Discover Container House Prices in China: Your Ultimate Guide (2025)
Introduction: Navigating the Global Market for container house price china
In an increasingly interconnected world, sourcing container houses from China offers a unique opportunity for international B2B buyers seeking innovative and cost-effective building solutions. However, navigating the complexities of container house pricing can pose significant challenges. This guide is designed to empower decision-makers from diverse regions—Africa, South America, the Middle East, and Europe, including Italy and Saudi Arabia—by providing a comprehensive overview of the factors influencing container house prices in China.
Throughout this guide, we will explore various types of container houses, their applications across different industries, and the essential criteria for vetting suppliers. Moreover, we will delve into cost considerations, allowing buyers to make informed decisions that align with their budget and project requirements. By addressing critical questions such as “What are the key features that impact container house pricing?” and “How can I effectively assess the credibility of a supplier?” this resource serves as a strategic tool for navigating the global market.
Ultimately, this guide aims to facilitate a smooth sourcing process, ensuring that you can confidently invest in container houses that meet your business needs while maximizing value. Whether you are looking to expand your construction capabilities or diversify your offerings, understanding the landscape of container house pricing in China is crucial to your success in the global marketplace.
Understanding container house price china Types and Variations
Type Name | Key Distinguishing Features | Primary B2B Applications | Brief Pros & Cons for Buyers |
---|---|---|---|
Standard Container Homes | Built from one or more shipping containers, versatile designs | Temporary housing, offices | Pros: Cost-effective, quick assembly. Cons: Limited customization. |
Modular Container Units | Prefabricated sections that can be combined for larger spaces | Schools, healthcare facilities | Pros: Highly customizable, scalable. Cons: Higher initial investment. |
Luxury Container Homes | High-end finishes and amenities, often multi-story | Hospitality, executive housing | Pros: Aesthetic appeal, modern living. Cons: Expensive, longer build time. |
Eco-Friendly Container Homes | Incorporate sustainable materials and energy-efficient designs | Green building projects, eco-tourism | Pros: Lower environmental impact, energy savings. Cons: Potentially higher costs. |
Portable Container Offices | Designed for mobility, easy to transport and set up | Construction sites, remote work | Pros: Flexibility, quick deployment. Cons: Limited space, can be less durable. |
What Are Standard Container Homes and Their B2B Suitability?
Standard container homes are primarily constructed from one or more shipping containers, offering a range of design options. They are particularly suitable for temporary housing solutions, such as site offices or living quarters for workers in remote locations. B2B buyers should consider their cost-effectiveness and rapid assembly times, which can significantly reduce project timelines. However, the limited customization options may not meet all specific needs.
How Do Modular Container Units Work for Businesses?
Modular container units consist of prefabricated sections that can be assembled into larger structures. This type is ideal for businesses looking to establish schools or healthcare facilities quickly. Their scalability and high level of customization allow for tailored solutions that meet specific operational requirements. Nevertheless, the initial investment may be higher compared to standard units, requiring careful financial planning.
What Makes Luxury Container Homes Attractive to B2B Buyers?
Luxury container homes are designed with high-end finishes and amenities, often featuring multiple stories. They cater to businesses in the hospitality sector or those seeking executive housing solutions. The aesthetic appeal and modern living environments can attract higher-end clientele, but buyers should be aware of the significant costs and longer construction timelines associated with these premium offerings.
Why Choose Eco-Friendly Container Homes for Sustainable Projects?
Eco-friendly container homes utilize sustainable materials and energy-efficient designs, making them ideal for green building projects and eco-tourism initiatives. B2B buyers focused on sustainability will find these homes appealing due to their lower environmental impact and potential energy savings over time. However, the upfront costs may be higher, necessitating a thorough cost-benefit analysis.
What Are the Benefits of Portable Container Offices?
Portable container offices are specifically designed for mobility, allowing businesses to transport and set them up easily at various locations. They are particularly useful for construction sites or remote work environments. The flexibility and quick deployment of these units are significant advantages, although buyers should consider the limitations in space and potential durability issues when making their purchasing decisions.
Related Video: China Expandable container house —10 minutes one house!
Key Industrial Applications of container house price china
Industry/Sector | Specific Application of Container House Price China | Value/Benefit for the Business | Key Sourcing Considerations for this Application |
---|---|---|---|
Construction | Temporary Site Offices | Cost-effective, portable solutions for project management | Quality of materials, compliance with local regulations |
Oil & Gas | Worker Accommodations | Enhanced workforce morale and safety in remote locations | Durability, insulation, and customization options |
Education | Mobile Classrooms | Flexible educational environments for underserved areas | Educational standards, accessibility features |
Hospitality | Modular Hotels | Rapid deployment and scalability for tourism hotspots | Aesthetic design, local market trends |
Agriculture | Storage Units for Equipment and Produce | Efficient space management and protection from elements | Ventilation, pest control, and temperature regulation |
How are Container Houses Used in Construction Projects?
In the construction industry, container houses serve as temporary site offices, providing a practical solution for managing various project activities. Their modular nature allows for quick setup and relocation, which is essential for projects in remote or developing areas. International buyers, particularly from Africa and South America, should consider sourcing options that ensure compliance with local building codes and regulations, as well as the quality of materials used to withstand environmental conditions.
