Discover Cost-Effective Control Panel Manufacturers (2025)
Introduction: Navigating the Global Market for Control Panel Manufacturers
Navigating the complexities of sourcing reliable control panel manufacturers can be a daunting challenge for international B2B buyers, particularly those in Africa, South America, the Middle East, and Europe. The need for high-quality control panels that comply with regional standards and regulations is paramount, yet the market is saturated with options, making the selection process overwhelming. This guide aims to demystify the landscape of control panel manufacturers by providing comprehensive insights into various types, applications, and the vital best practices for supplier vetting.
Throughout this guide, buyers will discover essential criteria for evaluating suppliers, including compliance with international standards and certifications, quality assurance practices, and cost considerations. Additionally, we will explore the diverse applications of control panels across industries such as energy, manufacturing, and automation, helping buyers understand how to align their specific needs with the right products.
Ultimately, this resource empowers B2B buyers to make informed purchasing decisions, ensuring they select manufacturers that not only meet their technical requirements but also align with their strategic business goals. By equipping buyers with the knowledge needed to navigate this competitive market, we aim to facilitate successful partnerships and drive operational efficiency across various sectors.
Understanding Control Panel Manufacturers Types and Variations
Type Name | Key Distinguishing Features | Primary B2B Applications | Brief Pros & Cons for Buyers |
---|---|---|---|
Custom Control Panels | Tailored design for specific operational needs | Manufacturing, Energy, Automation | Pros: Unique fit for requirements; optimized performance. Cons: Higher cost; longer lead times. |
Standard Control Panels | Pre-defined configurations for common applications | HVAC, Lighting, Water Treatment | Pros: Cost-effective; quicker delivery. Cons: Limited customization; may not fit all needs. |
Modular Control Panels | Composed of interchangeable components | Robotics, Packaging, Material Handling | Pros: Flexible design; easy upgrades. Cons: Complexity in assembly; potential compatibility issues. |
Integrated Control Panels | Combines control with monitoring and communication systems | Smart Buildings, Industrial Automation | Pros: Enhanced functionality; real-time data. Cons: Higher initial investment; may require specialized training. |
Explosion-Proof Control Panels | Designed for hazardous environments | Oil & Gas, Chemical Processing | Pros: Safety compliant; reliable in extreme conditions. Cons: Heavier and more expensive; limited availability. |
What Are Custom Control Panels and Their Benefits for B2B Buyers?
Custom control panels are specifically designed to meet the unique operational requirements of a business. They allow for tailored solutions that optimize performance in various applications, such as manufacturing and energy. B2B buyers should consider the upfront costs and lead times associated with these panels, as they tend to be more expensive and require longer production periods. However, the investment can lead to significant efficiency gains and reduced operational issues in the long run.
How Do Standard Control Panels Serve B2B Applications?
Standard control panels are pre-manufactured and designed for common applications, making them a cost-effective option for businesses. They are widely used in HVAC systems, lighting control, and water treatment facilities. The primary advantage of standard panels is their quick availability and lower price point. However, buyers should be aware that these panels may not fully meet specific operational needs, which could lead to inefficiencies in some cases.
What Are the Advantages of Modular Control Panels in B2B Settings?
Modular control panels consist of interchangeable components, allowing businesses to customize their systems as needs evolve. This flexibility is particularly beneficial in industries like robotics and packaging, where rapid changes in technology and processes are common. Buyers should consider the ease of upgrades and modifications that modular panels offer, although they may face challenges related to assembly complexity and compatibility of various components.
Why Choose Integrated Control Panels for Enhanced Functionality?
Integrated control panels combine control functions with advanced monitoring and communication systems, making them ideal for smart buildings and industrial automation. These panels provide real-time data and enhanced functionality, helping businesses streamline operations. While they offer significant advantages, B2B buyers should be prepared for a higher initial investment and the potential need for specialized training to effectively utilize the technology.
What Makes Explosion-Proof Control Panels Essential in Hazardous Environments?
Explosion-proof control panels are designed for use in hazardous environments, such as oil and gas or chemical processing industries. These panels are built to withstand extreme conditions and comply with safety regulations, ensuring reliable operation in dangerous settings. Although they come with higher costs and may be heavier than standard options, the safety and reliability they provide are critical for businesses operating in high-risk areas. Buyers must weigh the importance of safety against budgetary constraints when considering these options.
Related Video: What is an Electrical Control Panel? (PLC Panel Basics)
Key Industrial Applications of Control Panel Manufacturers
Industry/Sector | Specific Application of Control Panel Manufacturers | Value/Benefit for the Business | Key Sourcing Considerations for this Application |
---|---|---|---|
Energy & Infrastructure | Smart Grid Control Panels | Enhanced energy distribution and management | Compliance with local regulations and standards, reliability, and scalability |
Manufacturing | Automation Control Panels for Production Lines | Increased efficiency and reduced downtime | Customization options, integration capabilities with existing systems |
Water & Wastewater | SCADA Control Panels for Water Treatment Facilities | Improved monitoring and operational efficiency | Durability in harsh environments, ease of maintenance, and support services |
Food & Beverage | Process Control Panels for Production and Quality Assurance | Ensured product safety and consistency | Compliance with food safety standards, adaptability to various processes |
Transportation & Logistics | Control Panels for Automated Material Handling Systems | Streamlined operations and reduced labor costs | Robustness under varying loads, compatibility with automation technologies |
How Control Panel Manufacturers Enhance Energy & Infrastructure
In the energy and infrastructure sector, smart grid control panels are pivotal for managing and optimizing energy distribution. These panels enable real-time monitoring of electrical systems, allowing businesses to efficiently manage energy consumption and reduce operational costs. For international buyers, particularly in Africa and the Middle East, sourcing control panels that comply with local regulations and standards is crucial. Reliability and scalability are also key considerations, as these systems must adapt to growing energy demands and integrate with existing infrastructure.
