Discover Cost-Effective Solutions from a Rubber Manufacturer (2025)
Introduction: Navigating the Global Market for rubber manufacturer
In the dynamic landscape of international trade, sourcing high-quality rubber manufacturers can pose significant challenges for B2B buyers across various sectors. Whether you are seeking durable rubber components for automotive applications or flexible materials for consumer goods, understanding the nuances of the global rubber market is essential. This guide serves as a comprehensive resource for navigating the complexities of rubber manufacturing, offering insights into different types of rubber products, their applications, and critical factors to consider when vetting suppliers.
From evaluating the quality and sustainability practices of manufacturers to understanding cost structures and logistics, this guide empowers international B2B buyers—particularly those from Africa, South America, the Middle East, and Europe, including countries like Egypt and Spain—to make informed purchasing decisions. By exploring the various aspects of the rubber manufacturing process, including raw material sourcing, production capabilities, and compliance with international standards, buyers can better align their procurement strategies with their business objectives.
Furthermore, this resource will delve into the importance of building strong relationships with suppliers, assessing market trends, and identifying reliable channels for sourcing rubber products. With this knowledge, B2B buyers can mitigate risks, optimize costs, and enhance their supply chain efficiency, ultimately leading to a competitive edge in their respective markets.
Understanding rubber manufacturer Types and Variations
Type Name | Key Distinguishing Features | Primary B2B Applications | Brief Pros & Cons for Buyers |
---|---|---|---|
Natural Rubber Manufacturers | Sourced from rubber trees; excellent elasticity and resilience | Automotive tires, footwear, medical supplies | Pros: Eco-friendly, good tensile strength. Cons: Price volatility, limited supply. |
Synthetic Rubber Manufacturers | Produced from petrochemicals; customizable properties | Seals, gaskets, industrial hoses | Pros: Consistent quality, tailored properties. Cons: Environmental concerns, dependency on oil prices. |
Specialty Rubber Manufacturers | Focus on niche applications; high-performance materials | Aerospace, military, electronics | Pros: Tailored solutions, high durability. Cons: Higher cost, longer lead times. |
Recycled Rubber Manufacturers | Utilizes scrap rubber; environmentally sustainable | Playground surfaces, mats, insulation | Pros: Cost-effective, eco-friendly. Cons: Variable quality, limited application scope. |
Foam Rubber Manufacturers | Lightweight, cushioning materials; often used in composites | Packaging, automotive interiors, furniture | Pros: Excellent shock absorption, versatile. Cons: Limited temperature resistance, potential odor issues. |
What Are the Key Characteristics of Natural Rubber Manufacturers?
Natural rubber manufacturers source their products from rubber trees, primarily found in tropical regions. This type of rubber is known for its exceptional elasticity, resilience, and strength, making it ideal for applications such as automotive tires, footwear, and medical supplies. When purchasing natural rubber, buyers should consider factors like supply stability, as prices can fluctuate due to climatic conditions affecting rubber production.
How Do Synthetic Rubber Manufacturers Differ?
Synthetic rubber manufacturers create rubber from petrochemical feedstocks, allowing for a wide range of customizable properties. This flexibility makes synthetic rubber suitable for various applications, including seals, gaskets, and industrial hoses. B2B buyers should evaluate the specific performance requirements of their projects, as synthetic rubber can be engineered to meet precise specifications, though it may come with environmental concerns due to its petroleum base.
What Are Specialty Rubber Manufacturers Known For?
Specialty rubber manufacturers focus on producing high-performance rubber for niche applications, such as aerospace, military, and electronics. These manufacturers provide tailored solutions that meet stringent performance standards, often at a higher cost. Buyers should weigh the benefits of durability and specialized performance against the potential for increased pricing and longer lead times, particularly for unique projects.
Why Choose Recycled Rubber Manufacturers?
Recycled rubber manufacturers utilize scrap rubber to create new products, promoting sustainability and reducing waste. Common applications include playground surfaces, mats, and insulation materials. Buyers looking for cost-effective and environmentally friendly options may find recycled rubber appealing; however, they should be cautious of variable quality and the limitations on application scope.
What Are the Advantages of Foam Rubber Manufacturers?
Foam rubber manufacturers produce lightweight materials that provide excellent cushioning and shock absorption, making them ideal for packaging, automotive interiors, and furniture applications. Buyers should consider the versatility of foam rubber, which can be tailored for specific uses. However, potential drawbacks include limited temperature resistance and issues related to odors, which may affect certain applications.
Related Video: The Silicone Rubber Extrusion Process Explained
Key Industrial Applications of rubber manufacturer
Industry/Sector | Specific Application of Rubber Manufacturer | Value/Benefit for the Business | Key Sourcing Considerations for this Application |
---|---|---|---|
Automotive | Tires and Seals | Enhanced safety and performance in vehicles | Quality certifications, local regulations, durability standards |
Construction | Waterproofing Membranes and Gaskets | Improved building longevity and energy efficiency | Material specifications, climate adaptability, supplier reliability |
Healthcare | Medical Devices and Seals | Compliance with health regulations and patient safety | FDA approval, biocompatibility, manufacturing capabilities |
Consumer Goods | Footwear and Sports Equipment | Product comfort and durability | Design flexibility, material sourcing, market trends |
Industrial Equipment | Vibration Dampening and Hoses | Reduced machinery wear and increased lifespan | Customization options, performance metrics, lead times |
How is Rubber Used in the Automotive Sector?
