Cut Costs with Water Jet Cutting China: The Ultimate Guide (2025)
Introduction: Navigating the Global Market for water jet cutting china
In the ever-evolving landscape of global manufacturing, sourcing reliable water jet cutting solutions from China presents both opportunities and challenges for international B2B buyers. The intricate nature of water jet cutting technology, which utilizes high-pressure water to cut through various materials, requires a nuanced understanding of equipment types, applications, and supplier capabilities. This guide serves as an essential resource, equipping buyers from Africa, South America, the Middle East, and Europe—such as those in Indonesia and Poland—with the knowledge necessary to navigate this complex market effectively.
Throughout this comprehensive guide, we will delve into the different types of water jet cutting systems available, explore their diverse applications across industries, and provide strategies for vetting potential suppliers. Understanding cost structures and logistical considerations will also be key themes, ensuring that buyers can make informed decisions that align with their operational needs and budget constraints. By addressing common pain points, such as quality assurance and supply chain reliability, this guide empowers international B2B buyers to confidently engage with the Chinese market, ultimately facilitating successful partnerships and fostering innovation within their own organizations.
Understanding water jet cutting china Types and Variations
Type Name | Key Distinguishing Features | Primary B2B Applications | Brief Pros & Cons for Buyers |
---|---|---|---|
Pure Water Jet Cutting | Uses only water to cut softer materials. | Food industry, textiles, and plastics. | Pros: Eco-friendly, minimal kerf. Cons: Limited to softer materials. |
Abrasive Water Jet Cutting | Incorporates abrasive materials for cutting harder substances. | Metal fabrication, aerospace, and automotive. | Pros: High precision, versatile. Cons: Higher operational costs due to abrasives. |
5-Axis Water Jet Cutting | Allows for complex geometries and angles. | Aerospace components, custom parts. | Pros: Greater design flexibility, intricate cuts. Cons: Higher machine cost and maintenance. |
Robotic Water Jet Cutting | Integrates robotics for automated cutting processes. | Large-scale manufacturing, automotive. | Pros: Increased efficiency, reduced labor costs. Cons: Initial setup cost can be high. |
Water Jet Cutting with CNC | Combines CNC technology for precise control. | Electronics, metal parts, and glass. | Pros: Excellent accuracy, repeatability. Cons: Requires skilled operators for setup. |
What are the Key Characteristics of Pure Water Jet Cutting?
Pure water jet cutting is characterized by its use of high-pressure water jets to cut through softer materials such as food products, textiles, and plastics. This method is highly eco-friendly, producing no harmful waste and requiring no toxic chemicals. B2B buyers should consider its suitability for applications where precision is less critical and the materials involved are less dense. While it offers an environmentally safe solution, its limitations in cutting harder materials can restrict its application scope.
How Does Abrasive Water Jet Cutting Stand Out?
Abrasive water jet cutting utilizes a mixture of water and abrasive particles, allowing it to effectively cut through harder materials like metals and stone. This versatility makes it ideal for industries such as aerospace, automotive, and metal fabrication. B2B buyers should evaluate the higher operational costs associated with abrasives against the benefits of precision and the ability to handle a wider range of materials. This type is particularly valuable in applications demanding high accuracy and intricate designs.
What Advantages Does 5-Axis Water Jet Cutting Offer?
5-axis water jet cutting stands out due to its ability to create complex geometries and perform cuts at various angles. This capability is essential for industries like aerospace, where precision and design intricacy are paramount. B2B buyers should weigh the benefits of greater design flexibility against the higher costs of the machinery and maintenance. This type is particularly advantageous for projects requiring detailed and custom components, making it a worthwhile investment for specialized manufacturing.
Why Choose Robotic Water Jet Cutting?
Robotic water jet cutting integrates robotic technology to automate the cutting process, significantly enhancing efficiency in large-scale manufacturing environments. This method is especially beneficial in the automotive sector, where speed and precision are critical. B2B buyers need to consider the initial setup costs, which can be substantial, but the long-term savings in labor and time often justify the investment. This technology is ideal for businesses looking to optimize production lines and reduce operational costs.
How Does Water Jet Cutting with CNC Enhance Precision?
Water jet cutting with CNC (Computer Numerical Control) technology combines the benefits of water jet cutting with the precision of computerized controls. This method is widely used in industries such as electronics and glass manufacturing. B2B buyers should note that while it offers excellent accuracy and repeatability, it requires skilled operators for effective setup and operation. This type is particularly suited for high-volume production runs where precision is non-negotiable, making it a critical component in modern manufacturing processes.