Automation Control Panels in Manufacturing
Manufacturing industries leverage automation control panels to enhance production line efficiency. These panels facilitate the seamless operation of machinery, reducing downtime and increasing throughput. Buyers from South America and Europe should prioritize customization options to ensure that control panels meet specific manufacturing processes. Additionally, integration capabilities with existing systems are vital, as they ensure a smooth transition and minimal disruption during implementation.
SCADA Control Panels in Water & Wastewater Management
SCADA (Supervisory Control and Data Acquisition) control panels are essential in water treatment facilities, providing improved monitoring and operational efficiency. These panels allow for real-time data collection and analysis, enabling quick responses to system anomalies. For international buyers, especially in regions with challenging climates like Africa, sourcing durable control panels that can withstand harsh environments while being easy to maintain is critical. Support services and training for local staff should also be considered to ensure effective operation.
Process Control Panels in Food & Beverage Production
In the food and beverage sector, process control panels play a crucial role in maintaining product safety and quality. These panels monitor various production parameters, ensuring compliance with food safety standards. International buyers, particularly in Europe, must ensure that control panels are adaptable to various production processes and comply with stringent regulations. The ability to provide reliable data logging and reporting is also essential for meeting industry standards.
Control Panels for Transportation & Logistics Automation
Control panels are integral to automated material handling systems in transportation and logistics. They streamline operations by controlling equipment such as conveyor systems and automated guided vehicles, ultimately reducing labor costs. For buyers in South America and the Middle East, sourcing robust control panels that can handle varying loads and are compatible with automation technologies is crucial. Ensuring that these systems can integrate with existing logistics frameworks will further enhance operational efficiency.
Related Video: Industrial Control Panel Basics
3 Common User Pain Points for ‘Control Panel Manufacturers’ & Their Solutions
Scenario 1: Navigating Compliance with Regional Standards
The Problem: For B2B buyers in regions like Africa and South America, ensuring compliance with local and international standards for control panels can be a daunting task. Many manufacturers may not be fully aware of the specific regulations that apply to their products in different markets. This can lead to costly delays, rework, or even penalties if the panels fail to meet the required specifications. Buyers may struggle with understanding the certification processes, documentation requirements, and the implications of non-compliance for their operations.
The Solution: To effectively navigate compliance, B2B buyers should begin by conducting thorough research on the regulatory standards applicable in their regions, such as IEC standards or specific national regulations. Engage with control panel manufacturers who are transparent about their compliance certifications and can provide documented proof of adherence to relevant standards. Additionally, consider requesting samples or prototypes for testing before making bulk purchases. Establishing a collaborative relationship with manufacturers can also facilitate knowledge sharing on compliance requirements, ensuring that both parties are aligned on expectations and standards.
Scenario 2: Addressing Customization Needs Efficiently
The Problem: Many buyers require customized control panels to meet the unique operational demands of their industries. However, the process of communicating these specifications to manufacturers can lead to misunderstandings, resulting in products that do not meet expectations. This scenario is particularly common in sectors like energy and manufacturing, where specific functionalities or integration with existing systems are critical. The lack of effective communication can lead to increased lead times, higher costs, and operational inefficiencies.
The Solution: To overcome this challenge, buyers should clearly define their requirements using detailed specifications and diagrams. Utilizing tools such as 3D modeling or CAD software can help visualize the desired outcome, making it easier for manufacturers to understand the customization needed. Furthermore, establishing regular communication channels, such as weekly check-ins or project management platforms, can help keep both parties on the same page throughout the design and manufacturing process. Buyers should also seek manufacturers with a proven track record in customization and flexibility, as these companies are more likely to have processes in place that accommodate unique requests efficiently.
Scenario 3: Mitigating Downtime Due to Equipment Failure
The Problem: Unexpected equipment failure in industrial settings can lead to significant downtime, which is costly for any business. Buyers may find themselves frustrated when control panels malfunction, either due to poor design, inadequate testing, or the use of subpar components. This issue is particularly pressing in sectors such as manufacturing and energy, where continuous operation is critical to profitability. The resulting disruption can affect production schedules and strain customer relationships.
The Solution: To mitigate the risk of downtime, B2B buyers should prioritize sourcing from reputable control panel manufacturers known for their reliability and quality assurance processes. Look for manufacturers that offer warranties, after-sales support, and a robust history of performance in similar applications. It’s also advisable to implement a proactive maintenance strategy, including regular inspections and diagnostics of control panel systems. Buyers should consider investing in training for their teams on the operation and troubleshooting of control panels to reduce response times in the event of a failure. Additionally, establishing a partnership with manufacturers for ongoing support can provide access to expertise and resources that can help prevent issues before they escalate.
Strategic Material Selection Guide for Control Panel Manufacturers
What Are the Key Materials for Control Panel Manufacturers?
When selecting materials for control panels, manufacturers must consider various factors, including durability, cost, and application compatibility. Below, we analyze four common materials used in control panel manufacturing, focusing on their properties, advantages, disadvantages, and specific considerations for international B2B buyers.
How Does Steel Perform as a Material for Control Panels?
Key Properties: Steel is known for its high strength and durability, with a temperature rating that can withstand extreme conditions. It has good corrosion resistance when treated with coatings or galvanization.
Pros & Cons: The primary advantage of steel is its robustness, making it suitable for heavy-duty applications. However, it can be heavier and more expensive than alternatives like aluminum. Manufacturing complexity increases with the need for additional treatments to prevent rust and corrosion.