What Role Do Container Houses Play in the Oil & Gas Sector?
For the oil and gas industry, container houses are often utilized as worker accommodations in remote locations. These structures enhance workforce morale by providing safe, comfortable living quarters, which is crucial for productivity in challenging environments. Buyers in the Middle East and Europe should prioritize durability and insulation in their sourcing decisions to ensure that these units can withstand extreme weather conditions while offering customization options to meet specific operational needs.
How Can Container Houses Enhance Educational Opportunities?
Container houses are increasingly being repurposed as mobile classrooms, especially in regions with limited educational infrastructure. They provide a flexible and cost-effective solution for delivering education in underserved areas. International buyers, particularly in Africa and South America, should focus on educational standards and accessibility features when sourcing these units to ensure they meet the needs of diverse student populations.
In What Ways Do Container Houses Benefit the Hospitality Industry?
The hospitality sector has embraced container houses as modular hotels, allowing for rapid deployment in tourist hotspots. This innovative approach not only reduces construction time but also offers scalability to meet fluctuating demand. B2B buyers from Europe, particularly Italy, should consider aesthetic design and alignment with local market trends when sourcing container homes for hospitality purposes, ensuring that they appeal to the target demographic.
How are Container Houses Utilized in Agriculture?
In agriculture, container houses are effectively used as storage units for equipment and produce, providing efficient space management while protecting valuable assets from the elements. These structures can be customized for ventilation and pest control, which is vital for maintaining produce quality. Buyers from South America and Africa should pay attention to features such as temperature regulation and durability to ensure that their investments meet the specific requirements of their agricultural practices.
Related Video: The Most Affordable Way To Build Your First Container House!
3 Common User Pain Points for ‘container house price china’ & Their Solutions
Scenario 1: Navigating the Complexity of Pricing Structures for Container Houses
The Problem: B2B buyers often encounter confusion regarding the pricing structures associated with container houses sourced from China. Variations in pricing can arise due to several factors, including material quality, customization options, and fluctuating market conditions. Buyers may find it challenging to interpret quotes that include hidden fees or costs for shipping, taxes, and duties. This lack of transparency can lead to budget overruns and unexpected financial burdens, complicating the procurement process.
The Solution: To mitigate this challenge, B2B buyers should prioritize obtaining detailed quotations from multiple suppliers. It is essential to request itemized pricing that breaks down costs for materials, labor, customization, and shipping. Additionally, engaging in direct communication with suppliers can clarify any ambiguous terms and conditions. Utilizing tools such as price comparison websites and industry reports can provide insights into standard pricing trends, helping buyers to negotiate better deals. Establishing a transparent relationship with suppliers will not only streamline the purchasing process but also enhance trust, ensuring a smoother transaction.
Scenario 2: Quality Assurance Concerns When Buying Container Houses from China
The Problem: International buyers often grapple with concerns about the quality of container houses produced in China. The fear of receiving subpar products—due to inadequate quality control or differing construction standards—can deter companies from making significant investments. This is particularly critical in regions like Africa and South America, where local regulations may differ from those in China, making it harder to ensure compliance and safety.
The Solution: To address quality assurance concerns, B2B buyers should implement a rigorous vetting process for potential suppliers. This includes requesting certifications, such as ISO standards, which demonstrate adherence to international quality management practices. Additionally, prospective buyers should consider visiting manufacturing facilities or engaging third-party inspection services to conduct quality checks before shipment. Establishing a clear set of quality expectations and conducting regular audits can ensure that the final product meets the required standards. Furthermore, leveraging testimonials or case studies from previous clients can help gauge a supplier’s reliability and product quality.
Scenario 3: Overcoming Delivery Delays and Logistical Challenges
The Problem: Delivery delays are a common pain point for B2B buyers sourcing container houses from China. Factors such as shipping bottlenecks, customs clearance, and regional transportation issues can lead to significant project setbacks, affecting timelines and budgets. This situation can be particularly stressful for buyers in sectors like construction and real estate, where timely delivery is crucial for project success.
The Solution: To combat potential delivery delays, B2B buyers should develop a comprehensive logistics plan before placing orders. This plan should include selecting suppliers with a proven track record of on-time delivery and evaluating their shipping methods. Buyers should also consider using freight forwarders who specialize in international shipping to navigate customs regulations and expedite the clearance process. Building buffer time into project schedules can accommodate unforeseen delays, ensuring that timelines remain manageable. Regular communication with suppliers and logistics partners can also provide updates on shipment status, allowing buyers to make informed decisions and adjustments as needed.
Strategic Material Selection Guide for container house price china
When selecting materials for container houses, international B2B buyers must consider various factors that influence performance, cost, and compliance with local regulations. This guide analyzes common materials used in container house construction, focusing on their properties, advantages, disadvantages, and specific considerations for buyers from Africa, South America, the Middle East, and Europe.
What Are the Key Properties of Steel in Container House Construction?
Steel is the primary material used in the construction of shipping containers. Its key properties include high tensile strength, excellent durability, and resistance to various environmental factors. Steel can withstand significant pressure and temperature fluctuations, making it suitable for diverse climates.
