Cut Costs with Top MDF Board Manufacturers: A Complete Guide (2025)
Introduction: Navigating the Global Market for mdf board manufacturer
Navigating the global market for MDF board manufacturers presents unique challenges for international B2B buyers, especially those from regions like Africa, South America, the Middle East, and Europe. Sourcing high-quality MDF boards that meet specific project requirements can be daunting, given the diverse range of suppliers and product specifications available. This guide aims to demystify the complexities involved in selecting the right MDF board manufacturers, providing a comprehensive overview of types, applications, supplier vetting processes, and cost considerations.
Understanding the various types of MDF boards—such as standard, moisture-resistant, and fire-rated variants—is crucial for making informed purchasing decisions. Each type serves different applications, from furniture manufacturing to interior construction, making it essential for buyers to align their needs with the right products. Additionally, this guide will delve into effective supplier vetting strategies, ensuring that buyers can identify reputable manufacturers who adhere to international quality standards.
By equipping B2B buyers with actionable insights and practical strategies, this guide empowers them to navigate the global MDF board market confidently. It enables informed decision-making that can enhance project outcomes and optimize supply chain efficiency. Whether you’re a buyer in Australia looking for sustainable materials or a UAE-based company seeking innovative MDF solutions, this resource is tailored to address your specific needs and challenges.
Understanding mdf board manufacturer Types and Variations
Type Name | Key Distinguishing Features | Primary B2B Applications | Brief Pros & Cons for Buyers |
---|---|---|---|
Standard MDF | Made from wood fibers, uniform density, smooth finish | Furniture, cabinetry, panels | Pros: Cost-effective, versatile. Cons: Less moisture-resistant. |
Moisture-Resistant MDF | Treated with additives to resist water damage | Kitchens, bathrooms, outdoor use | Pros: Durable in humid conditions. Cons: Higher cost than standard MDF. |
Fire-Retardant MDF | Incorporates fire-resistant materials | Commercial buildings, safety applications | Pros: Enhanced safety, compliance with regulations. Cons: More expensive, may require special handling. |
High-Density MDF | Denser than standard MDF, provides better durability | High-end furniture, musical instruments | Pros: Superior strength, excellent finish. Cons: Heavier, more costly. |
Eco-Friendly MDF | Made from recycled materials, low in formaldehyde | Sustainable construction, furniture | Pros: Environmentally friendly, safer for indoor use. Cons: Limited availability, potentially higher price. |
What Are the Key Characteristics of Standard MDF?
Standard MDF is the most common type of medium-density fiberboard, composed of wood fibers bonded together with resin under heat and pressure. It features a smooth surface ideal for painting and veneering, making it a popular choice for furniture and cabinetry. When considering purchasing standard MDF, buyers should evaluate their specific application needs, as it may not perform well in high-moisture environments.
Why Choose Moisture-Resistant MDF for Specific Applications?
Moisture-resistant MDF is specifically engineered to withstand higher humidity levels, making it suitable for areas like kitchens and bathrooms. This type of MDF is treated with additives that enhance its resistance to water damage, thus extending its lifespan in challenging environments. B2B buyers should consider the potential for moisture exposure in their applications to justify the higher cost compared to standard MDF.
How Does Fire-Retardant MDF Enhance Safety in Commercial Spaces?
Fire-retardant MDF is designed to meet stringent fire safety regulations, incorporating materials that slow the spread of flames. This type is ideal for commercial buildings and public spaces where safety is a priority. When purchasing fire-retardant MDF, buyers must ensure compliance with local fire codes and consider the potential need for specialized installation techniques.
What Are the Advantages of High-Density MDF in Premium Products?
High-density MDF offers superior strength and durability, making it an excellent choice for high-end furniture and musical instruments. Its denser composition allows for finer details and a smoother finish, enhancing the overall aesthetic appeal. However, the increased weight and cost may be a consideration for buyers looking to balance quality with budget constraints.
Why Consider Eco-Friendly MDF for Sustainable Projects?
Eco-friendly MDF is produced from recycled materials and is often low in formaldehyde, making it a safer option for indoor environments. This type appeals to businesses focused on sustainability and meeting green building standards. Buyers should assess the availability of eco-friendly MDF in their region and be prepared for potentially higher prices due to its sustainable manufacturing processes.
Related Video: MDF and HDF
Key Industrial Applications of mdf board manufacturer
Industry/Sector | Specific Application of MDF Board Manufacturer | Value/Benefit for the Business | Key Sourcing Considerations for this Application |
---|---|---|---|
Furniture Manufacturing | Production of cabinets, tables, and shelving units | MDF provides a cost-effective solution with high durability and aesthetic finish. | Ensure compliance with international standards and certifications for quality. |
Interior Design & Décor | Wall paneling and custom fixtures | Offers design flexibility and ease of installation, enhancing interior aesthetics. | Look for suppliers with a variety of finishes and custom options. |
Construction & Building | Partition walls and acoustic panels | Provides sound insulation and can be customized for fire-resistance. | Verify the fire ratings and acoustic properties as per local regulations. |
Automotive Industry | Interior components such as dashboards and trims | Lightweight and easy to mold, improving fuel efficiency and design. | Assess the supplier’s capability to meet specific automotive standards. |
Retail Displays | Point-of-sale displays and merchandising units | Enhances product presentation and can be tailored to branding needs. | Consider the lead time for custom designs and the ability to scale production. |
How is MDF Board Manufacturer Used in Furniture Manufacturing?
