Cut Costs with Top Air Compressor Manufacturer Insights (2025)
Introduction: Navigating the Global Market for air compressor manufacturer
Navigating the global market for air compressors can be a daunting task for international B2B buyers, especially when sourcing reliable and efficient equipment for diverse applications. Whether you’re a manufacturer in Colombia, a construction firm in Saudi Arabia, or an industrial supplier in Europe, finding the right air compressor manufacturer is crucial to ensuring operational efficiency and cost-effectiveness. This guide is designed to address common challenges faced by buyers, such as understanding different types of air compressors, their specific applications, and the nuances of supplier vetting.
In this comprehensive resource, we will explore various types of air compressors, including rotary screw, reciprocating, and centrifugal models, alongside their unique applications across industries like manufacturing, construction, and automotive. We will also delve into the essential criteria for evaluating suppliers, from certifications and production capabilities to customer service and warranty options. Additionally, we will provide insights into cost factors, helping buyers make informed purchasing decisions.
By empowering B2B buyers with actionable insights and expert knowledge, this guide will facilitate the selection of the most suitable air compressor manufacturers, ultimately enhancing productivity and driving business growth in regions such as Africa, South America, the Middle East, and Europe. Whether you seek to optimize your supply chain or enhance your operational capabilities, this guide serves as your roadmap in the global air compressor market.
Understanding air compressor manufacturer Types and Variations
Type Name | Key Distinguishing Features | Primary B2B Applications | Brief Pros & Cons for Buyers |
---|---|---|---|
Reciprocating Compressors | Positive displacement design, high pressure output | Automotive, manufacturing, HVAC | Pros: High efficiency, suitable for high pressure. Cons: Noisy, requires more maintenance. |
Rotary Screw Compressors | Continuous operation, lower noise levels, compact design | Industrial applications, construction | Pros: Efficient for large volumes, lower operational costs. Cons: Higher initial investment. |
Centrifugal Compressors | High flow rates, suitable for large-scale applications | Oil & gas, power generation | Pros: Very efficient for high volume, minimal maintenance. Cons: Complex design, expensive. |
Scroll Compressors | Compact, quiet operation, fewer moving parts | Refrigeration, air conditioning | Pros: Energy-efficient, low noise. Cons: Limited pressure range, higher cost per unit. |
Diaphragm Compressors | Non-lubricated, suitable for corrosive gases | Chemical processing, laboratories | Pros: Safe for sensitive applications, minimal contamination. Cons: Lower flow rates, higher maintenance. |
What are the characteristics and suitability of Reciprocating Compressors for B2B buyers?
Reciprocating compressors utilize a piston mechanism to compress air, making them ideal for applications requiring high pressure. They are commonly used in automotive, manufacturing, and HVAC sectors. Buyers should consider the noise levels and maintenance frequency, as these compressors can be quite loud and require regular upkeep. However, their efficiency in generating high pressure makes them a reliable choice for businesses needing robust air supply.
How do Rotary Screw Compressors benefit various industries?
Rotary screw compressors operate continuously and are known for their compact design and lower noise output. They are particularly suited for industrial applications and construction, where consistent air supply is crucial. B2B buyers should focus on the initial investment versus long-term operational costs, as these compressors are efficient for large volumes, potentially leading to lower costs over time. Their reliability and efficiency make them a preferred choice in many sectors.
Why are Centrifugal Compressors essential for large-scale applications?
Centrifugal compressors excel in high flow rate applications, making them essential for industries like oil & gas and power generation. Their design allows for efficient operation in large-scale settings, and they require minimal maintenance. Buyers should weigh the complexity and cost of these compressors against their efficiency and performance capabilities. For businesses needing a reliable air supply for substantial operations, centrifugal compressors are often worth the investment.
What advantages do Scroll Compressors offer to B2B applications?
Scroll compressors are known for their compact size and quiet operation, making them suitable for refrigeration and air conditioning applications. They have fewer moving parts, which translates to lower maintenance and longer service life. However, their pressure range is limited, and they may come at a higher cost per unit. B2B buyers should consider the balance between energy efficiency and initial investment when selecting scroll compressors for their operations.
In what scenarios are Diaphragm Compressors the best choice?
Diaphragm compressors are ideal for applications involving corrosive gases, such as in chemical processing and laboratory settings. Their non-lubricated design minimizes contamination risks, making them safe for sensitive environments. Buyers should note that while diaphragm compressors offer lower flow rates and potentially higher maintenance needs, their safety and reliability in critical applications can justify the investment. For businesses focused on minimizing contamination, diaphragm compressors are often the best option.
Related Video: Air Compressor Types, How They Work, and How to Choose the Right One
Key Industrial Applications of air compressor manufacturer
Industry/Sector | Specific Application of air compressor manufacturer | Value/Benefit for the Business | Key Sourcing Considerations for this Application |
---|---|---|---|
Manufacturing | Pneumatic tools and machinery operation | Enhanced efficiency and productivity in production processes | Reliability, energy efficiency, and maintenance support |
Food and Beverage | Packaging and bottling processes | Improved hygiene and speed in packaging operations | Compliance with food safety standards and energy consumption |
Construction | Concrete mixing and pneumatic tools | Increased operational efficiency and reduced manual labor | Durability, portability, and performance under harsh conditions |
Automotive | Painting and assembly line operations | Consistent quality and reduced downtime in manufacturing | Compatibility with existing systems and energy efficiency |
Mining | Ore processing and pneumatic drilling | Enhanced productivity and reduced equipment wear | Robustness, service support, and adaptability to local conditions |
How is Air Compressor Technology Applied in Various Industries?
