Cut Costs with the Best Power Cords Supplier Guide (2025)
Introduction: Navigating the Global Market for power cords supplier
In today’s rapidly evolving global market, sourcing reliable power cords suppliers can pose significant challenges for international B2B buyers. With diverse applications ranging from consumer electronics to industrial machinery, the need for high-quality, compliant, and cost-effective power cords is paramount. This guide serves as an essential resource, providing a comprehensive overview of the types of power cords available, their various applications, and critical factors to consider when vetting suppliers.
For buyers in regions such as Africa, South America, the Middle East, and Europe—including key markets like the UK and Kenya—understanding the nuances of power cord specifications and compliance standards is vital. This guide not only outlines the essential criteria for selecting suppliers but also delves into cost analysis, market trends, and logistical considerations.
Empowering B2B buyers with actionable insights, this guide aims to facilitate informed purchasing decisions, ensuring that organizations can effectively navigate the complexities of sourcing power cords. Whether you are looking to establish long-term partnerships or seeking to optimize your supply chain, the information presented here will equip you with the knowledge needed to make strategic choices in your procurement process.
Understanding power cords supplier Types and Variations
Type Name | Key Distinguishing Features | Primary B2B Applications | Brief Pros & Cons for Buyers |
---|---|---|---|
Standard Power Cords | Common voltage ratings (110V, 220V), universal connectors | Consumer electronics, office equipment | Pros: Widely available, affordable. Cons: May lack specific certifications for industrial use. |
Heavy-Duty Power Cords | Enhanced insulation, higher current ratings | Industrial machinery, construction sites | Pros: Durable, withstands harsh environments. Cons: Higher cost, may require specialized connectors. |
Custom Power Cords | Tailored specifications for specific applications | Specialized equipment, medical devices | Pros: Optimized for unique needs, improves performance. Cons: Longer lead times, higher initial costs. |
Extension Cords | Length variations, multiple outlets | Temporary setups, outdoor events | Pros: Flexible, easy to use. Cons: Potential safety hazards if overused, less durable. |
Smart Power Cords | Integrated smart technology for energy management | Smart buildings, energy-efficient setups | Pros: Energy savings, remote monitoring. Cons: Higher complexity, requires compatible systems. |
What Are the Key Characteristics of Standard Power Cords?
Standard power cords are essential for everyday applications and are characterized by their universal connectors and common voltage ratings, typically 110V or 220V. They are widely used in consumer electronics and office equipment. For B2B buyers, these cords offer an affordable and readily available solution, though they may not meet specific industrial standards or certifications. Buyers should consider the compatibility of standard cords with their equipment and the potential need for additional safety certifications in certain environments.
How Do Heavy-Duty Power Cords Differ from Standard Options?
Heavy-duty power cords are designed for demanding applications, featuring enhanced insulation and higher current ratings. They are ideal for use in industrial settings, construction sites, and environments where durability is paramount. While they provide superior performance and can withstand harsh conditions, the trade-off is a higher cost. B2B buyers should assess their operational needs and weigh the benefits of longevity and reliability against the upfront investment.
Why Consider Custom Power Cords for Specialized Needs?
Custom power cords are tailored to meet specific requirements for unique applications, such as specialized equipment or medical devices. Their main advantage is the optimization for performance, ensuring safety and efficiency in operation. However, these cords often come with longer lead times and higher initial costs. B2B buyers should evaluate their specific needs and budget constraints, as the investment in custom solutions can lead to improved operational efficacy.
What Are the Advantages of Using Extension Cords in B2B Settings?
Extension cords are versatile and available in various lengths, often featuring multiple outlets for convenience. They are particularly useful for temporary setups or outdoor events where power access is limited. While they offer flexibility and ease of use, buyers must be cautious about potential safety hazards, such as overloading. B2B buyers should consider the intended use and ensure that extension cords are rated appropriately for the equipment they will power.
How Do Smart Power Cords Enhance Energy Management?
Smart power cords incorporate technology that allows for energy monitoring and management, making them ideal for smart buildings and energy-efficient setups. These cords can provide significant energy savings and facilitate remote monitoring of power usage. However, they can be more complex and may require compatible systems for full functionality. B2B buyers should assess the technological readiness of their infrastructure and the long-term benefits of integrating smart power solutions into their operations.
Related Video: All Power Supply Cable Types EXPLAINED
Key Industrial Applications of power cords supplier
Industry/Sector | Specific Application of Power Cords Supplier | Value/Benefit for the Business | Key Sourcing Considerations for this Application |
---|---|---|---|
Manufacturing | Powering machinery and equipment | Ensures operational efficiency and minimizes downtime | Compliance with local electrical standards and safety certifications |
Healthcare | Medical device connectivity | Critical for patient safety and compliance with regulations | Reliability and durability to withstand medical environments |
Information Technology | Data center power management | Supports uninterrupted service and data integrity | Scalability options and compatibility with existing infrastructure |
Construction | Temporary power supply for tools and equipment | Enhances productivity on job sites | Weather resistance and robustness for outdoor use |
Telecommunications | Powering communication equipment | Ensures reliable connectivity and service availability | Compatibility with various voltage standards and ease of installation |
How Are Power Cords Used in Manufacturing?
In the manufacturing sector, power cords are essential for powering machinery and equipment. They connect various machines to the electrical supply, ensuring that operations run smoothly. By sourcing high-quality power cords, manufacturers can reduce the risk of equipment failure, thereby minimizing downtime and enhancing productivity. International B2B buyers must ensure that the cords meet local electrical standards and safety certifications to comply with regulations in their respective regions.
What Role Do Power Cords Play in Healthcare?
