Discover Cost-Saving Strategies for Tables Custom (2025)
Introduction: Navigating the Global Market for tables custom
Navigating the global market for custom tables presents a unique set of challenges for international B2B buyers. Sourcing high-quality, durable tables tailored to specific business needs can be daunting, particularly when considering factors such as material selection, design specifications, and supplier reliability. This comprehensive guide delves into various types of custom tables, their applications across different industries, and essential criteria for vetting suppliers.
Understanding the diverse landscape of custom tables is critical for businesses in Africa, South America, the Middle East, and Europe, where local preferences and market trends can significantly influence purchasing decisions. This guide empowers B2B buyers by providing actionable insights into cost considerations, market demand, and effective negotiation strategies.
By addressing key questions such as “What are the different types of custom tables available?” and “How can I identify reliable suppliers?”, this resource aims to equip international buyers with the knowledge needed to make informed decisions. Whether you are looking to enhance office environments, retail spaces, or hospitality venues, navigating the custom tables market becomes more manageable with the right information at your fingertips. The ultimate goal is to streamline your purchasing process, ensuring that you invest in products that not only meet your operational needs but also align with your brand identity.
Understanding tables custom Types and Variations
Type Name | Key Distinguishing Features | Primary B2B Applications | Brief Pros & Cons for Buyers |
---|---|---|---|
Conference Tables | Large, often rectangular; designed for meetings | Corporate meetings, conferences | Pros: Promotes collaboration; customizable size. Cons: Requires ample space; may be expensive. |
Collaborative Tables | Modular designs; encourages teamwork and interaction | Co-working spaces, educational institutions | Pros: Flexible configurations; enhances creativity. Cons: May not suit formal settings; needs regular rearrangement. |
Dining Tables | Typically round or rectangular; used for meals | Restaurants, catering services | Pros: Creates a welcoming atmosphere; various styles available. Cons: Limited use outside dining; can be bulky. |
Training Tables | Lightweight and portable; often foldable | Training sessions, workshops | Pros: Easy to store and transport; versatile. Cons: May lack durability; can be less stable. |
Reception Tables | Sleek design; often includes branding opportunities | Lobbies, reception areas | Pros: Enhances first impressions; customizable branding. Cons: Limited functionality; may be costly for high-end designs. |
What Are Conference Tables and Their B2B Relevance?
Conference tables are designed for formal meetings and collaborative discussions, typically featuring large rectangular shapes to accommodate multiple participants. Their primary applications include corporate meetings and conferences, where the need for space and functionality is paramount. Buyers should consider the size of the table in relation to the meeting space, as well as the potential for customization to reflect company branding. While conference tables promote collaboration and can be customized in size, they require significant space and may come with higher costs.
How Do Collaborative Tables Enhance Teamwork?
Collaborative tables are characterized by their modular design, allowing for various configurations that promote teamwork and interaction. They are particularly suitable for co-working spaces and educational institutions, where creative brainstorming and group activities are common. When purchasing collaborative tables, B2B buyers should evaluate the flexibility of the design and how easily the tables can be rearranged. While these tables enhance creativity and adaptability, they may not be ideal for more formal settings and require regular adjustments to maintain an optimal layout.
Why Choose Dining Tables for B2B Applications?
Dining tables are often round or rectangular and are designed primarily for meals. Their applications in B2B settings include restaurants and catering services, where creating a welcoming atmosphere is essential. Buyers should look for dining tables that match the overall aesthetic of their venue while considering the durability of materials used. While dining tables help foster a pleasant dining experience, their use is generally limited outside of meal settings, and they can be cumbersome in smaller spaces.
What Makes Training Tables Ideal for Workshops?
Training tables are lightweight and often foldable, making them highly portable and easy to store. They are ideal for training sessions and workshops, where flexibility and mobility are crucial. B2B buyers should assess the stability and durability of training tables, especially if they will be used frequently. While they offer versatility and convenience, some training tables may compromise on sturdiness, which can affect the overall experience during events.
How Do Reception Tables Impact First Impressions?
Reception tables are designed with sleek aesthetics and often include branding opportunities, making them perfect for lobbies and reception areas. They play a vital role in creating a positive first impression for visitors. When selecting a reception table, B2B buyers should consider how well it aligns with their brand identity and the functionality it offers. Although these tables enhance the reception area’s appearance and can be customized for branding, their functionality may be limited, and high-quality designs can be costly.
Key Industrial Applications of tables custom
Industry/Sector | Specific Application of tables custom | Value/Benefit for the Business | Key Sourcing Considerations for this Application |
---|---|---|---|
Hospitality | Custom dining tables for restaurants and hotels | Enhances customer experience and ambiance | Material quality, design flexibility, and durability |
Education | Collaborative study tables for classrooms | Promotes interactive learning and group work | Ergonomic design, size adaptability, and safety standards |
Healthcare | Adjustable tables for medical facilities | Improves patient comfort and accessibility | Compliance with health regulations and materials used |
Manufacturing | Workstations tailored for production lines | Increases efficiency and productivity | Customization options and material resistance to wear |
Retail | Display tables for merchandise presentation | Boosts product visibility and sales | Aesthetic appeal, size customization, and material durability |
How Are Custom Tables Used in the Hospitality Sector?
In the hospitality industry, custom dining tables are essential for creating a unique atmosphere that aligns with a restaurant’s theme or a hotel’s luxury appeal. These tables can be designed to fit specific spatial constraints while accommodating various group sizes. International buyers need to consider local materials, cultural aesthetics, and durability against wear and tear, ensuring the tables not only look good but also withstand high traffic.
What Role Do Custom Tables Play in Education?
Custom tables in educational settings facilitate collaborative learning by providing flexible configurations for group activities. These tables can be designed to be mobile and adjustable, catering to different teaching methods and classroom layouts. Buyers from Africa, South America, the Middle East, and Europe should prioritize ergonomic designs that enhance comfort and promote engagement, while also adhering to safety standards for educational furniture.
