Cut Costs with the Best Compression Spring Supplier (2025)
Introduction: Navigating the Global Market for compression spring supplier
In the dynamic landscape of global commerce, sourcing reliable compression spring suppliers poses a significant challenge for international B2B buyers. Whether you are in Africa, South America, the Middle East, or Europe, finding the right supplier can impact your production efficiency and product quality. This guide aims to empower B2B buyers by providing a comprehensive overview of compression springs, covering various types, applications, and the critical factors to consider when vetting suppliers.
Understanding the nuances of compression springs is essential, as they play a pivotal role in numerous industries, from automotive to aerospace. Buyers will gain insights into the different types of compression springs, including their materials and design specifications, enabling informed decisions tailored to specific project requirements. Furthermore, the guide delves into supplier evaluation criteria, highlighting how to assess quality, reliability, and compliance with international standards.
Cost considerations are also addressed, offering strategies to negotiate favorable pricing without compromising on quality. By the end of this guide, B2B buyers will be equipped with actionable insights to navigate the complexities of sourcing compression springs, ensuring they make informed purchasing decisions that drive business success in their respective markets.
Understanding compression spring supplier Types and Variations
Type Name | Key Distinguishing Features | Primary B2B Applications | Brief Pros & Cons for Buyers |
---|---|---|---|
Music Wire Compression Springs | Made from high-carbon steel, excellent tensile strength, and flexibility. | Automotive, aerospace, and electronics. | Pros: High strength-to-weight ratio; Cons: Prone to corrosion if not coated. |
Oil-tempered Compression Springs | Heat-treated for increased durability, resistance to fatigue. | Industrial machinery, heavy equipment. | Pros: Long lifespan; Cons: Higher cost compared to standard options. |
Stainless Steel Compression Springs | Corrosion-resistant, suitable for harsh environments. | Food processing, medical equipment. | Pros: Excellent durability; Cons: More expensive than carbon steel springs. |
Plastic Compression Springs | Lightweight, non-corrosive, and electrically insulating. | Consumer goods, electronic devices. | Pros: Lightweight and cost-effective; Cons: Limited load-bearing capacity. |
Variable Pitch Compression Springs | Varying coil spacing, designed for specific load requirements. | Custom applications in machinery and automotive. | Pros: Tailored performance; Cons: More complex manufacturing process. |
What Are the Key Characteristics of Music Wire Compression Springs?
Music wire compression springs are crafted from high-carbon steel, which provides exceptional tensile strength and flexibility. This makes them ideal for applications in industries such as automotive, aerospace, and electronics, where reliability and performance are critical. When purchasing music wire springs, B2B buyers should consider the spring’s corrosion resistance, as uncoated wire can be susceptible to rust in certain environments.
How Do Oil-tempered Compression Springs Enhance Durability?
Oil-tempered compression springs undergo a heat treatment process that significantly enhances their durability and resistance to fatigue. These springs are commonly used in industrial machinery and heavy equipment, where they experience repeated stress. Buyers should evaluate the cost versus the long lifespan and reliability that oil-tempered springs provide, making them a worthwhile investment for demanding applications.
Why Choose Stainless Steel Compression Springs for Harsh Environments?
Stainless steel compression springs are known for their corrosion resistance, making them suitable for use in harsh environments such as food processing and medical equipment. Their durability ensures consistent performance over time. However, buyers should be prepared for a higher price point compared to carbon steel options, which can be justified by the longevity and reliability they offer in challenging conditions.
What Advantages Do Plastic Compression Springs Offer?
Plastic compression springs are lightweight, non-corrosive, and provide electrical insulation, making them a popular choice for consumer goods and electronic devices. They are cost-effective and can be produced in various shapes and sizes. However, B2B buyers should note that plastic springs have a limited load-bearing capacity, which may restrict their use in heavy-duty applications.
How Do Variable Pitch Compression Springs Meet Custom Needs?
Variable pitch compression springs feature coils with varying spacing, allowing them to be designed for specific load requirements. This customization makes them ideal for specialized applications in machinery and automotive sectors. Buyers should consider the complexity and potential cost of manufacturing these springs, as they often require more intricate design processes compared to standard springs, but offer tailored performance that can enhance operational efficiency.
Related Video: Simple Method Adjusting & Weakening A Compression Spring
Key Industrial Applications of compression spring supplier
Industry/Sector | Specific Application of Compression Spring Supplier | Value/Benefit for the Business | Key Sourcing Considerations for this Application |
---|---|---|---|
Automotive | Suspension systems in vehicles | Enhances ride comfort and vehicle stability | Durability under varying loads, compliance with safety standards |
Electronics | Keyboards and switches | Improved tactile response and longevity | Precision manufacturing, material quality, and cost-effectiveness |
Manufacturing | Industrial machinery and equipment | Increases efficiency and reduces downtime | Customization options, lead times, and bulk pricing |
Aerospace | Landing gear and control systems | Ensures safety and reliability in critical operations | Weight considerations, certification requirements, and performance metrics |
Medical Devices | Patient monitoring equipment | Enhances accuracy and reliability of devices | Compliance with medical regulations, biocompatibility, and sourcing from certified suppliers |
How Are Compression Springs Used in the Automotive Industry?
In the automotive sector, compression springs are integral to suspension systems. They absorb shocks from uneven surfaces, enhancing ride comfort and vehicle stability. International B2B buyers, particularly from Africa and South America, should prioritize suppliers that provide springs with high durability and compliance with safety standards to withstand the rigors of varied terrains. Additionally, understanding local regulations on automotive components is crucial for seamless integration into manufacturing processes.
What Role Do Compression Springs Play in Electronics?
