Cut Costs with Pre Fabricated Homes China: The Ultimate Guide (2025)
Introduction: Navigating the Global Market for pre fabricated homes china
As international B2B buyers increasingly seek efficient and sustainable building solutions, sourcing prefabricated homes from China presents a unique opportunity. The challenge lies in navigating a market that is rich in options yet complex in terms of quality and compliance standards. This comprehensive guide is designed to demystify the process of acquiring prefabricated homes from China, covering essential topics such as types of homes available, their applications across different sectors, and effective supplier vetting strategies.
Throughout this guide, we will delve into the various materials and construction methods used in prefabricated homes, helping you identify the best fit for your specific needs. Additionally, we will explore cost considerations, including pricing structures and potential hidden fees that could impact your budget. By providing insights into the regulatory environment and quality assurance practices, this guide empowers B2B buyers from regions like Africa, South America, the Middle East, and Europe—including Poland and the UK—to make informed purchasing decisions.
Equipped with this knowledge, you can approach the procurement of prefabricated homes with confidence, ensuring that your investments yield long-term benefits and align with your organizational goals.
Understanding pre fabricated homes china Types and Variations
Type Name | Key Distinguishing Features | Primary B2B Applications | Brief Pros & Cons for Buyers |
---|---|---|---|
Modular Homes | Built in sections, easily transportable, customizable | Residential, commercial, disaster relief | Pros: Quick assembly, flexible design. Cons: Transportation costs for remote areas. |
Container Homes | Utilizes shipping containers, eco-friendly, robust | Affordable housing, offices, pop-up shops | Pros: Low cost, durable. Cons: Limited space, insulation challenges. |
SIP (Structural Insulated Panel) Homes | High energy efficiency, quick assembly, solid insulation | Residential, energy-efficient buildings | Pros: Energy savings, reduced construction time. Cons: Higher initial cost. |
Prefab Timber Frame Homes | Traditional aesthetics, sustainable materials | Residential, vacation homes | Pros: Customizable, appealing design. Cons: Longer build times compared to modular. |
Panelized Homes | Flat-pack design, easy shipping, fast assembly | Residential, affordable housing | Pros: Cost-effective, quick setup. Cons: Limited design flexibility. |
What Are Modular Homes and How Are They Used in B2B Transactions?
Modular homes are constructed in sections (modules) in a factory setting before being transported to the site for assembly. This type of prefabricated home is ideal for both residential and commercial applications, including disaster relief housing. B2B buyers appreciate the quick assembly and customizable designs, allowing for tailored solutions to meet specific project requirements. However, transportation costs can be a concern, especially for buyers in remote areas.
How Do Container Homes Serve the B2B Market?
Container homes repurpose shipping containers into livable spaces, making them an eco-friendly choice for various applications, including affordable housing and temporary offices. Their robust construction appeals to businesses seeking durability and low costs. While they offer significant savings, potential buyers must consider space limitations and insulation challenges, which may affect comfort and utility.
What Are the Benefits of SIP Homes for B2B Buyers?
Structural Insulated Panel (SIP) homes are known for their high energy efficiency and rapid assembly time. They are particularly suitable for residential and energy-efficient building projects. B2B buyers can benefit from reduced energy costs over time, making them a wise investment. However, the initial cost may be higher than traditional building methods, which could be a barrier for some buyers.
Why Choose Prefab Timber Frame Homes for Your Projects?
Prefab timber frame homes combine traditional aesthetics with modern construction methods, utilizing sustainable materials. These homes are popular for residential and vacation properties, appealing to buyers looking for customizable and attractive designs. While they offer a unique look, the construction time may be longer compared to modular options, which is an important consideration for project timelines.
What Are Panelized Homes and Their Market Applications?
Panelized homes feature a flat-pack design that allows for easy shipping and quick assembly on-site. This type of prefabricated home is often used in residential projects and affordable housing initiatives. B2B buyers appreciate the cost-effectiveness and rapid setup, making them ideal for developers on tight schedules. However, the limited design flexibility may restrict some buyers looking for more customized solutions.
Related Video: The Harsh Reality Of Manufactured Homes From China
Key Industrial Applications of pre fabricated homes china
Industry/Sector | Specific Application of pre fabricated homes china | Value/Benefit for the Business | Key Sourcing Considerations for this Application |
---|---|---|---|
Construction | Modular housing for rapid deployment | Accelerates project timelines and reduces costs | Compliance with local building codes and standards |
Disaster Relief | Emergency shelters and housing solutions | Provides quick relief and housing in crisis | Durability and transportability for rapid setup |
Hospitality | Prefabricated hotels and lodges | Reduces construction time and enhances ROI | Aesthetic appeal and customization options |
Education | Temporary classrooms and dormitories | Addresses urgent educational needs | Sustainability and integration with existing infrastructure |
Healthcare | Mobile clinics and temporary healthcare facilities | Enhances access to medical services | Health standards compliance and adaptability to local needs |
How Are Prefabricated Homes Used in the Construction Industry?
In the construction sector, prefabricated homes from China serve as modular housing solutions that facilitate rapid deployment on-site. These homes significantly shorten project timelines, allowing businesses to meet tight deadlines while keeping labor costs manageable. International buyers, especially from regions like Africa and South America, should focus on compliance with local building regulations, which may vary significantly, to ensure successful project integration.
