Discover Cost-Effective Mini Lathe China Solutions (2025)
Introduction: Navigating the Global Market for mini lathe china
In the competitive landscape of manufacturing, sourcing a mini lathe from China can present unique challenges for international B2B buyers. As industries seek precision and efficiency, the ability to navigate the global market for mini lathes becomes essential. This guide serves as an essential resource for buyers from Africa, South America, the Middle East, and Europe, including countries like Egypt and Germany, who aim to make informed purchasing decisions.
We will explore various types of mini lathes, their applications across different industries, and the critical factors to consider when selecting a supplier. Understanding the nuances of supplier vetting, quality assurance, and pricing strategies will empower you to navigate the complexities of international procurement. Additionally, this guide will provide insights into the latest innovations in mini lathe technology, helping you stay ahead of the curve in a rapidly evolving market.
By delving into the intricacies of sourcing mini lathes from China, you will be equipped with the knowledge to enhance your operational efficiency and drive cost-effective solutions for your business. Whether you are looking to invest in robust machinery or seeking to optimize your supply chain, this comprehensive guide will be your roadmap to successful sourcing and procurement.
Understanding mini lathe china Types and Variations
Type Name | Key Distinguishing Features | Primary B2B Applications | Brief Pros & Cons for Buyers |
---|---|---|---|
Mini Bench Lathe | Compact design, variable speed control | Small workshops, prototyping | Pros: Space-efficient, versatile. Cons: Limited capacity for larger projects. |
CNC Mini Lathe | Computer Numerical Control for precision cutting | Manufacturing, custom machining | Pros: High precision, automated operation. Cons: Higher initial investment. |
Mini Metal Lathe | Designed for metalworking, robust construction | Metal fabrication, small parts production | Pros: Durable, suitable for metal. Cons: Heavier, requires more space. |
Mini Wood Lathe | Specifically for woodturning, lighter materials | Woodworking, crafts | Pros: Lightweight, easy to handle. Cons: Limited to wood materials. |
Mini Precision Lathe | High accuracy, fine-tuning capabilities | Aerospace, medical device manufacturing | Pros: Exceptional precision, suitable for intricate designs. Cons: More complex to operate. |
What Are the Characteristics of a Mini Bench Lathe?
Mini bench lathes are designed for small-scale operations, making them ideal for hobbyists and small workshops. They typically feature variable speed controls, allowing users to adjust the rotation speed for different materials and applications. This type of lathe is well-suited for prototyping and crafting small parts, making it a popular choice among B2B buyers in the crafting and DIY sectors. When considering a mini bench lathe, buyers should evaluate the machine’s power, stability, and ease of use, particularly if they need to train staff on its operation.
How Does a CNC Mini Lathe Enhance Manufacturing Efficiency?
CNC mini lathes incorporate advanced technology for automated and precise machining. These lathes are equipped with computer numerical control systems, enabling them to produce complex shapes and maintain high accuracy across multiple units. This makes them particularly valuable in manufacturing environments where consistency and precision are paramount. B2B buyers should consider the software compatibility and training requirements, as well as the initial investment costs, when integrating CNC mini lathes into their operations.
What Makes a Mini Metal Lathe Suitable for Industrial Applications?
Mini metal lathes are robust machines specifically designed for metalworking tasks. They provide the necessary durability and strength to handle various metals, making them suitable for small-scale metal fabrication and production of precise components. B2B buyers in industries such as automotive and aerospace will find these lathes essential for producing high-quality parts. When purchasing, considerations should include the lathe’s capacity, tooling options, and maintenance requirements to ensure longevity and efficiency.
Why Choose a Mini Wood Lathe for Crafting Projects?
Mini wood lathes are tailored for woodworking enthusiasts and professionals. Their lightweight and portable design makes them easy to maneuver, which is advantageous for crafting intricate wooden items. These lathes are perfect for small-scale production, such as turning bowls, spindles, and other decorative pieces. B2B buyers in the woodworking sector should assess the lathe’s motor power and features like variable speed control, which can enhance the quality of the finished products.
What Are the Advantages of a Mini Precision Lathe in Specialized Manufacturing?
Mini precision lathes are engineered for high-accuracy tasks, making them indispensable in specialized manufacturing sectors like aerospace and medical device production. These machines are capable of fine-tuning intricate designs with exceptional precision, catering to the stringent quality standards of these industries. Buyers should consider the machine’s specifications, including tolerance levels and operational complexity, as these factors can significantly impact production efficiency and product quality.
Related Video: 10 Years of Mini Lathe Ownership: Pros, Cons, Modifications and Improvements
Key Industrial Applications of mini lathe china
Industry/Sector | Specific Application of mini lathe china | Value/Benefit for the Business | Key Sourcing Considerations for this Application |
---|---|---|---|
Manufacturing | Precision component machining | High accuracy in producing intricate parts | Supplier certifications, machine specifications |
Automotive | Custom tooling and prototype development | Rapid prototyping reduces time to market | Material quality, lead times, and after-sales support |
Aerospace | Fabrication of lightweight components | Enhanced performance through weight reduction | Compliance with industry standards, precision tolerances |
Electronics | Creating housings and enclosures for devices | Cost-effective production of complex shapes | Customization options, tooling availability |
Jewelry | Crafting intricate designs and settings | Unique, high-quality pieces tailored to customer needs | Design capabilities, turnaround times |
How is Mini Lathe China Used in Manufacturing?
In the manufacturing sector, mini lathes from China are essential for precision component machining. These lathes allow businesses to create intricate parts with high accuracy, which is crucial for maintaining quality standards. International buyers, particularly from regions like Europe and South America, should consider the supplier’s certifications and the specific machine specifications to ensure they meet production needs effectively.
