Discover Cost-Effective Solutions from Top Tube Manufacturers (2025)
Introduction: Navigating the Global Market for tube manufacturer
Navigating the complexities of sourcing high-quality tubes can be a daunting task for international B2B buyers, particularly those operating across diverse markets in Africa, South America, the Middle East, and Europe. With a multitude of manufacturers to choose from, understanding the nuances of materials, manufacturing processes, and compliance standards becomes critical. This guide aims to empower buyers by providing a comprehensive overview of tube manufacturing, including the various types of tubes available, their applications across industries, and essential criteria for supplier vetting.
Buyers will learn how to effectively assess production capabilities, quality certifications, and pricing structures, ensuring they make informed purchasing decisions. The guide also delves into regional considerations, highlighting specific challenges and opportunities in sourcing from different continents, including insights relevant to markets in Vietnam and Australia. By equipping buyers with actionable insights and expert analysis, this resource serves as a valuable tool for those looking to navigate the global tube manufacturing landscape confidently and strategically.
Ultimately, whether you’re seeking tubes for construction, automotive, or industrial applications, this guide will help streamline your sourcing process, mitigate risks, and enhance the quality of your supply chain.
Understanding tube manufacturer Types and Variations
Type Name | Key Distinguishing Features | Primary B2B Applications | Brief Pros & Cons for Buyers |
---|---|---|---|
Seamless Tube Manufacturers | Produced without seams, offering high strength and durability | Aerospace, automotive, oil & gas | Pros: High pressure resistance; Cons: Higher cost due to manufacturing complexity. |
Welded Tube Manufacturers | Made by welding flat strips of metal into a tube shape | Construction, HVAC, furniture | Pros: Cost-effective; Cons: Weaker than seamless tubes. |
Precision Tube Manufacturers | Focus on tight tolerances and specific dimensions | Medical devices, automotive components | Pros: High accuracy; Cons: Limited material types available. |
Stainless Steel Tube Manufacturers | Specialize in corrosion-resistant stainless steel tubes | Food processing, pharmaceuticals, chemical processing | Pros: Excellent durability; Cons: Can be expensive compared to other materials. |
Plastic Tube Manufacturers | Use various plastics to create lightweight, flexible tubes | Packaging, plumbing, electrical insulation | Pros: Lightweight and versatile; Cons: Less durable than metal options. |
What Are Seamless Tube Manufacturers and Their B2B Suitability?
Seamless tube manufacturers create products without seams, which enhances strength and durability. These tubes are particularly suitable for industries that require high pressure handling, such as aerospace and oil & gas. When purchasing seamless tubes, buyers should consider factors like material specifications, pressure ratings, and certification standards to ensure compliance with industry regulations.
How Do Welded Tube Manufacturers Operate in the B2B Space?
Welded tube manufacturers produce tubes by welding flat strips, making them a cost-effective option for various applications, particularly in construction and HVAC systems. Buyers should consider the weld quality, tube dimensions, and material specifications when sourcing welded tubes. While they are generally cheaper, welded tubes may not withstand as much pressure as seamless options, which is a critical factor in certain applications.
What Makes Precision Tube Manufacturers Unique for B2B Buyers?
Precision tube manufacturers focus on producing tubes with tight tolerances and specific dimensions, essential for applications in medical devices and automotive components. B2B buyers should prioritize manufacturers that can meet stringent quality standards and offer customization options. While precision tubes can be more expensive, their accuracy can lead to reduced waste and improved performance in specialized applications.
Why Choose Stainless Steel Tube Manufacturers for Your Business Needs?
Stainless steel tube manufacturers specialize in corrosion-resistant tubes, making them ideal for industries such as food processing and pharmaceuticals. Buyers should evaluate the grade of stainless steel, wall thickness, and finish when selecting suppliers. Although the initial investment may be higher, the long-term durability and resistance to corrosion often justify the costs, especially in critical applications.
What Are the Advantages of Working with Plastic Tube Manufacturers?
Plastic tube manufacturers produce lightweight and flexible tubes suitable for applications in packaging, plumbing, and electrical insulation. When purchasing plastic tubes, B2B buyers should assess the material type, temperature resistance, and compliance with safety regulations. While plastic tubes are generally more affordable, their lower durability compared to metal options may limit their use in high-stress environments.
Related Video: HME Coppper Tube Plant
Key Industrial Applications of tube manufacturer
Industry/Sector | Specific Application of Tube Manufacturer | Value/Benefit for the Business | Key Sourcing Considerations for this Application |
---|---|---|---|
Oil & Gas | Pipeline construction and maintenance | Enhanced safety and efficiency in transporting resources | Compliance with international standards and material specifications |
Automotive | Exhaust systems and fuel lines | Improved performance and durability in vehicles | Supplier reliability and material certifications |
Construction | Structural tubing for frameworks and scaffolding | Increased strength and stability of structures | Availability of custom sizes and corrosion resistance |
Medical Devices | Tubing for intravenous and respiratory applications | Ensured patient safety and product reliability | Regulatory compliance and material biocompatibility |
Aerospace | Fuel and hydraulic lines | High-performance and lightweight components | Precision engineering and adherence to aerospace standards |
How is Tube Manufacturing Used in the Oil & Gas Industry?
In the oil and gas sector, tube manufacturers provide essential products for pipeline construction and maintenance. These tubes must withstand extreme pressure and corrosive environments, ensuring safe transportation of crude oil and gas. International buyers from regions like Africa and the Middle East should prioritize suppliers that comply with stringent safety standards and offer materials that meet specific API (American Petroleum Institute) specifications. This ensures reliability and minimizes downtime, which is critical in this high-stakes industry.
