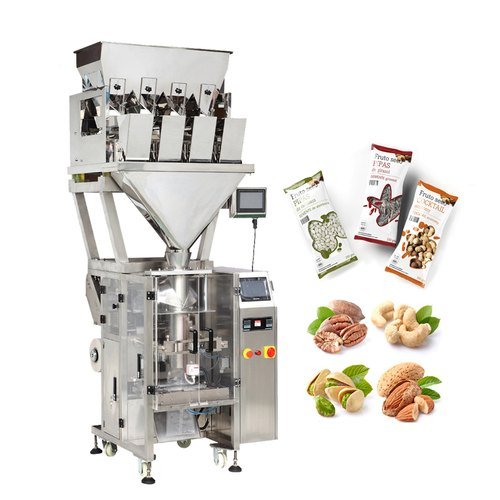
A stock image related to packaging machinery china.
Why Are Labeling Machines Essential for B2B Operations?
Labeling machines provide versatility in labeling options, allowing companies to apply labels at high speeds while maintaining accuracy. They are crucial in sectors like food packaging, consumer goods, and electronics, where branding and regulatory compliance are paramount. Buyers must consider the machine’s integration capabilities with their production lines and the types of labels used, as well as ongoing maintenance requirements.
How Do Shrink Wrapping Machines Benefit Businesses?
Shrink wrapping machines utilize heat to shrink film tightly around products, offering an effective way to package goods for e-commerce, food packaging, and industrial applications. They are particularly beneficial for protecting products during transit and enhancing shelf appeal. Buyers should assess the types of products being wrapped, the machine’s speed, and the cost of materials when making a purchasing decision.
What Advantages Do Cartoning Machines Provide?
Cartoning machines automate the loading, sealing, and forming of cartons, significantly streamlining the packaging process for industries like pharmaceuticals, food, and personal care products. They help reduce manual labor and increase efficiency. Buyers should consider the space requirements for installation and the types of cartons compatible with the machine when evaluating options.
Why Choose Vacuum Packaging Machines for Your Products?
Vacuum packaging machines are designed to remove air from packaging, extending shelf life and reducing spoilage for products like meat, dairy, and electronics. This technology is particularly valuable for businesses aiming to maintain product quality over time. Buyers should weigh the operational costs against the benefits of prolonged product freshness and assess the machine’s ease of use and maintenance.
Related Video: Automatic packaging machines and packaging systems for Kits
Key Industrial Applications of packaging machinery china
Industry/Sector | Specific Application of Packaging Machinery China | Value/Benefit for the Business | Key Sourcing Considerations for this Application |
---|---|---|---|
Food and Beverage | Automated filling and sealing machines | Increased efficiency and reduced labor costs | Compliance with health and safety regulations; local market preferences |
Pharmaceuticals | Blister packaging machines | Enhanced product protection and shelf life | Need for precision and compliance with international standards |
Consumer Goods | Cartoning and wrapping machines | Improved branding and customer appeal | Adaptability to different product sizes and materials |
Electronics | Vacuum packaging for sensitive components | Protection from moisture and contamination | Compatibility with various product dimensions and materials |
Cosmetics | Labeling and bottling machines | Streamlined production and enhanced product visibility | Customization options for branding and design elements |
How is Packaging Machinery from China Used in the Food and Beverage Industry?
In the food and beverage sector, packaging machinery from China, such as automated filling and sealing machines, plays a vital role in enhancing production efficiency. These machines help businesses minimize labor costs while ensuring consistent quality and hygiene in packaging. International buyers, particularly from regions like Africa and South America, should consider local market preferences and compliance with health and safety regulations, ensuring that the machinery meets the necessary standards for food safety.
What Role Does Packaging Machinery Play in the Pharmaceutical Industry?
Blister packaging machines are crucial in the pharmaceutical industry, providing enhanced protection for medications and extending their shelf life. These machines ensure that products are securely packaged, minimizing the risk of contamination and ensuring compliance with international standards. Buyers from Europe and the Middle East must prioritize precision in machinery to meet regulatory requirements, as well as consider the adaptability of the machines to various product sizes and configurations.
How Does Packaging Machinery Enhance Consumer Goods Production?
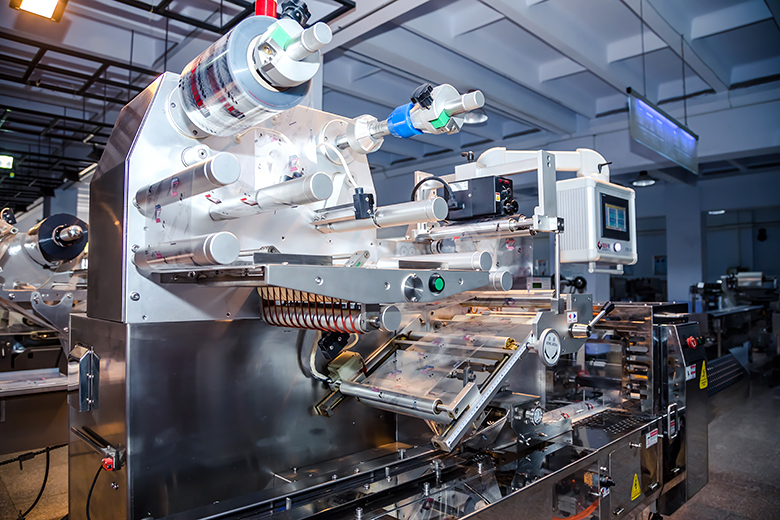
A stock image related to packaging machinery china.