In electronics, compression springs are commonly used in keyboards and switches. They provide a tactile response, improving user experience and ensuring longevity through repeated use. Buyers from Europe and the Middle East should focus on sourcing springs that are precision-engineered to maintain consistent performance under varying pressures. Consideration of material quality and cost-effectiveness is essential to maintain competitive pricing in the electronics market.
How Do Compression Springs Benefit Manufacturing?
Manufacturing industries utilize compression springs in various machinery and equipment to enhance operational efficiency. These springs can reduce downtime by providing reliable performance under heavy loads. Buyers should seek suppliers that offer customization options, allowing for tailored solutions that meet specific machinery requirements. Additionally, understanding lead times and bulk pricing can significantly impact production schedules and overall costs.
Why Are Compression Springs Critical in Aerospace Applications?
In the aerospace sector, compression springs are vital for landing gear and control systems. They ensure safety and reliability during critical operations, which is non-negotiable in aviation. B2B buyers must consider weight constraints and certification requirements when sourcing these components. It is essential to partner with suppliers who can demonstrate compliance with stringent aerospace standards and provide performance metrics to ensure reliability.
How Do Compression Springs Enhance Medical Devices?
Compression springs are essential in patient monitoring equipment, enhancing the accuracy and reliability of medical devices. They help maintain consistent pressure and functionality, which is crucial for patient safety. Buyers in the medical sector, particularly from regions like Africa and South America, should prioritize sourcing from suppliers who comply with medical regulations and offer biocompatible materials. This ensures that the devices not only function effectively but also meet health and safety standards.
Related Video: 9 kinds Power spring & Constant force spring Applications | Meta Spring Industry
3 Common User Pain Points for ‘compression spring supplier’ & Their Solutions
Scenario 1: Inconsistent Quality of Compression Springs
The Problem:
B2B buyers often encounter significant challenges when sourcing compression springs, particularly when it comes to maintaining consistent quality. Many suppliers may offer products that vary in material strength, coil diameter, or spring rate, leading to unpredictable performance in applications. This inconsistency can result in operational inefficiencies, increased costs due to product failures, and potential safety hazards. For buyers in industries such as automotive or aerospace, where precise specifications are crucial, the inability to trust the quality of supplied springs can be particularly detrimental.
The Solution:
To mitigate quality concerns, B2B buyers should prioritize suppliers that adhere to strict quality control processes and standards, such as ISO 9001 certification. It’s essential to conduct thorough due diligence by requesting detailed product specifications, material certifications, and test reports prior to purchase. Engaging with suppliers that offer samples or prototype springs can also help assess quality before committing to larger orders. Establishing a clear communication channel with the supplier regarding quality expectations and performance requirements is vital. Regular audits and feedback loops can further ensure that the products delivered consistently meet the agreed-upon standards.
Scenario 2: Difficulties in Customization and Sizing of Compression Springs
The Problem:
Another common pain point for B2B buyers is the challenge of customizing compression springs to fit unique applications. Off-the-shelf solutions often do not meet specific project requirements, leading to delays and additional costs when modifications are needed. Buyers may find themselves frustrated when suppliers lack the flexibility or technical expertise to create tailored solutions, especially in specialized industries like robotics or industrial machinery.
The Solution:
To address customization needs effectively, buyers should engage with compression spring suppliers that specialize in bespoke solutions. This involves providing comprehensive details about the application, including load requirements, environmental conditions, and space constraints. A collaborative approach with suppliers who have engineering capabilities can facilitate the design of springs that meet specific parameters. Utilizing 3D modeling or simulation tools offered by some advanced suppliers can help visualize and refine spring designs before production. Establishing long-term partnerships with flexible suppliers can enhance responsiveness to future customization needs.
Scenario 3: Supply Chain Delays and Reliability Issues
The Problem:
Supply chain disruptions pose a significant challenge for B2B buyers in need of timely deliveries of compression springs. Unforeseen delays in manufacturing or logistics can halt production lines, resulting in financial losses and missed deadlines. Buyers in regions such as Africa and South America, where logistics infrastructure may be less developed, often face compounded issues that exacerbate reliability concerns, leading to uncertainty in project timelines.
The Solution:
To combat supply chain delays, buyers should focus on sourcing compression springs from suppliers with robust logistics capabilities and a proven track record of reliability. Conducting a risk assessment of potential suppliers, including their manufacturing locations and logistics networks, can provide insights into their ability to meet delivery timelines. Establishing contingency plans, such as maintaining safety stock or identifying alternative suppliers, can also mitigate the impact of delays. Leveraging technology, such as supply chain management software, can enhance visibility into order statuses and streamline communication with suppliers, ensuring proactive management of potential disruptions.
Strategic Material Selection Guide for compression spring supplier
When selecting materials for compression springs, international B2B buyers must consider various factors that influence performance, durability, and compatibility with specific applications. Below, we analyze four common materials used in compression spring manufacturing, focusing on their properties, advantages, disadvantages, and implications for buyers from diverse regions.
What are the Key Properties of Music Wire for Compression Springs?
Music Wire is a high-carbon steel known for its excellent tensile strength and fatigue resistance. It typically has a temperature rating of up to 250°F (121°C) and offers good corrosion resistance when properly treated.
Pros and Cons: The primary advantage of music wire is its high strength-to-weight ratio, making it suitable for applications requiring resilience under stress. However, it can be more expensive than other materials and may require additional coatings for enhanced corrosion resistance, which adds to manufacturing complexity.
Impact on Application: Music wire is ideal for applications in automotive and aerospace industries, where performance under high stress is critical. Buyers should ensure that the wire meets relevant standards such as ASTM A228.
How Does Stainless Steel Compare for Compression Spring Applications?
