Discover Cost-Effective Solid Wood Furniture Suppliers (2025)
Introduction: Navigating the Global Market for solid wood furniture supplier
Navigating the global market for solid wood furniture suppliers can be a daunting task, especially for international B2B buyers who must balance quality, cost, and sustainability. As businesses increasingly seek to source high-quality, durable products like solid wood furniture for various applications—from office environments in South Africa to hospitality projects in Saudi Arabia—understanding the intricacies of supplier selection becomes essential. This guide aims to demystify the complexities of sourcing solid wood furniture by providing a comprehensive overview of the types of furniture available, their applications, and essential criteria for vetting suppliers.
Throughout this resource, you will discover actionable insights into the best practices for evaluating potential suppliers, understanding cost factors, and ensuring compliance with international quality standards. With a focus on empowering B2B buyers from diverse regions, including Africa, South America, the Middle East, and Europe, this guide is designed to facilitate informed purchasing decisions. Whether you are looking for sustainable sourcing options or navigating logistics challenges, our expertise will equip you with the knowledge to make strategic choices that align with your business goals.
By addressing common challenges and offering practical solutions, this guide serves as a valuable tool for international B2B buyers aiming to enhance their procurement processes and ultimately achieve greater success in the competitive landscape of solid wood furniture.
Understanding solid wood furniture supplier Types and Variations
Type Name | Key Distinguishing Features | Primary B2B Applications | Brief Pros & Cons for Buyers |
---|---|---|---|
Custom Solid Wood Furniture | Tailored designs based on client specifications | High-end retail, bespoke projects | Pros: Unique designs, personalized service. Cons: Higher costs, longer lead times. |
Mass-Produced Solid Wood Furniture | Standardized designs, often sourced from large manufacturers | Retail chains, e-commerce platforms | Pros: Cost-effective, quicker delivery. Cons: Limited customization, less uniqueness. |
Sustainable Solid Wood Suppliers | Focus on eco-friendly practices and materials | Green retailers, eco-conscious markets | Pros: Appeals to environmentally aware consumers. Cons: May have higher prices. |
Specialty Artisan Suppliers | Crafted by skilled artisans, often using traditional methods | Luxury markets, custom orders | Pros: High craftsmanship, unique pieces. Cons: Higher price point, limited availability. |
Regional Solid Wood Suppliers | Local suppliers offering region-specific wood types | Local businesses, regional markets | Pros: Supports local economies, shorter shipping times. Cons: Limited variety compared to larger suppliers. |
What Are the Characteristics of Custom Solid Wood Furniture Suppliers?
Custom solid wood furniture suppliers focus on creating unique pieces tailored to specific client needs. They often collaborate closely with designers and architects to ensure the final product aligns with the intended aesthetic and functional requirements. These suppliers are particularly suitable for high-end retail environments or bespoke projects where distinctiveness is paramount. Buyers should consider the potential for higher costs and longer lead times but can expect exceptional quality and personalization.
How Do Mass-Produced Solid Wood Furniture Suppliers Operate?
Mass-produced solid wood furniture suppliers manufacture standardized designs in large quantities. This approach allows them to offer competitive pricing and faster delivery times, making them ideal for retail chains and e-commerce platforms. While buyers benefit from lower costs, they may find the lack of customization and uniqueness a drawback. Companies looking to stock their stores with popular, cost-effective options often favor these suppliers.
What Makes Sustainable Solid Wood Suppliers Unique?
Sustainable solid wood suppliers prioritize eco-friendly practices, sourcing materials from responsibly managed forests. These suppliers appeal to businesses targeting environmentally conscious consumers, such as green retailers. While the products may come at a premium, the long-term benefits of brand loyalty and alignment with consumer values often outweigh the costs. Buyers should evaluate the sustainability credentials of these suppliers to ensure they meet their ethical standards.
Why Choose Specialty Artisan Suppliers for Solid Wood Furniture?
Specialty artisan suppliers produce furniture using traditional craftsmanship techniques, resulting in high-quality, unique pieces. These suppliers cater to luxury markets and custom orders, where the emphasis is on exceptional craftsmanship and artistry. Buyers should be prepared for higher price points and limited availability, but the investment often pays off in terms of quality and uniqueness that can enhance brand prestige.
What Are the Advantages of Working with Regional Solid Wood Suppliers?
Regional solid wood suppliers specialize in locally sourced wood types, supporting local economies and reducing shipping times. They are well-suited for local businesses that want to offer products with regional significance. While the variety may be less than that offered by larger suppliers, buyers benefit from a more personalized service and the ability to showcase local craftsmanship. This approach can also resonate well with consumers who value local sourcing and community support.
Related Video: Which Wood Type Should I Choose for my Furniture? (Wood Types Compared)
Key Industrial Applications of solid wood furniture supplier
Industry/Sector | Specific Application of solid wood furniture supplier | Value/Benefit for the Business | Key Sourcing Considerations for this Application |
---|---|---|---|
Hospitality | Custom furniture for hotels and restaurants | Enhances guest experience and brand image | Quality of wood, durability, design flexibility |
Office Furniture | Executive desks, conference tables | Improves workplace aesthetics and employee morale | Ergonomics, customization options, lead times |
Retail | Display units and shelving for boutiques | Increases product visibility and sales potential | Style alignment with brand, material sustainability |
Education | Desks and seating for schools and universities | Supports learning environments and student comfort | Compliance with safety standards, durability |
Residential | Custom furniture for homes | Adds value and personalization to living spaces | Design trends, finish options, delivery logistics |
How is Solid Wood Furniture Used in the Hospitality Sector?