In the automotive industry, rubber manufacturers produce essential components like tires and seals. Tires made from high-quality rubber enhance vehicle safety by providing better traction and durability under various conditions. Seals prevent leaks in critical systems, ensuring the longevity and reliability of vehicles. For international buyers, especially from regions like Africa and the Middle East, sourcing rubber products that meet regional climate challenges is crucial. Buyers must consider certifications and compliance with safety standards to ensure quality.
What Role Does Rubber Play in Construction?
Rubber manufacturers supply waterproofing membranes and gaskets that are vital for construction projects. These products help prevent water ingress, which can lead to structural damage and increased maintenance costs. In regions with heavy rainfall, such as parts of South America, the demand for high-performance waterproofing solutions is significant. Buyers should evaluate the material specifications and climate adaptability of rubber products to ensure they meet local building codes and standards.
How is Rubber Essential in Healthcare Applications?
In the healthcare sector, rubber is used to manufacture medical devices and seals that require stringent compliance with health regulations. Rubber components must be biocompatible to ensure patient safety, making it essential for manufacturers to provide FDA-approved materials. International buyers, particularly from Europe, should prioritize suppliers who can demonstrate compliance with these regulations and have robust manufacturing capabilities to ensure consistent quality.
Why is Rubber Important for Consumer Goods?
Rubber plays a crucial role in the production of footwear and sports equipment, providing comfort, flexibility, and durability. Products made from rubber can significantly enhance user experience, driving consumer satisfaction and brand loyalty. For B2B buyers in markets like Spain, understanding market trends and design flexibility is key to sourcing the right rubber materials that align with consumer preferences and seasonal demands.
How Does Rubber Benefit Industrial Equipment?
In industrial applications, rubber is utilized for vibration dampening and hoses, which are critical for reducing machinery wear and enhancing operational efficiency. High-quality rubber components can extend the lifespan of equipment, leading to cost savings and improved productivity. Buyers must consider customization options and performance metrics when sourcing rubber for industrial applications, ensuring the materials align with specific operational requirements and lead times.
Related Video: FANUC Industrial Robots | AUDI Case Study
3 Common User Pain Points for ‘rubber manufacturer’ & Their Solutions
Scenario 1: Navigating Quality Control Issues in Rubber Manufacturing
The Problem: International B2B buyers often face challenges related to quality control when sourcing rubber products. Inconsistent quality can lead to production delays, increased costs, and even legal liabilities, especially if the rubber components do not meet the required specifications. Buyers from regions like Africa or South America may struggle to ensure that the manufacturers adhere to international quality standards, leading to frustration and potential financial loss.
The Solution: To mitigate quality control issues, buyers should prioritize establishing clear specifications for the rubber products they need, including details on material grades, tolerances, and testing requirements. It is advisable to request certifications such as ISO 9001 or specific industry standards relevant to their sector. Furthermore, conducting pre-shipment inspections and audits of the manufacturing facility can help ensure compliance with quality standards. Engaging third-party quality assurance services can provide an extra layer of confidence, particularly for buyers unfamiliar with the local manufacturing practices.
Scenario 2: Understanding Supply Chain Disruptions in Rubber Procurement
The Problem: B2B buyers in Europe or the Middle East often face supply chain disruptions due to geopolitical issues, natural disasters, or economic instability affecting rubber-producing countries. Such disruptions can lead to unexpected lead times and cost fluctuations, making it difficult for businesses to plan effectively. This uncertainty can severely impact production schedules and overall business operations.
The Solution: To navigate supply chain disruptions, buyers should diversify their supplier base by sourcing rubber products from multiple manufacturers across different regions. Establishing relationships with suppliers in various countries can provide alternatives during crises. Additionally, implementing a robust supply chain management system can help buyers monitor potential risks and trends in real-time. Buyers should also negotiate flexible terms with suppliers, such as buffer stock agreements or priority allocation during shortages, to secure their supply chain against unexpected disruptions.
Scenario 3: Managing Cost Constraints While Sourcing Rubber Products
The Problem: For many international B2B buyers, particularly in emerging markets, managing costs while sourcing rubber products can be a significant challenge. Fluctuating raw material prices and increasing production costs can squeeze profit margins, making it essential for buyers to find cost-effective solutions without compromising quality.
The Solution: Buyers should consider leveraging bulk purchasing agreements to negotiate better pricing with rubber manufacturers. By committing to larger orders, they can often secure lower rates. Additionally, exploring alternative materials or manufacturing processes can provide cost savings. For instance, utilizing synthetic rubber or recycled rubber may be more economical depending on the application. Regularly reviewing market trends and establishing a good rapport with suppliers can also lead to better pricing and more favorable terms over time. Implementing a total cost of ownership (TCO) approach can help buyers evaluate not just the upfront costs, but the long-term value of their rubber sourcing decisions.
Strategic Material Selection Guide for rubber manufacturer
What Are the Key Properties of Common Rubber Manufacturing Materials?
When selecting materials for rubber manufacturing, it’s essential to understand the properties that influence product performance. Here, we analyze four common materials used in the rubber industry: Natural Rubber (NR), Styrene-Butadiene Rubber (SBR), Nitrile Rubber (NBR), and Ethylene Propylene Diene Monomer (EPDM). Each material has unique characteristics that affect its suitability for various applications.