Stainless Steel, particularly grades like 302 or 316, is widely used for compression springs due to its excellent corrosion resistance and ability to withstand higher temperatures (up to 800°F or 427°C).
Pros and Cons: The key advantage of stainless steel is its durability and resistance to rust, making it suitable for outdoor or marine applications. However, it is generally more expensive than carbon steel and can be harder to work with due to its toughness.
Impact on Application: Buyers in regions with high humidity or corrosive environments, such as coastal areas in South America or the Middle East, should prioritize stainless steel springs. Compliance with standards like ASTM A313 is essential for ensuring quality.
What are the Benefits of Oil-Tempered Steel for Compression Springs?
Oil-Tempered Steel is a type of carbon steel that undergoes a unique heat treatment process, enhancing its fatigue resistance and strength. This material can operate effectively at temperatures up to 400°F (204°C).
Pros and Cons: One of the main advantages of oil-tempered steel is its cost-effectiveness compared to stainless steel while still offering good performance. However, it may not provide the same level of corrosion resistance, necessitating protective coatings in certain applications.
Impact on Application: This material is commonly used in automotive and industrial applications where cost is a significant factor. Buyers should be aware of regional standards like DIN 17223 when sourcing oil-tempered springs.
How Do Plastic Springs Perform in Compression Applications?
Plastic Springs, often made from materials like polypropylene or nylon, are gaining popularity for specific applications due to their lightweight and corrosion-resistant properties. They can typically handle temperatures up to 200°F (93°C).
Pros and Cons: The main advantage of plastic springs is their resistance to corrosion and chemicals, making them suitable for applications in the food and pharmaceutical industries. However, they generally have lower load-bearing capacities and may not be suitable for high-stress applications.
Impact on Application: Buyers from regions focused on hygiene, such as the food processing sectors in Europe, should consider plastic springs. Compliance with standards like FDA regulations is crucial for these applications.
Summary Table of Material Selection for Compression Springs
Material | Typical Use Case for compression spring supplier | Key Advantage | Key Disadvantage/Limitation | Relative Cost (Low/Med/High) |
---|---|---|---|---|
Music Wire | Automotive and aerospace applications | High strength-to-weight ratio | Higher cost, requires coatings | Medium |
Stainless Steel | Marine and outdoor applications | Excellent corrosion resistance | More expensive, tougher to work with | High |
Oil-Tempered Steel | Automotive and industrial applications | Cost-effective, good performance | Lower corrosion resistance | Low |
Plastic Springs | Food and pharmaceutical industries | Lightweight, corrosion-resistant | Lower load-bearing capacity | Medium |
This strategic material selection guide provides valuable insights for international B2B buyers, ensuring they make informed decisions that align with their specific application needs and regional standards.
In-depth Look: Manufacturing Processes and Quality Assurance for compression spring supplier
What Are the Key Stages in the Manufacturing Process of Compression Springs?
The manufacturing process of compression springs involves several critical stages that ensure the final product meets the required specifications for durability and performance. Understanding these stages can help international B2B buyers assess potential suppliers effectively.
Material Preparation: How is Raw Material Selected and Processed?
The first step in manufacturing compression springs is material selection. Common materials include stainless steel, carbon steel, and alloy steel, chosen based on their mechanical properties, including tensile strength and fatigue resistance.
Once selected, the raw materials undergo preparation, which includes cutting the wire to the specified length and conditioning it to remove any surface imperfections. This stage often employs processes such as annealing, which enhances the material’s ductility and reduces brittleness, making it easier to form into springs.
Forming: What Techniques Are Used to Shape Compression Springs?
The forming process is where the wire is shaped into a spring. This typically involves methods like coiling, where the wire is wound into a helical shape using a coiling machine.
Several techniques can be used during this stage:
– Cold Coiling: This method is popular for producing springs with smaller diameters and requires the wire to be at room temperature.
– Hot Coiling: Suitable for larger diameter springs, hot coiling involves heating the wire to make it more malleable before shaping it.
Additionally, computer numerically controlled (CNC) machines are increasingly being used to improve precision and reduce production times.
Assembly: How Are Compression Springs Prepared for Final Inspection?
In some cases, compression springs may require additional assembly, especially if they are part of a larger assembly. This could involve adding end fittings or integrating them with other components.
Quality checks during assembly ensure that the springs meet design specifications and are free from defects. This stage is crucial for maintaining product integrity, especially in high-stakes applications like automotive or aerospace industries.
Finishing: What Processes Enhance the Durability and Aesthetics of Compression Springs?
The finishing process includes several treatments designed to enhance the performance and appearance of the springs. Common finishing techniques include:
– Surface Treatment: Processes such as shot peening or surface hardening improve fatigue resistance.
– Coating: Applying coatings, such as zinc plating, prevents corrosion and improves the spring’s lifespan.
– Heat Treatment: This process alters the physical properties of the springs to achieve the desired hardness and elasticity.
What Quality Assurance Practices Should International B2B Buyers Expect?
Quality assurance (QA) is paramount in the manufacturing of compression springs. Buyers should be aware of international standards and industry-specific certifications that ensure product reliability.
What International Standards Are Relevant for Compression Spring Quality Assurance?
One of the primary international standards is ISO 9001, which outlines the requirements for a quality management system. Compliance with this standard indicates that a supplier has a robust system in place for maintaining product quality.
