Discover Cost-Saving Strategies in Forging China (2025)
Introduction: Navigating the Global Market for forging china
Navigating the global market for forging in China presents a unique set of challenges for international B2B buyers. As businesses in Africa, South America, the Middle East, and Europe increasingly seek to source high-quality forged components, understanding the intricacies of this market is essential. The complexity of forging processes, coupled with varying quality standards and supplier reliability, can make sourcing forged products daunting. This guide aims to demystify these challenges by providing a comprehensive overview of forging in China, covering essential aspects such as types of forging processes, applications across industries, effective supplier vetting techniques, and cost considerations.
By delving into the various forging methods—such as open-die and closed-die forging—buyers will gain insights into which processes best meet their specific needs. Furthermore, this guide emphasizes the importance of thorough supplier evaluation to ensure that partnerships are established with reliable manufacturers who adhere to international quality standards. The insights provided here empower international B2B buyers, including those from Brazil and Italy, to make informed purchasing decisions that drive operational efficiency and enhance product quality. Ultimately, this resource serves as a strategic tool for navigating the complexities of sourcing forged components from China, ensuring that buyers can confidently engage with suppliers and optimize their procurement strategies.
Understanding forging china Types and Variations
Type Name | Key Distinguishing Features | Primary B2B Applications | Brief Pros & Cons for Buyers |
---|---|---|---|
Open Die Forging | Uses flat dies; allows for larger, simpler shapes; versatile. | Aerospace, automotive, and construction. | Pros: Cost-effective for large volumes. Cons: Limited precision for complex shapes. |
Closed Die Forging | Utilizes shaped dies; provides high precision and detail. | Precision components in machinery and tools. | Pros: High accuracy and surface finish. Cons: Higher setup costs. |
Rolled Forging | Involves rolling the metal into shape; ideal for long parts. | Rail tracks, rods, and bars. | Pros: Continuous production; good for long items. Cons: Limited to specific shapes. |
Hammer Forging | Employs hammers to shape metal; best for high-strength applications. | Heavy machinery, tools, and equipment. | Pros: Excellent mechanical properties. Cons: Labor-intensive and time-consuming. |
Precision Forging | Advanced techniques for intricate designs; ensures tight tolerances. | Medical devices, aerospace parts. | Pros: Very tight tolerances; reduces waste. Cons: More expensive due to complexity. |
What are the characteristics of Open Die Forging and its suitability for B2B buyers?
Open die forging is characterized by the use of flat dies to shape the metal, allowing for flexibility in producing larger and simpler shapes. This method is particularly suitable for industries such as aerospace and automotive, where large components are common. B2B buyers should consider the cost-effectiveness of this method for high-volume production, while keeping in mind that the precision may not meet the requirements for more complex designs.
How does Closed Die Forging differ and what are its key purchasing considerations?
Closed die forging involves the use of shaped dies that allow for higher precision and a better surface finish. This method is ideal for producing intricate components used in machinery and tools. B2B buyers should weigh the benefits of high accuracy against the increased initial setup costs, which can be significant. The investment in closed die forging can lead to substantial long-term savings due to reduced machining needs.
What advantages does Rolled Forging offer for specific applications?
Rolled forging is distinct in that it rolls the metal into the desired shape, making it particularly effective for long products like rail tracks and bars. This method supports continuous production, which is advantageous for B2B buyers needing consistent quantities of long items. However, the limitation to specific shapes may restrict flexibility, so buyers should evaluate their product requirements carefully.
What makes Hammer Forging a strong choice for heavy-duty applications?
Hammer forging utilizes heavy hammers to shape metal, resulting in high-strength components suitable for heavy machinery and tools. This method is known for producing excellent mechanical properties, making it a reliable choice for demanding applications. B2B buyers should consider the labor intensity and time required for hammer forging, which could impact lead times, especially for large orders.
Why is Precision Forging crucial for high-tech industries?
Precision forging employs advanced techniques to create intricate designs with tight tolerances, making it essential for high-tech industries such as medical devices and aerospace. This method minimizes waste and maximizes material efficiency, which is a significant consideration for B2B buyers focused on sustainability. However, the complexity of precision forging often translates to higher costs, so buyers must balance the need for precision with budget constraints.
Related Video: Aluminum Cold Forging Company in China
Key Industrial Applications of forging china
Industry/Sector | Specific Application of forging china | Value/Benefit for the Business | Key Sourcing Considerations for this Application |
---|---|---|---|
Automotive | Production of crankshafts and gears | Enhanced durability and performance of engine components | Need for high precision and quality control; compliance with international standards |
Aerospace | Manufacturing of landing gear components | Improved safety and reliability in critical applications | Certification requirements and traceability of materials used |
Oil & Gas | Creation of valves and fittings | Resistance to extreme pressures and temperatures | Sourcing from suppliers with experience in high-grade alloys and certifications |
Construction | Fabrication of structural components | Increased structural integrity and load-bearing capacity | Consideration of local regulations and standards for construction materials |
Marine | Production of propeller shafts and fittings | Enhanced corrosion resistance and longevity in harsh environments | Need for specialized materials that meet marine industry standards |
How is Forging China Used in the Automotive Industry?
In the automotive sector, forging China is essential for producing high-strength components like crankshafts and gears. These parts undergo significant stress and must maintain their integrity over time. By utilizing forging techniques, manufacturers can achieve superior mechanical properties, which translates to enhanced durability and performance of engine components. International buyers, particularly from Africa and South America, should prioritize suppliers who adhere to stringent quality control measures and international standards to ensure reliability.
What Are the Applications of Forging China in Aerospace Manufacturing?
Forging China plays a pivotal role in aerospace manufacturing, particularly in the production of landing gear components. These components are critical for aircraft safety and must withstand high loads and extreme conditions. The forging process enhances the material’s strength and reliability, making it suitable for such demanding applications. Buyers from Europe, such as Italy, must consider suppliers that can provide certified products and maintain traceability of materials to comply with industry regulations.
How is Forging China Beneficial in the Oil & Gas Sector?