What Are the Applications of Tubes in the Automotive Sector?
In the automotive industry, tubes are integral to the production of exhaust systems and fuel lines. Tube manufacturers supply components designed to improve vehicle performance and longevity under varying environmental conditions. Buyers, particularly from South America and Europe, should consider sourcing from manufacturers that provide robust quality assurance processes and certifications. This guarantees that the products can withstand high temperatures and pressures, thus enhancing overall vehicle safety and efficiency.
Why is Tube Manufacturing Important in Construction?
Construction applications often require structural tubing for frameworks and scaffolding. Tube manufacturers provide high-strength materials that contribute to the stability and safety of buildings and infrastructure projects. For international buyers in Europe or Africa, sourcing from manufacturers that offer custom sizes and corrosion-resistant options is vital. This flexibility allows for tailored solutions that meet specific project requirements, ultimately leading to safer and more durable constructions.
How Are Tubes Used in Medical Devices?
In the medical field, tubes are critical for applications like intravenous (IV) lines and respiratory devices. Tube manufacturers must ensure that their products meet strict regulatory standards and are made from biocompatible materials. International buyers, especially from developing regions, should focus on suppliers with a proven track record of compliance with health regulations. This is essential for ensuring patient safety and product efficacy, making it a priority for healthcare providers.
What Role Does Tube Manufacturing Play in Aerospace?
In the aerospace industry, tube manufacturers supply vital components such as fuel and hydraulic lines that must be lightweight yet extremely durable. These tubes must meet rigorous aerospace standards to ensure safety and performance at high altitudes. Buyers from Europe and the Middle East should seek manufacturers that specialize in precision engineering and have experience with aerospace applications. This focus on quality and compliance is essential to maintain the high safety standards required in aviation.
Related Video: Types Of Flowmeters And Their Industrial Applications.
3 Common User Pain Points for ‘tube manufacturer’ & Their Solutions
Scenario 1: Sourcing High-Quality Tubes for Specialized Applications
The Problem:
B2B buyers often encounter difficulties in sourcing tubes that meet specific industry standards and material requirements. For example, a manufacturer in the oil and gas sector may need corrosion-resistant tubes for offshore applications. However, many tube manufacturers do not provide detailed specifications or adequate certifications, leading to uncertainty about the product’s suitability. This can result in costly delays and project failures, especially in regions like Africa and South America, where local suppliers might not have the necessary expertise or quality control measures in place.
The Solution:
To effectively source high-quality tubes for specialized applications, buyers should start by clearly defining their specifications, including material type, dimensions, and applicable industry standards (e.g., ASTM, ISO). Next, leverage online platforms to research and compare different tube manufacturers, paying particular attention to those with a proven track record in your industry.
Engaging directly with potential suppliers for technical discussions can also yield valuable insights. Request detailed product data sheets and certificates of compliance to ensure they meet your requirements. Additionally, consider visiting the manufacturer’s facility if feasible or requesting a third-party audit report. This proactive approach not only mitigates risks but also builds a relationship with the supplier that can enhance future collaborations.
Scenario 2: Managing Lead Times and Delivery Schedules
The Problem:
Another common pain point for B2B buyers in the tube manufacturing industry is managing lead times and delivery schedules. Delays in the supply chain can disrupt production schedules, leading to increased costs and missed deadlines. For instance, a construction firm in the Middle East relying on imported tubes for a critical infrastructure project may find itself facing delays due to unforeseen circumstances such as shipping issues or production backlogs.
The Solution:
To manage lead times effectively, it is crucial to establish clear communication with your chosen tube manufacturer from the outset. Start by discussing your project timelines and delivery expectations during the initial negotiations. It is advisable to develop a buffer strategy by placing orders well in advance of your project’s needs.
Additionally, consider diversifying your supplier base to include multiple manufacturers across different regions. This strategy not only provides alternatives in case of delays but also enhances your bargaining power. Implementing a robust inventory management system can also help track usage rates and reorder points, ensuring you have enough stock on hand to avoid project interruptions.
Scenario 3: Ensuring Compliance with Local Regulations
The Problem:
B2B buyers often struggle with ensuring that the tubes they procure comply with local regulations and standards, which can vary significantly by region. For example, a buyer in Europe may face stringent environmental regulations that require tubes to be manufactured using sustainable practices and materials. Non-compliance can lead to legal repercussions, additional costs, and damage to reputation.
The Solution:
To navigate the complexities of compliance, it is essential for buyers to conduct thorough research on local regulations that pertain to tube manufacturing. This includes understanding both material compliance and manufacturing practices.
Engage with tube manufacturers who have experience in your target market and can provide documentation that demonstrates compliance with local standards. Request third-party certifications that validate adherence to environmental and safety regulations. Moreover, consider collaborating with legal experts or consultants familiar with local laws to ensure that your procurement processes are fully compliant. By being proactive about compliance, you can avoid potential pitfalls and maintain a positive reputation in your market.
Strategic Material Selection Guide for tube manufacturer
What Are the Key Properties of Common Materials Used in Tube Manufacturing?
When selecting materials for tube manufacturing, it is essential to understand the properties that influence product performance. Here, we analyze four commonly used materials: stainless steel, carbon steel, plastic (PVC), and copper. Each material has distinct characteristics that cater to specific applications and environments.