Manufacturing: How Do Air Compressors Enhance Production Efficiency?
In manufacturing, air compressors power pneumatic tools and machinery, streamlining operations and improving productivity. They enable quicker assembly, cutting, and material handling processes. For international buyers, especially in regions like Africa and South America, sourcing compressors with energy efficiency ratings is crucial to reduce operational costs. Additionally, reliability and ease of maintenance are significant considerations to minimize downtime.
Food and Beverage: What Role Do Air Compressors Play in Hygiene and Efficiency?
In the food and beverage sector, air compressors are integral to packaging and bottling processes. They ensure that packaging is completed swiftly and hygienically, which is vital for maintaining product quality. Buyers must ensure that compressors comply with food safety standards, particularly in the Middle East and Europe, where regulations are stringent. Energy consumption is another key consideration, as operational costs can significantly impact profitability.
Construction: How Do Air Compressors Improve Construction Efficiency?
Air compressors are essential in the construction industry for concrete mixing and powering pneumatic tools. They enhance operational efficiency by reducing manual labor and ensuring consistent performance in challenging environments. For buyers in regions like Saudi Arabia, where construction is booming, selecting durable and portable compressors is essential. Additionally, performance under extreme weather conditions is a critical factor to consider.
Automotive: How Do Air Compressors Contribute to Quality Control?
In the automotive industry, air compressors are used in painting and assembly line operations, ensuring consistent quality and reducing downtime. They help maintain a clean working environment, which is crucial for high-quality finishes. International buyers should look for compressors that are compatible with existing systems and provide energy efficiency to lower operational costs, particularly in competitive markets across Europe and South America.
Mining: What Are the Benefits of Air Compressors in Mining Operations?
Air compressors play a vital role in ore processing and pneumatic drilling in the mining sector. They enhance productivity by powering equipment that can operate in harsh conditions, while also reducing wear on machinery. For B2B buyers from Africa and the Middle East, sourcing robust compressors that can withstand local environmental challenges is essential. Service support and adaptability to specific mining operations should also be key considerations when selecting a supplier.
Related Video: Air Compressor (Basics, Parts, Diagram, Working & Applications) Explained with Animation
3 Common User Pain Points for ‘air compressor manufacturer’ & Their Solutions
Scenario 1: Navigating Compressor Selection for Unique Applications
The Problem:
B2B buyers often encounter the challenge of selecting the right air compressor that meets specific operational requirements. For instance, a manufacturing firm in Colombia may require a compressor that can handle high humidity and varying temperatures, impacting its efficiency and longevity. Without a clear understanding of the different types of compressors—such as reciprocating, rotary screw, or centrifugal—buyers may end up with equipment that doesn’t align with their operational needs, leading to inefficiencies, increased maintenance costs, and potential downtime.
The Solution:
To overcome this issue, it’s crucial for buyers to conduct a thorough needs assessment. Begin by evaluating the specific requirements of your operations, including the desired airflow, pressure levels, and environmental conditions. Engage with multiple air compressor manufacturers to discuss these needs in detail. Utilize their expertise to identify the most suitable compressor type and model. Additionally, requesting case studies or testimonials from similar industries can provide insights into performance and reliability. Don’t hesitate to ask for trial periods or demonstrations to ensure the selected compressor meets expectations before finalizing the purchase.
Scenario 2: Managing Energy Costs with Efficient Air Compressors
The Problem:
Energy consumption is a significant concern for many businesses that rely on air compressors. For instance, a construction company in Saudi Arabia may face soaring electricity bills due to inefficient compressors that operate continuously at high pressure, leading to wasted energy and increased operational costs. The challenge lies in identifying and implementing more energy-efficient solutions without sacrificing performance.
The Solution:
Implementing an energy audit can help identify inefficiencies in your current compressor system. Work with air compressor manufacturers who offer energy-efficient models, such as variable speed drive (VSD) compressors, which adjust their speed based on demand, reducing energy consumption. Additionally, consider integrating smart monitoring systems that track usage patterns and optimize compressor operation. Collaborate with your manufacturer to explore options for retrofitting existing compressors with energy-saving technologies. Investing in maintenance and regular servicing also ensures that compressors operate at peak efficiency, further curbing energy costs.
Scenario 3: Ensuring Reliable Air Supply During Peak Demand
The Problem:
Businesses often face challenges in maintaining a consistent air supply during peak operational periods. For example, a textile factory in Europe may experience sudden spikes in demand, requiring a reliable air supply to operate multiple machines simultaneously. If the air compressor fails to keep up, production can halt, leading to lost revenue and missed deadlines.
The Solution:
To ensure a reliable air supply, buyers should consider investing in a compressor system that includes redundancy, such as multiple compressors working in parallel. This setup allows for load sharing and provides backup in case one unit fails. Additionally, buyers should work with manufacturers to assess their current and future air demand accurately. Implementing a compressor management system can help monitor usage and dynamically adjust operations based on demand fluctuations. Furthermore, establishing a robust maintenance schedule will ensure that all equipment remains in optimal condition, reducing the risk of unexpected failures during critical operational times.