In healthcare, power cords are critical for connecting medical devices to power sources. They ensure the reliable operation of life-saving equipment, which is vital for patient safety. Buyers in this sector should prioritize sourcing cords that are durable and reliable, as they must withstand rigorous use in medical environments. Furthermore, compliance with strict healthcare regulations is essential, making it imperative to work with suppliers who understand these requirements.
Why Are Power Cords Important in Information Technology?
Power cords are indispensable in data centers for power management. They facilitate the connection of servers and networking equipment to power sources, ensuring uninterrupted service and data integrity. For international B2B buyers, sourcing cords that offer scalability and compatibility with existing infrastructure is crucial. Additionally, they should consider suppliers who can provide customized solutions to meet specific power demands.
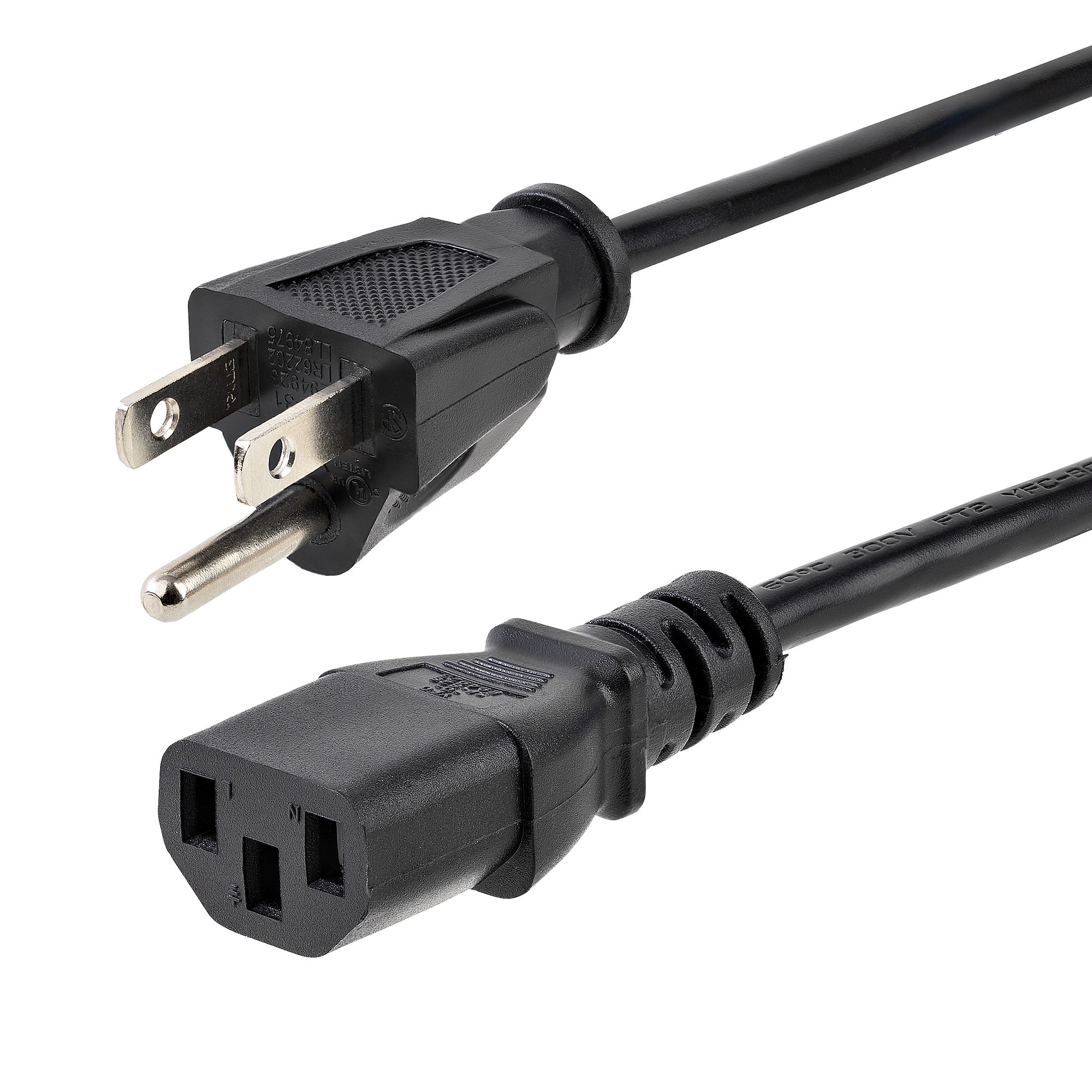
A stock image related to power cords supplier.
How Are Power Cords Used in Construction?
In the construction industry, power cords provide temporary power supply for tools and equipment used on job sites. This application enhances productivity by ensuring that all necessary tools are operational. Buyers should look for cords that are robust and weather-resistant, as they need to perform reliably in various outdoor conditions. Additionally, sourcing from suppliers who understand the unique challenges of construction sites can lead to better product performance.
What Is the Importance of Power Cords in Telecommunications?
Power cords play a vital role in powering communication equipment, ensuring reliable connectivity and service availability. In this sector, sourcing cords that are compatible with various voltage standards is essential for seamless operation. International buyers should consider suppliers who offer ease of installation and robust customer support to address any technical challenges that may arise during setup.
Related Video: Industrial Power Cables, LV cables, LT cables, Power cable Types and Markings, Cable classification
3 Common User Pain Points for ‘power cords supplier’ & Their Solutions
Scenario 1: Difficulty in Ensuring Compliance with Local Regulations
The Problem: Many international B2B buyers, particularly those in Africa and South America, face significant challenges in ensuring that power cords comply with local safety and quality standards. Different countries have varying regulations regarding voltage, material specifications, and environmental considerations. This can lead to costly delays, returns, or penalties if non-compliant products are imported.
