Discover Cost-Effective Queen Size Bed Frame Custom Solutions (2025)
Introduction: Navigating the Global Market for queen size bed frame custom
In the dynamic landscape of global commerce, sourcing a queen size bed frame custom to meet specific market demands can be a daunting challenge for B2B buyers. Whether you are catering to the burgeoning hospitality sector in Africa, the expanding furniture markets in South America, or the luxury accommodations in the Middle East and Europe, understanding the nuances of customization is essential. This guide is designed to equip international buyers with the knowledge and tools necessary to navigate the complexities of sourcing high-quality, tailored bed frames that align with regional preferences and standards.
Throughout this comprehensive guide, we will delve into various aspects of the custom queen size bed frame market. You will explore different types of materials and designs, applications across diverse sectors, and key considerations for supplier vetting. Furthermore, we will discuss cost structures and pricing strategies to ensure you make informed purchasing decisions.
By empowering B2B buyers with actionable insights and practical strategies, this guide aims to streamline the sourcing process, reduce risks, and enhance the overall quality of your procurement efforts. From understanding cultural preferences to evaluating supplier reliability, our focus is on providing you with the expertise to thrive in the competitive global market. Whether you’re in the UAE, Thailand, or beyond, this resource will serve as your go-to manual for successful sourcing of custom queen size bed frames.
Understanding queen size bed frame custom Types and Variations
Type Name | Key Distinguishing Features | Primary B2B Applications | Brief Pros & Cons for Buyers |
---|---|---|---|
Platform Bed Frame | Low-profile, no box spring needed | Hotels, hostels, and rental properties | Pros: Cost-effective, modern look. Cons: Limited storage options. |
Sleigh Bed Frame | Curved headboard and footboard, traditional style | Luxury hotels, boutique accommodations | Pros: Aesthetic appeal, sturdy. Cons: Higher shipping costs due to size. |
Upholstered Bed Frame | Soft fabric or leather finish, customizable designs | High-end residential, design-focused hotels | Pros: Comfort, diverse design options. Cons: Requires more maintenance. |
Adjustable Bed Frame | Mechanically adjustable for head and foot positions | Healthcare facilities, senior living | Pros: Increased comfort, versatile. Cons: Higher initial investment. |
Storage Bed Frame | Integrated drawers or compartments for storage | Small apartments, student housing | Pros: Maximizes space, functional. Cons: Heavier, more complex assembly. |
What Are the Characteristics of a Platform Bed Frame?
A platform bed frame is designed to support a mattress without the need for a box spring, making it a cost-effective option. These frames are typically low-profile, offering a sleek, modern aesthetic that appeals to contemporary buyers. For B2B applications, they are ideal for hotels, hostels, and rental properties, where budget considerations are crucial. When purchasing, buyers should consider the frame’s material and durability, as well as its compatibility with various mattress types.
How Do Sleigh Bed Frames Stand Out in the Market?
Sleigh bed frames are characterized by their distinctive curved headboards and footboards, which exude a traditional elegance. These frames are often made from solid wood, making them a sturdy choice for luxury hotels and boutique accommodations. When sourcing sleigh bed frames, B2B buyers should evaluate the craftsmanship and finish, as these factors significantly impact the perceived quality and longevity of the product. However, the larger size may incur higher shipping costs, which should be factored into budgeting.
What Are the Benefits of Upholstered Bed Frames for B2B Buyers?
Upholstered bed frames offer a soft finish, often available in various fabrics and colors, allowing for customization to fit specific branding or design themes. They are particularly suitable for high-end residential markets and design-focused hotels. Buyers should consider the fabric’s durability and ease of cleaning, as these frames may require more maintenance compared to wooden options. While they provide comfort and aesthetic appeal, the investment may be higher due to the materials and craftsmanship involved.
Why Are Adjustable Bed Frames Gaining Popularity in B2B Markets?
Adjustable bed frames are designed for mechanical adjustments, allowing users to elevate the head and foot of the bed. This feature is particularly beneficial in healthcare facilities and senior living environments, where comfort and support are paramount. B2B buyers should assess the frame’s motor quality and warranty, as these factors can affect long-term usability. While they offer significant comfort and versatility, the initial investment is generally higher than traditional frames, which should be accounted for in budget planning.
How Do Storage Bed Frames Maximize Space for Buyers?
Storage bed frames come equipped with built-in drawers or compartments, providing an efficient solution for maximizing space, especially in small apartments and student housing. These frames are particularly appealing to B2B buyers looking to furnish compact living spaces. When selecting a storage bed frame, considerations should include the ease of access to storage and the overall weight of the frame, as heavier frames may complicate assembly and transport. While they offer functional benefits, the complexity of assembly can be a drawback for some buyers.
Related Video: 2x4s ONLY! Queen Size Bed Frame ONE DAY BUILD!
Key Industrial Applications of queen size bed frame custom
Industry/Sector | Specific Application of queen size bed frame custom | Value/Benefit for the Business | Key Sourcing Considerations for this Application |
---|---|---|---|
Hospitality | Custom bed frames for hotels and resorts | Enhances guest experience, leading to higher ratings and repeat business | Durable materials, aesthetic appeal, and ease of assembly |
Furniture Retail | Boutique furniture stores offering customized options | Differentiates product line and meets specific customer demands | Design flexibility, cost-effectiveness, and supply chain reliability |
Health Care | Custom bed frames for patient rooms in clinics | Improves patient comfort and recovery, enhancing overall care quality | Compliance with health regulations, ergonomic design, and durability |
Interior Design | Custom bed frames for residential projects | Tailors to client specifications, boosting customer satisfaction | Unique designs, material sourcing, and delivery timelines |
E-commerce | Online retailers providing bespoke bed solutions | Expands market reach by catering to niche customer preferences | Efficient logistics, competitive pricing, and product customization options |
How is ‘queen size bed frame custom’ utilized in the hospitality industry?
