Discover Cost-Saving Benefits of GMC 2500 Custom (2025)
Introduction: Navigating the Global Market for gmc 2500 custom
Navigating the global market for the GMC 2500 custom can be a daunting task for B2B buyers, especially when considering the diverse needs and challenges faced by businesses across Africa, South America, the Middle East, and Europe. Sourcing the right vehicle to meet specific operational requirements—whether for logistics, construction, or specialized applications—requires a comprehensive understanding of the available options, supplier reliability, and market pricing. This guide aims to equip international buyers with the insights necessary to make informed decisions when purchasing GMC 2500 custom vehicles.
Throughout this guide, we will explore various types of GMC 2500 custom configurations, their applications across different industries, and crucial factors for vetting suppliers. Additionally, we will address cost considerations, maintenance requirements, and import/export regulations that may impact your purchasing strategy. By presenting a thorough analysis of these elements, we empower B2B buyers to navigate potential pitfalls and seize opportunities in the global market.
Whether you are a fleet manager in Johannesburg, a construction business owner in São Paulo, or a logistics coordinator in Dubai, understanding the dynamics of the GMC 2500 custom market will enhance your procurement strategy. This guide is designed to provide actionable insights tailored to your regional context, ensuring you can confidently select the best vehicle to meet your business’s unique demands.
Understanding gmc 2500 custom Types and Variations
Type Name | Key Distinguishing Features | Primary B2B Applications | Brief Pros & Cons for Buyers |
---|---|---|---|
GMC 2500 Custom Crew Cab | Spacious interior with four full-size doors, higher payload capacity | Construction, transportation of large teams | Pros: Ample space, versatile; Cons: Larger footprint may limit maneuverability. |
GMC 2500 Custom Regular Cab | Traditional two-door design, shorter wheelbase, lighter weight | Agricultural transport, fleet vehicles | Pros: Cost-effective, easy maintenance; Cons: Limited passenger capacity. |
GMC 2500 Custom Denali | Premium features, advanced technology, luxurious interior | Executive transport, high-end deliveries | Pros: Comfort and style, superior tech; Cons: Higher initial investment. |
GMC 2500 Custom All Terrain | Off-road capabilities, enhanced suspension, rugged design | Mining, construction in rough terrains | Pros: Durability, excellent off-road performance; Cons: May have lower fuel efficiency. |
GMC 2500 Custom SLT | Mid-range trim with a balance of features and affordability | General utility, small business transport | Pros: Good value for features; Cons: Less luxurious than Denali. |
What are the characteristics of the GMC 2500 Custom Crew Cab?
The GMC 2500 Custom Crew Cab is tailored for businesses requiring both passenger and cargo space. It features a spacious interior with four full-size doors, making it ideal for transporting teams to job sites. Its higher payload capacity allows for heavy-duty applications, making it suitable for construction and logistics. B2B buyers should consider their need for space versus maneuverability, as its larger size may pose challenges in tight urban environments.
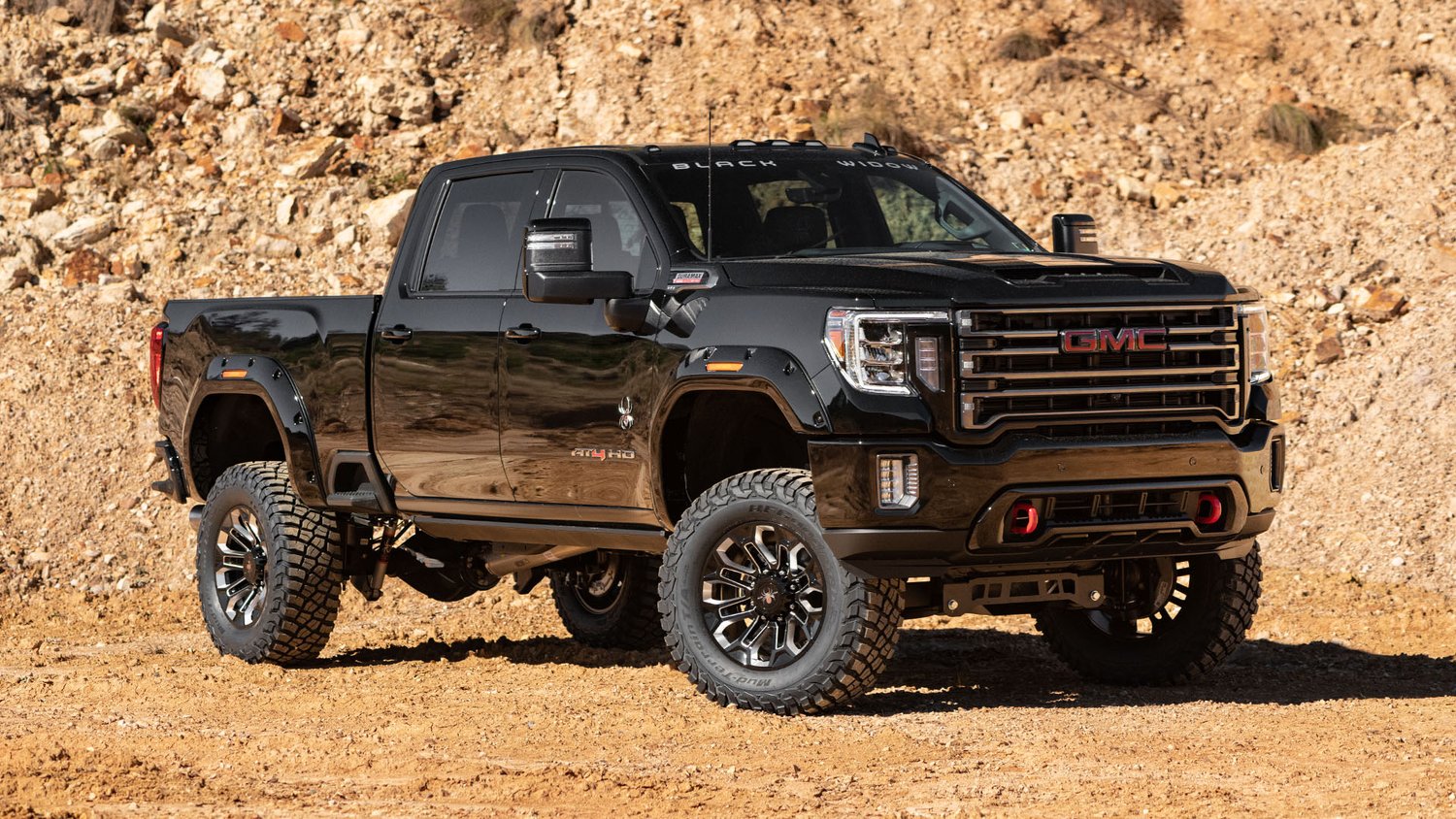
A stock image related to gmc 2500 custom.