In the consumer goods industry, cartoning and wrapping machines from China improve branding and customer appeal through efficient and attractive packaging. These machines streamline production processes, allowing for faster turnaround times and reduced operational costs. B2B buyers should focus on sourcing equipment that can adapt to different product sizes and materials, ensuring they can cater to diverse market demands effectively.
What Are the Benefits of Vacuum Packaging in Electronics?
For the electronics sector, vacuum packaging machines are essential for protecting sensitive components from moisture and contamination. This type of packaging extends the longevity and reliability of electronic products, which is critical for maintaining brand reputation. Buyers should ensure that the machinery is compatible with various product dimensions and materials, as well as consider sourcing from suppliers who offer robust after-sales support and maintenance services.
How Can Cosmetics Companies Benefit from Advanced Packaging Machinery?
In the cosmetics industry, labeling and bottling machines play a significant role in streamlining production while enhancing product visibility on retail shelves. These machines allow for customized branding options, which are vital for standing out in a competitive market. International buyers should seek machinery that offers flexibility in design elements and can accommodate varying bottle shapes and sizes, ensuring they meet consumer expectations and preferences effectively.
Related Video: Glenroy’s Flexible Packaging Manufacturing Process
3 Common User Pain Points for ‘packaging machinery china’ & Their Solutions
Scenario 1: Navigating Quality Control Issues with Chinese Packaging Machinery
The Problem:
B2B buyers often face significant challenges when sourcing packaging machinery from China, particularly regarding quality control. For instance, a company in Egypt may receive a batch of packaging machines that do not meet the promised specifications or have inconsistent performance, leading to production delays and increased costs. This situation becomes even more critical when the machinery is intended for high-demand markets, where reliability and efficiency are paramount. The fear of investing in subpar equipment can create hesitation and anxiety among buyers, impacting their supply chain and overall business operations.
The Solution:
To mitigate quality control issues, international buyers should prioritize working with reputable manufacturers who adhere to international quality standards. Before placing an order, conduct thorough due diligence by requesting certifications such as ISO 9001 or CE marking, which indicate compliance with quality assurance processes. Engage in factory audits or hire third-party inspection services to evaluate the manufacturing process and finished products. Additionally, consider establishing a clear communication channel with the manufacturer to define expectations, performance metrics, and after-sales support. Building a collaborative relationship can significantly enhance accountability and quality assurance throughout the procurement process.
Scenario 2: Overcoming Language and Cultural Barriers in Procurement
The Problem:
Language and cultural differences can pose significant barriers for B2B buyers sourcing packaging machinery from China. A company in South America might struggle to communicate its specific needs or understand the technical specifications due to language nuances. Misinterpretations can lead to incorrect orders, resulting in wasted resources and time. This is particularly challenging in industries that require precise machinery configurations tailored to unique product requirements.
The Solution:
To overcome these barriers, buyers should invest in professional translation services or hire bilingual intermediaries who understand both the technical aspects of the machinery and the cultural context. Providing detailed specifications in both languages can help ensure clarity and alignment with manufacturers. Additionally, consider utilizing visual aids like diagrams or videos to illustrate requirements and expectations. Engaging with local representatives or consultants who have experience in the Chinese manufacturing sector can also facilitate smoother negotiations and foster a better understanding of cultural nuances, ultimately enhancing the procurement experience.
Scenario 3: Managing Lead Times and Delivery Delays
The Problem:
International buyers often encounter lead times and delivery delays when sourcing packaging machinery from China, which can disrupt production schedules and supply chains. For example, a European company may plan its production around the expected delivery date of new packaging equipment, only to face unexpected delays that jeopardize product launches and contracts with clients. Such disruptions can lead to lost revenue and strained relationships with customers.
The Solution:
To effectively manage lead times, buyers should establish clear timelines and milestones with their suppliers from the outset. Utilize tools like project management software to track progress and set reminders for key dates. It is also advisable to have a contingency plan in place, such as alternative suppliers or temporary equipment solutions, to mitigate the impact of delays. Regular communication with manufacturers about production schedules and logistics can help buyers anticipate potential issues early on. Furthermore, consider negotiating terms that include penalties for late deliveries to encourage adherence to timelines, ensuring that both parties remain committed to the agreed-upon schedule.
Strategic Material Selection Guide for packaging machinery china
What Are the Key Properties of Stainless Steel for Packaging Machinery in China?