In the hospitality industry, solid wood furniture suppliers provide custom pieces for hotels and restaurants, including tables, chairs, and decorative elements. These furnishings not only enhance the aesthetic appeal of the establishments but also contribute to a memorable guest experience. For international buyers from regions like Africa and the Middle East, it is crucial to consider the durability of the wood due to varying climate conditions and the need for maintenance. Additionally, suppliers should offer designs that reflect local culture and trends to resonate with the target audience.
What Role Does Solid Wood Furniture Play in Office Environments?
In office settings, solid wood furniture suppliers deliver executive desks, conference tables, and collaborative workstations. Such furniture is designed to improve both functionality and aesthetics, fostering a positive work environment that can boost employee morale and productivity. International buyers, especially from Europe and South America, should prioritize ergonomic designs that comply with health regulations. Furthermore, customization options can help align the furniture with the company’s branding and office layout.
How Can Retail Businesses Benefit from Solid Wood Furniture?
Retail establishments leverage solid wood furniture suppliers for display units and shelving that enhance product visibility and customer engagement. High-quality wooden fixtures can create an inviting atmosphere that encourages shopping and increases sales potential. For B2B buyers in Africa and Europe, it is essential to source furniture that aligns with the store’s branding while considering sustainability practices, as consumers increasingly prefer eco-friendly products. Suppliers should also provide options that accommodate various retail layouts and merchandise types.
Why is Solid Wood Furniture Important in Educational Institutions?
Educational institutions require solid wood furniture for desks, chairs, and collaborative spaces to foster a conducive learning environment. Suppliers can address the specific needs of schools and universities by offering durable, easily maintainable furniture that meets safety standards. International buyers from the Middle East and South America should look for suppliers who can provide designs that cater to diverse student populations, ensuring comfort and usability across different age groups.
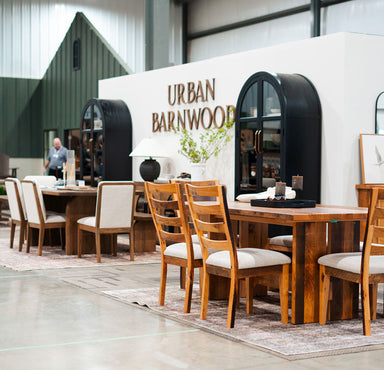
A stock image related to solid wood furniture supplier.
How Does Solid Wood Furniture Enhance Residential Spaces?
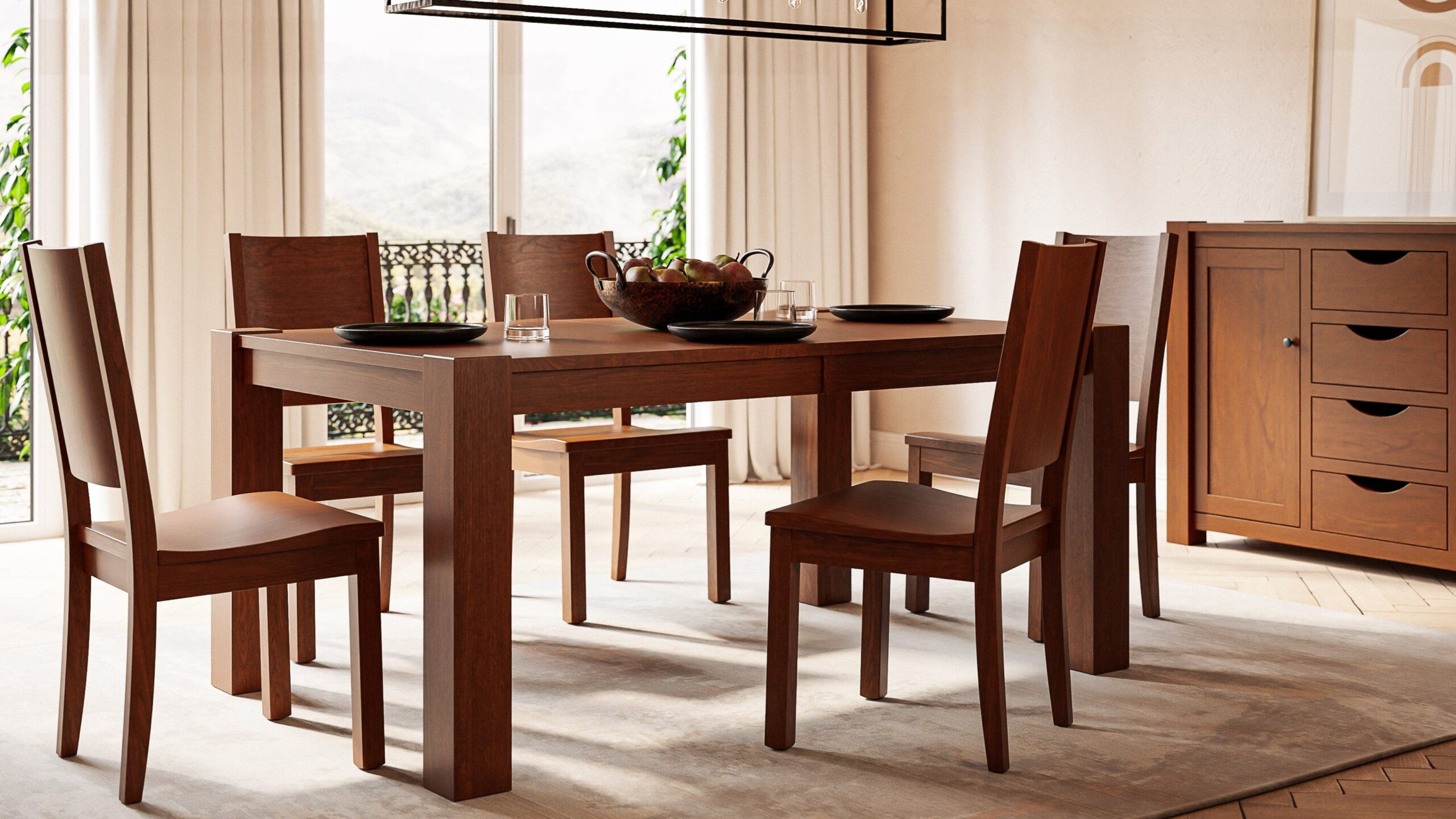
A stock image related to solid wood furniture supplier.