Pros and Cons of Using Steel:
– Pros: Steel is highly durable, has a long lifespan, and provides excellent structural integrity. It is also recyclable, which can appeal to environmentally conscious buyers.
– Cons: The initial cost can be high, and it may require additional treatments to prevent corrosion, especially in humid environments.
Impact on Application:
Steel’s strength makes it ideal for load-bearing structures, but its susceptibility to rust in coastal areas necessitates protective coatings. Buyers should consider the local environment to ensure longevity.
Considerations for International Buyers:
Compliance with international standards like ASTM A36 for structural steel is crucial. Buyers should also be aware of local regulations regarding the use of recycled materials.
How Does Wood Compare as a Material for Container Houses?
Wood is often used for interior finishes and insulation in container houses. Its natural insulating properties help maintain temperature control, which is essential in regions with extreme climates.
Pros and Cons of Using Wood:
– Pros: Wood is lightweight, easy to work with, and provides excellent thermal insulation. It can also enhance aesthetics, appealing to buyers looking for a more natural look.
– Cons: Wood is less durable than steel and is susceptible to pests and moisture damage, requiring regular maintenance.
Impact on Application:
Wood is suitable for non-structural applications but may not be ideal for load-bearing components. Buyers in humid regions should consider treated wood to prevent decay.
Considerations for International Buyers:
Buyers should ensure that the wood complies with local building codes and standards, such as the European EN 1995 for timber structures. Sustainable sourcing practices are increasingly important to European buyers.
What Are the Advantages of Using Insulation Materials in Container Houses?
Insulation materials, such as polyurethane foam or mineral wool, are critical for energy efficiency in container houses. They help regulate indoor temperatures, reducing heating and cooling costs.
Pros and Cons of Using Insulation:
– Pros: Insulation materials improve energy efficiency and comfort, and they can also reduce noise levels. They are relatively easy to install.
– Cons: Some insulation materials may have a higher upfront cost and require specific installation techniques to ensure effectiveness.
Impact on Application:
The choice of insulation affects the overall energy performance of the container house. Buyers should consider the insulation’s R-value to ensure adequate thermal resistance.
Considerations for International Buyers:
Compliance with energy efficiency standards, such as the International Energy Conservation Code (IECC), is essential. Buyers should also be aware of local regulations regarding fire safety and material safety data sheets (MSDS).
How Do Finishing Materials Affect the Overall Aesthetic of Container Houses?
Finishing materials, including paints, cladding, and flooring, play a vital role in the aesthetics and functionality of container houses. These materials can enhance the visual appeal and provide additional protection against environmental factors.
Pros and Cons of Using Finishing Materials:
– Pros: Finishing materials can improve the overall look and feel of a container house while providing protection against weathering.
– Cons: Some finishes may require regular maintenance and can be costly, depending on the quality and type selected.
Impact on Application:
Finishing materials can significantly impact the durability and maintenance of the structure. Buyers should consider the local climate when selecting finishes to ensure longevity.
Considerations for International Buyers:
Buyers should ensure that finishing materials comply with local aesthetic guidelines and environmental regulations. Certifications for low VOC (volatile organic compounds) emissions may also be essential in certain markets.
Summary Table of Material Selection for Container Houses
Material | Typical Use Case for container house price china | Key Advantage | Key Disadvantage/Limitation | Relative Cost (Low/Med/High) |
---|---|---|---|---|
Steel | Structural framework | High durability and strength | Corrosion risk in humid climates | High |
Wood | Interior finishes and insulation | Excellent thermal insulation | Susceptible to pests and moisture | Medium |
Insulation | Energy efficiency and comfort | Improves energy efficiency | Higher upfront cost | Medium |
Finishing Materials | Aesthetics and protection | Enhances visual appeal | Requires maintenance | Medium to High |
This strategic material selection guide provides B2B buyers with the necessary insights to make informed decisions when sourcing container houses from China. Understanding the properties, advantages, and compliance needs of each material will help ensure successful projects tailored to specific regional requirements.
In-depth Look: Manufacturing Processes and Quality Assurance for container house price china
What Are the Main Stages in the Manufacturing Process of Container Houses from China?
Manufacturing container houses involves several critical stages that ensure durability, functionality, and aesthetic appeal. Understanding these processes is vital for B2B buyers looking to source high-quality container houses from China.
Material Preparation: What Raw Materials Are Used in Container House Manufacturing?
The first stage in manufacturing container houses is material preparation. High-quality steel is the primary material used, known for its structural integrity and resistance to environmental factors. Other materials may include insulation materials, plywood, and high-grade paint for weatherproofing. Suppliers often source these materials from certified vendors, ensuring they meet specific industry standards.
B2B buyers should inquire about the origin of materials and any certifications they may have. This can provide assurance regarding the sustainability and quality of the materials used.
How Are Container Houses Formed During Manufacturing?
The forming stage involves cutting, welding, and assembling the steel containers into the desired shapes and sizes. Advanced techniques such as laser cutting and robotic welding are commonly employed to enhance precision and efficiency. This stage is crucial, as it directly affects the structural integrity of the final product.
Buyers should assess whether their suppliers utilize modern machinery and skilled labor in this stage. Inquire about the types of technology employed and the qualifications of the workforce, as this can impact both the quality and cost of the container houses.