In the oil and gas industry, forging China is utilized for the creation of valves and fittings that must endure high pressures and harsh environments. The forging process imparts superior mechanical properties, ensuring these components can withstand extreme conditions. For international buyers, especially in the Middle East, sourcing from experienced suppliers who specialize in high-grade alloys and possess necessary certifications is crucial to ensure safety and reliability in operations.
What Role Does Forging China Play in Construction Applications?
Forging China is integral in the construction industry for fabricating structural components that require high strength and durability. These components contribute to the overall integrity of buildings and infrastructure, ensuring they can bear significant loads. Buyers in this sector must be aware of local regulations and standards governing construction materials, as compliance is essential for project approval and safety.
How is Forging China Used in Marine Applications?
In the marine industry, forging China is vital for producing propeller shafts and fittings that require exceptional corrosion resistance and durability. These components are exposed to harsh marine environments, making the forging process essential for enhancing their longevity. Buyers should seek specialized materials that meet marine industry standards, ensuring that the components will perform reliably in challenging conditions.
Related Video: The World Biggest Heavy Duty Hammer Forging Factory
3 Common User Pain Points for ‘forging china’ & Their Solutions
Scenario 1: Navigating Quality Assurance in Forging China
The Problem:
B2B buyers often face significant challenges regarding quality assurance when sourcing forged products from China. Issues may arise from variations in manufacturing standards, particularly when dealing with suppliers who might not adhere to international quality benchmarks. For buyers from regions like Africa or South America, where local standards may differ considerably, the risk of receiving subpar products can jeopardize entire projects, leading to costly delays and reputation damage.
The Solution:
To mitigate these risks, it is essential for buyers to conduct thorough due diligence on potential suppliers. Start by requesting detailed documentation that showcases the supplier’s compliance with international quality standards, such as ISO certifications. Implementing a robust supplier evaluation process that includes site visits or third-party audits can also be beneficial. Buyers should consider utilizing inspection services that specialize in the Chinese manufacturing sector to verify product quality before shipment. Establishing clear communication channels and setting specific quality benchmarks in contracts will further ensure that expectations are met consistently.
Scenario 2: Managing Lead Times and Delivery Schedules
The Problem:
Long lead times and unpredictable delivery schedules are common pain points for B2B buyers sourcing forged components from China. Buyers may experience delays that stem from various factors, including production bottlenecks, customs issues, or unforeseen demand spikes. For businesses in Europe or the Middle East, this unpredictability can disrupt supply chains and affect production schedules, resulting in financial losses and strained customer relationships.
The Solution:
To address lead time challenges, buyers should develop a comprehensive supply chain strategy that includes multiple suppliers and contingency plans. When selecting suppliers, prioritize those with a proven track record of timely deliveries and transparent communication. Establishing a buffer stock of critical components can help manage short-term disruptions. Additionally, leveraging technology, such as supply chain management software, can enhance visibility and facilitate better planning. Regularly reviewing and optimizing inventory levels in response to market demands will also allow businesses to adapt quickly to changes.
Scenario 3: Overcoming Language and Cultural Barriers
The Problem:
Language and cultural barriers can create misunderstandings between international B2B buyers and Chinese forging suppliers. These barriers often lead to miscommunication about product specifications, timelines, and expectations. For buyers from regions like Africa or South America, where cultural contexts may differ significantly, the risk of misinterpretation can result in costly errors, such as ordering incorrect specifications or experiencing project delays.
The Solution:
To bridge the communication gap, buyers should consider employing bilingual staff or engaging local representatives who understand both the cultural nuances and the technical aspects of forging. Utilizing technology, such as translation software or communication platforms that support multiple languages, can also enhance clarity. Buyers should be explicit in their specifications and expectations, using visual aids like diagrams or samples to eliminate ambiguity. Establishing a rapport with suppliers through regular interactions can help build trust and foster better communication, ultimately leading to smoother transactions and successful partnerships.
Strategic Material Selection Guide for forging china
What are the Key Materials Used in Forging in China?
When selecting materials for forging in China, international B2B buyers must consider several factors, including the properties of the materials, their advantages and disadvantages, and their compliance with regional standards. Below, we analyze four common materials used in forging, focusing on their performance, application, and considerations for buyers from Africa, South America, the Middle East, and Europe.
How Does Carbon Steel Perform in Forging Applications?
Key Properties: Carbon steel is known for its high strength and hardness, making it suitable for high-stress applications. It has excellent wear resistance and can withstand elevated temperatures, which is critical in many industrial environments.
Pros & Cons: The primary advantage of carbon steel is its durability and strength, which make it ideal for heavy-duty applications. However, it is susceptible to corrosion if not properly treated, which can limit its use in certain environments. The manufacturing complexity can also increase with higher carbon content, requiring specialized processes.
Impact on Application: Carbon steel is often used in automotive and machinery components, where high tensile strength is essential. Its compatibility with various media makes it a versatile choice, but buyers must ensure proper surface treatments to prevent corrosion.
Considerations for International Buyers: Compliance with standards such as ASTM A36 or DIN 17100 is crucial for ensuring quality. Buyers should also consider local corrosion resistance requirements, especially in humid climates.
What Advantages Does Alloy Steel Offer for Forging?
Key Properties: Alloy steel contains various elements that enhance its properties, including improved toughness, hardness, and wear resistance. It is designed to perform well under extreme conditions, making it suitable for demanding applications.
Pros & Cons: The key advantage of alloy steel is its ability to be tailored for specific applications, providing a balance between strength and ductility. However, the cost can be higher than carbon steel due to the additional alloying elements, and the manufacturing process can be more complex.
Impact on Application: Alloy steel is commonly used in the manufacturing of gears, shafts, and other components that require high strength and resistance to fatigue. Its versatility allows it to be used in various industries, including aerospace and automotive.
Considerations for International Buyers: Buyers should be aware of the specific alloy compositions that meet their application needs and ensure compliance with international standards like JIS G4053. Understanding regional preferences for alloy grades can also influence purchasing decisions.
