Discover Cost-Effective Hand Sanitizer Custom Solutions (2025)
Introduction: Navigating the Global Market for hand sanitizer custom
In the wake of heightened global health awareness, sourcing hand sanitizer custom solutions has become a pivotal challenge for international B2B buyers. As businesses strive to ensure safety and hygiene, understanding the diverse types and applications of hand sanitizers is essential. This guide serves as a comprehensive resource, exploring various formulations, packaging options, and potential suppliers that cater specifically to markets in Africa, South America, the Middle East, and Europe, including nations such as Indonesia and the UAE.
Navigating this landscape requires a deep dive into the intricacies of supplier vetting, cost considerations, and regulatory compliance, as these factors are crucial for making informed purchasing decisions. Buyers will benefit from insights into the latest industry trends, effective sourcing strategies, and quality assurance processes that guarantee the efficacy and safety of hand sanitizer products.
By leveraging the knowledge contained within this guide, B2B buyers can confidently approach their sourcing endeavors. This resource not only demystifies the complexities of the global hand sanitizer market but also empowers businesses to forge strategic partnerships with trusted suppliers. Ultimately, the goal is to equip you with the necessary tools to navigate the evolving landscape of hand sanitizer procurement, ensuring your organization remains compliant and competitive in an increasingly health-conscious world.
Understanding hand sanitizer custom Types and Variations
Type Name | Key Distinguishing Features | Primary B2B Applications | Brief Pros & Cons for Buyers |
---|---|---|---|
Alcohol-Based Sanitizer | Contains 60-95% alcohol; effective against most pathogens | Healthcare, Hospitality, Retail | Pros: High efficacy; quick drying. Cons: Can be drying to skin; flammable. |
Gel Sanitizer | Thick, gel-like consistency; often contains moisturizers | Corporate Offices, Schools, Events | Pros: Convenient; less spillage. Cons: Can feel sticky; may require more product. |
Foam Sanitizer | Light, airy foam; often contains skin conditioners | Travel, Public Transport, Restaurants | Pros: Easy to apply; less waste. Cons: May require more time to dry; not as widely accepted. |
Spray Sanitizer | Liquid form that disperses as a fine mist | Manufacturing, Warehousing, Outdoor Events | Pros: Covers large areas quickly; versatile. Cons: Can be less effective if not applied correctly; potential for overuse. |
Natural/Organic Sanitizer | Made with natural ingredients; often alcohol-free | Eco-conscious businesses, Spas, Gyms | Pros: Gentle on skin; eco-friendly. Cons: May be less effective against some pathogens; higher cost. |
What Are the Key Characteristics of Alcohol-Based Sanitizers?
Alcohol-based sanitizers typically contain between 60% to 95% alcohol, making them highly effective at killing germs and viruses. They evaporate quickly, providing a fast-acting solution for hand hygiene. B2B buyers in sectors such as healthcare and hospitality prioritize these sanitizers due to their proven efficacy against a wide range of pathogens. However, it’s crucial to consider that frequent use can lead to skin irritation, and the product is flammable, necessitating proper storage and handling.
How Do Gel Sanitizers Differ in Use and Effectiveness?
Gel sanitizers are characterized by their thick, viscous consistency, which often includes moisturizers to counteract drying effects. They are ideal for environments like corporate offices and schools, where ease of use is paramount. Buyers should consider that while gel sanitizers minimize spillage and are convenient, they can leave a sticky residue and may require a larger quantity for effective use compared to other types.
What Benefits Do Foam Sanitizers Offer for B2B Applications?
Foam sanitizers provide a light, airy application that is easy to dispense and use. They are particularly well-suited for travel-related businesses and public transport systems where quick hand hygiene is essential. The foam formulation reduces waste and allows for a more controlled application. However, B2B buyers should note that foam sanitizers may take longer to dry and might not be as widely accepted in every industry.
In What Scenarios Are Spray Sanitizers Most Effective?
Spray sanitizers are versatile and can cover large areas quickly, making them suitable for manufacturing and warehousing environments. Their liquid form allows for easy application to surfaces, which is beneficial in high-traffic areas. However, buyers should be aware that improper application can lead to reduced effectiveness, and overuse may lead to waste. Ensuring proper training on usage is vital for maximizing their benefits.
Why Choose Natural or Organic Sanitizers for Your Business?
Natural or organic sanitizers are formulated with eco-friendly ingredients, making them a preferred choice for businesses that prioritize sustainability, such as spas and gyms. These products are typically gentler on the skin and appeal to eco-conscious consumers. However, buyers should carefully consider their effectiveness against certain pathogens, as they may not be as potent as traditional alcohol-based options, and they often come at a higher price point.
Related Video: Hand Sanitizer Labels Template | Custom Party Favors| Canva TemplateTutorial|DIY Labels
Key Industrial Applications of hand sanitizer custom
Industry/Sector | Specific Application of Hand Sanitizer Custom | Value/Benefit for the Business | Key Sourcing Considerations for this Application |
---|---|---|---|
Healthcare | Patient Care Facilities | Enhances hygiene standards and reduces infection rates | Compliance with health regulations; bulk purchasing options |
Food and Beverage | Food Processing Plants | Maintains food safety and hygiene protocols | FDA compliance; formulation effectiveness against pathogens |
Hospitality | Hotels and Restaurants | Ensures customer safety and satisfaction | Custom branding options; eco-friendly formulations |
Education | Schools and Universities | Protects students and staff from illnesses | Child-safe ingredients; large volume supply capabilities |
Retail | Supermarkets and Stores | Provides a safe shopping experience for customers | Custom packaging solutions; rapid replenishment options |
How is Hand Sanitizer Custom Used in Healthcare Settings?
In healthcare facilities, custom hand sanitizers are critical for maintaining hygiene among staff and patients. They help significantly reduce the risk of hospital-acquired infections, a major concern in patient care. Buyers in this sector should prioritize products that comply with local health regulations and have proven efficacy against a wide range of pathogens. Additionally, bulk purchasing options can help meet the high demand in hospitals and clinics, especially during outbreaks.