In the furniture manufacturing sector, MDF boards are primarily utilized for creating cabinets, tables, and shelving units. The material’s affordability, combined with its durability, makes it an ideal choice for mass production. MDF boards can be easily shaped and finished, allowing manufacturers to produce a wide range of aesthetically pleasing designs. International buyers should focus on sourcing MDF that meets their regional quality standards and specifications, ensuring the final products align with consumer expectations.
What Role Does MDF Play in Interior Design & Décor?
MDF boards are widely used in interior design for applications such as wall paneling and custom fixtures. Their versatility allows designers to create unique and stylish interiors that can be tailored to specific themes or preferences. The ease of installation and finishing options available with MDF products enables designers to execute complex designs efficiently. Buyers should prioritize suppliers that offer a diverse range of finishes and can accommodate custom requests to meet specific project requirements.
How is MDF Beneficial for Construction & Building?
In the construction sector, MDF boards serve as an excellent material for partition walls and acoustic panels. Their sound insulation properties help create quieter environments, while their customizable nature allows for compliance with various fire-resistance standards. When sourcing MDF for construction applications, it is crucial for international buyers to verify compliance with local building codes and regulations to ensure safety and quality.
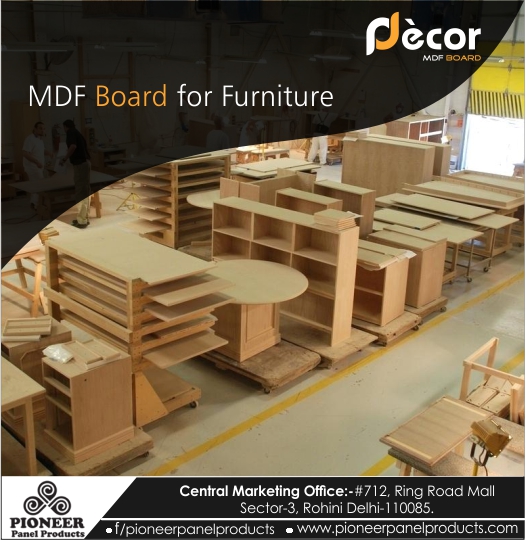
A stock image related to mdf board manufacturer.
Why is MDF Important in the Automotive Industry?
The automotive industry utilizes MDF boards for manufacturing lightweight interior components, such as dashboards and trims. The lightweight nature of MDF contributes to improved fuel efficiency, while its moldability allows for intricate designs that enhance the vehicle’s interior aesthetics. Buyers in this sector should evaluate suppliers based on their ability to meet stringent automotive industry standards and specifications.
How Does MDF Enhance Retail Displays?
In retail, MDF is commonly used for creating point-of-sale displays and merchandising units. The material’s ability to be customized ensures that displays can be tailored to fit branding and marketing strategies effectively. Additionally, MDF’s durability allows for repeated use in various retail contexts. When sourcing MDF for retail applications, businesses should consider the supplier’s capacity for custom designs and the potential lead times involved in production.
3 Common User Pain Points for ‘mdf board manufacturer’ & Their Solutions
Scenario 1: Inconsistent Quality of MDF Boards
The Problem:
International B2B buyers often face significant challenges when sourcing MDF boards due to quality inconsistency. For instance, a furniture manufacturer in South America may receive a batch of MDF boards that vary in density and finish from what was previously ordered. This inconsistency can lead to production delays, increased costs, and ultimately, dissatisfaction from their clients. Moreover, if the boards are not up to standard, the final products may suffer in durability and appearance, tarnishing the brand’s reputation.
The Solution:
To mitigate the risk of inconsistent quality, buyers should establish a comprehensive supplier evaluation process. This includes requesting samples from potential MDF board manufacturers and conducting thorough quality inspections. Buyers should specify detailed requirements regarding density, thickness, and surface finish in their purchase agreements. Additionally, developing a long-term partnership with a single manufacturer can yield better quality control, as they will be more familiar with the buyer’s specific needs. Regular audits and feedback sessions can also help maintain standards and address any quality concerns proactively.
Scenario 2: Limited Availability of Eco-Friendly MDF Options
The Problem:
As global awareness of environmental issues rises, many companies in Europe and Africa are under pressure to use sustainable materials. However, they often struggle to find MDF boards that are produced from recycled materials or without harmful adhesives. This situation not only complicates compliance with environmental regulations but can also alienate eco-conscious customers who prioritize sustainability in their purchasing decisions.
The Solution:
B2B buyers should actively seek out manufacturers who specialize in eco-friendly MDF boards. This can involve researching suppliers that are certified by recognized environmental standards, such as the Forest Stewardship Council (FSC) or those offering CARB-compliant products. Buyers can also engage in discussions with suppliers about their production processes and the materials used. Attending industry trade shows focused on sustainable building materials can provide valuable networking opportunities to discover manufacturers committed to environmentally friendly practices. Furthermore, buyers can consider forming groups with other businesses to increase their purchasing power and negotiate better terms for sustainable options.