What Role Do Prefabricated Homes Play in Disaster Relief?
Prefabricated homes are crucial in disaster relief scenarios, providing emergency shelters and housing solutions for displaced populations. These structures can be rapidly assembled, offering immediate shelter in crisis situations such as natural disasters. Buyers in the Middle East and Europe must prioritize durability and transportability, ensuring that these homes can withstand harsh conditions and be easily transported to affected areas.
How Are Prefabricated Homes Beneficial for the Hospitality Industry?
In the hospitality sector, prefabricated homes are increasingly used to construct hotels and lodges. These buildings allow for reduced construction time, which can significantly enhance return on investment (ROI) by enabling quicker openings. B2B buyers from Europe, particularly in the UK, should consider the aesthetic appeal and customization options available to align with their brand identity and guest expectations.
Why Are Prefabricated Homes Important for Educational Institutions?
Educational institutions utilize prefabricated homes to create temporary classrooms and dormitories, especially in areas facing urgent educational demands. These solutions can be deployed quickly to accommodate growing student populations or replace damaged facilities. Buyers must ensure that these structures are sustainable and can be integrated into existing infrastructure without significant disruption.
How Do Prefabricated Homes Enhance Healthcare Accessibility?
In the healthcare sector, prefabricated homes are used to create mobile clinics and temporary healthcare facilities, particularly in underserved areas. This application enhances access to medical services and can be critical during public health emergencies. International buyers should emphasize compliance with health standards and adaptability to local healthcare needs to maximize the effectiveness of these solutions.
Related Video: The whole installation process of China prefab Flat-pack container house in 6 minutes.
3 Common User Pain Points for ‘pre fabricated homes china’ & Their Solutions
Scenario 1: Navigating Quality Assurance in Prefabricated Homes
The Problem:
International B2B buyers often encounter quality assurance challenges when sourcing prefabricated homes from China. The primary concern is ensuring that the homes meet international building standards and local regulations. Without a robust inspection process, buyers may receive subpar products, leading to potential structural issues and costly renovations down the line. This scenario is particularly troubling for buyers in regions like Africa and South America, where local building codes may significantly differ from Chinese standards.
The Solution:
To mitigate these risks, B2B buyers should establish a comprehensive quality assurance protocol before placing orders. This includes engaging with reputable third-party inspection services that specialize in prefabricated structures. These services can conduct pre-shipment inspections to verify that the homes comply with both Chinese manufacturing standards and the specific regulations of the buyer’s country.
Moreover, buyers should request detailed documentation from manufacturers that outlines material specifications, construction methodologies, and compliance certifications. It is advisable to create a checklist based on local building codes to ensure all aspects are covered. Establishing a direct line of communication with the manufacturer to discuss quality concerns and expectations can also foster a more reliable partnership. This proactive approach not only secures a quality product but also builds trust with suppliers.
Scenario 2: Overcoming Logistical Challenges in Transportation
The Problem:
Transportation logistics present a significant hurdle for B2B buyers of prefabricated homes from China. The complexity of shipping large modular units can lead to delays, increased costs, and even damage during transit. Buyers in Europe, particularly in countries like Poland and the UK, may struggle with navigating customs regulations and ensuring that the homes arrive intact and on time.
The Solution:
To streamline logistics, buyers should partner with logistics companies that specialize in international shipping of prefabricated buildings. These firms can offer insights into the best shipping methods, whether by sea or land, and help navigate the intricate customs processes.
Additionally, buyers should consider modular designs that facilitate easier transport. Working closely with manufacturers to understand the dimensions and weight limits of shipping containers can prevent logistical issues. Implementing a phased delivery schedule, where components are shipped in stages rather than all at once, can also reduce the risk of damage and make the assembly process more manageable upon arrival.
Finally, creating a detailed shipping timeline that includes buffer periods for unexpected delays can ensure that projects remain on track despite potential disruptions.
Scenario 3: Addressing Customization Limitations in Prefabricated Homes
The Problem:
Customization is often a significant concern for B2B buyers seeking prefabricated homes. Many manufacturers in China offer limited design options, which can be a dealbreaker for buyers looking to meet specific aesthetic or functional requirements. This limitation can hinder projects in diverse markets across the Middle East and Europe, where cultural preferences and architectural styles vary widely.
The Solution:
To tackle customization challenges, buyers should engage manufacturers who are flexible and willing to collaborate on design modifications. Before finalizing a contract, it is essential to conduct thorough research on potential suppliers to assess their capability for customization. Requesting a portfolio of previous projects can provide insight into their flexibility and creativity.
Additionally, buyers should consider incorporating modular design principles that allow for easier customization without compromising structural integrity. Proposing a co-design approach, where both the buyer and manufacturer participate in the design process, can lead to tailored solutions that meet the buyer’s needs while leveraging the manufacturer’s expertise.
Finally, investing in 3D visualization tools can help buyers and manufacturers align their visions more effectively. By visualizing the final product before construction begins, both parties can make necessary adjustments early in the process, saving time and resources in the long run.
