Discover Affordable Drawstring Bags Custom for Your Business (2025)
Introduction: Navigating the Global Market for drawstring bags custom
In an increasingly competitive global market, sourcing custom drawstring bags can present significant challenges for international B2B buyers, particularly those in regions such as Africa, South America, the Middle East, and Europe. The demand for versatile and cost-effective promotional products has surged, making it essential for businesses to navigate the complexities of sourcing high-quality drawstring bags that meet their specific needs. This comprehensive guide aims to address critical aspects such as the various types of drawstring bags available, their diverse applications across industries, and effective strategies for vetting suppliers.
Understanding the nuances of the drawstring bag market is crucial for making informed purchasing decisions. This guide will delve into factors influencing pricing, materials used, and customization options, allowing buyers to weigh their options carefully. Additionally, we will provide insights on identifying reputable suppliers, ensuring product quality, and maximizing return on investment.
By equipping B2B buyers with actionable knowledge and practical tools, this guide empowers businesses to streamline their procurement processes and secure the best deals on custom drawstring bags. Whether you are a small startup or an established enterprise, understanding the landscape of this product category will enhance your ability to make strategic choices that align with your business objectives.
Understanding drawstring bags custom Types and Variations
Type Name | Key Distinguishing Features | Primary B2B Applications | Brief Pros & Cons for Buyers |
---|---|---|---|
Standard Drawstring Bags | Basic design with a single drawstring, often made from lightweight materials like nylon or polyester. | Promotional giveaways, trade shows, corporate events. | Pros: Cost-effective, lightweight, versatile. Cons: Limited durability, less customization. |
Heavy-Duty Drawstring Bags | Constructed from thicker, more durable materials, often with reinforced stitching. | Outdoor events, sports teams, and industrial use. | Pros: High durability, suitable for heavier items. Cons: Higher cost, may be bulkier. |
Custom Printed Drawstring Bags | Personalized with logos or designs, available in various colors and sizes. | Branding purposes, marketing campaigns, merchandise. | Pros: Enhances brand visibility, fully customizable. Cons: Higher production time, potential minimum order requirements. |
Eco-Friendly Drawstring Bags | Made from sustainable materials like organic cotton or recycled plastics. | Environmentally conscious brands, trade shows, eco-friendly events. | Pros: Appeals to green consumers, promotes sustainability. Cons: Often more expensive, limited styles. |
Multi-Compartment Drawstring Bags | Features multiple pockets or compartments for organization, often with zippers or additional closures. | Sports, travel, and educational purposes. | Pros: Increased functionality, better organization. Cons: Higher cost, can be heavier. |
What are the Characteristics of Standard Drawstring Bags?
Standard drawstring bags are the most common type, characterized by their lightweight and simple design. Typically made from materials like nylon or polyester, they are easy to carry and perfect for promotional purposes. For B2B buyers, these bags are ideal for events like trade shows or corporate giveaways due to their cost-effectiveness. However, their limited durability and customization options might not meet the needs of businesses looking for more robust solutions.
Why Choose Heavy-Duty Drawstring Bags for B2B Needs?
Heavy-duty drawstring bags are designed for more demanding applications, utilizing thicker materials and reinforced stitching. These bags excel in outdoor settings, making them suitable for sports teams or industrial use. B2B buyers should consider these bags for their durability, which allows them to carry heavier items without risk of damage. The downside is the higher price point, which may not align with every budget.
How Can Custom Printed Drawstring Bags Enhance Brand Visibility?
Custom printed drawstring bags allow businesses to showcase their branding effectively. With options for logos and designs, these bags can significantly enhance a company’s visibility during marketing campaigns or events. B2B buyers should evaluate their branding goals when considering these bags, as they provide a unique opportunity to engage customers. However, longer production times and minimum order requirements can be potential drawbacks.
What are the Benefits of Eco-Friendly Drawstring Bags?
Eco-friendly drawstring bags are crafted from sustainable materials, appealing to environmentally conscious consumers. They are an excellent choice for brands looking to promote sustainability at events or trade shows. For B2B buyers, these bags can enhance corporate responsibility efforts, aligning with modern consumer values. However, the increased cost and limited style options may pose challenges for some businesses.
When to Use Multi-Compartment Drawstring Bags?
Multi-compartment drawstring bags offer enhanced functionality with additional pockets for organization. These bags are particularly beneficial for sports, travel, or educational contexts where users need to carry multiple items. B2B buyers should consider these bags for their practicality; however, the added complexity can lead to higher costs and weight, which may not suit all applications.
Related Video: Lined Drawstring Bags | EASY DIY | Whitney Sews
Key Industrial Applications of drawstring bags custom
Industry/Sector | Specific Application of drawstring bags custom | Value/Benefit for the Business | Key Sourcing Considerations for this Application |
---|---|---|---|
Retail | Promotional giveaways during events or sales | Enhances brand visibility and customer engagement | Quality of materials, customization options, pricing |
Education | Student orientation kits and event swag | Fosters school spirit and promotes educational programs | Durability, design flexibility, bulk order capabilities |
Sports and Recreation | Team merchandise and event participation bags | Creates a sense of unity and enhances team branding | Size options, color choices, lead times for events |
Hospitality and Tourism | Welcome bags for guests or event attendees | Improves guest experience and promotes local attractions | Eco-friendliness, design aesthetics, branding options |
Health and Wellness | Patient information bags in clinics or health fairs | Increases patient awareness and promotes services | Compliance with health standards, ease of cleaning |
How Are Drawstring Bags Custom Used in Retail?
