Cut Costs with Tissue Paper China: The Ultimate Sourcing Guide (2025)
Introduction: Navigating the Global Market for tissue paper china
Navigating the global market for tissue paper from China presents unique challenges for international B2B buyers, particularly those from Africa, South America, the Middle East, and Europe. With varying quality standards, diverse applications, and complex supply chains, sourcing reliable tissue paper can be daunting. This guide is designed to demystify the process, equipping buyers with essential insights into the types of tissue paper available, their specific applications, and strategies for effective supplier vetting.
Understanding the nuances of the tissue paper market is crucial for making informed purchasing decisions. From identifying sustainable sourcing options to evaluating cost-effectiveness, this comprehensive resource will serve as your roadmap. We will explore key factors that influence pricing, the importance of quality certifications, and how to assess supplier reliability in a competitive landscape.
By leveraging the knowledge within this guide, B2B buyers will be empowered to navigate their sourcing challenges with confidence. Whether you’re in Mexico, Brazil, or any other region, this guide aims to enhance your procurement strategies, ensuring that you can secure high-quality tissue paper that meets your business needs while fostering productive international partnerships.
Understanding tissue paper china Types and Variations
Type Name | Key Distinguishing Features | Primary B2B Applications | Brief Pros & Cons for Buyers |
---|---|---|---|
Standard Tissue Paper | Lightweight, smooth texture, available in various colors | Packaging, gift wrapping, stationery | Pros: Cost-effective, versatile. Cons: Limited durability. |
Crepe Tissue Paper | Crinkled texture, thicker than standard tissue | Crafts, decorations, event planning | Pros: Unique appearance, excellent for crafting. Cons: Higher cost, less suitable for formal applications. |
Colored Tissue Paper | Vibrant colors, often acid-free, available in sheets or rolls | Retail packaging, promotional materials | Pros: Eye-catching, enhances branding. Cons: Color fading over time. |
Eco-Friendly Tissue Paper | Made from recycled materials, biodegradable | Sustainable packaging, eco-conscious brands | Pros: Environmentally friendly, aligns with sustainability goals. Cons: May have higher costs, limited color options. |
Printed Tissue Paper | Custom designs or logos, available in various patterns | Branding, special events, retail displays | Pros: Effective marketing tool, enhances product presentation. Cons: Longer lead times for custom orders. |
What are the characteristics of Standard Tissue Paper and its B2B purchasing considerations?
Standard tissue paper is characterized by its lightweight and smooth texture, making it an excellent choice for various applications such as packaging, gift wrapping, and stationery. It is typically available in a wide range of colors, which allows for customization based on brand identity. When purchasing, B2B buyers should consider factors such as the paper’s weight, color options, and cost-effectiveness, ensuring it meets their specific needs without compromising on quality.
How does Crepe Tissue Paper differ from other types for B2B applications?
Crepe tissue paper features a unique crinkled texture and is thicker than standard tissue, providing a more durable option for crafts and decorative purposes. Its distinct appearance makes it ideal for event planning and creative projects. B2B buyers should evaluate the thickness and texture to ensure it aligns with their intended use, as well as consider the price point, which may be higher than standard tissue due to its specialized nature.
What advantages does Colored Tissue Paper offer for branding?
Colored tissue paper is known for its vibrant hues and acid-free properties, making it suitable for retail packaging and promotional materials. It can significantly enhance the visual appeal of products and is a favored choice for businesses looking to create memorable unboxing experiences. Buyers should assess the color options available and consider how the tissue paper will hold up over time, particularly regarding color fading, to maintain brand integrity.
Why should B2B buyers consider Eco-Friendly Tissue Paper?
Eco-friendly tissue paper is made from recycled materials and is biodegradable, aligning with the growing demand for sustainable products. It is particularly suitable for businesses that prioritize sustainability in their operations. Buyers should weigh the benefits of supporting eco-friendly initiatives against potentially higher costs and the limited color options that may be available compared to traditional tissue papers.
How can Printed Tissue Paper enhance marketing efforts for businesses?
Printed tissue paper allows for custom designs, logos, and patterns, making it an effective marketing tool for branding and product presentation. It is often used in retail displays and special events to create a cohesive brand experience. B2B buyers should consider the lead times for custom orders and ensure that the quality of printing meets their standards, as this can impact their overall marketing strategy.
Related Video: How To Make Round Tissue Paper Flower – DIY Paper Craft
Key Industrial Applications of tissue paper china
Industry/Sector | Specific Application of tissue paper china | Value/Benefit for the Business | Key Sourcing Considerations for this Application |
---|---|---|---|
Healthcare | Medical wipes and surgical drapes | Ensures hygiene and reduces infection risks | Compliance with health regulations and quality standards |
Food Service | Disposable napkins and table covers | Enhances customer experience and cleanliness | Sourcing biodegradable options and bulk purchasing |
Retail | Packaging and wrapping materials | Protects products and improves presentation | Customization options and printing capabilities |
Personal Care | Facial tissues and toilet paper | Offers comfort and promotes brand loyalty | Softness, absorbency, and sustainability certifications |
Hospitality | Guest room amenities (tissue products) | Improves guest satisfaction and brand reputation | Quality assurance and supply chain reliability |
How is Tissue Paper Used in Healthcare Settings?
In the healthcare sector, tissue paper from China is primarily used for medical wipes and surgical drapes. These products are essential for maintaining hygiene and preventing infections in clinical environments. International B2B buyers should prioritize sourcing tissue paper that meets stringent health regulations, ensuring compliance with local and international standards. This includes verifying certifications for quality and safety, as well as assessing the absorbency and durability of the materials used.
What Role Does Tissue Paper Play in Food Service?
