Cut Costs with the Best Shopping Bag Manufacturer Guide (2025)
Introduction: Navigating the Global Market for shopping bag manufacturer
In today’s fast-paced global marketplace, sourcing quality shopping bags that meet both aesthetic and functional requirements poses a significant challenge for international B2B buyers. The demand for sustainable and versatile shopping solutions has surged, compelling businesses across Africa, South America, the Middle East, and Europe—particularly in countries like Germany and Egypt—to seek reliable shopping bag manufacturers that align with their brand values and operational needs. This comprehensive guide will delve into the diverse types of shopping bags available, their various applications, and essential considerations for vetting suppliers.
By providing actionable insights on cost structures, production timelines, and sustainability practices, this guide empowers B2B buyers to make informed purchasing decisions that can enhance their brand image and customer satisfaction. As the market evolves, understanding the nuances of sourcing shopping bags will be crucial for businesses aiming to stay ahead of the competition. Whether you are a retailer looking to enhance your packaging strategy or a distributor seeking reliable manufacturers, this guide will serve as your roadmap to successfully navigate the global market for shopping bag manufacturers.
What Types of Shopping Bags Are Available?
Explore the various styles and materials that cater to different market needs.
How Can You Vet Shopping Bag Suppliers Effectively?
Learn best practices for assessing supplier capabilities and reliability.
What Are the Cost Factors in Sourcing Shopping Bags?
Understand the elements that influence pricing and how to negotiate effectively.
How Do Sustainability Practices Impact Your Choice of Manufacturer?
Discover the importance of eco-friendly materials and practices in today’s market.
This guide equips you with the knowledge necessary to navigate these critical aspects, ensuring that your sourcing decisions are both strategic and beneficial for your business.
Understanding shopping bag manufacturer Types and Variations
Type Name | Key Distinguishing Features | Primary B2B Applications | Brief Pros & Cons for Buyers |
---|---|---|---|
Plastic Shopping Bags | Lightweight, waterproof, and customizable designs | Retail, supermarkets, and events | Pros: Cost-effective, versatile; Cons: Environmental concerns, less durable than alternatives. |
Paper Shopping Bags | Biodegradable, sturdy, and often recyclable | Boutiques, luxury brands, and eco-friendly retailers | Pros: Environmentally friendly, premium feel; Cons: Higher cost, less water-resistant. |
Reusable Shopping Bags | Durable materials, often made from fabric or recycled materials | Grocery stores, markets, and promotional events | Pros: Long-lasting, eco-friendly; Cons: Higher initial investment, requires cleaning. |
Non-Woven Polypropylene Bags | Durable, lightweight, and available in various colors | Trade shows, corporate gifts, and retail | Pros: Strong, reusable, customizable; Cons: May not be as eco-friendly as paper options. |
Cotton Shopping Bags | Natural fibers, reusable, and customizable | Eco-conscious brands and markets | Pros: Sustainable, strong; Cons: Higher cost, requires care to maintain. |
What Are the Characteristics of Plastic Shopping Bags?
Plastic shopping bags are widely recognized for their lightweight and waterproof properties. They are often produced in bulk, making them a cost-effective solution for retailers. These bags can be customized with logos and designs, making them suitable for promotional events. However, buyers should consider the environmental impact of plastic, as these bags contribute to pollution and are often not biodegradable.
How Do Paper Shopping Bags Compare?
Paper shopping bags are favored for their biodegradable nature and sturdy construction. They are commonly used by boutiques and luxury brands to convey a premium image. While they provide a more environmentally friendly option, buyers should be aware of their higher cost and reduced water resistance compared to plastic alternatives. Additionally, the design options for paper bags can enhance brand visibility.
Are Reusable Shopping Bags Worth the Investment?
Reusable shopping bags are designed for durability and are often made from fabric or recycled materials. They are ideal for grocery stores and markets, promoting eco-friendliness and long-term use. Although they require a higher initial investment, their longevity can lead to cost savings over time. Buyers should consider the cleaning requirements and consumer preferences when selecting reusable bags.
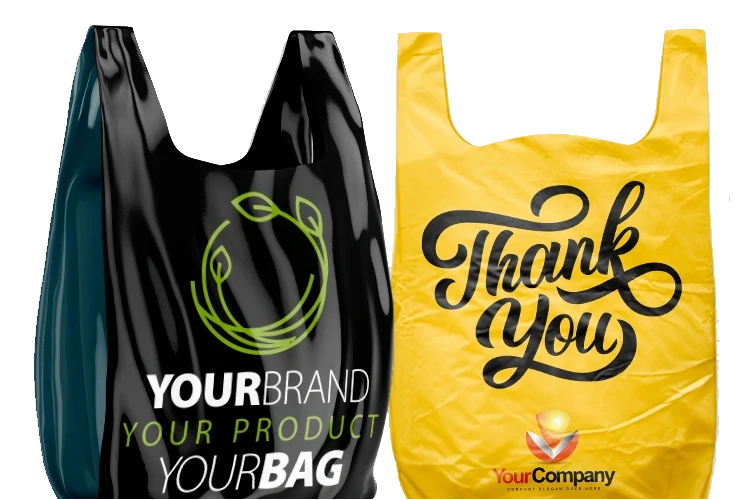
A stock image related to shopping bag manufacturer.
What Are Non-Woven Polypropylene Bags Best For?
Non-woven polypropylene bags are a popular choice for trade shows and corporate gifts due to their strength and lightweight nature. They can be produced in various colors and are often customizable, making them appealing for branding. While they are reusable, buyers should evaluate their environmental impact, as they may not be as sustainable as paper options.
Why Choose Cotton Shopping Bags?