In the residential sector, solid wood furniture suppliers create custom pieces that add both value and personalization to homes. From bespoke dining tables to handcrafted cabinets, these furnishings can significantly enhance the living experience. Buyers from Africa and Europe should focus on suppliers who offer a variety of design styles and finishes to suit different preferences. Additionally, considerations around delivery logistics and installation services are essential to ensure a smooth purchasing experience.
Related Video: High-end Wooden Furniture Manufacturing Process || Extremely Large Woodworking Skill of Carpenter
3 Common User Pain Points for ‘solid wood furniture supplier’ & Their Solutions
Scenario 1: Sourcing Quality Solid Wood Furniture on a Budget
The Problem: B2B buyers often face the challenge of balancing quality and cost when sourcing solid wood furniture. This is particularly acute for businesses in regions like Africa and South America, where the availability of high-quality materials may be limited, leading to concerns about durability and long-term investment. Buyers worry about selecting suppliers who may cut corners to offer lower prices, which can result in poor-quality furniture that does not meet their expectations.
The Solution: To overcome this challenge, B2B buyers should conduct thorough market research before making a purchase. Start by identifying reputable solid wood furniture suppliers with proven track records in your region or internationally. Utilize online platforms like industry-specific trade shows and directories to find suppliers who specialize in sustainable sourcing and craftsmanship. Request samples or visit their manufacturing facilities, if possible, to assess the quality of their products firsthand. Additionally, negotiating bulk purchase discounts or exploring financing options can help stretch your budget while ensuring you invest in quality furniture that will last.
Scenario 2: Navigating Long Lead Times and Delays in Delivery
The Problem: Another common pain point for B2B buyers is the long lead times associated with solid wood furniture orders. Buyers in the Middle East and Europe, for example, may find that suppliers have extended production schedules due to high demand or limited resources. This can disrupt project timelines, especially if businesses are relying on timely delivery for new office spaces or retail environments.
The Solution: To mitigate the risk of delays, it is crucial for B2B buyers to establish clear communication channels with their suppliers. Before placing an order, discuss and agree upon delivery timelines, including potential bottlenecks in production. Implementing a just-in-time inventory system can also help, allowing businesses to order furniture in phases rather than all at once. Consider suppliers that offer flexible shipping options and track delivery progress to proactively address any potential delays. Building a strong relationship with your supplier can also lead to more reliable service and quicker resolution of issues.
Scenario 3: Understanding Maintenance and Care for Solid Wood Furniture
The Problem: Once B2B buyers invest in solid wood furniture, they often struggle with the maintenance and care required to preserve its quality and appearance. This is particularly pertinent for businesses in humid climates, where wood can warp or degrade if not properly maintained. Buyers may lack the knowledge or resources to implement effective care routines, leading to dissatisfaction with their investment.
The Solution: To address this issue, suppliers should provide comprehensive maintenance guidelines alongside their products. B2B buyers should inquire about the best practices for caring for solid wood furniture, including recommended cleaning products and techniques. It is beneficial to establish a regular maintenance schedule, incorporating dusting, polishing, and conditioning the wood to prevent damage. Additionally, consider investing in protective measures like coasters and tablecloths to minimize wear and tear. Training staff on proper care techniques can also ensure that the furniture remains in excellent condition, maximizing its lifespan and enhancing the overall aesthetic of your space.
Strategic Material Selection Guide for solid wood furniture supplier
What Are the Key Properties of Common Materials Used in Solid Wood Furniture?
When selecting materials for solid wood furniture, international B2B buyers must consider various wood types, each with unique properties and applications. Here, we analyze three common materials: Oak, Teak, and Pine, focusing on their properties, advantages, disadvantages, and specific considerations for buyers from Africa, South America, the Middle East, and Europe.
How Does Oak Perform in Solid Wood Furniture?
Key Properties: Oak is known for its strength and durability, with a high resistance to wear and tear. It has a temperature rating that makes it suitable for various climates, and its natural grain patterns add aesthetic value.
Pros & Cons: The primary advantage of oak is its longevity and ability to withstand heavy use, making it ideal for furniture that sees frequent use, such as dining tables and chairs. However, oak can be relatively expensive compared to other woods, and its weight may complicate manufacturing and shipping processes.
Impact on Application: Oak is compatible with various finishes and stains, allowing for customization. Its robust nature makes it suitable for both indoor and outdoor furniture, although outdoor applications require proper sealing to prevent moisture damage.
Considerations for International Buyers: Buyers should be aware of compliance with international standards, such as ASTM and DIN, particularly regarding moisture content and treatment for pests. In regions like South Africa and Saudi Arabia, local preferences for oak can influence supply chain decisions.
What Are the Benefits of Using Teak in Furniture Production?
Key Properties: Teak is highly regarded for its natural oils, which provide excellent resistance to water, decay, and insects. It performs well in humid conditions, making it a preferred choice for outdoor furniture.
Pros & Cons: The key advantage of teak is its durability and low maintenance requirements, making it suitable for long-lasting outdoor applications. However, teak is one of the more expensive wood options, which can impact overall project budgets.
Impact on Application: Teak’s resistance to moisture makes it ideal for garden furniture and marine applications. Its rich color and grain also enhance aesthetic appeal, making it popular for high-end furniture.