The Solution: To overcome this issue, B2B buyers should first conduct thorough research on the specific regulations in their target markets. This includes understanding certifications required by local authorities, such as IEC (International Electrotechnical Commission) standards or local equivalent certifications. When sourcing from suppliers, buyers should explicitly request documentation proving compliance with these standards. Additionally, working with suppliers who have a solid track record in the target region can provide peace of mind. Establishing long-term relationships with reliable power cords suppliers who understand local regulations can help streamline compliance efforts, reducing the risk of costly setbacks.
Scenario 2: Inconsistent Quality and Reliability of Power Cords
The Problem: A common pain point for B2B buyers is the inconsistency in quality and reliability of power cords from different suppliers. Buyers may experience frequent product failures, leading to interruptions in their operations or even damage to connected devices. This inconsistency can stem from varying manufacturing processes, material quality, or lack of quality control measures.
The Solution: To address this challenge, buyers should implement a rigorous supplier evaluation process. This involves requesting samples and conducting thorough testing before placing large orders. Buyers can also consider suppliers who provide comprehensive quality assurance documentation and third-party testing certifications. Establishing clear quality standards and performance benchmarks in contracts can further ensure that suppliers adhere to the expected quality levels. Additionally, utilizing local suppliers who can respond quickly to quality issues may help mitigate risks associated with product failures.
Scenario 3: Challenges in Customization and Product Availability
The Problem: Many international B2B buyers require customized power cords to meet specific needs, such as unique lengths, connectors, or insulation materials. However, suppliers may not always offer the flexibility needed for customization, leading to delays in project timelines or the inability to meet specific operational requirements.
The Solution: To effectively navigate this issue, buyers should communicate their customization needs early in the supplier selection process. It’s crucial to identify suppliers known for their flexibility and willingness to accommodate specific requests. Engaging in early discussions about potential customization can help ensure that suppliers can meet these requirements before contracts are signed. Buyers should also consider suppliers who offer a range of product options and are capable of rapid prototyping, allowing them to test different configurations before committing to larger orders. Additionally, leveraging suppliers with a robust inventory can ensure that even customized orders are fulfilled in a timely manner, minimizing project delays.
Strategic Material Selection Guide for power cords supplier
When selecting materials for power cords, international B2B buyers must consider various factors that affect performance, durability, and compliance with regional standards. Below is an analysis of three common materials used in power cords, focusing on their properties, advantages, disadvantages, and implications for buyers from Africa, South America, the Middle East, and Europe.
What are the Key Properties of PVC in Power Cords?
Polyvinyl Chloride (PVC) is one of the most widely used materials for power cords due to its favorable properties. PVC can withstand temperatures ranging from -10°C to 70°C, making it suitable for various environments. It also exhibits good resistance to abrasion and chemicals, which is crucial for maintaining integrity in industrial applications.
Pros & Cons:
PVC is relatively low-cost and easy to manufacture, which makes it a popular choice for budget-conscious buyers. However, it has a limited temperature range compared to other materials and can become brittle over time, especially under UV exposure.
Impact on Application:
PVC is compatible with a wide range of media, making it suitable for indoor and outdoor applications. However, its limitations in extreme conditions may necessitate alternative materials for specific uses.
Considerations for International Buyers:
Buyers should ensure that PVC products comply with relevant standards such as ASTM D3032 and IEC 60227. In regions like Europe, restrictions on certain additives in PVC may also apply, necessitating careful supplier selection.
How Does Silicone Compare as a Material for Power Cords?
Silicone is another material commonly used in power cords, particularly in high-temperature applications. It has an impressive temperature rating, typically ranging from -60°C to 200°C, which allows it to perform well in extreme conditions.
Pros & Cons:
Silicone is highly flexible and durable, making it suitable for applications where cords need to bend or twist frequently. However, it is more expensive than PVC and may complicate manufacturing processes due to its unique properties.
Impact on Application:
Silicone’s high-temperature resistance makes it ideal for applications involving heat-generating equipment. However, its cost may be prohibitive for budget-sensitive projects.
Considerations for International Buyers:
Buyers in regions such as Africa and South America should be aware of the higher initial investment in silicone cords but may find long-term savings due to their durability and performance in harsh conditions. Compliance with international standards, such as UL and IEC, is also essential.
What are the Benefits and Limitations of Rubber in Power Cords?
Rubber is a traditional material known for its excellent flexibility and resilience. It can withstand temperatures from -40°C to 90°C, making it suitable for various applications, including outdoor and industrial use.
Pros & Cons:
Rubber offers superior resistance to abrasion, tearing, and environmental factors. However, it can be more expensive than PVC and may require specialized manufacturing techniques, which can increase production time.
Impact on Application:
Rubber is particularly effective in applications where cords are exposed to mechanical stress or outdoor conditions. However, its weight can be a disadvantage in applications requiring lightweight solutions.
Considerations for International Buyers:
International buyers should consider the specific environmental conditions in their regions. For example, in the Middle East, where temperatures can be extreme, rubber may offer a better long-term solution despite its higher cost. Compliance with local and international standards is also crucial.
Summary Table of Material Properties for Power Cords
Material | Typical Use Case for power cords supplier | Key Advantage | Key Disadvantage/Limitation | Relative Cost (Low/Med/High) |
---|---|---|---|---|
PVC | General indoor and outdoor applications | Low cost, good chemical resistance | Limited temperature range, can become brittle | Low |
Silicone | High-temperature and flexible applications | Excellent temperature resistance, durability | Higher cost, complex manufacturing | High |
Rubber | Outdoor and industrial applications | Superior flexibility and abrasion resistance | More expensive, heavier | Medium |
This strategic material selection guide provides essential insights for international B2B buyers, helping them choose the right power cord materials based on their specific needs and regional compliance requirements.