Why Are Custom Tables Important in Healthcare?
In healthcare facilities, adjustable custom tables are vital for patient care, particularly in examination rooms and treatment areas. These tables can be tailored for height and functionality, ensuring accessibility for all patients, including those with mobility challenges. Buyers must ensure compliance with health regulations regarding materials and designs, focusing on easy-to-clean surfaces that reduce infection risks.
How Do Custom Tables Enhance Manufacturing Efficiency?
In manufacturing, custom tables serve as workstations tailored to specific production processes. These tables can be designed to optimize workflow, accommodate tools and machinery, and enhance worker ergonomics. When sourcing these tables, businesses should consider customization options that fit their operational needs, as well as materials that can withstand the rigors of manufacturing environments.
What Benefits Do Custom Display Tables Provide in Retail?
Custom display tables in retail settings are crucial for showcasing products effectively and enhancing customer engagement. These tables can be designed to fit the store layout and branding, attracting customers’ attention to specific merchandise. B2B buyers in retail should focus on aesthetic appeal, size adaptability, and material durability to ensure that the tables not only support sales but also complement the overall shopping experience.
Related Video: How to Build an Industrial Metal & Wood Coffee Table | DIY Home Decor
3 Common User Pain Points for ‘tables custom’ & Their Solutions
Scenario 1: Customization Complexity in Diverse Markets
The Problem: International B2B buyers, especially from regions like Africa and South America, often face significant hurdles when trying to customize tables to meet specific regional needs. Cultural preferences, local materials, and design aesthetics can vary widely, leading to confusion about how to source the right products. Buyers may struggle with suppliers who do not understand the nuances of their market, resulting in misaligned expectations and wasted resources.
The Solution: To navigate this complexity, buyers should begin by conducting thorough market research to identify local trends and preferences. Engaging with local designers or consultants can provide insights into culturally relevant designs and materials that resonate with the target audience. When sourcing tables, it is vital to communicate specific customization requirements upfront, including dimensions, materials, and finishes. Establishing a clear design brief and collaborating closely with suppliers can help ensure that the final product aligns with market expectations, ultimately leading to a successful implementation in their respective markets.
Scenario 2: Quality Assurance and Consistency Challenges
The Problem: Quality assurance is a critical pain point for B2B buyers dealing with custom tables. With suppliers often located in different parts of the world, maintaining consistent quality can be a daunting task. Buyers might receive products that do not meet the promised specifications, leading to dissatisfaction among end-users and potential damage to their own brand reputation.
The Solution: To ensure quality consistency, buyers should implement a robust supplier evaluation process before placing large orders. This includes requesting samples, visiting production facilities if feasible, and checking for certifications that guarantee adherence to quality standards. Establishing clear quality benchmarks and conducting regular inspections during the production phase can mitigate risks. Utilizing third-party quality assurance services can also provide an unbiased assessment of product quality before shipment, ensuring that the tables meet the required specifications and standards upon arrival.
Scenario 3: Logistics and Supply Chain Disruptions
The Problem: Logistics is often a significant concern for international B2B buyers, particularly when dealing with custom products like tables. Delays in shipping, customs clearance issues, and unexpected costs can disrupt supply chains and lead to project delays, which is particularly challenging for businesses operating on tight timelines.
The Solution: To manage logistics effectively, buyers should work with suppliers that offer integrated logistics solutions, including shipping and customs management. It is advisable to establish a comprehensive timeline that accounts for all phases of the supply chain, from production to delivery. Buyers should also consider diversifying their supplier base to reduce dependency on a single source, which can help mitigate risks related to delays. Furthermore, engaging a logistics partner with expertise in international shipping can provide valuable insights into navigating customs regulations and optimizing shipping routes, ultimately ensuring a smoother delivery process for custom tables.
Strategic Material Selection Guide for tables custom
What Are the Key Properties of Common Materials for Custom Tables?
When selecting materials for custom tables, it is crucial to understand the properties that will affect product performance. Below, we analyze four common materials: wood, metal (steel), plastic, and glass. Each material has unique characteristics that can influence the durability, cost, and application suitability of custom tables.
How Does Wood Perform as a Material for Custom Tables?
Key Properties: Wood is known for its aesthetic appeal and natural insulation properties. It typically has a moderate temperature rating and is not prone to corrosion, making it suitable for various environments. However, it can be susceptible to warping and moisture damage.
Pros & Cons: The primary advantages of wood include its versatility in design and ease of machining. It can be finished in various ways to enhance its appearance. On the downside, wood is less durable compared to metals and may require regular maintenance to prevent wear and tear.
Impact on Application: Wood is ideal for indoor applications, especially in environments where aesthetics are important, such as offices and restaurants. It is less suitable for outdoor use unless treated for weather resistance.
Considerations for International Buyers: Buyers should consider local wood regulations and certifications, such as FSC (Forest Stewardship Council) standards. Compliance with environmental regulations is crucial, particularly in Europe and North America.
What Are the Advantages of Using Metal (Steel) for Custom Tables?
Key Properties: Steel boasts high strength and durability, with excellent temperature and pressure ratings. It is resistant to corrosion when treated, making it suitable for various applications.
Pros & Cons: The main advantage of steel is its longevity and robustness, making it perfect for heavy-duty tables. However, it can be heavier and more expensive than wood or plastic, and it may require specialized manufacturing processes.
Impact on Application: Steel tables are commonly used in industrial settings, outdoor environments, and places requiring high durability. They can withstand harsh conditions and heavy loads.
Considerations for International Buyers: Compliance with international standards such as ASTM (American Society for Testing and Materials) or DIN (Deutsches Institut für Normung) is essential. Buyers should also consider the availability of steel grades in their region.
Why Choose Plastic for Custom Tables?