How does the GMC 2500 Custom Regular Cab meet B2B needs?
The Regular Cab variant is designed for efficiency and practicality, featuring a traditional two-door configuration. Its shorter wheelbase and lighter weight make it a popular choice for agricultural transport and fleet vehicles. Buyers in this segment often prioritize cost-effectiveness and ease of maintenance, as the Regular Cab typically comes at a lower price point. However, its limited passenger capacity may not suit businesses needing to transport multiple employees.
Why choose the GMC 2500 Custom Denali for high-end applications?
The Denali trim stands out with its premium features, luxurious interior, and advanced technology, making it suitable for executive transport and high-end deliveries. This model is equipped with high-quality materials and offers a smooth ride, appealing to businesses aiming to impress clients. While the initial investment is higher, the comfort and style can enhance corporate image and employee satisfaction, making it a worthwhile consideration for B2B buyers focused on luxury.
What are the advantages of the GMC 2500 Custom All Terrain for rugged environments?
Built for off-road capabilities, the GMC 2500 Custom All Terrain features enhanced suspension and rugged design elements, making it ideal for mining and construction in rough terrains. Its durability and performance in challenging conditions make it a solid choice for companies operating in remote areas. However, potential buyers should weigh its off-road strengths against possible lower fuel efficiency, which could impact operational costs.
How does the GMC 2500 Custom SLT balance features and affordability?
The SLT variant offers a mid-range trim that balances essential features with affordability, making it a versatile option for general utility and small business transport. With a good mix of comfort and functionality, it appeals to businesses that require reliable vehicles without the luxury price tag. While it may lack some of the high-end features found in the Denali, it provides excellent value, making it an attractive option for budget-conscious buyers.
Related Video: 2024 GMC Denali 2500 HD lifted on 26s and 37s
Key Industrial Applications of gmc 2500 custom
Industry/Sector | Specific Application of gmc 2500 custom | Value/Benefit for the Business | Key Sourcing Considerations for this Application |
---|---|---|---|
Construction | Heavy-duty transportation of materials | Efficient delivery of construction materials reduces project timelines and costs. | Assess vehicle load capacity and compatibility with local terrain. |
Agriculture | Transport of agricultural products and equipment | Enhances productivity by ensuring timely delivery of harvests and supplies. | Look for customization options for specific farming needs. |
Logistics and Supply Chain | Freight and distribution services | Reliable logistics support increases customer satisfaction and operational efficiency. | Evaluate service network and availability of spare parts. |
Mining | Transportation of personnel and equipment | Facilitates access to remote sites, improving operational safety and efficiency. | Consider off-road capability and durability in harsh environments. |
Emergency Services | Rapid response vehicle for emergency situations | Improves response times, potentially saving lives and protecting property. | Ensure compliance with local regulations for emergency vehicles. |
How Is the GMC 2500 Custom Used in the Construction Industry?
In the construction sector, the GMC 2500 Custom plays a vital role in transporting heavy materials such as concrete, steel, and machinery. Its robust build and high towing capacity allow it to handle significant loads, which is essential for meeting project deadlines. International buyers, especially in regions like Africa and South America, should consider the vehicle’s adaptability to local terrains and its maintenance requirements to ensure long-term reliability.
What Are the Applications of the GMC 2500 Custom in Agriculture?
In agriculture, the GMC 2500 Custom is utilized for transporting harvested crops, fertilizers, and farming equipment. This vehicle’s versatility aids farmers in maintaining a steady supply chain from fields to markets. For B2B buyers, especially in the Middle East and Europe, it is crucial to evaluate the vehicle’s fuel efficiency and potential customization to suit specific agricultural operations, such as adding storage or towing capabilities.
How Does the GMC 2500 Custom Benefit Logistics and Supply Chain Operations?
The logistics and supply chain industry leverages the GMC 2500 Custom for freight and distribution, ensuring timely deliveries to clients. Its reliability and cargo capacity enhance overall operational efficiency, which is critical in maintaining customer satisfaction. Buyers from diverse regions should focus on the vehicle’s service network and availability of spare parts to minimize downtime and repair costs.
In What Ways Does the GMC 2500 Custom Support Mining Operations?
In mining, the GMC 2500 Custom is crucial for transporting personnel and equipment to remote sites. Its off-road capabilities and durability make it suitable for challenging environments, ensuring safe access to operations. B2B buyers in the mining sector should assess the vehicle’s performance under extreme conditions and consider modifications that may enhance safety and comfort for workers.
How Is the GMC 2500 Custom Used in Emergency Services?
Emergency services utilize the GMC 2500 Custom as a rapid response vehicle, enabling quick deployment during crises. Its spacious interior can accommodate necessary equipment and personnel, which is essential for effective emergency management. International buyers must ensure that the vehicle meets local regulations for emergency services, including equipment specifications and safety features, to guarantee operational readiness.
Related Video: FIRST 2024 GMC Sierra 2500 Customization
3 Common User Pain Points for ‘gmc 2500 custom’ & Their Solutions
Scenario 1: Difficulty in Customization for Specific Needs
The Problem: B2B buyers often find that the standard configurations of the GMC 2500 Custom do not meet their unique operational requirements. For instance, a construction company may need a truck with specific towing capabilities and cargo space that are not available in the default models. This limitation can lead to frustration, as businesses risk losing potential contracts if they cannot deliver on client expectations due to inadequate vehicle specifications.