Stainless steel is a widely used material in packaging machinery due to its excellent mechanical properties and resistance to corrosion. It typically has a temperature rating of up to 800°C and can withstand high-pressure environments, making it suitable for various applications. The most common grades, such as 304 and 316, offer different levels of corrosion resistance, with 316 being preferred for applications involving saline or acidic environments.
Pros and Cons of Stainless Steel
The durability of stainless steel is one of its most significant advantages; it can endure harsh conditions without degrading. However, it is relatively expensive compared to other materials, which can impact the overall cost of machinery. Additionally, the manufacturing complexity can be higher due to the need for specialized welding techniques and equipment.
Impact on Application
Stainless steel is compatible with a wide range of media, including food products, chemicals, and pharmaceuticals. Its non-reactive nature ensures that it does not contaminate the products being packaged. For international buyers, compliance with standards such as ASTM and FDA regulations is crucial, especially in industries like food and pharmaceuticals.
How Does Aluminum Perform as a Material for Packaging Machinery?
Aluminum is another popular choice for packaging machinery, known for its lightweight and high strength-to-weight ratio. It typically has a temperature resistance of up to 600°C and performs well under moderate pressure. Its natural corrosion resistance is enhanced when anodized, making it suitable for various environments.
Pros and Cons of Aluminum
The primary advantage of aluminum is its lightweight nature, which can reduce shipping costs and energy consumption during operation. However, it is less durable than stainless steel and can be prone to scratching and denting. The cost of aluminum is generally moderate, making it an attractive option for many manufacturers.
Impact on Application
Aluminum is compatible with a variety of products, including dry goods and some liquids. However, it may not be suitable for highly corrosive materials unless properly treated. International buyers should consider compliance with local standards such as JIS and DIN, especially when exporting to regions with stringent regulations.
What Are the Benefits of Plastic Composites in Packaging Machinery?
Plastic composites, including materials like polypropylene and polyethylene, are increasingly being utilized in packaging machinery due to their versatility and cost-effectiveness. These materials can withstand temperatures ranging from -40°C to 80°C, depending on the specific type of plastic used.
Pros and Cons of Plastic Composites
The key advantage of plastic composites is their low cost and ease of manufacturing, allowing for complex shapes and designs. However, they may not offer the same level of durability as metals and can be susceptible to UV degradation. Additionally, they have a lower pressure rating, making them unsuitable for high-pressure applications.
Impact on Application
Plastic composites are ideal for packaging non-corrosive products and can be tailored for specific applications, such as food packaging. For international B2B buyers, understanding the recycling and disposal regulations in their region is essential, as plastics face increasing scrutiny regarding environmental impact.
How Does Carbon Steel Compare in Packaging Machinery Applications?
Carbon steel is often used for its strength and affordability, particularly in structural components of packaging machinery. It has a temperature rating of up to 400°C and can handle moderate pressures effectively. However, it is less resistant to corrosion compared to stainless steel.
Pros and Cons of Carbon Steel
The primary advantage of carbon steel is its low cost, making it an attractive option for budget-conscious buyers. However, its susceptibility to rust and corrosion can lead to higher maintenance costs over time. Manufacturing complexity is moderate, but it requires protective coatings to enhance its longevity.
Impact on Application
Carbon steel is suitable for applications that do not involve corrosive materials, such as dry goods. International buyers should be aware of the need for protective coatings and compliance with local standards to ensure the longevity and safety of their machinery.
Material | Typical Use Case for packaging machinery china | Key Advantage | Key Disadvantage/Limitation | Relative Cost (Low/Med/High) |
---|---|---|---|---|
Stainless Steel | Food and pharmaceutical packaging machinery | Excellent corrosion resistance | Higher cost and manufacturing complexity | High |
Aluminum | Lightweight packaging machinery components | Lightweight and cost-effective | Less durable than stainless steel | Medium |
Plastic Composites | Non-corrosive product packaging | Low cost and easy to manufacture | Susceptible to UV degradation | Low |
Carbon Steel | Structural components in packaging machinery | Low cost and high strength | Prone to rust without coatings | Low |
This strategic material selection guide provides international B2B buyers with essential insights into the properties, advantages, and limitations of various materials used in packaging machinery. Understanding these factors will enable buyers to make informed decisions that align with their operational needs and compliance requirements.
In-depth Look: Manufacturing Processes and Quality Assurance for packaging machinery china
What Are the Main Stages of Manufacturing Packaging Machinery in China?
The manufacturing of packaging machinery in China involves several critical stages that ensure the production of high-quality equipment. Understanding these stages helps international B2B buyers make informed decisions when sourcing machinery.
1. Material Preparation
The first step in the manufacturing process is material preparation. Manufacturers typically use a variety of materials, including stainless steel, aluminum, and plastic, depending on the machine’s specifications and intended use. Quality suppliers conduct rigorous material inspections to ensure that all components meet the required standards. This step may involve:
- Sourcing Quality Raw Materials: Suppliers should provide certificates of compliance to verify material quality.
- Cutting and Shaping: Advanced CNC (Computer Numerical Control) machines are commonly used for precision cutting and shaping of materials.