What Role Does Hand Sanitizer Custom Play in Food and Beverage Industries?
In food processing plants, custom hand sanitizers are essential for adhering to strict hygiene protocols. They help prevent cross-contamination and ensure that food products are safe for consumption. Buyers need to consider FDA compliance and the effectiveness of the sanitizer against common foodborne pathogens. The formulation should be suitable for frequent use without causing skin irritation, given the high volume of handwashing in these environments.
How Does Hand Sanitizer Custom Enhance Hospitality Experiences?
In the hospitality sector, hotels and restaurants utilize custom hand sanitizers to promote a safe and welcoming environment for guests. These sanitizers can be branded to align with the establishment’s image, enhancing customer confidence in hygiene practices. Buyers should look for eco-friendly formulations that reflect sustainability values, as well as options for easy dispensing in high-traffic areas. This approach not only protects guests but also boosts the establishment’s reputation.
Why is Hand Sanitizer Custom Important in Educational Institutions?
Schools and universities deploy custom hand sanitizers to protect students and staff from infectious diseases. These products are particularly vital during flu seasons and outbreaks, ensuring a healthier learning environment. Buyers in the education sector should focus on child-safe ingredients and effective formulations that meet the needs of diverse age groups. Additionally, suppliers should be capable of delivering large volumes to accommodate the entire institution.
How Can Retailers Benefit from Custom Hand Sanitizer Solutions?
Retailers, including supermarkets and stores, use custom hand sanitizers to enhance the shopping experience and ensure customer safety. Providing accessible sanitizing stations encourages consumers to maintain hygiene while shopping, which can lead to increased customer loyalty. Buyers should consider custom packaging solutions that are visually appealing and promote the brand. Rapid replenishment options are also crucial to keep up with demand, especially during peak shopping seasons.
Related Video: Alcohol-based surgical hand disinfection | AMBOSS tutorial
3 Common User Pain Points for ‘hand sanitizer custom’ & Their Solutions
Scenario 1: Difficulty in Ensuring Product Quality and Compliance
The Problem: International B2B buyers often struggle with sourcing hand sanitizers that meet local and international regulatory standards. This challenge can be particularly acute in regions like Africa and the Middle East, where regulations may differ significantly from those in Europe or South America. Buyers may receive products that do not comply with necessary safety standards, leading to potential legal liabilities and health risks for consumers.
The Solution: To ensure compliance and quality, buyers should establish a rigorous vetting process for suppliers. This includes requesting certifications such as ISO, FDA, or EU compliance documents that validate the product’s quality and safety. Additionally, buyers should conduct audits or request third-party testing results to confirm the efficacy of the hand sanitizers. Engaging with manufacturers who specialize in custom formulations can also help tailor products that meet specific regional regulations. Consider setting up a trial order to evaluate the product before committing to larger purchases.
Scenario 2: Inconsistent Supply Chains and Delivery Issues
The Problem: B2B buyers often encounter disruptions in their supply chains, which can result in delayed shipments of hand sanitizers. This problem is exacerbated by global events such as pandemics or regional conflicts, which can hinder transportation and logistics. Such inconsistencies can lead to stock shortages, affecting the buyer’s ability to meet customer demands and maintain business operations.
The Solution: To combat supply chain issues, buyers should diversify their supplier base and consider local manufacturers who can provide hand sanitizers. Establishing relationships with multiple suppliers can create a buffer against disruptions, ensuring that if one supplier faces challenges, alternatives are readily available. Additionally, implementing a just-in-time inventory system can help manage stock levels more effectively, minimizing the risk of overstocking or shortages. Regular communication with suppliers about their production capacity and logistics capabilities can also aid in forecasting potential delays.
Scenario 3: Lack of Customization Options for Branding
The Problem: Many B2B buyers seek to personalize hand sanitizer products to align with their brand identity. However, they often find that suppliers offer limited customization options, which can hinder their marketing efforts. This lack of flexibility can make it difficult for businesses to differentiate themselves in a competitive market, especially in regions where brand loyalty is critical.
The Solution: Buyers should actively seek out suppliers who specialize in customizable hand sanitizers. This includes options for varying scents, packaging designs, and even formulation types (e.g., alcohol-based vs. non-alcohol-based). When discussing potential partnerships, buyers should clearly communicate their branding needs and inquire about the supplier’s capabilities in customization. Utilizing suppliers who offer small batch production runs can also facilitate more tailored solutions without requiring large minimum order quantities. Additionally, consider collaborating with suppliers who have experience in your specific industry to create hand sanitizers that resonate with your target audience while reinforcing your brand’s identity.
Strategic Material Selection Guide for hand sanitizer custom
When selecting materials for custom hand sanitizers, international B2B buyers must consider various factors that influence product performance, regulatory compliance, and market preferences. Here, we analyze four common materials used in hand sanitizer formulations, focusing on their properties, advantages, disadvantages, and specific considerations for buyers from Africa, South America, the Middle East, and Europe.
What Are the Key Properties of Ethanol in Hand Sanitizers?
Ethanol is one of the most widely used active ingredients in hand sanitizers due to its effectiveness against a broad spectrum of pathogens.
- Key Properties: Ethanol has a high evaporation rate, which allows for quick drying on the skin. It is effective at concentrations of 60-95% and has excellent biocidal activity.
- Pros & Cons: Ethanol is relatively inexpensive and readily available, making it a cost-effective choice for manufacturers. However, it can be drying to the skin and may cause irritation with prolonged use, which can affect user acceptance.
- Impact on Application: Ethanol is compatible with various skin types but may not be suitable for sensitive skin without additional moisturizing agents.
- Considerations for Buyers: Compliance with standards such as ASTM E2315 for antimicrobial effectiveness is crucial. Buyers in regions like the UAE and Europe should also consider regulations regarding flammable materials.
