Discover Cost-Effective Solutions: Kitchen Utensil Manufacturer (2025)
Introduction: Navigating the Global Market for kitchen utensil manufacturer
In today’s dynamic global marketplace, sourcing high-quality kitchen utensils is a complex challenge that international B2B buyers face. With the rising demand for innovative cooking solutions and the diverse culinary traditions across regions, manufacturers must navigate a myriad of options to find the right suppliers. This guide serves as a comprehensive resource for B2B buyers, particularly those from Africa, South America, the Middle East, and Europe, looking to streamline their sourcing process for kitchen utensils.
Our extensive exploration covers various types of kitchen utensils, their applications in both residential and commercial settings, and essential factors to consider when vetting suppliers. By providing insights into cost structures, material sourcing, and compliance with international standards, this guide empowers buyers to make informed purchasing decisions.
Additionally, we delve into strategies for negotiating contracts and building long-lasting relationships with manufacturers. Whether you are a retailer seeking to expand your product line or a restaurant owner aiming for efficiency in your kitchen, understanding the global market for kitchen utensil manufacturing is crucial.
By the end of this guide, you will have the tools and knowledge necessary to navigate the complexities of sourcing kitchen utensils, ultimately helping your business thrive in an increasingly competitive landscape.
Understanding kitchen utensil manufacturer Types and Variations
Type Name | Key Distinguishing Features | Primary B2B Applications | Brief Pros & Cons for Buyers |
---|---|---|---|
Mass Production Manufacturers | High-volume production capabilities, standardized designs | Retail chains, large-scale food service providers | Pros: Lower costs, consistent quality. Cons: Limited customization options. |
Custom Kitchen Utensil Manufacturers | Tailored designs, flexible production runs | Specialty retailers, niche markets | Pros: Unique products, personalized service. Cons: Higher costs, longer lead times. |
Eco-Friendly Utensil Manufacturers | Sustainable materials, environmentally-conscious practices | Health-conscious brands, eco-friendly retailers | Pros: Appeals to eco-conscious consumers, brand differentiation. Cons: Potentially higher prices, limited material availability. |
Small Batch Artisanal Manufacturers | Handmade products, unique craftsmanship | Gourmet shops, high-end restaurants | Pros: High quality, unique offerings. Cons: Higher prices, inconsistent supply. |
Technology-Driven Manufacturers | Use of advanced technology and automation | Tech-oriented kitchen brands, modern restaurants | Pros: Innovation, efficiency. Cons: Higher initial investment, potential tech dependency. |
What Are the Characteristics of Mass Production Manufacturers?
Mass production manufacturers are characterized by their ability to produce large quantities of kitchen utensils at a lower cost. They often utilize standardized designs and automated processes, making them ideal for retailers and large-scale food service providers. When considering B2B purchases from these manufacturers, buyers should evaluate the consistency of quality, price competitiveness, and the ability to meet large orders swiftly. However, buyers may find limited options for customization, which could be a drawback for brands seeking unique products.
How Do Custom Kitchen Utensil Manufacturers Differ?
Custom kitchen utensil manufacturers focus on creating tailored designs that meet specific client needs. They offer flexibility in production runs, making them suitable for specialty retailers and niche markets. B2B buyers should consider the potential for unique branding opportunities and personalized service when working with these manufacturers. However, the trade-off often includes higher costs and longer lead times, which may not align with all business models.
Why Choose Eco-Friendly Utensil Manufacturers?
Eco-friendly utensil manufacturers prioritize sustainable materials and environmentally-conscious practices. This type of manufacturer is increasingly relevant as consumer demand shifts toward sustainable products. B2B buyers can leverage eco-friendly utensils to appeal to health-conscious brands and retailers looking to differentiate themselves in the market. While these products can command higher prices, they also offer an opportunity for brands to enhance their corporate social responsibility profile.
What Are the Benefits of Small Batch Artisanal Manufacturers?
Small batch artisanal manufacturers produce handmade kitchen utensils that often feature unique craftsmanship. They cater to gourmet shops and high-end restaurants, making them a good fit for businesses that prioritize quality and uniqueness. B2B buyers should consider the artisanal appeal and the potential for high-margin products. However, they must also be aware of the higher prices and potential inconsistencies in supply that can arise from small-scale production.
How Do Technology-Driven Manufacturers Innovate?
Technology-driven manufacturers utilize advanced technology and automation to enhance efficiency in their production processes. They are particularly suited for tech-oriented kitchen brands and modern restaurants looking to stay ahead of the curve. B2B buyers should evaluate the innovative features offered and the potential for long-term cost savings. However, it is crucial to consider the higher initial investment and the potential risks associated with technology dependency.
Related Video: List Of Kitchen Utensils | 150 + Kitchen Equipments List With Name And Picture | Kitchen Vocabulary
Key Industrial Applications of kitchen utensil manufacturer
Industry/Sector | Specific Application of Kitchen Utensil Manufacturer | Value/Benefit for the Business | Key Sourcing Considerations for this Application |
---|---|---|---|
Food Service Industry | Custom kitchen utensils for restaurants | Enhances efficiency and consistency in food preparation | Material quality, durability, and compliance with safety standards |
Hospitality Sector | Bulk kitchen utensils for hotels and catering services | Streamlines operations and meets high-volume demands | Cost-effectiveness, design variety, and supplier reliability |
Retail and E-commerce | Private label kitchen utensils | Increases brand loyalty and market differentiation | Minimum order quantities, customization options, and lead times |
Educational Institutions | Kitchen utensils for culinary schools | Provides practical training tools for students | Ergonomic design, safety features, and educational alignment |
Food Processing Industry | Specialized utensils for food manufacturing | Ensures efficiency and compliance with hygiene standards | Compliance with food safety regulations and material certifications |
How are Kitchen Utensils Applied in the Food Service Industry?