Key Properties: Plastic materials are lightweight and resistant to moisture and chemicals. They can be molded into various shapes and colors, providing flexibility in design.
Pros & Cons: The advantages of plastic include cost-effectiveness and ease of maintenance. However, they may not have the same aesthetic appeal or durability as wood or metal, and some plastics can degrade under UV light.
Impact on Application: Plastic tables are suitable for casual settings, outdoor use, and environments where weight is a concern. They are often used in schools, cafes, and event spaces.
Considerations for International Buyers: Buyers should ensure that the plastic materials meet safety and environmental standards specific to their region, such as REACH (Registration, Evaluation, Authorisation and Restriction of Chemicals) in Europe.
What Are the Benefits of Using Glass for Custom Tables?
Key Properties: Glass is non-porous and resistant to stains, making it easy to clean. It can withstand moderate temperatures but may be prone to shattering under extreme pressure.
Pros & Cons: Glass tables offer a modern aesthetic and can create an illusion of space in smaller areas. However, they are generally more fragile than other materials and can be heavy, complicating transportation and assembly.
Impact on Application: Glass is often used in contemporary office environments, dining areas, and design-focused spaces. It is less suitable for high-traffic areas due to its fragility.
Considerations for International Buyers: Compliance with safety standards, such as tempered glass regulations, is critical. Buyers should also consider the logistics of shipping glass, which may require special handling.
Summary Table of Material Selection for Custom Tables
Material | Typical Use Case for tables custom | Key Advantage | Key Disadvantage/Limitation | Relative Cost (Low/Med/High) |
---|---|---|---|---|
Wood | Indoor furniture, offices, restaurants | Aesthetic appeal and versatility | Susceptible to moisture damage | Medium |
Metal (Steel) | Industrial settings, outdoor environments | High durability and strength | Heavier and more expensive | High |
Plastic | Casual settings, schools, cafes | Lightweight and cost-effective | Less durable and UV degradation | Low |
Glass | Contemporary offices, dining areas | Modern aesthetic and easy to clean | Fragile and heavy | Medium to High |
This guide provides a comprehensive overview of the strategic selection of materials for custom tables, helping international B2B buyers make informed decisions that align with their specific needs and compliance requirements.
In-depth Look: Manufacturing Processes and Quality Assurance for tables custom
What Are the Key Manufacturing Processes for Custom Tables?
When it comes to manufacturing custom tables, understanding the stages involved is crucial for B2B buyers. The typical manufacturing process comprises several key stages: material preparation, forming, assembly, and finishing. Each stage plays a vital role in ensuring the final product meets the required specifications and quality standards.
How Does Material Preparation Work in Custom Table Manufacturing?
Material preparation is the initial step in the manufacturing process, where raw materials such as wood, metal, or composite materials are sourced and prepared. This stage may involve cutting materials to size, treating wood for durability, or coating metals to prevent corrosion. B2B buyers should inquire about the sourcing of materials, as quality materials directly impact the longevity and aesthetic appeal of the tables.
What Forming Techniques Are Commonly Used in Custom Table Production?
Forming is the next stage, where the prepared materials are shaped into the desired form. Common techniques include:
- CNC Machining: This computer-controlled process allows for precise cuts and intricate designs, making it ideal for custom orders.
- Woodworking Techniques: Methods such as lamination, veneering, and joinery are employed to construct wooden tables with strength and style.
- Metal Fabrication: Techniques like welding, bending, and stamping are used for metal parts, ensuring structural integrity.
Understanding these techniques helps B2B buyers assess the capabilities of their suppliers and ensure that the manufacturing process aligns with their design specifications.
How Are Custom Tables Assembled?
The assembly phase involves bringing together all components of the table, including legs, tabletops, and any additional features like drawers or extensions. This stage may include:
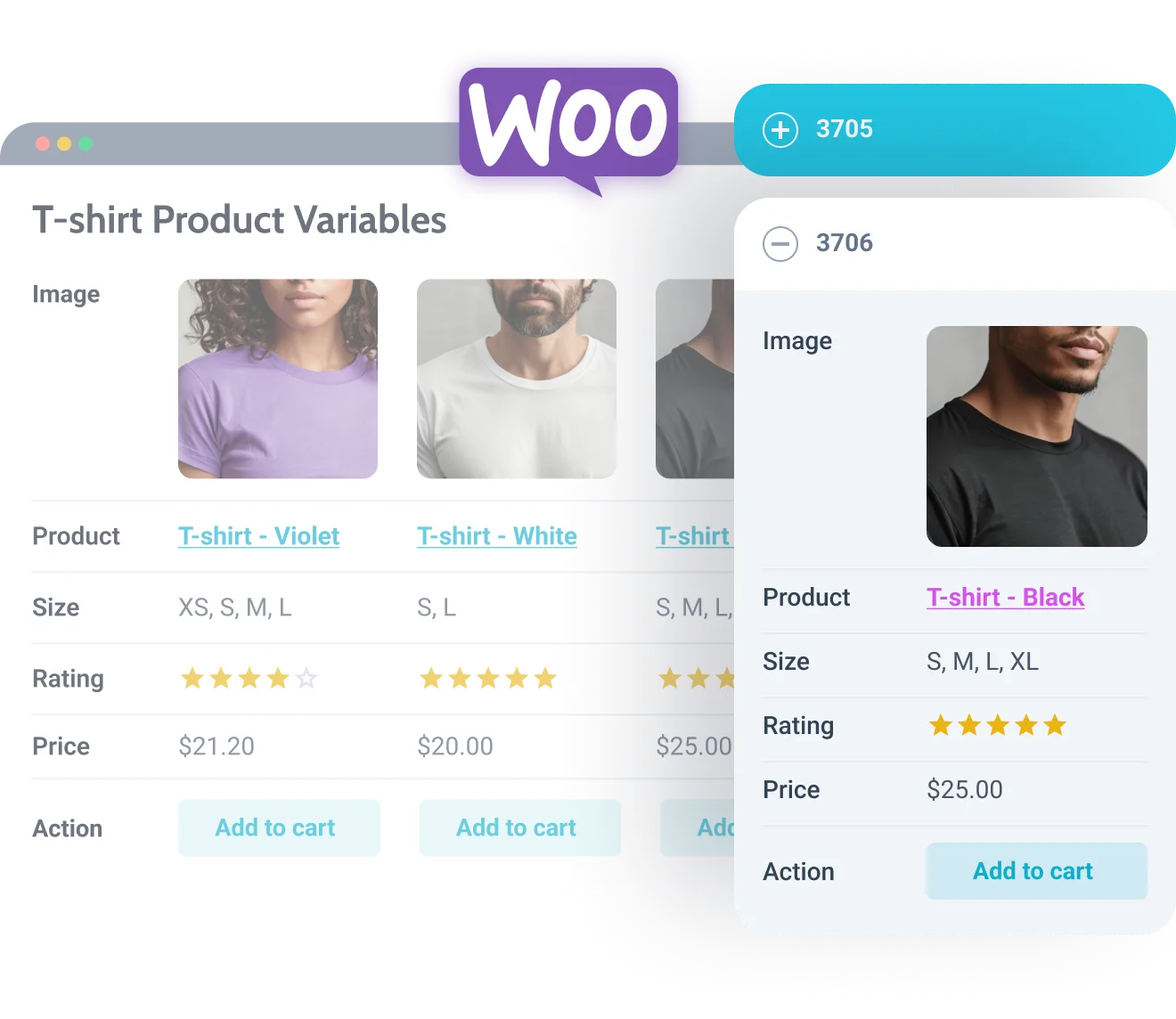
A stock image related to tables custom.
- Joinery: Using various techniques such as dowels, screws, or adhesives to secure parts together.
- Quality Checks: Conducting initial inspections to ensure that parts fit correctly and meet design specifications.