What Is Involved in the Assembly Process of Container Houses?
Following forming, the assembly process integrates various components, including windows, doors, plumbing, and electrical systems. This stage often involves a modular approach, allowing for customization according to client specifications.
International B2B buyers should ensure that their suppliers offer flexibility in design and are open to modifications to meet specific needs. A supplier with a robust assembly process can deliver a product that aligns closely with client expectations.
What Finishing Techniques Are Used to Enhance Container House Aesthetics?
Finishing touches are essential for both functionality and appearance. This includes painting, applying sealants, and adding interior finishes. Quality control during this stage is critical to ensure that the final product is not only visually appealing but also resistant to weather conditions.
Buyers should ask about the types of finishes available and any options for customization. Understanding the finishing techniques used can help buyers gauge the long-term durability of the container houses.
What Quality Assurance Measures Are Implemented in Container House Manufacturing?
Quality assurance (QA) is a fundamental aspect of the manufacturing process, ensuring that the final product meets international standards and customer requirements.
Which International Standards Are Relevant for Container House Manufacturing?
B2B buyers should look for suppliers that adhere to international quality standards such as ISO 9001, which emphasizes effective quality management systems. Additionally, industry-specific certifications like CE (Conformité Européenne) and API (American Petroleum Institute) may be applicable, depending on the intended use of the container houses.
Understanding these certifications can help buyers evaluate the credibility and reliability of suppliers. It’s advisable to request copies of these certifications during the sourcing process.
What Are the Key Quality Control Checkpoints in Container House Manufacturing?
Quality control is typically segmented into several checkpoints: Incoming Quality Control (IQC), In-Process Quality Control (IPQC), and Final Quality Control (FQC).
- Incoming Quality Control (IQC): This stage involves inspecting raw materials upon delivery. Ensuring that materials meet specified standards is crucial for the integrity of the final product.
- In-Process Quality Control (IPQC): During production, ongoing inspections ensure that each step complies with quality standards. This includes monitoring welding and assembly processes.
- Final Quality Control (FQC): Before shipping, a comprehensive inspection is conducted to ensure that the container houses meet all specifications and quality standards.
B2B buyers should inquire about the specific QC measures employed at each checkpoint and request detailed reports on these inspections.
How Can B2B Buyers Verify Supplier Quality Control?
To ensure that suppliers adhere to quality control standards, B2B buyers can undertake several verification methods:
- Conduct Audits: Performing audits on the manufacturing facilities can provide insights into the production process and adherence to quality standards.
- Request Quality Reports: Suppliers should provide detailed quality reports that outline the findings from each quality control checkpoint.
- Engage Third-party Inspectors: Utilizing third-party inspection services can add an extra layer of assurance. These inspectors can evaluate the manufacturing process and the final product independently.
For buyers from Africa, South America, the Middle East, and Europe, understanding the nuances of QC can facilitate smoother transactions and reduce the risk of sourcing inferior products.
What Common Testing Methods Are Used in Quality Assurance for Container Houses?
Several testing methods are commonly employed to ensure the quality and safety of container houses:
- Structural Integrity Tests: These tests assess the strength and durability of the container under various conditions.
- Thermal and Insulation Tests: These tests evaluate the effectiveness of insulation materials, ensuring energy efficiency and comfort.
- Water Resistance Tests: To confirm that the container houses can withstand heavy rainfall and moisture, water resistance testing is critical.
Buyers should inquire about the specific testing methods used and the results from recent tests. This information is vital for understanding the long-term viability of the container houses being purchased.
Conclusion: How to Ensure Quality in Sourcing Container Houses from China?
In summary, understanding the manufacturing processes and quality assurance measures for container houses is essential for B2B buyers. By focusing on material selection, manufacturing techniques, quality control checkpoints, and testing methods, buyers can make informed decisions that lead to successful sourcing from China. Engaging with suppliers who prioritize quality and transparency will ultimately result in more reliable partnerships and superior products.
Practical Sourcing Guide: A Step-by-Step Checklist for ‘container house price china’
The procurement of container houses from China can be a daunting task for international B2B buyers, especially when navigating varying regulations, quality standards, and logistical challenges. This practical sourcing guide aims to provide a clear checklist to streamline the purchasing process, ensuring that buyers make informed decisions that align with their business needs.
Step 1: Define Your Technical Specifications
Before reaching out to suppliers, establish your technical requirements. Determine the size, design, insulation, and materials needed for the container house. This clarity helps suppliers provide accurate quotes and solutions tailored to your needs.
- Consider local climate: Insulation requirements may vary significantly based on whether you are sourcing for Africa, Europe, or the Middle East.
- Purpose of the container house: Define if it’s for residential, commercial, or temporary use, as this impacts design and material choices.
Step 2: Conduct Market Research on Container House Prices
Understanding the market price for container houses in China is crucial for budget planning. Research the average costs, including shipping and import duties.
- Compare different suppliers: Use online platforms, trade shows, and industry reports to gather pricing data.
- Factor in total cost of ownership: Include installation, maintenance, and potential customization in your budget.
Step 3: Evaluate Potential Suppliers
Thoroughly vet potential suppliers to ensure reliability and quality. Request company profiles, certifications, and references from other international buyers.