The Solution: To effectively customize a GMC 2500 Custom to meet specific business needs, buyers should engage directly with GMC dealers who specialize in fleet vehicles. It is crucial to communicate clearly the operational demands, including expected payload, towing capacity, and any additional features like enhanced suspension or off-road capabilities. Additionally, leveraging aftermarket options such as custom towing packages or specialized bed configurations can enhance functionality. Buyers should also consider consulting with professionals who have experience in fleet management to ensure that the selected modifications align with industry standards and regulations.
Scenario 2: Challenges with Maintenance and Parts Availability
The Problem: Another significant pain point for B2B buyers of the GMC 2500 Custom is the accessibility of maintenance services and spare parts. In regions like Africa or South America, where access to authorized service centers may be limited, prolonged downtime due to vehicle maintenance can severely affect business operations and profitability.
The Solution: To mitigate this issue, B2B buyers should conduct thorough research on the availability of service centers and parts suppliers before finalizing their purchase. Establishing relationships with local mechanics who are familiar with GMC vehicles can also provide a backup option for maintenance. Additionally, buyers can consider investing in extended service plans that cover parts and labor, ensuring they are protected against unexpected repair costs. Keeping an inventory of critical spare parts, particularly for high-demand components, can also help minimize downtime.
Scenario 3: Regulatory Compliance and Vehicle Specifications
The Problem: International buyers, particularly in the Middle East and Europe, often face challenges related to regulatory compliance for vehicle specifications. Different countries have varying emission standards and safety regulations, which can complicate the procurement process for the GMC 2500 Custom. Buyers risk incurring hefty fines or being unable to register their vehicles if they do not adhere to local laws.
The Solution: To navigate regulatory challenges, B2B buyers should conduct a comprehensive review of the vehicle regulations specific to their country before making a purchase. This includes understanding the required emissions standards, safety features, and any import tariffs that may apply. Collaborating with local automotive consultants or legal advisors who specialize in vehicle compliance can provide invaluable insights. Furthermore, buyers should inquire with GMC dealers about models that are pre-approved for their specific market, ensuring that they select configurations that meet all necessary legal requirements. Engaging in these practices not only streamlines the purchasing process but also fosters long-term operational efficiency.
Strategic Material Selection Guide for gmc 2500 custom
When selecting materials for the GMC 2500 Custom, international B2B buyers must consider various factors that influence performance, durability, and compliance with regional standards. Below is an analysis of four common materials used in the construction of this vehicle, focusing on their properties, pros and cons, and implications for specific markets.
What are the Key Properties of Steel in GMC 2500 Custom Applications?
Steel is a primary material in the GMC 2500 Custom, known for its strength and versatility. It typically has high tensile strength, excellent weldability, and good resistance to deformation under stress.
Pros & Cons: The durability of steel makes it suitable for structural components, but it can be prone to corrosion if not adequately treated. While steel is generally cost-effective, the manufacturing complexity increases with the need for protective coatings, especially in humid or corrosive environments.
Impact on Application: Steel components can withstand high pressure and temperature, making them ideal for engine and chassis applications. However, in markets with high humidity, such as parts of Africa and South America, buyers should consider corrosion-resistant coatings.
Specific Considerations: Compliance with international standards like ASTM A36 or EN 10025 is crucial. Buyers in Europe may prefer steel that meets EU directives, while those in the Middle East might focus on local standards.
How Does Aluminum Benefit the GMC 2500 Custom?
Aluminum is increasingly used in automotive applications due to its lightweight nature and resistance to corrosion. It typically has a lower density than steel, which contributes to better fuel efficiency.
Pros & Cons: The key advantage of aluminum is its corrosion resistance, which is vital for vehicles operating in coastal or wet regions. However, aluminum can be more expensive than steel and may require specialized welding techniques, increasing manufacturing complexity.
Impact on Application: Aluminum is suitable for body panels and components where weight reduction is critical. Its compatibility with various media is excellent, but buyers should be aware of potential galvanic corrosion when used with dissimilar metals.
Specific Considerations: Buyers should ensure compliance with standards such as ASTM B221 for aluminum extrusions. In South America and Africa, where cost sensitivity is high, the initial investment in aluminum may be offset by long-term savings in fuel efficiency.
What Role Does Composite Material Play in GMC 2500 Custom?
Composite materials, including fiberglass and carbon fiber, are utilized for specific applications in the GMC 2500 Custom. They offer excellent strength-to-weight ratios and can be tailored for specific performance needs.
Pros & Cons: Composites are lightweight and resistant to corrosion, making them ideal for interior components and non-structural applications. However, they can be costly and may require complex manufacturing processes, which can limit their use in mass production.
Impact on Application: Composites are particularly beneficial in applications requiring high strength without added weight, such as in the vehicle’s body and interior. However, they may not be suitable for high-load-bearing components.
Specific Considerations: International buyers should check for compliance with standards like ASTM D3039 for composite materials. In Europe, the use of composites is becoming more prevalent, but understanding local regulations is essential.
How Does Plastic Fit into the GMC 2500 Custom?
Plastic is often employed in non-structural components such as interior trims, dashboards, and exterior panels. It is lightweight, cost-effective, and offers good resistance to chemicals and moisture.
Pros & Cons: The primary advantage of plastic is its versatility and lower cost compared to metals. However, plastics may not offer the same level of durability and can degrade under UV exposure unless treated.
Impact on Application: Plastics are suitable for a variety of applications, but their performance can be affected by temperature extremes. In hot climates, such as parts of Africa and the Middle East, selecting UV-stabilized plastics is crucial.
Specific Considerations: Compliance with standards such as ASTM D638 for tensile properties is important. Buyers from Europe may also need to consider REACH regulations regarding chemical safety.