In the retail sector, custom drawstring bags serve as effective promotional giveaways during events or sales. They enhance brand visibility by allowing businesses to distribute their branding in a practical format that customers can reuse. For international B2B buyers, it is crucial to consider the quality of materials used, as well as the customization options available, to ensure that the bags reflect the brand image effectively. Pricing should also be competitive to maximize the return on investment.
What Are the Applications in Education?
Custom drawstring bags are widely used in educational institutions for student orientation kits and event swag. These bags help foster school spirit and promote educational programs by providing students with essential items and information in a branded format. Buyers in this sector should focus on durability and design flexibility, ensuring that the bags can withstand daily use while accommodating various branding needs. Bulk order capabilities are also essential for educational institutions looking to outfit large groups.
How Do Sports Teams Utilize Custom Drawstring Bags?
In the sports and recreation industry, teams often use custom drawstring bags for merchandise and as participation bags during events. These bags create a sense of unity among team members and enhance team branding, making them an essential tool for any sports organization. Buyers should consider size options and color choices to match team colors and logos, while also ensuring that lead times align with the event schedule for timely distribution.
What Is the Role of Custom Drawstring Bags in Hospitality?
The hospitality and tourism sector employs custom drawstring bags as welcome bags for guests or event attendees. These bags improve the guest experience by providing useful items and promoting local attractions, making them a valuable marketing tool. When sourcing these bags, businesses should prioritize eco-friendliness and design aesthetics, as modern consumers increasingly favor sustainable products. Additionally, branding options are key to ensuring that the bags effectively represent the hospitality brand.
How Are They Used in Health and Wellness?
In the health and wellness industry, custom drawstring bags are often utilized as patient information bags in clinics or health fairs. They play a vital role in increasing patient awareness and promoting services, providing a practical means of distributing important information. For international buyers, compliance with health standards is essential, along with ease of cleaning, to maintain hygiene in healthcare settings. Customization options should also be considered to align with the branding of healthcare providers.
3 Common User Pain Points for ‘drawstring bags custom’ & Their Solutions
Scenario 1: Quality Control Issues in Custom Drawstring Bags
The Problem: A common challenge faced by B2B buyers when ordering custom drawstring bags is ensuring product quality. Many manufacturers may offer lower prices, but this often comes at the cost of inferior materials or inconsistent production standards. This can lead to significant issues such as bags that tear easily, poor print quality, or even non-compliance with local regulations regarding materials. For buyers from regions like Africa or South America, where supply chain logistics can complicate returns or exchanges, receiving subpar products can result in financial losses and reputational damage.
The Solution: To mitigate quality control issues, B2B buyers should establish clear specifications and standards before placing orders. This includes requesting samples to evaluate the material, stitching, and printing quality. Additionally, it’s beneficial to work with manufacturers that have certifications (like ISO) and a track record of quality assurance. Building a relationship with a reliable supplier can also help; regular communication and feedback loops will ensure that any issues are addressed promptly. Finally, consider utilizing third-party inspection services to verify product quality before shipment, especially when ordering in large quantities.
Scenario 2: Long Lead Times Affecting Supply Chain Efficiency
The Problem: International B2B buyers often face long lead times when sourcing custom drawstring bags, particularly when ordering from overseas suppliers. These delays can disrupt marketing campaigns, event planning, or seasonal promotions, leading to missed opportunities and dissatisfied customers. This challenge is especially pronounced for businesses in the Middle East and Europe, where timely delivery is critical for competitive advantage.
The Solution: To combat long lead times, buyers should conduct thorough research to identify suppliers with a reputation for prompt delivery. When negotiating contracts, include clear timelines and penalties for delays to hold suppliers accountable. Implementing a just-in-time inventory system can also help manage stock levels effectively. Additionally, consider placing orders well in advance of peak seasons or promotional events. Collaborating with local suppliers or those with production facilities closer to your region can significantly reduce shipping times and enhance overall supply chain efficiency.
Scenario 3: Limited Customization Options Impacting Brand Identity
The Problem: B2B buyers often encounter limitations in customization options for drawstring bags, which can hinder their ability to create unique products that resonate with their brand identity. This is particularly frustrating for companies in Europe, where brand differentiation is key to standing out in a competitive market. Buyers may find that many manufacturers offer only a limited range of colors, sizes, or printing methods, making it difficult to achieve the desired aesthetic.
The Solution: To overcome the challenge of limited customization, buyers should seek out manufacturers that specialize in bespoke solutions. When initiating discussions with potential suppliers, clearly communicate your branding needs and ask about their capabilities in terms of colors, materials, and printing techniques. Look for manufacturers who offer a wide range of options and flexibility in production. Additionally, consider leveraging digital printing technologies, which can provide more detailed designs and a broader color palette. By fostering an open dialogue with suppliers about your customization needs, you can ensure the final product aligns perfectly with your brand identity.
Strategic Material Selection Guide for drawstring bags custom
What Are the Best Materials for Custom Drawstring Bags?
When selecting materials for custom drawstring bags, international B2B buyers must consider various factors, including durability, cost, and application suitability. Here, we analyze four common materials used in the production of drawstring bags, providing insights into their properties, advantages, disadvantages, and considerations for global markets.
1. Polyester: A Versatile and Cost-Effective Choice
Key Properties: Polyester is known for its excellent strength-to-weight ratio, resistance to stretching, and quick-drying capabilities. It performs well in a range of temperatures and is resistant to mildew and abrasion.
Pros & Cons: The durability of polyester makes it suitable for everyday use, while its low cost makes it an attractive option for bulk purchases. However, it may not be as environmentally friendly as natural fibers and can be less breathable, which may not suit all applications.