In the hospitality sector, custom queen size bed frames are essential for hotels and resorts aiming to provide exceptional guest experiences. These bed frames can be designed to match the hotel’s aesthetic, ensuring a cohesive look throughout the property. By investing in high-quality, tailored bed frames, businesses can enhance guest comfort, leading to positive reviews and increased occupancy rates. International buyers should consider sourcing durable materials that withstand heavy usage, while also ensuring that the designs align with local cultural preferences.
What role does ‘queen size bed frame custom’ play in furniture retail?
Boutique furniture stores often leverage custom queen size bed frames to differentiate themselves in a competitive market. By offering bespoke options, retailers can cater to specific customer needs and preferences, enhancing their product lineup. This not only attracts a wider customer base but also allows for higher profit margins on custom orders. When sourcing, retailers should prioritize design flexibility and establish reliable supply chains to meet varying customer demands, particularly in regions like South America and Europe where design trends can vary significantly.
How does ‘queen size bed frame custom’ improve patient care in healthcare settings?
In healthcare facilities, custom queen size bed frames are vital for patient rooms, as they contribute to both comfort and recovery. These frames can be tailored to meet specific ergonomic needs, ensuring that patients have a restful environment conducive to healing. Sourcing considerations include compliance with health regulations and the use of durable materials that can withstand rigorous cleaning protocols. International buyers in the Middle East and Africa should also ensure that the designs accommodate various cultural practices related to healthcare.
Why are ‘queen size bed frame custom’ significant for interior design projects?
Interior designers frequently utilize custom queen size bed frames to create personalized spaces for their clients. These bespoke solutions allow designers to tailor each project according to the client’s vision, enhancing overall customer satisfaction. The sourcing process should focus on unique designs and the availability of varied materials to match different themes and styles. In Europe, for example, buyers may seek eco-friendly materials, reflecting a growing trend towards sustainability in design.
How can e-commerce businesses benefit from ‘queen size bed frame custom’?
E-commerce platforms are increasingly offering custom queen size bed frames to cater to niche markets and diverse customer preferences. This approach not only expands their product offerings but also enhances customer engagement through personalization. Key sourcing considerations for e-commerce businesses include efficient logistics to ensure timely delivery and competitive pricing to attract price-sensitive consumers. In regions like Africa and South America, where online shopping is rapidly growing, businesses must also focus on user-friendly customization tools to enhance the shopping experience.
Related Video: Queen Size DIY Floating Bed Frame
3 Common User Pain Points for ‘queen size bed frame custom’ & Their Solutions
Scenario 1: Difficulty in Sourcing Quality Materials for Custom Bed Frames
The Problem: International B2B buyers, especially those from emerging markets in Africa and South America, often face challenges in sourcing high-quality materials for custom queen size bed frames. This issue can stem from a lack of local suppliers with the necessary quality certifications, leading to delays and increased costs. Additionally, language barriers and differing standards of material quality can result in misunderstandings, ultimately affecting the durability and aesthetic appeal of the final product.
The Solution: To effectively navigate this sourcing challenge, buyers should establish relationships with reputable suppliers who specialize in custom furniture manufacturing. Start by researching manufacturers that have a proven track record of exporting to your region. Utilize platforms like Alibaba or Global Sources to find suppliers with high ratings and positive reviews. Engage with suppliers to request samples and certifications that demonstrate the quality of materials used. Furthermore, consider visiting trade shows or industry expos in Europe or the Middle East to build face-to-face relationships and gain insights into material standards. By prioritizing quality sourcing, buyers can ensure their custom queen size bed frames meet market expectations and reduce the risk of costly returns or replacements.
Scenario 2: Customization and Design Misalignment
The Problem: Another significant pain point for B2B buyers is the difficulty in conveying specific design requirements for custom queen size bed frames. Buyers may have unique cultural or regional preferences that are not well understood by manufacturers, leading to misaligned expectations and dissatisfaction with the final product. This misalignment can result in wasted resources and time, particularly when modifications are needed after the initial production.
The Solution: To mitigate design misalignment, it is crucial to develop a detailed specification document that outlines every aspect of the desired bed frame, including dimensions, materials, color schemes, and design elements. Including visual aids, such as sketches or reference images, can also help bridge communication gaps. Additionally, consider using 3D modeling software to create a virtual representation of the bed frame, which can be shared with the manufacturer for precise feedback. Regular communication throughout the design process is essential, so schedule check-ins to review progress and make adjustments as necessary. This proactive approach ensures that the final product aligns with the buyer’s vision, ultimately leading to higher satisfaction and stronger supplier relationships.
Scenario 3: Logistical Challenges in Shipping Custom Bed Frames
The Problem: Logistical issues often arise when shipping custom queen size bed frames, particularly for B2B buyers in regions like the Middle East and Africa. These challenges can include high shipping costs, customs delays, and damages during transit. Such complications can significantly affect the supply chain and lead to lost sales opportunities, especially in a competitive market where timely delivery is critical.
The Solution: To address logistical challenges, buyers should work with logistics partners who have experience in handling large and delicate shipments. Seek companies that offer comprehensive services, including freight forwarding and customs brokerage, to streamline the shipping process. It’s advisable to conduct a thorough risk assessment of potential shipping routes and choose options that minimize transit times while maintaining cost-effectiveness. Additionally, invest in quality packaging materials to protect the bed frames during shipping and consider insurance to cover potential damages. By taking these precautions, buyers can significantly reduce the risks associated with shipping custom queen size bed frames, ensuring that they arrive safely and on time to meet customer demands.
Strategic Material Selection Guide for queen size bed frame custom
When selecting materials for custom queen size bed frames, international B2B buyers must consider a variety of factors that impact performance, durability, and compliance with regional standards. Below, we analyze four common materials used in the manufacturing of queen size bed frames, providing insights tailored for buyers from Africa, South America, the Middle East, and Europe.
What Are the Key Properties of Solid Wood for Queen Size Bed Frames?
Solid wood is a traditional choice for bed frames, known for its aesthetic appeal and durability. Key properties include high strength-to-weight ratio and natural resistance to temperature fluctuations. Different types of wood, such as oak, maple, and pine, exhibit varying levels of hardness and moisture resistance, which can be crucial in humid climates like those found in parts of Africa and South America.