How Does Stainless Steel Perform in Tube Manufacturing?
Stainless steel is renowned for its excellent corrosion resistance, high strength, and ability to withstand extreme temperatures and pressures. It is often used in industries such as food processing, pharmaceuticals, and chemical manufacturing. The key properties of stainless steel include a temperature rating of up to 1,500°F (815°C) and pressure ratings that can exceed 10,000 psi, depending on the grade.
Pros: The durability and longevity of stainless steel make it a preferred choice for high-stress applications. It is also easy to clean, which is crucial in sanitary environments.
Cons: On the downside, stainless steel can be more expensive than other materials, and its manufacturing processes can be complex, requiring specialized equipment.
Impact on Application: Stainless steel is compatible with a wide range of media, including corrosive chemicals, making it suitable for diverse applications.
Considerations for International Buyers: Buyers from Africa, South America, the Middle East, and Europe should ensure compliance with international standards such as ASTM A312 or DIN 17440, which govern the quality and specifications of stainless steel tubes.
What Are the Advantages of Carbon Steel in Tube Manufacturing?
Carbon steel is another popular material for tube manufacturing, especially in construction and structural applications. It offers good tensile strength and is generally more cost-effective than stainless steel. Carbon steel tubes typically have a temperature rating of up to 800°F (427°C) and can handle moderate pressure ratings.
Pros: The primary advantage of carbon steel is its affordability and availability, making it an attractive option for large-scale projects.
Cons: However, carbon steel is prone to corrosion, which can limit its use in harsh environments unless properly coated or treated.
Impact on Application: Carbon steel is suitable for transporting water, oil, and gas, but it may not be ideal for corrosive substances.
Considerations for International Buyers: Compliance with standards such as ASTM A53 or API 5L is crucial for ensuring quality and safety in applications across different regions.
Why Choose Plastic (PVC) for Tube Manufacturing?
Plastic, particularly PVC (Polyvinyl Chloride), is increasingly used in tube manufacturing due to its lightweight and corrosion-resistant properties. PVC tubes can handle temperatures up to 140°F (60°C) and are suitable for low-pressure applications.
Pros: The primary advantage of PVC is its cost-effectiveness and ease of installation. It is also resistant to many chemicals, making it suitable for various applications.
Cons: However, PVC is not suitable for high-temperature applications and can become brittle over time when exposed to UV light.
Impact on Application: PVC is commonly used in plumbing, irrigation, and drainage systems, where it can efficiently transport water and other non-corrosive liquids.
Considerations for International Buyers: Buyers should look for compliance with standards such as ASTM D1784 and ensure that the PVC used is suitable for their specific application.
What Are the Benefits of Using Copper in Tube Manufacturing?
Copper is a traditional material known for its excellent thermal and electrical conductivity. It is often used in plumbing, HVAC systems, and electrical applications. Copper tubes can handle temperatures up to 400°F (204°C) and moderate pressure ratings.
Pros: The key advantage of copper is its antimicrobial properties, making it suitable for applications in healthcare and food processing.
Cons: However, copper is more expensive than other materials and can be susceptible to corrosion in certain environments.
Impact on Application: Copper is ideal for transporting hot water and steam, as well as in refrigeration applications.
Considerations for International Buyers: Compliance with standards such as ASTM B280 is essential for ensuring the quality and safety of copper tubes in various applications.
Summary Table of Material Selection for Tube Manufacturing
Material | Typical Use Case for Tube Manufacturer | Key Advantage | Key Disadvantage/Limitation | Relative Cost (Low/Med/High) |
---|---|---|---|---|
Stainless Steel | Food processing, pharmaceuticals | Excellent corrosion resistance | Higher cost and complex manufacturing | High |
Carbon Steel | Construction, structural applications | Cost-effective and widely available | Prone to corrosion without treatment | Medium |
Plastic (PVC) | Plumbing, irrigation, drainage | Lightweight and easy to install | Not suitable for high temperatures | Low |
Copper | Plumbing, HVAC systems | Antimicrobial properties | Higher cost and potential corrosion | High |
This guide provides actionable insights for international B2B buyers, aiding in the selection of the most suitable materials for tube manufacturing based on specific application needs and regional compliance requirements.
In-depth Look: Manufacturing Processes and Quality Assurance for tube manufacturer
What Are the Main Stages in Tube Manufacturing Processes?
The manufacturing of tubes involves several critical stages, each designed to ensure the final product meets the specific needs of B2B buyers. Understanding these stages is essential for international buyers looking to assess potential suppliers.
-
Material Preparation
The first step in tube manufacturing is material preparation, which involves selecting the right raw materials, typically metals like stainless steel, aluminum, or carbon steel. The materials undergo processes such as cutting, cleaning, and surface treatment to remove impurities and prepare them for forming. Buyers should inquire about the source and quality of materials, as these factors directly influence the durability and performance of the tubes. -
Forming
After preparation, the material is subjected to various forming techniques. Common methods include extrusion, rolling, and bending. Extrusion is particularly popular for producing tubes with consistent diameters and wall thicknesses. During this stage, the material is shaped into the desired form, ensuring that it aligns with the specifications provided by the buyer. It’s crucial for buyers to verify the forming techniques used by suppliers to ensure they are suitable for their applications. -
Assembly
In some cases, tube manufacturing may require assembly processes, particularly for complex tube structures or systems. This can involve welding, joining, or mechanically fastening various components. The assembly stage must be meticulously executed to maintain structural integrity, which is especially important for applications in industries such as oil and gas, where safety is paramount. -
Finishing
The final stage involves finishing processes, which enhance the tube’s appearance and performance. Techniques such as polishing, coating, or plating are employed to improve corrosion resistance and aesthetic appeal. Buyers should inquire about the finishing options available and how they impact the tube’s longevity and suitability for specific environments.