How Does Isopropyl Alcohol Compare as a Material for Hand Sanitizers?
Isopropyl Alcohol (IPA) is another popular choice for hand sanitizers, particularly in formulations where a slower evaporation rate is desired.
- Key Properties: IPA is effective at 60-90% concentrations and has a lower evaporation rate compared to ethanol, providing longer contact time with pathogens.
- Pros & Cons: IPA is less irritating to the skin than ethanol, making it suitable for sensitive skin formulations. However, it is generally more expensive than ethanol and may not be as effective against certain viruses.
- Impact on Application: Its slower evaporation allows for better efficacy but may leave a residue that some users find unpleasant.
- Considerations for Buyers: Buyers must ensure compliance with local regulations, particularly in regions like South America, where specific formulations may be preferred.
What Role Does Glycerin Play in Hand Sanitizer Formulations?
Glycerin is often included in hand sanitizer formulations as a humectant to counteract the drying effects of alcohol.
- Key Properties: Glycerin is a viscous liquid that retains moisture, enhancing the skin feel of the product.
- Pros & Cons: It improves user experience by preventing skin dryness but can increase the viscosity of the product, complicating manufacturing processes.
- Impact on Application: Glycerin can enhance the moisturizing properties of hand sanitizers, making them more appealing to consumers.
- Considerations for Buyers: Buyers should look for glycerin that meets quality standards such as USP or EP, particularly in European markets where ingredient quality is heavily regulated.
Why Is Aloe Vera a Popular Ingredient in Hand Sanitizers?
Aloe Vera is often added to hand sanitizers for its soothing properties and skin benefits.
- Key Properties: Aloe Vera contains vitamins, minerals, and amino acids that promote skin health.
- Pros & Cons: It enhances the moisturizing effect of hand sanitizers, making them more suitable for frequent use. However, the cost of sourcing high-quality Aloe Vera can be a limitation.
- Impact on Application: Aloe Vera can improve the overall user experience, making the product more desirable in markets where consumer preference leans towards natural ingredients.
- Considerations for Buyers: Buyers should verify the source and quality of Aloe Vera to ensure compliance with organic and natural product standards, which are increasingly important in European and Middle Eastern markets.
Summary Table of Material Selection for Hand Sanitizers
Material | Typical Use Case for hand sanitizer custom | Key Advantage | Key Disadvantage/Limitation | Relative Cost (Low/Med/High) |
---|---|---|---|---|
Ethanol | General-purpose hand sanitizers | Fast-acting and effective | Can be drying to the skin | Low |
Isopropyl Alcohol | Sensitive skin formulations | Less irritating | More expensive than ethanol | Medium |
Glycerin | Moisturizing hand sanitizers | Improves skin feel | Increases viscosity | Medium |
Aloe Vera | Natural ingredient formulations | Enhances moisturizing properties | Higher sourcing costs | High |
By understanding the properties, advantages, and limitations of these materials, international B2B buyers can make informed decisions that align with regulatory requirements and market preferences.
In-depth Look: Manufacturing Processes and Quality Assurance for hand sanitizer custom
What Are the Main Stages in the Manufacturing Process of Custom Hand Sanitizers?
The manufacturing process of custom hand sanitizers involves several critical stages that ensure product quality and compliance with international standards. Understanding these stages helps B2B buyers evaluate potential suppliers effectively.
1. Material Preparation
The first step in manufacturing hand sanitizers is material preparation. This involves sourcing high-quality raw materials such as alcohol (ethanol or isopropyl), glycerin, hydrogen peroxide, and essential oils for fragrance. Suppliers should prioritize materials that comply with relevant regulatory requirements, such as the World Health Organization (WHO) guidelines.
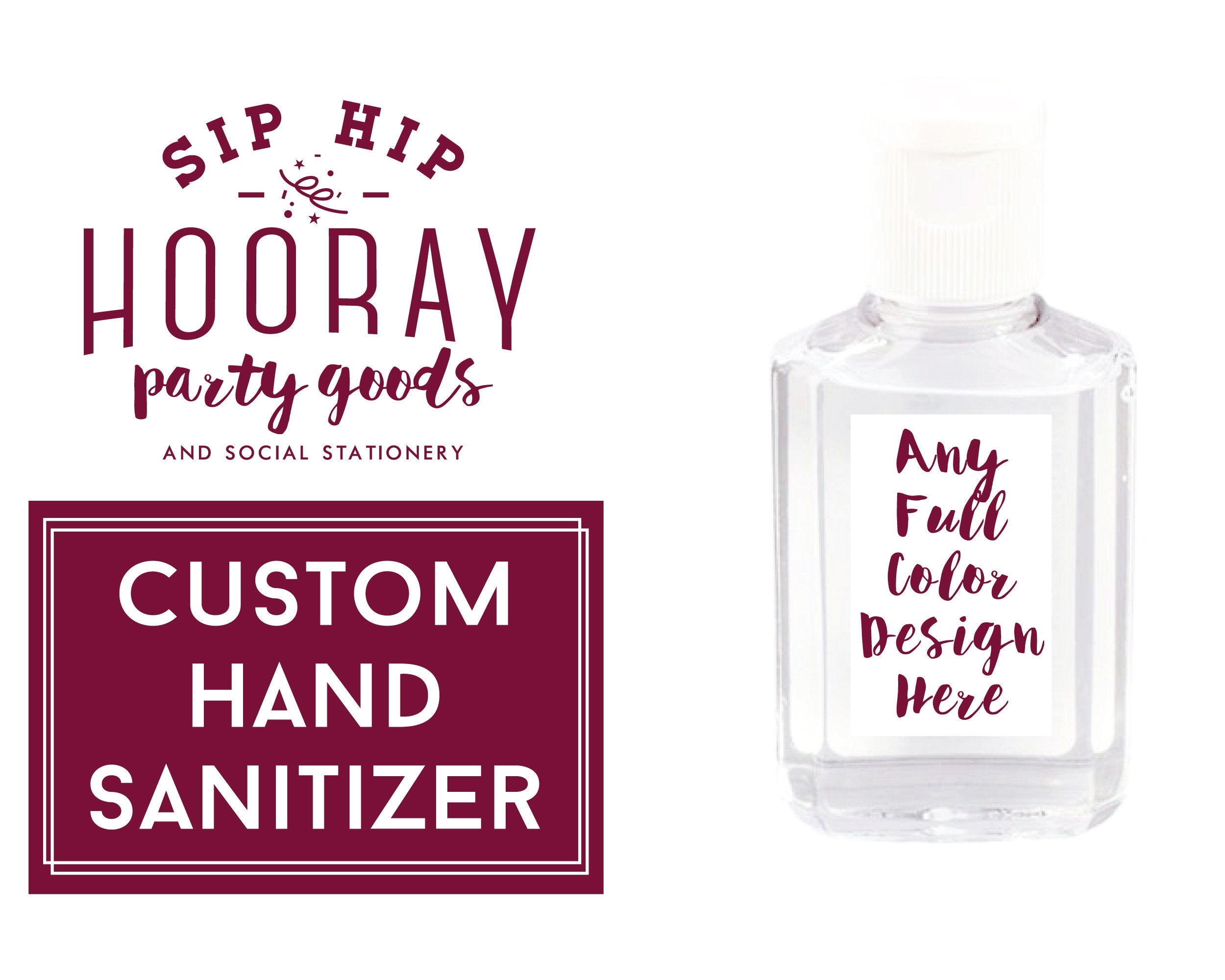
A stock image related to hand sanitizer custom.
