Discover Cost-Saving Strategies with RV Parts Manufacturers (2025)
Introduction: Navigating the Global Market for RV Parts Manufacturers
In today’s competitive landscape, sourcing RV parts manufacturers can present a daunting challenge for B2B buyers, especially those operating in diverse markets such as Africa, South America, the Middle East, and Europe. The global RV industry is rapidly evolving, driven by increasing consumer demand for recreational vehicles and the need for high-quality components that ensure safety, durability, and performance. This comprehensive guide addresses the complexities of navigating the global market for RV parts, equipping buyers with essential insights into various types of parts, their applications, and the intricacies of supplier vetting.
This guide delves into critical factors that influence purchasing decisions, including cost structures, quality standards, and logistical considerations. By outlining best practices for evaluating suppliers and understanding market trends, we empower international B2B buyers from regions like Colombia and Argentina to make informed and strategic sourcing decisions. Whether you are looking to establish new supplier relationships or optimize existing ones, this guide will serve as your roadmap to successfully navigate the RV parts manufacturing landscape.
Through actionable insights and expert recommendations, you will be positioned to enhance your procurement processes, ensuring that you source the best products that meet your operational needs while maximizing value for your business.
Understanding RV Parts Manufacturers Types and Variations
Type Name | Key Distinguishing Features | Primary B2B Applications | Brief Pros & Cons for Buyers |
---|---|---|---|
OEM Manufacturers | High-quality, brand-specific parts; extensive warranties | Large RV manufacturers and dealerships | Pros: Reliable quality, brand compatibility. Cons: Higher cost, limited customization. |
Aftermarket Parts Suppliers | Wide variety of parts, often at lower prices | Independent RV service centers and retailers | Pros: Cost-effective, diverse options. Cons: Variable quality, potential compatibility issues. |
Specialty Parts Manufacturers | Focused on niche markets or specific components | Custom RV builders and specialized repair shops | Pros: Tailored solutions, expert knowledge. Cons: Limited availability, potential higher costs. |
Global Parts Distributors | Wide-reaching networks, often with international shipping | International RV dealers and export businesses | Pros: Broad access to parts, competitive pricing. Cons: Shipping delays, customs complications. |
E-commerce Platforms | Online marketplaces with various manufacturers | Small businesses and DIY RV enthusiasts | Pros: Convenience, easy price comparisons. Cons: Inconsistent quality, lack of direct support. |
What Are the Characteristics of OEM Manufacturers in RV Parts?
OEM (Original Equipment Manufacturer) manufacturers produce parts that are specifically designed for RV brands. Their products are made to meet strict quality standards, ensuring compatibility and performance. OEM parts are typically backed by extensive warranties, which can be a significant selling point for B2B buyers prioritizing reliability. However, they are often more expensive than alternatives, making them a consideration primarily for larger manufacturers or dealerships that require assured quality.
How Do Aftermarket Parts Suppliers Operate in the RV Industry?
Aftermarket parts suppliers provide a broad range of components that can fit various RV models. These suppliers often offer products at lower prices compared to OEMs, making them attractive to independent service centers and retailers. The major downside is the variability in quality, which can lead to compatibility issues. B2B buyers should conduct thorough research and possibly request samples before committing to large orders to ensure quality meets their standards.
What Benefits Do Specialty Parts Manufacturers Offer?
Specialty parts manufacturers focus on niche markets or specific components, such as custom RV accessories or high-performance parts. They cater to custom RV builders and specialized repair shops that require unique solutions not available from mainstream suppliers. While these manufacturers often provide tailored solutions and expert insights, their products may come at a premium and may not be as readily available, requiring careful planning for inventory management.
Why Choose Global Parts Distributors for RV Parts?
Global parts distributors have extensive networks that allow them to supply a wide array of RV parts across international markets. They are beneficial for international dealers and export businesses seeking competitive pricing and variety. However, buyers should be aware of potential shipping delays and customs issues, which can affect lead times and overall supply chain efficiency. Establishing strong relationships with these distributors can mitigate some of these risks.
How Do E-commerce Platforms Transform RV Parts Purchasing?
E-commerce platforms have revolutionized how RV parts are purchased, providing easy access to a multitude of manufacturers in one place. These platforms are particularly popular among small businesses and DIY enthusiasts looking for convenience and the ability to compare prices quickly. However, the inconsistency in product quality and lack of direct customer support can be significant drawbacks. Buyers should prioritize platforms with strong seller ratings and return policies to safeguard their purchases.
Related Video: The 6 Different types of RV Slide technologies and how they work!
Key Industrial Applications of RV Parts Manufacturers
Industry/Sector | Specific Application of RV Parts Manufacturers | Value/Benefit for the Business | Key Sourcing Considerations for this Application |
---|---|---|---|
Tourism and Recreational Vehicles | Manufacturing and supplying parts for RVs and trailers | Enhances customer satisfaction and safety | Quality certifications, compatibility with existing models, lead times |
Construction and Mobile Offices | Custom RV parts for mobile offices and site accommodations | Increases operational efficiency and comfort | Durability under diverse conditions, ease of installation, cost-effectiveness |
Emergency Services | Specialized RV parts for mobile command units | Improves response times and operational readiness | Reliability under extreme conditions, rapid availability, and support services |
Hospitality Industry | RV parts for luxury mobile accommodations | Attracts high-end clientele and boosts revenue | Aesthetic compatibility, comfort features, and maintenance support |
Agriculture | RV parts for mobile farming equipment | Enhances productivity and mobility in the field | Weather resistance, load capacity, and serviceability |
How Are RV Parts Manufacturers Used in the Tourism and Recreational Vehicle Sector?
In the tourism industry, RV parts manufacturers play a crucial role by providing components that enhance the functionality and safety of recreational vehicles. For international buyers from regions like Africa and South America, sourcing high-quality parts ensures that RVs meet safety standards and customer expectations. This sector benefits from reliable suppliers who can offer a range of components, such as braking systems and electrical systems, tailored to various models and specifications.