Considerations for International Buyers: Buyers should consider sourcing teak from sustainable forests to comply with environmental regulations and certifications. Awareness of local regulations regarding imported wood can also affect procurement strategies in regions like Europe and South America.
Why Choose Pine for Solid Wood Furniture?
Key Properties: Pine is a softwood that is lightweight and easy to work with. It has a lower density than hardwoods, which makes it less durable but allows for easier manipulation during manufacturing.
Pros & Cons: The main advantage of pine is its cost-effectiveness, making it a popular choice for budget-conscious projects. However, its softness means it is more susceptible to dents and scratches, limiting its use in high-traffic areas.
Impact on Application: Pine is often used for children’s furniture and decorative pieces where a rustic appearance is desired. Its ability to take paint and stain well allows for versatile design options.
Considerations for International Buyers: Buyers should ensure that the pine sourced complies with local safety standards, especially concerning chemical treatments. In regions like Africa and the Middle East, preferences may lean towards sustainably sourced pine to align with environmental goals.
Summary Table of Material Selection for Solid Wood Furniture
Material | Typical Use Case for solid wood furniture supplier | Key Advantage | Key Disadvantage/Limitation | Relative Cost (Low/Med/High) |
---|---|---|---|---|
Oak | Dining tables and chairs | Longevity and durability | Higher cost and weight | High |
Teak | Outdoor and marine furniture | Water resistance and low maintenance | Expensive | High |
Pine | Children’s furniture and decorative items | Cost-effective and easy to work with | Susceptible to dents and scratches | Low |
This strategic material selection guide provides valuable insights for international B2B buyers, helping them make informed decisions based on the properties, advantages, and limitations of various wood types. Understanding these factors is crucial for ensuring product quality and compliance with regional standards.
In-depth Look: Manufacturing Processes and Quality Assurance for solid wood furniture supplier
What Are the Key Stages in Manufacturing Solid Wood Furniture?
Manufacturing solid wood furniture involves a series of meticulous stages, each critical to ensuring the final product meets quality standards. The primary stages include material preparation, forming, assembly, and finishing.
-
Material Preparation: This initial stage involves selecting high-quality wood species, such as oak, walnut, or mahogany. The wood is then dried to an appropriate moisture level to prevent warping and cracking. Proper storage and handling are essential to maintain the integrity of the wood, often utilizing climate-controlled environments.
-
Forming: In this phase, the dried wood is cut and shaped using various tools and machinery. Techniques such as CNC (Computer Numerical Control) machining allow for precision in cutting and shaping, ensuring that all components fit together seamlessly. Handcrafting techniques may also be employed for intricate designs, allowing artisans to add unique touches to the furniture.
-
Assembly: Once the individual components are shaped, they are assembled. This process may involve joining techniques like mortise and tenon or dowel joints, which are known for their strength and durability. Attention to detail during assembly is crucial, as it affects the overall sturdiness of the furniture.
-
Finishing: The final stage involves sanding, staining, and applying protective coatings. This not only enhances the aesthetic appeal but also protects the wood from moisture, stains, and scratches. Finishing techniques vary widely, from natural oils to synthetic varnishes, depending on the desired look and durability.
How Is Quality Assurance Implemented in Solid Wood Furniture Manufacturing?
Quality assurance (QA) is vital in the production of solid wood furniture to ensure that each piece meets international standards and customer expectations. Several key components are involved in the QA process.
What International Standards Should B2B Buyers Look For?
International standards such as ISO 9001 are essential benchmarks for quality management systems. This certification indicates that a manufacturer adheres to consistent quality control practices. Additionally, industry-specific standards, such as CE marking in Europe and American National Standards Institute (ANSI) standards in the U.S., ensure compliance with safety and quality requirements.
What Are the Quality Control Checkpoints in the Manufacturing Process?
Quality control is implemented at various checkpoints throughout the manufacturing process:
-
Incoming Quality Control (IQC): This initial checkpoint assesses the quality of raw materials before production. Suppliers should provide documentation proving the wood’s origin and quality.
-
In-Process Quality Control (IPQC): During the manufacturing stages, regular inspections are conducted to ensure compliance with design specifications. This includes checking dimensions, joint integrity, and finish quality.
-
Final Quality Control (FQC): Before shipping, a thorough inspection of the finished product is performed. This includes checking for defects, ensuring the finish is uniform, and verifying that all components are functioning as intended.
Which Testing Methods Are Commonly Used in Quality Assurance?
B2B buyers should be aware of common testing methods used to validate product quality:
-
Visual Inspections: Simple yet effective, these inspections help identify surface defects, color inconsistencies, or finish issues.
-
Mechanical Testing: This includes stress tests to evaluate the durability of joints and materials, ensuring that the furniture can withstand typical usage.
-
Environmental Testing: Furniture may be subjected to humidity and temperature variations to assess how well it adapts to different environments, crucial for international buyers in varied climates.
How Can B2B Buyers Verify Supplier Quality Control?
International B2B buyers must take proactive steps to ensure their suppliers maintain high quality standards. Here are actionable strategies:
-
Supplier Audits: Conducting regular audits of potential suppliers allows buyers to assess their manufacturing processes and quality control measures firsthand. This can include reviewing their quality management systems and compliance with international standards.
-
Requesting Quality Reports: Buyers should request detailed quality control reports that outline the results of inspections and tests conducted throughout the manufacturing process. This documentation provides transparency and builds trust.
-
Third-Party Inspections: Engaging third-party inspection agencies can provide an unbiased assessment of the supplier’s quality control practices. These agencies can conduct inspections at various production stages and provide comprehensive reports.
What Are the Nuances of Quality Control for International B2B Buyers?