Key Techniques:
– Sourcing: Ensure that suppliers have reliable sources for raw materials, preferably from certified vendors.
– Testing: Conduct quality checks on incoming materials to verify their purity and efficacy. This often includes checking for contaminants and ensuring that the ingredients meet specified standards.
2. Forming
In this stage, the prepared raw materials are combined to create the hand sanitizer formulation. The formulation typically follows a specific recipe that balances the active ingredients to achieve the desired alcohol concentration (at least 60% for effectiveness).
Key Techniques:
– Mixing: Automated mixing systems are commonly used to ensure uniformity in the product. Manual mixing may also be employed, especially for small batches or custom formulations.
– Temperature Control: Maintaining the appropriate temperature during mixing is crucial for the stability and efficacy of the product.
3. Assembly
After forming the hand sanitizer, the next step is assembly, which involves packaging the product into containers. The choice of packaging is vital for maintaining product integrity and ensuring ease of use.
Key Techniques:
– Filling: Use automated filling machines to ensure accuracy and minimize contamination risks.
– Sealing: Proper sealing techniques are essential to prevent leakage and contamination during shipping and storage.
4. Finishing
The finishing stage encompasses labeling, quality checks, and preparing the product for shipment. Labels should include important information such as ingredients, usage instructions, and compliance certifications.
Key Techniques:
– Labeling: Ensure that labels are printed clearly and comply with local regulations regarding product information.
– Final Inspection: Conduct a final inspection of the product for defects in packaging or labeling. This step often involves visual checks and sampling.
How Is Quality Assurance Managed in Hand Sanitizer Manufacturing?
Quality assurance (QA) is a critical component in the manufacturing of hand sanitizers, ensuring that products meet safety and efficacy standards. B2B buyers should be aware of the various QA practices and standards relevant to their purchases.
Relevant International Standards for Hand Sanitizers
B2B buyers should verify that their suppliers adhere to recognized international standards, such as:
- ISO 9001: A standard that outlines the requirements for a quality management system, ensuring consistent quality in products and services.
- CE Marking: Indicates that products comply with EU safety, health, and environmental protection standards.
- API Standards: Relevant for suppliers that produce hand sanitizers with active pharmaceutical ingredients.
What Are the Key Quality Control Checkpoints?
Effective quality control (QC) checkpoints are essential throughout the manufacturing process to ensure that the final product meets all specifications. Key checkpoints include:
- Incoming Quality Control (IQC): Inspection of raw materials upon arrival to ensure they meet predefined quality standards.
- In-Process Quality Control (IPQC): Ongoing checks during the manufacturing process, including monitoring critical parameters like temperature and mixing time.
- Final Quality Control (FQC): Comprehensive testing of the finished product, including stability testing, microbial testing, and efficacy assessments.
What Common Testing Methods Are Used for Hand Sanitizers?
Testing is a crucial part of quality assurance in hand sanitizer production. B2B buyers should be familiar with common testing methods to evaluate supplier capabilities.
- Microbial Testing: Ensures that the product is free from harmful microorganisms. This is particularly important for products that are intended for skin application.
- Efficacy Testing: Conducted to verify that the hand sanitizer effectively reduces or eliminates pathogens. This often involves using standardized test methods such as the EN 1500 test.
- Stability Testing: Assesses how the product performs over time under various conditions, ensuring that it retains its efficacy and safety throughout its shelf life.
How Can B2B Buyers Verify Supplier Quality Control?
B2B buyers must take proactive steps to verify that suppliers adhere to stringent quality control practices. Here are some actionable strategies:
Conduct Supplier Audits
Regular audits of potential suppliers can provide insights into their manufacturing processes, quality management systems, and adherence to safety standards. Audits can be conducted by the buyer’s quality assurance team or third-party inspectors.
Request Quality Assurance Documentation
Suppliers should be willing to provide documentation related to their quality assurance processes, including:
- Quality management system certifications (e.g., ISO 9001)
- Results of recent quality control tests
- Records of compliance with industry standards (e.g., CE marking)
Engage Third-Party Inspection Services
Using third-party inspection services can add an extra layer of assurance. These services can conduct independent checks on the manufacturing process, raw materials, and finished products to verify compliance with agreed-upon standards.