Why is Stainless Steel a Preferred Material in Forging?
Key Properties: Stainless steel is renowned for its corrosion resistance, making it ideal for applications in harsh environments. It maintains its strength at high temperatures and is easy to clean, which is vital in industries like food processing and pharmaceuticals.
Pros & Cons: The main advantage of stainless steel is its durability and resistance to rust and corrosion. However, it can be more expensive than carbon and alloy steels, and its machining can be more challenging due to its toughness.
Impact on Application: Stainless steel is widely used in applications requiring hygiene and corrosion resistance, such as in the food and beverage industry. Its compatibility with a variety of media makes it a versatile choice for international buyers.
Considerations for International Buyers: Compliance with standards such as ASTM A240 or EN 10088 is essential for ensuring product quality. Buyers must also consider the specific grades of stainless steel (e.g., 304, 316) that meet their application requirements.
How Does Titanium Impact Forging Processes?
Key Properties: Titanium is known for its high strength-to-weight ratio and excellent corrosion resistance. It performs well in extreme temperatures and is non-toxic, making it suitable for medical applications.
Pros & Cons: The primary advantage of titanium is its lightweight nature combined with exceptional strength, making it ideal for aerospace and medical applications. However, it is significantly more expensive than other materials and requires specialized forging processes.
Impact on Application: Titanium is often used in aerospace components, medical implants, and high-performance automotive parts. Its compatibility with various media is a significant advantage, especially in corrosive environments.
Considerations for International Buyers: Buyers must be aware of the high costs associated with titanium and ensure compliance with standards such as ASTM F136 for medical applications. Understanding the specific requirements for titanium alloys can also guide purchasing decisions.
Summary Table of Common Forging Materials
Material | Typical Use Case for forging china | Key Advantage | Key Disadvantage/Limitation | Relative Cost (Low/Med/High) |
---|---|---|---|---|
Carbon Steel | Automotive components | High strength and durability | Susceptible to corrosion | Medium |
Alloy Steel | Gears and shafts | Tailored properties for specific needs | Higher cost and manufacturing complexity | High |
Stainless Steel | Food processing equipment | Excellent corrosion resistance | More expensive and challenging to machine | High |
Titanium | Aerospace and medical implants | Lightweight with high strength | Very high cost and specialized processes | High |
This strategic material selection guide provides international B2B buyers with critical insights into the properties, advantages, and considerations for various materials used in forging in China. Understanding these factors can aid in making informed purchasing decisions that align with specific application requirements and regional standards.
In-depth Look: Manufacturing Processes and Quality Assurance for forging china
What Are the Main Stages of the Manufacturing Process for Forging in China?
The manufacturing process for forging in China consists of several key stages, each crucial for ensuring the integrity and quality of the final product. Understanding these stages can help international B2B buyers make informed decisions when sourcing forged components.
Material Preparation: How Is Raw Material Selected and Processed?
The first step in the forging process is material preparation, where the appropriate raw materials, typically metals like steel or aluminum, are chosen based on the specifications of the final product. Suppliers should provide detailed information about the grades of materials used, as this impacts strength, ductility, and overall performance.
Once the material is selected, it undergoes processes such as cutting, heating, and surface cleaning. The heating process is critical as it alters the material properties, making it easier to shape without cracking. Buyers should inquire about the methods used for material preparation to ensure that they meet industry standards.
Forming: What Techniques Are Employed in Forging?
The forming stage involves shaping the heated metal into the desired form through various techniques. Common methods include:
-
Open Die Forging: This method allows for large pieces to be shaped by applying pressure from multiple directions. It is ideal for creating large components but requires skilled operators for precision.
-
Closed Die Forging: In this technique, the metal is placed in a mold and shaped under high pressure. This method offers tighter tolerances and is suitable for producing complex shapes.
-
Upset Forging: This method involves increasing the diameter of a workpiece while reducing its length, often used for creating specific features like flanges.
Each method has its advantages and applications, depending on the complexity and size of the component required. B2B buyers should understand which techniques are used by their suppliers to ensure they align with their product requirements.
Assembly: How Are Forged Components Joined Together?
In cases where multiple forged components are required, assembly becomes essential. This stage may involve welding, bolting, or other joining techniques. Each method has its implications for the strength and integrity of the final assembly.
Buyers should ask suppliers about their assembly processes and the quality controls in place during this stage to prevent potential failures in the final product. It is also advisable to understand if the assembly process adheres to any international or industry-specific standards.
Finishing: What Post-Processing Techniques Are Commonly Used?
Finishing is the final stage in the forging process, involving various treatments to enhance the physical properties of the forged components. This may include:
-
Heat Treatment: This process improves the mechanical properties of the metal, such as hardness and tensile strength, through controlled heating and cooling cycles.
-
Surface Treatment: Techniques like shot blasting, polishing, or coating are applied to improve corrosion resistance and surface finish.
-
Machining: Final machining may be performed to achieve precise dimensions and tolerances.
Understanding the finishing processes used by suppliers helps B2B buyers ensure that the final products will meet their operational requirements and environmental conditions.
What Quality Assurance Measures Are Implemented in Forging?
Quality assurance is a critical aspect of the forging process, ensuring that products meet international standards and client specifications. Here are the key quality assurance measures that B2B buyers should be aware of:
Which International Standards Should Buyers Consider?
Many manufacturers in China adhere to international quality management standards such as ISO 9001, which ensures consistent quality across processes. Additionally, industry-specific certifications such as CE (for European markets) and API (for oil and gas applications) are essential for specific sectors.
Buyers should verify that their suppliers hold the necessary certifications and understand how these standards impact the manufacturing process and product quality.
What Are the Key Quality Control Checkpoints?
Quality control (QC) checkpoints are critical at various stages of the manufacturing process. Key checkpoints include:
-
Incoming Quality Control (IQC): This involves inspecting raw materials before they enter the production process to ensure they meet specified criteria.
-
In-Process Quality Control (IPQC): During manufacturing, regular inspections are conducted to monitor the process and ensure conformity to specifications.