B2B buyers should ensure that the assembly process is efficient and that it adheres to industry standards to minimize defects.
What Finishing Techniques Enhance the Quality of Custom Tables?
Finishing is the final stage of the manufacturing process, where the table’s surface is treated to enhance its appearance and durability. Common finishing techniques include:
- Staining and Sealing: Applying stains to enhance the wood’s natural beauty, followed by sealants to protect against wear and moisture.
- Painting and Powder Coating: For metal components, these techniques provide a durable and attractive finish.
- Polishing: This process gives the final product a smooth surface and a high-gloss appearance.
B2B buyers should discuss finishing options with suppliers to ensure that the desired aesthetic and durability are achieved.
What Quality Assurance Measures Are Essential for Custom Tables?
Quality assurance (QA) is a critical aspect of the manufacturing process, ensuring that the final product meets the required specifications and standards. International standards like ISO 9001 and industry-specific certifications such as CE or API play a significant role in establishing credibility and quality.
How Do International Standards Influence Quality Assurance in Custom Table Manufacturing?
ISO 9001 is a widely recognized standard that outlines the criteria for a quality management system. Compliance with this standard indicates that the manufacturer has robust processes in place to ensure consistent quality. B2B buyers should prioritize suppliers who are ISO certified, as this can reduce the risk of defects and enhance customer satisfaction.
What Are the Key Quality Control Checkpoints in Custom Table Manufacturing?
Quality control (QC) checkpoints are integral to maintaining high standards throughout the manufacturing process. Typical checkpoints include:
- Incoming Quality Control (IQC): Inspection of raw materials upon arrival to ensure they meet specifications.
- In-Process Quality Control (IPQC): Ongoing inspections during the manufacturing process to identify any issues early on.
- Final Quality Control (FQC): A thorough inspection of the finished product before it is shipped to customers.
Implementing these checkpoints helps identify defects at various stages, ultimately leading to a higher-quality product.
How Can B2B Buyers Verify Supplier Quality Control Processes?
B2B buyers should take proactive steps to verify the quality control processes of their suppliers. Here are some actionable strategies:
- Conduct Audits: Schedule regular audits of suppliers’ facilities to review their quality management systems and manufacturing processes.
- Request Quality Reports: Suppliers should provide documentation detailing their quality control measures, including inspection results and compliance with international standards.
- Engage Third-Party Inspectors: Utilizing third-party inspection services can provide an unbiased assessment of the supplier’s quality control processes.
By actively engaging in these practices, B2B buyers can ensure that they are partnering with reliable manufacturers who prioritize quality.
What Nuances Should International B2B Buyers Consider for Quality Assurance?
For international B2B buyers, particularly those from Africa, South America, the Middle East, and Europe, understanding the nuances of quality assurance is crucial. Different regions may have specific regulations and standards that impact manufacturing practices.
- Local Regulations: Buyers should familiarize themselves with local regulations and standards that may influence product safety and quality in their respective markets.
- Cultural Differences: Communication styles and business practices may vary across regions, impacting negotiations and agreements. Establishing clear expectations around quality can help mitigate misunderstandings.
- Currency and Logistics: Consider the implications of currency fluctuations and shipping logistics, which can affect the overall cost and quality of the final product.
By understanding these nuances, B2B buyers can make informed decisions and build successful partnerships with suppliers across the globe.
Practical Sourcing Guide: A Step-by-Step Checklist for ‘tables custom’
In the competitive landscape of B2B procurement, sourcing custom tables requires a structured approach to ensure quality, compliance, and cost-effectiveness. This guide provides a practical checklist for international buyers, particularly from Africa, South America, the Middle East, and Europe, to navigate the complexities of sourcing custom tables.
Step 1: Define Your Requirements Clearly
Start by outlining the specific requirements for your custom tables. Consider dimensions, materials, design features, and functionality. A clear specification helps suppliers understand your needs and minimizes miscommunication.