How Is Quality Assurance Integrated into Tube Manufacturing?
Quality assurance (QA) is a vital component in the tube manufacturing process, ensuring that the products meet international standards and buyer specifications. Here’s how QA is typically structured:
-
International Standards Compliance
Adhering to international quality standards such as ISO 9001 is fundamental for tube manufacturers. ISO 9001 sets the criteria for a quality management system, ensuring consistent quality in products and services. For B2B buyers, confirming that suppliers hold relevant certifications can serve as a reassurance of their commitment to quality. -
Industry-Specific Certifications
Depending on the application, specific certifications may be necessary. For instance, tubes used in the oil and gas industry may require API (American Petroleum Institute) certification, while those used in construction might need CE marking. Buyers should assess which certifications are applicable to their industry to ensure compliance with regulations and safety standards.
What Are the Key QC Checkpoints in Tube Manufacturing?
Quality control (QC) involves several checkpoints throughout the manufacturing process to identify and rectify issues before the final product is shipped. The primary QC checkpoints include:
-
Incoming Quality Control (IQC)
This initial checkpoint involves inspecting raw materials upon arrival at the manufacturing facility. IQC ensures that materials meet specified requirements and standards before they enter the production process. Buyers can request IQC reports to verify that the materials used in their tubes are of high quality. -
In-Process Quality Control (IPQC)
During the manufacturing process, IPQC is conducted to monitor the production stages. This includes regular inspections at various points, such as after forming and before assembly. By implementing IPQC, manufacturers can quickly identify defects or deviations from specifications, allowing for immediate corrective actions. -
Final Quality Control (FQC)
The FQC stage occurs after the manufacturing process is complete. Here, the final products are subjected to rigorous testing to ensure they meet all quality standards and specifications. Common testing methods include dimensional inspections, pressure tests, and non-destructive testing (NDT). B2B buyers should request FQC reports to confirm that the tubes meet their quality expectations.
How Can B2B Buyers Verify Supplier Quality Control?
For international B2B buyers, ensuring the quality of products is paramount. Here are several actionable steps to verify supplier QC:
-
Conduct Supplier Audits
Performing audits of potential suppliers can provide deep insights into their manufacturing processes and quality control measures. During an audit, buyers can assess the factory’s adherence to quality standards, equipment maintenance, and employee training. -
Request Detailed Quality Reports
Buyers should request comprehensive quality reports, including IQC, IPQC, and FQC data. These reports should outline the testing methods used, results, and any corrective actions taken in response to quality issues. -
Engage Third-Party Inspection Services
Utilizing third-party inspection services can provide an unbiased evaluation of the manufacturer’s quality control processes. These inspectors can conduct pre-shipment inspections, ensuring that products meet the required specifications before leaving the factory.
What Nuances Should International B2B Buyers Consider Regarding QC?
For buyers from regions such as Africa, South America, the Middle East, and Europe, understanding the nuances of QC in tube manufacturing is crucial:
-
Cultural and Regulatory Differences: Different regions may have varying expectations regarding quality and regulatory compliance. Buyers should familiarize themselves with local standards and practices to ensure alignment with supplier capabilities.
-
Communication Barriers: Language and cultural differences can lead to misunderstandings regarding quality expectations. Establishing clear communication channels and documentation can help mitigate these risks.
-
Supply Chain Dynamics: The global supply chain can affect the availability of materials and the consistency of quality. Buyers should consider the supplier’s sourcing practices and how they impact the quality of the final product.
In conclusion, a thorough understanding of the manufacturing processes and quality assurance practices in tube manufacturing is essential for international B2B buyers. By focusing on these aspects, buyers can make informed decisions and ensure they receive high-quality products that meet their specific needs.
Practical Sourcing Guide: A Step-by-Step Checklist for ‘tube manufacturer’
To successfully navigate the procurement process for tube manufacturing, it’s essential for international B2B buyers to follow a structured approach. This checklist provides actionable insights to ensure you make informed decisions when sourcing suppliers, particularly from regions like Africa, South America, the Middle East, and Europe.
Step 1: Define Your Technical Specifications
Clearly outline the technical requirements for the tubes you need. This includes dimensions, materials, tolerances, and any industry standards that must be met. Having detailed specifications helps in communicating your needs to potential suppliers and ensures that the products you receive will meet your operational requirements.
Step 2: Conduct Market Research
Investigate the tube manufacturing market to identify potential suppliers. Look for manufacturers with a strong reputation and experience in your specific industry. Utilize online databases, trade shows, and industry publications to gather information about various suppliers’ capabilities and product offerings.
Step 3: Evaluate Potential Suppliers
Before committing to a supplier, conduct a thorough evaluation. Request company profiles, product catalogs, and case studies to understand their manufacturing capabilities. Additionally, ask for references from other clients in similar industries to gauge reliability and product quality.
- Key Considerations:
- Manufacturing processes and technology
- Production capacity and lead times
- Quality assurance practices
Step 4: Verify Supplier Certifications
Ensure that the suppliers you are considering have the necessary certifications for quality management (e.g., ISO 9001) and compliance with industry standards. Certifications indicate a supplier’s commitment to maintaining quality and adhering to regulations, which is crucial in industries where safety and performance are paramount.