Pros and Cons: Solid wood frames are highly durable and can last for decades with proper care. However, they can be expensive, particularly hardwoods, and may require complex manufacturing processes to achieve desired designs. Additionally, they are susceptible to warping in extreme humidity, which could be a concern in tropical regions.
Impact on Application: Solid wood frames are compatible with various mattress types, including memory foam and innerspring. However, buyers should be aware of potential weight restrictions based on wood type and frame design.
Considerations for International Buyers: Compliance with local standards, such as the European Union’s EN 747 for safety, is essential. Buyers should also consider the sustainability of wood sources, as certifications like FSC (Forest Stewardship Council) are increasingly important in Europe and North America.
How Does Metal Compare as a Material for Custom Bed Frames?
Metal bed frames, typically made from steel or aluminum, offer a modern aesthetic and exceptional strength. Key properties include high tensile strength and resistance to corrosion when treated properly. Steel frames, for instance, can withstand significant weight and pressure, making them ideal for heavy-duty applications.
Pros and Cons: Metal frames are generally more affordable than solid wood and can be easier to manufacture into intricate designs. However, they can be prone to rust if not properly coated, especially in humid environments. Additionally, metal frames may not provide the same warmth and aesthetic appeal as wood.
Impact on Application: Metal frames are compatible with various mattress types but may require specific slat configurations to ensure mattress support. They also tend to be lighter, making them easier to transport.
Considerations for International Buyers: Buyers should ensure that metal frames comply with relevant standards, such as ASTM A123 for hot-dip galvanized coatings. In regions like the Middle East, where humidity can be high, selecting rust-resistant finishes is crucial.
What Are the Benefits of Engineered Wood in Bed Frame Manufacturing?
Engineered wood, such as plywood or MDF (Medium Density Fiberboard), offers a cost-effective alternative to solid wood. Key properties include uniform strength and resistance to warping, which can be particularly beneficial in variable climate conditions.
Pros and Cons: Engineered wood is generally less expensive and easier to work with than solid wood. However, it may not have the same aesthetic appeal and can be less durable over time. Additionally, some engineered wood products may contain adhesives that emit VOCs (volatile organic compounds), which could be a concern for health-conscious buyers.
Impact on Application: Engineered wood frames can support various mattress types and are often designed to be lightweight, making them easier to handle and transport.
Considerations for International Buyers: Compliance with emission standards, such as the European E1 standard for formaldehyde emissions, is essential. Buyers in Europe and the Middle East should prioritize products that meet these standards to ensure safety and sustainability.
Why Choose Upholstered Bed Frames for Custom Designs?
Upholstered bed frames, often made from a wooden or metal base covered in fabric, provide a luxurious feel and aesthetic versatility. Key properties include comfort and the ability to customize fabric choices to suit various markets.
Pros and Cons: Upholstered frames can be visually appealing and comfortable, but they may require more maintenance and are generally less durable than solid wood or metal frames. They can also be more complex to manufacture due to the additional materials involved.
Impact on Application: Upholstered frames are compatible with various mattress types and can enhance the overall bedroom aesthetic. However, they may not be suitable for high-humidity environments without proper fabric treatments.
Considerations for International Buyers: Buyers should consider the fabric’s durability and maintenance requirements, especially in regions with high humidity. Compliance with fire safety standards, such as those set by the UK’s Furniture and Furnishings (Fire) (Safety) Regulations, is also crucial.
Summary Table of Material Selection for Queen Size Bed Frames
Material | Typical Use Case for queen size bed frame custom | Key Advantage | Key Disadvantage/Limitation | Relative Cost (Low/Med/High) |
---|---|---|---|---|
Solid Wood | High-end residential markets, custom designs | Durability and aesthetic appeal | Expensive and susceptible to warping | High |
Metal | Modern designs, budget-friendly options | Strength and affordability | Prone to rust without treatment | Medium |
Engineered Wood | Cost-effective solutions, mass production | Uniform strength and cost-effective | Less durable and potential VOCs | Low |
Upholstered | Luxury markets, custom aesthetics | Comfort and design versatility | Requires maintenance and less durable | Medium |
This guide aims to equip B2B buyers with actionable insights to make informed decisions when selecting materials for custom queen size bed frames, ensuring compliance and suitability for their specific markets.
In-depth Look: Manufacturing Processes and Quality Assurance for queen size bed frame custom
What Are the Main Stages in the Manufacturing Process of Custom Queen Size Bed Frames?
The manufacturing of custom queen size bed frames involves several critical stages that ensure both functionality and aesthetic appeal. Understanding these stages will help B2B buyers make informed decisions when selecting suppliers.
Material Preparation: What Materials Are Commonly Used?
The first step in the manufacturing process is material preparation. Common materials include hardwoods (such as oak and maple), softwoods (like pine), and engineered wood products (like MDF and plywood). Each material has its own benefits; for example, hardwoods are often preferred for their durability and aesthetic quality, while engineered woods may offer cost advantages.
Suppliers typically source materials from certified vendors to ensure quality. Buyers should inquire about the origin of materials and any certifications, as this can affect the sustainability and compliance of the final product.
How Are Custom Bed Frames Formed?
Once materials are prepared, the next stage is forming. This involves cutting, shaping, and joining materials to create the frame’s components, including the headboard, footboard, side rails, and slats. Techniques such as CNC machining, laser cutting, and traditional joinery are commonly employed.
CNC machining allows for precision cuts and complex designs, which is crucial for custom orders. Buyers should look for suppliers that utilize advanced technology, as this often leads to higher-quality products with fewer defects.
What Does the Assembly Process Entail?
After forming, the assembly process begins. This stage involves joining all the components using methods like doweling, mortise and tenon joints, or metal fasteners. Quality assembly is vital for ensuring the structural integrity of the bed frame.
Buyers should inquire about the assembly techniques used by potential suppliers. Robust assembly methods indicate a commitment to quality and longevity, essential for customer satisfaction.
How Is the Finishing Touch Applied to Bed Frames?