Impact on Application: Steel is compatible with a variety of media, including oils and chemicals, but may not be suitable for environments with high humidity unless adequately protected.
Considerations for International Buyers: Buyers from regions like Africa and the Middle East should ensure compliance with local corrosion resistance standards, such as ASTM A123 for galvanized steel.
What Are the Advantages of Using Aluminum in Control Panels?
Key Properties: Aluminum is lightweight and has excellent corrosion resistance, especially when anodized. It can withstand moderate temperatures and pressures.
Pros & Cons: The key advantage of aluminum is its low weight, which simplifies installation and reduces shipping costs. However, it is less strong than steel and can be more expensive per unit of strength.
Impact on Application: Aluminum is compatible with many media, including water and mild chemicals, making it a versatile choice for various applications.
Considerations for International Buyers: European buyers often prefer aluminum due to its recyclability and compliance with environmental regulations. Standards such as DIN EN 573 for aluminum alloys should be considered.
How Does Plastic Compare for Control Panel Applications?
Key Properties: Plastics, such as polycarbonate and ABS, are lightweight and have excellent insulation properties. They also offer good chemical resistance and can handle moderate temperatures.
Pros & Cons: The main advantage of plastic is its low cost and ease of manufacturing, making it suitable for mass production. However, plastics may not be as durable as metals and can degrade under UV exposure.
Impact on Application: Plastics are suitable for environments where electrical insulation is critical, but they may not withstand high mechanical stress.
Considerations for International Buyers: Buyers in South America should look for compliance with international standards like ISO 9001 for quality management systems, which can affect the reliability of plastic components.
What Role Does Stainless Steel Play in Control Panel Manufacturing?
Key Properties: Stainless steel offers excellent corrosion resistance and can withstand high temperatures and pressures, making it ideal for harsh environments.
Pros & Cons: The key advantage of stainless steel is its durability and aesthetic appeal. However, it is generally more expensive than carbon steel and can be more challenging to machine.
Impact on Application: Stainless steel is highly compatible with a wide range of media, including corrosive substances, making it suitable for chemical and food processing industries.
Considerations for International Buyers: Compliance with standards like ASTM A240 for stainless steel grades is crucial for buyers in Europe and the Middle East, where quality and safety regulations are stringent.
Summary Table of Material Selection for Control Panel Manufacturers
Material | Typical Use Case for Control Panel Manufacturers | Key Advantage | Key Disadvantage/Limitation | Relative Cost (Low/Med/High) |
---|---|---|---|---|
Steel | Heavy-duty industrial applications | High strength and durability | Heavier and requires corrosion treatment | Medium |
Aluminum | Lightweight control panels for various media | Lightweight and corrosion resistant | Less strength than steel | Medium |
Plastic | Electrical insulation in moderate environments | Low cost and easy to manufacture | Less durable, UV degradation possible | Low |
Stainless Steel | Harsh environments, chemical processing | Excellent corrosion resistance | Higher cost and machining complexity | High |
By understanding the properties and implications of these materials, international B2B buyers can make informed decisions that align with their operational needs and compliance requirements.
In-depth Look: Manufacturing Processes and Quality Assurance for Control Panel Manufacturers
What Are the Main Stages of Manufacturing Processes for Control Panels?
Manufacturing control panels involves a series of precise steps, each critical to ensuring the final product meets industry standards and customer expectations. The main stages include material preparation, forming, assembly, and finishing.
-
Material Preparation
– The process begins with sourcing high-quality materials, such as metals for enclosures, wires, and electronic components. Suppliers should be vetted for compliance with international standards like ISO 9001 to ensure quality consistency.
– In this stage, raw materials are inspected for defects, and specifications are confirmed. This initial quality check is critical, as it sets the foundation for the entire manufacturing process. -
Forming
– Forming involves shaping the materials into the desired configuration. This can include cutting, bending, and machining processes. Advanced techniques such as CNC (Computer Numerical Control) machining ensure precision and repeatability.
– For B2B buyers, understanding the forming techniques used can indicate the level of sophistication in the manufacturing process. Reliable manufacturers often invest in state-of-the-art machinery to maintain high standards. -
Assembly
– The assembly stage is where components are integrated into the panel. This includes wiring, mounting devices like switches and relays, and ensuring proper connectivity.
– Attention to detail is crucial; manufacturers often implement strict protocols to minimize errors. Using techniques like modular assembly can facilitate easier repairs and upgrades in the future. -
Finishing
– The finishing stage involves applying protective coatings, labeling, and conducting final inspections. This ensures that the panels not only function correctly but also comply with aesthetic and safety standards.
– Quality control measures during this phase can significantly impact the longevity and reliability of the control panels.
How Is Quality Assurance Implemented in Control Panel Manufacturing?
Quality assurance (QA) is an integral part of the control panel manufacturing process, ensuring that products meet both international and industry-specific standards.
-
What Are the Relevant International Standards for Control Panels?
– Control panel manufacturers often adhere to ISO 9001 for quality management systems. This certification signifies a commitment to continuous improvement and customer satisfaction.
– Other industry-specific certifications may include CE marking for compliance with European safety standards and API (American Petroleum Institute) certifications for panels used in the oil and gas sector. -
What Are the Key Quality Control Checkpoints?
– Incoming Quality Control (IQC): This is the first checkpoint where materials are inspected upon arrival. Ensuring that raw materials meet specified criteria prevents defects in the final product.
– In-Process Quality Control (IPQC): During the manufacturing process, regular inspections are conducted to monitor assembly and fabrication stages. This proactive approach helps identify and rectify issues before they escalate.
– Final Quality Control (FQC): Once the panels are fully assembled, a comprehensive final inspection is conducted. This includes functional testing to ensure that all components work as intended. -
What Common Testing Methods Are Used in Quality Assurance?