In the food service industry, kitchen utensil manufacturers provide custom utensils tailored to the specific needs of restaurants and catering businesses. These utensils enhance efficiency in food preparation, allowing chefs to perform tasks consistently and quickly. International B2B buyers must consider the quality of materials used, durability under high usage, and compliance with local safety standards. Sourcing from manufacturers that offer a range of custom designs can significantly improve operational workflows.
What are the Benefits of Kitchen Utensils in the Hospitality Sector?
In the hospitality sector, bulk kitchen utensils are essential for hotels and catering services, where high-volume food preparation is the norm. Manufacturers supply durable, functional tools that streamline operations, ensuring that service remains efficient even during peak hours. For buyers, cost-effectiveness is crucial, alongside the reliability of suppliers to meet large orders on time. Ensuring that utensils are designed for heavy use can lead to long-term cost savings and improved guest experiences.
How Do Private Label Kitchen Utensils Impact Retail and E-commerce?
Private label kitchen utensils allow retail and e-commerce businesses to create unique brand identities. By partnering with kitchen utensil manufacturers, retailers can offer differentiated products that foster brand loyalty among consumers. Buyers should focus on minimum order quantities that align with their sales forecasts, as well as customization options that meet market trends. Additionally, understanding lead times for production and shipping can help manage inventory effectively.
Why are Kitchen Utensils Important for Educational Institutions?
Culinary schools rely on high-quality kitchen utensils to provide students with hands-on training experiences. Manufacturers supply ergonomic, safe, and durable utensils that help students learn essential cooking techniques. Buyers in this sector should prioritize utensils that adhere to safety features and educational standards, ensuring that students receive the best practical training. Collaborating with manufacturers that understand educational needs can enhance the learning experience.
How are Specialized Utensils Used in the Food Processing Industry?
In the food processing industry, specialized kitchen utensils are critical for ensuring hygiene and efficiency in food manufacturing processes. Manufacturers provide tools that meet stringent food safety regulations, which are essential for compliance and quality assurance. International B2B buyers must consider the certifications and material safety data sheets when sourcing these utensils. Investing in high-quality, compliant tools can significantly reduce operational risks and enhance product quality.
Related Video: Types of Kitchen Knives and Their Uses
3 Common User Pain Points for ‘kitchen utensil manufacturer’ & Their Solutions
Scenario 1: Supply Chain Disruptions Affecting Kitchen Utensil Availability
The Problem: International B2B buyers often face significant challenges due to disruptions in the supply chain, particularly for kitchen utensils sourced from manufacturers. Factors such as political instability, natural disasters, or global pandemics can lead to unexpected delays and shortages. This situation can severely impact the operations of restaurants, catering services, and retail outlets, resulting in lost revenue and dissatisfied customers.
The Solution: To mitigate the risk of supply chain disruptions, buyers should establish strong relationships with multiple kitchen utensil manufacturers across different regions. Diversifying the supply base can help cushion against localized disruptions. Additionally, implementing robust inventory management systems that utilize real-time data analytics can help businesses forecast demand and adjust orders accordingly. Regularly reviewing supplier performance and maintaining open lines of communication can further enhance the resilience of the supply chain, ensuring a steady supply of essential kitchen utensils.
Scenario 2: Inconsistent Quality Across Kitchen Utensil Products
The Problem: Quality inconsistency is a common pain point for B2B buyers who deal with kitchen utensil manufacturers. Variations in product quality can arise from differences in manufacturing processes, materials used, and quality control measures. This inconsistency can lead to customer complaints, returns, and ultimately damage to the buyer’s brand reputation.
The Solution: To address quality inconsistencies, buyers should prioritize working with manufacturers that have established and certified quality assurance processes, such as ISO certifications. Conducting thorough due diligence, including factory visits and audits, can help buyers assess the manufacturing capabilities and quality control protocols of potential suppliers. Additionally, implementing a clear product specification guide that outlines exact quality standards can ensure that all products meet the required criteria. Establishing a feedback loop with manufacturers to discuss quality issues and improvements can also enhance product consistency over time.
Scenario 3: Difficulty in Customizing Kitchen Utensils to Meet Local Preferences
The Problem: B2B buyers often struggle with the challenge of offering kitchen utensils that cater to local culinary traditions and preferences. This can be particularly true for buyers in diverse regions like Africa and South America, where local cooking practices may require specialized utensils that are not readily available from standard manufacturers.
The Solution: To effectively customize kitchen utensils for local markets, buyers should engage in collaborative product development with manufacturers. This involves sharing insights about local culinary practices and preferences, which can guide the design of specialized utensils. Establishing a flexible manufacturing agreement that allows for product modifications and small-batch production can also help meet specific local demands. Furthermore, conducting market research to understand consumer preferences and trends can inform the development of tailored kitchen utensil lines that resonate with local buyers, ultimately driving sales and enhancing customer satisfaction.
Strategic Material Selection Guide for kitchen utensil manufacturer
What Are the Key Properties of Stainless Steel for Kitchen Utensils?
Stainless steel is a popular choice for kitchen utensils due to its excellent resistance to corrosion, staining, and rust. It can withstand high temperatures, making it suitable for various cooking applications. The material typically has a temperature rating of up to 800°F (427°C), which is beneficial for utensils used in high-heat cooking environments.
Pros and Cons of Stainless Steel
The primary advantage of stainless steel is its durability; it is robust and can endure daily wear and tear. However, it can be more expensive than other materials, which may impact the overall cost of production. Manufacturing complexity is moderate, as stainless steel requires specific techniques for shaping and finishing. In terms of end-product suitability, stainless steel is compatible with a wide range of food media, but it can conduct heat, which may lead to hot handles.