The final stage in manufacturing is finishing, which includes sanding, staining, painting, or varnishing the bed frame. This not only enhances the aesthetic appeal but also protects the wood from wear and tear. The finishing process can include multiple layers, with drying time between each to ensure a smooth, durable surface.
Buyers should ask suppliers about the finishing materials used, particularly regarding VOC emissions and environmental impact. Compliance with international standards can be a significant selling point, especially in regions with strict environmental regulations.
What Quality Assurance Measures Should B2B Buyers Look For?
Quality assurance (QA) is crucial in the manufacturing process, ensuring that the final product meets both international and industry-specific standards. Understanding these measures will help buyers ensure they are sourcing high-quality products.
Which International Standards Are Relevant for Bed Frame Manufacturing?
International standards such as ISO 9001 are essential for ensuring consistent quality across manufacturing processes. ISO 9001 focuses on quality management systems and requires companies to document their processes, ensuring that products meet customer and regulatory requirements.
In addition to ISO, other certifications like CE marking (for European markets) and specific industry standards (e.g., API for certain materials) may also be relevant. B2B buyers should verify that their suppliers possess the necessary certifications to ensure compliance with their local regulations.
What Are the Key QC Checkpoints in the Manufacturing Process?
Quality Control (QC) checkpoints are critical in maintaining product quality throughout the manufacturing process. These typically include:
-
Incoming Quality Control (IQC): This stage involves inspecting raw materials upon arrival to ensure they meet specified standards. Buyers should ask suppliers how they perform IQC and what criteria are used.
-
In-Process Quality Control (IPQC): During manufacturing, regular checks are conducted to ensure that production processes align with quality standards. This may include dimensional checks and visual inspections.
-
Final Quality Control (FQC): Once the product is assembled and finished, a final inspection is performed. This typically involves testing for stability, finish quality, and overall aesthetics.
B2B buyers should inquire about the frequency and methodology of these inspections to gauge the supplier’s commitment to quality.
What Common Testing Methods Are Used to Ensure Quality?
To ensure that custom queen size bed frames meet quality standards, various testing methods may be employed. Common tests include:
- Load Testing: Assessing the frame’s ability to support weight without deformation.
- Stability Testing: Checking the frame’s resistance to tipping or wobbling.
- Finish Testing: Evaluating the durability of paint or varnish under wear and tear conditions.
Buyers can request test reports from suppliers to verify that their products have undergone rigorous quality checks.
How Can B2B Buyers Verify Supplier Quality Control?
Verifying a supplier’s quality control processes is essential for B2B buyers looking to ensure that they receive high-quality products. Here are some actionable steps:
What Steps Can Buyers Take to Conduct Supplier Audits?
Conducting supplier audits is a proactive way to assess a manufacturer’s quality management system. Buyers can either perform audits themselves or hire third-party inspection agencies. During an audit, buyers should evaluate:
- The manufacturing process and equipment used.
- Quality control measures in place.
- Compliance with international standards.
Regular audits help buyers identify any potential issues before they become significant problems.
How Can Buyers Access QC Reports?
Requesting quality control reports from suppliers is another effective way to assess product quality. These reports should detail the QC processes implemented, including results from IQC, IPQC, and FQC. Buyers should look for transparency in reporting and any certifications related to the testing performed.
Why Consider Third-Party Inspection Services?
Third-party inspection services provide an unbiased assessment of a supplier’s quality control practices. These services can conduct thorough inspections at various manufacturing stages, offering buyers peace of mind regarding their purchases.
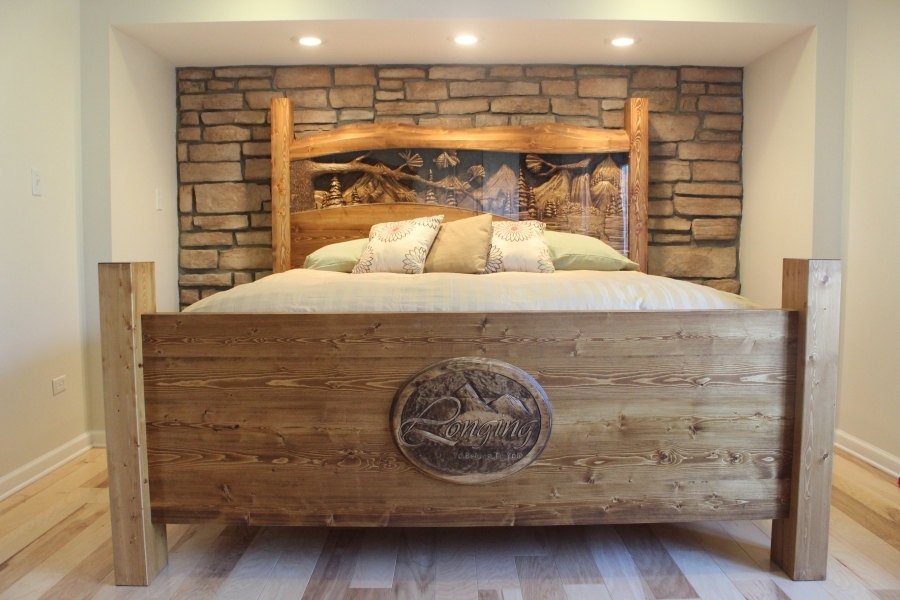
A stock image related to queen size bed frame custom.
Engaging third-party inspectors is particularly beneficial for international buyers who may not be able to visit suppliers in person, ensuring that they receive products that meet their quality expectations.
What Are the Nuances of QC and Certification for International B2B Buyers?
For B2B buyers from Africa, South America, the Middle East, and Europe, understanding the nuances of quality control and certification is critical. Regional regulations can vary significantly, impacting how products must be manufactured and tested.
Buyers should familiarize themselves with local requirements, as well as the certifications that are recognized in their target markets. For example, CE marking is essential for products sold in the European Union, while other regions may have different requirements.
Additionally, buyers should be aware of the implications of sourcing from different countries. Factors such as shipping costs, import duties, and potential delays can all impact the final cost and delivery timelines.
By taking these considerations into account, B2B buyers can navigate the complexities of international sourcing more effectively, ensuring that they partner with reliable suppliers who prioritize quality assurance.