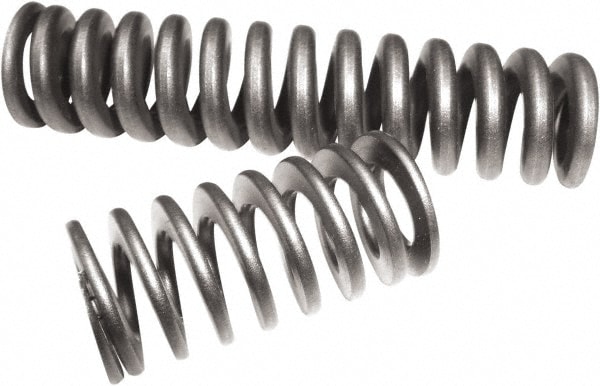
A stock image related to compression spring supplier.
In addition to ISO certifications, industry-specific standards may apply, such as:
– CE Marking: Essential for products sold in the European market, indicating compliance with health and safety standards.
– API Standards: Relevant for suppliers serving the oil and gas industry, ensuring that products meet stringent operational and safety requirements.
What QC Checkpoints Should Be Implemented During Production?
Quality control checkpoints should be integrated throughout the manufacturing process to ensure that any defects are identified and corrected early. Key checkpoints include:
- Incoming Quality Control (IQC): Inspection of raw materials before they enter the manufacturing process.
- In-Process Quality Control (IPQC): Continuous monitoring during the production stages, ensuring that any deviations from specifications are addressed immediately.
- Final Quality Control (FQC): Comprehensive testing of finished products to verify they meet all design and regulatory requirements.
How Can B2B Buyers Verify Supplier Quality Control?
To ensure that a compression spring supplier maintains high-quality standards, buyers can take several steps to verify their quality control measures:
What Are the Best Practices for Conducting Supplier Audits?
Conducting regular supplier audits is one of the most effective ways to assess a manufacturer’s quality control processes. During an audit, buyers should:
– Review the supplier’s quality management systems and documentation.
– Evaluate the manufacturing processes and equipment used.
– Observe the implementation of quality control measures in practice.
How Can Buyers Utilize Reports and Third-Party Inspections?
Requesting detailed quality reports from suppliers can provide insights into their production and quality control processes. Additionally, engaging third-party inspection services can offer an unbiased assessment of the supplier’s compliance with international standards.
What Are the Nuances of Quality Control for International B2B Buyers?
When sourcing from suppliers across Africa, South America, the Middle East, and Europe, buyers should be aware of regional differences in quality standards and practices.
- Cultural Considerations: Understanding the local business culture can facilitate better communication and expectations regarding quality standards.
- Regulatory Compliance: Different regions may have unique regulatory requirements, making it essential to verify that suppliers are compliant with both local and international regulations.
By taking these steps, international B2B buyers can ensure they select reliable compression spring suppliers that adhere to stringent quality assurance processes, ultimately safeguarding their supply chain and product quality.
Practical Sourcing Guide: A Step-by-Step Checklist for ‘compression spring supplier’
To successfully procure compression springs from a supplier, it’s crucial to follow a structured approach. This guide provides a step-by-step checklist designed specifically for international B2B buyers, ensuring that your sourcing process is efficient and effective.
Step 1: Define Your Technical Specifications
Before reaching out to suppliers, clearly outline your technical requirements for the compression springs. This includes dimensions, material types, load capacity, and intended applications.
– Why it’s important: A precise specification helps prevent misunderstandings and ensures that the springs will meet your operational needs.
– What to look for: Consider industry standards and any specific certifications relevant to your region or sector.
Step 2: Research Potential Suppliers
Conduct thorough research to identify potential compression spring suppliers. Look for manufacturers with a solid reputation in your target regions, such as Africa, South America, the Middle East, and Europe.
– Why it’s important: A well-researched supplier list reduces risks associated with quality and reliability.
– What to look for: Supplier reviews, case studies, and their experience in your industry can provide valuable insights.
Step 3: Evaluate Supplier Capabilities
Assess the capabilities of each potential supplier to ensure they can meet your specifications. This includes their manufacturing processes, quality control measures, and production capacity.
– Why it’s important: Understanding a supplier’s capabilities ensures they can deliver the required quantity and quality on time.
– What to look for: Request details about their production technology, lead times, and any customization options.
Step 4: Verify Supplier Certifications
Ensure that the suppliers you consider hold relevant certifications, such as ISO 9001 or other industry-specific qualifications.
– Why it’s important: Certifications indicate a commitment to quality and adherence to international standards, providing assurance of the supplier’s reliability.
– What to look for: Check for recent audits or inspections that validate their compliance with these standards.
Step 5: Request Samples for Testing
Once you have narrowed down your list, request samples of the compression springs you intend to purchase. Testing these samples in your application is crucial.
– Why it’s important: Testing allows you to verify that the springs meet your performance requirements before making a bulk purchase.
– What to look for: Evaluate the springs for durability, load-bearing capacity, and any specific functional tests relevant to your application.
Step 6: Negotiate Terms and Pricing
Engage in discussions with your shortlisted suppliers regarding pricing, payment terms, and delivery schedules.
– Why it’s important: Clear negotiations help to establish a mutually beneficial agreement and avoid potential disputes later on.
– What to look for: Ensure that the pricing reflects the quality and service provided, and consider discussing volume discounts for larger orders.
Step 7: Establish Communication Protocols
Set up effective communication channels with your chosen supplier to facilitate smooth interactions throughout the procurement process.
– Why it’s important: Strong communication can prevent misunderstandings and ensure timely updates on order status.
– What to look for: Agree on preferred communication methods, response times, and points of contact for both parties.
By following this checklist, you can navigate the complexities of sourcing compression springs more effectively, ensuring that you partner with a reliable supplier who meets your specific needs.
Comprehensive Cost and Pricing Analysis for compression spring supplier Sourcing
What Are the Key Cost Components in Sourcing Compression Springs?