In-depth Look: Manufacturing Processes and Quality Assurance for power cords supplier
What Are the Main Stages of Manufacturing Power Cords?
The manufacturing process for power cords involves several critical stages that ensure the final product meets quality and safety standards. Understanding these stages is essential for international B2B buyers, especially those in Africa, South America, the Middle East, and Europe.
1. Material Preparation
The first stage in the power cord manufacturing process is material preparation. This involves sourcing high-quality raw materials such as copper wire, PVC or rubber insulation, and connectors. Buyers should ensure that suppliers use materials compliant with international standards such as RoHS (Restriction of Hazardous Substances) and REACH (Registration, Evaluation, Authorisation, and Restriction of Chemicals).
High-purity copper is preferred for wire conductors due to its excellent electrical conductivity, while PVC and rubber are commonly used for insulation due to their durability and flexibility. International buyers should inquire about the suppliers’ material sourcing practices and certifications to ensure they meet local regulations.
2. Forming
Once the materials are prepared, the next step is the forming process. This includes the drawing of copper wires to the desired gauge and the extrusion of insulation materials. Extrusion involves forcing melted plastic through a die to create the insulation layer around the wire.
This stage may also include the formation of specific connector types, such as NEMA or IEC connectors, depending on the end-use of the power cords. Buyers should look for suppliers that utilize advanced extrusion technology to ensure consistent quality and minimize defects.
3. Assembly
The assembly stage combines all components into a complete power cord. This involves stripping the ends of the wires, connecting them to the appropriate connectors, and ensuring secure connections through soldering or crimping techniques.
For B2B buyers, it’s crucial to verify that the assembly process adheres to strict quality control protocols. Suppliers should be able to demonstrate their assembly processes, including the methods they use to ensure reliability and safety.
4. Finishing
The final stage is the finishing process, which includes quality checks, marking, and packaging. Power cords undergo visual inspections to check for insulation defects, connector integrity, and overall appearance.
Packaging is also vital for ensuring that power cords remain undamaged during shipping. Buyers should ask suppliers about their packaging standards and practices, as this can impact the product’s integrity upon delivery.
How Is Quality Assurance Implemented in Power Cord Manufacturing?
Quality assurance is a cornerstone of the power cord manufacturing process, ensuring that products are safe, reliable, and meet industry standards. Here’s how it is typically implemented:
Relevant International Standards for Power Cords
International standards play a critical role in quality assurance. For power cords, key standards include:
- ISO 9001: This standard outlines the requirements for a quality management system, ensuring that manufacturers consistently provide products that meet customer and regulatory requirements.
- CE Marking: In Europe, power cords must comply with safety directives to obtain CE marking, indicating they meet EU safety, health, and environmental protection standards.
- UL Certification: In the US, Underwriters Laboratories (UL) certification is essential for power cords to ensure they are tested for safety.
B2B buyers should confirm that their suppliers have these certifications and can provide documentation as proof.
What Are the Quality Control Checkpoints?
Effective quality control involves multiple checkpoints throughout the manufacturing process:
- Incoming Quality Control (IQC): This is the first checkpoint where incoming materials are inspected for compliance with specifications before they enter production.
- In-Process Quality Control (IPQC): During the manufacturing stages, IPQC ensures that processes are followed and products are regularly inspected to catch defects early.
- Final Quality Control (FQC): Before products are packaged, FQC involves thorough testing of the finished power cords, including electrical tests and visual inspections.
Buyers should ask suppliers about their quality control processes and how they document these inspections.
What Common Testing Methods Are Used for Power Cords?
Testing methods are essential to ensure the safety and performance of power cords. Common testing methods include:
- Electrical Continuity Tests: These tests ensure that the electrical path is intact and that there are no short circuits.
- Insulation Resistance Tests: This verifies that the insulation material can adequately prevent electrical leakage.
- Mechanical Strength Tests: These tests assess the durability of the power cords under various stress conditions, including bending and pulling.
- Temperature Rise Tests: These tests simulate the conditions under which the cords will operate to ensure they do not overheat.
International buyers should verify that suppliers conduct these tests and provide detailed reports on their findings.
How Can B2B Buyers Verify Supplier Quality Control?
To ensure quality and compliance, B2B buyers should consider the following strategies to verify supplier quality control:
- Supplier Audits: Conducting on-site audits of suppliers can provide insights into their manufacturing processes, quality control measures, and adherence to international standards.
- Requesting Quality Reports: Buyers should request detailed quality assurance reports, including results from all quality checkpoints and testing methods.
- Third-Party Inspections: Engaging third-party inspection services can add an additional layer of verification, ensuring that suppliers adhere to agreed-upon quality standards.
What Are the QC and Certification Nuances for International Buyers?
For international buyers, particularly in regions like Africa, South America, the Middle East, and Europe, understanding the nuances of quality control and certification is vital.
- Regional Compliance: Different regions have varying compliance requirements. Buyers should be aware of local standards and regulations and ensure that their suppliers meet these criteria.
- Documentation and Traceability: Proper documentation is crucial for quality assurance. Buyers should ensure that suppliers provide complete documentation for all certifications, testing results, and quality control procedures.
By considering these factors, international B2B buyers can make informed decisions and establish successful partnerships with power cord suppliers.
Practical Sourcing Guide: A Step-by-Step Checklist for ‘power cords supplier’
Introduction
Sourcing power cords from reliable suppliers is critical for businesses that rely on electronic devices. This guide provides a practical checklist for B2B buyers, particularly those in Africa, South America, the Middle East, and Europe, to streamline their procurement process. By following these steps, you can ensure that you select a supplier that meets your technical requirements, compliance standards, and logistical needs.