Practical Sourcing Guide: A Step-by-Step Checklist for ‘queen size bed frame custom’
To assist international B2B buyers in sourcing custom queen size bed frames, this practical guide provides a step-by-step checklist. Each step is designed to facilitate informed decision-making, ensuring that buyers secure high-quality products tailored to their specific needs.
Step 1: Define Your Technical Specifications
Understanding the exact requirements for your queen size bed frame is crucial. Define the dimensions, materials (such as wood, metal, or upholstered options), weight capacity, and design style. Consider the target market’s preferences, including cultural factors that may influence design choices, especially in regions like Africa and the Middle East.
Step 2: Conduct Market Research
Research the current market trends for custom queen size bed frames in your target regions. Investigate popular designs, materials, and price points. Utilize online tools, industry reports, and trade publications to gather insights that can inform your purchasing decisions and help you align with customer expectations.
Step 3: Evaluate Potential Suppliers
Before committing to a supplier, it’s essential to conduct a thorough evaluation. Request company profiles, customer testimonials, and references from other businesses in your industry. Look for suppliers who have experience working with international clients and can demonstrate a solid track record of reliability and quality.
- Check for local regulations: Ensure suppliers are compliant with local manufacturing and import regulations, particularly in regions with strict safety standards.
Step 4: Request Samples
Always request product samples before finalizing your order. This step allows you to assess the quality of the materials and craftsmanship firsthand. Pay attention to details such as finish, sturdiness, and overall design fidelity to your specifications.
- Consider shipping logistics: When requesting samples, factor in shipping times and costs, especially if you’re sourcing from overseas suppliers.
Step 5: Negotiate Terms and Conditions
Engage in negotiations to establish clear terms regarding pricing, payment methods, lead times, and minimum order quantities. Make sure to discuss warranties and return policies to protect your investment.
- Be clear about customization options: Ensure the supplier understands your specific custom requirements and can accommodate changes during production.
Step 6: Verify Supplier Certifications
It’s vital to verify that your chosen supplier holds necessary certifications and adheres to international standards. Certifications can indicate a commitment to quality and safety, which is particularly important when dealing with products intended for consumer use.
- Look for ISO certifications: These can provide assurance regarding quality management systems, especially when sourcing from regions with varying manufacturing standards.
Step 7: Plan for Logistics and Distribution
Once you have finalized your order, develop a logistics plan for shipping and distribution. Consider the most cost-effective and reliable shipping methods to your region. Factor in customs duties, taxes, and any potential delays to ensure a smooth delivery process.
- Establish a local distribution network: If you plan to sell in multiple regions, consider setting up partnerships with local distributors to streamline your supply chain.
By following this checklist, B2B buyers can effectively navigate the complexities of sourcing custom queen size bed frames, ensuring they make informed decisions that meet their business needs and customer expectations.
Comprehensive Cost and Pricing Analysis for queen size bed frame custom Sourcing
What are the Key Cost Components in Custom Sourcing of Queen Size Bed Frames?
When sourcing custom queen size bed frames, understanding the cost structure is essential for international B2B buyers. The primary cost components include:
-
Materials: The choice of materials significantly influences the overall cost. Solid wood, metal, and engineered wood have varying price points. Higher-quality materials often lead to increased durability and consumer satisfaction, which can justify a higher price.
-
Labor: Labor costs can vary widely depending on the region of manufacturing. In countries with lower labor costs, such as some South American nations, you may find competitive pricing. However, skilled craftsmanship may come at a premium, particularly in regions known for quality furniture production, like Europe.
-
Manufacturing Overhead: This encompasses costs related to production facilities, utilities, and administrative expenses. Manufacturers with advanced technology may incur higher overhead but can offer better efficiency and lower defect rates.
-
Tooling: Custom designs often require specialized tooling, which can add to upfront costs. Understanding the tooling setup can help buyers gauge the long-term viability of a supplier relationship.
-
Quality Control (QC): Ensuring that the bed frames meet specific standards requires investments in quality control processes. This is particularly crucial for international buyers concerned about compliance with local regulations and certifications.
-
Logistics: Shipping costs vary based on the distance, weight, and shipping methods. International buyers should be aware of potential tariffs and customs duties that can impact total costs.
-
Margin: Finally, suppliers will build in a profit margin, which can vary based on competition and demand for custom products.
How Do Price Influencers Affect the Cost of Queen Size Bed Frames?
Several factors influence the pricing of custom queen size bed frames:
-
Volume/MOQ (Minimum Order Quantity): Larger orders often lead to lower per-unit costs. Negotiating for bulk purchases can be beneficial, especially for businesses planning to resell the products.
-
Specifications and Customization: Unique design elements or specifications can significantly raise the price. Buyers should clearly define their requirements to avoid unexpected costs.
-
Materials and Quality Certifications: Premium materials and certifications (like ISO or FSC) may increase costs but can also enhance the product’s marketability.
-
Supplier Factors: The reputation and reliability of the supplier can influence pricing. Established suppliers with proven track records might charge more, but they often provide better assurance of quality and timely delivery.
-
Incoterms: Understanding the terms of trade (like FOB, CIF) is crucial for international transactions. These terms define who bears the costs and risks at various points in the shipping process, affecting the overall cost structure.
What Buyer Tips Can Help in Negotiating Costs Effectively?
To ensure cost-efficiency in sourcing queen size bed frames, consider the following actionable tips:
-
Negotiate Smartly: Always negotiate based on comprehensive market research. Understand the typical price range for the materials and specifications you are considering.
-
Evaluate Total Cost of Ownership (TCO): Instead of focusing solely on the purchase price, consider the TCO, which includes maintenance, shipping, and potential resale value. This broader view can lead to more informed purchasing decisions.
-
Understand Pricing Nuances for International Transactions: Be aware of fluctuations in currency exchange rates and regional economic conditions that could impact pricing. Contracts should account for these variables to avoid unexpected costs.
-
Build Relationships with Suppliers: Establishing a strong partnership with suppliers can lead to better pricing, priority service, and more favorable terms over time.