In the food service industry, tissue paper is commonly utilized for disposable napkins and table covers. These products not only enhance the dining experience but also contribute to cleanliness and sanitation in restaurants and cafes. B2B buyers should consider sourcing biodegradable options to align with sustainability practices, which are increasingly important in markets across Africa, South America, the Middle East, and Europe. Bulk purchasing can also lead to cost savings while ensuring consistent supply.
How is Tissue Paper Beneficial for Retail Packaging?
In retail, tissue paper serves as an effective packaging and wrapping material. It protects products during transit and enhances their visual appeal, which is crucial for attracting customers. Buyers in this sector should explore customization options, including printed designs that align with their brand identity. Additionally, understanding the supply chain dynamics is vital to ensure timely delivery and maintain inventory levels.
Why is Tissue Paper Important in Personal Care Products?
Tissue paper plays a significant role in personal care products, particularly in the production of facial tissues and toilet paper. These items are designed for comfort and convenience, fostering brand loyalty among consumers. International buyers should focus on sourcing tissue that offers superior softness and absorbency, as well as certifications for sustainability. This is especially relevant in markets where eco-friendly products are gaining traction.
How Does Tissue Paper Enhance Guest Experiences in Hospitality?
In the hospitality sector, tissue paper products are essential for guest room amenities, contributing to overall guest satisfaction. High-quality tissue products can elevate the perception of a hotel or resort, enhancing its reputation. Buyers should ensure that the sourced tissue products meet high standards for quality and reliability, as they directly impact the guest experience. Additionally, evaluating the supplier’s ability to provide consistent quality and timely deliveries is crucial for maintaining service excellence.
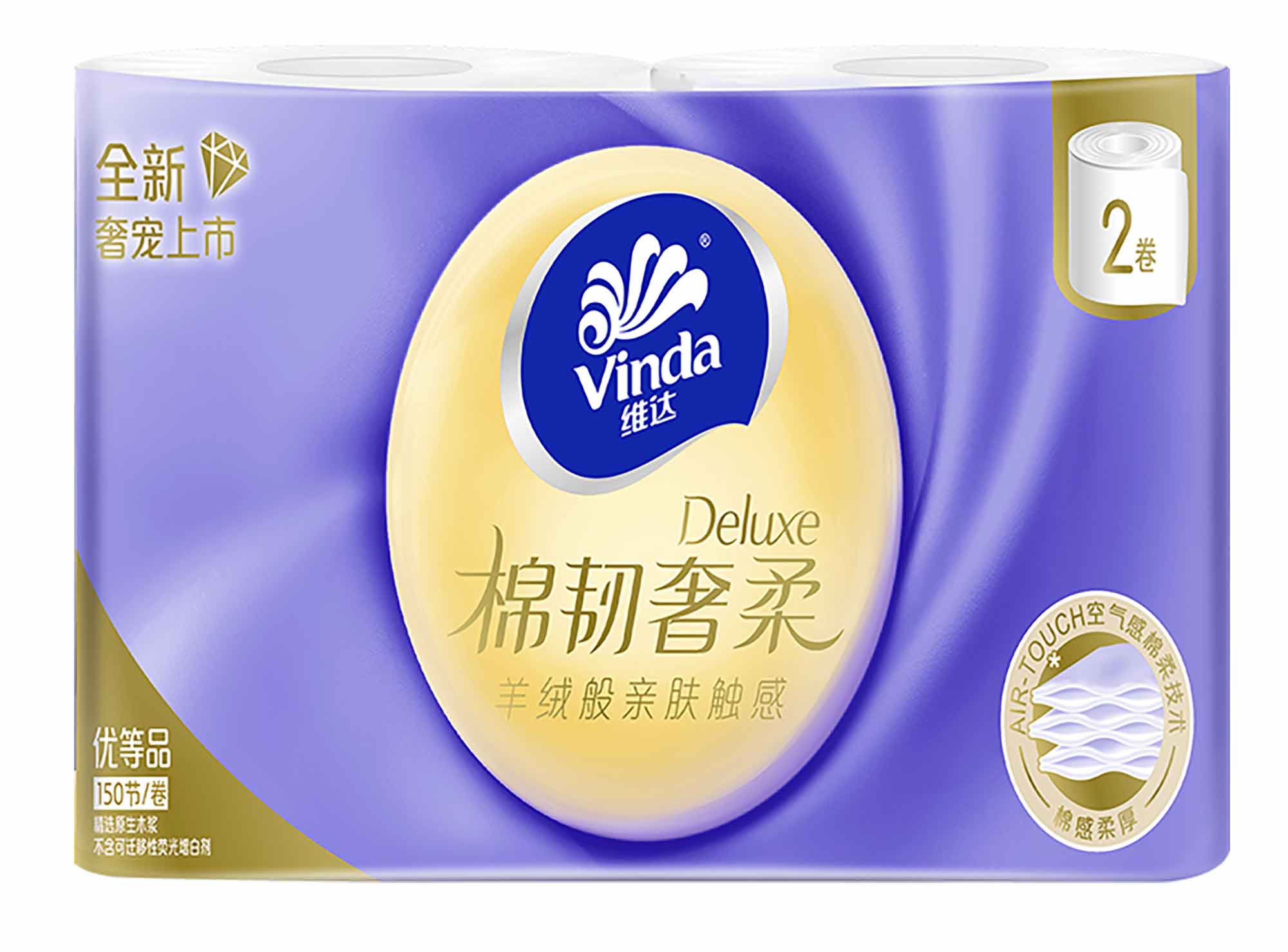
A stock image related to tissue paper china.