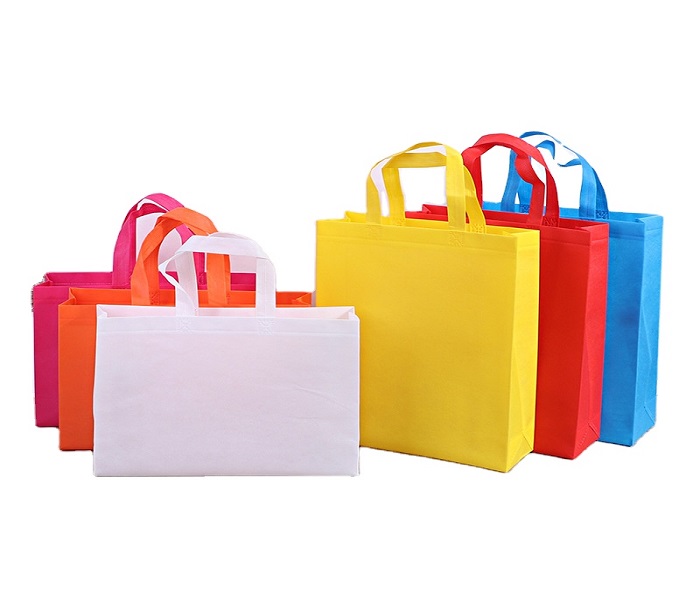
A stock image related to shopping bag manufacturer.
Cotton shopping bags are made from natural fibers, making them a sustainable choice for eco-conscious brands. They are strong and can be customized, enhancing brand identity. However, the higher cost and care requirements, such as washing, may deter some buyers. Overall, cotton bags are a premium option that aligns with environmentally responsible practices.
Related Video: The Perfect Tote Bag Tutorial! – Learn to Sew Series
Key Industrial Applications of shopping bag manufacturer
Industry/Sector | Specific Application of shopping bag manufacturer | Value/Benefit for the Business | Key Sourcing Considerations for this Application |
---|---|---|---|
Retail | Custom branded shopping bags | Enhances brand visibility and customer loyalty | Material quality, customization options, sustainability practices |
Food and Beverage | Eco-friendly takeaway bags | Meets consumer demand for sustainable packaging solutions | Compliance with food safety regulations, durability, design options |
E-commerce | Protective shipping bags | Ensures product safety during transit, reduces returns | Size variability, material strength, cost-effectiveness |
Events and Promotions | Promotional tote bags | Increases brand exposure during events and trade shows | Design flexibility, order volume, lead times |
Pharmaceutical | Medical supply bags | Ensures secure transportation of sensitive products | Regulatory compliance, material safety, customization options |
How Are Custom Branded Shopping Bags Used in Retail?
In the retail sector, shopping bag manufacturers create custom branded bags that serve as a vital marketing tool. These bags not only provide functional use for customers but also enhance brand visibility as they are carried in public. For international B2B buyers, especially those in Europe and Africa, it’s crucial to consider the bag’s material quality and printing capabilities. Sustainable options are increasingly favored, aligning with consumer preferences for eco-friendly practices.
What Role Do Eco-Friendly Takeaway Bags Play in Food and Beverage Industries?
The food and beverage industry increasingly relies on eco-friendly takeaway bags to meet consumer demands for sustainable packaging. Shopping bag manufacturers provide solutions that comply with food safety regulations while also being durable enough for heavy food items. B2B buyers from regions like South America and the Middle East should prioritize suppliers who offer biodegradable materials and can demonstrate compliance with local regulations to appeal to environmentally conscious consumers.
How Do Protective Shipping Bags Benefit E-commerce Businesses?
In the e-commerce sector, protective shipping bags are essential for safeguarding products during transit. Shopping bag manufacturers supply a variety of sizes and materials that ensure products arrive undamaged, thus reducing return rates and enhancing customer satisfaction. Buyers in Africa and Europe should focus on sourcing bags that offer strength and cost-effectiveness, as this directly impacts their bottom line and customer experience.
Why Are Promotional Tote Bags Important for Events and Promotions?
Promotional tote bags are widely used in events and trade shows to increase brand exposure. Shopping bag manufacturers can create eye-catching designs that not only serve as functional items but also as marketing tools. For international buyers, understanding lead times and order volumes is critical, as these factors can influence the effectiveness of promotional campaigns during high-traffic events.
What Are the Key Considerations for Medical Supply Bags in the Pharmaceutical Sector?
In the pharmaceutical industry, shopping bag manufacturers provide specialized medical supply bags that ensure the secure transportation of sensitive products. These bags must comply with stringent regulatory standards and utilize materials that guarantee safety. B2B buyers should prioritize manufacturers who can offer customization options while ensuring compliance with local and international regulations to mitigate risks associated with product handling.
Related Video: 25 Amazing Uses for IBC Totes
3 Common User Pain Points for ‘shopping bag manufacturer’ & Their Solutions
Scenario 1: Sourcing High-Quality Sustainable Shopping Bags
The Problem:
International B2B buyers, especially those in regions like Africa and South America, often struggle to find shopping bag manufacturers that provide high-quality, sustainable products. The increasing consumer demand for eco-friendly options poses a challenge for buyers who need to ensure that their suppliers not only meet environmental standards but also deliver durable and appealing bags. Many manufacturers may claim to be sustainable, but the lack of transparency in their sourcing and production processes can lead to issues with quality and compliance.