What Should You Keep in Mind Regarding Indicative Prices?
While it is essential to understand the cost structure and pricing influences, remember that prices can fluctuate based on market conditions and specific supplier capabilities. Always request detailed quotations and consider conducting a price comparison among multiple suppliers to ensure competitive pricing.
Alternatives Analysis: Comparing queen size bed frame custom With Other Solutions
Exploring Alternatives to Custom Queen Size Bed Frames: What Are the Best Options?
When it comes to selecting bed frames for commercial use, particularly queen size bed frames, buyers often face a variety of options. Custom queen size bed frames offer unique advantages, but there are also alternative solutions that may better suit specific business needs. This section explores viable alternatives, comparing them based on performance, cost, ease of implementation, maintenance, and best use cases.
Comparison Aspect | Queen Size Bed Frame Custom | Alternative 1: Ready-Made Queen Bed Frames | Alternative 2: Adjustable Bed Bases |
---|---|---|---|
Performance | High durability, tailored design | Standard durability, design varies | Offers personalized comfort, adjustable positions |
Cost | Higher investment for customization | Generally lower cost, no customization | Mid-range pricing, additional features increase cost |
Ease of Implementation | Requires time for design and manufacturing | Immediate availability, easy setup | Moderate complexity, requires assembly |
Maintenance | Dependent on materials; may need periodic upkeep | Minimal maintenance, standard materials | Moderate maintenance, mechanical parts may require servicing |
Best Use Case | Luxury hotels, boutique accommodations | Budget hotels, hostels, short-term rentals | Elderly care facilities, home health services |
What Are the Advantages and Disadvantages of Ready-Made Queen Bed Frames?
Ready-made queen bed frames are a popular alternative due to their immediate availability and cost-effectiveness. These frames typically come in standardized designs and materials, which can reduce upfront costs. However, they may not meet specific aesthetic or functional needs for high-end establishments. While maintenance is generally low, the durability may not match that of custom solutions, making them less suitable for luxury markets.
How Do Adjustable Bed Bases Compare to Custom Queen Bed Frames?
Adjustable bed bases present a unique alternative that caters to user comfort through customizable positions. These bases can be particularly beneficial in healthcare settings, where patients may require specific positions for optimal comfort. However, the complexity of assembly and potential mechanical issues can be a drawback. Additionally, the cost is usually higher than ready-made frames but can be justified by the added comfort and health benefits they provide.
Conclusion: How Can B2B Buyers Choose the Right Bed Frame Solution?
Choosing the right bed frame solution depends on several factors, including budget, target market, and specific operational needs. For luxury hotels and boutique accommodations, custom queen size bed frames may offer the best balance of durability and aesthetic appeal. Conversely, budget hotels and hostels might find ready-made options more feasible. Adjustable bed bases cater to specialized markets, such as healthcare, where comfort and adaptability are paramount. By assessing these alternatives, B2B buyers can make informed decisions that align with their strategic goals and customer expectations.
Essential Technical Properties and Trade Terminology for queen size bed frame custom
What Are the Key Technical Properties of a Custom Queen Size Bed Frame?
When sourcing a custom queen size bed frame, understanding essential technical properties is crucial for ensuring product quality and suitability for market needs. Here are several critical specifications to consider:
1. Material Grade
The choice of material directly influences durability, aesthetics, and cost. Common materials for bed frames include solid wood, metal, and engineered wood. Solid wood offers longevity and a premium feel, while metal frames are often more affordable and lightweight. Understanding the grade of the material can help buyers assess quality and suitability for their target market.
2. Weight Capacity
This specification determines how much weight the bed frame can support safely. A standard queen size bed frame should accommodate at least 500-600 pounds, which includes the mattress and occupants. Buyers should inquire about the weight capacity to ensure it meets consumer expectations and safety standards in their region.
3. Dimensions and Tolerance
Custom bed frames should fit standard mattress dimensions, which for queen size is typically 60 inches wide by 80 inches long. Tolerances refer to the acceptable variations in measurements. For example, a tolerance of ±1/8 inch is often acceptable for fitting. Accurate dimensions and tolerances are vital for ensuring compatibility with mattresses and bedding accessories.
4. Finish and Coating
The finish on a bed frame can affect its appearance, maintenance, and durability. Common finishes include varnish, paint, or powder coating. Each type has its characteristics; for instance, powder coating offers excellent resistance to scratches and rust, making it suitable for humid climates. Understanding the finish can help buyers select frames that align with market preferences and environmental conditions.
5. Assembly Requirements
Buyers should consider how easily a bed frame can be assembled. Some frames come with pre-drilled holes and clear instructions, while others may require advanced tools or skills. Knowing the assembly requirements can aid in logistics and customer satisfaction, especially in regions where assembly services may not be readily available.
What Common Trade Terms Should International Buyers Know?
Navigating the world of B2B transactions can be complex, especially when dealing with international suppliers. Familiarity with industry terminology can facilitate smoother negotiations and purchasing processes.
1. OEM (Original Equipment Manufacturer)
An OEM refers to a company that produces parts or products that are used in another company’s final product. In the context of custom bed frames, an OEM might manufacture the frame while another company brands and sells it. Understanding OEM relationships can help buyers identify potential suppliers and negotiate better terms.
2. MOQ (Minimum Order Quantity)
MOQ is the smallest number of units that a supplier is willing to sell. This term is critical for B2B buyers, especially those looking to enter new markets, as it can affect initial investment and inventory management. Knowing the MOQ allows buyers to plan their orders according to their budget and market demand.
3. RFQ (Request for Quotation)
An RFQ is a formal process where buyers request pricing information from suppliers for specific products or services. For custom queen size bed frames, submitting an RFQ can help buyers gather competitive pricing and assess potential suppliers’ capabilities and responsiveness.
4. Incoterms
Incoterms (International Commercial Terms) define the responsibilities of buyers and sellers in international trade. They outline who is responsible for shipping, insurance, and tariffs. For instance, “CIF” (Cost, Insurance, Freight) means the seller covers these costs until the goods reach the buyer’s port. Understanding Incoterms is essential for managing risks and costs in international transactions.