What Role Does Mini Lathe China Play in Automotive Applications?
In the automotive industry, mini lathes are frequently used for custom tooling and prototype development. They enable manufacturers to rapidly prototype components, significantly reducing time to market. For B2B buyers from Africa and the Middle East, it is vital to assess material quality and lead times, as well as after-sales support, to ensure that they can rely on their machinery for ongoing production needs.
How is Mini Lathe China Beneficial for Aerospace Fabrication?
The aerospace sector utilizes mini lathes for the fabrication of lightweight components, which is critical for enhancing performance and fuel efficiency in aircraft. These lathes allow for the precise machining of materials that meet strict aerospace standards. Buyers in this field must prioritize compliance with industry standards and precision tolerances when sourcing mini lathes to ensure safety and performance.
In What Ways Does Mini Lathe China Support Electronics Manufacturing?
In electronics, mini lathes are used to create housings and enclosures for various devices. Their ability to produce complex shapes at a cost-effective rate makes them invaluable in this fast-paced industry. Buyers should focus on customization options and tooling availability when sourcing mini lathes, especially in competitive markets in Europe and South America.
How is Mini Lathe China Used in Jewelry Crafting?
In the jewelry industry, mini lathes facilitate the crafting of intricate designs and settings, allowing jewelers to produce unique, high-quality pieces tailored to specific customer needs. For B2B buyers, it is essential to evaluate the design capabilities and turnaround times of suppliers to ensure they can meet market demands efficiently.
Related Video: The Best Milling Set-Up For The Chinese Mini Lathe
3 Common User Pain Points for ‘mini lathe china’ & Their Solutions
Scenario 1: Inconsistent Quality from Suppliers
The Problem:
B2B buyers often face the challenge of inconsistent quality when sourcing mini lathes from Chinese manufacturers. This inconsistency can stem from variations in production standards, materials used, or even the calibration of the machines. For buyers in Africa or South America, where quality assurance processes may not be as robust, receiving a mini lathe that does not meet specifications can lead to costly downtime and project delays. For example, a manufacturer in Egypt may receive a batch of lathes that have misaligned components, affecting their ability to produce precise parts.
The Solution:
To mitigate this risk, international buyers should prioritize sourcing from manufacturers with ISO certifications and a proven track record of quality control. Conducting factory visits, if possible, or utilizing third-party inspection services can ensure that the products meet the required specifications before shipping. Additionally, requesting detailed product samples and conducting rigorous testing on these samples can help buyers assess the quality of the mini lathes before committing to larger orders. Establishing a solid communication channel with the supplier can also facilitate adjustments and improvements based on buyer feedback.
Scenario 2: Language Barriers and Miscommunication
The Problem:
Language barriers can create significant challenges for B2B buyers when negotiating terms, understanding product specifications, and managing after-sales service. For instance, a European buyer may struggle to communicate their technical requirements or may misinterpret a supplier’s warranty conditions, leading to potential disputes. This situation can be particularly frustrating when urgent issues arise, such as needing technical support or replacement parts.
The Solution:
To overcome language barriers, buyers should consider working with bilingual procurement agents or hiring a local consultant who understands both the market and the language. Using professional translation services for contracts and specifications can also minimize misunderstandings. Additionally, establishing clear and detailed documentation that outlines every aspect of the purchase—including warranty terms, service agreements, and technical specifications—can prevent miscommunication. Utilizing visual aids or diagrams can further clarify complex requirements.
Scenario 3: Limited Technical Support and Spare Parts Availability
The Problem:
Another common pain point for B2B buyers is the lack of adequate technical support and availability of spare parts for mini lathes sourced from China. Buyers in the Middle East may find themselves in a situation where, after purchasing a mini lathe, they encounter a technical issue but cannot access timely support. Additionally, if spare parts are not readily available, this can lead to prolonged downtime, affecting production schedules and overall operational efficiency.
The Solution:
To address this issue, buyers should prioritize suppliers who offer comprehensive after-sales support, including technical assistance and a clear spare parts availability policy. Before finalizing a purchase, it’s crucial to inquire about the supplier’s support infrastructure, including contact points for technical help and estimated delivery times for spare parts. Buyers can also negotiate service level agreements (SLAs) that guarantee response times for support requests and parts availability. Building a relationship with multiple suppliers can provide a safety net, ensuring that buyers have options for support and parts if their primary supplier falls short.
Strategic Material Selection Guide for mini lathe china
When selecting materials for mini lathes manufactured in China, international B2B buyers must consider various factors that influence product performance, manufacturing processes, and compliance with regional standards. Here, we analyze four common materials used in mini lathes, focusing on their properties, advantages, disadvantages, and implications for buyers from Africa, South America, the Middle East, and Europe.
What are the Key Properties of Cast Iron in Mini Lathes?
Cast Iron is a widely used material for mini lathes due to its excellent vibration dampening properties and durability. It can withstand high temperatures and is resistant to wear, making it suitable for heavy-duty machining applications. The material typically has a temperature rating of up to 600°C and can handle moderate pressure.
Pros:
– High durability and resistance to wear.
– Excellent vibration dampening, leading to improved machining accuracy.
– Cost-effective compared to other materials.
Cons:
– Prone to corrosion if not properly maintained.
– Heavier than alternatives, which may affect portability.
Impact on Application:
Cast iron is compatible with a variety of machining processes, including turning and milling. However, buyers must consider its susceptibility to rust, especially in humid environments.
Considerations for International Buyers:
Buyers should ensure compliance with ASTM standards for cast iron. Countries like Germany may have specific regulations regarding material quality that must be adhered to.