-
Final Quality Control (FQC): This final inspection assesses the finished product against quality standards and specifications before shipment.
B2B buyers should inquire about the QC measures in place at each of these checkpoints to ensure that their suppliers maintain high-quality standards throughout the manufacturing process.
What Common Testing Methods Are Utilized?
To verify the quality of forged components, several testing methods are commonly employed, including:
-
Non-Destructive Testing (NDT): Techniques like ultrasonic testing and magnetic particle inspection assess the integrity of the material without causing damage.
-
Destructive Testing: This includes tensile tests and impact tests that evaluate the mechanical properties of the forged components by applying stress until failure.
Buyers should request information about the testing methods used by suppliers and the results of these tests to ensure compliance with quality standards.
How Can B2B Buyers Verify Supplier Quality Control?
Verifying a supplier’s quality control measures is essential for international B2B buyers, especially those from regions like Africa, South America, the Middle East, and Europe. Here are several strategies:
What Are the Best Practices for Supplier Audits?
Conducting audits is one of the most effective ways to assess a supplier’s quality control systems. Buyers can perform:
-
On-Site Audits: Visiting the manufacturing facility allows buyers to observe processes, equipment, and QC measures firsthand.
-
Third-Party Inspections: Engaging independent inspection agencies can provide unbiased reports on a supplier’s quality management systems.
Buyers should establish a clear audit schedule and criteria to ensure consistent evaluation of supplier performance.
How to Request Quality Reports and Certifications?
Buyers should always request quality reports and certifications from suppliers before finalizing contracts. These documents provide insights into the manufacturing processes, QC measures, and adherence to relevant standards.
Ensuring that suppliers provide transparent documentation helps mitigate risks associated with quality issues in the supply chain.
Conclusion
Understanding the manufacturing processes and quality assurance measures for forging in China is crucial for international B2B buyers. By focusing on material preparation, forming, assembly, finishing, and the various quality control checkpoints, buyers can ensure they select reliable suppliers that meet their specific requirements. Engaging with suppliers on quality standards and verification practices will further enhance the procurement process, leading to successful partnerships and high-quality products.
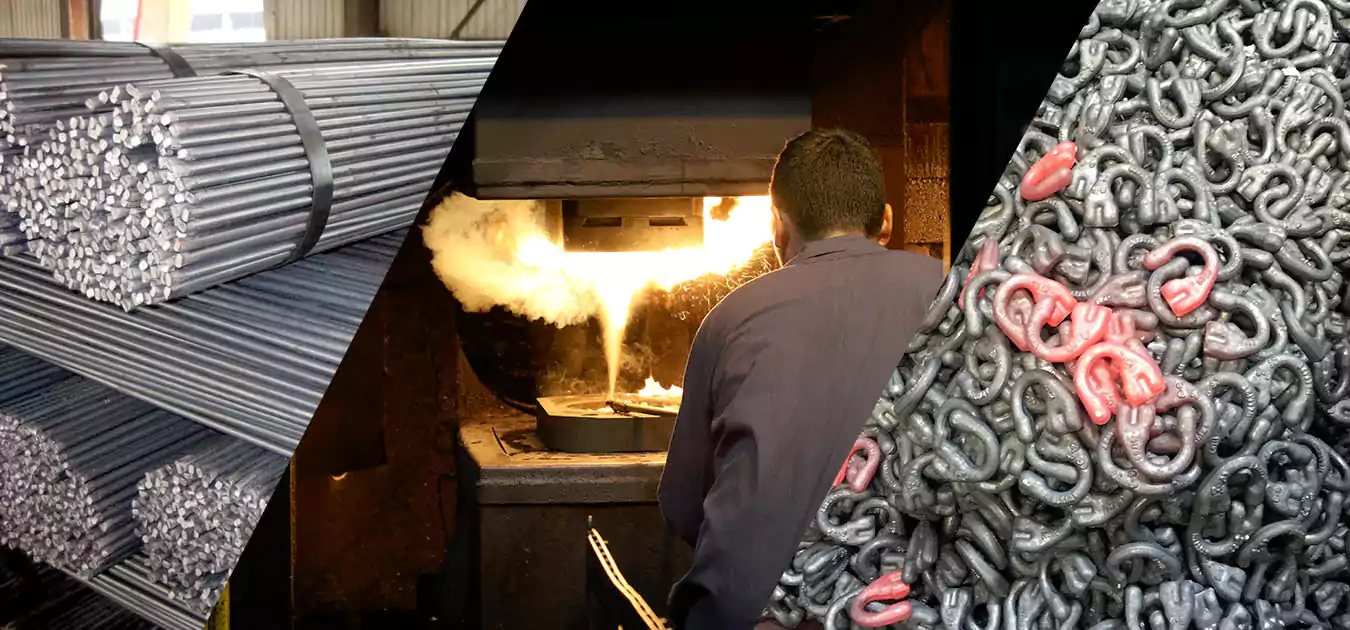
A stock image related to forging china.
Practical Sourcing Guide: A Step-by-Step Checklist for ‘forging china’
In the competitive landscape of international B2B trade, particularly for buyers looking to source forging products from China, having a structured approach is essential. This practical sourcing guide will provide a step-by-step checklist to streamline your procurement process, ensuring you make informed decisions and secure quality products.
Step 1: Define Your Technical Specifications
Establishing clear technical specifications is critical for successful sourcing. Determine the materials, dimensions, tolerances, and any specific standards required for your project. This clarity helps suppliers understand your exact needs and reduces the risk of miscommunication.
- Material Requirements: Specify the type of metal (e.g., steel, aluminum) and any coatings or treatments needed.
- Dimensional Accuracy: Provide detailed drawings or CAD files to communicate precise measurements.
Step 2: Research Potential Suppliers
Conduct thorough research to identify potential suppliers in China specializing in forging. Utilize online platforms, trade shows, and industry directories to compile a list of candidates.
- Supplier Reputation: Look for suppliers with a proven track record in your industry. Read reviews and testimonials from other B2B buyers.