2. Forming
Once the materials are prepared, the next step is forming, where components are shaped into the desired form. Techniques used include:
- Stamping: This is often used for creating metal parts quickly and efficiently.
- Molding: For plastic components, injection molding is a prevalent technique that allows for high-volume production with consistent quality.
This stage is vital for ensuring that components fit together correctly in later assembly stages.
3. Assembly
After forming, the components move to the assembly stage. This is where the machinery starts taking shape. Key activities include:
- Component Assembly: Skilled technicians assemble parts, often using automated assembly lines to enhance efficiency and reduce human error.
- Integration of Systems: Electrical and mechanical systems are integrated, ensuring that all parts work cohesively.
Attention to detail during assembly is crucial, as it affects the machine’s overall functionality and durability.
4. Finishing
The final stage of manufacturing is finishing, which involves several processes to prepare the machinery for delivery:
- Surface Treatment: This may include painting, anodizing, or plating to enhance durability and aesthetics.
- Final Assembly and Testing: Before leaving the factory, each machine undergoes final assembly and testing to ensure it meets quality standards.
How Do Quality Assurance Processes Ensure High Standards in Packaging Machinery Manufacturing?
Quality assurance (QA) is an integral part of the manufacturing process for packaging machinery in China. It ensures that products meet international standards and buyer expectations.
International and Industry-Specific Standards
Adherence to international standards is critical for B2B buyers. Key standards include:
- ISO 9001: This standard focuses on quality management systems and ensures that manufacturers have processes in place to maintain consistent quality.
- CE Marking: A requirement for products sold within the European Economic Area, indicating compliance with health, safety, and environmental protection standards.
- API (American Petroleum Institute): For machinery used in oil and gas applications, adherence to API standards is often required.
B2B buyers should verify that their suppliers are certified to these standards, as it reflects their commitment to quality.
What Are the Key QC Checkpoints in the Manufacturing Process?
Quality Control (QC) checkpoints are strategically placed throughout the manufacturing process. These checkpoints include:
- Incoming Quality Control (IQC): Inspection of raw materials upon delivery to ensure they meet specifications.
- In-Process Quality Control (IPQC): Continuous monitoring of the manufacturing process, allowing for adjustments to be made in real time.
- Final Quality Control (FQC): Comprehensive testing of the finished product to ensure it meets all specifications and standards.
These checkpoints help identify defects early, reducing the risk of faulty machinery reaching the buyer.
What Common Testing Methods Are Used for Packaging Machinery?
Testing methods are essential for verifying the performance and safety of packaging machinery. Common methods include:
- Functional Testing: Ensures that all machine functions operate correctly under various conditions.
- Durability Testing: Machines are subjected to stress tests to evaluate their longevity and performance under heavy usage.
- Safety Testing: This includes checks for electrical safety, mechanical safety, and compliance with relevant safety standards.
B2B buyers should request detailed test reports to assess the reliability of the machinery.
How Can B2B Buyers Verify Supplier Quality Control?
Verifying a supplier’s quality control processes is crucial for B2B buyers, particularly those from Africa, South America, the Middle East, and Europe. Here are some effective strategies:
- Conduct Supplier Audits: Regular audits can provide insights into the manufacturing processes and quality assurance measures in place.
- Request QC Reports: Manufacturers should provide comprehensive quality control reports that document inspections and tests performed throughout the production process.
- Engage Third-Party Inspectors: Utilizing independent inspection services can ensure an unbiased evaluation of product quality before shipment.
By taking these steps, B2B buyers can minimize risks associated with sourcing machinery from international suppliers.
What Are the Quality Control Nuances for International B2B Buyers?
International B2B buyers must navigate various nuances when dealing with quality control in China. These include:
- Cultural Differences: Understanding local business practices and communication styles is vital for effective collaboration with Chinese manufacturers.
- Regulatory Compliance: Buyers should be aware of the specific regulations and standards applicable in their home countries to ensure imported machinery complies with local laws.
- Language Barriers: Clear communication is essential to avoid misunderstandings regarding specifications and quality expectations.
By addressing these nuances, B2B buyers can foster successful partnerships with Chinese packaging machinery manufacturers, ensuring that they receive high-quality products that meet their needs.
Practical Sourcing Guide: A Step-by-Step Checklist for ‘packaging machinery china’
To effectively navigate the procurement process of packaging machinery from China, B2B buyers must adopt a systematic approach. This guide provides a clear checklist to help international buyers, particularly from Africa, South America, the Middle East, and Europe, streamline their sourcing efforts and ensure successful transactions.
Step 1: Define Your Technical Specifications
Clearly articulating your technical requirements is essential before reaching out to suppliers. This includes the type of machinery needed, production capacity, material compatibility, and any specific features that are critical for your operations.
– Why it matters: Defining specifications helps avoid misunderstandings and ensures that the machinery meets your operational needs.
– What to consider: Engage your engineering team to draft a comprehensive list of requirements.
Step 2: Conduct Market Research
Perform thorough market research to identify potential suppliers and understand market trends.
– Why it matters: This step helps you gauge the competitive landscape and find suppliers who specialize in the type of machinery you require.