Strategic Material Selection Guide for pre fabricated homes china
What Are the Key Materials Used in Prefabricated Homes from China?
When considering prefabricated homes from China, the selection of materials is crucial for ensuring product performance, longevity, and compliance with international standards. Below, we analyze four common materials used in the construction of these homes, focusing on their properties, advantages, disadvantages, and specific considerations for international B2B buyers.
Steel: A Durable Choice for Prefabricated Homes
Key Properties
Steel is renowned for its high strength-to-weight ratio, making it an ideal choice for structural frameworks. It offers excellent temperature and pressure ratings, along with superior corrosion resistance when treated with protective coatings.
Pros & Cons
The durability of steel contributes to the longevity of prefabricated homes, while its relatively low cost compared to other metals makes it an attractive option. However, the manufacturing complexity can be higher, requiring specialized equipment and skilled labor. Additionally, steel structures may require insulation to mitigate thermal conductivity.
Impact on Application
Steel is particularly compatible with various media, including water and electrical systems, making it versatile for different applications in prefabricated homes.
Considerations for International Buyers
B2B buyers from regions like Africa and the Middle East should ensure compliance with local building codes and standards such as ASTM and EN. The availability of steel can vary, so sourcing from reliable suppliers is essential.
Concrete: The Foundation of Stability
Key Properties
Concrete is known for its compressive strength and durability, with excellent fire resistance and thermal mass properties that help regulate indoor temperatures.
Pros & Cons
While concrete is relatively inexpensive and widely available, its weight can complicate transportation and assembly. Additionally, it may require longer curing times, which can delay project timelines.
Impact on Application
Concrete is suitable for foundations and load-bearing walls, providing stability in various environmental conditions. Its compatibility with insulation materials enhances energy efficiency.
Considerations for International Buyers
Buyers in Europe, particularly in countries like Poland, should consider local regulations regarding concrete quality and environmental impact. Compliance with standards such as DIN can influence material selection.
Wood: A Sustainable and Aesthetic Option
Key Properties
Wood is lightweight and offers good insulation properties, making it a popular choice for residential applications. Its natural aesthetic appeal is another significant advantage.
Pros & Cons
While wood is renewable and can be sourced sustainably, it is susceptible to pests and moisture, which can compromise its durability. Additionally, the cost can vary significantly based on the type of wood used.
Impact on Application
Wood is ideal for interior finishes and non-load-bearing walls, providing flexibility in design. However, its compatibility with certain climates, particularly humid regions, must be assessed.
Considerations for International Buyers
Buyers from South America and Africa should prioritize wood sourced from sustainably managed forests to meet environmental regulations. Familiarity with local building codes regarding wood treatment and fire safety is essential.
Composite Materials: Innovation in Construction
Key Properties
Composite materials, often made from a combination of wood fibers and plastic, offer excellent weather resistance and durability. They are lightweight and can be molded into various shapes.
Pros & Cons
The main advantage of composites is their low maintenance requirements and resistance to rot and decay. However, they can be more expensive than traditional materials and may not have the same structural integrity as steel or concrete.
Impact on Application
Composites are often used for exterior cladding and decking, providing aesthetic appeal and durability against the elements.
Considerations for International Buyers
Compliance with international standards for composites, such as ASTM D7032, is crucial for buyers from Europe and the Middle East. Understanding the environmental impact and recyclability of composite materials is also important for sustainable practices.
Summary Table of Material Selection
Material | Typical Use Case for Prefabricated Homes China | Key Advantage | Key Disadvantage/Limitation | Relative Cost (Low/Med/High) |
---|---|---|---|---|
Steel | Structural frameworks and load-bearing components | High strength and durability | Requires insulation for thermal efficiency | Medium |
Concrete | Foundations and load-bearing walls | Excellent fire resistance | Heavy and requires curing time | Low |
Wood | Interior finishes and non-load-bearing walls | Aesthetic appeal and insulation | Susceptible to pests and moisture | Medium to High |
Composite | Exterior cladding and decking | Low maintenance and weather resistance | Higher cost and lower structural integrity | High |
This guide provides a comprehensive overview of the materials commonly used in prefabricated homes from China, enabling international B2B buyers to make informed decisions that align with their specific needs and compliance requirements.
In-depth Look: Manufacturing Processes and Quality Assurance for pre fabricated homes china
What Are the Key Manufacturing Processes for Prefabricated Homes in China?
The manufacturing of prefabricated homes in China involves a series of well-defined stages, ensuring efficiency and quality. Understanding these processes is crucial for international B2B buyers looking to source reliable prefabricated housing solutions.
How Is Material Preparation Conducted in Prefabricated Home Manufacturing?
The first step in the manufacturing process is material preparation. This involves sourcing high-quality raw materials such as steel, wood, and insulation. Suppliers often prefer materials that meet international standards to ensure durability and safety. Key techniques include:
- Material Sourcing: Establishing relationships with reputable suppliers to guarantee the quality of materials.
- Quality Inspection: Conducting Incoming Quality Control (IQC) to verify the materials meet specified standards before they enter the production line.
What Forming Techniques Are Utilized in Prefabricated Home Manufacturing?