Related Video: How Toilet Paper Is Made in Factory – Toilet Tissue Paper Making Machine
3 Common User Pain Points for ’tissue paper china’ & Their Solutions
Scenario 1: Navigating Quality Control Issues in Tissue Paper Sourcing
The Problem: One of the most pressing challenges faced by B2B buyers of tissue paper from China is ensuring consistent quality. Many buyers have encountered situations where the product delivered does not meet the specifications outlined in contracts. This discrepancy can stem from varying manufacturing processes, lack of standardized quality checks, or differences in raw material quality. For businesses in Africa and South America, where consumer expectations for quality are rising, receiving subpar products can lead to customer dissatisfaction and increased costs due to returns and reorders.
The Solution: To mitigate quality control issues, B2B buyers should implement a thorough vetting process when selecting suppliers. This includes conducting factory audits to assess production capabilities and quality assurance protocols. Additionally, establishing clear and detailed product specifications is crucial. These specifications should include not only material quality but also the desired weight, absorbency, and packaging standards. Utilizing third-party quality control services can further enhance reliability, ensuring that products are inspected before shipment. Regular communication with suppliers about quality expectations can foster a collaborative relationship that prioritizes quality.
Scenario 2: Overcoming Import and Compliance Barriers
The Problem: Import regulations and compliance standards can pose significant hurdles for B2B buyers looking to source tissue paper from China. Different countries in Europe and the Middle East have distinct regulations regarding the importation of paper products, including environmental certifications and packaging requirements. Failure to comply with these regulations can result in costly delays, fines, or even the rejection of shipments at customs.
The Solution: Buyers should conduct comprehensive research on the import regulations specific to their countries. Collaborating with local trade experts or import consultants can provide valuable insights into necessary certifications and documentation. It’s advisable to source tissue paper from suppliers who are already compliant with international standards, such as FSC (Forest Stewardship Council) or ISO certifications. Additionally, establishing a clear line of communication with freight forwarders and customs brokers can ensure that all paperwork is in order before shipments arrive, reducing the risk of delays or penalties.
Scenario 3: Managing Fluctuations in Pricing and Supply Chain Disruptions
The Problem: B2B buyers often face unpredictable pricing and supply chain disruptions when sourcing tissue paper from China. Factors such as fluctuating raw material costs, shipping delays, and geopolitical tensions can affect pricing stability and product availability. For businesses in regions like Europe and Africa, where the demand for tissue paper is increasing, these fluctuations can complicate budgeting and inventory management.
The Solution: To navigate these challenges, it’s essential for buyers to build flexible supply chain strategies. Establishing long-term partnerships with multiple suppliers can provide alternatives in case one supplier faces disruptions. Buyers should also consider negotiating fixed pricing agreements to hedge against market volatility. Implementing just-in-time inventory management can help maintain lower stock levels while meeting demand efficiently. Additionally, keeping abreast of market trends and economic indicators can help buyers anticipate changes in pricing and make informed purchasing decisions. Regularly reviewing supplier performance and market conditions will enable businesses to adapt quickly to any shifts in the supply landscape.
Strategic Material Selection Guide for tissue paper china
What Are the Common Materials Used in Tissue Paper Production?
When selecting materials for tissue paper production, particularly in the context of sourcing from China, international B2B buyers must consider various factors that impact product performance and compliance. Below are analyses of four common materials used in tissue paper manufacturing.
What Are the Key Properties of Virgin Pulp in Tissue Paper?
Virgin Pulp is the primary raw material for high-quality tissue paper. This material is derived from freshly harvested wood fibers, ensuring superior softness and absorbency.
- Key Properties: Virgin pulp has excellent tensile strength and absorbency, making it ideal for products requiring high performance under pressure. It is also biodegradable and environmentally friendly.
- Pros & Cons: The primary advantage of virgin pulp is its high quality, which translates into a premium product. However, it is more expensive than recycled alternatives and may involve complex supply chains. Furthermore, sourcing virgin pulp can raise sustainability concerns among environmentally conscious buyers.
- Impact on Application: Virgin pulp is particularly suitable for luxury tissue products such as facial tissues and high-end toilet paper, where softness is paramount.
- Considerations for International Buyers: Buyers from regions such as Africa, South America, and Europe should be aware of compliance with sustainability certifications like FSC (Forest Stewardship Council). Additionally, adherence to local standards such as EN (European Norms) is crucial.
How Does Recycled Pulp Compare in Tissue Paper Manufacturing?
Recycled Pulp is made from post-consumer paper waste, making it a more sustainable option.
- Key Properties: Recycled pulp offers reasonable absorbency and strength but may not match the softness of virgin pulp. It is also less energy-intensive to produce.
- Pros & Cons: The significant advantage of recycled pulp is its lower cost and reduced environmental impact. However, the quality can vary, and it may not be suitable for all applications, particularly those requiring a premium feel.
- Impact on Application: Recycled pulp is often used in everyday products like napkins and standard toilet paper.
- Considerations for International Buyers: Buyers should ensure that recycled pulp meets local recycling standards, such as ASTM D6866 in the United States or ISO 14021 in Europe.
What Role Does Bamboo Pulp Play in Tissue Paper Production?
Bamboo Pulp is gaining popularity due to its rapid growth and renewability.
- Key Properties: Bamboo pulp is naturally antibacterial and has high absorbency. It also boasts a unique softness that can rival virgin pulp.
- Pros & Cons: The main advantage of bamboo pulp is its sustainability, as bamboo grows quickly and requires less water. However, it can be more expensive to process and may not be as readily available as traditional wood pulp.
- Impact on Application: Bamboo pulp is suitable for eco-friendly tissue products and is increasingly favored in markets focused on sustainability.
- Considerations for International Buyers: Buyers should verify the sourcing of bamboo pulp to ensure compliance with local environmental regulations and standards, particularly in Europe where eco-labels are important.
What Are the Benefits of Non-Woven Fabrics in Tissue Paper Products?
Non-Woven Fabrics, often made from synthetic fibers, are sometimes used in tissue paper products for specific applications.