Considerations for International B2B Buyers
For buyers in Africa, South America, the Middle East, and Europe, compliance with international standards such as ASTM and DIN is crucial. Additionally, preferences for eco-friendly materials are growing, so sourcing stainless steel that meets sustainability criteria can enhance marketability.
How Does Silicone Compare for Kitchen Utensils?
Silicone is another material gaining traction in the kitchen utensil market due to its flexibility and heat resistance. It can typically withstand temperatures from -40°F to 450°F (-40°C to 232°C), making it suitable for various cooking methods, including baking and stovetop cooking.
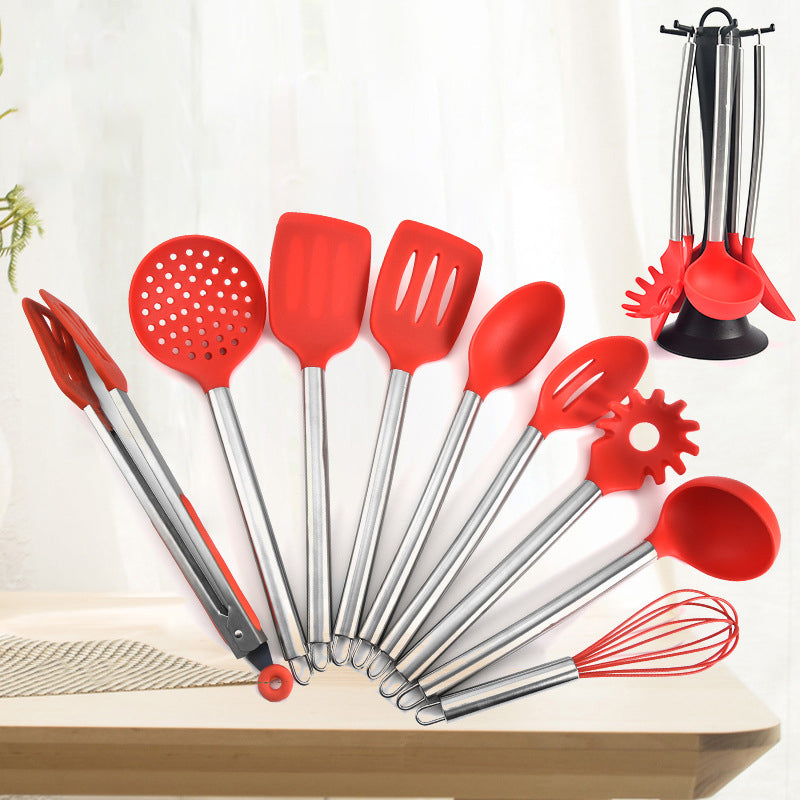
A stock image related to kitchen utensil manufacturer.
Pros and Cons of Silicone
The key advantage of silicone is its non-stick properties, which facilitate easy food release and cleaning. It is also lightweight and comes in various colors and designs, appealing to consumers. However, silicone may not be as durable as stainless steel, especially when subjected to sharp objects, which can lead to tearing. The manufacturing process for silicone can be complex, requiring specialized molds and curing processes.
Considerations for International B2B Buyers
Buyers should consider the FDA and EU regulations regarding food safety when sourcing silicone materials. Additionally, the growing demand for BPA-free products can influence purchasing decisions, especially in regions with strict consumer safety standards.
What Are the Advantages of Wood for Kitchen Utensils?
Wood has long been a traditional material for kitchen utensils, valued for its aesthetic appeal and functional properties. Wood is generally resistant to heat and does not conduct it as readily as metal, making it safe for use with non-stick cookware.
Pros and Cons of Wood
The primary advantage of wood is its natural insulating properties, which prevent heat transfer and protect users from burns. It is also biodegradable, making it an environmentally friendly option. However, wood can absorb moisture, leading to warping or cracking over time. The manufacturing complexity can be high, as it requires skilled craftsmanship to produce quality utensils.
Considerations for International B2B Buyers
When sourcing wooden utensils, compliance with international sustainability standards is essential. Buyers should also consider the type of wood used, as some species may be restricted or regulated in certain regions. Certifications like FSC (Forest Stewardship Council) can enhance credibility in the marketplace.
What Role Does Plastic Play in Kitchen Utensils?
Plastic is widely used in kitchen utensils due to its versatility and cost-effectiveness. It can be molded into various shapes and sizes, making it suitable for a broad range of products.
Pros and Cons of Plastic
The key advantage of plastic is its low cost and lightweight nature, which makes it easy to handle and store. However, plastic utensils may not withstand high temperatures, leading to deformation or melting. The manufacturing process is generally straightforward, but the quality can vary significantly based on the type of plastic used.
Considerations for International B2B Buyers
Buyers should prioritize sourcing plastics that comply with food safety standards, such as FDA regulations in the U.S. and similar standards in Europe. Additionally, the trend towards recyclable and biodegradable plastics is gaining momentum, especially in environmentally conscious markets.
Summary Table of Material Selection for Kitchen Utensil Manufacturers
Material | Typical Use Case for kitchen utensil manufacturer | Key Advantage | Key Disadvantage/Limitation | Relative Cost (Low/Med/High) |
---|---|---|---|---|
Stainless Steel | Cooking tools, cutlery | High durability and corrosion resistance | Higher cost than other materials | High |
Silicone | Baking mats, spatulas | Non-stick and flexible | Less durable against sharp objects | Medium |
Wood | Spoons, cutting boards | Natural insulation and aesthetic appeal | Prone to moisture absorption | Medium |
Plastic | Mixing spoons, measuring cups | Low cost and lightweight | May deform under high temperatures | Low |
In-depth Look: Manufacturing Processes and Quality Assurance for kitchen utensil manufacturer
What Are the Key Stages in the Manufacturing Process of Kitchen Utensils?