How Does Natural Rubber (NR) Perform in Various Conditions?
Natural Rubber (NR) is renowned for its excellent elasticity and resilience. It performs well at temperatures ranging from -50°C to 80°C and can withstand moderate pressures. However, NR has limited resistance to oils and solvents, which can cause degradation.
Pros:
– Exceptional tensile strength and elongation properties.
– Biodegradable and sustainable.
Cons:
– Poor resistance to heat, ozone, and aging.
– Limited compatibility with petroleum-based products.
Impact on Application:
NR is ideal for applications requiring high elasticity, such as tires and shock absorbers, but is unsuitable for environments with exposure to oils.
Considerations for International Buyers:
Buyers in regions like Africa and the Middle East should be aware of local climate conditions that may affect NR’s performance. Compliance with ASTM standards is crucial for ensuring quality.
What Advantages Does Styrene-Butadiene Rubber (SBR) Offer?
Styrene-Butadiene Rubber (SBR) is a synthetic rubber that combines the properties of styrene and butadiene. It has a temperature range of -40°C to 100°C and offers good abrasion resistance.
Pros:
– Cost-effective and widely available.
– Good aging stability and resistance to wear.
Cons:
– Inferior heat resistance compared to NR.
– Limited chemical resistance, particularly to oils.
Impact on Application:
SBR is commonly used in tire manufacturing and industrial applications where abrasion resistance is critical, but it may not perform well in oily environments.
Considerations for International Buyers:
In Europe, SBR is often preferred for its cost-effectiveness, but buyers should ensure compliance with EU regulations regarding synthetic materials.
How Does Nitrile Rubber (NBR) Compare in Terms of Oil Resistance?
Nitrile Rubber (NBR) is specifically designed for applications requiring oil and fuel resistance. It operates effectively within a temperature range of -40°C to 120°C.
Pros:
– Excellent resistance to oils and fuels.
– Good mechanical properties and durability.
Cons:
– Poor ozone and weather resistance.
– Less elastic than NR.
Impact on Application:
NBR is ideal for seals, gaskets, and hoses in automotive and aerospace industries due to its oil resistance.
Considerations for International Buyers:
Buyers in South America and the Middle East should consider local oil compatibility standards and ensure that NBR products meet ASTM specifications.
What Are the Benefits of Ethylene Propylene Diene Monomer (EPDM)?
Ethylene Propylene Diene Monomer (EPDM) is a synthetic rubber known for its excellent weather and ozone resistance. It performs well in temperatures ranging from -50°C to 150°C.
Pros:
– Outstanding resistance to UV radiation and aging.
– Excellent flexibility at low temperatures.
Cons:
– Poor resistance to petroleum products.
– Higher manufacturing costs compared to other rubbers.
Impact on Application:
EPDM is suitable for roofing membranes, automotive weather stripping, and electrical insulation due to its durability against environmental factors.
Considerations for International Buyers:
European buyers should ensure that EPDM materials comply with local environmental regulations, while African buyers should consider the material’s performance in high UV exposure conditions.
Summary Table of Rubber Manufacturing Materials
Material | Typical Use Case for rubber manufacturer | Key Advantage | Key Disadvantage/Limitation | Relative Cost (Low/Med/High) |
---|---|---|---|---|
Natural Rubber (NR) | Tires, shock absorbers | Exceptional elasticity | Poor resistance to oils | Medium |
Styrene-Butadiene Rubber (SBR) | Tire manufacturing, industrial applications | Cost-effective | Limited oil resistance | Low |
Nitrile Rubber (NBR) | Seals, gaskets, hoses | Excellent oil resistance | Poor ozone resistance | Medium |
Ethylene Propylene Diene Monomer (EPDM) | Roofing membranes, weather stripping | Outstanding weather resistance | Poor petroleum resistance | High |
This strategic material selection guide provides essential insights for international B2B buyers, enabling informed decisions based on product performance, application suitability, and regional compliance standards.
In-depth Look: Manufacturing Processes and Quality Assurance for rubber manufacturer
What Are the Main Stages of Manufacturing Processes for Rubber Products?
The manufacturing process for rubber products typically consists of several key stages: material preparation, forming, assembly, and finishing. Understanding these stages is crucial for B2B buyers seeking to partner with reliable rubber manufacturers.
Material Preparation: What Are the Key Steps?
The first step in the rubber manufacturing process is material preparation, which involves selecting and preparing the raw materials. Natural rubber, synthetic rubber, or a blend of both can be used, depending on the application requirements.
- Compounding: This involves mixing the rubber with various additives such as accelerators, fillers, and antioxidants to enhance its properties.
- Milling: The compounded rubber is then processed through mills to achieve a uniform texture and to facilitate further processing.
- Preforming: In this stage, the rubber is shaped into preliminary forms, such as sheets or blocks, which are easier to handle during the forming stage.
How Is Rubber Formed into Finished Products?
The forming stage is where the prepared rubber material is transformed into its desired shapes. This can be accomplished through several techniques:
- Molding: The most common method, which involves placing the rubber into a mold and applying heat and pressure. This method is suitable for producing complex shapes and is widely used for items like seals and gaskets.