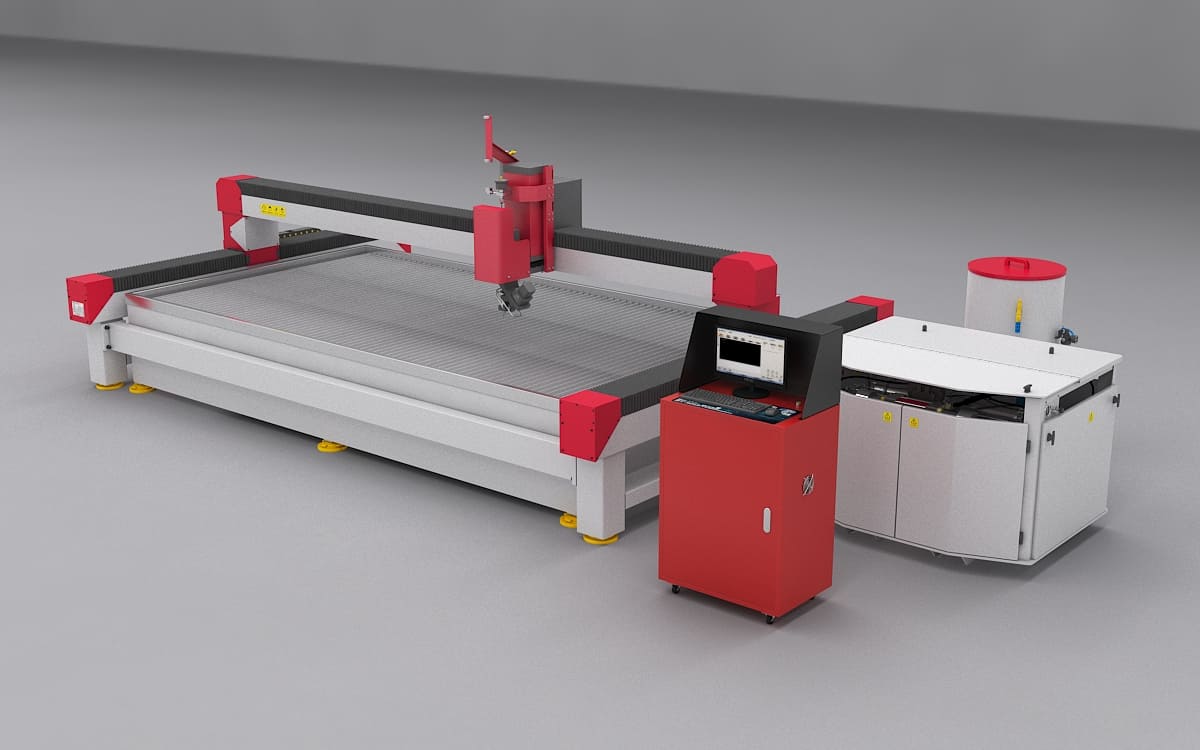
A stock image related to water jet cutting china.
Related Video: Water Jet Pressure ka Magic – High-Pressure Cutting Explained
Key Industrial Applications of water jet cutting china
Industry/Sector | Specific Application of Water Jet Cutting China | Value/Benefit for the Business | Key Sourcing Considerations for this Application |
---|---|---|---|
Aerospace | Precision cutting of complex aircraft components | Enhances safety and performance through precise cuts. | Certification standards, quality control, lead times. |
Automotive | Cutting of metal and composite materials | Reduces waste and improves material utilization. | Supplier reliability, technology compatibility. |
Metal Fabrication | Custom shapes and designs for various products | Offers flexibility and rapid prototyping capabilities. | Equipment maintenance, part tolerances, and costs. |
Architecture and Design | Artistic features and structural components | Enables intricate designs without compromising strength. | Material sourcing, design capabilities, and delivery timelines. |
Manufacturing | High-volume production of parts and components | Increases efficiency and reduces production costs. | Scalability, machine capabilities, and after-sales support. |
How is Water Jet Cutting Used in Aerospace?
In the aerospace industry, water jet cutting is employed for the precision cutting of complex aircraft components such as wing structures and fuselage panels. The ability to cut materials like titanium and aluminum without introducing heat distortion ensures high safety and performance standards. International buyers, particularly from Africa and Europe, must consider suppliers that meet stringent certification standards and can demonstrate robust quality control processes to ensure compliance with aerospace regulations.
What Role Does Water Jet Cutting Play in the Automotive Sector?
Water jet cutting is widely used in the automotive sector for cutting metal and composite materials, including parts for engines and interiors. This method minimizes waste and enhances material utilization, which is critical in a competitive market focused on cost efficiency. B2B buyers in South America and the Middle East should prioritize supplier reliability and the technology’s compatibility with existing manufacturing systems to ensure seamless integration and production continuity.
Why is Water Jet Cutting Essential for Metal Fabrication?
In metal fabrication, water jet cutting allows for the creation of custom shapes and designs for a variety of products, from furniture to industrial machinery. This technology supports flexibility in design and rapid prototyping, which is invaluable for businesses looking to innovate quickly. Buyers should assess equipment maintenance capabilities, part tolerances, and overall costs when sourcing water jet cutting services, especially in regions with fluctuating material prices like Africa.
How Does Water Jet Cutting Enhance Architectural Design?
Architects and designers utilize water jet cutting for creating artistic features and structural components that require intricate designs without compromising the strength of the materials. This capability is essential for modern architecture, which often blends aesthetics with functionality. Buyers in Europe and the Middle East should focus on material sourcing options, the supplier’s design capabilities, and delivery timelines to ensure that projects meet both artistic and structural requirements.
What Advantages Does Water Jet Cutting Offer in Manufacturing?
In the manufacturing sector, water jet cutting is employed for high-volume production of parts and components, providing increased efficiency and reduced production costs. This technology can handle a variety of materials, making it a versatile choice for manufacturers. International B2B buyers should evaluate scalability options, machine capabilities, and after-sales support when considering suppliers, particularly in emerging markets in South America and Africa where production demands are rapidly evolving.
Related Video: How Water Jet Cutting Can Slice Through Metal Like Butter | #FactTheFact-33 #short |
3 Common User Pain Points for ‘water jet cutting china’ & Their Solutions
Scenario 1: Navigating Quality Assurance in Water Jet Cutting Services
The Problem:
B2B buyers often face challenges related to quality assurance when sourcing water jet cutting services from China. Variability in material quality, precision, and adherence to specifications can lead to costly errors and delays. Buyers might receive subpar products that don’t meet their exact requirements, resulting in wasted resources and diminished trust in suppliers. This scenario is particularly prevalent in industries such as aerospace and automotive, where precision is paramount.
The Solution:
To mitigate these quality assurance issues, buyers should implement a rigorous supplier vetting process. This includes requesting samples and reviewing past project portfolios to assess the supplier’s capabilities. Buyers can also establish clear quality metrics and expectations in the initial agreement. It is beneficial to incorporate third-party quality assurance services or audits to verify that the supplier adheres to international standards. Additionally, engaging in regular communication and feedback loops throughout the production process can help maintain quality and address any discrepancies before they escalate.