What Are the Applications of RV Parts in Construction and Mobile Offices?
RV parts manufacturers supply custom components for mobile offices and construction trailers, improving comfort and functionality on job sites. Buyers in the Middle East and Europe often require parts that can withstand extreme conditions while providing a professional workspace. Key considerations include the durability of materials and the ease of installation, ensuring minimal downtime during projects.
How Do RV Parts Enhance Emergency Services Operations?
In emergency services, RV parts are vital for mobile command units that require specialized equipment to operate efficiently. Manufacturers provide parts that enhance the reliability and readiness of these vehicles, crucial for rapid response scenarios. Buyers must consider the reliability of components under stress, as well as the availability of support services to ensure operational continuity during emergencies.
How Are RV Parts Utilized in the Hospitality Industry?
The hospitality sector uses RV parts to create luxury mobile accommodations, appealing to high-end clientele seeking unique experiences. Manufacturers must focus on aesthetic compatibility and comfort features to meet the expectations of this market. Buyers from regions like Europe and South America should prioritize suppliers who can provide stylish and functional components that enhance the guest experience.
What Role Do RV Parts Play in Agricultural Applications?
In agriculture, RV parts are used for mobile farming equipment, enhancing productivity and mobility in the field. Manufacturers supply parts that are weather-resistant and capable of handling heavy loads, which is essential for farmers operating in diverse conditions. Buyers need to assess the serviceability of parts and their compatibility with existing agricultural machinery to ensure seamless integration and operational efficiency.
Related Video: What is Industrial Automation?
3 Common User Pain Points for ‘RV Parts Manufacturers’ & Their Solutions
Scenario 1: Difficulty in Sourcing High-Quality RV Parts
The Problem:
B2B buyers often struggle to find reliable RV parts manufacturers that offer high-quality products. This issue is particularly pronounced in regions like Africa and South America, where the local market may not have established manufacturers. Buyers may encounter substandard parts that do not meet safety standards or fail prematurely, leading to increased costs and potential liability issues. Additionally, the lack of established relationships with manufacturers can result in longer lead times and inconsistent supply.
The Solution:
To overcome sourcing challenges, B2B buyers should focus on building relationships with reputable manufacturers and suppliers. Research and due diligence are critical; utilize platforms such as industry trade shows, online directories, and industry associations to identify credible RV parts manufacturers. Look for certifications or endorsements from recognized industry bodies that attest to quality and safety standards.
Moreover, consider establishing long-term contracts with manufacturers that demonstrate reliability and a commitment to quality. This can include negotiating service-level agreements (SLAs) that outline delivery timelines and quality expectations. Engaging in a pilot program with potential suppliers can also help assess their product quality and service before committing to larger orders.
Scenario 2: Managing Inventory and Supply Chain Issues
The Problem:
Inventory management can be a significant pain point for B2B buyers dealing with RV parts. Fluctuating demand, unexpected delays in manufacturing, and shipping issues can lead to stockouts or excess inventory. In regions like the Middle East and parts of Europe, where seasonal demand for RVs can vary greatly, maintaining the right inventory levels is crucial but challenging. This often results in lost sales opportunities or increased holding costs for excess parts.
The Solution:
To effectively manage inventory, B2B buyers should implement a robust inventory management system that utilizes data analytics and demand forecasting. This system should be capable of analyzing historical sales data, seasonal trends, and market dynamics to make informed purchasing decisions.
Additionally, establishing a just-in-time (JIT) inventory strategy can help mitigate the risks of overstocking while ensuring parts are available when needed. Collaborating with manufacturers to synchronize production schedules with buyer demand can enhance supply chain efficiency.
Investing in technology such as inventory management software can also facilitate real-time tracking of stock levels and automate reordering processes, thus minimizing the risk of stockouts or overstocking. Regular communication with suppliers about market trends and demand forecasts can further enhance supply chain responsiveness.
Scenario 3: Compliance with International Standards and Regulations
The Problem:
Navigating compliance with international standards and regulations can be daunting for B2B buyers in the RV parts sector. Different countries have varying regulations regarding safety, emissions, and material sourcing, which can complicate the purchasing process. Buyers may face challenges in ensuring that the parts they procure comply with the necessary legal requirements, risking fines or product recalls if standards are not met.
The Solution:
B2B buyers should prioritize sourcing RV parts manufacturers who have a strong understanding of international compliance regulations. Engaging with manufacturers that hold certifications such as ISO, CE, or other relevant industry standards can provide reassurance of their commitment to quality and regulatory compliance.
Buyers should also consider working with compliance consultants or legal advisors who specialize in the RV industry to stay informed about the latest regulations. Establishing a checklist of required certifications and documentation for each part can help streamline the procurement process and ensure compliance.
Regular training for procurement teams on compliance matters can further enhance understanding and vigilance. Creating a feedback loop with manufacturers to report on compliance issues can also foster a culture of accountability and improvement, ultimately benefiting both parties.
Strategic Material Selection Guide for RV Parts Manufacturers
When selecting materials for RV parts manufacturing, it is essential to consider various factors that influence product performance, durability, and compliance with international standards. Below, we analyze four common materials used in the industry, focusing on their properties, advantages, disadvantages, and implications for international buyers.
What Are the Key Properties of Aluminum in RV Parts Manufacturing?
Aluminum is a widely used material in RV parts due to its favorable properties. It boasts excellent strength-to-weight ratio, making it ideal for lightweight applications. Aluminum has good corrosion resistance, especially when anodized, and can withstand a broad range of temperatures.