Scenario 3: Complicated Sizing and Customization Requirements
The Problem:
Many B2B buyers encounter difficulties when it comes to specific sizing and customization of MDF boards. A construction company in the Middle East, for example, may require boards cut to unique dimensions for a specific project but finds that many manufacturers offer only standard sizes. This limitation can lead to additional costs for cutting and processing, which can affect project timelines and budgets.
The Solution:
To address these challenges, buyers should clearly communicate their sizing and customization needs upfront. When soliciting quotes from manufacturers, they should specify not only the dimensions required but also any additional custom features, such as pre-drilled holes or special finishes. It is advisable to work with manufacturers that have flexible production capabilities and a track record of accommodating custom orders. Building a relationship with a supplier who understands the buyer’s project requirements can streamline the process and reduce costs. Additionally, implementing advanced project management tools can help keep track of specifications and deadlines, ensuring that custom orders are fulfilled accurately and on time.
Strategic Material Selection Guide for mdf board manufacturer
What Are the Key Materials Used in MDF Board Manufacturing?
MDF (Medium Density Fiberboard) is a versatile engineered wood product made from wood fibers, wax, and resin. The choice of material significantly influences the performance, cost, and application of MDF boards. Here, we analyze several common materials used in MDF production, focusing on their properties, advantages, disadvantages, and considerations for international B2B buyers.
Which Wood Types Are Commonly Used for MDF Production?
1. Pine Wood
Key Properties: Pine wood fibers are lightweight and have a good strength-to-weight ratio. They provide excellent bonding properties when mixed with adhesives, making them suitable for MDF production.
Pros & Cons: Pine is relatively inexpensive and widely available, making it a cost-effective option. However, it may not be as durable as hardwood alternatives, leading to potential issues in high-stress applications.
Impact on Application: Pine MDF is often used in furniture and cabinetry, where aesthetic appeal and moderate durability are sufficient. Its compatibility with various finishes enhances its usability.
Considerations for Buyers: Buyers in regions like Africa and South America should ensure compliance with local environmental standards related to sourcing pine. Additionally, understanding the availability of pine in local markets can influence production timelines.
2. Oak Wood
Key Properties: Oak is known for its strength, durability, and aesthetic appeal. It has a high density, which contributes to its resistance to wear and tear.
Pros & Cons: Oak MDF offers superior durability and a premium finish, making it ideal for high-end furniture and cabinetry. However, it comes at a higher cost, which may not be suitable for budget-conscious projects.
Impact on Application: Due to its robust nature, oak MDF is often used in applications requiring longevity, such as flooring and high-quality furniture.
Considerations for Buyers: Buyers from Europe and the Middle East should be aware of the stringent compliance standards for oak sourcing, including certification for sustainable forestry practices.
3. Birch Wood
Key Properties: Birch wood is characterized by its fine grain and light color, making it aesthetically pleasing. It has good strength and is relatively easy to work with.
Pros & Cons: Birch MDF is known for its excellent machining properties and surface finish, making it suitable for detailed work. However, it can be more expensive than other wood types, which may limit its use in large-scale projects.
Impact on Application: Birch MDF is frequently used in cabinetry, decorative panels, and high-end furniture due to its attractive appearance and workability.
Considerations for Buyers: Buyers in regions like Australia and the UAE should consider the cost implications of sourcing birch, as well as any import tariffs that may apply.
4. Poplar Wood
Key Properties: Poplar wood is lightweight and has a straight grain, which contributes to ease of machining. It has a moderate density and good bonding characteristics.
Pros & Cons: Poplar MDF is cost-effective and suitable for a variety of applications, including interior furnishings. However, it may not offer the same level of durability as hardwoods, which can be a limitation in high-stress environments.
Impact on Application: Poplar MDF is often used for applications where weight savings are essential, such as in lightweight furniture and temporary structures.
Considerations for Buyers: International buyers should assess the availability of poplar in their regions and consider the environmental impact of sourcing practices.
Summary Table of Material Selection for MDF Board Manufacturing
Material | Typical Use Case for MDF Board Manufacturer | Key Advantage | Key Disadvantage/Limitation | Relative Cost (Low/Med/High) |
---|---|---|---|---|
Pine Wood | Furniture, cabinetry | Cost-effective and widely available | Less durable than hardwood alternatives | Low |
Oak Wood | High-end furniture, cabinetry | Superior durability and aesthetic appeal | Higher cost | High |
Birch Wood | Cabinetry, decorative panels | Excellent machining properties | More expensive than other woods | Med |
Poplar Wood | Lightweight furniture, temporary structures | Cost-effective and easy to work with | Lower durability in high-stress areas | Low |
By understanding the properties and implications of these materials, international B2B buyers can make informed decisions that align with their specific needs and regional considerations.
In-depth Look: Manufacturing Processes and Quality Assurance for mdf board manufacturer
What Are the Key Stages in the Manufacturing Process of MDF Boards?
The manufacturing of Medium Density Fiberboard (MDF) involves several critical stages that ensure the final product meets quality and performance standards. Understanding these stages can help international B2B buyers evaluate suppliers effectively.
Material Preparation: What Raw Materials Are Used?