When sourcing compression springs, understanding the cost structure is crucial for international B2B buyers. The primary cost components include:
-
Materials: The choice of materials significantly impacts the overall cost. Common materials for compression springs include stainless steel, carbon steel, and specialty alloys. Prices can vary based on market conditions and the specific properties required.
-
Labor: Labor costs are often influenced by the location of the manufacturing facility. In regions with higher labor costs, such as parts of Europe, the overall price of compression springs may be elevated compared to manufacturers in regions with lower labor expenses, such as parts of Africa or South America.
-
Manufacturing Overhead: This encompasses the indirect costs associated with production, such as utilities, rent, and administrative expenses. Efficient production processes can help lower these overheads, contributing to more competitive pricing.
-
Tooling: Initial tooling costs can be significant, especially for custom designs. Buyers should consider whether the supplier has existing tooling for their specific needs or if new tooling will be required, which could increase upfront costs.
-
Quality Control (QC): Ensuring that compression springs meet specified standards involves quality control processes. The investment in QC can vary based on the supplier’s protocols and the certifications required by the buyer.
-
Logistics: Transportation and handling costs can fluctuate based on the distance from the supplier to the buyer, as well as the chosen Incoterms. Understanding these costs is essential for accurate budgeting.
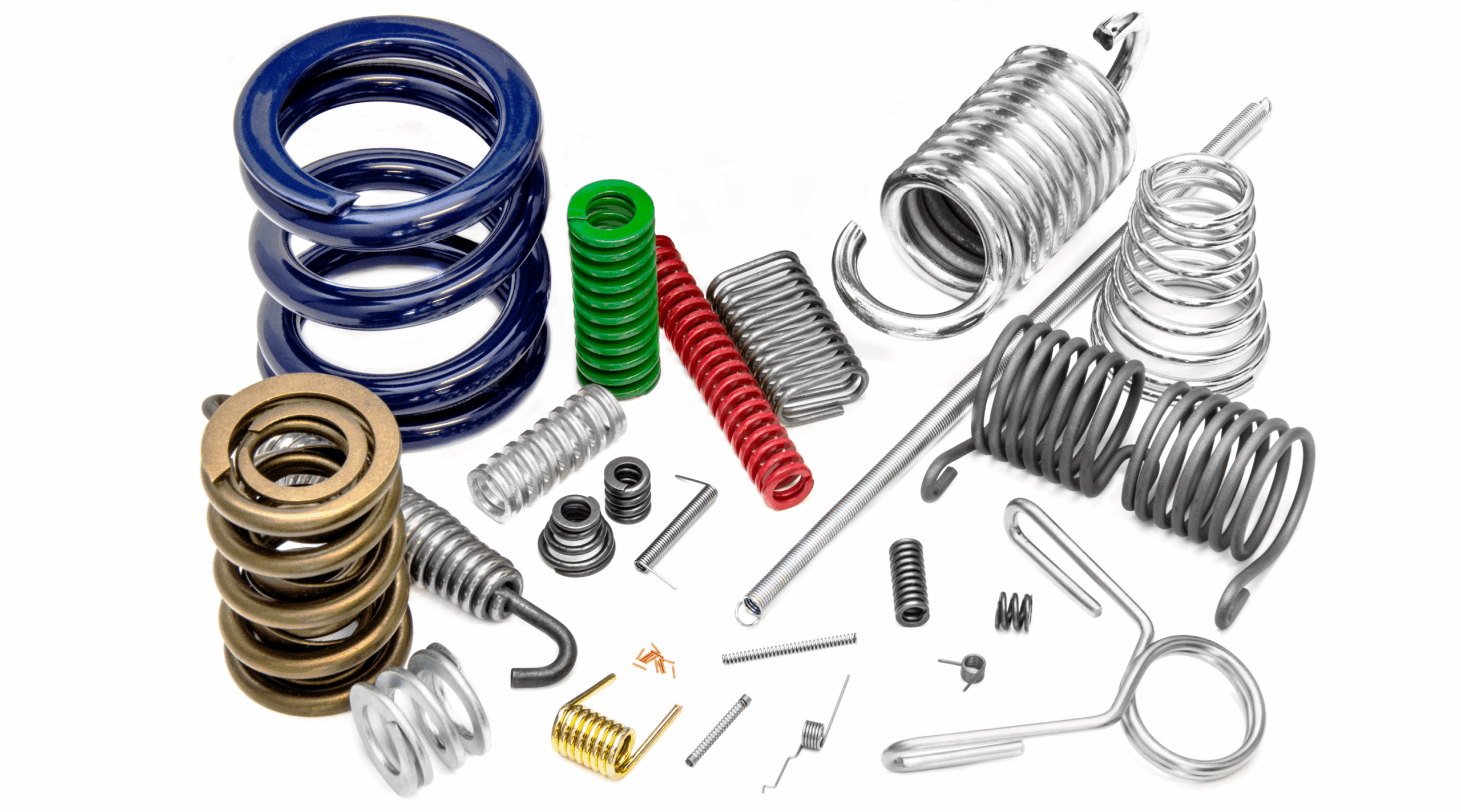
A stock image related to compression spring supplier.
- Margin: Suppliers will include a profit margin in their pricing, which can vary significantly based on market competition, brand reputation, and the perceived value of the product.
How Do Price Influencers Impact Compression Spring Costs?
Several factors can influence the pricing of compression springs, including:
-
Volume and Minimum Order Quantity (MOQ): Larger orders often lead to lower per-unit costs due to economies of scale. Buyers should negotiate MOQs to align with their production needs while maximizing cost efficiency.
-
Specifications and Customization: Custom springs tailored to specific applications may incur additional costs. Buyers should clearly communicate their requirements to obtain accurate pricing.