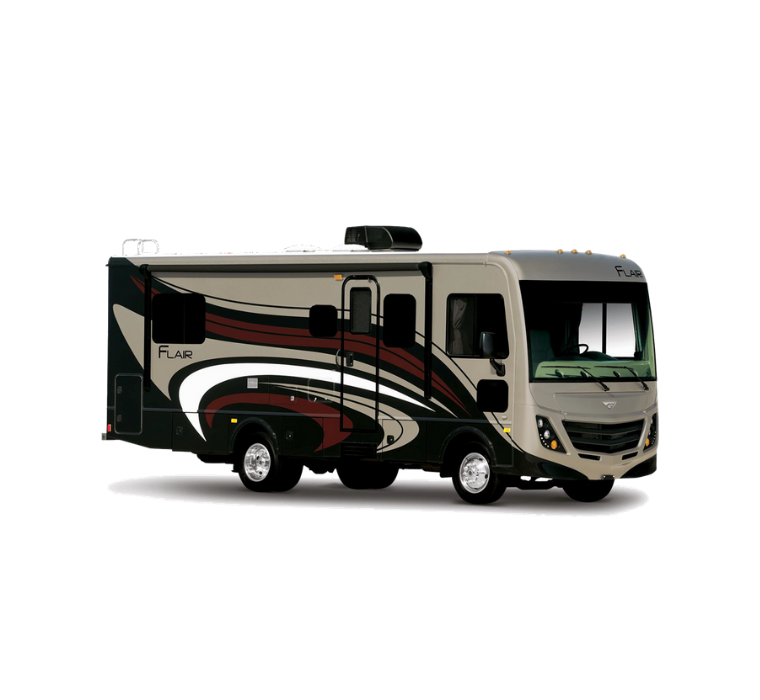
A stock image related to RV Parts Manufacturers.
Pros & Cons:
The primary advantage of aluminum is its lightweight nature, which enhances fuel efficiency and overall performance. However, it can be more expensive than other materials, and its manufacturing process can be complex, requiring specialized equipment. Additionally, aluminum may not be as durable as steel in high-impact applications.
Impact on Application:
Aluminum is compatible with various media, including water and fuel, making it suitable for tanks and structural components. However, care must be taken to avoid galvanic corrosion when paired with dissimilar metals.
Considerations for International Buyers:
Buyers from regions like Africa and South America should be aware of local sourcing options and compliance with standards such as ASTM for aluminum alloys. Understanding the local market’s preferences for weight versus cost is crucial.
How Does Steel Compare as a Material for RV Parts?
Steel is another popular choice for RV parts, known for its high strength and durability. It can handle significant stress and is less prone to deformation under load. Steel also offers excellent temperature resistance.
Pros & Cons:
The key advantage of steel is its robustness and longevity, making it suitable for high-stress applications. However, it is heavier than aluminum, which can negatively impact fuel efficiency. Steel is also susceptible to rust and corrosion unless properly treated, adding to maintenance costs.
Impact on Application:
Steel is ideal for structural components and frames, where strength is paramount. It is less compatible with corrosive environments unless coated or treated.
Considerations for International Buyers:
In Europe and the Middle East, compliance with DIN standards for steel grades is essential. Buyers should also consider the availability of treated steel options to mitigate corrosion issues.
What Are the Benefits of Composite Materials in RV Parts?
Composite materials, including fiberglass and carbon fiber, are increasingly used in RV manufacturing due to their lightweight and high strength. They offer excellent resistance to environmental factors, including UV radiation and moisture.
Pros & Cons:
The primary advantage of composites is their weight reduction, which enhances overall vehicle efficiency. However, they can be more expensive and may require specialized manufacturing techniques. Additionally, repair processes for composites can be more complex than for metals.
Impact on Application:
Composites are often used in body panels and interior components, where aesthetics and weight are critical. Their compatibility with various media is generally high, but they may not be suitable for high-temperature applications.
Considerations for International Buyers:
Buyers in regions like South America and Africa should investigate local suppliers of composite materials and their compliance with relevant standards. Understanding the cost implications of composites versus traditional materials is also vital.
Why Consider Plastics for RV Parts Manufacturing?
Plastics, particularly engineering plastics like ABS and polycarbonate, are used for various RV components due to their versatility and ease of manufacturing. They are lightweight and can be molded into complex shapes.
Pros & Cons:
The advantages of plastics include low weight, corrosion resistance, and lower manufacturing costs. However, they may not provide the same level of strength as metals and can be affected by UV exposure over time.
Impact on Application:
Plastics are commonly used for interior components, fixtures, and non-structural parts. They generally have good compatibility with fluids but may not withstand high temperatures.
Considerations for International Buyers:
International buyers should be aware of the different grades of plastics and their compliance with safety standards. Understanding the local market’s acceptance of plastic components is also crucial.
Summary Table of Material Selection for RV Parts Manufacturers
Material | Typical Use Case for RV Parts Manufacturers | Key Advantage | Key Disadvantage/Limitation | Relative Cost (Low/Med/High) |
---|---|---|---|---|
Aluminum | Structural components, tanks | Lightweight and corrosion-resistant | Higher cost and complex manufacturing | Medium |
Steel | Frames, structural components | High strength and durability | Heavier and prone to corrosion | Low |
Composite | Body panels, interior components | Lightweight and UV resistant | Higher cost and complex repairs | High |
Plastics | Interior fixtures, non-structural parts | Low weight and cost-effective | Lower strength and UV sensitivity | Low |
This guide provides a comprehensive overview of material selection considerations for RV parts manufacturers, aiding international B2B buyers in making informed decisions tailored to their specific market needs.
In-depth Look: Manufacturing Processes and Quality Assurance for RV Parts Manufacturers
What Are the Main Stages in the Manufacturing Process of RV Parts?
The manufacturing process for RV parts typically involves several critical stages, each essential for ensuring the quality and functionality of the final product. These stages include:
-
Material Preparation: This initial phase involves sourcing high-quality materials suitable for RV parts, such as aluminum, steel, and various plastics. Suppliers should provide certifications for these materials, ensuring they meet international standards, which is crucial for B2B buyers to verify.
-
Forming: During this stage, materials are shaped into the required forms using techniques such as stamping, extrusion, or molding. Advanced technologies like CNC (Computer Numerical Control) machining can enhance precision, which is vital for parts that require a perfect fit in RV assemblies.