Strategic Material Selection Guide for air compressor manufacturer
When selecting materials for air compressors, manufacturers must consider various factors that directly impact performance, durability, and cost-effectiveness. Below is a comprehensive analysis of four common materials used in air compressor manufacturing, focusing on their properties, advantages, disadvantages, and implications for international B2B buyers, particularly from Africa, South America, the Middle East, and Europe.
What are the Key Properties of Aluminum in Air Compressors?
Aluminum is widely used in air compressor components due to its favorable properties. It has excellent corrosion resistance, a high strength-to-weight ratio, and can withstand temperatures up to 200°C (392°F). These properties make aluminum suitable for various applications, including compressor housings and components that require lightweight and durable materials.
Pros & Cons:
Aluminum offers durability and is lightweight, which enhances the efficiency of portable compressors. However, it can be more expensive than other materials like steel and may require specialized manufacturing processes, increasing production complexity.
Impact on Application:
Aluminum is compatible with a variety of media, including air and gas, but may not be suitable for applications involving aggressive chemicals or high temperatures.
Considerations for International Buyers:
Buyers in regions like the Middle East and Europe should ensure compliance with local standards such as ASTM and DIN. Additionally, the availability of aluminum can vary by region, impacting lead times and costs.
How Does Steel Compare as a Material for Air Compressors?
Steel, particularly carbon steel, is another common material used in air compressor manufacturing. It boasts high tensile strength, excellent wear resistance, and can handle high-pressure applications, making it ideal for compressor frames and pressure vessels.
Pros & Cons:
Steel is generally more affordable than aluminum and offers superior strength and durability. However, it is heavier, which can be a disadvantage for portable applications. Additionally, steel is prone to corrosion, necessitating protective coatings or treatments.
Impact on Application:
Steel is suitable for high-pressure applications and can handle a wide range of gases and fluids. However, its susceptibility to rust means that it may not be the best choice for humid or corrosive environments without proper treatment.
Considerations for International Buyers:
International buyers should consider the local availability of quality steel and adherence to standards such as JIS in Japan or ASTM in the U.S. Compliance with these standards ensures that the steel used meets safety and performance requirements.
What Role Does Stainless Steel Play in Air Compressor Manufacturing?
Stainless steel is often used in air compressors due to its excellent corrosion resistance and durability. It can withstand a wide range of temperatures and is often used in applications involving moisture or corrosive environments.
Pros & Cons:
The main advantage of stainless steel is its resistance to rust and corrosion, which extends the lifespan of compressor components. However, it is more expensive than carbon steel and can be more challenging to machine, increasing manufacturing complexity.
Impact on Application:
Stainless steel is ideal for applications involving water or chemicals, making it suitable for compressors used in industries such as food processing or pharmaceuticals.
Considerations for International Buyers:
Buyers in regions like Africa and South America should verify that the stainless steel meets local standards and specifications. Ensuring compliance with ASTM or other relevant standards can help avoid issues with material quality.
Why is Copper Used in Air Compressor Components?
Copper is commonly used in air compressors, particularly for piping and heat exchangers, due to its excellent thermal conductivity and resistance to corrosion.
Pros & Cons:
Copper’s high thermal conductivity enhances heat exchange efficiency, making it ideal for cooling applications. However, it is relatively expensive compared to aluminum and steel, and its softness can lead to wear in high-stress applications.
Impact on Application:
Copper is suitable for air and gas applications but may not be ideal for environments with high mechanical stress.
Considerations for International Buyers:
International buyers should consider the cost implications of using copper, especially in regions where copper is not readily available. Compliance with local material standards is also crucial to ensure product reliability.
Summary Table of Material Selection for Air Compressor Manufacturing
Material | Typical Use Case for air compressor manufacturer | Key Advantage | Key Disadvantage/Limitation | Relative Cost (Low/Med/High) |
---|---|---|---|---|
Aluminum | Compressor housings, lightweight components | Lightweight, corrosion-resistant | Higher cost, manufacturing complexity | Medium |
Steel | Frames, pressure vessels | High strength, cost-effective | Heavier, prone to corrosion | Low |
Stainless Steel | Moisture or chemical applications | Excellent corrosion resistance | Higher cost, machining challenges | High |
Copper | Piping, heat exchangers | Superior thermal conductivity | Expensive, softer material | High |
This guide aims to provide actionable insights for international B2B buyers in selecting the appropriate materials for air compressors, ensuring they make informed decisions that align with their operational needs and regional standards.
In-depth Look: Manufacturing Processes and Quality Assurance for air compressor manufacturer
What are the Main Stages of Manufacturing Air Compressors?
The manufacturing process for air compressors is intricate and typically consists of several key stages: material preparation, forming, assembly, and finishing. Understanding these stages can help international B2B buyers ensure they are selecting manufacturers that adhere to high-quality standards.
How is Material Prepared for Air Compressor Manufacturing?
The first step involves selecting the right materials, which often include steel, aluminum, and various polymers. These materials must be inspected for quality and compliance with international standards before being approved for use. This step is crucial for ensuring that the final product can withstand the operational pressures typical of air compressor applications.
Once approved, materials undergo cutting, shaping, and machining to prepare them for the forming stage. Techniques such as laser cutting and CNC machining are commonly employed, allowing for precision and efficiency. This stage is critical as it lays the groundwork for the performance and durability of the compressor.
What Techniques are Used in the Forming Process?
Forming is the next stage, where the prepared materials are transformed into specific components of the air compressor. Techniques such as stamping, forging, and casting are commonly used. Each technique has its own advantages: stamping is ideal for mass production of flat parts, while forging enhances the strength of metal components through deformation.