-
Materials: The choice of material not only affects cost but also the performance characteristics of the spring. High-performance materials can increase costs but may be necessary for specific applications.
-
Quality and Certifications: Suppliers offering higher quality and certified products may charge more. Buyers in industries with stringent regulatory requirements must weigh the importance of certification against potential savings.
-
Supplier Factors: A supplier’s reputation, reliability, and production capabilities can influence pricing. Established suppliers with proven track records may command higher prices but could offer better service and product consistency.
-
Incoterms: The choice of Incoterms impacts logistics costs and responsibilities. Buyers should be aware of their obligations under different terms to avoid unexpected expenses.
What Are the Essential Buyer Tips for Cost-Efficiency in Compression Spring Sourcing?
For international B2B buyers, especially from regions such as Africa, South America, the Middle East, and Europe, here are actionable tips to enhance cost-efficiency:
-
Negotiate Wisely: Engage in open discussions with suppliers about pricing, especially for larger orders. Leverage your purchasing power to secure better terms.
-
Consider Total Cost of Ownership (TCO): Analyze not just the purchase price but also the long-term costs associated with the product, including maintenance, failure rates, and logistics.
-
Understand Pricing Nuances: Be aware that prices can vary widely based on the supplier’s location and market conditions. International buyers should keep abreast of currency fluctuations and regional economic factors.
-
Conduct Supplier Audits: Before finalizing agreements, conduct audits or site visits to ensure that suppliers meet quality standards and can deliver on their promises.
-
Build Long-term Relationships: Establishing long-term relationships with reliable suppliers can lead to better pricing, improved service, and priority access to new products.
Disclaimer on Indicative Prices
Prices for compression springs can vary widely based on the factors discussed. It is advisable for buyers to request detailed quotations that reflect their specific needs and to remain flexible in negotiations to achieve the best possible outcomes.
Alternatives Analysis: Comparing compression spring supplier With Other Solutions
Exploring Alternatives to Compression Spring Suppliers
In the realm of industrial applications, compression springs are crucial components utilized in various mechanical systems. However, international B2B buyers might find themselves exploring alternative solutions that can provide similar functionalities. This section presents a detailed comparison of compression spring suppliers against two viable alternatives: gas springs and pneumatic actuators. Each alternative comes with its own set of advantages and drawbacks, which can significantly influence a buyer’s decision-making process.
Comparison Aspect | Compression Spring Supplier | Gas Springs | Pneumatic Actuators |
---|---|---|---|
Performance | High load capacity; reliable in static and dynamic applications | Moderate load capacity; offers smooth operation | High speed and versatility; suitable for various applications |
Cost | Variable, often dependent on material and manufacturing process | Generally lower initial cost, but replacement can be frequent | Higher initial investment; operational costs can accumulate |
Ease of Implementation | Requires careful installation and adjustment | Simple installation; minimal adjustments needed | Requires more complex setup and maintenance |
Maintenance | Low maintenance if properly selected and installed | Moderate; can require frequent replacement | Higher maintenance demands due to air supply management |
Best Use Case | Suitable for applications with consistent load requirements | Ideal for applications needing controlled motion with space constraints | Best for applications requiring rapid movement and flexibility |
What Are the Advantages and Disadvantages of Gas Springs?
Gas springs, also known as gas-filled struts, provide a reliable alternative to compression springs, particularly in applications where controlled movement is essential. They offer a smoother operation and can easily adjust to varying loads. However, their load capacity is generally moderate compared to traditional compression springs. They also tend to have a lower initial cost, but frequent replacements can lead to higher long-term expenses. Gas springs are best utilized in applications such as automotive lifts or adjustable office furniture, where space constraints and controlled motion are crucial.
How Do Pneumatic Actuators Compare to Compression Springs?
Pneumatic actuators are another alternative that utilizes compressed air to generate motion. They are known for their speed and versatility, making them suitable for applications requiring rapid movement. While they provide high performance, pneumatic actuators often come with a higher initial investment and greater operational costs due to the need for an air supply system. Their complexity in setup and maintenance can also be a drawback, especially for companies with limited technical resources. Pneumatic actuators excel in environments such as assembly lines or packaging machinery, where flexibility and speed are paramount.
How Can B2B Buyers Choose the Right Solution?
Choosing the right solution between compression springs, gas springs, and pneumatic actuators depends on several factors, including application requirements, cost considerations, and maintenance capabilities. B2B buyers should evaluate their specific needs, such as load capacity, space limitations, and operational speed. Conducting a thorough analysis of each alternative’s pros and cons can lead to informed decisions that enhance operational efficiency. Engaging with suppliers for tailored advice based on industry-specific needs can also provide valuable insights, ensuring that the chosen solution aligns with both immediate and long-term business goals.
Essential Technical Properties and Trade Terminology for compression spring supplier
What Are the Key Technical Properties of Compression Springs?
When sourcing compression springs, understanding the critical technical properties is essential for ensuring the components meet specific application requirements. Here are some vital specifications to consider:
1. Material Grade
Definition: The material grade of a compression spring refers to the type of metal used in its construction, such as stainless steel, carbon steel, or alloy steel.
Importance: Different materials offer varying levels of strength, corrosion resistance, and fatigue properties. Selecting the appropriate material grade is crucial for the spring’s performance, durability, and longevity in specific environments, particularly in industries like automotive and aerospace.
2. Wire Diameter
Definition: This specification indicates the thickness of the wire used to create the spring, typically measured in millimeters or inches.
Importance: The wire diameter directly influences the spring’s load-bearing capacity and flexibility. A thicker wire can handle greater loads but may also be less flexible, making it vital to balance these properties based on application requirements.
3. Spring Free Length
Definition: The free length of a spring is the length of the spring when it is not under any load.