- Industry Experience: Prioritize suppliers who have experience with similar products or industries to ensure they understand your specific needs.
Step 3: ✅ Verify Supplier Certifications
Before proceeding, verify that potential suppliers have the necessary certifications. This step ensures that they comply with international quality and safety standards.
- Quality Management Systems: Check for ISO 9001 certification or equivalent.
- Material Certifications: Request certificates for the materials they use to ensure they meet your specifications.
Step 4: Request Samples for Evaluation
To assess the quality of a supplier’s products, request samples of their forging work. This evaluation will help you determine if their products meet your technical specifications and quality expectations.
- Sample Testing: Conduct mechanical and dimensional tests on the samples to ensure they meet your requirements.
- Lead Time Assessment: Use this opportunity to gauge the supplier’s responsiveness and ability to meet deadlines.
Step 5: Negotiate Terms and Conditions
Once you have selected a potential supplier, engage in negotiations to finalize terms and conditions. This includes pricing, payment terms, and delivery schedules.
- Transparent Pricing: Ensure all costs are clearly outlined, including shipping and customs duties.
- Payment Options: Discuss payment methods that offer security for both parties, such as letters of credit.
Step 6: Establish a Quality Assurance Plan
A robust quality assurance plan is essential to ensure that the final products meet your specifications. Collaborate with your supplier to define quality control measures throughout the production process.
- Inspection Protocols: Determine the frequency and type of inspections that will be conducted during production.
- Final Inspection: Specify who will be responsible for the final quality check before shipment.
Step 7: Plan for Logistics and Customs Clearance
Finally, develop a logistics plan to manage the transportation and customs clearance of your forging products. Understanding the logistics involved will help prevent delays and additional costs.
- Shipping Options: Evaluate different shipping methods (air vs. sea) based on urgency and cost.
- Customs Regulations: Familiarize yourself with import regulations in your country to ensure smooth clearance.
By following this comprehensive checklist, international B2B buyers can navigate the complexities of sourcing forging products from China effectively. Each step is designed to minimize risks, enhance communication, and ultimately ensure a successful procurement process.
Comprehensive Cost and Pricing Analysis for forging china Sourcing
What Are the Key Cost Components in Forging China Sourcing?
When considering the sourcing of forged components from China, understanding the cost structure is essential. The main cost components include:
-
Materials: The type and quality of raw materials significantly influence costs. Common materials used in forging, such as carbon steel, alloy steel, and titanium, each have varying price points. Ensure to factor in market fluctuations in metal prices, which can impact your overall costs.
-
Labor: Labor costs in China can vary depending on the region and the skill level required. While China generally offers competitive labor rates, specialized labor for high-precision forging may demand higher wages.
-
Manufacturing Overhead: This includes expenses related to utilities, facility costs, and administrative expenses. Efficient manufacturing processes can help minimize these overheads, thus affecting the overall pricing.
-
Tooling: Tooling costs, which cover the design and production of molds and dies, are significant, especially for custom forged components. Higher initial tooling costs may be justified by lower per-unit costs in larger production runs.
-
Quality Control (QC): Implementing stringent QC measures is essential, particularly for industries with high safety standards. Quality assurance can add to costs but helps avoid potential losses from defective products.
-
Logistics: Transportation, customs duties, and warehousing can add significant costs, particularly for international shipments. Choosing the right shipping options and understanding Incoterms can optimize these expenses.
-
Margin: Suppliers typically include a profit margin in their pricing. Understanding the market dynamics and competitive landscape can help in negotiating a fair margin.
How Do Price Influencers Affect Forging Costs?
Several factors can influence the final pricing of forged products:
-
Volume and Minimum Order Quantity (MOQ): Larger order volumes typically lead to lower per-unit costs due to economies of scale. It’s crucial to discuss MOQs with suppliers to find a balance between affordability and inventory management.
-
Specifications and Customization: Custom specifications can lead to higher costs due to the need for unique tooling and processes. Clearly defining your requirements upfront can mitigate unexpected costs later.
-
Material Selection: The choice of materials not only impacts the cost but also the quality and performance of the final product. High-grade materials may incur higher initial costs but can lead to long-term savings through durability.
-
Quality Certifications: Depending on your industry, specific quality certifications may be required, which can add to costs. Suppliers with ISO or other relevant certifications may charge a premium but can offer peace of mind regarding product quality.
-
Supplier Factors: The reputation and reliability of the supplier can influence pricing. Established suppliers may charge more due to their proven track record and reliability.
-
Incoterms: Understanding Incoterms is vital for international transactions. They define responsibilities regarding shipping costs, insurance, and risk. Proper negotiation of Incoterms can lead to significant savings.
What Are the Best Buyer Tips for Cost-Efficiency in Forging?
-
Negotiate Effectively: Building a solid relationship with suppliers can lead to better pricing. Be prepared to negotiate terms and explore long-term partnerships, which may provide additional discounts.
-
Consider Total Cost of Ownership (TCO): When evaluating costs, factor in the TCO, which includes purchase price, maintenance, and potential savings from higher quality. A lower upfront cost may not always result in the best long-term value.
-
Research Market Prices: Stay informed about market trends and pricing for raw materials and labor. This knowledge can empower you during negotiations and help you identify fair pricing.
-
Be Clear on Specifications: Providing detailed specifications from the outset minimizes the risk of miscommunication and unexpected costs later on.
-
Evaluate Multiple Suppliers: Don’t settle for the first quote. Obtain multiple quotes from different suppliers to compare pricing, quality, and delivery times.
Disclaimer on Indicative Prices
Prices for forging components can fluctuate based on market conditions, material availability, and supplier-specific factors. Therefore, it is advisable to conduct thorough market research and obtain updated quotes before making purchasing decisions.
Alternatives Analysis: Comparing forging china With Other Solutions
When considering options for metalworking, international B2B buyers must evaluate various techniques and solutions to determine the best fit for their specific needs. This analysis focuses on comparing “forging China” with two viable alternatives: die casting and machining. Each method has unique advantages and applications, making it essential for businesses to assess their requirements and constraints before making a decision.