The first step in the MDF manufacturing process is the preparation of raw materials. The most common materials used include wood fibers from various sources such as pine, oak, and birch. Suppliers often utilize wood chips, shavings, and sawdust, which are processed to create a uniform fiber consistency.
- Wood Debarking and Chipping: Logs are debarked and chipped into smaller pieces. This process is crucial as it prepares the wood for further processing.
- Fiber Separation: The chips are subjected to mechanical and thermal treatments that break them down into fibers. This is often done using a refiner or a mechanical pulping process.
Forming: How Are MDF Boards Shaped?
Once the fibers are prepared, they are mixed with adhesive resins to enhance bonding and durability. The mixture is then formed into mats.
- Mat Formation: The fiber-resin mixture is spread onto a forming table, where it is compressed into mats. This stage is vital as it determines the board’s density and thickness.
- Pressing: The formed mats are subjected to high pressure and temperature in a hot press. This process not only consolidates the mats into solid boards but also cures the adhesive, ensuring strong bonds.
Assembly: What Additional Features Are Included?
After the boards are formed, they may undergo additional processes to enhance their properties.
- Trimming and Cutting: The large MDF panels are trimmed to specific dimensions as per customer requirements. This ensures uniformity and meets client specifications.
- Surface Treatment: Depending on the end-use, boards may receive surface treatments such as sanding, priming, or veneering to improve aesthetics and performance.
Finishing: What Final Touches Are Applied?
The finishing stage involves several treatments to enhance the board’s appearance and durability.
- Coating: MDF boards can be coated with various finishes, including melamine, lacquer, or paint. This not only improves visual appeal but also adds a layer of protection against moisture and wear.
- Quality Control: Throughout the manufacturing process, quality checks are performed to ensure that the boards meet industry standards.
How Is Quality Assurance Implemented in MDF Manufacturing?
Quality assurance (QA) is a critical aspect of MDF manufacturing, ensuring that the final product meets international and industry-specific standards.
Which International Standards Are Relevant for MDF Boards?
International standards such as ISO 9001 play a significant role in maintaining quality in MDF manufacturing. ISO 9001 focuses on quality management systems, ensuring that manufacturers consistently provide products that meet customer and regulatory requirements.
- CE Marking: For products sold in the European market, CE marking is essential, indicating compliance with safety, health, and environmental protection standards.
- API Standards: In some markets, adherence to American Petroleum Institute (API) standards may be necessary, especially for MDF used in specific industrial applications.
What Are the Key Quality Control Checkpoints in MDF Production?
Quality control in MDF manufacturing typically includes several checkpoints throughout the production process:
- Incoming Quality Control (IQC): Raw materials are inspected upon arrival to ensure they meet specified standards. This includes checking for moisture content, fiber quality, and contaminants.
- In-Process Quality Control (IPQC): During production, continuous monitoring occurs at various stages, including fiber preparation and pressing. This helps identify and rectify issues early.
- Final Quality Control (FQC): Once the boards are completed, they undergo final inspections for physical dimensions, surface quality, and overall performance.
What Testing Methods Are Commonly Used for MDF Boards?
B2B buyers should be aware of the various testing methods used to ensure MDF boards meet required specifications:
- Physical Testing: This includes tests for density, moisture content, and thickness, which are crucial for assessing the board’s structural integrity.
- Mechanical Testing: Tests for bending strength, tensile strength, and internal bond strength help determine the MDF’s durability and suitability for different applications.
- Environmental Testing: For products intended for specific markets, testing for emissions (such as formaldehyde levels) is essential to comply with health and safety regulations.
How Can B2B Buyers Verify Supplier Quality Control?
To ensure that suppliers maintain high-quality standards, B2B buyers should implement several verification strategies:
- Supplier Audits: Conducting audits of potential suppliers can provide insights into their manufacturing processes, quality control measures, and adherence to international standards.
- Quality Reports: Requesting detailed quality reports, including results from testing and inspections, can help buyers assess a supplier’s commitment to quality.
- Third-Party Inspections: Engaging third-party inspection services can provide an unbiased evaluation of a supplier’s quality control processes and products.
What Are the Specific Quality Control Nuances for International Buyers?
For international B2B buyers, particularly those from Africa, South America, the Middle East, and Europe, understanding the nuances of quality control is crucial:
- Regulatory Compliance: Familiarize yourself with local regulations and standards applicable to MDF products in your region, as these can vary significantly.
- Cultural Considerations: Building relationships with suppliers in different regions may require understanding cultural nuances that affect business practices and quality expectations.
- Logistical Challenges: Be aware of the logistics involved in transporting MDF boards internationally, including potential impacts on product quality during shipping.

A stock image related to mdf board manufacturer.
By understanding the manufacturing processes and quality assurance measures in MDF production, international B2B buyers can make informed decisions, ensuring they source high-quality products that meet their specific requirements.
Practical Sourcing Guide: A Step-by-Step Checklist for ‘mdf board manufacturer’
In today’s competitive market, sourcing high-quality MDF boards requires a strategic approach. This step-by-step checklist will guide international B2B buyers, particularly from Africa, South America, the Middle East, and Europe, through the essential steps to ensure they select the right MDF board manufacturer.