– Testing methods can include electrical performance tests, thermal cycling tests, and environmental stress tests. These procedures help simulate real-world conditions, ensuring reliability and safety.
– Manufacturers may also use automated testing equipment for efficiency, allowing for consistent and accurate results.
How Can B2B Buyers Verify Supplier Quality Control?
International B2B buyers must take proactive steps to ensure that their suppliers maintain high-quality standards. Here are some actionable insights:
-
Conduct Supplier Audits
– Regular audits of potential suppliers can reveal their adherence to quality standards. An audit should assess their manufacturing processes, equipment, and quality control measures.
– Buyers from regions like Africa, South America, and the Middle East may need to consider travel logistics or utilize virtual audit tools to connect with suppliers. -
Request Quality Reports and Certifications
– B2B buyers should request copies of quality assurance reports and certifications from manufacturers. These documents provide insight into the supplier’s compliance with international standards.
– Look for certifications from recognized organizations, as these can serve as a benchmark for quality. -
Engage Third-Party Inspection Services
– Utilizing third-party inspection services can provide an unbiased assessment of the manufacturer’s quality control processes. These inspectors can verify compliance with relevant standards and provide detailed reports.
– This step is particularly beneficial for buyers unfamiliar with the local manufacturing landscape or for those importing products from regions with different regulatory requirements.
What Are the Quality Control Nuances for International B2B Buyers?
Understanding the quality control nuances specific to various markets is essential for international B2B buyers.
-
Cultural and Regulatory Differences
– Buyers from Europe may have different expectations regarding quality assurance compared to those from Africa or South America. Familiarize yourself with local regulations and standards to ensure compliance.
– For example, European standards often emphasize environmental sustainability and energy efficiency, while Middle Eastern markets may focus on durability and resilience in harsh climates. -
Supply Chain Considerations
– The supply chain’s complexity can affect quality control. Buyers should consider local sourcing vs. international sourcing and the implications for quality assurance.
– Establishing strong relationships with suppliers can facilitate better communication regarding quality expectations and lead to improved outcomes. -
Technological Advancements in Quality Control
– The adoption of Industry 4.0 technologies, such as IoT (Internet of Things) and AI (Artificial Intelligence), is transforming quality control processes. Buyers should inquire about their suppliers’ technological capabilities to ensure they are using the latest methods for quality assurance.
By understanding these manufacturing processes and quality assurance practices, international B2B buyers can make informed decisions when selecting control panel manufacturers, ultimately ensuring the reliability and performance of their investments.
Practical Sourcing Guide: A Step-by-Step Checklist for ‘Control Panel Manufacturers’
This guide is designed to assist international B2B buyers in effectively sourcing control panel manufacturers. Given the complexity and critical nature of control panels in various industries, following a structured approach will ensure that you choose the right supplier to meet your specific needs.
Step 1: Define Your Technical Specifications
Before initiating the sourcing process, clearly outline your technical requirements. This includes the type of control panel you need, such as PLC-based, HMI-integrated, or safety control panels. Clearly defined specifications not only help in communicating your needs to potential suppliers but also ensure that you receive accurate quotes and proposals.
- Considerations:
- Voltage and current ratings
- Environmental conditions (temperature, humidity, etc.)
- Compliance with local and international standards
Step 2: Research Potential Suppliers
Conduct thorough research to compile a list of potential control panel manufacturers. Use online directories, industry associations, and trade shows to identify reputable suppliers with a proven track record.
- Key Sources:
- Industry-specific websites
- Networking platforms like LinkedIn
- Trade exhibitions relevant to your sector
Step 3: Evaluate Supplier Certifications
Confirm that your shortlisted suppliers hold relevant industry certifications. These may include ISO 9001 for quality management, UL certification for safety, and CE marking for compliance with European regulations.
- Why It Matters:
- Certifications indicate adherence to quality and safety standards.
- They can prevent future liabilities and ensure reliability in operations.
Step 4: Request Detailed Proposals
Once you have narrowed down your options, request detailed proposals from the selected manufacturers. This should include pricing, delivery timelines, and warranty information.
- What to Look For:
- Transparency in pricing (including hidden costs)
- Comprehensive service agreements
- Clear timelines for project milestones and delivery
Step 5: Assess Manufacturing Capabilities
Understanding the manufacturing capabilities of your potential suppliers is crucial. Evaluate their production capacity, technology used, and whether they can customize solutions to meet your specific needs.
- Key Questions:
- What technologies do they use for manufacturing?
- Can they scale production to meet future demands?
- Do they offer customization for unique project requirements?
Step 6: Check References and Past Projects
Request references and case studies from previous clients. This will provide insights into the supplier’s reliability, quality of work, and customer service.
- Considerations:
- Look for clients in similar industries or regions.
- Evaluate the outcomes of past projects and any challenges faced.
Step 7: Negotiate Terms and Finalize the Contract
Once you have selected a supplier, negotiate the terms of the contract. Ensure that all details, including payment terms, delivery schedules, and post-installation support, are clearly outlined.
- Key Focus Areas:
- Payment milestones
- Penalties for late delivery
- Support and maintenance agreements post-purchase
By following this checklist, international B2B buyers can streamline the sourcing process for control panel manufacturers, ensuring they make informed and strategic decisions that align with their operational needs.
Comprehensive Cost and Pricing Analysis for Control Panel Manufacturers Sourcing
What Are the Key Cost Components in Control Panel Manufacturing?
When sourcing control panels, understanding the comprehensive cost structure is essential for B2B buyers. The primary cost components include:
-
Materials: The choice of materials significantly affects the overall cost. High-quality components, such as durable enclosures, reliable circuit boards, and advanced wiring, can drive up expenses but are crucial for ensuring longevity and compliance with safety standards.