Summary Table of Material Selection for GMC 2500 Custom
Material | Typical Use Case for gmc 2500 custom | Key Advantage | Key Disadvantage/Limitation | Relative Cost (Low/Med/High) |
---|---|---|---|---|
Steel | Structural components, chassis | High strength and durability | Susceptible to corrosion | Medium |
Aluminum | Body panels, engine components | Lightweight and corrosion-resistant | Higher cost and complex welding | High |
Composite | Interior trims, non-structural parts | Excellent strength-to-weight ratio | Costly and complex manufacturing | High |
Plastic | Dashboard, exterior trim | Cost-effective and versatile | Less durable, UV degradation potential | Low |
This guide provides a comprehensive overview of material selection for the GMC 2500 Custom, emphasizing the importance of understanding regional requirements and material properties for international B2B buyers.
In-depth Look: Manufacturing Processes and Quality Assurance for gmc 2500 custom
What Are the Main Stages of Manufacturing for the GMC 2500 Custom?
The manufacturing process for the GMC 2500 Custom involves several critical stages that ensure both quality and durability. Understanding these stages is essential for B2B buyers looking to source reliable vehicles.
-
Material Preparation: The process begins with the selection of high-quality raw materials, including steel and aluminum. These materials undergo rigorous testing to assess their mechanical properties and suitability for automotive applications. Sourcing materials from reputable suppliers who comply with international standards is crucial, as it directly impacts the vehicle’s performance and longevity.
-
Forming: This stage includes processes such as stamping and molding. Advanced machinery is utilized to shape the raw materials into various components like body panels and chassis. Techniques like hydroforming, which uses high-pressure fluids to form materials, are often employed to achieve complex shapes while maintaining structural integrity.
-
Assembly: Once formed, components are assembled in a systematic manner. This involves robotic automation and skilled labor to ensure precision. Key components such as the engine, transmission, and electrical systems are integrated. The assembly line is designed for efficiency, allowing for quick transitions between different model configurations.
-
Finishing: The final stage includes painting, coating, and quality finishing. The GMC 2500 Custom typically undergoes a multi-layer painting process to enhance aesthetics and protect against corrosion. Quality checks at this stage ensure that the vehicle meets both visual and functional standards before it leaves the production facility.
How Is Quality Assurance Implemented in the GMC 2500 Custom Manufacturing?
Quality assurance (QA) is a pivotal aspect of the manufacturing process, particularly in the automotive sector. B2B buyers should be aware of the international standards and industry-specific certifications that govern quality in vehicle production.
-
International Standards: Compliance with ISO 9001 is essential. This standard outlines the requirements for a quality management system (QMS) that organizations must meet to ensure consistent quality in products and services. Buyers should inquire if suppliers maintain such certifications, as it reflects a commitment to quality.
-
Industry-Specific Certifications: Additional certifications like CE (Conformité Européenne) for European markets and API (American Petroleum Institute) for parts related to engines are crucial. These certifications ensure that products meet regional safety and performance standards.
-
Quality Control Checkpoints:
– Incoming Quality Control (IQC): This step involves inspecting raw materials upon arrival. Suppliers must provide documentation proving that materials meet specified standards.
– In-Process Quality Control (IPQC): During the manufacturing process, various checkpoints are established to ensure that each component meets quality specifications before proceeding to the next stage.
– Final Quality Control (FQC): This final inspection assesses the completed vehicle against a checklist of operational and aesthetic criteria.
What Common Testing Methods Are Used in Quality Assurance?
Several testing methods are employed throughout the manufacturing process to ensure quality and reliability in the GMC 2500 Custom. B2B buyers should be familiar with these methods to assess supplier capabilities.
-
Material Testing: Techniques such as tensile testing, hardness testing, and fatigue testing are commonly used to evaluate the mechanical properties of materials.
-
Functional Testing: This includes assessments of engine performance, braking systems, and electronic functionalities. Dynamic testing on tracks may also be performed to simulate real-world conditions.
-
Durability Testing: Vehicles undergo rigorous tests to assess their performance over time, including exposure to extreme temperatures, humidity, and road conditions.
How Can B2B Buyers Verify Supplier Quality Control?
For international B2B buyers, particularly from regions like Africa, South America, the Middle East, and Europe, verifying supplier quality control is essential to ensure product reliability and compliance with local regulations.
-
Supplier Audits: Conducting regular audits of suppliers allows buyers to assess their compliance with quality standards and manufacturing processes. Buyers should request audit reports to gain insights into the supplier’s practices.
-
Documentation and Reporting: Suppliers should provide comprehensive documentation of their quality assurance processes, including IQC, IPQC, and FQC reports. These documents serve as evidence of adherence to quality standards.
-
Third-Party Inspections: Engaging third-party inspection agencies can provide an unbiased evaluation of the manufacturing processes. These agencies often conduct random inspections and testing to validate the supplier’s claims.
What Quality Control Nuances Should International B2B Buyers Consider?
When dealing with international suppliers, B2B buyers must navigate various quality control nuances that can impact their purchasing decisions.
-
Cultural Differences: Different regions may have varying standards of quality and business practices. Understanding these cultural differences can help buyers negotiate better terms and ensure compliance with local expectations.
-
Regulatory Compliance: Each market has its own set of regulations governing automotive standards. Buyers must ensure that suppliers are not only compliant with international standards but also with local laws specific to their target markets.
-
Supply Chain Transparency: A transparent supply chain helps in tracing the origin of materials and ensuring that they meet quality standards. Buyers should seek suppliers who can provide complete transparency regarding their sourcing and manufacturing processes.
By understanding the manufacturing processes and quality assurance practices for the GMC 2500 Custom, B2B buyers can make informed decisions, ensuring they procure vehicles that meet their operational needs and quality expectations.
Practical Sourcing Guide: A Step-by-Step Checklist for ‘gmc 2500 custom’
In today’s competitive landscape, sourcing a GMC 2500 Custom requires a strategic approach tailored to meet the unique needs of your business. This guide outlines essential steps to help international B2B buyers streamline their procurement process, ensuring you make informed decisions that align with your operational requirements.
Step 1: Define Your Technical Specifications
Begin by clearly outlining the technical specifications of the GMC 2500 Custom that you require. Consider factors such as engine type, towing capacity, payload, and any custom modifications necessary for your operations. Having a well-defined specification helps in communicating your needs effectively to potential suppliers and ensures that you receive accurate quotes.