Scenario 2: Overcoming Language and Cultural Barriers in Communication
The Problem:
International buyers often encounter significant language and cultural barriers when dealing with Chinese suppliers for water jet cutting services. Miscommunications can lead to misunderstandings regarding project specifications, timelines, and payment terms. This challenge can be particularly acute for companies in Africa and South America, where English may not be the primary language. Such barriers can result in delays, increased costs, and strained business relationships.
The Solution:
To address these communication challenges, buyers should consider employing bilingual staff or hiring a local intermediary familiar with both cultures and languages. Utilizing clear and concise written communication is essential; buyers should provide detailed specifications and use visual aids like diagrams and photos to clarify expectations. Additionally, leveraging technology such as translation tools or software can help bridge language gaps. Regular video calls can also foster better understanding and rapport, allowing for real-time clarification of any issues.
Scenario 3: Managing Logistics and Supply Chain Complexity
The Problem:
The complexity of logistics and supply chain management can be a significant pain point for B2B buyers sourcing water jet cutting services from China. Issues such as shipping delays, customs clearance problems, and unexpected tariffs can disrupt timelines and inflate costs. Buyers in regions like Europe or the Middle East may find themselves particularly vulnerable to these challenges due to varying regulations and trade policies.
The Solution:
To effectively manage logistics, buyers should work with logistics partners who have a deep understanding of international shipping and customs regulations. Establishing a clear timeline and buffer periods in contracts for potential delays can help mitigate risks. Buyers should also stay informed about trade policies and tariffs that may impact their costs and timelines, allowing them to adjust their sourcing strategies accordingly. Utilizing technology to track shipments and automate customs documentation can also streamline the process, making it easier to manage the complexities of international logistics.
By acknowledging and addressing these common pain points, international B2B buyers can better navigate the challenges of sourcing water jet cutting services from China, ultimately leading to more successful and sustainable business relationships.
Strategic Material Selection Guide for water jet cutting china
What Are the Key Materials Used in Water Jet Cutting in China?
Water jet cutting technology is versatile and can process a wide range of materials. Understanding the properties, advantages, and limitations of each material is crucial for international B2B buyers, especially those from Africa, South America, the Middle East, and Europe. Here, we analyze four common materials used in water jet cutting: steel, aluminum, glass, and stone.
How Does Steel Perform in Water Jet Cutting Applications?
Key Properties: Steel is known for its strength and durability. It has a high-temperature rating and excellent pressure resistance, making it suitable for various applications.
Pros & Cons: The primary advantage of using steel is its robustness, which allows for the production of durable end products. However, it can be relatively expensive compared to other materials and may require additional post-processing to achieve a smooth finish.
Impact on Application: Steel is compatible with a range of media, including water and abrasive materials, making it suitable for cutting thick sections.
Considerations for International Buyers: Buyers should ensure compliance with international standards such as ASTM and DIN. Additionally, the cost can vary significantly based on the grade of steel, which should be factored into procurement decisions.
What Are the Advantages of Using Aluminum in Water Jet Cutting?
Key Properties: Aluminum is lightweight yet strong, with good corrosion resistance and a lower melting point than steel.
Pros & Cons: The key advantage of aluminum is its lightweight nature, which makes it easier to handle and transport. However, it can be more susceptible to deformation under high-pressure conditions, which may affect precision.
Impact on Application: Aluminum is ideal for applications requiring a lightweight material, such as aerospace components. Its compatibility with various cutting media enhances its versatility.
Considerations for International Buyers: Buyers should be aware of the specific aluminum grades and their properties. Compliance with standards like JIS may be necessary, especially for clients in Japan or regions with strict regulatory environments.
Why Is Glass a Popular Choice for Water Jet Cutting?
Key Properties: Glass is brittle but can be cut with precision using water jet technology. It has a low thermal conductivity, which helps prevent cracking during the cutting process.
Pros & Cons: The primary advantage of glass cutting is the ability to create intricate designs without the risk of chipping. However, the brittleness of glass can lead to breakage if not handled properly.
Impact on Application: Glass is commonly used in architectural applications and decorative elements. Its compatibility with water jet cutting allows for complex shapes and designs.
Considerations for International Buyers: Buyers should consider the thickness and type of glass being cut, as different types may require specific handling and cutting techniques. Compliance with local building codes is also essential.
What Are the Key Considerations for Using Stone in Water Jet Cutting?
Key Properties: Stone is dense and durable, with high resistance to wear and tear. It can withstand high-pressure cutting without significant deformation.
Pros & Cons: The durability of stone makes it suitable for heavy-duty applications, such as countertops and flooring. However, the weight can complicate transportation and installation.
Impact on Application: Stone is ideal for high-end architectural applications where aesthetics and durability are paramount. Water jet cutting allows for detailed designs that traditional cutting methods cannot achieve.
Considerations for International Buyers: Buyers should be aware of the local availability of stone types and their respective cutting requirements. Compliance with industry standards is crucial, especially in regions with strict construction regulations.