The Solution:
To effectively source high-quality, sustainable shopping bags, buyers should prioritize manufacturers that provide clear documentation of their sustainability practices. Look for certifications such as ISO 14001 for environmental management or FSC certification for paper products. Engaging in direct communication with potential suppliers about their sourcing materials, production processes, and waste management can also help assess their commitment to sustainability. Additionally, consider requesting samples to evaluate the quality firsthand before placing large orders. Building long-term relationships with reliable suppliers who demonstrate consistent quality and transparency will pay off in the long run.
Scenario 2: Navigating Complex Import Regulations for Shopping Bags
The Problem:
B2B buyers in the Middle East and Europe often encounter complex import regulations that can delay shipments of shopping bags. These regulations can include tariffs, customs documentation, and compliance with local packaging laws. Misunderstanding these requirements can lead to unexpected costs, fines, and disruptions in the supply chain, ultimately affecting the buyer’s ability to meet customer demands.
The Solution:
To navigate these complex import regulations, buyers should invest in understanding the specific requirements for their target markets. This can involve consulting with logistics experts or customs brokers who specialize in the packaging industry. Creating a checklist of necessary documentation and compliance standards based on the importing country’s regulations can streamline the process. Buyers should also consider sourcing from manufacturers who have experience exporting to their region, as they can provide valuable insights and support in ensuring compliance. Establishing a reliable logistics partner can further mitigate risks associated with shipping delays and customs issues.
Scenario 3: Managing Fluctuating Prices and Availability of Materials
The Problem:
B2B buyers frequently face challenges with fluctuating prices and availability of materials used in shopping bags, especially in volatile markets like Europe and Africa. The recent global supply chain disruptions have made it difficult for manufacturers to maintain consistent pricing, which can affect budgeting and forecasting for buyers. This unpredictability can lead to last-minute changes in orders or even stock shortages.
The Solution:
To manage the risks associated with material price fluctuations and availability, buyers should adopt a proactive procurement strategy. This includes establishing long-term contracts with manufacturers to lock in prices and ensure a consistent supply of materials. Additionally, diversifying the supplier base can help mitigate risks related to single-source dependency. Buyers should also stay informed about market trends and potential disruptions by engaging with industry networks or subscribing to market intelligence reports. Implementing a just-in-time inventory approach can also help balance costs and stock levels effectively, allowing buyers to respond more flexibly to market changes.
Strategic Material Selection Guide for shopping bag manufacturer
What Are the Key Materials Used in Shopping Bag Manufacturing?
When selecting materials for shopping bags, manufacturers often consider several common options, each with unique properties, advantages, and limitations. Understanding these materials is crucial for international B2B buyers, especially those operating in diverse markets such as Africa, South America, the Middle East, and Europe.
How Does Polypropylene (PP) Perform in Shopping Bag Applications?
Polypropylene is a popular material for shopping bags due to its lightweight nature and strength. It boasts a high melting point, making it suitable for various temperature conditions. Polypropylene bags are resistant to moisture and chemicals, which enhances their durability in different environments.
Pros and Cons:
– Pros: Durable, reusable, and cost-effective. They can withstand heavy loads without tearing and are often recyclable.
– Cons: Limited UV resistance can lead to degradation if exposed to sunlight for extended periods. Manufacturing can be complex due to the need for specialized equipment.
Impact on Application:
Polypropylene bags are ideal for groceries and retail shopping due to their strength and resistance to moisture. However, they may not be suitable for high-temperature applications.
Considerations for International Buyers:
Buyers should ensure compliance with local regulations regarding recyclability and safety standards, such as ASTM and DIN. In regions like Germany, there is a strong emphasis on sustainability, making recyclable materials more favorable.
What Advantages Does Cotton Offer for Shopping Bags?
Cotton is a natural fiber that provides a sustainable option for shopping bags. It is biodegradable and can be produced organically, appealing to environmentally conscious consumers. Cotton bags are breathable, which prevents moisture buildup.
Pros and Cons:
– Pros: Highly durable and reusable, cotton bags can last for years with proper care. They also offer a premium feel and can be printed with vibrant designs.
– Cons: Cotton bags can be more expensive to produce and may require more complex manufacturing processes. They are also less resistant to moisture compared to synthetic materials.
Impact on Application:
Cotton bags are suitable for high-end retail and boutique applications, where branding and aesthetics are essential. They are less ideal for wet or heavy items unless treated for moisture resistance.
Considerations for International Buyers:
Buyers should consider the sourcing of organic cotton and compliance with certifications such as GOTS (Global Organic Textile Standard). In regions like Egypt, where cotton is a traditional crop, sourcing locally can reduce costs and support local economies.
Why Choose Recycled PET (rPET) for Shopping Bags?
Recycled PET, made from post-consumer plastic bottles, is gaining traction in the shopping bag industry. It is a sustainable alternative that reduces plastic waste and promotes recycling.
Pros and Cons:
– Pros: rPET bags are lightweight, strong, and resistant to moisture. They also align with sustainability goals, appealing to eco-conscious consumers.
– Cons: The production process can be energy-intensive, and the quality may vary based on the source of the recycled materials.
Impact on Application:
rPET bags are excellent for retail and grocery applications, providing a strong and sustainable option for consumers. They are particularly well-received in markets with stringent environmental regulations.
Considerations for International Buyers:
Buyers should verify the recycling standards and certifications of rPET materials, ensuring compliance with local regulations. In Europe, for example, adherence to EU regulations on plastic waste is critical.
What Role Does Paper Play in Shopping Bag Manufacturing?
Paper bags are a traditional choice for shopping bags, especially in retail environments. They are biodegradable and can be produced from recycled materials, making them an eco-friendly option.
Pros and Cons:
– Pros: Paper bags are easily customizable, cost-effective, and biodegradable. They are suitable for branding and can be produced in various sizes and strengths.