Step 2: Conduct Market Research
Engage in thorough market research to identify reputable suppliers of the GMC 2500 Custom. Look for companies with a solid track record in your region, particularly those that specialize in heavy-duty vehicles. Utilize platforms like trade shows, industry forums, and online marketplaces to gather information about potential suppliers.
Step 3: Evaluate Potential Suppliers
Before committing, it’s crucial to vet suppliers thoroughly. Request company profiles, case studies, and references from buyers in a similar industry or region. Key evaluation criteria should include:
– Experience: Look for suppliers with a proven history of supplying GMC vehicles.
– Reputation: Check online reviews and ratings to gauge customer satisfaction.
Step 4: Verify Supplier Certifications
Ensure that potential suppliers possess the necessary certifications and licenses to operate in your region. This may include ISO certifications, local compliance certificates, and safety standards adherence. Valid certifications not only indicate reliability but also ensure that the vehicles meet international quality and safety standards.
Step 5: Request Detailed Quotations
Once you have shortlisted potential suppliers, request detailed quotations that outline all costs associated with the GMC 2500 Custom, including base price, customization fees, shipping, and any additional services. A comprehensive quotation will help you compare offers effectively and identify the best value for your investment.
Step 6: Assess After-Sales Support and Warranty
Before finalizing your purchase, inquire about after-sales support and warranty options. A reliable supplier should offer robust support, including maintenance services and parts availability. Understand the warranty terms thoroughly to ensure that you are protected against potential defects or issues.
Step 7: Negotiate Terms and Finalize the Purchase
Once you have selected a supplier, negotiate the terms of the purchase, including payment methods, delivery timelines, and any additional services required. Clear communication during this phase is vital to establish a good working relationship and ensure that both parties are aligned on expectations.
By following this checklist, international B2B buyers can effectively navigate the sourcing process for the GMC 2500 Custom, ultimately leading to a successful procurement experience that meets their operational needs.
Comprehensive Cost and Pricing Analysis for gmc 2500 custom Sourcing
What Are the Key Cost Components in Sourcing a GMC 2500 Custom?
When sourcing a GMC 2500 custom, understanding the detailed cost structure is crucial for effective budgeting and price negotiation. The primary cost components include:
-
Materials: The cost of raw materials is a significant factor in the total price. For the GMC 2500, this may include high-strength steel, aluminum, and specialized components that meet durability and performance standards.
-
Labor: Labor costs encompass both direct and indirect labor. Direct labor refers to the workers directly involved in manufacturing the vehicle, while indirect labor includes support staff and management. The labor cost can vary significantly based on the region, with higher costs typically found in developed countries.
-
Manufacturing Overhead: This includes costs associated with running the production facility, such as utilities, maintenance, and depreciation of manufacturing equipment. Efficient production processes can help minimize these costs.
-
Tooling: Customization of the GMC 2500 may require specialized tooling, which can add to upfront costs. The complexity of the customization will influence tooling expenses, as more intricate designs necessitate advanced equipment.
-
Quality Control (QC): Ensuring that each vehicle meets quality standards is critical. QC costs can include inspection, testing, and compliance certifications, which are essential for international markets where safety and emissions regulations may vary.
-
Logistics: Transportation and handling costs from the manufacturer to the buyer’s location can be substantial, especially for international shipments. Factors like shipping distance, mode of transport, and customs duties contribute to the logistics cost.
-
Margin: Suppliers typically apply a profit margin to cover their costs and generate profit. This margin can vary based on market demand, competition, and the perceived value of the customization offered.
How Do Price Influencers Affect the Cost of GMC 2500 Custom Sourcing?
Several factors can influence the pricing of a GMC 2500 custom:
-
Volume/MOQ (Minimum Order Quantity): Larger orders often qualify for bulk pricing, which can significantly lower the per-unit cost. Buyers should consider their purchasing strategy to maximize cost efficiency.
-
Specifications and Customization: The level of customization requested can greatly affect the price. Unique features, enhanced performance specs, or additional accessories will typically incur higher costs.
-
Materials: The choice of materials directly impacts pricing. For instance, opting for premium materials will increase costs, while standard materials may offer savings.
-
Quality and Certifications: Higher quality standards and relevant certifications (e.g., ISO, CE) may lead to increased costs due to more stringent manufacturing processes and inspections.
-
Supplier Factors: The reputation and reliability of the supplier can influence pricing. Established suppliers may charge a premium for their products, while newer or less reputable suppliers might offer lower prices but with increased risk.
-
Incoterms: The terms of delivery (Incoterms) dictate who is responsible for shipping costs and risks. Understanding these terms is vital for international buyers, as they can affect the total landed cost of the vehicle.
What Are Effective Buyer Tips for Negotiating GMC 2500 Custom Prices?
For international B2B buyers, particularly from Africa, South America, the Middle East, and Europe, several strategies can enhance negotiation outcomes:
-
Negotiate Terms: Always negotiate terms of sale, including payment terms, delivery timelines, and pricing. This can lead to significant savings and better cash flow management.
-
Focus on Total Cost of Ownership (TCO): Consider not just the purchase price but the TCO, which includes maintenance, fuel efficiency, and resale value. A higher upfront cost may be justified if the vehicle offers lower operational costs over time.
-
Research Market Prices: Familiarize yourself with market prices for the GMC 2500 custom. This knowledge can empower you during negotiations and help you identify competitive offers.
-
Evaluate Multiple Suppliers: Don’t settle for the first offer. Engage multiple suppliers to compare prices, quality, and service levels. This can provide leverage in negotiations.
-
Understand Local Regulations: Be aware of local regulations that may impact the cost and specifications of the GMC 2500. Compliance with local standards can prevent costly modifications later.
Disclaimer on Pricing
Prices for the GMC 2500 custom can fluctuate based on market conditions, supplier availability, and changes in material costs. It is advisable for buyers to obtain current quotes and engage in thorough discussions with suppliers to establish accurate pricing structures.