-
Assembly: The assembly process combines various components to create the final RV part. Techniques such as welding, riveting, or adhesive bonding are commonly employed. Each assembly line should be designed for efficiency, minimizing waste and reducing lead times, which are significant considerations for international buyers.
-
Finishing: This final stage involves surface treatments such as painting, anodizing, or coating to enhance durability and aesthetic appeal. Finishing processes must comply with environmental regulations, which can vary by region, so understanding these regulations is crucial for buyers, especially those importing products from different continents.
How Do Quality Assurance Standards Impact RV Parts Manufacturing?
Quality assurance (QA) is vital in the manufacturing of RV parts, ensuring that products meet both safety and performance standards. International standards such as ISO 9001 provide a framework for quality management systems, which is particularly relevant for B2B buyers looking to ensure consistency and reliability in their supply chain.
What Are the Relevant International and Industry-Specific Standards?
-
ISO 9001: This standard outlines the criteria for a quality management system and is recognized globally. Manufacturers certified under ISO 9001 demonstrate their commitment to maintaining quality and continuous improvement.
-
CE Marking: This certification indicates that a product meets EU safety, health, and environmental protection standards. For buyers in Europe, verifying that RV parts carry the CE mark is crucial for compliance with local regulations.
-
API Specifications: For RV parts that involve oil and gas components, API (American Petroleum Institute) standards can be relevant. Compliance ensures that parts can withstand the specific pressures and conditions found in these environments.
What Are the Key Quality Control Checkpoints in RV Parts Manufacturing?
Effective quality control (QC) practices are critical to the manufacturing process. Key checkpoints include:
-
Incoming Quality Control (IQC): This initial inspection checks raw materials against specifications before they enter production. Ensuring that materials are up to standard is crucial to avoid defects later in the process.
-
In-Process Quality Control (IPQC): During production, random inspections are conducted to monitor processes and ensure compliance with standards. This checkpoint helps identify issues early, allowing for immediate corrective action.
-
Final Quality Control (FQC): Once production is complete, final inspections and tests are conducted to verify that the finished product meets all specifications and standards. This stage is essential for ensuring that the product is ready for market.
What Common Testing Methods Are Used in RV Parts Quality Assurance?
Various testing methods are employed to ensure the integrity and performance of RV parts, including:
-
Mechanical Testing: This includes tensile tests, fatigue tests, and impact tests to assess the strength and durability of materials.
-
Dimensional Inspection: Tools like calipers and gauges are used to check the dimensions of parts, ensuring they meet design specifications.
-
Non-Destructive Testing (NDT): Techniques such as ultrasonic testing and radiography help identify internal flaws without damaging the parts, providing an additional layer of quality assurance.
How Can B2B Buyers Verify Supplier Quality Control Practices?
For international B2B buyers, especially those from Africa, South America, the Middle East, and Europe, verifying a supplier’s QC practices is crucial. Here are some actionable steps:
-
Conduct Audits: Regular audits of suppliers’ manufacturing facilities can provide insights into their processes and adherence to quality standards. Buyers should request audit reports to ensure compliance.
-
Request Documentation: Suppliers should provide detailed QC reports, including results from IQC, IPQC, and FQC. These documents should outline any issues found and corrective actions taken.
-
Engage Third-Party Inspectors: Utilizing independent inspection services can provide unbiased assessments of product quality. This is particularly useful for buyers who may not have the resources to conduct their inspections.
What Are the Quality Control Nuances for International B2B Buyers?
International buyers need to be aware of several nuances regarding QC:
-
Cultural Differences: Understanding cultural attitudes toward quality and business practices in different regions can help buyers navigate supplier relationships more effectively.
-
Regulatory Compliance: Each region may have its own regulations regarding product standards, which can affect the certification process. Buyers must ensure that their suppliers understand and comply with these regulations.
-
Logistics and Supply Chain Management: Delays in the supply chain can impact quality. Buyers should consider logistics when evaluating suppliers, as timely delivery is crucial for maintaining production schedules.
Conclusion
The manufacturing processes and quality assurance practices for RV parts are intricate and require careful consideration from international B2B buyers. By understanding each stage of production, relevant standards, and effective QC practices, buyers can make informed decisions that ensure they source high-quality, reliable components for their needs. This diligence not only protects their investment but also enhances their reputation in the competitive RV market.
Practical Sourcing Guide: A Step-by-Step Checklist for ‘RV Parts Manufacturers’
To successfully procure RV parts from manufacturers, international B2B buyers must navigate a complex landscape of suppliers and products. This checklist serves as a comprehensive guide to streamline the sourcing process, ensuring that you find reliable partners who meet your specific needs.
Step 1: Define Your Technical Specifications
Before initiating the sourcing process, clearly outline the technical specifications for the RV parts you require. This includes dimensions, materials, and any industry standards that must be adhered to. A well-defined specification helps prevent miscommunication and ensures that suppliers understand your exact needs.
- Consider industry standards: Research relevant standards in your region, such as ISO certifications, to ensure compliance.
- Detail functional requirements: Specify how the parts will be used and any performance metrics they must meet.
Step 2: Conduct Market Research
Understanding the market landscape is essential for identifying potential suppliers and assessing their capabilities. Investigate the various manufacturers in your target regions, focusing on those with a strong reputation for quality and reliability.
- Use online platforms: Leverage B2B marketplaces, trade shows, and industry forums to gather information.
- Examine reviews and testimonials: Look for feedback from other buyers, especially those within your region, to gauge supplier performance.
Step 3: Evaluate Potential Suppliers
Before committing to a supplier, conduct thorough evaluations to ensure they can meet your needs. Request detailed company profiles, including their history, production capabilities, and relevant certifications.
- Request samples: Evaluate product quality by obtaining samples before making bulk orders.
- Check references: Reach out to previous clients to learn about their experiences, focusing on communication and reliability.