International buyers, particularly from regions like Africa, South America, the Middle East, and Europe, face unique challenges in ensuring quality control:
-
Cultural Differences: Understanding local manufacturing practices and quality expectations is crucial. Buyers should engage in open communication with suppliers to align on quality standards.
-
Regulatory Compliance: Different regions may have specific regulations concerning furniture production. Buyers should familiarize themselves with these requirements to ensure compliance and avoid costly penalties.
-
Logistical Considerations: International shipping can affect product quality, so ensuring that packaging and transportation methods are optimized for protection during transit is vital.
By focusing on these manufacturing processes and quality assurance measures, B2B buyers can confidently source solid wood furniture that meets their needs and expectations. Engaging with suppliers who prioritize quality at every stage of production will ultimately lead to successful partnerships and customer satisfaction.
Practical Sourcing Guide: A Step-by-Step Checklist for ‘solid wood furniture supplier’
In today’s global market, sourcing solid wood furniture requires a strategic approach. Whether you’re an international buyer from Africa, South America, the Middle East, or Europe, understanding the nuances of selecting the right supplier is crucial. This guide provides a step-by-step checklist to streamline your sourcing process and ensure you make informed decisions.
Step 1: Identify Your Requirements Clearly
Before you begin your search for suppliers, it’s essential to define your specific needs. This includes the type of solid wood furniture, styles, dimensions, and any customizations you require.
- Considerations: What wood types are you interested in (e.g., oak, teak, mahogany)? Do you have specific design aesthetics in mind?
- Importance: Clear requirements help suppliers provide accurate quotes and reduce the likelihood of misunderstandings later.
Step 2: Research Potential Suppliers Thoroughly
Begin your search by researching potential suppliers online. Utilize platforms like Alibaba, Global Sources, or industry-specific directories to find reputable manufacturers.
- Check Reviews: Look for reviews and ratings from previous clients to gauge reliability and product quality.
- Industry Associations: Verify if the supplier is part of recognized industry associations, which often indicates adherence to certain standards.
Step 3: Evaluate Supplier Certifications and Compliance
It’s crucial to ensure that your chosen suppliers meet relevant industry standards and regulations.
- Certifications to Look For: ISO 9001 (quality management), FSC (sustainable forestry), or any local certifications that apply to your region.
- Why It Matters: Certifications serve as proof of a supplier’s commitment to quality and sustainability, which is increasingly important in today’s market.
Step 4: Request Samples Before Committing
Before finalizing your order, always request samples of the furniture you intend to purchase.
- What to Assess: Pay attention to craftsmanship, wood quality, and finish. Ensure the sample aligns with your expectations.
- Importance of Samples: This step is vital for verifying the supplier’s claims about quality and can prevent costly mistakes in bulk orders.
Step 5: Discuss Payment Terms and Conditions
Understanding the payment structure is essential to avoid any financial disputes later on.
- Common Terms: Discuss upfront payments, payment milestones, and acceptable payment methods (e.g., letters of credit, PayPal).
- Why It’s Important: Clear payment terms protect both parties and ensure a smoother transaction process.
Step 6: Evaluate Shipping and Logistics Options
Consider how the furniture will be shipped and delivered to your location.
- Shipping Methods: Discuss options such as air freight for quicker delivery or sea freight for cost-effective solutions.
- Logistics Planning: Ensure the supplier can handle customs clearance and provide tracking information for your shipment.
Step 7: Establish Clear Communication Channels
Effective communication is key throughout the sourcing process.
- Preferred Channels: Determine the best ways to communicate (e.g., email, phone, video calls) and establish a point of contact.
- Importance of Communication: Clear and consistent communication helps to address any issues promptly, ensuring a smoother purchasing experience.
By following this checklist, international B2B buyers can navigate the complexities of sourcing solid wood furniture more effectively, ensuring they partner with the right suppliers for their needs.
Comprehensive Cost and Pricing Analysis for solid wood furniture supplier Sourcing
What Are the Key Cost Components in Sourcing Solid Wood Furniture?
When sourcing solid wood furniture, understanding the cost structure is crucial for making informed purchasing decisions. The primary cost components include:
-
Materials: The type of wood (e.g., oak, mahogany, teak) significantly affects pricing. Sustainable and certified woods tend to be more expensive due to their sourcing requirements. The quality and availability of the wood can also lead to fluctuations in costs.
-
Labor: Skilled craftsmanship is essential in producing high-quality solid wood furniture. Labor costs vary by region, with countries in Africa and South America often having lower wages compared to Europe. However, the skill level and craftsmanship quality should be considered, as lower labor costs may lead to inferior products.
-
Manufacturing Overhead: This includes costs associated with the factory’s operations, such as utilities, rent, and equipment maintenance. Efficient manufacturing processes can reduce overhead costs, which may be passed on to buyers.
-
Tooling: The costs of machinery and tools used in the production process can be significant. Custom tooling for unique designs can drive up costs but may be necessary for specialized orders.
-
Quality Control (QC): Implementing robust quality control measures ensures that products meet international standards. This may add to the overall cost but is critical for maintaining brand reputation, especially in competitive markets.
-
Logistics: Shipping and handling costs can vary widely based on the destination and the chosen Incoterms. International buyers must account for freight charges, customs duties, and potential delays that can affect lead times.
-
Margin: Suppliers typically add a profit margin to cover their costs and ensure sustainability. Margins can vary based on market conditions, competition, and the supplier’s positioning.
How Do Price Influencers Affect Solid Wood Furniture Costs?
Several factors influence pricing in the solid wood furniture market, including:
-
Volume and Minimum Order Quantity (MOQ): Larger orders often come with discounts, making it essential for buyers to assess their needs carefully. Understanding the MOQ can help negotiate better pricing.