-
Labor: Labor costs vary significantly based on geographical location. Manufacturers in regions with lower labor costs may offer competitive pricing, but it is essential to assess their skill level and experience to ensure quality.
-
Manufacturing Overhead: This includes indirect costs such as utilities, rent, and administrative expenses associated with the manufacturing process. Understanding the overhead can provide insights into the manufacturer’s pricing strategy.
-
Tooling: Initial tooling costs can be substantial, especially for custom control panels. Buyers should inquire about whether these costs are included in the price or charged separately.
-
Quality Control (QC): Implementing stringent quality control measures is vital for ensuring product reliability. Manufacturers may pass these costs onto buyers, so understanding their QC processes can help buyers gauge the overall value.
-
Logistics: Shipping and handling costs can vary widely based on the supplier’s location and the chosen Incoterms. International shipping can introduce additional costs, including customs duties and taxes.
-
Margin: Suppliers typically add a profit margin to their costs. Understanding industry standards for margins can help buyers negotiate better prices.
How Do Price Influencers Impact Control Panel Costs?
Several factors influence the pricing of control panels, which B2B buyers should consider:
-
Volume and Minimum Order Quantity (MOQ): Suppliers often provide discounts for larger orders, which can significantly reduce the per-unit cost. Understanding the MOQ can help buyers plan their purchases more effectively.
-
Specifications and Customization: Custom-designed control panels may incur additional costs due to unique specifications. Buyers should clearly communicate their requirements to avoid unexpected charges.
-
Materials: The selection of materials not only impacts durability but also pricing. High-grade materials may lead to higher upfront costs but can reduce long-term maintenance expenses.
-
Quality and Certifications: Panels that meet specific industry standards or certifications may be priced higher. Buyers should weigh the benefits of compliance against the cost.
-
Supplier Factors: Reputation, experience, and reliability of the supplier can influence pricing. Established suppliers with proven track records may charge more but offer better quality and service.
-
Incoterms: The chosen Incoterms can significantly affect total costs. Buyers should understand their responsibilities regarding shipping, insurance, and duties to avoid hidden costs.
What Are the Best Negotiation Tips for B2B Buyers?
To maximize cost-efficiency when sourcing control panels, consider the following strategies:
-
Research and Compare: Collect quotes from multiple suppliers to understand the market price. This information can serve as leverage during negotiations.
-
Focus on Total Cost of Ownership (TCO): Instead of solely considering the initial purchase price, evaluate the TCO, which includes maintenance, durability, and potential downtime costs. This approach can justify higher upfront costs for better quality.
-
Be Transparent About Needs: Clearly communicate your needs and constraints to suppliers. This transparency can foster collaboration and lead to better pricing agreements.
-
Negotiate Payment Terms: Consider negotiating payment terms to improve cash flow, such as extended payment periods or discounts for upfront payments.
-
Consider Long-Term Relationships: Building a long-term partnership with a supplier can lead to better pricing and priority service. Suppliers may offer loyalty discounts or favorable terms for repeat business.
What Should International Buyers Keep in Mind?
For international B2B buyers, particularly from Africa, South America, the Middle East, and Europe, understanding the nuances of pricing is crucial:
-
Currency Fluctuations: Be aware of how currency exchange rates may impact pricing, especially for large transactions.
-
Cultural Differences: Negotiation styles and business practices vary across regions. Understanding these differences can enhance communication and facilitate better deals.
-
Regulatory Compliance: Ensure that the control panels meet local regulations and standards to avoid additional costs related to compliance failures.
-
Supply Chain Reliability: Assess the supplier’s ability to deliver on time, as delays can lead to increased costs in production and project timelines.
In conclusion, understanding the comprehensive cost structure, price influencers, and effective negotiation strategies is essential for international B2B buyers in the control panel manufacturing sector. By focusing on these aspects, buyers can make informed decisions that enhance their procurement process and overall business efficiency.
Alternatives Analysis: Comparing Control Panel Manufacturers With Other Solutions
When considering the procurement of control panel solutions, B2B buyers must evaluate various alternatives to traditional control panel manufacturers. The choice of solution can significantly impact operational efficiency, safety, and cost-effectiveness. This section delves into viable alternatives, comparing them across critical aspects that matter to international buyers, particularly in regions like Africa, South America, the Middle East, and Europe.
Comparison Table of Control Panel Solutions
Comparison Aspect | Control Panel Manufacturers | Programmable Logic Controllers (PLCs) | Remote Monitoring Systems |
---|---|---|---|
Performance | High reliability and customization | High flexibility with automation capabilities | Real-time data analytics and monitoring |
Cost | Typically higher due to customization | Moderate initial cost with potential for long-term savings | Varies widely based on technology and scale |
Ease of Implementation | Requires skilled technicians for installation | User-friendly interfaces; relatively easy to implement | May require integration with existing systems |
Maintenance | Regular checks and updates needed | Low maintenance, but requires software updates | Dependent on network reliability and security |
Best Use Case | Complex and large-scale industrial applications | Manufacturing processes needing automation | Facilities requiring continuous monitoring and data collection |
What Are the Pros and Cons of Programmable Logic Controllers (PLCs)?
PLCs serve as a flexible alternative to traditional control panels, especially in automation-heavy environments. They are designed to perform discrete and continuous control tasks, making them suitable for various industries, from manufacturing to food processing.
Pros:
– Flexibility: Easily programmed to handle different tasks and processes.
– Automation Capabilities: Can integrate with sensors and other devices to automate operations, reducing labor costs and errors.
Cons:
– Learning Curve: While user-friendly, there can still be a learning curve for new users unfamiliar with programming languages.