The manufacturing of kitchen utensils involves several critical stages that ensure both efficiency and product quality. Understanding these stages will empower B2B buyers to make informed decisions when selecting suppliers.
-
Material Preparation: The first step involves sourcing raw materials, which can include stainless steel, silicone, plastic, or wood. Suppliers should provide documentation regarding the material’s origin and compliance with international standards. For instance, stainless steel should ideally meet the ASTM (American Society for Testing and Materials) specifications to ensure durability and safety.
-
Forming: This stage involves shaping the materials into the desired forms using techniques such as injection molding for plastics, stamping for metals, or handcrafting for wooden utensils. Each technique has its benefits and limitations. For example, injection molding allows for high-volume production with precise designs, while handcrafting can offer unique, artisanal products that appeal to niche markets.
-
Assembly: After forming, the various components of kitchen utensils are assembled. This may involve mechanical fastening, welding, or adhesive bonding. It’s crucial for B2B buyers to inquire about the assembly techniques employed, as these can significantly affect the product’s overall strength and usability.
-
Finishing: The final stage includes processes like polishing, coating, or surface treatment to enhance the utensil’s aesthetics and functionality. For instance, non-stick coatings on pans or heat-resistant finishes on spatulas are common. Buyers should look for suppliers who can provide certifications for these finishes, ensuring they are safe for food contact.
How Is Quality Control Implemented in Kitchen Utensil Manufacturing?
Quality assurance is a vital aspect of the manufacturing process that ensures products meet specified standards and customer expectations. Understanding the quality control checkpoints can help B2B buyers assess potential suppliers effectively.
-
International Standards and Certifications: Suppliers should comply with international quality standards, such as ISO 9001, which focuses on quality management systems. In addition, industry-specific certifications like CE (Conformité Européenne) for products sold in Europe or FDA approval for food-safe materials are essential. Buyers should verify these certifications during the supplier evaluation process.
-
Quality Control Checkpoints: Effective quality control involves multiple checkpoints throughout the manufacturing process:
– Incoming Quality Control (IQC): This initial stage checks the quality of raw materials before production begins.
– In-Process Quality Control (IPQC): Continuous monitoring during the manufacturing process ensures that any deviations are addressed immediately.
– Final Quality Control (FQC): At this stage, finished products undergo rigorous testing to ensure they meet quality standards. -
Common Testing Methods: Various testing methods are employed to validate product quality. These may include:
– Mechanical Testing: Assessing the strength and durability of materials.
– Chemical Testing: Ensuring that materials are free from harmful substances and comply with safety regulations.
– Performance Testing: Evaluating how well the product performs under typical usage conditions.
How Can B2B Buyers Verify Supplier Quality Control Processes?
For B2B buyers, especially those sourcing from international markets, verifying a supplier’s quality control processes is critical for minimizing risks. Here are actionable steps to ensure quality assurance:
-
Conduct Supplier Audits: An on-site audit can provide a comprehensive view of the supplier’s manufacturing processes and quality control systems. This includes evaluating their compliance with international standards, inspecting production facilities, and assessing workforce training.
-
Request Quality Control Reports: Suppliers should provide regular quality control reports that detail their testing methods, results, and any corrective actions taken. Reviewing these documents can offer insights into the supplier’s commitment to quality.
-
Utilize Third-Party Inspection Services: Engaging third-party inspection services can offer an unbiased assessment of product quality before shipment. These services can conduct random sampling and testing to ensure compliance with agreed-upon specifications.
What Are the Quality Control Nuances for International B2B Buyers?
When sourcing kitchen utensils from regions like Africa, South America, the Middle East, and Europe, buyers must navigate specific nuances related to quality control.
-
Understanding Regional Standards: Different regions may have varying quality standards and certifications. For instance, products exported to the European market must comply with CE marking, while those entering the Middle Eastern market may require local regulatory approvals. Familiarizing oneself with these requirements is crucial for smooth market entry.
-
Cultural Considerations: Cultural differences can influence manufacturing practices and quality perceptions. Buyers should be aware of local practices that may affect quality, such as different approaches to labor and craftsmanship. Building relationships and trust with suppliers can lead to better communication and adherence to quality standards.
-
Logistics and Supply Chain Factors: The logistics involved in international trade can impact product quality. Delays in shipping or inadequate storage conditions may affect the integrity of kitchen utensils. B2B buyers should ensure that suppliers have robust logistics practices in place to maintain product quality throughout the supply chain.
Conclusion: Prioritizing Quality and Reliability in Kitchen Utensil Manufacturing
In the competitive landscape of kitchen utensil manufacturing, understanding the intricacies of manufacturing processes and quality assurance is essential for B2B buyers. By focusing on material selection, production techniques, and rigorous quality control practices, buyers can select reliable suppliers that meet their needs. Moreover, verifying quality standards and practices through audits, reports, and third-party inspections can significantly mitigate risks associated with international sourcing. As markets continue to evolve, staying informed about these manufacturing and quality assurance processes will empower buyers to make strategic decisions that align with their business goals.
Practical Sourcing Guide: A Step-by-Step Checklist for ‘kitchen utensil manufacturer’
In the competitive landscape of kitchen utensil manufacturing, international B2B buyers must adopt a systematic approach to sourcing. This guide provides a practical checklist designed to help you navigate the complexities of selecting the right kitchen utensil manufacturer. By following these steps, you can ensure that your procurement process is efficient, cost-effective, and aligned with your specific needs.