Once materials are prepared, the next stage is forming. This process shapes the raw materials into components for the prefabricated home. Techniques commonly employed include:
- CNC Machining: Computer Numerical Control (CNC) machines are used for precision cutting and shaping of materials, ensuring uniformity and accuracy.
- Molding and Casting: For concrete components, molds are created to form walls and other structures, providing structural integrity and design flexibility.
How Are Components Assembled in Prefabricated Home Production?
The assembly stage involves putting together the prefabricated components into a complete structure. This process typically includes:
- Modular Assembly: Components are prefabricated in a factory setting, which minimizes on-site construction time and reduces labor costs.
- Quality Checks: In-Process Quality Control (IPQC) is essential during assembly to ensure that components fit correctly and meet design specifications.
What Finishing Techniques Are Applied to Prefabricated Homes?
Finishing is the final stage in the manufacturing process, where the home is prepared for delivery. This includes:
- Painting and Coating: Applying finishes to protect materials and enhance aesthetic appeal.
- Final Assembly: Final touches such as installing fixtures and fittings take place, followed by a thorough inspection.
What Quality Assurance Measures Are Implemented for Prefabricated Homes?
Quality assurance is critical in ensuring that prefabricated homes meet international standards and buyer expectations. Various quality control measures are integrated throughout the manufacturing process.
Which International Standards Are Relevant for Prefabricated Home Quality?
International standards play a significant role in the quality assurance of prefabricated homes. Key standards include:
- ISO 9001: This standard focuses on quality management systems, ensuring consistent quality in products and services.
- CE Marking: A certification that indicates conformity with health, safety, and environmental protection standards for products sold within the European Economic Area.
- API Standards: For homes that utilize steel components, adherence to American Petroleum Institute (API) standards ensures the quality of materials used.
What Are the Critical QC Checkpoints During Manufacturing?
Quality control checkpoints are integrated at various stages of the manufacturing process:
- Incoming Quality Control (IQC): Inspecting raw materials upon arrival to ensure they meet required specifications.
- In-Process Quality Control (IPQC): Continuous monitoring during the assembly phase to identify any defects or deviations from standards.
- Final Quality Control (FQC): A comprehensive inspection of the finished product before it is shipped to ensure it meets all specifications and quality requirements.
What Common Testing Methods Are Used for Quality Assurance?
To ensure quality, several testing methods are employed, including:
- Destructive and Non-Destructive Testing: Methods such as tensile testing for materials and ultrasonic testing for welds to ensure structural integrity.
- Thermal Imaging: Used to detect insulation effectiveness and energy efficiency in finished homes.
- Water Tightness Tests: Ensuring the home can withstand environmental elements without compromising safety.
How Can B2B Buyers Verify Supplier Quality Assurance?
For international B2B buyers, verifying the quality assurance processes of suppliers is crucial. Here are some actionable steps:
- Conduct Audits: Regular supplier audits can help assess compliance with quality standards and processes. This can be done in person or through third-party agencies.
- Request Quality Reports: Suppliers should provide documentation of quality tests and inspections, demonstrating adherence to international standards.
- Engage Third-Party Inspectors: Hiring independent inspectors can provide an unbiased assessment of the quality of prefabricated homes before purchase.
What Are the Quality Control Nuances for International B2B Buyers?
International buyers, particularly from regions like Africa, South America, the Middle East, and Europe, should be aware of specific nuances related to quality control:
- Cultural Considerations: Understanding local manufacturing practices and regulatory environments can help buyers better assess quality.
- Regulatory Compliance: Different regions may have varying standards; ensuring compliance with local regulations is essential for successful importation.
- Communication: Establishing clear communication channels with suppliers regarding quality expectations can prevent misunderstandings and ensure product conformity.
Conclusion
Understanding the manufacturing processes and quality assurance measures for prefabricated homes in China is essential for B2B buyers. By focusing on material preparation, forming techniques, assembly methods, and quality control measures, buyers can make informed decisions and ensure they source high-quality prefabricated homes that meet their specific needs and standards.
Practical Sourcing Guide: A Step-by-Step Checklist for ‘pre fabricated homes china’
To successfully source prefabricated homes from China, it’s essential to follow a structured approach that minimizes risks and maximizes value. This guide provides a practical checklist to help B2B buyers navigate the complexities of international procurement in this sector.
Step 1: Define Your Technical Specifications
Before initiating the sourcing process, clearly outline your technical specifications for the prefabricated homes. This includes dimensions, materials, design styles, and any specific building codes relevant to your target market.
– Why It Matters: Defining your requirements ensures that you communicate effectively with suppliers and receive accurate quotations.
– What to Look For: Ensure your specifications align with local regulations in your country, such as environmental standards or safety codes.
Step 2: Research the Market Landscape
Conduct thorough research on the current market for prefabricated homes in China. Identify the leading manufacturers and their product offerings.
– Why It Matters: Understanding market dynamics helps you identify potential suppliers and assess their capabilities.
– What to Look For: Pay attention to trends, innovations, and the competitive landscape to make informed decisions.
Step 3: Evaluate Potential Suppliers
Before committing, it’s crucial to vet suppliers thoroughly. Request company profiles, case studies, and references from buyers in a similar industry or region.