Summary Table of Materials for Water Jet Cutting
Material | Typical Use Case for Water Jet Cutting China | Key Advantage | Key Disadvantage/Limitation | Relative Cost (Low/Med/High) |
---|---|---|---|---|
Steel | Structural components, machinery parts | High durability and strength | Higher cost, requires post-processing | High |
Aluminum | Aerospace parts, automotive components | Lightweight and corrosion-resistant | Susceptible to deformation | Medium |
Glass | Architectural features, decorative items | Precision cutting with intricate designs | Brittle, can break easily | Medium |
Stone | Countertops, flooring, monuments | High durability and aesthetic appeal | Heavy, complicates transportation | High |
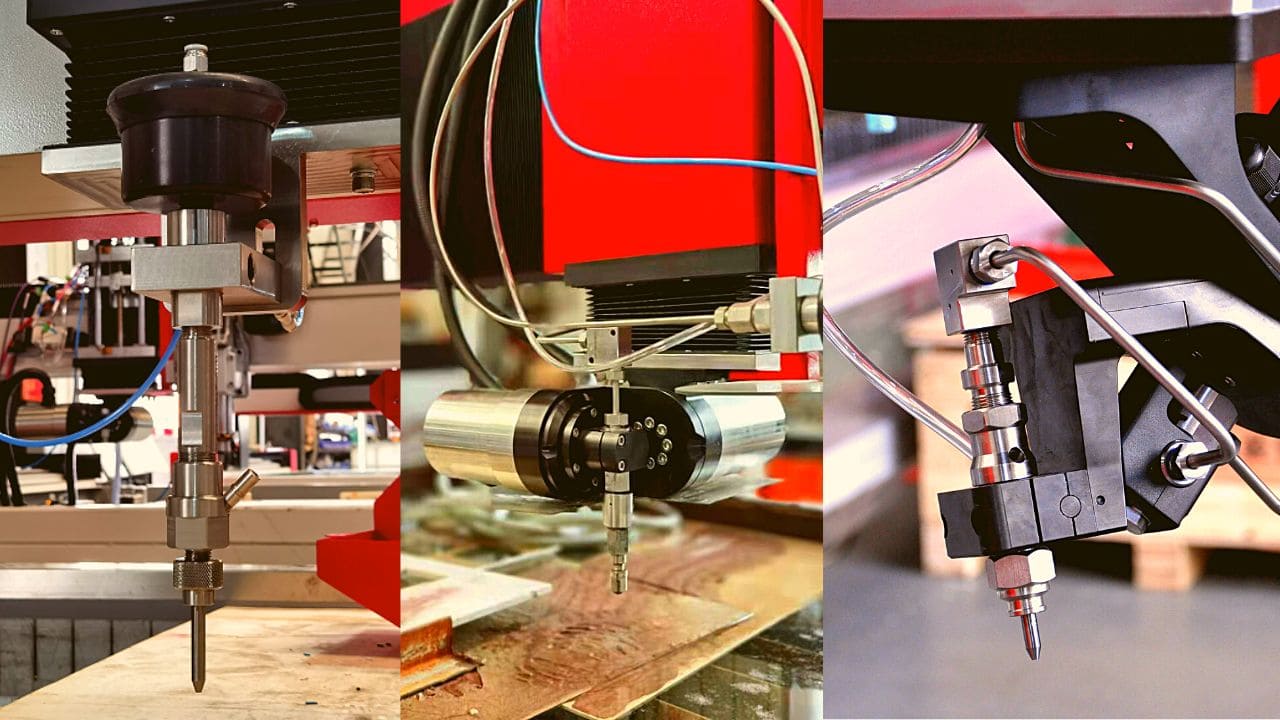
A stock image related to water jet cutting china.
This guide provides valuable insights for international B2B buyers looking to make informed decisions regarding material selection for water jet cutting applications in China. Understanding the unique properties and considerations of each material will help in optimizing procurement strategies and ensuring compliance with relevant standards.
In-depth Look: Manufacturing Processes and Quality Assurance for water jet cutting china
What Are the Key Manufacturing Processes for Water Jet Cutting in China?
The manufacturing process for water jet cutting involves several critical stages that ensure precision and quality. Understanding these stages can significantly aid international B2B buyers in making informed decisions when sourcing from China.
1. Material Preparation: What Steps Are Involved?
Material preparation is the first step in the water jet cutting process. This stage involves selecting the right type of material, which can range from metals like steel and aluminum to softer materials like rubber and plastics. The materials are then cleaned and inspected for defects to ensure they meet the required specifications.
Cutting plans are created using CAD (Computer-Aided Design) software, where the design is translated into a format that the water jet cutting machine can understand. The accurate setup of the material on the cutting bed is crucial, as any misalignment can lead to errors in the final product.
2. Forming: How Does the Water Jet Cutting Process Work?
The actual cutting process utilizes a high-pressure stream of water mixed with abrasives to cut through the material. This high-pressure water stream typically operates at pressures of 30,000 to 90,000 psi (pounds per square inch). The cutting head is maneuvered using CNC (Computer Numerical Control) technology, allowing for intricate shapes and designs to be achieved with high precision.
The advantages of water jet cutting include its ability to cut complex geometries without the need for secondary finishing operations, as well as its capability to work with a wide range of materials. This method is particularly beneficial for industries requiring detailed cuts, such as aerospace and automotive.
3. Assembly: What Are the Considerations?
Once the cutting is complete, the parts may need to be assembled into larger components or systems. This stage may involve welding, fastening, or additional machining. Effective communication between the manufacturing team and the buyer is essential to ensure that all specifications are met during the assembly phase.
4. Finishing: What Techniques Are Commonly Used?
Finishing processes are crucial for enhancing the appearance and performance of the cut parts. Techniques such as deburring, polishing, and surface coating are commonly employed. Depending on the end-use of the product, finishing can significantly impact durability and resistance to corrosion or wear.
How Is Quality Assurance Managed in Water Jet Cutting?
Quality assurance (QA) is vital in maintaining the standards expected by international buyers. Manufacturers in China often adhere to specific international standards to ensure product consistency and reliability.
1. What International Standards Are Relevant for Water Jet Cutting?
The most widely recognized international standard for quality management is ISO 9001. Compliance with ISO 9001 indicates that a manufacturer has implemented a robust quality management system that consistently produces products that meet customer and regulatory requirements.
In addition to ISO 9001, other industry-specific certifications may apply, such as CE marking for products sold in the European market and API (American Petroleum Institute) standards for oil and gas components. Understanding these certifications can help B2B buyers assess the credibility of potential suppliers.