-
Specifications and Customization: Custom designs or specific finishes can increase costs. Buyers should be clear about their requirements from the outset to avoid unexpected expenses.
-
Material Quality and Certifications: Premium materials and certifications (like FSC certification) can raise prices but may be necessary for buyers focused on sustainability and quality.
-
Supplier Factors: The supplier’s reputation, reliability, and production capacity can impact pricing. Established suppliers may charge more due to their experience and product quality.
-
Incoterms: The chosen Incoterms (e.g., FOB, CIF) determine the responsibilities of buyers and sellers regarding shipping costs and risks. Understanding these terms can help buyers estimate total costs more accurately.
What Are Effective Buyer Tips for Negotiating Solid Wood Furniture Prices?
International B2B buyers should consider the following strategies to optimize their purchasing process:
-
Negotiate Wisely: Leverage volume and long-term relationships to negotiate better terms. Suppliers may be more willing to offer discounts for repeat business or bulk orders.
-
Focus on Cost-Efficiency: Look beyond the initial price tag and consider the Total Cost of Ownership (TCO). This includes maintenance, durability, and the potential for resale value, which can significantly affect the overall investment.
-
Understand Pricing Nuances: Different markets have unique pricing structures. For example, buyers from Africa may face different challenges and costs compared to those in Europe, impacting negotiations and expectations.
-
Research and Compare Suppliers: Conduct thorough research and gather quotes from multiple suppliers to ensure competitive pricing. Pay attention to reviews and past performance to gauge reliability.
Disclaimer on Pricing
It is essential to note that prices for solid wood furniture can fluctuate based on market conditions, availability of materials, and changes in labor costs. The insights provided here are indicative and should be used as a guideline for budgeting and negotiations. Buyers are encouraged to conduct their own market research and obtain specific quotes from suppliers to ensure accurate pricing for their projects.
Alternatives Analysis: Comparing solid wood furniture supplier With Other Solutions
When considering the procurement of solid wood furniture, B2B buyers must evaluate various alternatives to determine the most suitable option for their specific needs. The choice between solid wood furniture suppliers and other solutions can significantly impact cost, performance, and overall satisfaction. Below, we compare solid wood furniture suppliers with two viable alternatives: engineered wood furniture and metal furniture.
Comparison Aspect | Solid Wood Furniture Supplier | Engineered Wood Furniture | Metal Furniture |
---|---|---|---|
Performance | High durability and aesthetics; maintains structural integrity over time. | Moderate durability; can be less stable in humid conditions. | Very durable; resistant to wear and tear. |
Cost | Higher upfront costs; long-term investment value. | Generally lower cost; more budget-friendly. | Mid-range costs; dependent on design and finish. |
Ease of Implementation | Requires skilled craftsmanship for assembly and finishing. | Easier to assemble; often comes pre-finished. | Simple assembly; lightweight materials make handling easier. |
Maintenance | Requires regular care (oiling, polishing) to maintain appearance. | Low maintenance; easy to clean. | Very low maintenance; resistant to staining and scratches. |
Best Use Case | Ideal for high-end markets, luxury hotels, and bespoke projects. | Suitable for budget-conscious consumers and mass production. | Great for modern office spaces and industrial settings. |
What Are the Pros and Cons of Engineered Wood Furniture Compared to Solid Wood Furniture?
Engineered wood furniture is made from composite materials, such as plywood or particleboard, which are designed to mimic the look and feel of solid wood.
Pros:
– Cost-Effective: Engineered wood tends to be less expensive, making it an attractive option for businesses with tight budgets.
– Sustainability: Often made from recycled materials, engineered wood can be a more eco-friendly choice.
Cons:
– Durability Concerns: While engineered wood can be durable, it is generally not as long-lasting as solid wood, especially in humid environments.
– Lower Aesthetic Appeal: Many buyers prefer the unique grain patterns and richness of solid wood, which engineered alternatives may lack.
How Does Metal Furniture Compare to Solid Wood Furniture?
Metal furniture includes items made from steel, aluminum, or other metals, often utilized in both residential and commercial settings.
Pros:
– Durability: Metal furniture is highly resistant to damage and wear, making it ideal for high-traffic areas.
– Modern Appeal: The sleek, minimalist look of metal can complement contemporary design aesthetics.
Cons:
– Comfort Issues: Metal furniture can be less comfortable than wood, especially for seating options, unless padded.
– Temperature Sensitivity: Metal can become hot or cold depending on the environment, potentially affecting user comfort.
How Can International B2B Buyers Choose the Right Furniture Solution?
Selecting the appropriate furniture solution hinges on understanding your organization’s specific needs, budget constraints, and aesthetic preferences. For businesses in Africa, South America, the Middle East, and Europe, considerations such as local climate, cultural preferences, and market trends should inform your decision. Solid wood furniture may be the best choice for high-end applications where durability and aesthetics are paramount. Conversely, engineered wood and metal furniture could serve well in budget-conscious projects or environments requiring easy maintenance. By weighing these factors, international B2B buyers can make informed decisions that align with their operational goals and customer expectations.
Essential Technical Properties and Trade Terminology for solid wood furniture supplier
What Are the Essential Technical Properties of Solid Wood Furniture?
When sourcing solid wood furniture, understanding the technical properties is crucial for B2B buyers. Here are some key specifications to consider:
1. Material Grade: Why Does It Matter?
Material grade refers to the quality and characteristics of the wood used. Common grades include A, B, C, and D, with A being the highest quality, featuring fewer knots and defects. For international buyers, especially from regions like Africa and South America, specifying the material grade ensures that the furniture meets durability and aesthetic standards, which can influence customer satisfaction and brand reputation.