Step 1: Define Your Technical Specifications
Before you begin sourcing, it’s essential to have a clear understanding of your technical requirements. This includes the types of utensils you need, materials (e.g., stainless steel, silicone), and design specifications. Detailed specifications help narrow down potential suppliers and streamline communication, ensuring that you receive products that meet your quality standards.
Step 2: Research Potential Manufacturers
Conduct thorough research to identify manufacturers who specialize in kitchen utensils. Look for suppliers with a solid reputation in your target regions, such as Africa, South America, the Middle East, and Europe. Utilize platforms like Alibaba, Global Sources, or industry-specific trade shows to gather a list of potential candidates.
- Tip: Review online forums and industry publications for insights and reviews about manufacturers.
Step 3: Evaluate Supplier Certifications and Compliance
It’s crucial to verify that potential suppliers meet international quality standards and certifications, such as ISO 9001 or FDA approvals. This step not only ensures product quality but also compliance with safety regulations in your target market.
- Action: Request copies of relevant certifications and check their validity through official channels.
Step 4: Request Samples and Conduct Quality Checks
Before making a bulk order, always request samples of the products. This allows you to evaluate the quality of materials, craftsmanship, and design. Conduct a thorough quality check, assessing durability, usability, and compliance with your specifications.
- Insight: If possible, perform a comparative analysis of samples from different suppliers to make an informed decision.
Step 5: Negotiate Terms and Pricing
Once you have identified a suitable manufacturer, engage in negotiations regarding pricing, payment terms, and delivery schedules. Establish clear expectations to avoid misunderstandings later in the process.
- Important Note: Consider the total landed cost, which includes shipping, customs duties, and any additional fees, to ensure accurate budgeting.
Step 6: Establish a Communication Plan
Effective communication is key to a successful partnership. Set up regular check-ins to discuss progress, address concerns, and ensure alignment on production timelines. Utilize tools like video conferencing and project management software to maintain clear communication channels.
- Best Practice: Document all agreements and changes to avoid potential disputes.
Step 7: Monitor Production and Delivery
Stay involved during the production phase to ensure that timelines are met and quality standards are maintained. Request periodic updates and, if possible, conduct factory visits or audits. Once production is complete, verify the quality of the delivered products before final acceptance.
- Final Tip: Establish a contingency plan in case of delays or quality issues to minimize impact on your operations.
By following this step-by-step checklist, you can enhance your sourcing strategy for kitchen utensils and make informed decisions that align with your business objectives.
Comprehensive Cost and Pricing Analysis for kitchen utensil manufacturer Sourcing
What Are the Key Cost Components in Kitchen Utensil Manufacturing?
Understanding the cost structure of kitchen utensil manufacturing is essential for international B2B buyers looking to source competitively. The main cost components include:
-
Materials: The type and quality of materials used significantly impact the overall cost. For instance, stainless steel, silicone, and bamboo are popular choices, each carrying different price points. Sourcing high-quality materials can enhance product durability, which is crucial for buyers aiming for long-term partnerships.
-
Labor: Labor costs vary by region, influenced by local wage standards and workforce availability. Countries with lower labor costs might seem attractive, but it’s essential to consider the skill level of the workforce, which can affect product quality.
-
Manufacturing Overhead: This encompasses all indirect costs related to production, such as utilities, rent, and administrative expenses. Understanding these costs helps buyers gauge the overall pricing strategy of a manufacturer.
-
Tooling: Initial tooling costs can be substantial, especially for custom designs. Buyers should account for these costs when evaluating quotes, as they can significantly influence unit pricing.
-
Quality Control (QC): Implementing robust QC processes ensures that the products meet international standards, which can add to the manufacturing costs. However, investing in QC can prevent costly returns and enhance brand reputation.
-
Logistics: Shipping costs, customs duties, and warehousing can add a significant amount to the total cost. Buyers should consider the total logistics framework when selecting suppliers, especially for international shipments.
-
Margin: Manufacturers typically add a markup to cover their operational costs and profit margins. Understanding the standard margins in specific regions can help buyers negotiate better pricing.
How Do Price Influencers Impact Kitchen Utensil Sourcing?
Several factors influence the pricing of kitchen utensils, which buyers should consider to make informed decisions:
-
Volume and Minimum Order Quantity (MOQ): Larger orders often come with bulk pricing discounts. Buyers should evaluate their demand and negotiate MOQs that align with their sales forecasts.
-
Specifications and Customization: Customized products usually incur higher costs due to additional design and production complexities. Buyers must weigh the benefits of customization against the added expense.
-
Materials and Quality Certifications: Premium materials and certifications (like ISO or FDA compliance) can raise costs but may be necessary for specific markets. Buyers should assess the importance of certifications in their target markets.
-
Supplier Factors: The reputation, reliability, and location of the supplier can also influence pricing. Established manufacturers with a proven track record may command higher prices due to their reliability.
-
Incoterms: Understanding Incoterms (International Commercial Terms) is crucial for B2B buyers. They dictate who is responsible for shipping, insurance, and tariffs, which can significantly affect overall costs.
What Are the Best Negotiation Tips for International B2B Buyers?
Effective negotiation can lead to substantial cost savings. Here are several actionable tips for international buyers:
-
Conduct Thorough Market Research: Understanding the typical price range and cost components in your target regions can provide leverage during negotiations.
-
Evaluate Total Cost of Ownership (TCO): Consider all costs associated with the product, including shipping, customs duties, and potential quality-related expenses. This broader view can help justify price points.
-
Build Long-Term Relationships: Establishing a rapport with suppliers can lead to better pricing and terms over time. Consider negotiating contracts that encourage long-term partnerships.
-
Be Clear About Your Needs: Clearly communicate your specifications and expectations to avoid misunderstandings that could lead to additional costs.
-
Stay Flexible: Be willing to explore different suppliers or materials to find the best value. Flexibility can often lead to more favorable pricing.