5. Lead Time
Lead time refers to the time taken from placing an order to delivery. It is a critical factor for inventory management and customer fulfillment. Buyers should clarify lead times with suppliers to ensure they align with their sales strategies and market demands.
By understanding these technical properties and trade terms, international B2B buyers can make informed decisions when sourcing custom queen size bed frames, ultimately enhancing their competitiveness in the market.
Navigating Market Dynamics and Sourcing Trends in the queen size bed frame custom Sector
What Are the Current Market Dynamics and Key Trends in the Queen Size Bed Frame Custom Sector?
The global market for custom queen size bed frames is experiencing significant growth, driven by several key factors. Firstly, there is an increasing demand for personalized furniture solutions that cater to individual preferences in aesthetics and functionality. This trend is particularly pronounced in emerging markets in Africa and South America, where consumers are looking for unique designs that reflect cultural influences. Furthermore, technological advancements in manufacturing, such as CNC machining and 3D printing, are enabling manufacturers to produce customized bed frames efficiently, thus reducing lead times.
International B2B buyers should also note the rising significance of e-commerce platforms that facilitate direct sourcing from manufacturers. In regions like the Middle East and Europe, platforms that offer virtual showrooms and augmented reality tools are transforming how buyers assess product suitability. Additionally, the integration of AI and data analytics in supply chain management is optimizing inventory levels and improving demand forecasting, allowing buyers to make informed purchasing decisions.
How Important Is Sustainability and Ethical Sourcing in the Queen Size Bed Frame Custom Sector?
Sustainability is becoming a central focus for B2B buyers in the queen size bed frame custom sector, particularly in response to increasing consumer awareness about environmental issues. The furniture industry is notorious for its impact on deforestation and waste generation. Thus, sourcing from manufacturers that prioritize sustainable practices is essential. Look for suppliers who use reclaimed wood, eco-friendly finishes, and other sustainable materials.
Moreover, ethical sourcing is critical as it reflects a commitment to social responsibility. Buyers should seek out suppliers who adhere to fair labor practices and demonstrate transparency in their supply chains. Certifications such as Forest Stewardship Council (FSC) and Global Organic Textile Standard (GOTS) can serve as indicators of a supplier’s commitment to sustainability. Incorporating these elements into sourcing strategies not only enhances brand reputation but also appeals to an increasingly conscientious consumer base.
How Has the Queen Size Bed Frame Custom Market Evolved Over Time?
The evolution of the queen size bed frame custom market can be traced back to the shift from mass-produced furniture to more personalized solutions. In the early 2000s, the furniture industry began to recognize the limitations of conventional retail, leading to the introduction of custom designs that cater to individual preferences. This shift was further accelerated by the rise of online marketplaces, which democratized access to custom furniture options for consumers globally.
In recent years, as sustainability and ethical sourcing gained traction, manufacturers have adapted their practices to meet these demands. The incorporation of advanced manufacturing technologies has also played a vital role in this evolution, allowing for more complex designs and shorter production times. Consequently, the market has become more competitive, with international B2B buyers now having access to a wider range of options than ever before. This continuous evolution underscores the importance of staying abreast of trends to make informed sourcing decisions.
Frequently Asked Questions (FAQs) for B2B Buyers of queen size bed frame custom
-
How can I ensure the quality of a custom queen size bed frame before purchasing?
To ensure quality, start by researching potential suppliers thoroughly. Request samples or photos of previous work to assess craftsmanship. Look for certifications that indicate adherence to international quality standards. Conduct factory visits if feasible, or use third-party inspection services to verify materials and processes. Additionally, read reviews or ask for references from other businesses that have sourced custom bed frames from the supplier. -
What customization options are available for queen size bed frames?
Customization options for queen size bed frames can vary significantly by supplier. Common options include selecting materials (wood, metal, upholstered), finishes (stains, paints, fabrics), sizes, and additional features like storage drawers or adjustable bases. Some suppliers may also offer bespoke designs tailored to specific aesthetic preferences. It’s advisable to communicate your requirements clearly during initial discussions to explore all available options. -
What is the minimum order quantity (MOQ) for custom queen size bed frames?
MOQs for custom queen size bed frames can vary widely depending on the supplier and the complexity of the customization. Many manufacturers set a MOQ ranging from 50 to 200 units to cover production costs effectively. However, some suppliers may accommodate smaller orders, especially for first-time buyers or startups. Always confirm MOQs in advance to avoid surprises and factor this into your purchasing strategy. -
What payment terms should I expect when ordering custom queen size bed frames?
Payment terms can vary by supplier, but typical arrangements include a deposit (usually 30-50%) at the time of order, with the balance due prior to shipment. Some suppliers may offer flexible terms depending on your business relationship or order size. It’s essential to clarify payment methods accepted, such as bank transfers or letters of credit, and ensure that you have a clear understanding of any potential fees associated with international transactions. -
How can I vet potential suppliers for custom queen size bed frames?
Vetting suppliers requires a multi-faceted approach. Start by checking their business registration and industry certifications. Evaluate their portfolio for previous work that aligns with your needs. Engage in direct communication to assess responsiveness and professionalism. Consider using platforms that provide ratings and reviews, or consult industry networks for recommendations. Finally, request references from other B2B buyers to gain insights into their reliability and service quality. -
What logistics considerations should I keep in mind when importing custom queen size bed frames?
Logistics for importing custom bed frames involve several key considerations. First, determine shipping options and associated costs, including freight forwarders and customs brokerage services. Understand the import regulations and tariffs specific to your country to avoid unexpected charges. It’s also important to plan for lead times, factoring in production and shipping durations to ensure timely delivery. Lastly, consider warehousing options if you need to store inventory upon arrival. -
What are the common challenges in sourcing custom queen size bed frames internationally?
Common challenges include language barriers, cultural differences in business practices, and varying quality standards. Additionally, navigating international shipping regulations can be complex. Time zone differences may lead to delays in communication, impacting order timelines. Establishing clear contracts and maintaining open lines of communication with suppliers can help mitigate these challenges, ensuring a smoother sourcing process.