2. Moisture Content: How Does It Affect Longevity?
Moisture content is the percentage of water in the wood. Ideal moisture levels for solid wood furniture typically range between 6% to 8%. High moisture content can lead to warping, cracking, or mold growth, while too low can result in brittleness. B2B buyers should request moisture content specifications to ensure that the furniture will withstand varying climates, particularly in humid regions like the Middle East.
3. Tolerance Levels: What Should Buyers Know?
Tolerance levels indicate the permissible variations in dimensions during manufacturing. For example, a tolerance of ±1mm might be acceptable for furniture joints. Understanding these tolerances is vital for buyers to ensure that the furniture fits perfectly into their intended spaces. This is especially important in markets with strict building regulations, such as those in Europe.
4. Finish Type: How Does It Impact Maintenance?
The finish type—whether oil, lacquer, or polyurethane—affects both the aesthetics and maintenance of the furniture. Oil finishes are easier to repair but may require more frequent maintenance, while lacquer provides a hard, protective surface. Buyers should communicate their preferred finish type to suppliers to ensure compatibility with their market’s expectations regarding durability and care.
5. Structural Integrity: Why Is It Essential?
Structural integrity refers to the furniture’s ability to withstand weight and pressure without compromising its form. This includes factors such as joinery techniques and the thickness of materials used. For B2B buyers, understanding structural integrity is crucial for ensuring that the furniture can support the intended usage, particularly in commercial settings.
What Are Common Trade Terms Used in Solid Wood Furniture Supply?
Familiarizing oneself with industry jargon is essential for effective communication and negotiation. Here are some common terms that B2B buyers should know:
1. OEM (Original Equipment Manufacturer): What Does It Mean?
OEM refers to companies that produce goods that are sold under another company’s brand name. For B2B buyers, sourcing from OEMs can provide opportunities to customize products while leveraging the manufacturing expertise of established suppliers.
2. MOQ (Minimum Order Quantity): Why Is It Important?
MOQ is the minimum number of units a supplier is willing to produce or sell. Understanding MOQ is crucial for buyers to manage inventory effectively and avoid excess stock. This is particularly relevant for businesses in regions like Africa or South America, where market demand may fluctuate.
3. RFQ (Request for Quotation): How Does It Work?
An RFQ is a document sent to suppliers to request pricing and terms for specific products. B2B buyers should use RFQs to compare offers from multiple suppliers, ensuring they get the best deal and terms for their solid wood furniture needs.
4. Incoterms: What Do They Represent?
Incoterms are international trade terms that define the responsibilities of buyers and sellers in shipping arrangements. For instance, “FOB” (Free On Board) indicates that the seller covers costs until the goods are on board the shipping vessel. Understanding Incoterms helps buyers from different regions navigate logistics and minimize shipping risks.
5. Lead Time: Why Should Buyers Pay Attention?
Lead time refers to the time taken from placing an order until the goods are delivered. Knowing the lead time is essential for buyers to plan their inventory and sales strategies effectively, especially when dealing with suppliers across continents.
By grasping these technical properties and trade terms, B2B buyers can make informed decisions that align with their business goals and market needs, ensuring a successful procurement process in the solid wood furniture sector.
Navigating Market Dynamics and Sourcing Trends in the solid wood furniture supplier Sector
What Are the Key Trends Shaping the Solid Wood Furniture Supplier Market?
The solid wood furniture sector is undergoing significant transformation, influenced by various global drivers. One primary factor is the increasing consumer demand for sustainable and high-quality products. This trend is particularly pronounced among B2B buyers in regions like Africa, South America, the Middle East, and Europe, where there is a growing emphasis on durability and craftsmanship. As a result, suppliers are leveraging advanced manufacturing technologies, such as CNC machining and digital design tools, to enhance precision and reduce waste.
Moreover, the rise of e-commerce and digital platforms is reshaping sourcing trends. International buyers can now access a broader range of suppliers, compare prices, and evaluate product quality through online marketplaces. This shift towards digitalization enables B2B buyers to streamline their procurement processes, making sourcing more efficient and transparent. In addition, the integration of data analytics and AI in inventory management allows suppliers to respond swiftly to market demands, ensuring they remain competitive in an ever-evolving landscape.
How Important Is Sustainability and Ethical Sourcing for B2B Buyers in the Solid Wood Furniture Sector?
Sustainability and ethical sourcing have become paramount considerations for B2B buyers in the solid wood furniture market. The environmental impact of deforestation and resource depletion has led to heightened awareness and demand for sustainable practices. Buyers are increasingly seeking suppliers who adhere to responsible sourcing methods, ensuring that wood is harvested from well-managed forests certified by organizations such as the Forest Stewardship Council (FSC).
Additionally, the importance of transparency in supply chains cannot be overstated. B2B buyers are now looking for detailed information about the origins of materials, manufacturing processes, and labor practices. This shift is not only about compliance with regulations but also about aligning with the values of end consumers who prefer ethically sourced products. Suppliers that can demonstrate their commitment to sustainability—through certifications, eco-friendly materials, and transparent practices—will have a competitive edge in attracting discerning international buyers.
What Historical Factors Have Influenced the Solid Wood Furniture Supplier Market?
The solid wood furniture market has evolved significantly over the centuries, influenced by cultural shifts, technological advancements, and economic changes. Historically, craftsmanship was the cornerstone of furniture production, with artisans handcrafting pieces that reflected local traditions and materials. As industrialization took hold in the 19th and 20th centuries, mass production techniques emerged, enabling suppliers to meet growing consumer demands for affordability and accessibility.