- Look for experience: Suppliers with a proven track record in exporting to your region may have better insights into compliance and logistics.
- Check for quality certifications: ISO certifications or local quality marks can indicate a commitment to high manufacturing standards.
Step 4: Request Detailed Quotations
Once you have identified potential suppliers, request detailed quotations that break down costs. This transparency is essential for accurate budgeting.
- Ask for itemized costs: Ensure that quotes include all aspects such as materials, labor, shipping, and any applicable taxes.
- Inquire about payment terms: Understand the payment schedule, including deposits and final payments.
Step 5: Verify Compliance with Local Regulations
Ensure that the container houses comply with local building codes and safety regulations in your region. This is particularly important for international shipments.
- Consult local authorities: Engaging with local building inspectors can provide insights into what is required for compliance.
- Check for necessary permits: Some regions may require specific permits for imported structures.
Step 6: Negotiate Terms and Conditions
Once you are satisfied with a supplier, enter negotiations to finalize the terms. Address payment terms, delivery timelines, and warranty conditions.
- Be clear about expectations: Ensure that both parties understand the terms to avoid misunderstandings later.
- Discuss after-sales support: Ask about warranty coverage and support for repairs or modifications.
Step 7: Plan for Logistics and Shipping
Finally, consider the logistics of transporting your container house. Work with a freight forwarder experienced in handling large shipments.
- Evaluate shipping options: Compare costs and transit times for different shipping methods.
- Understand customs requirements: Ensure all documentation is in order to avoid delays at customs.
By following these steps, B2B buyers can navigate the complexities of sourcing container houses from China effectively, ensuring they secure the best value while meeting their specific needs.
Comprehensive Cost and Pricing Analysis for container house price china Sourcing
What Are the Key Cost Components for Container Houses Sourced from China?
When evaluating the cost of container houses sourced from China, it’s essential to understand the various cost components involved. The primary cost factors include:
-
Materials: The choice of materials significantly impacts the overall price. Steel prices fluctuate based on global demand, and additional features like insulation, finishes, and fixtures can add to the material costs.
-
Labor: Labor costs in China are relatively low compared to many Western countries. However, the quality of labor can vary, influencing the craftsmanship and, ultimately, the price.
-
Manufacturing Overhead: This includes costs related to factory operations such as utilities, rent, and administrative expenses. Efficient manufacturing processes can help minimize these costs.
-
Tooling: If custom modifications or specialized designs are required, tooling costs can increase. It’s crucial to communicate specific requirements to suppliers to get accurate tooling estimates.
-
Quality Control (QC): Ensuring the product meets international standards requires investment in quality control processes. This might include inspections and testing, which are vital for compliance with regulations in the buyer’s country.
-
Logistics: Transportation costs can vary based on the shipping method (sea freight, air freight) and distance. Additionally, customs duties and taxes must be factored into the total cost.
-
Margin: Suppliers will also incorporate their profit margin into the final pricing. This varies based on the supplier’s market positioning and their perceived value of the product.
How Do Price Influencers Affect Container House Pricing?
Several factors influence the pricing of container houses sourced from China:
-
Volume and Minimum Order Quantity (MOQ): Larger orders often attract bulk discounts. Understanding the supplier’s MOQ is crucial for cost efficiency.
-
Specifications and Customization: Custom designs or specific features can increase costs. Buyers should clearly outline their requirements to receive accurate quotes.
-
Materials: The choice of high-quality or eco-friendly materials can raise the price. Buyers should weigh the benefits of these materials against their budget constraints.
-
Quality and Certifications: Products that meet international certifications (like ISO or CE) may command higher prices due to the assurance of quality and safety.
-
Supplier Factors: Established suppliers with a strong reputation may charge more. However, their reliability can save costs in the long run through reduced risk of defects and delays.
-
Incoterms: Understanding Incoterms (International Commercial Terms) is vital, as they define the responsibilities of buyers and sellers regarding shipping, insurance, and tariffs. This can significantly affect the total landed cost.
What Are the Best Negotiation Tips for International B2B Buyers?
To optimize costs when sourcing container houses from China, international B2B buyers can leverage several negotiation strategies:
-
Research and Benchmarking: Understand market prices and benchmarks before initiating negotiations. This knowledge will empower you to negotiate better terms and prices.
-
Build Relationships: Establishing a good rapport with suppliers can lead to more favorable terms and pricing. Regular communication fosters trust, which can yield long-term benefits.
-
Focus on Total Cost of Ownership (TCO): Rather than solely negotiating the initial purchase price, consider the TCO, which includes shipping, installation, maintenance, and operational costs. This holistic view can lead to better financial decisions.
-
Be Transparent: Clearly communicate your budget constraints and requirements. Suppliers are more likely to work with you if they understand your needs and limitations.
-
Consider Payment Terms: Negotiating favorable payment terms can improve cash flow. Discuss options like partial payments or extended payment periods.
What Pricing Nuances Should Buyers from Africa, South America, the Middle East, and Europe Consider?
International B2B buyers from regions such as Africa, South America, the Middle East, and Europe should be aware of specific pricing nuances:
-
Currency Fluctuations: Exchange rates can affect the final cost. Using hedging strategies or negotiating prices in a stable currency can mitigate risks.