How Does Aluminum Enhance Performance in Mini Lathes?
Aluminum is another popular choice for mini lathes, particularly for components that require a lightweight yet strong material. Aluminum has excellent thermal conductivity, making it ideal for applications that involve heat dissipation.
Pros:
– Lightweight, enhancing portability and ease of handling.
– Good resistance to corrosion, especially when anodized.
– High thermal conductivity, beneficial for heat-sensitive applications.
Cons:
– Lower strength compared to cast iron, which may limit its use in heavy-duty applications.
– More expensive than cast iron.
Impact on Application:
Aluminum is often used in applications where weight is a critical factor, such as in portable mini lathes. Its corrosion resistance makes it suitable for environments with high humidity.
Considerations for International Buyers:
Buyers should check for compliance with DIN standards for aluminum components. Countries like Egypt may have specific import regulations regarding aluminum alloys.
What Role Does Steel Play in Mini Lathe Manufacturing?
Steel, particularly carbon steel, is frequently used in the construction of mini lathes due to its strength and versatility. Steel can be heat-treated to enhance its hardness and wear resistance, making it suitable for high-performance applications.
Pros:
– High strength and durability, suitable for heavy machining tasks.
– Versatile and can be easily machined into complex shapes.
Cons:
– Heavier than aluminum, which may affect the overall weight of the lathe.
– Prone to corrosion if not properly treated.
Impact on Application:
Steel is ideal for components that undergo significant stress and wear. However, its weight can be a disadvantage for portable models.
Considerations for International Buyers:
Compliance with JIS standards is crucial for steel components. Buyers from South America should be aware of local regulations regarding the import of steel products.
How Does Plastic Contribute to Mini Lathe Design?
Plastic, particularly high-density polyethylene (HDPE) and polycarbonate, is increasingly used in mini lathes for non-structural components. These materials are lightweight and can be molded into various shapes.
Pros:
– Extremely lightweight, enhancing portability.
– Resistant to corrosion and chemical damage.
Cons:
– Lower strength compared to metals, limiting its use in structural applications.
– May not withstand high temperatures as well as metals.
Impact on Application:
Plastic components are often used in housings and covers, where strength is less critical. They are suitable for applications that require resistance to chemicals.
Considerations for International Buyers:
Buyers should ensure that plastic materials meet relevant safety and environmental standards, which may vary by region.
Summary Table of Material Selection for Mini Lathes
Material | Typical Use Case for mini lathe china | Key Advantage | Key Disadvantage/Limitation | Relative Cost (Low/Med/High) |
---|---|---|---|---|
Cast Iron | Base and structural components | Excellent durability and vibration dampening | Prone to corrosion | Low |
Aluminum | Portable components | Lightweight and corrosion-resistant | Lower strength compared to cast iron | Medium |
Steel | Heavy-duty components | High strength and versatility | Heavier and prone to corrosion | Medium |
Plastic | Non-structural components | Lightweight and chemical resistant | Lower strength and temperature limitations | Low |
By understanding the properties, advantages, and limitations of these materials, international B2B buyers can make informed decisions that align with their specific needs and compliance requirements.
In-depth Look: Manufacturing Processes and Quality Assurance for mini lathe china
What Are the Main Stages of Manufacturing Mini Lathes in China?
The manufacturing process of mini lathes in China involves several critical stages that ensure the quality and efficiency of the final product. Understanding these stages can help international B2B buyers assess potential suppliers effectively.
1. Material Preparation: What Materials Are Used in Mini Lathe Manufacturing?
The first step in manufacturing mini lathes is the selection and preparation of materials. Commonly used materials include high-grade steel and aluminum alloys, which provide strength and durability. The material preparation phase involves cutting, machining, and sometimes heat treating the raw materials to meet the specific requirements of the mini lathe components.
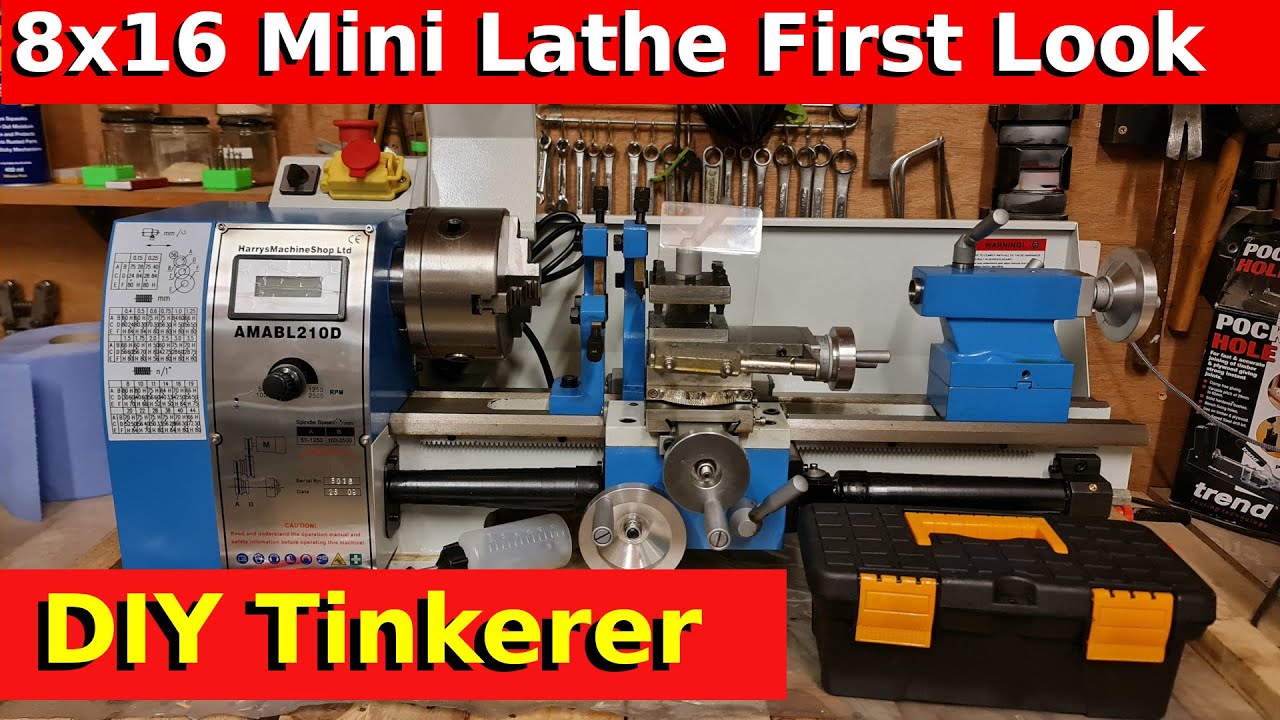
A stock image related to mini lathe china.