Impact on Application: Polyester bags are ideal for promotional events, giveaways, and retail packaging. They can hold various media, including lightweight items like clothing or promotional materials.
Considerations for International Buyers: Buyers should ensure compliance with international standards such as ASTM and REACH, especially in markets like Europe where environmental regulations are stringent.
2. Cotton: The Eco-Friendly Alternative
Key Properties: Cotton is a natural fiber known for its softness, breathability, and biodegradability. It is generally safe for sensitive skin and offers good moisture absorption.
Pros & Cons: While cotton bags are durable and environmentally friendly, they tend to be more expensive than synthetic options. They also require more care in manufacturing to ensure quality and consistency.
Impact on Application: Cotton drawstring bags are perfect for organic products, cosmetics, and food items. Their breathable nature makes them suitable for items that require ventilation.
Considerations for International Buyers: Buyers from regions with strong sustainability initiatives, like Europe, may prefer cotton for its eco-friendly properties. Compliance with organic certification standards can also be a selling point.
3. Nylon: Strength and Flexibility
Key Properties: Nylon is a synthetic material known for its high tensile strength and resistance to wear and tear. It is lightweight and has excellent elasticity, making it suitable for various applications.
Pros & Cons: The main advantage of nylon is its durability and resistance to environmental factors. However, it can be more expensive than polyester and may not be as environmentally friendly due to its synthetic nature.
Impact on Application: Nylon bags are ideal for outdoor activities, sports, and travel, as they can withstand rough handling and various weather conditions.
Considerations for International Buyers: Buyers should consider the environmental impact of nylon and its compliance with local regulations, especially in markets that are increasingly focused on sustainability.
4. Non-Woven Polypropylene: Cost-Effective and Recyclable
Key Properties: Non-woven polypropylene is a lightweight, durable material that is resistant to water and tearing. It is made from recycled materials, making it a more sustainable option compared to other plastics.
Pros & Cons: The affordability of non-woven polypropylene makes it a popular choice for promotional bags. However, its durability is lower than that of woven materials, which may limit its use for heavy items.
Impact on Application: Non-woven bags are commonly used for promotional giveaways, grocery bags, and trade shows. They are suitable for carrying lightweight items and can be printed with vibrant designs.
Considerations for International Buyers: Buyers should check for compliance with recycling regulations in their respective countries, particularly in Europe, where sustainability is a key factor in purchasing decisions.
Summary Table of Material Selection for Custom Drawstring Bags
Material | Typical Use Case for drawstring bags custom | Key Advantage | Key Disadvantage/Limitation | Relative Cost (Low/Med/High) |
---|---|---|---|---|
Polyester | Promotional events, retail packaging | Cost-effective and durable | Less breathable and eco-friendly | Low |
Cotton | Organic products, cosmetics | Eco-friendly and soft | Higher cost and care in quality | Med |
Nylon | Outdoor activities, sports | High durability and flexibility | More expensive and less eco-friendly | High |
Non-Woven Polypropylene | Grocery bags, trade shows | Affordable and recyclable | Lower durability for heavy items | Low |
This guide provides a comprehensive overview of the materials available for custom drawstring bags, helping international B2B buyers make informed decisions that align with their product needs and market requirements.
In-depth Look: Manufacturing Processes and Quality Assurance for drawstring bags custom
What Are the Typical Manufacturing Processes for Custom Drawstring Bags?
The manufacturing of custom drawstring bags involves several key stages that ensure the final product meets the desired specifications and quality. Understanding these processes is crucial for B2B buyers who need reliable and high-quality products.
How Is Material Prepared for Custom Drawstring Bags?
The first step in manufacturing custom drawstring bags is the preparation of materials. Common materials include polyester, cotton, nylon, and canvas.
-
Material Selection: Buyers should consider the intended use of the bags, as different materials offer varying durability, weight, and cost. For instance, polyester is lightweight and water-resistant, making it ideal for outdoor promotional events, while cotton provides a more eco-friendly option with a softer feel.
-
Cutting: Once the materials are selected, they are cut into specific shapes and sizes based on the design specifications. Advanced cutting techniques, such as laser cutting, can enhance precision and reduce waste.
What Techniques Are Used in the Forming Stage?
After material preparation, the next stage is forming the bag. This involves several techniques that shape the bag into its final form.
-
Sewing: The cut pieces are sewn together using industrial sewing machines. This step may include techniques like double stitching for added strength, especially in high-stress areas such as the seams and drawstring openings.
-
Printing and Customization: Many buyers opt for custom printing on their drawstring bags. Techniques such as screen printing and heat transfer are commonly used. It is essential to ensure that the printing method selected aligns with the material used to avoid issues like fading or peeling.
How Are Custom Drawstring Bags Assembled and Finished?
The assembly and finishing stages finalize the product before it reaches the buyer.
-
Assembly: This includes attaching the drawstring mechanism, which can be a cord or a strap, and ensuring that it functions correctly. Quality assembly ensures that the bags can open and close smoothly and securely.
-
Finishing Touches: The final stage involves additional processes such as quality checks, folding, and packaging. Proper finishing not only enhances the bag’s appearance but also prepares it for shipping.
What Quality Assurance Standards Should B2B Buyers Look For?
Quality assurance (QA) is critical in the manufacturing process to ensure that the final product meets specific standards and customer expectations. B2B buyers should be familiar with several international and industry-specific standards.
Which International Standards Are Relevant for Custom Drawstring Bags?