Step 4: Verify Supplier Certifications
Ensuring that your suppliers hold necessary certifications is crucial for compliance and quality assurance. Look for manufacturers that are certified by recognized organizations relevant to the RV parts industry.
- Common certifications: ISO 9001, ISO 14001, and specific automotive industry certifications.
- Request documentation: Ask for copies of certifications and verify them through the issuing bodies.
Step 5: Negotiate Terms and Conditions
Once you have shortlisted potential suppliers, it’s time to negotiate the terms of your partnership. This includes pricing, payment terms, delivery schedules, and warranties.
- Be clear on expectations: Clearly outline your expectations regarding quality, delivery, and after-sales support.
- Consider long-term relationships: Discuss potential for future orders and volume discounts to foster a long-term partnership.
Step 6: Establish Communication Channels
Effective communication is critical for a successful sourcing relationship. Establish clear communication channels and protocols to ensure all parties are aligned throughout the process.
- Choose preferred communication methods: Determine whether email, phone calls, or video conferencing works best for both parties.
- Set regular check-ins: Schedule periodic updates to discuss progress and address any concerns.
Step 7: Monitor and Review Supplier Performance
After establishing a partnership, continuously monitor and review supplier performance against the agreed-upon terms. This helps identify any issues early and ensures that the supplier maintains quality standards.
- Implement performance metrics: Use key performance indicators (KPIs) related to delivery times, quality, and responsiveness.
- Provide feedback: Regularly communicate your feedback to help suppliers improve and maintain a strong working relationship.
By following this sourcing checklist, international B2B buyers can enhance their procurement strategies for RV parts, ensuring they partner with trustworthy manufacturers who meet their specific requirements.
Comprehensive Cost and Pricing Analysis for RV Parts Manufacturers Sourcing
What Are the Key Cost Components in Sourcing RV Parts?
When analyzing the costs associated with sourcing RV parts from manufacturers, several key components must be considered. These include:
-
Materials: The type and quality of materials used significantly impact the overall cost. For instance, aluminum and fiberglass may be more expensive but provide better durability and weight savings compared to alternatives.
-
Labor: Labor costs vary by region and are influenced by local wage standards and the skill level required for manufacturing. Countries with lower labor costs can offer competitive pricing, but may also affect quality and consistency.
-
Manufacturing Overhead: This encompasses costs related to utilities, facility maintenance, and administrative expenses. Efficient manufacturing processes can help minimize these overheads, affecting the final price.
-
Tooling: The initial investment in tooling and machinery can be substantial. Manufacturers often pass these costs onto buyers, especially if custom tooling is required for specific parts.
-
Quality Control (QC): Ensuring that parts meet safety and regulatory standards involves additional QC processes, which can contribute to higher costs. Buyers should verify that suppliers have robust QC practices in place.
-
Logistics: Shipping and handling costs can vary greatly depending on the supplier’s location and the chosen shipping method. These costs should be calculated into the total price to avoid surprises.
-
Margin: Manufacturers will include a profit margin in their pricing. Understanding typical margins in the RV parts industry can help buyers gauge whether a quote is reasonable.
How Do Price Influencers Affect the Cost of RV Parts?
Several factors influence the pricing of RV parts, including:
-
Volume and Minimum Order Quantity (MOQ): Larger orders typically attract lower per-unit costs due to economies of scale. Buyers should negotiate MOQs that align with their purchasing capabilities.
-
Specifications and Customization: Customized parts often incur additional costs due to the need for specialized tooling and manufacturing processes. Clear specifications can help minimize unexpected costs.
-
Materials and Quality Certifications: The choice of materials and necessary certifications (e.g., ISO, CE) can significantly influence the price. High-quality materials and certifications may justify a higher cost due to their long-term benefits.
-
Supplier Factors: The reputation, location, and reliability of the supplier can impact pricing. Established suppliers may charge more but often deliver superior quality and service.
-
Incoterms: Understanding Incoterms (International Commercial Terms) is crucial as they define the responsibilities of buyers and sellers in shipping. They can affect the overall cost and delivery timelines.
What Are Effective Buyer Tips for Cost-Efficiency?
For international B2B buyers, especially from regions like Africa, South America, the Middle East, and Europe, here are actionable tips to ensure cost-efficient sourcing:
-
Negotiate Wisely: Always negotiate pricing and payment terms with suppliers. A well-prepared negotiation can lead to significant savings.
-
Consider Total Cost of Ownership (TCO): Look beyond the initial purchase price. TCO includes maintenance, logistics, and potential quality issues over time, which can greatly affect long-term costs.
-
Understand Pricing Nuances: Be aware of local economic conditions that may impact pricing, such as tariffs, currency fluctuations, and import duties. This knowledge can inform better purchasing decisions.
-
Build Relationships with Suppliers: Establishing long-term partnerships can lead to preferential pricing, better terms, and improved service.
-
Conduct Market Research: Regularly assess market prices and trends. This will help you stay informed and negotiate effectively.
Disclaimer on Indicative Prices
It is important to note that the prices for RV parts can vary widely based on several factors, including market conditions, supplier pricing strategies, and specific buyer requirements. Always seek multiple quotes and conduct thorough due diligence to ensure you receive competitive pricing.
Alternatives Analysis: Comparing RV Parts Manufacturers With Other Solutions
Understanding Alternatives to RV Parts Manufacturers
When considering the procurement of RV parts, it’s essential to evaluate not only traditional manufacturers but also alternative solutions that can meet your business needs. These alternatives may offer distinct advantages in terms of cost, performance, and implementation. This section provides a comparative analysis of RV parts manufacturers against two viable alternatives: aftermarket parts and 3D printing technology.