Step 1: Define Your Technical Specifications
Before initiating the sourcing process, clearly outline your technical specifications for MDF boards. Consider factors such as thickness, density, surface finish, and intended application. Having precise specifications helps you communicate effectively with suppliers and ensures that the products meet your quality standards.
- Thickness and Density: Specify the required thickness (e.g., 18mm, 25mm) and density (e.g., standard, high-density) based on your project needs.
- Surface Finish: Determine if you need raw MDF, veneered, or laminated options for aesthetic or functional purposes.
Step 2: Conduct Market Research
Perform thorough market research to identify potential manufacturers of MDF boards. Utilize online platforms, industry reports, and trade shows to gather a list of suppliers. Understanding the market landscape will help you compare various manufacturers effectively.
- Industry Directories: Use platforms like Alibaba, Global Sources, or local trade associations to find reputable suppliers.
- Competitor Analysis: Look into where competitors source their MDF boards to uncover potential suppliers.
Step 3: Verify Supplier Certifications
Ensure that your selected suppliers have the necessary certifications to guarantee product quality and compliance with international standards. Certifications like ISO 9001 and CARB compliance can indicate a manufacturer’s commitment to quality and environmental responsibility.
- Quality Assurance: Confirm that the manufacturer has a quality management system in place.
- Environmental Standards: Check for certifications that demonstrate compliance with environmental regulations, especially if you are sourcing from regions with stringent laws.
Step 4: Request Samples for Evaluation
Before making a bulk purchase, request samples of the MDF boards to assess their quality. This step is crucial to ensure that the product meets your specifications and expectations.
- Quality Assessment: Evaluate the samples for physical attributes such as surface smoothness, edge finish, and structural integrity.
- Performance Testing: If applicable, conduct tests for moisture resistance, durability, and other performance metrics relevant to your application.
Step 5: Evaluate Potential Suppliers
Engage in a thorough evaluation of potential suppliers. This includes reviewing company profiles, requesting case studies, and seeking references from other buyers in your industry or region.
- Company Stability: Assess the supplier’s financial stability and operational capacity to fulfill your order volume.
- Past Performance: Look for testimonials or reviews that speak to the reliability and quality of the supplier’s products.
Step 6: Negotiate Terms and Conditions
Once you have shortlisted suppliers, initiate negotiations on pricing, delivery timelines, and payment terms. Clear and mutually agreed-upon terms will help prevent misunderstandings later in the process.
- Pricing Structures: Discuss bulk pricing options and potential discounts for long-term contracts.
- Delivery and Logistics: Confirm lead times and shipping arrangements to ensure timely delivery to your location.
Step 7: Finalize the Contract
After reaching an agreement, draft a formal contract that outlines all terms, conditions, and specifications. A well-structured contract protects both parties and sets clear expectations.
- Legal Considerations: Include clauses that address quality assurance, payment schedules, and dispute resolution mechanisms.
- Review Period: Allow for a review period before finalizing to ensure all details are accurate and agreed upon.
By following this checklist, international B2B buyers can streamline their sourcing process for MDF boards, ensuring they partner with reliable manufacturers who meet their specific needs.
Comprehensive Cost and Pricing Analysis for mdf board manufacturer Sourcing
What Are the Key Cost Components in MDF Board Manufacturing?
When sourcing MDF boards, understanding the cost structure is critical for international B2B buyers. The primary cost components include:
-
Materials: The choice of wood fibers significantly impacts costs. Commonly used materials include pine, oak, and birch, with prices varying based on availability and quality. Sourcing from local suppliers may reduce costs.
-
Labor: Labor costs depend on the manufacturing location. Regions with lower labor costs, such as some parts of Africa and South America, may offer competitive pricing. However, skilled labor for quality control can increase expenses.
-
Manufacturing Overhead: This includes utilities, factory rent, and equipment maintenance. Efficient manufacturing processes can help mitigate overhead costs.
-
Tooling: Initial tooling costs for specialized machinery can be high. However, these costs can be amortized over larger production runs, benefiting bulk buyers.
-
Quality Control (QC): Ensuring product quality may involve additional costs for testing and certification. Certifications like ISO can enhance product value but may also add to the price.
-
Logistics: Transportation costs can vary significantly, especially for international shipping. Factors like distance, shipping method, and customs duties will influence overall logistics expenses.
-
Margin: Manufacturers typically add a profit margin to their costs. Understanding the competitive landscape can help buyers negotiate better pricing.
How Do Pricing Influencers Affect MDF Board Costs?
Pricing for MDF boards is influenced by various factors, particularly relevant for buyers from Africa, South America, the Middle East, and Europe:
-
Volume and Minimum Order Quantity (MOQ): Higher order volumes can lead to discounted pricing. Buyers should assess their needs carefully to negotiate favorable terms with suppliers.
-
Specifications and Customization: Custom MDF boards may incur additional costs due to unique specifications. Buyers should clearly define their requirements to avoid unexpected expenses.
-
Material Quality and Certifications: The quality of raw materials and relevant certifications can drive prices up. Buyers should evaluate the importance of certifications for their markets when making purchasing decisions.
-
Supplier Factors: Supplier reliability, production capacity, and reputation can impact pricing. Engaging with suppliers who have a proven track record can mitigate risks associated with quality and delivery timelines.