-
ISO 9001: This standard focuses on quality management systems and is applicable to any organization seeking to ensure that it consistently meets customer and regulatory requirements. Suppliers certified with ISO 9001 demonstrate a commitment to quality and continuous improvement.
-
CE Marking: For products sold within the European Economic Area, CE marking indicates compliance with safety and environmental protection standards. Buyers should ensure that their suppliers meet these regulations, especially if the bags are to be used for promotional purposes.
What Are the Key Quality Control Checkpoints?
Quality control (QC) should be integrated throughout the manufacturing process. Here are the main QC checkpoints:
-
Incoming Quality Control (IQC): Before production begins, incoming materials should be inspected to ensure they meet specifications. This step prevents defective materials from entering the production line.
-
In-Process Quality Control (IPQC): During manufacturing, regular checks should be conducted to monitor processes and identify any deviations from the quality standards.
-
Final Quality Control (FQC): After production, the finished bags should undergo a final inspection to confirm they meet the required quality and specifications before shipping.
How Can B2B Buyers Verify Supplier Quality Control?
For international buyers, verifying a supplier’s quality control processes is essential to ensure product reliability and compliance with standards.
What Methods Can Buyers Use to Confirm Quality?
-
Supplier Audits: Conducting on-site audits allows buyers to assess the supplier’s manufacturing processes and quality assurance practices directly. This helps establish trust and ensures that the supplier adheres to agreed-upon standards.
-
Quality Reports: Requesting detailed quality reports from suppliers can provide insights into their QC processes, including defect rates and corrective actions taken.
-
Third-Party Inspections: Engaging third-party inspection services can offer an unbiased evaluation of the manufacturing processes and the final product quality. This is particularly beneficial for buyers from regions like Africa and South America, where local suppliers may not have established quality systems.
What Are the Nuances of QC and Certification for International Buyers?
Understanding the nuances of quality control and certification is crucial for B2B buyers, especially when dealing with international suppliers.
-
Cultural and Regional Differences: Buyers should be aware that quality standards may vary significantly between regions. For instance, suppliers in Europe may have stricter environmental regulations compared to those in Africa. Understanding these differences helps buyers set realistic expectations.
-
Documentation and Compliance: Ensure that all necessary documentation, including compliance certificates and inspection reports, is provided by the supplier. This documentation not only serves as proof of compliance but also aids in customs clearance processes.
By comprehensively understanding the manufacturing processes and quality assurance practices for custom drawstring bags, B2B buyers can make informed decisions, ensuring they partner with reliable suppliers who deliver high-quality products.
Practical Sourcing Guide: A Step-by-Step Checklist for ‘drawstring bags custom’
Introduction
This practical sourcing guide aims to assist international B2B buyers, particularly from Africa, South America, the Middle East, and Europe, in effectively procuring custom drawstring bags. By following this step-by-step checklist, you can streamline your sourcing process, ensure quality, and establish successful partnerships with suppliers.
Step 1: Define Your Technical Specifications
Clearly outlining your technical specifications is essential for ensuring that the custom drawstring bags meet your exact needs. Consider factors such as size, material, color, and printing methods. This clarity will help suppliers provide accurate quotes and samples, reducing the risk of miscommunication and errors later in the process.
- Material Choices: Decide if you prefer eco-friendly options like organic cotton or durable synthetic materials.
- Size Variations: Specify dimensions to fit your intended use, whether for giveaways, retail, or corporate branding.
Step 2: Conduct Market Research for Suppliers
Understanding the market landscape is critical to finding reliable suppliers for custom drawstring bags. Research potential suppliers based on their reputation, product offerings, and customer reviews. Utilize B2B platforms, trade shows, and industry networks to gather insights.
- Supplier Ratings: Look for suppliers with positive feedback and ratings from previous buyers.
- Industry Experience: Prioritize suppliers with a proven track record in producing custom bags.
Step 3: Evaluate Potential Suppliers
Before making a commitment, it’s crucial to vet suppliers thoroughly. Request company profiles, case studies, and references from buyers in a similar industry or region. Don’t just rely on their website; conduct interviews to gauge their responsiveness and professionalism.
- Sample Requests: Ask for product samples to assess the quality and craftsmanship firsthand.
- Production Capacity: Ensure that the supplier can meet your order volume and timeline.
Step 4: Verify Supplier Certifications
Ensure that your selected suppliers hold relevant certifications that guarantee quality standards and compliance with international regulations. Certifications such as ISO 9001 for quality management systems or Oeko-Tex for textile safety can provide peace of mind.
- Documentation Check: Request copies of certifications and verify their authenticity.
- Compliance Standards: Inquire about their adherence to environmental and labor standards.
Step 5: Negotiate Pricing and Terms
Negotiation is a vital step in achieving a favorable deal for your custom drawstring bags. Discuss pricing structures, payment terms, and delivery timelines to ensure mutual understanding. Be prepared to negotiate based on order volume and long-term partnership potential.
- Bulk Discounts: Consider negotiating for lower prices on larger orders to maximize cost efficiency.
- Payment Terms: Discuss flexible payment options that may suit your financial planning.
Step 6: Establish Clear Communication Channels
Effective communication is key to a successful sourcing relationship. Establish clear lines of communication with your suppliers to facilitate quick responses to inquiries and concerns. Utilize tools such as email, video conferencing, and project management software to maintain ongoing dialogue.
- Point of Contact: Designate a primary contact person on both sides for streamlined communication.
- Regular Updates: Schedule periodic updates to discuss production progress and address any issues.
Step 7: Finalize the Contract and Monitor Production
Once all terms are agreed upon, finalize a written contract that outlines all specifications, pricing, and delivery schedules. Monitor production closely, especially during the initial phases, to ensure that the supplier adheres to agreed-upon standards.