– What to look for: Utilize online marketplaces, trade directories, and industry reports to compile a list of qualified suppliers.
Step 3: Verify Supplier Credentials
Once you have a shortlist of suppliers, it’s crucial to validate their credentials. This includes checking business licenses, certifications (ISO, CE), and their reputation in the market.
– Why it matters: Supplier credentials are indicators of reliability and compliance with international standards.
– What to do: Request copies of certifications and conduct background checks through third-party verification services.
Step 4: Request Samples and Quotes
Engage with selected suppliers to request samples of their machinery along with detailed quotes.
– Why it matters: Evaluating samples allows you to assess the quality and suitability of the machinery for your production needs.
– What to include: Ensure quotes cover not just the price, but also shipping, installation, warranty, and after-sales service.
Step 5: Evaluate Potential Suppliers
Before committing, it’s crucial to vet suppliers thoroughly. Request company profiles, case studies, and references from buyers in a similar industry or region.
– Why it matters: A supplier’s track record can reveal their reliability and customer service quality.
– What to look for: Seek testimonials and reviews from other clients to gauge satisfaction levels and support responsiveness.
Step 6: Negotiate Terms and Conditions
Once you have selected a supplier, enter into negotiations regarding pricing, payment terms, delivery schedules, and warranties.
– Why it matters: Clear agreements can prevent disputes and ensure both parties have aligned expectations.
– What to focus on: Aim for terms that protect your interests, such as payment milestones tied to delivery stages.
Step 7: Plan for Logistics and Customs
Prepare for the logistics of shipping and customs clearance when importing machinery from China.
– Why it matters: Understanding logistics and customs regulations can prevent delays and additional costs.
– What to arrange: Collaborate with a logistics partner experienced in international shipping to streamline the process.
By following this structured checklist, B2B buyers can enhance their sourcing strategy for packaging machinery from China, ensuring a smoother procurement process and successful partnerships.
Comprehensive Cost and Pricing Analysis for packaging machinery china Sourcing
What Are the Key Cost Components in Sourcing Packaging Machinery from China?
When sourcing packaging machinery from China, understanding the comprehensive cost structure is essential for international B2B buyers. The primary cost components include:
-
Materials: The choice of materials directly influences the overall cost. High-quality materials, such as stainless steel and specialized polymers, may incur higher initial costs but can lead to lower maintenance and longer lifespan.
-
Labor: Labor costs in China are generally lower than in Europe or North America. However, this can vary based on the complexity of the machinery and the skill level required. Specialized labor for high-tech machinery can increase costs.
-
Manufacturing Overhead: This encompasses costs related to utilities, rent, and equipment depreciation. Factories with advanced technologies may have higher overheads but can produce machinery more efficiently.
-
Tooling: Custom tooling for specific machinery designs can represent a significant upfront investment. Understanding the tooling costs is crucial as they can affect the overall pricing structure.
-
Quality Control (QC): Implementing stringent QC processes ensures that the machinery meets international standards. While this adds to the cost, it can prevent costly defects and operational failures later.
-
Logistics: Shipping costs from China to the destination country can vary greatly depending on the mode of transport (sea or air), distance, and any tariffs that may apply.
-
Margin: Suppliers typically include a profit margin that can vary widely based on their market positioning and the competitive landscape.
How Do Price Influencers Affect the Cost of Packaging Machinery?
Several factors influence the pricing of packaging machinery sourced from China:
-
Volume/MOQ (Minimum Order Quantity): Larger orders often lead to lower per-unit costs due to economies of scale. Buyers should assess their needs against the supplier’s MOQ.
-
Specifications and Customization: Custom machinery tailored to specific requirements will generally cost more. Buyers must weigh the benefits of customization against the additional costs.
-
Materials and Quality Certifications: The use of premium materials or certifications (like CE, ISO) can increase costs but may provide assurance of quality and compliance with international standards.
-
Supplier Factors: The reputation and reliability of the supplier can influence pricing. Established suppliers may charge a premium for their experience and track record.
-
Incoterms: The terms of shipping and delivery (e.g., FOB, CIF) can significantly affect total costs. Understanding these terms helps buyers calculate the total landed cost more accurately.
What Are the Best Negotiation Tips for International B2B Buyers?
To ensure cost-efficiency in sourcing packaging machinery from China, consider the following strategies:
-
Conduct Thorough Market Research: Familiarize yourself with industry pricing standards to negotiate effectively. Understanding the market will empower you during discussions with suppliers.
-
Leverage Volume Discounts: If possible, consolidate orders to meet or exceed the MOQ. This can yield substantial savings and strengthen your negotiating position.
-
Evaluate Total Cost of Ownership (TCO): Look beyond the purchase price. Consider factors like maintenance, energy efficiency, and operational longevity to make an informed decision.
-
Be Transparent About Your Needs: Clear communication about your requirements can help suppliers provide tailored pricing, potentially leading to better deals.
-
Build Relationships: Establishing a good rapport with suppliers can lead to more favorable terms and pricing. Long-term partnerships often result in better service and support.