– What to Include:
– Size and shape preferences (e.g., rectangular, round).
– Material choices (e.g., wood, metal, glass).
– Intended use (e.g., conference, dining, or workspace).
Step 2: Conduct Market Research on Suppliers
Research potential suppliers to identify those who specialize in custom table manufacturing. Understanding the market landscape is crucial to finding a supplier that aligns with your quality and budget expectations.
– Key Actions:
– Use platforms like Alibaba, ThomasNet, or local directories.
– Look for suppliers with positive reviews and a strong online presence.
Step 3: Evaluate Supplier Credentials and Experience
Before engaging with suppliers, verify their credentials and industry experience. An established supplier is likely to deliver higher quality and reliability.
– What to Check:
– Certifications (e.g., ISO, CE) that demonstrate quality standards.
– Years in business and previous projects similar to your requirements.
Step 4: Request and Review Samples
Always request samples before making a bulk order. This step allows you to assess the quality of materials, craftsmanship, and overall design.
– Considerations:
– Ensure the samples reflect your exact specifications.
– Evaluate the durability and finish of the materials used.
Step 5: Negotiate Terms and Pricing
Once you’ve shortlisted suppliers, initiate negotiations to secure the best terms. Discuss pricing, payment terms, lead times, and warranty provisions.
– Focus Areas:
– Look for flexibility in payment terms, especially for larger orders.
– Clarify delivery timelines to ensure they align with your project schedule.
Step 6: Verify Logistics and Shipping Capabilities
Understanding the supplier’s logistics is essential to avoid delays. Confirm their shipping capabilities, especially if you are sourcing internationally.
– Key Questions:
– What shipping methods do they use, and what are the associated costs?
– How do they handle customs clearance and potential tariffs?
Step 7: Establish a Quality Control Process
Before finalizing your order, set up a quality control process. This ensures that the final products meet your specifications and quality standards upon delivery.
– Steps to Implement:
– Define quality benchmarks that the supplier must adhere to.
– Consider third-party inspections if sourcing from overseas suppliers.
By following this structured checklist, international B2B buyers can navigate the complexities of sourcing custom tables effectively, ensuring that they receive quality products that meet their specific needs.
Comprehensive Cost and Pricing Analysis for tables custom Sourcing
What Are the Key Cost Components in Custom Tables Sourcing?
When sourcing custom tables, understanding the cost structure is crucial for international B2B buyers. The primary cost components include:
-
Materials: The choice of materials (e.g., hardwood, metal, glass) significantly impacts the overall cost. Premium materials will increase the base price but can enhance durability and aesthetics, which may justify the investment.
-
Labor: Labor costs vary by region. In countries with lower labor costs, such as parts of Africa and South America, you may find competitive pricing. However, skilled craftsmanship in regions like Europe can lead to higher labor expenses but often results in superior quality.
-
Manufacturing Overhead: This includes indirect costs associated with production, such as utilities, rent, and equipment maintenance. Understanding the overhead in different regions can influence your choice of suppliers.
-
Tooling: Custom designs may require specific tooling, which can be a one-time investment or a recurring cost depending on the production scale. It’s essential to factor this into your budget, especially for large orders.
-
Quality Control (QC): Ensuring product quality can add costs, but it is a vital investment. QC processes help minimize defects and ensure compliance with international standards.
-
Logistics: Shipping costs can vary greatly based on the distance, mode of transport, and freight terms. Understanding Incoterms (International Commercial Terms) can help you negotiate better shipping arrangements.
-
Margin: Suppliers typically include a profit margin in their pricing. Understanding the market standards for margins can help you assess whether a quote is competitive.
How Do Price Influencers Affect Custom Tables Pricing?
Several factors influence the pricing of custom tables:
-
Volume and Minimum Order Quantity (MOQ): Larger orders often lead to lower per-unit costs due to economies of scale. Suppliers may offer discounts for bulk purchases, so consider your inventory needs carefully.
-
Specifications and Customization: Highly customized tables (unique designs, sizes, or features) may incur additional costs. Ensure your design specifications are clear to avoid unexpected price increases.
-
Materials and Quality Certifications: Premium materials and certified products (e.g., eco-friendly or safety standards) can increase costs. However, these features can enhance your brand’s reputation and appeal in the market.
-
Supplier Factors: Established suppliers may charge higher prices due to their reputation and reliability. Conversely, new entrants might offer lower prices to gain market share. Evaluating supplier reliability is crucial to ensure quality.
What Are the Best Buyer Tips for Cost-Efficient Sourcing?
To navigate the complexities of custom table sourcing, consider these actionable tips:
-
Negotiation: Don’t hesitate to negotiate terms and pricing. Suppliers often have room to adjust costs based on order size or payment terms.
-
Cost-Efficiency: Analyze the Total Cost of Ownership (TCO), which includes purchase price, maintenance, and potential resale value. Sometimes, investing more upfront can save costs in the long run.
-
Pricing Nuances for International Buyers: Be aware of currency fluctuations, tariffs, and taxes that can affect pricing. Engage with suppliers who understand these factors to avoid surprises.
-
Local Market Insights: For buyers in Africa, South America, the Middle East, and Europe, leveraging local market insights can provide valuable data for negotiating prices and assessing supplier credibility.
-
Quality Over Price: While it may be tempting to choose the lowest price, consider the long-term benefits of quality. A well-made table can enhance your business image and reduce replacement costs.
Disclaimer on Indicative Prices
Pricing for custom tables can vary widely based on the factors discussed. Always request detailed quotes and be prepared for fluctuations based on market conditions, material availability, and other external factors.
Alternatives Analysis: Comparing tables custom With Other Solutions
In the evolving landscape of B2B solutions, understanding the range of available options is crucial for making informed purchasing decisions. When considering custom tables, international buyers should evaluate viable alternatives that can meet their unique requirements. This comparison will provide insights into various solutions, helping businesses from Africa, South America, the Middle East, and Europe make strategic choices.