What Are the Quality Control and Certification Nuances for International B2B Buyers?
For international B2B buyers, understanding the nuances of quality control and certification is crucial. Different regions may have specific regulations and standards that affect the import and sale of hand sanitizers.
Regional Compliance Requirements
- Africa: Buyers should be aware of local regulations, which may vary by country. Some countries require registration with local health authorities before products can be sold.
- South America: Regulatory frameworks can differ significantly; thus, understanding local compliance requirements is essential for successful market entry.
- Middle East: Buyers should ensure that products meet the Gulf Cooperation Council (GCC) standards, which may require additional certifications.
- Europe: Compliance with EU regulations, including REACH (Registration, Evaluation, Authorisation and Restriction of Chemicals), is mandatory for importing hand sanitizers.
Conclusion
Understanding the manufacturing processes and quality assurance practices for custom hand sanitizers is essential for international B2B buyers. By focusing on material preparation, forming, assembly, and finishing, along with stringent quality control measures, buyers can make informed decisions when selecting suppliers. Familiarity with international standards and testing methods further enables buyers to ensure that they are sourcing high-quality products that meet their specific needs.
Practical Sourcing Guide: A Step-by-Step Checklist for ‘hand sanitizer custom’
To successfully procure custom hand sanitizer for your business, it is essential to follow a systematic approach that ensures quality, compliance, and value. This guide provides a step-by-step checklist tailored for international B2B buyers, particularly those from Africa, South America, the Middle East, and Europe.
Step 1: Define Your Technical Specifications
Understanding your specific needs is crucial. Define the formulation (e.g., alcohol concentration, scent, and additives) and packaging requirements (size, type of dispenser). This clarity helps in communicating effectively with suppliers and ensures that the product meets your standards and regulations.
Step 2: Research Regulatory Compliance Requirements
Different regions have varying regulations concerning hand sanitizer. Ensure that you are aware of the local regulations in your target market, such as the FDA guidelines in the U.S. or the EU Cosmetic Regulation. Compliance with these standards not only protects your business but also builds trust with your customers.
Step 3: Evaluate Potential Suppliers
Before committing, thoroughly vet potential suppliers. Look for their company profiles, production capabilities, and certifications like ISO or GMP. Request references from other businesses in your industry to gauge their reliability and quality standards. This step mitigates risks associated with supplier reliability.
Step 4: Request Samples for Quality Assurance
Always request samples to evaluate product quality firsthand. Assess the consistency, scent, texture, and overall efficacy of the sanitizer. This step is critical in ensuring that the product aligns with your specifications and customer expectations.
Step 5: Verify Supplier Certifications
Ensure that your supplier holds relevant certifications, such as Good Manufacturing Practices (GMP) and safety data sheets (SDS). This validation indicates that the supplier adheres to industry standards and regulations, which is essential for maintaining product quality and safety.
Step 6: Discuss Pricing and Payment Terms
Engage in detailed discussions regarding pricing, minimum order quantities, and payment terms. Ensure that the pricing reflects the quality of the product and aligns with your budget. Transparent payment terms can help avoid misunderstandings later in the procurement process.
Step 7: Establish Clear Communication Channels
Establishing clear communication channels with your supplier is vital for ongoing collaboration. Confirm who your point of contact will be and ensure that both parties understand expectations regarding timelines, updates, and any potential issues. Effective communication can lead to smoother transactions and a more reliable supply chain.
By following this checklist, B2B buyers can streamline their sourcing process for custom hand sanitizer, ensuring they make informed decisions that align with their business needs and regulatory requirements.
Comprehensive Cost and Pricing Analysis for hand sanitizer custom Sourcing
When sourcing custom hand sanitizer, understanding the comprehensive cost structure and pricing elements is crucial for international B2B buyers. This analysis breaks down the various cost components and pricing influencers that can affect procurement decisions.
What Are the Key Cost Components in Custom Hand Sanitizer Sourcing?
-
Materials: The primary ingredient in hand sanitizers is ethanol or isopropyl alcohol, which can vary in price based on purity and source. Additional components such as moisturizers, fragrances, and colorants can also contribute to costs. Buyers should consider sourcing materials from reputable suppliers to ensure quality and compliance with international regulations.
-
Labor: Labor costs include wages for production staff, quality control personnel, and administrative support. In regions like Africa or South America, labor costs may be lower, but factors such as worker skill level and local labor laws can influence overall expenses.
-
Manufacturing Overhead: This encompasses indirect costs associated with production, such as utilities, equipment maintenance, and facility rent. Efficient production processes can help minimize these overheads, potentially leading to lower prices for buyers.
-
Tooling: If custom packaging or specific production techniques are required, tooling costs can add significantly to the initial investment. It’s essential to evaluate whether the tooling costs will be justified by the expected volume of sales.
-
Quality Control (QC): Implementing robust QC measures ensures the product meets safety and efficacy standards. Costs associated with laboratory testing, certifications (e.g., WHO, FDA), and compliance checks should be factored into the budget.
-
Logistics: Shipping costs vary based on distance, mode of transport, and the volume of goods. International buyers should consider Incoterms that define responsibilities for shipping and customs clearance, which can significantly impact total costs.
-
Margin: Suppliers typically include a profit margin in their pricing. Understanding market dynamics and competitor pricing can provide leverage during negotiations.
How Do Price Influencers Affect Custom Hand Sanitizer Costs?
-
Volume/MOQ (Minimum Order Quantity): Larger orders often result in lower per-unit prices due to economies of scale. Buyers should assess their demand to negotiate favorable terms.
-
Specifications and Customization: Unique formulations or packaging options can increase costs. Buyers must balance the need for customization with budget constraints.
-
Material Quality and Certifications: Higher-quality materials and certifications can drive up costs but may be necessary for market acceptance, especially in stringent markets like Europe.
-
Supplier Factors: The reliability, reputation, and location of the supplier can influence pricing. Suppliers with established track records may charge premium prices for their assurance of quality and timely delivery.