Comparison Table of RV Parts Manufacturers and Alternatives
Comparison Aspect | RV Parts Manufacturers | Aftermarket Parts | 3D Printing Technology |
---|---|---|---|
Performance | High quality, OEM standards | Variable, depends on brand | Customizable, high precision |
Cost | Often higher due to OEM pricing | Generally lower, varies by brand | Initial setup cost may be high, but low per-part cost |
Ease of Implementation | Straightforward, established supply chains | Easy to source, many vendors | Requires specialized equipment and skills |
Maintenance | Reliable with long-term support | Varies by part quality | Minimal, but depends on material used |
Best Use Case | New RV production, certified repairs | Cost-effective repairs, older models | Prototyping, custom parts for specific needs |
What Are the Advantages and Disadvantages of Aftermarket Parts?
Aftermarket parts are a popular alternative to OEM parts, often providing a cost-effective solution for RV repairs and upgrades. These parts are produced by third-party manufacturers and can be less expensive than OEM parts. However, the quality can be inconsistent, which may lead to performance issues or shorter lifespans. For businesses looking to minimize costs on older RV models, aftermarket parts can be a practical choice, but buyers should thoroughly research brands to ensure reliability.
How Does 3D Printing Technology Compare to RV Parts Manufacturers?
3D printing technology represents a transformative approach to manufacturing RV parts. It allows for the creation of customized components on-demand, which can significantly reduce inventory costs and lead times. The precision and adaptability of 3D printing are particularly beneficial for prototyping or producing unique parts that are no longer available through traditional channels. However, the initial investment in 3D printing equipment and the learning curve associated with operating this technology can be barriers for some businesses. Additionally, the choice of materials can impact the durability of printed parts.
Conclusion: How Should B2B Buyers Choose the Right Solution?
In selecting the right solution for RV parts procurement, B2B buyers should carefully assess their specific needs, including budget constraints, part performance requirements, and the types of RVs they service. For businesses focused on new RV production or those requiring certified repairs, RV parts manufacturers may be the best choice due to their reliability and quality assurance. Conversely, if cost reduction is a priority, especially for older models, aftermarket parts could provide substantial savings. Finally, for companies looking to innovate and customize, investing in 3D printing technology may offer unparalleled flexibility and efficiency. By weighing these factors, buyers can make informed decisions that align with their operational goals.
Essential Technical Properties and Trade Terminology for RV Parts Manufacturers
What are the Essential Technical Properties for RV Parts Manufacturers?
Understanding the technical properties of RV parts is crucial for B2B buyers. Here are several key specifications that influence the quality, durability, and overall performance of RV components:
-
Material Grade
– Material grade refers to the classification of materials based on their composition and mechanical properties. Common materials in RV parts include aluminum, steel, and composite materials. Selecting the right material grade is essential for ensuring that parts can withstand environmental stresses such as temperature fluctuations, moisture, and physical wear. For B2B buyers, knowing the material grade helps in evaluating the durability and performance of parts. -
Tolerance
– Tolerance indicates the permissible limit of variation in a physical dimension or measurement. For example, a tolerance of ±0.01 mm in a part’s dimensions can significantly affect its fit and function. Tight tolerances are critical in components that require precision, such as engine parts and chassis components. Buyers must understand tolerance specifications to ensure compatibility and performance in assembly processes. -
Load Capacity
– Load capacity denotes the maximum load that a part can safely support without failure. This specification is vital for components like axles, frames, and suspension systems, which endure substantial forces during operation. B2B buyers should assess load capacity to ensure the safety and reliability of RVs, especially in commercial applications. -
Corrosion Resistance
– Corrosion resistance is the ability of a material to withstand deterioration due to chemical reactions with its environment. RV parts often encounter moisture and harsh weather conditions, making this property essential. Buyers should prioritize parts with high corrosion resistance to prolong the lifespan and maintain the integrity of RVs, especially in regions with high humidity or salt exposure. -
Thermal Stability
– Thermal stability refers to a material’s ability to maintain its properties under varying temperature conditions. Parts exposed to heat, such as engine components and exhaust systems, must have high thermal stability to prevent deformation or failure. Understanding this property helps buyers select components that can withstand the operational demands of RV usage.
What are Common Trade Terms in the RV Parts Industry?
Familiarity with industry terminology is essential for effective communication and negotiation in the RV parts market. Here are several critical trade terms:
-
OEM (Original Equipment Manufacturer)
– OEM refers to companies that produce parts that are used as components in the manufacturing of a larger product. In the RV industry, OEM parts are often preferred due to their compatibility and quality assurance. Buyers should consider OEM parts for reliability and warranty coverage. -
MOQ (Minimum Order Quantity)
– MOQ is the minimum number of units that a supplier is willing to sell. Understanding MOQ is crucial for B2B buyers, as it affects inventory management and cash flow. Buyers should negotiate MOQs to align with their purchasing strategies and budget constraints. -
RFQ (Request for Quotation)
– An RFQ is a document sent to suppliers requesting pricing for specific quantities of parts. It is a standard practice for B2B buyers to use RFQs to gather competitive pricing and terms. This process helps buyers make informed purchasing decisions based on cost and supplier capabilities. -
Incoterms (International Commercial Terms)
– Incoterms are a set of predefined commercial terms that outline the responsibilities of buyers and sellers in international transactions. These terms define who is responsible for shipping, insurance, and tariffs. Familiarity with Incoterms is essential for international buyers to avoid misunderstandings and ensure smooth logistics. -
Lead Time
– Lead time refers to the time it takes from placing an order to receiving the goods. Understanding lead times is critical for inventory planning and ensuring that RV manufacturing schedules are met. Buyers should inquire about lead times when negotiating with suppliers to align production timelines effectively.
By grasping these technical properties and trade terms, international B2B buyers in regions such as Africa, South America, the Middle East, and Europe can make more informed decisions when sourcing RV parts, ultimately leading to better product performance and customer satisfaction.
Navigating Market Dynamics and Sourcing Trends in the RV Parts Manufacturers Sector
What Are the Current Market Dynamics and Key Trends in the RV Parts Manufacturers Sector?