Comparison Aspect | Tables Custom | Modular Tables | Folding Tables |
---|---|---|---|
Performance | High durability and tailored for specific use cases | Versatile but may lack the robustness of custom builds | Good for temporary use but less durable |
Cost | Higher initial investment but long-term savings | Moderate cost with flexibility | Lower initial cost but may require replacement sooner |
Ease of Implementation | Requires design and manufacturing time | Quick to assemble and disassemble | Very easy to set up and transport |
Maintenance | Low maintenance if designed properly | Moderate maintenance required | Regular maintenance needed for hinges and joints |
Best Use Case | Ideal for permanent installations requiring specific dimensions | Suitable for multi-functional spaces | Great for events and temporary setups |
What are the Pros and Cons of Modular Tables as an Alternative?
Modular tables offer a flexible solution for businesses needing adaptable spaces. Their design allows for various configurations, making them suitable for both collaborative environments and formal settings. The moderate cost and ease of assembly make them appealing for companies with fluctuating space requirements. However, the performance might not match that of custom tables, particularly in terms of durability and longevity. Over time, modular tables may require more frequent replacements, impacting overall cost-effectiveness.
How Do Folding Tables Compare as an Alternative?
Folding tables are a practical option for businesses that prioritize portability and quick setup. They are cost-effective and perfect for temporary events or situations where space is limited. Their lightweight nature and ease of transport make them ideal for trade shows, conferences, and outdoor gatherings. Nevertheless, their durability is often compromised compared to custom and modular tables. Frequent use can lead to wear and tear, necessitating more regular replacements, which can add to long-term costs.
Conclusion: How Can B2B Buyers Choose the Right Solution for Their Needs?
Selecting the right table solution hinges on understanding the specific needs of your business. Buyers should assess their priorities, such as budget constraints, intended use, and required durability. Custom tables, while requiring a higher upfront investment, offer tailored solutions that can provide significant long-term value. In contrast, modular and folding tables can serve well in flexible environments but may not offer the same durability. By evaluating these factors and the comparative advantages of each option, B2B buyers can make informed decisions that align with their operational goals.
Essential Technical Properties and Trade Terminology for tables custom
What Are the Key Technical Properties of Custom Tables?
When sourcing custom tables, understanding specific technical properties is crucial for ensuring that the product meets your business requirements. Here are some critical specifications to consider:
1. Material Grade
The material used in manufacturing custom tables significantly impacts durability, aesthetics, and maintenance. Common materials include hardwoods, metal, and composite materials. Each material has its own grade, which indicates its quality and suitability for different applications. For instance, high-grade hardwoods like oak or cherry are preferable for high-end furniture due to their strength and visual appeal.
2. Tolerance
Tolerance refers to the allowable deviation from a specified dimension. In the context of custom tables, tight tolerances ensure that components fit together precisely, enhancing stability and longevity. For B2B buyers, understanding tolerance specifications is essential to avoid costly adjustments and ensure a seamless assembly process.
3. Finish Type
The finish applied to a custom table affects both its appearance and resistance to wear and tear. Common finishes include varnish, lacquer, and oil. Each type has its own advantages; for instance, lacquer provides a glossy look but may require more maintenance over time. Selecting the right finish is vital for aligning with the intended use and environment of the table.
4. Load Capacity
Understanding the load capacity is critical for ensuring that the custom table can support the intended weight without compromising safety or structural integrity. This specification is particularly important for tables used in commercial settings, such as restaurants or offices, where heavy items may be placed on them regularly.
5. Dimensions
Custom tables are made to fit specific spaces and needs. Therefore, accurate measurements of height, width, and depth are fundamental. Buyers should provide precise dimensions to manufacturers to avoid issues during installation. Additionally, considering ergonomic dimensions can enhance user comfort, especially in work environments.
What Are Common Trade Terms in the Custom Tables Industry?
Familiarizing yourself with industry jargon can streamline the purchasing process and foster effective communication with suppliers. Here are several essential terms to know:
1. OEM (Original Equipment Manufacturer)
An OEM refers to a company that produces parts or equipment that may be marketed by another manufacturer. In the context of custom tables, understanding whether you are dealing with an OEM can affect product quality and customization options.
2. MOQ (Minimum Order Quantity)
MOQ is the smallest number of units a supplier is willing to sell. This term is crucial for buyers to understand as it can affect inventory levels and overall costs. For businesses looking to minimize expenses, negotiating MOQs can lead to significant savings.
3. RFQ (Request for Quotation)
An RFQ is a formal document sent to suppliers requesting pricing and terms for specific products or services. For B2B buyers, crafting a detailed RFQ can lead to better pricing and service agreements, ensuring that your business receives competitive offers.
4. Incoterms (International Commercial Terms)
Incoterms are internationally recognized terms that define the responsibilities of buyers and sellers in international transactions. Understanding these terms is essential for B2B buyers engaged in cross-border purchases, as they clarify shipping costs, risks, and delivery obligations.
5. Lead Time
Lead time refers to the amount of time from placing an order to delivery. This term is critical for project planning, as longer lead times can affect business operations. Buyers should inquire about lead times during negotiations to ensure timely delivery of custom tables.
Conclusion
Navigating the complexities of purchasing custom tables involves a clear understanding of both technical properties and industry terminology. By familiarizing yourself with these specifications and terms, you can make informed decisions that align with your business needs, ultimately leading to successful procurement and enhanced operational efficiency.
Navigating Market Dynamics and Sourcing Trends in the tables custom Sector
What Are the Current Market Dynamics and Key Trends in the Custom Tables Sector?