This stage is crucial, as the quality of raw materials significantly influences the performance and longevity of the final product. B2B buyers should inquire about the types of materials used and any certifications that ensure they meet industry standards.
2. Forming: How Are Components Shaped and Assembled?
The forming stage involves various manufacturing techniques, including CNC machining, casting, and forging. CNC (Computer Numerical Control) machining is particularly prevalent due to its precision and ability to produce complex shapes.
During this phase, components such as the bed, headstock, tailstock, and carriage are formed. The precision of these components is critical for the mini lathe’s functionality and accuracy. Buyers should verify that suppliers use state-of-the-art machinery and skilled labor to achieve high tolerances in their components.
3. Assembly: What Is the Process of Assembling Mini Lathes?
After forming, the components undergo assembly, where they are meticulously put together to create the mini lathe. This stage often involves a series of sub-assemblies, including the installation of the drive mechanism, electrical wiring, and control systems.
Quality during assembly is essential; even minor errors can lead to significant performance issues. Buyers should look for suppliers who implement standardized assembly procedures and use skilled technicians to ensure that each unit is assembled correctly.
4. Finishing: What Techniques Are Used for Surface Treatment?
The finishing stage is where the mini lathe is prepared for the market. This process typically includes surface treatments such as painting, anodizing, or powder coating, which enhance corrosion resistance and aesthetic appeal.
Finishing also involves quality checks to ensure that the cosmetic aspects meet customer expectations. B2B buyers should inquire about the finishing processes used by suppliers, as this can impact the overall durability and marketability of the product.
What Quality Assurance Measures Are Standard in Mini Lathe Manufacturing?
Quality assurance (QA) is a vital part of the manufacturing process for mini lathes, ensuring that products meet international standards and customer requirements.
1. What International Standards Should B2B Buyers Be Aware Of?
Most reputable manufacturers in China adhere to international quality standards such as ISO 9001, which outlines requirements for a quality management system. This certification indicates that the manufacturer has established processes to ensure consistent quality in their products.
Additionally, compliance with industry-specific standards like CE (Conformité Européenne) for the European market and API (American Petroleum Institute) standards for machinery used in the oil and gas sector can further assure buyers of the quality and safety of the mini lathes.
2. What Are the Key Quality Control Checkpoints?
Quality control (QC) checkpoints are integrated throughout the manufacturing process. Key stages include:
- Incoming Quality Control (IQC): Inspects raw materials upon arrival to ensure they meet specifications.
- In-Process Quality Control (IPQC): Monitors the manufacturing process through regular inspections to catch defects early.
- Final Quality Control (FQC): Conducts comprehensive testing on the finished product before it is packaged and shipped.
These checkpoints help maintain high-quality standards and reduce the likelihood of defects reaching the customer.
3. What Testing Methods Are Commonly Used for Mini Lathes?
Various testing methods are employed to ensure the functionality and durability of mini lathes. Common tests include:
- Functional Testing: Verifying that all components operate correctly.
- Performance Testing: Assessing the lathe’s efficiency and accuracy under load.
- Durability Testing: Evaluating how well the lathe withstands prolonged use.
B2B buyers should request details about the testing methods used by suppliers to ensure that their products meet the required performance specifications.
How Can International B2B Buyers Verify Supplier Quality Control?
To ensure that suppliers maintain high-quality standards, B2B buyers can take several proactive steps.
1. What Audit Processes Should Buyers Consider?
Conducting supplier audits is an effective way to verify quality control practices. Buyers can perform on-site inspections or hire third-party auditing services to assess the supplier’s manufacturing processes, quality control systems, and adherence to international standards.
2. How Important Are Quality Control Reports?
Requesting quality control reports from suppliers can provide valuable insights into their manufacturing practices. These reports should detail the results of the various QC checkpoints and any corrective actions taken to address issues.
3. What Role Do Third-Party Inspections Play?
Engaging third-party inspection services can further assure buyers of the quality of their orders. These services can conduct inspections at various stages of the manufacturing process, ensuring that the products meet the specified standards before shipping.
What Are the Nuances of Quality Certification for International Buyers?
Quality certifications can vary significantly by region, and understanding these nuances is essential for B2B buyers, especially those from Africa, South America, the Middle East, and Europe.
1. How Do Regional Certifications Differ?
Different regions may have specific certification requirements. For instance, products sold in Europe typically require CE marking, while other regions may prioritize different certifications. Buyers should familiarize themselves with the relevant standards in their target markets.