- Key Properties: Non-woven fabrics are known for their durability and strength, making them suitable for heavy-duty applications.
- Pros & Cons: The advantage of non-woven fabrics is their high durability, which can extend the life of the product. However, they are less biodegradable than traditional paper products and may not appeal to eco-conscious consumers.
- Impact on Application: Non-woven materials are typically used in industrial wipes and cleaning products where strength is essential.
- Considerations for International Buyers: Buyers should consider the environmental impact of non-woven materials and ensure that they comply with relevant regulations, such as REACH in Europe.
Summary Table of Material Selection for Tissue Paper China
Material | Typical Use Case for tissue paper china | Key Advantage | Key Disadvantage/Limitation | Relative Cost (Low/Med/High) |
---|---|---|---|---|
Virgin Pulp | High-end facial tissues and toilet paper | Superior softness and absorbency | Higher cost and sustainability concerns | High |
Recycled Pulp | Standard toilet paper and napkins | Lower cost and eco-friendly | Variable quality and lesser softness | Medium |
Bamboo Pulp | Eco-friendly tissue products | Sustainable and naturally antibacterial | Higher processing costs | High |
Non-Woven Fabrics | Industrial wipes and cleaning products | High durability | Less biodegradable and eco-friendly | Medium |
This structured approach to material selection will help international B2B buyers make informed decisions that align with their product requirements and sustainability goals.
In-depth Look: Manufacturing Processes and Quality Assurance for tissue paper china
The manufacturing of tissue paper in China involves a series of intricate processes and stringent quality assurance measures that are critical for international B2B buyers. Understanding these can help buyers from Africa, South America, the Middle East, and Europe make informed decisions when sourcing tissue paper products.
What are the Main Stages in the Manufacturing Process of Tissue Paper?
1. Material Preparation
The first stage of tissue paper production is material preparation, primarily involving the selection and processing of raw materials. The most common raw materials include wood pulp, recycled paper, and other cellulose fibers. Suppliers typically source these materials from sustainable forests or recycling plants.
During this stage, the raw materials undergo mechanical and chemical treatments to ensure they are free from impurities. This includes processes such as:
- Defibrillation: Breaking down the raw fibers to achieve a uniform consistency.
- Bleaching: Using environmentally friendly bleaching agents to achieve the desired whiteness without compromising the paper’s quality.
2. Forming
Once prepared, the fibers are mixed with water to create a slurry. This slurry is then spread onto a moving mesh screen in a process called sheet formation. Key techniques involved include:
- Wet Pressing: The water is removed from the slurry, and the fibers are pressed together to form a continuous sheet.
- Drying: The wet sheets are passed through heated rollers to eliminate remaining moisture, resulting in a dry sheet of tissue paper.
3. Assembly
After forming, the sheets are rolled into large reels. This stage may also involve converting the reels into finished products such as toilet paper, paper towels, and facial tissues. The assembly process includes:
- Cutting: The large reels are cut into smaller sheets or rolls based on customer specifications.
- Packaging: Finished products are packaged for shipping, ensuring they are protected from moisture and contamination.
4. Finishing
The final stage involves additional treatments to enhance the quality of the tissue paper. This may include:
- Embossing: Adding texture to the paper for improved absorbency and aesthetic appeal.
- Coating: Applying a light coating to enhance softness or strength.
How is Quality Assurance Implemented in Tissue Paper Manufacturing?
Quality assurance (QA) in tissue paper manufacturing is essential to ensure that the products meet international standards and customer expectations. The following aspects are vital for a robust QA process:
Relevant International Standards for Tissue Paper Quality
International standards such as ISO 9001 are crucial in the tissue paper industry. This standard focuses on quality management systems and ensures that manufacturers consistently produce products that meet customer and regulatory requirements. Additionally, industry-specific certifications like CE (Conformité Européenne) and API (American Petroleum Institute) may apply depending on the intended use of the tissue products.
What are the Key Quality Control Checkpoints?
Quality control checkpoints are strategically placed throughout the manufacturing process to maintain high standards. These include:
- Incoming Quality Control (IQC): Inspecting raw materials upon arrival to ensure they meet specified quality criteria.
- In-Process Quality Control (IPQC): Conducting checks during the manufacturing stages to identify any deviations from quality standards.
- Final Quality Control (FQC): Performing comprehensive inspections on finished products before packaging to ensure they meet all specifications.
Common Testing Methods Used in Tissue Paper Quality Assurance
To verify the quality of tissue paper, various testing methods are employed, including:
- Physical Testing: Assessing properties such as thickness, tensile strength, and absorbency.
- Chemical Testing: Checking for the presence of harmful substances and ensuring compliance with health and safety standards.
- Performance Testing: Evaluating how the product performs in real-world applications, such as absorbency tests for paper towels.
How Can B2B Buyers Verify Supplier Quality Control?
For B2B buyers, especially those from regions like Africa, South America, the Middle East, and Europe, verifying a supplier’s quality control processes is crucial. Here are some actionable steps:
Conduct Supplier Audits
Regular audits of suppliers can provide insights into their manufacturing and quality assurance practices. During these audits, buyers should assess:
- Compliance with international standards.
- The effectiveness of quality control checkpoints.
- The reliability of testing methods used.
Request Quality Assurance Reports
Buyers should request detailed quality assurance reports from suppliers. These reports should include information on:
- Results from IQC, IPQC, and FQC.
- Any certifications obtained (e.g., ISO, CE).
- Historical data on product quality and any corrective actions taken in the past.
Engage Third-Party Inspectors
Utilizing third-party inspection services can provide an unbiased evaluation of the supplier’s quality control processes. These inspectors can conduct thorough assessments and provide reports on compliance with international standards and product quality.