-
Regulatory Compliance: Ensure that the container houses meet local building codes and regulations. Non-compliance can lead to additional costs for modifications or fines.
-
Cultural Considerations: Understanding cultural differences in negotiation styles can enhance communication with suppliers. This is particularly important in regions with distinct business practices.
Disclaimer for Indicative Prices
Prices for container houses sourced from China can vary widely based on the aforementioned factors. It is advisable to obtain multiple quotes and conduct thorough market research to ensure competitive pricing. Always consider the total cost of ownership in your decision-making process.
Alternatives Analysis: Comparing container house price china With Other Solutions
In the realm of innovative housing solutions, the demand for container houses from China has surged, especially among international B2B buyers. However, it is crucial for buyers to explore alternative options that can meet their specific needs. This section will compare the pricing and features of container houses from China with two viable alternatives: prefabricated modular homes and traditional brick-and-mortar construction.
Comparison Table of Container House Price China and Alternatives
Comparison Aspect | Container House Price China | Prefabricated Modular Homes | Traditional Brick-and-Mortar Construction |
---|---|---|---|
Performance | Durable and weather-resistant | High energy efficiency | Excellent thermal mass |
Cost | $1,200 – $2,500 per unit | $1,500 – $3,000 per unit | $2,000 – $4,500 per unit |
Ease of Implementation | Quick setup (1-2 weeks) | Moderate setup (4-8 weeks) | Lengthy setup (3-6 months) |
Maintenance | Low maintenance required | Moderate maintenance | High maintenance due to material wear |
Best Use Case | Affordable housing, remote areas | Urban housing, temporary sites | Permanent housing, high-density areas |
What Are the Advantages and Disadvantages of Prefabricated Modular Homes?
Prefabricated modular homes are built off-site and then assembled on location. They offer a balance between efficiency and customization. The benefits include energy efficiency and faster construction compared to traditional methods. However, they often come with higher initial costs and may not provide the same level of durability as container houses. For B2B buyers in regions with strict building codes, such as Europe, modular homes can offer a compliant alternative that meets sustainability goals.
How Do Traditional Brick-and-Mortar Constructions Compare?
Traditional brick-and-mortar construction remains a popular choice due to its long-standing reputation for durability and thermal efficiency. These structures can withstand extreme weather conditions and are often viewed as more aesthetically pleasing. However, the high costs and lengthy construction times can deter buyers, particularly in fast-paced markets. For B2B buyers in Africa and South America, where rapid urbanization is occurring, this method may not be the most practical option for meeting immediate housing needs.
Conclusion: How Can B2B Buyers Choose the Right Housing Solution?
When selecting a housing solution, B2B buyers must consider several factors such as budget, project timelines, and specific use cases. Container houses from China offer a cost-effective and quick-to-implement solution ideal for affordable housing and temporary projects. On the other hand, prefabricated modular homes provide a more energy-efficient option suitable for urban developments. Traditional brick-and-mortar construction, while durable, may not align with the urgency of modern housing demands in many regions. Ultimately, the best choice will depend on the buyer’s unique requirements, local market conditions, and long-term goals.
Essential Technical Properties and Trade Terminology for container house price china
What Are the Key Technical Properties of Container Houses from China?
When sourcing container houses from China, understanding the technical properties is crucial for ensuring quality and suitability for your specific needs. Here are some essential specifications to consider:
-
Material Grade
– Container houses are typically constructed from high-grade steel, often Corten or marine-grade steel, which provides superior corrosion resistance. The material grade directly affects durability and lifespan, making it essential for international buyers to request detailed specifications from suppliers. -
Tolerance Levels
– Tolerance refers to the permissible limits of variation in a physical dimension. For container houses, this can include wall thickness and structural dimensions. Precise tolerances ensure structural integrity and facilitate easier assembly, especially important for modular projects. Understanding these levels helps buyers avoid costly modifications later. -
Insulation Properties
– The thermal insulation value, often measured in R-values, indicates how well the container house can retain heat or coolness. In regions with extreme climates, such as the Middle East or South America, adequate insulation is vital for energy efficiency and occupant comfort. Buyers should inquire about insulation materials used and their performance ratings. -
Weight Capacity
– Each container has a specified weight capacity that dictates what can be safely placed inside. This is critical for buyers planning to use the container house for specific purposes, such as residential living or commercial storage. Ensure that your supplier provides detailed load-bearing specifications to avoid structural issues. -
Dimensions and Customization Options
– Standard shipping containers come in various sizes (20ft, 40ft, etc.), but customization is often necessary for specific applications. Understanding the dimensions and available modifications is essential for aligning the product with your project requirements. Discussing customization options with suppliers can lead to cost-effective solutions tailored to your needs.
What Common Trade Terms Should B2B Buyers Know When Sourcing Container Houses?