Step 5: Request Samples and Prototypes
Once you have shortlisted suppliers, request samples or prototypes of the tubes. This step allows you to assess the quality and performance of the products firsthand. Evaluate how well the samples meet your specifications and whether they are suitable for your application.
Step 6: Negotiate Terms and Pricing
Engage in discussions regarding pricing, payment terms, and delivery schedules with your chosen suppliers. Ensure that all terms are clearly outlined in a contract to avoid misunderstandings later. Consider factors such as bulk pricing, discounts for long-term contracts, and shipping costs when negotiating.
Step 7: Establish a Communication Plan
Set up a clear communication plan with your chosen supplier. Regular updates and feedback loops can help address any issues promptly and ensure that production stays on track. Effective communication fosters a strong partnership and can lead to better collaboration on future projects.
By following these steps, international B2B buyers can streamline the sourcing process for tube manufacturing, minimizing risks and ensuring they partner with reliable suppliers that meet their specific needs.
Comprehensive Cost and Pricing Analysis for tube manufacturer Sourcing
What Are the Key Cost Components for Tube Manufacturing?
When sourcing tubes from manufacturers, understanding the cost structure is crucial for making informed purchasing decisions. The main cost components include:
-
Materials: The type of raw materials used (e.g., steel, aluminum, plastic) significantly affects the overall cost. Higher-grade materials will increase expenses but may also enhance durability and performance.
-
Labor: Labor costs can vary significantly based on the region and the skill level required. In regions like Africa and South America, labor may be less expensive, potentially offering cost advantages.
-
Manufacturing Overhead: This includes expenses related to factory operations, such as utilities, rent, and administrative costs. Efficient operations can help minimize overhead, impacting pricing favorably.
-
Tooling: The costs associated with molds and tools for production can be substantial, especially for custom designs. Understanding these costs can help buyers negotiate better terms.
-
Quality Control (QC): Implementing rigorous QC measures ensures product reliability but can add to costs. Certifications (e.g., ISO, ASTM) may also incur additional expenses.
-
Logistics: Shipping, handling, and customs fees can vary widely, especially for international transactions. Buyers should account for these costs to get an accurate picture of total expenses.
-
Margin: Finally, the manufacturer’s profit margin will be factored into the pricing. This can depend on market conditions, competition, and the supplier’s pricing strategy.
How Do Price Influencers Impact Tube Manufacturing Costs?
Several factors can influence the pricing of tubes, making it essential for buyers to understand these dynamics:
-
Volume and Minimum Order Quantity (MOQ): Ordering in larger quantities often leads to lower per-unit costs. Buyers should negotiate MOQs to achieve better pricing.
-
Specifications and Customization: Custom specifications can drive up costs due to the need for specialized tooling or materials. Buyers should balance customization with cost-effectiveness.
-
Material Quality and Certifications: Higher quality materials and specific certifications can increase costs but may be necessary for certain applications. Buyers must weigh the benefits against the additional expense.
-
Supplier Factors: The reputation and reliability of a supplier can affect pricing. Established suppliers may charge a premium for their proven track record.
-
Incoterms: Understanding the Incoterms (International Commercial Terms) used in the transaction can impact total costs. For example, choosing FOB (Free on Board) may shift some shipping responsibilities and costs to the buyer.
What Are the Best Buyer Tips for Cost-Efficient Tube Sourcing?
To maximize value in tube sourcing, buyers should consider the following strategies:
-
Negotiation: Always negotiate pricing and terms. Suppliers may have flexibility in their pricing structures, especially for larger orders or long-term contracts.
-
Total Cost of Ownership (TCO): Consider not just the purchase price but the total cost of ownership, which includes maintenance, operational costs, and potential replacement costs over the product’s lifespan.
-
Understand Pricing Nuances for International Transactions: International buyers, particularly from Africa, South America, and the Middle East, should be aware of currency fluctuations, import tariffs, and shipping times that can influence overall costs.
-
Research and Compare Suppliers: Take the time to compare multiple suppliers. Look for manufacturers that offer transparency in their pricing and cost structures, which can help in making more informed decisions.
-
Stay Informed About Market Trends: Keeping up with market trends and material costs can provide leverage in negotiations and help anticipate price changes.
Disclaimer for Indicative Prices
While the information provided offers a framework for understanding costs and pricing in tube manufacturing, actual prices can vary based on numerous factors including market conditions, specific supplier agreements, and geographical considerations. Always request detailed quotes tailored to your specific needs before finalizing any procurement decisions.
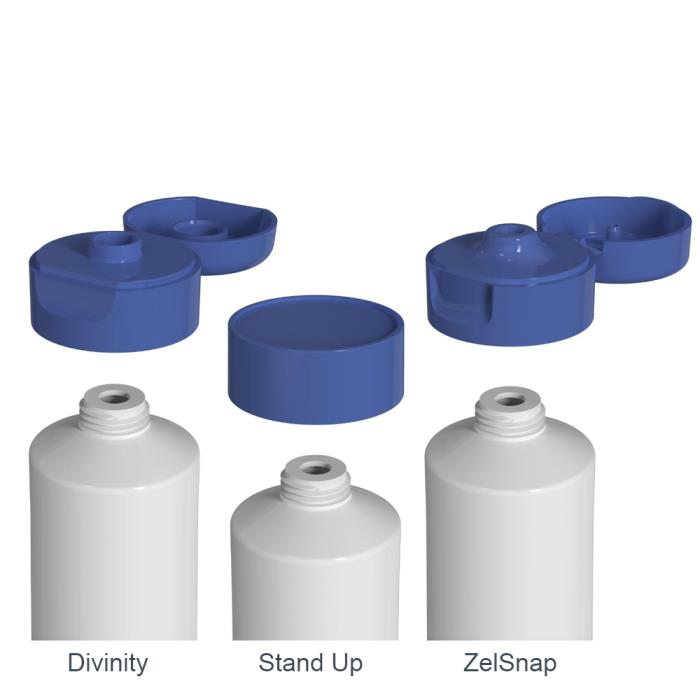
A stock image related to tube manufacturer.