– Why It Matters: A comprehensive evaluation reduces the risk of fraud and ensures that the supplier can meet your quality standards.
– What to Look For:
– Certifications: Ensure suppliers have relevant certifications such as ISO 9001 for quality management.
– Production Capacity: Assess if the supplier can meet your volume requirements within your timeline.
Step 4: Request Samples and Prototypes
Once you have shortlisted potential suppliers, request samples or prototypes of their prefabricated homes. This step is vital to assess quality firsthand.
– Why It Matters: Evaluating samples allows you to ensure that the product meets your expectations before making a larger investment.
– What to Look For: Examine the quality of materials, craftsmanship, and adherence to your specifications.
Step 5: Negotiate Terms and Conditions
Engage in negotiations to establish clear terms of service, including payment terms, delivery schedules, and warranties.
– Why It Matters: Clear agreements help prevent misunderstandings and ensure that both parties are aligned.
– What to Look For: Be cautious of terms that seem too favorable; ensure they are realistic and provide adequate protection for your investment.
Step 6: Verify Logistics and Shipping Arrangements
Discuss logistics and shipping arrangements in detail with your supplier. Confirm shipping timelines, packaging standards, and customs documentation.
– Why It Matters: Understanding logistics is crucial for timely delivery and avoiding unexpected costs.
– What to Look For: Ensure that the supplier has experience handling international shipments and can provide support with customs clearance.
Step 7: Plan for Post-Purchase Support
Establish a plan for post-purchase support, including installation assistance and after-sales service.
– Why It Matters: A reliable support system enhances your investment and ensures customer satisfaction.
– What to Look For: Check the supplier’s policies on warranty claims and the availability of spare parts.
By following this structured sourcing checklist, international B2B buyers can make informed decisions when procuring prefabricated homes from China, ensuring a successful partnership and investment.
Comprehensive Cost and Pricing Analysis for pre fabricated homes china Sourcing
Understanding the cost structure and pricing dynamics of prefabricated homes sourced from China is essential for international B2B buyers, particularly those from regions like Africa, South America, the Middle East, and Europe. This analysis will break down the various components of costs and the factors influencing pricing, as well as provide actionable tips for buyers.
What Are the Key Cost Components in Prefabricated Homes Sourcing?
-
Materials: The choice of materials significantly impacts the overall cost. Common materials include steel, wood, and concrete. High-quality materials often come at a premium but can enhance durability and reduce long-term maintenance costs.
-
Labor: Labor costs in China can vary based on the region and the skill level of the workforce. Skilled labor may command higher wages, but investing in quality craftsmanship can lead to better outcomes and reduce the risk of defects.
-
Manufacturing Overhead: This encompasses the indirect costs of production, including utilities, rent, and administrative expenses. Efficient manufacturing processes can help minimize these costs, which can be a critical factor in competitive pricing.
-
Tooling: Initial tooling costs can be significant, especially for customized designs. Buyers should be aware that these costs may be amortized over larger orders, making bulk purchases more economical.
-
Quality Control (QC): Implementing robust QC processes ensures that products meet specified standards. While this adds to costs, it can prevent costly returns and improve buyer satisfaction.
-
Logistics: Shipping costs can fluctuate based on distance, shipping method, and current fuel prices. Understanding Incoterms is crucial, as they define the responsibilities of buyers and sellers in terms of shipping and risk.
-
Margin: Suppliers typically include a profit margin in their pricing, which can vary based on market demand and competition. Understanding market conditions can provide leverage during negotiations.
How Do Price Influencers Affect the Cost of Prefabricated Homes?
-
Volume and Minimum Order Quantity (MOQ): Purchasing in larger quantities usually leads to discounts. Buyers should negotiate MOQs that align with their project needs while maximizing cost-efficiency.
-
Specifications and Customization: Customized designs can drive up costs. Buyers should assess whether standard models could meet their needs to avoid unnecessary expenses.
-
Material Choices: The selection of materials can drastically alter pricing. Buyers should balance between cost and quality to optimize their investment.
-
Quality and Certifications: Products that meet international standards may carry higher initial costs but can offer long-term savings through durability and reduced risk of compliance issues.
-
Supplier Factors: The reputation and reliability of suppliers play a crucial role in pricing. Established suppliers may offer better quality and service but could be pricier. Buyers should conduct thorough due diligence.
-
Incoterms: Understanding the implications of different Incoterms (like FOB, CIF, etc.) is essential for predicting total costs, as they define who bears shipping costs and risks.
What Buyer Tips Can Optimize Cost Efficiency in Sourcing Prefabricated Homes?
-
Negotiation: Engage in open discussions with suppliers about pricing, especially if you have a strong purchasing volume. Leverage competitive quotes from multiple suppliers to strengthen your position.
-
Total Cost of Ownership (TCO): Consider not just the initial purchase price but also long-term factors such as maintenance, energy efficiency, and resale value. A higher upfront cost may lead to savings over time.
-
Understand Pricing Nuances: International buyers should be aware of currency fluctuations and tariffs that could affect costs. Engaging a local expert or consultant may provide insights into the local market dynamics.