Navigating the trade landscape requires familiarity with specific jargon that can impact negotiations and transactions. Here are key terms relevant to sourcing container houses from China:
-
OEM (Original Equipment Manufacturer)
– This term refers to companies that produce products based on specifications provided by another company. In the context of container houses, an OEM might manufacture containers designed by an architectural firm. Understanding OEM relationships can help buyers secure unique designs and quality assurance. -
MOQ (Minimum Order Quantity)
– MOQ is the minimum number of units a supplier is willing to sell. This is particularly important for B2B buyers, as it can impact budget and inventory management. Knowing the MOQ helps buyers gauge potential costs and negotiate better deals, especially when dealing with international suppliers. -
RFQ (Request for Quotation)
– An RFQ is a formal process where buyers solicit price quotes from suppliers for specific products. This is essential for comparing prices and terms across multiple vendors, ensuring that buyers get the best value for their investment in container houses. -
Incoterms (International Commercial Terms)
– These are a set of predefined international trade terms that clarify the responsibilities of buyers and sellers in shipping agreements. Familiarity with Incoterms (like FOB, CIF, and EXW) helps buyers understand shipping costs, risks, and logistics involved in importing container houses from China. -
Lead Time
– Lead time refers to the time taken from placing an order to delivery. Understanding lead times is crucial for project planning, especially in regions with tight construction schedules. Buyers should communicate with suppliers to set realistic timelines based on production capacity and shipping logistics.
By familiarizing yourself with these technical properties and trade terms, you can make informed decisions when sourcing container houses from China, ensuring that your investment aligns with your project requirements and business objectives.
Navigating Market Dynamics and Sourcing Trends in the container house price china Sector
What are the Current Market Dynamics and Key Trends in the Container House Price China Sector?
The container house market, particularly in China, is experiencing significant growth due to several global drivers. Increasing urbanization and a pressing demand for affordable housing solutions are at the forefront of this trend. Countries in Africa and South America, where traditional construction methods may not meet the rising demand for housing, are looking towards container homes as a viable alternative. In the Middle East, particularly in Saudi Arabia, the focus on rapid urban development and infrastructure projects further fuels interest in modular housing solutions.
Emerging B2B technology trends, such as digital supply chain management and e-commerce platforms, are transforming how international buyers source container houses. Companies are increasingly adopting digital tools to facilitate transparency and efficiency in their procurement processes. Additionally, the integration of Building Information Modeling (BIM) in design and construction phases is gaining traction, allowing for better visualization and customization of container homes, which is particularly appealing to European buyers seeking tailored solutions.
Moreover, fluctuating raw material prices and international trade policies are influencing container house pricing in China. Buyers must stay informed about these dynamics to negotiate better deals and optimize their supply chain strategies.
How is Sustainability Impacting Sourcing Trends for Container Houses from China?
Sustainability has become a crucial factor for international B2B buyers in the container house sector. The environmental impact of construction is under scrutiny, and buyers are increasingly favoring suppliers who prioritize sustainable practices. This includes using recycled materials, minimizing waste, and implementing energy-efficient designs.
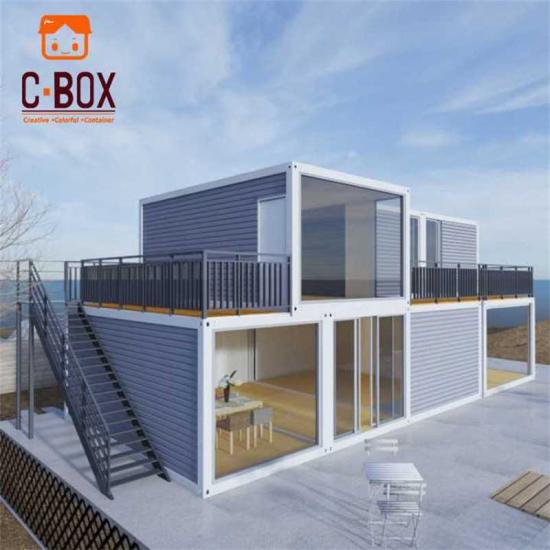
A stock image related to container house price china.
Ethical sourcing is equally important, as buyers from Europe and the Middle East are demanding transparency in their supply chains. This has led to an increase in certifications for ‘green’ materials and practices, such as LEED (Leadership in Energy and Environmental Design) and ISO 14001, which are becoming essential in supplier evaluations. Buyers should seek out manufacturers in China who not only meet these standards but can also provide documentation to verify their compliance.
Investing in sustainable container houses not only meets regulatory requirements but also appeals to environmentally conscious consumers, ultimately enhancing brand reputation and market competitiveness. Therefore, B2B buyers should prioritize partnerships with suppliers who demonstrate a commitment to sustainability and ethical sourcing.
What is the Historical Evolution of the Container House Market in China?
The container house concept originated in the 1950s as a means to provide quick and affordable housing solutions. Over the decades, this idea evolved, particularly in China, where rapid industrialization and urbanization necessitated innovative housing solutions. The 21st century marked a significant turning point, as the Chinese government began to promote container houses as a part of its sustainable development agenda.
In recent years, the container house market has expanded beyond temporary housing to include permanent residential and commercial structures. This evolution reflects a growing acceptance of alternative building methods and materials among international buyers. As the market continues to mature, the focus is shifting towards customization, sustainability, and integration with smart technologies, positioning container homes as a forward-thinking solution in the global housing crisis.
By understanding these dynamics, international B2B buyers can make informed decisions that align with market trends and consumer preferences.