During this stage, careful control of parameters such as temperature and pressure is vital to ensure that components meet design specifications. Quality assurance begins here, as deviations can lead to significant performance issues later in the manufacturing process.
How is the Assembly of Air Compressors Conducted?
Once components are formed, they proceed to the assembly stage. This involves integrating various parts such as the motor, pump, and tank into a cohesive unit. Assembly can be done manually or through automated systems, depending on the manufacturer‘s scale and capabilities.
During assembly, it’s crucial to adhere to precise torque specifications and alignment tolerances. Each component must fit perfectly to ensure efficient operation and minimize wear. Manufacturers often employ assembly line techniques to streamline this process, enhancing productivity while maintaining quality.
What Finishing Processes are Important for Air Compressors?
The final stage, finishing, involves treating the assembled air compressors to enhance their durability and aesthetics. This may include processes like painting, powder coating, or anodizing, which protect against corrosion and improve the product’s lifespan.
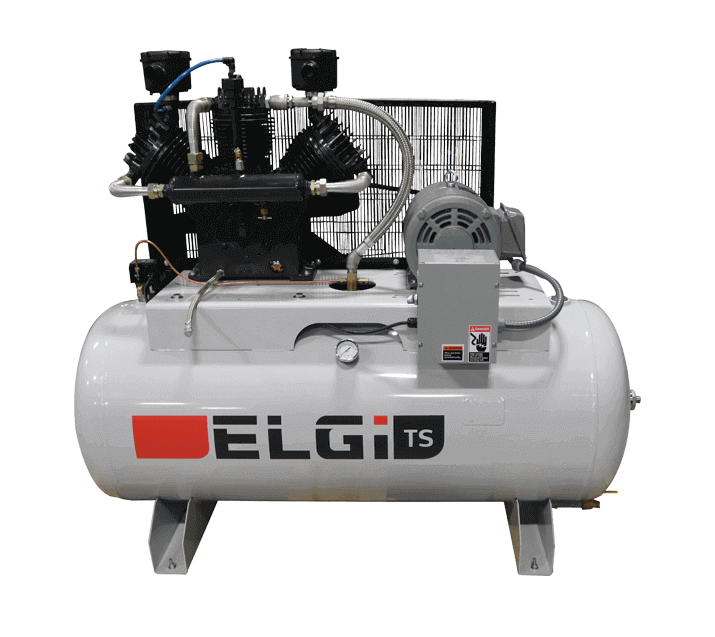
A stock image related to air compressor manufacturer.

A stock image related to air compressor manufacturer.
Quality control checks are integral during this stage to ensure that the finished product meets all specifications. Any discrepancies can lead to failures in the field, potentially damaging the manufacturer’s reputation and incurring costs for replacements or repairs.
How is Quality Assurance Implemented in Air Compressor Manufacturing?
Quality assurance (QA) is an ongoing process throughout the manufacturing stages. International standards such as ISO 9001 provide a framework for manufacturers to implement effective QA practices. Compliance with these standards is essential for B2B buyers, as it signifies a commitment to quality and continuous improvement.
What are the Key International Standards for Air Compressors?
In addition to ISO 9001, air compressor manufacturers often comply with industry-specific standards such as CE marking for European markets and API standards for oil and gas applications. These certifications ensure that products meet safety, health, and environmental protection requirements.
B2B buyers should look for manufacturers that have these certifications, as they indicate adherence to rigorous quality and safety protocols.
What are the Critical Quality Control Checkpoints?
Quality control (QC) typically involves several checkpoints during the manufacturing process:
-
Incoming Quality Control (IQC): This is the first line of defense, where raw materials and components are inspected upon arrival. This ensures that only high-quality materials enter the production process.
-
In-Process Quality Control (IPQC): During the manufacturing stages, ongoing inspections are conducted to monitor the quality of the product. This involves checking dimensions, tolerances, and other critical parameters to catch defects early.
-
Final Quality Control (FQC): Once the air compressor is fully assembled, a final inspection is performed. This includes functional testing to ensure that the compressor operates as intended and meets performance specifications.
What Common Testing Methods are Used for Air Compressors?
Testing methods vary by manufacturer but typically include:
- Pressure Tests: To ensure that the compressor can handle the required operational pressures without leaking.
- Performance Testing: Verifying the compressor’s output and efficiency under various conditions.
- Durability Testing: Simulating long-term usage to assess the lifespan and reliability of the compressor.
How Can B2B Buyers Verify Supplier Quality Control?
For B2B buyers, verifying the quality control measures of potential suppliers is crucial. Here are several actionable steps:
- Request Audits and Reports: Suppliers should be able to provide documentation of their quality control processes, including audit reports and compliance certifications.
- Third-Party Inspections: Engaging third-party inspection services can provide an unbiased evaluation of the manufacturer’s processes and products.
- Site Visits: If feasible, visiting the manufacturing facility can give buyers firsthand insight into the quality control measures in place.
What are the Quality Control Nuances for International B2B Buyers?
International buyers, especially from regions like Africa, South America, the Middle East, and Europe, should be aware of specific nuances in quality control. For instance, cultural differences may affect communication regarding quality expectations. Additionally, varying regulatory environments can impact compliance with local standards.
Understanding these factors is essential for establishing effective partnerships with suppliers. B2B buyers should engage in open dialogue with manufacturers about their quality assurance processes and ensure that all parties are aligned on expectations.