Alternatives Analysis: Comparing gmc 2500 custom With Other Solutions
When considering the GMC 2500 Custom for heavy-duty tasks, it’s essential to explore viable alternatives that may better suit specific needs and requirements. This comparison will help international B2B buyers, particularly from Africa, South America, the Middle East, and Europe, make informed decisions based on performance, cost, and other critical factors.
Comparison Aspect | GMC 2500 Custom | Ford F-250 Super Duty | Ram 2500 |
---|---|---|---|
Performance | High torque, reliable payload capacity | Comparable torque, excellent towing capabilities | Strong performance with diesel option |
Cost | Moderate initial investment, good resale value | Higher upfront cost, but strong market demand | Competitive pricing, often lower than GMC |
Ease of Implementation | User-friendly interface, straightforward maintenance | Requires specialized knowledge for some features | Similar ease of use, with some complex configurations |
Maintenance | Routine maintenance is manageable, parts readily available | Slightly higher maintenance costs due to complexity | Generally affordable, with good parts availability |
Best Use Case | Ideal for construction and agriculture | Excellent for towing heavy trailers | Best for mixed-use applications |
What Are the Advantages and Disadvantages of the Ford F-250 Super Duty?
The Ford F-250 Super Duty is a strong competitor in the heavy-duty truck market, offering robust performance and a higher towing capacity than the GMC 2500 Custom. Its advanced technology features, such as the Pro Trailer Backup Assist, make it particularly useful for businesses that require efficient towing solutions. However, the initial investment is higher, and maintenance can be slightly more complex due to its advanced features, which might require specialized knowledge.
How Does the Ram 2500 Compare to the GMC 2500 Custom?
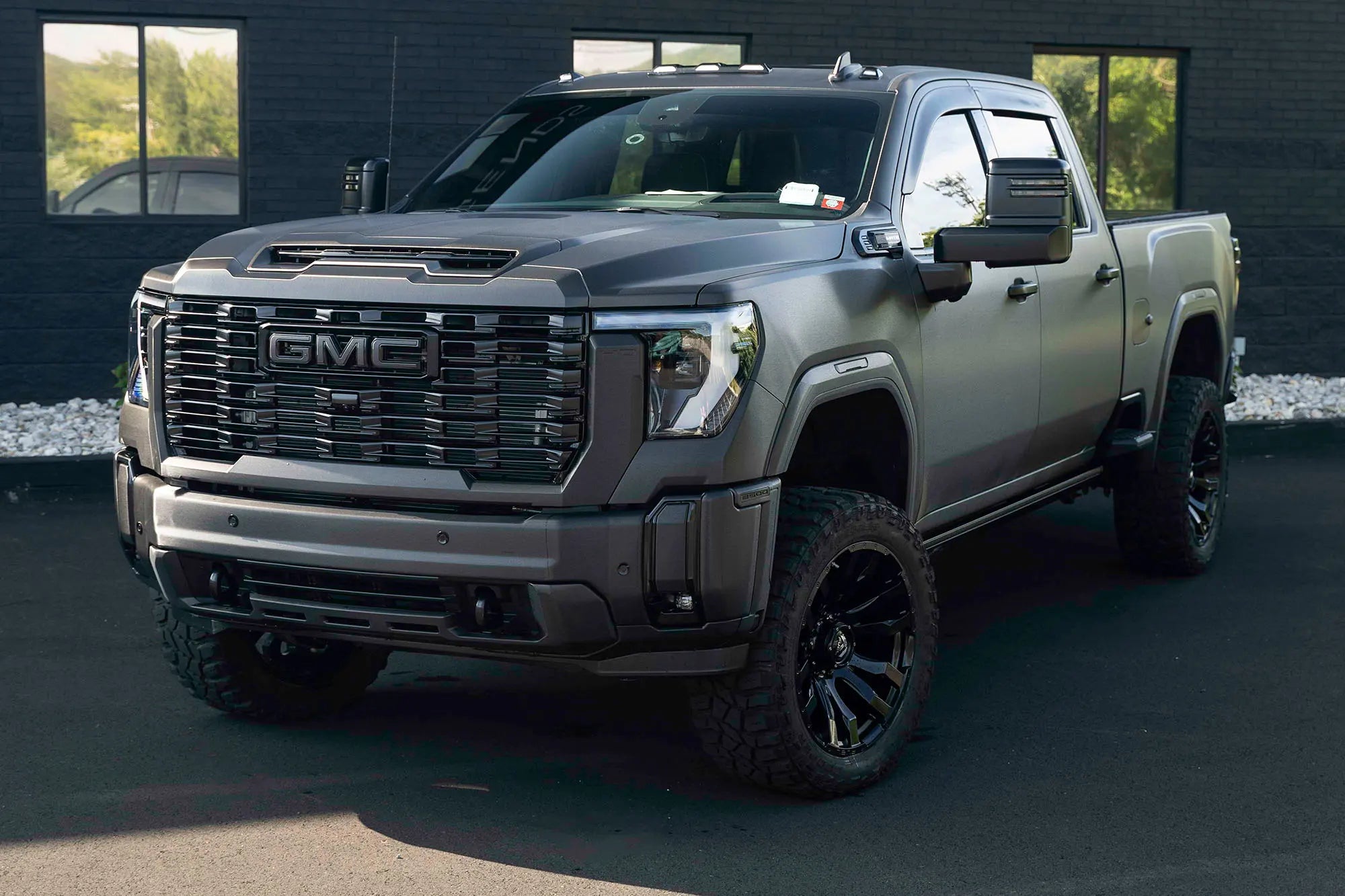
A stock image related to gmc 2500 custom.
The Ram 2500 is known for its comfortable interior and advanced technology, which can enhance the driving experience for long hauls. Its diesel engine option provides strong performance for heavy loads, making it suitable for diverse applications, from agriculture to construction. The competitive pricing of the Ram 2500 is appealing, but it may not match the GMC 2500 Custom’s reputation for reliability and resale value, which could impact long-term ownership costs.
How Can B2B Buyers Choose the Right Solution for Their Needs?