Frequently Asked Questions (FAQs) for B2B Buyers of container house price china
-
How do I determine the average container house price from China?
To assess the average container house price from China, consider factors such as design specifications, materials used, and shipping costs. Research multiple suppliers on platforms like Alibaba or Global Sources, and request detailed quotations. Pricing can vary significantly based on customization options, size, and additional features like insulation or electrical systems. Additionally, engage with trade associations or industry reports that provide insights into market trends and pricing benchmarks. -
What are the key factors influencing container house prices in China?
Container house prices in China are influenced by several factors, including material quality, design complexity, size, and insulation features. The choice of manufacturer also plays a crucial role; established manufacturers with a good reputation may charge a premium for their products. Additionally, fluctuations in raw material costs, labor expenses, and exchange rates can impact pricing. Always request a detailed breakdown of costs from suppliers to understand these influences better. -
What customization options are available for container houses from China?
Most manufacturers in China offer a range of customization options for container houses, including layout modifications, interior finishes, and exterior designs. You can choose from various materials for insulation, flooring, and roofing. Additionally, many suppliers allow for adjustments in size and the inclusion of features like windows, doors, and utilities. Always confirm the customization capabilities of your chosen supplier to ensure they align with your project requirements. -
What is the minimum order quantity (MOQ) for container houses from Chinese suppliers?
The minimum order quantity (MOQ) for container houses varies by supplier and can range from a single unit to several units. Smaller manufacturers may accept lower MOQs, while larger companies might require orders of multiple units to ensure cost-effectiveness. Discuss your project needs directly with potential suppliers to negotiate favorable terms, especially if you are looking for a single unit or a small batch for testing purposes. -
What payment terms should I expect when sourcing container houses from China?
Payment terms for container houses typically include a deposit upfront (often 30% to 50%) with the balance due before shipping. Some suppliers may offer flexible terms, such as letters of credit or payment through escrow services to ensure security. It’s essential to clarify payment terms early in negotiations to avoid misunderstandings. Always conduct due diligence on the supplier’s payment reputation and consider using secure payment methods. -
How can I vet suppliers for container houses in China?
Vetting suppliers involves checking their business licenses, certifications, and industry reputation. Utilize platforms like Alibaba’s Trade Assurance or Global Sources to identify verified suppliers. Request references or testimonials from previous clients and conduct factory visits if possible. Additionally, consider engaging third-party inspection services to assess product quality before shipment, ensuring that the supplier meets your standards. -
What quality assurance measures should I implement when sourcing container houses?
Implementing quality assurance measures includes establishing clear specifications and standards before placing an order. Conduct regular communication with suppliers throughout the production process and consider third-party inspections to verify compliance with your quality requirements. Request samples or prototypes before finalizing larger orders to ensure the product meets your expectations. Having a clear agreement on quality standards in your contract can also help mitigate potential issues. -
What are the logistics considerations for importing container houses from China?
Logistics considerations include understanding shipping methods (e.g., sea freight is common for large units), customs regulations, and potential tariffs. Plan for the transportation of container houses from the manufacturer to your destination, considering inland transportation and final delivery logistics. Work with a freight forwarder experienced in handling containerized goods to navigate the complexities of international shipping. Ensure all necessary documentation, such as bills of lading and customs declarations, are prepared to avoid delays.
Important Disclaimer & Terms of Use
⚠️ Important Disclaimer
The information provided in this guide, including content regarding manufacturers, technical specifications, and market analysis, is for informational and educational purposes only. It does not constitute professional procurement advice, financial advice, or legal advice.
While we have made every effort to ensure the accuracy and timeliness of the information, we are not responsible for any errors, omissions, or outdated information. Market conditions, company details, and technical standards are subject to change.
B2B buyers must conduct their own independent and thorough due diligence before making any purchasing decisions. This includes contacting suppliers directly, verifying certifications, requesting samples, and seeking professional consultation. The risk of relying on any information in this guide is borne solely by the reader.
Strategic Sourcing Conclusion and Outlook for container house price china
As the global demand for container houses continues to grow, particularly in emerging markets across Africa, South America, the Middle East, and Europe, strategic sourcing becomes paramount for international B2B buyers. Understanding the fluctuating prices of container houses in China is crucial for making informed purchasing decisions. Key factors influencing these prices include raw material costs, transportation logistics, and evolving market trends.
How Can Strategic Sourcing Enhance Your Procurement Process?
Implementing a strategic sourcing approach enables businesses to identify reliable suppliers, negotiate favorable terms, and optimize supply chains. By fostering strong relationships with manufacturers in China, buyers can secure competitive pricing and ensure consistent quality. This strategic alignment not only mitigates risks associated with price volatility but also enhances overall project timelines and efficiency.
What Is the Future Outlook for Container House Prices in China?
Looking ahead, international buyers should remain vigilant about market dynamics and technological advancements that could impact container house pricing. The rise of sustainable construction practices and increased demand for customizable solutions may reshape the landscape. By staying informed and proactive, B2B buyers can leverage opportunities for growth and innovation.
In conclusion, the key to successful procurement lies in strategic sourcing. Engage with your suppliers, explore market trends, and position your business for success in the evolving container house market.