2. What Are the Key Quality Control Checkpoints?
Quality control (QC) is typically structured into several checkpoints throughout the manufacturing process:
- Incoming Quality Control (IQC): This involves the inspection of raw materials upon arrival to ensure they meet specified criteria before processing begins.
- In-Process Quality Control (IPQC): This stage includes monitoring and inspecting the cutting process itself to detect any deviations from the standards in real-time.
- Final Quality Control (FQC): After the product is finished, a thorough inspection is conducted to confirm that it meets all specifications before shipment.
Employing these QC checkpoints helps minimize defects and ensures that only products meeting quality standards reach the buyer.
3. What Common Testing Methods Are Used?
Common testing methods for water jet cut products include dimensional inspections, surface roughness measurements, and strength tests. Techniques such as X-ray inspection and ultrasonic testing may also be used for critical applications, particularly in industries such as aerospace and automotive.
How Can B2B Buyers Verify Supplier Quality Control?
For international B2B buyers, verifying the quality control processes of potential suppliers is essential. Here are some actionable steps:
1. What Role Do Audits Play in Supplier Verification?
Conducting on-site audits is one of the most effective ways to assess a supplier’s quality control processes. During an audit, buyers can evaluate the manufacturing environment, inspect equipment, and review quality control documentation. This firsthand observation can provide insights into the supplier’s adherence to standards and practices.
2. How Can Buyers Leverage Reports and Certifications?
Buyers should request quality control reports and relevant certifications from potential suppliers. These documents should detail the QC processes, testing methods, and results of previous inspections. Reviewing these reports can help buyers assess whether a supplier’s quality assurance aligns with their requirements.
3. What Is the Importance of Third-Party Inspections?
Engaging third-party inspection services can add an additional layer of confidence. These independent inspections verify that the products meet specified quality standards before shipment. This practice is particularly beneficial for buyers from regions with stringent quality requirements, such as Europe and North America.
Conclusion: Why Is Quality Assurance Critical for International Buyers?
For international B2B buyers, particularly those from Africa, South America, the Middle East, and Europe, understanding the manufacturing processes and quality assurance practices in water jet cutting is crucial. By focusing on key manufacturing stages, relevant standards, and effective verification methods, buyers can ensure they partner with reliable suppliers who meet their quality expectations.
Practical Sourcing Guide: A Step-by-Step Checklist for ‘water jet cutting china’
To successfully procure water jet cutting services from suppliers in China, it’s vital to follow a structured approach that ensures quality and reliability. This checklist will guide international B2B buyers through the essential steps to make informed decisions.
Step 1: Define Your Technical Specifications
Begin by detailing your project requirements, including material types, thicknesses, and dimensions. Clearly defined specifications help suppliers understand your needs and minimize the risk of miscommunication. Additionally, consider including tolerance levels and surface finish requirements to ensure the final product meets your expectations.
Step 2: Research Potential Suppliers
Conduct thorough research to identify reputable water jet cutting service providers in China. Utilize online directories, industry associations, and trade shows to compile a list of potential suppliers. Look for companies with a solid track record in your specific industry, as this can indicate their capability to meet your needs.
Step 3: Evaluate Supplier Certifications
Verify that potential suppliers hold relevant certifications, such as ISO 9001 for quality management systems. Certifications demonstrate a commitment to quality and adherence to international standards. Additionally, inquire about any environmental certifications, especially if sustainability is a priority for your business.
Step 4: Request and Review Samples
Before finalizing any contracts, request samples of previous work or prototypes based on your specifications. Evaluating samples allows you to assess the supplier’s quality and capabilities firsthand. Pay attention to details such as precision, surface finish, and overall craftsmanship.
Step 5: Check References and Client Feedback
Reach out to past clients or industry contacts who have previously worked with the suppliers you are considering. Gathering feedback on their experiences can provide valuable insights into the supplier’s reliability, communication, and problem-solving abilities. Look for patterns in feedback to gauge overall satisfaction.
Step 6: Understand Pricing Structures and Terms
Request detailed quotations from multiple suppliers to compare pricing and services offered. Ensure that quotes include all relevant costs, such as setup fees, shipping, and potential tariffs. Understanding pricing structures will help you avoid hidden costs and facilitate budget planning.
Step 7: Negotiate Terms and Finalize Contracts
Once you have selected a supplier, engage in negotiations to finalize terms that are mutually beneficial. Discuss payment terms, delivery schedules, and penalties for delays or quality issues. A well-drafted contract protects both parties and ensures clarity in expectations.
By following this step-by-step checklist, international B2B buyers can navigate the complexities of sourcing water jet cutting services from China effectively. This structured approach not only enhances the likelihood of a successful procurement process but also fosters long-term partnerships with reliable suppliers.
Comprehensive Cost and Pricing Analysis for water jet cutting china Sourcing
What Are the Key Cost Components in Water Jet Cutting China Sourcing?
When sourcing water jet cutting services from China, understanding the cost structure is crucial for international B2B buyers. The main cost components include:
-
Materials: The choice of materials significantly influences pricing. Common materials processed include metals, plastics, and glass, each with varying costs. It’s important to select materials that not only fit your project requirements but also align with your budget.
-
Labor: Labor costs in China are generally lower than in many Western countries. However, skilled labor, particularly for specialized water jet cutting services, may command higher wages. It’s essential to account for labor costs, especially for projects requiring high precision.
-
Manufacturing Overhead: This includes costs related to facility maintenance, utilities, and administrative expenses. Understanding the overhead costs can help buyers gauge the overall pricing from suppliers.
-
Tooling: The initial setup for water jet cutting can involve significant tooling costs. These costs are generally amortized over production runs, so larger orders can lead to lower per-unit costs.
-
Quality Control (QC): Ensuring high-quality outputs often requires rigorous QC processes, which can add to the overall cost. Buyers should inquire about the QC measures in place and whether they affect pricing.