- Quality Checks: Implement quality control measures during production to mitigate issues before shipment.
- Feedback Loop: Provide feedback to suppliers on samples and production to foster improvements and collaboration.
By following this comprehensive checklist, B2B buyers can ensure a smooth and successful procurement process for custom drawstring bags, ultimately leading to enhanced brand visibility and customer satisfaction.
Comprehensive Cost and Pricing Analysis for drawstring bags custom Sourcing
What Are the Key Cost Components in Custom Drawstring Bag Sourcing?
When sourcing custom drawstring bags, several cost components significantly influence the overall pricing structure. Understanding these elements can help international B2B buyers, particularly from Africa, South America, the Middle East, and Europe, make informed purchasing decisions.
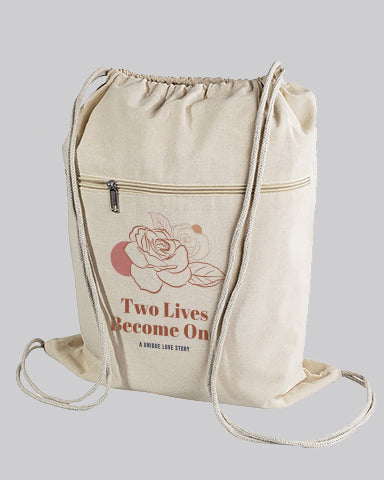
A stock image related to drawstring bags custom.
-
Materials: The choice of fabric, such as polyester, cotton, or recycled materials, directly affects the cost. Higher quality materials usually lead to increased durability and aesthetic appeal, which can justify a higher price point.
-
Labor: Labor costs vary by region and are influenced by local wage standards. Countries with lower labor costs may provide competitive pricing; however, this can sometimes correlate with lower quality.
-
Manufacturing Overhead: This includes costs related to the production facility, utilities, and equipment maintenance. Efficient production processes can help minimize these overheads, impacting the final price.
-
Tooling Costs: If the design requires specialized molds or tools, these costs will be factored into the pricing. Custom designs that necessitate unique tooling will typically incur higher initial costs.
-
Quality Control (QC): Ensuring the final product meets specified standards requires investment in quality control processes. Suppliers who implement rigorous QC protocols may charge more but can provide greater assurance of product reliability.
-
Logistics: Shipping costs, including freight, insurance, and customs duties, can vary widely based on the origin and destination. Understanding Incoterms is crucial for managing these costs effectively.
-
Profit Margin: Suppliers will add a margin to cover their business expenses and profit, which can vary based on market competition and the perceived value of the product.
How Do Price Influencers Affect Custom Drawstring Bag Sourcing?
Several key factors can influence the pricing of custom drawstring bags:
-
Volume and Minimum Order Quantity (MOQ): Larger orders typically reduce the per-unit cost due to economies of scale. Be sure to discuss MOQs with suppliers to find the best pricing strategy.
-
Specifications and Customization: Unique designs, colors, and additional features (like pockets or branding) can drive costs up. Buyers should balance desired customizations with budget constraints.
-
Quality and Certifications: Certifications related to environmental standards or safety can increase costs. Ensure that the product meets necessary standards for your target market, as this can impact both price and customer satisfaction.
-
Supplier Factors: The supplier’s reputation, location, and production capabilities can influence pricing. Established suppliers may offer higher prices but also provide reliability and quality assurance.
-
Incoterms: Understanding shipping terms (e.g., FOB, CIF) is essential, as they dictate who bears shipping costs and risks. This knowledge helps in accurately calculating the total landed cost of the products.
What Are Some Buyer Tips for Cost-Efficiency in Sourcing Custom Drawstring Bags?
-
Negotiate Effectively: Engage in open discussions with suppliers about pricing, especially if you can commit to larger orders. Building a long-term relationship can also lead to better deals.
-
Consider Total Cost of Ownership (TCO): Look beyond the initial purchase price. Evaluate maintenance, shipping, and potential returns in your cost analysis to make more informed decisions.
-
Research Market Trends: Understanding market trends in your region can help gauge fair pricing. Prices may fluctuate due to seasonality, demand, and supply chain disruptions.
-
Evaluate Multiple Suppliers: Don’t settle for the first quote. Comparing offers from multiple suppliers can reveal significant price differences and highlight the best value for your needs.
-
Stay Informed About Pricing Nuances: Different regions may have varying pricing structures based on local economies and demand. For international buyers, remaining aware of these nuances can lead to better negotiation outcomes.
Conclusion
While the prices for custom drawstring bags can vary significantly based on numerous factors, understanding the cost components and price influencers can empower international B2B buyers to make informed decisions. By applying the outlined buyer tips, businesses can navigate the complexities of sourcing efficiently and effectively, ultimately leading to better financial outcomes.
- Disclaimer: Prices mentioned in this analysis are indicative and may vary based on market conditions and specific supplier negotiations.*
Alternatives Analysis: Comparing drawstring bags custom With Other Solutions
Understanding Alternatives to Custom Drawstring Bags
In the world of promotional products and functional carrying solutions, custom drawstring bags have become increasingly popular due to their versatility and branding potential. However, B2B buyers must consider alternative solutions that may meet their specific needs more effectively. This analysis compares custom drawstring bags with two viable alternatives: tote bags and backpack-style bags, focusing on various aspects critical to international buyers from Africa, South America, the Middle East, and Europe.