2. Why Is Communication with Suppliers Critical?
Effective communication with suppliers about quality standards and certifications is crucial. B2B buyers should clarify their quality requirements upfront and ensure that suppliers can meet these expectations.
By understanding the manufacturing processes and quality assurance measures involved in mini lathe production, international B2B buyers can make informed decisions when sourcing from Chinese manufacturers. This knowledge not only enhances the purchasing process but also helps establish long-term relationships with reliable suppliers.
Practical Sourcing Guide: A Step-by-Step Checklist for ‘mini lathe china’
In today’s competitive manufacturing landscape, sourcing a mini lathe from China can be a strategic move for businesses looking to enhance their production capabilities. This guide provides a step-by-step checklist to help international B2B buyers, particularly those from Africa, South America, the Middle East, and Europe, navigate the sourcing process effectively.
Step 1: Define Your Technical Specifications
Before initiating the sourcing process, it is essential to have a clear understanding of your requirements for the mini lathe. This includes specifications such as size, power, precision, and features like digital readouts or CNC capabilities. Defining these parameters will streamline your search and ensure that potential suppliers can meet your operational needs.
- Key Considerations:
- What is the maximum workpiece size you need to handle?
- Do you require additional features such as variable speed control or automatic tool changers?
Step 2: Research Potential Suppliers
Conduct thorough research to identify reputable suppliers in China. Utilize online platforms like Alibaba, Made-in-China, and Global Sources to find manufacturers with positive reviews and a strong track record. Investigate their product offerings and compare them with your specifications.
- What to Look For:
- Supplier ratings and feedback from previous buyers.
- Years of experience in manufacturing mini lathes.
Step 3: Verify Supplier Certifications
Ensure that the suppliers you are considering have the necessary certifications, such as ISO 9001, CE, or other relevant quality standards. Certification indicates that the supplier adheres to quality management practices and can deliver reliable products.
- Importance of Certification:
- Protects your investment by ensuring the product meets international quality standards.
- Reduces the risk of sourcing from unreliable manufacturers.
Step 4: Request Product Samples
Before making a bulk purchase, request samples of the mini lathe. This allows you to evaluate the quality, functionality, and suitability of the product firsthand. Testing a sample can help prevent costly mistakes in the procurement process.
- Evaluation Criteria:
- Precision and accuracy in machining operations.
- Ease of use and maintenance.
Step 5: Discuss Pricing and Payment Terms
Engage in negotiations regarding pricing, payment terms, and order quantities. Understanding the total cost of ownership, including shipping and tariffs, is crucial for budgeting. Be wary of unusually low prices, which may indicate subpar quality.
- Negotiation Tips:
- Consider bulk order discounts.
- Clarify payment methods (e.g., letter of credit, PayPal).
Step 6: Review Shipping and Logistics Options
Shipping costs and logistics can significantly affect your overall procurement budget. Discuss shipping options with suppliers, including lead times and incoterms (e.g., FOB, CIF). Ensure that the chosen logistics partner is reliable and experienced in handling international shipments.
- Logistics Considerations:
- Delivery timelines and potential delays.
- Customs clearance processes in your country.
Step 7: Establish After-Sales Support and Warranty Terms
Finally, inquire about after-sales support and warranty terms. A reputable supplier should offer assistance post-purchase, including technical support and replacement parts. Understanding warranty terms will provide peace of mind regarding the longevity of your investment.
- Support Aspects:
- Availability of spare parts.
- Technical assistance for troubleshooting.
By following this practical sourcing guide, B2B buyers can make informed decisions when procuring mini lathes from China, ensuring they select the right supplier to meet their production needs.
Comprehensive Cost and Pricing Analysis for mini lathe china Sourcing
What Are the Key Cost Components in Sourcing Mini Lathes from China?
Understanding the cost structure when sourcing mini lathes from China is critical for international B2B buyers. The primary cost components include:
-
Materials: The choice of materials greatly influences the overall cost. For mini lathes, common materials include cast iron for the body and high-speed steel for tools. Prices can fluctuate based on market conditions, so it is advisable to monitor commodity prices.
-
Labor: Labor costs in China can vary significantly based on the region and the skill level required. More skilled labor may increase costs but can also enhance product quality and consistency.
-
Manufacturing Overhead: This includes costs associated with factory operations, utilities, and administrative expenses. Efficient factories may have lower overhead, impacting the final pricing positively.
-
Tooling: The initial investment in tooling can be substantial, especially for custom designs. Depending on the complexity of the mini lathe, tooling costs can vary, so consider standard designs to reduce this expense.
-
Quality Control (QC): Implementing stringent QC processes is essential to ensure product reliability. This may increase initial costs but can save money in the long run by reducing defects and returns.
-
Logistics: Shipping costs are a significant factor, particularly for international buyers. Factors such as shipping method, distance, and Incoterms will affect overall logistics costs.
-
Margin: Supplier margins can vary widely. Understanding the supplier’s profit expectations can aid in negotiations and help in establishing a fair price.
How Do Price Influencers Affect the Sourcing of Mini Lathes?
Several factors can influence the pricing of mini lathes sourced from China:
-
Volume and Minimum Order Quantity (MOQ): Larger orders typically result in lower per-unit prices. Understanding the supplier’s MOQ can help in planning purchases effectively.
-
Specifications and Customization: Customized mini lathes may incur additional costs. Buyers should be clear about their specifications to avoid unexpected price increases.
-
Materials and Quality Certifications: Higher quality materials and certifications (e.g., ISO, CE) can lead to increased costs but are often justified by enhanced product performance and reliability.
-
Supplier Factors: The reputation and reliability of the supplier can impact pricing. Established suppliers may charge a premium, but they often provide better quality assurance and customer service.