By focusing on the manufacturing processes and quality assurance practices, B2B buyers can make informed decisions when selecting air compressor manufacturers, ensuring they receive high-quality products that meet their operational needs.
Practical Sourcing Guide: A Step-by-Step Checklist for ‘air compressor manufacturer’
In the competitive landscape of air compressor manufacturing, making informed sourcing decisions is paramount for international B2B buyers. This practical checklist serves as a guide to streamline the procurement process, ensuring that you select a manufacturer that meets your specific needs while maintaining quality and compliance standards.
Step 1: Define Your Technical Specifications
Before reaching out to potential manufacturers, clearly outline the technical specifications of the air compressors you need. Consider factors such as power requirements, pressure output, tank capacity, and intended applications. This step is crucial as it allows you to communicate your requirements effectively and ensures that suppliers can meet your expectations.
Step 2: Research Potential Manufacturers
Conduct thorough research to identify reputable air compressor manufacturers. Utilize industry directories, trade shows, and online platforms to compile a list of candidates. Focus on manufacturers with a proven track record in your target regions, such as Africa, South America, the Middle East, and Europe. This will help you narrow down suppliers who understand the specific market dynamics and regulations in your area.
Step 3: Evaluate Supplier Certifications
✅ Verify Supplier Certifications
Ensure that the manufacturers you consider hold relevant certifications, such as ISO 9001 for quality management and ISO 14001 for environmental management. These certifications indicate a commitment to quality and compliance with industry standards. Additionally, check for specific certifications relevant to your industry or region, as these can enhance trust and reliability.
Step 4: Request Detailed Quotations
Once you have identified potential suppliers, request detailed quotations that break down costs, lead times, and payment terms. This step is vital for comparing offers and understanding the total cost of ownership, including shipping and customs fees. Look for transparency in pricing and any additional costs that may arise during the procurement process.
Step 5: Assess Quality Control Measures
How do manufacturers ensure product quality?
Inquire about the quality control measures that manufacturers have in place. This includes understanding their testing procedures, quality assurance protocols, and how they handle defects or returns. A robust quality control process indicates that the manufacturer prioritizes product reliability and customer satisfaction, which is essential for your operational efficiency.
Step 6: Check References and Reviews
Reach out to existing customers for feedback about their experiences with the manufacturers you are considering. Reviews and references can provide valuable insights into the reliability of the supplier, their customer service, and post-purchase support. This step helps mitigate risks associated with selecting a new supplier and can reveal potential issues that may not be evident during initial discussions.
Step 7: Negotiate Terms and Conditions
Before finalizing your decision, engage in negotiations regarding terms and conditions, including warranty coverage, delivery timelines, and after-sales support. Clear agreements in these areas protect your investment and ensure that you have recourse if issues arise. A well-negotiated contract lays the foundation for a successful partnership, fostering trust and collaboration.
By following this structured checklist, B2B buyers can confidently navigate the sourcing process for air compressors, ensuring they select a manufacturer that aligns with their technical and operational requirements.
Comprehensive Cost and Pricing Analysis for air compressor manufacturer Sourcing
What Are the Key Cost Components in Air Compressor Manufacturing?
Understanding the cost structure of air compressor manufacturing is crucial for international B2B buyers. The primary components contributing to the total cost include:
-
Materials: Raw materials, such as aluminum, steel, and specialized components, form a significant part of the manufacturing cost. Prices can fluctuate based on market demand and availability, impacting the overall pricing.
-
Labor: Skilled labor is essential for assembly and quality control. Labor costs can vary significantly by region, with countries in Europe often facing higher wages than those in Africa or South America.
-
Manufacturing Overhead: This includes utilities, depreciation of equipment, and indirect labor costs. Efficient production processes can help minimize overhead and improve profit margins.
-
Tooling: The cost of tools and molds used in production is a critical factor, especially for custom designs. Initial investments can be high, but they amortize over larger production runs.
-
Quality Control (QC): Implementing rigorous QC processes ensures product reliability and compliance with international standards. This can add to the cost but ultimately protects the brand and reduces warranty claims.
-
Logistics: Shipping costs are a major consideration, especially for international buyers. Factors such as distance, mode of transport, and customs duties significantly affect the final price.
-
Margin: Manufacturers typically mark up their prices to maintain profitability, which can vary based on competition and market positioning.
How Do Price Influencers Affect Air Compressor Sourcing?
Several factors influence the pricing of air compressors, particularly for international buyers:
-
Volume and Minimum Order Quantity (MOQ): Higher purchase volumes generally lead to lower per-unit costs. Establishing a relationship with suppliers can also negotiate better terms.
-
Specifications and Customization: Custom-built compressors tailored to specific needs often incur additional costs. Clear communication of specifications can prevent unexpected expenses.
-
Materials and Quality Certifications: Premium materials and certifications (like ISO standards) can drive up costs. Buyers should weigh the benefits of enhanced quality against their budget constraints.
-
Supplier Factors: The supplier’s reputation, reliability, and location can affect pricing. Suppliers in regions with established manufacturing capabilities may offer better pricing due to economies of scale.
-
Incoterms: Understanding shipping terms is vital for cost management. Different Incoterms (like FOB or CIF) dictate who bears shipping costs and risks, impacting the overall price.
What Buyer Tips Can Help Optimize Costs in Air Compressor Sourcing?