– Initial Costs: Although they may save costs in the long run, the initial investment can be significant, especially for advanced systems.
How Do Remote Monitoring Systems Compare?
Remote monitoring systems provide real-time visibility into operations, which can enhance decision-making and responsiveness. They are particularly useful in environments where continuous oversight is required, such as utilities and large manufacturing plants.
Pros:
– Real-Time Insights: Allow for immediate data access, enabling quick responses to issues.
– Scalability: Can be expanded easily as business needs grow without significant additional infrastructure.
Cons:
– Dependency on Connectivity: Effectiveness is tied to internet and network reliability, which can be a concern in some regions.
– Security Risks: Increased connectivity can expose systems to cyber threats, necessitating robust cybersecurity measures.
How Can B2B Buyers Choose the Right Solution?
In selecting the appropriate solution, B2B buyers should consider their specific operational needs, budget constraints, and long-term goals. If flexibility and automation are paramount, PLCs may be the best fit. However, for organizations focused on real-time data and monitoring, remote monitoring systems could provide significant advantages. Ultimately, understanding the unique requirements of their operations will guide buyers toward the most suitable choice, ensuring they maximize efficiency and minimize costs in their control systems.
Essential Technical Properties and Trade Terminology for Control Panel Manufacturers
What Are the Key Technical Properties for Control Panels?
Understanding the essential technical properties of control panels is crucial for B2B buyers in ensuring the quality and reliability of their purchases. Here are some critical specifications to consider:
1. Material Grade: Why Does It Matter?
The material used in control panel construction significantly impacts durability, thermal conductivity, and resistance to environmental factors. Common materials include steel, aluminum, and fiberglass. Selecting the right material grade ensures that the panel can withstand specific environmental conditions, such as humidity and temperature fluctuations, which is especially important in regions like Africa and South America.
2. Tolerance Levels: How Do They Affect Performance?
Tolerance levels refer to the acceptable variation in dimensions and specifications. In control panels, precise tolerances are vital for ensuring components fit together correctly and function as intended. Poor tolerances can lead to operational inefficiencies, increased wear and tear, and ultimately, higher maintenance costs.
3. IP Rating: What Protection Does Your Panel Offer?
Ingress Protection (IP) ratings classify the degree of protection a control panel offers against dust and moisture. An IP65 rating, for instance, indicates that the panel is dust-tight and protected against water jets. For buyers in humid or dusty environments, understanding IP ratings can prevent costly damage and operational downtime.
4. Voltage and Current Ratings: What Are the Limits?
Voltage and current ratings define the electrical limits of the control panel. These ratings are crucial for ensuring that the panel can handle the intended load without overheating or failing. Buyers should verify that the ratings align with their specific application requirements to ensure safety and reliability.
5. Thermal Management: How Is Heat Dissipation Managed?
Effective thermal management is essential for the longevity of control panels. This involves the design of heat sinks, ventilation systems, or the use of cooling fans. Understanding thermal management strategies can help buyers select panels that maintain optimal operating temperatures, especially in high-load applications.
What Are the Common Trade Terms in Control Panel Manufacturing?
Familiarity with industry terminology can streamline communication and negotiations between buyers and manufacturers. Here are several essential terms:
1. OEM (Original Equipment Manufacturer): What Does It Signify?
An OEM refers to a company that produces parts or equipment that may be marketed by another manufacturer. For buyers, working with OEMs can ensure high-quality components that meet specific standards, which is especially important when sourcing equipment from international suppliers.
2. MOQ (Minimum Order Quantity): Why Is It Important?
MOQ defines the smallest quantity of a product that a supplier is willing to sell. Understanding MOQ is vital for buyers to manage inventory effectively and minimize costs. For companies in emerging markets, negotiating MOQs can lead to more favorable terms and cost savings.
3. RFQ (Request for Quotation): How Should You Use It?
An RFQ is a document sent to suppliers to request pricing for specific products or services. This is a critical tool for buyers to obtain competitive pricing and evaluate supplier capabilities. A well-prepared RFQ can lead to better deals and stronger supplier relationships.
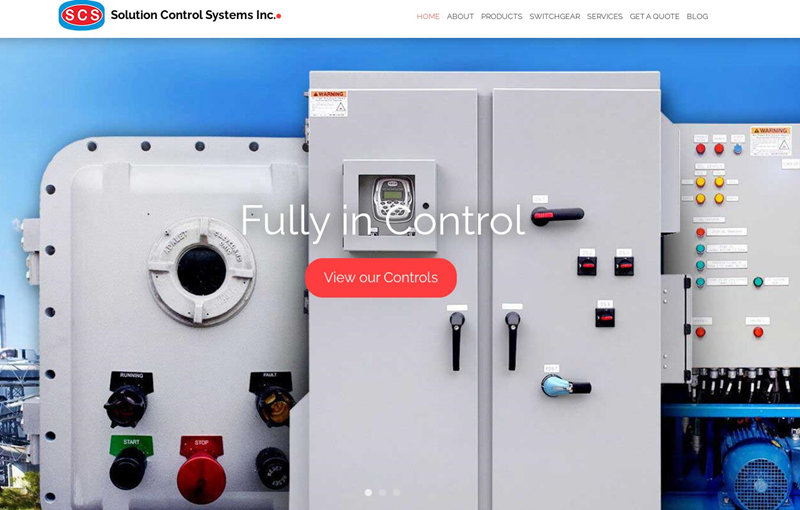
A stock image related to Control Panel Manufacturers.