Step 1: Define Your Technical Specifications
Establishing clear technical specifications is the foundation of your sourcing process. Identify the type of power cords required, including voltage, amperage, length, and connector types. Consider the environment where the cords will be used—indoors, outdoors, or in specialized settings (e.g., industrial or medical).
- Voltage and Amperage: Ensure the cords can handle the required electrical load without overheating.
- Material Quality: Look for cords made from durable materials that comply with safety standards.
Step 2: Research Potential Suppliers
Conduct thorough research to compile a list of potential power cord suppliers. Utilize industry databases, trade shows, and online marketplaces to identify manufacturers and distributors.
- Market Reputation: Check reviews and testimonials from other businesses, especially those in your region.
- Product Range: Ensure that the suppliers offer a variety of power cords that can cater to your diverse needs.
Step 3: Verify Supplier Certifications
Before proceeding with a supplier, it is essential to verify their certifications. Certifications such as ISO, CE, and UL can indicate compliance with international safety standards.
- Quality Assurance: Suppliers with recognized certifications often have stringent quality control processes.
- Legal Compliance: Ensure that the cords meet local regulations to avoid legal issues and ensure customer safety.
Step 4: Request Samples for Testing
Once you narrow down your list, request samples of the power cords. Testing these samples allows you to assess their quality and compatibility with your equipment.
- Performance Testing: Check for durability, flexibility, and resistance to wear and tear.
- Compatibility: Ensure the connectors fit seamlessly with your devices and systems.
Step 5: Evaluate Pricing and Payment Terms
Review the pricing structures of your shortlisted suppliers. While cost is a critical factor, consider the value offered in terms of product quality and after-sales service.
- Bulk Discounts: Inquire about discounts for large orders, which can significantly reduce overall costs.
- Payment Flexibility: Understand payment terms, including deposits, credit options, and payment timelines.
Step 6: Assess Logistics and Delivery Options
Understanding the logistics of shipping and delivery is crucial for timely procurement. Evaluate the supplier’s ability to deliver within your required timeframe.
- Shipping Methods: Confirm available shipping options and associated costs.
- Lead Times: Ask about production lead times, especially if custom specifications are required.
Step 7: Establish Communication and Support Channels
Clear communication is vital throughout the sourcing process. Ensure that the supplier provides reliable channels for support and updates.
- Point of Contact: Identify a dedicated representative for your account who can address inquiries promptly.
- Response Times: Gauge how quickly the supplier responds to queries during the initial stages of communication.
Following this checklist will help you make informed decisions when sourcing power cords, ensuring that you partner with a supplier who meets your technical and logistical needs effectively.
Comprehensive Cost and Pricing Analysis for power cords supplier Sourcing
What Are the Key Cost Components for Power Cords Suppliers?
When sourcing power cords, understanding the cost structure is essential for making informed decisions. The primary cost components include:
-
Materials: The choice of materials significantly influences the overall cost. High-quality copper conductors, durable insulation, and robust connectors can increase the price but also enhance performance and safety.
-
Labor: Labor costs vary by region and can impact the price of power cords. Suppliers in countries with higher wage standards may have increased labor costs, which can be passed on to buyers.
-
Manufacturing Overhead: This includes expenses related to production facilities, equipment maintenance, and utilities. Efficient manufacturing processes can help reduce overhead costs.
-
Tooling: Custom tooling for specialized power cord designs can incur substantial costs. Suppliers often amortize these costs over production runs, affecting pricing.
-
Quality Control (QC): Implementing rigorous QC processes ensures compliance with international standards but adds to the overall cost structure.
-
Logistics: Shipping and handling costs can vary widely based on the destination and chosen shipping methods, impacting the final price.
-
Margin: Suppliers set their profit margins based on market conditions, competition, and demand fluctuations.
How Do Price Influencers Affect Power Cord Sourcing?
Several factors can influence the pricing of power cords, which international B2B buyers should consider:
-
Volume/MOQ: Minimum Order Quantities (MOQs) often dictate price breaks. Larger orders typically result in lower per-unit costs, making it beneficial for buyers to consolidate purchases.
-
Specifications and Customization: Custom designs or specific technical specifications can lead to higher costs. Buyers must weigh the need for customization against potential price increases.
-
Materials Quality and Certifications: The quality of materials and adherence to safety certifications (like CE, UL, or RoHS) can affect pricing. Higher quality materials often come at a premium but can yield long-term cost savings through durability.
-
Supplier Factors: The supplier’s reputation, location, and production capabilities can influence pricing. Established suppliers with proven track records may charge more due to their reliability.
-
Incoterms: Understanding Incoterms is crucial for determining who bears the cost of shipping, insurance, and risk during transit. This knowledge can help buyers manage their total costs effectively.
What Buyer Tips Can Help Maximize Cost-Efficiency?
International B2B buyers can implement several strategies to optimize their sourcing costs for power cords:
-
Negotiate Terms: Leverage your buying power to negotiate better terms, including price reductions, improved payment terms, or reduced shipping costs. Building a long-term relationship with suppliers can also yield discounts.
-
Evaluate Total Cost of Ownership (TCO): Consider not just the purchase price but also the long-term costs associated with the power cords, such as maintenance, warranty, and potential replacements.
-
Understand Pricing Nuances: Be aware of regional pricing differences, particularly between suppliers from Africa, South America, the Middle East, and Europe. Currency fluctuations, import tariffs, and local market conditions can affect pricing.
-
Request Samples: Before committing to a large order, request samples to assess quality and performance. This can help avoid costly mistakes later in the procurement process.