-
Logistics: Shipping costs can vary based on the mode of transport (air vs. sea), distance, and weight of materials. International buyers must consider these logistics costs as they can significantly impact the final price.
-
Margin: Suppliers typically include a profit margin in their pricing. Understanding industry norms for margins can help buyers negotiate better prices.
How Do Price Influencers Affect Water Jet Cutting Costs?
Several factors can influence the pricing of water jet cutting services:
-
Volume/MOQ: Bulk orders often lead to discounted pricing. Suppliers may have minimum order quantities (MOQ), and negotiating for larger quantities can yield better pricing.
-
Specifications/Customization: Custom designs and specifications can increase costs. Buyers should clearly communicate their requirements to avoid unexpected charges.
-
Materials: The type and quality of materials used can significantly affect pricing. High-grade materials will generally cost more, so it’s vital to balance quality with budget.
-
Quality Certifications: Suppliers offering certifications (e.g., ISO, CE) may charge higher prices. Buyers should assess whether these certifications are necessary for their specific projects.
-
Supplier Factors: The supplier’s reputation, location, and operational efficiencies can all influence pricing. Established suppliers may offer reliability but at a premium.
-
Incoterms: Understanding Incoterms (International Commercial Terms) is crucial for international transactions. They define responsibilities for shipping, insurance, and tariffs, impacting overall costs.
What Are the Best Buyer Tips for Cost Efficiency in Water Jet Cutting?
To maximize value when sourcing water jet cutting services, consider the following tips:
-
Negotiate Effectively: Always negotiate pricing based on your understanding of the cost components. Highlighting your volume or long-term partnership potential can strengthen your position.
-
Evaluate Total Cost of Ownership (TCO): Look beyond initial pricing and consider the TCO, which includes maintenance, logistics, and potential wastage. This holistic view can lead to more informed purchasing decisions.
-
Understand Pricing Nuances: Different regions may have varying pricing structures. For buyers in Africa, South America, the Middle East, and Europe, understanding local market conditions can provide leverage in negotiations.
-
Request Detailed Quotations: Ensure that suppliers provide detailed quotes that break down costs. This transparency can help identify areas for negotiation and clarify what is included in the price.
-
Build Relationships with Suppliers: Establishing long-term relationships can lead to better pricing and service. Suppliers may offer loyalty discounts or prioritize your orders when they know you are a repeat customer.
Disclaimer on Indicative Prices
Please note that the prices mentioned in this analysis are indicative and can vary based on market conditions, supplier pricing strategies, and specific project requirements. Always conduct thorough due diligence before finalizing any contracts.
Alternatives Analysis: Comparing water jet cutting china With Other Solutions
Understanding Alternatives to Water Jet Cutting in China
In the competitive landscape of manufacturing and precision cutting, selecting the right technology is crucial for efficiency and cost-effectiveness. While water jet cutting in China is a popular choice due to its versatility and precision, there are alternative methods that may suit specific applications better. This section explores these alternatives, offering a comparative analysis to assist international B2B buyers in making informed decisions.
Comparison Table of Cutting Solutions
Comparison Aspect | Water Jet Cutting China | Laser Cutting | Plasma Cutting |
---|---|---|---|
Performance | High precision; suitable for various materials including metals, glass, and composites. | Extremely precise; best for thin materials. | Good for thick metals, but less precise. |
Cost | Moderate initial investment; lower operational costs due to minimal waste. | High initial investment; operational costs can vary based on material. | Lower equipment costs; higher consumable costs. |
Ease of Implementation | Requires skilled operators; can be complex to set up. | Easier to set up; requires training for optimal operation. | Simpler setup; less training required. |
Maintenance | Regular maintenance needed; potential for wear in components. | Low maintenance; periodic lens replacement required. | Moderate maintenance; consumables need frequent replacement. |
Best Use Case | Ideal for complex shapes and sensitive materials. | Best for high-speed cutting of metals and plastics. | Suitable for heavy-duty applications in metal fabrication. |
Detailed Breakdown of Alternatives
What Are the Advantages and Disadvantages of Laser Cutting?
Laser cutting technology employs focused light to melt or vaporize materials, providing high precision and speed. One of its primary advantages is its ability to cut intricate designs on thin materials such as stainless steel and plastics without causing thermal distortion. However, the initial investment for laser cutting equipment can be substantial, and while operational costs can be lower than water jet cutting, they vary significantly based on the material used. Additionally, laser cutting is less effective for thicker materials, making it unsuitable for all applications.
How Does Plasma Cutting Compare?
Plasma cutting utilizes a high-velocity jet of ionized gas (plasma) to cut through electrically conductive materials. It is particularly advantageous for heavy-duty applications where speed is a priority, such as in metal fabrication. Plasma cutting equipment is generally more affordable than laser systems, which can make it appealing for budget-conscious businesses. However, it lacks the precision of water jet or laser cutting, leading to rougher edges and requiring additional finishing processes. Furthermore, its effectiveness diminishes with thicker materials, making it less versatile than water jet cutting.
Conclusion: How Can B2B Buyers Choose the Right Cutting Solution?
When evaluating cutting solutions, B2B buyers must consider the specific requirements of their projects. Water jet cutting in China offers unmatched versatility and precision, particularly for complex shapes and sensitive materials. However, for high-speed operations or budget constraints, laser or plasma cutting may present viable alternatives. Ultimately, the choice should align with the operational context, desired outcomes, and available resources, ensuring that the selected technology meets both immediate and long-term needs. By weighing the pros and cons of each option, buyers can make strategic decisions that enhance productivity and cost-efficiency in their manufacturing processes.
Essential Technical Properties and Trade Terminology for water jet cutting china
What Are the Key Technical Properties of Water Jet Cutting?