Important Considerations for International Buyers
When sourcing kitchen utensils internationally, particularly from regions like Africa, South America, the Middle East, and Europe, it’s vital to be aware of market-specific nuances. Currency fluctuations, regional trade agreements, and local economic conditions can all influence pricing.
Buyers should remain vigilant and conduct regular market assessments to adapt their sourcing strategies accordingly. Additionally, be cautious of indicative prices provided by suppliers, as these can fluctuate based on changing market conditions and raw material costs.
Alternatives Analysis: Comparing kitchen utensil manufacturer With Other Solutions
Introduction: Exploring Alternatives to Kitchen Utensil Manufacturing
When considering kitchen utensils for B2B procurement, understanding the available alternatives to traditional manufacturing methods is crucial. This analysis provides insights into how different solutions stack up against the conventional kitchen utensil manufacturer. By evaluating performance, cost, ease of implementation, maintenance, and best use cases, international buyers can make informed decisions that align with their operational needs and market demands.
Comparison Table of Kitchen Utensil Solutions
Comparison Aspect | Kitchen Utensil Manufacturer | 3D Printing Technology | Outsourced Production (Asia) |
---|---|---|---|
Performance | High durability and quality | Moderate durability; design flexibility | High volume, consistent quality |
Cost | Moderate to high setup costs | Lower initial investment, variable material costs | Competitive pricing, shipping costs apply |
Ease of Implementation | Requires significant setup | Quick to implement, design-based | Longer lead times, dependency on suppliers |
Maintenance | Low maintenance if high quality | Limited maintenance; depends on material used | Maintenance varies by supplier |
Best Use Case | Custom, high-quality utensils | Prototyping, unique designs | Mass production of standard utensils |
What Are the Advantages and Disadvantages of 3D Printing Technology for Kitchen Utensils?
3D printing technology offers a modern alternative to traditional kitchen utensil manufacturing. One of its significant advantages is the ability to create custom designs quickly, allowing businesses to cater to niche markets or specific customer preferences. Moreover, the lower initial investment makes it accessible for startups or small businesses. However, the durability of 3D printed utensils may not match that of traditionally manufactured products, which can impact their long-term usability. Additionally, material costs can vary widely, potentially leading to higher expenses for specific designs.
Why Consider Outsourced Production in Asia for Kitchen Utensils?
Outsourced production, particularly in Asia, provides a highly competitive option for businesses looking to produce kitchen utensils at scale. The primary benefits include lower unit costs and the ability to mass-produce items to meet high demand. This method is ideal for businesses that require consistent quality across large volumes. However, buyers must consider longer lead times and the complexities of managing relationships with overseas suppliers. Additionally, shipping costs can add to the total expenditure, making it essential to factor these into the overall budget.
Conclusion: How to Choose the Right Kitchen Utensil Solution for Your Business
Selecting the appropriate kitchen utensil solution requires a careful assessment of your business’s unique needs. Consider your target market and production volumes when weighing the benefits of traditional manufacturing against alternatives like 3D printing or outsourced production. For instance, if you prioritize custom designs and quick prototyping, 3D printing may be the best fit. Conversely, for businesses aiming for mass production at a lower cost, outsourced production could be more advantageous. Ultimately, understanding these alternatives will empower B2B buyers from regions like Africa, South America, the Middle East, and Europe to make strategic purchasing decisions that align with their operational goals.
Essential Technical Properties and Trade Terminology for kitchen utensil manufacturer
What Are the Key Technical Properties Essential for Kitchen Utensil Manufacturing?
When sourcing kitchen utensils, understanding the technical properties is crucial for ensuring product quality and performance. Here are some critical specifications that every B2B buyer should consider:
-
Material Grade
– The material grade refers to the specific classification of the material used in production, such as stainless steel, silicone, or wood. Each material offers distinct advantages in terms of durability, heat resistance, and ease of cleaning. For instance, high-grade stainless steel is preferred for its resistance to corrosion and staining, making it suitable for long-term use in commercial kitchens. -
Tolerance
– Tolerance indicates the permissible limit of variation in the dimensions of a utensil. It is vital for ensuring that parts fit together properly and function as intended. Tight tolerances are particularly important for precision tools, like measuring cups and knives, where accuracy directly impacts usability and safety. -
Finish Type
– The finish type refers to the surface treatment applied to a utensil, which can affect aesthetics, safety, and functionality. Common finishes include brushed, polished, or matte. For instance, a non-stick coating can enhance usability but may require specific care to maintain its integrity over time. Understanding finish types helps buyers select products that meet their operational needs. -
Heat Resistance
– Heat resistance measures how well a material can withstand high temperatures without degrading or losing functionality. This property is especially important for utensils like spatulas and ladles that are often exposed to heat. Materials with high heat resistance can endure the rigors of cooking without warping or melting, ensuring longevity and safety. -
Weight
– The weight of a utensil impacts its handling and user experience. Heavier utensils may provide a sense of durability and stability, while lighter options can be easier to maneuver. Understanding the weight specifications helps in selecting products that align with the desired user experience, whether for home kitchens or industrial settings.
What Are Common Trade Terms in Kitchen Utensil Manufacturing?