– Cons: They are less durable than synthetic options and can be susceptible to moisture damage. Their load-bearing capacity is generally lower than that of plastic or fabric bags.
Impact on Application:
Paper bags are commonly used in retail settings, particularly for clothing and lightweight items. They are less suitable for heavy or wet products.
Considerations for International Buyers:
Buyers should consider the paper’s weight and strength, ensuring it meets the needs of their products. Compliance with local recycling and waste regulations is also essential, especially in countries with strict environmental policies.
Summary Table of Material Selection for Shopping Bags
Material | Typical Use Case for Shopping Bag Manufacturer | Key Advantage | Key Disadvantage/Limitation | Relative Cost (Low/Med/High) |
---|---|---|---|---|
Polypropylene | Grocery and retail bags | Durable and reusable | Limited UV resistance | Medium |
Cotton | High-end retail and boutique bags | Premium feel and sustainable | Higher production costs | High |
Recycled PET | Retail and grocery bags | Eco-friendly and strong | Variable quality | Medium |
Paper | Retail bags for clothing and lightweight items | Biodegradable and customizable | Susceptible to moisture | Low |
This guide provides a comprehensive overview of materials commonly used in shopping bag manufacturing, helping international B2B buyers make informed decisions based on their specific market needs and compliance requirements.
In-depth Look: Manufacturing Processes and Quality Assurance for shopping bag manufacturer
What Are the Key Stages in the Manufacturing Process of Shopping Bags?
The manufacturing process for shopping bags typically consists of several essential stages, each crucial for ensuring the final product meets quality and durability standards. Understanding these stages can help B2B buyers, especially those from regions like Africa, South America, the Middle East, and Europe, make informed decisions when selecting suppliers.
1. Material Preparation
The first step involves selecting the right materials based on the type of shopping bag being produced. Common materials include:
- Polyethylene (PE): Widely used for its lightweight and waterproof properties.
- Kraft Paper: Preferred for eco-friendly options, offering good strength and printability.
- Non-Woven Fabric: Known for its durability and reusable nature, appealing to environmentally conscious consumers.
Once materials are selected, they undergo preparation processes such as cutting, treating, or printing. This step is vital, as the quality of the raw materials significantly influences the bag’s performance.
2. Forming the Bag Structure
After preparation, the next stage is forming the bag. This can involve different techniques depending on the material:
- Extrusion: Used for plastic bags, where plastic pellets are melted and formed into sheets.
- Die Cutting: For paper bags, sheets are cut into specific shapes using a die.
- Sewing or Heat Sealing: For non-woven fabric bags, edges are sewn or sealed using heat to create a sturdy structure.
Understanding these techniques allows buyers to assess the manufacturing capabilities of their suppliers, ensuring they can produce the desired bag type.
3. Assembly of Components
In this stage, additional components such as handles, reinforcements, and closures are added. For example, paper bags might have twisted paper handles, while plastic bags may use integrated handles. The assembly process can vary significantly:
- Manual Assembly: Common for smaller production runs or customized orders.
- Automated Assembly: Ideal for large-scale production, using machines to attach components quickly and consistently.
Buyers should inquire about the assembly methods used by potential suppliers, as this can affect lead times and overall production costs.
4. Finishing Touches
The final stage involves finishing processes, which may include:
- Printing: Custom designs, logos, or branding are printed using various methods like flexography or digital printing.
- Quality Coating: Some bags receive coatings for added durability or aesthetic appeal.
- Packaging: Finished bags are packaged for shipment, ensuring they remain undamaged during transport.
This stage is critical for ensuring that the bags not only meet functional requirements but also align with branding expectations.
How Is Quality Assurance Implemented in Shopping Bag Manufacturing?
Quality assurance (QA) is integral to the manufacturing process, ensuring that the final products meet international standards and customer expectations. For B2B buyers, understanding QA processes can help mitigate risks associated with product quality.
Relevant International Standards for Shopping Bag Manufacturing
Several international standards govern the quality of shopping bags, including:
- ISO 9001: Focuses on maintaining quality management systems, emphasizing continuous improvement and customer satisfaction.
- CE Marking: Required for products sold in the European Economic Area, indicating compliance with health and safety standards.
- API Standards: Applicable for bags used in specific industries, ensuring products meet technical specifications.
B2B buyers should verify that suppliers are compliant with these standards, as this can significantly impact product reliability and marketability.
What Are the Key Quality Control Checkpoints?
Quality control (QC) is typically structured around several checkpoints during the manufacturing process:
- Incoming Quality Control (IQC): Inspection of raw materials upon arrival to ensure they meet specified standards.
- In-Process Quality Control (IPQC): Continuous monitoring during the production process to identify and rectify defects early.
- Final Quality Control (FQC): Comprehensive inspection of finished products before packaging and shipping, ensuring they meet all specifications.
These checkpoints are crucial for maintaining quality throughout the manufacturing process. Buyers should request information on the QC practices of potential suppliers to ensure they adhere to rigorous standards.
What Common Testing Methods Are Used to Ensure Quality?
Quality testing is essential to validate that shopping bags meet performance and safety criteria. Common testing methods include:
- Tensile Strength Testing: Measures the maximum load a bag can withstand before breaking.
- Tear Resistance Testing: Assesses how well a bag can resist tearing under stress.
- Environmental Testing: Evaluates how materials perform under various environmental conditions, including exposure to moisture and temperature changes.
B2B buyers should inquire about the specific testing methods used by suppliers and request access to testing reports to verify compliance with quality standards.
How Can B2B Buyers Verify Supplier Quality Control?
Verifying a supplier’s quality control practices is essential for B2B buyers to ensure product reliability. Here are several effective strategies:
- Audits: Conduct regular audits of suppliers to assess their manufacturing processes and quality control systems. This can include on-site inspections and reviews of their quality management documentation.