- Extrusion: In this method, the rubber is forced through a die to create continuous shapes, such as hoses or tubing. This process is efficient for producing long lengths of rubber products.
- Calendering: This technique involves passing the rubber through a series of rollers to produce sheets of consistent thickness, ideal for applications requiring large surface areas.
What Are the Assembly and Finishing Processes?
After forming, the next steps involve assembly and finishing:
- Assembly: For products that require multiple components, such as tires or automotive parts, assembly involves joining these components using adhesives or mechanical fasteners.
- Finishing: This final stage includes processes such as trimming, surface treatment, and quality checks to ensure the product meets the required specifications. Surface treatments may include painting or coating to enhance durability.
What Quality Assurance Standards Should B2B Buyers Look For?
Quality assurance (QA) is critical in rubber manufacturing, ensuring that products meet international standards and customer expectations. B2B buyers should be familiar with relevant QA standards to evaluate potential suppliers.
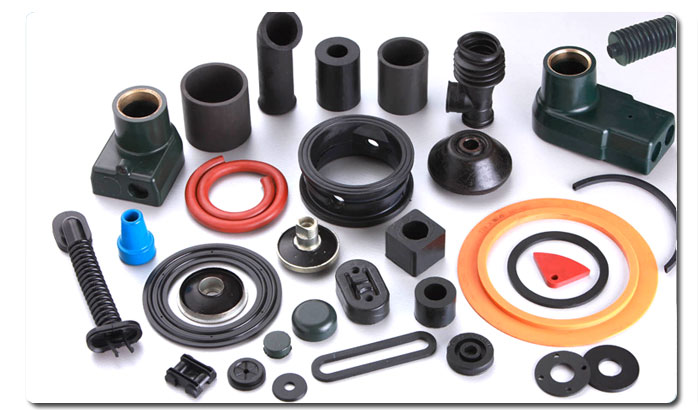
A stock image related to rubber manufacturer.
Which International Standards Are Important?
- ISO 9001: This widely recognized standard focuses on quality management systems, ensuring that manufacturers maintain consistent quality in their products and services.
- CE Marking: For products sold within the European Union, CE marking indicates compliance with safety and environmental requirements.
- API Standards: Specifically relevant for rubber products used in the oil and gas industry, API standards ensure that products can withstand harsh operating conditions.
How Do Quality Control Checkpoints Work?
Quality control (QC) is integrated at various stages of the manufacturing process to identify and rectify defects. Key QC checkpoints include:
- Incoming Quality Control (IQC): At this stage, raw materials and components are inspected upon arrival to ensure they meet specified standards.
- In-Process Quality Control (IPQC): Ongoing checks during the manufacturing process help identify any deviations from quality standards, allowing for immediate corrective actions.
- Final Quality Control (FQC): The final product undergoes thorough inspection and testing to verify that it meets all specifications before shipment.
What Common Testing Methods Are Used in Rubber Manufacturing?
B2B buyers should be aware of the common testing methods employed in rubber manufacturing to ensure product reliability and performance:
- Tensile Testing: Measures the strength and elasticity of the rubber, indicating how much force the product can withstand before failing.
- Hardness Testing: Evaluates the hardness of rubber, which is critical for applications where abrasion resistance is important.
- Aging Tests: Simulate long-term exposure to environmental factors like UV light, heat, and ozone, ensuring that the rubber maintains its properties over time.
How Can B2B Buyers Verify Supplier Quality Control?
To ensure they are partnering with a reputable rubber manufacturer, B2B buyers should take proactive steps to verify supplier quality control processes:
- Supplier Audits: Conducting audits of potential suppliers allows buyers to assess their manufacturing practices, quality control systems, and compliance with international standards.
- Requesting Quality Reports: Manufacturers should provide documentation of their quality control processes, including inspection reports and compliance certificates.
- Third-Party Inspections: Engaging independent third-party inspectors can provide an unbiased assessment of the manufacturer’s quality control measures and product reliability.
What Are the QC and Certification Nuances for International Buyers?
International B2B buyers, particularly from regions like Africa, South America, the Middle East, and Europe, must navigate specific nuances in quality control and certification:
- Regulatory Compliance: Understanding local regulations and standards is essential, as they can vary significantly between regions. For instance, rubber products sold in Europe must adhere to CE marking requirements, while those in the Middle East may require compliance with local standards.
- Cultural and Logistical Considerations: Cultural differences may impact communication and negotiation processes. Additionally, logistical challenges such as shipping times and customs clearance can affect the timely delivery of quality products.
- Sustainability Standards: Increasingly, buyers are looking for suppliers who adhere to sustainability practices. Certifications like ISO 14001 (Environmental Management) can be an indicator of a manufacturer’s commitment to sustainable practices.
By understanding the manufacturing processes and quality assurance standards in the rubber industry, international B2B buyers can make informed decisions and establish successful partnerships with reliable suppliers.
Practical Sourcing Guide: A Step-by-Step Checklist for ‘rubber manufacturer’
To assist international B2B buyers in effectively sourcing rubber manufacturers, this checklist provides a systematic approach to ensure you select the most suitable supplier for your needs. By following these steps, you can mitigate risks and enhance the quality of your procurement process.