-
Incoterms: The chosen Incoterms (e.g., FOB, CIF) will determine who bears the shipping costs and risks. This can significantly affect the total landed cost of the mini lathe.
What Tips Can Help International B2B Buyers Negotiate Better Prices?
For buyers in Africa, South America, the Middle East, and Europe, negotiating effectively can yield substantial savings:
-
Conduct Thorough Market Research: Understand prevailing prices and trends within the mini lathe market. This knowledge will empower you during negotiations.
-
Evaluate Total Cost of Ownership (TCO): Consider not just the purchase price, but also maintenance, operational costs, and potential downtime. This holistic view can justify a higher initial investment in quality.
-
Utilize Competitive Quotes: Obtain quotes from multiple suppliers to create a competitive bidding environment. This can leverage better pricing and terms.
-
Negotiate Payment Terms: Flexible payment terms can improve cash flow. Explore options like extended payment periods or discounts for early payment.
-
Communicate Clearly: Ensure all specifications and expectations are clearly communicated to avoid misunderstandings that could lead to additional costs.
Disclaimer on Indicative Prices
Prices for mini lathes can vary significantly based on the above factors and market conditions. It is advisable for buyers to request current pricing directly from suppliers to obtain the most accurate and relevant information.
Alternatives Analysis: Comparing mini lathe china With Other Solutions
When considering purchasing a mini lathe, international B2B buyers should explore various alternatives that may meet their machining needs. Each option presents unique advantages and disadvantages, influencing the overall decision-making process. This analysis compares ‘Mini Lathe China’ with CNC milling machines and manual lathes, two viable alternatives that serve similar purposes in manufacturing and machining.
Comparison Aspect | Mini Lathe China | CNC Milling Machine | Manual Lathe |
---|---|---|---|
Performance | High precision for small parts | Exceptional precision, suitable for complex shapes | Good precision, but limited to simpler operations |
Cost | Affordable (low to mid-range) | Higher initial investment | Generally lower cost than CNC but varies widely |
Ease of Implementation | Easy setup and operation | Requires skilled operator and programming knowledge | Simple to operate for experienced machinists |
Maintenance | Low maintenance, easy to service | Higher maintenance due to complexity | Moderate maintenance, depends on usage |
Best Use Case | Small-scale production and prototyping | Large-scale production and intricate designs | Hobbyists and basic machining tasks |
What Are the Advantages and Disadvantages of CNC Milling Machines Compared to Mini Lathes?
CNC milling machines provide exceptional precision and can handle complex designs that a mini lathe may struggle with. They are ideal for large-scale production due to their efficiency and ability to automate processes. However, they come with a higher initial investment and require skilled operators who can program and manage the machine effectively. Maintenance is also more demanding, as the complexity of CNC machines can lead to more frequent repairs and downtime.
How Do Manual Lathes Compare with Mini Lathes in Terms of Usability and Cost?
Manual lathes are often more affordable than CNC machines, making them a popular choice for small workshops and hobbyists. They offer a straightforward operation for those with machining experience, allowing for hands-on crafting of parts. However, they lack the precision and versatility of CNC milling and are limited to simpler operations. Maintenance is generally moderate, but the user must be skilled in manual operations to achieve the desired results.
Conclusion: How Should B2B Buyers Choose the Right Machining Solution?
When selecting a machining solution, B2B buyers should carefully assess their specific needs, including production volume, budget constraints, and the complexity of the parts they intend to manufacture. If precision and automation are paramount, investing in a CNC milling machine may be worthwhile despite the higher cost. For smaller scale productions with simpler requirements, ‘Mini Lathe China’ can provide a cost-effective and efficient solution. Manual lathes serve well for hobbyists or those needing basic machining capabilities. Ultimately, the choice should align with the operational goals and the technical expertise available within the organization.
Essential Technical Properties and Trade Terminology for mini lathe china
What Are the Essential Technical Properties of Mini Lathes from China?
When considering the purchase of mini lathes from China, understanding their technical specifications is vital for making informed decisions. Here are some key properties to consider:
1. Material Grade: Why Is It Critical?
The material grade of a mini lathe significantly impacts its durability and performance. Common materials include cast iron and steel. Cast iron provides vibration dampening, essential for precision machining, while high-grade steel offers enhanced strength and longevity. Buyers should assess the material based on the intended application, as it affects both maintenance and operational costs.
2. Tolerance Levels: What Do They Mean for Precision?
Tolerance levels indicate the permissible limit of variation in the dimensions of the lathe components. For mini lathes, a typical tolerance range is ±0.01 mm. This precision is crucial for producing parts that fit seamlessly in assemblies. For international buyers, understanding tolerance specifications is essential for ensuring that the lathe can meet their specific machining requirements.
3. Spindle Speed: How Does It Affect Machining Operations?
Spindle speed, often measured in RPM (revolutions per minute), determines the cutting efficiency of the lathe. Mini lathes typically offer variable spindle speeds, ranging from 50 to 3000 RPM. Higher speeds allow for quicker material removal and finer finishes, making it essential for buyers to match spindle speed capabilities with their machining tasks.
4. Power Rating: What Is Its Role in Performance?
The power rating, usually measured in watts or horsepower, indicates the motor’s capability to handle different materials. Mini lathes often have power ratings between 250W and 750W. A higher power rating allows the lathe to cut through tougher materials and handle larger workpieces, which is particularly important for industrial applications.
5. Bed Length: Why Is This Measurement Important?
The bed length of a mini lathe affects the maximum length of workpieces that can be machined. Standard bed lengths range from 300 mm to 1200 mm. Understanding the bed length is essential for buyers to ensure that the lathe can accommodate their specific project requirements.