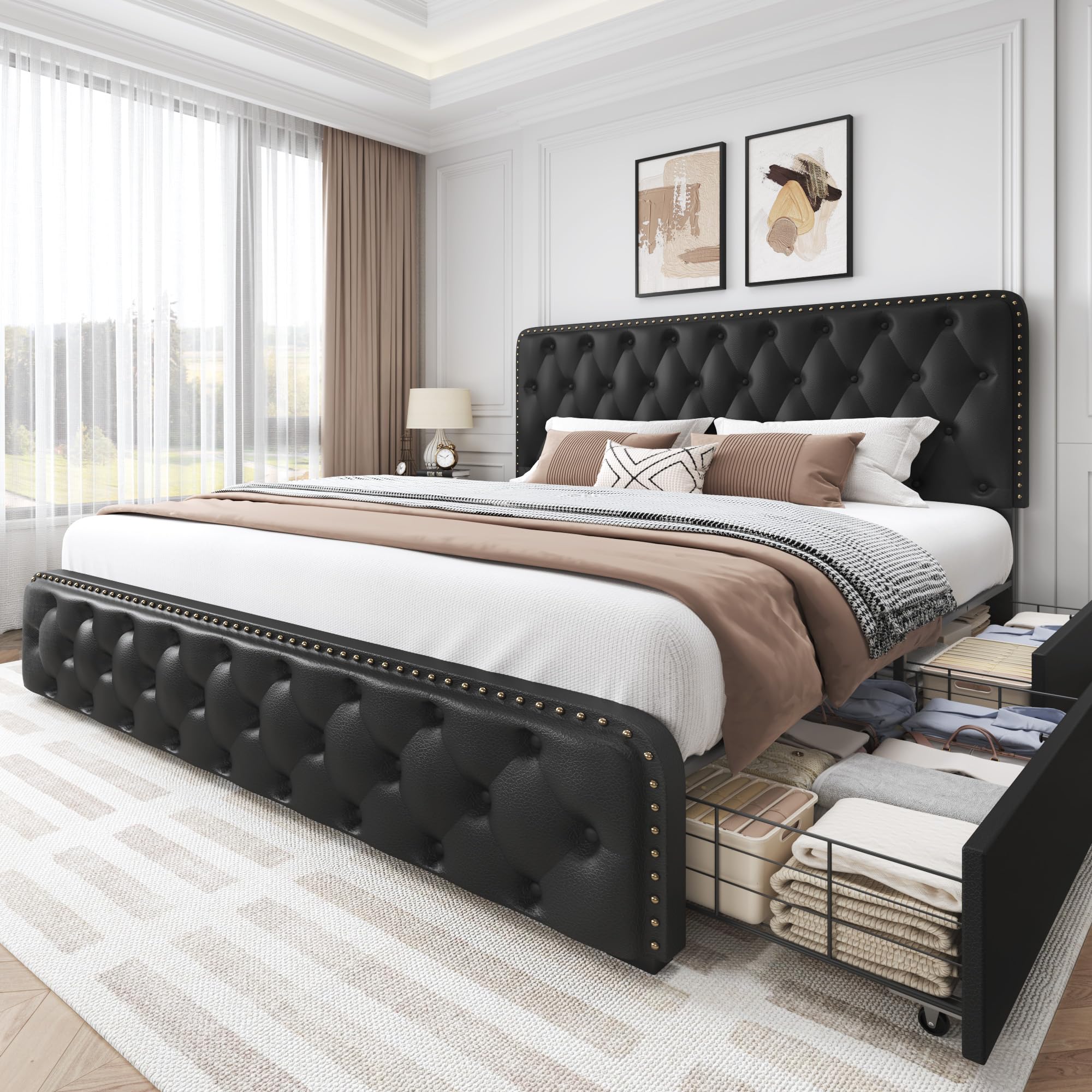
A stock image related to queen size bed frame custom.
- How can I ensure effective communication with international suppliers when ordering custom queen size bed frames?
Effective communication starts with clarity and detail. Use straightforward language and avoid jargon that may not translate well. Utilize visual aids, such as sketches or photographs, to convey your design ideas. Establish regular check-ins through video calls or emails to address any questions or concerns. Finally, be patient and open to feedback, as cultural differences may affect communication styles and expectations.
Important Disclaimer & Terms of Use
⚠️ Important Disclaimer
The information provided in this guide, including content regarding manufacturers, technical specifications, and market analysis, is for informational and educational purposes only. It does not constitute professional procurement advice, financial advice, or legal advice.
While we have made every effort to ensure the accuracy and timeliness of the information, we are not responsible for any errors, omissions, or outdated information. Market conditions, company details, and technical standards are subject to change.
B2B buyers must conduct their own independent and thorough due diligence before making any purchasing decisions. This includes contacting suppliers directly, verifying certifications, requesting samples, and seeking professional consultation. The risk of relying on any information in this guide is borne solely by the reader.
Strategic Sourcing Conclusion and Outlook for queen size bed frame custom
In summary, strategic sourcing for custom queen size bed frames offers international B2B buyers an opportunity to enhance their product offerings while optimizing costs and quality. By focusing on supplier relationships, understanding regional market dynamics, and leveraging technology, buyers from Africa, South America, the Middle East, and Europe can make informed purchasing decisions that drive their business success.
What are the key benefits of strategic sourcing in the custom furniture market? First, it allows for better negotiation power, ensuring that businesses secure favorable terms and pricing. Additionally, collaborating with reliable manufacturers can lead to improved product quality and consistency, meeting the diverse needs of consumers across various regions.
Looking ahead, the demand for custom furniture will continue to grow, fueled by evolving consumer preferences and the rise of e-commerce. International B2B buyers should actively seek partnerships with innovative suppliers who can provide unique designs and sustainable materials. By embracing these strategies, businesses can position themselves for long-term success in the competitive custom furniture landscape.
Take the next step in your sourcing journey: evaluate your current suppliers, explore new markets, and invest in technology that streamlines your procurement processes. The future of your business depends on the strategic decisions you make today.