Step 1: Define Your Technical Specifications
Clearly outline the specifications of the rubber products you need. This includes details such as the type of rubber (natural or synthetic), required hardness, temperature resistance, and any specific certifications needed for compliance in your industry. Understanding your requirements helps in narrowing down suppliers who can meet your specific needs.
- Consider application: Identify the application of the rubber products to ensure compatibility.
- Quality standards: Research industry standards that the products must adhere to.
Step 2: Conduct Market Research
Investigate potential suppliers in the global market. Utilize online platforms, trade directories, and industry exhibitions to gather a list of rubber manufacturers. Pay attention to their market reputation and customer reviews, particularly from businesses in Africa, South America, the Middle East, and Europe.
- Industry reports: Analyze market reports for insights on top-performing suppliers.
- Networking: Engage with industry peers to get recommendations based on their experiences.
Step 3: Evaluate Potential Suppliers
Thoroughly vet the shortlisted suppliers. Request company profiles, production capabilities, and case studies. It’s essential to check their experience in producing the specific rubber products you require, as well as their history in your target market.
- References: Ask for references from previous clients, especially those in similar industries or regions.
- Production capacity: Ensure they can handle your order volume without compromising quality.
Step 4: Verify Certifications and Compliance
Check for necessary certifications and compliance with international standards. This is particularly important if you are sourcing from regions with varying regulatory standards. Certifications such as ISO 9001, REACH, or ASTM compliance can indicate a supplier’s commitment to quality and safety.
- Documentation: Request copies of certifications and ensure they are up to date.
- Regulatory knowledge: Confirm that the supplier understands local regulations relevant to your market.
Step 5: Assess Production and Quality Control Processes
Inquire about the supplier’s production methods and quality control measures. A robust quality management system is crucial for ensuring consistent product quality. Understanding their processes helps you gauge their reliability and ability to meet your specifications.
- Factory visits: If possible, conduct a site visit to observe their operations firsthand.
- Quality checks: Ask about their quality assurance processes and the frequency of inspections.
Step 6: Negotiate Terms and Conditions
Discuss pricing, payment terms, and delivery schedules with potential suppliers. Clear communication about expectations can prevent misunderstandings later in the procurement process. Consider factors such as bulk pricing, payment methods, and lead times.
- Flexibility: Assess the supplier’s willingness to negotiate terms that suit your business needs.
- Contract details: Ensure all agreed terms are documented in a formal contract to avoid disputes.
Step 7: Establish a Trial Order
Before making a large commitment, place a trial order. This allows you to assess the supplier’s ability to deliver on time and meet quality standards without significant risk. Evaluate the entire process from order placement to delivery.
- Feedback loop: Use this opportunity to provide feedback and gauge the supplier’s responsiveness.
- Long-term relationship: A successful trial order can lead to a more fruitful long-term partnership.
By following this checklist, B2B buyers can streamline their sourcing process, ensuring they partner with reliable rubber manufacturers that align with their business goals and compliance requirements.
Comprehensive Cost and Pricing Analysis for rubber manufacturer Sourcing
What Are the Key Cost Components in Rubber Manufacturing?
When sourcing from rubber manufacturers, understanding the cost structure is critical for international B2B buyers. The main components that contribute to the overall cost include:
-
Materials: The quality and type of rubber (natural vs. synthetic) can significantly impact pricing. Specialty rubbers with unique properties will often command higher prices.
-
Labor: Labor costs vary by region. Countries with higher wages will naturally see increased production costs. Understanding local labor markets can help buyers negotiate better.
-
Manufacturing Overhead: This includes costs associated with utilities, rent, and administrative expenses. Manufacturers with higher operational efficiencies may offer more competitive pricing.
-
Tooling: Custom molds and tooling are often required for specific products. The initial cost can be significant, but it is essential for ensuring product quality and consistency.
-
Quality Control (QC): Robust QC processes ensure product reliability and compliance with international standards. This can add to the overall cost but is crucial for maintaining quality.
-
Logistics: Transportation costs, especially for international shipping, can vary widely based on distance and shipping methods. Incoterms also influence logistics costs and responsibilities.
-
Margin: Manufacturers will include a profit margin in their pricing, which varies based on competition, market demand, and the value-added services they provide.
How Do Price Influencers Affect Rubber Manufacturing Costs?
Several factors influence the pricing of rubber products, particularly for international buyers:
-
Volume and Minimum Order Quantity (MOQ): Higher order volumes often lead to lower per-unit costs. Buyers should negotiate MOQs that align with their purchasing needs.
-
Specifications and Customization: Customized products usually incur higher costs due to additional tooling and production time. Buyers should clarify their specifications early in the negotiation process to avoid unexpected costs.
-
Materials Quality and Certifications: Premium materials and necessary certifications (e.g., ISO, ASTM) can increase costs but are essential for ensuring product quality and compliance in certain markets.
-
Supplier Factors: The reliability and reputation of the supplier can influence pricing. Established suppliers with a track record may offer better terms or pricing structures.
-
Incoterms: Understanding Incoterms is crucial as they dictate who bears the cost of shipping, insurance, and tariffs. This affects the total landed cost of the products.
What Negotiation Strategies Should International Buyers Consider?
For B2B buyers from Africa, South America, the Middle East, and Europe, effective negotiation can lead to significant cost savings. Here are some actionable strategies:
-
Understanding Total Cost of Ownership (TCO): Look beyond the initial purchase price. Consider logistics, maintenance, and operational costs when evaluating suppliers.