What Trade Terms Should International Buyers Understand?
Navigating the procurement process for mini lathes involves familiarizing oneself with industry terminology. Here are some common trade terms that every buyer should know:
1. OEM (Original Equipment Manufacturer): What Does It Mean?
An OEM refers to a company that manufactures products or components that are sold by another company under its brand name. For mini lathes, buyers often deal with OEMs to customize machines according to their specifications, ensuring that they receive tailored solutions that meet their operational needs.
2. MOQ (Minimum Order Quantity): How Does It Impact Purchases?
MOQ represents the minimum number of units a supplier is willing to sell in one order. Understanding MOQ is crucial for budget management, as it can affect inventory levels and pricing. Buyers should negotiate MOQs that align with their production schedules and financial plans.
3. RFQ (Request for Quotation): What Is Its Purpose?
An RFQ is a formal document sent to suppliers to request pricing and terms for a specific product or service. For mini lathes, submitting an RFQ allows buyers to compare offers from different manufacturers, helping them make cost-effective purchasing decisions.
4. Incoterms (International Commercial Terms): Why Are They Important?
Incoterms define the responsibilities of buyers and sellers in international transactions, outlining who is responsible for shipping, insurance, and tariffs. Familiarity with Incoterms helps international buyers understand their obligations and avoid unexpected costs during the importation process.
5. Lead Time: What Should Buyers Expect?
Lead time refers to the period from placing an order to receiving the product. For mini lathes, this can vary based on production schedules and shipping arrangements. Understanding lead time is essential for planning and ensuring that machinery arrives in time for production needs.
By grasping these technical properties and trade terms, international buyers can navigate the complexities of purchasing mini lathes from China with greater confidence and clarity.
Navigating Market Dynamics and Sourcing Trends in the mini lathe china Sector
What Are the Key Trends Driving the Mini Lathe Market in China?
The mini lathe market in China is currently experiencing significant growth, driven by several global factors. The increasing demand for precision engineering across various industries, such as automotive, aerospace, and electronics, is a primary driver. Moreover, the rise of small-scale manufacturing and DIY projects has broadened the customer base for mini lathes, particularly among small and medium enterprises (SMEs). International B2B buyers from regions like Africa, South America, the Middle East, and Europe are increasingly sourcing mini lathes from China due to competitive pricing and advanced technology.
Emerging technologies such as automation and Industry 4.0 are reshaping the sourcing landscape. Buyers are seeking suppliers who can integrate smart features into their mini lathes, such as CNC capabilities and IoT connectivity, which enhance efficiency and accuracy. Additionally, the trend towards customization is gaining traction, with buyers looking for manufacturers that can offer tailored solutions to meet specific production needs.
How Are Sustainability and Ethical Sourcing Impacting the Mini Lathe Market?
Sustainability has become a pivotal concern for international B2B buyers, influencing their sourcing decisions. In the mini lathe sector, this includes the environmental impact of manufacturing processes and the materials used. Buyers are increasingly prioritizing suppliers who implement eco-friendly practices and minimize waste in their production lines.
Ethical sourcing is also crucial, particularly for companies looking to enhance their corporate social responsibility (CSR) initiatives. Certifications such as ISO 14001 (Environmental Management) and ISO 9001 (Quality Management) are becoming essential for suppliers to demonstrate their commitment to sustainable practices. Furthermore, the use of green materials in manufacturing mini lathes not only reduces environmental impact but also appeals to a growing base of environmentally-conscious consumers. As a result, buyers should conduct thorough due diligence to ensure that their suppliers adhere to these sustainability standards.
What is the Brief History of Mini Lathes and Their Evolution?
The mini lathe has a rich history, tracing its roots back to the late 18th century during the Industrial Revolution. Initially designed for larger-scale operations, the introduction of smaller, more versatile lathes in the 20th century made them accessible to hobbyists and SMEs. In recent decades, advancements in technology have led to the development of CNC mini lathes, which offer improved precision and automation.
As the global market continues to evolve, mini lathes are becoming integral to modern manufacturing processes. The shift towards more compact, efficient machinery is driving innovation, enabling manufacturers in China to produce high-quality mini lathes that meet the diverse needs of international B2B buyers. This evolution not only reflects the changing demands of various industries but also highlights the importance of adaptability in the manufacturing sector.
Frequently Asked Questions (FAQs) for B2B Buyers of mini lathe china
-
How do I choose the right mini lathe from China for my business needs?
Selecting the appropriate mini lathe involves assessing your specific requirements such as the materials you’ll be working with, the precision needed, and the size of the projects. Research different models based on their specifications, including spindle speed, power, and bed length. Request samples if possible, and read reviews from other buyers in your industry. Additionally, consider the support and warranty offered by the supplier, as this can significantly impact your operational efficiency. -
What are the common customization options available for mini lathes from Chinese suppliers?
Many Chinese manufacturers offer customization options to meet specific operational needs. Common customizations include modifications to the lathe’s size, additional tooling, and enhanced features like digital readouts or automatic feeds. Discuss your requirements with potential suppliers during the initial inquiry phase. Be clear about your production needs, as this will help the supplier provide tailored solutions that align with your business objectives. -
What is the typical minimum order quantity (MOQ) for mini lathes sourced from China?
The MOQ for mini lathes can vary significantly depending on the manufacturer and the model you are interested in. Generally, the MOQ ranges from 1 to 10 units for standard models. However, for customized options or specialized models, the MOQ may be higher. It’s advisable to confirm these details during your initial discussions with suppliers to ensure alignment with your purchasing strategy. -
What payment terms should I expect when sourcing mini lathes from Chinese suppliers?