What Should International Buyers Consider Regarding Pricing Nuances?
For international buyers, particularly from regions like Africa, South America, the Middle East, and Europe, there are unique pricing nuances to consider:
-
Currency Fluctuations: Exchange rate variations can impact the final price. It’s advisable to negotiate prices in a stable currency or include clauses that account for currency fluctuations.
-
Tariffs and Duties: Be aware of any import tariffs or duties that may apply to your machinery. These can significantly affect the total cost.
-
Local Regulations: Compliance with local regulations and standards can lead to additional costs, especially if modifications are needed to meet these requirements.
Disclaimer on Indicative Prices
Prices for packaging machinery sourced from China can vary widely based on the factors discussed above. It’s essential for buyers to conduct thorough due diligence and obtain multiple quotes to ensure a competitive price tailored to their specific needs.
Alternatives Analysis: Comparing packaging machinery china With Other Solutions
Introduction: What Are the Alternatives to Packaging Machinery from China?
When considering packaging machinery for your business, it’s vital to explore various alternatives that may better suit your operational needs and budget constraints. While packaging machinery from China offers competitive pricing and a wide range of options, other solutions may provide unique advantages in terms of performance, reliability, and service. This analysis will compare ‘packaging machinery China’ against two alternative solutions: European Packaging Systems and Automated Packaging Solutions from the USA.
Comparison Table of Packaging Machinery Solutions
Comparison Aspect | Packaging Machinery China | European Packaging Systems | Automated Packaging Solutions (USA) |
---|---|---|---|
Performance | Good, variable quality | High, consistent quality | Excellent, advanced technology |
Cost | Lower initial investment | Higher initial investment | Moderate to high investment |
Ease of Implementation | Moderate, requires setup | Easy, often plug-and-play | Complex, may require customization |
Maintenance | Variable, often limited support | Reliable, good support | Excellent, comprehensive support |
Best Use Case | High-volume, budget-conscious operations | Quality-focused, regulated industries | Custom solutions for diverse needs |
Detailed Breakdown of Alternatives
What Are the Advantages and Disadvantages of European Packaging Systems?
European Packaging Systems are known for their high-quality engineering and reliability. These systems typically offer advanced technology that ensures consistent performance, making them ideal for industries with stringent regulatory requirements, such as pharmaceuticals and food. While the initial investment is higher than Chinese machinery, the long-term reliability and low maintenance costs can make them more economical over time. However, businesses with tight budgets may find the upfront costs prohibitive.
How Do Automated Packaging Solutions from the USA Compare?
Automated Packaging Solutions from the USA leverage advanced technology to enhance efficiency and reduce labor costs. These systems are ideal for businesses that require flexibility and customization in their packaging processes. Although the initial investment may be moderate to high, the return on investment can be significant due to increased throughput and reduced waste. However, the complexity of these systems may require specialized training and setup, which can pose challenges for smaller businesses.
Conclusion: How Should B2B Buyers Choose the Right Packaging Solution?
Choosing the right packaging machinery requires a thorough understanding of your specific operational needs and budget constraints. For businesses focused on cost-efficiency and high-volume production, packaging machinery from China may provide the best initial solution. However, if quality and reliability are paramount, investing in European Packaging Systems or Automated Packaging Solutions could yield better long-term benefits. Assessing the total cost of ownership, including maintenance, support, and the potential for operational disruptions, will help you make an informed decision that aligns with your strategic goals.
Essential Technical Properties and Trade Terminology for packaging machinery china
What Are the Key Technical Properties of Packaging Machinery from China?
When sourcing packaging machinery from China, understanding the technical properties is crucial for ensuring that the equipment meets your operational needs. Here are some critical specifications to consider:
1. Material Grade
The material grade of packaging machinery determines its durability, resistance to wear, and overall lifespan. Common materials include stainless steel, which is preferred for its corrosion resistance, and aluminum, which is lightweight yet strong. For B2B buyers, selecting the right material grade can affect maintenance costs and product integrity.
2. Tolerance
Tolerance refers to the permissible limit of variation in a physical dimension. In packaging machinery, tighter tolerances can lead to more precise operations, reducing waste and improving product quality. For international buyers, understanding tolerance levels is essential to ensure that the machinery can operate efficiently within the specific requirements of their production processes.
3. Speed and Capacity
Speed indicates how quickly the machinery can operate, usually measured in products per minute. Capacity refers to the maximum volume of product that can be processed in a given time. Evaluating speed and capacity is vital for aligning machinery performance with production demands, particularly for buyers in fast-growing markets in Africa and South America.
4. Power Consumption
Power consumption is a critical factor in the operational costs of packaging machinery. Machines that are energy-efficient can significantly reduce electricity costs over time. For B2B buyers, understanding power consumption ratings can lead to better budgeting and sustainability practices.
5. Automation Level
The level of automation—ranging from manual to fully automated systems—affects operational efficiency and labor costs. Fully automated packaging machinery can minimize human error and enhance throughput. Buyers need to assess their workforce capabilities and production requirements to determine the appropriate level of automation.