- Quality Reports: Request detailed quality reports that outline testing results, compliance with standards, and any corrective actions taken.
- Third-Party Inspections: Engage independent third-party inspectors to evaluate the manufacturing processes and product quality before shipment.
These measures can significantly reduce risks associated with poor-quality products and enhance buyer confidence in their suppliers.
Conclusion: Navigating Quality Assurance in International B2B Buying
For international B2B buyers, particularly those from diverse regions like Africa, South America, the Middle East, and Europe, understanding manufacturing processes and quality assurance is vital. By focusing on the key stages of production and implementing robust quality control measures, buyers can ensure they source reliable, high-quality shopping bags that meet their specific needs and standards.
Practical Sourcing Guide: A Step-by-Step Checklist for ‘shopping bag manufacturer’
In the competitive landscape of sourcing shopping bags, particularly for international B2B buyers from regions like Africa, South America, the Middle East, and Europe, it’s essential to have a structured approach. This guide provides a step-by-step checklist to streamline your sourcing process, ensuring you make informed decisions that align with your business needs.
Step 1: Define Your Technical Specifications
Establishing clear technical specifications is the foundation of effective sourcing. Consider the materials, dimensions, and design features you require for your shopping bags.
– Material Type: Decide between options like biodegradable plastics, cotton, or recycled materials based on your sustainability goals.
– Size and Weight: Determine the sizes needed for various products to ensure functionality and convenience for your customers.
Step 2: Research and Identify Potential Suppliers
Conduct thorough market research to compile a list of potential suppliers. Utilize online directories, trade shows, and industry networks to find manufacturers that specialize in shopping bags.
– Use of Trade Platforms: Leverage platforms like Alibaba or ThomasNet to discover verified suppliers.
– Local Insights: Engage with local business chambers or trade associations in your target regions to find reputable manufacturers.
Step 3: Evaluate Potential Suppliers
Before committing, it’s crucial to vet suppliers thoroughly. Request company profiles, case studies, and references from buyers in a similar industry or region.
– Financial Stability: Assess the supplier’s financial health to ensure they can meet your long-term needs.
– Production Capacity: Confirm that the supplier can handle your order volume within your required timeframe.
Step 4: Verify Supplier Certifications
Confirm that potential suppliers hold relevant certifications that demonstrate compliance with international standards. This step is vital for ensuring product quality and ethical practices.
– ISO Standards: Look for ISO certifications related to quality management and environmental impact.
– Sustainability Certifications: If sustainability is a priority, check for certifications such as FSC (Forest Stewardship Council) for paper products or GRS (Global Recycled Standard) for recycled materials.
Step 5: Request Samples and Conduct Quality Inspections
Always request samples before placing a bulk order. This allows you to evaluate the quality and suitability of the products for your brand.
– Sample Evaluation: Test the durability, design, and overall quality of the samples against your specifications.
– Quality Control Checks: Consider hiring a third-party inspection service to assess the manufacturing process and final products before shipment.
Step 6: Negotiate Terms and Conditions
Once you’ve selected a supplier, negotiate terms that protect your interests. This includes pricing, payment terms, delivery schedules, and quality guarantees.
– Flexible Payment Options: Consider options like letters of credit to mitigate risks.
– Delivery Timelines: Establish clear delivery timelines to avoid potential supply chain disruptions.
Step 7: Establish a Long-Term Relationship
Building a strong relationship with your supplier can lead to better pricing, priority service, and a partnership that benefits both parties.
– Regular Communication: Maintain open lines of communication for ongoing feedback and improvements.
– Future Collaborations: Explore opportunities for co-developing new products or exclusive designs that cater to your market.
Following this checklist will equip B2B buyers with the necessary steps to procure shopping bags effectively, ensuring both quality and compliance with their business standards.
Comprehensive Cost and Pricing Analysis for shopping bag manufacturer Sourcing
What Are the Key Cost Components in Shopping Bag Manufacturing?
When sourcing shopping bags from manufacturers, understanding the cost structure is essential. The primary cost components include:
-
Materials: The choice of material significantly impacts the cost. Common materials include plastic, paper, and biodegradable options. Prices can vary widely based on sustainability certifications and sourcing regions.
-
Labor: Labor costs depend on the country of manufacture and local wage standards. For instance, labor costs in Africa may differ significantly from those in Europe or South America, influencing overall pricing.
-
Manufacturing Overhead: This includes costs associated with factory operations, utilities, and administrative expenses. Manufacturers in regions with higher operational costs will likely pass these costs onto buyers.
-
Tooling: Initial setup costs for molds and machinery can be substantial, especially for custom designs. Buyers should inquire about tooling fees as they can impact the initial order cost.
-
Quality Control (QC): Implementing stringent quality checks adds to the cost but ensures product reliability. It is advisable for buyers to discuss QC processes with manufacturers to understand potential implications on pricing.
-
Logistics: Shipping costs can vary based on distance, shipping method, and current freight rates. Understanding logistics costs is vital for calculating the total landed cost of shopping bags.
-
Margin: Manufacturers typically add a profit margin to cover their costs and ensure profitability. This margin can vary based on the market and product demand.
How Do Price Influencers Affect Shopping Bag Costs?
Several factors can influence the pricing of shopping bags:
-
Volume/MOQ (Minimum Order Quantity): Larger orders often lead to lower per-unit costs. Buyers should negotiate the MOQ to achieve cost efficiencies while meeting their needs.
-
Specifications and Customization: Custom designs, sizes, and features can increase costs. Buyers should weigh the benefits of customization against the potential price increase.