-
Incoterms: Understanding Incoterms is crucial for international transactions. Terms like FOB (Free On Board) or CIF (Cost Insurance and Freight) can significantly affect landed costs.
What Are the Best Buyer Tips for Cost-Efficient MDF Board Sourcing?
For international B2B buyers looking to optimize their sourcing strategy for MDF boards, consider the following tips:
-
Negotiate Effectively: Don’t hesitate to negotiate terms with suppliers. Leverage your order volume and long-term potential to secure better pricing.
-
Assess Total Cost of Ownership (TCO): Look beyond the purchase price. Evaluate the entire lifecycle cost, including logistics, maintenance, and potential waste.
-
Understand Pricing Nuances: Be aware of regional pricing variations. For instance, suppliers in Europe may have different pricing structures compared to those in Africa or South America due to local market conditions.
-
Conduct Market Research: Regularly analyze market trends and price fluctuations. This knowledge can empower buyers during negotiations and sourcing decisions.
-
Build Long-Term Relationships: Establishing strong relationships with suppliers can lead to more favorable pricing and terms over time. Loyalty can often translate into better service and support.
Conclusion
While this analysis provides a comprehensive overview of the cost structure and pricing influencers in MDF board manufacturing, it is essential for buyers to conduct their own research and engage in thorough negotiations. Prices can vary significantly based on numerous factors, and being informed will help buyers make better purchasing decisions.
Alternatives Analysis: Comparing mdf board manufacturer With Other Solutions
When considering the procurement of wood-based products, especially for international B2B buyers, it is crucial to evaluate the alternatives to MDF (Medium Density Fiberboard) to ensure you make an informed decision that aligns with your business needs. This section explores viable alternatives to MDF, highlighting their advantages and disadvantages in comparison to MDF board manufacturing.
Comparison Aspect | Mdf Board Manufacturer | Plywood Manufacturer | Particle Board Manufacturer |
---|---|---|---|
Performance | Good durability, smooth finish, and consistent quality. | High strength, moisture-resistant variants available. | Lower strength, but suitable for low-load applications. |
Cost | Moderate cost, often higher than particle board but lower than plywood. | Generally higher due to material quality and manufacturing process. | Usually the lowest cost among alternatives, making it budget-friendly. |
Ease of Implementation | Requires specialized tools for cutting and finishing. | Easy to work with; can be cut and shaped with standard tools. | Very easy to handle, can be cut with minimal tools. |
Maintenance | Low maintenance, but can be sensitive to moisture. | Requires sealing for moisture resistance; generally durable. | Low maintenance; however, susceptible to damage from moisture. |
Best Use Case | Ideal for furniture, cabinetry, and decorative applications. | Best for structural applications, cabinetry, and high-quality furniture. | Suitable for low-cost furniture, packaging, and decorative uses. |
What are the Advantages and Disadvantages of Plywood as an Alternative to MDF?
Plywood is a popular alternative to MDF, made from layers of wood veneer glued together. Its primary advantage lies in its strength and durability, making it suitable for structural applications. Plywood can also be treated to enhance moisture resistance, making it an excellent choice for environments with high humidity. However, it generally comes at a higher cost compared to MDF, which may not be suitable for all budgets. Additionally, plywood may have a less uniform surface, requiring more finishing work.
How Does Particle Board Compare with MDF in Terms of Cost and Performance?
Particle board, constructed from wood chips, sawmill shavings, and a resin binder, is typically the most cost-effective option available. Its lower price point makes it an attractive choice for budget-conscious buyers. However, particle board lacks the strength and durability of both MDF and plywood, making it less suitable for high-load applications. Its susceptibility to moisture can lead to swelling and damage, which limits its use in certain environments. Despite this, it works well for low-cost furniture and applications where high strength is not a priority.
Conclusion: Which Wood-Based Solution is Right for Your Business Needs?
In choosing between MDF, plywood, and particle board, B2B buyers must consider the specific requirements of their projects. If durability and strength are paramount, plywood may be the best option despite its higher cost. Conversely, if budget constraints are significant, particle board offers an economical alternative for lower-load applications. MDF provides a balanced choice, delivering a good mix of performance and affordability for decorative and furniture applications. Ultimately, the decision should align with both the technical specifications required and the financial parameters of the project.
Essential Technical Properties and Trade Terminology for mdf board manufacturer
What Are the Essential Technical Properties of MDF Board?
When sourcing MDF (Medium Density Fiberboard) for various applications, understanding its technical properties is crucial for B2B buyers. Here are some of the key specifications to consider:
1. Material Grade
MDF is categorized into different grades based on its density and intended use. Common grades include standard MDF, moisture-resistant MDF, and fire-rated MDF. The choice of grade affects durability, resistance to moisture, and fire safety, which are critical factors for construction and furniture applications. Buyers should select the appropriate grade based on their specific requirements to ensure longevity and compliance with safety standards.
2. Density
The density of MDF typically ranges from 600 to 800 kg/m³. Higher density boards are generally stronger and provide better sound insulation, making them suitable for high-quality furniture and cabinetry. Conversely, lower density boards are lighter and more cost-effective, often used in applications where structural strength is less critical. Understanding density helps buyers match the MDF with the intended use, optimizing performance and cost.