-
Stay Informed About Market Trends: Regularly monitor market trends and pricing dynamics. This knowledge can provide leverage during negotiations and help buyers make timely purchasing decisions.
By understanding the complexities of cost structures and pricing influencers, international B2B buyers can navigate the sourcing landscape more effectively, ensuring they achieve optimal pricing and quality in their power cord procurement.
Alternatives Analysis: Comparing power cords supplier With Other Solutions
Understanding Alternatives to Power Cords Supplier Solutions
In today’s rapidly evolving technological landscape, B2B buyers must consider various solutions when sourcing power cords and related products. While traditional power cords suppliers offer a reliable option, exploring alternatives can uncover innovative solutions that may better meet specific operational needs. This section provides a detailed comparison between power cords suppliers and two notable alternatives: wireless power transmission and power distribution units (PDUs).
Comparison Table
Comparison Aspect | Power Cords Supplier | Wireless Power Transmission | Power Distribution Units (PDUs) |
---|---|---|---|
Performance | High, with stable power delivery | Moderate, dependent on distance and obstacles | High, can manage multiple devices |
Cost | Generally low to moderate | Higher initial investment, but potential savings on installation | Moderate, depending on features |
Ease of Implementation | Simple, plug-and-play | Complex, requires specialized installation | Relatively straightforward with some planning |
Maintenance | Minimal, replace when damaged | Low, but technology may need upgrades | Moderate, requires regular checks and updates |
Best Use Case | General applications, home and office use | Charging devices in spaces without outlets | Data centers, server rooms, and high-density environments |
Detailed Breakdown of Alternatives
What Are the Benefits and Drawbacks of Wireless Power Transmission?
Wireless power transmission utilizes electromagnetic fields to transfer energy without physical connectors. This technology is particularly advantageous in environments where traditional wiring is impractical, such as in certain medical or industrial applications. The primary benefit of this method is the elimination of cord clutter and the potential for remote charging of devices. However, it does come with drawbacks, including higher initial costs and performance limitations over longer distances or through obstacles, which may not be suitable for all applications.
How Do Power Distribution Units (PDUs) Serve as an Alternative?
Power Distribution Units (PDUs) are devices that distribute electric power to multiple outputs, typically used in data centers and server rooms. PDUs can manage power loads efficiently and provide features like remote monitoring and surge protection. Their best use case lies in environments where multiple devices need to be powered and monitored, ensuring optimal power usage. While PDUs can be more expensive than traditional power cords, they offer enhanced functionality, making them a valuable investment for organizations with high energy demands. However, they require some level of planning and installation, which could pose a challenge for smaller operations.
How Should B2B Buyers Choose the Right Solution for Their Needs?
When selecting the appropriate solution, B2B buyers should carefully assess their specific requirements. Key considerations include the scale of operations, the types of devices to be powered, and the existing infrastructure. For general applications, a power cords supplier may offer the most straightforward solution. However, for environments with high energy demands or where space is a concern, exploring wireless power transmission or PDUs could provide significant long-term benefits. Ultimately, the right choice will align with the operational goals, budget constraints, and technological capabilities of the organization.
Essential Technical Properties and Trade Terminology for power cords supplier
What Are the Essential Technical Properties of Power Cords?
When sourcing power cords, understanding their technical properties is crucial for ensuring quality, safety, and compatibility with your specific applications. Here are some key specifications that every B2B buyer should consider:
1. Material Grade: What Should You Know?
The material used in power cords typically includes copper for conductors and PVC or rubber for insulation. Copper is favored for its excellent conductivity, while PVC is cost-effective and offers good insulation properties. High-grade materials can reduce energy loss and enhance durability, which is essential for long-term use in various environments.
2. Current Rating: Why Is It Important?
The current rating, measured in amperes (A), indicates the maximum current the power cord can safely carry without overheating. Selecting a cord with an appropriate current rating is vital to prevent electrical fires and equipment damage. Always ensure the rating matches or exceeds the requirements of the devices you intend to power.
3. Voltage Rating: How Does It Affect Performance?
Voltage ratings, typically expressed in volts (V), denote the maximum voltage the power cord can handle. Using a cord with a voltage rating lower than the system’s operating voltage can lead to insulation breakdown and potential hazards. Make sure to match the voltage rating with your electrical systems to ensure safe operation.
4. Temperature Rating: What Are the Limits?
Power cords are designed to operate within specific temperature ranges. The temperature rating indicates the maximum ambient temperature the cord can withstand without degrading. This is particularly important in industrial or high-temperature environments. Selecting cords with appropriate temperature ratings ensures reliability and longevity.
5. Length and Flexibility: How Do They Impact Usage?
The length of the power cord affects its usability in different settings. Longer cords provide more flexibility but may result in voltage drop over distance, especially in high-current applications. Consider the balance between length and flexibility based on your operational needs while adhering to the specifications to avoid performance issues.
What Trade Terminology Should You Understand When Purchasing Power Cords?
Familiarizing yourself with common trade terms can streamline your procurement process and enhance communication with suppliers.
1. OEM (Original Equipment Manufacturer): What Does It Mean?
OEM refers to companies that produce components or products that are marketed by another company under its brand name. Understanding OEM relationships can help you identify reputable suppliers who adhere to industry standards and can provide customized solutions tailored to your needs.
2. MOQ (Minimum Order Quantity): Why Is It Relevant?
MOQ indicates the smallest number of units a supplier is willing to sell in a single order. Knowing the MOQ helps you gauge whether a supplier can meet your purchasing needs without overcommitting to inventory that might not be required.
3. RFQ (Request for Quotation): How Do You Use It?
An RFQ is a document that invites suppliers to bid on providing specific products or services. Issuing an RFQ can help you obtain competitive pricing and terms, ensuring you make informed purchasing decisions while fostering supplier relationships.