-
Materials: The choice of eco-friendly or premium materials can significantly affect pricing. Buyers should consider the long-term value of sustainable options, especially in markets with increasing environmental regulations.
-
Quality and Certifications: Higher-quality bags that meet specific certifications (e.g., ISO, FSC) may come at a premium but offer better performance and market appeal.
-
Supplier Factors: The reliability and reputation of suppliers can influence pricing. Established manufacturers may charge higher prices due to their track record and quality assurance.
-
Incoterms: Understanding Incoterms is critical for international buyers. These terms define the responsibilities of buyers and sellers regarding shipping, insurance, and tariffs, directly affecting total costs.
What Are Effective Negotiation Tips for International B2B Buyers?
For international buyers, especially from Africa, South America, the Middle East, and Europe, negotiation plays a crucial role in securing favorable pricing. Here are some actionable tips:
-
Research Market Rates: Understand the average pricing in your region to negotiate effectively. Awareness of local market conditions can provide leverage in discussions.
-
Discuss Total Cost of Ownership (TCO): Focus on the TCO, which includes not just the purchase price but also shipping, handling, and potential waste costs. This perspective can help justify higher upfront costs for better quality products.
-
Build Relationships: Establishing strong relationships with suppliers can lead to better pricing and service. Long-term partnerships often result in more favorable terms and conditions.
-
Be Clear About Expectations: Clearly communicate your quality standards and delivery timelines to avoid misunderstandings that can lead to unexpected costs.
-
Utilize Competitive Quotes: Gather quotes from multiple manufacturers to create competition. This can encourage suppliers to offer better pricing or terms.
Disclaimer on Pricing Information
It is essential to note that pricing information provided in this analysis is indicative and may vary based on market fluctuations, specific supplier negotiations, and changes in material costs. Always confirm current pricing directly with manufacturers to ensure accuracy and relevance to your sourcing needs.
Alternatives Analysis: Comparing shopping bag manufacturer With Other Solutions
Understanding Alternatives to Shopping Bag Manufacturing
When considering sourcing solutions for shopping bags, international B2B buyers often explore various alternatives to traditional shopping bag manufacturers. Understanding these alternatives is crucial for making informed decisions that align with sustainability goals, budget constraints, and operational efficiency. Below, we delve into a comparative analysis of shopping bag manufacturers against viable alternatives, including reusable shopping bags and biodegradable bags.
Comparison Aspect | Shopping Bag Manufacturer | Reusable Shopping Bags | Biodegradable Bags |
---|---|---|---|
Performance | High durability and custom designs | Moderate durability; can be reused multiple times | Limited durability; intended for single use or short-term |
Cost | Higher initial investment for quality | Moderate upfront cost, but savings over time | Generally lower cost per unit, but may vary by material |
Ease of Implementation | Requires supplier relationships and lead time | Easy to source; often available in bulk | Easy to source, though quality may vary |
Maintenance | Minimal maintenance; typically disposable | Requires washing and care | No maintenance; single-use |
Best Use Case | Retail environments needing custom branding | Eco-conscious retailers promoting sustainability | Events or stores requiring quick, disposable solutions |
What Are the Advantages and Disadvantages of Reusable Shopping Bags?
Reusable Shopping Bags are designed for longevity and can significantly reduce waste. They often feature branding options, making them excellent for marketing. The primary advantage is their sustainability; they can be used repeatedly, reducing the need for single-use bags. However, they require care and cleaning, and their initial cost can be higher than disposable options. They are best suited for businesses looking to enhance their eco-friendly image while encouraging customer loyalty through practical, branded solutions.
How Do Biodegradable Bags Compare to Traditional Shopping Bags?
Biodegradable Bags offer an environmentally friendly alternative to traditional plastic bags. They are designed to break down more quickly than standard plastic when exposed to natural environmental conditions. The primary advantage is their lower environmental impact, making them ideal for companies focused on sustainability. However, they typically have a shorter lifespan and may not hold up under heavy loads. Biodegradable bags work well for retailers and events where customers expect quick, disposable options without the associated environmental guilt.
Conclusion: How Can B2B Buyers Choose the Right Solution for Their Needs?
Choosing the right solution for shopping bags depends on various factors, including budget, brand image, and sustainability goals. For businesses focused on long-term customer relationships and sustainability, reusable shopping bags may be the best option. In contrast, companies needing a quick, eco-friendly solution for events may find biodegradable bags more suitable. Ultimately, B2B buyers should assess their specific needs, consider their target market, and evaluate the total cost of ownership associated with each alternative to make the most informed decision.
Essential Technical Properties and Trade Terminology for shopping bag manufacturer
What Are the Essential Technical Properties for Shopping Bag Manufacturing?
When engaging with shopping bag manufacturers, understanding the technical specifications is crucial for ensuring product quality, compliance, and cost-effectiveness. Here are some key properties to consider:
1. Material Grade
Material grade refers to the quality and type of materials used to produce shopping bags, such as polyethylene, polypropylene, or biodegradable options. For B2B buyers, selecting the appropriate material grade is essential for durability and environmental compliance. A higher grade typically indicates better strength and longevity, which translates to reduced replacement costs and enhanced brand reputation.
2. Load Capacity
Load capacity specifies the maximum weight a shopping bag can safely carry without tearing or becoming unusable. This property is vital for buyers who need to ensure that the bags meet the demands of their customers. Understanding load capacity helps in selecting bags that are not only functional but also capable of handling typical customer purchases, thereby minimizing returns and complaints.