To effectively navigate the complexities of air compressor sourcing, consider these actionable tips:
-
Negotiate Wisely: Leverage your purchasing power by discussing bulk discounts and flexible payment terms. Be prepared to walk away if terms do not meet your expectations.
-
Focus on Cost-Efficiency: Look beyond the initial purchase price. Analyze the Total Cost of Ownership (TCO), which includes maintenance, energy consumption, and potential downtime.
-
Understand Pricing Nuances for International Sourcing: Different regions have unique pricing structures influenced by local market conditions. For instance, buyers from South America may find more favorable terms in neighboring countries due to reduced shipping costs.
-
Stay Informed About Market Trends: Regularly review material costs and industry trends to better time your purchases and negotiate more effectively.
-
Build Long-Term Relationships: Establishing rapport with suppliers can lead to better pricing and service. Suppliers may offer favorable terms to repeat customers or those who show loyalty.
Disclaimer on Indicative Prices
Prices for air compressors can vary widely based on the factors discussed above. It is essential for buyers to conduct thorough market research and obtain multiple quotes to ensure they secure the best possible deal.
Alternatives Analysis: Comparing air compressor manufacturer With Other Solutions
When considering the purchase of air compressors, international B2B buyers often seek alternatives that can fulfill similar operational requirements. Understanding the various solutions available helps in making an informed decision that aligns with specific business needs. Below is a comparison of air compressors against alternative technologies that achieve similar goals, providing insights into their performance, cost, and suitability for different applications.
Comparison Aspect | Air Compressor Manufacturer | Electric Pump System | Pneumatic Tools |
---|---|---|---|
Performance | High pressure output, versatile applications | Moderate pressure output, limited to specific tasks | High efficiency for specific tasks, variable pressure |
Cost | Mid to high initial investment | Lower initial cost, variable operating costs | Low initial cost, but can incur higher long-term costs |
Ease of Implementation | Requires significant setup and space | Easy to install and use | Simple to implement, portable |
Maintenance | Regular maintenance required for optimal performance | Minimal maintenance needed | Low maintenance, but parts may need replacement |
Best Use Case | Industrial and manufacturing settings, heavy-duty tasks | Small to medium applications, automotive repairs | Construction, assembly lines, quick tasks |
What Are the Advantages and Disadvantages of Electric Pump Systems?
Electric pump systems serve as a viable alternative to traditional air compressors, particularly in applications requiring moderate pressure. They are easier to install and operate, making them suitable for small to medium-sized tasks such as automotive repairs or light industrial applications. However, their performance may be limited compared to air compressors, especially in high-demand scenarios. Additionally, while the initial investment is lower, the operating costs can vary based on electricity prices and usage frequency.
How Do Pneumatic Tools Compare to Air Compressors?
Pneumatic tools are commonly used in construction and assembly lines, offering high efficiency for specific tasks. They can deliver variable pressure and are known for their portability, making them suitable for quick jobs. The initial investment for pneumatic tools is generally low; however, the long-term costs can accumulate due to the need for additional air supply equipment, maintenance, and potential replacement parts. While they excel in specific applications, they may not provide the versatility or pressure output of a dedicated air compressor system.
Conclusion: Which Solution Should B2B Buyers Choose?
When deciding between air compressors and alternative solutions, B2B buyers must assess their specific operational needs, budget constraints, and the intended application of the equipment. For heavy-duty industrial tasks that require consistent high pressure, air compressors remain the most effective choice. However, for smaller-scale operations or specific tasks, electric pump systems and pneumatic tools offer cost-effective, simpler alternatives. By evaluating performance, cost, ease of implementation, and maintenance requirements, buyers can make informed decisions that enhance their operational efficiency and align with their business objectives.
Essential Technical Properties and Trade Terminology for air compressor manufacturer
What Are the Essential Technical Properties of Air Compressors for B2B Buyers?
Understanding the technical properties of air compressors is crucial for B2B buyers, especially when making informed purchasing decisions. Below are some key specifications that international buyers should consider:
1. Material Grade: What Materials Are Used in Air Compressors?
The material grade of an air compressor affects its durability and performance. Common materials include cast iron, aluminum, and various alloys. Cast iron is often favored for its strength and resistance to wear, making it ideal for heavy-duty applications. Aluminum is lighter and corrosion-resistant, suitable for portable models. Buyers should assess their specific application needs to choose the appropriate material.
2. Tolerance Levels: Why Are Tolerances Important in Air Compressors?
Tolerance refers to the permissible limit of variation in a physical dimension. In air compressors, tighter tolerances lead to better efficiency and performance. For instance, a compressor with a tolerance of ±0.01 mm will operate more reliably than one with ±0.05 mm. Understanding tolerance levels helps buyers evaluate product quality and reliability, particularly in precision-demanding environments.
3. Pressure Ratings: What Do Pressure Ratings Indicate?
Pressure ratings, usually measured in PSI (pounds per square inch), indicate the maximum pressure the compressor can safely handle. A higher pressure rating typically means the compressor can support more demanding tasks. Buyers should match pressure ratings with their specific application requirements to ensure optimal performance and safety.
4. Flow Rate: How Is Flow Rate Measured and Why Is It Important?
Flow rate, measured in CFM (cubic feet per minute), indicates the volume of air the compressor can deliver. A higher flow rate is essential for applications requiring substantial air output, such as pneumatic tools or industrial processes. Buyers need to assess their operational needs to determine the minimum required flow rate for their applications.