What Are Common Trade Terms Used in the Packaging Machinery Industry?
Understanding trade terminology is essential for navigating the complexities of international transactions. Here are some common terms that B2B buyers should know:
1. OEM (Original Equipment Manufacturer)
OEM refers to a company that produces parts or equipment that may be marketed by another manufacturer. In the context of packaging machinery, buyers may seek OEM products to ensure they receive high-quality components that meet their specifications, often with the option for customization.
2. MOQ (Minimum Order Quantity)
MOQ is the smallest quantity of a product that a supplier is willing to sell. This term is crucial for buyers to understand as it can affect inventory management and initial investment costs. Buyers should negotiate MOQs to align with their production needs while minimizing excess inventory.
3. RFQ (Request for Quotation)
An RFQ is a document that a buyer sends to suppliers to request pricing and availability for specific products or services. This process helps buyers compare offers and choose suppliers that meet their financial and operational criteria.
4. Incoterms (International Commercial Terms)
Incoterms are a set of predefined commercial terms published by the International Chamber of Commerce. They define the responsibilities of buyers and sellers regarding shipping, insurance, and tariffs. Familiarity with Incoterms is essential for international B2B transactions, as they help clarify obligations and reduce the risk of misunderstandings.
5. Lead Time
Lead time refers to the period between the initiation of an order and its completion. In packaging machinery procurement, understanding lead times is critical for planning production schedules and ensuring timely delivery of equipment, especially in regions with fluctuating demand like the Middle East and Europe.
By grasping these technical properties and trade terms, international B2B buyers can make informed decisions when sourcing packaging machinery from China, ultimately leading to enhanced operational efficiency and cost savings.
Navigating Market Dynamics and Sourcing Trends in the packaging machinery china Sector
What Are the Current Market Dynamics and Key Trends in the Packaging Machinery Sector from China?
The global packaging machinery market is experiencing robust growth, driven by increasing demand for automation and efficiency in production processes. International B2B buyers, particularly from Africa, South America, the Middle East, and Europe, should be aware of several key trends shaping the landscape. Firstly, the rise of e-commerce is pushing manufacturers to adopt flexible packaging solutions that cater to rapid delivery demands. This is particularly evident in regions like Egypt and Mexico, where logistics networks are evolving to support burgeoning online retail markets.
Moreover, advancements in Industry 4.0 technologies, such as IoT, AI, and robotics, are transforming the capabilities of packaging machinery. These technologies enable real-time monitoring, predictive maintenance, and improved operational efficiency, providing significant cost savings for manufacturers. For buyers looking to invest in new machinery, seeking suppliers who integrate these technologies can lead to long-term benefits.
Another noteworthy trend is the increasing focus on customization and personalization in packaging. As consumer preferences shift towards unique and tailored products, packaging machinery that offers flexibility in design and production will be crucial for companies aiming to differentiate themselves in competitive markets. Buyers should prioritize suppliers who can provide adaptable machinery that meets these evolving requirements.
How Important Is Sustainability and Ethical Sourcing in the Packaging Machinery Sector?
Sustainability has become a critical consideration for B2B buyers in the packaging machinery sector, particularly as global environmental concerns intensify. The packaging industry is under scrutiny for its environmental impact, prompting a shift towards sustainable practices. For international buyers, particularly those in regions like South America and the Middle East, sourcing machinery that minimizes waste and energy consumption is essential.
Ethical sourcing is equally important, as consumers increasingly demand transparency in supply chains. Buyers should seek out suppliers who adhere to sustainable practices and possess certifications such as ISO 14001, which focuses on effective environmental management systems. Additionally, the use of biodegradable materials and recyclable packaging is on the rise, making it imperative for buyers to consider suppliers who offer machinery compatible with these materials.
Investing in sustainable packaging machinery not only enhances a company’s brand reputation but also positions it favorably in a market that values corporate responsibility. By prioritizing ethical sourcing and sustainability, B2B buyers can contribute to a greener future while reaping the benefits of modern, efficient machinery.
How Has the Packaging Machinery Sector in China Evolved Over Time?
The evolution of the packaging machinery sector in China can be traced back several decades, marked by rapid industrialization and technological advancements. Initially, the focus was on basic machinery to meet domestic demands. However, as the global market expanded, Chinese manufacturers began investing heavily in R&D, resulting in innovative solutions that meet international standards.
By the early 2000s, China emerged as a leading exporter of packaging machinery, leveraging its manufacturing capabilities and cost advantages. The sector has since evolved to incorporate advanced technologies like automation and smart machinery, positioning China as a key player in the global market. For B2B buyers, understanding this evolution is crucial, as it reflects the ongoing commitment of Chinese manufacturers to improve quality and adapt to global trends, ensuring that they remain competitive in an increasingly demanding marketplace.
Frequently Asked Questions (FAQs) for B2B Buyers of packaging machinery china
-
How do I choose the right packaging machinery supplier in China?