-
Establishing Long-Term Relationships: Building a strong rapport with suppliers can lead to better pricing and terms. Loyalty often results in discounts and priority service.
-
Leveraging Market Knowledge: Awareness of market trends and competitor pricing can provide leverage during negotiations. Buyers should conduct thorough research to inform their discussions.
-
Being Clear on Requirements: Clearly communicating specifications and expectations can prevent costly misunderstandings later in the process. This helps suppliers provide more accurate quotes.
-
Timing of Orders: Placing orders during off-peak seasons can sometimes yield better pricing, as manufacturers may be more willing to negotiate to fill production schedules.
Are There Pricing Nuances for International B2B Buyers?
International buyers must be aware of specific pricing nuances that can affect their sourcing decisions:
-
Currency Fluctuations: Exchange rates can significantly impact costs. Buyers should consider hedging strategies if sourcing from countries with volatile currencies.
-
Import Duties and Taxes: Understanding the local regulations regarding import duties can help buyers calculate the true cost of sourcing from a particular manufacturer.
-
Cultural Differences: Negotiation styles can vary by region. Understanding local customs and practices can enhance communication and facilitate smoother negotiations.
Disclaimer on Pricing Information
The prices discussed in this analysis are indicative and subject to change based on market conditions, supplier negotiations, and other variables. Buyers should always conduct their due diligence and obtain updated quotes before making purchasing decisions.
Alternatives Analysis: Comparing rubber manufacturer With Other Solutions
When exploring the landscape of rubber manufacturing, it is essential to consider viable alternatives that can achieve similar goals while meeting the unique needs of B2B buyers. This analysis will compare rubber manufacturers with other solutions, helping buyers make informed decisions based on performance, cost, ease of implementation, maintenance, and specific use cases.
Comparison Aspect | Rubber Manufacturer | Synthetic Rubber Production | Natural Rubber Sourcing |
---|---|---|---|
Performance | High durability and flexibility | Good performance but varies | Excellent elasticity and strength |
Cost | Higher initial investment | Generally lower production costs | Fluctuating costs due to supply |
Ease of Implementation | Requires specialized machinery | Easier setup for synthetic plants | Complex sourcing logistics |
Maintenance | Requires ongoing maintenance | Lower maintenance needs | Seasonal dependencies |
Best Use Case | Heavy-duty applications | General-purpose applications | Specialized applications |
What Are the Advantages and Disadvantages of Synthetic Rubber Production?
Synthetic rubber production involves the use of petrochemical feedstocks, resulting in a versatile material often used in tires, footwear, and various industrial applications. Pros include lower production costs and the ability to customize properties for specific applications, making it an attractive option for manufacturers looking to optimize performance. However, it may lack the durability and elasticity of natural rubber, which can be a significant drawback in applications requiring high flexibility and resilience.
How Does Natural Rubber Sourcing Compare to Rubber Manufacturing?
Natural rubber is derived from the sap of rubber trees, providing a renewable resource with outstanding mechanical properties. Its advantages include superior elasticity and tensile strength, making it ideal for specialized applications such as medical devices and high-performance tires. On the downside, sourcing natural rubber can be complex due to geographical limitations, seasonal availability, and fluctuating prices influenced by climate and market demand. This variability can impact supply chain reliability, making it less predictable for manufacturers.
How Should B2B Buyers Choose the Right Solution for Their Needs?
In conclusion, the choice between rubber manufacturers and alternative solutions such as synthetic rubber production or natural rubber sourcing depends on the specific requirements of the business. B2B buyers should carefully assess their application needs, budget constraints, and supply chain dynamics. For instance, if durability and performance are critical, investing in rubber manufacturing may be justified despite higher costs. Conversely, if cost-effectiveness and ease of implementation are priorities, synthetic rubber might be the better choice. Ultimately, understanding the strengths and weaknesses of each option will empower buyers to select the most suitable solution for their unique business challenges.
Essential Technical Properties and Trade Terminology for rubber manufacturer
What Are the Key Technical Properties of Rubber That Buyers Should Consider?
When sourcing rubber products, understanding the essential technical properties is crucial for making informed purchasing decisions. Here are some key specifications to consider:
1. Material Grade
Definition: Material grade refers to the classification of rubber based on its chemical composition and intended use. Common grades include natural rubber (NR), styrene-butadiene rubber (SBR), and ethylene propylene diene monomer (EPDM).
B2B Importance: Selecting the appropriate material grade is vital for ensuring that the rubber meets specific performance requirements, such as elasticity, temperature resistance, and chemical compatibility. This affects the longevity and functionality of the end product.
2. Hardness (Shore A)
Definition: Hardness is measured using the Shore A scale, which quantifies the resistance of rubber to indentation. A higher Shore A value indicates a harder rubber.
B2B Importance: Hardness affects the rubber’s flexibility and durability. Buyers must choose the right hardness level to suit their application, whether for tires, seals, or gaskets. This specification is critical for performance and product reliability.
3. Tensile Strength
Definition: Tensile strength measures the maximum amount of tensile (pulling) stress that a material can withstand before failing or breaking.
B2B Importance: High tensile strength is essential for applications that require durability and resistance to wear and tear. Understanding tensile strength helps buyers assess whether a rubber product will perform adequately under stress.