4. Incoterms (International Commercial Terms): What Should You Consider?
Incoterms define the responsibilities of buyers and sellers regarding shipping, insurance, and tariffs. Familiarizing yourself with these terms is essential for understanding the logistics of your purchase, particularly when dealing with international suppliers, to avoid unexpected costs and delays.
5. Certification Standards: Why Are They Essential?
Certification standards, such as UL, CE, or RoHS, indicate compliance with safety and environmental regulations. Ensuring that power cords meet these standards is crucial for legal compliance and to guarantee the safety and reliability of your electrical systems.
By understanding these technical properties and trade terms, B2B buyers can make informed purchasing decisions, ensuring they select the right power cords for their specific applications while fostering smooth interactions with suppliers.
Navigating Market Dynamics and Sourcing Trends in the power cords supplier Sector
What Are the Current Market Dynamics and Key Trends in the Power Cords Supplier Sector?
The global power cords market is experiencing significant growth, driven by increased demand across various sectors, including consumer electronics, automotive, and industrial applications. A surge in electronic device usage in emerging markets like Africa and South America is propelling this demand. Additionally, the rise of smart homes and IoT devices in regions such as Europe and the Middle East is transforming sourcing trends. International B2B buyers should focus on suppliers that are innovating to meet these demands, as the ability to adapt to changing technology and consumer preferences is critical.
Emerging trends include a shift towards customizable power solutions and the integration of smart technology in power cords. Suppliers are leveraging advanced manufacturing processes to produce high-quality, durable cords that comply with international safety standards. Moreover, the increasing importance of digital platforms for sourcing is making it easier for buyers to connect with manufacturers globally, facilitating better price negotiations and product comparisons. Buyers from regions like Kenya and the UK should leverage these platforms to identify reliable suppliers who can meet their specific requirements.
How Is Sustainability Impacting Sourcing in the Power Cords Supplier Sector?
Sustainability is becoming a cornerstone of sourcing strategies in the power cords sector. International B2B buyers are increasingly prioritizing suppliers who demonstrate a commitment to reducing their environmental impact. This includes using recyclable materials, minimizing energy consumption during production, and ensuring responsible waste management practices. The environmental footprint of power cords, often overlooked, is significant, especially when considering the materials used and the manufacturing processes involved.
Buyers should look for suppliers with recognized sustainability certifications, such as ISO 14001 or those adhering to the Global Recycled Standard (GRS). These certifications indicate a supplier’s commitment to ethical sourcing and environmental stewardship. Furthermore, the demand for “green” materials is rising, with buyers seeking cords made from biodegradable or recycled components. By prioritizing sustainability, B2B buyers can not only comply with regulatory requirements but also enhance their brand reputation and appeal to environmentally conscious consumers.
What Is the Evolution of the Power Cords Supplier Sector and Its Relevance to B2B Buyers?
The power cords supplier sector has evolved significantly over the past few decades. Initially dominated by basic, unregulated products, the market has transitioned to a landscape characterized by stringent safety standards and technological advancements. The introduction of international regulations, such as the Restriction of Hazardous Substances (RoHS) directive in Europe, has pushed suppliers to innovate and enhance the safety and efficiency of their products.
This evolution is crucial for B2B buyers as it underscores the importance of selecting suppliers who not only meet current standards but are also proactive in adapting to future regulations. Understanding the historical context of power cords can help buyers make informed decisions about the suppliers they choose to partner with. By aligning with suppliers who prioritize innovation and compliance, businesses can mitigate risks and ensure a steady supply of high-quality products that meet both local and international standards.
Frequently Asked Questions (FAQs) for B2B Buyers of power cords supplier
-
How do I choose the right power cord supplier for my business needs?
Selecting the right power cord supplier involves several key considerations. Firstly, assess their product range to ensure they offer the types of cords you need, such as UL-listed or CE-certified options. Secondly, evaluate their reputation and reliability by checking customer reviews and industry certifications. Additionally, inquire about their production capabilities, lead times, and quality assurance processes. Establishing clear communication and understanding their customer support is also crucial. Finally, consider suppliers who can accommodate your specific requirements, such as custom designs or packaging. -
What are the common certifications for power cords that I should look for?
When sourcing power cords, ensure they have relevant certifications that guarantee safety and compliance. Look for UL (Underwriters Laboratories) certification in the United States, CE (Conformité Européenne) marking in Europe, and RoHS (Restriction of Hazardous Substances) compliance for environmental safety. In Africa and the Middle East, check for local certifications that might be required. These certifications not only demonstrate the quality of the product but also protect your business from potential liability issues. -
How can I customize power cords to meet my specific requirements?
Customization of power cords can involve altering the length, color, connector type, or even the materials used. To initiate customization, discuss your needs directly with potential suppliers, as many manufacturers offer bespoke services. Ensure you provide clear specifications and request prototypes to evaluate before placing large orders. Be mindful of minimum order quantities (MOQs) that may apply to customized products, as this can affect your budget and inventory management. -
What is the typical MOQ for ordering power cords from suppliers?
Minimum order quantities (MOQs) for power cords can vary significantly among suppliers. Typically, MOQs can range from a few hundred to several thousand units depending on the type of product, complexity of customization, and the supplier’s production capabilities. When negotiating with suppliers, clarify MOQs and see if they can accommodate smaller orders, especially for initial trials or new products. Understanding the MOQ will help you manage your inventory and cash flow effectively. -
What payment terms should I expect when sourcing power cords internationally?