When selecting a packaging machinery supplier in China, consider their experience, industry reputation, and product quality. Check for certifications such as ISO and CE, which indicate adherence to international standards. Engage in direct communication to assess their responsiveness and willingness to customize solutions. Additionally, request references from previous clients to gauge reliability. Conducting a factory audit, if possible, can provide firsthand insight into their operational capabilities and quality control processes. -
What are the typical payment terms for B2B transactions in China?
Payment terms in China can vary widely but often include options such as T/T (Telegraphic Transfer), L/C (Letter of Credit), or D/P (Documents against Payment). A common arrangement is a 30% deposit upfront with the remaining 70% paid before shipment. Ensure to negotiate favorable terms that protect your interests. It’s advisable to clarify payment methods early in the negotiation to avoid misunderstandings that could delay the procurement process. -
What is the minimum order quantity (MOQ) for packaging machinery from China?
MOQs for packaging machinery can differ significantly based on the supplier and the type of machinery. Typically, MOQs range from one unit for high-end or customized machinery to several units for standard models. Be sure to discuss MOQs during initial conversations with suppliers, as some may offer flexibility depending on your business needs or the potential for future orders. -
How can I ensure quality assurance for my packaging machinery order?
To guarantee quality assurance, request a detailed quality control plan from the supplier. This should include the inspection stages during production and pre-shipment testing. Consider hiring a third-party inspection service to evaluate the machinery before shipping. Additionally, ask for product samples or prototypes to assess quality firsthand. Clear communication regarding quality expectations is essential to ensure the final product meets your specifications. -
What should I know about logistics and shipping when importing from China?
Understanding logistics is crucial when importing packaging machinery from China. Determine whether the supplier offers Incoterms like FOB (Free On Board) or CIF (Cost Insurance and Freight), as these will affect your shipping costs and responsibilities. Plan for potential delays, especially during peak seasons. Collaborate with a reliable freight forwarder who can navigate customs regulations and ensure timely delivery. It’s also wise to factor in additional costs such as tariffs and local taxes. -
How can I customize packaging machinery to meet my specific needs?
Most Chinese manufacturers offer customization options for their machinery. Begin by clearly defining your requirements, including size, capacity, and specific functionalities. Discuss these needs with potential suppliers to assess their ability to adapt their products. Request detailed proposals and timelines for customization. Be prepared for potential cost increases and ensure that customization aligns with your production timelines to avoid disruptions. -
What are the common types of packaging machinery available from Chinese suppliers?
Chinese suppliers offer a wide range of packaging machinery, including but not limited to filling machines, sealing machines, labeling machines, and cartoning machines. The choice of machinery often depends on the product type and packaging requirements. Research the specific machinery that best suits your industry and application, and consult with suppliers to identify the most effective solutions for your packaging needs. -
How do I handle after-sales service and support for machinery purchased from China?
After-sales service is a critical factor in ensuring the longevity and efficiency of your packaging machinery. Before finalizing a purchase, inquire about the supplier’s warranty and support policies. Confirm if they provide spare parts, technical support, and training for your staff. Establish clear communication channels for after-sales inquiries and consider suppliers with a strong track record of customer service to mitigate potential issues post-purchase.
Important Disclaimer & Terms of Use
⚠️ Important Disclaimer
The information provided in this guide, including content regarding manufacturers, technical specifications, and market analysis, is for informational and educational purposes only. It does not constitute professional procurement advice, financial advice, or legal advice.
While we have made every effort to ensure the accuracy and timeliness of the information, we are not responsible for any errors, omissions, or outdated information. Market conditions, company details, and technical standards are subject to change.
B2B buyers must conduct their own independent and thorough due diligence before making any purchasing decisions. This includes contacting suppliers directly, verifying certifications, requesting samples, and seeking professional consultation. The risk of relying on any information in this guide is borne solely by the reader.
Strategic Sourcing Conclusion and Outlook for packaging machinery china
What Are the Key Takeaways for Strategic Sourcing in Packaging Machinery from China?
In summary, strategic sourcing from China for packaging machinery presents a wealth of opportunities for international B2B buyers. By leveraging China’s advanced manufacturing capabilities and competitive pricing, businesses from Africa, South America, the Middle East, and Europe can enhance their operational efficiency and product packaging quality. Key takeaways include the importance of due diligence in supplier selection, the necessity of understanding local regulations, and the benefits of building long-term partnerships with reputable manufacturers.
How Can Buyers Prepare for Future Opportunities?
As the packaging machinery market continues to evolve, staying informed about technological advancements and market trends will be crucial. Buyers should prioritize flexibility and adaptability in their sourcing strategies to remain competitive. Engaging in continuous dialogue with suppliers can foster innovation and improve supply chain resilience.
What Steps Should International Buyers Take Next?
Now is the time for international buyers to take action. Begin by identifying potential suppliers in China, assessing their capabilities, and exploring collaborative opportunities. Invest in building relationships that can drive mutual growth and adaptation to changing market demands. Embrace the potential of strategic sourcing to transform your packaging operations and position your business for future success in a dynamic global marketplace.