Importance: This measurement is critical for ensuring that the spring fits correctly within the intended assembly and performs optimally when compressed. Buyers should specify the desired free length to avoid compatibility issues in applications.
4. Spring Rate
Definition: The spring rate (or stiffness) measures the amount of force required to compress the spring by a specific distance, typically expressed in pounds per inch (lbs/in) or newtons per millimeter (N/mm).
Importance: Understanding the spring rate is essential for determining how much load a spring can handle while still functioning effectively. This property is particularly important in applications requiring precise control over mechanical movement.
5. Tolerance
Definition: Tolerance refers to the allowable variation in the dimensions of the spring, including wire diameter, free length, and overall shape.
Importance: Tight tolerances are crucial in high-precision applications where even minor deviations can lead to malfunction. Understanding tolerance levels helps buyers ensure that their springs will fit and function correctly within their systems.
What Common Trade Terms Should B2B Buyers Know When Purchasing Compression Springs?
Familiarity with industry jargon can help streamline negotiations and procurement processes. Here are some essential terms to understand:
1. OEM (Original Equipment Manufacturer)
Definition: An OEM is a company that manufactures products that are sold under another company’s brand name.
Importance: For B2B buyers, partnering with an OEM can ensure that the compression springs are designed and manufactured to meet specific quality and performance standards required by the brand.
2. MOQ (Minimum Order Quantity)
Definition: MOQ refers to the smallest number of units that a supplier is willing to sell in a single order.
Importance: Understanding MOQ is vital for budget planning and inventory management. Buyers should negotiate MOQs to align with their production needs and financial capabilities.
3. RFQ (Request for Quotation)
Definition: An RFQ is a formal document sent to suppliers requesting a price quote for specific products or services.
Importance: Submitting an RFQ allows buyers to compare prices and terms from different suppliers, facilitating informed purchasing decisions and cost negotiations.
4. Incoterms (International Commercial Terms)
Definition: Incoterms are a series of predefined commercial terms published by the International Chamber of Commerce (ICC) that define the responsibilities of buyers and sellers in international transactions.
Importance: Familiarity with Incoterms helps buyers understand shipping responsibilities, risk management, and cost allocation during international procurement, which is crucial for ensuring smooth logistics and compliance.
5. Lead Time
Definition: Lead time is the amount of time it takes from placing an order until it is received.
Importance: Understanding lead time is essential for inventory management and production planning. Buyers must consider lead time in their procurement strategies to avoid delays in production schedules.
By understanding these key technical properties and trade terminologies, B2B buyers from regions like Africa, South America, the Middle East, and Europe can make informed decisions when sourcing compression springs, ensuring that their specific application needs are met efficiently.
Navigating Market Dynamics and Sourcing Trends in the compression spring supplier Sector
What Are the Current Market Dynamics and Key Trends in the Compression Spring Supplier Sector?
The compression spring supplier sector is experiencing notable shifts driven by global market dynamics and technological advancements. One significant driver is the rising demand for lightweight and durable materials across industries such as automotive, aerospace, and consumer electronics. As these sectors evolve, B2B buyers are increasingly focused on sourcing springs that not only meet performance specifications but also provide cost efficiency.
Emerging technologies such as additive manufacturing (3D printing) and automation in production processes are reshaping sourcing strategies. These technologies allow suppliers to customize compression springs with precise specifications, reducing lead times and inventory costs. Additionally, the integration of data analytics into supply chain management enhances decision-making, allowing buyers to forecast demand more accurately and optimize their procurement processes.
Moreover, international B2B buyers from regions like Africa, South America, the Middle East, and Europe must navigate varying regulatory environments and standards. Understanding local market needs and compliance requirements is crucial for successful sourcing. For instance, European buyers often prioritize quality certifications, while buyers in emerging markets may seek competitive pricing alongside acceptable quality levels.
How Is Sustainability Impacting Sourcing Decisions in the Compression Spring Sector?
Sustainability has become a cornerstone of sourcing strategies in the compression spring supplier sector. As environmental concerns gain prominence, B2B buyers are prioritizing suppliers who demonstrate a commitment to ethical sourcing and sustainable practices. This involves evaluating the environmental impact of materials used in manufacturing compression springs, including the carbon footprint associated with production processes.
The importance of ethical supply chains cannot be overstated. Buyers are increasingly scrutinizing suppliers for compliance with international labor standards and environmental regulations. This shift is not just a moral obligation; it also presents a competitive advantage, as businesses that adopt sustainable practices often enjoy enhanced brand loyalty and customer trust.
Furthermore, ‘green’ certifications and the use of sustainable materials are becoming essential criteria for selecting suppliers. Certifications such as ISO 14001 (Environmental Management) and the use of recycled materials in production can significantly influence purchasing decisions. Buyers should seek out suppliers that can provide transparent documentation regarding their sustainability practices and material sourcing to ensure compliance with their own corporate social responsibility goals.
How Has the Compression Spring Supplier Sector Evolved Over Time?
The evolution of the compression spring supplier sector is marked by significant technological advancements and changes in consumer demand. Initially dominated by traditional manufacturing methods, the industry has gradually embraced automation and advanced materials. In the early days, compression springs were primarily produced using metal wire, with limited options for customization.
As industries diversified and the demand for precision increased, manufacturers began to explore new materials and technologies. The introduction of computer-aided design (CAD) systems allowed for more complex spring designs, catering to specific applications. More recently, the rise of 3D printing has revolutionized the sector, enabling rapid prototyping and customization at lower costs.
This historical progression underscores the importance of adaptability for suppliers. B2B buyers today must consider not just the product quality but also the supplier’s ability to innovate and respond to changing market demands. Understanding this evolution provides valuable context for making informed sourcing decisions in an increasingly competitive landscape.