What are the Quality Control Nuances for International B2B Buyers?
B2B buyers must be aware of specific nuances in quality control when sourcing tissue paper internationally. These include:
- Understanding Regional Standards: Different regions may have varying standards and regulations. For instance, products sold in the EU must comply with CE marking, while products in the U.S. may need to adhere to specific FDA regulations.
- Cultural Differences in Quality Expectations: Buyers should consider cultural differences in quality perception and consumer expectations. Tailoring products to meet local preferences can enhance market acceptance.
- Logistical Considerations: Understanding the logistics of transporting goods from China to their respective markets is crucial, as delays or mishandling can affect product quality.
By understanding the manufacturing processes and quality assurance measures in place, international B2B buyers can make informed decisions and establish successful partnerships with tissue paper suppliers in China.
Practical Sourcing Guide: A Step-by-Step Checklist for ’tissue paper china’
In the competitive landscape of global sourcing, particularly for products like tissue paper from China, B2B buyers must approach procurement strategically. This practical checklist serves as a guide to help international buyers navigate the complexities of sourcing tissue paper, ensuring they make informed decisions while minimizing risks.
Step 1: Define Your Technical Specifications
Establishing clear technical specifications is essential for ensuring that the tissue paper meets your business needs. Consider factors such as thickness, absorbency, and any special features like eco-friendliness or fragrance. Specificity in your requirements will also help suppliers understand your needs better, allowing for accurate quotes and timely delivery.
Step 2: Research and Identify Potential Suppliers
Conduct thorough research to identify reputable suppliers in China. Utilize platforms like Alibaba, Made-in-China, and Global Sources to find manufacturers with strong ratings and reviews. Pay attention to suppliers that specialize in tissue paper, as they are more likely to meet your specific requirements.
Step 3: Evaluate Potential Suppliers
Before committing, it’s crucial to vet suppliers thoroughly. Request company profiles, case studies, and references from buyers in a similar industry or region. This due diligence will help you assess their production capabilities and reliability.
– Check for certifications: Look for ISO certifications or industry-specific standards that ensure quality.
– Inquire about production capacity: Ensure they can meet your order volume and delivery timelines.
Step 4: Request Samples for Quality Assessment
Always request samples before finalizing any order. This allows you to physically assess the quality of the tissue paper, ensuring it meets your specifications. When evaluating samples, consider aspects such as softness, durability, and overall appearance.
– Test different grades: If possible, compare different grades of tissue paper to find the best fit for your needs.
Step 5: Negotiate Terms and Pricing
Once you have selected a few potential suppliers, initiate negotiations on pricing and terms. Be transparent about your budget and expectations while seeking a win-win arrangement.
– Discuss payment terms: Opt for secure payment methods that offer protection, such as escrow services.
– Clarify shipping and logistics: Understand who bears the shipping costs and the expected delivery timeline.
Step 6: Verify Compliance with Regulations
Ensure that the tissue paper complies with regulations in your target market. Different regions may have specific requirements regarding materials and safety standards.
– Request documentation: Ask for proof of compliance, such as certificates that confirm the product is free from harmful substances.
Step 7: Establish a Communication Plan
Effective communication is vital for successful sourcing. Set up a clear communication plan with your selected supplier, outlining how and when you will exchange information.
– Regular updates: Schedule regular check-ins to discuss production progress, potential issues, and delivery schedules.
By following this checklist, B2B buyers can streamline their sourcing process for tissue paper from China, ensuring they partner with reliable suppliers who can deliver quality products that meet their specifications.
Comprehensive Cost and Pricing Analysis for tissue paper china Sourcing
What Are the Key Cost Components in Tissue Paper Sourcing from China?
When sourcing tissue paper from China, understanding the cost structure is crucial for international buyers. The primary cost components include:
-
Materials: The quality of raw materials significantly influences the overall cost. High-quality pulp or recycled materials can vary in price, impacting the final product’s quality and price point.
-
Labor: Labor costs in China are relatively low compared to other regions. However, the skill level of workers, especially in quality control (QC), can affect production efficiency and product quality.
-
Manufacturing Overhead: This includes costs associated with factory operations, such as utilities, equipment depreciation, and maintenance. Efficient factories often have lower overhead costs, which can lead to more competitive pricing.
-
Tooling: The cost of molds and machinery used for producing specific designs or sizes of tissue paper can vary. Custom tooling may increase initial costs but can lead to lower per-unit prices at higher volumes.
-
Quality Control (QC): Ensuring that products meet quality standards requires investment in inspection and testing processes. This is a critical area that can affect both costs and customer satisfaction.
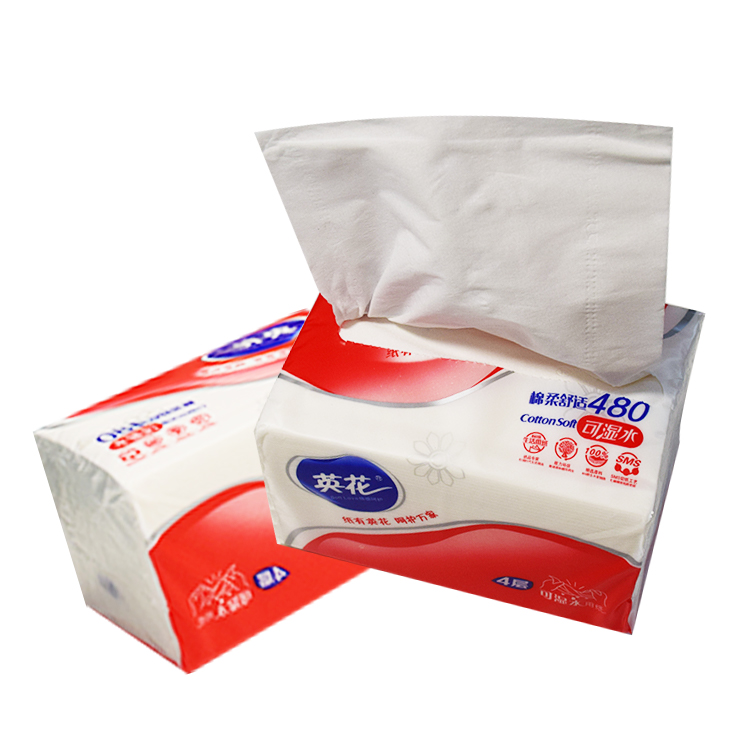
A stock image related to tissue paper china.