Comparison Table: Forging China vs. Alternatives
Comparison Aspect | Forging China | Die Casting | Machining |
---|---|---|---|
Performance | High strength and durability | Good surface finish, complex shapes | High precision and flexibility |
Cost | Moderate initial investment | Higher tooling costs, lower material waste | Variable costs based on design complexity |
Ease of Implementation | Requires skilled labor and specific equipment | Automated processes available | Requires skilled machinists and equipment |
Maintenance | Lower maintenance needs | Moderate maintenance; dies need replacement | Higher maintenance due to tool wear |
Best Use Case | Structural components, high-stress applications | Mass production of complex shapes | Custom parts, low to medium volume |
What Are the Pros and Cons of Die Casting as an Alternative to Forging China?
Die casting is a metal casting process that involves forcing molten metal into a mold under high pressure.
Pros:
– Complex Shapes: Die casting can produce intricate designs with thin walls, making it ideal for components that require detailed shapes.
– Surface Finish: It yields smooth surfaces that often require less finishing work.
– Efficiency: High production rates reduce the per-unit cost for large batches.
Cons:
– Material Limitations: It is primarily suitable for non-ferrous metals, which may not be as strong as forged products.
– High Tooling Costs: The initial investment in tooling can be significant, making it less viable for small runs.
How Does Machining Compare to Forging China?
Machining involves removing material from a workpiece to achieve desired dimensions and surface finishes.
Pros:
– Precision: Machining offers high accuracy and can produce parts to very tight tolerances.
– Material Versatility: It can work with a wide range of materials, including metals and plastics.
– Flexibility: Changes can be made easily to designs without the need for new molds.
Cons:
– Material Waste: This process can result in significant waste material, which can increase costs.
– Labor-Intensive: Skilled machinists are required, and setup times can be lengthy, affecting overall production efficiency.
How Can B2B Buyers Choose the Right Solution for Their Needs?
Choosing the right metalworking solution depends on multiple factors, including production volume, material requirements, and cost constraints. B2B buyers should start by assessing their project’s specific needs. For high-strength components, forging may be the best option. If the project requires intricate designs and high-volume production, die casting could be more suitable. Conversely, for high-precision components with lower production runs, machining might be the ideal choice. By aligning their production goals with the strengths and limitations of each method, buyers can make informed decisions that optimize both cost and performance.
Essential Technical Properties and Trade Terminology for forging china
What Are the Essential Technical Properties for Forging in China?
Understanding the technical properties of forged products is crucial for international B2B buyers. Here are some key specifications that can significantly impact procurement decisions:
-
Material Grade
The material grade refers to the specific type of metal used in forging, such as carbon steel, alloy steel, or stainless steel. Each grade has distinct mechanical properties, including strength, ductility, and corrosion resistance. For buyers, selecting the appropriate material grade ensures that the forged components meet the specific requirements of their applications, enhancing durability and performance. -
Tolerance
Tolerance indicates the permissible limit of variation in a physical dimension of the forged part. It is critical for ensuring that parts fit correctly during assembly and function as intended. In sectors like automotive or aerospace, where precision is paramount, understanding tolerance specifications helps buyers avoid costly rework and delays. -
Surface Finish
The surface finish of forged components can affect both aesthetics and functionality. Common finishes include rough, machined, or polished surfaces. Buyers should consider how surface quality influences wear resistance, corrosion protection, and the overall appearance of the final product. Proper surface treatments can enhance longevity and reduce maintenance costs. -
Mechanical Properties
Key mechanical properties include yield strength, tensile strength, and elongation. These properties determine how the forged product will perform under stress and load conditions. Buyers must assess these properties based on their application requirements to ensure reliability and safety. -
Heat Treatment
Heat treatment processes like quenching and tempering can significantly alter the mechanical properties of forged parts. Understanding the heat treatment process used for a specific product can help buyers gauge its performance under various conditions. This knowledge is essential for applications requiring specific strength and hardness levels.
What Trade Terminology Should International Buyers Know?
Familiarity with industry jargon can facilitate smoother negotiations and enhance communication with suppliers. Here are some common terms relevant to forging in China:
-
OEM (Original Equipment Manufacturer)
OEM refers to a company that produces parts and equipment that may be marketed by another manufacturer. For B2B buyers, working with OEMs can ensure high-quality components tailored to specific needs, often with custom designs. -
MOQ (Minimum Order Quantity)
MOQ is the smallest number of units a supplier is willing to sell. Understanding MOQ is crucial for buyers, especially for startups or smaller companies, as it can affect cash flow and inventory management. Negotiating lower MOQs can open opportunities for smaller orders without compromising quality. -
RFQ (Request for Quotation)
An RFQ is a document sent to suppliers requesting pricing and terms for specific products. For buyers, issuing an RFQ allows them to gather competitive quotes, facilitating informed decision-making regarding pricing and supplier selection. -
Incoterms (International Commercial Terms)
Incoterms are standardized trade terms that define the responsibilities of buyers and sellers in international transactions. Familiarity with terms like FOB (Free On Board) or CIF (Cost, Insurance, and Freight) helps buyers understand shipping responsibilities and costs, reducing potential disputes. -
Lead Time
Lead time refers to the period between placing an order and receiving the goods. For buyers, understanding lead times is essential for planning production schedules and inventory levels. It can also impact customer satisfaction if products are needed urgently. -
Die Forging vs. Open Die Forging
Die forging involves shaping metal using pre-made dies, while open die forging allows for more flexibility in shape and size. Buyers should understand these processes to choose the right type of forging based on their product specifications and production needs.
By mastering these technical properties and trade terms, international B2B buyers can navigate the complexities of the forging industry in China more effectively, ensuring they make informed purchasing decisions that align with their business goals.
Navigating Market Dynamics and Sourcing Trends in the forging china Sector
What Are the Current Market Dynamics and Key Trends in the Forging Sector in China?