4. Elongation at Break
Definition: Elongation at break refers to the percentage increase in length a rubber material can withstand before it ruptures.
B2B Importance: A higher elongation at break indicates better stretchability, which is essential for products that must conform to specific shapes or endure significant movement. This property is crucial for applications like automotive parts and flexible seals.
5. Temperature Resistance
Definition: Temperature resistance indicates the range of temperatures that rubber can withstand without losing its mechanical properties.
B2B Importance: Buyers must ensure that the rubber products can operate effectively in the intended environmental conditions. This is particularly important in industries such as automotive and aerospace, where exposure to extreme temperatures is common.
What Are Common Trade Terms Used in the Rubber Manufacturing Industry?
Understanding industry jargon can facilitate smoother negotiations and transactions. Here are some common terms every B2B buyer should know:
1. OEM (Original Equipment Manufacturer)
Definition: OEM refers to a company that produces parts or equipment that may be marketed by another manufacturer.
B2B Importance: Recognizing OEM specifications ensures that the rubber products you purchase are compatible with existing equipment and meet industry standards.
2. MOQ (Minimum Order Quantity)
Definition: MOQ is the smallest quantity of a product that a supplier is willing to sell.
B2B Importance: Understanding MOQ helps buyers plan their purchasing strategies and manage inventory effectively. It’s essential for budgeting and ensuring that production requirements are met.
3. RFQ (Request for Quotation)
Definition: RFQ is a document sent to suppliers to request pricing and terms for specific products or services.
B2B Importance: Using RFQs enables buyers to compare offers from multiple suppliers, ensuring competitive pricing and favorable terms. It is a critical step in the procurement process.
4. Incoterms (International Commercial Terms)
Definition: Incoterms are a series of pre-defined commercial terms published by the International Chamber of Commerce (ICC) that clarify the responsibilities of buyers and sellers in international transactions.
B2B Importance: Familiarity with Incoterms helps buyers understand shipping costs, risks, and responsibilities, ensuring that all parties are aligned on the terms of delivery.
5. Lead Time
Definition: Lead time refers to the time taken from placing an order to receiving the product.
B2B Importance: Understanding lead times is crucial for planning and inventory management. Buyers should factor in lead times to avoid production delays and ensure timely delivery of products.

A stock image related to rubber manufacturer.
By grasping these technical properties and trade terms, international B2B buyers can enhance their procurement processes, minimize risks, and make informed decisions when sourcing rubber products.
Navigating Market Dynamics and Sourcing Trends in the rubber manufacturer Sector
What Are the Current Market Dynamics and Key Trends in the Rubber Manufacturing Sector?
The global rubber manufacturing market is experiencing robust growth, driven by increasing demand from various industries such as automotive, construction, and consumer goods. As international B2B buyers from regions like Africa, South America, the Middle East, and Europe seek to capitalize on this trend, understanding the underlying market dynamics becomes crucial. Key drivers include the rising production of electric vehicles, which require specialized rubber components, and the growing construction sector, particularly in emerging markets.
Emerging B2B technologies, including automation and Industry 4.0 practices, are reshaping sourcing trends. For instance, companies are increasingly adopting smart manufacturing techniques to enhance operational efficiency and reduce costs. Digital platforms are also becoming vital in streamlining procurement processes, allowing buyers to access a wider array of suppliers and negotiate better terms. Additionally, the shift towards circular economy principles is gaining traction, prompting manufacturers to innovate sustainable practices.
For buyers in regions like Egypt and Spain, the ability to navigate these trends is essential. By leveraging digital tools and focusing on sustainable sourcing, B2B buyers can enhance their competitive edge in the global marketplace.
How Does Sustainability and Ethical Sourcing Impact the Rubber Manufacturing Sector?
Sustainability has become a pivotal concern in the rubber manufacturing industry, significantly affecting sourcing strategies for B2B buyers. The environmental impact of rubber production, particularly in terms of deforestation and carbon emissions, is prompting companies to re-evaluate their supply chains. Ethical sourcing is increasingly important, as consumers and regulatory bodies demand transparency and accountability from manufacturers.
To address these challenges, many manufacturers are adopting sustainable practices, such as sourcing rubber from certified plantations that adhere to environmentally friendly practices. Certifications like the Forest Stewardship Council (FSC) and the Rainforest Alliance Certified seal are becoming essential for buyers aiming to ensure that their suppliers meet high sustainability standards. Furthermore, the use of alternative materials, such as synthetic rubber derived from renewable resources, is gaining popularity, allowing manufacturers to reduce their environmental footprint.
For international B2B buyers, particularly in emerging markets, prioritizing suppliers with sustainable certifications can enhance brand reputation and meet the growing demand for eco-friendly products. This not only aligns with global sustainability goals but also fosters long-term business relationships with ethically-minded manufacturers.
How Has the Rubber Manufacturing Sector Evolved Over Time?
The rubber manufacturing sector has undergone significant evolution over the last century, transitioning from traditional methods to advanced technological processes. Initially dominated by natural rubber sourced from tropical trees, the industry has seen a shift towards synthetic rubber due to advancements in chemical engineering and the need for more versatile materials.