-
Logistics: Shipping costs, including freight, insurance, and customs duties, can add significant expenses to the total sourcing cost. The choice of Incoterms will also influence these costs.
-
Margin: Suppliers typically include a profit margin in their pricing. Understanding the market standards for margins can help buyers negotiate better deals.
How Do Price Influencers Affect Tissue Paper Costs?
Several factors can influence the final price of tissue paper sourced from China:
-
Volume and Minimum Order Quantity (MOQ): Larger orders often lead to lower prices per unit due to economies of scale. Buyers should negotiate MOQs that suit their purchasing needs while optimizing cost efficiency.
-
Specifications and Customization: Customized products may incur additional costs due to tooling and production adjustments. Buyers should clearly define their requirements to avoid unexpected charges.
-
Materials and Quality Certifications: Premium materials and certifications (like FSC certification) can increase costs. Buyers must balance quality needs with budget constraints.
-
Supplier Factors: The reputation and reliability of suppliers can affect pricing. Established suppliers with a track record may charge more but can provide better quality assurance and service.
-
Incoterms: The chosen Incoterms (e.g., FOB, CIF) significantly influence shipping costs and responsibilities, impacting the total cost of ownership.
What Buyer Tips Can Enhance Cost Efficiency in Tissue Paper Sourcing?
To maximize cost efficiency when sourcing tissue paper from China, consider the following strategies:
-
Negotiation: Engage in thorough negotiations with suppliers. Discuss not only price but also payment terms and delivery schedules to achieve a more favorable deal.
-
Total Cost of Ownership (TCO): Assess the total cost, including purchase price, shipping, tariffs, and any additional costs related to quality control and returns. This holistic view will help in making informed purchasing decisions.
-
Pricing Nuances for International Buyers: Be aware of currency fluctuations and international trade tariffs that can affect costs. Establishing contracts in stable currencies can mitigate some risks.
-
Supplier Relationships: Building long-term relationships with suppliers can lead to better pricing and preferential treatment over time. Regular communication and feedback can enhance collaboration.
By understanding the cost components, price influencers, and employing strategic negotiation techniques, international buyers can effectively navigate the complexities of sourcing tissue paper from China, ensuring they achieve the best value for their investments.
Alternatives Analysis: Comparing tissue paper china With Other Solutions
Understanding Alternatives to Tissue Paper China
In the competitive landscape of tissue products, it is essential for international B2B buyers to evaluate alternatives to “tissue paper china.” Various solutions can meet similar needs while offering distinct advantages or disadvantages. This section provides a comparative analysis of “tissue paper china” against two viable alternatives: recycled paper products and bamboo tissue paper.
Comparison Table
Comparison Aspect | Tissue Paper China | Recycled Paper Products | Bamboo Tissue Paper |
---|---|---|---|
Performance | High absorbency and softness | Moderate absorbency; may vary by brand | High absorbency and strength |
Cost | Moderate to high | Generally lower | Higher than recycled but competitive with virgin paper |
Ease of Implementation | Readily available | Widely available, some brands may require special sourcing | Requires reliable suppliers |
Maintenance | Low maintenance | Low maintenance | Low maintenance |
Best Use Case | Hospitality, high-end retail | General-purpose use, eco-conscious consumers | Eco-friendly markets, premium segments |
What Are the Advantages and Disadvantages of Recycled Paper Products?
Recycled paper products are an environmentally friendly option that repurposes existing materials. They generally come at a lower cost compared to tissue paper china, making them attractive for budget-conscious buyers. However, the performance can vary significantly based on the brand and quality, which may lead to inconsistency in absorbency and texture. Additionally, while they are easier to source, buyers may need to ensure that they are purchasing from reputable manufacturers to guarantee quality.
How Does Bamboo Tissue Paper Compare?
Bamboo tissue paper is gaining popularity due to its sustainable sourcing and impressive performance. It offers high absorbency and strength, making it suitable for premium markets. While the cost of bamboo products tends to be higher than that of recycled paper, it often competes closely with tissue paper china. Buyers interested in eco-friendly solutions will find bamboo tissue appealing. The main drawback is sourcing; it may not be as readily available in all markets, which can complicate procurement.
Conclusion: How Can B2B Buyers Choose the Right Solution?
When choosing between tissue paper china and its alternatives, B2B buyers should consider factors such as performance, cost, and the specific needs of their business. For companies focused on high-end applications, tissue paper china may be the best fit due to its superior softness and absorbency. Conversely, businesses looking to promote sustainability without sacrificing quality might lean toward bamboo tissue paper. Finally, those operating on a tighter budget or targeting a general audience may find recycled paper products to be the most cost-effective solution. Ultimately, understanding the unique strengths and weaknesses of each option will empower buyers to make informed decisions tailored to their operational goals.
Essential Technical Properties and Trade Terminology for tissue paper china
What Are the Key Technical Properties of Tissue Paper from China?