-
Explore Financing Options: Some suppliers may offer financing or payment plans that can ease the upfront financial burden, allowing for better cash flow management.
-
Build Relationships: Establishing long-term relationships with suppliers can lead to more favorable terms and pricing. Consistent business often results in loyalty discounts and priority service.
Disclaimer on Pricing
Please note that the prices mentioned in this analysis are indicative and may vary based on current market conditions, specific supplier negotiations, and project requirements. It is crucial for buyers to conduct their own research and obtain updated quotes to ensure accurate budgeting for their projects.
Alternatives Analysis: Comparing pre fabricated homes china With Other Solutions
Understanding Alternatives to Pre-Fabricated Homes from China
In the evolving construction landscape, international B2B buyers are increasingly exploring alternatives to pre-fabricated homes from China. These alternatives can offer varying benefits in terms of cost, performance, and suitability for specific market needs. This analysis aims to provide a clear comparison between pre-fabricated homes from China and other viable housing solutions, enabling buyers to make informed decisions.
Comparison Table
Comparison Aspect | Pre Fabricated Homes China | Modular Homes | Traditional Brick-and-Mortar Construction |
---|---|---|---|
Performance | Quick assembly, high quality | Flexible designs, durable | High durability, good insulation |
Cost | Competitive pricing | Moderate to high cost | High upfront costs, long-term value |
Ease of Implementation | Fast setup, minimal site work | Requires skilled labor | Lengthy process, extensive labor needed |
Maintenance | Low maintenance, durable materials | Moderate maintenance | High maintenance, dependent on materials |
Best Use Case | Rapid deployment, temporary or permanent needs | Custom residential projects | Long-term residential and commercial buildings |
Exploring Alternative Housing Solutions
What are Modular Homes and How Do They Compare?
Modular homes are prefabricated structures built in sections in a factory and assembled on-site. They offer flexibility in design and can be customized to meet specific buyer needs. While the initial cost can be moderate to high, modular homes typically provide excellent long-term value due to their durability. However, they require skilled labor for assembly, which may complicate the implementation process compared to the straightforward assembly of pre-fabricated homes from China.
How Does Traditional Brick-and-Mortar Construction Stack Up?
Traditional brick-and-mortar construction involves building homes on-site using conventional materials like bricks and concrete. This method is renowned for its durability and excellent insulation properties, making it suitable for long-term residential and commercial use. However, it typically involves higher upfront costs and a lengthy construction timeline. Additionally, maintenance can be significant due to wear and tear over time. Compared to pre-fabricated homes, traditional construction lacks the speed and efficiency of assembly, which could be a crucial consideration for buyers needing rapid deployment.
Conclusion: Choosing the Right Solution for Your Needs
When evaluating housing solutions, B2B buyers must consider specific needs such as budget, project timeline, and intended use. Pre-fabricated homes from China offer a compelling option for those needing quick, cost-effective solutions without sacrificing quality. In contrast, modular homes may appeal to buyers looking for customization and design flexibility, while traditional construction remains a strong choice for long-term investments despite its higher costs and longer timelines. Ultimately, the right choice will depend on the unique circumstances and goals of the buyer.
Essential Technical Properties and Trade Terminology for pre fabricated homes china
What Are the Essential Technical Properties of Prefabricated Homes from China?
When considering prefabricated homes from China, international B2B buyers must pay close attention to several critical technical properties that affect quality, durability, and compliance with local regulations. Here are key specifications to understand:
1. Material Grade and Composition
The grade of materials used in prefabricated homes, such as steel, wood, or composite materials, is crucial for assessing strength and durability. Higher-grade materials typically indicate better resistance to environmental factors, longevity, and overall structural integrity. For buyers, understanding material grades helps in evaluating quality and ensuring compliance with local building codes.
2. Tolerance Levels
Tolerance refers to the allowable deviation in dimensions during the manufacturing process. For prefabricated homes, maintaining precise tolerances is vital to ensure that components fit together correctly on-site. Buyers should specify tolerance levels in their contracts to avoid costly adjustments and ensure the structural stability of the assembled home.
3. Insulation Values
Insulation values, often represented by R-values or U-values, indicate a material’s effectiveness in preventing heat loss or gain. In regions with extreme climates, high insulation ratings can significantly impact energy efficiency and comfort levels. Buyers from varying climates should prioritize insulation specifications to ensure that the homes meet energy efficiency standards and provide comfort.
4. Load-Bearing Capacity
Understanding the load-bearing capacity is essential for ensuring that the prefabricated home can support the weight of occupants, furniture, and environmental factors such as snow or wind. This specification is particularly important in regions prone to extreme weather conditions. Buyers must verify that the designs meet local safety regulations and standards.
5. Fire Resistance Ratings
Fire resistance ratings indicate how well a material can withstand fire exposure. This specification is critical for safety and regulatory compliance. Buyers should inquire about the fire ratings of materials used in prefabricated homes, especially in regions with strict fire safety regulations.
6. Environmental Certifications
Many buyers are now looking for homes that meet specific environmental standards or certifications, such as LEED (Leadership in Energy and Environmental Design) or ISO certifications. These certifications indicate that the home meets certain sustainability criteria, which can be a significant selling point in many markets.