Comparison Table of Custom Drawstring Bags and Alternatives
Comparison Aspect | Drawstring Bags Custom | Tote Bags | Backpack-Style Bags |
---|---|---|---|
Performance | Lightweight, easy to carry | Moderate weight capacity; good for groceries or events | High weight capacity; ergonomic design |
Cost | Generally low-cost | Moderate cost; varies with material | Higher cost due to design and materials |
Ease of Implementation | Quick turnaround time; simple design | Easy to produce; variety of styles | More complex production; requires design input |
Maintenance | Easy to clean; machine washable | Varies by material; some are machine washable | Requires careful handling; spot cleaning often needed |
Best Use Case | Events, giveaways, and casual use | Grocery shopping, promotional events | School, travel, and outdoor activities |
Detailed Breakdown of Alternatives
What Are the Advantages and Disadvantages of Tote Bags?
Tote bags are a popular alternative to custom drawstring bags, particularly for their spacious design and versatility. They are typically made from durable materials like canvas or non-woven fabric, making them suitable for carrying heavier items such as groceries or books. The pros of tote bags include their larger capacity and branding opportunities due to their flat surfaces. However, they are generally bulkier and may not be as easy to carry as drawstring bags, particularly over long distances.
How Do Backpack-Style Bags Compare to Custom Drawstring Bags?
Backpack-style bags offer an ergonomic alternative for carrying heavier loads. They are designed to distribute weight evenly across the shoulders, making them ideal for school students, travelers, and outdoor enthusiasts. The advantages of backpacks include their high weight capacity and comfort during extended wear. However, they tend to be more expensive than drawstring bags and may require more intricate designs, which can lead to longer production times. Additionally, their maintenance can be more demanding, often needing spot cleaning to maintain appearance.
Conclusion: How to Choose the Right Solution for Your Needs
When selecting between custom drawstring bags and alternatives like tote bags or backpack-style bags, B2B buyers should assess their specific needs and use cases. If the goal is to provide lightweight, cost-effective promotional items for events, drawstring bags are a solid choice. However, for applications requiring higher capacity or ergonomic benefits, tote bags or backpacks may be more suitable. Ultimately, understanding the context in which these products will be used can guide buyers to the solution that best aligns with their branding and functional requirements.
Essential Technical Properties and Trade Terminology for drawstring bags custom
What Are the Essential Technical Properties of Custom Drawstring Bags?
When sourcing custom drawstring bags, understanding their technical properties is crucial for making informed purchasing decisions. Here are some key specifications that B2B buyers should consider:
1. Material Grade
The material used in drawstring bags significantly affects their durability, appearance, and functionality. Common materials include polyester, cotton, and nylon. Polyester is lightweight and water-resistant, making it ideal for outdoor use, while cotton offers a more premium feel but may lack water resistance. Understanding the material grade helps buyers assess the bag’s quality and suitability for their intended use.
2. Weight Capacity
Weight capacity refers to the maximum load a drawstring bag can carry without compromising its integrity. This specification is vital for businesses that intend to use these bags for promotional purposes or events. A bag with a higher weight capacity can accommodate heavier items, making it more versatile for different applications.
3. Dimensions and Tolerance
The dimensions of the drawstring bag, including height, width, and depth, should align with the buyer’s requirements. Tolerance indicates the allowable variation in these dimensions during manufacturing. Ensuring accurate dimensions is essential for functionality and aesthetics, especially for businesses that plan to use these bags for specific items.
4. Printing Options
Custom drawstring bags often feature branding or designs. Understanding the printing options available—such as screen printing, digital printing, or embroidery—allows buyers to choose the best method for their branding needs. Each printing method has different implications for cost, durability, and visual appeal.
5. Closure Type
Most drawstring bags utilize a simple drawstring mechanism, but some may offer additional closure types, such as toggles or zippers. The closure type influences the ease of use and security of the items stored within. Buyers should consider how the closure aligns with their target audience’s needs.
6. Environmental Compliance
With increasing global emphasis on sustainability, many buyers are looking for eco-friendly materials and manufacturing processes. Certification for materials like recycled polyester can enhance a brand’s image and appeal to environmentally conscious consumers.
Which Trade Terms Should B2B Buyers Know When Sourcing Custom Drawstring Bags?
Familiarizing yourself with industry jargon can streamline communication with suppliers and help you navigate the procurement process more effectively. Here are some essential trade terms related to custom drawstring bags:
1. OEM (Original Equipment Manufacturer)
OEM refers to a company that produces goods that are then marketed by another company under its brand name. In the context of custom drawstring bags, partnering with an OEM can provide access to high-quality manufacturing capabilities while allowing businesses to focus on branding and marketing.
2. MOQ (Minimum Order Quantity)
MOQ is the smallest number of units that a supplier is willing to sell. Understanding MOQ is essential for budgeting and inventory management. Buyers should negotiate MOQs that align with their sales forecasts to avoid excess stock or missed sales opportunities.
3. RFQ (Request for Quotation)
An RFQ is a document sent to suppliers to solicit pricing and terms for specific products. When sourcing custom drawstring bags, submitting an RFQ allows buyers to compare different suppliers’ offers, ensuring they secure the best deal.
4. Incoterms (International Commercial Terms)
Incoterms are a set of international rules that define the responsibilities of buyers and sellers in shipping agreements. Familiarity with these terms helps businesses understand shipping costs, insurance, and risk, which is crucial when sourcing products from overseas suppliers.
5. Lead Time
Lead time refers to the period from placing an order to receiving the goods. For custom drawstring bags, understanding lead time is vital for planning marketing campaigns or events. Shorter lead times may be more desirable but could come at a premium.