Understanding the technical specifications of tissue paper is essential for B2B buyers to ensure they select the right product for their needs. Here are some critical properties to consider:
1. Material Grade
Material grade refers to the quality of the raw materials used in tissue paper production. Common grades include virgin pulp, recycled pulp, and mixed pulp. Virgin pulp is often preferred for its softness and absorbency, making it ideal for high-end products. Buyers should assess their target market to determine the appropriate material grade that balances quality and cost-effectiveness.
2. Basis Weight
Basis weight is the weight of the paper measured in grams per square meter (gsm). It directly impacts the thickness, strength, and absorbency of the tissue paper. For example, a higher basis weight indicates a thicker and more durable product. B2B buyers should evaluate their product requirements and choose a basis weight that meets the desired functionality, such as softness for facial tissues or strength for industrial wipes.
3. Tolerance Levels
Tolerance levels indicate the acceptable variation in the dimensions and weight of the tissue paper. For instance, if a product specification states a basis weight of 18 gsm with a tolerance of ±1 gsm, the actual weight can vary between 17 and 19 gsm. Understanding tolerances is crucial for maintaining product consistency and quality, which can influence customer satisfaction and brand reputation.
4. Absorbency Rate
Absorbency rate measures how much liquid a tissue paper can hold before it begins to leak. This property is particularly important for products like napkins or towels, where quick absorption is essential. B2B buyers should assess absorbency rates based on their end-use applications to ensure they meet customer expectations.
5. Softness
Softness refers to the tactile quality of the tissue paper, which affects user experience. Softer tissue is often more desirable for consumer products like toilet paper and facial tissues. Various manufacturing processes, such as embossing and the addition of softening agents, can enhance softness. Buyers should consider the target demographic and product positioning when evaluating softness.
Which Trade Terminology Should B2B Buyers Know?
Familiarity with industry jargon can help B2B buyers navigate negotiations and contracts more effectively. Here are some key terms:
1. OEM (Original Equipment Manufacturer)
OEM refers to companies that produce goods that are branded by another company. In the context of tissue paper, an OEM may manufacture products for retailers under private labels. Understanding OEM agreements is vital for buyers looking to collaborate with manufacturers for customized products.
2. MOQ (Minimum Order Quantity)
MOQ indicates the smallest number of units a supplier is willing to sell. This term is critical for budgeting and inventory planning. Buyers should negotiate MOQs that align with their purchasing capacity and market demand to avoid excess stock or under-supply issues.
3. RFQ (Request for Quotation)
An RFQ is a formal process where buyers request pricing and terms from suppliers. It typically includes detailed specifications about the products required. Submitting RFQs helps buyers compare offers and negotiate better deals, ensuring they receive competitive pricing for tissue paper products.
4. Incoterms (International Commercial Terms)
Incoterms are a set of rules that define the responsibilities of buyers and sellers in international trade. They clarify aspects such as shipping, insurance, and duties. Understanding Incoterms is essential for buyers to assess the risks and costs associated with importing tissue paper from China.
5. Lead Time
Lead time is the duration between placing an order and receiving the goods. It includes manufacturing time and shipping duration. For B2B buyers, understanding lead times helps in inventory management and ensures timely product availability in the market.
By grasping these essential technical properties and trade terms, B2B buyers can make informed decisions when sourcing tissue paper from China, ultimately enhancing their procurement strategy and supplier relationships.
Navigating Market Dynamics and Sourcing Trends in the tissue paper china Sector
What Are the Current Market Dynamics and Key Trends in the Tissue Paper Sector from China?
The tissue paper sector in China has been experiencing significant growth, driven by increasing consumer demand for hygiene products and a shift towards more sustainable practices. Global drivers include the rise in disposable income and urbanization, particularly in developing regions such as Africa and South America. These factors have led to a surge in the demand for tissue paper products, which has prompted manufacturers to innovate and expand their production capabilities.
In terms of B2B technology and sourcing trends, digital transformation is reshaping how international buyers engage with suppliers. The adoption of e-commerce platforms and digital supply chain solutions allows for streamlined procurement processes, better inventory management, and enhanced transparency. Additionally, data analytics is becoming essential for understanding market trends and consumer preferences, enabling businesses to make informed purchasing decisions.
Moreover, sustainability is increasingly influencing sourcing decisions. Buyers are looking for suppliers who prioritize eco-friendly materials and practices, reflecting a broader global trend towards responsible consumption. This shift is particularly prominent in Europe and the Middle East, where regulatory frameworks are encouraging sustainable sourcing practices.
How Can International Buyers Ensure Sustainability and Ethical Sourcing in Tissue Paper Products?
Sustainability and ethical sourcing have become paramount in the tissue paper industry. The environmental impact of tissue production includes deforestation, water pollution, and high energy consumption. International buyers must be vigilant in selecting suppliers that adhere to sustainable practices. This involves verifying that raw materials are sourced from responsibly managed forests and that production processes minimize waste and emissions.
Certifications such as FSC (Forest Stewardship Council) and PEFC (Programme for the Endorsement of Forest Certification) are critical indicators of a supplier’s commitment to sustainability. These certifications assure buyers that the tissue paper products are made from materials that meet rigorous environmental standards. Additionally, the use of recycled materials in the production of tissue paper is gaining traction, providing an alternative that reduces the overall carbon footprint.
Buyers should also consider engaging with suppliers who utilize renewable energy sources in their manufacturing processes. This not only aligns with global sustainability goals but also often results in cost savings in the long run. By prioritizing ethical sourcing, international buyers can contribute to a more sustainable tissue paper supply chain while meeting the growing demand for eco-friendly products.
What Is the Historical Context Behind the Growth of the Tissue Paper Sector in China?
The tissue paper industry in China has evolved considerably over the past few decades. Initially, the market was characterized by low-quality products and limited production capacity. However, the economic reforms of the late 20th century spurred rapid industrialization, leading to significant advancements in manufacturing technologies.