What Negotiation Tips Can Help Ensure Cost Efficiency for Buyers?
-
Understand Total Cost of Ownership (TCO): Beyond initial purchase prices, consider long-term costs associated with quality, compliance, and logistics. This holistic view can reveal hidden costs that impact profitability.
-
Leverage Relationships: Building strong relationships with suppliers can provide access to better pricing and terms. Regular communication and feedback can foster collaboration and trust.
-
Be Informed About Market Trends: Keeping up-to-date with global supply chain dynamics and raw material prices can empower buyers during negotiations, enabling them to make informed decisions.
-
Consider Alternative Suppliers: Exploring suppliers from different regions (like Southeast Asia or Eastern Europe) can yield competitive pricing options. However, ensure that they meet quality and regulatory standards.
-
Negotiate Incoterms: Clarifying shipping responsibilities can lead to cost savings. Incoterms such as FOB (Free on Board) or CIF (Cost, Insurance, and Freight) can change the cost structure significantly.
Final Thoughts
While prices for custom hand sanitizer can fluctuate based on multiple factors, international B2B buyers must conduct thorough due diligence. Always request indicative pricing from multiple suppliers and ensure all costs are clearly outlined to avoid surprises. By understanding the cost components and leveraging negotiation tactics, buyers can secure the best value for their investments.
Alternatives Analysis: Comparing hand sanitizer custom With Other Solutions
Understanding the Importance of Evaluating Alternatives
In the realm of hygiene and sanitation, especially in the context of B2B operations, the choice of disinfection solutions can significantly impact health and safety protocols. While custom hand sanitizers offer tailored benefits, it is crucial for international buyers to evaluate alternative solutions that may meet their specific needs more effectively. This analysis will compare custom hand sanitizers with two viable alternatives: antimicrobial surface wipes and UV-C disinfection technology.
Comparison Table of Hand Sanitizer Custom with Alternative Solutions
Comparison Aspect | Hand Sanitizer Custom | Antimicrobial Surface Wipes | UV-C Disinfection Technology |
---|---|---|---|
Performance | High efficacy against bacteria and viruses; tailored formulations possible | Effective against a wide range of pathogens; surface application | Kills up to 99.9% of germs; effective on all surfaces |
Cost | Moderate; varies based on formulation and quantity | Low to moderate; cost-effective for bulk purchases | High initial investment; ongoing maintenance costs |
Ease of Implementation | Requires proper dispensing systems; easy to apply | Simple to use; portable and convenient | Requires trained personnel for setup; must ensure safety precautions |
Maintenance | Low; periodic replenishment required | Low; must ensure stock levels | Moderate; needs regular maintenance and safety checks |
Best Use Case | Personal use in offices, events, and healthcare settings | High-traffic areas needing quick sanitization | Large facilities, such as hospitals and warehouses, for thorough disinfection |
What are the Pros and Cons of Antimicrobial Surface Wipes?
Antimicrobial surface wipes are a popular alternative to custom hand sanitizers, especially in environments that require quick cleaning of surfaces. One of the main advantages is their portability and ease of use; they can be deployed quickly across various surfaces in high-traffic areas, such as offices and public spaces. However, they may not be as effective for personal hand hygiene compared to custom hand sanitizers. Additionally, while wipes can provide a surface-level clean, they may not penetrate or eliminate all pathogens effectively as hand sanitizers do on skin.
How Does UV-C Disinfection Technology Compare?
UV-C disinfection technology represents a more advanced method of sanitization, utilizing ultraviolet light to kill germs on surfaces. This technology is particularly effective in environments such as hospitals, where thorough disinfection is critical. The primary benefit is its high efficacy rate—capable of eliminating up to 99.9% of pathogens. However, the initial investment can be significant, and the technology requires trained personnel to operate safely. Regular maintenance is also necessary to ensure the equipment functions correctly, which could add to operational costs.
Making an Informed Decision: Which Solution is Right for Your Business?
When selecting a disinfection solution, B2B buyers should consider their specific operational needs and environment. Custom hand sanitizers provide flexibility and targeted efficacy for personal hygiene, making them ideal for settings where hand cleanliness is paramount. On the other hand, antimicrobial surface wipes offer convenience for rapid sanitation, while UV-C technology is best suited for comprehensive disinfection in larger facilities. Evaluating these alternatives based on performance, cost, ease of implementation, and maintenance can help buyers make informed decisions that align with their health and safety objectives. Ultimately, the right choice will depend on the unique requirements of each business and the environments they operate within.
Essential Technical Properties and Trade Terminology for hand sanitizer custom
Understanding the essential technical properties and trade terminology is crucial for international B2B buyers involved in the custom hand sanitizer market. Here’s a comprehensive breakdown of the key specifications and industry terms that will empower decision-making.
What Are the Key Technical Properties of Custom Hand Sanitizers?
1. Active Ingredient Concentration
The effectiveness of hand sanitizers primarily depends on the concentration of active ingredients like ethanol or isopropyl alcohol. The World Health Organization (WHO) recommends a minimum of 60% alcohol for effective microbial kill rates. For B2B buyers, ensuring compliance with local regulations regarding active ingredient concentrations is vital for market entry and consumer safety.
2. Viscosity
Viscosity determines how easily a hand sanitizer can be dispensed and applied. It affects user experience; a product that is too thick may not dispense properly, while one that is too thin might not adhere well to the skin. Understanding the required viscosity helps buyers select products that meet end-user expectations, enhancing customer satisfaction and brand loyalty.
3. pH Level
The pH level of hand sanitizers impacts skin compatibility. A pH that is too high or too low can lead to skin irritation. Ideally, hand sanitizers should have a pH level close to that of human skin (around 5.5). B2B buyers should verify pH levels to ensure product safety and minimize liability.