The RV parts manufacturing sector is experiencing robust growth driven by several global factors. Rising disposable incomes and a growing interest in recreational activities, particularly in Africa, South America, the Middle East, and Europe, are leading to increased demand for RVs and their parts. Additionally, the post-pandemic resurgence in outdoor activities has significantly boosted the RV market, with consumers looking for safe travel alternatives. B2B buyers should note that this trend is not just limited to traditional markets; emerging markets in Colombia and Argentina are witnessing a surge in RV ownership, presenting lucrative opportunities for manufacturers and suppliers.
Technological advancements are reshaping sourcing strategies, with digital platforms facilitating efficient procurement processes. B2B tech trends like e-commerce integration, data analytics, and supply chain automation are becoming indispensable. Buyers can leverage these technologies to streamline operations, optimize inventory management, and enhance supplier relationships. Furthermore, the emphasis on direct-to-consumer sales models is gaining traction, allowing manufacturers to bypass traditional distribution channels and engage directly with end-users.
How Important Is Sustainability and Ethical Sourcing in the RV Parts Manufacturing Sector?
Sustainability and ethical sourcing have become pivotal in the RV parts manufacturing landscape. Environmental concerns are prompting manufacturers to adopt practices that minimize ecological impact. Buyers should prioritize suppliers that demonstrate commitment to sustainability through transparent sourcing practices, which can include the use of recycled materials, eco-friendly manufacturing processes, and waste reduction strategies.
The demand for ‘green’ certifications is growing, as consumers increasingly seek assurance that their purchases are environmentally responsible. Certifications such as ISO 14001 (Environmental Management) and the Forest Stewardship Council (FSC) for wood products are becoming essential criteria for B2B buyers when selecting suppliers. Understanding these certifications can aid buyers in making informed decisions that align with their corporate sustainability goals while appealing to environmentally conscious consumers.
What Has Been the Evolution of the RV Parts Manufacturing Sector?
The RV parts manufacturing sector has evolved significantly over the past few decades. Initially dominated by a few major players, the landscape has diversified with the entry of numerous smaller manufacturers and suppliers, particularly in emerging markets. This evolution has been fueled by technological advancements that have lowered entry barriers for new companies and enhanced production capabilities.
In the early 2000s, the industry began to see a shift towards more specialized parts, reflecting the growing complexity of RV designs and consumer preferences. Today, the focus is increasingly on customization and innovation, with manufacturers developing tailored solutions to meet specific consumer needs. This evolution underscores the importance for B2B buyers to stay informed about market developments and emerging suppliers that can offer unique value propositions.
Frequently Asked Questions (FAQs) for B2B Buyers of RV Parts Manufacturers
-
How can I effectively source RV parts from manufacturers?
To effectively source RV parts, start by identifying potential manufacturers through industry trade shows, online directories, and trade associations specific to RV components. Evaluate suppliers based on their reputation, product range, and compliance with international standards. Utilize platforms like Alibaba or Global Sources, but ensure to verify the legitimacy of suppliers through customer reviews and third-party audits. Establish clear communication regarding your requirements, including quality standards, delivery timelines, and pricing to foster a strong partnership. -
What are the common quality assurance practices among RV parts manufacturers?
Most reputable RV parts manufacturers implement stringent quality assurance practices, including ISO certification, regular audits, and adherence to international standards such as ISO 9001. They conduct thorough inspections during various production stages and perform final testing to ensure parts meet specifications. As a buyer, inquire about their quality control processes and request documentation to verify compliance. This step is crucial to ensure the reliability and durability of the parts you are sourcing. -
What are the typical minimum order quantities (MOQs) for RV parts?
Minimum order quantities (MOQs) can vary significantly among RV parts manufacturers, typically ranging from 100 to 1,000 units depending on the product type and manufacturer. Factors influencing MOQs include production capabilities, inventory levels, and customization options. As an international buyer, negotiate MOQs that align with your business needs while ensuring the manufacturer can meet your quality and timeline requirements. Consider ordering a smaller batch initially to assess quality before committing to larger orders. -
What payment terms should I expect when sourcing RV parts internationally?
Payment terms in international B2B transactions often include options like 30% upfront and 70% upon delivery, or full payment in advance for smaller orders. Some manufacturers may offer payment via letter of credit for larger transactions, providing security for both parties. Discuss payment methods such as wire transfers, PayPal, or escrow services to safeguard your investment. It’s advisable to clarify payment terms early in negotiations to avoid misunderstandings later. -
How can I customize RV parts to meet my specific needs?
To customize RV parts, communicate your specifications clearly to the manufacturer. Many manufacturers offer customization options such as size, material, and branding. It’s essential to provide detailed drawings or prototypes if available. Discuss lead times for custom orders and any additional costs involved. Establishing a close partnership with the manufacturer can facilitate smoother communication and adjustments during the design process, ensuring the final product aligns with your requirements. -
What logistics considerations should I keep in mind when importing RV parts?
When importing RV parts, consider factors such as shipping methods, freight costs, and customs regulations in your country. Choose between air freight for faster delivery or sea freight for cost-effectiveness, depending on your urgency and budget. Familiarize yourself with import duties and taxes to avoid unexpected costs. Collaborate with a freight forwarder to navigate logistics efficiently, ensuring timely delivery and compliance with international trade regulations.