When selecting between the GMC 2500 Custom and its alternatives, B2B buyers should assess their specific requirements, including the nature of their operations, budget constraints, and anticipated usage scenarios. Performance metrics like towing capacity and payload are crucial, but so are cost considerations, maintenance requirements, and the vehicle’s overall longevity. Engaging with suppliers and reading user reviews can provide additional insights into real-world performance, helping buyers make a well-informed decision.
Essential Technical Properties and Trade Terminology for gmc 2500 custom
What Are the Essential Technical Properties of the GMC 2500 Custom?
Understanding the technical specifications of the GMC 2500 Custom is crucial for international B2B buyers, especially those from diverse regions such as Africa, South America, the Middle East, and Europe. Here are some key specifications that influence purchasing decisions:
-
Engine Specifications (Horsepower and Torque)
– The GMC 2500 Custom typically features a powerful V8 engine that delivers high horsepower (often around 400 HP) and substantial torque (around 464 lb-ft). This is vital for buyers in industries requiring heavy-duty performance, such as construction and logistics, ensuring that the vehicle can handle demanding loads and off-road conditions. -
Payload Capacity
– With a payload capacity often exceeding 3,500 lbs, the GMC 2500 Custom is designed for heavy lifting. This specification is critical for businesses involved in freight and transportation, as it directly affects operational efficiency and vehicle utilization rates. -
Towing Capacity
– The towing capacity of the GMC 2500 Custom can reach up to 18,500 lbs when properly equipped. For international buyers, especially in agriculture and logistics, this capability is essential for transporting trailers, equipment, or livestock, thereby enhancing productivity. -
Material Composition
– The use of high-strength steel in the chassis and aluminum components in the bodywork enhances durability while reducing weight. This balance is significant for B2B buyers focused on long-term investment and operational cost savings due to improved fuel efficiency and lower maintenance costs. -
Safety Features
– Advanced safety features, such as lane-keeping assist, automatic emergency braking, and a robust airbag system, are integral to the GMC 2500 Custom. For companies prioritizing employee safety and compliance with international safety standards, these features can influence purchasing decisions. -
Fuel Efficiency
– Fuel efficiency ratings, which can vary based on engine choice and load, are a critical consideration for B2B buyers. A vehicle that offers better fuel economy translates to lower operational costs, which is especially important in regions where fuel prices are high.
What Trade Terms Should International Buyers Know for the GMC 2500 Custom?
Navigating the international trade landscape involves familiarizing oneself with specific jargon and terms that can impact procurement processes. Here are some essential trade terms:
-
OEM (Original Equipment Manufacturer)
– This term refers to companies that manufacture products that may be marketed by another company. Understanding OEM relationships can help buyers ensure they are sourcing authentic parts and vehicles, which is crucial for maintaining warranty and service quality. -
MOQ (Minimum Order Quantity)
– MOQ is the minimum number of units a supplier is willing to sell. For B2B buyers, knowing the MOQ is important for budgeting and inventory management, especially when ordering custom vehicles like the GMC 2500. -
RFQ (Request for Quotation)
– An RFQ is a document used to invite suppliers to bid on specific products or services. It is a critical step in the purchasing process, allowing buyers to compare prices and terms from different suppliers, facilitating informed decision-making. -
Incoterms (International Commercial Terms)
– These are pre-defined commercial terms published by the International Chamber of Commerce (ICC) related to international commercial law. Understanding Incoterms is essential for buyers to clarify the responsibilities of buyers and sellers regarding shipping, insurance, and tariffs. -
Lead Time
– This refers to the time it takes for a supplier to fulfill an order. For B2B buyers, particularly in fast-paced industries, knowing the lead time helps in planning and managing supply chain logistics effectively. -
Warranty and Service Agreements
– These are commitments from the manufacturer regarding the repair and maintenance of the vehicle. For businesses, understanding the terms of warranty and service agreements can significantly impact long-term operational costs and vehicle uptime.
By grasping these technical properties and trade terms, international B2B buyers can make more informed decisions when considering the GMC 2500 Custom, ultimately leading to better operational outcomes and investment returns.
Navigating Market Dynamics and Sourcing Trends in the gmc 2500 custom Sector
What Are the Key Market Dynamics and Trends Influencing the GMC 2500 Custom Sector?
The GMC 2500 Custom sector is witnessing significant transformation driven by various global factors. One of the primary drivers is the increasing demand for robust and versatile vehicles capable of handling diverse terrains, particularly in emerging markets across Africa, South America, the Middle East, and Europe. The rise in construction and logistics activities in these regions has amplified the need for reliable heavy-duty trucks like the GMC 2500 Custom, which are engineered for performance and durability.
In terms of sourcing trends, technology adoption is at the forefront. The integration of digital platforms for procurement has streamlined the sourcing process, enabling international B2B buyers to access a broader range of suppliers and negotiate better deals. Additionally, the emergence of data analytics allows companies to make informed decisions based on market forecasts, demand patterns, and supply chain efficiencies. This data-driven approach is vital for buyers aiming to optimize their inventory and reduce costs.
Moreover, sustainability is becoming a significant factor influencing market dynamics. Buyers are increasingly prioritizing suppliers who adhere to environmentally responsible practices, which is shaping sourcing strategies. This trend is particularly relevant for international buyers from Europe, where stringent regulations on emissions and environmental impact are in place.
How Is Sustainability Shaping Sourcing Practices in the GMC 2500 Custom Sector?
The importance of sustainability in the GMC 2500 Custom sector cannot be overstated. As the global focus shifts towards reducing environmental impact, B2B buyers are increasingly looking for suppliers that prioritize ethical sourcing and sustainability. This includes the use of ‘green’ materials and certifications that demonstrate a commitment to environmental stewardship.
Buyers should seek out suppliers who utilize sustainable manufacturing processes and materials, such as recycled metals and eco-friendly coatings. Certifications like ISO 14001 (Environmental Management) or other green certifications can be indicators of a supplier’s commitment to sustainable practices. Furthermore, implementing a transparent supply chain that minimizes waste and reduces carbon footprints is becoming a crucial requirement for many businesses.
In the context of the GMC 2500 Custom, this sustainability trend also extends to the lifecycle of the vehicle, including end-of-life recycling programs that ensure materials are repurposed rather than ending up in landfills. By prioritizing sustainability, international buyers not only contribute to environmental protection but also enhance their brand reputation and appeal to a growing segment of eco-conscious consumers.