4. Fragrance and Additives
While the primary function of hand sanitizers is to kill germs, the inclusion of fragrances and skin-conditioning agents can enhance user experience. Buyers must balance consumer preferences for scents with potential allergens and regulatory restrictions on certain additives. Understanding these properties aids in developing products that appeal to target demographics.
5. Packaging Compatibility
The type of packaging used can affect the product’s shelf life and user convenience. Buyers should consider materials that are compatible with alcohol-based products, as some plastics may degrade over time. Proper packaging also influences transportation costs and environmental impact, which are important factors for sustainability-focused businesses.
What Are Common Trade Terms in the Hand Sanitizer Industry?
1. OEM (Original Equipment Manufacturer)
OEM refers to a company that produces products that are sold under another company’s brand. In the hand sanitizer industry, buyers often work with OEMs to create customized formulations or packaging. This allows businesses to leverage existing manufacturing capabilities while focusing on brand development.
2. MOQ (Minimum Order Quantity)
MOQ is the smallest quantity of a product that a supplier is willing to sell. Understanding the MOQ is critical for B2B buyers, as it affects inventory management and cash flow. Buyers must negotiate MOQs that align with their sales forecasts to optimize procurement strategies.
3. RFQ (Request for Quotation)
An RFQ is a document issued by buyers to suppliers requesting pricing and terms for specific quantities of goods or services. For hand sanitizer procurement, submitting an RFQ helps buyers compare offers and ensure they are receiving competitive pricing and favorable terms.
4. Incoterms (International Commercial Terms)
Incoterms define the responsibilities of buyers and sellers in international shipping. They outline who is responsible for costs, risks, and insurance during transport. Familiarity with Incoterms helps B2B buyers negotiate better shipping arrangements and manage logistics efficiently.
5. Certification Standards
Certifications such as ISO, FDA, or CE mark signify that products meet specific safety and quality standards. For hand sanitizers, compliance with these standards is essential to ensure market access and consumer trust. Buyers should prioritize suppliers who can demonstrate proper certifications.
By grasping these technical properties and trade terms, B2B buyers in Africa, South America, the Middle East, and Europe can make informed decisions that enhance their market position and operational efficiency.
Navigating Market Dynamics and Sourcing Trends in the hand sanitizer custom Sector
What Are the Current Market Dynamics and Key Trends in the Hand Sanitizer Custom Sector?
The global hand sanitizer market has experienced significant growth, driven by heightened hygiene awareness due to the COVID-19 pandemic. This surge in demand is expected to persist as consumers and businesses increasingly prioritize cleanliness. For international B2B buyers, particularly from Africa, South America, the Middle East, and Europe, understanding the current and emerging trends is crucial.
Emerging technologies such as artificial intelligence and blockchain are revolutionizing sourcing strategies. AI is being utilized for demand forecasting, enabling companies to optimize inventory levels and reduce waste. Blockchain technology enhances transparency in the supply chain, allowing buyers to track the origins of ingredients used in hand sanitizers, ensuring quality and compliance with safety standards.
Additionally, there is a growing emphasis on customization in product offerings. B2B buyers are increasingly seeking hand sanitizers tailored to specific market needs, including varying scent profiles, packaging sizes, and formulations that align with local regulations. This trend highlights the importance of collaborating with manufacturers who can provide flexible solutions.
How Is Sustainability Impacting the Hand Sanitizer Custom Sector?
Sustainability is becoming a pivotal factor in B2B purchasing decisions. Buyers are increasingly aware of the environmental impact of their sourcing choices and are looking for suppliers that prioritize eco-friendly practices. This includes the use of biodegradable packaging and formulations that minimize water usage and harmful chemicals.
Ethical sourcing is also gaining traction. Businesses are expected to ensure that their suppliers adhere to fair labor practices and contribute positively to their communities. Certifications such as EcoCert or USDA Organic can provide assurance to buyers that products meet specific environmental and ethical standards.
Incorporating sustainable practices not only addresses consumer demand but can also lead to cost savings in the long term. For instance, companies that invest in green certifications often experience enhanced brand loyalty and can tap into new market segments that prioritize sustainability.
What Is the Historical Context of the Hand Sanitizer Custom Sector?
Historically, hand sanitizers were considered niche products, primarily used in healthcare settings. However, the onset of the COVID-19 pandemic in 2020 propelled hand sanitizers into the mainstream market. This rapid evolution was driven by urgent public health messaging and widespread availability of hand sanitizers in retail environments.
The shift in consumer behavior—from viewing hand sanitizers as an optional hygiene product to a daily essential—has transformed the landscape for B2B buyers. Companies are now exploring new opportunities in product innovation and market expansion, recognizing the sustained demand for customized hand sanitizers that cater to diverse consumer needs across global markets.
Conclusion
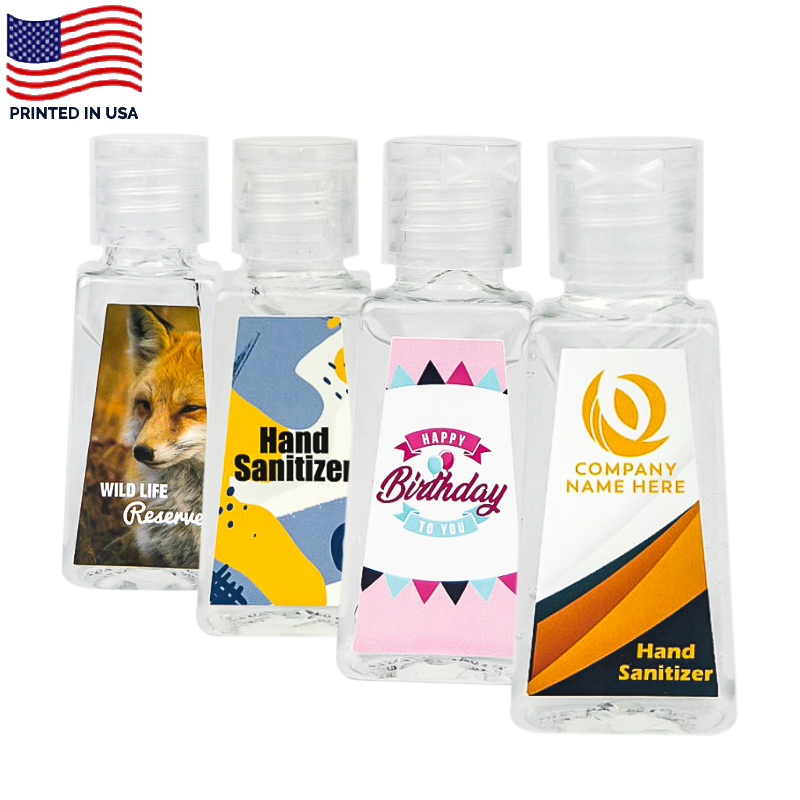
A stock image related to hand sanitizer custom.