Frequently Asked Questions (FAQs) for B2B Buyers of compression spring supplier
-
How do I choose the right compression spring supplier for my business?
Selecting the right compression spring supplier involves assessing several key factors. First, evaluate the supplier’s experience and expertise in manufacturing compression springs relevant to your industry. Next, consider their production capabilities, including customization options and quality control processes. It’s also crucial to review their reputation through customer testimonials and certifications. Finally, ensure they have efficient logistics to meet your delivery timelines, especially if you are sourcing from regions like Africa or South America. -
What are the common specifications to look for when sourcing compression springs?
When sourcing compression springs, focus on specifications such as material type (e.g., stainless steel, carbon steel), wire diameter, spring diameter, and the required load capacity. Additionally, understand the spring’s free length and the number of active coils, as these factors affect its performance. If your application requires specific tolerances or finishes, ensure the supplier can meet those needs. Clearly communicating these specifications will help you receive accurate quotes and products that meet your quality standards. -
What is the importance of minimum order quantities (MOQ) when sourcing compression springs?
Minimum order quantities (MOQ) are crucial because they impact your initial investment and inventory management. Suppliers often set MOQs to ensure production efficiency and cost-effectiveness. As an international B2B buyer, it’s essential to negotiate MOQs that align with your demand forecasts. If your needs are lower than the MOQ, consider discussing options for smaller batches or partnering with other businesses to meet the MOQ, thus optimizing your costs while ensuring adequate supply. -
How can I ensure the quality of compression springs from international suppliers?
To ensure quality, start by requesting samples before placing a bulk order. This allows you to assess the spring’s performance and durability. Additionally, inquire about the supplier’s quality assurance processes, such as material inspections and testing methods. Certifications like ISO 9001 can indicate a commitment to quality management. Lastly, consider conducting audits or third-party inspections, especially if you are sourcing from regions with varying quality standards, such as the Middle East or Africa. -
What payment terms should I negotiate with compression spring suppliers?
Negotiating favorable payment terms is vital for managing cash flow and mitigating risks. Common terms include a deposit upfront, with the balance due upon delivery or after quality inspection. Explore options like letter of credit for international transactions, which can protect both parties. Ensure that the terms are clearly documented in the contract to avoid disputes. It’s also wise to discuss currency fluctuations and their potential impact on pricing, especially when sourcing from different continents. -
How do I handle logistics and shipping when sourcing compression springs internationally?
Effective logistics management is essential for timely delivery and cost control. Discuss shipping options with your supplier, including Incoterms (like FOB or CIF) to clarify responsibilities. Research freight forwarders experienced in handling industrial goods, and consider the shipping timeframes, customs regulations, and duties involved in importing compression springs to your region. Ensure you have a contingency plan for potential delays, especially if sourcing from regions like South America or Europe, where logistics can vary significantly. -
What customization options should I consider when sourcing compression springs?
Customization can significantly enhance the functionality of compression springs for specific applications. Discuss options like varying wire diameters, coil configurations, and surface treatments (e.g., coating or plating) with your supplier. Additionally, consider if you require unique load capacities or dimensions tailored to your project. Ensure the supplier has the capability and experience to produce custom springs efficiently, and request prototypes to validate the design before bulk production. -
How can I establish a long-term relationship with my compression spring supplier?
Building a long-term relationship with your supplier involves open communication, mutual trust, and consistent feedback. Engage in regular discussions about your requirements and market changes to align your goals. Consider establishing performance metrics to evaluate their service and product quality. Additionally, timely payments and honoring commitments can foster goodwill. Participating in joint ventures or collaborative projects can also strengthen this relationship, especially in diverse markets across Africa, Europe, and South America.
Important Disclaimer & Terms of Use
⚠️ Important Disclaimer
The information provided in this guide, including content regarding manufacturers, technical specifications, and market analysis, is for informational and educational purposes only. It does not constitute professional procurement advice, financial advice, or legal advice.
While we have made every effort to ensure the accuracy and timeliness of the information, we are not responsible for any errors, omissions, or outdated information. Market conditions, company details, and technical standards are subject to change.
B2B buyers must conduct their own independent and thorough due diligence before making any purchasing decisions. This includes contacting suppliers directly, verifying certifications, requesting samples, and seeking professional consultation. The risk of relying on any information in this guide is borne solely by the reader.
Strategic Sourcing Conclusion and Outlook for compression spring supplier
In navigating the complex landscape of sourcing compression springs, international B2B buyers from Africa, South America, the Middle East, and Europe must prioritize strategic sourcing as a critical component of their procurement strategy. Understanding the unique specifications and applications of compression springs, alongside market dynamics, can significantly enhance purchasing decisions. Establishing strong supplier relationships is essential, as it not only ensures quality and consistency but also fosters innovation and responsiveness to market demands.
How Can Strategic Sourcing Enhance Your Competitive Edge?
By leveraging strategic sourcing, businesses can optimize their supply chain efficiency, reduce costs, and improve product quality. This approach allows buyers to evaluate suppliers based on their capabilities, reliability, and alignment with your business goals. Furthermore, engaging with suppliers from diverse regions can lead to access to new technologies and manufacturing processes, ultimately driving competitive advantage.
What’s Next for International B2B Buyers?
As the global market continues to evolve, staying informed about emerging trends and shifts in supplier capabilities will be crucial. Buyers should actively seek opportunities to collaborate with reputable compression spring suppliers who demonstrate a commitment to sustainability and innovation. By doing so, you position your business to not only meet current needs but also to anticipate future demands. Embrace the journey of strategic sourcing, and watch as it transforms your procurement processes and elevates your business performance.