What Is the Historical Context Behind the GMC 2500 Custom’s Development?
The GMC 2500 Custom has a rich history that dates back to its origins in the mid-20th century when it was initially designed for military and industrial applications. Over the years, its robust design and reliability have made it a preferred choice for various sectors, including agriculture, construction, and logistics.
The evolution of the GMC 2500 Custom reflects broader trends in automotive technology and customer needs. As vehicles became more sophisticated, the GMC 2500 Custom incorporated advanced features such as improved fuel efficiency, enhanced safety protocols, and cutting-edge infotainment systems. This evolution has not only maintained its relevance in the marketplace but has also positioned it as a leading choice for international B2B buyers seeking a dependable vehicle that meets modern demands.
Understanding this historical context allows buyers to appreciate the value of the GMC 2500 Custom, recognizing that its legacy of performance and reliability is backed by continuous innovation and adaptation to market needs.
Frequently Asked Questions (FAQs) for B2B Buyers of gmc 2500 custom
-
How do I ensure the GMC 2500 Custom meets my business needs?
To ensure the GMC 2500 Custom aligns with your business requirements, start by defining your specific needs such as payload capacity, towing capabilities, and engine specifications. Consult with local dealers or manufacturers who can provide detailed information on available configurations. Additionally, consider conducting a test drive or seeking feedback from other businesses that use the model. This thorough evaluation helps in making an informed decision tailored to your operational demands. -
What customization options are available for the GMC 2500 Custom?
The GMC 2500 Custom offers a variety of customization options, including engine choices, transmission types, and bed configurations. You can also opt for specific features like upgraded suspension systems, towing packages, and interior finishes. Discussing your customization needs with your supplier is crucial, as they can guide you through available options and any associated costs, ensuring the vehicle perfectly fits your business requirements. -
What is the minimum order quantity (MOQ) for the GMC 2500 Custom?
The MOQ for the GMC 2500 Custom varies based on the supplier and the customization options chosen. Typically, OEMs may require a minimum of 5-10 units for bulk orders. However, some dealers might accommodate smaller orders depending on their inventory and willingness to negotiate. It’s advisable to communicate directly with suppliers to understand their specific MOQ policies and any potential for flexibility. -
What payment terms should I expect when purchasing a GMC 2500 Custom?
Payment terms for the GMC 2500 Custom can vary widely among suppliers. Common arrangements include a deposit upon order confirmation, followed by the balance due before delivery. Some suppliers may offer financing options or extended payment plans, especially for larger orders. It’s essential to clarify payment terms in advance, including any penalties for late payments, to ensure smooth transaction processes. -
How can I vet suppliers when sourcing the GMC 2500 Custom internationally?
Vetting suppliers is critical to ensuring quality and reliability. Start by researching potential suppliers through trade platforms and industry networks. Check for certifications, reviews, and case studies from previous clients. Request references and engage in direct discussions to gauge their responsiveness and expertise. Additionally, consider visiting the supplier’s facility if possible, or arrange for third-party audits to verify their operations and quality standards. -
What quality assurance processes should I expect from my GMC 2500 Custom supplier?
A reputable GMC 2500 Custom supplier should implement stringent quality assurance (QA) processes. These may include pre-production quality checks, in-process inspections, and final product evaluations. Request documentation of their QA processes and any relevant certifications like ISO standards. Understanding these practices helps ensure that the vehicles meet your quality expectations and comply with international standards. -
What logistics considerations should I keep in mind when importing the GMC 2500 Custom?
When importing the GMC 2500 Custom, consider logistics aspects such as shipping methods, customs regulations, and delivery timelines. Engage a freight forwarder familiar with automotive imports to navigate complex regulations and ensure compliance. Additionally, factor in potential duties and tariffs, as well as insurance for the vehicles during transit. Planning these logistics in advance can help avoid delays and additional costs. -
How can I troubleshoot common issues with the GMC 2500 Custom?
Common issues with the GMC 2500 Custom can often be resolved through proper maintenance and understanding of the vehicle’s systems. For instance, regular checks on the engine, transmission, and electrical systems can prevent major breakdowns. If you encounter specific problems, consult the vehicle’s manual or reach out to your supplier for technical support. Additionally, consider joining forums or communities of GMC users for shared experiences and solutions.
Important Disclaimer & Terms of Use
⚠️ Important Disclaimer
The information provided in this guide, including content regarding manufacturers, technical specifications, and market analysis, is for informational and educational purposes only. It does not constitute professional procurement advice, financial advice, or legal advice.
While we have made every effort to ensure the accuracy and timeliness of the information, we are not responsible for any errors, omissions, or outdated information. Market conditions, company details, and technical standards are subject to change.
B2B buyers must conduct their own independent and thorough due diligence before making any purchasing decisions. This includes contacting suppliers directly, verifying certifications, requesting samples, and seeking professional consultation. The risk of relying on any information in this guide is borne solely by the reader.
Strategic Sourcing Conclusion and Outlook for gmc 2500 custom
In the evolving landscape of B2B procurement, strategic sourcing for the GMC 2500 Custom emerges as a critical component for international buyers. By understanding the unique specifications, performance capabilities, and customization options of the GMC 2500, businesses can make informed purchasing decisions that align with their operational needs. The value of strategic sourcing lies in its ability to not only reduce costs but also enhance supply chain resilience and ensure the acquisition of high-quality vehicles tailored to specific market demands.
For buyers in Africa, South America, the Middle East, and Europe, leveraging local partnerships and understanding regional regulations can further enhance sourcing strategies. Engaging with trusted suppliers and utilizing platforms that facilitate transparent communication and comparison can lead to more favorable terms and conditions.
Looking ahead, the demand for versatile and reliable vehicles like the GMC 2500 Custom will continue to rise. International buyers are encouraged to act decisively, seizing opportunities to integrate these vehicles into their fleets. By prioritizing strategic sourcing practices, businesses can position themselves for sustainable growth and competitive advantage in their respective markets.