The forging sector in China is experiencing transformative changes driven by globalization, technological advancements, and shifting consumer preferences. International B2B buyers, especially from regions like Africa, South America, the Middle East, and Europe, need to understand these dynamics to make informed sourcing decisions.
One of the primary drivers is the increasing demand for high-quality forged products across industries such as automotive, aerospace, and construction. The adoption of advanced manufacturing technologies, including automation and artificial intelligence, is enhancing production efficiency and product quality. Moreover, the rise of Industry 4.0 is facilitating real-time data analytics and predictive maintenance, allowing manufacturers to optimize their operations and reduce lead times.
Emerging trends include a focus on customization and the use of lightweight materials, which are critical for sectors like aerospace where weight reduction can lead to significant fuel savings. Furthermore, the shift towards online B2B platforms is making it easier for international buyers to connect with Chinese suppliers, compare prices, and evaluate product quality.
It is also essential to consider geopolitical factors, such as trade agreements and tariffs, which can affect sourcing strategies. For instance, buyers from Europe and the Middle East may face different regulations than those from Africa or South America. Understanding these nuances can aid in navigating the complexities of the global supply chain.
How Does Sustainability Impact Sourcing in the Forging Sector?
Sustainability and ethical sourcing are increasingly becoming non-negotiable aspects for B2B buyers in the forging sector. The environmental impact of forging processes, which can be resource-intensive and generate significant waste, has led to heightened scrutiny from both consumers and regulatory bodies.
To address these challenges, many Chinese manufacturers are adopting sustainable practices such as recycling scrap metal and implementing energy-efficient technologies. Buyers should seek suppliers who are committed to sustainability, as this not only reduces the carbon footprint but also enhances brand reputation. Certifications such as ISO 14001 can serve as indicators of a supplier’s commitment to environmental management.
Moreover, the demand for ‘green’ materials, including those with lower emissions during production, is on the rise. Buyers should prioritize suppliers who offer eco-friendly forging solutions, as this aligns with global sustainability goals and can lead to cost savings in the long run. Engaging with suppliers who uphold ethical labor practices is also essential, as transparency in supply chains is becoming a key criterion for international buyers.
What Is the Historical Context of the Forging Industry in China?
The forging industry in China has evolved significantly over the last few decades. Initially dominated by traditional methods, the sector has rapidly modernized since the 1980s, driven by economic reforms and increased foreign investment.
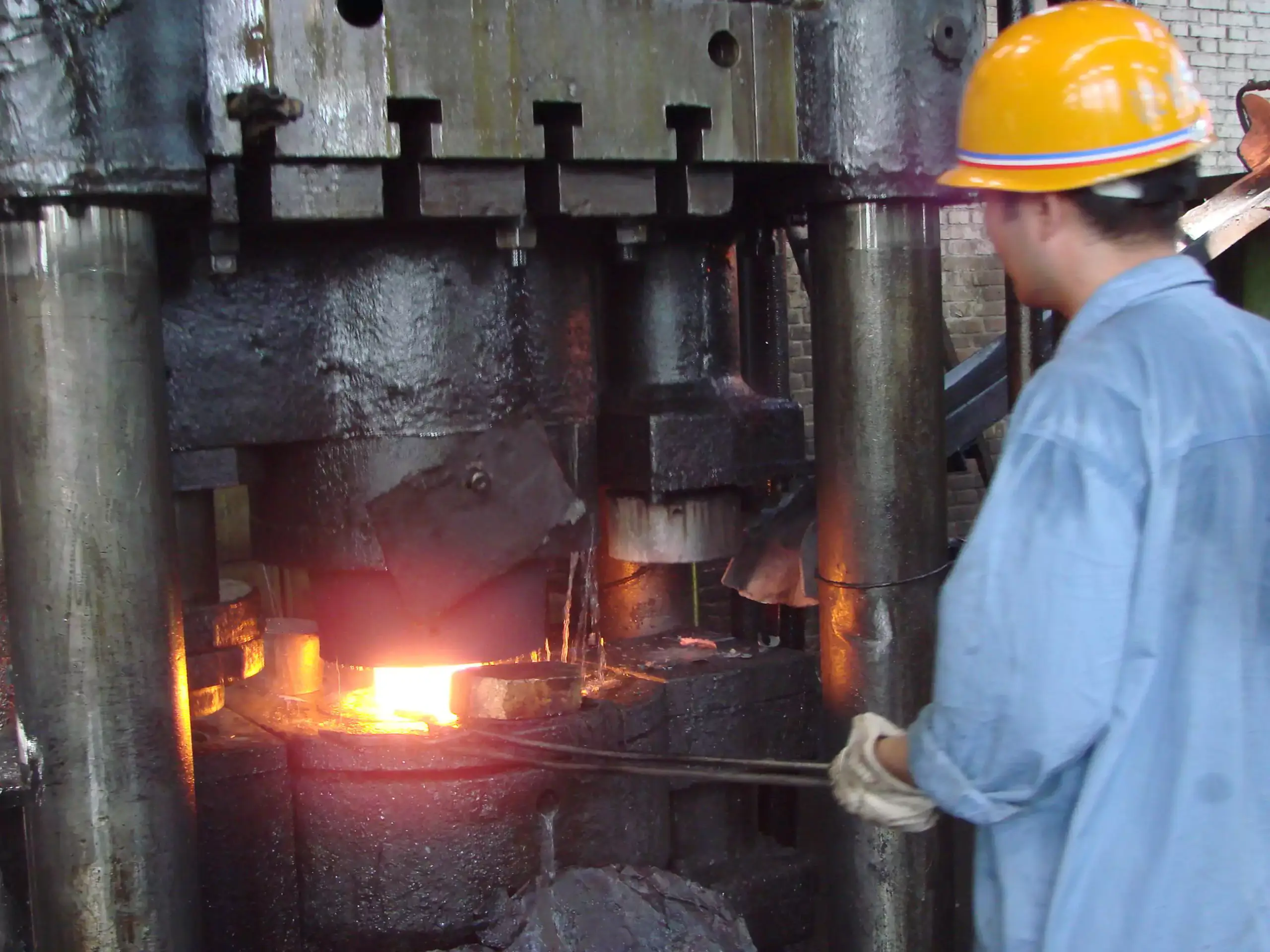
A stock image related to forging china.