The custom tables market is witnessing significant transformations driven by globalization and technological advancements. International B2B buyers, particularly from Africa, South America, the Middle East, and Europe, should recognize the growing demand for bespoke solutions that cater to specific business needs. Key trends include the increasing adoption of digital platforms for sourcing, which facilitates easier access to suppliers and enhances procurement processes. Technologies such as augmented reality (AR) are emerging, allowing buyers to visualize custom designs in their intended environments before making a purchase.
Moreover, the rise of e-commerce and online marketplaces has expanded the reach of manufacturers and suppliers, making it easier for international buyers to compare options and negotiate deals. In addition, sustainability is becoming a critical factor in the decision-making process, as businesses are increasingly prioritizing eco-friendly materials and ethical sourcing practices. This shift is particularly evident in markets where consumers are demanding transparency in supply chains, pushing companies to adopt responsible sourcing strategies.
How Can International Buyers Ensure Sustainability and Ethical Sourcing in Custom Tables?
As the environmental impact of production processes comes under scrutiny, sustainability in the custom tables sector is gaining prominence. Buyers should consider the lifecycle of materials used in manufacturing tables, opting for sustainable options such as reclaimed wood, bamboo, or recycled materials. Certifications such as Forest Stewardship Council (FSC) and Global Recycle Standard (GRS) can provide assurance that suppliers adhere to responsible practices.
Ethical sourcing not only involves selecting sustainable materials but also ensuring fair labor practices within the supply chain. Buyers should conduct thorough due diligence to verify that suppliers maintain ethical labor standards, particularly in regions where these practices may be compromised. Building partnerships with suppliers who prioritize sustainability can enhance brand reputation and appeal to environmentally conscious consumers.
What Is the Evolution of the Custom Tables Market and Its Implications for B2B Buyers?
The custom tables market has evolved significantly over the last few decades, transitioning from traditional craftsmanship to a blend of modern technology and artisanal skills. Initially, custom tables were primarily crafted by local artisans, limiting availability and accessibility. However, the advent of globalization has enabled manufacturers to scale their operations while maintaining bespoke offerings.
Today, buyers benefit from a broader range of design options and materials, supported by technological innovations that allow for greater customization. This evolution has transformed the procurement process, enabling businesses to source unique products that align with their brand identity and operational needs. For B2B buyers, understanding this evolution is crucial as it highlights the importance of leveraging both traditional craftsmanship and modern technology in sourcing strategies.
In summary, navigating the custom tables market requires an awareness of current trends, a commitment to sustainability, and an understanding of the market’s evolution to make informed purchasing decisions. By prioritizing these aspects, international B2B buyers can ensure they are sourcing high-quality, ethically produced custom tables that meet their specific needs while contributing positively to the environment and society.
Frequently Asked Questions (FAQs) for B2B Buyers of tables custom
-
How do I choose the right supplier for custom tables?
Choosing the right supplier for custom tables involves several key considerations. Start by evaluating the supplier’s experience and specialization in the type of tables you need. Request samples of their previous work to assess quality and craftsmanship. Check for certifications or compliance with international standards, especially if you’re sourcing from regions like Africa or South America, where quality assurance may vary. Finally, read reviews and ask for references from other B2B clients to ensure reliability and good customer service. -
What are the key factors to consider when customizing tables for my business?
When customizing tables, consider the material, size, design, and functionality. Determine the specific needs of your business, such as the type of use (e.g., dining, office, display), and the environment (indoor or outdoor). Collaborate closely with your supplier to explore design options and materials that align with your brand. Additionally, ensure that the chosen customization options adhere to local regulations and market preferences in your region. -
What are typical minimum order quantities (MOQs) for custom tables?
Minimum order quantities for custom tables can vary significantly based on the supplier and the complexity of the design. Generally, MOQs can range from as low as 10 to as high as 100 units. Suppliers may offer lower MOQs for simpler designs or more standardized products. It’s advisable to discuss your specific needs with potential suppliers to negotiate favorable terms, especially if you’re a small business or just starting. -
What payment terms should I expect when sourcing custom tables internationally?
Payment terms for international B2B transactions often include upfront deposits, milestone payments, and final payments upon delivery. Common practices involve a 30-50% deposit before production begins, with the balance due upon completion or delivery. Ensure to clarify payment methods, such as bank transfers or letters of credit, and consider using escrow services for added security. Understanding the payment terms upfront can prevent misunderstandings and facilitate smoother transactions. -
How can I ensure quality assurance (QA) for my custom tables?
To ensure quality assurance for custom tables, establish a clear QA process with your supplier. This may include setting quality standards, conducting regular inspections throughout the production process, and requesting pre-shipment samples. It’s also beneficial to have a third-party inspection company review the products before they are shipped to ensure they meet your specifications and standards. This proactive approach helps mitigate risks associated with product defects or non-compliance. -
What logistics considerations should I keep in mind when importing custom tables?
When importing custom tables, consider shipping methods, customs duties, and lead times. Depending on the size and weight of the tables, you might choose sea freight for cost efficiency or air freight for speed. Be aware of import regulations in your country, including necessary documentation and tariffs. Work closely with your logistics provider to plan for potential delays and ensure that your tables arrive in optimal condition. -
How do I handle disputes with suppliers over custom table orders?
Handling disputes with suppliers requires clear communication and documentation. Start by discussing the issue directly with the supplier to seek an amicable resolution. If necessary, refer to the contractual terms agreed upon at the outset of the transaction. Mediation or arbitration may be options if direct communication fails. It’s crucial to maintain a professional demeanor and focus on finding a solution that satisfies both parties, as long-term relationships are vital in B2B transactions.