As consumer preferences shifted towards higher quality and more diverse tissue products, Chinese manufacturers responded by investing in modern production techniques and materials. This evolution has positioned China as a leading exporter of tissue paper products, catering to the growing demand from international markets, especially in Africa, South America, and Europe.
The combination of rising domestic consumption and robust export capabilities has transformed China’s tissue paper sector into a global powerhouse, making it essential for international B2B buyers to stay informed about market dynamics and sourcing trends to capitalize on emerging opportunities.
Frequently Asked Questions (FAQs) for B2B Buyers of tissue paper china
-
How do I assess the quality of tissue paper suppliers in China?
To evaluate the quality of tissue paper suppliers in China, consider requesting product samples to assess texture, absorbency, and durability. Additionally, verify the supplier’s certifications, such as ISO or FSC, to ensure they adhere to industry standards. Conducting on-site visits or utilizing third-party inspection services can provide further assurance. Finally, reviewing customer feedback and ratings on platforms like Alibaba or Global Sources can help gauge supplier reliability. -
What are the typical minimum order quantities (MOQs) for tissue paper from China?
Minimum order quantities for tissue paper can vary significantly depending on the supplier and product specifications. Generally, MOQs range from 1,000 to 10,000 units per order. Larger manufacturers may offer lower MOQs, while smaller suppliers might require higher quantities. When negotiating, consider your budget and inventory capacity, and communicate your needs clearly to the supplier for potential flexibility. -
What payment terms should I negotiate with Chinese tissue paper suppliers?
Common payment terms include a 30% deposit with the order and the remaining 70% before shipment. However, you may negotiate terms like letters of credit or payment upon delivery for more security. It’s crucial to assess the supplier’s reliability and your comfort level with their payment practices. Always document the agreed terms in the contract to avoid future disputes.
-
How can I customize tissue paper products to meet my brand’s requirements?
Customization options for tissue paper typically include print design, color selection, and packaging styles. When sourcing from China, communicate your specific requirements to the supplier during the initial discussions. Many manufacturers offer design services, so providing high-quality mock-ups or samples can facilitate the process. Remember to confirm the lead time for customized products to ensure they align with your marketing timelines. -
What logistics considerations should I keep in mind when importing tissue paper from China?
When importing tissue paper, consider shipping methods (air or sea), transit times, and customs regulations in your destination country. Collaborating with a freight forwarder can streamline the logistics process, ensuring compliance with import duties and taxes. Additionally, factor in potential delays due to customs inspections, especially during peak shipping seasons, to avoid inventory shortages. -
How do I ensure compliance with international quality standards for tissue paper?
To ensure compliance with international quality standards, verify that your supplier adheres to relevant regulations, such as EN 13432 for compostability or FDA standards for food contact materials. Request documentation proving compliance, and consider engaging third-party auditors for thorough quality inspections. Establishing a quality assurance protocol with the supplier can also help maintain standards throughout production. -
What are the common challenges faced when sourcing tissue paper from China?
Common challenges include language barriers, quality inconsistency, and navigating the complexities of international shipping. To mitigate these issues, establish clear communication channels and consider using professional translation services if necessary. Developing strong relationships with suppliers and conducting thorough research can also help minimize risks associated with quality and delivery timelines. -
How can I effectively vet tissue paper suppliers in China?
To vet suppliers, start by researching their background, including years in business and customer reviews. Utilize platforms like Alibaba or Made-in-China to access supplier ratings and feedback. Verify their business licenses and certifications to ensure legitimacy. Conduct interviews, request references, and consider visiting their facilities if possible. Engaging a local sourcing agent can also provide valuable insights and facilitate the vetting process.
Important Disclaimer & Terms of Use
⚠️ Important Disclaimer
The information provided in this guide, including content regarding manufacturers, technical specifications, and market analysis, is for informational and educational purposes only. It does not constitute professional procurement advice, financial advice, or legal advice.
While we have made every effort to ensure the accuracy and timeliness of the information, we are not responsible for any errors, omissions, or outdated information. Market conditions, company details, and technical standards are subject to change.
B2B buyers must conduct their own independent and thorough due diligence before making any purchasing decisions. This includes contacting suppliers directly, verifying certifications, requesting samples, and seeking professional consultation. The risk of relying on any information in this guide is borne solely by the reader.
Strategic Sourcing Conclusion and Outlook for tissue paper china
What Are the Key Takeaways for International B2B Buyers in Tissue Paper Sourcing?
In the competitive landscape of tissue paper sourcing from China, international B2B buyers must prioritize strategic sourcing to maximize their procurement efficiency. Understanding the nuances of supplier capabilities, pricing structures, and quality assurance processes is crucial. By leveraging a network of trusted suppliers and utilizing data-driven insights, businesses can secure the best possible deals while ensuring product quality and compliance with international standards.
How Can Strategic Sourcing Enhance Your Supply Chain?
Investing in strategic sourcing not only reduces costs but also enhances supply chain resilience. Buyers from Africa, South America, the Middle East, and Europe should actively engage with suppliers to negotiate favorable terms and explore opportunities for collaboration. This proactive approach enables businesses to adapt swiftly to market changes and consumer demands, ensuring a steady supply of high-quality tissue paper products.
What Is the Future Outlook for Tissue Paper Sourcing from China?
Looking ahead, the demand for sustainable and eco-friendly tissue products is expected to rise. Buyers should consider suppliers who prioritize environmentally friendly practices, as this aligns with global trends towards sustainability. By embracing these changes, international B2B buyers can position themselves as industry leaders in sustainability and innovation.
In conclusion, the path to successful tissue paper sourcing lies in informed decision-making and strategic partnerships. Now is the time to explore the vast opportunities within the Chinese market and elevate your sourcing strategy. Take the next step towards optimizing your supply chain today!