3. Tolerance Levels
Tolerance levels indicate the acceptable variations in dimensions and weight during the manufacturing process. Tighter tolerances mean better consistency in product quality, which is important for branding and customer satisfaction. For international B2B transactions, ensuring that manufacturers adhere to specified tolerances can prevent issues related to product usability and compliance with local regulations.
4. Printability
Printability refers to the ability of the bag’s surface to accept and hold ink during the printing process. This property is significant for businesses that wish to brand their bags with logos or promotional materials. A high printability rating ensures that the final product meets aesthetic standards and contributes to effective marketing strategies.
5. Environmental Compliance
With increasing global awareness of environmental issues, compliance with regulations such as the EU’s Single-Use Plastics Directive is becoming essential. This property assesses whether the materials and manufacturing processes align with sustainability goals. B2B buyers should prioritize manufacturers who offer eco-friendly options to enhance their brand’s corporate social responsibility.
What Trade Terms Should International Buyers Know When Working with Shopping Bag Manufacturers?
Understanding industry jargon can significantly streamline communication and negotiations between B2B buyers and manufacturers. Here are some common terms:
1. OEM (Original Equipment Manufacturer)
OEM refers to a company that produces parts or products that are used in another company’s end product. For buyers, working with an OEM can mean customized shopping bags tailored to specific requirements, enhancing product differentiation in the marketplace.
2. MOQ (Minimum Order Quantity)
MOQ is the smallest quantity of a product that a supplier is willing to sell. This term is crucial for B2B buyers as it affects inventory management and cost efficiency. Understanding the MOQ helps in budgeting and determining the feasibility of product launches or promotional events.
3. RFQ (Request for Quotation)
An RFQ is a document sent by a buyer to potential suppliers requesting price quotes for specific quantities and specifications. It’s an important tool for B2B buyers to gauge market prices and select suppliers based on cost and capability, ensuring they receive competitive offers.
4. Incoterms (International Commercial Terms)
Incoterms are a series of predefined commercial terms published by the International Chamber of Commerce. They clarify the responsibilities of buyers and sellers regarding shipping, insurance, and tariffs. For international transactions, understanding Incoterms is essential to avoid disputes and ensure smooth logistics.
5. Lead Time
Lead time refers to the time taken from placing an order to the delivery of the product. It is a critical factor for B2B buyers who need to plan inventory and manage supply chains effectively. Knowing the lead time allows businesses to align their purchasing strategies with market demand.
Conclusion
For international B2B buyers, particularly from diverse regions like Africa, South America, the Middle East, and Europe, grasping these essential technical properties and trade terminologies is crucial. It not only ensures that they select the right products but also fosters effective communication with manufacturers, ultimately leading to successful partnerships.
Navigating Market Dynamics and Sourcing Trends in the shopping bag manufacturer Sector
What Are the Key Market Dynamics and Trends Influencing the Shopping Bag Manufacturer Sector?
The shopping bag manufacturer sector is undergoing significant transformations driven by global market trends and consumer preferences. A surge in e-commerce and retail activities, particularly in Africa, South America, the Middle East, and Europe, is propelling demand for innovative and sustainable shopping bags. As international B2B buyers, understanding these dynamics is crucial for making informed sourcing decisions.
One of the primary drivers is the increasing consumer awareness surrounding sustainability and environmental impact. This awareness is not only leading brands to seek eco-friendly options but also pushing manufacturers to innovate by utilizing biodegradable and recyclable materials. Additionally, digital transformation is reshaping the procurement landscape. B2B buyers are leveraging advanced technologies, such as AI and blockchain, to enhance supply chain transparency and efficiency. These technologies facilitate better tracking of materials and help in verifying the sustainability claims of manufacturers.
Emerging trends such as customization and personalization are also gaining traction. Buyers are increasingly looking for shopping bags that reflect their brand identity, which can be achieved through tailored designs and materials. Furthermore, regulatory frameworks in regions like Europe are tightening, mandating the reduction of plastic usage, thus driving the shift towards sustainable alternatives.
How Important Is Sustainability and Ethical Sourcing in the Shopping Bag Manufacturer Sector?
Sustainability and ethical sourcing have become paramount in the shopping bag manufacturing industry. The environmental impact of traditional plastic bags has spurred a movement towards more sustainable practices. This shift is particularly relevant for international B2B buyers who are seeking to align their procurement strategies with global sustainability goals.
Ethical supply chains are crucial not just for compliance with regulations but also for brand reputation. Companies that prioritize sustainability often enjoy enhanced customer loyalty and brand differentiation. Certifications such as FSC (Forest Stewardship Council), Cradle to Cradle, and Global Organic Textile Standard (GOTS) are vital indicators of a manufacturer’s commitment to sustainable practices. These certifications assure buyers that the materials used are sourced responsibly and that the production processes minimize environmental harm.
Furthermore, the use of alternative materials, such as organic cotton, jute, and recycled plastics, is becoming increasingly popular. These materials not only reduce the carbon footprint but also resonate with consumers who prefer eco-conscious brands. As B2B buyers, investing in suppliers who adhere to ethical sourcing practices can enhance your brand’s market position and contribute positively to the environment.
What Is the Historical Context of the Shopping Bag Manufacturer Sector?
The evolution of the shopping bag manufacturer sector reflects broader societal changes regarding consumer habits and environmental awareness. Initially dominated by single-use plastic bags, the industry has seen a significant shift towards reusable and sustainable alternatives over the past two decades. This transition was catalyzed by increasing environmental concerns and regulatory pressures aimed at reducing plastic waste.
In the early 2000s, many countries began to implement bans on plastic bags, prompting manufacturers to innovate and diversify their product offerings. The introduction of biodegradable materials and reusable bags became a focal point for manufacturers looking to stay relevant in a rapidly changing market. Today, the sector continues to evolve, with technological advancements and sustainability at the forefront of manufacturing processes, making it an exciting time for international B2B buyers to engage with innovative suppliers in this space.