What Key Trade Terms Should International Buyers Understand?
Navigating the world of prefabricated homes also requires familiarity with industry-specific terminology. Here are some essential trade terms that buyers should know:
1. OEM (Original Equipment Manufacturer)
OEM refers to a company that produces parts or equipment that may be marketed by another manufacturer. In the context of prefabricated homes, it often denotes the supplier of components. Understanding OEM relationships can help buyers ensure they are sourcing high-quality materials.
2. MOQ (Minimum Order Quantity)
MOQ is the smallest quantity of a product that a supplier is willing to sell. For B2B buyers, knowing the MOQ is essential for budgeting and inventory management. Low MOQs can offer flexibility for smaller projects, while higher MOQs may lead to cost savings on larger orders.
3. RFQ (Request for Quotation)
An RFQ is a document issued by a buyer to request pricing and other terms from suppliers. It is a critical step in the procurement process for prefabricated homes, allowing buyers to compare offers and ensure they receive competitive pricing and terms.
4. Incoterms (International Commercial Terms)
Incoterms are a set of predefined commercial terms published by the International Chamber of Commerce that clarify the responsibilities of buyers and sellers in international transactions. Familiarity with these terms helps buyers understand shipping costs, risk transfer, and delivery responsibilities.
5. Lead Time
Lead time refers to the amount of time it takes from placing an order to receiving the product. In the prefabricated home industry, understanding lead times is crucial for project planning and meeting construction schedules.
6. Warranty and After-Sales Support
Warranty terms specify the conditions under which a supplier will repair or replace defective products. Understanding warranty conditions and after-sales support is vital for buyers to ensure they have recourse in case of defects or issues post-purchase.
In conclusion, understanding these technical properties and trade terms is essential for international B2B buyers of prefabricated homes from China. This knowledge not only aids in making informed purchasing decisions but also ensures compliance with local regulations and quality expectations.
Navigating Market Dynamics and Sourcing Trends in the pre fabricated homes china Sector
What Are the Key Trends Driving the Prefabricated Homes Market in China?
The prefabricated homes sector in China is currently experiencing significant growth, driven by various global factors. One of the primary drivers is the increasing demand for affordable housing solutions in urban areas, particularly in developing regions across Africa, South America, and the Middle East. The rapid urbanization in these areas necessitates innovative housing solutions that can be delivered quickly and cost-effectively.
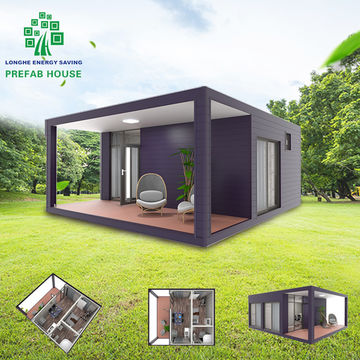
A stock image related to pre fabricated homes china.
Another trend is the integration of advanced technologies in the prefabrication process. B2B buyers are increasingly looking for suppliers who employ cutting-edge manufacturing techniques, such as 3D printing and automation, which enhance efficiency and reduce costs. Furthermore, the rise of digital platforms for sourcing and procurement is reshaping how international buyers engage with Chinese manufacturers, allowing for streamlined communication and transaction processes.
Sustainability is also emerging as a critical factor in sourcing decisions. International buyers are prioritizing suppliers that adhere to sustainable practices and offer eco-friendly materials, reflecting a broader global shift toward environmental responsibility. The Chinese government’s support for green building initiatives further propels this trend, making it easier for B2B buyers to find compliant suppliers.
How Can B2B Buyers Ensure Sustainability and Ethical Sourcing in Prefabricated Homes?
As global awareness of environmental issues grows, sustainability and ethical sourcing have become paramount considerations for B2B buyers in the prefabricated homes sector. The environmental impact of construction materials and processes is under scrutiny, pushing buyers to seek suppliers that prioritize sustainability.
Buyers should look for manufacturers that use certified green materials, such as recycled steel, sustainably sourced wood, and low-VOC (volatile organic compounds) paints. Certifications like LEED (Leadership in Energy and Environmental Design) and ISO 14001 (Environmental Management) can serve as indicators of a supplier’s commitment to sustainable practices.
Additionally, ethical supply chains play a crucial role in ensuring that the materials sourced are not only environmentally friendly but also socially responsible. This includes fair labor practices and transparency in sourcing. Buyers are encouraged to conduct due diligence on their suppliers, including site visits and audits, to verify claims of sustainability and ethical practices.
What is the Historical Context of Prefabricated Homes in China for B2B Buyers?
The history of prefabricated homes in China dates back to the 1950s, primarily as a response to housing shortages following the establishment of the People’s Republic of China. Initially, these homes were constructed using basic materials and methods, focusing on rapid deployment rather than design or sustainability.
However, the market has evolved significantly over the decades. The 1990s saw the introduction of more advanced prefabrication techniques and materials, spurred by urbanization and a growing middle class. In recent years, the focus has shifted towards high-quality, customizable solutions that cater to the diverse needs of international buyers.
Today, prefabricated homes are not just a domestic solution but a viable export option for Chinese manufacturers. With advancements in technology and a commitment to sustainability, the sector is well-positioned to meet the demands of global B2B buyers, especially those from regions looking for innovative and efficient housing solutions.