Payment terms for international transactions can vary widely based on supplier policies and your negotiating power. Common terms include upfront payments, partial payments (e.g., 30% deposit and 70% before shipping), or payment upon delivery. In some cases, suppliers may accept letters of credit or escrow services to protect both parties. It’s essential to discuss payment methods early in negotiations to ensure that you’re comfortable with the terms and can manage your cash flow accordingly. -
How can I ensure quality assurance when sourcing power cords?
To ensure quality assurance, request detailed specifications and certifications from your supplier before placing an order. Implement a rigorous inspection process that includes pre-shipment inspections and random sampling during production. Additionally, consider third-party quality control services for an unbiased assessment of product quality. Establishing a clear quality control agreement with your supplier will also help mitigate risks associated with defective products. -
What are the logistics considerations for importing power cords from suppliers?
When importing power cords, consider shipping costs, lead times, and customs regulations. Work closely with your supplier to determine the best shipping method, whether by air or sea, based on urgency and budget. Be aware of any import duties or taxes that may apply in your country. It’s beneficial to partner with a reliable freight forwarder who can streamline the logistics process and ensure compliance with international trade regulations. -
How do I handle disputes with power cord suppliers?
Handling disputes with suppliers requires a structured approach. Start by documenting all communications and agreements to establish a clear record. If an issue arises, communicate directly and professionally with the supplier to resolve it amicably. If necessary, consider mediation or arbitration as a means to settle disputes without escalating to legal action. Having a well-defined contract that includes dispute resolution clauses can also protect your interests in the event of disagreements.
Important Disclaimer & Terms of Use
⚠️ Important Disclaimer
The information provided in this guide, including content regarding manufacturers, technical specifications, and market analysis, is for informational and educational purposes only. It does not constitute professional procurement advice, financial advice, or legal advice.
While we have made every effort to ensure the accuracy and timeliness of the information, we are not responsible for any errors, omissions, or outdated information. Market conditions, company details, and technical standards are subject to change.
B2B buyers must conduct their own independent and thorough due diligence before making any purchasing decisions. This includes contacting suppliers directly, verifying certifications, requesting samples, and seeking professional consultation. The risk of relying on any information in this guide is borne solely by the reader.
Strategic Sourcing Conclusion and Outlook for power cords supplier
In conclusion, effective strategic sourcing in the power cords supply sector is paramount for international B2B buyers aiming to optimize their supply chains and enhance operational efficiency. By prioritizing partnerships with reliable suppliers and leveraging data-driven decision-making, businesses can ensure the procurement of high-quality power cords that meet safety standards and performance expectations.
How Can Strategic Sourcing Drive Competitive Advantage?
Investing in strategic sourcing not only reduces costs but also enables buyers to adapt to changing market demands and technological advancements. For buyers from Africa, South America, the Middle East, and Europe, understanding local regulations and supply chain dynamics is essential for successful sourcing strategies.
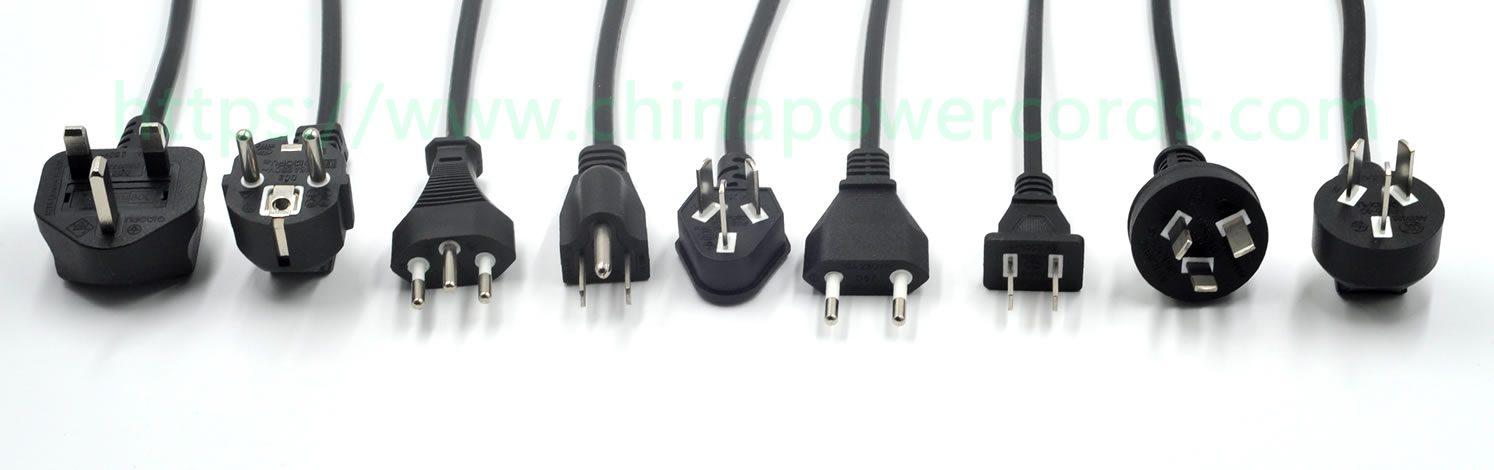
A stock image related to power cords supplier.
As we look toward the future, the emphasis on sustainable sourcing practices and innovative supply chain solutions will only grow stronger. B2B buyers are encouraged to actively engage with suppliers who prioritize eco-friendly materials and manufacturing processes. By doing so, you not only contribute to a sustainable future but also enhance your brand’s reputation in a competitive marketplace.
What Steps Should Buyers Take Next?
To capitalize on these insights, it is crucial for buyers to conduct thorough market research, establish clear communication channels with suppliers, and continuously evaluate sourcing strategies. Embrace the opportunity to build resilient supply chains that can withstand global challenges and position your business for success in the evolving landscape of power cords supply.