Frequently Asked Questions (FAQs) for B2B Buyers of shopping bag manufacturer
-
How do I choose the right shopping bag manufacturer for my business needs?
Selecting the right shopping bag manufacturer involves assessing their capabilities, quality standards, and industry reputation. Start by researching manufacturers that specialize in the type of bags you require, whether reusable, biodegradable, or custom-designed. Request samples to evaluate material quality and craftsmanship. Additionally, consider their production capacity, lead times, and past client testimonials, especially from businesses similar to yours. Engaging in direct communication can also provide insights into their customer service and willingness to accommodate specific requests. -
What customization options are available when sourcing shopping bags?
Most shopping bag manufacturers offer a variety of customization options, including size, material, color, and design. You can opt for printed logos, unique patterns, or eco-friendly materials to align with your brand identity. Some manufacturers may also provide options for additional features like reinforced handles or custom closures. When discussing your project, be clear about your branding requirements and any specific functionality you need to ensure the final product meets your expectations. -
What is the minimum order quantity (MOQ) for shopping bags from manufacturers?
Minimum order quantities (MOQs) can vary significantly among manufacturers and depend on factors such as the type of bag, material, and customization complexity. Typically, MOQs can range from 500 to several thousand units. It’s advisable to communicate your needs upfront and negotiate terms if you are a smaller business or seeking a one-time order. Some manufacturers may be open to lower MOQs for trial orders or if you agree to a longer lead time. -
What payment terms should I expect when working with a shopping bag manufacturer?
Payment terms can differ based on the manufacturer’s policies and your negotiation. Common practices include a deposit (usually 30-50%) upfront, with the balance paid upon completion or prior to shipping. Additionally, some manufacturers might offer net payment terms, allowing you to pay within a specified period after receiving goods. Ensure you have a clear understanding of these terms before proceeding, and consider using secure payment methods to protect your transaction. -
How can I ensure quality assurance in my shopping bag orders?
To ensure quality assurance, it’s essential to establish clear specifications and standards before production. Consider requesting a pre-production sample to verify that the manufacturer understands your requirements. Additionally, you may want to conduct periodic quality inspections during the manufacturing process, either by hiring a third-party quality control service or sending a representative. This proactive approach can help identify issues early, reducing the risk of receiving subpar products. -
What are the logistics considerations when importing shopping bags?
Logistics play a critical role in the successful importation of shopping bags. Key factors include understanding shipping options (air vs. sea), customs regulations, and tariffs that may apply to your order. It’s advisable to work with a freight forwarder who can help navigate these complexities and ensure compliance with local import laws. Additionally, consider the lead times involved in shipping and factor these into your inventory management to avoid stockouts. -
How do I vet a shopping bag manufacturer to avoid potential risks?
Vetting a manufacturer involves several steps: check their business credentials, certifications (such as ISO standards), and industry experience. Request references and follow up with past clients to understand their experiences. It’s also beneficial to visit the manufacturing facility, if possible, to assess their operational practices and quality control measures. Engaging in clear communication throughout the vetting process can also help gauge their professionalism and responsiveness. -
What sustainable options should I consider when sourcing shopping bags?
As sustainability becomes increasingly important, consider sourcing from manufacturers that offer eco-friendly materials such as recycled plastics, organic cotton, or biodegradable options. Inquire about their production processes to ensure they adhere to environmentally responsible practices, such as reducing waste and utilizing renewable energy sources. Additionally, explore manufacturers who are committed to social responsibility, as this can enhance your brand’s reputation while aligning with consumer preferences for sustainable products.
Important Disclaimer & Terms of Use
⚠️ Important Disclaimer
The information provided in this guide, including content regarding manufacturers, technical specifications, and market analysis, is for informational and educational purposes only. It does not constitute professional procurement advice, financial advice, or legal advice.
While we have made every effort to ensure the accuracy and timeliness of the information, we are not responsible for any errors, omissions, or outdated information. Market conditions, company details, and technical standards are subject to change.
B2B buyers must conduct their own independent and thorough due diligence before making any purchasing decisions. This includes contacting suppliers directly, verifying certifications, requesting samples, and seeking professional consultation. The risk of relying on any information in this guide is borne solely by the reader.
Strategic Sourcing Conclusion and Outlook for shopping bag manufacturer
How Can Strategic Sourcing Benefit International B2B Buyers in the Shopping Bag Industry?
In conclusion, the strategic sourcing of shopping bags is not merely a procurement function but a critical driver of business success for international buyers. By prioritizing sustainable materials and reliable suppliers, businesses can enhance their brand image while meeting the growing consumer demand for environmentally-friendly products. Moreover, understanding regional market trends, particularly in Africa, South America, the Middle East, and Europe, allows B2B buyers to tailor their offerings effectively, ensuring alignment with local preferences and compliance with regulations.
What Should B2B Buyers Focus on Moving Forward?
As you navigate the complexities of sourcing shopping bags, focus on building strong partnerships with manufacturers who share your commitment to sustainability and quality. Leverage data analytics to assess supplier performance and market trends, optimizing your procurement strategies for better cost-effectiveness and reliability.
What’s Next for Your Sourcing Strategy?
Looking ahead, the future of shopping bag manufacturing will be shaped by innovation and consumer preferences. Embrace these changes by staying informed about advancements in materials and production techniques. By doing so, you position your business to not only meet current demands but also to anticipate future market shifts. Engage with suppliers, attend industry events, and participate in forums to expand your network and gain insights that will empower your strategic sourcing decisions.