4. Incoterms: What Are They and Why Do They Matter?
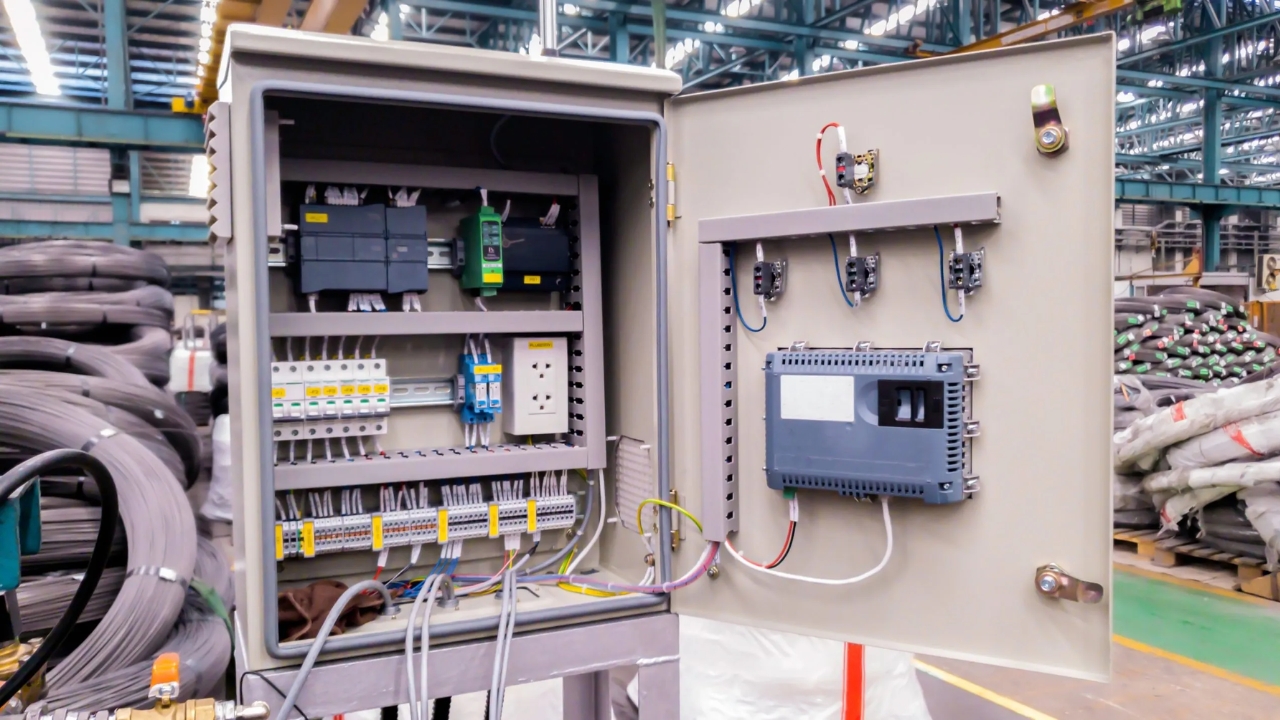
A stock image related to Control Panel Manufacturers.
Incoterms (International Commercial Terms) define the responsibilities of buyers and sellers in international transactions. They clarify aspects such as shipping costs, insurance, and risk transfer. Understanding Incoterms helps buyers avoid unexpected costs and ensures smoother logistics, which is particularly important for international transactions.
5. Lead Time: How Does It Impact Your Supply Chain?
Lead time refers to the time taken from placing an order to its delivery. For B2B buyers, understanding lead times is essential for planning and ensuring that projects stay on schedule. Long lead times can disrupt operations, so it’s important to factor this into procurement strategies.
By grasping these technical properties and industry terms, international B2B buyers can make informed decisions, ensuring they select the right control panel manufacturers for their specific needs.
Navigating Market Dynamics and Sourcing Trends in the Control Panel Manufacturers Sector
What Are the Key Market Dynamics and Trends in Control Panel Manufacturing?
The control panel manufacturing sector is experiencing a transformative phase driven by several global factors. Increasing automation in industries such as manufacturing, energy, and transportation is pushing demand for advanced control panels that facilitate efficient operations. Notably, the surge in smart manufacturing, which incorporates IoT technologies, has led to a rise in the integration of control panels with advanced monitoring and control systems. International buyers from Africa, South America, the Middle East, and Europe should consider the implications of these technological advancements in their sourcing strategies.
Additionally, the shift towards digitalization is prompting manufacturers to adopt cloud-based solutions, enabling remote monitoring and management of control systems. This trend is particularly relevant for buyers looking to enhance operational efficiency and reduce downtime. Emerging markets are also witnessing a rise in infrastructure development, creating opportunities for control panel manufacturers. Understanding these dynamics is crucial for international buyers to align their procurement strategies with market trends.
How Can Sustainability and Ethical Sourcing Impact Control Panel Manufacturing?
Sustainability and ethical sourcing have become pivotal considerations for international B2B buyers in the control panel manufacturing sector. The environmental impact of production processes is under scrutiny, compelling manufacturers to adopt sustainable practices. This includes the use of eco-friendly materials and energy-efficient production methods. Buyers should prioritize suppliers that adhere to sustainability certifications, such as ISO 14001, which demonstrates a commitment to environmental management.
Moreover, ethical sourcing practices are gaining traction as consumers increasingly demand transparency in supply chains. Buyers are encouraged to evaluate potential suppliers based on their labor practices and commitment to social responsibility. Engaging with manufacturers who prioritize ethical sourcing not only enhances brand reputation but also mitigates risks associated with non-compliance to international labor standards. By focusing on sustainability and ethics, international buyers can contribute to a greener future while ensuring the reliability of their supply chains.
How Has the Control Panel Manufacturing Sector Evolved Over Time?