Payment terms can vary by supplier but commonly include options like a 30% deposit with the balance due before shipment or a Letter of Credit (LC) for larger orders. It’s crucial to negotiate terms that suit your cash flow and risk management strategies. Always ensure you understand the implications of the payment method on your order’s safety and delivery timeline, especially if you’re new to international transactions. -
How can I verify the credibility of a mini lathe supplier in China?
To vet a supplier’s credibility, start by checking their business licenses and certifications, such as ISO standards. Look for online reviews and testimonials from other international buyers. Engaging a third-party inspection service for factory audits can provide additional assurance. Moreover, consider attending trade shows or visiting the supplier’s facility to establish a direct relationship and observe their manufacturing processes. -
What quality assurance measures should I implement when sourcing mini lathes from China?
Implementing quality assurance measures involves several steps, including specifying quality standards in your contract, conducting pre-shipment inspections, and requesting certificates of conformity for components used in the lathe. Establishing clear communication with your supplier regarding quality expectations and maintaining a consistent follow-up schedule can help mitigate risks associated with product defects. -
What logistics considerations should I keep in mind when importing mini lathes from China?
When importing mini lathes, consider shipping options, costs, and timelines. Air freight is faster but more expensive, while sea freight is cost-effective for larger shipments. Ensure you understand customs regulations in your country to avoid delays. Collaborating with a freight forwarder can streamline the logistics process, handling documentation and ensuring compliance with import regulations. -
What after-sales support can I expect from Chinese mini lathe suppliers?
After-sales support can vary, but reputable suppliers often provide warranty coverage, technical assistance, and access to spare parts. Inquire about the duration of the warranty, what it covers, and the process for obtaining support. Additionally, ask if they offer training for your staff on the machine’s operation and maintenance, as this can greatly enhance your operational efficiency and reduce downtime.
Important Disclaimer & Terms of Use
⚠️ Important Disclaimer
The information provided in this guide, including content regarding manufacturers, technical specifications, and market analysis, is for informational and educational purposes only. It does not constitute professional procurement advice, financial advice, or legal advice.
While we have made every effort to ensure the accuracy and timeliness of the information, we are not responsible for any errors, omissions, or outdated information. Market conditions, company details, and technical standards are subject to change.
B2B buyers must conduct their own independent and thorough due diligence before making any purchasing decisions. This includes contacting suppliers directly, verifying certifications, requesting samples, and seeking professional consultation. The risk of relying on any information in this guide is borne solely by the reader.
Strategic Sourcing Conclusion and Outlook for mini lathe china
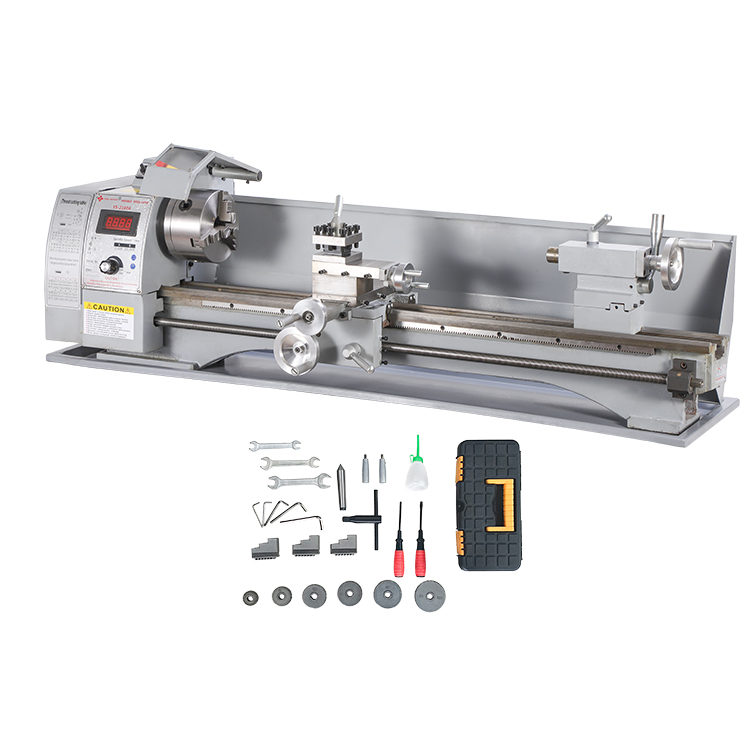
A stock image related to mini lathe china.
In conclusion, strategic sourcing of mini lathes from China presents a unique opportunity for international B2B buyers, especially those in Africa, South America, the Middle East, and Europe. By leveraging China’s competitive pricing, advanced manufacturing capabilities, and a diverse range of products, businesses can enhance their operational efficiency and product offerings.
Why is Strategic Sourcing Essential for B2B Buyers?
Understanding the nuances of strategic sourcing allows buyers to mitigate risks associated with supply chain disruptions and quality inconsistencies. Establishing strong relationships with reliable Chinese manufacturers can lead to better negotiation terms, improved product quality, and reduced lead times. Buyers should prioritize suppliers that demonstrate transparency, quality control measures, and a commitment to after-sales support.
How Can Buyers Prepare for Future Trends in Mini Lathes?
As technology continues to evolve, staying ahead of market trends will be crucial. Buyers should consider suppliers that are investing in innovative technologies and sustainable practices. Engaging in ongoing market research and supplier evaluation will empower businesses to adapt to changing demands effectively.
In a rapidly changing global market, now is the time for international B2B buyers to embrace strategic sourcing from China. By taking decisive action and forming strategic partnerships, businesses can position themselves for long-term success. Explore your options today to secure a competitive edge in your industry.