6. Sample Approval
Sample approval is the process of reviewing a prototype or initial batch of products before full production. This step is critical for ensuring that the final product meets the buyer’s specifications and quality standards.
By grasping these technical properties and trade terms, B2B buyers can make more informed decisions when sourcing custom drawstring bags, ultimately enhancing their supply chain efficiency and product offerings.
Navigating Market Dynamics and Sourcing Trends in the drawstring bags custom Sector
What Are the Current Market Dynamics and Key Trends in the Custom Drawstring Bags Sector?
The custom drawstring bags market is witnessing significant growth, driven by an increasing demand for sustainable and practical packaging solutions across various industries. In recent years, the global emphasis on eco-friendly products has led to a surge in the use of drawstring bags, particularly in retail and promotional sectors. International B2B buyers from Africa, South America, the Middle East, and Europe are increasingly sourcing these bags due to their versatility and lightweight nature, making them an ideal choice for events, giveaways, and merchandise.
Emerging trends include the integration of digital printing technologies, allowing for high-quality, customized designs that cater to specific branding needs. Additionally, the rise of e-commerce has prompted businesses to seek efficient packaging solutions that enhance customer experience while minimizing costs. Buyers should also be aware of the growing popularity of biodegradable and recyclable materials, as these options align with global sustainability goals and consumer preferences.
Furthermore, the shift towards online procurement platforms is reshaping the sourcing landscape. B2B buyers are leveraging these digital marketplaces to compare prices, quality, and supplier reliability, ensuring they make informed purchasing decisions. Adopting a data-driven approach to analyze market trends and supplier performance can significantly enhance sourcing strategies.
How Are Sustainability and Ethical Sourcing Impacting the Custom Drawstring Bags Market?
Sustainability is no longer just a trend but a critical factor influencing purchasing decisions in the custom drawstring bags sector. The environmental impact of plastic waste has led to a growing demand for eco-friendly alternatives, prompting manufacturers to adopt sustainable practices. International B2B buyers are increasingly prioritizing suppliers who demonstrate a commitment to ethical sourcing and sustainability, which includes using organic or recycled materials in their products.
Certifications such as Global Organic Textile Standard (GOTS) or OEKO-TEX can add significant value to a supplier’s offerings, reassuring buyers of the environmental integrity of their products. Additionally, the importance of transparency in supply chains cannot be overstated. Buyers are encouraged to conduct thorough due diligence to ensure their suppliers adhere to ethical labor practices and environmental regulations.
Investing in sustainable options not only enhances brand reputation but also meets the expectations of environmentally conscious consumers. As such, incorporating sustainability into sourcing strategies can provide a competitive edge in the increasingly conscious marketplace.
What Is the Historical Context of the Custom Drawstring Bags Market?
The custom drawstring bags market has evolved significantly over the past few decades. Initially popularized in the athletic and outdoor industries, these bags were primarily seen as functional items. However, the rise of branding and promotional activities in the late 1990s and early 2000s transformed their perception into stylish and practical marketing tools. As businesses began to realize the potential of drawstring bags as a cost-effective promotional item, their usage expanded across various sectors, including retail, education, and corporate events.
Today, the combination of technological advancements in materials and printing, along with a heightened focus on sustainability, has positioned custom drawstring bags as a staple in both marketing strategies and eco-friendly practices. This evolution underscores the importance of staying informed about market dynamics and sourcing trends for B2B buyers looking to optimize their procurement strategies.
Frequently Asked Questions (FAQs) for B2B Buyers of drawstring bags custom
-
How do I choose the right supplier for custom drawstring bags?
Selecting a reliable supplier for custom drawstring bags involves several steps. Start by researching potential suppliers through B2B platforms, trade shows, and industry referrals. Evaluate their experience, production capabilities, and customer reviews. Request samples to assess the quality of materials and craftsmanship. Additionally, verify their compliance with international trade regulations and sustainability practices, especially if sourcing from overseas. A thorough vetting process can mitigate risks and ensure you partner with a trustworthy supplier. -
What are the most important factors to consider when customizing drawstring bags?
When customizing drawstring bags, consider material quality, size, and design elements such as color, logo placement, and printing techniques. Choose materials that are durable and aligned with your brand image, whether it be eco-friendly fabrics or premium textiles. Additionally, ensure the size of the bags fits your target audience’s needs. Collaborate closely with your supplier to create a design that resonates with your brand identity while also being functional for end-users. -
What is the minimum order quantity (MOQ) for custom drawstring bags?
Minimum order quantities (MOQs) for custom drawstring bags vary by supplier, but they typically range from 100 to 1000 units. Factors influencing MOQ include the complexity of customization, production capabilities, and material costs. When negotiating with suppliers, discuss your specific needs and see if they can accommodate smaller orders, especially if you are a new business or testing a new product line. Understanding MOQs will help you plan your budget and inventory effectively. -
What payment terms should I expect when sourcing custom drawstring bags?
Payment terms when sourcing custom drawstring bags can vary widely among suppliers. Common practices include a deposit (typically 30-50%) upfront, with the balance due upon delivery or prior to shipping. Some suppliers may offer credit terms for established businesses. Ensure you clarify payment terms early in negotiations to avoid misunderstandings. Additionally, consider using secure payment methods such as letters of credit or escrow services to protect your financial interests. -
How can I ensure the quality of custom drawstring bags before delivery?