The control panel manufacturing sector has undergone significant evolution, shaped by technological advancements and changing market demands. Initially, control panels were simple assemblies designed for basic electrical functions. However, the advent of programmable logic controllers (PLCs) in the late 20th century revolutionized the industry, allowing for more complex and flexible control systems.
In recent years, the integration of IoT and AI technologies has further transformed control panel functionality, enabling real-time data analytics and predictive maintenance. This evolution has not only enhanced operational efficiency but also opened new avenues for international B2B buyers to leverage advanced technologies in their operations. Understanding this historical context is essential for buyers looking to make informed decisions in a rapidly changing marketplace.
Frequently Asked Questions (FAQs) for B2B Buyers of Control Panel Manufacturers
-
How do I select the right control panel manufacturer for my needs?
Choosing the right control panel manufacturer requires a clear understanding of your project specifications, including industry standards and regulatory requirements. Start by evaluating manufacturers based on their experience in your sector, customer reviews, and certifications. It’s also beneficial to request samples or case studies that demonstrate their expertise in similar projects. Furthermore, consider their capacity for customization, as well as their ability to meet your timelines and budget constraints. -
What are the key factors to consider when customizing a control panel?
When customizing a control panel, consider the specific functionalities you need, such as control types, input/output requirements, and safety features. Additionally, assess the environmental conditions where the panel will be installed, as this will influence material choices and design. Communication with the manufacturer is essential to ensure they understand your requirements and can deliver a product that meets both technical specifications and regulatory compliance. -
What is the typical minimum order quantity (MOQ) for control panels?
Minimum order quantities (MOQs) for control panels can vary significantly by manufacturer and the complexity of the design. Generally, MOQs may range from a few units for standard designs to larger quantities for customized solutions. It is advisable to discuss your specific needs with potential suppliers to determine their MOQ and negotiate terms that suit your procurement strategy, particularly if you are looking to minimize inventory costs. -
What payment terms should I expect when purchasing from control panel manufacturers?
Payment terms can vary widely among control panel manufacturers. Common arrangements include a deposit upfront (typically 30-50%), with the balance due upon delivery or installation. Some suppliers may offer flexible payment options, including financing or installment plans. Always clarify payment terms in advance, and ensure they are documented in your purchase agreement to avoid any misunderstandings. -
How can I ensure quality assurance when sourcing control panels internationally?
To ensure quality assurance when sourcing control panels, select manufacturers with established quality management systems, such as ISO 9001 certification. Request documentation of quality control processes, including inspection reports and testing certifications. Additionally, consider third-party inspections or audits to verify compliance with international standards. Establishing a clear communication channel with the manufacturer can also facilitate timely updates on production quality. -
What are the logistics considerations for importing control panels from overseas?
When importing control panels, consider shipping methods, customs regulations, and potential tariffs that may apply. It’s crucial to work with suppliers who understand international logistics and can provide detailed shipping timelines. Ensure that all necessary documentation, such as invoices, packing lists, and certificates of origin, is prepared to facilitate smooth customs clearance. Collaborating with a freight forwarder can also help manage logistics efficiently. -
What are the common certifications I should look for in control panel manufacturers?
Look for manufacturers that hold relevant certifications such as UL, CE, or IECEx, depending on your industry and geographical location. These certifications indicate compliance with safety standards and regulations that are critical for electrical equipment. Additionally, inquire about any industry-specific certifications that may apply to your project, as these can impact the reliability and safety of the control panels. -
How do I handle after-sales support and service for control panels?
After-sales support is vital for the longevity of your control panels. Discuss warranty terms and the manufacturer’s commitment to technical support before purchasing. Ensure they offer maintenance services, troubleshooting assistance, and spare parts availability. Establishing a service agreement can also be beneficial, as it outlines the support you can expect, including response times and costs associated with repairs or replacements.
Important Disclaimer & Terms of Use
⚠️ Important Disclaimer
The information provided in this guide, including content regarding manufacturers, technical specifications, and market analysis, is for informational and educational purposes only. It does not constitute professional procurement advice, financial advice, or legal advice.
While we have made every effort to ensure the accuracy and timeliness of the information, we are not responsible for any errors, omissions, or outdated information. Market conditions, company details, and technical standards are subject to change.
B2B buyers must conduct their own independent and thorough due diligence before making any purchasing decisions. This includes contacting suppliers directly, verifying certifications, requesting samples, and seeking professional consultation. The risk of relying on any information in this guide is borne solely by the reader.
Strategic Sourcing Conclusion and Outlook for Control Panel Manufacturers
In today’s dynamic marketplace, strategic sourcing remains a cornerstone for international B2B buyers in the control panel manufacturing sector. By leveraging comprehensive supplier evaluations, understanding local market nuances, and aligning with manufacturers that adhere to global design standards, businesses can significantly enhance their operational efficiency and product reliability. Buyers from Africa, South America, the Middle East, and Europe must prioritize partnerships that offer not only competitive pricing but also robust technical support and innovative solutions tailored to specific industry needs.
How Can B2B Buyers Future-Proof Their Sourcing Strategies?
As the industry evolves, embracing technological advancements such as IoT integration and automation in control panels will be vital. Buyers should actively seek suppliers who are committed to ongoing innovation and sustainability, ensuring that their operations remain competitive and compliant with emerging regulations. The future of control panel manufacturing is bright, with potential for growth across emerging markets.
What Steps Should International Buyers Take Next?
Engaging in proactive supplier relationship management and continuous market analysis will empower buyers to make informed decisions. This approach will not only optimize sourcing strategies but also foster resilience against market fluctuations. As you navigate this landscape, consider taking immediate steps to assess your current sourcing partnerships and explore new opportunities that align with your strategic goals. The right sourcing decisions today will set the foundation for success tomorrow.