In recent decades, a resurgence of interest in handmade and artisanal products has emerged, driven by consumer preferences for unique, quality items over mass-produced alternatives. This trend has been further fueled by the digital age, which allows artisans and small suppliers to reach global markets through online platforms. Consequently, the solid wood furniture sector today balances traditional craftsmanship with modern production techniques, appealing to a diverse range of B2B buyers who seek both quality and sustainability.
Frequently Asked Questions (FAQs) for B2B Buyers of solid wood furniture supplier
-
How do I choose the right solid wood furniture supplier for my business?
Selecting the right supplier involves several critical steps. First, assess the supplier’s reputation by checking online reviews and seeking testimonials from other B2B buyers. Next, evaluate their product quality by requesting samples or visiting their showroom. Additionally, consider their capacity to meet your order requirements, including customization options and minimum order quantities (MOQs). Lastly, confirm their compliance with international trade regulations and their ability to deliver on time, especially if you are sourcing from regions like Africa or South America. -
What are the key factors to consider when vetting a solid wood furniture supplier?
When vetting suppliers, focus on their experience in the industry, production capabilities, and adherence to quality standards. Investigate their certifications, such as ISO or FSC, which reflect their commitment to sustainable practices. Communication is vital; ensure they respond promptly and professionally. Additionally, assess their financial stability and ask for references from existing clients. This due diligence will help you gauge reliability and build a long-term partnership. -
What customization options should I expect from solid wood furniture suppliers?
Most reputable solid wood furniture suppliers offer various customization options, including wood type, finish, size, and design. Some may even provide bespoke solutions tailored to your specific business needs. It’s essential to discuss your requirements upfront and verify if the supplier can accommodate your requests. Inquire about their design capabilities and the time required for custom orders, as this can impact your overall project timeline. -
What is the typical minimum order quantity (MOQ) for solid wood furniture?
Minimum order quantities (MOQs) for solid wood furniture can vary significantly among suppliers, typically ranging from 10 to 100 units per order. Factors influencing MOQ include the type of furniture, production processes, and the supplier’s operational capacity. If you’re a smaller business, consider negotiating MOQs or exploring suppliers who cater specifically to small and medium enterprises (SMEs) to find a suitable arrangement. -
What payment terms are common when working with solid wood furniture suppliers?
Payment terms can differ widely, but common arrangements include a deposit (usually 30-50%) upfront, with the balance due before shipping or upon delivery. Some suppliers may offer favorable terms based on your purchasing history or creditworthiness. Always clarify the payment methods accepted, such as bank transfers or letters of credit, and ensure that the terms align with your cash flow management strategies. -
How can I ensure quality assurance when sourcing solid wood furniture?
To ensure quality, implement a rigorous quality assurance (QA) process. This may include setting clear specifications in your purchase order and conducting pre-shipment inspections. Request certifications that validate the quality and sustainability of the wood used. Additionally, establish a feedback loop with your supplier to address any quality concerns promptly. Building a relationship based on trust and transparency will further enhance the quality assurance process.
-
What logistics considerations should I keep in mind when importing solid wood furniture?
Logistics play a crucial role in importing solid wood furniture. Consider factors such as shipping methods, lead times, and customs clearance processes. It’s advisable to work with logistics providers experienced in handling furniture shipments, as they can navigate the complexities of international shipping. Additionally, factor in costs related to duties, taxes, and potential delays. Planning for these elements will help ensure a smooth supply chain and timely delivery. -
How do I handle disputes with solid wood furniture suppliers?
Handling disputes effectively requires clear communication and documentation. Begin by addressing the issue directly with the supplier, providing specific details and evidence of the problem. If a resolution isn’t reached, consult your contract for dispute resolution procedures, which may include mediation or arbitration. Maintaining a professional tone throughout the process is essential, as it can help preserve the business relationship while working towards a satisfactory outcome.
Important Disclaimer & Terms of Use
⚠️ Important Disclaimer
The information provided in this guide, including content regarding manufacturers, technical specifications, and market analysis, is for informational and educational purposes only. It does not constitute professional procurement advice, financial advice, or legal advice.
While we have made every effort to ensure the accuracy and timeliness of the information, we are not responsible for any errors, omissions, or outdated information. Market conditions, company details, and technical standards are subject to change.
B2B buyers must conduct their own independent and thorough due diligence before making any purchasing decisions. This includes contacting suppliers directly, verifying certifications, requesting samples, and seeking professional consultation. The risk of relying on any information in this guide is borne solely by the reader.
Strategic Sourcing Conclusion and Outlook for solid wood furniture supplier
In the dynamic landscape of solid wood furniture sourcing, the importance of strategic sourcing cannot be overstated. For international B2B buyers, particularly those from Africa, South America, the Middle East, and Europe, the ability to identify reliable suppliers who prioritize quality, sustainability, and ethical practices is paramount. By leveraging strategic sourcing, businesses can enhance their supply chain resilience, reduce costs, and ensure compliance with local regulations and market demands.
What Are the Key Takeaways for B2B Buyers in Solid Wood Furniture?
-
Supplier Diversity: Engage with a range of suppliers to mitigate risks associated with supply disruptions. This diversity not only enhances bargaining power but also fosters innovation in product offerings.
-
Sustainability Matters: Consider suppliers who adhere to sustainable practices, as global consumers increasingly demand eco-friendly products. This aligns with corporate social responsibility goals and enhances brand reputation.
-
Quality Assurance: Prioritize suppliers that implement stringent quality control measures. Building long-term partnerships with these suppliers can lead to improved product consistency and customer satisfaction.
As you navigate the complexities of sourcing solid wood furniture, embrace these strategic insights to make informed decisions. The future of your business hinges on the relationships you build today. Take action now to explore new supplier partnerships that align with your organizational values and market needs. Together, we can foster a more sustainable and prosperous furniture industry.