Alternatives Analysis: Comparing tube manufacturer With Other Solutions
When evaluating options for sourcing or manufacturing tubes, B2B buyers must consider various alternatives that can meet their specific needs. The choice of solution can significantly impact performance, cost, and overall operational efficiency. Below, we compare ‘tube manufacturer’ with two viable alternatives: 3D Printing and Extrusion.
Comparison Aspect | Tube Manufacturer | 3D Printing | Extrusion |
---|---|---|---|
Performance | High precision and quality | Moderate, variable quality | High throughput and consistency |
Cost | Higher initial investment | Lower initial costs, but variable material costs | Moderate, depending on scale |
Ease of Implementation | Established processes | Requires skilled operators | Standardized machinery needed |
Maintenance | Routine checks required | Low, but depends on technology | Regular maintenance required |
Best Use Case | Large-scale production | Custom, low-volume production | Continuous production of standard shapes |
What Are the Pros and Cons of 3D Printing as an Alternative to Tube Manufacturing?
3D printing offers unique advantages, particularly in the realm of customization. This method allows for rapid prototyping and the ability to produce complex geometries without the need for extensive tooling. However, the quality can be inconsistent, especially for larger parts, and material costs can escalate depending on the requirements. Additionally, the need for skilled operators can complicate implementation.
How Does Extrusion Compare to Traditional Tube Manufacturing?
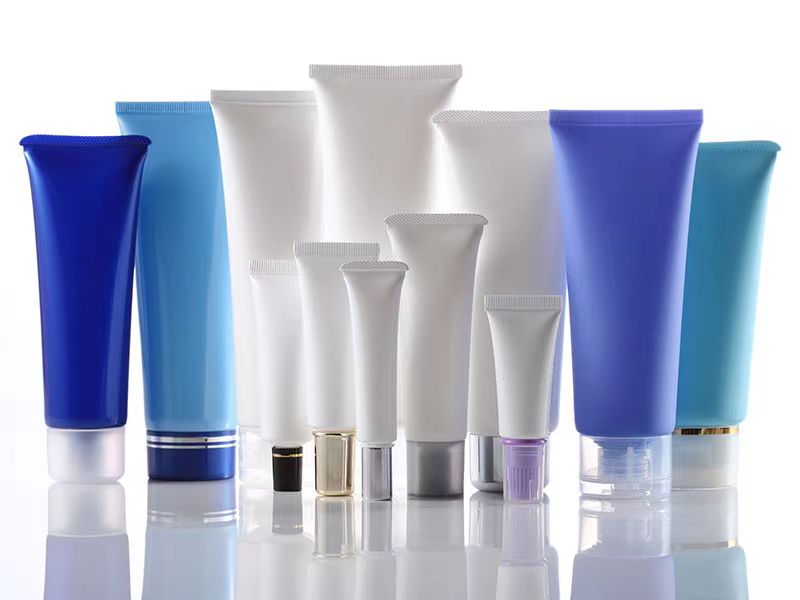
A stock image related to tube manufacturer.
Extrusion is a widely-used manufacturing process that excels in producing long lengths of uniform shapes. It offers high throughput and is often more cost-effective for large-scale production runs compared to traditional tube manufacturing. However, it typically lacks the flexibility for custom designs that 3D printing provides. Extrusion also requires regular maintenance to ensure machinery operates efficiently, which can lead to downtime if not managed properly.
Conclusion: How Can B2B Buyers Choose the Right Tube Manufacturing Solution?
Choosing the right solution for tube manufacturing depends on your specific operational needs and production scale. If high precision and quality are paramount for large-scale production, traditional tube manufacturing remains the best option. Conversely, if your focus is on customization and rapid iteration, 3D printing could be more suitable, albeit with some trade-offs in quality and cost. Finally, for businesses looking for a balance between cost and production speed, extrusion may present an ideal compromise. By carefully assessing these factors, B2B buyers from Africa, South America, the Middle East, and Europe can make informed decisions that align with their strategic goals.
Essential Technical Properties and Trade Terminology for tube manufacturer
What Are the Essential Technical Properties for Tube Manufacturing?
Understanding the technical specifications of tubes is crucial for international B2B buyers. These properties not only affect product performance but also influence pricing, manufacturing processes, and compliance with industry standards. Here are some key specifications to consider:
1. Material Grade: How Does It Impact Tube Quality?
Material grade is a critical specification that defines the composition and properties of the tube material, commonly metals like steel, aluminum, or plastic. Different grades offer varying strengths, corrosion resistance, and weight characteristics. For instance, a higher-grade steel tube will be more durable and suitable for high-pressure applications, making it essential for buyers to choose the right grade to meet their specific operational needs.