Frequently Asked Questions (FAQs) for B2B Buyers of pre fabricated homes china
-
How do I select the right supplier for prefabricated homes from China?
Selecting the right supplier involves thorough research and due diligence. Start by assessing the supplier’s reputation through online reviews, industry certifications, and client testimonials. Request samples or visit previous projects to evaluate quality. It’s crucial to ensure they comply with international building standards and regulations pertinent to your region. Additionally, consider their capacity for customization and responsiveness to inquiries, which are indicators of reliability and partnership potential. -
What are the common payment terms when sourcing prefabricated homes from China?
Payment terms can vary significantly among suppliers, but most commonly include a deposit (usually 30% upfront) followed by the balance upon shipment or delivery. Some suppliers may offer letters of credit or escrow services to enhance security. It’s important to negotiate terms that protect your interests, considering factors like order size and payment history. Always ensure that the payment method aligns with international trade regulations and is secure. -
What is the minimum order quantity (MOQ) for prefabricated homes from Chinese manufacturers?
The MOQ for prefabricated homes can vary widely depending on the manufacturer and the complexity of the design. Typically, MOQs range from one complete unit to several units for bulk orders. Some suppliers may be flexible with MOQs for first-time buyers or smaller projects. It’s advisable to discuss your specific needs upfront to negotiate favorable terms that suit your purchasing strategy. -
How can I ensure the quality of prefabricated homes sourced from China?
Ensuring quality begins with choosing a reputable supplier who adheres to international standards. Request certifications such as ISO and CE, and consider third-party inspections during production and before shipment. Establish clear quality control protocols and specifications in your contract. Regular communication with the supplier throughout the manufacturing process can also help address any concerns promptly. -
What customization options are available for prefabricated homes from China?
Many Chinese manufacturers offer extensive customization options, including floor plans, materials, and finishes. Discuss your specific requirements during initial negotiations to understand what is feasible. Some suppliers may have design teams to assist with architectural plans, while others may work with your own designs. Ensure that customization capabilities align with your project timelines and budget. -
What are the logistics considerations when importing prefabricated homes from China?
Logistics involve multiple factors, including shipping methods, customs clearance, and delivery timelines. Determine whether you prefer sea freight or air freight based on cost and urgency. Collaborate with a freight forwarder experienced in handling prefabricated structures to navigate shipping regulations and ensure compliance with local import laws. It’s also wise to plan for potential delays and have contingency plans in place. -
What are the key factors to consider regarding after-sales support for prefabricated homes?
After-sales support is crucial for maintaining a good relationship with your supplier. Inquire about warranty terms, maintenance services, and availability of spare parts. Understand the supplier’s policies on addressing defects or damages post-delivery. A reputable supplier should provide comprehensive support, including guidance on installation and any necessary adjustments after the homes are assembled. -
How do I handle disputes with suppliers of prefabricated homes from China?
Handling disputes effectively requires clear communication and documentation. Start by addressing issues directly with the supplier, referencing contracts and agreements. If necessary, involve third-party mediators or legal counsel familiar with international trade laws. Establishing clear terms regarding dispute resolution in your initial agreements can also help mitigate potential conflicts and provide a framework for resolution.
Important Disclaimer & Terms of Use
⚠️ Important Disclaimer
The information provided in this guide, including content regarding manufacturers, technical specifications, and market analysis, is for informational and educational purposes only. It does not constitute professional procurement advice, financial advice, or legal advice.
While we have made every effort to ensure the accuracy and timeliness of the information, we are not responsible for any errors, omissions, or outdated information. Market conditions, company details, and technical standards are subject to change.
B2B buyers must conduct their own independent and thorough due diligence before making any purchasing decisions. This includes contacting suppliers directly, verifying certifications, requesting samples, and seeking professional consultation. The risk of relying on any information in this guide is borne solely by the reader.
Strategic Sourcing Conclusion and Outlook for pre fabricated homes china
In conclusion, the landscape of prefabricated homes in China presents a wealth of opportunities for international B2B buyers, particularly those from Africa, South America, the Middle East, and Europe. As buyers seek to leverage cost-effective and innovative housing solutions, strategic sourcing emerges as a critical factor. Understanding local regulations, quality standards, and logistical considerations can greatly enhance procurement strategies, ensuring that buyers not only secure competitive pricing but also maintain high standards of quality and sustainability.
The value of forming strategic partnerships with reliable Chinese manufacturers cannot be overstated. Engaging with suppliers who are well-versed in international trade can facilitate smoother transactions and mitigate risks associated with sourcing abroad. Additionally, as global demand for sustainable and affordable housing continues to rise, aligning procurement strategies with manufacturers committed to eco-friendly practices will position buyers favorably in their respective markets.
Looking forward, now is the ideal time for international B2B buyers to explore the vast potential within the prefabricated housing sector in China. By embracing strategic sourcing and fostering collaborative relationships, buyers can not only enhance their supply chains but also contribute to the broader goal of addressing housing shortages worldwide. Take the next step in your sourcing journey today and unlock the benefits of prefabricated homes from China.