For international B2B buyers, navigating the dynamic landscape of the hand sanitizer custom sector requires a keen understanding of market trends, sustainability considerations, and the historical evolution of the product. By staying informed and aligning sourcing strategies with these insights, businesses can effectively meet the demands of an increasingly conscientious market.
Frequently Asked Questions (FAQs) for B2B Buyers of hand sanitizer custom
-
How do I ensure the quality of custom hand sanitizer before purchasing?
To ensure the quality of custom hand sanitizer, request samples from potential suppliers. Verify that the product complies with international standards such as WHO guidelines and local regulations in your region. Additionally, inquire about the ingredients used and their efficacy against pathogens. It’s also beneficial to check supplier certifications and customer reviews to gauge their reliability. -
What is the best way to customize hand sanitizer for my brand?
The best way to customize hand sanitizer for your brand is to collaborate closely with your supplier. Discuss your requirements for scent, color, and packaging. Many suppliers offer private labeling services, allowing you to create a unique product that reflects your brand identity. Ensure that the customization does not compromise the sanitizer’s effectiveness. -
What are the minimum order quantities (MOQs) for custom hand sanitizer?
Minimum order quantities (MOQs) for custom hand sanitizer can vary significantly by supplier, typically ranging from 500 to 10,000 units. It’s essential to communicate your needs and budget to potential suppliers to negotiate suitable MOQs. Some manufacturers may offer flexibility, especially for first-time orders or long-term partnerships. -
How can I vet suppliers for custom hand sanitizer?
To vet suppliers for custom hand sanitizer, conduct thorough research. Check their business credentials, certifications, and compliance with safety standards. Request references and case studies from previous clients. Engaging in direct communication to assess their responsiveness and transparency is also crucial in evaluating their reliability. -
What payment terms should I consider when sourcing custom hand sanitizer?
When sourcing custom hand sanitizer, consider payment terms that protect your interests. Common practices include a deposit (usually 30-50%) upfront, with the balance due upon delivery. Discuss and agree on payment methods that suit both parties, such as letters of credit or escrow services, to mitigate risks in international transactions. -
What logistics considerations are important when importing hand sanitizer?
Logistics considerations for importing hand sanitizer include understanding shipping methods, customs regulations, and tariffs in your country. Work with suppliers who provide clear shipping timelines and trackable delivery options. Additionally, ensure that the packaging meets international shipping standards to avoid damages or delays during transit.
-
How do I handle regulatory compliance for custom hand sanitizer in my region?
Handling regulatory compliance for custom hand sanitizer involves researching the specific regulations in your region, such as ingredient restrictions and labeling requirements. Collaborate with your supplier to ensure that the product meets these standards. You may also need to obtain certifications or licenses before distribution, depending on local laws. -
What are the common challenges when sourcing custom hand sanitizer internationally?
Common challenges when sourcing custom hand sanitizer internationally include language barriers, differing regulations, and cultural differences that may affect business practices. Additionally, fluctuations in shipping costs and delays in customs clearance can impact delivery schedules. To mitigate these challenges, establish clear communication, and consider partnering with logistics experts familiar with international trade.
Important Disclaimer & Terms of Use
⚠️ Important Disclaimer
The information provided in this guide, including content regarding manufacturers, technical specifications, and market analysis, is for informational and educational purposes only. It does not constitute professional procurement advice, financial advice, or legal advice.
While we have made every effort to ensure the accuracy and timeliness of the information, we are not responsible for any errors, omissions, or outdated information. Market conditions, company details, and technical standards are subject to change.
B2B buyers must conduct their own independent and thorough due diligence before making any purchasing decisions. This includes contacting suppliers directly, verifying certifications, requesting samples, and seeking professional consultation. The risk of relying on any information in this guide is borne solely by the reader.
Strategic Sourcing Conclusion and Outlook for hand sanitizer custom
In conclusion, the strategic sourcing of custom hand sanitizers is critical for international B2B buyers looking to enhance their product offerings while meeting the growing demand for hygiene solutions. By leveraging strategic sourcing practices, businesses can optimize their supply chain, ensure compliance with local regulations, and foster sustainable partnerships with manufacturers.
What Are the Key Benefits of Strategic Sourcing for Hand Sanitizers?
Buyers should focus on establishing relationships with reputable suppliers, especially those that prioritize quality and transparency. This approach not only mitigates risks associated with product quality but also ensures that the hand sanitizers meet the specific needs of diverse markets across Africa, South America, the Middle East, and Europe.
How Can International Buyers Prepare for Future Trends in Hand Sanitizer Customization?
Looking ahead, the demand for customized hand sanitizers will continue to rise, driven by consumer preferences for personalization and unique branding opportunities. B2B buyers are encouraged to stay informed about market trends and innovations to remain competitive.
Engaging with suppliers who can adapt to changing market dynamics will be essential. Therefore, as you navigate your sourcing strategies, prioritize flexibility and responsiveness in your partnerships. By doing so, you will be well-positioned to capitalize on emerging opportunities in the hand sanitizer market.