2. Tolerance: What Is Its Role in Manufacturing?
Tolerance refers to the permissible limit of variation in a tube’s dimensions. It is vital for ensuring that tubes fit correctly into their intended applications. Tight tolerances are essential in industries like aerospace and automotive, where precision is critical. Understanding tolerance levels helps buyers ensure compatibility with other components and reduces the risk of costly rework or failures.
3. Wall Thickness: Why Is It Important for Strength?
The wall thickness of a tube affects its structural integrity and ability to withstand pressure. Thicker walls generally provide greater strength and durability, making them suitable for high-stress applications. For international buyers, assessing wall thickness is crucial, especially in industries like oil and gas or construction, where safety and reliability are paramount.
4. Finish: How Does It Affect Performance?
The finish of a tube refers to its surface treatment, which can include processes like polishing, anodizing, or coating. A good finish enhances corrosion resistance and aesthetic appeal, which can be vital in consumer-facing applications. Buyers should consider the finish required for their specific use case to ensure long-lasting performance and compliance with industry standards.
5. Length and Diameter: What Are Their Implications for Use?
Length and diameter specifications determine how the tubes will fit into designs and applications. Custom lengths and diameters may be required for specific projects, so buyers must communicate their needs clearly to manufacturers. Understanding standard sizes and the implications of custom orders can significantly affect lead times and costs.
What Are Common Trade Terms in Tube Manufacturing?
Familiarity with industry jargon can streamline communication between buyers and manufacturers. Here are some essential trade terms:
1. OEM (Original Equipment Manufacturer): What Does It Mean?
OEM refers to companies that produce parts or equipment that may be marketed by another manufacturer. In the tube manufacturing sector, OEMs often supply tubes that are integrated into larger systems, making it essential for buyers to identify reputable OEM partners for quality assurance.
2. MOQ (Minimum Order Quantity): Why Is It Significant?
MOQ defines the smallest quantity of product a supplier is willing to sell. Understanding MOQ is crucial for buyers, especially smaller businesses that may not need large quantities. It can also impact pricing and negotiation strategies, as higher volumes often lead to discounts.
3. RFQ (Request for Quotation): How Should It Be Used?
An RFQ is a document issued by a buyer to solicit price quotes from suppliers. Crafting a clear RFQ can help buyers receive accurate pricing and terms. Including detailed specifications like material grade, dimensions, and tolerances can ensure suppliers provide the most relevant quotes.
4. Incoterms (International Commercial Terms): What Do They Cover?
Incoterms are a set of international rules that define the responsibilities of sellers and buyers for the delivery of goods. Understanding Incoterms helps international buyers clarify shipping costs, risks, and responsibilities, which is essential for effective logistics planning.
5. Lead Time: Why Is It Critical for Project Planning?
Lead time refers to the amount of time from placing an order to receiving the goods. For international buyers, understanding lead times is vital for project scheduling and avoiding delays. It’s advisable to confirm lead times during the ordering process to ensure timely delivery.
By grasping these technical properties and trade terms, international B2B buyers can make informed decisions, enhancing their procurement strategies and fostering successful partnerships with tube manufacturers.
Navigating Market Dynamics and Sourcing Trends in the tube manufacturer Sector
What Are the Current Market Dynamics and Key Trends in the Tube Manufacturing Sector?
The global tube manufacturing market is experiencing significant transformations driven by several key factors. The demand for lightweight and durable materials has surged, particularly in industries such as automotive, construction, and medical devices. In addition, the rise of e-commerce has led to an increased need for innovative packaging solutions, prompting tube manufacturers to explore advanced materials and technologies. This evolution is particularly noticeable among international B2B buyers in Africa, South America, the Middle East, and Europe, who are seeking high-quality products that can meet stringent regulatory standards.
Emerging technologies such as Industry 4.0, IoT (Internet of Things), and AI (Artificial Intelligence) are reshaping the sourcing landscape. These technologies enable manufacturers to optimize production processes, improve supply chain transparency, and enhance customer engagement. For buyers, this translates into opportunities for better pricing, faster delivery times, and customized solutions. Additionally, sustainability is becoming a crucial element in supplier selection, with companies increasingly favoring those that demonstrate eco-friendly practices and innovations.
How Is Sustainability Influencing Sourcing Trends in Tube Manufacturing?
The importance of sustainability in the tube manufacturing sector cannot be overstated. Environmental concerns related to plastic waste and resource depletion are prompting manufacturers to adopt sustainable practices. Buyers from regions such as Africa and Europe are increasingly prioritizing suppliers who utilize recycled materials and implement waste reduction strategies. This shift is not only beneficial for the planet but also aligns with consumer preferences for greener products.
Ethical sourcing is another critical aspect, as businesses are held accountable for their supply chain practices. B2B buyers are now more likely to engage with manufacturers that can provide transparency about their sourcing methods, labor practices, and environmental impact. Certifications such as ISO 14001 (Environmental Management) and FSC (Forest Stewardship Council) are becoming essential for manufacturers seeking to establish credibility in the market. By focusing on sustainability and ethical sourcing, international buyers can not only enhance their brand reputation but also mitigate risks associated with regulatory compliance and supply chain disruptions.
What Is the Historical Context of Tube Manufacturing for B2B Buyers?
The tube manufacturing industry has evolved significantly over the past century, transitioning from traditional methods to advanced technologies. Initially, production processes were labor-intensive and relied heavily on manual labor. However, the introduction of automation and high-precision machinery has revolutionized manufacturing efficiency and product quality.