Water jet cutting is a versatile and precise manufacturing method widely used across various industries. Understanding its technical specifications is crucial for international B2B buyers looking to make informed purchasing decisions. Below are essential properties to consider:
1. Material Grade
Material grade refers to the specific classification of the material being cut, such as metals, plastics, glass, or stone. Each grade has unique properties affecting its hardness, tensile strength, and machinability. For buyers, knowing the material grade is essential to ensure the water jet cutting process is compatible with the intended application and meets industry standards.
2. Tolerance
Tolerance is the permissible limit of variation in a physical dimension or measured value. In water jet cutting, high tolerance levels (often ±0.005 inches or better) are vital for applications requiring precision, such as aerospace or medical components. Buyers should prioritize suppliers who can consistently deliver products within specified tolerances to avoid costly rework and delays.
3. Cutting Speed
Cutting speed, measured in inches per minute (IPM), indicates how quickly the water jet can cut through a material. Higher speeds can improve productivity but may compromise cut quality. B2B buyers must balance the need for speed with the quality requirements of their projects, making it essential to consult with suppliers about optimal cutting speeds for specific materials.
4. Water Pressure
Water pressure, typically measured in PSI (pounds per square inch), is a critical factor that influences cutting performance. Standard pressures range from 30,000 to 90,000 PSI, with higher pressures allowing for more efficient cutting of thicker materials. Buyers should inquire about the water pressure capabilities of the cutting equipment to ensure it aligns with their production needs.
5. Abrasive Type and Size
For abrasive water jet cutting, the type and size of the abrasive material (such as garnet) significantly affect the cutting efficiency and surface finish. Finer abrasives produce smoother cuts but may require longer processing times. Buyers should consider their end-product requirements when selecting suppliers and specify their abrasive needs clearly.
What Common Trade Terms Should B2B Buyers Know in Water Jet Cutting?
Understanding industry jargon is essential for effective communication and negotiation in the water jet cutting sector. Here are some key terms that B2B buyers should be familiar with:
1. OEM (Original Equipment Manufacturer)
An OEM is a company that produces parts or equipment that may be marketed by another manufacturer. In the context of water jet cutting, buyers should consider whether they are purchasing from OEMs, as these suppliers often provide high-quality, compatible components that meet specific industry standards.
2. MOQ (Minimum Order Quantity)
MOQ refers to the smallest quantity of a product that a supplier is willing to sell. Understanding MOQs is crucial for buyers, as it can affect inventory costs and cash flow. Buyers should negotiate MOQs to align with their operational needs while ensuring they maintain favorable pricing.
3. RFQ (Request for Quotation)
An RFQ is a document sent to suppliers requesting detailed pricing information for specific products or services. For water jet cutting, an RFQ should include material specifications, quantities, and required tolerances. This process helps buyers compare offers and select suppliers that best meet their requirements.
4. Incoterms
Incoterms (International Commercial Terms) are a set of predefined international trade terms that outline the responsibilities of buyers and sellers in shipping and freight. Familiarity with Incoterms helps B2B buyers understand shipping costs, risk transfer, and delivery obligations, which are vital for managing international transactions effectively.
5. Lead Time
Lead time is the amount of time from placing an order to receiving the product. In the context of water jet cutting, shorter lead times can enhance project timelines. Buyers should communicate their lead time requirements clearly to suppliers to ensure timely delivery and project success.
Conclusion
By understanding these technical properties and trade terms associated with water jet cutting, B2B buyers can make informed decisions, enhance communication with suppliers, and ultimately improve their operational efficiency. As international markets continue to evolve, staying informed on these aspects will be crucial for maintaining competitive advantage.
Navigating Market Dynamics and Sourcing Trends in the water jet cutting china Sector
What Are the Current Market Dynamics and Key Trends in the Water Jet Cutting Sector?
The water jet cutting sector is experiencing significant growth driven by technological advancements and increasing demand for precision cutting across various industries, including aerospace, automotive, and metal fabrication. International B2B buyers from regions like Africa, South America, the Middle East, and Europe should be aware of the rising adoption of automation and Industry 4.0 technologies. These innovations are enabling manufacturers to enhance efficiency and reduce operational costs, making water jet cutting a more attractive option for precision work.
Emerging trends such as customization and the use of advanced materials are reshaping sourcing strategies. Buyers are increasingly looking for suppliers who can provide tailored solutions that meet specific project requirements. Additionally, the global push for sustainability is influencing purchasing decisions, with companies preferring vendors that offer eco-friendly alternatives and energy-efficient machinery. Buyers in regions like Poland and Indonesia should also consider the local regulations and standards that may affect sourcing decisions, ensuring compliance while optimizing their supply chains.
How Important Is Sustainability and Ethical Sourcing in the Water Jet Cutting Industry?
Sustainability and ethical sourcing have become crucial considerations for B2B buyers in the water jet cutting sector. The environmental impact of manufacturing processes is under scrutiny, with companies facing pressure to adopt greener practices. Water jet cutting is already a more environmentally friendly method compared to traditional cutting techniques, as it produces minimal waste and does not emit harmful gases. However, buyers should seek suppliers who go beyond the cutting process by ensuring that their materials are sourced responsibly and sustainably.
In addition to minimizing environmental impact, ethical supply chains are gaining traction among conscious consumers and businesses alike. Certifications such as ISO 14001 for environmental management and the use of recycled or sustainably sourced materials can significantly enhance a supplier’s appeal. Buyers should prioritize partnerships with manufacturers that are committed to ethical practices, as this not only aligns with corporate social responsibility goals but also improves brand reputation and customer loyalty.
What Is the Brief Evolution and History of Water Jet Cutting Technology?
Water jet cutting technology has evolved significantly since its inception in the 1960s. Initially used primarily in the aerospace industry for cutting soft materials, it has expanded to various applications across multiple sectors. The introduction of abrasive water jet cutting in the 1980s allowed for the processing of harder materials, including metals and ceramics. Today, advancements in computer numerical control (CNC) technology have further refined the precision and capabilities of water jet systems.