The introduction of synthetic rubber in the mid-20th century allowed manufacturers to produce a wide range of products with improved durability and performance characteristics. This evolution has been further accelerated by globalization, which has opened new markets and diversified supply chains. Today, the sector is not only focused on meeting demand but also on addressing environmental challenges and adapting to changing consumer preferences.
Understanding this historical context can help B2B buyers appreciate the complexities of the rubber supply chain and the importance of choosing suppliers that are not only innovative but also committed to sustainability and ethical practices.
Frequently Asked Questions (FAQs) for B2B Buyers of rubber manufacturer
- How do I identify a reliable rubber manufacturer for my business needs?
To identify a reliable rubber manufacturer, start by researching their industry reputation through online reviews, testimonials, and case studies. Verify their certifications (e.g., ISO 9001) to ensure adherence to quality standards. Additionally, request references from previous clients and assess their ability to meet your specific requirements, such as product specifications, lead times, and customization options. Engaging in direct communication to discuss your needs can also help gauge their responsiveness and professionalism.
- What is the best way to assess the quality of rubber products from a manufacturer?
To assess the quality of rubber products, request product samples for testing and evaluation. Review the manufacturer’s quality assurance processes, including testing methods for durability, flexibility, and resistance to wear. Certifications from recognized standards organizations can also provide assurance of quality. Furthermore, consider visiting the manufacturing facility if possible, to observe production practices and quality control measures in place.
-
What are the common minimum order quantities (MOQs) for rubber products?
Minimum order quantities for rubber products can vary significantly based on the manufacturer and the type of product. Typically, MOQs range from 100 to several thousand units. It’s important to discuss your specific needs with the manufacturer, as some may offer flexibility in MOQs for new clients or larger orders. Understanding your own capacity for inventory and cash flow will help you negotiate terms that are favorable for both parties. -
What payment terms should I expect when dealing with international rubber manufacturers?
Payment terms with international rubber manufacturers can vary, but common practices include partial upfront payments (30-50%) with the balance due upon delivery or after a specified period. Some manufacturers may offer letters of credit or escrow services to protect both parties. Always clarify payment terms before finalizing contracts and ensure they align with your financial practices and capabilities. -
How can I ensure timely delivery of rubber products from manufacturers?
To ensure timely delivery, establish clear communication channels with the manufacturer regarding production timelines and shipping schedules. Consider incorporating penalties for delays in your contracts to encourage adherence to deadlines. Additionally, inquire about their logistics capabilities, including partnerships with reliable shipping companies, and track your orders throughout the shipping process to anticipate any potential issues.
-
What customization options are typically available when sourcing rubber products?
Many rubber manufacturers offer customization options, including variations in rubber compounds, colors, sizes, and designs. Discuss your specific requirements early in the conversation to understand the manufacturer’s capabilities. Some may provide prototyping services to develop tailored solutions, while others may have limitations based on their production processes. Ensure that any customizations align with your intended application and performance criteria. -
What quality assurance practices should I look for in a rubber manufacturer?
Look for manufacturers that implement rigorous quality assurance practices, such as regular inspections, testing of raw materials, and adherence to industry standards. Inquire about their quality management systems and whether they have third-party certifications. It’s beneficial if they have a dedicated quality control team responsible for overseeing production and addressing any defects or inconsistencies promptly. -
How do trade regulations affect sourcing rubber products from different regions?
Trade regulations can significantly impact sourcing rubber products, including tariffs, import/export restrictions, and compliance with local standards. Research the specific regulations applicable to the countries involved in your transactions, particularly if sourcing from or selling to regions like Africa, South America, the Middle East, and Europe. Engaging a trade compliance expert can help navigate these complexities and ensure adherence to all legal requirements.
Important Disclaimer & Terms of Use
⚠️ Important Disclaimer
The information provided in this guide, including content regarding manufacturers, technical specifications, and market analysis, is for informational and educational purposes only. It does not constitute professional procurement advice, financial advice, or legal advice.
While we have made every effort to ensure the accuracy and timeliness of the information, we are not responsible for any errors, omissions, or outdated information. Market conditions, company details, and technical standards are subject to change.
B2B buyers must conduct their own independent and thorough due diligence before making any purchasing decisions. This includes contacting suppliers directly, verifying certifications, requesting samples, and seeking professional consultation. The risk of relying on any information in this guide is borne solely by the reader.
Strategic Sourcing Conclusion and Outlook for rubber manufacturer
In today’s competitive landscape, strategic sourcing has emerged as a pivotal approach for international B2B buyers in the rubber manufacturing sector. By focusing on building strong supplier relationships and optimizing procurement processes, businesses can significantly enhance their operational efficiency and reduce costs. Key takeaways include the importance of understanding local market dynamics, leveraging technology for better supplier management, and fostering sustainable practices that resonate with consumers and regulatory bodies alike.
For buyers from Africa, South America, the Middle East, and Europe, particularly in regions like Egypt and Spain, the time to act is now. Engaging with reputable rubber manufacturers not only ensures a consistent supply of quality materials but also opens up avenues for innovation and collaboration. As the global demand for rubber products continues to rise, aligning your sourcing strategy with market trends will be crucial.
Embrace this opportunity to refine your sourcing practices, build resilient partnerships, and position your business for sustainable growth in the rubber industry. Take the first step today—evaluate your current suppliers, explore new markets, and commit to strategic sourcing that propels your business forward.