Navigating the kitchen utensil manufacturing landscape requires familiarity with key trade terms. Here are some essential terms that B2B buyers should know:
-
OEM (Original Equipment Manufacturer)
– OEM refers to a company that produces parts or products that are used in another company’s end product. Buyers often work with OEMs to customize utensils according to their specifications. Understanding OEM relationships can help buyers ensure product quality and brand consistency. -
MOQ (Minimum Order Quantity)
– MOQ indicates the smallest number of units a supplier is willing to sell. This term is crucial for budgeting and inventory management, particularly for smaller businesses. Buyers must negotiate MOQs that align with their production needs while considering potential storage costs. -
RFQ (Request for Quotation)
– An RFQ is a formal request sent to suppliers to obtain price quotes for specific products or services. It is an essential step in the procurement process, allowing buyers to compare costs and make informed purchasing decisions. A well-structured RFQ can facilitate better negotiations and supplier relationships. -
Incoterms (International Commercial Terms)
– Incoterms are internationally recognized rules that define the responsibilities of buyers and sellers in international trade. Understanding these terms is crucial for managing shipping costs, risks, and delivery timelines. For instance, terms like FOB (Free On Board) or CIF (Cost, Insurance, and Freight) can significantly impact overall procurement strategies. -
Lead Time
– Lead time refers to the amount of time it takes from placing an order to receiving the goods. This metric is vital for supply chain planning and inventory management. Buyers must consider lead times when forecasting demand to ensure they have the necessary stock on hand.
Understanding these technical properties and trade terms will empower B2B buyers to make informed decisions when selecting kitchen utensils, ensuring product quality and operational efficiency.
Navigating Market Dynamics and Sourcing Trends in the kitchen utensil manufacturer Sector
What are the Key Market Dynamics and Sourcing Trends in the Kitchen Utensil Manufacturing Sector?
The kitchen utensil manufacturing sector is experiencing significant transformation driven by several global factors. Increasing urbanization, particularly in regions such as Africa and South America, is propelling demand for innovative kitchen solutions that cater to both functionality and aesthetic appeal. B2B buyers are now more inclined towards products that combine modern design with practical use, reflecting a shift in consumer preferences. Furthermore, advancements in manufacturing technologies, including automation and smart manufacturing, are enabling manufacturers to improve efficiency and reduce lead times, which is crucial for international buyers seeking quick turnaround times.
Emerging trends such as e-commerce integration and digital marketplaces are reshaping the sourcing landscape. Buyers from Europe and the Middle East are increasingly leveraging online platforms to source products, allowing for greater access to diverse suppliers and competitive pricing. Additionally, the rise of direct-to-consumer (DTC) brands is prompting traditional manufacturers to adapt their strategies, ensuring they remain relevant in a rapidly changing market. As a result, B2B buyers must be vigilant in identifying suppliers that not only meet quality standards but also possess the technological capabilities to thrive in this evolving landscape.
How is Sustainability and Ethical Sourcing Impacting Kitchen Utensil Manufacturing?
Sustainability and ethical sourcing have become paramount considerations for B2B buyers in the kitchen utensil manufacturing sector. The environmental impact of production processes, from raw material extraction to waste management, is under scrutiny. Buyers are increasingly prioritizing suppliers who adopt sustainable practices, such as using eco-friendly materials and implementing waste reduction strategies. This shift is not only beneficial for the planet but also enhances brand reputation and customer loyalty.
Certifications such as ISO 14001 for environmental management and the Forest Stewardship Council (FSC) label for wood products are gaining importance. B2B buyers should look for these certifications when selecting suppliers to ensure compliance with international sustainability standards. Additionally, the demand for biodegradable and recyclable materials is on the rise, pushing manufacturers to innovate in their product offerings. For buyers in Africa and South America, understanding local regulations related to sustainability can further enhance their sourcing strategies, ensuring they align with both global standards and regional expectations.
How Has the Kitchen Utensil Manufacturing Sector Evolved Over Time?
The kitchen utensil manufacturing sector has evolved significantly over the past few decades, transitioning from traditional craftsmanship to a more industrialized and technology-driven approach. Initially dominated by small-scale artisans, the sector has seen the rise of large manufacturers capable of mass production. This shift has allowed for greater consistency in product quality and availability, which is essential for B2B buyers requiring reliable supply chains.
Moreover, the globalization of trade has opened up new markets, enabling manufacturers to source materials and labor from different regions, often leading to cost efficiencies. As international trade agreements become more favorable, buyers from regions such as Europe and the Middle East can access a wider variety of products at competitive prices. This evolution reflects a broader trend in the B2B landscape, where adaptability and innovation are key to staying competitive in an ever-changing market.
Frequently Asked Questions (FAQs) for B2B Buyers of kitchen utensil manufacturer
-
How do I evaluate a kitchen utensil manufacturer for quality assurance?
To evaluate a kitchen utensil manufacturer, first, assess their certifications, such as ISO 9001 or other relevant industry standards that indicate adherence to quality management practices. Request samples to inspect the material quality and craftsmanship. Additionally, investigate their production processes, including the use of raw materials and adherence to safety regulations. Customer testimonials and case studies can also provide insight into their reliability and service quality. Finally, consider visiting their facility if possible, as this can give you a firsthand view of their operational standards. -
What are the key factors to consider when selecting a kitchen utensil supplier?
When selecting a kitchen utensil supplier, consider their production capacity and lead times to ensure they can meet your demand. Evaluate their pricing structure and payment terms to maintain cash flow. It’s crucial to assess their ability to customize products according to your specifications, as this can enhance your brand’s uniqueness. Additionally, research their experience in international shipping, including logistics, import regulations, and customs compliance, especially if you are sourcing from Africa, South America, the Middle East, or Europe. -
What minimum order quantities (MOQs) should I expect from kitchen utensil manufacturers?
Minimum order quantities (MOQs) can vary significantly among kitchen utensil manufacturers, typically ranging from 100 to 10,000 units, depending on the product type and customization level. Larger manufacturers may offer lower MOQs for standard items, while specialized or custom designs might require higher MOQs. Always clarify the MOQ during initial discussions and consider negotiating terms if your order volume is lower. Understanding MOQs is essential to managing your inventory effectively and ensuring cost-efficiency. -
What payment terms are common in international B2B transactions for kitchen utensils?