To ensure quality, establish a clear quality assurance (QA) process with your supplier. Request pre-production samples to confirm that the specifications meet your expectations. During production, consider scheduling quality inspections at various stages, or hire third-party inspection services if necessary. Clear communication regarding quality standards and expectations is crucial. Lastly, review the supplier’s return and refund policy to understand your options in case the delivered products do not meet the agreed specifications. -
What are the best practices for international shipping of custom drawstring bags?
For international shipping of custom drawstring bags, it’s vital to choose a reliable logistics provider experienced in handling bulk orders. Understand the shipping options available, including air freight for speed and sea freight for cost-effectiveness. Ensure all customs documentation is in order to avoid delays at borders. Additionally, consider insurance for high-value shipments. Collaborate with your supplier to determine the best shipping method that aligns with your budget and delivery timeline. -
How do I handle customs duties and import taxes for drawstring bags?
When importing custom drawstring bags, be aware of potential customs duties and import taxes that may apply. These costs depend on the country of origin, the destination, and the value of the goods. Research your country’s import regulations or consult with a customs broker to understand applicable tariffs. Accurate invoicing from your supplier can aid in a smoother customs process. Planning for these additional costs in your budget is essential to maintain profitability.
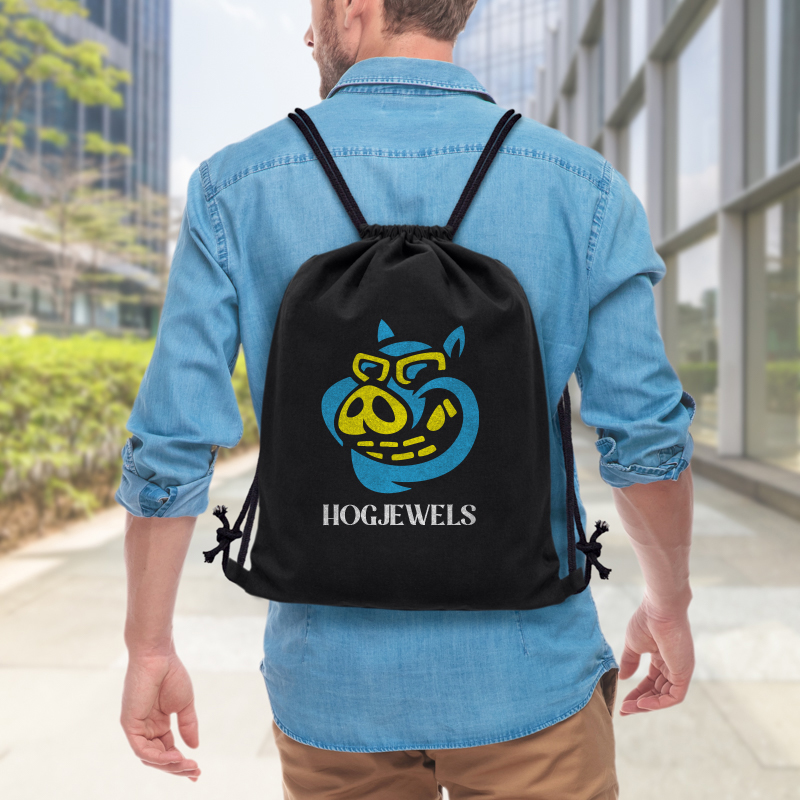
A stock image related to drawstring bags custom.
- What trends should I be aware of in the custom drawstring bag market?
Staying informed about market trends is crucial for competitive advantage. Currently, there is a growing demand for eco-friendly materials and designs that promote sustainability. Customization options such as unique prints and functional features (like pockets or reinforced straps) are also gaining popularity. Additionally, personalization is on the rise, with consumers seeking products that reflect their individual styles. Monitoring these trends can help you align your offerings with market demands and enhance customer satisfaction.
Important Disclaimer & Terms of Use
⚠️ Important Disclaimer
The information provided in this guide, including content regarding manufacturers, technical specifications, and market analysis, is for informational and educational purposes only. It does not constitute professional procurement advice, financial advice, or legal advice.
While we have made every effort to ensure the accuracy and timeliness of the information, we are not responsible for any errors, omissions, or outdated information. Market conditions, company details, and technical standards are subject to change.
B2B buyers must conduct their own independent and thorough due diligence before making any purchasing decisions. This includes contacting suppliers directly, verifying certifications, requesting samples, and seeking professional consultation. The risk of relying on any information in this guide is borne solely by the reader.
Strategic Sourcing Conclusion and Outlook for drawstring bags custom
In the competitive landscape of custom drawstring bags, strategic sourcing emerges as a critical component for international B2B buyers. By leveraging a well-defined sourcing strategy, businesses can ensure they obtain high-quality products at competitive prices, tailored to their specific needs. This approach not only optimizes supply chain efficiency but also enhances brand visibility, particularly in diverse markets across Africa, South America, the Middle East, and Europe.
How Can International Buyers Benefit from Strategic Sourcing of Custom Drawstring Bags?
Effective strategic sourcing allows buyers to identify reliable suppliers who can deliver consistent quality and innovation. Engaging with manufacturers that understand local market trends can lead to the development of unique designs that resonate with target audiences. Additionally, establishing long-term partnerships with suppliers can result in better pricing, priority in production, and improved service levels.
What Should Buyers Consider Moving Forward?
As the demand for eco-friendly and customized products continues to rise, it is essential for B2B buyers to stay ahead of trends and consumer preferences. By actively exploring sustainable materials and innovative designs, businesses can position themselves as market leaders. The future of the custom drawstring bag market is bright, and proactive sourcing strategies will play a pivotal role in navigating this evolving landscape.
Take action today by evaluating your sourcing strategies and exploring new partnerships that can elevate your brand in the global marketplace.