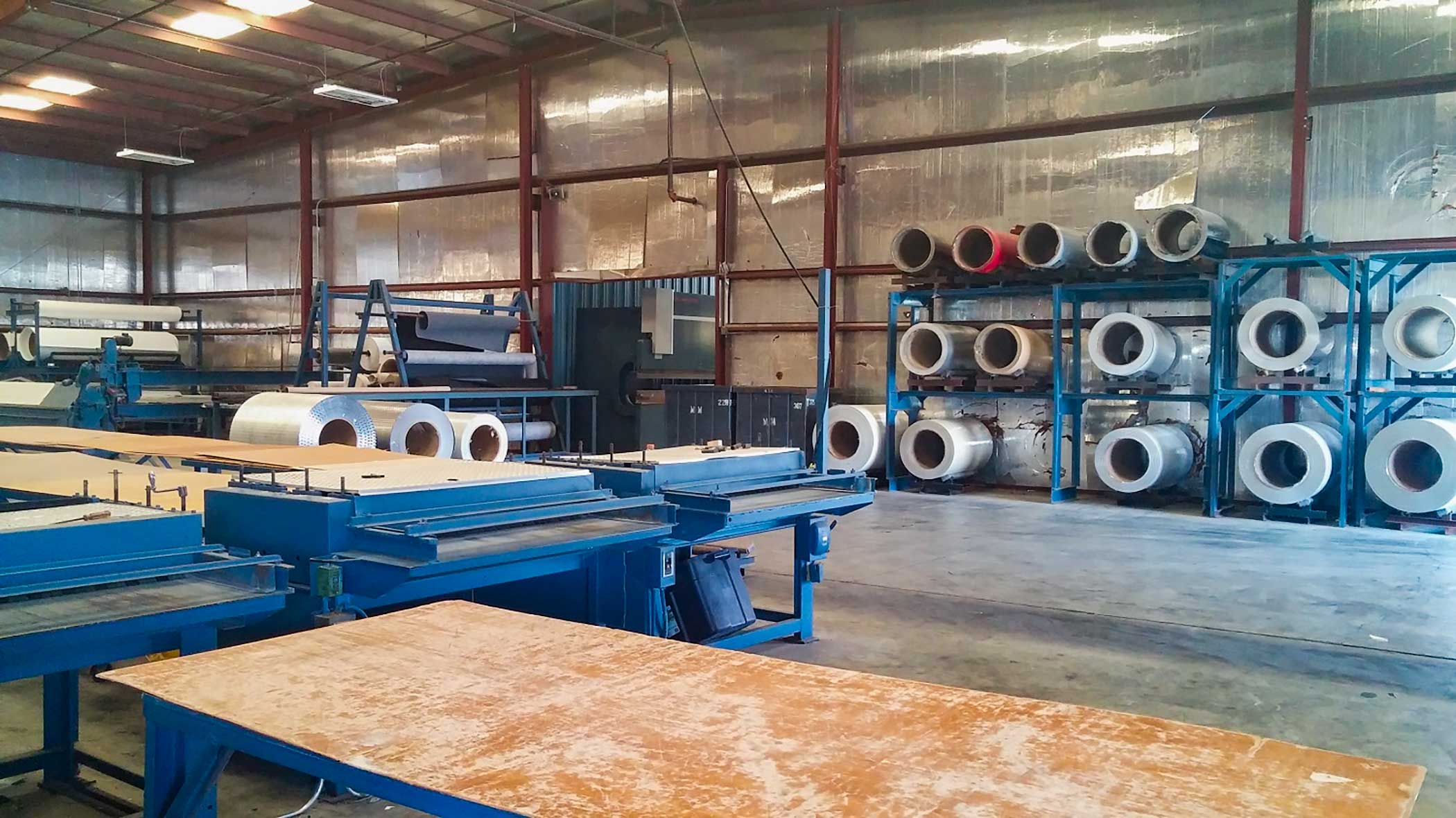
A stock image related to RV Parts Manufacturers.
-
What should I know about after-sales support from RV parts manufacturers?
After-sales support varies among RV parts manufacturers, but it is crucial for maintaining long-term relationships. Inquire about warranty policies, return procedures, and technical support for troubleshooting. A reliable manufacturer should offer assistance with installation and usage guidelines. Evaluate their responsiveness to customer inquiries and issues, as strong after-sales support can significantly enhance your operational efficiency and satisfaction with the products. -
How do I vet RV parts suppliers to ensure reliability?
Vetting RV parts suppliers involves thorough research and due diligence. Start by checking for industry certifications and customer reviews. Request references from previous clients and assess their experience with the supplier. Conduct factory visits if possible, or opt for third-party audits to evaluate manufacturing practices. Using a checklist that includes quality standards, delivery performance, and communication effectiveness can help ensure you partner with a reliable manufacturer.
Important Disclaimer & Terms of Use
⚠️ Important Disclaimer
The information provided in this guide, including content regarding manufacturers, technical specifications, and market analysis, is for informational and educational purposes only. It does not constitute professional procurement advice, financial advice, or legal advice.
While we have made every effort to ensure the accuracy and timeliness of the information, we are not responsible for any errors, omissions, or outdated information. Market conditions, company details, and technical standards are subject to change.
B2B buyers must conduct their own independent and thorough due diligence before making any purchasing decisions. This includes contacting suppliers directly, verifying certifications, requesting samples, and seeking professional consultation. The risk of relying on any information in this guide is borne solely by the reader.
Strategic Sourcing Conclusion and Outlook for RV Parts Manufacturers
What Are the Key Takeaways for B2B Buyers in RV Parts Manufacturing?
In conclusion, strategic sourcing remains a cornerstone for international B2B buyers in the RV parts manufacturing sector. By prioritizing long-term partnerships with manufacturers, buyers can not only reduce costs but also enhance quality and reliability. This is particularly crucial for buyers from regions such as Africa, South America, the Middle East, and Europe, where supply chain dynamics may differ significantly from those in traditional markets.
How Can International Buyers Navigate the Future of RV Parts Sourcing?
As the RV market continues to evolve, buyers must adapt to trends such as sustainability, digitalization, and innovation in manufacturing processes. Embracing these changes will empower buyers to make informed decisions that align with their business goals. Moreover, leveraging technology to analyze supplier performance and market conditions will provide a competitive edge.
What Should B2B Buyers Do Next?
International B2B buyers are encouraged to actively engage with RV parts manufacturers, conduct thorough market research, and participate in industry trade shows to uncover new sourcing opportunities. By doing so, they can ensure a resilient supply chain that meets the demands of an increasingly competitive landscape. The future of RV parts sourcing is ripe with potential—seize it now for sustained growth and success.