Common payment terms in international B2B transactions include wire transfers, letters of credit, and payment upon delivery. Manufacturers may request a deposit upfront, typically ranging from 30% to 50% of the total order value, with the balance due before shipment or upon receipt. Familiarize yourself with the payment practices in the country of your supplier to avoid misunderstandings. Always ensure that payment methods align with your cash flow management and risk tolerance. -
How can I ensure compliance with international trade regulations when sourcing kitchen utensils?
To ensure compliance with international trade regulations, familiarize yourself with the import laws of your country and the export regulations of the supplier’s country. Consult with trade compliance experts or legal advisors to understand tariffs, duties, and any specific requirements for kitchen utensils, such as safety and health regulations. Additionally, ensure that your supplier provides all necessary documentation, including certificates of origin and compliance. Regularly review trade agreements that may affect your sourcing strategy. -
What customization options are typically available from kitchen utensil manufacturers?
Many kitchen utensil manufacturers offer a range of customization options, including material selection, color variations, branding (like logos), and packaging designs. Some may also provide bespoke designs tailored to your unique specifications. When discussing customization, clarify lead times and any additional costs associated with these services. Understanding the extent of customization can help you differentiate your products in competitive markets. -
How do I assess the logistics capabilities of a kitchen utensil supplier?
To assess the logistics capabilities of a kitchen utensil supplier, inquire about their shipping options, delivery times, and partnerships with freight carriers. Understand their experience with international shipping, including handling customs clearance and documentation. Ask for references or case studies that demonstrate their ability to manage logistics efficiently. A supplier with robust logistics capabilities can significantly reduce delays and enhance your supply chain reliability, especially for international buyers.
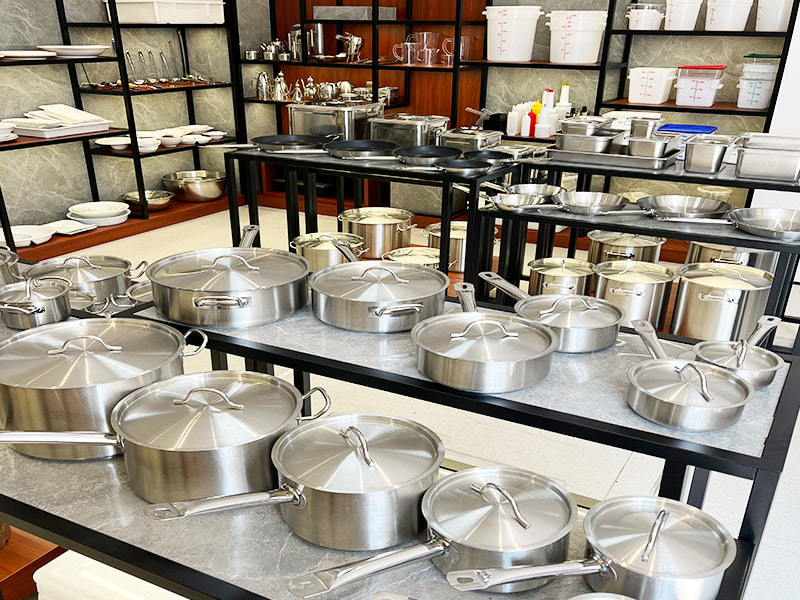
A stock image related to kitchen utensil manufacturer.
- What quality assurance processes should I expect from a kitchen utensil manufacturer?
You should expect kitchen utensil manufacturers to have comprehensive quality assurance processes in place, including raw material inspections, in-process quality checks, and final product testing. Inquire about their quality control certifications and methodologies, such as Six Sigma or Total Quality Management. Additionally, they should offer a clear process for handling defects or product returns. Understanding these processes will help ensure that you receive products that meet your standards and reduce the risk of costly returns or reputational damage.
Important Disclaimer & Terms of Use
⚠️ Important Disclaimer
The information provided in this guide, including content regarding manufacturers, technical specifications, and market analysis, is for informational and educational purposes only. It does not constitute professional procurement advice, financial advice, or legal advice.
While we have made every effort to ensure the accuracy and timeliness of the information, we are not responsible for any errors, omissions, or outdated information. Market conditions, company details, and technical standards are subject to change.
B2B buyers must conduct their own independent and thorough due diligence before making any purchasing decisions. This includes contacting suppliers directly, verifying certifications, requesting samples, and seeking professional consultation. The risk of relying on any information in this guide is borne solely by the reader.
Strategic Sourcing Conclusion and Outlook for kitchen utensil manufacturer
In the rapidly evolving landscape of kitchen utensil manufacturing, strategic sourcing emerges as a pivotal factor for international B2B buyers looking to optimize supply chains and enhance product offerings. By focusing on key regions such as Africa, South America, the Middle East, and Europe, businesses can leverage local insights, cultural preferences, and emerging trends to make informed purchasing decisions.
What are the key benefits of strategic sourcing for kitchen utensils? Effective sourcing not only reduces costs but also fosters relationships with suppliers that can lead to innovation and customization. Engaging with manufacturers who understand regional tastes and regulations ensures compliance and enhances customer satisfaction, ultimately positioning your brand as a leader in the market.
As we look ahead, the demand for sustainable and eco-friendly kitchen utensils is expected to rise. Buyers are encouraged to explore partnerships with manufacturers who prioritize sustainability in their production processes. This not only aligns with global trends but also meets the growing consumer demand for responsible products.
In conclusion, the future of kitchen utensil manufacturing is bright for those who embrace strategic sourcing. International B2B buyers should act now to forge meaningful connections with suppliers who can help them navigate this dynamic market. By prioritizing strategic partnerships, you can ensure your business thrives in the global kitchen utensil arena.