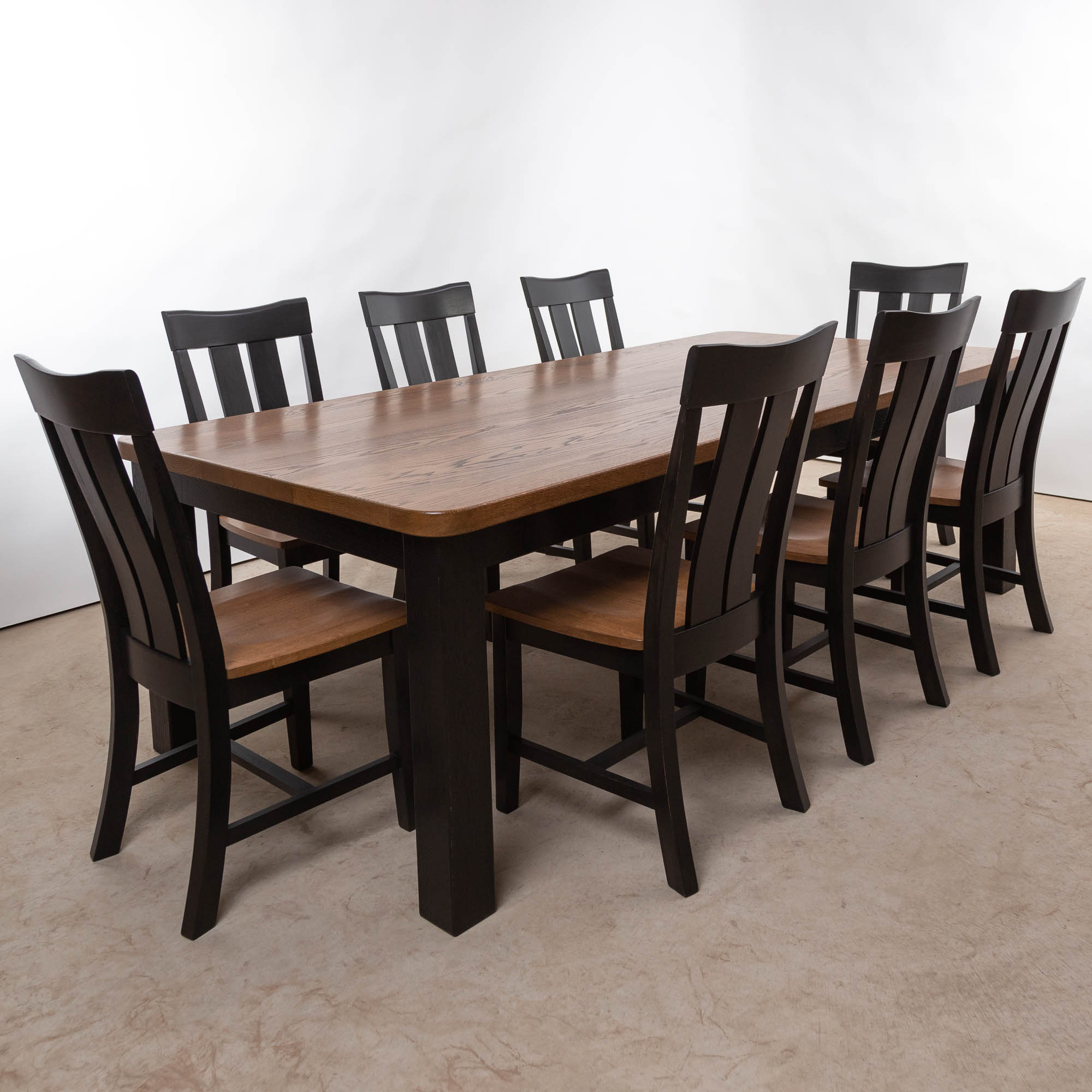
A stock image related to tables custom.
- What are the trends in custom table design that I should be aware of?
Current trends in custom table design include sustainability, multifunctionality, and ergonomic features. Buyers are increasingly looking for eco-friendly materials and designs that support remote work or flexible use in various environments. Additionally, customization that reflects unique branding and cultural significance is gaining popularity, especially in diverse markets across Africa, South America, the Middle East, and Europe. Staying informed about these trends can help you make more informed purchasing decisions that resonate with your target audience.
Important Disclaimer & Terms of Use
⚠️ Important Disclaimer
The information provided in this guide, including content regarding manufacturers, technical specifications, and market analysis, is for informational and educational purposes only. It does not constitute professional procurement advice, financial advice, or legal advice.
While we have made every effort to ensure the accuracy and timeliness of the information, we are not responsible for any errors, omissions, or outdated information. Market conditions, company details, and technical standards are subject to change.
B2B buyers must conduct their own independent and thorough due diligence before making any purchasing decisions. This includes contacting suppliers directly, verifying certifications, requesting samples, and seeking professional consultation. The risk of relying on any information in this guide is borne solely by the reader.
Strategic Sourcing Conclusion and Outlook for tables custom
What Are the Key Takeaways for B2B Buyers in Custom Tables?
In conclusion, strategic sourcing for custom tables is pivotal for B2B buyers aiming to enhance their operational efficiency and product offerings. Understanding the nuances of supplier selection, material choices, and design flexibility enables companies to tailor solutions that meet specific market demands. By leveraging partnerships with manufacturers from diverse regions, including Africa, South America, the Middle East, and Europe, buyers can access innovative designs and competitive pricing.
How Can International Buyers Enhance Their Strategic Sourcing Approach?
To maximize the value from strategic sourcing, international B2B buyers should prioritize clear communication and establish long-term relationships with suppliers. This not only fosters trust but also encourages collaboration on innovative designs that can set companies apart in a competitive marketplace. Engaging in market research to understand regional trends and consumer preferences can further inform sourcing decisions.
What Does the Future Hold for Custom Tables in Global Markets?
Looking ahead, the demand for customizable and sustainable table solutions is expected to rise. Buyers should remain proactive by adapting to changing market dynamics and consumer preferences. By integrating sustainable practices into sourcing strategies, businesses can not only enhance their brand reputation but also align with global sustainability goals. Now is the time for international B2B buyers to take action and refine their sourcing strategies to capitalize on emerging opportunities in the custom tables market.