Today, China is one of the largest producers of forged products globally, benefiting from a robust manufacturing infrastructure and a skilled workforce. This evolution has positioned Chinese manufacturers as key players in the global supply chain, catering to various industries with high-quality forged components. For international B2B buyers, understanding this historical context provides insights into the capabilities and competitive advantages that Chinese forging suppliers bring to the market.
In summary, navigating the forging sector in China requires a keen understanding of market dynamics, a commitment to sustainability, and an appreciation for the industry’s historical evolution. By leveraging these insights, international B2B buyers can make strategic sourcing decisions that align with their business goals and ethical standards.
Frequently Asked Questions (FAQs) for B2B Buyers of forging china
-
How do I choose the right forging supplier in China?
Selecting the right forging supplier involves thorough research and vetting. Start by evaluating the supplier’s experience and expertise in the specific type of forging you require, whether it’s open die forging or closed die forging. Request references and case studies from previous clients, focusing on those in your industry. Additionally, assess their certifications, such as ISO 9001, which indicates quality management standards. Finally, consider visiting the facility, if possible, to inspect their operations and quality control processes firsthand. -
What is the minimum order quantity (MOQ) for forging products in China?
The MOQ for forging products can vary significantly based on the supplier and the complexity of the items being forged. Generally, MOQs range from 500 to 1,000 units for standard products. However, some suppliers may accommodate lower quantities for initial orders, especially if you are establishing a long-term partnership. It’s crucial to communicate your needs clearly and negotiate MOQs that align with your business requirements while considering the supplier’s production capabilities. -
What are the typical payment terms for international forging orders in China?
Payment terms for forging orders typically involve a deposit followed by a final payment upon completion. Common arrangements include a 30% deposit to initiate production and the remaining 70% before shipment. However, terms can vary based on supplier relationships and order sizes. Be sure to clarify payment methods, including wire transfers and letters of credit, and ensure that these terms are documented in your purchase agreement to avoid misunderstandings later. -
How can I ensure quality assurance in my forging orders from China?
To ensure quality assurance, establish clear specifications and standards before placing your order. Engage in regular communication with your supplier throughout the production process. Consider hiring a third-party inspection service to conduct quality checks at various stages, including raw materials, in-process inspections, and final product evaluations. Additionally, requesting samples before full-scale production can help you assess the quality of the forging work and make necessary adjustments. -
What are the shipping and logistics considerations when importing forged products from China?
When importing forged products, consider factors such as shipping methods, lead times, and customs regulations. Air freight is faster but more expensive, while sea freight is cost-effective for larger shipments. Ensure that you have a clear understanding of incoterms (International Commercial Terms) to define responsibilities for shipping costs, risks, and insurance. Collaborating with a reliable freight forwarder can streamline logistics and assist with customs clearance, ensuring compliance with import regulations in your country. -
Can I customize my forging orders, and what is the process?
Yes, many Chinese forging suppliers offer customization options tailored to your specifications. Start by discussing your design requirements and any specific material properties you need. Most suppliers will require detailed technical drawings or CAD files. Once your design is agreed upon, they will provide prototypes or samples for approval. Be prepared for iterative communication to refine the product until it meets your standards, and ensure that any customizations are documented in your contract. -
What materials are commonly used in forging, and how do I select the right one?
Common materials for forging include carbon steel, alloy steel, stainless steel, and aluminum. The choice of material depends on the intended application, required strength, and environmental conditions. For high-strength applications, alloy steel may be preferred, while stainless steel is suitable for corrosive environments. Consult with your supplier or a metallurgist to understand the properties of different materials and select the most appropriate one for your specific needs. -
How do I handle communication and cultural differences with Chinese suppliers?
Effective communication with Chinese suppliers is crucial for successful transactions. Be clear and concise in your requests and expectations, and avoid jargon that may lead to misunderstandings. Utilize tools like translation services if language barriers exist. Understanding cultural nuances, such as the importance of building relationships (Guanxi), can enhance your interactions. Regular follow-ups and being responsive to your supplier’s queries will foster a positive working relationship and facilitate smoother negotiations.
Important Disclaimer & Terms of Use
⚠️ Important Disclaimer
The information provided in this guide, including content regarding manufacturers, technical specifications, and market analysis, is for informational and educational purposes only. It does not constitute professional procurement advice, financial advice, or legal advice.
While we have made every effort to ensure the accuracy and timeliness of the information, we are not responsible for any errors, omissions, or outdated information. Market conditions, company details, and technical standards are subject to change.
B2B buyers must conduct their own independent and thorough due diligence before making any purchasing decisions. This includes contacting suppliers directly, verifying certifications, requesting samples, and seeking professional consultation. The risk of relying on any information in this guide is borne solely by the reader.
Strategic Sourcing Conclusion and Outlook for forging china
What Are the Key Takeaways for B2B Buyers in the Forging Industry?
In summary, strategic sourcing in the forging industry is essential for international B2B buyers seeking competitive advantages. Understanding the differences between forging and other manufacturing processes, such as die-casting, can help companies select the right suppliers and materials that meet their specific needs. Additionally, leveraging China’s advanced forging capabilities allows businesses from Africa, South America, the Middle East, and Europe to access high-quality products at competitive prices.
How Can International Buyers Enhance Their Sourcing Strategies?
To optimize sourcing strategies, buyers should focus on building long-term relationships with reliable suppliers and continuously assess market trends and innovations. Engaging with manufacturers who prioritize quality control and sustainable practices can lead to better product outcomes and enhance brand reputation.
What Does the Future Hold for Forging in Global Markets?
Looking ahead, the forging industry is poised for growth driven by technological advancements and increased demand across various sectors. International B2B buyers are encouraged to stay informed and proactive in their sourcing strategies. By embracing strategic sourcing now, companies can position themselves favorably in the evolving global marketplace and ensure they remain competitive in the years to come.