As global markets continue to demand high-quality and efficient cutting solutions, the evolution of water jet technology represents a critical opportunity for B2B buyers to engage with innovative suppliers. Understanding this historical context can aid in making informed decisions about sourcing and adopting cutting-edge technologies that meet modern production needs.
Frequently Asked Questions (FAQs) for B2B Buyers of water jet cutting china
-
How do I choose the right water jet cutting supplier in China?
Selecting the right supplier for water jet cutting in China requires a thorough evaluation of their capabilities and reliability. Start by researching their industry reputation through reviews and testimonials. Verify their certifications, such as ISO standards, to ensure quality assurance. Request samples of their work to assess precision and finish quality. Additionally, consider their experience with international clients, as this often indicates their ability to navigate logistics and compliance with international standards. -
What are the common customization options available for water jet cutting services in China?
Chinese suppliers typically offer a range of customization options for water jet cutting services. This includes the choice of materials, such as metals, plastics, and composites, along with various thicknesses. You can also specify the dimensions and tolerances required for your project. Some suppliers may provide additional services, such as post-processing, finishing, and assembly, allowing you to receive a fully tailored solution that meets your specific needs. -
What is the minimum order quantity (MOQ) for water jet cutting services in China?
The MOQ for water jet cutting services can vary significantly among suppliers in China. While some may have a low MOQ of just a few pieces, others might require larger orders to justify production costs. It’s essential to communicate your requirements directly with potential suppliers to understand their MOQ policies. If your needs are smaller, consider negotiating or looking for suppliers who specialize in low-volume production. -
How can I ensure quality assurance when sourcing water jet cutting services from China?
To ensure quality assurance, it’s critical to establish clear quality standards and specifications upfront. Request certifications that demonstrate the supplier’s commitment to quality control, such as ISO 9001. Implement a robust inspection process, which may include pre-shipment inspections and on-site audits. Additionally, consider using third-party quality assurance services to verify that the products meet your standards before they are shipped. -
What payment terms are typical when working with water jet cutting suppliers in China?
Payment terms can vary widely among suppliers in China. Common practices include a 30% deposit before production, with the remaining 70% due upon completion or before shipment. Some suppliers may offer more flexible terms based on your relationship and order size. It’s advisable to discuss payment terms early in negotiations and consider using secure payment methods, such as letters of credit, to mitigate risks. -
What logistics considerations should I keep in mind when importing water jet cut parts from China?
Logistics is a crucial aspect of importing water jet cut parts from China. Ensure you have a reliable freight forwarder who can handle customs clearance and shipping logistics. Understand the incoterms (International Commercial Terms) that define the responsibilities of both parties in the shipping process. Additionally, factor in lead times for production, shipping duration, and potential delays due to customs to ensure timely delivery of your products. -
How do international trade regulations affect sourcing water jet cutting services from China?
International trade regulations can significantly impact your sourcing strategy. It’s essential to stay informed about tariffs, import duties, and compliance requirements specific to your country. Ensure that your supplier adheres to international standards for materials and processes, as failing to comply can lead to costly delays or penalties. Consulting with a trade expert or legal advisor can help you navigate these regulations effectively. -
What are the advantages of using water jet cutting technology in manufacturing?
Water jet cutting technology offers numerous advantages, making it a preferred choice in various manufacturing sectors. It provides high precision and can cut through a wide range of materials without altering their properties. This method is also environmentally friendly, as it produces minimal waste and does not require harmful chemicals. Additionally, water jet cutting allows for complex designs and intricate patterns, which can enhance product functionality and aesthetics in your projects.
Important Disclaimer & Terms of Use
⚠️ Important Disclaimer
The information provided in this guide, including content regarding manufacturers, technical specifications, and market analysis, is for informational and educational purposes only. It does not constitute professional procurement advice, financial advice, or legal advice.
While we have made every effort to ensure the accuracy and timeliness of the information, we are not responsible for any errors, omissions, or outdated information. Market conditions, company details, and technical standards are subject to change.
B2B buyers must conduct their own independent and thorough due diligence before making any purchasing decisions. This includes contacting suppliers directly, verifying certifications, requesting samples, and seeking professional consultation. The risk of relying on any information in this guide is borne solely by the reader.
Strategic Sourcing Conclusion and Outlook for water jet cutting china
What Are the Key Takeaways for B2B Buyers in Water Jet Cutting?
As the global demand for precision manufacturing continues to rise, water jet cutting technology from China presents a compelling opportunity for international B2B buyers. Key takeaways include the importance of understanding the technological advancements in this field, as well as the cost-effectiveness and versatility of water jet cutting solutions. Buyers should prioritize suppliers who adhere to international quality standards and can demonstrate a robust track record in delivering reliable services.
How Does Strategic Sourcing Enhance Competitive Advantage?
Strategic sourcing is vital in ensuring that B2B buyers optimize their procurement processes while minimizing risks. By establishing strong partnerships with reputable water jet cutting manufacturers in China, businesses can achieve significant cost savings and enhance production capabilities. It is essential for buyers from regions like Africa, South America, the Middle East, and Europe to engage with suppliers who are not only cost-competitive but also innovative and responsive to market trends.
What Is the Future Outlook for Water Jet Cutting in Global Markets?
Looking ahead, the future of water jet cutting technology is promising, with advancements in automation and eco-friendly practices on the horizon. International B2B buyers are encouraged to stay informed about these developments and consider integrating water jet cutting into their operations to remain competitive. Embrace this opportunity to connect with leading Chinese suppliers and leverage their expertise to drive your business forward. The time to act is now; explore partnerships that will elevate your manufacturing processes and set you apart in the global marketplace.