3. Tolerance
Tolerance refers to the allowable variation in the dimensions of MDF boards. Standard tolerances are typically ±1mm for thickness and ±2mm for width and length. Precise tolerances are essential for applications requiring exact fitting, such as cabinetry and millwork. Buyers should inquire about the manufacturer’s tolerance standards to ensure compatibility with their project specifications.
4. Surface Finish
The surface finish of MDF can significantly affect its aesthetic appeal and suitability for various applications. Options include raw, primed, or laminated finishes. A smooth finish is essential for painting or veneering, while laminated surfaces offer additional durability and moisture resistance. Buyers should consider the desired finish based on their project needs, as this impacts both appearance and performance.
5. Formaldehyde Emissions
Formaldehyde is a common adhesive used in MDF production, and its emissions can vary significantly between manufacturers. Low-emission MDF is increasingly preferred, especially in regions with stringent environmental regulations. B2B buyers should verify compliance with standards such as E1 or E0 to ensure a safe product for indoor use.
Which Trade Terminology Should International B2B Buyers Understand?
Familiarity with industry jargon is crucial for effective communication and negotiation in the MDF market. Here are some common terms:
1. OEM (Original Equipment Manufacturer)
OEM refers to a company that produces products that are sold under another brand’s name. For MDF buyers, understanding OEM relationships can help in sourcing high-quality products from reputable manufacturers without incurring brand premiums.
2. MOQ (Minimum Order Quantity)
MOQ is the smallest quantity a supplier is willing to sell. It is crucial for buyers to know the MOQ to plan their purchases effectively and manage inventory costs. Negotiating MOQs can also lead to better pricing or terms.
3. RFQ (Request for Quotation)
An RFQ is a document used to invite suppliers to bid on specific products or services. For MDF buyers, submitting an RFQ can facilitate competitive pricing and terms from multiple manufacturers, ensuring they receive the best possible deal.
4. Incoterms (International Commercial Terms)
Incoterms define the responsibilities of buyers and sellers regarding shipping, insurance, and tariffs. Understanding Incoterms like FOB (Free on Board) or CIF (Cost, Insurance, and Freight) helps buyers clarify their obligations and costs associated with international shipping, thus avoiding misunderstandings.
5. Lead Time
Lead time refers to the time taken from placing an order to delivery. For B2B buyers, understanding lead times is essential for project planning and ensuring timely availability of materials. Buyers should always confirm lead times with suppliers to align their production schedules.
By grasping these technical properties and trade terminologies, international B2B buyers can make informed decisions when sourcing MDF boards, leading to successful procurement and project execution.
Navigating Market Dynamics and Sourcing Trends in the mdf board manufacturer Sector
What Are the Current Market Dynamics Affecting MDF Board Manufacturing?
The MDF (Medium Density Fiberboard) market is experiencing robust growth driven by several global factors. Key drivers include the increasing demand for sustainable building materials, urbanization, and the rise of the furniture and interior design industries. Particularly in regions like Africa, South America, the Middle East, and Europe, international B2B buyers are witnessing a shift towards eco-friendly products that align with green building standards. As companies seek to enhance their sustainability profiles, MDF manufacturers are innovating by using recycled wood fibers and sustainable adhesives, which appeals to environmentally conscious buyers.
Emerging technologies are also reshaping the MDF manufacturing landscape. The adoption of automation and Industry 4.0 technologies is streamlining production processes, improving quality control, and enhancing operational efficiency. For B2B buyers, this means greater reliability and consistency in product quality. Additionally, digital platforms for sourcing are gaining traction, allowing buyers to access a wider range of suppliers and products, which fosters competitive pricing and improved supply chain transparency.
How Are Sustainability and Ethical Sourcing Impacting the MDF Board Sector?
Sustainability is a critical concern for today’s B2B buyers in the MDF sector. The environmental impact of MDF production, particularly concerning deforestation and carbon emissions, has led to increased scrutiny of sourcing practices. Buyers are increasingly prioritizing suppliers that demonstrate a commitment to ethical sourcing, which often involves obtaining wood from certified sustainable forests.
Certifications like FSC (Forest Stewardship Council) and PEFC (Programme for the Endorsement of Forest Certification) are becoming essential for manufacturers aiming to appeal to international markets. These certifications not only help in minimizing environmental impact but also assure buyers of responsible sourcing practices. Furthermore, the use of low-VOC (Volatile Organic Compounds) adhesives and finishes is gaining importance, as buyers seek to minimize health risks associated with indoor air quality.
By prioritizing sustainable and ethical sourcing, B2B buyers can enhance their brand reputation while supporting global efforts to combat climate change. This focus on sustainability also opens up opportunities for collaboration with suppliers who are innovating in this space, leading to new product offerings that meet evolving market demands.
What Has Been the Evolution of the MDF Board Manufacturing Sector?
The MDF board manufacturing sector has evolved significantly since its inception in the 1960s. Initially developed as a cost-effective alternative to plywood, MDF gained popularity due to its versatility and ease of machining. Over the decades, advancements in technology and manufacturing processes have improved the quality and consistency of MDF products, making them a staple in the furniture and construction industries.