5. Efficiency Rating: What Is the Significance of Efficiency Ratings?
Efficiency ratings, often expressed in terms of energy consumption versus output, are vital for cost management. An efficient air compressor minimizes energy usage while maximizing output, leading to lower operational costs. Buyers should look for models with high efficiency ratings to ensure long-term savings.
What Are the Common Trade Terms Used in the Air Compressor Industry?
Familiarity with industry jargon can significantly enhance negotiation and purchasing processes. Here are some essential terms:
1. OEM (Original Equipment Manufacturer): What Does OEM Mean in B2B Transactions?
OEM refers to companies that manufacture products that are sold under another company’s brand. In the air compressor industry, buyers often source components from OEMs to ensure compatibility and quality. Understanding OEM relationships can help buyers identify reliable suppliers.
2. MOQ (Minimum Order Quantity): How Does MOQ Affect Purchasing Decisions?
MOQ represents the smallest quantity a supplier is willing to sell. This term is crucial for B2B buyers, as it can affect inventory costs and cash flow. Knowing the MOQ helps buyers plan their orders effectively, especially in regions like Africa and South America where inventory management can be challenging.
3. RFQ (Request for Quotation): What Is the Purpose of an RFQ?
An RFQ is a formal document sent to suppliers to request pricing and terms for specific products. In the air compressor market, submitting an RFQ allows buyers to compare offers from multiple manufacturers, facilitating better negotiation and purchase decisions.
4. Incoterms (International Commercial Terms): How Do Incoterms Influence Trade?
Incoterms are internationally recognized terms that define the responsibilities of buyers and sellers in shipping and logistics. For air compressor buyers, understanding Incoterms like FOB (Free On Board) or CIF (Cost, Insurance, and Freight) is critical for managing shipping costs and risks.
5. After-Sales Support: Why Is After-Sales Support Important?
After-sales support includes services provided to customers post-purchase, such as maintenance, repairs, and customer service. For B2B buyers, robust after-sales support is essential for ensuring long-term operational efficiency and minimizing downtime in their processes.
By understanding these technical properties and trade terms, B2B buyers from regions such as Africa, South America, the Middle East, and Europe can make more informed decisions, ultimately leading to better purchasing outcomes in the air compressor market.
Navigating Market Dynamics and Sourcing Trends in the air compressor manufacturer Sector
What Are the Current Market Dynamics in the Air Compressor Manufacturing Sector?
The air compressor manufacturing sector is experiencing significant transformations driven by technological advancements and increasing demand across various industries. Key global drivers include the growth of automation in manufacturing, rising energy efficiency regulations, and the increasing reliance on pneumatic tools in sectors such as construction, automotive, and food processing. For international B2B buyers, particularly from regions like Africa, South America, the Middle East, and Europe, understanding these dynamics is crucial for effective sourcing and procurement strategies.
Emerging trends include the adoption of IoT technologies, which enhance compressor performance monitoring and predictive maintenance capabilities. This shift not only improves operational efficiency but also extends the lifespan of equipment, offering a compelling value proposition to buyers. Additionally, the market is witnessing a surge in demand for portable and energy-efficient compressors, driven by the need for flexibility and sustainability in operations. Buyers should also pay attention to the increasing integration of smart technologies that facilitate real-time data analysis, enabling better decision-making and resource allocation.
Furthermore, the competitive landscape is evolving as manufacturers focus on product differentiation through innovation, leading to enhanced performance and lower total cost of ownership. Buyers should evaluate suppliers based on their technological capabilities and product offerings that align with the specific needs of their industries, especially in emerging markets where cost-effectiveness is paramount.
How Can Sustainability and Ethical Sourcing Impact Air Compressor Manufacturing?
Sustainability is becoming a cornerstone in the air compressor manufacturing sector, influencing both production practices and purchasing decisions. The environmental impact of manufacturing processes, particularly energy consumption and emissions, has prompted buyers to seek out suppliers that prioritize eco-friendly practices. This shift is especially relevant for B2B buyers in regions like Europe and South America, where regulatory pressures around sustainability are intensifying.
Ethical sourcing is equally important, as consumers and businesses increasingly demand transparency in supply chains. Buyers should consider manufacturers that adhere to recognized ‘green’ certifications, such as ISO 14001 for environmental management and Energy Star ratings for energy-efficient products. These certifications not only demonstrate a commitment to sustainability but also enhance brand reputation and customer loyalty.
Moreover, the use of sustainable materials in the production of air compressors can significantly reduce environmental footprints. Suppliers that invest in research and development to create eco-friendly compressors—such as those using recyclable materials or renewable energy sources—can provide a competitive advantage. B2B buyers must conduct due diligence to ensure their suppliers are committed to ethical practices, as this can lead to long-term partnerships and a positive impact on their own sustainability goals.
What Is the Evolution of the Air Compressor Manufacturing Sector?
The air compressor manufacturing sector has undergone substantial evolution since its inception in the 19th century. Initially, air compressors were primarily utilized in mining and construction, primarily as a means to power pneumatic tools. Over the decades, advancements in technology led to the development of more efficient and versatile compressors, expanding their applications across various industries.
By the late 20th century, the introduction of electric and portable compressors revolutionized the market, allowing for greater flexibility and ease of use. Today, the integration of digital technologies, including IoT and AI, is transforming the landscape yet again, enabling predictive maintenance and enhanced performance monitoring. This evolution reflects the sector’s adaptability to changing market demands and technological innovations, providing international B2B buyers with an array of sophisticated solutions tailored to their operational needs.