In the last few decades, globalization has further transformed the sector, allowing for the establishment of extensive supply chains and access to a broader range of materials. This evolution has been particularly beneficial for international B2B buyers, who can now source products from various regions, ensuring competitive pricing and diverse options. As the industry continues to innovate, understanding its historical context is vital for buyers looking to navigate current trends and leverage emerging opportunities effectively.
Frequently Asked Questions (FAQs) for B2B Buyers of tube manufacturer
-
How do I find a reliable tube manufacturer for international sourcing?
Finding a reliable tube manufacturer involves thorough research and vetting. Start by identifying potential suppliers through industry directories, trade shows, or online marketplaces. Evaluate their credibility by checking certifications (such as ISO), customer reviews, and their track record with international clients. Engage in direct communication to assess their responsiveness and willingness to provide references. Conducting factory visits or third-party inspections can further ensure the manufacturer meets your quality and operational standards. -
What are the key factors to consider when vetting a tube manufacturer?
When vetting a tube manufacturer, consider factors such as quality control processes, production capacity, experience in your specific industry, and adherence to international standards. Assess their supply chain reliability, lead times, and flexibility in meeting custom orders. Additionally, inquire about their financial stability and reputation within the industry to minimize risks associated with international trade. -
What is the minimum order quantity (MOQ) for tube manufacturing?
Minimum order quantities (MOQ) for tube manufacturing can vary significantly based on the manufacturer, material, and customization required. Generally, MOQs can range from a few hundred to several thousand units. It’s essential to discuss your specific needs with potential suppliers, as many manufacturers may offer flexibility for first-time buyers or smaller companies. Understanding the MOQ will help you gauge pricing and production capabilities effectively. -
What are the common payment terms for international tube suppliers?
Payment terms for international tube suppliers typically include options like advance payment, letters of credit, or payment upon delivery. Most suppliers may require a deposit (often 30-50%) upfront, with the balance due before shipment. It’s crucial to negotiate favorable terms that balance risk and cash flow. Additionally, consider using secure payment methods to protect your financial interests in international transactions. -
How can I ensure quality assurance when sourcing tubes internationally?
To ensure quality assurance when sourcing tubes internationally, request detailed quality control documentation from the manufacturer, including inspection reports and certifications. Consider implementing a pre-shipment inspection by a third-party quality assurance firm to verify product specifications and compliance with standards. Establishing clear communication regarding quality expectations and conducting regular audits can also help maintain consistent product quality. -
What logistics considerations should I keep in mind when importing tubes?
When importing tubes, consider logistics aspects such as shipping methods, freight costs, and customs regulations. Choose a reliable logistics partner experienced in international shipping to navigate potential challenges, such as delays or compliance issues. Be aware of tariffs, duties, and necessary documentation required for customs clearance in your destination country. Planning your logistics strategy can optimize delivery times and costs. -
How can I customize tube specifications to fit my needs?
Customizing tube specifications involves collaborating closely with your manufacturer to define your specific requirements, including dimensions, materials, and coatings. Provide detailed drawings or prototypes to ensure clarity in your expectations. Most manufacturers are equipped to handle custom orders, but it’s essential to discuss lead times and any additional costs associated with customization. Establishing a clear communication channel will facilitate a smoother design and production process. -
What are the advantages of sourcing tubes from manufacturers in Africa, South America, or the Middle East?
Sourcing tubes from manufacturers in Africa, South America, or the Middle East can offer several advantages, such as competitive pricing, access to local materials, and reduced shipping times within those regions. Additionally, these areas may provide unique products tailored to specific regional needs or environmental conditions. Engaging with local manufacturers can also foster stronger relationships and support community development, enhancing your company’s corporate social responsibility initiatives.
Important Disclaimer & Terms of Use
⚠️ Important Disclaimer
The information provided in this guide, including content regarding manufacturers, technical specifications, and market analysis, is for informational and educational purposes only. It does not constitute professional procurement advice, financial advice, or legal advice.
While we have made every effort to ensure the accuracy and timeliness of the information, we are not responsible for any errors, omissions, or outdated information. Market conditions, company details, and technical standards are subject to change.
B2B buyers must conduct their own independent and thorough due diligence before making any purchasing decisions. This includes contacting suppliers directly, verifying certifications, requesting samples, and seeking professional consultation. The risk of relying on any information in this guide is borne solely by the reader.
Strategic Sourcing Conclusion and Outlook for tube manufacturer
The significance of strategic sourcing in the tube manufacturing sector cannot be overstated. As international B2B buyers from regions such as Africa, South America, the Middle East, and Europe navigate complex supply chains, a well-defined sourcing strategy becomes essential for optimizing costs and ensuring quality. By leveraging local suppliers and maintaining robust relationships with manufacturers, businesses can mitigate risks associated with supply disruptions and price volatility.
Furthermore, understanding market trends and regional demands will empower buyers to make informed decisions, enhancing their competitive edge. For instance, incorporating sustainable practices in sourcing not only aligns with global standards but also appeals to environmentally-conscious consumers, thus opening up new market opportunities.
As we look ahead, the landscape of tube manufacturing will evolve with advancements in technology and shifts in consumer preferences. International B2B buyers are encouraged to adopt a proactive approach—investing in market research, embracing digital tools for supply chain management, and fostering innovation within their sourcing strategies. Engaging with a diverse range of suppliers will not only enhance supply chain resilience but also drive business growth in an increasingly interconnected global market.