In recent years, the evolution has been marked by a stronger emphasis on sustainability and innovation. The introduction of environmentally friendly production methods and materials has reshaped the industry’s landscape, catering to a growing demand for sustainable building materials. This shift is particularly relevant for international B2B buyers who are looking for suppliers that not only provide high-quality products but also adhere to ethical and sustainable practices. As the market continues to evolve, staying informed about trends and innovations will be crucial for buyers seeking to maintain a competitive edge.
Frequently Asked Questions (FAQs) for B2B Buyers of mdf board manufacturer
-
How do I choose the right MDF board manufacturer for my business needs?
When selecting an MDF board manufacturer, consider their production capacity, quality certifications (such as ISO), and the variety of products they offer. Research their reputation by checking reviews and testimonials from previous clients. Additionally, inquire about their sourcing of raw materials and whether they use sustainable practices. It’s also beneficial to request samples to assess the quality of the MDF boards before committing to a larger order. -
What are the most common types of wood used in MDF board production?
The most common types of wood used in MDF board production include pine, oak, and birch. Pine is favored for its cost-effectiveness and good strength, while oak is valued for its durability and aesthetic appeal. Birch provides a lightweight option with excellent machining properties. Understanding the wood types can help you choose the right MDF for your specific applications, whether for furniture, cabinetry, or decorative elements. -
What customization options are available when sourcing MDF boards?
Many MDF board manufacturers offer customization options such as different thicknesses, sizes, and surface finishes. Some may provide special formulations for moisture resistance or fire retardancy. When discussing customization, clearly communicate your specifications and intended applications to ensure the manufacturer can meet your requirements. Always confirm lead times for custom orders, as they may differ from standard offerings. -
What is the minimum order quantity (MOQ) for MDF boards?
The minimum order quantity (MOQ) for MDF boards can vary significantly among manufacturers. Typically, MOQs can range from a few hundred to several thousand square meters, depending on the supplier’s production capabilities and your specific needs. It’s essential to clarify the MOQ during your discussions with potential suppliers, especially if you are a smaller business or just starting out. -
What payment terms should I expect when sourcing MDF boards internationally?
Payment terms can vary widely based on the manufacturer’s policies and your negotiation power. Common terms include a deposit upfront (usually 30-50%) with the balance due before shipment or upon delivery. Some suppliers may also offer letters of credit or payment through escrow services for added security. Always ensure that the payment terms are clearly outlined in the contract to avoid any misunderstandings later. -
How can I ensure quality assurance when purchasing MDF boards?
To ensure quality assurance, request certifications and quality control processes from the manufacturer. Inquire about their testing methods for density, moisture content, and formaldehyde emissions, which are crucial for safety standards. Additionally, consider arranging for third-party inspections or audits, especially if you are ordering large quantities or working with a new supplier. Consistent quality checks will help mitigate risks associated with inferior products. -
What logistics considerations should I take into account when importing MDF boards?
When importing MDF boards, consider logistics aspects such as shipping methods, lead times, and customs regulations in your country. Determine whether the supplier offers delivery services or if you need to arrange transportation. Be aware of potential tariffs or import duties that may apply, as these can impact overall costs. Collaborating with a freight forwarder can help streamline the import process and ensure compliance with local regulations. -
What factors influence the pricing of MDF boards in international markets?
The pricing of MDF boards in international markets is influenced by several factors, including raw material costs, production methods, and shipping expenses. Fluctuations in timber prices, currency exchange rates, and regional demand can also affect pricing. Additionally, manufacturers that prioritize sustainable practices may charge a premium for eco-friendly products. When sourcing, it’s advisable to obtain quotes from multiple suppliers to compare prices and negotiate favorable terms.
Important Disclaimer & Terms of Use
⚠️ Important Disclaimer
The information provided in this guide, including content regarding manufacturers, technical specifications, and market analysis, is for informational and educational purposes only. It does not constitute professional procurement advice, financial advice, or legal advice.
While we have made every effort to ensure the accuracy and timeliness of the information, we are not responsible for any errors, omissions, or outdated information. Market conditions, company details, and technical standards are subject to change.
B2B buyers must conduct their own independent and thorough due diligence before making any purchasing decisions. This includes contacting suppliers directly, verifying certifications, requesting samples, and seeking professional consultation. The risk of relying on any information in this guide is borne solely by the reader.
Strategic Sourcing Conclusion and Outlook for mdf board manufacturer
In the rapidly evolving landscape of MDF board manufacturing, strategic sourcing emerges as a critical component for international B2B buyers. By understanding the diverse wood types utilized in MDF production—such as pine, oak, and birch—buyers can better assess quality, durability, and cost-effectiveness. Establishing strong relationships with manufacturers not only enhances supply chain efficiency but also ensures compliance with sustainability standards, which are increasingly prioritized in global markets.
The value of strategic sourcing lies in its ability to mitigate risks associated with supply chain disruptions, particularly relevant for buyers in Africa, South America, the Middle East, and Europe. Engaging with reliable suppliers who prioritize innovation and quality can lead to significant long-term cost savings and improved product offerings.
As we look to the future, international B2B buyers should actively seek partnerships with MDF manufacturers that embrace sustainable practices and technological advancements. By prioritizing strategic sourcing, buyers can not only enhance their competitive edge but also contribute to a more sustainable industry. Now is the time to explore new opportunities and forge relationships that will drive growth and innovation in your projects.