In summary, understanding the market dynamics, sustainability practices, and historical evolution of the air compressor manufacturing sector equips B2B buyers with the insights necessary to make informed sourcing decisions that align with both current trends and future demands.
Frequently Asked Questions (FAQs) for B2B Buyers of air compressor manufacturer
-
How do I choose the right air compressor for my business needs?
Selecting the appropriate air compressor involves assessing your specific requirements, including the type of tools you’ll be using, the required pressure and flow rate, and the duration of operation. Consider whether you need a portable or stationary unit, as well as the power source—electric or gas. Additionally, evaluate the noise level, energy efficiency, and maintenance needs of the compressor. Consulting with manufacturers about your applications can provide tailored recommendations to ensure optimal performance. -
What are the advantages of purchasing air compressors from international manufacturers?
International manufacturers often offer advanced technology, competitive pricing, and a diverse range of products. By sourcing from global suppliers, buyers can benefit from innovations not available locally and gain access to larger production capacities. Furthermore, many international companies provide comprehensive warranties and after-sales support, ensuring reliability and peace of mind. However, it’s essential to verify their reputation and compliance with international quality standards. -
What is the typical minimum order quantity (MOQ) for air compressors?
Minimum order quantities can vary significantly between manufacturers and depend on the type of compressor. For larger industrial units, MOQs may range from 1 to 10 units, while smaller or portable models could have lower MOQs. It’s advisable to discuss your needs with the manufacturer to see if they can accommodate smaller orders, especially if you are a new business or testing the market. Some manufacturers might also offer sample units for evaluation before committing to larger orders. -
What payment terms should I expect when purchasing air compressors internationally?
Payment terms can vary widely depending on the supplier and the country of origin. Common terms include a deposit (often 30% to 50%) upfront with the balance due upon shipping or delivery. Some manufacturers may offer letters of credit or payment through escrow services to ensure transaction security. It’s crucial to negotiate terms that align with your cash flow while considering the risk levels associated with international transactions. Always ensure that the terms are documented in the contract. -
How can I ensure the quality of the air compressors I am buying?
To ensure quality, start by verifying the manufacturer’s certifications, such as ISO 9001 or CE marking, which indicate adherence to international quality standards. Request samples or arrange for factory visits to inspect production processes and materials. Additionally, ask for references or case studies from other international buyers. Establishing a quality assurance (QA) plan that includes regular inspections and testing can also help maintain standards throughout the procurement process. -
What logistics considerations should I be aware of when importing air compressors?
Logistics is critical when importing air compressors, involving shipping methods (air, sea, or land), customs regulations, and potential tariffs. Assess the most cost-effective shipping options based on your timeline and budget. Be prepared for customs documentation, including invoices, packing lists, and certificates of origin. It’s also wise to work with a logistics partner experienced in handling heavy machinery to navigate the complexities of international shipping and ensure timely delivery. -
Can I customize the air compressor specifications to fit my business needs?
Many manufacturers offer customization options for their air compressors, allowing you to specify features such as tank size, horsepower, and additional attachments. Customization can enhance efficiency and ensure that the compressor meets your specific operational requirements. When discussing options with manufacturers, provide detailed information about your applications and any specific challenges you face. This collaboration can result in tailored solutions that improve performance and productivity. -
What should I know about after-sales service for air compressors?
After-sales service is crucial for maintaining the longevity and efficiency of your air compressor. Inquire about the warranty period, coverage details, and availability of spare parts. A reliable manufacturer should offer comprehensive support, including maintenance services, troubleshooting, and access to technical resources. Establishing a good relationship with the supplier can also facilitate prompt assistance and repairs, minimizing downtime and ensuring optimal operation of your equipment.
Important Disclaimer & Terms of Use
⚠️ Important Disclaimer
The information provided in this guide, including content regarding manufacturers, technical specifications, and market analysis, is for informational and educational purposes only. It does not constitute professional procurement advice, financial advice, or legal advice.
While we have made every effort to ensure the accuracy and timeliness of the information, we are not responsible for any errors, omissions, or outdated information. Market conditions, company details, and technical standards are subject to change.
B2B buyers must conduct their own independent and thorough due diligence before making any purchasing decisions. This includes contacting suppliers directly, verifying certifications, requesting samples, and seeking professional consultation. The risk of relying on any information in this guide is borne solely by the reader.
Strategic Sourcing Conclusion and Outlook for air compressor manufacturer
In today’s competitive landscape, strategic sourcing is essential for international B2B buyers, especially in regions such as Africa, South America, the Middle East, and Europe. Leveraging strategic sourcing not only optimizes procurement processes but also ensures access to high-quality air compressors that meet specific operational needs. Buyers should focus on establishing long-term partnerships with reputable manufacturers, as this can lead to better pricing, reliability, and tailored solutions.
As you navigate the sourcing journey, consider key factors such as supplier certifications, product specifications, and after-sales support. Engaging with manufacturers who understand local market conditions and compliance requirements can significantly enhance your procurement strategy.
Looking ahead, the demand for advanced air compressor technologies is set to rise, driven by sectors such as manufacturing, construction, and energy. Now is the time for international buyers to take proactive steps in evaluating potential suppliers and investing in quality solutions. By prioritizing strategic sourcing, you can secure a competitive edge and drive sustainable growth in your operations. Embrace this opportunity to enhance your sourcing strategies and ensure your business is well-prepared for future challenges.